SKF MicroDosage System User manual

MDU micro-metering unitMDR lubricant reservoir
Tool spindleMachine tool control unit
MDR
MDU
Assembly instructions acc. to EC Dir. 2006/42/EC
for partly completed machinery with associated operating instructions EN
MicroDosage System (MDS)
Version 04
for continuous lubrication of high-speed spindles
with minimum quantities of oil from 0.5 to 5 mm3/min

Page 2
EN

Page 3 EN
Notes
Masthead
These assembly instructions with associated
operating instructions according to EC
Machinery Directive 2006/42/EC are an inte-
gral part of the described product and must
be kept for future use.
These assembly instructions with associated
operating instructions have been prepared in
accordance with the established standards and
rules for technical documentation, VDI 4500
and EN 292.
© SKF Lubrication Systems Germany GmbH
This documentation is protected by copyright.
SKF Lubrication Systems Germany GmbH re-
serves all rights, including those to the photo-
mechanical reproduction, duplication, and dis-
tribution by means of special procedures (e.g.,
data processing, data media, and data net-
works) of this documentation in whole or in
part.
Subject to changes in contents and technical
information.
Service
If you have technical questions, please contact
the following addresses:
SKF Lubrication Systems Germany GmbH
Berlin Plant
Motzener Strasse 35/37
12277 Berlin
Germany
Tel. +49 (0)30 72002-0
Fax +49 (0)30 72002-111
lubrication-germa[email protected]om
www.skf.com/lubrication
Hockenheim Plant
2. Industriestrasse 4
68766 Hockenheim
Germany
Tel. +49 (0)62 05 27-0
Fax +49 (0)62 05 27-101
lubrication-germa[email protected]om
www.skf.com/lubrication

Page 4
EN Table of contents
Table of contents
MicroDosage System (MDS) 1
Service 3
Information concerning EC Declaration of
Conformity and EC Declaration of Incorporation 6
Explanation of symbols and signs 7
1. Safety instructions 8
1.1 Intended use 8
1.2 Authorized personnel 9
1.3 Electric shock hazard 9
1.4 System pressure hazard 10
1.5 Compressed air hazard 10
1.6 Warranty and liability 10
1.7 Existing residual risks 11
2. Lubricants 13
2.1 General information 13
2.2 Selection of lubricants 13
2.3 Approved lubricants 14
2.4 Lubricants and the environment 15
2.5 Lubricant hazards 15
3. Overview 16
3.1 SKF microdosage system 16
3.2 MDU micro-metering unit 17
3.3 MDR lubricant reservoir designs 18
4. Assembly 19
4.1 General information 19
4.2 Setup and attachment 20
4.2.1 General information on
lubrication line arrangement 20
4.3 MDR lubricant reservoir 21
4.3.1 Attachment of MDR lubricant reservoir 22
4.3.2 Assembly drawing with minimum
installation dimensions 22
4.3.3 Electricallllevelindicator 23
4.3.4 Initialllingandventingofthe
MDR lubricant reservoir 23
4.3.5 Connecting compressed air connection 25
4.4 MDU micro-metering unit 26
4.4.1 Attachment of the MDU micro-
metering unit 26
4.4.2 Assembly drawing with minimum
installation dimensions 27
4.4.3 Capillary line connection 29
4.4.4 Arrangement of capillary lines 30
4.5 Main lubricant line and venting 30
4.5.1 Venting the main lubricant line
and MDU micro-metering unit 31
4.6 Note on the rating plate 33
4.6.1 MDU rating plate 33
4.6.2 MDR rating plate 33
Assembly instructions

Page 5 EN
Table of contents
Operating instructions
Microdosage system (MDS) 35
1. Safety instructions 36
1.1 General information 36
1.2 Disclaimer of liability 36
2. Lubricants 36
3. Transport, delivery, and storage 37
3.1 Lubrication units 37
3.2 Electronic and electrical devices 37
3.3 General information on storage 37
4. Assembly 38
4.1 Information on assembly 38
4.2 Installation and use on spindles 38
4.2.1 Spindle design 38
4.2.2 Lubricant quantity 40
4.2.3 Filling lubricant ducts in the spindle 41
5. Design and function 42
5.1 General information42
5.2 Principle of the SKF microdosage system 43
6. Operation 45
6.1 General information 45
6.2 Microdosage system parameters 46
6.2.1 Conguringthesystem 47
6.2.2 Determining quantity of lubricant 47
6.3 Commissioning/venting the system 48
6.3.1 Venting the system 48
6.3.2 Filling spindle lubricant ducts 50
6.4 Calibration of the system 51
6.4.1 General 51
6.4.2 Manual calibration 51
6.5 Externaladjustmentofvolumetricow 52
6.4.3 Automatic calibration 52
7. Shutdown and disposal 55
7.1 Temporary shutdown 55
7.2 Permanent shutdown 55
8. Maintenance and service 56
8.1 General information 56
8.2 Maintenance and repair 57
9. Malfunctions 58
9.1 General 58
9.2 Malfunctions, causes, and remedies 59
9.3 Questions and answers on using the
SKF microdosage system 59
10. Technical data 61
10.1 MDU micro-metering unit 61
10.2 MDR lubricant reservoir 61
11. Accessories 62

