Smartrise HPV900-PM Installation and operation manual



Drive Startup Manual HPV900-PM
December 17, 2019 ©2019 Smartrise Engineering, Inc. All Rights Reserved Page i
Document History
Date
Version
Summary of Changes
October 23,2018
1.0
Initial Submittal
December 17, 2019
2.0
Changed cover page
New document format
Reworked display screen shots to display as viewed
Expanded on step by step procedures
Replaced Construction section to include wiring to
the CXN board

Drive Startup Manual HPV900-PM
Page ii © 2019 Smartrise Engineering, Inc. All Rights Reserved December 17, 2019
Page intentionally left blank

Drive Startup Manual HPV900-PM
December 17, 2019 ©2019 Smartrise Engineering, Inc. All Rights Reserved Page iii
Table of Contents
HPV900-S2 PM Drive...............................................................................................1
Equipment/Settings Verification..............................................................................1
Magnetek Parameter Location Reference ............................................................................... 2
Grounding Requirements ........................................................................................3
Wiring .....................................................................................................................3
Power .................................................................................................................................... 3
Brake .................................................................................................................................... 4
Motor / Encoder ..................................................................................................................... 4
Construction ........................................................................................................................... 5
Powering Up ...........................................................................................................6
Final Setup ..............................................................................................................7
Auto Tuning ............................................................................................................9
Motor Alignment .................................................................................................................... 9
Encoder Alignment (Non-Rotational)....................................................................................... 9
Operation..............................................................................................................11
No Faults ...............................................................................................................................11
Proper Direction ....................................................................................................................11
At Speed ................................................................................................................................11
Under Control........................................................................................................................11
Troubleshooting....................................................................................................11
Drive Fault/Encoder Fault.......................................................................................................11
Brake Not Lifting ....................................................................................................................12
Wrong Direction ....................................................................................................................12
Car Moving to Slow or Rough .................................................................................................12
Setup Fault One .....................................................................................................................12
Appendix...............................................................................................................13

Drive Startup Manual HPV900-PM
Page iv © 2019 Smartrise Engineering, Inc. All Rights Reserved December 17, 2019
List of Figures
Figure 1: HPV900-S2 PM Drive ......................................................................................................................................1
Figure 2: Example of Parameter Table ..........................................................................................................................1
Figure 3: Ground Bus Terminal......................................................................................................................................3
Figure 4: Example of Construction Wiring.....................................................................................................................6
Figure 5: Breakers..........................................................................................................................................................7
Figure 6: MAIN MENU –Setup ......................................................................................................................................7
Figure 7: SETUP Menu –Misc........................................................................................................................................8
Figure 8: MISC Menu –Bypass Term Limits...................................................................................................................8
Figure 9: Bypass Term Limits Menu –NO......................................................................................................................8
Figure 10: Bypass Term Limits Menu –YES ...................................................................................................................8
Figure 11: Main Line Connections ...............................................................................................................................13
Figure 12: EnDat Card..................................................................................................................................................14

Drive Startup Manual HPV900-PM
December 17, 2019 ©2019 Smartrise Engineering, Inc. All Rights Reserved Page v
List of Tables
Table 1: Wiring References for Common Encoders.......................................................................................................4
Table 2: Parameters for BASICS U9 .............................................................................................................................10
Table 3: Parameters for AUTOTUNE SEL U12 ..............................................................................................................10
Table 4: Parameters for ROTOR ALIGN U10 ................................................................................................................10
Table 5: Parameters for DRIVE INFO U6......................................................................................................................10

Drive Startup Manual HPV900-PM
Page vi © 2019 Smartrise Engineering, Inc. All Rights Reserved December 17, 2019
Page intentionally left blank

Drive Startup Manual HPV900-PM
December 17, 2019 ©2019 Smartrise Engineering, Inc. All Rights Reserved Page 1
HPV900-S2 PM Drive
The HPV900-S2 drive is a permanent magnet AC drive.
Figure 1: HPV900-S2 PM Drive
Equipment/Settings Verification
Set and verify the equipment matches the job specific parameters for proper operation. See V2
Controller sheet 01 Getting Started Parameter Table for more information.
Figure 2: Example of Parameter Table

Drive Startup Manual HPV900-PM
Page 2 © 2019 Smartrise Engineering, Inc. All Rights Reserved December 17, 2019
Magnetek Parameter Location Reference
Adjust A0
•Drive A1
•Encoder Pulses (Encoder PPR –1024/2048)
•Power Convert –A4
•Input L-L Volts
•Motor –A5
•Rated Mtr Power (Kw)
•Rated Mtr Volts (VAC)
•Rated Exit Freq (60Hz)
•Rated Motor Curr (FLA –Amps)
•Motor Poles
•Rated Mtr Speed (RPM)
Configure C0
•User Switches –C1
•Motor Rotation
•Forward/Reverse
•Encoder Connect
•Forward/Reverse

