Sumake SMT-30A User manual

OPERATION AND MAINTENANCE MANUAL
ITEM NO.: SMT-30A, SMT-50A, SMT-70A
SMT-120A, SMT-180A, SMT-250A
TRANSDUCERIZED DC ANGLE DC40V
BRUSHLESS ELECTRIC SCREWDRIVER
SMT-30A, SMT-50A, SMT-70A
SMT-120A, SMT-180A
SMT-250A
SMT-30(50)(70)(120)(180)(250)A-I-2309C-K2

1
※Specification
* 1N.m=10.2Kgf.cm 1N.m=8.85Lbf.in
*Accessories
1. BIT Type:
No. 00 ... Bit use in dia 1.3~1.8mm screw
No. 0... .Bit use in dia 1.8~2.0mm screw
No. 1... .Bit use in dia 2.0~2.6mm screw
No. 2.. ..Bit use in dia 3.0~4.0mm screw
2. SMT-30A with BIT 2# 2 Pcs.
SMT-50A with BIT 2# 2 Pcs.
SMT-70A with BIT 2# & 3# 1 Pcs. Each
SMT-30(50)(70)A W Type Not attached Socket
MODEL
SMT-30A
SMT-50A
SMT-70A
Input Voltage (DC)
DC40V
Power Consumption
90W
Torque
(N.m)
0.6-3
1-5
1.4-7
(kgf.cm)
6.11-30.59
10.2-51.00
14.27-71.39
(Lbf.in)
5.31-26.55
8.85-44.25
12.39-61.96
Repeatable Torque Accuracy
+/- 3sigma / AVG., 7.5%
Unloaded Rotation Speed (r/min)
Can be set and adjusted
120-1100
80-800
50-450
Working Time
1s ON / 3s OFF
Weight (g)
1150
Length (mm)
330
Power Controller
SMT-C1
Software
N-DAS
EAA-AMS
Bit Type
B9.5
W 3/8"sq
B9.5
W 3/8"sq
B9.5
W 3/8"sq

2
※Specification
* 1N.m=10.2Kgf.cm 1N.m=8.85Lbf.in
*Accessories
1. BIT Type:
No. 00 ... Bit use in dia 1.3~1.8mm screw
No. 0... .Bit use in dia 1.8~2.0mm screw
No. 1... .Bit use in dia 2.0~2.6mm screw
No. 2.. ..Bit use in dia 3.0~4.0mm screw
2. SMT-120A with BIT 3# 2 Pcs.
SMT-180A with BIT 3# 2 Pcs.
SMT-250A with BIT 3# 2 Pcs.
SMT-120(180)(250)A W Type Not attached Socket
MODEL
SMT-120A
SMT-180A
SMT-250A
Input Voltage (DC)
DC40V
Power Consumption
90W
Torque
(N.m)
2.4-12
3.6-18
5-25
(kgf.cm)
24.48-122.4
36.72-183.6
51-255
(Lbf.in)
21.24-106.21
31.86-159.32
44.26-221.28
Repeatable Torque Accuracy
+/- 3sigma / AVG., 7.5%
Unloaded Rotation Speed (r/min)
Can be set and adjusted
100-1000
60-600
40-400
Working Time
1s ON / 3s OFF
Weight (g)
2230
2810
Length (mm)
393
439
Power Controller
SMT-C1B
Software
N-DAS
EAA-AMS
Bit Type
B9.5
W 3/8"sq
B9.5
W 3/8"sq
B9.5
W 3/8"sq

3
Metal Assembly sensor screwdriver are designed for installing threaded fasteners in light industrial and appliance manufacturing
applications.
SUMAKE is not responsible for customer modification of tools for applications on which SUMAKE was not consulted.
Important safety information enclosed.
Read all these instructions before placing tool in service or operation this tool and save these instructions. It is the responsibility of the
employer to place the information in this manual into the hands of the operator. Failure to observe the following warnings could result
in injury. When using electric tools, Basic safety precautions should always be followed to reduce the risk of fire, electric shock and
personal injury, including the following:
WARNING
NOTICE

4
WARNING! Read all instructions Failure to follow all instructions listed below may result in electric shock fire and/or serious
injury. The term “power tool” in all of the warning listed below refer to your mains operated (corded) power tool or battery operated
(cordless) power tool.
SAVE THIS INSTRUCTIONS
1) Electrical Safety
a) Keep work area clean and well lit. Cluttered and dark areas invite accidents.
b) Do not operate power tools in explosive atmosphere, such as in the presence of flammable liquids, gases or dust. Power tools
create sparks which may ignite the dust of fumes.
c) Keep children, and bystanders away while operating a power tool. Distractions can cause you to lose control.
2) Electrical Safety
a) Power tool plugs must match the outlet. Never modify the plug in any way. Do not use any adapter plugs with earthed
(grounded) power tools. Unmodified plugs and matching outlets will reduce risk of electric shock.
b) Avoid body contact with earthed or grounded surfaces such as pipes, radiators, ranges and refrigerators. There is an
increased risk of electric shock if your body is earthed or grounded.
c) Don’t expose power tools to rain or wet conditions. Water entering a power tool will increase the risk of electric shock.
d) Do not abuse the cord. Never use the cord to carry, pull or unplug the power tool. Keep cord away from heat, oil, sharp
edges or moving parts. Damaged or entangled cords increase the risk of electric shock.
e) When operating a power tool outdoors, use an extension cord suitable for outdoor use. Use of cord suitable for outdoor use
reduces the risk of electric shock.
3) Personal Safety
a) Stay alert, watch what you are doing and use common sense when operating a power tool. Do not use power tool while you
are tired or under the influence of drugs, alcohol, or medication.
A moment of inattention while operating power tools may result in serious personal injury.
b) Use safety equipment. Always wear eye protection. Safety equipment such as dust mask, non-skid safety shoes, hard hat, or
hearing protection used for appropriate conditions will reduce personal injuries.
Rubber gloves and non-skid footwear are recommended when working outdoors.
c) Avoid accidentally starting the sensor screwdriver. Pay attention to that the voltage used is suitable for this model.
Before plugging in the power plug of the sensor screwdriver, first make sure that the switch is off .
d) Remove any adjusting keys or wrench before turning the power tool on.
A wrench or a key that is left attached to a rotating part of the power tool may result in personal injury.
e) Do not overreach. Keep proper footing and balance at all times.
This enables better control of the power tool in unexpected situations.
f) Dress properly. Do not wear loose clothing or jewelry. Keep your hair, clothing, and gloves away from moving parts. Loose
clothes, jewelry, or long hair can be caught in moving parts.
g) Secure work. Use clamps or a vice to hold the work. It is safer than using your hand and frees both hands to operate the tool.
h) If devices are provided for the connection of dust extraction and collection facilities, ensure these are connected and
properly used. Use of these devices can reduce dust related hazards.
4) Power tool Use and Care
a) Do not force the power tool. Use the correct power tool for your application.
The correct power tool will do the job better and safer at the rate for which it was designed.
b) Do not use power tool if switch does not turn it on or off.
Any power tool that cannot be controlled with the switch is dangerous and must be repaired.
c) Disconnect the plug from the power source before making any adjustments, changing accessories, or storing the power tools.
Such preventive safety measures reduce the risk of starting the power tool accidentally.
d) Store idle power tools out of reach of children and do not allow persons unfamiliar with the power tool or these instructions
to operate the power tool.
Power tools are dangerous in the hands of untrained users.
Do not let visitors touch the tool or extension cord. All visitors should be kept away from work area.
e) Maintain power tools. Check for misalignment or binding of moving parts, breakage of parts and any other condition that
may affect the power tools operation. If damaged, have the power tool repaired before use.
Important Safety Rules

