Pilz PRBT 6 User manual

Service Robotics Modules
System Description-1004870-EN-05
}Robotics

Preface
This document is the original document.
All rights to this documentation are reserved by Pilz GmbH & Co. KG. Copies may be made
for the user's internal purposes. Suggestions and comments for improving this documenta-
tion will be gratefully received.
Source code from third-party manufacturers or open source software has been used for
some components. The relevant licence information is available on the Internet on the Pilz
homepage.
Pilz®, PIT®, PMI®, PNOZ®, Primo®, PSEN®, PSS®, PVIS®, SafetyBUS p®,
SafetyEYE®, SafetyNET p®, the spirit of safety® are registered and protected trademarks
of Pilz GmbH & Co. KG in some countries.
SD means Secure Digital

Contents
System Description Service Robotics Modules
1004870-EN-05 | 3
1 Introduction ............................................................................................................................ 6
1.1 Validity of documentation.......................................................................................................... 6
1.2 Retaining the documentation .................................................................................................... 6
1.3 Definition of symbols................................................................................................................. 7
2 Overview ................................................................................................................................. 8
2.1 Overview of industrial robots with service robotics modules from Pilz ..................................... 8
2.2 Overview of robot arm from Pilz ............................................................................................... 10
2.3 Overview of teach pendant from Pilz ........................................................................................ 11
2.4 Overview of robot control module from Pilz .............................................................................. 14
3 Safety ...................................................................................................................................... 16
3.1 Additional documents that apply............................................................................................... 16
3.2 Intended use ............................................................................................................................. 17
3.3 Foreseeable misuse and abuse................................................................................................ 18
3.4 Safety guidelines ...................................................................................................................... 19
3.4.1 Use of qualified personnel ........................................................................................................ 19
3.4.2 Definition of the responsibilities of persons .............................................................................. 19
3.5 EMCD ....................................................................................................................................... 21
3.6 Warranty and liability ................................................................................................................ 21
4 Function description ............................................................................................................. 22
4.1 Triggering of safety-related functions ....................................................................................... 22
4.2 Overview of stop reactions ....................................................................................................... 23
4.3 Emergency stop function .......................................................................................................... 25
4.4 Protective stop function for protective stop external ................................................................. 27
4.5 Protective stop function for PSENmlock (safety gate function) ................................................ 29
4.6 Safe retention with holding brakes............................................................................................ 31
4.7 Enabling function ...................................................................................................................... 32
4.8 Brake test function .................................................................................................................... 36
4.8.1 Brake test function after a cold start ......................................................................................... 38
4.8.2 Brake test function with cyclical brake test ............................................................................... 40
4.8.3 Brake test function when prompted via the teach pendant....................................................... 42
4.8.4 Brake test function with an external prompt.............................................................................. 43
4.8.5 Evaluation of brake test ............................................................................................................ 44
4.8.6 Default robot program for brake test......................................................................................... 46
4.9 Robot movement with time-limited motion enable .................................................................... 47
4.10 Operating modes ...................................................................................................................... 48
4.10.1 "Automatic" operating mode ..................................................................................................... 49
4.10.2 Operating mode "Manual reduced speed"................................................................................ 51
4.10.3 Operating mode "Manual high-speed"...................................................................................... 54
4.10.4 Changing the operating mode and motion enable.................................................................... 57
4.11 Stopping time and stopping distance in the event of STOP1 .................................................. 59
4.12 Stopping time in the event of a complete stop.......................................................................... 60
4.13 Controlling the robot program in the operating mode "Automatic" with teach pendant ............ 61
4.14 Controlling the robot program in the operating mode "Automatic" with external controller....... 62

Contents
System Description Service Robotics Modules
1004870-EN-05 | 4
5 Design and planning ............................................................................................................. 66
5.1 Coordinate system.................................................................................................................... 66
5.2 Positions and orientation of the coordinate systems on the robot arm ..................................... 68
5.3 Tool centre point (TCP) ............................................................................................................ 69
5.4 Building an industrial robot with service robotics modules from Pilz ........................................ 70
5.5 Planning the position for the brake test .................................................................................... 72
5.6 Planning an external emergency stop device ........................................................................... 74
5.7 Planning external protective stop devices ................................................................................ 75
5.8 Planning an external reset device for an external emergency stop device............................... 77
5.9 Planning an external reset device for a protective stop device................................................. 78
5.10 Planning a restart after a protective stop .................................................................................. 79
5.11 Planning the prompt for the manual brake test......................................................................... 80
5.12 Circuit diagram.......................................................................................................................... 81
5.13 Test plan ................................................................................................................................... 82
6 Installation .............................................................................................................................. 84
6.1 Setting up the robot control module (control cabinet) ............................................................... 84
6.2 Setting up and installing the robot arm ..................................................................................... 84
6.3 Installing the wall holder for the teach pendant ........................................................................ 84
7 Interfaces ................................................................................................................................ 85
7.1 Bridging plug's connector pin assignment ................................................................................ 85
8 Wiring ...................................................................................................................................... 86
8.1 Connections for external devices.............................................................................................. 86
8.2 Connections for external control of robot program ................................................................... 92
8.3 Wiring the robot control module (control cabinet) ..................................................................... 93
8.4 Wiring the teach pendant.......................................................................................................... 95
8.5 Using the bridging plug ............................................................................................................. 96
9 Commissioning ...................................................................................................................... 97
9.1 Initial commissioning................................................................................................................. 97
9.2 Recommissioning ..................................................................................................................... 100
10 Change, maintenance, decommissioning ........................................................................... 101
10.1 Change ..................................................................................................................................... 101
10.2 Maintenance ............................................................................................................................. 102
10.2.1 Exchanging the robot control module PRCM1.......................................................................... 102
10.2.2 Exchanging the safety control system ...................................................................................... 104
10.2.3 Exchanging the teach pendant ................................................................................................. 105
10.2.4 Exchanging the robot arm......................................................................................................... 106
10.3 Decommissioning ..................................................................................................................... 107
10.3.1 Decommissioning the robot arm ............................................................................................... 107
10.3.2 Decommissioning the teach pendant........................................................................................ 108
10.3.3 Decommissioning the robot control module.............................................................................. 108