Drive Startup Manual HPV900-PM
December 17, 2019 ©2019 Smartrise Engineering, Inc. All Rights Reserved Page 3
Grounding Requirements
NOTE: A proper and effective building ground connection is required for the safe and successful
operation of the controller.
Examples of a proper building-to-controller ground is as follows:
1. Attach the ground wire to the street side of a water main.
2. Attach the ground wire to a grounding rod in the pit.
The controller has a common ground bus terminal connection.
Figure 3: Ground Bus Terminal
•The building, motor, transformer, and filter(s) must all share a common ground. This
removes ground loops, limits impedance, and routes noise into the ground.
Wiring
A checklist must be completed during the drive wiring process. See Appendix for terminal
location.
Power
Perform the following to connect power. See V2 Controller sheet 03 Machine Room for job
specific information.
•Connect main line power to terminal blocks L1/L2/L3.
•Connect the ground wire to the yellow/green terminal block next to L1-L3.

Drive Startup Manual HPV900-PM
Page 4 © 2019 Smartrise Engineering, Inc. All Rights Reserved December 17, 2019
Brake
Perform the following to connect the brakes. See V2 Controller sheet 05 Brakes for job specific
information.
•Connect the main brake wiring to terminal K1/K2 and the secondary brake wiring (if
equipped) to terminals J1/J2 located on the terminal block next to the M Contactor.
•Jump EB to the terminal on Construction Box and connect either the rope gripper or
sheave brake to EBR (if installed). See V2 Controller sheet 01 Getting Started for more
information.
Motor / Encoder
Perform the following to connect the drive to the motor and encoder cable. See V2 Controller
sheet 04 Motor and Drive Connections for job specific information.
•Connect motor leads to the M contactor at T1/T2/T3.
•Connect the encoder cable to the drive terminal block TB1. See Figure 12.
The table below lists the Wiring References for Common Encoders. Record the encoder wire
color code for future release.
Table 1: Wiring References for Common Encoders
Encoder
Endat
Termination
Black
Heidenhain
Ziehl
Green
Encoder
Cable
Torin
Encoder
Cable
On-Site
Color
/A
A-
TB2-1
Yellow and
Black
Red and
Blue
Yellow
Brown
A
A+
TB2-2
Green and
Black
Gray and
Pink
Green
Green
/B
B-
TB2-3
Red and
Black
Red
Red
Yellow
B
B+
TB2-4
Blue and
Black
Blue
Blue
Blue
/DATA
DAT-
TB2-5
Pink
Brown
Pink
Silver
DATA
DAT+
TB2-6
Gray
White
Gray
Gray
/CLOCK
CLK-
TB2-7
Yellow
Black
Violet
White
CLOCK
CLK+
TB2-8
Violet
Violet
Black
Violet
0V com
COM
TB2-9
Green and
White
Pink
White
Black/Red
and
White
+5V
+5V
TB2-10
Green and
Brown
Gray
Brown
Red and
Pink

Drive Startup Manual HPV900-PM
December 17, 2019 ©2019 Smartrise Engineering, Inc. All Rights Reserved Page 5
Encoder
Endat
Termination
Black
Heidenhain
Ziehl
Green
Encoder
Cable
Torin
Encoder
Cable
On-Site
Color
0V Sense (If
Present)
SEN-
TB2-11
White
Yellow
+5V Sense (If
Present)
SEN+
TB2-12
Blue
Green
Cable Shield
Shield
TB2-13
Encoder
Cable
Shield
Encoder
Cable
Shield
Encoder
Cable
Shield
Red
EnDat Board
Ground
(Magnetek
GRN factory
wire tied to
ground stud)
Shield
TB2-13
Construction
Perform the following to wire the Construction box. See V2 Controller sheet 01 Getting Started
for job specific information.
1. Install jumpers between M24 and Input/Output (IO)as per print.
2. Using an external run box?
a. If using an external run box, go to step 3.
b. If not using an external run box, go to step 5.
3. Remove factory wires on inputs 521 and 522.
4. Install the Run Bug UP/DOWN switch to IOs 521 and 522.
5. Install the Run Bug UP/DOWN TIME switch to M24.
6. Install the Temporary Run switch between 120 and SFIN on the CXN board and 120 to
THL, MHL, and BHL on the CXN board.
7. Are there two sheave brakes and no rope gripper?
a. If there are two sheave brakes and no rope gripper, go to step 8.
b. If there is a rope gripper or a single sheave brake, the process ends.
8. Install a jumper between EB and SOUT.

