Sullair SD Series User manual

SD-220 / SD-600
DDS OPTION
3V OPTION
SD Heatless Desiccant
Compressed Air Dryers
REF: 02250130-734
SERIES SD

INSTALLATION, START-UP & MAINTENANCE MANUAL
MODEL NO.: SD-220 TO SD-600- DDS OPTION
REV 0 – May 24,,.2001
2
TABLE OF CONTENTS
FOREWORD................................................................................................................................. 4
SECTION 1 INTRODUCTION.................................................................................................. 5
1.1 GENERAL INFORMATION............................................................................................. 5
1.2 SAFETY INSTRUCTIONS................................................................................................ 5
1.2.1 Identification of signs and symbols in this technical manual ..................................... 6
1.2.2 Safety tips for maintenance, inspection and assembly work....................................... 6
1.3 PERSONNEL QUALIFICATION...................................................................................... 7
1.4 PRODUCT INFORMATION............................................................................................. 8
1.4.1 Pressure vessel regulations.......................................................................................... 8
1.4.2 Airtightness test .......................................................................................................... 8
1.4.3 Overloading................................................................................................................. 8
1.4.4 Technical data sheet.................................................................................................... 9
1.4.5 Transport................................................................................................................... 10
1.4.6 Storage ...................................................................................................................... 10
1.4.7 Use of a pre and after filter ....................................................................................... 10
SECTION 2 INSTALLATION.................................................................................................. 11
2.1 SET-UP AND INSTALLATION...................................................................................... 11
SECTION 3 START UP AND OPERATION........................................................................ 12
3.1 START UP/ SHUT DOWN.............................................................................................. 12
3.2 DESCRIPTION OF THE OPERATION .......................................................................... 13
3.2.1 Description of the operation...................................................................................... 13
3.2.2 Dryer operating sequence (No control or alarm option)........................................... 14
3.2.3 Operating sequence (DDS Option)........................................................................... 15
3.2.4 Alarms....................................................................................................................... 16
3.2.5 Electrical control....................................................................................................... 17
3.3 SPECIAL EQUIPMENT .................................................................................................. 18
3.3.1 DDS Controls............................................................................................................ 18
3.3.2 DDS Controls – Start up and operation .................................................................... 18
SECTION 4 MAINTENANCE................................................................................................. 20
4.1 REPLACEMENT OF THE DESICCANT ....................................................................... 21
4.2 DISPOSAL OF THE DESICCANT ................................................................................. 21
4.3 CHANGING OF THE REGENERATION ORIFICE ...................................................... 22
4.4 TECHNICAL DOCUMENTS.......................................................................................... 23
4.4 TECHNICAL DOCUMENTS.......................................................................................... 24
4.5 FILTERS........................................................................................................................... 25
4.5.1 General comments and use ....................................................................................... 25
4.5.2 Function .................................................................................................................... 25
4.5.3 Assembly and installation......................................................................................... 25
4.5.4 Maintenance.............................................................................................................. 25
4.5.5 Changing of filter elements....................................................................................... 26
4.5.6 Accessories ............................................................................................................... 26

INSTALLATION, START-UP & MAINTENANCE MANUAL
MODEL NO.: SD-220 TO SD-600- DDS OPTION
REV 0 – May 24,,.2001
3
SECTION 5 DRYER FLOW CAPACITY AND PURGE ADJUSTMENT.......................... 27
5.1 DRYER FLOW CAPACITY............................................................................................ 27
5.2 CORRECTION FACTOR FOR INLET TEMPERATURE............................................. 27
5.3 PURGE ADJUSTMENT.................................................................................................. 28
SECTION 6 SPARE PARTS LIST......................................................................................... 29
6.1 SPARE PARTS LIST FOR SD-220 TO SD-400 ............................................................. 29
6.1 SPARE PARTS LIST FOR SD-500 TO SD-600 ............................................................. 30
6.2 INLET-EXHAUST VALVE MANIFOLD....................................................................... 31
6.2 OUTLET-CHECK VALVE MANIFOLD........................................................................ 32
SECTION 7 TROUBLE SHOOTING & FAULTS................................................................. 33
7.1 THE DEW POINT IS TOO HIGH ................................................................................... 33
7.2 THE ADSORPTION DRYER DOES NOT SWITCH OVER......................................... 33
7.3 BACK PRESSURE IS TOO HIGH DURING REGENERATION PHASE.................... 34
7.4 SHORT-TERM SHUT-DOWN........................................................................................ 34
7.5 SHUT-DOWN IN CASE OF A FAULT OR FOR MAINTENANCE............................. 35
7.6 RE-STARTING ................................................................................................................ 35
SECTION 8 ANNEX................................................................................................................... 1

INSTALLATION, START-UP & MAINTENANCE MANUAL
MODEL NO.: SD-220 TO SD-600- DDS OPTION
REV 0 – May 24,,.2001
4
FOREWORD
This technical manual of S
Su
ul
ll
la
ai
ir
r®
®
is an aid in getting to know the adsorption dryer
better and in utilising its possibilities for application in accordance with its intended
use. Furthermore, this manual contains important information for safe, proper and
economic operation.
All instructions must be followed as written in order to avoid danger and damages
which could cause downtime and premature wear and tear on the adsorption dryer.
In addition to the technical manual and the accident prevention regulations which
are valid and compulsory in the country and in the particular workplace where the
adsorption dryer is being used, the recognized special rules for safe and proper
working procedures are also to be heeded. The technical manual must always be
within reach wherever the adsorption dryer is being used.
Each person involved with the set-up, start-up, operation, maintenance and repair
of the adsorption dryer in the User Company must have first read and understood
the technical manual and especially the safety tips.