Contents
System Description Service Robotics Modules
1004870-EN-05 | 5
11 Diagnostics and troubleshooting ......................................................................................... 109
12 Technical details .................................................................................................................... 111
12.1 Safety characteristic data ......................................................................................................... 111
13 Order reference ...................................................................................................................... 115
13.1 Product ..................................................................................................................................... 115
13.2 Accessories .............................................................................................................................. 116
14 Appendix ................................................................................................................................ 118
14.1 Hash value for integrity check of a download ........................................................................... 118
14.1.1 Calculate hash value with the command line tool "Certutil"...................................................... 119
14.1.2 Calculate hash value with Windows PowerShell ...................................................................... 120
14.1.3 Check the integrity of a file ....................................................................................................... 121
14.1.4 Download file for the teach pendant PRTM1 ............................................................................ 122
14.2 Terminology .............................................................................................................................. 123

Introduction
System Description Service Robotics Modules
1004870-EN-05 | 6
1 Introduction
This operating manual contains information about the intended use of the service robotics
modules from Pilz.
Using the robot arm PRBT 6 together with the robot control module PRCM1 (control cab-
inet) and the teach pendant PRTM1, an industrial robot can be built that corresponds to the
harmonised standard ENISO10218-1.
This operating manual is intended for operators and system or plant integrators of industrial
robots and/or industrial robot systems.
This operating manual is not for guidance in the operation of an industrial robot and/or in-
dustrial robot system.
1.1 Validity of documentation
This documentation is valid for an industrial robot composed of the service robotics mod-
ules PRBT 6, PRCM1 and PRTM1. The documentation is valid until new documentation is
published.
The current documentation is available in the download area of the Pilz homepage
(www.pilz.de -> Downloads).
1.2 Retaining the documentation
This documentation is intended for instruction and should be retained for future reference.

Introduction
System Description Service Robotics Modules
1004870-EN-05 | 7
1.3 Definition of symbols
Information that is particularly important is identified as follows:
DANGER!
This warning must be heeded! It warns of a hazardous situation that poses
an immediate threat of serious injury and death and indicates preventive
measures that can be taken.
WARNING!
This warning must be heeded! It warns of a hazardous situation that could
lead to serious injury and death and indicates preventive measures that can
be taken.
CAUTION!
This refers to a hazard that can lead to a less serious or minor injury plus
material damage, and also provides information on preventive measures
that can be taken.
NOTICE
This describes a situation in which the product or devices could be dam-
aged and also provides information on preventive measures that can be
taken. It also highlights areas within the text that are of particular import-
ance.
INFORMATION
This gives advice on applications and provides information on special fea-
tures.

Overview
System Description Service Robotics Modules
1004870-EN-05 | 8
2 Overview
2.1 Overview of industrial robots with service robotics modules
from Pilz
Using the robot arm PRBT 6 together with the robot control module PRCM1 (control cab-
inet) and the teach pendant PRTM1, an industrial robot can be built that corresponds to the
harmonised standard ENISO10218-1.
[1]
[2]
[3]
Safety control system
Motion controller
Ethernet
- Enable signal for operating mode selection
- Emergency stop signal
- Enabling signal
STO
CANopen
24 VDC
24 VDC
Robot arm
End-effector
X1 (Power)
[4]
[5]
[7]
X3 (AUX)
[6]
X2 (Signals)
230 VAC
Fig.: Industrial robots with service robotics modules from Pilz
Legend
[1] Robot arm PRBT 6 with
}Inputs for triggering STO and SBC via two separate shutdown paths
}Flange for attachment of a suitable end-effector
}Communication interface (CANopen) for controlling the axes and the end-effector
[2] Teach pendant PRTM1 with
}Software from Pilz for programming, commissioning and diagnostics of the Pilz in-
dustrial robots
}Key switch to release the operating mode selection
}Emergency stop pushbutton
}Enabling device (3-stage) for the manual operating modes

Overview
System Description Service Robotics Modules
1004870-EN-05 | 9
}Communication interface (Ethernet) for transmitting the robot program from the
teach pendant to the motion controller
[3] Robot control module PRCM1
Control cabinet with
}Safety control system from Pilz including
– Pre-installed PSS4000 user program
– Digital FS and ST inputs
– Digital FS outputs
}Motion controller from Pilz including
– Pre-installed motion control user program
– Communication interface (CANopen) for controlling the axes and the end-ef-
fector
– Communication interface (Ethernet) for transmitting the robot program from
the teach pendant to the motion controller
}Low voltage power supply (24 V DC)
}Control cabinet main switch
[4] Connection cable to X3 (AUX) of the robot arm with
Lines for control of an end-effector
[5] Connection cable to X2 (signals) of the robot arm with
}STO lines from the safety control system to the robot arm
}CANopen lines from the motion controller to the robot arm
[6] Connection cable to X1 (power) of the robot arm with
Voltage supply lines for supplying the robot arm and an end-effector with 24V DC
[7] Connection cable to the teach pendant with
}Lines to the safety control system and to the motion controller
}Voltage supply lines for supplying the teach pendant with 24V DC

Overview
System Description Service Robotics Modules
1004870-EN-05 | 10
2.2 Overview of robot arm from Pilz
The robot arm PRBT 6 is a multi-purpose manipulator with 6 axes. This type of manipulator
is also called an articulated robot. The robot arm may be classified as a light-weight robot
arm.
The robot arm is used as a component to operate the industrial robot in compliance with the
standards in accordance with ENISO10218-1.
[1]
[2]
[3]
[4]
[5]
[6]
[7]
Fig.: Design and components of the robot arm
Legend
[1] Base of the robot arm
}For mounting of the robot arm on a suitable surface
}With connections for tying to the voltage supply
}With communication interface for connection to the motion controller
}With connections for triggering the safety functions STO and SBC
[2] Joint 1 with axes A1 and A2
[3] Connecting element 1 (large)
[4] Joint 2 with axes A3 and A4
[5] Connecting element 2 (small)
[6] Joint 3 with axes A5 and A6
[7] Flange for attachment of a suitable end-effector (e.g. gripper)