5
Many accidents are cause by poorly maintained power tools.
Inspect extension cords periodically and replace, if damaged.
f) Keep cutting tools sharp and clean,
Properly maintained cutting tools with sharp cutting edges are less likely to bind and are easier to control.
g) Use the power tools, accessories and tool bits etc., in accordance with these instructions and in the manner intended for the
particular type of power tool, taking into account the working conditions and the work to be performed.
Use of the power tool for operations different from intended could result in a hazardous situation.
5) SERVICE
a) Have your power tool serviced by qualified repair person using only identical replacement parts, this will ensure that the safety of
the power tool is maintained.
Additional information shall be provided.
a) Instruction for putting into use.
1. Setting-up or fixing power tool in a stable position as appropriate for power tools which can be mounted on a support.
2. Assembly
3. Connection to power supply, cable, fuse, socket type and earthing requirements.
4. Illustrated description of functions.
5. Limitations on ambient conditions.
6. List of contents.
b) Operating Instructions.
1. Setting and testing.
2. Tool changing.
3. Clamping of work.
4. Limits on size of work piece.
5. General instructions for use.
c) Maintenance and servicing.
1. Regular cleaning, maintenance, and lubrication.
2. Servicing by manufacturer or agent, list of addresses.
3. List of user-replaceable parts.
4. Special tools which may be required.

6
1、This tool should be grounded while in use to protect the operator from electric shock. NOTICE! To ensure the grounding result,
the grounding conductor of the power cord must be well connected with the grounding terminal of power facility. This tool is
equipped with grounding conductors. The Green (or Green and Yellow) conductor in the Power Cord is the grounding wire.
Never connect Green (or Green and Yellow) to a live terminal. The grounding wires in this tool can not only earth the electric
leakage safely, but also can eliminate ESD-the electrostatic that tool occurred while in use.
WARNING!
DO NOT OPERATE THIS TOOL WITHOUT
PROTECTIVE EARTH CONNECTED
1) Do not allow chemicals such as acetone, benzene, thinner, trichloroethylene ketone, or other similar chemicals to come in
contact with the sensor screwdriver housing as damage will result.
2) Use the sensor screwdriver carefully, do not drop or be impacted, it is best to use a balancer to lift it, and set it on the auxiliary
arm for operation.
3) Loading and unloading the sensor driver head: Simply pull down the screwdriver head cap with your fingertips to freely attach
or detach the sensor screwdriver head, release the finger to return the screwdriver head cap to fix the sensor screwdriver head.
Note: Make sure to turn off the power switch and remove the power plug from the socket when installing and removing the
sensor driver.
4) Do not drop or abuse the sensor screwdriver.
5) Connect the power cord to a power outlet.
CAUTION: Danger of electric shock due to wet power cord plug or hands.
6) Do not use this screwdriver for tightening wood screws. This is “Metal Assembly sensor screwdriver.”
7) The control settings of the sensor screwdriver can be set by the SMT-C1 controller. Please refer to the SMT-C1 operation
manual for setting adjustment.
8) The sensor screwdriver operation can be set to the press-plate start/down-press start/pull-screw start…etc. by
SMT-C1 controller. Please refer to SMT-C1 operation manual.
9) Operation frequency: Over frequently using makes the motor overheated and damage to screwdriver. Enough
heat-dissipation is good for screwdriver. Please refer to the Working Time from the Technical Specification sheet.
10) Whenever the sensor screwdriver is not used, turn off the power for the controller or unplug the power cord.
11) Don't touch switch during operating for keeping system from wrong judgement.
12) Please use the designated connection cable for SMT-C1.
13) Install/Removal 90°angle head Steps
Grounding Instructions
Operations Cautions

7
nnect SMT screwdriver and cable
Notice: The two cables are fully connected with no gaps.
Notice: The cable and controller are fully connected with no gaps.
Install
Removal

8
Function / Operating Introduction
1). Start Mode: Set the start mode on the controller.
(1). Independent press-plate mode
2). Signal light
3). Button Switch: Turn on and off the setting for screw removal, there will be no OK or NG signal action when screw removal
is in action.
It is recommended to set the direction on the controller first, before setting screw removal, which includes CW and CCW.
Please refer to the following table for 9-level torque and speed setting. The torque to remove screw should be larger than that
to fasten screw. For detailed controller setting, please refer to SMT-C1 controller operating manual.
4). Attaching / detaching bit
and bit type
Pull down the holder clamp by fingertip, and it will be unlocked. Thus, the bit can be freely attached and detached
(Single finger notion type) select such a bit whose shank is equal to the size shown below.
5). Press-plate Start.
pressed down sensor screwdriver starts functioning when the switch trigger has been pressed down; on the contrary, it
stops when the screw has been tightened up or the trigger has been released.
Number
Product Name
Description Use
(1)
Hanging Hole
Hanging hole is available, to hang the screwdriver
(2)
Signal Light
Display OK light, NG light, screw removal starts and stop signal
(3)
Button Switch
Switch rotation direction CW/CCW
(4)
Front Lock Ring
Lock stationary gearbox and housing
(5)
Headgear
Load/unload and fixing the screwdriver bits
(6)
fixing ring
Fixing ring is for connecting right angle attachment to screwdriver.
(7)
Trigger switch:
press the trigger switch the screwdriver starts; on the contrary, it stops when the
screw has been tightened up or the trigger has been released.
(8)
Hook wrench
A tool is for attaching and detaching right angle attachment.
OK Light
NO Light
Controller:
Program setting
Direction
Screwdriver light
signal (action)
Controller setting
Edit work order setting
Screw removal setting
Screwdriver light
signal (action)
CW
Forward
CW
Forward
CCW
Backward
CCW
Backward
CCW
Backward
CW
Forward
CW
Forward
CCW
Backward
(1)
(3)
(7)
(4)
(2)
(6)
(5)
(1)
(3)
(7)
(4)
(2)
(6)
(5)
(8)

9
Maintenance and Inspection:
1. The screwdriver must be operated in top condition, one day working hour must be not more than eight hours.
cording to operating frequency and torque loaded, we suggest adding lubricating oils in clutch per 3-6 months,
and kindly contact with distributor when product's maintenance.
2. Please note don’t let the motor get over heated, Please refer to the Working Time from the Technical Specification sheet.
3. The frequency use of this electric sensor screwdriver is over than eight hours a day, still it needs periodically testing and
treatment.
4. Inspect tool cords periodically and if damaged, have them repaired by an authorized service facility. Inspect extension cords
periodically and replace if damaged.
5. Do not remove any labels. Replace any damaged label.
6. To adjust the torque on this sensor screwdriver. Proceed as follows :
Stop the sensor driver first and adjust it with the SMT-C1 controller.
1. The use of other than genuine SUMAKE replacement parts may Result in decreased
tool performance and increased maintenance and may invalidate all warranties.
2. All repairs and maintenance of this tool and its word must be performed by an authorized service center.
3. SUMAKE is not responsible for customer modification of tools for applications on which SUMAKE was not consulted.
4. Repairs should be made only by authorized, trained personnel. Consult your nearest SUMAKE authorized service center.
5. It is the responsibility of the employer to place the information in this manual into the hands of the operator.
DO NOT ATTEMPT TO REPAIR THIS
ELECTRIC SCREWDRIVER
SAVE THESE INSTRUCTIONS
DO NOT DESTROY
Servicing
CAUTION
CAUTION
Our company reserves the right to modify
the product without prior notice.