Drive Startup Manual HPV900-PM
Page 6 © 2019 Smartrise Engineering, Inc. All Rights Reserved December 17, 2019
Figure 4: Example of Construction Wiring
Powering Up
Perform the following to power up the drive.
1. Apply external power by closing the main disconnect.
2. Close the two-pole breaker and all pushbutton breakers.

Drive Startup Manual HPV900-PM
December 17, 2019 ©2019 Smartrise Engineering, Inc. All Rights Reserved Page 7
3. Verify the LCD on the Smartrise board and the drive powers up.
Figure 5: Breakers
Final Setup
Perform the following to set the Bypass Term Limit.
NOTE: The selected menu within the menu options is shown with a *.
1. Toggle the Inspection/Normal switch to Inspection.
2. On the Smartrise Machine Room board, press the left arrow (ESC) button several times
to get to the MAIN SCREEN.
3. Press the right button to access the Main Menu.
4. From the MAIN MENU, scroll and select Setup.
Figure 6: MAIN MENU –Setup

Drive Startup Manual HPV900-PM
Page 8 © 2019 Smartrise Engineering, Inc. All Rights Reserved December 17, 2019
5. From the SETUP menu, scroll and select Misc.
Figure 7: SETUP Menu –Misc
6. From the MISC menu, scroll and select Bypass Term Limits.
Figure 8: MISC Menu –Bypass Term Limits
7. From the BYPASS TERM LIMITS menu, set the bypass term limits from NO to YES.
Figure 9: Bypass Term Limits Menu –NO
8. Scroll and change NO to YES.
Figure 10: Bypass Term Limits Menu –YES
9. Scroll right and press Enter to save.
10. Press the left button several times to get to the MAIN SCREEN.
11. Verify the LCD displays Construction Mode on the MAIN SCREEN.

Drive Startup Manual HPV900-PM
December 17, 2019 ©2019 Smartrise Engineering, Inc. All Rights Reserved Page 9
12. Does the drive show a Setup Fault One on the display?
a. If the drive shows a Setup Fault One, go to Setup Fault One.
b. If the drive does not show a Setup Fault One, the process ends.
Auto Tuning
The auto tune function must be performed for a PM motor to properly operate. The two
functions are Encoder Alignment and Motor Alignment. Complete the checklist during the
verification process.
NOTE: During the alignment process, the Smartrise SRU board may display several faults. These
are normal and won’t affect the alignment procedure.
Motor Alignment
Perform the following to align the motor.
1. Use the Left|Right arrow buttons to select the AUTOTUNE SEL U12 menu.
2. Use the Up|Down arrow buttons to change AUTOTUNE SELECT to YES but DON’T PRESS
THE ENTER BUTTON.
3. Press and hold the M contactor button.
4. Press the Enter button on the drive to start the alignment.
Encoder Alignment (Non-Rotational)
Perform the following to align the encoder.
1. On the drive –In the ROTOR ALIGN U10 menu change the following parameters:
•Set the alignment method to either HF INJECT or AUTO ALIGN and press Enter. See
Table 4 HF INJECT Note to verify if the HF INJECT method can be used.
•Change alignment from disabled to enable.
•Select BEGIN ALIGNMENT to Yes but DON’T PRESS THE ENTER BUTTON.
2. Press and hold the M contactor button.
3. Press the Enter Button on the drive to start the alignment.
NOTE: If the drive displays the error message “CAN NOT CHANGE AT THIS TIME”, verify
U10 ROTOR ALIGN –ALIGNMENT is set to Enable. If there are other faults during this
process, see Magnetek HPV900 for diagnostic information.

Drive Startup Manual HPV900-PM
Page 10 © 2019 Smartrise Engineering, Inc. All Rights Reserved December 17, 2019
The table below lists the Parameters for BASICS U9.
Table 2: Parameters for BASICS U9
Parameter
Description
Choices
Drive Mode
Drive Operation
Open Loop
Closed Loop
PM
The table below lists the Parameters for AUTOTUNE SEL U12.
Table 3: Parameters for AUTOTUNE SEL U12
Parameter
Description
Choices
Autotune Select
Allows autotune to run
Disable
On Run
Yes
The table below lists the Parameters for ROTOR ALIGN U10.
Table 4: Parameters for ROTOR ALIGN U10
Parameter
Description
Choices
Alignment
Allows alignment to be
performed
Enable
Disable
Begin Alignment
Determines when to
perform alignment
Yes
On Run
No
Alignment Method
How alignment will be
performed
Open Loop
Auto Align
HF INJECT *
*NOTE: HF INJECT only works if the drive version is A4810-xxxx15.xx or above. Navigate to U6
DRIVE INFO and check the drive version. If the drive is not version 15 or above, then use AUTO
ALIGN.
The table below lists the Parameters for DRIVE INFO U6.
Table 5: Parameters for DRIVE INFO U6
Parameter
Description
Choices
Drive Version
Shows the software
version of the drive
software
A4810-xxxx15.xx

