Omron D4B-N - User manual

G-243D4B-@N
D4B-
@
N
Safety Limit Switch
D4B-#N
• Snap-action or slow-action contact for
accurate switching with safe operation
via a direct opening mechanism with
metal deposition between mating con-
tacts.
• Two sets of contacts: one (NC) for safe-
ty category circuit and the other (NO)
for control circuit.
• Contacts opened by direct opening
mechanism (NC contacts only), thus
preventing faulty operation due to fac-
tors such as metal deposition.
• Wide standard operating temperature
range:
–40°C to 80°C (standard type).
• Safety of lever settings ensured using a
mechanism that engages a gear be-
tween the operating position indicator
plate and the lever.
• Equipped with a mechanism that indi-
cates the applicable operating zone, as
well as push-button switching to control
left and right motion.
• Conforms to EN (TÜV) standards cor-
responding to the CE marking.
• 3-conduit switches are available.
• Metric conduit types available.
Model Number Structure
Model Number Legend
1. Conduit
1: PG13.5 (1-conduit)
2: G1/2 (PF1/2) (1-conduit)
3: 1/2-14NPT (1-conduit)
4: M20
5: PG13.5 (3-conduit)
6: G1/2 (PF1/2) (3-conduit)
7: 1/2-14NPT (3-conduit)
8: M20 (3-conduit)
2. Built-in Switch
1: 1NC/1NO (snap-action)
3: 1NC/1NO (slow-action) gold-plated contacts
5: 1NC/1NO (slow-action) (see note)
A: 2NC (slow-action)
B: 2NC (slow-action) gold-plated contacts
Note: Excluding D4B-##81N and D4B-##87N models.
3. Actuator
00: Switch box (without head)
11: Roller lever (standard)
16: Adjustable roller lever
17: Adjustable rod lever
1R: Roller lever
(conventional D4B-compatible)
70: Top plunger
71: Top roller plunger
81: Coil spring
87: Plastic rod
1 2 3
D4B-####N
F502-EN2-04.book Seite 243 Dienstag, 26. Juli 2005 5:48 17

G-244 Safety Sensors / Components
Ordering Information
List of Models Safety limit switch, mechanical form lock
Switches (EN50041)
Note: 1. Mechanically speaking, these models are basic limit switches.
2. The D4B-#N is a Limit Switch conforming to European standards, and PG13.5 is commonly used in Europe.
3-conduit Switch
Note: 1. Mechanically speaking, these models are basic limit switches.
2. The D4B-#N is a Limit Switch conforming to European standards, and M20/PG13.5 is commonly used in Europe.
3. The wobble lever models are ordinary limit switches and are not approved under EN, GS, and SUVA’s Direct Opening Certificate.
Actuator
Conduit size
PG13.5 (see note 2) G1/2 M20
1NC/1NO
(Snap-
action)
1NC/1NO
(Slow-
action)
2NC
(Slow-
action)
1NC/1NO
(Snap-
action)
1NC/1NO
(Slow-
action)
2NC
(Slow-
action)
1NC/1NO
(Snap-
action)
1NC/1NO
(Slow-
action)
2NC
(Slow-
action)
Side
rotary
Roller
lever
(form A)
D4B-1111N D4B-1511N
D4B-1A11N D4B-2111N
D4B-2511N
D4B-2A11N D4B-4111N
D4B-4511N
D4B-4A11N
Adjustable
roller lever
(see note 1)
D4B-1116N D4B-1516N
D4B-1A16N D4B-2116N
D4B-2516N
D4B-2A16N D4B-4116N
D4B-4516N
D4B-4A16N
Adjustable
rod lever
(form D)
(see note 1)
D4B-1117N D4B-1517N
D4B-1A17N D4B-2117N
D4B-2517N
D4B-2A17N D4B-4117N
D4B-4517N
D4B-4A17N
Top
plunger
Plain
(form B) D4B-1170N D4B-1570N
D4B-1A70N D4B-2170N
D4B-2570N
D4B-2A70N D4B-4170N
D4B-4570N
D4B-4A70N
Roller
(form C) D4B-1171N D4B-1571N
D4B-1A71N D4B-2171N
D4B-2571N
D4B-2A71N D4B-4171N
D4B-4571N
D4B-4A71N
Wobble
lever
(see
note 1)
Coil spring D4B-1181N ---
D4B-1A81N D4B-2181N
---
D4B-2A81N D4B-4181N
---
Plastic rod D4B-1187N ---
D4B-1A87N D4B-2187N
---
D4B-2A87N D4B-4187N
---
Actuator
Conduit size
PG13.5 (see note 2) G1/2 M20
1NC/1NO
(Snap-
action)
1NC/1NO
(Slow-
action)
2NC
(Slow-
action)
1NC/1NO
(Snap-
action)
1NC/1NO
(Slow-
action)
2NC
(Slow-
action)
1NC/1NO
(Snap-
action)
1NC/1NO
(Slow-
action)
2NC
(Slow-
action)
Side
rotary
Roller
lever
(form A)
D4B-5111N D4B-5511N
D4B-5A11N D4B-6111N
D4B-6511N
D4B-6A11N D4B-8111N
--- ---
Adjust-
ableroller
lever (see
note 1)
D4B-5116N D4B-5516N
D4B-5A16N D4B-6116N
D4B-6516N
D4B-6A16N D4B-8116N
--- ---
Adjustable
rod lever
(form D)
(see note
1)
D4B-5117N D4B-5517N
D4B-5A17N D4B-6117N
D4B-6517N
D4B-6A17N D4B-8117N
--- ---
Top
plunger
Plain
(form B) D4B-5170N D4B-5570N
D4B-5A70N D4B-6170N
D4B-6570N
D4B-6A70N
--- --- ---
Roller
(form C) D4B-5171N D4B-5571N
D4B-5A71N D4B-6171N
D4B-6571N
D4B-6A71N D4B-8171N
---
D4B-8A71N
Wob-
ble le-
ver
(see
note 1)
Coil
spring D4B-5181N ---
D4B-5A81N D4B-6181N
---
D4B-6A81N
--- --- ---
Plastic
rod D4B-5187N ---
D4B-5A87N D4B-6187N
---
D4B-6A87N
--- --- ---
F502-EN2-04.book Seite 244 Dienstag, 26. Juli 2005 5:48 17

