Pilz PSSu E F 4DO 0.5 User manual

PSSu E F 4DO 0.5(-T)(-R)
Operating Manual-21316-EN-08
}Decentralised system PSSuniversal I/O

Preface
This document is a translation of the original document.
All rights to this documentation are reserved by Pilz GmbH & Co. KG. Copies may be made
for internal purposes. Suggestions and comments for improving this documentation will be
gratefully received.
Source code from third-party manufacturers or open source software has been used for
some components. The relevant licence information is available on the Internet on the Pilz
homepage.
Pilz®, PIT®, PMI®, PNOZ®, Primo®, PSEN®, PSS®, PVIS®, SafetyBUS p®,
SafetyEYE®, SafetyNET p®, the spirit of safety® are registered and protected trademarks
of Pilz GmbH & Co. KG in some countries.
SD means Secure Digital

Contents
Operating Manual PSSu E F 4DO 0.5(-T)(-R)
21316-EN-08 3
Section 1 Introduction 5
1.1 Validity of documentation 5
1.1.1 Retaining the documentation 5
1.1.2 Terminology: System environment A and B 5
1.2 Definition of symbols 6
Section 2 Overview 7
2.1 Module structure 7
2.2 Module features 7
2.3 Front view 8
Section 3 Safety 10
3.1 Intended use 10
3.2 Safety regulations 11
3.2.1 Use of qualified personnel 11
3.2.2 Warranty and liability 12
3.2.3 Disposal 12
Section 4 Function description 13
4.1 Block diagram 13
4.2 Module features 13
4.2.1 Functions 13
4.2.2 Integrated protection mechanisms 16
4.2.3 Reaction times 16
4.3 Configuration 17
4.3.1 PSSu assignment in system environment A 17
4.3.1.1 Addresses in the process image 17
4.3.2 PSSu assignment in system environment B 17
Section 5 Installation 18
5.1 General installation guidelines 18
5.1.1 Dimensions 18
5.2 Installing the base module 19
5.3 Inserting and removing an electronic module 20
5.3.1 Inserting an electronic module 21
5.3.2 Removing an electronic module 22
5.3.3 Changing an electronic module during operation 22
Section 6 Wiring 23
6.1 General wiring guidelines 23
6.1.1 Mechanical connection of the base modules 23
6.2 Terminal configuration 26
6.3 Connecting the module 28
6.4 Function test during commissioning 29
Section 7 Operation 30
7.1 Messages 30

Contents
Operating Manual PSSu E F 4DO 0.5(-T)(-R)
21316-EN-08 4
7.2 Display elements 31
7.2.1 Display elements for module diagnostics 31
7.2.2 Display elements for an output's FS enable 31
7.2.3 Display elements for output status 32
Section 8 Technical details 33
8.1 Safety characteristic data 36
Section 9 Order reference 38
9.1 Product 38
9.2 Accessories 38

Introduction
Operating Manual PSSu E F 4DO 0.5(-T)(-R)
21316-EN-08 5
1 Introduction
1.1 Validity of documentation
This documentation is valid for the product types PSSu E F 4DO 0.5, PSSu E F 4DO 0.5-T
and PSSu E F 4DO 0.5-R. It is valid until new documentation is published.
This operating manual explains the function and operation, describes the installation and
provides guidelines on how to connect the product.
1.1.1 Retaining the documentation
This documentation is intended for instruction and should be retained for future reference.
1.1.2 Terminology: System environment A and B
The PSSu system can be used in two different system environments. The module's applic-
ation area is described in the chapter "Intended Use" of the manual.
The distinction is made between
}PSSu in system environment A
}PSSu in system environment B
The distinction is based on the application area of the PSSu system.
PSSu in system environment A may be used in the
}Decentralised system PSSu I/O
}Not in the automation system PSS 4000
PSSu in system environment B may be used in the
}Automation system PSS 4000, e.g. with
– Decentralised system PSSu I/O with SafetyNET p
– Control system PSSu PLC
– Control system PSSu multi

Introduction
Operating Manual PSSu E F 4DO 0.5(-T)(-R)
21316-EN-08 6
1.2 Definition of symbols
Information that is particularly important is identified as follows:
DANGER!
This warning must be heeded! It warns of a hazardous situation that poses
an immediate threat of serious injury and death and indicates preventive
measures that can be taken.
WARNING!
This warning must be heeded! It warns of a hazardous situation that could
lead to serious injury and death and indicates preventive measures that can
be taken.
CAUTION!
This refers to a hazard that can lead to a less serious or minor injury plus
material damage, and also provides information on preventive measures
that can be taken.
NOTICE
This describes a situation in which the product or devices could be dam-
aged and also provides information on preventive measures that can be
taken. It also highlights areas within the text that are of particular import-
ance.
INFORMATION
This gives advice on applications and provides information on special fea-
tures.

Overview
Operating Manual PSSu E F 4DO 0.5(-T)(-R)
21316-EN-08 7
2 Overview
2.1 Module structure
A module consists of
}Electronic module and
}Base module with
– Screw terminals or
– Cage clamp terminals
The base modules are the carrier units for the electronic modules and are used to connect
the field wiring. The electronic modules are inserted on to the base modules and determine
the module's function.
Details of the base modules that can be used are available in the chapter entitled “Intended
Use”.
2.2 Module features
The product has the following features:
}4 Digital outputs
– Semiconductor technology
– Single-pole
– Positive-switching
– Current load capacity per output: 0,5 A
– Short circuit-proof
– Overload-proof
– Free from feedback
}LEDs for:
– Switch status per output
– FS enable per output
– Module error
}For failsafe applications in system environment A and B
}T-type:
PSSu E F 4DO 0.5-T: for increased environmental requirements
}R-type:
PSSu E F 4DO 0.5-R: for railway applications