Overview
System Description Service Robotics Modules
1004870-EN-05 | 11
2.3 Overview of teach pendant from Pilz
The teach pendant PRTM1 is a mobile control unit that is used by programmers for the pro-
gramming, commissioning and diagnostics of industrial robots from Pilz. The teach pendant
is equipped with
}Software for programming, commissioning and diagnostics of the Pilz industrial robot
}E-STOP pushbutton for triggering the robot’s emergency stop function
}Key switch for operating mode selection and enable of the selected operating mode
}Enabling device to allow robot movement in the manual operating modes
}Control button to move the axes of the robot arm in the manual operating modes (only in
combination with the enabling device)
The following operating modes can be selected with the teach pendant:
}"Automatic" operating mode
}"Manual reduced speed" operating mode
}"Manual high speed" operating mode
The teach pendant is an optional service robotics module; i.e. the teach pendant is not ab-
solutely necessary during productive mode (automatic operating mode).
The teach pendant is used as a component to operate an industrial robot that conforms to
standards in accordance with ENISO10218-1.
NOTICE
A programmer may use the teach pendant to program, commission and dia-
gnose precisely one industrial robot from Pilz.

Overview
System Description Service Robotics Modules
1004870-EN-05 | 12
[1] [2] [3]
[4]
[5] [6]
Fig.: Front view of the teach pendant
Legend
[1] Power button
Status LEDs:
PWR When the supply voltage is applied, the LED will light up green
RUN The LED will light up green when the motion enable for the drives is
present
ERR Fault diagnostics
The LED will light up red when diagnostic messages from the safety
control system and/or the motion controller are present.
[2] Key switch with two switch settings to enable/lock the selection of operating modes
[3] Emergency stop pushbutton
[4] Touchscreen
[5] Reset button (2nd) with status LED
[6] Membrane keys for start, stop and enter
Functions and meaning depend on the current view
Start (play) with status LED
Stop robot movement
Enter (accept)

Overview
System Description Service Robotics Modules
1004870-EN-05 | 13
[2]
[1]
[3b]
[3a]
Fig.: Rear view of the teach pendant
Legend
[1] Control buttons for moving the axes of the robot arm (only for manual operating
modes)
[2] Handle and device bracket
[3a] Enabling switch
[3b] Enabling switch

Overview
System Description Service Robotics Modules
1004870-EN-05 | 14
2.4 Overview of robot control module from Pilz
The robot control module PRCM1 (control cabinet) contains all the components needed to
control the robot arm and any additional equipment depending on the application (e.g. end-
effectors, indicator lights) and to evaluate the signals from any additional equipment de-
pendent on the application (e.g. emergency stop pushbutton, safety gate). The control cab-
inet is equipped with:
}Safety control system from Pilz including
– Pre-installed PSS4000 user program
– Digital FS and ST inputs
– Digital FS outputs
}Motion controller from Pilz including
– Pre-installed motion control user program
– Communication interface (CANopen) for controlling the axes and the end-effector
– Communication interface (Ethernet) for transmitting the robot program from the teach
pendant to the motion controller
}Low voltage power supply (24 VDC)
}Control cabinet main switch
All of the industrial robot's service robotics modules can be switched to a de-energised
state via the control cabinet main switch. The switch position for "de-energised state" is
lockable.
[1] [2] [3] [4]
Fig.: Elements and components of the robot control module (control cabinet)
Legend
[1] Control cabinet main switch
[2] Safety control system from the automation system PSS4000
[3] Motion controller
[4] Connection for the teach pendant connection cable or
connection for the bridging plug

Overview
System Description Service Robotics Modules
1004870-EN-05 | 15
The robot control module PRCM1 (control cabinet) is used as a component to operate the
industrial robot in compliance with the standards in accordance with ENISO10218-1.
The robot control module PRCM1 (control cabinet) is constructed in accordance with IEC
60204-1. It meets the relevant requirements arising from this standard.

Safety
System Description Service Robotics Modules
1004870-EN-05 | 16
3 Safety
3.1 Additional documents that apply
Refer to the safety guidelines in the operating manuals for the relevant products.
Please also read the information in the
}Operating manual for the robot arm PRBT 6
}Operating manual and online help for the teach pendant PRTM1
}Assembly instructions and operating manual for the relevant end-effector
}Operating manual for the robot control module PRCM1

Safety
System Description Service Robotics Modules
1004870-EN-05 | 17
3.2 Intended use
The industrial robot is classed as partly completed machinery in the context of the EC Ma-
chinery Directive. The industrial robot is intended for use within an industrial robot system.
Commissioning and operation are only permitted under the following conditions:
}The system/plant integrator has integrated the industrial robot in such a way that it consti-
tutes a standard-compliant industrial robot system when combined with other compon-
ents
}The system/plant integrator has integrated the industrial robot in such a way that it consti-
tutes final plant or machinery in the context of the EC Machinery Directive when com-
bined with other components
}The plant or machine complies with the EC Machinery Directive
}The plant or machine has a declaration of conformity
}The plant or machine has a CE mark
Application conditions
}A mechanical overload of the robot arm can cause the mechanical components to fail and
therefore the arm to sag with its load. For this reason the technical details for the robot
arm must be adhered to.
}The robot arm is a vertical axis, or more specifically a gravity-loaded axis. The following
requirements for the plant or machine design must be adhered to:
– The robot arm is exclusively intended for applications in which the head or body of the
robot operator is never below the robot arm.
– The robot arm is exclusively intended for applications in which the upper limbs are
only below the robot arm for short periods.
– The system or plant integrator must check whether a warning sign must be affixed to
the plant/machine that states "Do not stand under the vertical axis!" or something sim-
ilar.
}The risks of unintended dropping must also be considered during the risk assessment.
}If the risk assessment shows the need for a guard with access protection via a safety
gate, you should check whether a safety gate with guard locking is required.
Intended use includes making the electrical installation EMC-compliant. Please note the
guidelines given under "Wiring".
The following is deemed improper use in particular:
}Any component, technical or electrical modification,
including modifications to the mechanics (e.g.drilling holes);
}The use in areas outside of those documented;
}Any use that is not in accordance with the documented technical details.