G-245D4B-@N
D4B-
@
N
Replacement Part
Because the D4B-#N employs a block mounting construction, the switch box, operating head, and lever (side rotary type only) may be ordered as
a complete assembly or individually as replacement parts. (Replacement parts are not available as a switch box and head assembly or as a head
and lever assembly.)
Switch Box
Operating Heads
Levers (for Side Rotary Switches)
Note: Other types of lever are also available.
EN50041 3-conduit type
PG13.5 G1/2 1/2-14NPT PG13.5 G1/2 1/2-14NPT
D4B-1100N D4B-2100N D4B-3100N D4B-5100N D4B-6100N D4B-7100N
D4B-1500N D4B-2500N D4B-3500N D4B-5500N D4B-6500N D4B-7500N
D4B-1A00N D4B-2A00N D4B-3A00N D4B-5A00N D4B-6A00N D4B-7A00N
Actuator Type Model
Side rotary Standard D4B-0010N
Top plunger Plain D4B-0070N
Roller D4B-0071N
Wobble lever Coil spring D4B-0081N
Plastic rod D4B-0087N
Actuator Length Diameter of roller Model
Standard 31.5 17.5 dia. D4B-0001N
Adjustable roller lever 25 to 89 19 dia. D4B-0006N
Adjustable rod lever 145 max. --- D4B-0007N
Interchangeable with D4B-0001 33.7 19 dia. D4B-000RN
=++
Switch box Head Lever (side rotary type only)
D4B-2100Nex. D4B-2111N =+ D4B-0010N D4B-0001N+
1NC/1NO
(Snap-action)
1NC/1NO
(Slow-action)
2NC
(Slow-action)
F502-EN2-04.book Seite 245 Dienstag, 26. Juli 2005 5:48 17

G-246 Safety Sensors / Components
Specifications
Approved Standards
Snap-action Models
Note: 1. Adjustable roller lever, adjustable rod lever, coil spring, and
plastic rod models only.
2. Not including adjustable roller lever, adjustable rod lever,
coil spring, and plastic rod models.
Slow-action Models
Note: Not including adjustable roller lever, adjustable rod lever, coil spring, and
plastic rod models.
Standards and EC Directives
•Conforms to the following EC Directives:
Machinery Directive
Low Voltage Directive
EN1088
EN50041
Approved Standard Ratings
TÜV Rheinland: EN60947-5-1
Note: As protection against short-circuiting, use either a gI-type or gG-type 10-A fuse that conforms to IEC269.
UL/CSA: (UL508, CSA C22.2 No. 14)
A600
Agency Standard File No.
TÜV Rheinland EN60947-5-1
UL UL508 E76675
CSA C22.2 No. 14 LR45746
BIA (See note 2.) GS-ET-15 1-conduit: 9202158
3-conduit: 9309655
R9851083
(Direct opening:
approved)
R9151372
(Direct opening:
approval pending)
(See note 1.)
Agency Standard File No.
TÜV Rheinland EN60947-5-1
UL UL508 E76675
CSA C22.2 No. 14 LR45746
BIA (See note.) GS-ET-15 1-conduit: 9202158
3-conduit: 9309655
SUVA (See note.) SUVA
1-conduit: E6188/
1.d
3-conduit: E6189/
1.d
R9151643
(Direct opening:
approved)
(See note)
Utilization category AC-15
Rated operating current (Ie)2A
Rated operating voltage (Ue) 400 V
Rated voltage Carry current Current Volt-amperes
Make Break Make Break
120 VAC
240 VAC
480 VAC
600 VAC
10 A 60 A
30 A
15 A
12 A
6 A
3 A
1.5 A
1.2 A
7,200 VA 720 VA
F502-EN2-04.book Seite 246 Dienstag, 26. Juli 2005 5:48 17

G-247D4B-@N
D4B-
@
N
Characteristics
Note: 1. The above values are initial values.
2. The above values may vary depending on the model. Consult your OMRON sales representative for details.
3. The durability is for an ambient temperature of 5°C to 35°C and ambient humidity of 40% to 70%. For further conditions, consult your
OMRON sales representative.
4. –25°C to 80°C for the flexible-rod type.
Operating Characteristics
Note: 1. The operating characteristics of these Switches were measured with the roller lever set at 31.5 mm.
2. The operating characteristics of these Switches were measured with the rod lever set at 140 mm.
3. Only for slow-action models.
4. Only for snap-action models.
Item Snap-action Slow-action
Durability
(see note 3)
Mechanical 30,000,000 operations min. 10,000,000 operations min.
Electrical 500,000 operations min. (at a 250 VAC, 10-A resistive load)
Operating speed 1 mm/s to 0.5 m/s
Operating frequency Mechanical:120 operations/min
Electrical:30 operations/min
Rated frequency 50/60 Hz
Insulation resistance 100 MΩmin. (at 500 VDC) between terminals of the same polarity and between each termi-
nal and non-current-carrying part
Contact resistance 25 mΩmax. (initial value)
Dielectric strength (Uimp)
Between terminals of same polarity Uimp 2.5 kV Uimp 4 kV
Between terminals of different polarity --- Uimp 4 kV
Between current-carrying metal parts
and ground Uimp 4 kV Uimp 4 kV
Between each terminal and non-cur-
rent-carrying parts Uimp 4 kV Uimp 4 kV
Rated insulation voltage (Ui) 600 VAC (EN60947-5-1)
Counter electromotive voltage at switching 1,500 VAC max. (EN60947-5-1)
Operating environmental pollution level 3 (EN60947-5-1)
Conditional short-circuit current 100 A (EN60947-5-1)
Conventional enclosed thermal current (Ithe) 20 A (EN60947-5-1)
Electric shock protection class Class I (with ground terminal)
Vibration resistance Malfunction:10 to 55 Hz, 0.75 mm single amplitude
Shock resistance Destruction:1,000 m/s2min.
Malfunction:300 m/s2min.
Ambient temperature Operating:–40°C to 80°C (with no icing) (see note 4)
Ambient humidity Operating:95% max.
Degree of protection IP67 (EN60947-5-1)
Weight Approx. 250 g
Model D4B-##11N D4B-##16N
(see note 1)
D4B-##17N
(see note 2) D4B-##70N D4B-##71N D4B-##81N D4B-##87N
OF max. 9.41 N 2.12 N 18.63 N 1.47 N
RF min. 1.47 N 0.29 N 1.96 N ---
PT 21±3° 2.0 mm max. 15° max.
PT (2nd)
(see note 3) (45°) (3.0 mm) ---
OT min. 50° 5.0 mm ---
MD max.
(see note 4) 12° 1.0 mm ---
DOT min. 35° (Slow-action models) 3.2 mm ---
55° (Snap-action models)
DOF min. 19.61 N 49.03 N ---
TT (75°) 7.0 mm ---
FP max. --- 38 mm 51 mm ---
OP --- 35±1 mm 48±1 mm ---
F502-EN2-04.book Seite 247 Dienstag, 26. Juli 2005 5:48 17

