SenseAir aSENSE User manual

Document
UMA 139
Rev
2
Page
1 (7)
CO2/ temperature transmitter
General
The IAQ-sensor product aSENSE is used to measure indoor air carbon dioxide
concentration and temperature in rooms. The aSENSE is available both with and
without display, (LCD). Both are available for wall mounting as well as for duct
mounting.
The unit is designed for connecting to Direct Digital Control (DDC). The linear output
functions are pre-programmed as CO2 and temperature transmitters with jumper
selected outputs 0-10 V / 2-10 V / 0-20 mA / 4-20 mA. The measuring ranges can be
modified from a PC (Windows NT, XP, 7) and use of the software UIP (version 5 or
higher) together with the RS232 communication cable.
Figure 1 aSENSE for wall mounting and duct mounting
Gas and Air Sensors
aSENSE
User Manual

Document
UMA 139
Rev
2
Page
2 (7)
Terminal
Default Output
Default Output
Range
Outputs of this
sensor
Output Range of
this sensor
Out(1)
0-10VDC
0-2000 ppm CO2
Out(2)
0-10VDC
0-50 oC
32-122 oF
Table I. Default output configurations for aSENSE
Formulas for calculation of output values
Configuration
Output Range
Formula for calculation
0-10 VDC
0-2000 ppm CO2
0-50 oC
32-122 oF
CO2value = Volt/10*2000
Temperature value in oC = Volt/10*50 = Volt*5
Temperature value in oF = Volt*9+32
2-10 VDC
0-2000 ppm CO2
0-50 oC
32-122 oF
CO2value = (Volt –2)/8*2000
Temperature value in oC = (Volt –2)/8*50
Temperature value in oF = (Volt –2)/8*(122-32)+32
4-20 mA
0-2000 ppm CO2
0-50 oC
32-122 oF
CO2value = (mA-4)*2000/16
Temperature value in oC = (mA-4)*50/16
Temperature value in oF = (mA-4)/16*(122-32)+32
a-b
c–d
Value = (reading-a)/(b-a)*(d-c)+c
a = lowest value of the configuration
b = highest value of the configuration
c = lowest value of the range
d = highest value of the range
Table II. Calculation of CO2value and temperature value for aSENSE
Output Configurations
The sensors/controllers are supplied from the factory (unless otherwise ordered) with
0...10VDC linear outputs for Out(1) and Out(2)(see Table I). If other options are
needed for the application, the output jumpers have to be configured before the unit
is powered up. Each jumper selection is independent from the others, except for the
“Start point selection” jumper, which affects both Out(1) and Out(2)linear outputs.
Alternative measuring ranges of the outputs can be selected with the software UIP
(version 5 or later).

Document
UMA 139
Rev
2
Page
3 (7)
Jumper
Position
Function
Start
point
selection
jumper
0%
20%
Jumper top position provides 0Vdc or 0mA start point for Out(1), Out(2)
(0-20mA or 0-10V).
Jumper bottom position provides 2Vdc or 4mA start point for Out(1), Out(2) (4-
20mA or 2-10V).
NOTE! The start point jumper is missing on some models!
Out(1)
Current
Voltage
Connection in position “Current” provides 0/4-20mA output range for Out(1).
Current output is not recommended for temperature measurements
Connection in position “Voltage” provides 0/2-10VDC output range for Out(1).
Please note! Temperature measurements accuracy is valid only for units
configured in voltage outputs mode.
Out(2)
Current
Voltage
Connection in position “Current” provides 0/4-20mA output range for Out(2).
Current output is not recommended for temperature measurements
Connection in position “Voltage” provides 0/2-10VDC output range for Out(2).
Please note! Temperature measurements accuracy is valid only for units
configured in voltage outputs mode.
Table II. Configuration jumpers for aSENSE
Self-diagnostics
The system contains complete self-diagnostic procedures. A full system test is
executed automatically every time the power is turned on. In addition, constantly
during operation, the sensor probes are checked against failure by checking the valid
dynamic measurement ranges. All EEPROM updates, initiated by the sensor itself,
as well as by external connections, are checked by subsequent memory read back
and data comparisons. These different system checks return error bytes to the
system RAM. The error codes are available by connecting a PC with a special
RS232 cable connected to the UART port slide connector. The error codes are
shown in the software UIP (version 5 or later). Warm up and Out of Range are the
only bits that are reset automatically after return to normal state. All other error bits
have to be reset manually after return to normal by power off/on.
The yellow LED lights yellow at heating phase after power up and if an error has
been detected.