Safety
System Description Service Robotics Modules
1004870-EN-05 | 18
3.3 Foreseeable misuse and abuse
}The robot arm is not suitable for use in areas with increased environmental requirements
(e.g. potentially explosive areas).
}The following is an example of misuse or abuse and is not permitted:
– Use for the transport of people or animals
– Use as a climbing aid
– Use underground
– Use outside
– Use without risk analysis
– Use without the required protective devices that result from the risk analysis

Safety
System Description Service Robotics Modules
1004870-EN-05 | 19
3.4 Safety guidelines
3.4.1 Use of qualified personnel
The products may only be assembled, installed, programmed, commissioned, operated,
maintained and decommissioned by competent persons.
A competent person is a qualified and knowledgeable person who, because of their train-
ing, experience and current professional activity, has the specialist knowledge required. To
be able to inspect, assess and operate devices, systems and machines, the person has to
be informed of the state of the art and the applicable national, European and international
laws, directives and standards.
It is the company’s responsibility only to employ personnel who
}Are familiar with the basic regulations concerning health and safety / accident prevention,
}Have read and understood the information provided in the section entitled Safety
}Have a good knowledge of the generic and specialist standards applicable to the specific
application.
3.4.2 Definition of the responsibilities of persons
The following defines persons and their responsibilities.
Operator
The operator is the legal person who uses the industrial robots or industrial robot systems
and is responsible for the personnel employed in operating the robot. This may be the com-
pany, employer or delegated person who is responsible for the use of the industrial robot or
industrial robot system.
}The operator is obligated to observe and implement occupational health and safety regu-
lations.
}The operator must discharge his supervisory duties.
}The operator must provide instruction for the personnel employed at regular defined inter-
vals.
During this instruction, the personnel employed must be taught about the type and scope
of the work as well as possible hazards. This is particularly true for personnel only em-
ployed occasionally such as commissioning, maintenance and service personnel.
Furthermore, instruction must be offered after each extraordinary incident and after each
technical modification.
System or plant integrator
The system or plant integrator is the person who is responsible for
}The safety-related integration of the robot arm into a plant/machine
}The commissioning of the plant/machine
}The creating of robot programs

