nekos SKY 650 User manual

Code 4420005 Edition no. 5 of November 2013
S
SK
KY
Y
6
65
50
0
RACK OPERATED ACTUATOR
FORCE 600 N-TRUCKS 180, 230, 350, 550, 750, 1000 MM
VOLTAGE 110÷230V~ (A.C.), 50/60 HZ –24V═(D.C.)
MANUAL FOR INSTALLATION AND USE
English
Page 2
nekos products are specially manufactured in safe
materials in compliance with the requirements of legislation
in force. When correctly mounted, installed and used in
accordance with the present instructions, our products
constitute no danger to people, animals or property.
Products subject to EU directives comply with the essential
requirements stipulated by the latter. markings mean
that our products can be sold and installed throughout the
European Union without any further formality.
The mark on our products, packaging and user manuals
provided with the product, indicate “presumed in conformity
with directives” issued by the EU. nekos holds the technical
file with all the documentation to show that our products
have all been inspected to ensure compliance with
directives conformity.
Symbols used in the manual
DANGER This indication draw the attention about potential
dangers for safety and health of peoples and animals.
INFORMATION This information give further suggestions.
ATTENTION This indication draw the attention about potential
dangers for the product itself.
WARNING This indication draw the attention about potential
damages to goods.
ENVIRONMENTAL
INSTRUCTION Environmental indication draw the attention about
potential dangers for the environment.

Page 3
Contents
1. Safety indications...............................................................................................4
2. Formulas and recommendations for installation ................................................5
2.1. Calculation of opening / closure force.......................................................5
2.2. Maximum opening in accordance with sash height...................................5
3. Technical information about function .................................................................6
4. Construction and standards...............................................................................6
5. Id plate and marking data..................................................................................6
6. Technical specifications.....................................................................................7
7. Electrical supply.................................................................................................7
7.1. Section choice of supply cables................................................................8
8. Instructions for assembly...................................................................................8
8.1. Preparation of actuator for assembly........................................................9
8.2. Assembly with outward opening window...................................................9
8.3. Assembly for cupolas or dormer windows...............................................10
8.4. Assembly for transom windows ..............................................................10
8.5. Assembly for louvered windows with no mechanical block and for sun
screens..................................................................................................10
8.6. Assembly of more than one actuator with connection bar.......................11
9. Electrical connections......................................................................................12
10.Limit switches .................................................................................................13
10.1. Stroke-end at opening and closure.........................................................13
10.2. Stroke adjustment where required..........................................................13
11.Checking for correct assembly........................................................................13
12.Emergency manoeuvres, maintenance and cleaning......................................14
13.Troubleshooting..............................................................................................14
14.Environmental protection ................................................................................14
15.Certificate of guarantee...................................................................................14
16.Declaration of conformity................................................................................15
Page 4
1. Safety indications
ATTENTION:
P
LEASE READ THE FOLLOWING SAFETY INDICATIONS CAREFULLY
BEFORE ATTEMPTING INSTALLATION OF THIS APPLIANCE
.
THESE INDICATIONS WILL
HELP TO AVOID CONTACT WITH ELECTRICAL CURRENT
,
INJURY AND OTHER
ACCIDENTS
.
PLEASE KEEP THIS MANUAL FOR FUTURE CONSULTATION
.
The SKY650 rack operated actuator has been designed exclusively for moving outward
opening windows, transom windows, cupolas, dormer windows, large industrial
skylights, sliding windows and blinds.
Any use of the actuator for applications other than those indicated must previously be
authorized by the manufacturer upon technical verification of the application.
The device must only be installed by competent and qualified technical staff.
After removing all packaging, please verify that all parts of the appliance are
present.
Any plastic bags, polystyrene, or small metallic parts such as nails, clips, etc.
must be stored out of the reach of children as they constitute potential sources
of danger.
Before connecting the appliance to the electricity supply, check that the
electricity supply in use has the same characteristics as those indicated on the
technical data label on the device.
This appliance is destined exclusively for the use for which it has been designed
and the manufacture cannot be held responsible for any damages incurred by
improper use.
The manufacturer must be consulted for any special application.
Installation of the device must be carried out in accordance with the instructions
set out by the manufacturer. Failure to follow these instructions could
compromise safety.
Electricity supply installation must be carried out in accordance with regulations
in force.
To ensure effective separation from the electricity grid, we suggest installation
of a temporary approved type bipolar switch (push button). A multi-pole main
switch with minimum contact opening of 3 mm should be installed at the start of
the command line.
Never clean the device with solvents or jets of water. Never immerse appliance
in water.
Eventual repairs must only be carried out by qualified staff at a service centre
authorized by the manufacturer.
Always require exclusive use of original spare parts. Failure to comply with this
stipulation could compromise safety and forfeit warranty benefits for the device.
In the event of trouble or doubts, please refer to your trust retailer or directly to
NEKOS S.r.l.

Page 5
ATTENTION
Warning: risk of injury in the event that the window should fall on outward
opening window frames. A safety system should be mounted onto the window
to guard against falls. This system should be able to withstand at least three
times the total weight of the window.
Warning:
this device may cause injury by crushing or dragging. During function,
when the actuator closes the frame, it applies a pressure force of 660N against
the ledge of the casing, and all due measures, care and attention should be
taken to avoid any crushing of fingers.