Document
UMA 139
Rev
2
Page
4 (7)
Error code and action plan
Bit #
Error
code
Error description
Suggested action
0
N/A
Fatal Error
Try to restart sensor by power
OFF/ON. Contact local distributor
1
2
Reserved
2
4
Algorithm Error.
Indicate wrong EEPROM
configuration.
Try to restart sensor by power
OFF/ON.
Check detailed settings and
configuration with UIP software
version 5 and higher.
Contact local distributor.
3
8
Output Error
Detected errors during output
signals calculation and
generation.
Check connections and loads of
outputs.
Check detailed status of outputs
with UIP software version 5 and
higher.
4
16
Self-Diagnostic Error.
Algorithm timeout
Check detailed self-diagnostic status
with UIP software version 5 and
higher.
Contact local distributor
5
32
Out of Range Error
Accompanies most of other
errors.
Resets automatically after
source of error disappearance.
Try sensor in fresh air.
Check connections of temperature
and relative humidity probe.
Check detailed status of
measurements with UIP software
version 5 and higher.
See Note 1!
6
64
Memory Error
Non-fatal error during memory
operations.
Check detailed settings and
configuration with UIP software
version 5 and higher.
7
128
Warm Up state
Is always set after power up or
power failure. Resets after
restart sequence.
If it doesn’t disappear in half a
minute, check power stability.
Note 1. Any probe is out of range. Occurs, for instance, during over exposure of CO2sensor, in
which case the error code will automatically reset when the measurement values return to normal.
Could also indicate the need of zero point calibration. If the CO2readings are normal, and still the
error code remains, the temperature sensor can be defect or the connections to it are broken.

Document
UMA 139
Rev
2
Page
5 (7)
Remark:If several errors are detected at the same time the different error code numbers will be
added together into one single error code!
PLEASE NOTE! The sensor accuracy is defined at continuous operation (at
least 3 weeks after installation)
Maintenance
The aSENSE is basically maintenance free. An internal self-adjusting calibration
function takes care of normal long term drift associated to the CO2sensor. To secure
the highest accuracy, a time interval of five years is recommended between CO2
calibrations, unless some special situations have occurred. A zero calibration can be
performed by use of pure nitrogen or air that has passed through a chemical
absorber and a PC together with the UIP software version 5 (or higher). The Zero
Calibration bag can be used to produce carbon dioxide free air. The software can be
free downloaded from www.senseair.com. The RS232-cable and the zero calibration
bag can be ordered from SenseAir. The cable is to be connected to the UART port
slide connector (see Fig. 5). For change of control parameters and re-calibration
(CO2and temperature) this PC tool has to be used. The check can be done on site
without interfering with the ventilation system. Re-calibration can be done with a PC
orby shortening of marked holes for at least 10 seconds.
A Back-ground calibration is an easy way to correct a sensor’s zero point. The
sensor needs fresh air (380-420 ppm CO2). Shorten marked holes for at least 10
seconds.
This is for sensors with measuring ranges between 0-3000 ppm and 0-4%:
When a zero calibration shall be executed a plastic tube with 2.2 mm outer diameter
and 0.8 mm inner diameter shall be inserted in marked holes of the sensor. Plastic
tubing is connected to the tube. The gas flow should be between 0.3 and 1.0 l/min.
Shorten marked holes for at least 10 seconds. A succesful calibration is
acknowledged by 5 flashes of the yellow LED. If unsuccessful, please release input
and waits at least 10 seconds before repeating the procedure again. Make sure that
the sensor environment is steady and calm!
Gas inlet
Figure 2 Part of the PCB with holes for gas inlets marked.

Document
UMA 139
Rev
2
Page
6 (7)
Duct mounting
If for some reason the printed circuit board (PCB) needs to be removed, special
precaution must be taken in order not to damage the temperature probe in the
sampling tube. When putting the PCB back in the protective housing, the probe must
be gently positioned in the sampling tube.
Figure 3 The aSENSE printed circuit board
Figure 4 The aSENSE for duct mounting. The temperature probe is the black body in the sampling
tube.