Safety
System Description Service Robotics Modules
1004870-EN-05 | 20
The system or plant integrator is obligated to:
}Perform a risk assessment
}Implement the safety functions and protective devices resulting from the risk assessment.
}Assemble the robot arm
}Connect the robot arm
}Create the operating manual for the complete plant/machine
}Issue the declaration of conformity
}Affix the CE mark
Robot operator
The robot operator is a person who is assigned with starting, monitoring and stopping the
proper operation of an industrial robot or industrial robot system and performing the neces-
sary work during productive operation (e.g.inserting workpieces).
The robot operator must be trained for the tasks assigned to him.
Table of contents
Other Pilz Control Unit manuals
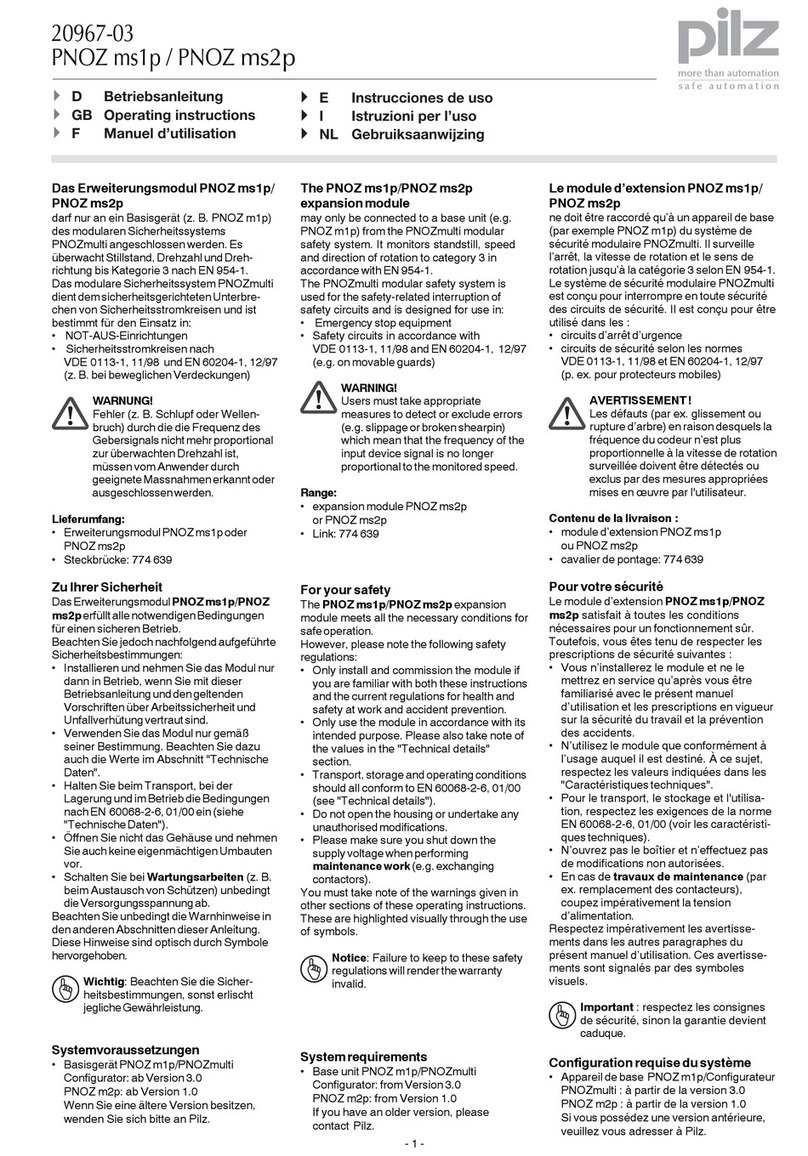
Pilz
Pilz PNOZ ms1p User manual
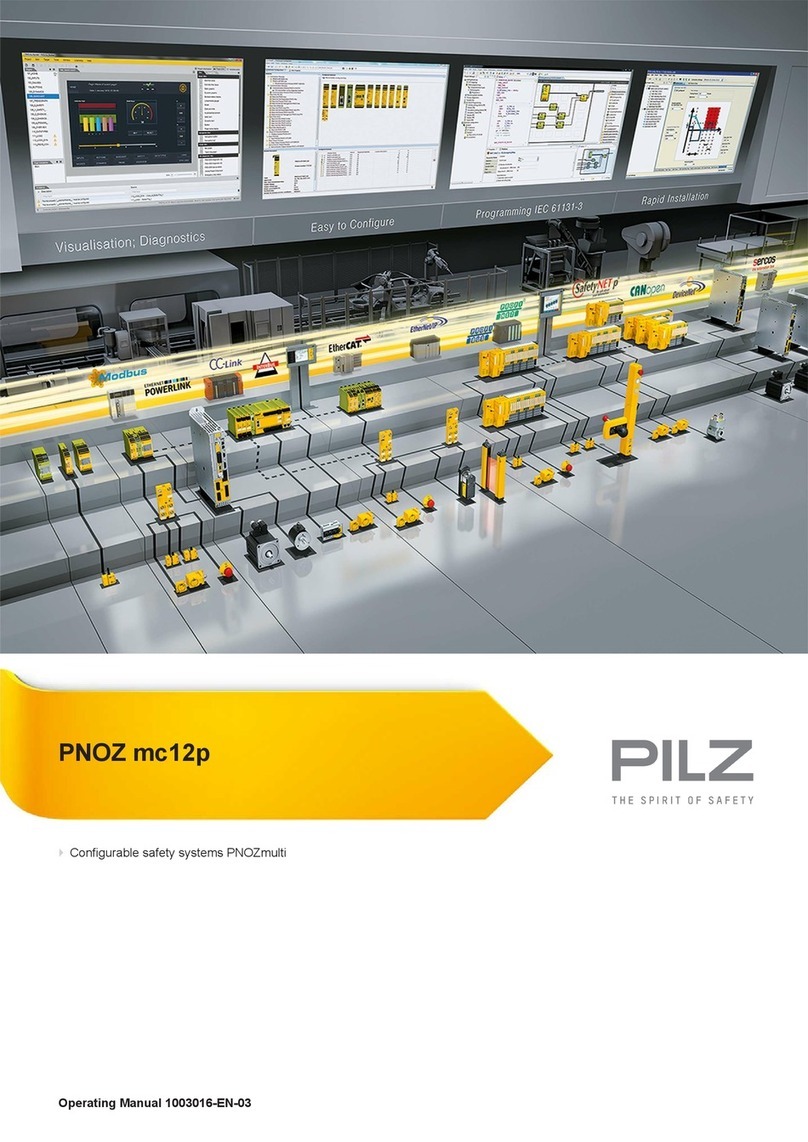
Pilz
Pilz PNOZ mc12p User manual
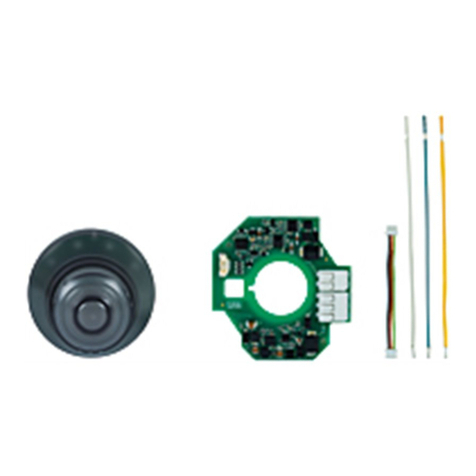
Pilz
Pilz PIT es Set10u-5c PCB User manual
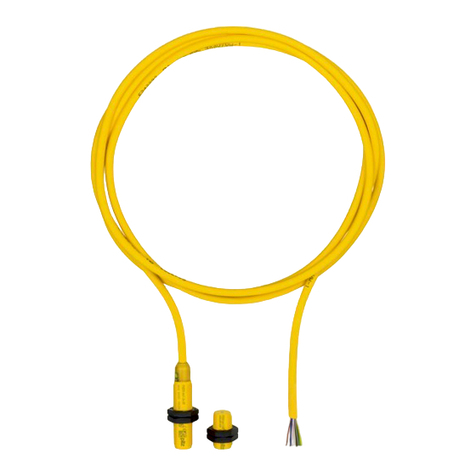
Pilz
Pilz PSEN ma1.3a/b-22 User manual

Pilz
Pilz PNOZ p1vp User manual
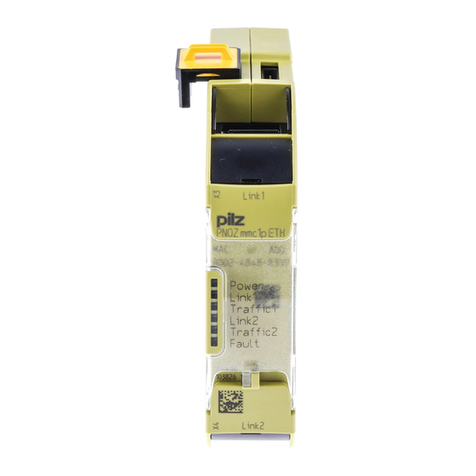
Pilz
Pilz PNOZ mmc1p User manual
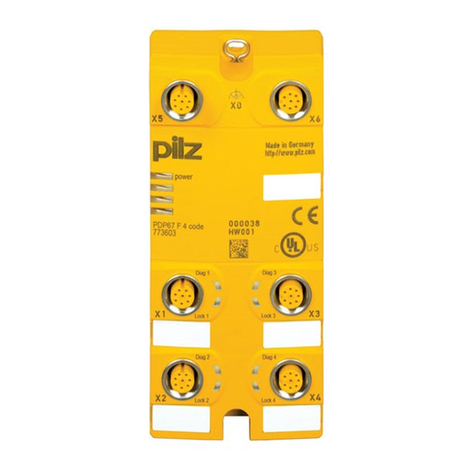
Pilz
Pilz PDP67 F 4 code User manual
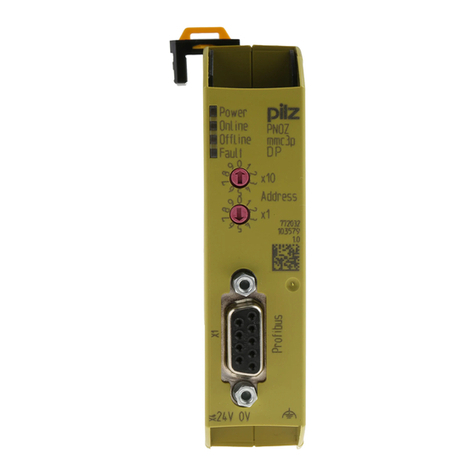
Pilz
Pilz PNOZmulti PNOZ mmc3p User manual

