Sullair RC Series Troubleshooting guide

Failure to follow the instructions
and procedures in this manual or,
misuse of this equipement will
VOID its warranty!
WARRANTY NOTICE
PART NUMBER:
KEEP FOR
FUTURE
REFERENCE
USER/SERVICE MANUAL
©SULLAIR CORPORATION
The information in this manual is current
as of its publication date, and applies to
compressor serial number:
and all subsequent serial numbers.
02250195-402 R01
RC SERIES
REFRIGERATED CYCLING COMPRESSED AIR DRYER
150-3000 CFM
0711SA0250

AIR CARE SEMINAR TRAINING
Sullair Air Care Seminars are courses that provide hands-on instruction for the proper operation, maintenance,
and servicing of Sullair products. Individual seminars on Industrial compressors and compressor electrical
systems are offered at regular intervals throughout the year at Sullair’s corporate headquarters training facility
located at Michigan City, Indiana.
Instruction includes training on the function and installation of Sullair service parts, troubleshooting common
faults and malfunctions, and actual equipment operation. These seminars are recommended for maintenance,
contractor maintenance, and service personnel.
For detailed course outlines, schedule, and cost information contact:
SULLAIR TRAINING DEPARTMENT
1-888-SULLAIR or
219-879-5451 (ext. 5623)
www.sullair.com
- Or Write -
Sullair Corporation
3700 E. Michigan Blvd.
Michigan City, IN 46360
Attn: Service Training Department.

TABLE OF CONTENTS
SECTION 1—SAFETY INSTRUCTIONS
7 1.1 SAFETY REGULATIONS:
7 1.2 ISSUES TO AVOID
7 1.3 RECEIVING AND INSPECTION
8 1.4 TRANSPORTATION
8 1.5 INSTALLATION LAYOUT REQUIREMENTS
8 1.6 ENVIRONMENTAL PROTECTION
SECTION 2—INTRODUCTION
SECTION 3—SPECIFICATIONS
11 3.1 PRODUCT PICTURE / PRODUCT FINAL ASSEMBLY DRAWING
12 3.2 PRODUCT MODELS AND SPECIFICATIONS
SECTION 4—PRODUCT DESCRIPTION
15 4.1 PRODUCT FEATURES
SECTION 5—PRINCIPLE OF OPERATION
19 5.1 REFRIGERATION HEAT EXCHANGER
20 5.2 COMPRESSED AIR HEAT EXCHANGER
21 5.3 TYPICAL INSTALLATION DIAGRAM
21 5.4 PIPE/CONNECTION REQUIREMENTS
21 5.5 ELECTRICAL CONNECTION REQUIREMENTS
21 5.6 OPERATING PRECAUTIONS
22 5.7 INSTALLATION
23 5.8 OPERATING PROCEDURES
24 5.9 ED—RC 175
26 5.10 ED—RC 200
28 5.11 ED—RC 250
30 5.12 ED—RC 325
32 5.13 ED—RC 400
34 5.14 ED—RC 500

TABLE OF CONTENTS
36 5.15 ED—RC 700
38 5.16 ED—RC 700 WATER COOLED
40 5.17 ED—RC 850 AIR COOLED
42 5.18 ED—RC 850 WATER COOLED
44 5.19 ED—RC 1000 AIR COOLED
46 5.20 ED—RC 1000 WATER COOLED
48 5.21 ED—RC 1200 AIR COOLED
50 5.22 ED—RC 1200 WATER COOLED
52 5.23 ED—RC 1600 AIR COOLED
54 5.24 ED—RC 1600 WATER COOLED
56 5.25 ED—RC 2000 AIR COOLED
58 5.26 ED—RC 2000 WATER COOLED
60 5.27 ED—RC 2400 AIR COOLED
62 5.28 ED—RC 2400 WATER COOLED
64 5.29 ED—RC 3000 AIR COOLED
66 5.30 ED—RC 3000 WATER COOLED
68 5.31 P&I—RC150-850
70 5.32 P&I—RC400-850
72 5.33 P&I—RC1000-3000
74 5.34 P&I—RC1000-3000
75 5.35 P&I—RC1000-3000
76 5.36 ID—RC 175-200
78 5.37 ID—RC 250-400
80 5.38 ID—RC 500-850
82 5.39 ID—RC 1000-1200 AIR COOLED
83 5.40 ID—RC 1000-1200 WATER COOLED
84 5.41 ID—RC 1600-2000 AIR COOLED
85 5.42 ID—RC 1600-2000 WATER COOLED
86 5.43 ID—RC 2400-3000 AIR COOLED
87 5.44 ID—RC 2400-3000 WATER COOLED
88 5.45 WIRING DIAGRAM—CONTROL CIRCUIT RC 150 (110/120-1-50/60-A,
208/230-1-50/60-A)
90 5.46 WIRING DIAGRAM—POWER CIRCUIT RC 150 (110/120-1-50/60-A,
208/230-1-50/60-A)
92 5.47 WIRING DIAGRAM—CONTROL CIRCUIT RC 200 (208/230-1-50/60-A)
94 5.48 WIRING DIAGRAM—POWER CIRCUIT RC 200 (208/230-1-50/60-A)
96 5.49 WIRING DIAGRAM—CONTROL CIRCUIT RC 250 (208/230-1-50/60-A)
98 5.50 WIRING DIAGRAM—POWER CIRCUIT RC 250 (208/230-1-50/60-A)
100 5.51 WIRING DIAGRAM—CONTROL CIRCUIT RC 250/3000 (230-3-50/60-A,
400/460-3-50/60-A)
102 5.52 WIRING DIAGRAM—POWER CIRCUIT RC 250/3000 (230-3-50/60-A,
400/460-3-50/60-A)
104 5.53 WIRING DIAGRAM—RC 150-250 (115/220/1 50/60 AC)
106 5.54 WIRING DIAGRAM—RC 250-400 (230/3 60 AC)