Document
UMA 139
Rev
2
Page
7 (7)
+
~
Figure 5 Terminals and jumpers on aSENSE.The darker positions are default settings. The start point
jumper is not mounted on some models.
WARRANTY AND LIMITATION OF LIABILITY
1. SenseAir warrants that for a period of twenty-four (24) months following receipt by
Buyer the Product supplied by SenseAir to Buyer will be, under normal use and care,
free from defects in workmanship or material and to be in material conformity with
SenseAir's specifications. Units returned to SenseAir for warranty repairs shall be
shipped to SenseAir, at Buyer’s expense, according to SenseAir's instruction. Within
ninety (90) days of the receipt of product, SenseAir shall replace or repair such units
and shall ship them to Buyer’s designated return destination freight pre-paid.
2. Warranty Limitations. This warranty does not extend to any unit that has been
subject to misuse, neglect or accident; that has been damaged by causes external to
the unit; that has been used in violation of SenseAir's instructions; that has been
affixed to any non-standard Accessory attachment; or that has been modified,
disassembled, or reassembled by anyone other than SenseAir.
3. The retailer is not responsible for any consequential loss or damages, which may
occur by reason of purchase and use of this product. The warranty is, in any event,
strictly limited to the replacement/repair of the product
This product is in accordance with the
EMC 2004/108/EC, 92/31/EEG
including amendments by the CE-marking Directive 93/68/EEC
The product fulfils the following demand:
EN 61326-1:2006, Class B equipment, Table 1 - Basic immunity test requirements
Other manuals for aSENSE
7
Table of contents
Other SenseAir Transmitter manuals
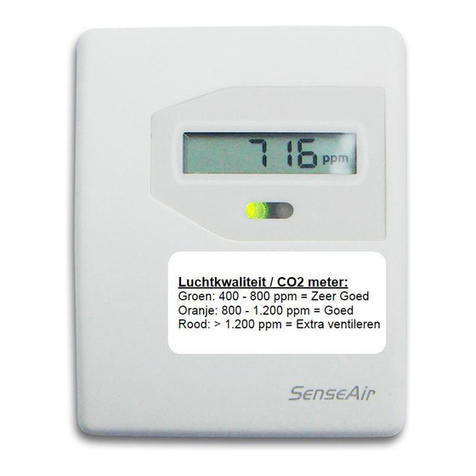
SenseAir
SenseAir eSENSE User manual