EU Declaration of Conformity (DOC)
We: SUMAKE INDUSTRIAL CO., LTD.
4F, No. 351, Yangguang St., Neihu District, Taipei City, Taiwan
declare in sole responsibility that the equipment
Equipment: ELECTRIC SCREWDRIVER
Model/ Serial No.: SMT-10SI, SMT-30SI, SMT-30I, SMT-50I, SMT-70I, SMT-120I, SMT-180I,
SMT-250I, SMT-30A, SMT-50A, SMT-70A, SMT-120A, SMT-180A,
SMT-250A
The object of the declaration described above is in conformity with the relevant union
harmonization legislation:
Machinery Directive 2006/42/EC
Electromagnetic Compatibility 2014/30/EU
RoHS 2011/65/EU
The following harmonised standards and technical specifications have been applied:
EN 62841-1:2015/AC:2015
EN 62841-2-2:2014/AC:2015
EN IEC 55014-1:2021
EN IEC 61000-3-2:2019+A1:2021
EN 61000-3-3:2013+A1:2019
EN IEC 55014-2:2021
Data:
Noise level:
Sound pressure level: No Load: 66.6 dB(A)
Sound power level: No Load: 76.6 dB(A)
Uncertainty K= 3dB
Vibration level:
No Load: 0.6974 m/s²
Uncertainty K= 1.5 m/s²
Name and Signature/Position Date and Place
2023/7/1
Mike Su – Managing Director Taipei, Taiwan
SMT-series-D-2307F-K2

NOTE
www.SUMAKE.com
www.aircompressors.com.tw
This manual suits for next models
5
Table of contents
Other Sumake Power Screwdriver manuals
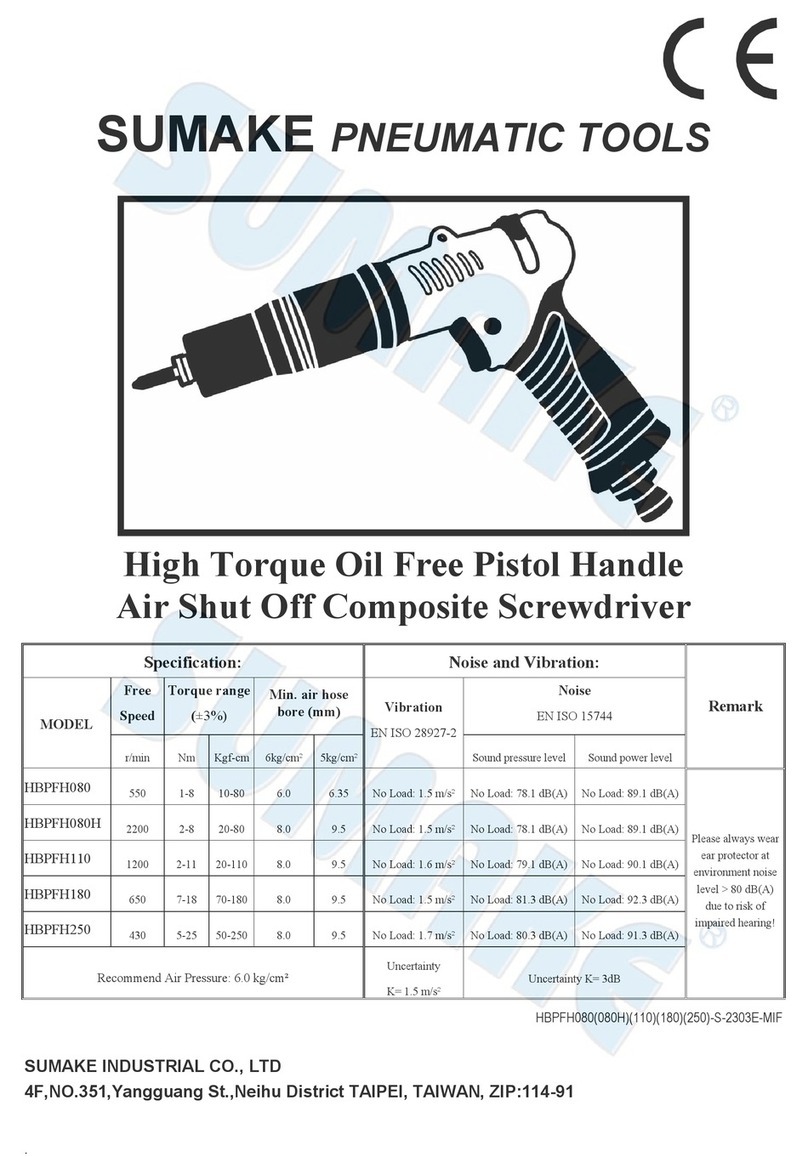
Sumake
Sumake HBPFH080 User manual
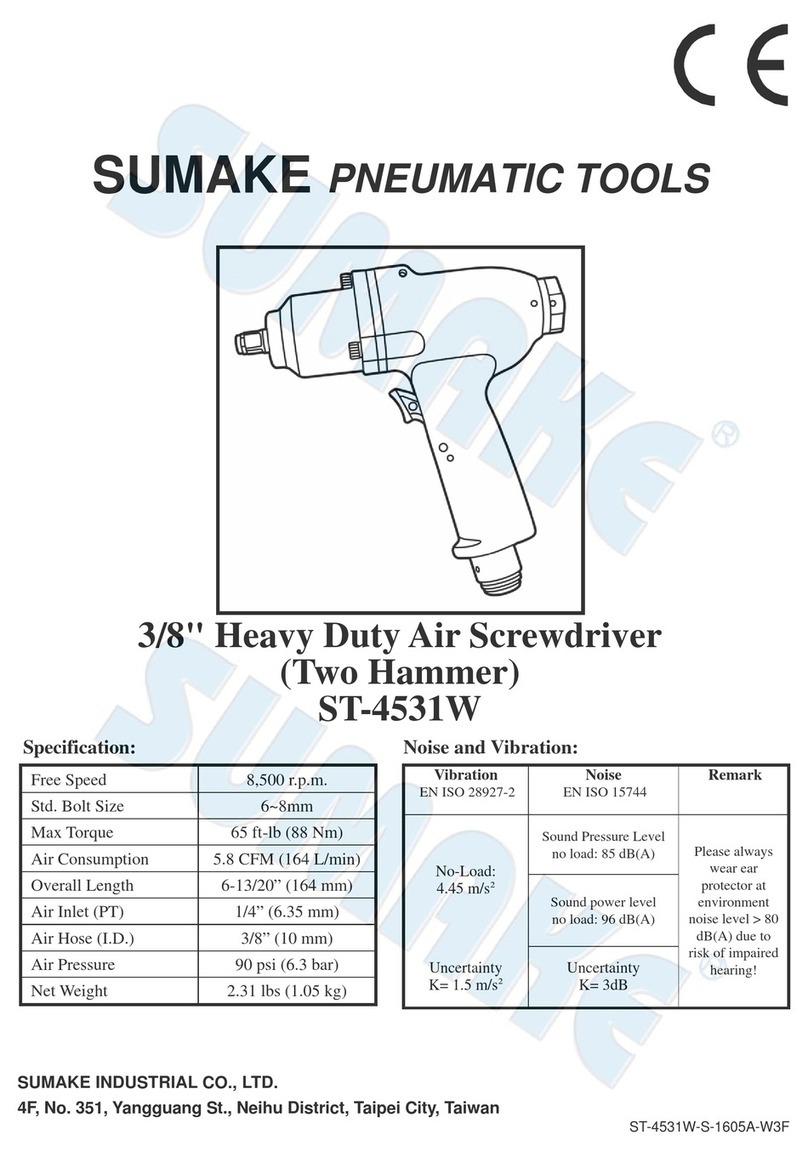
Sumake
Sumake ST-4531W User manual