Warning:
in the event of damage or malfunction, switch off the device,
disconnect any electrical connections and request the intervention of a qualified
technician.
2. Formulas and recommendations for installation
2.1.
Calculation of opening / closure force
Using the formulas on this page, approximate calculations can be made for the force required
toopen or close the window considering allthe factors that determine the calculation.
Symbols used for the calculation
F (Kg) = Force for opening or closing P (Kg) = Weight of the window (mobile sash only)
C (cm) = Opening stroke (actuator stroke) H (cm) = Height of the mobile sash
For horizontal light domes or skylights
F = 0,54 x P
(Eventual weight of snow or wind on the
cupola should be calculated separately).
For vertical windows
TOP HUNG WINDOWS
,
OUTWARD OPENING
(A)
BOTTOM HUNG WINDOWS
(B)
F = 0,54 x P x C : H
(Eventual load of favourable or unfavourable
wind on the sash should be calculated
separately.)
2.2.
Maximum opening in accordance with sash height
The actuator stroke should be selected in accordance with the height of the sash and
its application. Make sure that the actuator does not touch the profile of the sash when
Page 6
moving along its track, and ensure there are no obstacles blocking the opening and that
the rack moves smoothly along the window frame.
A
TTENTION
. For safety reasons, always check application before fixing the
actuator to the frame or sash. In the event of difficulty, request assistance from
the manufacturer to check application.
3. Technical information about function
The rack actuator performs opening and closing movements for the window using a
round section steel rack. Movement is powered by electricity that feeds a reduction
motor controlled by a functional electronic device.
The opening stroke for the window CANNOT be programmed as it is regulated by the
length of the rod on the reduction motor. The electronic control device allows the rack to
protrude until it encounters an obstacle that blocks its stroke. This could be provided by
the internal lock on the rack or complete closing/opening of the window.
In both outwards and return directions the stroke-end uses a self-defining electronic
process with power absorption, and for this reason, no adjustment is required.
4. Construction and standards
The SKY650 rack actuator has been designed and manufactured to open and close top
hung windows opening outwards, bottom hung windows, dormer windows, light domes,
skylights and louvered windows or sun blades. Specific use is for ventilation and airing
of areas; any other use must previously be approved by the manufacturer.
Application is performed using the brackets provided and any other type of assembly
should be checked with the manufacturer, who will not accept any responsibility for
incorrect or malfunctioning assembly.
Electrical connections must comply with standards in force on the design and
production of electrical appliances.
The actuator has been manufactured according to European Union directives and
conforms to marking.
Any eventual service or control device for the actuator must be produced according to
standards in force and must comply with the standards issued by the European
Community.
The SKY650 actuator comes packaged in a cardboard container which contains two
pieces. Boxes for tandem actuators each contain all parts required for movement of
windows. Each package contains:
•2 actuators with 2 metre (±5%) lead.
•2 standard support brackets with respective grips and fixing screws.
•2 brackets for fixing to the frame.
•Small parts packaging.
•Instruction manual.
5. Id plate and marking data
All actuators have marking and are destined for use in the European Union without further
requirements.

Page 7
The marking on the product, packaging and indications for use
provided with the product indicate ‘presumed conformity to the
directives’ issued by the European Community.
The manufacturer holds the technical archive with documentation
providing that products have been examined and evaluated for
conformity to directives.
ID plate data are indicated on a polyethylene adhesive label applied
externally on the outside of the container, printed in black on a grey
background. Values conform to EC requirements inforce.
See figure for example of labelling.
6. Technical specifications
Model SKY650 230V SKY650 24V
Thrust and traction force 600 N
Course lengths 180, 230, 350, 550, 750, 1000 mm (*)
Input voltage 110÷230V~AC
50/60 Hz 24V═DC
Current absorption at nominal load 0,320 A 1,600 A
Power absorption at nominal load ~ 38 W ~ 38 W
Travel speed without load 11 mm/s 9,5 mm/s
Length of run without load In accordance with length of truck run
Double electrical insulation Yes Low tension
Type of service S
2
of 3 min
Max. and min. temperatures for function -5 +65 ºC
Degree of protection for electrical devices IP55
Adjustment of socket at casing Position self regulating
Connection in parallel of two or more motors Yes
Connection in tandem or in series Yes
Limit switch stop at opening and closure At absorption of power
Protection against overload at opening and
closure At absorption of power
Dimensions 115x42x(Course length+135) mm
Weight Varies according to construction
Information presented in these illustrations is not binding and is also subject to variation without prior notice.
(*) Technical personnel can shorten track runs by adjusting the internal limit switches.
7. Electrical supply
Depending on which model is used, the actuator can function on 24VDC (direct
current), with two cables in the lead, or on 230VAC (alternating current) 50 Hz with a
three cable lead.
For the low voltage version, a feeder with an outcoming tension correspondent to the
one indicated on the technical data label attached to the device and which transforms
supply mains voltage (230VAC 50Hz or other) in 24VDC should be used. The feeder
must have class II protection, and correct functioning is guaranteed if a feeder type
approved or suggested by the manufacturer is used.
