Smartrise C4 Installation and operation manual


Page intentionally left blank

Drive Startup Manual M1000
March 5, 2020 ©2020 Smartrise Engineering, Inc. All Rights Reserved Page i
Document History
Date Version Summary of Changes
October 23,2018
1.0
Initial Submittal
August 23, 2019
2.0
Changed cover page
New document format
Added secondary brake wiring
November 4, 2019
3.0
Added tuning steps
March 5, 2020
4.0
Updated Construction procedure to include the run
box must be set to ON

Drive Startup Manual M1000
Page ii © 2020 Smartrise Engineering, Inc. All Rights Reserved March 5, 2020
Page intentionally left blank

Drive Startup Manual M1000
March 5, 2020 ©2020 Smartrise Engineering, Inc. All Rights Reserved Page iii
Table of Contents
M1000 Drive ...........................................................................................................1
Equipment/Settings Verification..............................................................................1
Grounding Requirements ........................................................................................2
Wiring .....................................................................................................................3
Power .................................................................................................................................... 3
Brake .................................................................................................................................... 3
Motor / Encoder ..................................................................................................................... 3
Construction ........................................................................................................................... 4
Powering Up ...........................................................................................................6
Closed Loop Induction Motor Quick Start-Up Guide................................................6
Induction Motor Key Drive Parameters ...................................................................7
Closed Loop Permanent Magnet Quick Startup Guide...........................................10
Induction Motor Key Drive Parameters .................................................................11
Operation..............................................................................................................14
No Faults ...............................................................................................................................14
Proper Direction ....................................................................................................................15
Brake Not Lifting ....................................................................................................................15
Appendix...............................................................................................................16

Drive Startup Manual M1000
Page iv © 2020 Smartrise Engineering, Inc. All Rights Reserved March 5, 2020
List of Figures
Figure 1: M1000 Drive ...................................................................................................................................................1
Figure 2: Example of Parameter Table ..........................................................................................................................1
Figure 3: Ground Bus Terminal......................................................................................................................................2
Figure 4: Example of Construction Wiring.....................................................................................................................5
Figure 5: Breakers ..........................................................................................................................................................6
Figure 6: Terminal Locations........................................................................................................................................16

Drive Startup Manual M1000
March 5, 2020 ©2020 Smartrise Engineering, Inc. All Rights Reserved Page v
List of Tables
Table 1: Wiring References for Common Encoders.......................................................................................................3
Table 2: Parameters for A1 Drive ..................................................................................................................................7
Table 3: Parameters for A4 Power Convert ...................................................................................................................8
Table 4: Parameters for A5 Motor.................................................................................................................................8
Table 5: Parameters for C1 User Switches.....................................................................................................................9
Table 6: Parameters for U8 Basic...................................................................................................................................9
Table 7: Parameters for U9 Autotune .........................................................................................................................10
Table 8: Parameters for A1 Drive ................................................................................................................................11
Table 9: Parameters for A4 Power Convert .................................................................................................................12
Table 10: Parameters for A5 Motor.............................................................................................................................12
Table 11: Parameters for C1 User Switches.................................................................................................................13
Table 12: Parameters for U8 Basic...............................................................................................................................14
Table 13: Parameters for U9 Autotune .......................................................................................................................14

Drive Startup Manual M1000
Page vi © 2020 Smartrise Engineering, Inc. All Rights Reserved March 5, 2020
Page intentionally left blank

Drive Startup Manual M1000
March 5, 2020 ©2020 Smartrise Engineering, Inc. All Rights Reserved Page 1
M1000 Drive
The M1000 drive is an AC drive.
Figure 1: M1000 Drive
Equipment/Settings Verification
Set and verify the equipment matches the job specific parameters for proper operation. See the
C4 Controller sheet 01 Getting Started Parameter Table for more information.
Figure 2: Example of Parameter Table

Drive Startup Manual M1000
Page 2 © 2020 Smartrise Engineering, Inc. All Rights Reserved March 5, 2020
Grounding Requirements
NOTE: A proper and effective building ground connection is required for the safe and successful
operation of the controller.
Examples of a proper building-to-controller ground is as follows:
Attach the ground wire to the street side of a water main.
Attach the ground wire to a grounding rod in the pit.
The controller has a common ground bus terminal connection.
Figure 3: Ground Bus Terminal
•The building, motor, transformer, and filter(s) must all share a common ground. This
removes ground loops, limits impedance, and routes noise into the ground.