TABLE OF CONTENTS
108 5.55 WIRING DIAGRAM—RC 250-400 (230/3 60 AC)
110 5.56 WIRING DIAGRAM—RC 250-400 (400/460/575/3 50/60 AC)
112 5.57 WIRING DIAGRAM—RC 250-400 (400/460/575/3 50/60 AC)
114 5.58 WIRING DIAGRAM—RC (500-1000) 230/60 AC
116 5.59 WIRING DIAGRAM—RC (500-1000) 230/60 AC
118 5.60 WIRING DIAGRAM—RC 500-3000 (400/460/575/3 50/60 AC)
120 5.61 WIRING DIAGRAM—RC 500-3000 (400/460/575/3 50/60 AC)
122 5.62 WIRING DIAGRAM—RC 700-3000 (400/460/575/3 50/60 AC)
124 5.63 WIRING DIAGRAM—RC RC 700-3000 (400/460/575/3 50/60 AC)
126 5.64 HOW TO CHANGE WATER / GYLICOL TEMPERATURE SET POINT:
SECTION 6—MAINTENANCE
127 6.1 MAINTENANCE BY AN ENGINEER/TECHNICIAN
127 6.2 MAINTENANCE BY THE USER
128 6.3 RECOMMENDED MAINTENANCE
130 6.4 REPLACEMENT PARTS
SECTION 7—TROUBLESHOOTING
SECTION 8—HORIZONTAL CLOSE COUPLED PUMP
155 8.1 GENERAL INSTRUCTIONS
157 8.2 SERVICE
161 8.3 PARTS AND REPAIR SERVICES
161 8.4 LIMITED WARRANTY
163 8.5 INSTALLATION NOTES

TABLE OF CONTENTS

Section 1
7
SAFETY INSTRUCTIONS
SAFETY INSTRUCTIONS
1.1 SAFETY REGULATIONS:
1. When operating the air dryer, the operator
must adopt safe working methods and
observe all local safety instructions and rele-
vant regulations.
2. Prior to installation, the dryer and the com-
pressed air system are to be depressurized
and disconnected from the electrical main
supply.
3. The user is responsible for safe operating
conditions. Parts and accessories must be
replaced if inspection shows that it is unsafe
to operate the dryer.
4. Installation, operation, maintenance and
repair are only to be performed by autho-
rized, trained and skilled technicians.
5. The minimum and maximum values listed on
the data label must be strictly followed. If
your application does not fall within the
parameters indicated on the data label—
STOP. Contact your Sullair representative/
distributor and clarify the issue before pro-
ceeding or operating the dryer.
6. All safety procedures and practices men-
tioned in this manual must be observed, as
well as all of the federal, state and local
safety precautions.
7. If any statement in this manual does not
comply with the local legislation, the stron-
gest standard is to be applied.
1.2 ISSUES TO AVOID
1. Any structural changes made to the dryer
without the advise of Sullair or Sullair repre-
sentatives will void all warranty.
2. Compressed air from this dryer does not
meet the OSHA standards for breathing and
hence it should not be used for breathing
purposes.
None of the protective alarms, equipment or
devices should be tampered with. These pro-
tective items have been designed and
installed on this dryer for your safety.
3. Do not operate the dryer at pressures, tem-
peratures of flow other than the ones men-
tioned on the data label.
1.3 RECEIVING AND
INSPECTION
Sullair dryers are factory tested prior to shipment.
However, during shipment, there are chances that
the dryer was mishandled or certain parts were
broken or might have come loose. In order to ensure
that the dryer you have received is fit for installation
and operation, we recommend you take a few
minutes to inspect the dryer for any physical abuse
or damage during shipment.
If you notice any damage to the shipment, we
recommend you take the following steps to ensure
proper arrangements can be made to address the
issue.
1. Immediately file a complaint with the ship-
ping company.
2. Contact Sullair or Sullair distributor and
inform them of the damage. (Email or fax the
copy of the shipper claim and acknowledge-
ment)
If there is no physical damage to the dryer—
1. Remove all the crating and packaging.
2. Inspect the dryer for electrical and piping
connection and make sure that they are all
tight.
3. Check the data label, your packing slip and
make sure that it is the correct unit you had
ordered.
4. Follow the recommended safety procedures
and get the dryer ready for installation.

8
NOTES
1.4 TRANSPORTATION
1. Use care and caution when transporting the
dryer. Avoid sudden jerks, tilting, dropping
and other physical abuse.
2. A forklift can be used to transport the dryer
provided the forks are long enough to sup-
port the full width or length. Caution must be
used throughout the move.
1.5 INSTALLATION LAYOUT
REQUIREMENTS
1. The dryer must be installed horizontally. A
minimum of at least 1 ½ feet clearance
around the dryer is necessary to allow free
air circulation and easy access for servicing.
2. The ambient temperature in the room
should not exceed 120° F and should not
be below 40° F, taking into account the
heat radiated by the dryer. (About 18 watts
for each SCFM under ISO 7183-5 condition
or 40 watt for each liter/sec under ISO 7183-
A condition).
1.6 ENVIRONMENTAL
PROTECTION
1. US/EU laws protect the environment against
refrigerant being released into the atmo-
sphere.
2. An annual leak control test at less than 5.0
gr/year should be performed by a qualified
engineer if the refrigerant dryer contains
more than 4.4 lbs/ 2 kg of refrigerant. This
control test has to be done twice a year if the
dryer contains more than 66 lbs/30 kg.
3. Prior to dryer disposal, the refrigerant must
be properly recovered by a qualified engi-
neer.