Page 8
Warning:
SKY650 24VDC has been realized and programmed to function with
a stabilized tension of 24VDC. Therefore, if fed with a stabilized tension lower
than 24VDC the 600N the power is not guaranteed, while if fed with a stabilized
tension higher than 24VDC some breakings could occur due to the high power
the engine gives. For this we suggest, before feeding the device and during its
functioning, to check that the tension applied has the correct value (24VDC
stabilized).
So, if fed with a rectified but not stabilized tension, the actuator can NOT have a
correct functioning.
7.1.
Section choice of supply cables
In low tension supply systems, tension falls due to current passage in conductors is a
basic aspect for safety and good appliance function. It is therefore extremely important
that the conductor section in function of cable length is calculated correctly. The
following table indicates cable lengths for an actuator connected at nominal charge.
Cables section
Actuator using
24VDC 230VAC
4,00 mm
2
~ 1.000 m ~ 3.000 m
2,50 mm
2
~ 750 m ~ 2.200 m
1,50 mm
2
~ 450 m ~ 1.350 m
0,75 mm
2
~ 160 m ~ 500 m
0,50 mm
2
~ 130 m ~ 400 m
8. Instructions for assembly
These indications are intended for the attention of technicians and specialized
personnel. Basic job and safety techniques are therefore not included.
All preparatory operations, assembly and electrical connections must be carried out by
technical and specialized personnel to guarantee best performances and good function
of the chain operated actuator. First of all, please check that the following fundamental
points have been satisfied:
Gear motor performances must be sufficient to move the window; any limits
indicated in the technical data table on the product cannot be exceeded (page
7). Any eventual calculations may be made using the formula on page 5 of this
manual.
Warning
: Check that appliance has electrical feeding type equal to the one
provided by checking with the data reported on the label attached to the gear
motor. The actuator with the 3 (three) cable lead functions on 230VAC 50/60Hz.
The actuator with the 2 (two) cable lead functions on 24VDC supplied either by
batteries or by means of the lead.
Check that the actuator has not been damaged during transport, first visually
and then by working it in both directions.
Transom window frames entail the risk of injury caused by accidental fall of the
window. A compass limit switch or alternative safety system suitably designed
to prevent any accidental falls should be installed.

Page 9
8.1.
Preparation of actuator for assembly
Before starting assembly of the actuator, prepare the following material for completion,
equipment and tools.
For fixing onto metal window frames: M5 threaded inserts (6 pieces), M5x12 flat
headed metric screws (6 pieces).
For fixing onto wooden window frames: self threading screws for wood Ø4.5 (6 pieces).
For fixing onto PVC window frames: self threading screws for metal Ø4.8 (6 pieces).
Equipment and tools: measuring tape, pencil, drill/screwdriver, set of drill heads for
metal, insert for screwing in, electricians pliers, screwdrivers.
Fig. 1 Fig. 2 Fig. 3 Fig. 3 bis
Fig. 4 Fig. 5 Fig. 5 bis Fig. 6
8.2.
Assembly with outward opening window
A. Mark the centre line of the frame in pencil on both moveable and fixed parts (Fig. 1).
B. Place the motor support bracket along the edge of the fixed part of the frame in line
with the centre line marked out previously and mark the positions for the four holes
for the fixing screws (Fig. 2).
C. Drill holes into the frame and screw in the motor support bracket, making sure that
all screws are fitted tightly (Fig. 3 and 3bis).
D. Line up the front bracket along the centre line on the moveable part of the frame and
mark out the three holes required for the screws (Fig. 4).
E. Drill the holes and screw in the front bracket, making sure that all screws are fitted
tightly (Fig. 5 and 5bis).
F. Assemble the clamp screws onto the motor support bracket and screw in lightly.
G. Insert the dove-tailed section of the actuator into the clamp screws. Make sure the
shaped part of the base fits neatly into the slot to ensure the actuator runs smoothly
along its axis.
H. Now position the actuator so the eyebolt head is inserted into the front bracket
support. Insert the M6x25 screw into the bracket and into the eyebolt and tighten the
self-locking bolt with two 10 spanners.
I. Manually move the actuator along its axis to close the frame and make it weather
tight. Tighten the clamp screws previously only placed and set the actuator in line
with the frame. Suggested tightening torque is 5÷7 Nm.
Page 10
J. Plug the actuator in and carry out a test to check opening and closure of the frame.
Make sure the frame closes fully and is weather tight. The limit switch for the
actuator is automatic on reentry.
K. The equipment will exert a pressure of over 660 N to guarantee even the largest of
frames is completely weather tight.
8.3.
Assembly for cupolas or dormer windows
(Follow the instructions set out in “Assembly for outward opening windows”).
8.4.
Assembly for transom windows
A. Mark the centre line of the frame in pencil on both moveable and fixed parts (Fig. 1).
B. Place the motor support bracket along the edge of the moveable part of the frame in
line with the centre line marked out previously and mark the positions for the four
holes for the fixing screws (Fig. 2).
C. Drill holes into the frame and screw in the motor support bracket, making sure that
all screws are fitted tightly (Fig. 3 and 3bis).
D. Line up the front bracket along the centre line on the fixed part of the frame and
mark out the three holes required for the screws (Fig. 4).
E. Drill the holes and screw in the front bracket, making sure that all screws are fitted
tightly (Fig. 5 and 5bis).