Page 6
EN
The products,
metering unit MDU
lubricant reservoir MDR
of the minimal quantity lubrication system
MDS SKF microdosage system
are hereby confirmed to comply with the es-
sential protection requirements stipulated by
the following Directive(s) of the Council on the
approximation of laws of the Member States:
Machinery Directive 2006 2006/42/EG
Electromagnetic Compatibility 2014/30/EU
Low Voltage Devices 2014/35/EU
RoHS II Directive 2011/65/EU
Notes:
Information concerning EC Declaration of Conformity and EC Declaration of Incorporation
Information concerning EC Declaration of Conformity and EC Declaration of Incorporation
The products are neither designed nor ap-
proved for use in conjunction with fluids of
Group 1 (Dangerous Fluids) as defined in
Article 2, Para. 2 of Directive 67/548/EEC of
June 27, 1967. The products are neither de-
signed nor approved for use in conjunction
with gases, liquefied gases, pressurized gases
in solution, vapors, or and such fluids whose
vapor pressure exceeds normal atmospheric
pressure (1013 mbar) by more than 0.5 bar
at their maximum permissible temperature.
When used in conformity with their intended
use, the products supplied by SKF Lubrication
Systems Germany GmbH do not reach the
limit values listed in Article 3, Para. 1, Clauses
1.1 to 1.3 and Para. 2 of Directive 97/23/EC.
They are therefore not subject to the require-
ments of Annex 1 of the Directive.
Consequently, they do not bear a CE marking
in respect of Directive 97/23/EC. SKF
Lubrication Systems Germany GmbH classifies
them according to Article 3, Para. 3 of the
Directive. The Declaration of Conformity and
Incorporation forms part of the product docu-
mentation and is supplied together with the
products.
(a) This declaration certifies compliance with
the aforementioned Directives but does not
constitute a guarantee of characteristics.
(b) The safety instructions in the documenta-
tion included with the products must be
observed.
(c) The commissioning of the products here
certified is prohibited until the machine,
tool, or similar in which the product is in-
stalled conforms with the provisions and
requirements of the applicable Directives.
(d) The operation of the products at non-stan-
dard supply voltage, as well as non-adher-
ence to the installation instructions, can
negatively impact the EMC characteristics
and electrical safety.
We further declare:
The aforementioned products are, accord-
ing to EC Machinery Directive 2006/42/
EC, Annex II Part B, designed for installa-
tion in machinery / for incorporation with
other machinery to form a machine. Within
the scope of the EC Directive, commission-
ing shall be prohibited until the machinery
in which these products are installed con-
forms with the provisions of this Directive.
The aforementioned products may, with
reference to EC Directive 97/23/EC con-
cerning pressure equipment, only be used
in accordance with their intended use and
in conformity with the instructions provided
in the documentation. The following must
be observed in this regard:

Page 7 EN
Informational symbolsSafety signal words and their meaning
Hazard symbols
Explanation of symbols
Explanation of symbols and signs
You will find these symbols, which warn of
specific dangers to persons, material assets, or
the environment, next to all safety instructions
in these assembly and operating instructions.
Please heed these instructions and proceed
with special care in such cases. Please forward
all safety instructions to other users.
General hazard
DIN 4844-2-W000
Electrical voltage/current
Hot surface
Signal word Meaning
Danger! Risk of serious injury or death
Warning! Risk of damage to property
and the environment
Note! Provides additional information
Note
• Prompts an action
Used for itemizing
Refers to other facts, causes, or
consequences
Provides additional information
Environmentally sound disposal
Instructions placed directly on the product,
such as:
Rotation arrows
Fluid connection labels
must be followed and kept in fully legible
condition.
You are responsible!
Please read the assembly and operating in-
structions thoroughly and follow the safety
instructions.
Note: Not all the symbols listed are necessar-
ily used in these instructions.
Danger of being drawn into machinery
DIN 4844-2-W008
DIN 4844-2-W026
BGV 8A
Slipping hazard
DIN 4844-2-W028