INSTALLATION, START-UP & MAINTENANCE MANUAL
MODEL NO.: SD-220 TO SD-600- DDS OPTION
REV 0 – May 24,,.2001
5
SECTION 1 INTRODUCTION
1.1 GENERAL INFORMATION
The adsorption dryer of the SD-220 / SD-600 series is built according to the latest
technological developments and recognized safety rules. Its use however can
endanger life and limb of the user or of third parties, and can lead to considerable
damage to the adsorption dryer and other material assets if:
•it is operated by personnel not trained or instructed in its use,
•it is improperly used,
•it is improperly maintained or serviced.
This can result in the loss of all damage claims.
This adsorption dryer is designed for neutral media free of aggressive water, oil and
solid elements. S
Su
ul
ll
la
ai
ir
r®
®
accepts no liability for corrosion damage and malfunctions
caused by aggressive media.
Applications other than those mentioned in this manual must be agreed to by S
Su
ul
ll
la
ai
ir
r®
®
and confirmed in writing.
In the interest of further development, S
Su
ul
ll
la
ai
ir
r®
®
reserves the right to make changes at
any time, which, in keeping with the essential characteristics of the adsorption dryer
described here, may be necessary for increasing efficiency or for reasons relating
to safety or to normal business practice.
1.2 SAFETY INSTRUCTIONS
This technical manual contains basic tips, which must be followed during set-up,
operation and servicing. It is thus of utmost importance that it be read by the
assembly technician before installation and start-up as well as by the specialist /
operator in charge, and it must always be within reach at the place where the
adsorption dryer is being used.

INSTALLATION, START-UP & MAINTENANCE MANUAL
MODEL NO.: SD-220 TO SD-600- DDS OPTION
REV 0 – May 24,,.2001
6
SECTION 1
1.2.1 Identification of signs and symbols in this technical manual
The safety tips contained in this technical manual, whose disregard could endanger
people and machines, are indicated by a general danger sign and the additional
markings Danger! or Attention!
Danger! / Caution!
Safety sign in accordance with DIN 4844 - W9
Warning against electrical voltage!
Safety sign in accordance with DIN 4844 - W8
Safety tips printed directly on the adsorption dryer must be heeded at all times and
must be kept completely legible.
*Advices
This sign refers to a procedure or sequence of particular interest
or importance. All tips must be followed to ensure proper use of
this adsorption dryer.
•This dot refers to working or operational steps. The steps are to
be carried out in the order of their appearance from top to bottom.
•The sign of a hyphen marks enumerations.
1.2.2 Safety tips for maintenance, inspection and assembly work
The operator is to make sure that all maintenance, inspection and assembly work
is carried out by special personnel who are authorized and qualified, and who are
adequately informed through careful study of the technical manual. For this reason,
special attention should be paid to the following attention and danger sign:

INSTALLATION, START-UP & MAINTENANCE MANUAL
MODEL NO.: SD-220 TO SD-600- DDS OPTION
REV 0 – May 24,,.2001
7
SECTION 1
CAUTION!
•Never make structural changes to the adsorption dryer!
•Only use original spare and accessory parts!
•Never weld on a pressure vessel or change it in any way!
Carry out maintenance work only when the adsorption dryer is
switched off, is depressurized and disconnected from the electric
power supply.
*Advices
Refer to the desiccant material safety data sheet (MSDS) when
installing or disposing of desiccant.
DANGER!
Wear protective goggles when working with the desiccant!
*Advices for protection
•If desiccant comes into contact with the eyes, rinse eyes
immediately with a lot of clear water.
•If the desiccant is spilled, clean up without causing swirls of dust.
•In case of fire, there is no restriction on the use of fire extinguishing
material; the reaction with water and foam is defined as strong.
•A mask must be worn.
1.3 PERSONNEL QUALIFICATION
The personnel involved in operation, maintenance, inspection and assembly must
have the corresponding qualifications to do this work. Areas of responsibility and
supervision of the personnel must be precisely established by the operator. Should
the personnel not possess the necessary knowledge, then they must be trained and
instructed. If need be, this training may be carried out by the manufacturer / supplier
at the request of the operator of the adsorption dryer. Further, the operator is to
make sure that the personnel completely understand the contents of the technical
manual.

INSTALLATION, START-UP & MAINTENANCE MANUAL
MODEL NO.: SD-220 TO SD-600- DDS OPTION
REV 0 – May 24,,.2001
8
SECTION 1
1.4 PRODUCT INFORMATION
The adsorption dryer is used for the purpose of drying compressed air and other
gases according to its respective design. As a "standard model" the adsorption dryer
is equipped with two desiccant vessels and a pre- and after-filter, and depending on
certain conditions at the outlet, provides pure, dry and oil-free compressed air or
gases.
1.4.1 Pressure vessel regulations
The pressure vessels are designed according to the standard technical
requirements. They fulfill the test of the certifying procedure and carry the “U”,
“UM” ASME Symbol.
Range of application
Type SD-220 TO SD-600
Operating overpressure Max. 150 PSIG
Temperature Max.
Min. 500 °F
-20 °F
1.4.2 Airtightness test
All adsorption dryers are subjected to an airtightness test prior to shipment using
compressed air.
1.4.3 Overloading
CAUTION!
Protect the adsorption dryer from overloads!
The adsorption dryer can become overloaded, if:
•The flow capacity of the medium to be dried increases,
•The temperature of the air at entry, and correspondingly its
humidity increases,
•The min. operating pressure is under cut,
•The pre-filtration and separation of impurities are not sufficient, or
filter drain fails.