Drive Startup Manual HPV900-PM
December 17, 2019 ©2019 Smartrise Engineering, Inc. All Rights Reserved Page 11
Operation
Run the car and complete the checklist during the verification process.
No Faults
Make sure the car is moving without triggering a fault either on the Smartrise SRU board or the
drive. If the SRU board displays a drive fault, look at the drive to see what the fault is. See Drive
Fault/Encoder Fault for troubleshooting drive fault.
Proper Direction
Make sure the car is moving in the same direction as the control switch on the Run Bug. See
Wrong Direction for troubleshooting proper direction faults.
At Speed
Make sure the car is moving at the proper inspection speed (approximately 50 fpm). See Car
Moving to Slow or Rough for troubleshooting at speed faults.
Under Control
Make sure that the car is moving under full control. The car should stop when commanded
from the Run Bug. Verify that the car runs with no faults for 10 seconds or more. See Brake Not
Lifting for troubleshooting under control faults.
Troubleshooting
The following sections list troubleshooting procedures.
Drive Fault/Encoder Fault
The most common fault at drive startup is the Encoder fault.
Perform the following checks to correct this fault:
•Check for a solid shield-to-ground connection at the motor and drive.
•Check for correct colored encoder wires to the terminals.
•Verify the C1-Encoder Select is set to endat.
•If any encoder wiring has been changed, the Encoder Alignment must be run again.
See Encoder Alignment.

Drive Startup Manual HPV900-PM
Page 12 © 2019 Smartrise Engineering, Inc. All Rights Reserved December 17, 2019
Brake Not Lifting
If the brake is not picking, make sure that the brake is wired according to V2 Controller sheet 05
Brake Connection and verify that the EB terminal is jumpered to the terminal. See V2 Controller