Overview
Operating Manual PSSu E F 4DO 0.5(-T)(-R)
21316-EN-08 8
2.3 Front view
2111
2212
2313
2414
11
O0
21
O1
12
0V
22
0V
13
(C)
23
(C)
14
O2
24
O3
PSSu E F
4DO 0.5
11
14
21
24
Err
FS0 FS1
FS2 FS3
PSSu E F
4DO 0.5
312210
000000
001
10
1
3
4
9
8
5
6
7
11
2
12
A
B
Legend:
}A: Electronic module
}B: Base module
}1: LEDs for
– Module diagnostics
– Displaying an output's FS enable (enable principle)
}2: Labelling strip with:
– Name of electronic module
– Order number
– Serial number
– Hardware version number
– 2D code
}3: Labelling strip for the terminal configuration on the base module
}4: Status LEDs
}5: Name of electronic module
}6: Connection level 1

Overview
Operating Manual PSSu E F 4DO 0.5(-T)(-R)
21316-EN-08 9
}7: Connection level 2
}8: Connection level 3
}9: Connection level 4
}10: Square mounting holes (connection levels 1, 2, 3 and 4)
– With screw to loosen/tighten the screw terminal on base modules with screw termin-
als
– With mechanism to operate the cage clamp on base modules with cage clamp ter-
minals
}11: Round connection holes (connection levels 1, 2, 3 and 4) for connecting the signal
lines
}12: Mounting slot for colour marker to label the connection level (connection levels 1, 2,
3 and 4)

Safety
Operating Manual PSSu E F 4DO 0.5(-T)(-R)
21316-EN-08 10
3 Safety
3.1 Intended use
The module may be used for failsafe applications in system environment A and B (automa-
tion system PSS 4000).
The module meets the requirements of ENIEC61508 up to SIL 3.
The modules PSSu E F 4DO 0.5 and PSSu E F 4DO 0.5-T may be used as a safety com-
ponents in accordance with the Lifts Directive 95/16/EC in accordance with the require-
ments of EN81-1/2:1998+A3:2009, EN81-20:2015, EN81-50:2015, EN81-22:2014 and
EN115-1:2008+A1:2010.
The programmable safety system should be installed in a protected environment that meets
at least the requirements of pollution degree 2. Example: Protected inside space or control
cabinet with protection class IP54 and corresponding air conditioning.
It provides type 1 failsafe outputs in accordance with IEC 61131-2.
The outputs may be used to switch:
}Resistive loads
}Inductive loads
}Capacitive loads
The module PSSu E F 4DO 0.5-T is suitable for use where there are increased environ-
mental requirements (see Technical Details).
The module PSSu E F 4DO 0.5-R is suitable for use where there are increased environ-
mental requirements demanded by railway applications (see Technical details).
Intended use includes making the electrical installation EMC-compliant. Please refer to the
guidelines stated in the "PSSuniversal Installation Manual". The module is designed for use
in an industrial environment. It is not suitable for use in a domestic environment, as this can
lead to interference.
The following is deemed improper use in particular:
}Any component, technical or electrical modification to the module
}Use of the module outside the areas described in this manual
}Any use of the module that is not in accordance with the technical details.
INFORMATION
The module is supported by
}PSSuniversal Configurator and PSSuniversal Assistant from Version
1.4.0 (base type, T-type)
}PAS4000 from Version 1.1.1 (base type, T-type)
}PAS4000 from Version 1.5.0 (R-type)
– We recommend that you always use the latest version (download
from www.pilz.com).

Safety
Operating Manual PSSu E F 4DO 0.5(-T)(-R)
21316-EN-08 11
The PSSu E F 4DO 0.5 module may be used in conjunction with the following base mod-
ules:
}PSSu BP 1/8 S
}PSSu BP 1/8 C
}PSSu BP-C 1/8 S
}PSSu BP-C 1/8 C
}PSSu BP 1/12 S
}PSSu BP 1/12 C
}PSSu BP-C1 1/12 S
}PSSu BP-C1 1/12 C
The PSSu E F 4DO 0.5-T and PSSu E F 4DO 0.5-R modules may be used in conjunction
with the following base modules:
}PSSu BP 1/8 S-T
}PSSu BP 1/8 C-T
}PSSu BP-C 1/8 S-T
}PSSu BP-C 1/8 C-T
}PSSu BP 1/12 S-T
}PSSu BP 1/12 C-T
}PSSu BP-C1 1/12 S-T
}PSSu BP-C1 1/12 C-T
3.2 Safety regulations
3.2.1 Use of qualified personnel
The products may only be assembled, installed, programmed, commissioned, operated,
maintained and decommissioned by competent persons.
A competent person is a qualified and knowledgeable person who, because of their train-
ing, experience and current professional activity, has the specialist knowledge required. To
be able to inspect, assess and operate devices, systems and machines, the person has to
be informed of the state of the art and the applicable national, European and international
laws, directives and standards.
It is the company’s responsibility only to employ personnel who
}Are familiar with the basic regulations concerning health and safety / accident preven-
tion,
}Have read and understood the information provided in this description under "Safety"
}Have a good knowledge of the generic and specialist standards applicable to the spe-
cific application.

Safety
Operating Manual PSSu E F 4DO 0.5(-T)(-R)
21316-EN-08 12
3.2.2 Warranty and liability
All claims to warranty and liability will be rendered invalid if
}The product was used contrary to the purpose for which it is intended
}Damage can be attributed to not having followed the guidelines in the manual
}Operating personnel are not suitably qualified
}Any type of modification has been made (e.g. exchanging components on the PCB
boards, soldering work etc.).
3.2.3 Disposal
}In safety-related applications, please comply with the mission time TM in the safety-re-
lated characteristic data.
}When decommissioning, please comply with local regulations regarding the disposal of
electronic devices (e.g. Electrical and Electronic Equipment Act).

Function description
Operating Manual PSSu E F 4DO 0.5(-T)(-R)
21316-EN-08 13
4 Function description
4.1 Block diagram
Module Bus
Periphery
Supply
+ 24 V DC
Module
Supply
+ 5 V DC
Data
(FS)
0 V
11 12
0 V
21 22
0 V
14 13
0 V
24 23
13 23
(C-Rail)
4.2 Module features
4.2.1 Functions
Module supply
}The module supply provides the module with voltage.
Signals at the output
}"0" signal (0V) at the output:
– Output is high impedance
– No current to the load
}"1" signal (+24V) at the output:
– Output is low impedance
– Current is supplied to the load
Periphery supply
}The module routes the periphery supply from the module bus to the base module ter-
minals.
}The periphery supply is used to supply the outputs.
Outputs
}The head module sets the output status via the module bus.
}The max. capacity at an output depends on the load (see characteristic). Connecting a
higher capacity may lead to an error.
}Operation with electronic contactors has not been tested and may lead to errors.
Please contact our Customer Support team if you are using electronic contactors.