Sumake
Sumake ST-4464 User manual
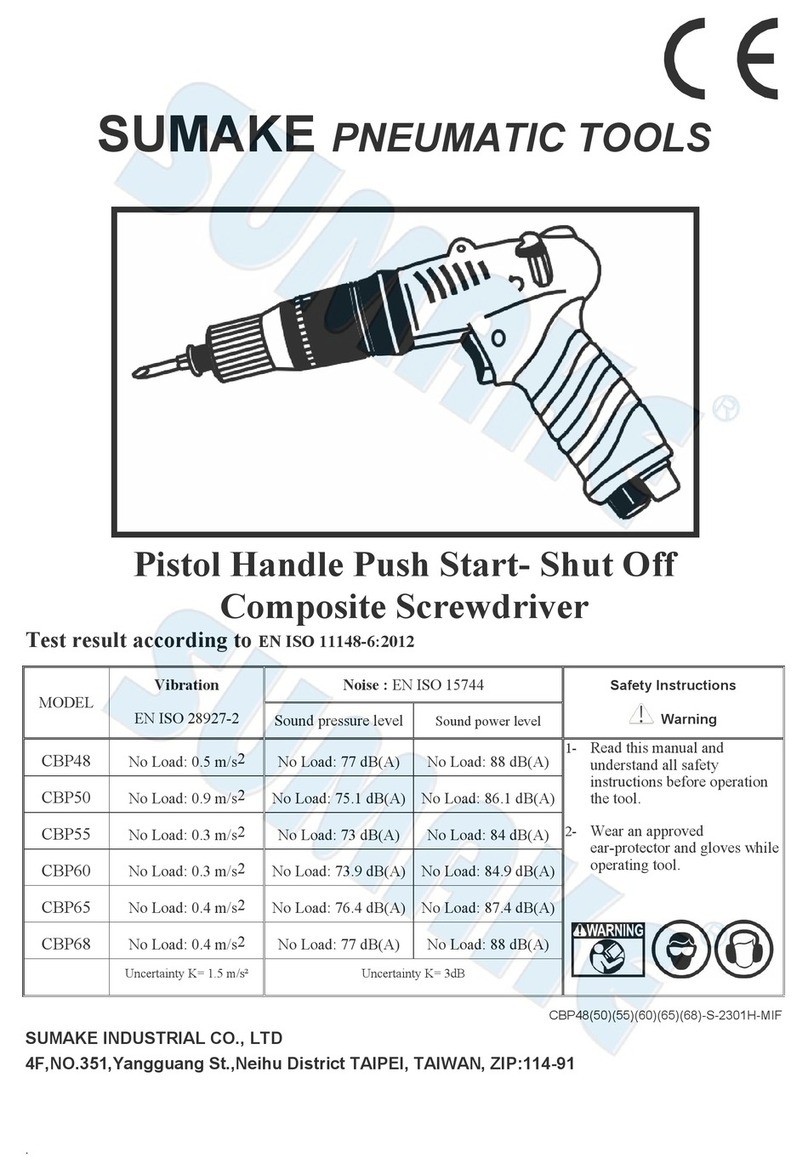
Sumake
Sumake CBP48 User manual
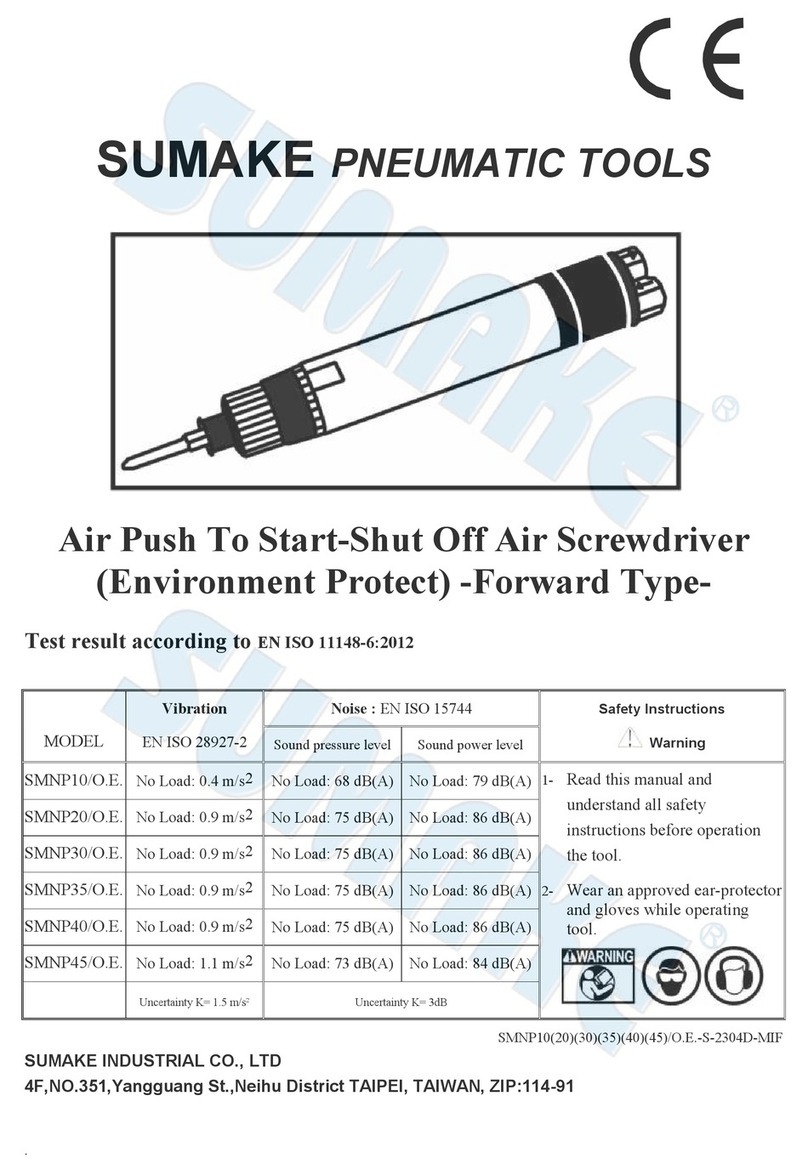
Sumake
Sumake SMNP10/O.E. User manual