sheet 01 Getting Started for more information.
If the brake has the proper voltage check the following:
•During a run command, check the DC voltage between points K1/K2 and J1/J2 if
secondary brake is installed. Verify the voltages are also at the brake coil(s) when
commanded to pick.
•Verify that the actual brake voltage matches the brake coil voltage shown on the V2
Controller sheet 01 Getting Started Parameter table.
Wrong Direction
If the car is moving in the wrong direction check the following:
•On the Smartrise controller board make sure that IO 521 comes on when commanding
the UP direction and IO 522 comes on when commanding the DOWN direction.
•Change the direction of the motor in the drive by going to C1-Motor Rotation and
toggling between FORWARD/REVERSE.
•Swap two of the motor leads (T1 with T2).
•After swapping the motor wires, it may be necessary to change C1 –Motor Rotation
again.
Car Moving to Slow or Rough
If the car is moving to slow or rough perform the following:
•Verify the brakes are lifting fully.
Setup Fault One
This fault is caused when the HPV900 is programmed with motor data (A5) that conflicts with
the drive software.
1. Unplug the CAT5 cable from the drive port on the the Machine Room board. This will
restore access to the HPV LCD screen.
2. Navigate to A5 –Motor Parameters –Motor Poles and verify that you have the correct
number of poles listed.
3. Navigate to A5 –Motor Parameters –Rated Motor Speed and lower the RPM by 15-20
rpms and save.
4. Plug the CAT5 cable into the drive port on the Machine Room board.
Table of contents
Other Smartrise DC Drive manuals
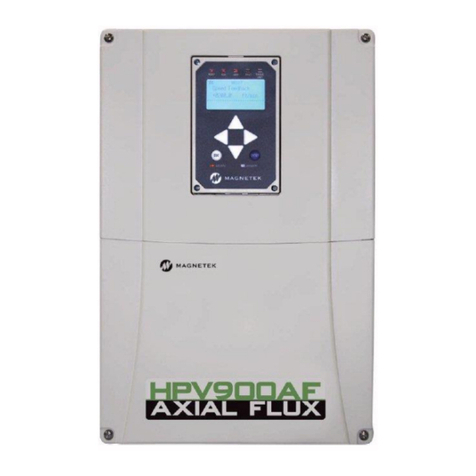
Smartrise
Smartrise Magnetek HPV900AF Installation and operation manual
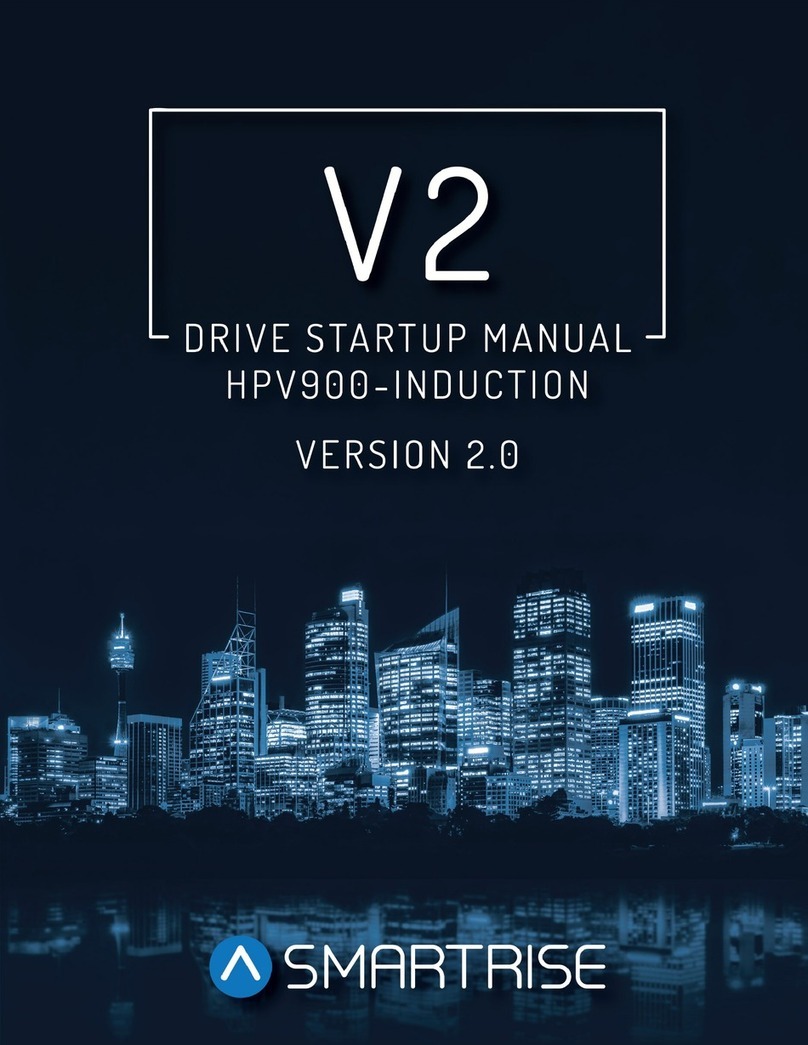
Smartrise
Smartrise HPV900-INDUCTION Installation and operation manual