Pilz
Pilz PNOZ mc2.1p User manual
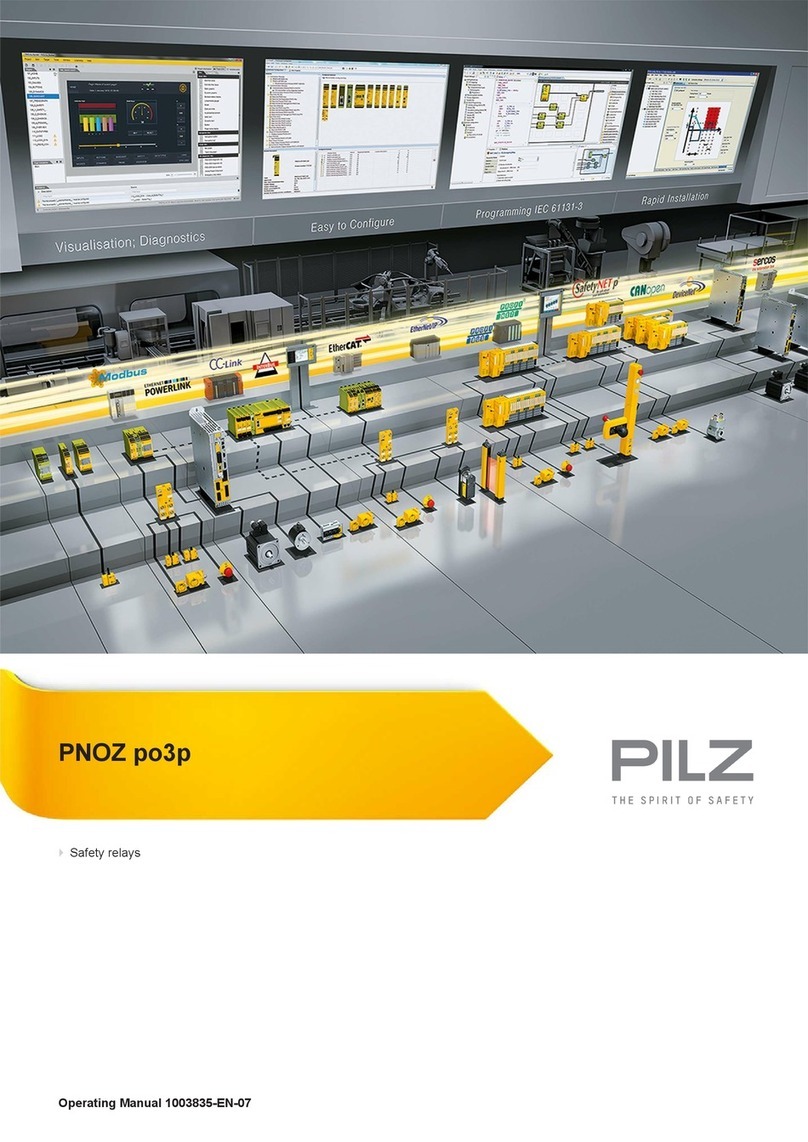
Pilz
Pilz PNOZ po3p User manual
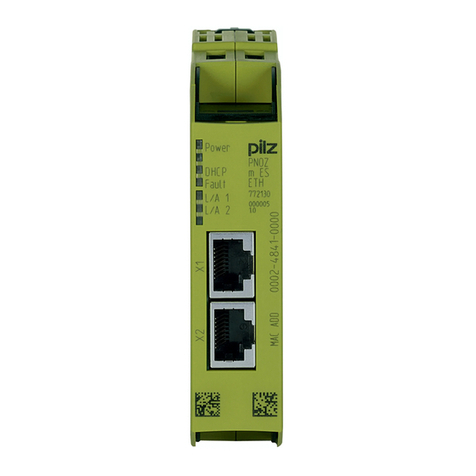
Pilz
Pilz PNOZ m ES ETH User manual
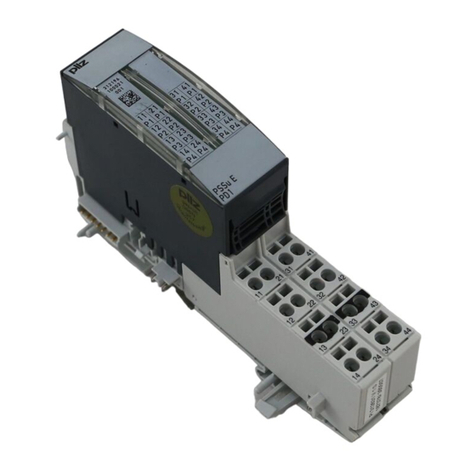
Pilz
Pilz PSSu E PD1-T User manual
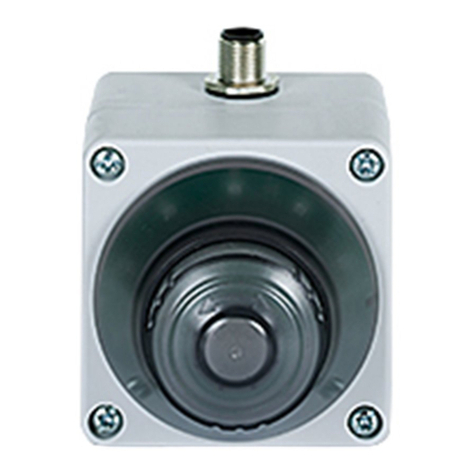