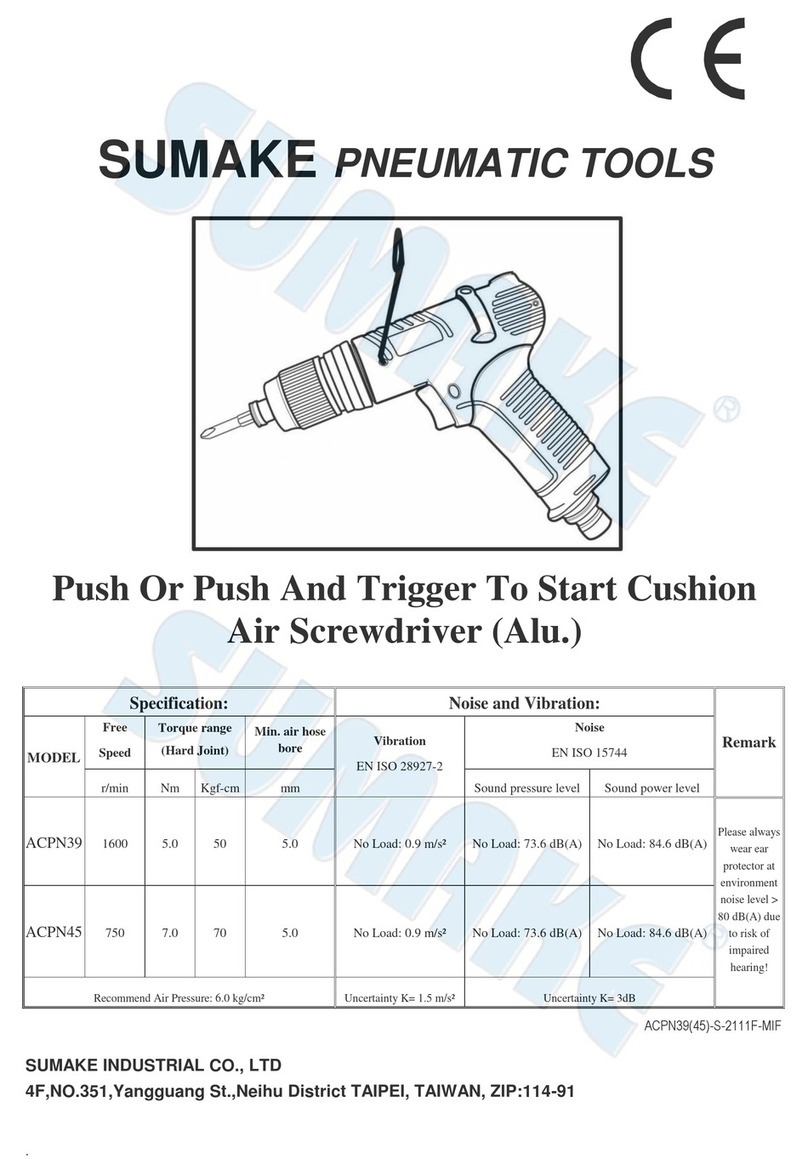
Sumake
Sumake ACPN39 User manual
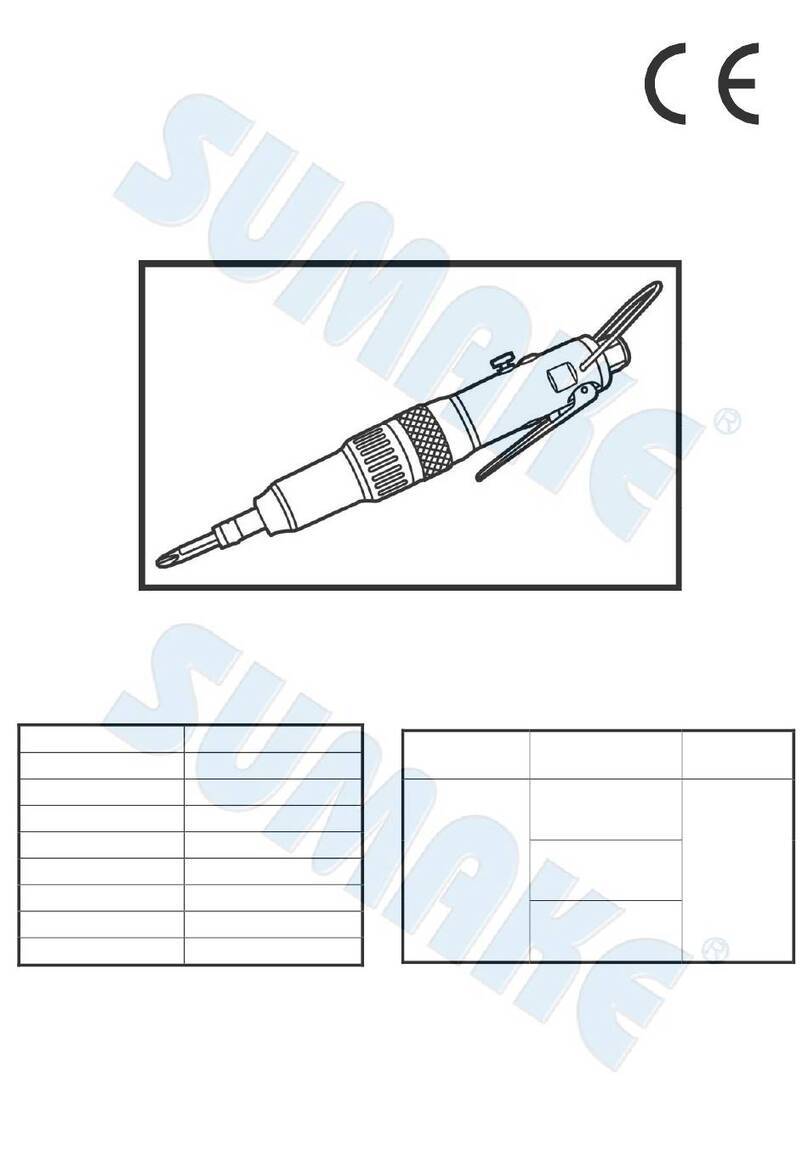
Sumake
Sumake ST-4450 User manual
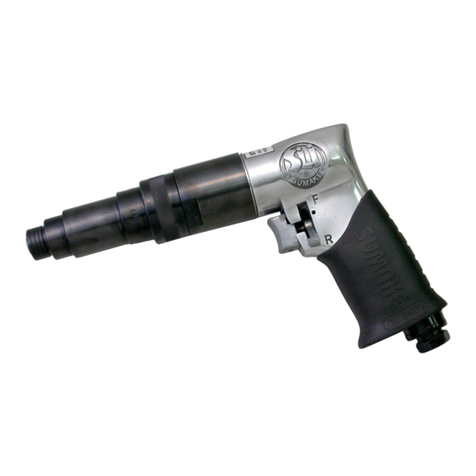
Sumake
Sumake ST-4481 User manual