Smartrise
Smartrise KEB-Induction Installation and operation manual
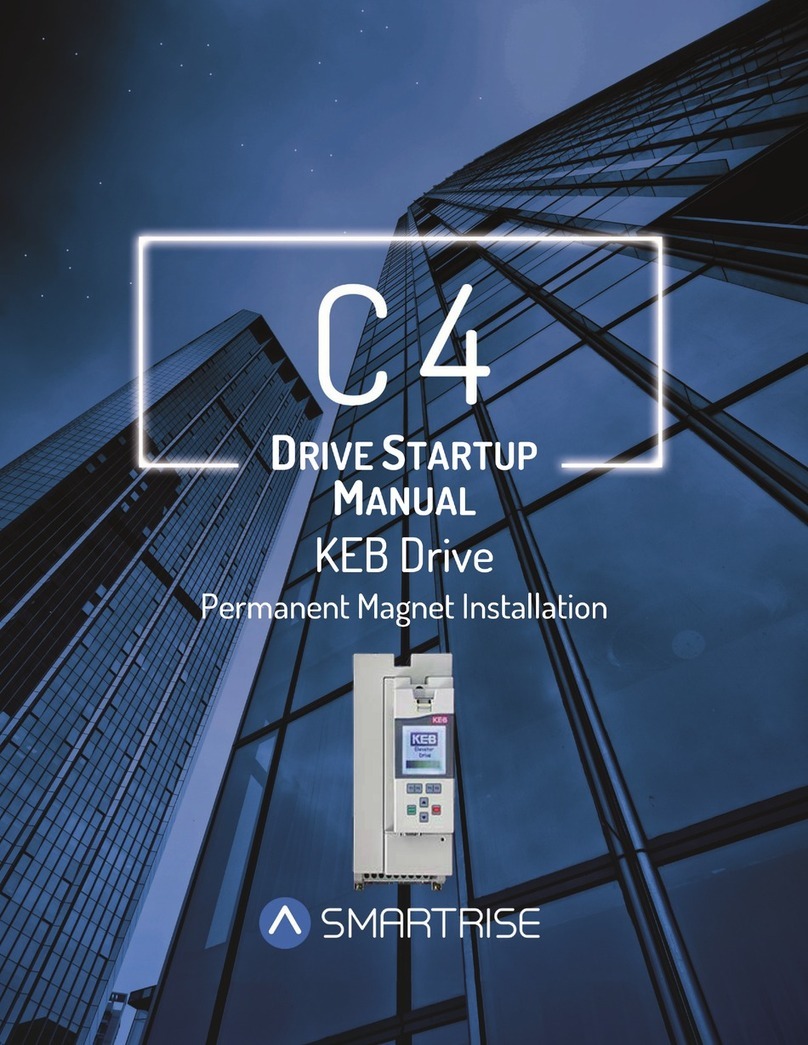
Smartrise
Smartrise C4 User manual
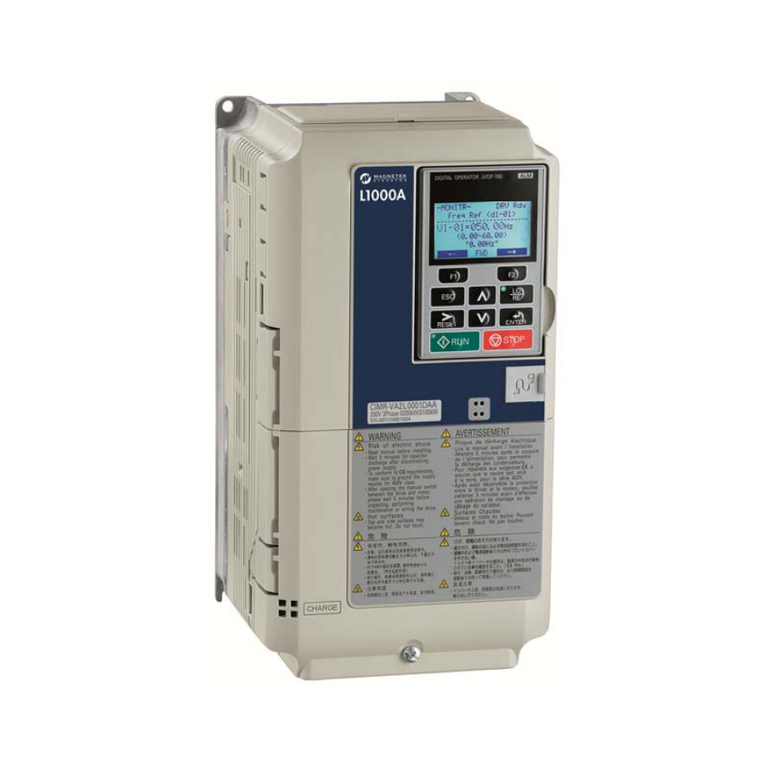
Smartrise
Smartrise Magnetek L1000A Installation and operation manual