Drive Startup Manual M1000
March 5, 2020 ©2020 Smartrise Engineering, Inc. All Rights Reserved Page 3
Wiring
A checklist must be completed during the drive wiring process. See Appendix for terminal
locations.
Power
Perform the following to connect power. See the C4 Controller sheet 03 Machine Room for job
specific information.
•Connect main line power to terminal blocks L1/L2/L3.
•Connect the ground wire to the yellow/green terminal block next to L1-L3.
Brake
Perform the following to connect the brakes. See the C4 Controller sheet 5 Brakes for job
specific information.
•Connect the main brake wiring to terminal K1 / K2 and the secondary brake wiring (if
equipped) to terminals J1 / J2 located on the terminal block next to the M Contactor.
Motor / Encoder
Perform the following to connect the drive to the motor and encoder cable. See the C4
Controller sheet 04 Drive and Motor for job specific information.
•Connect motor leads to the M contactor at T1/T2/T3.
•Connect the encoder cable, if applicable, to the PG card located under the top cover.
The table below lists the Terminal Descriptions. Record the encoder wiring color code for future
release.
Table 1: Wiring References for Common Encoders
Encoder Drive Hollister
Whitney Heidenhain Torin ECN413 Zeihl
PWR
IP
Brown
Green/Blue + Brown
Red/Pink
Gary/Green
COM
IG
White
Green/White + White
Black + Red/White
Pink/Yellow
A
A+
Green
Green/Black
Green + Black
Gray/Pink
/A
A-
Yellow
Yellow/Black
Yellow + Black
Red/Blue
B
B+
Blue
Blue/Black
Blue + Black
Blue
/B
B-
Red
Red/Black
Red + Black
Red
Z
/Z
CLOCK+ CK Black Gray Gray White
CLOCK- CK
Violet
Pink
Clear OR Silver
Brown

Drive Startup Manual M1000
Page 4 © 2020 Smartrise Engineering, Inc. All Rights Reserved March 5, 2020
Encoder Drive Hollister
Whitney Heidenhain Torin ECN413 Zeihl
DATA+
DT
Gray
Violet
Purple
Violet
DATA-
DT
Pink
Yellow
White
Black
SHIELD
FE
Shield
Shield
Large Red
Shield
Construction
All safety inputs are functional during Construction mode on the C4 product. When these safety
devices are installed, they are connected per the C4 Controller sheet 02 Machine Room I/O of
the prints, even if still on Construction mode. The following includes instructions for when none
of these devices have been installed prior to beginning on Construction mode.
Perform the following to wire the Construction Box. See the C4 Controller sheet 01 – Getting
Started for job specific information.
Connect a jumper from L120 to terminals LFT, LFM, and LFB.
a. If rear doors are used, connect LRT, LRM, and LRB.
Connect a jumper from H120 to PIT, BUF, BFL, and TFL.
If secondary brake is present, connect M120 to SFM.
Connect H120 through your machine room Run/Stop switch and connect it to SFH. A
closed switch indicates run; an open switch indicates stop. If no Run/Stop switch is being
used, connect H120 to SFH.
Connect your run bug. Wire the Up button to input CUP and the Down to input CDN.
Wire the Enable to CEN, jump high if not available.
a. If no run bug is being used, leave the inputs unwired.
Enable Run box by setting the option in Setup |Miscellaneous | Enable Const. Box to
ON.
NOTE: When this option is ON, the onboard inspection buttons are disabled.
Connect a jumper from 24VDC to MM.
Verify the Car Door Bypass and Hoistway Bypass switches are in the OFF position.
Place the Inspection switch to INSPECTION.

Drive Startup Manual M1000
March 5, 2020 ©2020 Smartrise Engineering, Inc. All Rights Reserved Page 5
Figure 4: Example of Construction Wiring

Drive Startup Manual M1000
Page 6 © 2020 Smartrise Engineering, Inc. All Rights Reserved March 5, 2020
Powering Up
Perform the following to power up the drive.
Apply external power by closing the main disconnect.
Close the two-pole breaker and all pushbutton breakers.
Verify the LCD on the Smartrise board and the Magnetek Drive powers up.
Figure 5: Breakers
Closed Loop Induction Motor Quick Start-Up Guide
This quick start-up guide outlines the general parameters that must be changed/verified when a
drive is installed with information that is readily available. The drive will not run if ONLY these
parameters are set. Because different elevator controller manufacturers have different
interfaces, it is recommended that the parameters in the drive be set to the settings
recommended by the elevator controller in the drive technical documentation.
The following are the start-up steps.
Set/verify that the drive is set up to run in Closed Loop Vector for Control Method (U8).
Verify that the drive has an Encoder board.
NOTE: The PG-X3 is the most common card used for closed-loop induction motors. See
the Magnetek M1000 AC Elevator Drive for the PG-X3 Option Card encoder setup.
Set / verify that the hoistway parameters are set up properly.
•The Contract Car Speed (A1) should be set to the elevator contract speed in ft/min.
•The Contract Mtr Speed (A1) should be set to an RPM where the elevator contract
speed can be achieved (measured with a hand tachometer).
Set / verify that the Input Voltage (A4) is the same as the measured incoming voltage.