INSTALLATION, START-UP & MAINTENANCE MANUAL
MODEL NO.: SD-220 TO SD-600- DDS OPTION
REV 0 – May 24,,.2001
9
SECTION 1
1.4.4 Technical data sheet
TYPE SD-220 SD-300 SD-400 SD-500 SD-600
Medium Air, free of aggressive elements
Connection NPT 1-1/2" NPT 1-1/2" NPT 1-1/2" NPT 2” 2”
Flow capacity (1) (STD) SCFM 220 300 400 500 600
Desiccant
Standard Input temp.: from 100°F and dew point (2) -40°C (-40°F)
Filled with: activated alumina
Quantity of desiccant / Vessel
[Lbs.] 126 167 220 272 350
Filter size (mph/mpr) 300 300 420 470 700
Control Electronic board or PLC Controller
Operating Voltage
Standard 120 V / 60 Hz (AC)
Special voltage Consult factory
Drying time
Standard 5 min
(1) Flow capacity in SCFM at 100 PSIG according to DIN ISO 7183
(2) Pressure dew point
NOTE: Settings for DDS:
Standard dryers DDS Control (-41°C) High humidity (-36°C)

INSTALLATION, START-UP & MAINTENANCE MANUAL
MODEL NO.: SD-220 TO SD-600- DDS OPTION
REV 0 – May 24,,.2001
10
SECTION 1
1.4.5 Transport
After the adsorption dryer has been delivered, it must be checked for damage that
may have occurred during transport. If necessary, the Transport company must be
informed to register the damage.
*Advices
For transport within the company, only the skid of the adsorption
dryers SD-220 /SD- 600 may be used.
1.4.6 Storage
If the adsorption dryer is to be stored for a longer period of time, its place of storage
must be dry and free of dust. There has to be a min. ambient temp. of +1°C (33°F).
1.4.7 Use of a pre and after filter
In order to prevent droplets of condensate, oil and dirt from getting into the
desiccant, a pre-filter is installed in front of the adsorption dryer, since an oil film on
the desiccant reduces the drying capacity and the dewpoint. In order to prevent
breakdowns in downstream consumers caused by material that has been abraded
from the desiccant bed, an after-filter is mounted behind the adsorption dryer. Since
no condensate accumulates in the after-filter, this filter is always equipped with a
manual valve.
Both filters are equipped with a differential pressure gauge (standard) as this
ensures an indirect display of the degree of contamination of the filter elements.

INSTALLATION, START-UP & MAINTENANCE MANUAL
MODEL NO.: SD-220 TO SD-600- DDS OPTION
REV 0 – May 24,,.2001
11
SECTION 2 INSTALLATION
2.1 SET-UP AND INSTALLATION
Once at the installation location, the adsorption dryers of the series SD-220 / SD-
600, which are supplied with a base frame, must be positioned so that sides are
easily accessible. The piping is to be connected to the adsorption dryer at a light
slope. A shut-off valve is to be installed on the inlet and outlet sides of the
adsorption dryer. Also, a by-pass pipe with an additional shut-off valve should be
mounted onto the adsorption dryer, in order to be able to guarantee an
uninterrupted supply of compressed air in case the adsorption dryer breaks down.
Should vibrations occur on the installation location, the adsorption dryer is to be
placed onto vibration dampers.
Since the adsorption dryer has already been completely wired at our factory, the
customer only has to connect the power supply cable to the terminal strip according
to the supplied wiring diagrams.
*Advice
Should you still have questions regarding installation, you can
request installation blueprints separately from S
Su
ul
ll
la
ai
ir
r®
®
,
,
Michigan
City, IN.
CAUTION!
Do not hydrotest dryer, all vessel assemblies are factory
pressure tested per design requirements prior to release from the
manufacturer.

INSTALLATION, START-UP & MAINTENANCE MANUAL
MODEL NO.: SD-220 TO SD-600- DDS OPTION
REV 0 – May 24,,.2001
12
SECTION 3 START UP AND OPERATION
3.1 START UP/ SHUT DOWN
CAUTION!
All pipes and wire connections are to be tightened!
Furthermore, before start-up:
•The pipes must be checked for the presence of scale, abraded
material from the threading, or other similar impurities.
•All shut off valves on the pre-filter, adsorption dryer, after-filter and
on the bypass line should be closed.
•The ambient temperature must not be less than 33°F
Breakdowns resulting from faulty installation do not fall under S
Su
ul
ll
la
ai
ir
r's warranty
obligation.
*Advices
The following sequence is to be heeded for the initial start-up:
•Slowly open the inlet valve and observe the pressure build-up
on the chamber pressure gauge of the adsorption dryer. A too
abrupt pressure build-up is to be avoided.
•Turn the switch to the "POWER ON" position.
•The adsorption dryer must be powered approx. 3-4 h with the shut
off valve behind the after-filter closed; this regenerates the
desiccant.
•After the regeneration phase, open the shut off valve behind the
after-filter slowly while observing the chamber pressure gauge; if
the shut off valve is opened too abruptly, it could put a stress on
the system.
•The adsorption dryer is now ready for operation and functions
continuously and fully automatically.