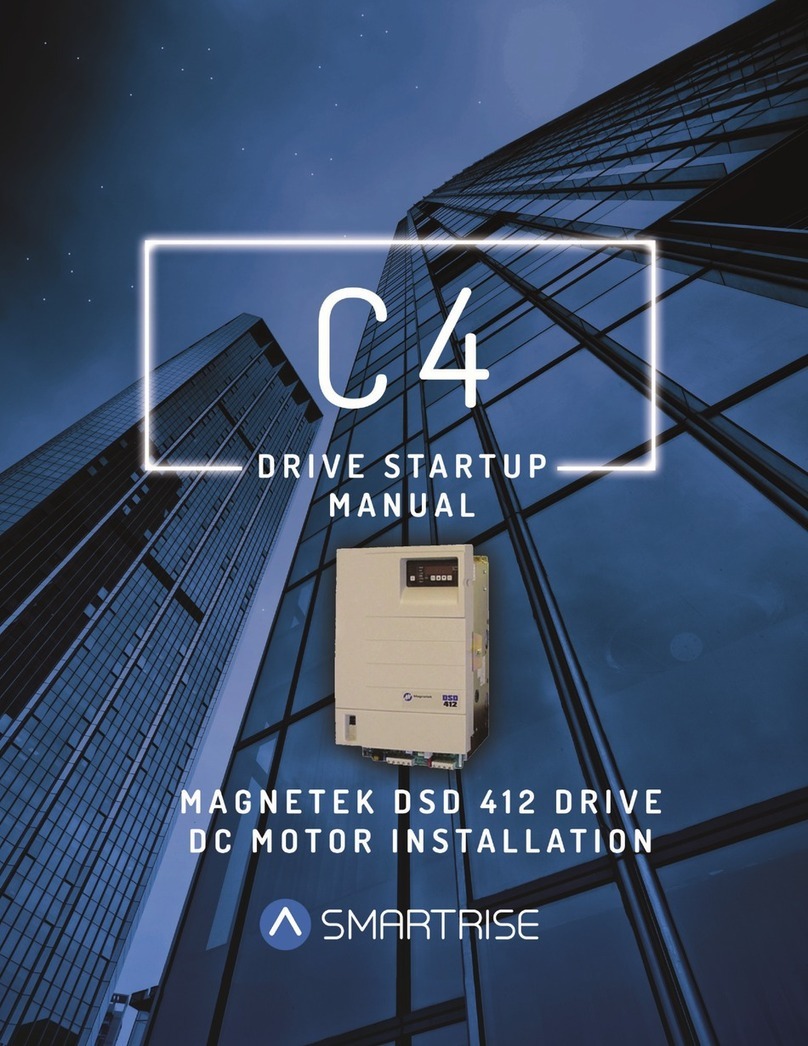
Smartrise
Smartrise C4 Installation and operation manual
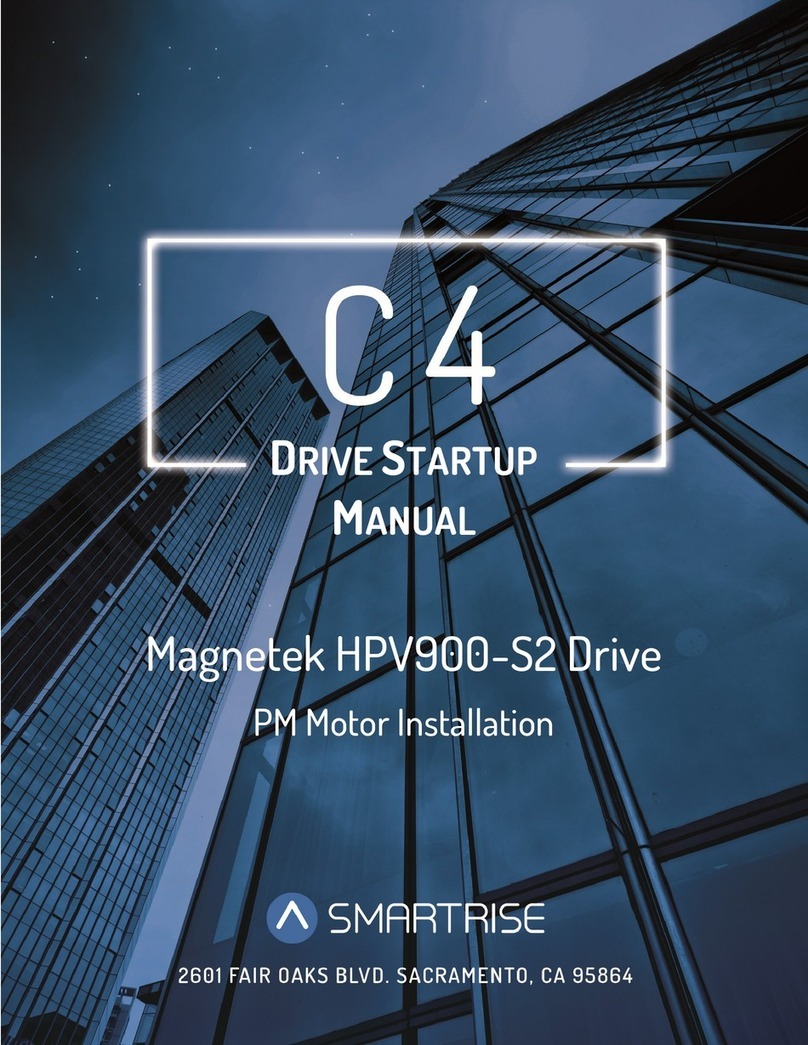
Smartrise
Smartrise HPV900-S2 Installation and operation manual
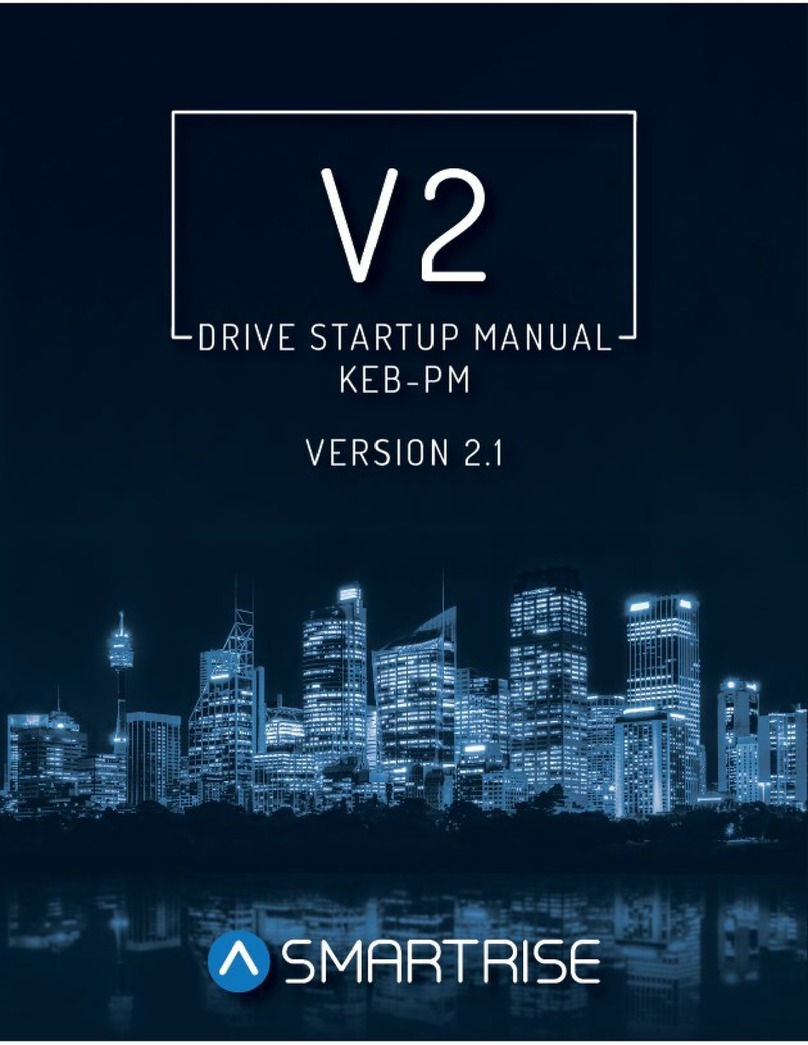