G-248 Safety Sensors / Components
Contact Form (EN50013)
Direct Opening Mechanism
1NO/1NC Contact (Snap-action)
If metal deposition between mating contacts occurs on the NC contact side, they can be pulled apart by the shearing force and tensile force gen-
erated when part B of the safety cam or plunger engages part A of the movable contact blade. When the safety cam or plunger is moved in the
direction of the arrow, the Limit Switch releases.
1NC/1NO Contact (Slow-action)
2NC Contact (Slow-action)
Model Contact Diagrams Explanation
D4B-#1#N1NC/1NO
(Snap-action)
D4B-#5#N1NC/1NO
(Slow-action)
D4B-#A#N2NC
(Slow-action)
13
11
14
12
Za 11-12
13-14
Stroke
ON
Only NC contact 11-12 has an
approved direct opening
mechanism.
Terminal numbers 11-12 and
13-14 cannot be used as unlike
poles.
11 12
23 24
Zb 11-12
23-24
Stroke
ON
Only NC contact 11-12 has an
approved direct opening
mechanism.
Terminal numbers 11-12 or
23-24 can be used as unlike
poles.
11
21
12
22
Zb 11-12
21-22
Stroke
ON Both NC contacts 11-12 and
21-22 have an approved direct
opening mechanism.
Terminal numbers 11-12 and
21-22 can be used as unlike
poles.
A
B
1. When metal deposition occurs. 2. When contacts are being pulled apart.
Movable contact
Plunger
Safety cam
Fixed contact (NC)
Movable contact
blade
Safety cam directly
pushes up the
movable contact
blade.
3. When contacts are completely
pulled apart.
Contact spring
Return spring
Fixed contact (NC)
Movable contact
Plunger
Conforms to EN60947-5-1 Direct Opening
When metal deposition occurs, the contacts
are separated from each other by the plunger
being pushed in.
Fixed contact (NO)
Contact spring
Return spring
Fixed contact (NC)
Movable contact
Plunger
Conforms to EN60947-5-1
When metal deposition occurs, the contacts
are separated from each other by the plunger
being pushed in.
is marked on the product to indicate ap-
proval of direct opening.
F502-EN2-04.book Seite 248 Dienstag, 26. Juli 2005 5:48 17

G-249D4B-@N
D4B-
@
N
Engineering Data
Electrical Durability (Snap-action)
Nomenclature
250 VAC
125 VAC
10,000
5,000
3,000
1,000
500
300
100
480 VAC
250 VAC
500 VAC
10,000
7,000
5,000
3,000
1,000
700
500
300
(cosj= 1) (cosj= 0.4)
Operations (x 103)
Operations (x 103)
Switching current (A) Switching current (A)
Operating frequencies:
30 times/min., cosf= 1
Operating frequencies:
30 times/min., cosf= 0.4
Head
Operating Position Mark
(arrow)
Conduit Opening
Safety-oriented Lever Setting
Ground Terminal Screw
A ground terminal is provided to improve safety.
Equipped with Operating Position Indicator Plate
Push and rotate
Switch Box Material
Aluminum die-cast
Contact Material
Ag alloy
With roller lever models, the direction of the switch head can
be varied to any of the four directions by loosening the roller
lever switch screws at the four corners of the head.
The roller lever switch em-
ploys a system which allows
selection of operation on on-
ly one side (left or right)
or both sides without the
use of any tools.
Available in four different types of conduit threads:
Pg 13.5, G1/2 or 1/2-14NPT, M20
Grooves which engage the lever every 90∞are cut in the
operating position indicator plate to prevent the lever from
slipping against the rotary shaft.
An optimum overtravel (OT) value may be secured by
setting a desired OT value with a projection.
Shearing Force Contact Separating Mechanism
(NC Contact Section Only)
Should any abnormality occur in the contact area, the
contacts are positively pulled apart from each other by
shearing force.
F502-EN2-04.book Seite 249 Dienstag, 26. Juli 2005 5:48 17

G-250 Safety Sensors / Components
Dimensions
Note: 1. All units are in millimeters unless otherwise indicated.
2. Unless otherwise specified, a tolerance of ±0.4 mm applies to all dimensions.
3. When placing your order, specify the conduit type by adding a code from the list below to the blank box of the following model numbers
as shown below.
Standard Switches 3-conduit Switches
1: PG 13.5 5: PG 13.5
2: G 1/2 6: G 1/2
3: 1/2-14NPT 7: 1/2-14NPT
4: M20 8: M20
Switches
5.3
7.3
56 16
131.3±1.2
Conduit
23
8
28.3
22.5
99.5
77
74
15
31.5
43
11.5
31.5R
30±0.2
62±1
PT 21∞±3∞
60±0.2
40
+1
0
17.5 dia. x 6.6 resin roller
Cover
Roller Lever
D4B-##11N
M5 x 12
Allen-head
bolt
Set position
indicator
plate
Two, 5.3-dia.
mounting holes
Two, M4 x 12 cover
clamping screws
Four, M3.5 x 24.5 head
clamping screws
safety limit switch,
mechanical form lock
60±0.2
23
8
5.3
7.3
64.4
53
46.81628.3
22.5
99.5
77
74
15
31.5
43
71±1
Conduit
30±0.2
40+1
0
25 to 89R
Cover
Adjustable Roller Lever
D4B-##16N
19 dia. x 7
resin roller
M5 x 16
Allen-
head bolts
Two, 5.3-dia.
mounting holes
Two, M4 x 12
cover clamping
screws
Four, M3.5 x 24.5
head clamping screws
5.4
23
87.3
5.3
56.8
28.3 16
22.5
99.5
77
74
15
31.5
43
60±0.2
30±0.2
66±1
Conduit
40+1
0
145 max.
Cover
Adjustable Rod Lever
D4B-##17N 3 dia. x 160
stainless steel
rod
M5 x 12
Allen-head
bolts
Two, 5.3-dia.
mounting holes
Two, M4 x 12 cover
clamping screws
Four, M3.5 x 24.5
head clamping screws
F502-EN2-04.book Seite 250 Dienstag, 26. Juli 2005 5:48 17