Drive Startup Manual M1000
March 5, 2020 ©2020 Smartrise Engineering, Inc. All Rights Reserved Page 7
Perform the U9 Autotune.
•Perform the “Tune-No Rotate1” for Tuning Mode Sel (U9).
•Enter the motor nameplate HP
•Enter the motor nameplate voltage
•Enter the motor nameplate current
•Enter the motor nameplate frequency
•Enter the motor poles
•Enter the nameplate rated speed (where slip is incorporated in)
•Enter the encoder PPR
•Leave the pre-calculated default for no-load current unless the no-load
current is printed on the nameplate
•BEGIN ALIGNMENT to Yes but DON’T PRESS THE ENTER BUTTON.
•Turn on DIP 6A. The M contactor automatically engages, and the screen displays
TUNE command. Press the Enter Button on the drive to start the alignment.
Did the Tune-No Rotate1 (U9) pass?
a. If the Tune-No Rotate1 (U9) did not pass, go to step 7.
b. If the Tune-No Rotate1 (U9) passed, turn off DIP 6A and the process ends.
If you are running on construction/inspection and run into the following:
•If the motor is running slowly/uncontrolled and drawing high current:
•Swap Encoder Connect (C1)
•Verify that the encoder is working
•If the elevator is running at controlled/proper speed but in the opposite direction of
what it is being told:
•Swap both the Encoder Connect (C1) and Motor Rotation (C1). Go to step 5.
Induction Motor Key Drive Parameters
The table below lists the Parameters for A1 Drive.
Table 2: Parameters for A1 Drive
Parameter Description Default Units Suggested Adjustments
Contract
Car Spd
Elevator contract
speed
400
fpm
Set to the speed the elevator will be
certified at.
Contract
Mtr Spd
Rotational motor
shaft speed that
makes the
elevator run at
contract speed
1130
RPM
Adjust this value to ensure the actual
running speed of the elevator matches the
contract car speed. If the elevator is
traveling too fast, lower the value. If the
elevator is traveling too slow, increase the
value.
NOTE: A power cycle may be required for
this to have an effect.

Drive Startup Manual M1000
Page 8 © 2020 Smartrise Engineering, Inc. All Rights Reserved March 5, 2020
Parameter Description Default Units Suggested Adjustments
Response
Sets the
sensitivity of the
speed regulator
10.0
Normally, the default of 10 is used. An
increase to 20 will make the drive more
responsive. Too low of a value causes the
drive to have sluggish responsiveness.
Inertia
System inertia
2.00
sec
Normally, the default of 2 is used.
Encoder
Pulses
Encoder's pulses
per revolution
1024
PPR
Set this to match the encoder nameplate
PPR.
Mtr
Torque
Limit
Sets the
maximum
motoring torque
the drive can
produce
200
%
It is recommended to set this to 250%.
Regen
Torq Limit
Sets the
maximum
regenerative
torque the drive
can produce
200
%
It is recommended to set this to 250%.
The table below lists the Parameters for A4 Power Convert.
Table 3: Parameters for A4 Power Convert
Parameter Description Default Units Suggested Adjustments
Input
Voltage
Nominal line-to-
line AC input
voltage in RMS
Per
drive
model
VAC Set the input voltage to match the
measured voltage across R, S, and T.
The table below lists the Parameters for A5 Motor.
Table 4: Parameters for A5 Motor
Parameter Description Default Units Suggested Adjustments
Mtr Rated
Power
Motor rated
output power on
the nameplate
Per
drive
model
HP
This parameter should be set to match the
motor nameplate power. This parameter is
automatically populated after a successful
U9 AUTOTUNE.
Mtr Rated
Voltage
Motor rated
voltage on the
nameplate
Per
drive
model
VAC This parameter should be set to match the
motor nameplate voltage. This parameter
is automatically populated after a
successful U9 AUTOTUNE.
Max
Frequency
Motor rated
frequency on the
nameplate
60
Hz
This parameter should be set to match the
motor nameplate frequency.
This parameter is automatically populated
after a successful U9 AUTOTUNE.
Motor
Rated FLA
Motor rated
current on the
nameplate
Per
drive
model
A
This parameter should be set to match the
motor nameplate current. This parameter

Drive Startup Manual M1000
March 5, 2020 ©2020 Smartrise Engineering, Inc. All Rights Reserved Page 9
Parameter Description Default Units Suggested Adjustments
is automatically populated after a
successful U9 AUTOTUNE.
Number of
Poles
Number of poles
the motor has
4
--
This parameter should be set to match the
number of poles inside the motor. This
parameter is automatically populated
after a successful U9 AUTOTUNE.
Motor
Rated Slip
Slip frequency of
the motor
Per
drive
model
Hz
It is recommended that this setting be
determined by a U9 AUTOTUNE.
No-Load
Current
Magnetizing
current of the
motor
Per
drive
model
A
It is recommended that this setting be
determined by a U9 AUTOTUNE.
Leak
Inductance
Inductance of the
motor
Per
drive
model
%
It is recommended that this setting be
determined by a U9 AUTOTUNE.
Term
Resistance
Resistance of the
motor
Per
drive
model
∧
It is recommended that this setting be
determined by a U9 AUTOTUNE.
The table below lists the Parameters for C1 User Switches.
Table 5: Parameters for C1 User Switches
Parameter Description Default Units Suggested Adjustments
Motor
Rotation
Rotation of the
motor that the
drive interprets
as up or down
Forward Forward
Reverse
If the elevator is running controlled
but in the wrong direction, swap BOTH
this parameter and Encoder Connect.
The table below lists the Parameters for U8 Basic.
Table 6: Parameters for U8 Basic
Parameter Description Default Units Suggested Adjustments
Control
Method
Sets the type of
motor control
technique
Closed
Loop Vect
Closed Loop
Open Loop Vector
PM ClosedLoopVct
V/f Control
Set this parameter to
Closed Loop Vect.