Smartrise
Smartrise KEB-PM Installation and operation manual
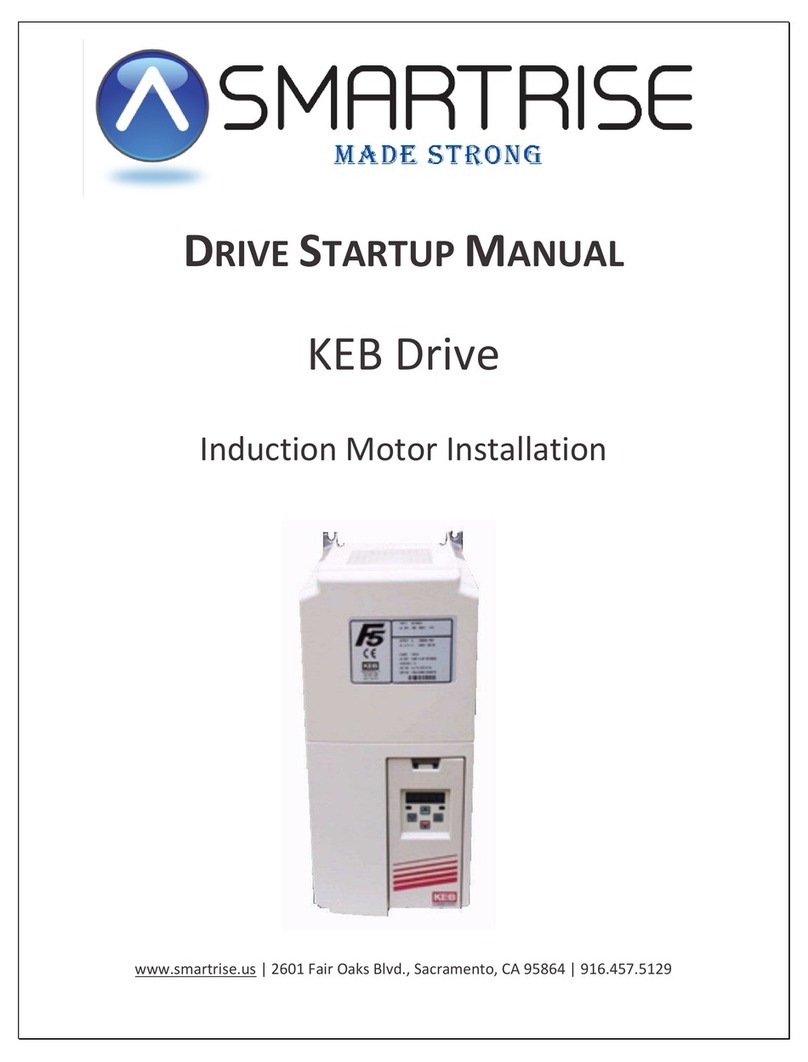
Smartrise
Smartrise KEB Series Installation and operation manual

Smartrise
Smartrise KEB-Induction Installation and operation manual