Page 8
EN
The operator of the described pro-
duct must ensure that the assembly
instructions are read and understood by
all persons tasked with the assembly,
operation, maintenance, and repair of
the product. The assembly instructions
must be kept readily available.
Note that the assembly instructions
form part of the product and must
accompany the product if sold to a new
owner.
1. Safety instructions
In addition to the assembly instructions,
statutory regulations and other general
regulations for accident prevention
and environmental protection must be
observed and applied.
The described product is manufactured in
accordance with the generally accepted rules
and standards of industry practice and with
occupational safety and accident prevention
regulations. Risks may, however, arise from its
usage and may result in physical harm to per-
sons or damage to other material assets.
Therefore the product may only be used in
proper technical condition and in observance
of the assembly instructions. In particular, any
malfunctions which may affect safety must be
remedied immediately.
1.1 Intended use
All products from SKF Lubrication
Systems Germany GmbH may be used
only for their intended purpose and in
accordance with the information in the
product's assembly instructions.
The SKF microdosage system MDS, together
with the products MDU micro-metering unit
and MDR lubricant reservoir, is used to
supply lubricant to high-speed spindles and
high-speed bearings.
The plastic or stainless steel capillary lines re-
quired between the MDU and the lubrication
points must have an internal diameter of
0.5 mm and cannot have an overall length
greater than 4 m.
The oils used must be filtered; prescribed filter
rating ≤ 5 µm.
Any other use is deemed non-compliant with
the intended use and could result in damage,
malfunction, or even injury.
Assembly instructions

Page 9 EN
Assembly instructions
In particular, the described products are neither
designed nor approved for use in conjunction
with fluids of Group 1 (Dangerous Fluids) as
defined in Article 2, Para. 2 of Directive
67/548/EEC of June 27, 1967.
The described products are neither designed
nor approved for use in conjunction with gases,
liquefied gases, pressurized gases in solution,
vapors, or and such fluids whose vapor pres-
sure exceeds normal atmospheric pressure
(1013 mbar) by more than 0.5 bar at their
maximum permissible temperature.
Unless specially indicated otherwise, products
from SKF Lubrication Systems Germany GmbH
are not approved for use in potentially explosive
areas as defined in the ATEX Directive 94/9/EC.
1.2 Authorized personnel
Only qualified technical personnel may install,
operate, maintain, and repair the products
described in the assembly instructions.
Qualified technical personnel are persons who
have been trained, assigned, and instructed by
the operator of the final product into which
the described product is incorporated. Such
persons are familiar with the relevant stan-
dards, rules, accident prevention regulations,
and assembly conditions as a result of their
training, experience, and instruction. They are
qualified to carry out the required activities
and in doing so recognize and avoid any po-
tential hazards.
The definition of qualified personnel and the
prohibition against employing non-qualified
personnel are laid down in DIN VDE 0105 and
IEC 364.
1.3 Electric shock hazard
Electrical connections for the described product
may only be established by qualified and
trained personnel authorized to do so by the
operator, and in observance of the local condi-
tions for connections and local regulations
(e.g., DIN, VDE). Serious injury or death and
property damage may result from improperly
connected products.
Danger!
Performing work on an energized
product may result in serious
injury or death.
Assembly, maintenance, and repair
work may only be performed on pro-
ducts that have been de-energized by
qualiedtechnicalpersonnel.The
supply voltage must be switched off
before opening any of the product's
components.

Page 10
EN
1.5 Compressed air hazard
The lubricant reservoir is pressurized with
compressed air.
Danger!
The described product is pressurized
during operation. The product must
therefore be depressurized before
starting assembly, maintenance or
repairwork,oranysystemmodications
or system repairs.
1.6 Warranty and liability
SKF Lubrication Systems Germany GmbH as-
sumes no warranty or liability for the
following:
o Non-compliant usage
o Improper assembly, configuration, filling,
disassembly, or improper operation
o Use of unsuitable or contaminated lubricants
o Maintenance and repair work performed
improperly or not performed at all
o Use of non-original SKF components or
spare parts
o Alterations or modifications performed
without written approval from SKF
Lubrication S ys tem s Ge rm an y G mb H
o Results of improper response to
malfunctions
o Independent modification of system
components
o Non-compliance with the instructions for
transport and storage
1.4 System pressure hazard
Danger!
Centralized lubrication systems are
pressurized during operation. Centralized
lubrication systems must therefore be
depressurized before starting assembly,
maintenance, or repair work, or any
systemmodicationsorsystemrepairs.
Assembly instructions
Note!
The MDU metering unit contains elec-
tronic components that can be destroy-
ed by accidental electrostatic charge or
discharge (ESD). To prevent possible da-
mage due to ESD, hands and any tools
must be discharged on a bare grounded
position on the installation site prior
to performing any work in the area of
the opened control unit’s circuit board.
Conductors or component connections
within the device must not be touched
under any circumstances.