INSTALLATION, START-UP & MAINTENANCE MANUAL
MODEL NO.: SD-220 TO SD-600- DDS OPTION
REV 0 – May 24,,.2001
13
SECTION 3
3.2 DESCRIPTION OF THE OPERATION
The S
Su
ul
ll
la
ai
ir
r®
®
adsorption dryer of the series SD-220 / SD-600 functions according to
the pressure change principle, using dry air regeneration. Two adsorption vessels
filled with desiccant are installed parallel to each other for this purpose. While the
medium is being dried in one vessel, regeneration takes place in the other vessel.
The changeover from one vessel to the other is performed in a fixed rhythm by
means of a time-dependent control system. The adsorption dryer operates
continuously and fully automatically.
3.2.1 Description of the operation
•The S
Su
ul
ll
la
ai
ir
r®
®
SD dryer has a NEMA cycle time of 10 minutes. In a 10 minute
cycle, 5 minutes is dedicated to drying for each chamber (5 minutes half cycle).
•Through the inlet switching valve wet air enters either desiccant chamber at the
inlet (bottom) and is dried as it flows upward through the desiccant bed. Dry air
exits the dryer through the outlet check valve.
•At the outlet of each chamber, a portion of the dry air (purge air) is diverted to
the regenerating chamber. The dry air, at near atmospheric pressure, will
remove previously adsorbed moisture as it flows downward through the
desiccant bed exiting through the purge exhaust mufflers.
•The purge air is controlled by a purge adjusting valve and purge orifices located
in the purge line. Purge pressure can be monitored on the purge pressure
gauge. Refer to section on purge adjustment for instructions on setting the
purge rate.
•Near the end of each half cycle, the chamber being regenerated will be re-
pressurized. For this to occur, the exhaust valve of the chamber being
regenerated closes while purge air continues to flow. Re-pressurizing the
regenerated chamber to operating pressure before placing it into service
minimizes fluidization of the desiccant and helps prevent desiccant abrasion
which causes desiccant dust to prematurely block pilot and after-filter elements.
•Dryers operating at pressures greater than 120-125 PSIG or in an accelerated
NEMA cycle could be fitted with a re-pressurizing valve. This valve assists the
regenerated chamber to reach dryer operating pressure before chamber
switchover.
•Chamber switchover takes place when both towers are fully pressurized to
minimize desiccant movement.
When switchover is complete, the regenerated tower will be placed into service and
the exhausted tower will begin a depressurization/regeneration cycle.

INSTALLATION, START-UP & MAINTENANCE MANUAL
MODEL NO.: SD-220 TO SD-600- DDS OPTION
REV 0 – May 24,,.2001
14
SECTION 3
3.2.2 Dryer operating sequence (No control or alarm option)
The S
Su
ul
ll
la
ai
ir
r®
®
SD-220 / SD-600 heatless air dryers use a PLC as its standard
controller. In the event of a power failure, the inlet valves will remain in their
positions and the exhaust valves will close. The dryer system will repressurize.
Energizing control panel: Power is turned ON – electrical circuit energized.
When power is applied or restored to the control panel, the dryer will remain in a
standby state for one (1) minute period, allowing the dryer system to repressurize.
STEP 1 SELECT LEFT CHAMBER DRYING.
- De-energize solenoid EV-1R and EV-2L.
- Energize solenoid EV-1L and EV-2R.
- Inlet valve positioned for left chamber drying.
- Exhaust valve opened for right chamber regeneration.
- When regeneration time is complete, go to STEP 2
STEP 2 RIGHT CHAMBER REPRESSURIZATION.
- De-energize solenoid EV-1L and EV-2R.
- Inlet valves remain in open position.
- Right chamber exhaust valve closes.
- The repressurization timer starts a countdown of 45 sec.
- When repressurization time is complete, go to STEP 3
STEP 3 SELECT RIGHT CHAMBER DRYING.
- Energize solenoid EV-1R and EV-2L.
- Inlet valve positioned for right chamber drying.
- Exhaust valve opened for left chamber regeneration.
- When regeneration time is complete, go to STEP 4
STEP 4 LEFT CHAMBER REPRESSURIZATION
- De-energize solenoid EV-1R and EV-2L
- Inlet valves remain in open position.
- Left chamber exhaust valve closes.
- The repressurization timer starts a countdown of 45 sec.
- When repressurization time is complete, go to STEP 1
The dryer has completed one (1) full cycle and will repeat steps 1 through 4 until
power is removed from the control panel.

INSTALLATION, START-UP & MAINTENANCE MANUAL
MODEL NO.: SD-220 TO SD-600- DDS OPTION
REV 0 – May 24,,.2001
15
SECTION 3
3.2.3 Operating sequence (DDS Option)
The S
Su
ul
ll
la
ai
ir
r®
®
SD-220-DDS – SD-600-DDS heatless air dryer uses a PLC as its
standard controller. In the event of a power failure, the inlet valves remain in their
position, and the exhaust valves will close and dryer will pressurize both chambers.
The dryer will return to the same step in the cycle dryer was in before power was
lost. (See NOTE 2)
Energizing control panel: Power is turned ON – electrical circuit energized.
STEP 1 SELECT LEFT CHAMBER DRYING.
- De-energize solenoid EV-1R.
- Energize solenoid EV-1L.
- Inlet valve positioned for left chamber drying.
- When 3 seconds have passed, go to STEP 2
STEP 2 RIGHT CHAMBER DE-PRESSURIZATION.
- Keep energized EV-1L
If not in DDS mode:
- Energize EV-2R opening right chamber dump/exhaust valve.
If in DDS mode and dewpoint is better than hygrometer setpoint:
-EV-2R does not energize.
When regeneration time has passed, go to STEP 3
STEP 3 RIGHT CHAMBER REPRESSURIZATION.
- Keep energized EV-1L.
- De–energize EV-2R closing right chamber dump/exhaust valve.
- The repress timer begins a countdown of 45 sec. (See Note 1)
- Inlet valve remains in current position.
- When repressurization time has passed, go to STEP 4
STEP 4 RIGHT CHAMBER DRYING.
- De-energize solenoid EV-1L
- Energize solenoid EV-1R.
- Inlet valve positioned for right chamber drying.
- When 3 seconds have passed, go to STEP 5
STEP 5 LEFT CHAMBER DEPRESSURIZATION.
- Keep energized EV-1R
If not in DDS mode:
- Energize EV-2L opening right chamber dump/exhaust valve.
If in DDS mode and dewpoint is better than hygrometer setpoint:
- EV-2R does not energize.
When regeneration time has passed, go to STEP 6