Function description
Operating Manual PSSu E F 4DO 0.5(-T)(-R)
21316-EN-08 14
Output test
}Outputs that are switched on are checked via regular off tests.
– Test pulses for outputs that are switched on: see Technical details"
– Outputs that are switched on are switched off for the duration of the test pulse.
– The load must not switch off because of the test.
}Outputs that are switched off are checked via regular on tests.
– Test pulses for outputs that are switched off: see Technical details"
– Outputs that are switched off are switched on for the duration of the test pulse.
– The load must not switch on because of the test.
Excluding individual outputs from the output test:
}If a plant is particularly sensitive to the test pulses, they may be switched off for indi-
vidual outputs.
}The test must be replaced by other measures, depending on the safety requirement.
}When test pulses are switched off:
– The correct switch status is always checked.
– The output's ability to switch will not be detected until the next time the output is
switched on/off.
Testing for shorts
}A test is regularly carried out to check for shorts between the outputs.
}For applications in accordance with Category 4, PL e and SIL 3, detection of shorts
between contacts must be guaranteed either via the on/off test or through other meas-
ures (e.g. asynchronous switching). A short between contacts must be simulated during
commissioning.
WARNING!
When wiring an output with capacitance it is essential to note the pulse dur-
ation, repetition period and scan time of the power-up test, otherwise the
load may switch on unintentionally.

Function description
Operating Manual PSSu E F 4DO 0.5(-T)(-R)
21316-EN-08 15
Timing diagram
"1"-Signal
t2
t1t1t3t1
t
t3t1
U
"0"-Signal
}t1 Pulse duration on on test (see Technical details)
}t2 Cycle time of on test when test is repeated (ca. 4 ms)
}t3 Cycle time of on test in normal circumstances (approx. 5 min.)
Characteristic: Output capacitance C dependent on load current I
1
2
3
4
5
0
50 100 150 200 250 300 350 400 450 500
6
C [µF]
I [mA]

Function description
Operating Manual PSSu E F 4DO 0.5(-T)(-R)
21316-EN-08 16
Derating diagram (PSSu E F 4DO 0.5(-T)(-R)): Permitted ambient temperature T depend-
ent on load current I
20
40
60
80
100
0
0,25 0,50
T [°C]
I [A]
0,350,30 0,40 0,450,100,05 0,15 0,20
4.2.2 Integrated protection mechanisms
When the PSSuEFPS1(-T) or PSSu E F PS2(-T)(-R) is used to supply the system, the
module supply is buffered for 20ms if the supply voltage is interrupted.
The module has the following protection mechanisms:
}Common second shutdown route, tested regularly
}Cyclical output tests
}Tests for shorts between the outputs
The module provides the following diagnostic data:
}Start-up error
}Configuration error
}FS communication error
}Bus termination error
}Temperature error: too warm
}Temperature error: too hot
}Output error
4.2.3 Reaction times
Information on the reaction times of the outputs can be found in the PSSuniversal System
Description.

Function description
Operating Manual PSSu E F 4DO 0.5(-T)(-R)
21316-EN-08 17
4.3 Configuration
4.3.1 PSSu assignment in system environment A
Functions for the FS outputs of a PSSu are defined in the PSSuniversal Configurator on the
PSSWIN-PRO system software:
}Read access through the standard bus system
(configured per module):
Configuration "R"
}Read/write access through the standard bus system
(configured per FS output):
"&" configuration (local enable principle)
}Optimisation of ST process image by combining adjacent bits of the same type.
Configuration "*"
}Exclude individual outputs from the output test
(configured per FS output).
4.3.1.1 Addresses in the process image
The module occupies 4 consecutive bit addresses in the process image. The process im-
age in which the outputs are shown depends on the configuration.
With write access ("&"), the Bits in the ST-PIO are used to switch the FS outputs with the
local enable principle.
Configuration SafetyBUS p Standard bus system
FS-PIO ST-PII ST-PIO
None 4 Bit
(e. g.: 32.00 … 32.03)
- - - - - -
Read ST (“R”) 4 Bit - - -
ST read and write (“&”) 4 Bit 4 Bit
4.3.2 PSSu assignment in system environment B
Data access is via pre-defined I/O data types:
I/O data name I/O data type I/O data element Meaning
O0(11), O1(21), O2(14),
O3(24)
FS_O_DO Data: SAFEBOOL Output data O0 ... O3

Installation
Operating Manual PSSu E F 4DO 0.5(-T)(-R)
21316-EN-08 18
5 Installation
5.1 General installation guidelines
Please also refer to the PSSuniversal Installation Manual.
NOTICE
Damage due to electrostatic discharge!
Electrostatic discharge can damage components. Ensure against discharge
before touching the product, e.g. by touching an earthed, conductive sur-
face or by wearing an earthed armband.
5.1.1 Dimensions
Base modules with four connection levels:
12,6 mm
76 mm
52,1 mm8,1 mm
67,7 mm
12,6 mm
56,1 mm 71,8 mm 0,8 mm
128,9 mm
72,6 mm
(2.051")(0.319")
(0.496") (2.858")
(0.496")
(2.99")
(2.209") (2.827") (0.031")
(5.075")
(2.665")

Installation
Operating Manual PSSu E F 4DO 0.5(-T)(-R)
21316-EN-08 19
Base modules with six connection levels:
12,6 mm
76 mm
52,1 mm8,1 mm
67,7 mm
82,0 mm 71,8 mm 0,8 mm
72,6 mm
(2.051")(0.319")
(2.858")
(0.496")
(2.99")
(3.228") (2.827") (0.031")
(2.665")
12,6 mm
(0.496")
154,6 mm
(6.087")
5.2 Installing the base module
Prerequisite:
}The head module must be installed.
}If the head module does not have an integrated power supply, a supply voltage module
must be installed to the right of the head module.
Please note:
}For mechanical reasons it is not possible to mix base modules with screw terminals and
base modules with cage clamp terminals.
}All contacts should be protected from contamination.
}The mechanics of the base modules are designed for 50 plug in/out cycles.
Procedure:
}We recommend that you wire up the base modules before inserting the electronic mod-
ules.
}Slot the groove on the base module on to the mounting rail from below [1].
}Push the base module back [2] until you hear it lock into position.
}On the mounting rail, slide the base module to the left until you hear the two lateral
mounting hooks on the adjacent module lock into position [3].