Drive Startup Manual M1000
Page 10 © 2020 Smartrise Engineering, Inc. All Rights Reserved March 5, 2020
The table below lists the Parameters for U9 Autotune.
Table 7: Parameters for U9 Autotune
Parameter Description Default Units Suggested Adjustments
Tuning
Mode
Sel
Sets the type of
autotuning the
drive performs
TuneNo
Rotate1
Standard Tuning
Tune-No Rotate1
Term Resistance
Tune-No Rotate2
For convenience, it is
recommended that the
Tune-No Rotate1 is
performed.
Closed Loop Permanent Magnet Quick Startup Guide
This quick startup guide outlines the general parameters that must be changed/verified when a
drive is installed with information that is readily available. The drive will not run if ONLY these
parameters are set. Because different elevator controller manufacturers have different
interfaces, it is recommended that the parameters in the drive be set to the settings
recommended by the elevator controller in the drive technical documentation.
The following are the startup steps
Set / verify that the drive is set up to run in PM ClosedLoopVCT for Control Method (U8).
Verify that the drive has an encoder board.
NOTE: The PG-X3 is the most common card used for closed-loop permanent magnet
motors. See the Magnetek M1000 AC Elevator Drive for the PG-X3 Option Card encoder
setup.
Set/verify that the hoistway parameters are set up properly:
•The Contract Car Speed (A1) should be set to the elevator contract speed in ft/min.
•The Contract Mtr Speed (A1) should be set to an RPM where the elevator contract
speed can be achieved (measured with a hand tachometer).
Set / verify that the Input Voltage (A4) is the same as the measured incoming voltage.
Perform the U9 Autotune.
•Perform the “Tune-No Rotate1” for Tuning Mode Sel (U9).
•Enter the motor nameplate HP
•Enter the motor nameplate voltage
•Enter the motor nameplate current
•Enter the motor nameplate frequency
•Enter the motor poles
•Enter the nameplate rated speed (where slip is incorporated in)
•Enter the encoder PPR
•BEGIN ALIGNMENT to Yes but DON’T PRESS THE ENTER BUTTON.
•Turn on DIP 6A. The M contactor automatically engages, and the screen displays
TUNE command. Press the Enter Button on the drive to start the alignment.

Drive Startup Manual M1000
March 5, 2020 ©2020 Smartrise Engineering, Inc. All Rights Reserved Page 11
Perform the InitPoleEstPrms for PM Tuning Mode (U9).
•BEGIN ALIGNMENT to Yes but DON’T PRESS THE ENTER BUTTON.
•Turn on DIP 6A. The M contactor automatically engages, and the screen displays
TUNE command. Press the Enter Button on the drive to start the alignment.
NOTE: If this fails with an angle deviation fault, a non-rotational alignment should not be
performed.
Did the InitPoleEstPrms for PM Tuning Mode (U9) fail for angle deviation?
a. If the InitPoleEstPrms for PM Tuning Mode (U9) fail for angle deviation, see the
Magnetek M1000 AC Elevator Drive for PM Autotune then go to step 9.
b. If the InitPoleEstPrms for PM Tuning Mode (U9) did not fail angle deviation, turn off
DIP 6A and go to step 8.
Perform the PolePos-norotate for PM Tuning Mode (U9).
•BEGIN ALIGNMENT to Yes but DON’T PRESS THE ENTER BUTTON.
•Turn on DIP 6A. The M contactor automatically engages, and the screen displays
TUNE command. Press the Enter Button on the drive to start the alignment.
Did the PolePos-norotate for PM Tuning Mode (U9) pass?
a. If the PolePos-norotate for PM Tuning Mode (U9) did not pass, go to step 10.
b. If the PolePos-norotate for PM Tuning Mode (U9) passed, turn off DIP 6A and the
process ends.
If you are running on construction/inspection and run into the following:
•If the motor is running slowly/uncontrolled and drawing high current:
•Swap Encoder Connect (C1)
•Verify that the encoder is working
•If the elevator is running at controlled/proper speed but in the opposite direction of
what it is being told:
•Swap both the Encoder Connect (C1) and Motor Rotation (C1). Go to step 8.
Induction Motor Key Drive Parameters
The table below lists the Parameters for the A1 Drive.
Table 8: Parameters for A1 Drive
Parameter Description Default Units Suggested Adjustments
Contract
Car Spd
Elevator contract
speed
400
fpm
Set to the speed the elevator will be
certified at.