G-251D4B-@N
D4B-
@
N
20
74 77 97
15
31.5
16
7.3
5.3
OP
PT
43
60±0.2
30±0.2
Conduit
40+1
0
8
16
20
77 97
PT
OP
85.3
7.3
15
31.5
43
74
60±0.2
30±0.2 Conduit
40+1
0
9.2 dia.
Cover
9.2 dia.
Cover
Top Plunger
D4B-##70N
Top Roller Plunger
D4B-##71N
Stainless steel
plunger
Two, 5.3-dia.
mounting holes
Two, M4 x 12 cover
clamping screws
Four, M3.5 x 24.5
head clamping screws
12.7 dia. x 4.8
stainless steel roller
Two, 5.3-dia.
mounting holes
Two, M4 x 12
cover clamping
screws
Four, M3.5 x 24.5
head clamping screws
safety limit switch,
mechanical form lock
safety limit switch,
mechanical form lock
29.1
74
203.5±1.2
8
5.3
7.3
15.7 16
2.7
77
15
31.5
43
60±0.2
30±0.2
Conduit
40+1
0
Coil Spring
D4B-##81N
18.2 dia. Rubber cap
Stainless steel coil spring
6.6 dia.
Cover
40 (see note 2)
(see note 1)
Coil Spring
Four, M3.5 x 7
clamping screws
Two, 5.3-dia.
mounting holes
Two, M4 x 12 cover
clamping screws
Note: 1. The coil spring may be operated
from any directions except axial
directions (Ø).
2. Be sure to adjust the dog to within
40 mm from the top end of the coil
spring.
203.5±1.2
60±0.2
30±0.2
61.5
29.1
7.3
5.3
43
31.5
15
74 77
2.7
15.7 16
8
Conduit
40+1
0
18.2 dia.
40 (see note)
6.6 dia.
Plastic rod
Seal cap
Cover
Plastic Rod
D4B-##87N
Four, M3.5 x 7
head mounting
screws
Two, 5.3-dia.
mounting holes
Two, M4 x 12 cover
mounting screws
The Switch can
be actuated to all
directions except
to the axis center.
Note: Be sure to adjust the dog to within 40 mm
from the top end of the plastic rod.
F502-EN2-04.book Seite 251 Dienstag, 26. Juli 2005 5:48 17

G-252 Safety Sensors / Components
3-conduit Switches
17.5 dia. x 6.6 resin roller
Two, caps
Three, Conduit
Cover
Two, 5 +0.15/0-dia. holes (depth: 6)
40 to 42
Roller Lever
D4B-##11N M5 x 12
Allen-head bolt
Operating
position indicator
(see note)
Six, 5.3-dia.
mounting holes
Four, M3.5 x 10
cover mounting screws
Four, M3.5 x 24.5
head mounting screws
Note: The lever can be set to any desired position
by turning the operating position indicator.
31.5R
safety limit switch,
mechanical form lock
66.4
Adjustable Roller Lever
D4B-##16N
Adjustable Rod Lever
D4B-##17N
145 max.
Two, caps Cover
Three, Conduit
19 dia. x 7 resin roller
Two, caps Cover
Three, Conduit
25 to 89R
40 to 42
40 to 42
Two, 5 +0.15/0-dia. holes (depth: 6)
Two, 5 +0.15/0-dia. holes (depth: 6)
Operating posi-
tion indicator
(see note)
M5 x 16
Allen-head
bolts
Six, 5.3-dia.
Mounting holes
Four, M3.5 x 10 Cover
mounting screws
Four, M3.5 x 24.5 head
mounting screws
Note: The lever can be set to any desired position
by turning the operating position indicator.
3 dia. x 160
stainless steel rod
Operating position
indicator
(see note)
M5 x 12
Allen-head
bolts
Six, 5.3-dia.
mounting holes
Four, M3.5 x 10 cover
mounting screws
Four, M3.5 x 24.5
head mounting screws
Note: The lever can be set to any desired position
by turning the operating position indicator.
F502-EN2-04.book Seite 252 Dienstag, 26. Juli 2005 5:48 17

G-253D4B-@N
D4B-
@
N
Top Plunger
D4B-##70N
Top Roller Plunger
D4B-##71N
Six, 5.3-dia.
mounting holes
Four, M3.5 x 10 cover
mounting screws
Two, caps
9.2 dia.
Cover
Three, Conduit
Two, caps
9.2 dia.
Cover
Three, Conduit
40 to
42
40 to 42
Two, 5 +0.15/0-dia. holes (depth: 6)
Two, 5 +0.15/0-dia. holes (depth: 6)
Stainless steel
plunger
Four, M3.5 x 19.5
head mounting screws
12.7 dia. x 4.8
stainless steel roller
Six, 5.3-dia.
mounting screws
Four, M3.5 x 10
cover mounting screws
Four, M3.5 x 19.5
head mounting screws
safety limit switch,
mechanical form lock
safety limit switch,
mechanical form lock
201.9±1.2
Coil Spring
D4B-##81N
18.2 dia.
40 to 42
Stainless steel coil spring
Seal cap
Two, caps
6.6 dia.
Cover
Three, Conduit
Plastic Rod
D4B-##87N
Plastic rod
18.2 dia.
40 to 42
Seal cap
Two, caps
6.6 dia.
Cover
Three, Conduit
(40) (see note)
(40) (see note)
Two, 5 +0.15/0-dia. holes (depth: 6)
Two, 5 +0.15/0-dia. holes (depth: 6)
The Switch can be actuated
to all directions except to
the axis center
Four, M3.5 x 7
head mounting screws
Six, 5.3-dia.
mounting holes
Four, M3.5 x 10 cover
mounting screws
Note: Set the spring so that the dog comes in
contact at a point 40 mm from the tip.
The Switch can be actuated to all
directions except to the axis center.
Four, M3.5 x 7
head mounting screws
Six, 5.3-dia.
mounting holes
Four, M3.5 x 10
cover mounting screws
Note: Set the spring so that the dog comes in
contact at a point 40 mm from the tip.
F502-EN2-04.book Seite 253 Dienstag, 26. Juli 2005 5:48 17