Installation
Operating Manual PSSu E F 4DO 0.5(-T)(-R)
21316-EN-08 20
Schematic representation:
[2]
[1]
[3]
5.3 Inserting and removing an electronic module
Please note:
}Only insert on to base modules that are already installed.
}Preferably these base modules should be ready wired.
}Electronic modules with outputs may only be inserted and removed when the load is
switched off. Unforeseeable error reactions may be triggered if modules are inserted
and removed under load.
}When an electronic module is plugged into a base module for the first time, one part of
the coding element remains on the electronic module, while its counterpart is fixed on to
the base module. This is how the base module is coded.
}The mechanics of the electronic modules are designed for 50 plug in/out cycles.
This manual suits for next models
2
Table of contents
Other Pilz Control Unit manuals
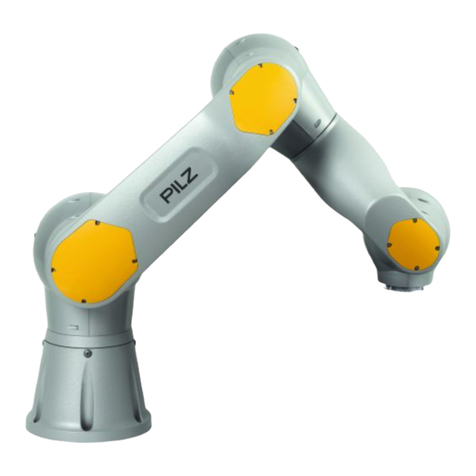
Pilz
Pilz PRBT 6 User manual
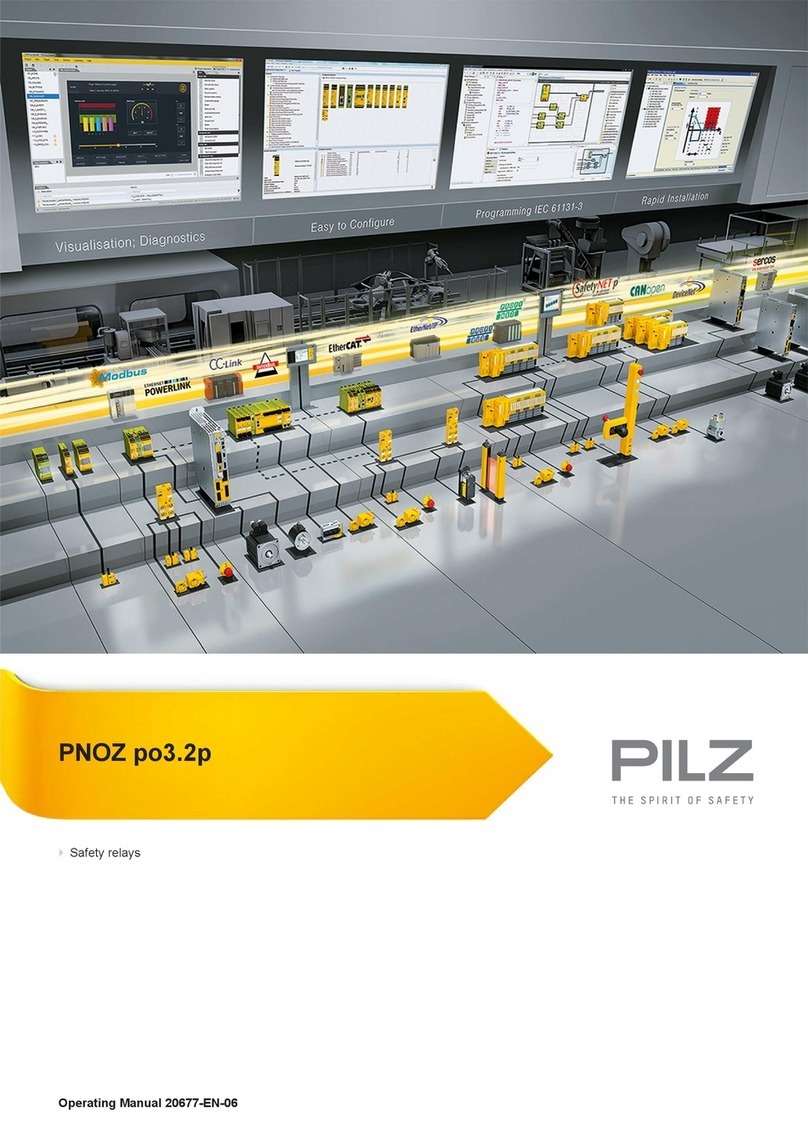
Pilz
Pilz PNOZ po3.2p User manual
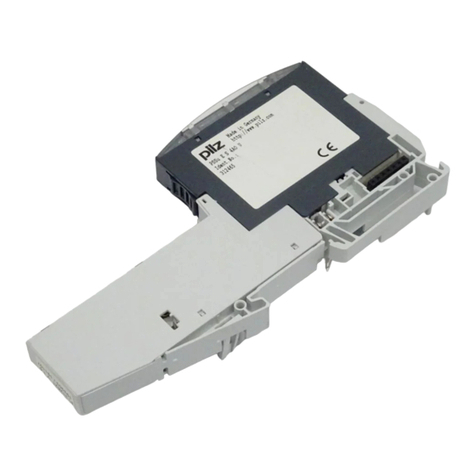
Pilz
Pilz PSS u2 ES 4AO U/I User manual
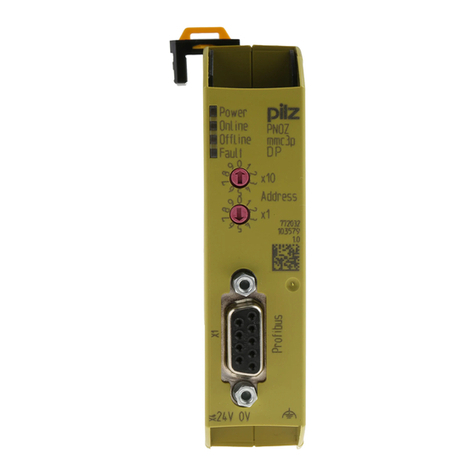
Pilz
Pilz PNOZmulti PNOZ mmc3p User manual
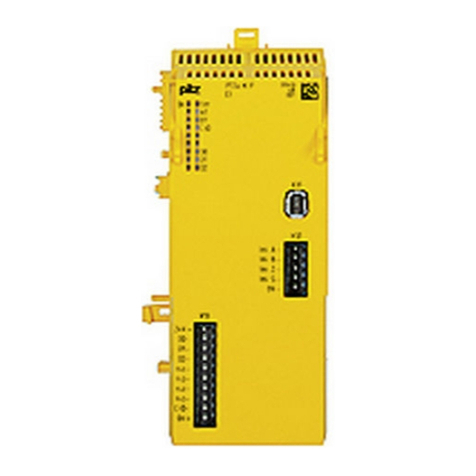
Pilz
Pilz PSSu K F EI User manual
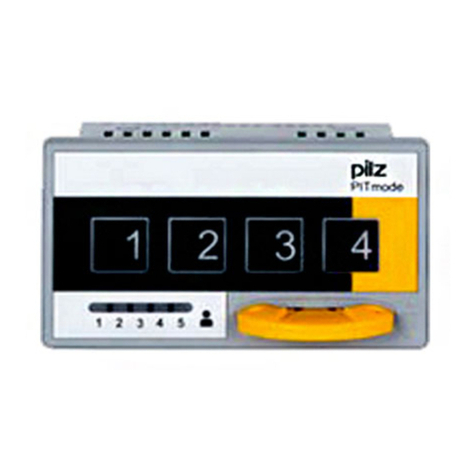
Pilz
Pilz PIT m3.3p User manual