Page 11 EN
Assembly instructions
1.7 Existing residual risks (residual risk assessment)
Residual risk Remedy
Life cycle: Assembly
Manual filling:
lubricant discharge from the pressure
regulating valve of the lubricant reservoir
in case of overfilling
• Perform filling of the lubricant reservoir carefully and stop once the “MAX fill level” (sight glass on
lubricant reservoir) or electrical max. signal is reached.
Risk of slipping due to contamination of
floor by spilled or leaked lubricant
• Proceed carefully when filling the lubricant reservoir using a filler coupling.
• Promptly apply suitable binding agents and remove the leaked or spilled lubricant
• Follow statutory and company regulations for the handling of lubricants
Tearing/damage to supply, compressed
air, and lubricant lines when installed on
moving machine components.
• If possible, do not install on moving machine parts; If this cannot be avoided, use flexible supply,
compressed air, and lubricant lines.
Life cycle: Commissioning/operation
Lubricant spraying out due to faulty instal-
lation of fittings/screw unions on lubricant
lines
• Tighten all fittings/screw unions with the appropriate torques (where specified). Use fittings/screw
unions and lubricant lines suitable for the indicated operating pressures. Check all fittings/screw unions
and lubricant lines for correct connection and damage before commissioning
Risk of slipping due to contamination of
floor by spilled or leaked lubricant
• Proceed carefully when filling the lubricant reservoir using a filler coupling.
• Promptly apply suitable binding agents and remove the leaked or spilled lubricant
• Follow statutory and company regulations for the handling of lubricants

Page 12
EN Assembly instructions
Residual risk Remedy
Life cycle: Setup, retrofit
Risk of slipping due to contamination of floor by
spilled or leaked lubricant
• Proceed carefully when filling the lubricant reservoir using a filler coupling.
• Promptly apply suitable binding agents and remove the leaked or spilled lubricant.
• Follow statutory and company regulations for the handling of lubricants.
Life cycle: Malfunctions, fault-finding
Risk of slipping due to contamination of floor by
spilled or leaked lubricant
• Proceed carefully when filling the lubricant reservoir using a filler coupling.
• Promptly apply suitable binding agents and remove the leaked or spilled lubricant.
• Follow statutory and company regulations for the handling of lubricants.
Life cycle: Maintenance, repair
Risk of slipping due to contamination of floor by
spilled or leaked lubricant
• Proceed carefully when filling the lubricant reservoir using a filler coupling.
• Promptly apply suitable binding agents and remove the leaked or spilled lubricant.
• Follow statutory and company regulations for the handling of lubricants.
Life cycle: Decommissioning, disposal
Contamination of the environment with lubricant
and components that have come into contact with
lubricant
• Properly dispose of lubricants and components that have come into contact with lubricants.
Follow the statutory and company regulations for the handling of lubricants.
Risk of slipping due to contamination of floor by
spilled or leaked lubricant
• Proceed carefully when filling the lubricant reservoir using a filler coupling.
• Promptly apply suitable binding agents and remove the leaked or spilled lubricant.
• Follow statutory and company regulations for the handling of lubricants.

Page 13 EN
2. Lubricants
2.1 General information
All products from SKF Lubrication
Systems Germany GmbH may be used
only for their intended purpose and in
accordance with the information in the
product's assembly instructions.
Intended use is the use of the products for the
purpose of providing centralized lubrication/
lubrication of bearings and friction points with
lubricants within the physical usage limits
which can be found in the documentation for
the device, e.g., assembly instructions/operat-
ing instructions and the product descriptions,
e.g., technical drawings and catalogs.
Particular attention is called to the fact that
hazardous materials of any kind, especially the
materials classified as hazardous by
EC Directive 67/548/EEC, Article 2, Para. 2,
may only be filled into SKF centralized lubrication
systems and components and delivered and/or
distributed with the same after consultation
with and written approval from SKF
Lubrication Systems Germany GmbH.
No products manufactured by SKF Lubrication
Systems Germany GmbH are approved for use
in conjunction with gases, liquefied gases,
pressurized gases in solution, vapors, or such
fluids whose vapor pressure exceeds normal
atmospheric pressure (1013 mbar) by more
than 0.5 bar at their maximum permissible
temperature.
Other media which are neither lubricant nor
hazardous substance may only be fed after
consultation with and written approval from
SKF Lubrication Systems Germany GmbH.
SKF Lubrication Systems Germany GmbH
considers lubricants to be an element of sys-
tem design that must always be factored into
the selection of components and the design of
centralized lubrication systems.
The lubricating properties of the lubricants are
critically important in making these selections.
2.2 Selection of lubricants
Observe the instructions from the
machine manufacturer regarding the
lubricants that are to be used.
Note!
The amount of lubricant required at
alubricationpointisspeciedbythe
spindle or machine manufacturer. It
must be ensured that that the required
quantity of lubricant is provided to the
lubrication point. The lubrication point
may otherwise not receive adequate
lubrication, which can lead to damage
and failure of the bearing.
Selection of a lubricant suitable for the lubri-
cation task is made by the spindle/machine
manufacturer and/or the operator of the ma-
chine/system in cooperation with the lubricant
supplier. When selecting a lubricant, the type
of spindle/bearing/friction points, the expected
load during operation,
Assembly instructions