Drive Startup Manual M1000
Page 12 © 2020 Smartrise Engineering, Inc. All Rights Reserved March 5, 2020
Parameter Description Default Units Suggested Adjustments
Contract
Mtr Spd
Rotational motor
shaft speed that
makes the elevator
run at contract speed
1130
RPM
Adjust this value to ensure the actual
running speed of the elevator matches
the contract car speed. If the elevator is
traveling too fast, lower the value. If
the elevator is traveling too slow,
increase the value.
NOTE: A power cycle may be required
for this to have an effect.
Response Sets the sensitivity of
the speed regulator
10.0 Normally, the default of 10 is used. An
increase to 20 makes the drive more
responsive. Too low of a value causes
the drive to have sluggish
responsiveness.
Inertia
System inertia
2.00
sec
Normally, the default of 2 is used.
Encoder
Pulses
Encoder's pulses per
revolution
1024
PPR
Set this to match the encoder
nameplate PPR.
Mtr
Torque
Limit
Sets the maximum
motoring torque the
drive can produce
200 % It is recommended to set this to 250%.
Regen
Torq Limit
Sets the maximum
regenerative torque
the drive can produce
200
%
It is recommended to set this to 250%.
The table below lists the Parameters for A4 Power Convert.
Table 9: Parameters for A4 Power Convert
Parameter Description Default Units Suggested Adjustments
Input
Voltage
Nominal line-to-
line AC input
voltage in RMS.
Per
drive
model
VAC
Set the input voltage to match the
measured voltage across R, S, and T.
The table below lists the Parameters for A5 Motor.
Table 10: Parameters for A5 Motor
Parameter Description Default Units Suggested Adjustments
PM Mtr
Power
Motor rated
output power on
the nameplate
Per
drive
model
HP
This parameter should be set to match the
motor nameplate power. This parameter is
automatically populated after a successful
U9 AUTOTUNE.
Mtr Rated
Voltage
Motor rated
voltage on the
nameplate
Per
drive
model
VAC
This parameter should be set to match the
motor nameplate voltage. This parameter
is automatically populated after a
successful U9 AUTOTUNE.
Other manuals for C4
5
This manual suits for next models
1
Table of contents
Other Smartrise DC Drive manuals
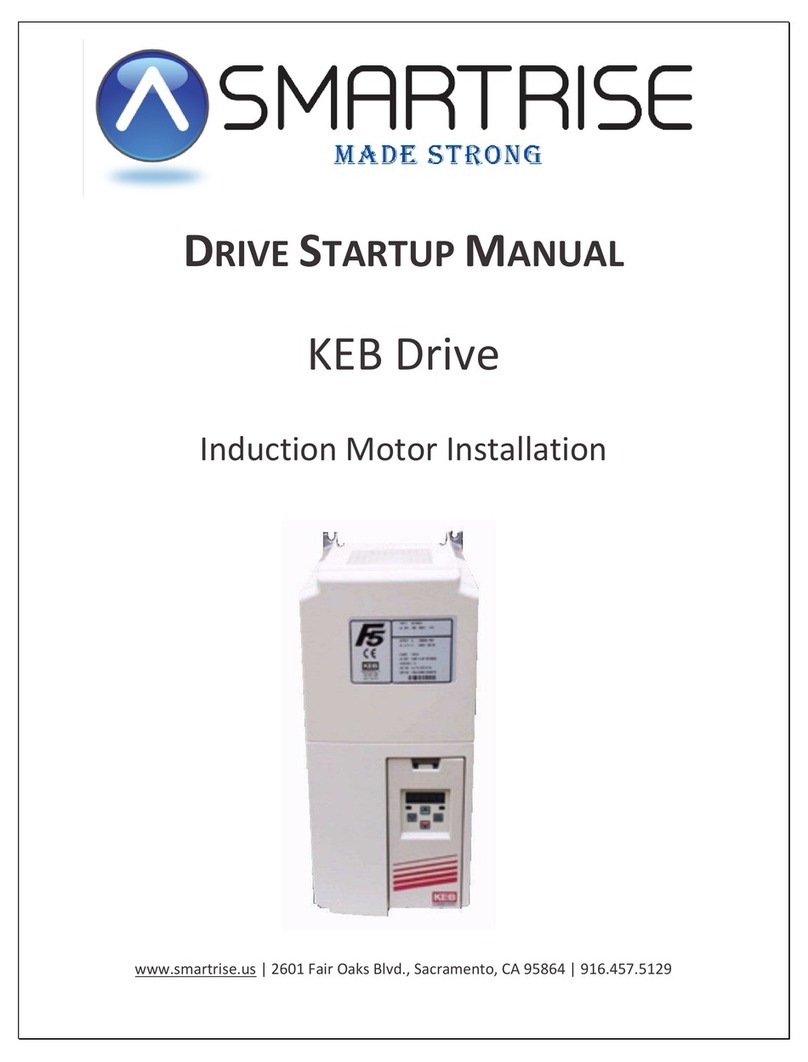
Smartrise
Smartrise KEB Series Installation and operation manual