INSTALLATION, START-UP & MAINTENANCE MANUAL
MODEL NO.: SD-220 TO SD-600- DDS OPTION
REV 0 – May 24,,.2001
16
SECTION 3
3.2.3 Operating sequence (DDS option) – (Continued)
STEP 6 LEFT CHAMBER REPRESSURIZATION.
- Keep energized EV-1R.
- De–energize EV-2L closing left chamber dump/exhaust valve.
- The repress timer begins a countdown of 45 sec. (See note 1)
- Inlet valve remains in current position.
NOTE 1:EV-3 and repress valves could be used if dryer operating at pressure
above 125 PSI (G) and / or dryer operating on a timing cycle other
than 10 minute cycle. Refer to the specification sheet in this manual
or to the flow schematic supplied with the dryer.
NOTE 2:If power failure occurs to the dryer or unit is turned off, both exhaust
valves will close. The inlet valve will remain in their position.
NOTE 3: The actual timer setting may differ from the previously noted
sequence. Example: A dryer requiring 30 seconds to re-pressurize the
regenerating chamber will have a regeneration time of 4 minutes and
30 seconds. The half cycle time will remain at 5 minutes and full cycle
at 10 minutes.
NOTE 4: The regeneration and repressurization times should be adjusted by
S
Su
ul
ll
la
ai
ir
r®
®
trained personnel only. Changing the factory settings will result
in loss of dewpoint and/or failure to repressurize before changeover.
3.2.4 Alarms
COMMON ALARM RELAY
Common alarm relay comes with any optional alarm. If any one of the alarms are
activated, the common alarm relay will also be activated.
SWITCHING FAILURE ALARM (OPTIONAL, INCLUDED WITH DDS OPTION)
Two pressure switches, sensing desiccant chamber pressure, are provided. An
alarm will be activated if both chambers remain at full pressure when regeneration
is required. Furthermore, if pressure in both chambers remain below set pressure,
after depressurization an alarm will be activated.
NOTE:Dryers equipped with DDS and operating in the DDS mode do not
depressurize during the purge cycle (and do not purge) when an
acceptable dew point is maintained. During this condition, the
switching failure alarm is cancelled.
The alarm has a one-(1) minute delay.

INSTALLATION, START-UP & MAINTENANCE MANUAL
MODEL NO.: SD-220 TO SD-600- DDS OPTION
REV 0 – May 24,,.2001
17
SECTION 3
3.2.4 Alarms (Continued)
HIGH HUMIDITY ALARM (OPTIONAL, INCLUDED WITH DDS OPTION)
The hygrometer provided has been programmed to initiate an alarm if the dryer
outlet dew point falls below the setting. An alarm light is provided.
NOTE:The alarm has a 20-minute delay when the dryer is first powered up,
then the alarm is instant if the condition exists.
IF THE HYGROMETER BOARD TO PROBE CONNECTION FAILS,
then a fault will observed by the hygrometer. The high humidity alarm light will flash
on and off. The dryer will go into a fixed cycle mode. The digital display will indicate
“OPN”.
3.2.5 Electrical control
DANGER!
Work on electrical installations may only be done by a specialist
or by other persons instructed in this type of work as long as
they are under the instruction and supervision of a specialist; the
general rules for working with electricity must be followed!
You find the corresponding operating and control voltage on the data
sheet.
The S
Su
ul
ll
la
ai
ir
r®
®
adsorption dryer of the SD series is normally operated with a PLC
controller. The set times are adjusted at the factory during the test run.
CAUTION!
Do not change these adjustments!

INSTALLATION, START-UP & MAINTENANCE MANUAL
MODEL NO.: SD-220 TO SD-600- DDS OPTION
REV 0 – May 24,,.2001
18
SECTION 3
3.3 SPECIAL EQUIPMENT
3.3.1 DDS Controls
The DDS control option is a dewpoint demand switching system that monitors the
dryer dewpoint performance and manages the requirement for regeneration of the
dryer. The DDS controls major components are a digital dewpoint display
hygrometer and a humidity sensor.
The S
Su
ul
ll
la
ai
ir
r®
®
type SD Air dryer is designed to provide a specific pressure dewpoint
performance (generally –40 F (-40 C)) at the most severe operating conditions
specified. (Maximum flow at lowest pressure and highest inlet temperature). The
regeneration purge flow rate required for the dryer is calculated and adjusted to
achieve this dewpoint and is based on these conditions.
For example, for dryers operating at 100 PSIG (690 kPa) and 100 F (38 C) the
purge flow rate is approximately 15% of the specified maximum inlet flow. Dryers
operating under less severe inlet conditions will introduce a reduced humidity load.
The DDS controls have been factory programmed to monitor the dryer outlet
dewpoint performance and prevent initiation of a regeneration cycle under these
conditions.
The DDS controls system has the following standard features, refer to the enclosed
technical bulletin for a complete overview of the digital hygrometer display.
Digital display can be toggled to degrees F, C, and PPM.
Detection for cable fault between hygrometer and moisture probe.
Stainless steel humidity probe sampling cell with service valves.
3.3.2 DDS Controls – Start up and operation
The DDS controls system when supplied should be disabled for the initial 8 hours
of dryer operation. A dryer fitted with the DDS control will have a 3-position selector
switch on the electrical control panel. The 3 positions of this switch will perform the
following actions:
Position 1: POWER OFF
Position 2: POWER ON
Position 3: DDS ON