Pilz
Pilz PIT es Set10u-5ns (AIDA) basic User manual
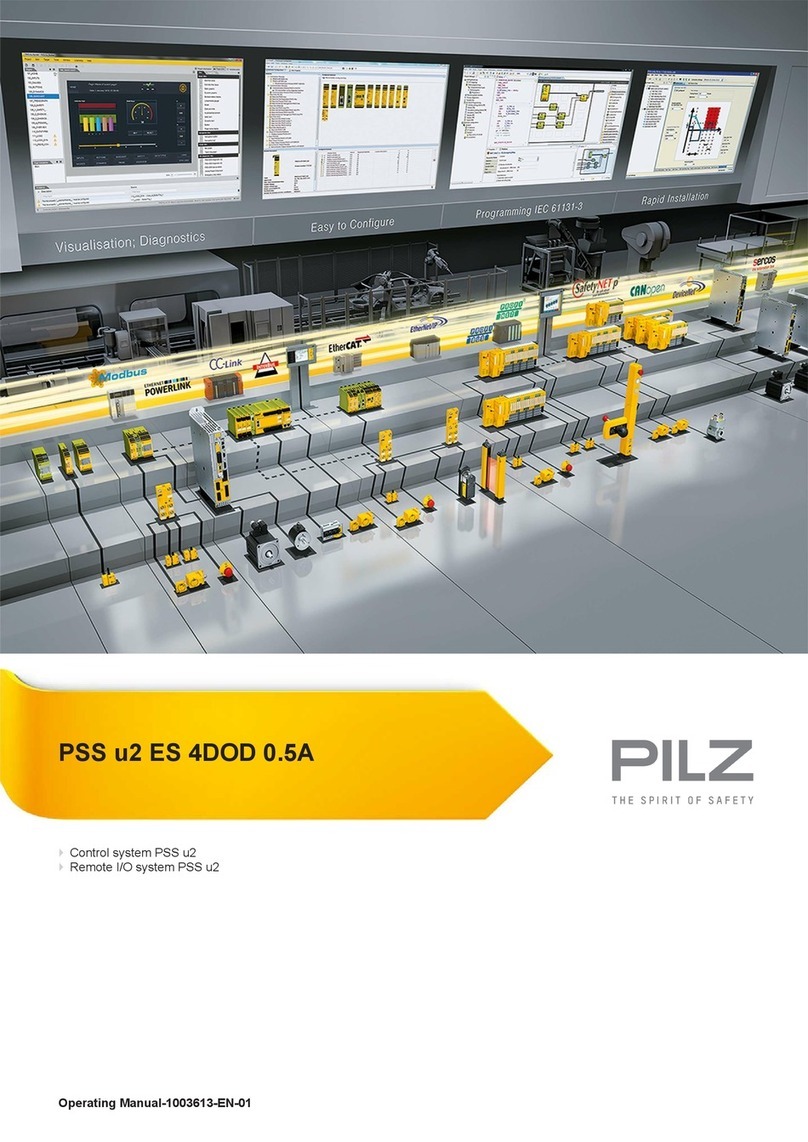
Pilz
Pilz PSS u2 ES 4DOD 0.5A User manual
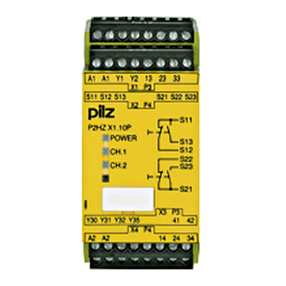
Pilz
Pilz P2HZ X1.10P User manual
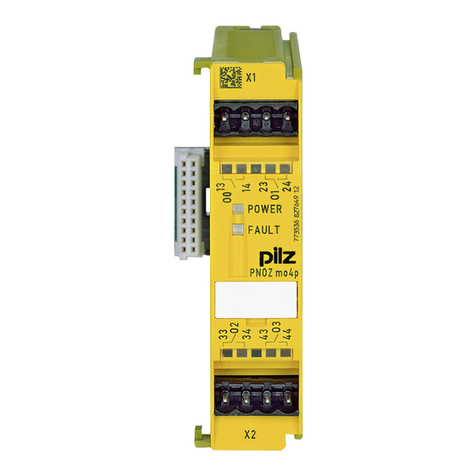
Pilz
Pilz PNOZ mo4p User manual