Smartrise
Smartrise KEB-Induction Installation and operation manual
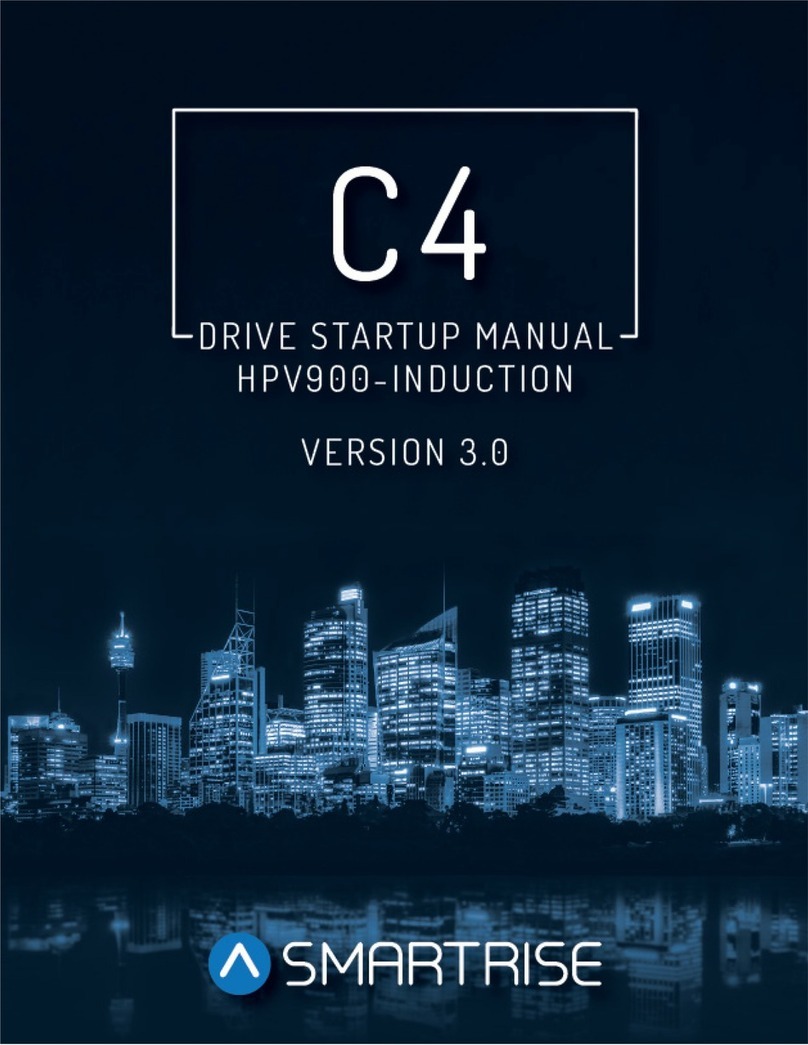
Smartrise
Smartrise HPV900 Installation and operation manual
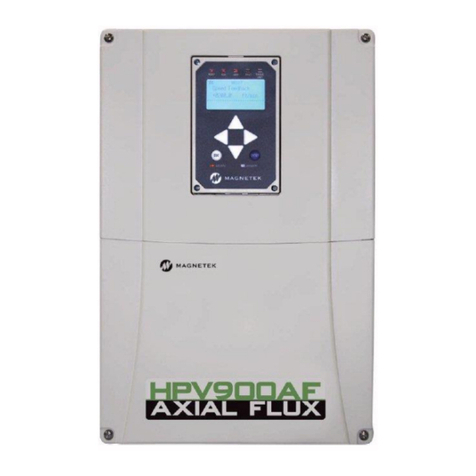
Smartrise
Smartrise Magnetek HPV900AF Installation and operation manual