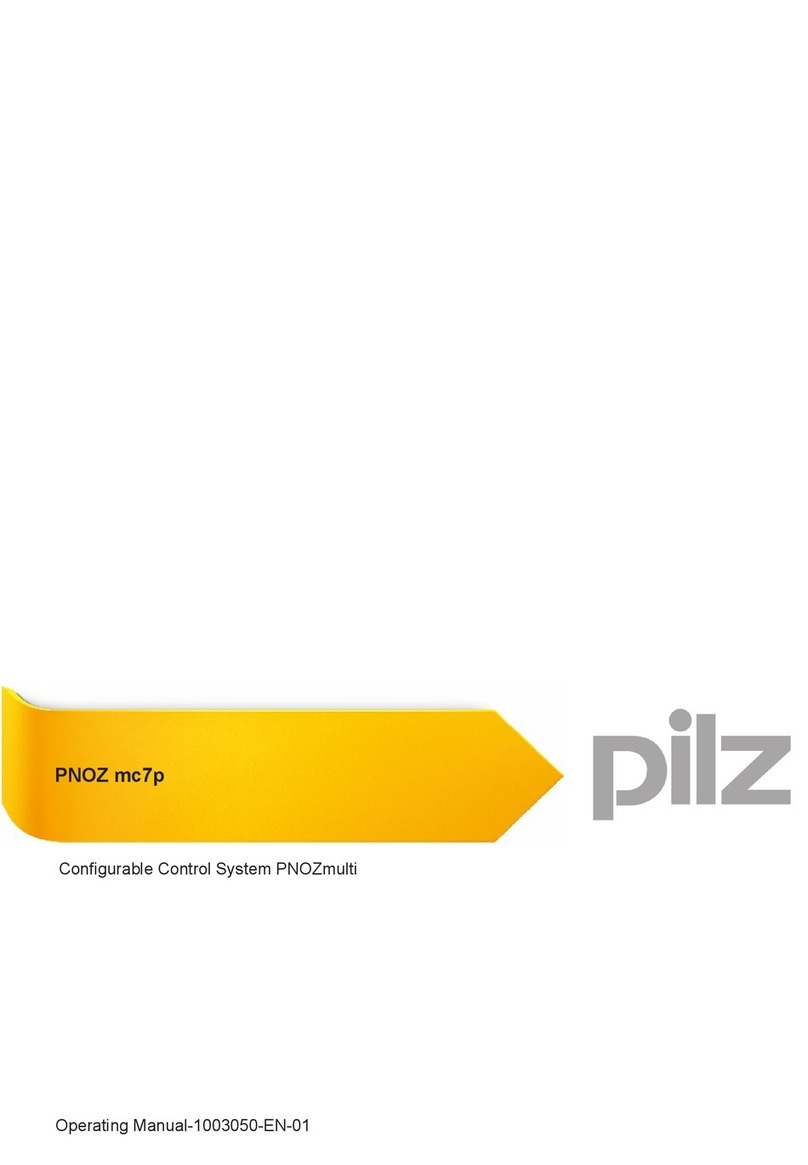
Pilz
Pilz PNOZ mc7p User manual
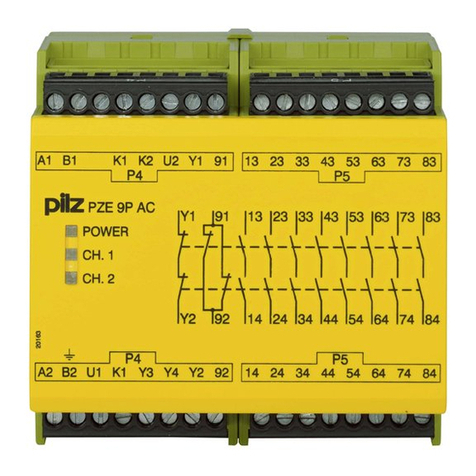
Pilz
Pilz PZE 9P User manual
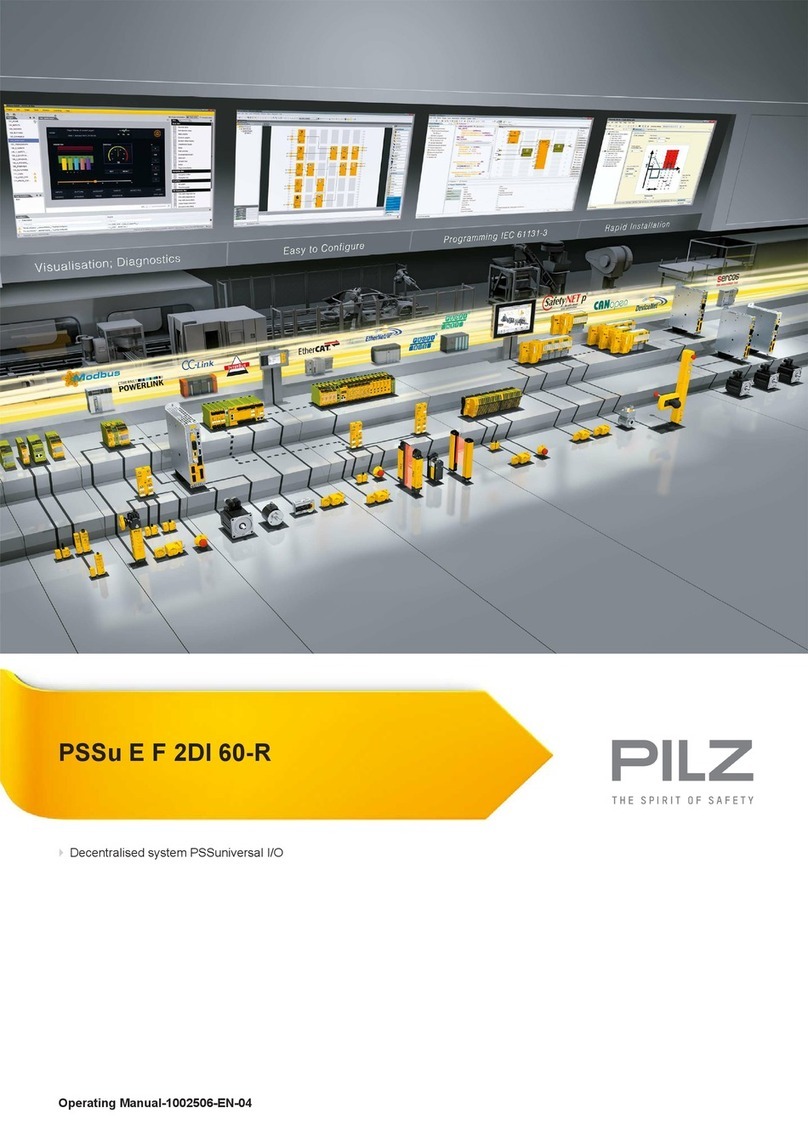
Pilz
Pilz PSSu E F 2DI 60-R User manual
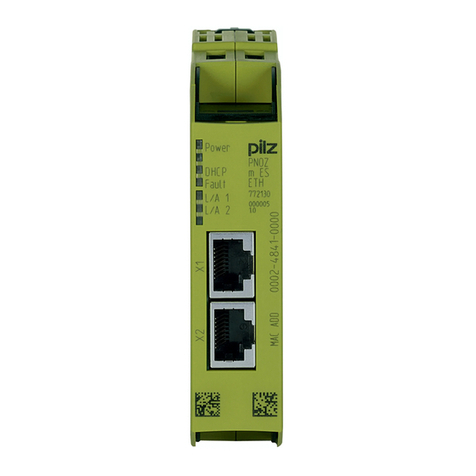
Pilz
Pilz PNOZ m ES ETH User manual
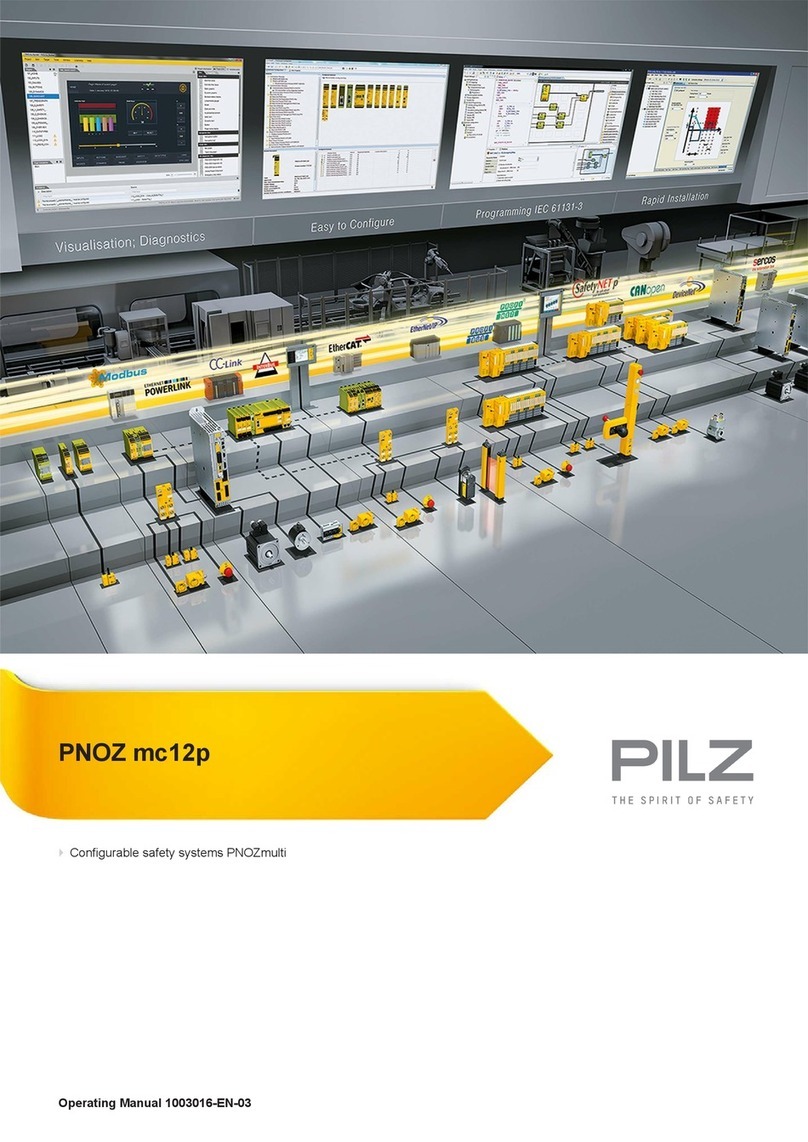
Pilz
Pilz PNOZ mc12p User manual
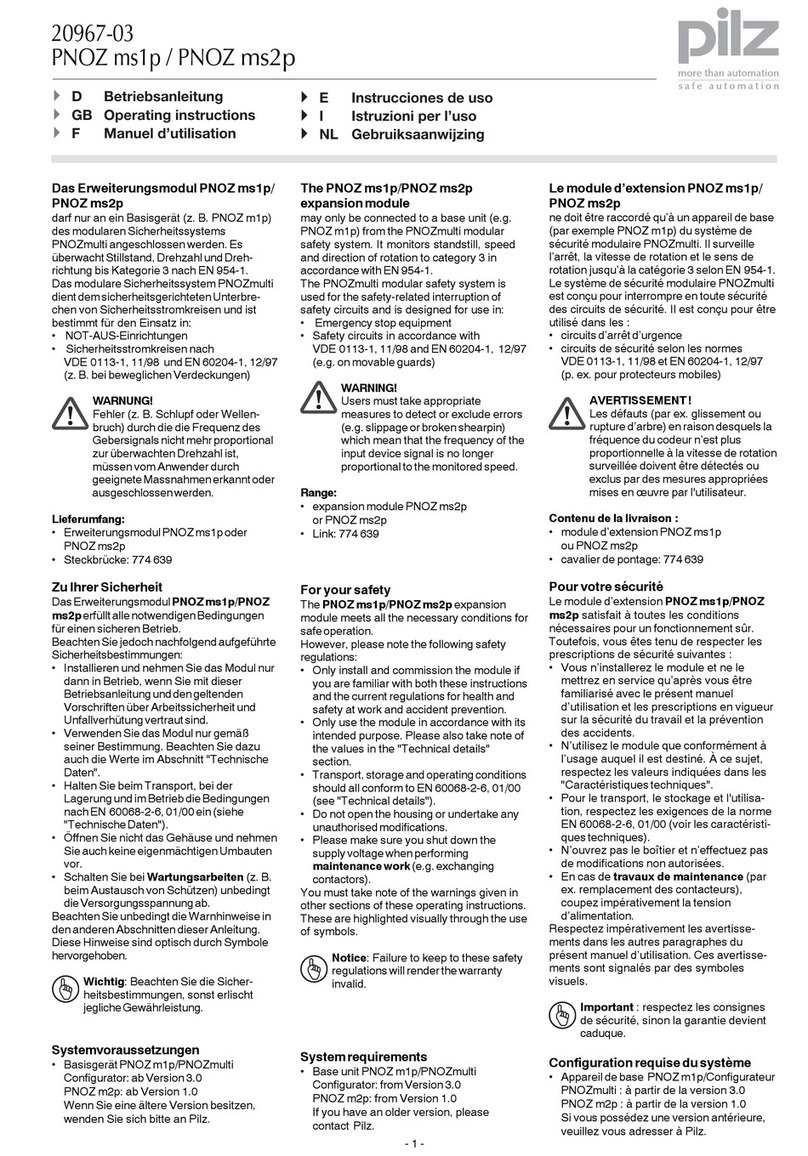
Pilz
Pilz PNOZ ms1p User manual