Page 14
EN
and the anticipated ambient conditions must
be taken into account. All economic and envi-
ronmental aspects must also be considered.
If required, SKF Lubrication Systems
Germany GmbH can help customers
to select suitable components for the
conveyance of the selected lubricant
and to plan and design their centralized
lubrication system.
Please contact SKF Lubrication Systems
Germany GmbH if you have further questions
regarding lubricants. It is possible for lubri-
cants to be tested in the company's laboratory
for their suitability for pumping in centralized
lubrication systems (e.g., "bleeding").
You can request an overview of the lubricant
tests offered by SKF from the company's Sales
department.
2.3 Approved lubricants
Note!
Only lubricants approved for the pro-
duct may be used. Unsuitable lubricants
can lead to failure of the product and to
property damage.
Note!
Different lubricants must not be mixed
together. Doing so can cause damage
and require extensive cleaning of the
product/centralized lubrication system.
It is recommended that an indication of
the lubricant in use be attached to the
lubricant reservoir in order to prevent
accidental mixing of lubricants.
The product described here can be operated
using lubricants that meet the specifications in
the technical data.
Note that in rare cases, there may be lubri-
cants whose properties are within the permis-
sible limits values but whose other character-
istics render them unsuitable for use in
centralized lubrication systems. For example,
synthetic lubricants may be incompatible with
elastomers.
Oils with a viscosity different than those in
Table 1 should be avoided because the meter-
ing system cannot be ensured to function
properly with them.
Oils with solid additives must not be used,
since with these oils there is a risk that the
solid particles will deposit within the metering
unit and could cause clogging of the metering
unit.
Assembly instructions

Page 15 EN
2.4 Lubricants and the environment
Note!
Lubricants can contaminate soil and
waterways. Lubricants must be used
and disposed of properly. Observe the
local regulations and laws regarding the
disposal of lubricants.
It is important to note that lubricants are envi-
ronmentally hazardous, flammable substances
which require special precautionary measures
during transport, storage, and processing.
2.5 Lubricant hazards
Danger!
Centralized lubrication systems must al-
ways be free of leaks. Leaking lubricant
is hazardous due to the risk of slipping
and injury. Beware of any lubricant
leaking out during assembly, operation,
maintenance, or repair of centralized
lubrication systems. Leaks must be
sealed off without delay.
Lubricant leaking from centralized lubrication
systems is a serious hazard. Leaking lubricant
can create risks that may result in physical
harm to persons or damage to other material
assets.
Follow the safety instructions on the
lubricant's safety data sheet.
Lubricants are hazardous substances. Follow
the safety instructions on the lubricant's safety
data sheet. The safety data sheet for a lubricant
can be requested from the lubricant
manufacturer.
Consult the safety data sheet from the lubri-
cant manufacturer for information regarding
transport, storage, processing, and environ-
mental hazards of the lubricant that will be
used.
The safety data sheet for a lubricant can be
requested from the lubricant manufacturer.
Assembly instructions
Approved oils, Table 1
Requirement Values
Recommended
oil purity level
13/10 (ISO 4406)
or:
Class 4 (NAS 1638)
Recommended
ISO VG class
32 ... 68
Based on 40 °C
Approved
additives
EP additives
Prohibited
additives
Solids

Page 16
EN Assembly instructions
3. Overview
Application example of the microdosage system on a machine tool
Legend
Item Description Chapter
1 MDR lubricant reservoir 3.3
1a Electr. fill level switch 4.3.3
1b Max. fill level sight glass 3.3
1c Compressed air connection
4.5-10 bar
1d Min. fill level sight glass 3.3
1e Filler coupling 3.3/4.3.4
2 Main lubricant line for MDU
(lubricant pressure 4 bar) 4.5
3 High-speed spindle
provided by customer
4 MDU micro-metering unit 3.2/4.4
to supply up to 4 lubrication
points
5 Capillary lines to the
lubrication points 4.4.3/4.4.4
6 Lubrication points (spindle bearing) OI/Chap. 4
7 Data lines for MDU/MDR OI/Chap. 5
for customer’s machine tool
control unit
(OI = Operating Instructions)
1
2
3
4
5
PLC
1a
1b
1d
1e
7
6
3.1 Overview of the SKF microdosage system
1c