Sumake
Sumake CP12 User manual

Sumake
Sumake ABP35 User manual
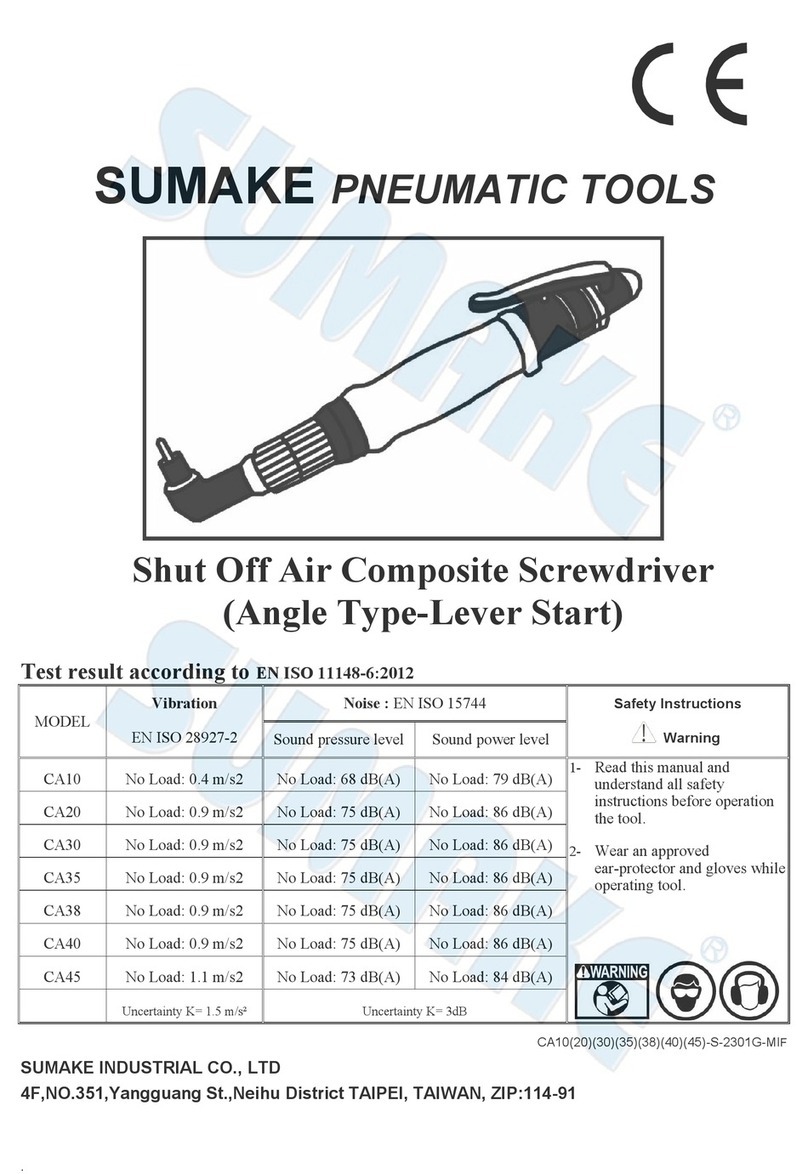
Sumake
Sumake CA10 User manual
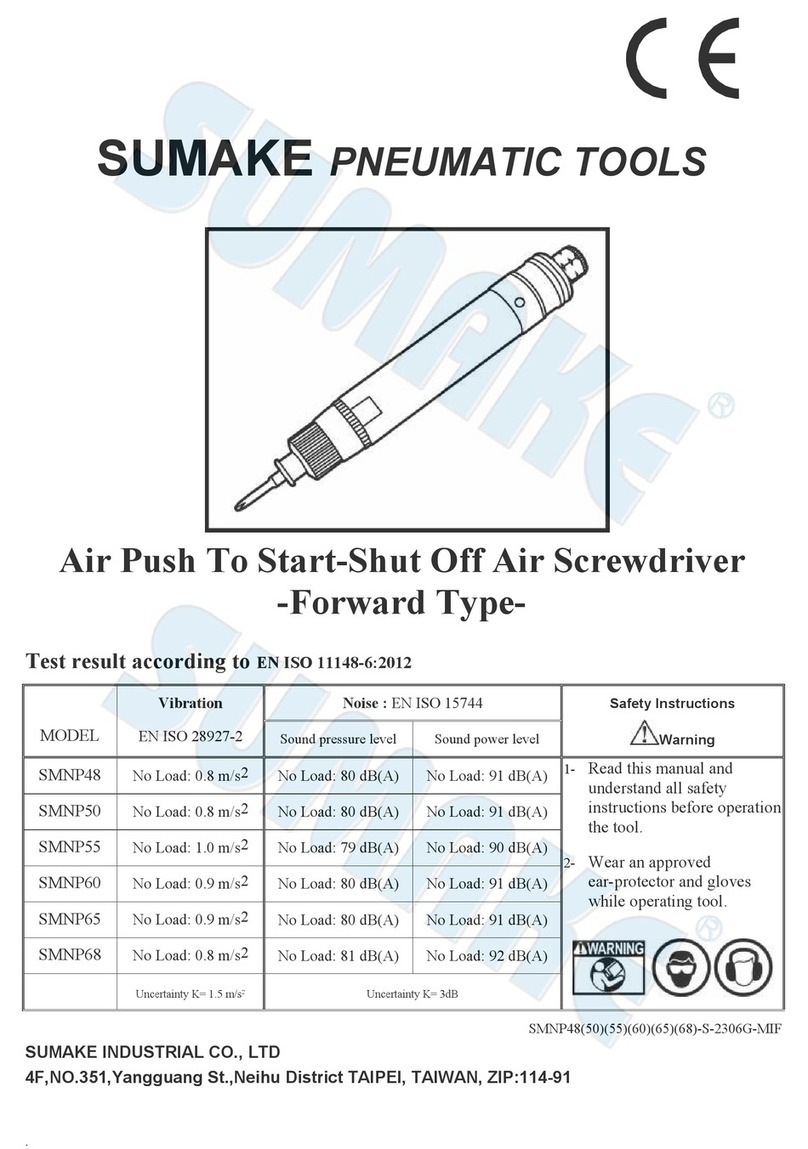
Sumake
Sumake SMNP48 User manual