G-254 Safety Sensors / Components
Levers
31.5
15
17
11.8
11.5
97
15.9
20
26
20.2
12.8
3.2
160
5.4
21.6
12.5
2
8
17
11
D4B-0001N
17.5 dia. x 6.8 nylon roller
7.3 dia.
D4B-0006N
M5 hexagon
socket head
screw
6.4 adjusting scale
19 dia. x 7 nylon roller
M5 hexagon
socket head
screw
Adjustable
range
(25 to 89)
D4B-0007N
Stainless rod
145 max.
3 dia.
M5 hexagon
socket head
screw
Roller Lever Adjustable Roller Lever Adjustable Rod Lever
mechanical form lock
12
33.7
18
17.8
12
40.2±0.8
23.6
38 54.8
16
Note: Reverse the indicator plate when mounting.
20.1±0.8
11.5
11.4
D4B-000RN WL-1A118
19 dia. x 7 nylon roller
7.3 dia.
M5 hexagon
socket head
screw
Roller Lever (compatible with
previous D4B model) Roller Lever
17.5 dia. ¥30
nylon roller
7.3
+0.1
dia.
0
M5 hexagon socket
head screw (length: 12)
Roller Lever
WL-1A106
50 dia. ¥6 nylon roller
M5 hexagon
socket head screw
7.3 dia.
Note: Reverse the indicator
p
late when mountin
g
.
mechanical form lock
25.7
16.7
50 66.8
16 11.4
17.9
12.6
63±0.3 79.8
16 11.4
38 54.3
16
15.9
11.1
11.5
Roller Lever
WL-1A206
17.5 dia. ¥15
stainless steel roller
7.3
+0.1
dia.
0
M5 hexagon socket
head screw (length: 12)
Roller Lever
WL-1A300
17.5 dia. ¥7
stainless steel roller
7.3
+0.1
dia.
0
M5 hexagon socket
head screw (length: 12)
Roller Lever
WL-1A400
17 dia. ¥6 bearing roller
7.3 dia.
M5 hexagon
socket head
screw
Note: Reverse the indicator plate when mounting. Note: Reverse the indicator plate when mounting. Note: Reverse the indicator plate when mounting.
mechanical form lock
F502-EN2-04.book Seite 254 Dienstag, 26. Juli 2005 5:48 17

G-255D4B-@N
D4B-
@
N
Note: 1. Unless otherwise specified, a tolerance of ±0.4 mm applies to all dimensions.
2. Safety Limit Switch specifications are satisfied with D4B-####AN Levers only.
5.5
13.4
12.8
400±2
8.0±0.4
611
65±2
9
150±10
60±10
(23.6)
611
7.5
7.5
13.8
5.5 33
25 max.
Adjustable Rod Lever
WL-3A100
Spring Rod Lever
WL-4A201
Resin Loop Lever
D4A-F00
Note: Reverse the indicator plate when mounting. Note: Reverse the indicator plate when mounting. Note: Reverse the indicator plate when mounting.
25.5
max.
7.3 dia.
Adjustable range (350 to 380)
3.2 dia. stainless steel
operation rod
M5 ¥16 hexagon
socket head screw
M5 hexagon socket head screw
2 dia. stainless
steel spring
Adjustable
range
(290 max.)
13 dia.
7.3 dia.
M5 hexagon socket head screws
M5 hexagon socket head screw
4 dia. Nylon
F502-EN2-04.book Seite 255 Dienstag, 26. Juli 2005 5:48 17

G-256 Safety Sensors / Components
Precautions
If the D4B-#N is applied to a safety category circuit for prevention of
injury, use the D4B-#N model that has an NC contact equipped with
a direct opening mechanism, and make sure that the D4B-#N oper-
ates in the direct opening mode. Furthermore, secure the D4B-#N
with screws or equivalent parts that are tightened in a single direc-
tion so that the D4B-#N cannot be easily removed. Then provide a
protection cover for the D4B-#N and post a warning label near the
D4B-#N.
In order to protect the D4B-#N from damage due to short-circuiting,
connect a fuse breaking a current 1.5 to 2 times higher than the
rated current in parallel with the D4B-#N.
If an application satisfying EN standards is to employ the D4BL,
apply the 10-A gI or gG fuse approved by IEC269.
Do not apply the D4B-#N to the door without applying a stopper to
the door.
If the D4B-#N is used with the actuator normally pressed, the
D4B-#N may malfunction or may soon have reset failures. Be sure to
check and replace the D4B-#N regularly.
Correct Use
Operating Environment
The D4B-#N is for indoor use. The D4B-#N may malfunction if the
D4B-#N is used outdoors. Be sure to use a model with a lever-type
actuator for outdoor use instead.
Do not use the D4B-#N in the following locations:
•Locations subject to severe temperature changes
•Locations subject to high temperatures or condensation
•Locations subject to severe vibration
•Locations where the product may come in contact with metal dust,
oil, or chemicals
Tightening Torque
Note: Apply a tightening torque of 0.78 to 0.88 N·m to conduit models.
Mounting
Use four M5 screws with washers to mount the standard model. Be
sure to apply the proper torque to tighten each screw. The D4B-#N
can be mounted more securely by using the four screws plus two
5–0.05/–0.15-mm protruding parts, each of which has a maximum
height of 4.8 mm as shown below.
Mounting Dimensions (M5)
Changes in Actuator Mounting Position
To change the angle of the lever, loosen the Allen-head bolts on the
side of the lever.
The operating position indicator plate has protruding parts which
engage with the lever, thus allowing changes to the lever position by
90°.
The back of the operating position indicator plate has no protruding
parts. The lever can be set at any angle by attaching the operating
position indicator plate to the Switch so that this side will face the
lever. In this case, however, the D4B-#N will not be approved by
SUVA or BIA. Make sure that the lever engages with the operating
position indicator plate securely so that the lever will not slip.
Changes in Head Mounting Position
By removing the screws on the four corners of the head, the head
can be reset in any of four directions. Make sure that no foreign
materials will penetrate through the head.
Type Torque
1 M3.5 terminal screw 0.59 to 0.78 N·m
2Cover-mounting screw
(see note) 1.18 to 1.37 N·m
3 Head mounting screw 0.78 to 0.98 N·m
4 M5 body mounting screw 4.90 to 5.88 N·m
5 Connector 1.77 to 2.16 N·m
6Cap screw
(for three-conduit models) 1.27 to 1.67 N·m
(3)
(4)
(1)
(5) (2)
Be sure to tighten each
screw of the D4B-#N
properly, otherwise the
D4B-#N may malfunction.
30
60 59.3±0.1 30
40
42
27±0.1
5
-0.05
dia. holes, max. 5 height
-0.15
Standard Model 3-conduit Model
Protruding portions
F502-EN2-04.book Seite 256 Dienstag, 26. Juli 2005 5:48 17