Section 2
9
INTRODUCTION
INTRODUCTION
The Sullair Cycling Refrigerated air dryers are
designed for constant full load operation. They use
specially designed heat exchangers with integrated
components to provide consistent dewpoint and
trouble-free service for years to come.
The dryers remove the moisture, oil vapors and other
harmful contaminants from the compressed air
stream. By using basic refrigeration, the hot
saturated air is cooled in the highly efficient heat-
exchangers and the moisture is condensed and
removed. Additional filtration eliminates other
contaminants and particles.
Water (moisture) is one of the greatest enemies of air
tools and piping. Left untreated in the compressed air
stream, this moisture will deteriorate the tools,
equipment and piping with corrosion, pipe scaling,
freezing and a host of other problems that will
diminish the life of your entire compressed air
system. With a Sullair refrigerant dryer, you can be
assured of clean, dry air with consistent dewpoint
between 36 ~ 40 Deg. F. The unique three-in-one
heat exchanger combination -
•Air to Air—
Pre-cooler/re-heater Heat Exchanger
•Air to Refrigerant—
High efficiency Heat Exchanger
•Integrated Separator—
Located at the coldest point to maximize
moisture extraction
heats up the exiting air, thereby eliminating the
chances of freezing even in relatively cooler ambient
conditions. Warm dry air will not affect the piping nor
the tools and the result is extended tool life. In
addition, applications that require clean dry air can
rely upon Sullair’s cycling refrigerated air dryers to
provide dry air at full load continuously.

10
NOTES

Section 3
11
SPECIFICATIONS
SPECIFICATIONS
Pay attention to the Minimum and Maximum operating conditions before installing and operating the dryer.
If your application does not match the above criteria, contact your Sullair distributor and they will be able to
provide the right dryer for your application.
3.1 PRODUCT PICTURE / PRODUCT FINAL ASSEMBLY DRAWING
Normal Operating Pressure 100 PSIG
Normal Operating Temperature 100 Deg. F
Normal Ambient Temperature 100 Deg. F
Maximum Operating Pressure 230 PSIG
Minimum Operating Pressure 75 PSIG
Maximum Ambient Temperature 120 Deg. F
Minimum Ambient Temperature 40 Deg. F
Maximum Operating Temperature 150 Deg. F

12
NOTES
3.2 PRODUCT MODELS AND SPECIFICATIONS
Cycling RC 60 02250193-793 DRYER, RC150CFM, 115/1/60-AC RC-0150-115-1-60-A 115/1/60 A
Cycling RC 50 02250193-864 DRYER, RC150CFM, 220/1/50-AC RC-0150-220-1-50-A 220/1/50 A
Cycling RC 60 02250193-820 DRYER, RC150CFM, 208-230/1/60-AC RC-0150-230-1-60-A 208-230/1/60 A
Cycling RC 50 02250193-865 DRYER, RC175CFM, 220/1/50-AC RC-0175-220-1-50-A 220/1/50 A
Cycling RC 60 02250193-821 DRYER, RC175CFM, 208-230/1/60-AC RC-0175-230-1-60-A 208-230/1/60 A
Cycling RC 50 02250193-866 DRYER, RC200CFM, 220/1/50-AC RC-0200-220-1-50-A 220/1/50 A
Cycling RC 60 02250193-822 DRYER, RC200CFM, 208-230/1/60-AC RC-0200-230-1-60-A 208-230/1/60 A
Cycling RC 50 02250193-867 DRYER, RC250CFM, 220/1/50-AC RC-0250-220-1-50-A 220/1/50 A
Cycling RC 60 02250193-823 DRYER, RC250CFM, 230/3/60-AC RC-0250-230-3-60-A 230/3/60 A
Cycling RC 50 02250193-904 DRYER, RC250CFM, 400/3/50-AC RC-0250-400-3-50-A 400/3/50 A
Cycling RC 60 02250193-963 DRYER, RC250CFM, 460/3/60-AC RC-0250-460-3-60-A 460/3/60 A
Cycling RC 60 02250194-121 DRYER, RC250CFM, 575/3/60-AC RC-0250-575-3-60-A 575/3/60 A
Cycling RC 60 02250193-824 DRYER, RC325CFM, 230/3/60-AC RC-0325-230-3-60-A 230/3/60 A
Cycling RC 50 02250193-905 DRYER, RC325CFM, 400/3/50-AC RC-0325-400-3-50-A 400/3/50 A
Cycling RC 60 02250193-964 DRYER, RC325CFM, 460/3/60-AC RC-0325-460-3-60-A 460/3/60 A
Cycling RC 60 02250194-122 DRYER, RC325CFM, 575/3/60-AC RC-0325-575-3-60-A 575/3/60 A
Cycling RC 60 02250193-825 DRYER, RC400CFM, 230/3/60-AC RC-0400-230-3-60-A 230/3/60 A
Cycling RC 60 02250193-854 DRYER, RC400CFM, 230/3/60-WC RC-0400-230-3-60-W 230/3/60 W
Cycling RC 50 02250193-906 DRYER, RC400CFM, 400/3/50-AC RC-0400-400-3-50-A 400/3/50 A
Cycling RC 50 02250193-930 DRYER, RC400CFM, 400/3/50-WC RC-0400-400-3-50-W 400/3/50 W
Cycling RC 60 02250193-965 DRYER, RC400CFM, 460/3/60-AC RC-0400-460-3-60-A 460/3/60 A
Cycling RC 60 02250193-996 DRYER, RC400CFM, 460/3/60-WC RC-0400-460-3-60-W 460/3/60 W
Cycling RC 60 02250194-123 DRYER, RC400CFM, 575/3/60-AC RC-0400-575-3-60-A 575/3/60 A
Cycling RC 60 02250194-150 DRYER, RC400CFM, 575/3/60-WC RC-0400-575-3-60-W 575/3/60 W
Cycling RC 60 02250193-826 DRYER, RC500CFM, 230/3/60-AC RC-0500-230-3-60-A 230/3/60 A
Cycling RC 60 02250193-855 DRYER, RC500CFM, 230/3/60-WC RC-0500-230-3-60-W 230/3/60 W
Cycling RC 50 02250193-907 DRYER, RC500CFM, 400/3/50-AC RC-0500-400-3-50-A 400/3/50 A
Cycling RC 50 02250193-932 DRYER, RC500CFM, 400/3/50-WC RC-0500-400-3-50-W 400/3/50 W
Cycling RC 60 02250193-966 DRYER, RC500CFM, 460/3/60-AC RC-0500-460-3-60-A 460/3/60 A
Cycling RC 60 02250193-997 DRYER, RC500CFM, 460/3/60-WC RC-0500-460-3-60-W 460/3/60 W
Cycling RC 60 02250194-124 DRYER, RC500CFM, 575/3/60-AC RC-0500-575-3-60-A 575/3/60 A
Cycling RC 60 02250194-151 DRYER, RC500CFM, 575/3/60-WC RC-0500-575-3-60-W 575/3/60 W
Cycling RC 60 02250193-827 DRYER, RC700CFM, 230/3/60-AC RC-0700-230-3-60-A 230/3/60 A
Cycling RC 60 02250193-856 DRYER, RC700CFM, 230/3/60-WC RC-0700-230-3-60-W 230/3/60 W
Cycling RC 50 02250193-908 DRYER, RC700CFM, 400/3/50-AC RC-0700-400-3-50-A 400/3/50 A
Cycling RC 50 02250193-933 DRYER, RC700CFM, 400/3/50-WC RC-0700-400-3-50-W 400/3/50 W
Cycling RC 60 02250193-967 DRYER, RC700CFM, 460/3/60-AC RC-0700-460-3-60-A 460/3/60 A
Cycling RC 60 02250193-998 DRYER, RC700CFM, 460/3/60-WC RC-0700-460-3-60-W 460/3/60 W
Cycling RC 60 02250194-125 DRYER, RC700CFM, 575/3/60-AC RC-0700-575-3-60-A 575/3/60 A
Cycling RC 60 02250194-152 DRYER, RC700CFM, 575/3/60-WC RC-0700-575-3-60-W 575/3/60 W
Cycling RC 60 02250193-828 DRYER, RC850CFM, 230/3/60-AC RC-0850-230-3-60-A 230/3/60 A
Cycling RC 60 02250193-858 DRYER, RC850CFM, 230/3/60-WC RC-0850-230-3-60-W 230/3/60 W
Cycling RC 50 02250193-909 DRYER, RC850CFM, 400/3/50-AC RC-0850-400-3-50-A 400/3/50 A
Cycling RC 50 02250193-934 DRYER, RC850CFM, 400/3/50-WC RC-0850-400-3-50-W 400/3/50 W