INSTALLATION, START-UP & MAINTENANCE MANUAL
MODEL NO.: SD-220 TO SD-600- DDS OPTION
REV 0 – May 24,,.2001
19
SECTION 3
3.3.2 DDS Controls – Start up and operation (Continued)
The POWER ON position will allow the hygrometer to be energized yet force the
dryer to operate on a FIXED CYCLE mode. The dryer SHOULD BE OPERATED IN
THIS POSITION AT TIME OF INITIAL STARTUP AND AT ALL TIMES WHEN THE
HYGROMETER OR HUMIDITY PROBE ARE REMOVED FOR SERVICE OR
CALIBRATION.
The DDS ON position will control the dryer regeneration steps when the dewpoint
of the dryer is better than the factory adjusted setpoint programmed into the digital
hygrometer.
The startup procedure for the DDS system will be as follows. Refer to the assembly
drawing in the following section.
1. Verify that the sample line (1/8 Teflon tube) is connected from the dryer outlet (see flow
schematic enclosed) to the inlet valve on the humidity probe sample cell. The humidity
probe comes in a transport container found inside the control panel. Remove probe from
container, and install in sample humidity cell. Close the container and keep inside the
control panel for future maintenance.
2. Connect the coaxial cable to the humidity probe
3. Fully open the inlet valve to the sample cell
4. Partially open the discharge valve of the sample cell to bleed off a small amount of
sample air. Do not fully open discharge valve
5. Perform a soap test to verify for leaks on all parts of the sample line connections and the
humidity sample cell.
6. The digital display will now read the dewpoint of the dryer system. It will take a short
period of time for a humidity probe to be purged of humidity.
Humidity cell assembly