G-257D4B-@N
D4B-
@
N
CW, CCW or Two-way Operation
The head of Side Rotary Switches can be converted in seconds to
CW, CCW, or two-way operation. The conversion procedure follows.
Procedure
1. Dismount the head by loosening the four screws that secure it.
2. Turn over the head to set the desired operation (CW, CCW, or
both). The desired operation can be selected by setting the mode
selector knob shown in the figure. This knob is factory set to the
“CW + CCW” (two-way operation) position.
3. Set the CW hole on the head at the operation position mark
(arrow) for clockwise operation or set the CCW hole right at the
arrow for counterclockwise operation. In either case, be sure to
set the hole position exactly at the arrow point.
Wiring
Do not connect the bare lead wires directly to the terminals but be
sure to connect each of them by using an insulation tube and M3.5
round crimp terminals and tighten each terminal screw within the
specified torque range.
The proper lead wire is 20 to 14 AWG (0.5 to 2.5 mm2) in size.
Make sure that all crimp terminals come into contact with the casing
or cover as shown below, otherwise the cover may not be mounted
properly or the D4B-#N may malfunction.
Connector
Make sure that each connector is tightened within the specified
torque range. The casing may be damaged if the connector is tight-
ened excessively.
If the 1/2-14NPT is used, cover the cable and conduit end with seal-
ing tape in order to ensure IP67.
The Pg13.5 connector must be Nippon Flex’s ABS-08Pg13.5 or
ABS-12 Pg13.5.
Use OMRON’s SC-series connector which is suited to the cable in
diameter.
Properly attach the provided conduit cap to the unused conduit open-
ing and securely tighten the cap screw within the specified torque
when wiring the D4B-#N.
Others
The load for the actuator (roller) of the Switch must be imposed on
the actuator in the horizontal direction, otherwise the actuator or the
rotating axis may be deformed or damaged.
When using a long lever model like the D4B-##16N or
D4B-##17N, the Switch may telegraph. To avoid telegraphing, take
the following precautions.
1. Set the lever to operate in one direction. For details, see page G-
257, CW, CCW or Two-way Operation.
2. Modify the rear end of the dog to an angle of 15° to 30° as shown
below or to a secondary-degree curve.
3. Modify the circuit so as not to detect the wrong operating signals.
Head cover (Push and rotate)
Operating posi-
tion mark (arrow)
D dia.
dz dia.
dz dia.: 3.7
D dia.: 4.5
B: 7.0
L: 20.2
F: 7.7
l: 9.0 (mm)
Casing
Cover
Terminal screw
Crimp terminal
Terminal screw
Casing
Terminal screw
Cover
Crimp terminal
Correct
Correct
Incorrect
Incorrect
Crimp
terminal
Crimp terminal
Crimp terminal
Correct
Incorrect
Dog
Dog
Top View
Correct Incorrect
θθ
θ ≥30°15°≤θ≤30°
F502-EN2-04.book Seite 257 Dienstag, 26. Juli 2005 5:48 17

G-258 Safety Sensors / Components
In the interest of product improvement, specifications are subject to change without notice.
ALL DIMENSIONS SHOWN ARE IN MILLIMETERS.
To convert millimeters into inches, multiply by 0.03937. To convert grams into ounces, multiply by 0.03527.
Cat. No. C005-E2-09A-X
F502-EN2-04.book Seite 258 Dienstag, 26. Juli 2005 5:48 17
This manual suits for next models
98
Table of contents
Other Omron Switch manuals
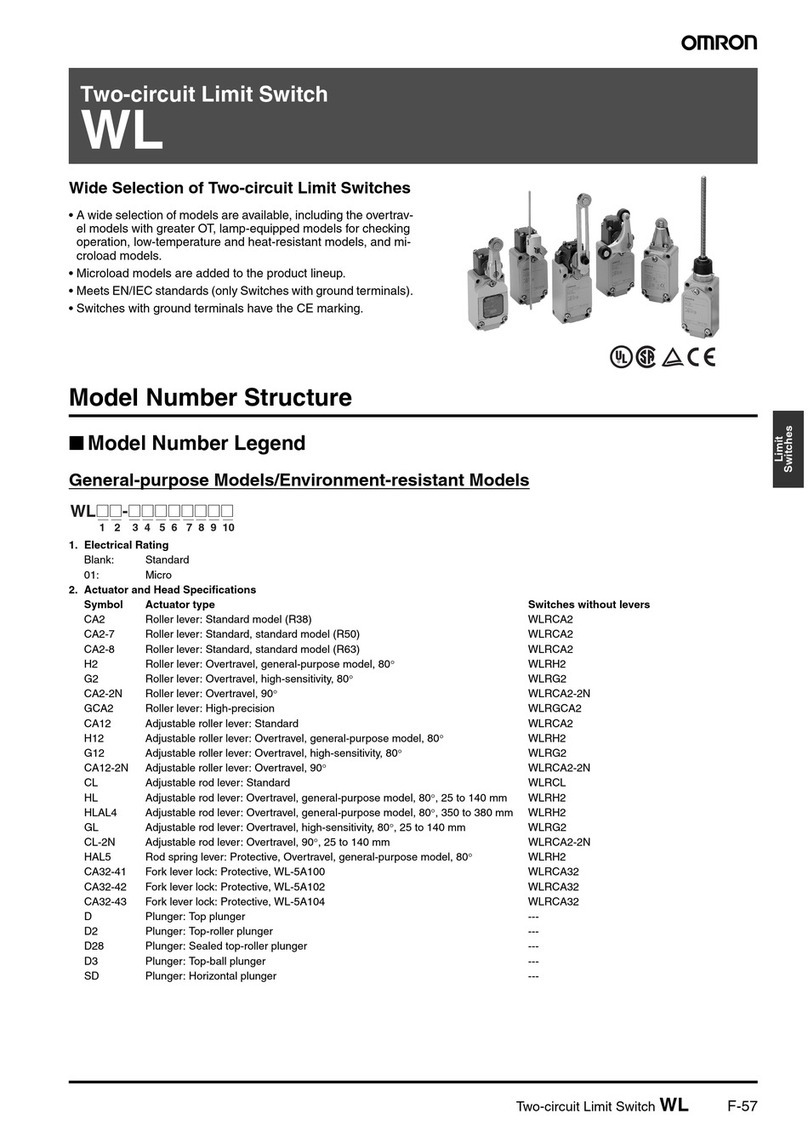
Omron
Omron WL - User manual