Pilz
Pilz PNOZ p1vp User manual

Pilz
Pilz PNOZ mc1p User manual
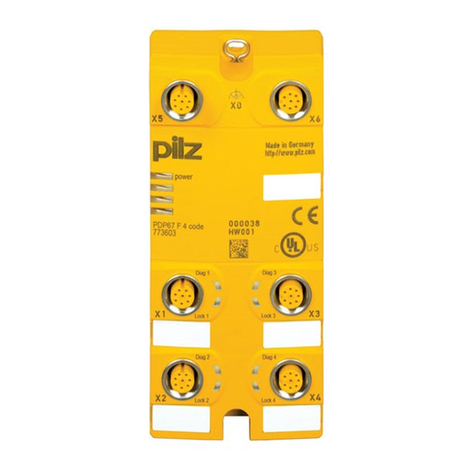
Pilz
Pilz PDP67 F 4 code User manual
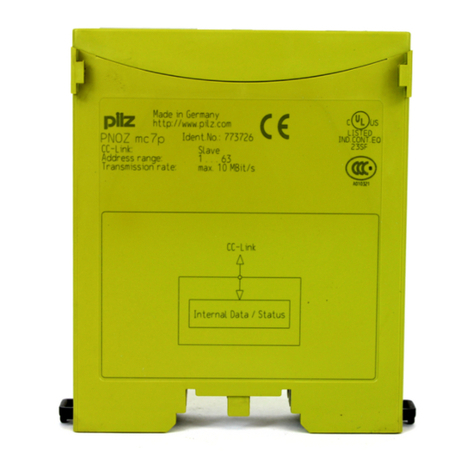
Pilz
Pilz PNOZ mc7p User manual
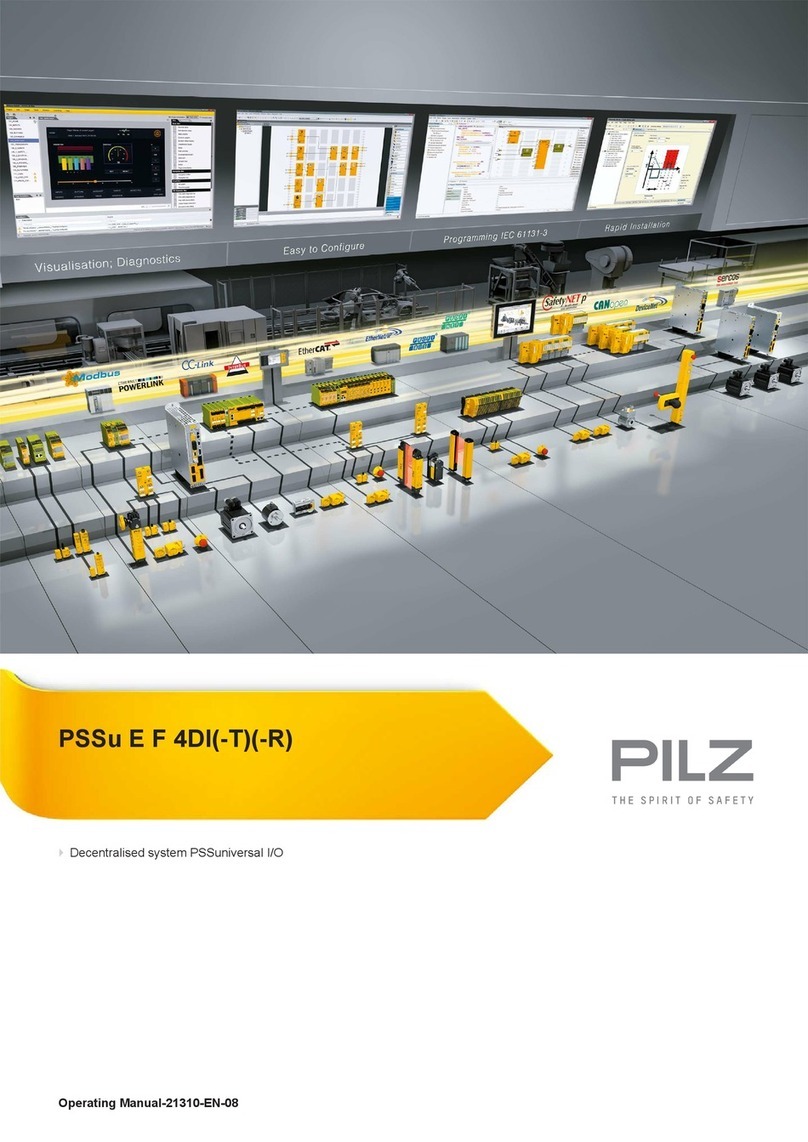
Pilz
Pilz PSSu E F 4DI-T User manual
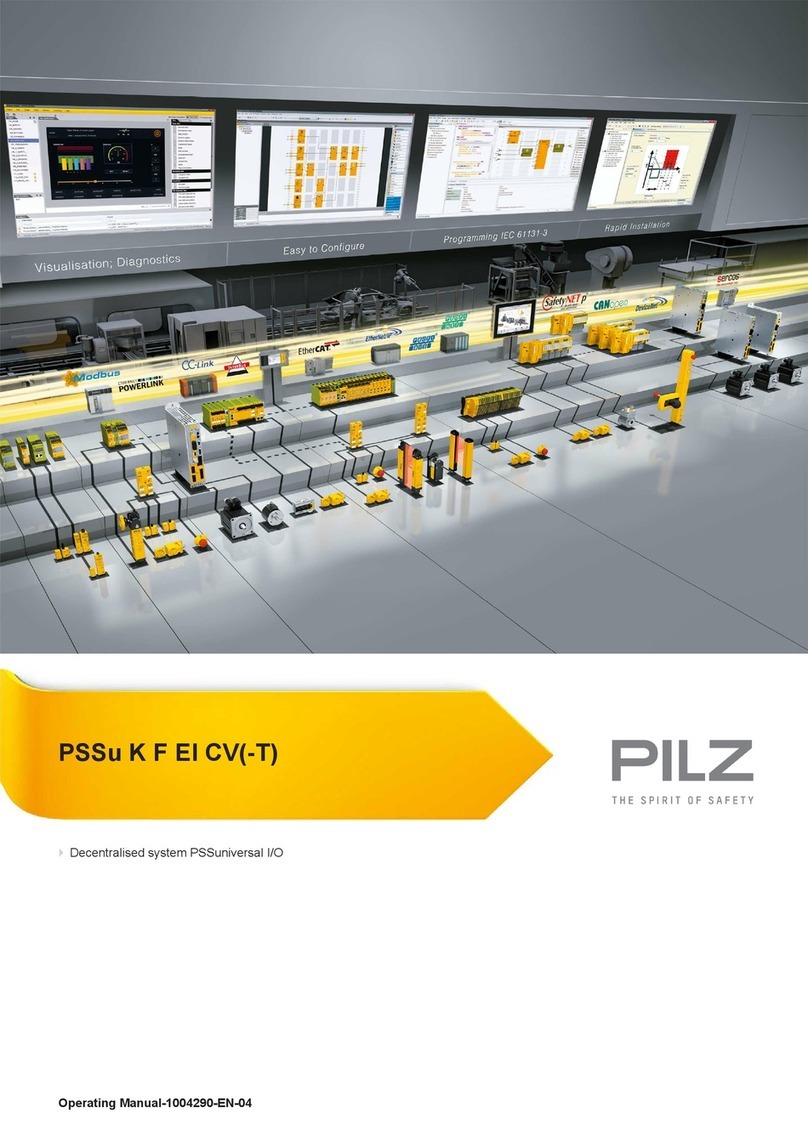
Pilz
Pilz PSSu K F EI CV User manual

Pilz
Pilz PNOZ s11 User manual
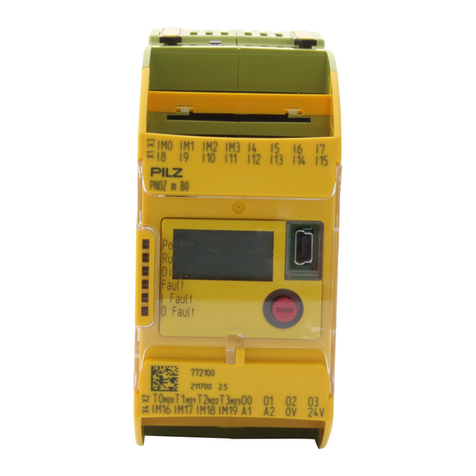
Pilz
Pilz PNOZmulti 2 User manual