INSTALLATION, START-UP & MAINTENANCE MANUAL
MODEL NO.: SD-220 TO SD-600- DDS OPTION
REV 0 – May 24,,.2001
20
SECTION 4 MAINTENANCE
*Advice
In order to ensure continuous and trouble-free operation, a
maintenance contract with S
Su
ul
ll
la
ai
ir
r®
®
is recommended.
Also, the following points should be checked regularly:
Daily •Carry out a general visual check and watch out for possible disturbances
during operation.
•Check function by manually operating the automatic condensate drain on
the pre-filter.
•Do an optical color test on the blue gel indicator for non-DDS dryers:
Indicator Color Approx. dew point [ °C]
Blue gel Blue
Pink
Transparent
- 25
0
+ 15
Weekly
•Check the differential pressure on the pre-filter, which should not exceed
10 PSID. Values greater than this indicate that the filter cartridge must be
changed.
•Check the differential pressure on the after-filter, which should not exceed
10 PSID. Values greater than this indicate that the filter cartridge must be
changed.
•Check the backpressure at the silencer placed behind the exhaust valve
combination; it should not exceed 5 PSIG. Use the gauge of the vessel
that is to be regenerated.
•Drain inlet and exhaust valve chambers using valves provided below the
valve (refer to photo attached).
•Drain pilot air filter housing of condensate (refer to photo attached).
Other manuals for SD Series
3
This manual suits for next models
2
Table of contents
Other Sullair Dehumidifier manuals
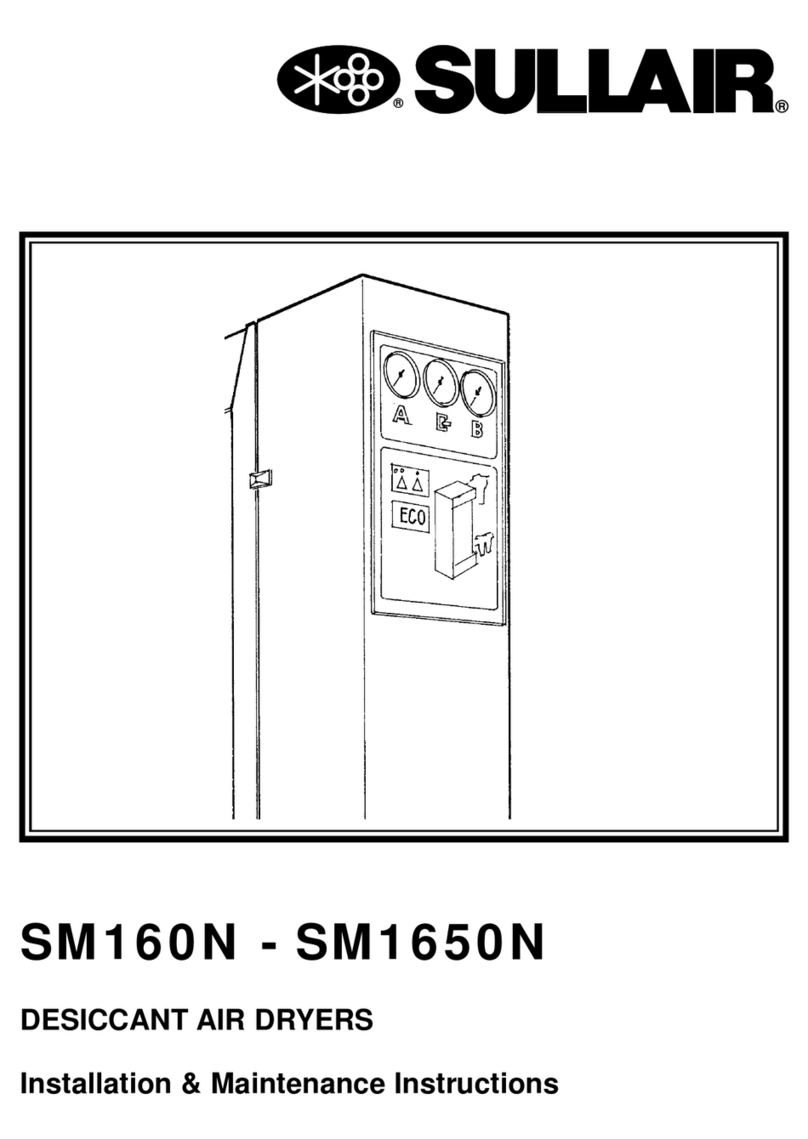
Sullair
Sullair SM-160N Installation and operating instructions
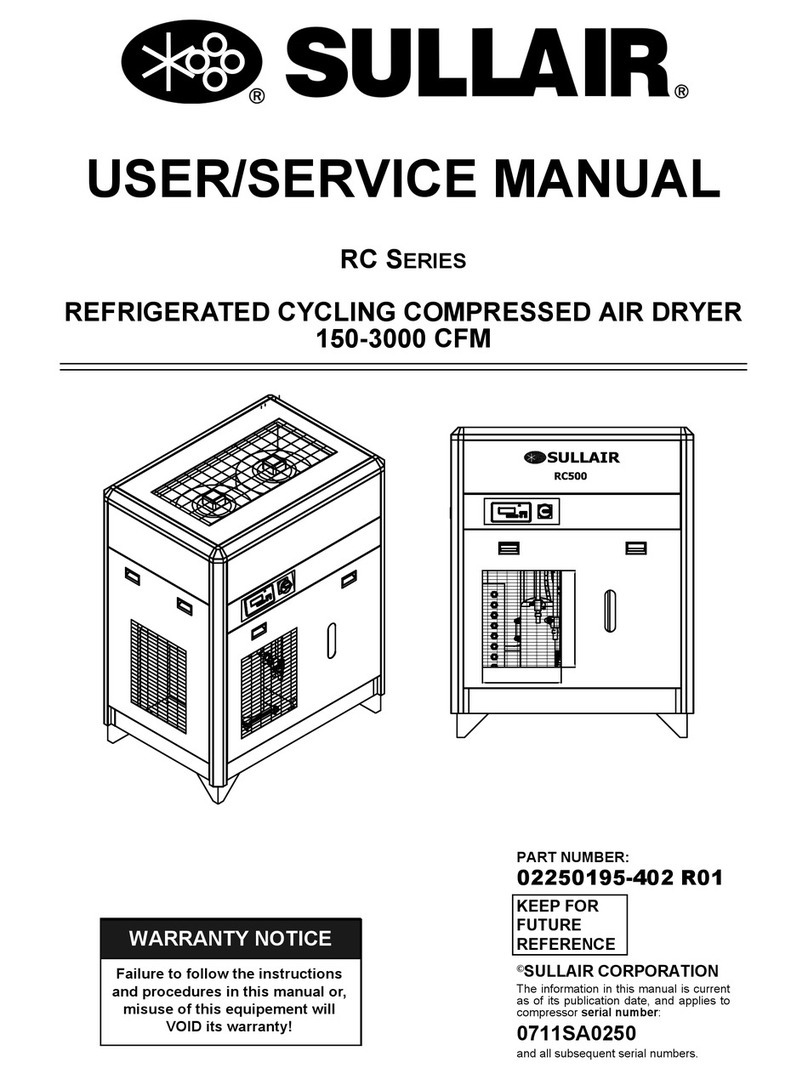
Sullair
Sullair RC Series Troubleshooting guide
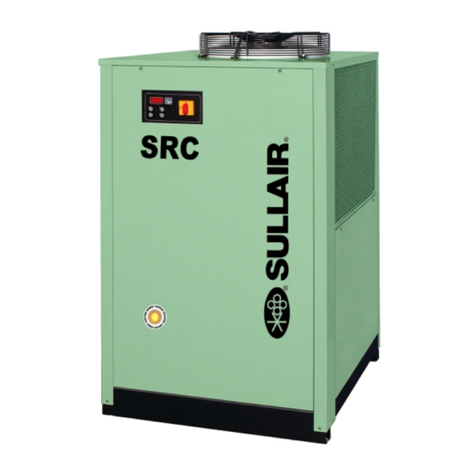
Sullair
Sullair SRC User manual