Page 17 EN
Assembly instructions
MDU micro-metering unit Components of the MDU micro-metering unit
Item Description Chapter
1 MDU micro-metering unit 4.4
2 Power supply LED (green power LED)
3 LED enable signal (yellow enable LED) OI/Chap. 6
4 Error notification LED (red error LED)
5 LEDs for outlet 1 to outlet 4 (OUT1- OUT4)
6 Push connector/connecting cable for lubricant feed 4.4.
7 Connection for supply/control voltage 4.33
8 Flow sensor OI/5
9 Rotary switch for setting lubricant quantity (x4) OI/6.2
10 Connection for capillary lines, lubricant outlet (x4)
OUT1 to OUT4 4.4.3
11 Capillary lines (x 4) 4.3.4
12 DIP switches for system configuration OI/6.2.1
13 Side vent plug OI/6.3.1
14 Top vent plug OI/6.3.1
(OI = Operating Instructions)
1
3.2 Overview of MDU micro-metering unit
2
3
4
6
7
8
9
12
13
14
5
10/11

Page 18
EN Assembly instructions
MDR lubricant reservoir Components of an MDR lubricant reservoir
Item Description Chapter
1 MDR lubricant reservoir 4.3.1
2 Vent plug 4.3.4
3 Electrical fill level monitoring 4.3.3
4 Compressed air control valve 4.3
5 Compressed air input port 4.3.5
6 Pressure gauge for compressed air 4.3.5
7 Assembly holes (4x) 4.3.1
8 Sight glass, visual fill level
monitoring, max. fill level 4.3.3
9 Lubricant outlet port
(to the MDU) 4.2
10 Lubricant outlet stopcock 4.3.3
11 Sight glass, visual fill level
monitoring, min. fill level 4.3.3
12 Pressure regulating valve 4.3.1
13 Filler coupling 4.3.1
3.3 Overview of MDR lubricant reservoir designs
2
10
4
5
6
8
11
9,
1
3
12
7
13
The inlets and outlets on the lubricant reservoir can be located on the left or right, and their
position can be switched according to need and the installation space.
Examples of various connectivity options,
area of inlet/outlet/filling

Page 19 EN
Assembly instructions
4. Assembly
4.1 General information
Only qualified technical personnel may install,
operate, maintain, and repair the micro-me-
tering products described in the assembly in-
structions. Qualified technical personnel are
persons who have been trained, assigned, and
instructed by the operator of the final product
into which the described microdosage system
is incorporated. Such persons are familiar with
the relevant standards, rules, accident preven-
tion regulations, and operating conditions as a
result of their training, experience, and in-
struction. They are authorized to carry out the
required activities and in doing so recognize
and avoid potential hazards.
The definition of trained personnel and the
prohibition of employing non-qualified per-
sonnel are laid down in DIN VDE 0105 and
IEC 364.
Before assembling/setting up the micro-me-
tering products, the packaging material and
any shipping braces (e.g., plugs) must be re-
moved. The packaging material must be pre-
served until any discrepancies are resolved.
Note!
Do not tilt or drop the MDR lubricant
reservoir.
During all assembly work on machinery, ob-
serve the local accident prevention regulations
as well as the applicable operating and main-
tenance specifications.
Note!
The MDR lubricant reservoir, MDU
micro-metering unit, and the entire
MDS system must be vented carefully.
A feature of the MDS microdosage system is
its ease of use. However, careful commission-
ing is required for reliable operation. After the
system has been configured and put into op-
eration, the only necessary actions are routine
checks and any adjustments that may be nec-
essary.
Careful venting of the system is a very impor-
tant point of the commissioning. Small air
pockets can strongly affect the exact metered
quantity.
For correct commissioning, the MDR lubricant
reservoir, the MDU unit, and the main lubri-
cant line must be free of any air.
Utmost cleanliness must be maintained while
installing and commissioning the MDS system.
The oils used must be filtered; prescribed filter
rating </= 5µm.
The microdosage system should be assembled
and commissioned according to the following
sequence:
MDR lubricant reservoir(Chapter 4.3)
Attachment of MDR lubricant reservoir
o Install the lubricant reservoir
o Electrical connection, fill level control
o Initial filling and venting
o Connect compressed air connection