SECTION 3 SPECIFICATIONS
13
Cycling RC 60 02250193-968 DRYER, RC850CFM, 460/3/60-AC RC-0850-460-3-60-A 460/3/60 A
Cycling RC 60 02250193-999 DRYER, RC850CFM, 460/3/60-WC RC-0850-460-3-60-W 460/3/60 W
Cycling RC 60 02250194-126 DRYER, RC850CFM, 575/3/60-AC RC-0850-575-3-60-A 575/3/60 A
Cycling RC 60 02250194-153 DRYER, RC850CFM, 575/3/60-WC RC-0850-575-3-60-W 575/3/60 W
Cycling RC 60 02250193-829 DRYER, RC1000CFM, 230/3/60-AC RC-1000-230-3-60-A 230/3/60 A
Cycling RC 60 02250193-859 DRYER, RC1000CFM, 230/3/60-WC RC-1000-230-3-60-W 230/3/60 W
Cycling RC 50 02250193-910 DRYER, RC1000CFM, 400/3/50-AC RC-1000-400-3-50-A 400/3/50 A
Cycling RC 50 02250193-935 DRYER, RC1000CFM, 400/3/50-WC RC-1000-400-3-50-W 400/3/50 W
Cycling RC 60 02250193-969 DRYER, RC1000CFM, 460/3/60-AC RC-1000-460-3-60-A 460/3/60 A
Cycling RC 60 02250194-100 DRYER, RC1000CFM, 460/3/60-WC RC-1000-460-3-60-W 460/3/60 W
Cycling RC 60 02250194-127 DRYER, RC1000CFM, 575/3/60-AC RC-1000-575-3-60-A 575/3/60 A
Cycling RC 60 02250194-154 DRYER, RC1000CFM, 575/3/60-WC RC-1000-575-3-60-W 575/3/60 W
Cycling RC 50 02250193-911 DRYER, RC1200CFM, 400/3/50-AC RC-1200-400-3-50-A 400/3/50 A
Cycling RC 50 02250193-936 DRYER, RC1200CFM, 400/3/50-WC RC-1200-400-3-50-W 400/3/50 W
Cycling RC 60 02250193-970 DRYER, RC1200CFM, 460/3/60-AC RC-1200-460-3-60-A 460/3/60 A
Cycling RC 60 02250194-101 DRYER, RC1200CFM, 460/3/60-WC RC-1200-460-3-60-W 460/3/60 W
Cycling RC 60 02250194-128 DRYER, RC1200CFM, 575/3/60-AC RC-1200-575-3-60-A 575/3/60 A
Cycling RC 60 02250194-155 DRYER, RC1200CFM, 575/3/60-WC RC-1200-575-3-60-W 575/3/60 W
Cycling RC 50 02250193-912 DRYER, RC1600CFM, 400/3/50-AC RC-1600-400-3-50-A 400/3/50 A
Cycling RC 50 02250193-937 DRYER, RC1600CFM, 400/3/50-WC RC-1600-400-3-50-W 400/3/50 W
Cycling RC 60 02250193-971 DRYER, RC1600CFM, 460/3/60-AC RC-1600-460-3-60-A 460/3/60 A
Cycling RC 60 02250194-102 DRYER, RC1600CFM, 460/3/60-WC RC-1600-460-3-60-W 460/3/60 W
Cycling RC 60 02250194-129 DRYER, RC1600CFM, 575/3/60-AC RC-1600-575-3-60-A 575/3/60 A
Cycling RC 60 02250194-156 DRYER, RC1600CFM, 575/3/60-WC RC-1600-575-3-60-W 575/3/60 W
Cycling RC 50 02250193-913 DRYER, RC2000CFM, 400/3/50-AC RC-2000-400-3-50-A 400/3/50 A
Cycling RC 50 02250193-938 DRYER, RC2000CFM, 400/3/50-WC RC-2000-400-3-50-W 400/3/50 W
Cycling RC 60 02250193-972 DRYER, RC2000CFM, 460/3/60-AC RC-2000-460-3-60-A 460/3/60 A
Cycling RC 60 02250194-103 DRYER, RC2000CFM, 460/3/60-WC RC-2000-460-3-60-W 460/3/60 W
Cycling RC 60 02250194-130 DRYER, RC2000CFM, 575/3/60-AC RC-2000-575-3-60-A 575/3/60 A
Cycling RC 60 02250194-157 DRYER, RC2000CFM, 575/3/60-WC RC-2000-575-3-60-W 575/3/60 W
Cycling RC 50 02250193-914 DRYER, RC2400CFM, 400/3/50-AC RC-2400-400-3-50-A 400/3/50 A
Cycling RC 50 02250193-939 DRYER, RC2400CFM, 400/3/50-WC RC-2400-400-3-50-W 400/3/50 W
Cycling RC 60 02250193-973 DRYER, RC2400CFM, 460/3/60-AC RC-2400-460-3-60-A 460/3/60 A
Cycling RC 60 02250194-104 DRYER, RC2000CFM, 460/3/60-WC RC-2400-460-3-60-W 460/3/60 W
Cycling RC 60 02250194-131 DRYER, RC2400CFM, 575/3/60-AC RC-2400-575-3-60-A 575/3/60 A
Cycling RC 60 02250194-158 DRYER, RC2400CFM, 575/3/60-WC RC-2400-575-3-60-W 575/3/60 W
Cycling RC 50 02250193-915 DRYER, RC3000CFM, 400/3/50-AC RC-3000-400-3-50-A 400/3/50 A
Cycling RC 50 02250193-940 DRYER, RC3000CFM, 400/3/50-WC RC-3000-400-3-50-W 400/3/50 W
Cycling RC 60 02250193-974 DRYER, RC3000CFM, 460/3/60-AC RC-3000-460-3-60-A 460/3/60 A
Cycling RC 60 02250194-105 DRYER, RC3000CFM, 460/3/60-WC RC-3000-460-3-60-W 460/3/60 W
Cycling RC 60 02250194-132 DRYER, RC3000CFM, 575/3/60-AC RC-3000-575-3-60-A 575/3/60 A
Cycling RC 60 02250194-159 DRYER, RC3000CFM, 575/3/60-WC RC-3000-575-3-60-W 575/3/60 W