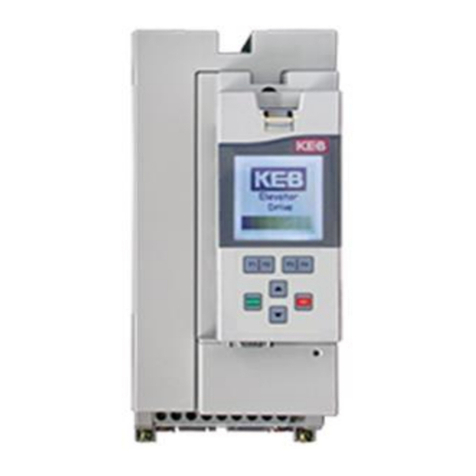
Smartrise
Smartrise KEB-PM Installation and operation manual
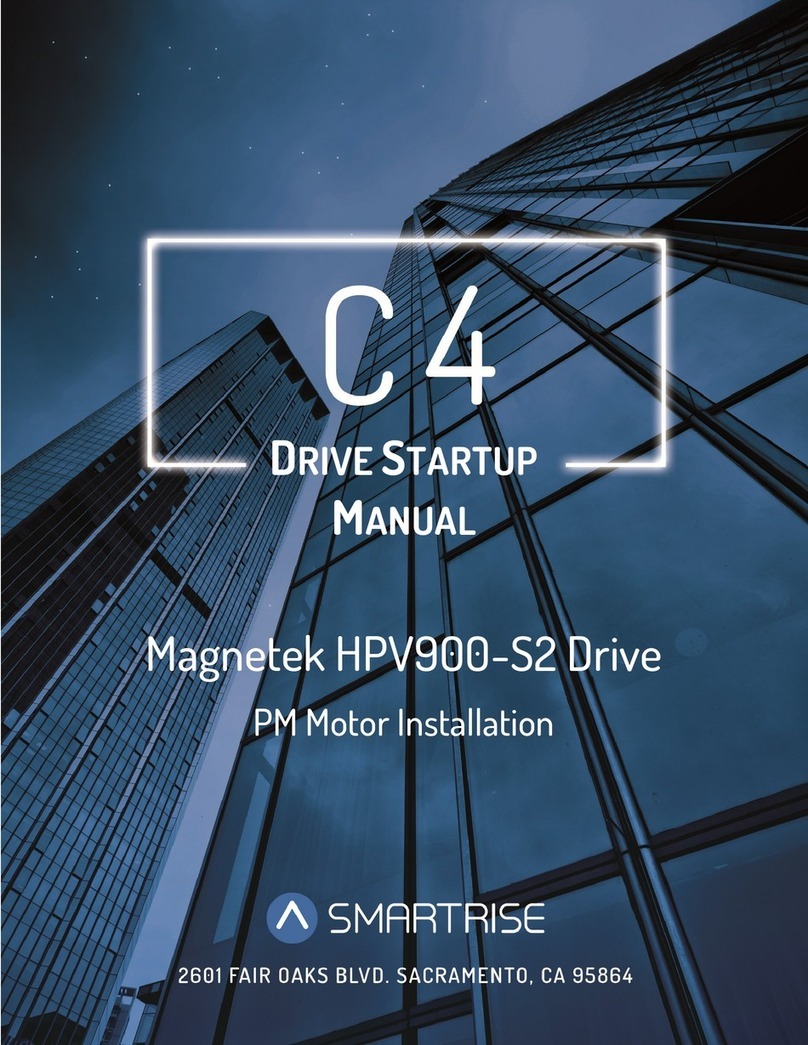
Smartrise
Smartrise HPV900-S2 Installation and operation manual
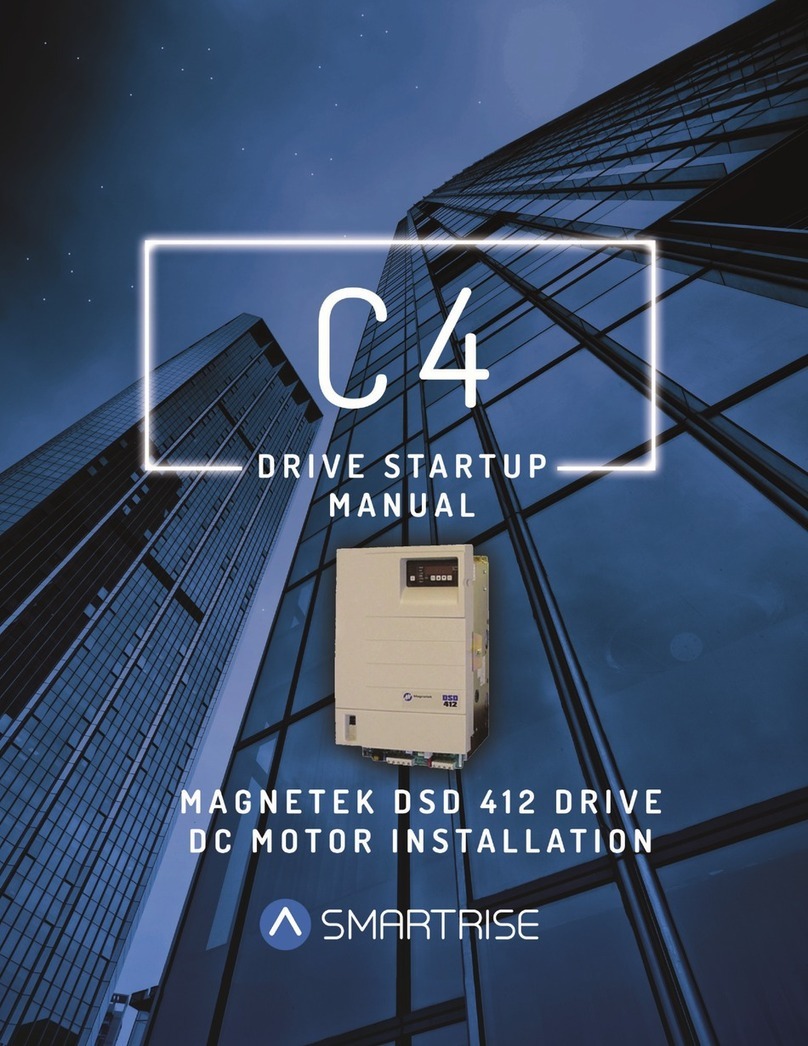
Smartrise
Smartrise C4 Installation and operation manual