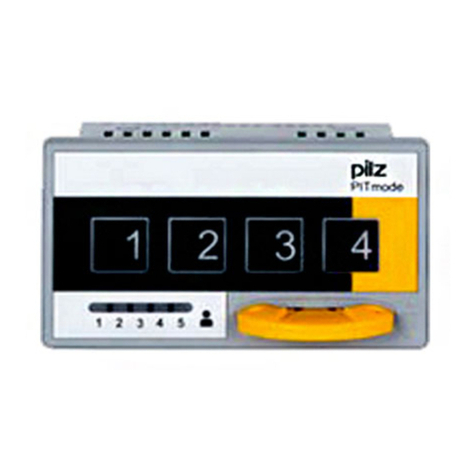
Pilz
Pilz PIT m3.3p User manual
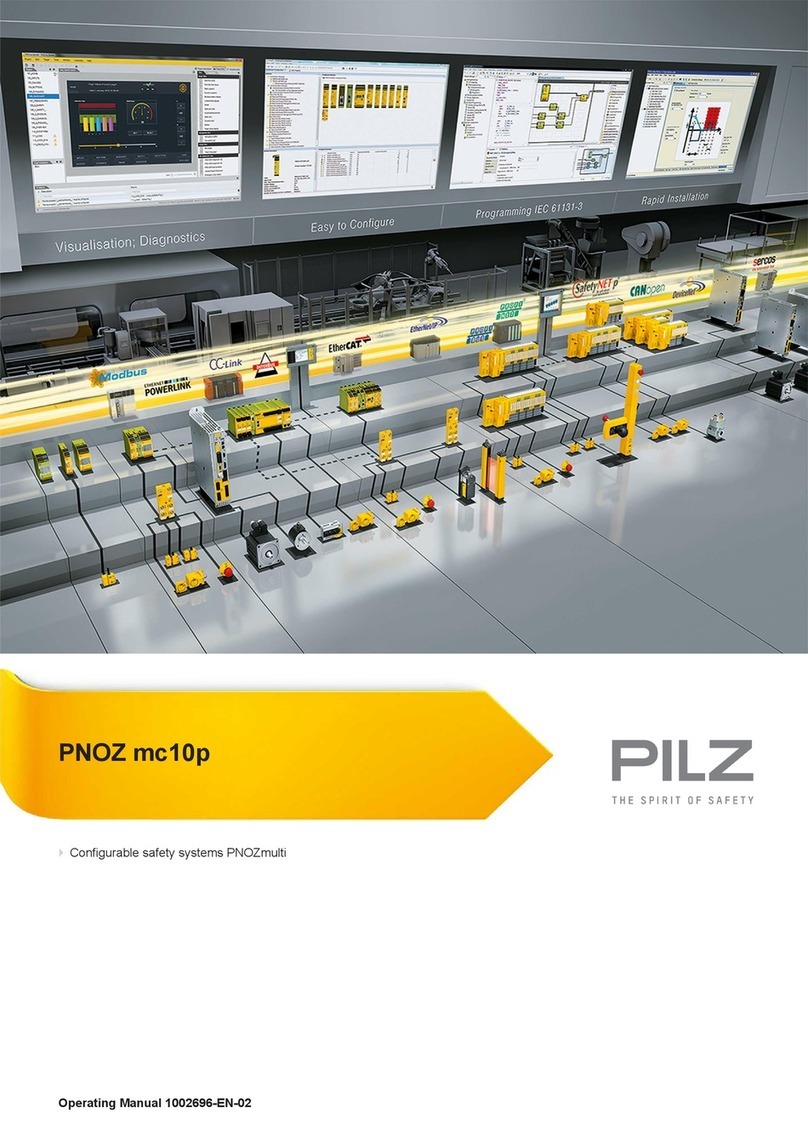
Pilz
Pilz PNOZ mc10p User manual
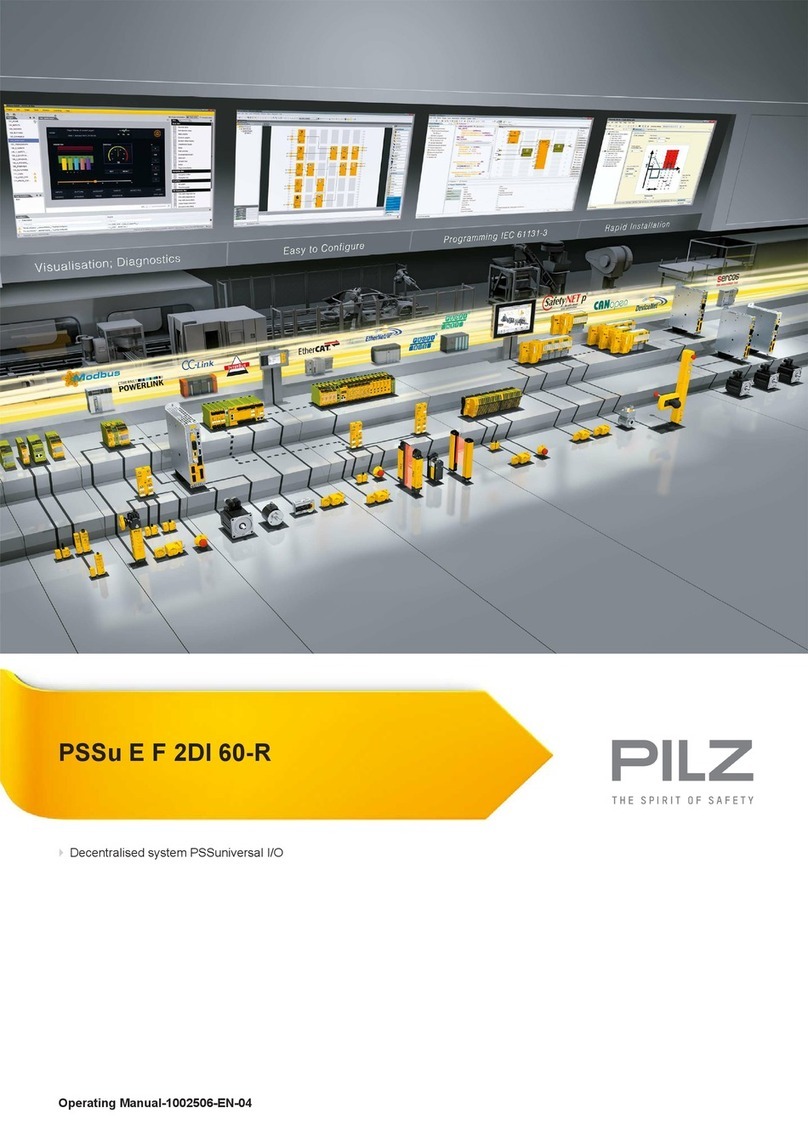
Pilz
Pilz PSSu E F 2DI 60-R User manual
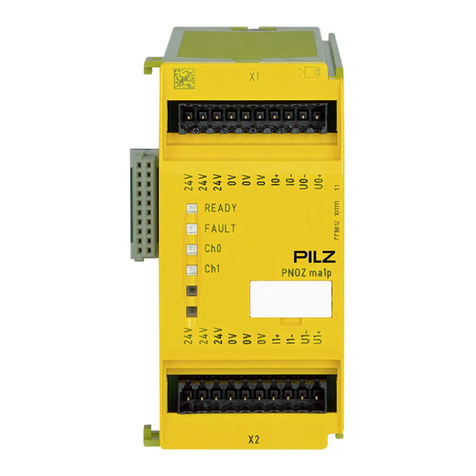
Pilz
Pilz PNOZ ma1p User manual