14
NOTES

Section 4
15
PRODUCT DESCRIPTION
PRODUCT DESCRIPTION
This refrigerated compressed air dryer has been
designed to remove water vapor from industrial
compressed air that is free of any aggressive
contaminants like ammonia, gaseous acid, dust, rust,
liquid condensate, any other chemical or mineral
substances capable of attacking or clogging the heat
exchanger(s).
The optional, water-cooled condenser is not
designed for use with seawater or water containing
aggressive contaminants.
Please contact your factory representative for further
questions on this issue. This dryer has been
designed for indoor operation only.
The minimum and maximum values stated must be
observed, as well as the safety precautions
described in this manual.
4.1 PRODUCT FEATURES
4.1.1 REFRIGERANT COMPRESSOR
The refrigerant compressor is fully hermetically
sealed and requires no maintenance.
4.1.2 CONDENSER
1. Air cooled models: The refrigerant con-
denser is equipped with fans that are cycled
on and off to maintain a minimum high side
pressure.
2. Water-cooled dryers Utilize a water control
valve piloted by a sensing bulb that reacts to
the high side refrigerant pressure control-
ling the water flow Maintain a minimum high
side pressure.
4.1.3 REFRIGERANT CIRCUIT PROTECTION
1. Overload protector:
Single phase compressors are equipped
with an overload protector which is a current/
temperature switch that reacts to the motor
winding amps and temperature of the com-
pressor motor. When the switch detects a
high current or a high temperature condition
with the compressor motor it opens causing
loss of voltage to the compressor. This
switch automatically resets as the motor
cools down to a factory preset temperature.
This cool down period can take as long as 8
hours. A waRCing lamp will light to indicate
that the protector has tripped.
2. High/Low pressure safety switch:
Refrigerant circuits are protected against
excessive pressure by a safety switch that
stops the compressor in cases of high or low
refrigerant pressure. If this safety switch has
tripped out on high refrigerant pressure, it
has to be manually reset before the dryer
can be restarted. A low pressure trip will
automatically reset
4.1.4 FILTER DRYER
Total water removal in the refrigerant circuit is
achieved by a filter dryer who also traps any solid
particles that may have migrated into the circuit
during assembly.
4.1.5 CRANKCASE HEATER
3-Phase dryers are equipped with an electric
crankcase heater. The heater provides preliminary
pre-heating of the refrigerant compressor to
evaporate liquid refrigerant possibly condensed in
the crankcase. This will prevent liquid shock that can
damage the compressor.

PRODUCT DESCRIPTION SECTION 4
16
4.1.6 REFRIGERANT CIRCUIT REGULATION IN
RC-0150 – RC-3000
1. The liquid refrigerant is injected into the
evaporator through a metering device trying
to maintain the refrigerant in the evaporator
at a constant pressure
2. The evaporating pressure is kept constant by
a controlled injection of hot gas from the
high-pressure side into the low-pressure
section of the circuit through a hot gas by-
pass valve. This constant pressure corre-
sponds to a stable evaporating temperature
adjusted as close to 32 Deg. F as possible.
3. The mixture of hot gas from the by-pass
valve and cold gas from the evaporator is
called superheat and is adjusted at (50 ± 5)
Deg. F
4.1.7 CONDENSATE DRAIN - TRAP
ASSEMBLY
Dismantling the drain is easy because it can be
isolated from the air circuit under pressure with a ball
valve. Always isolate the drain before disassembly.
4.1.8 HEAT EXCHANGER, MODULAR DESIGN
The dryers are equipped with compact, modular
design heat exchangers. This assembly has been
specially designed to dry compressed air and
consists of:
1. An air/air heat exchanger which pre-cools
the entering hot air with the exiting chilled air.
2. An evaporator which is an air/refrigerant heat
exchanger which cools down the com-
pressed air
3. An integral separator that separates the
moisture from the air stream at the coldest
point. Maximum condensation of moisture
occurs at the coldest point and it is at that
exact junction that the moisture is removed
and drained.
4.1.9 ELECTRONIC CONTROL PANEL
It is important to note that when changing the
controller’s reading from C to F or F to C the
technician must change all of the parameters. The
controller program lists each temperature setting one
at a time for programming. The last parameter is the
displayed reading. Once the controller is set to read
either C or F it will then read all of the parameter
settings as that scale.
Example: The AStL (low glycol temp set point) is set
from the factory at 1◦C.
The technician changes the scale from Centigrade to
Fahrenheit.
The AStL parameter will now read 1◦F.
The dryer will now try to pull the glycol temperature
down to 1◦F causing the dryer to freeze.
The AStL parameter will now need to reset to 28
which will be read by the controller as 28◦F.