F. Assemble the clamp screws onto the motor support bracket and screw in lightly.
G. Insert the dove-tailed section of the actuator into the clamp screws. Make sure the
shaped part of the base fits neatly into the slot to ensure the actuator runs smoothly
along its axis.
H. Now position the actuator so the eyebolt head is inserted into the front bracket
support. Insert the M6x25 screw into the bracket and into the eyebolt and tighten the
self-locking bolt with two 10 spanners.
I. Manually move the actuator along its axis to close the frame and make it weather
tight. Tighten the clamp screws previously only placed and set the actuator in line
with the frame. Suggested tightening torque is 5÷7 Nm.
J. Plug the actuator in and carry out a test to check opening and closure of the frame.
Make sure the frame closes fully and is weather tight.
K. The limit switch for the actuator is automatic on reentry. The equipment will exert a
pressure of over 660N to guarantee even the largest of frames is completely
weather tight.
8.5.
Assembly for louvered windows with no mechanical block and for
sun screens
This type of assembly requires electricity to move the actuator. Check the technical
specifications label on the motor for required voltages.
A. Connect the actuator to the electricity supply, and turn it on until the bar reaches the
limit switch maximum opening point.
B. Close the louvres of the frame by manually operating the levers on the frame.
C. Place the eyebolt head of the actuator in between the two levers (or in line with the
opening on the lever if there is only one), insert the pin and lock into position with
the nuts provided.

Page 11
D. Assemble the clamp screws onto the motor support shaft and screw lightly into
position.
E. Mount the motor support shaft onto the profile of the actuator, ensuring the clamp
screws fit correctly into the profile socket, and make sure the socket is positioned
correctly into the base of the actuator (Fig. 6).
F. Keep louvres or sun screen closed and place the shaft on the wall vertical to the
frame, making sure that the axis of the actuator is parallel to the lever and
perpendicular to the connection pin. Check the shaft has been inserted into the base
of the actuator
G. Mark out the four holes for drilling for the screws for the motor support shaft.
H. Drill holes, insert the screws and fix the motor support shaft to the frame.
I. Tighten the clamp screws. Suggested tightening torque is 5÷7 Nm.
J. Turn on the actuator and carry out a complete test to check window opens and
closes correctly.
8.6.
Assembly of more than one actuator with connection bar
SKY650 actuators can be used in tandem or series by means of a mechanical
connection bar. Movement is thus transmitted mechanically and uniformly and at the
same speed.
Two or more actuators can be mounted on the frame with one or more motors in
accordance with force requirements. The following diagram indicates position and
distance between centres to be used during mounting.
TANDEM WITH TWO MOTORS
TANDEM WITH ONE MOTOR
DISTANCE BETWEEN CENTRES OF THE CONNECTION BARS
Code Description Length of bar
(mm) “D”
distance between
centres (mm)
4010009
Connection bar 1000 mm length 1.035
1.000
4010010 Connection bar 1500 mm length 1.535 1.500
4010011
Connection bar 2000 mm length 2.035
2.000
4010011
Connection bar 2500 mm length 2.535
2.500
Page 12
Assemble as follows:
A. Mark the assembly distance between centres for the two
actuators out onto the frame in accordance with the
measurements in the above table.
B. Place the support brackets of the actuator into position, mark
out the holes for drilling, drill the frame and mount the
brackets (see “Assembly for outward opening windows” for
details).
C. Place the front brackets into position, mark out the holes for
drilling, drill the frame and mount the front brackets (see
“Assembly for outward opening windows” for details).
D. Mount the actuators (see “Assembly for outward opening
windows” for details) – see Fig.7.
E. Mount the connection bar as follows:
•Insert the connection bar first into one of the actuators, and then into the second
actuator. Make sure the bar protrudes at least 2 mm from each actuator (Fig. 7 bis).
•Mount and screw the M8x14 mm flat headed screw (provided with connection
bar), into the two ends of the bar to prevent the bar from slipping out.
9. Electrical connections
The actuator comes with a 2 m long circa (±5%) lead which has been calculated in
accordance with safety rules.
In the event that the distance between the actuator and the control button should
exceed this length, the cable should be extended. See table on page 8 for conductor
section indications. For harness, please follow the these diagrams.
After connecting the electricity supply to the control button (bipolar with arrows if possible),
check that the up key function opens the window frame and the and down key function
closes it. In the event of incorrect function, invert the two wires marked light blue and
Fig. 7
Fig. 7 bis

Page 13
brown in the case of 24VDC motors and invert the two wires marked black and brown for
230VAC motors.
WARNING: after every limit switch or electronic protection device function the
rack will back track for around 2 mm in the opposite direction. This is quite
normal, and has been designed to release tension on mechanical parts and
allow complete weather proofing to enhance durability of mechanical parts.
10. Limit switches
10.1.
Stroke-end at opening and closure
The limit switch at opening / closure is automatic, electronically operated and cannot be
programmed. The actuator stops when the charge is absorbed when the window is
completely open / closed, or when the charge absorbed is more than 10% of the nominal
charge. In this case, at maximum charge the actuator exercises a traction force of over
660N.
10.2.
Stroke adjustment where required
Factory settings for track lengths can be shortened to regulate how much of the rod
protrudes. This operation must be carried out at the workbench with proper equipment
by technical personnel qualified to operate with maximum care and safety.