Omron
Omron D4NS - User manual
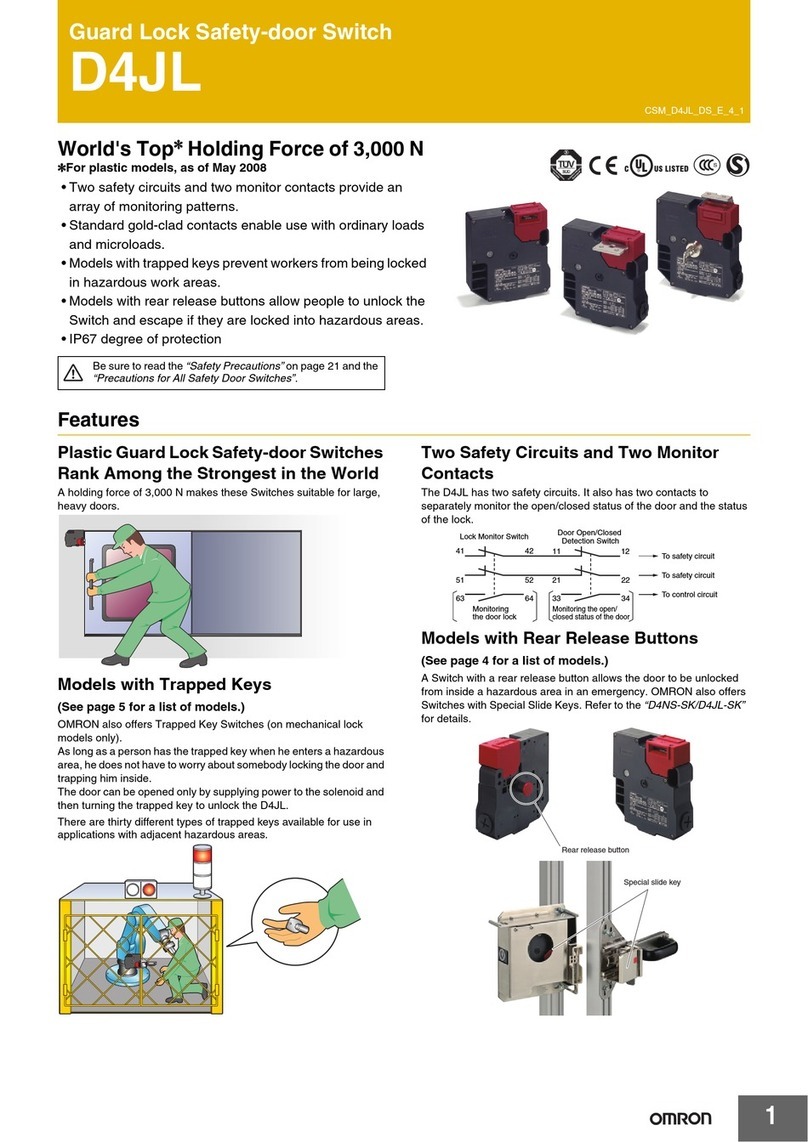
Omron
Omron D4JL Series User manual