Sullair
Sullair SD Series User manual
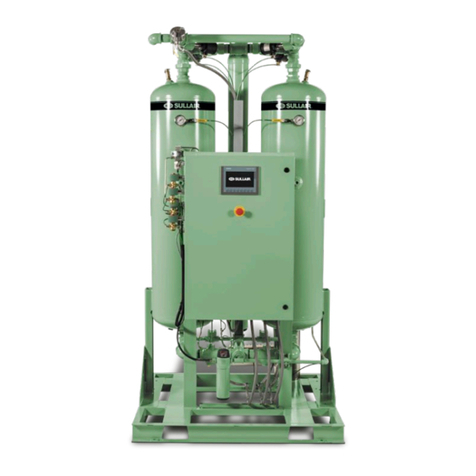
Sullair
Sullair DHL-80 User manual
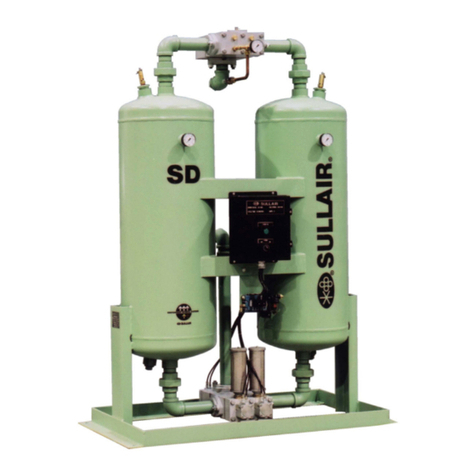
Sullair
Sullair SD Series User manual
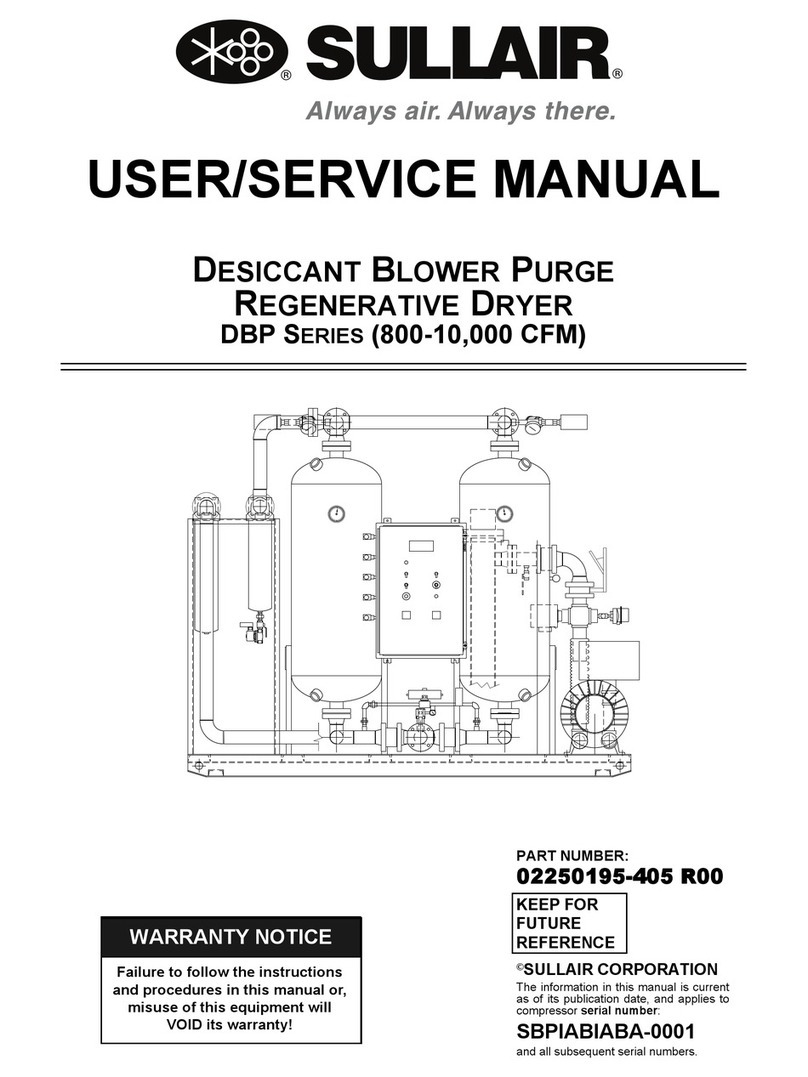
Sullair
Sullair DBP Series Troubleshooting guide
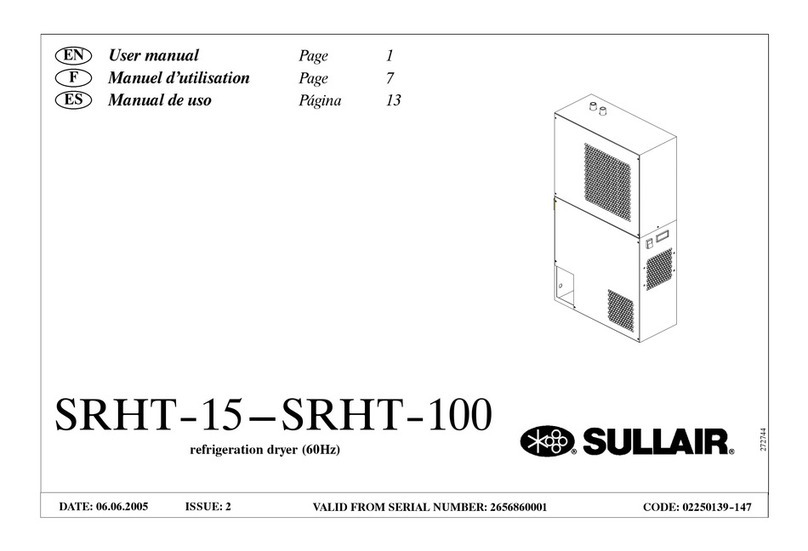
Sullair
Sullair SRHT-15 User manual

Sullair
Sullair SM1100 Installation and operating instructions
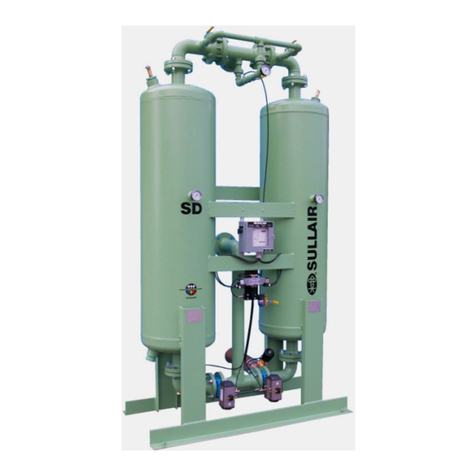
Sullair
Sullair SD-820 Series User manual