Procedure:
1. Remove the four screws on the front head of the SKY650 actuator.
2. Extract the head and rod from the body of the actuator.
3. Unscrew the two screws locking the two limit switch block pieces.
4. Move the rubber stopper and block to the required position.
5. Screw the two screws used for fixing the block into position back in again.
6. Re mount everything back onto the body of the actuator.
7. Screw in the four screws on the front head and check the settings for the new track
run.
11. Checking for correct assembly
Check that the frame has closed completely, even at the corners, and check
there are no obstacles caused by assembly in the wrong position.
Make sure the actuator is aligned with the axis of the window at 90°to the
window itself, otherwise the rack will exert incorrect pressure on the rod and
consume more voltage.
Check the lead is not too tight, as this could damage the actuator during
rotation, opening and closing of the window.
Check all screws and nuts have been properly tightened.
Page 14
12. Emergency manoeuvres, maintenance and cleaning
Should the window have to be opened manually in the event of no electricity, mechanical
failure, or for normal maintenance or cleaning of the external surface of the window frame,
the following instructionsshould be followed:
1. Unscrew the nut from the pin screw fixing the eyebolt head to the front shaft.
2. Hold the window with one hand and use the other hand to remove the pin screw
(this operation should be performed with the window open at least 10 cm to make
it easier to remove the screw).
3. Manually open the window.
A
TTENTION
:
RISK OF THE WINDOW FALLING OUT
;
THE SASH IS IN DANGER OF
FALLING OUT AS IT IS NO LONGER HELD IN PLACE BY THE RACK
.
4. After maintenance and/or cleaning operations are complete, repeat points 1 and
2 in reverse order.
In the event in which the cable of feeding it is damaged, to make to replace it from the
constructor or a qualified technician.
13. Troubleshooting
Please consult the following table for any eventual problems with function during
installation or normal use:
Problem Possible cause Solution
•Gear motor does not
work.
•
No electricity at source.
•Leadnot connected,or
one of the wires has come
loose.
•
Check trip switch and
safety switch.
•Check all electrical
connections on gear motor.
14. Environmental protection
All materials used in the manufacture of this appliance are recyclable.
We recommend that the device itself, and any accessories, packaging, etc. be
sent to a centre for ecological recycling as established from laws in force on
recycling.
The device is mainly made from the following materials: aluminium, zinc, iron,
plastic of various type, cuprum. Dispose materials in conformity with local
regulations about removal.
15. Certificate of guarantee
The manufacturer will guarantee good function of the appliance. The manufacturer
shall undertake to replace defective parts due to poor quality materials or
manufacturing defects in accordance with article 1490 of the Civil Code.
The guarantee covers products and individual parts for 2 years from the date
of purchase. The latter is valid as long as the purchaser possesses proof of
purchase and completion of all agreed conditions of payment.
Guarantee of good function of appliances agreed by the manufacturer implies

Page 15
that the latter undertakes to repair or replace free of charge and in the
shortest period possible any parts that break while under warranty.
The purchaser is not entitled to any reimbursement for eventual direct or
indirect damage or other expenses incurred. Attempt to repair by personnel
unauthorised by the manufacture shall render the warranty null and invalid.
The warranty does not cover fragile parts or parts subject to natural wear and
tear or corrosion, overload, however temporary etc. The manufacturer will
accept no responsibility for eventual damage incurred by erroneous assembly,
manoeuvre or insertion, excessive stress or inexpert use.
Repairs performed under guarantee are always "ex factory of the
manufacturer". Respective transport expenses (out/back) are the
responsibility of the purchaser.
16. Certificato di conformità
Declaration of conformity
NEKOS
S.r.l. - Via Capitoni, 7/5
36064 Mason Vicentino (VI) – ITALY
+39 0424 411011 – Fax +39 0424 411013
www.nekos.it [email protected]
Il sottoscritto legale rappresentante del costruttore NEKOS S.r.l.
The undersigned, representative of the following manufacturer
dichiara
declares
che il prodotto elettrico:
that the electrical product:
è conforme alle disposizioni legislative che traspongono le seguenti direttive:
Direttiva 2004/108 CE (Direttiva EMC) e successivi emendamenti
Direttiva 2006/95 CE (Direttiva Bassa Tensione) e successivi emendamenti
Is in accordance with the following Directives:
2004/108 EC Directive (EMC Directive) and subsequent amendments
2006/95 EC Directive (Low Voltage Directive) and subsequent amendments
Ultime due cifre dell’anno in cui è affissa la marcatura CE: 06
Last two figures of the year of the CE marking:
Luogo: Mason Vicentino (VI) - Italy
Place:
Data: 15/12/2006 / 2006/12/15
Date:
Firma: Giuliano Galliazzo
President
Signature:
Modello / Model
Designazione / Designation
SKY650 Attuatore a cremagliera 110÷230VAC - 24VDC
Rack actuator 110÷230VAC - 24VDC
Page 16
NEKOS
S.r.l.