SECTION 4 PRODUCT DESCRIPTION
17
PROCEDURE TO CHANGE THE CONTROLLER FROM
CENTIGRADE TO FAHRENHEIT:
The controller is password protected. Press the Enter
and the Star key at the same time to display
the password screen. Use the Up arrow to
display the number 10 and press Enter .
The first parameter is AStL (Alarm ; Low glycol
temperature set point). AStL will flash on the screen
and then the current value will be displayed. Use the
Up arrow to change the value to 28 (28◦F). Press
the Enter button.
The second parameter is AStH (Alarm; High glycol
temperature set point). AStH will flash quickly on the
display and then show the current setting. Use the
Up arrow to change the value to 58 (58◦F). Press
Enter to move to the next parameter.
The next parameter is SEtL (Set point; low glycol
temperature). SEtL will display for about one second
and then the current value will be displayed. Use the
Up arrow to change the value to 28 (28◦F). Press
Enter to accept this value and move to the next
parameter.
The fourth parameter is SEtH (Set point; high glycol
temperature). SEtH will display quickly on then the
current parameter value will be displayed. Use the
Up arrow to change this value to 36 (36◦F). Press
the Enter button to accept the setting and move
to the next parameter.
The fifth parameter is SFt (calibration setting). This
parameter should be set at 0. This parameter is only
used for calibration of the temperature probe. Press
Enter .
The sixth parameter is UNt (Units). UNt will display
then quickly show the current value. 0 is for
Centigrade and 1 is for Fahrenheit. Press Enter
to accept the value.
The display will now roll back to the first parameter
(AStL).
Use the Star key to exit the program mode.
PROCEDURE TO CHANGE THE CONTROLLER FROM
FAHRENHEIT TO CENTIGRADE:
Use the above procedure to change the values at
each parameter. The list below will give you the
settings needed to operate in a Centigrade scale.
AStL: -4
AStH:14
SEtL:-2
SEtH: 2
SFt:0
UNt:0
Press Star to exit the programming mode.

18
NOTES

Section 5
19
PRINCIPLE OF OPERATION
PRINCIPLE OF OPERATION
The refrigerant circuit can be divided in 3 parts:
1. Low pressure section with an evaporator
(heat exchanger)
2. High pressure section including: Condenser,
liquid receiver, (if installed) and the filter
dryer.
3. Control circuit including: Compressor, meter-
ing device, hot gas by-pass valve (if
installed), fan pressure switch, safety high/
low pressure switch. Water cooled dryers are
equipped with a water flow control valve.
5.1 REFRIGERATION HEAT
EXCHANGER
1. There are two (2) basic sections, commonly
referred to as the high and low-pressure sec-
tions, in a refrigeration circuit. The high side
begins at the refrigerant compressor dis-
charge port and ends at the expansion
devise. The circuit leaving the expansion
devise through the air to refrigerant heat
exchanger and up to the compressor suction
port is known as the low pressure circuit. The
compressor takes in low pressure refrigerant
gas and compresses it to a high pressure
and high temperature gas. The high temper-
ature gas passes into the refrigerant con-
denser where it is cooled and liquefied. The
refrigerant then passes through the filter
dryer where moisture and any foreign parti-
cles are removed. The refrigerant then
passes through an expansion device where
the liquid refrigerant is throttled and a tem-
perature drop will occur as part of the liquid
turns into gas. The cold refrigerant gas and
liquid then enters the refrigerant-to-glycol
heat exchanger where it absorbs the heat
from the glycol as it evaporates. The low-
pressure refrigerant gas returns to the com-
pressor for repetition of the process.
2. Glycol Side: The thermal mass is food safe
and environmentally friendly polypropylene
glycol solution. It is pumped continuously
through the heat exchangers to eliminate
any dew point fluctuations commonly found
in other cycling dryers. The glycol is stored in
a stainless steel insulated tank with welded
connections. The glycol flows through the
pump to the Air-to-Glycol chamber located in
what is commonly termed as the heat
exchanger where it cools the compressed air
by counter flow. From there, it travels to the
evaporator where heat is extracted out by
the refrigerant. The heat saturated glycol
then returns to the storage tank. A tempera-
ture probe in the tank monitors the tempera-
ture and turns off the compressor when the
glycol reaches its set point. A float switch
inside the glycol tank shuts off the unit if the
glycol level drops below the minimum height.
3. Refrigerant controls: High-low refrigerant
cut-out switch senses high and low refriger-
ant pressure at refrigerant compressor inlet
and outlet ports shutting the compressor
down in the event of high refrigerant dis-
charge pressures or low refrigerant suction
pressure.
4. Liquid line filter dryer: Filters refrigerant of
moisture and any foreign particles. Must be
replaced if the refrigerant system has been
opened causing exposure to atmospheric
pressures.
5. Expansion device: Meters refrigerant flow in
the evaporator.
6. Electronic drain valve: An electronic drain
valve on the separator is designed to open
and close automatically to drain away con-
densate.
7. Crank case heater: A safety device which
prevents refrigerant migration back to the
compressor during shutdown.
8. Air cooled models Cooling air flows from the
front to the back of the dryer. Air must be
drawn from a clean source in order to reduce