SenseAir
SenseAir tSENSE VAV User manual
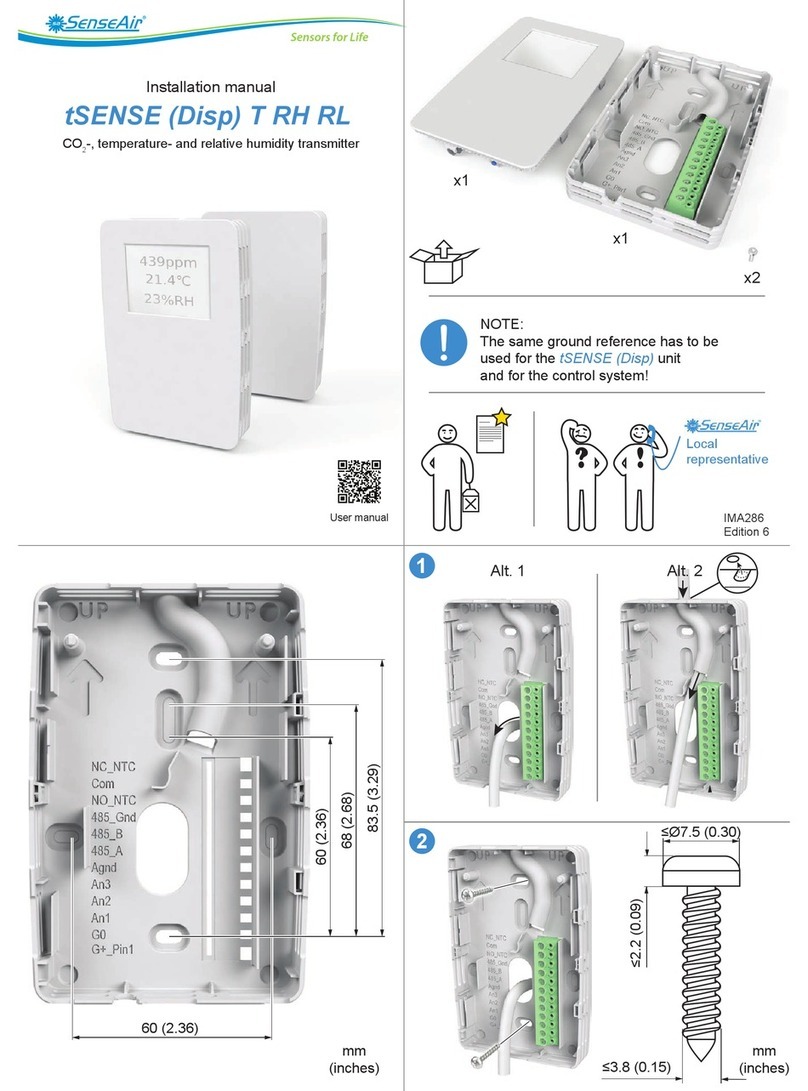
SenseAir
SenseAir tSENSE (Disp) T RH RL User manual
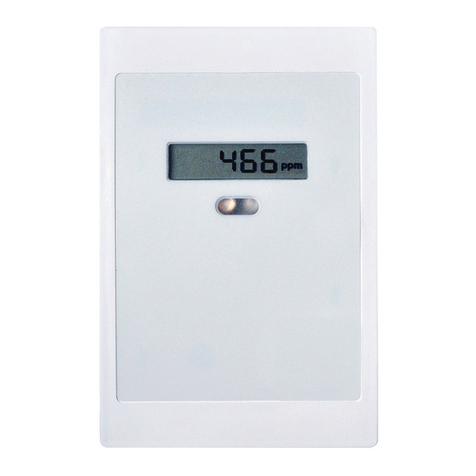
SenseAir
SenseAir eSENSE II User manual
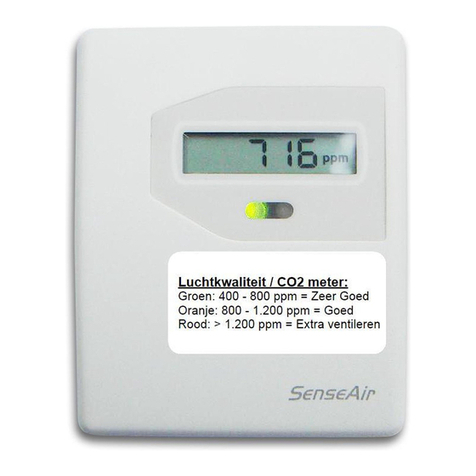
SenseAir
SenseAir eSENSE User manual
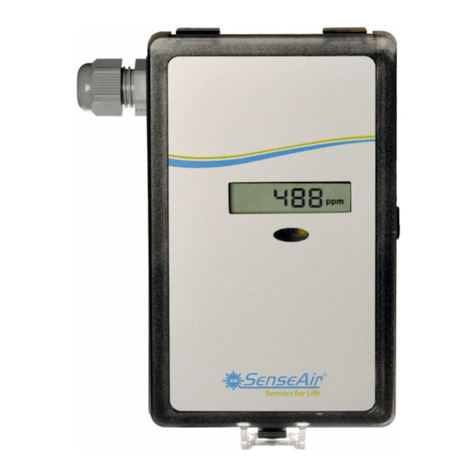