I - 36064 - MASON VICENTINO (VI) - Via Capitoni, 7/5
Telephone (0039)
0424 411011
Fax (0039)
0424 411013
Table of contents
Other nekos Controllers manuals

nekos
nekos SKY 650 User manual
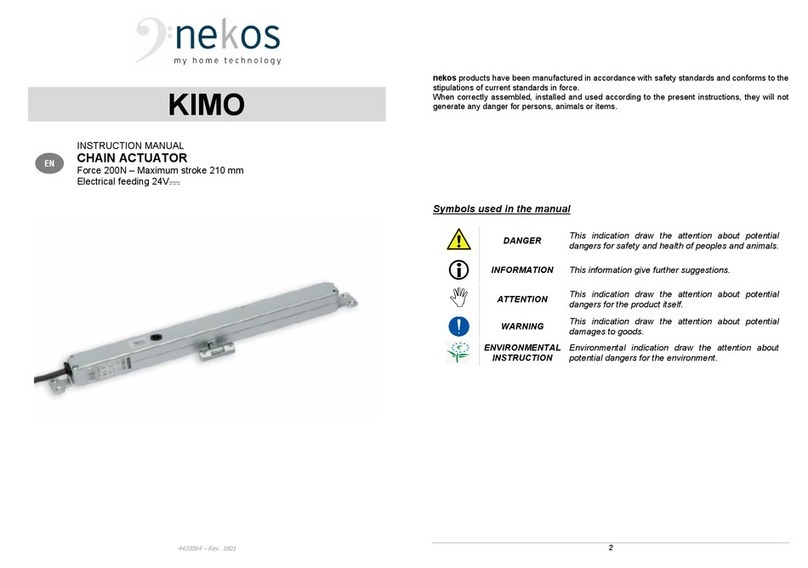
nekos
nekos KIMO User manual

nekos
nekos SKY 450 User manual
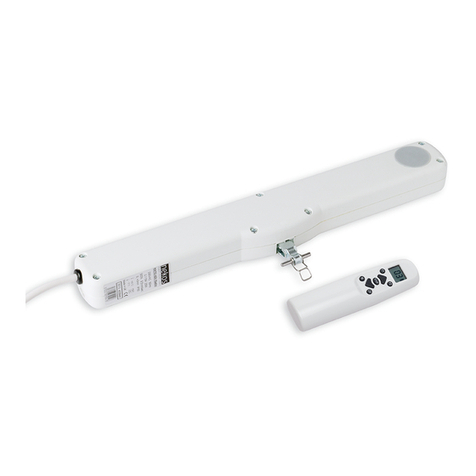
nekos
nekos KATO ADV RADIO User manual
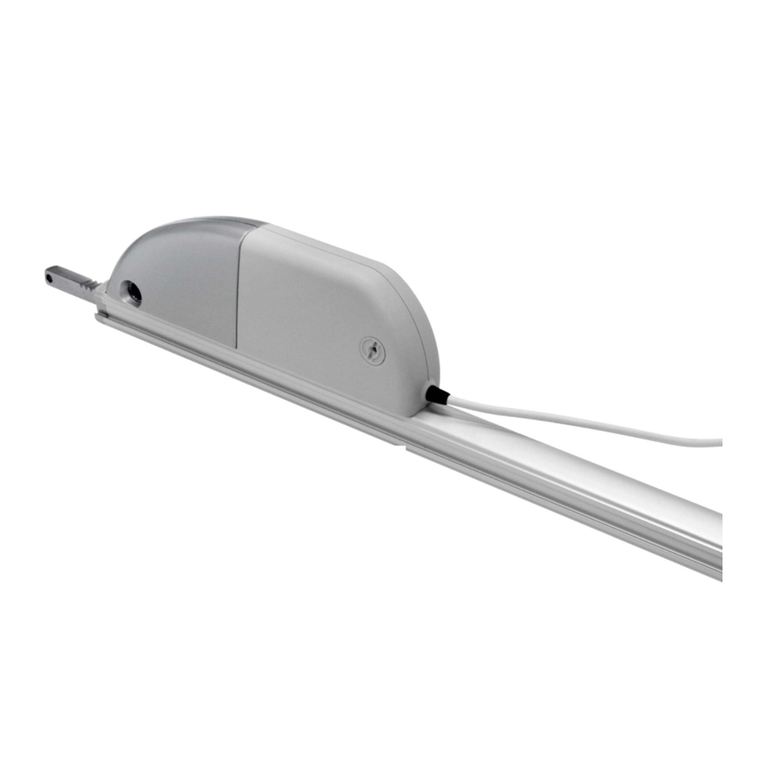
nekos
nekos SKYRO 850 User manual