Omron
Omron D4CC-1001 User manual
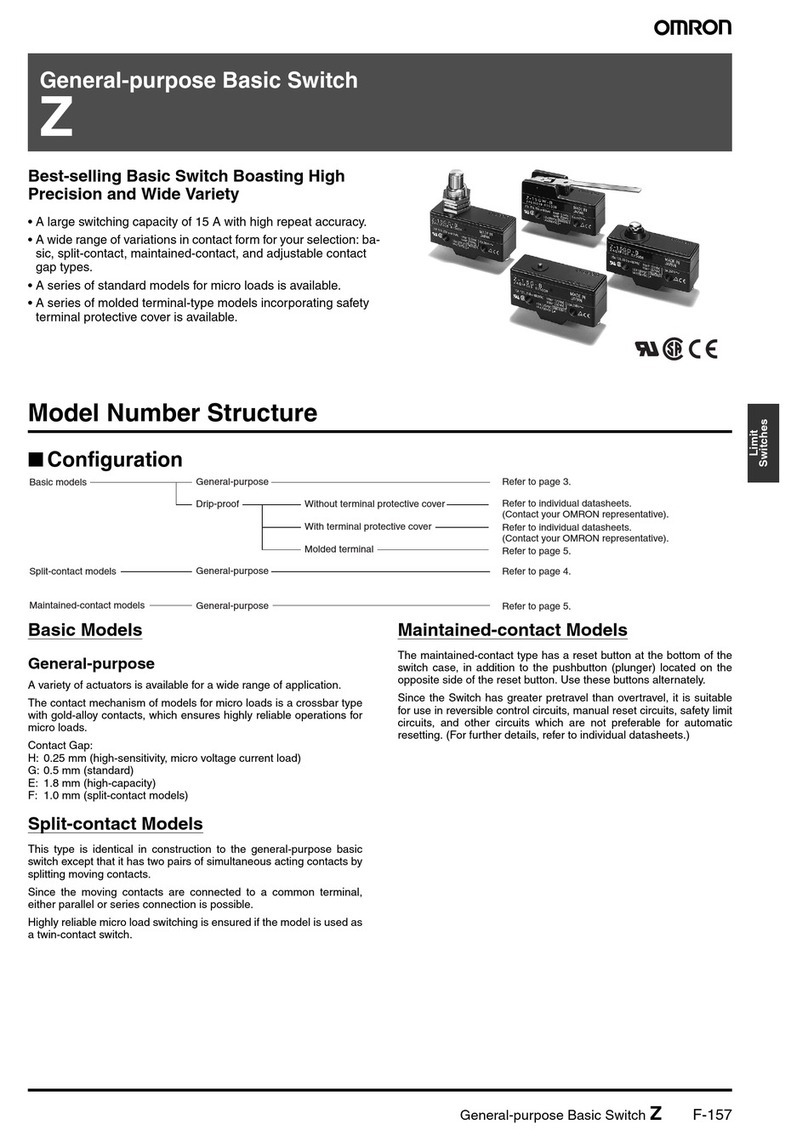
Omron
Omron Z User manual
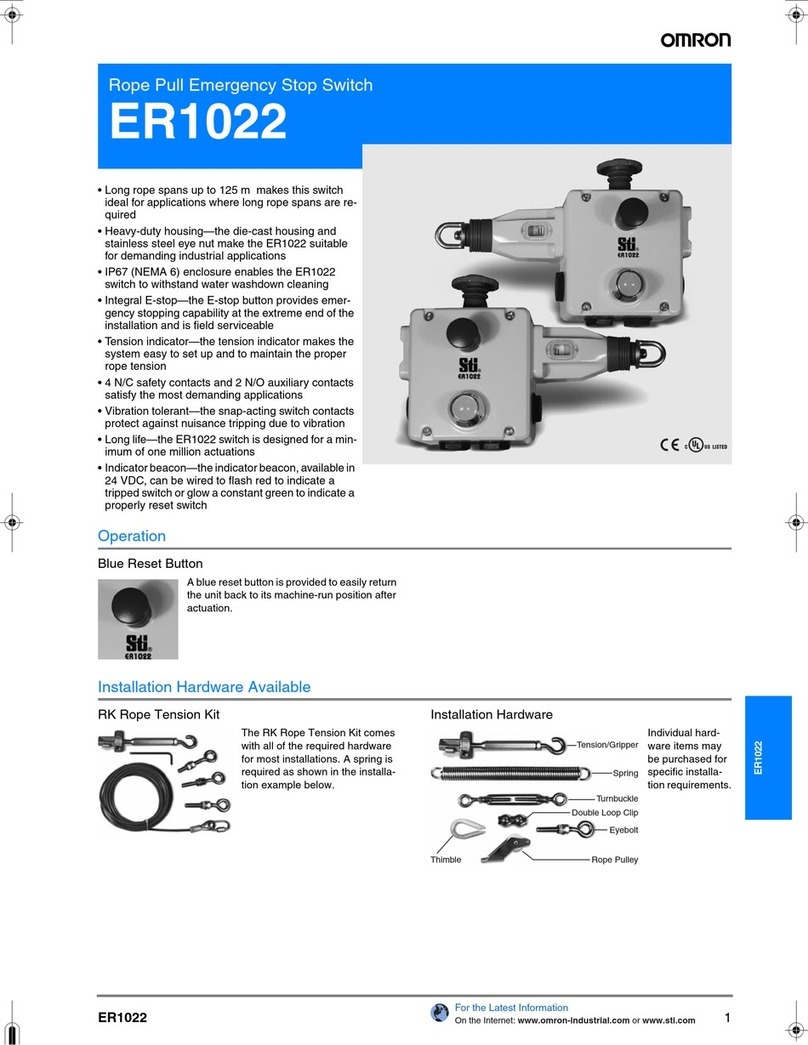
Omron
Omron ER1022 User manual
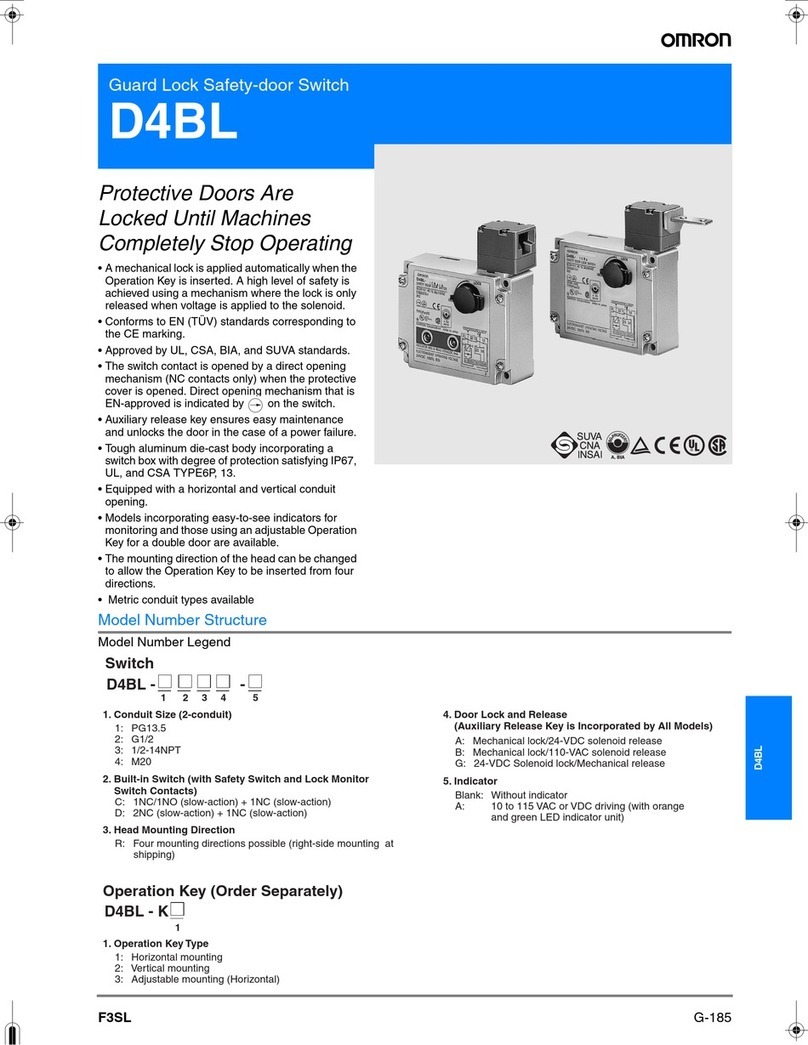
Omron
Omron D4BL - User manual
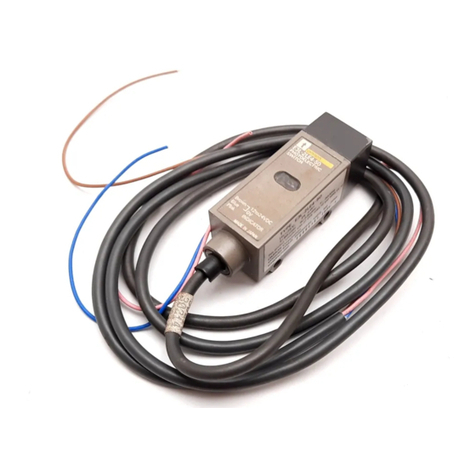
Omron
Omron E3L-2 4 Series User manual

Omron
Omron WLM - User manual
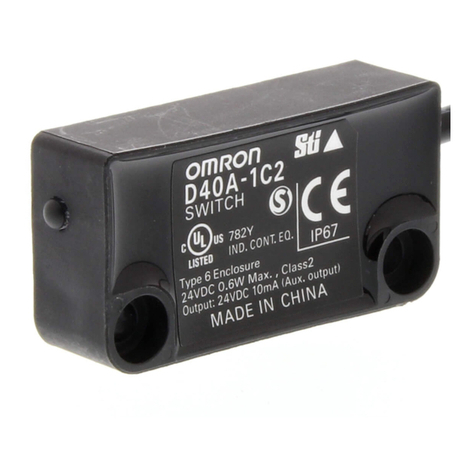
Omron
Omron G9SX Series User manual