Page 20
EN Assembly instructions
The MDU micro-metering unit and the MDR
lubricant reservoir system should be protected
from humidity and mounted in a low-vibration
and easily accessible position, allowing all fur-
ther installation work to be done without dif-
ficulty.
Ensure that there is sufficient air circulation to
prevent excessive heating. For the maximum
permissible ambient temperature, see
“Technical data.”
Ensure adequate space for refilling the lubri-
cant reservoir (manual refilling).
Consult these assembly and operating
instructions for the technical data for
the MDR lubricant reservoir and the
MDU micro-metering unit.
These documents can also be down-
loaded from the homepage of SKF
Lubrication Systems Germany GmbH.
MDU micro-metering unit (Chapter 4.4)
Attachment of the micro-metering unit
o Electrical connection
o Capillary line connection
o Arrangement of capillary lines/
connection of lubrication points
Main lubricant line and venting (Chapter 4.5)
Information on preparing the bearings is con-
tained in Chapter 5 of the enclosed operating
instructions.
See also the setting options for the microdos-
age system in Chapter 6.
4.2 Setup and attachment
Note
Absolute cleanliness is required when
connecting the MDR, the MDU, the
main lubricant line, and the capillary
lines. Ensure that no dust particles
enter the metering system.
Warning!
Lubrication lines must always be free
of leaks. Lubricants can contaminate
soil and waterways. Lubricants must be
used and disposed of properly. Observe
the local regulations and laws regarding
the disposal of lubricants.
Danger!
Centralized lubrication systems must al-
ways be free of leaks. Leaking lubricant
is hazardous due to the risk of slipping
and injury. Beware of any lubricant
leaking out during assembly, operation,
maintenance, or repair of centralized
lubrication systems. Leaks must be
sealed off without delay.
Follow the safety instructions on the
lubricant's safety data sheet.
4.2.1 General information on
lubrication line arrangement
This manual suits for next models
1
Table of contents
Other SKF Control System manuals
Popular Control System manuals by other brands