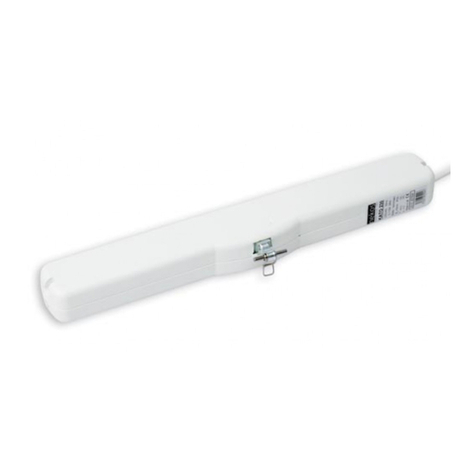
nekos
nekos KATO RADIO 230V User manual

nekos
nekos INKA 356 Series User manual
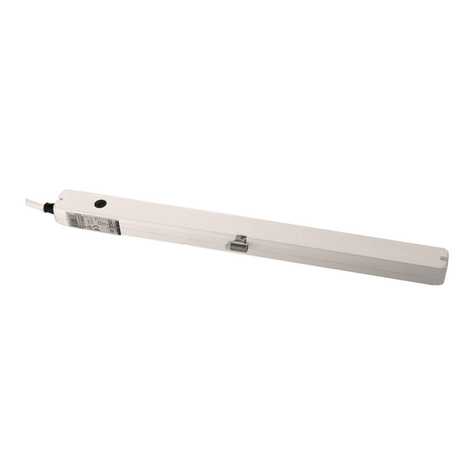
nekos
nekos KIMO 202 User manual
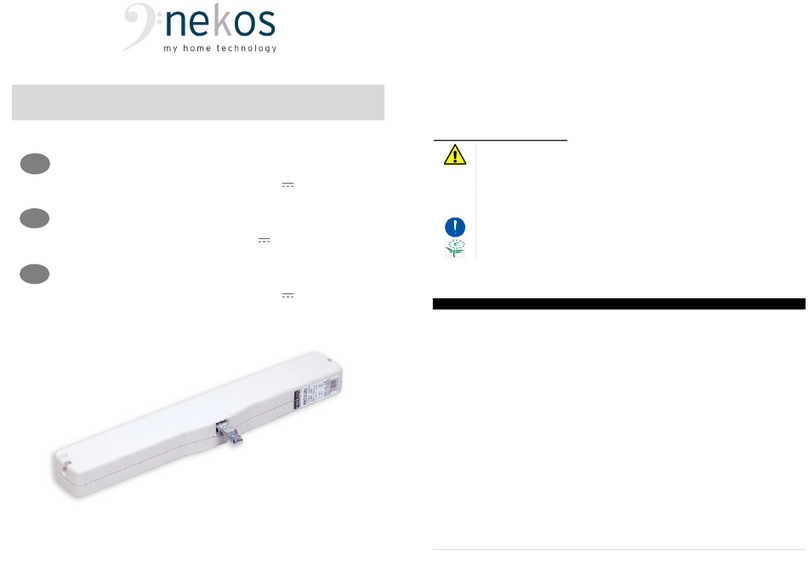
nekos
nekos KATO 253 User manual
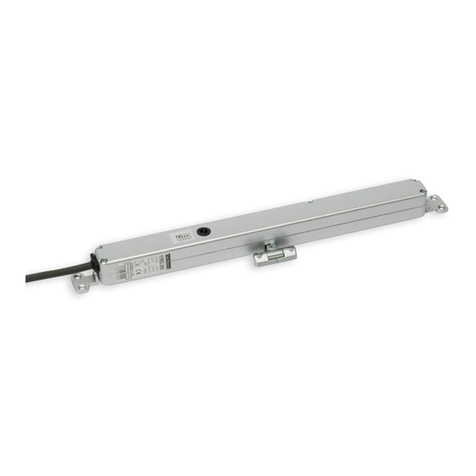
nekos
nekos KIMO 24V User manual
Popular Controllers manuals by other brands
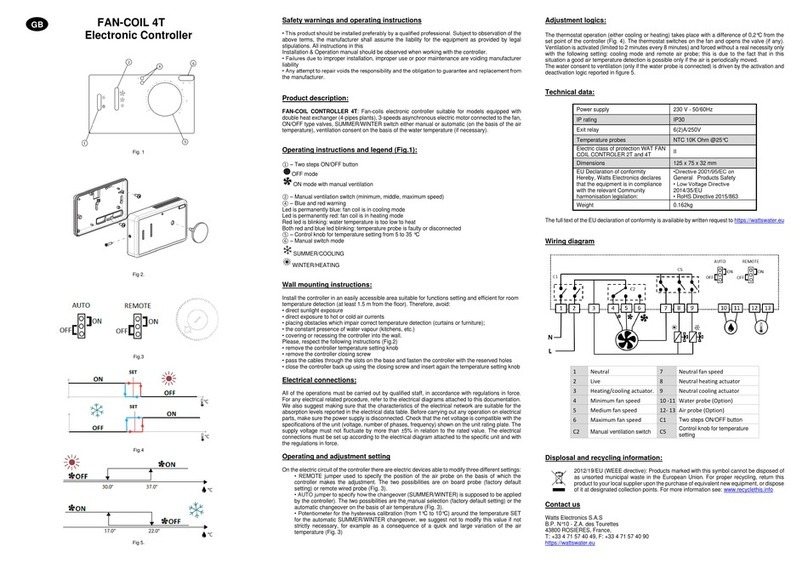
Watts Electronics