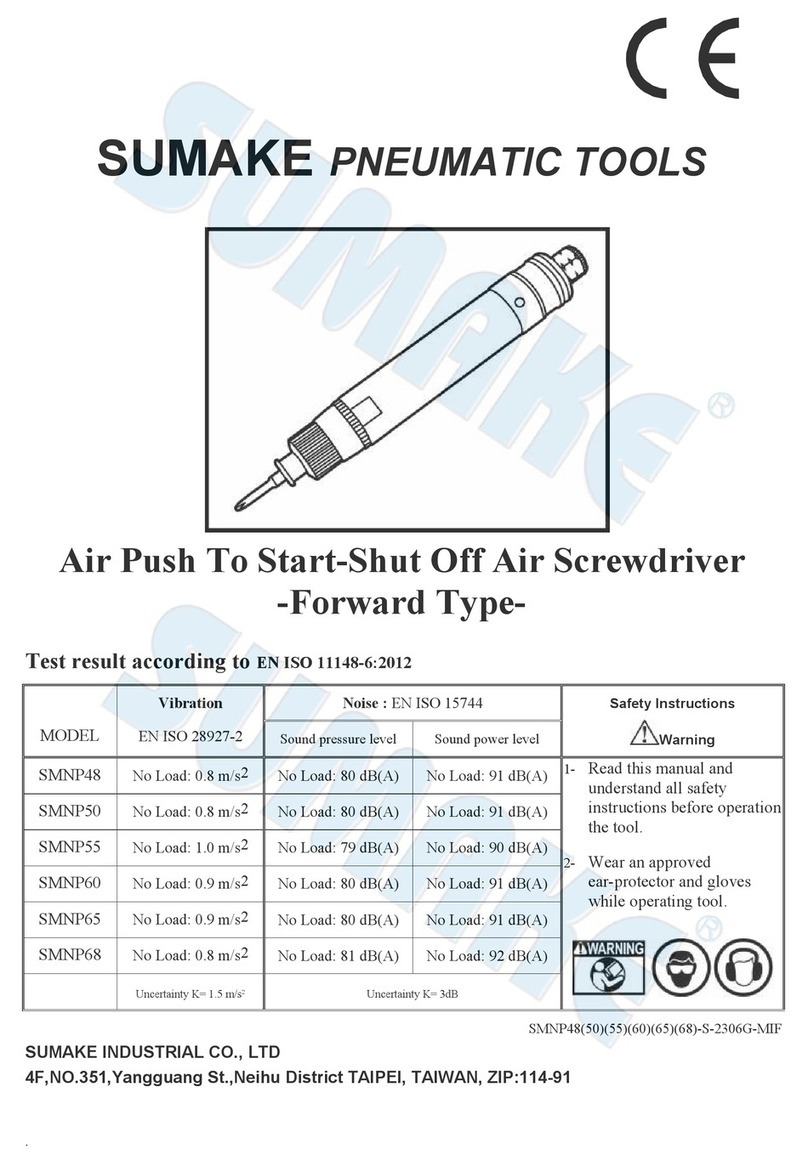
Sumake
Sumake SMNP48 User manual
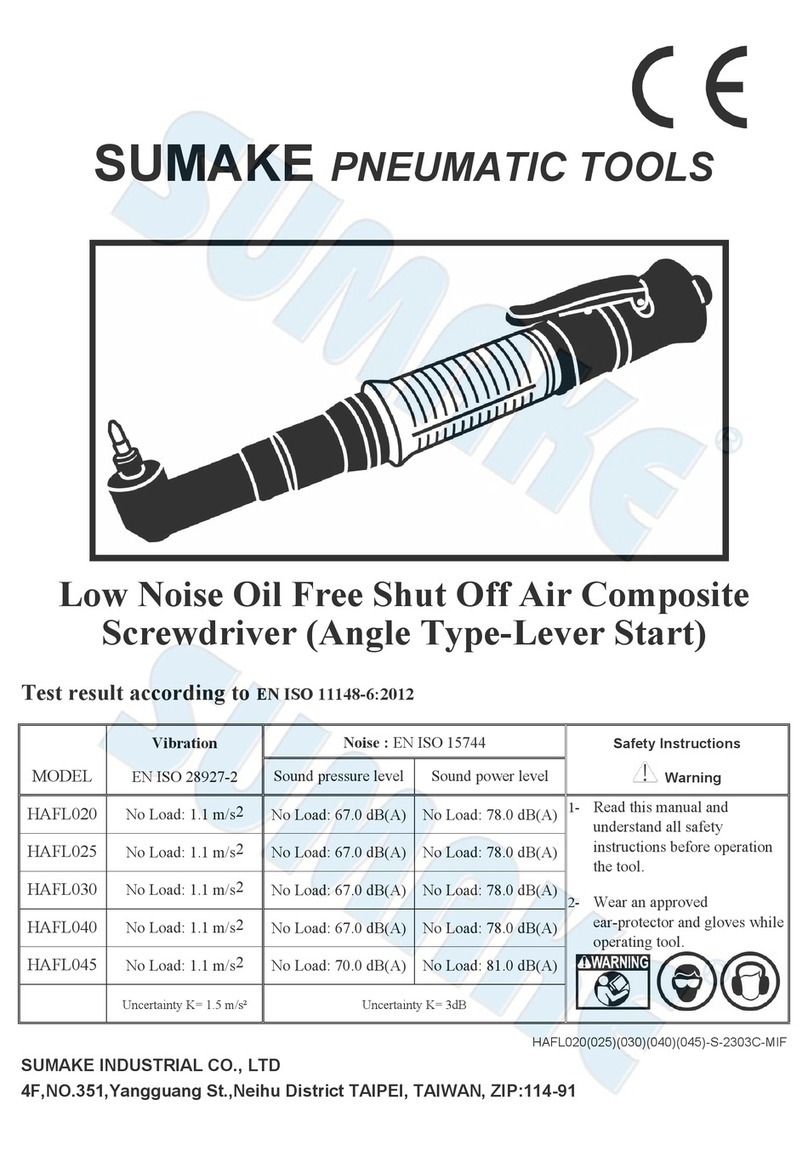
Sumake
Sumake HAFL020 User manual
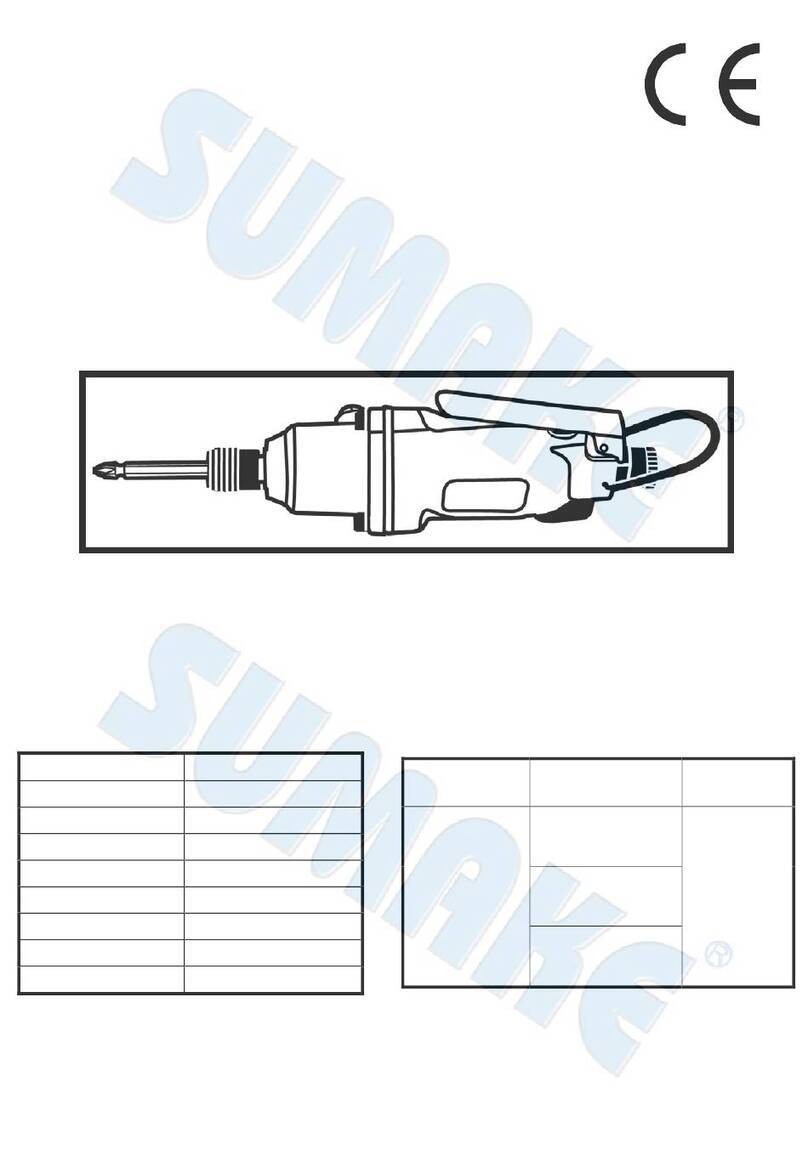
Sumake
Sumake ST-6SSLD User manual