BWO
BWO CONTROL SYSTEM 900 Hardware installation

HWH
HWH 200 series installation manual
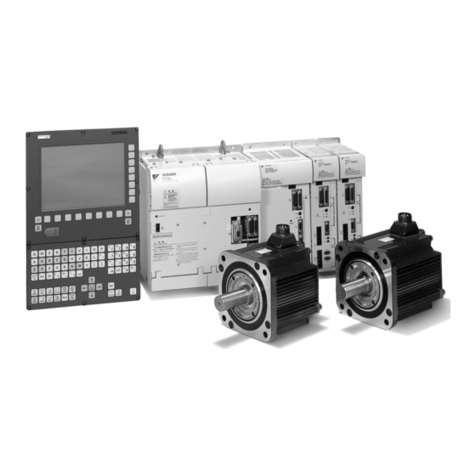
YASKAWA SIEMENS
YASKAWA SIEMENS CNC Series Maintenance Manual, Serviceman Handbook
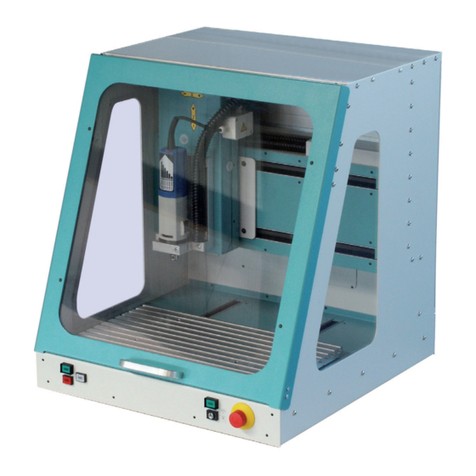
Isel
Isel ICP 4030 operating and maintaining instruction
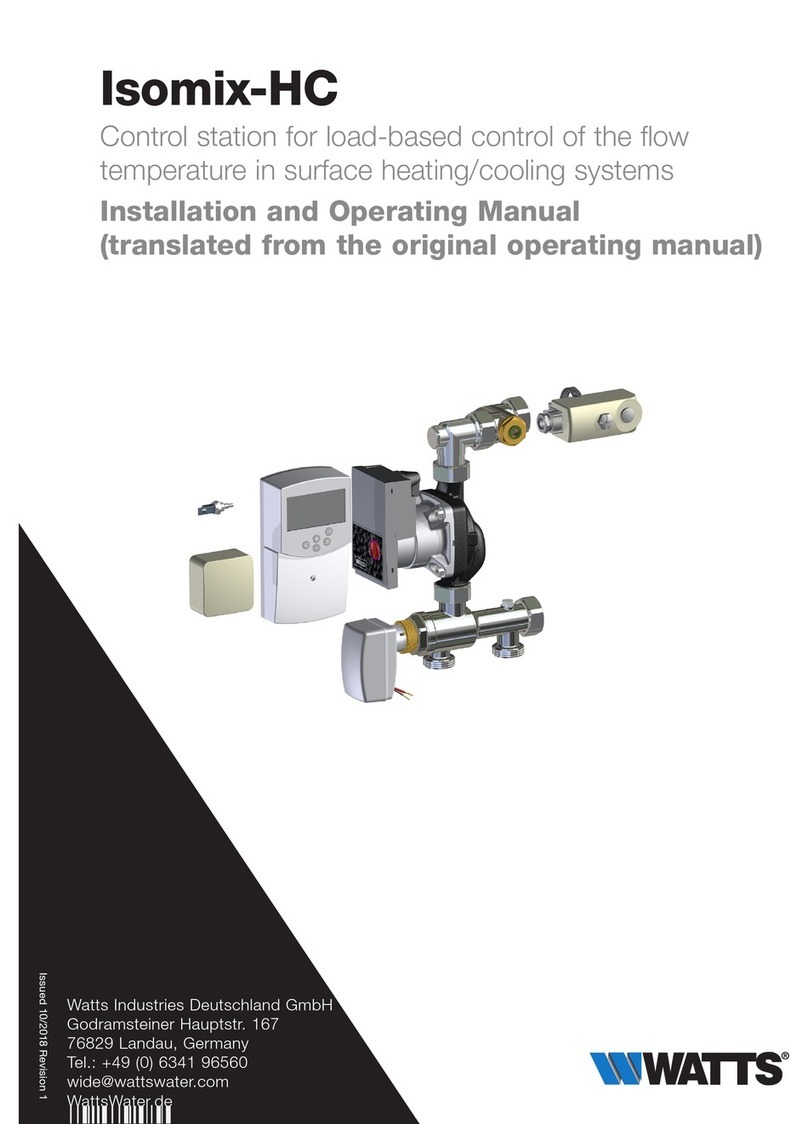
Watts Industries
Watts Industries Isomix-HC Installation and operating manual
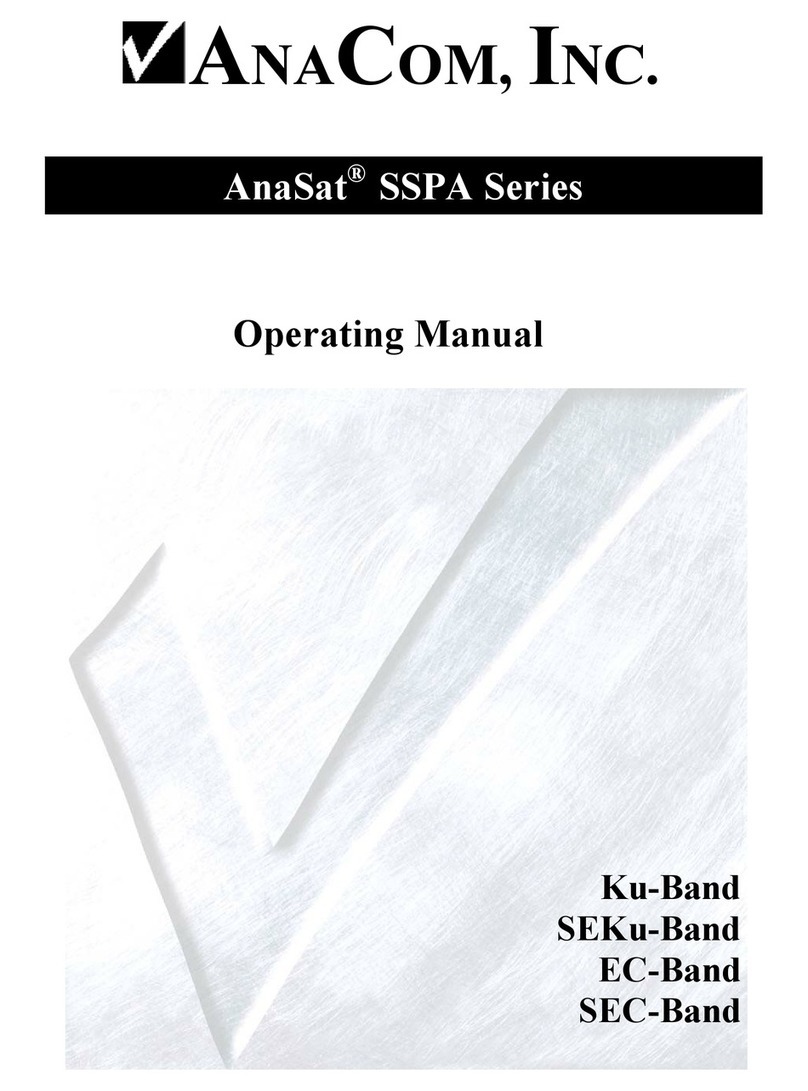
AnaCom
AnaCom AnaSat SSPA series operating manual