PRINCIPLE OF OPERATION SECTION 5
20
dust and dirt accumulation on the condenser
coils. Air temperature should not exceed
110ºF(43ºC). A clearance of 24 inches (61
cm)
9. Fan motor and compressor rotation: This unit
has been equipped with a phase sensing
controller. If the unit will not start please
reverse any two of the three phases and
restart the unit. Cooling air should exhaust
through the condenser coils away from the
fan motors.
5.2 COMPRESSED AIR HEAT
EXCHANGER
AIR TO AIR SIDE
1. Pre cooling: Warm, saturated compressed
air enters the air-to-air heat exchanger,
where it is cooled by the outgoing cooled
compressed air flowing in a counter flow
direction.
2. Pre-separation: As the air is pre-cooled,
some of the moisture condenses. During this
phase, all condensed moisture and oil is
separated from the compressed air.
3. Thermal Mass: The air then enters and is fur-
ther cooled in the refrigeration air to glycol
chamber. The air stream is cooled to 35-39ºF
(1.6-3.8ºC), reducing its dew point to this
temperature.
4. Separation: As the air is cooled in the air to
glycol chamber, the moisture condenses into
a liquid. At this point, all liquid, passing
through the separator is removed from the
air stream and drained away with an elec-
tronic drain
5. Recuperation: The cold, dry air is reheated
by incoming warm air as it passes back
through the air to air heat exchanger in a
counter flow direction.
This manual suits for next models
15
Table of contents
Other Sullair Dehumidifier manuals
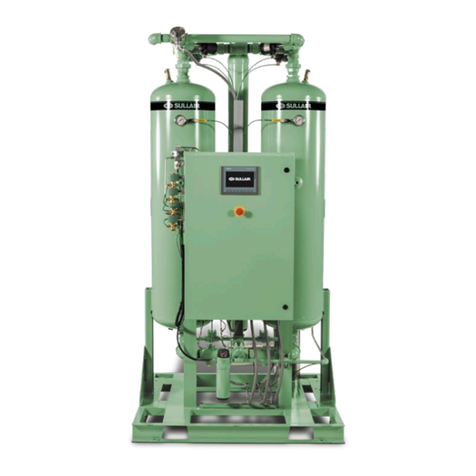
Sullair
Sullair DHL-80 Troubleshooting guide

Sullair
Sullair SD Series User manual
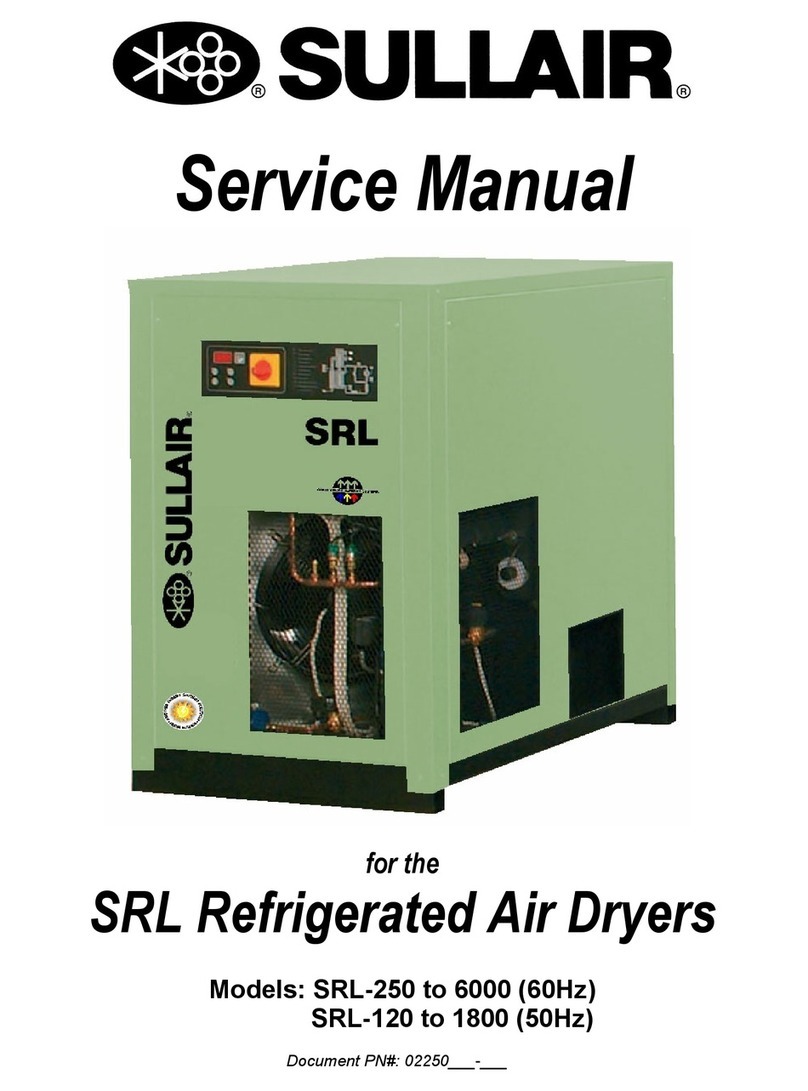
Sullair
Sullair SRL Series User manual
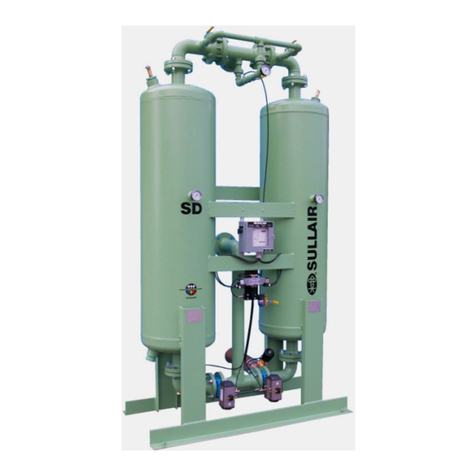
Sullair
Sullair SD-820 Series User manual
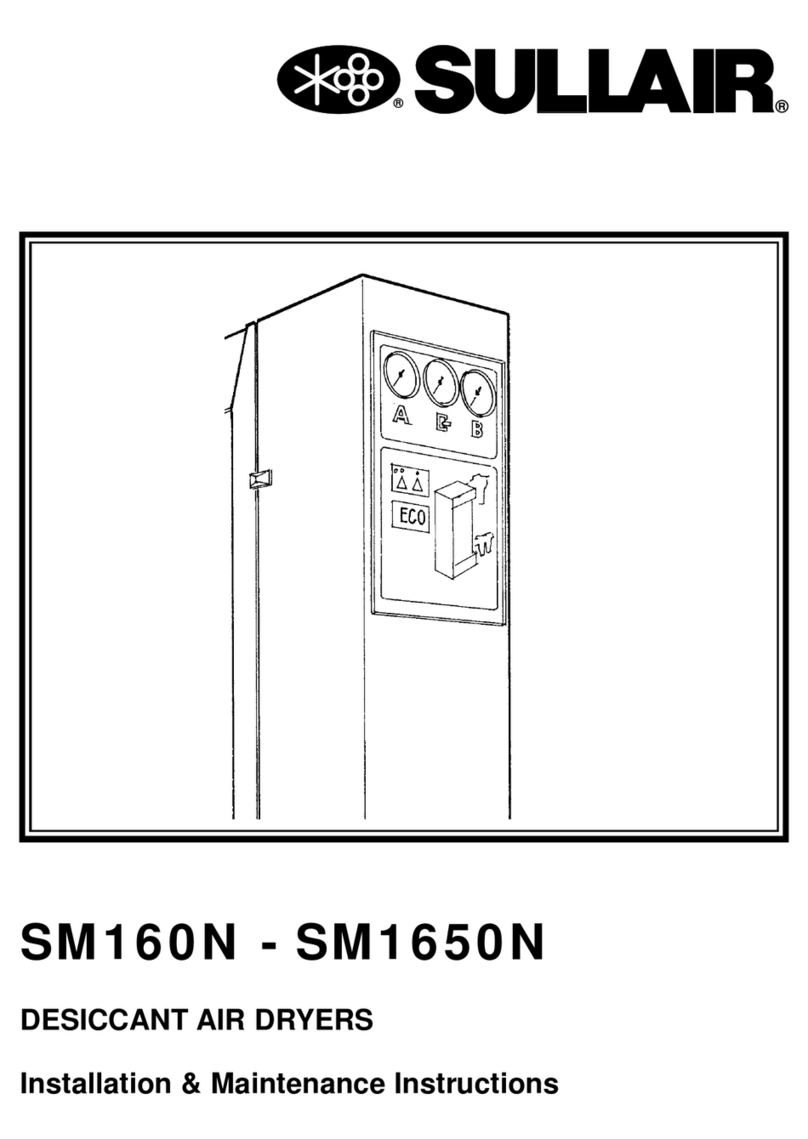
Sullair
Sullair SM-160N Installation and operating instructions