Watts Electronics FAN-COIL 4T quick start guide

Thermomax
Thermomax SMX 100 user manual
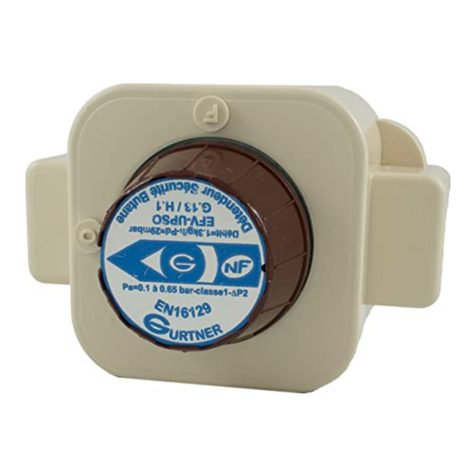
GURTNER
GURTNER EN16129 manual
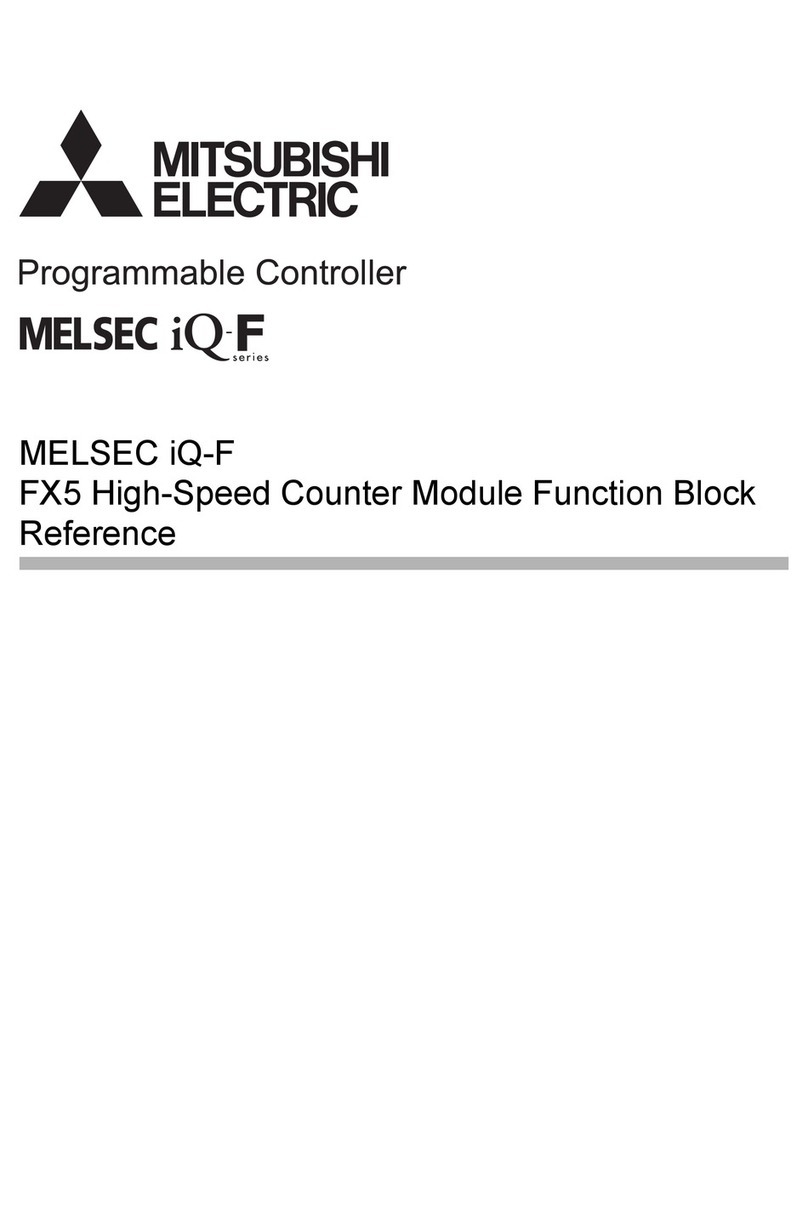
Mitsubishi Electric
Mitsubishi Electric MELSEC iQ-F Series manual
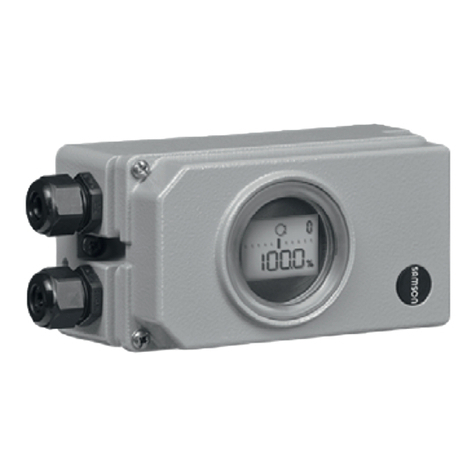
Samson
Samson 3730 Series Mounting and operating instructions
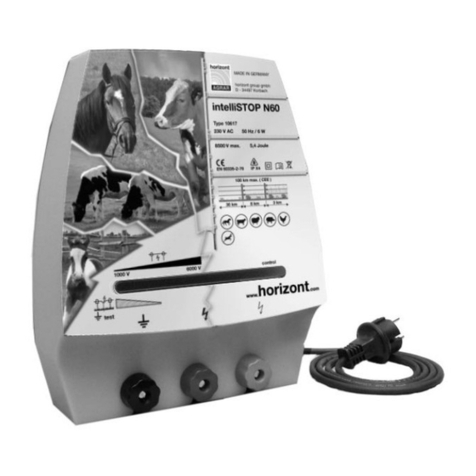
Horizon Fitness
Horizon Fitness intelliSTOP N60 Operating instruction