SenseAir
SenseAir eSENSE Ind User manual
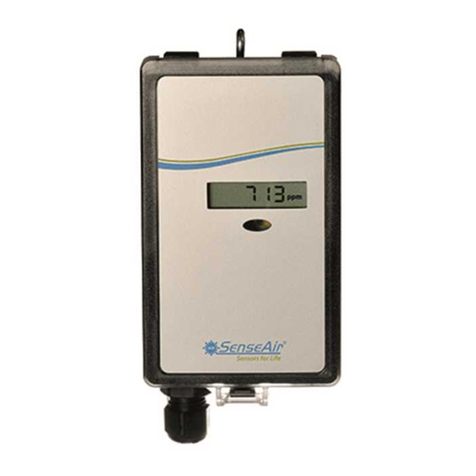
SenseAir
SenseAir aSENSE GH (Disp) RL User manual
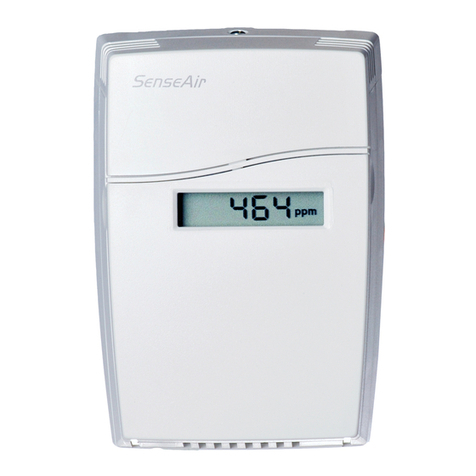
SenseAir
SenseAir aSENSE User manual
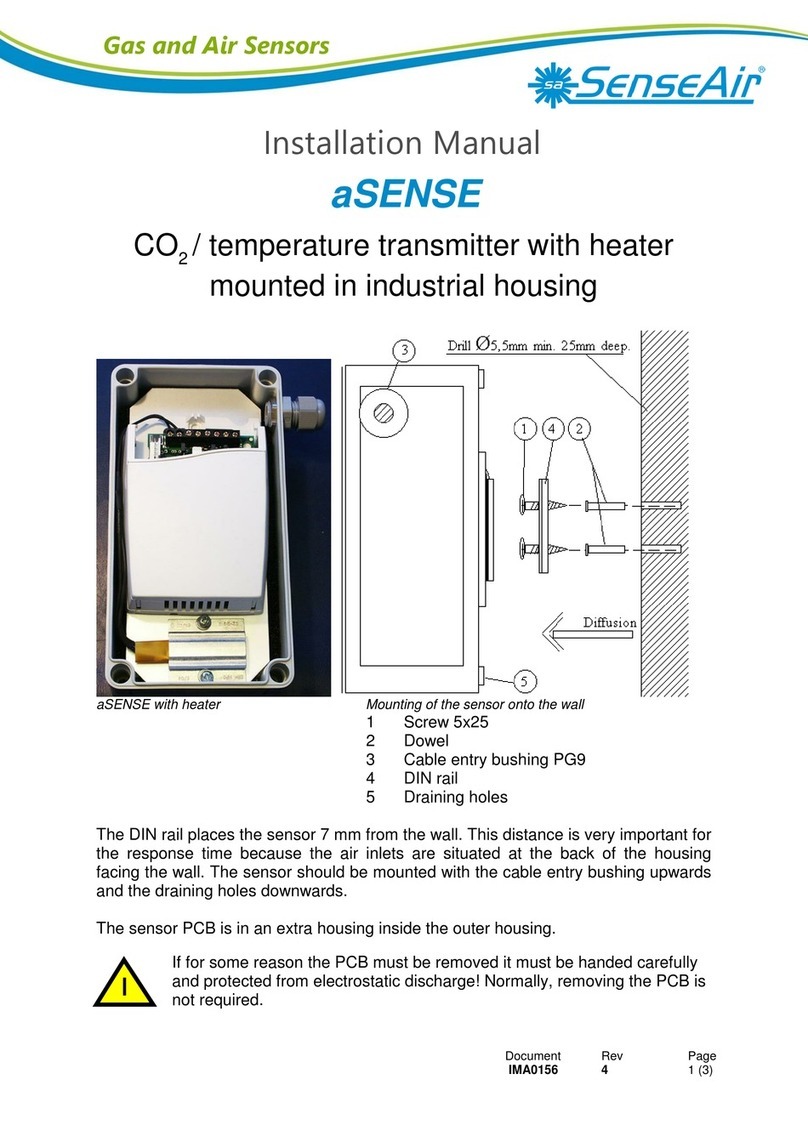
SenseAir
SenseAir aSENSE User manual

SenseAir
SenseAir aSENSE User manual