Sullair
Sullair SR 10 AC User manual

Sullair
Sullair SAR024 User manual
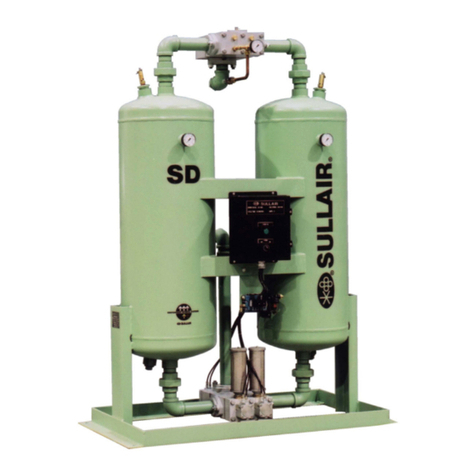
Sullair
Sullair SD Series User manual
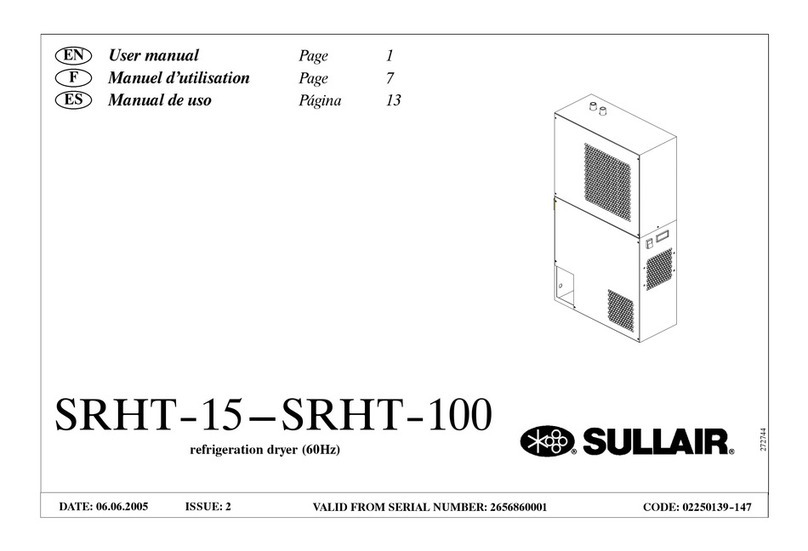
Sullair
Sullair SRHT-15 User manual
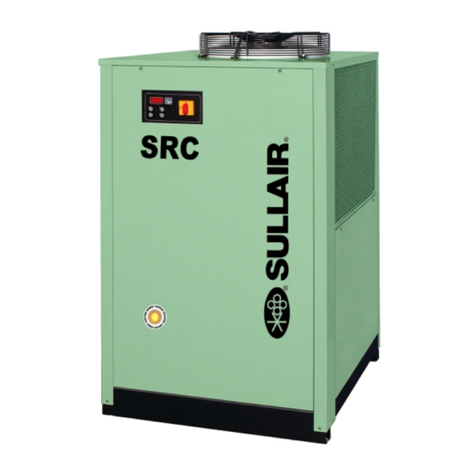
Sullair
Sullair SRC User manual