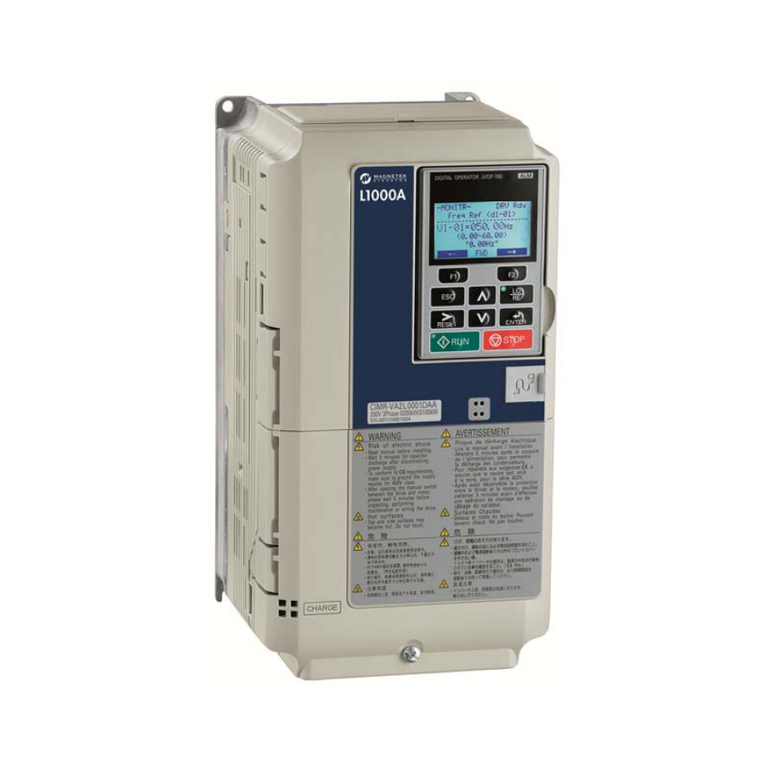
Smartrise
Smartrise Magnetek L1000A Installation and operation manual
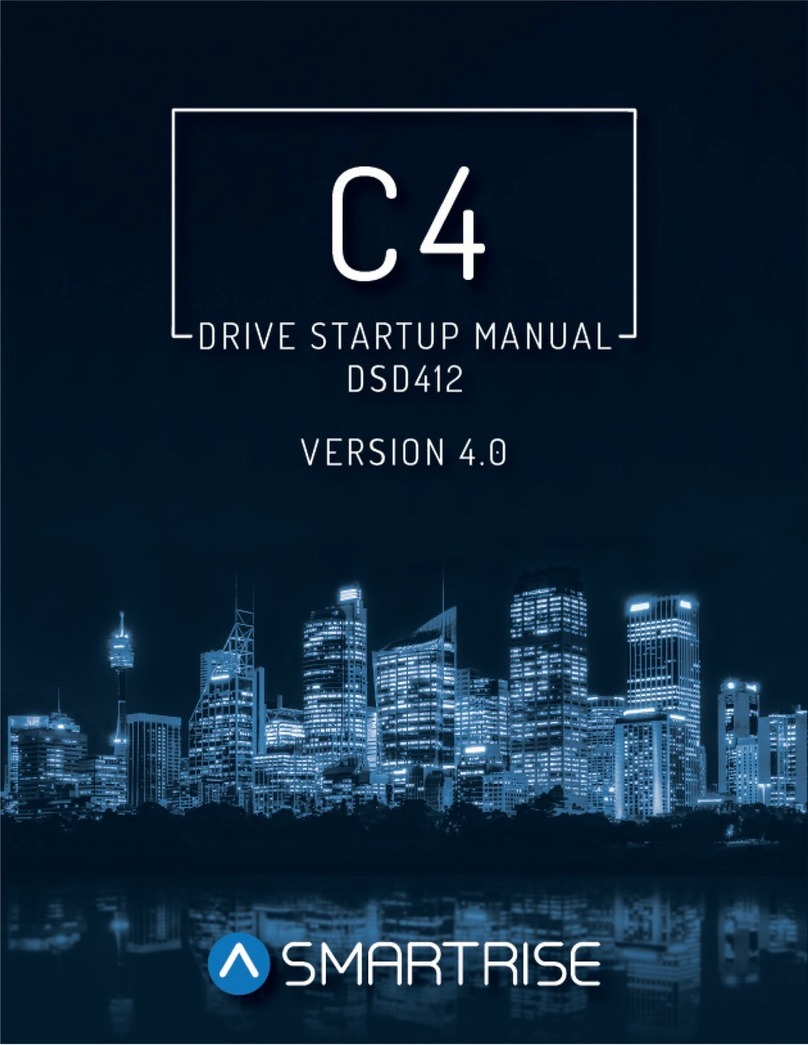
Smartrise
Smartrise DSD412 Installation and operation manual

Smartrise
Smartrise KEB-Induction Installation and operation manual