Sumake
Sumake ST-SD151 User manual
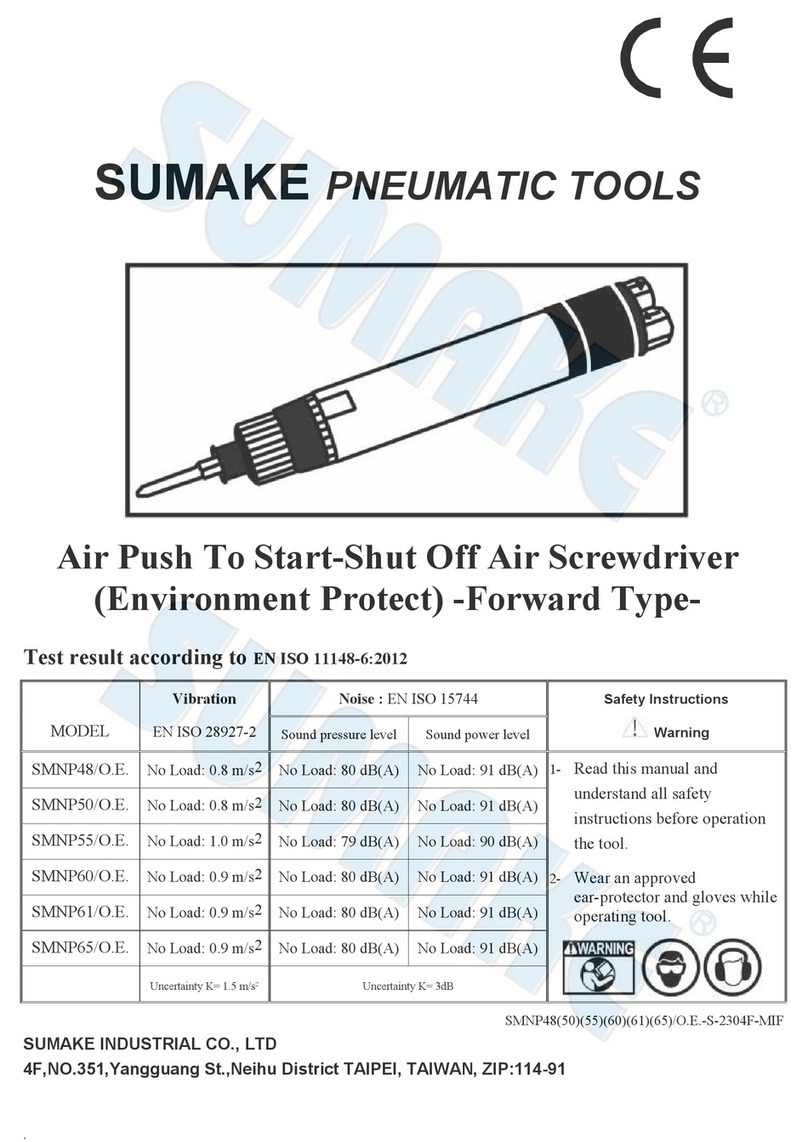
Sumake
Sumake SMNP48/O.E. User manual
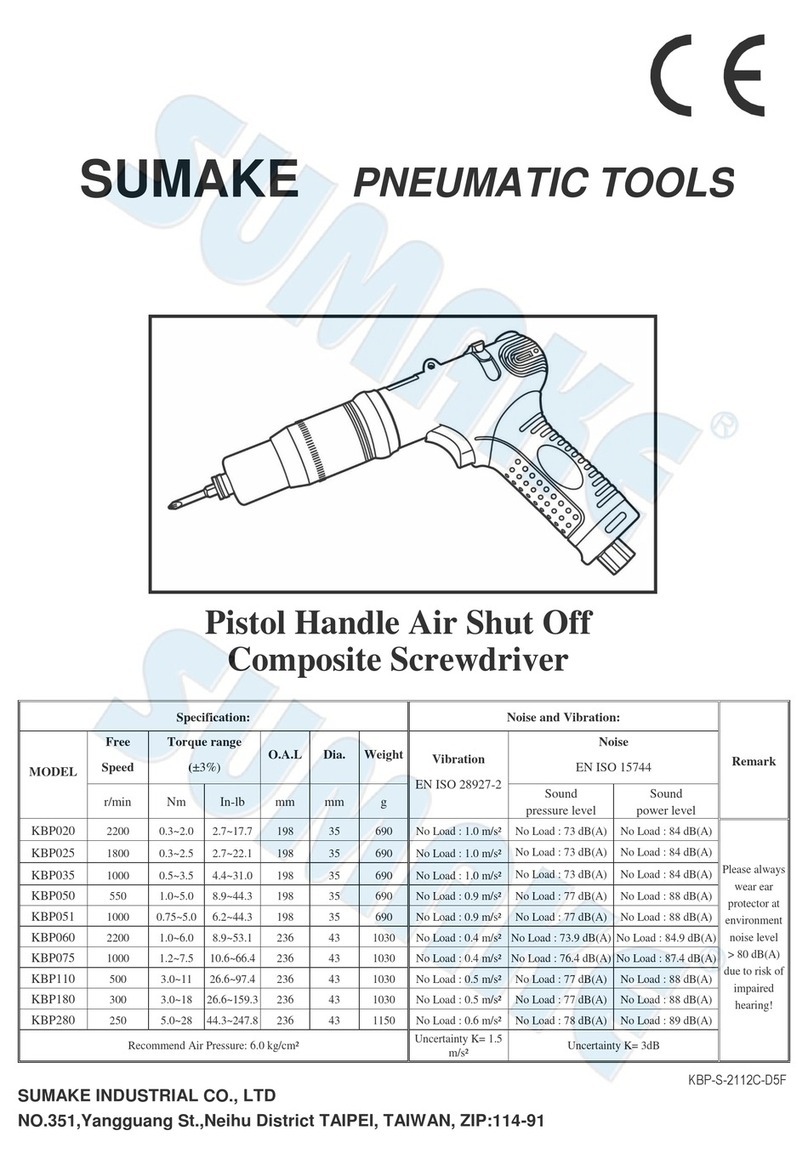
Sumake
Sumake KBP020 User manual
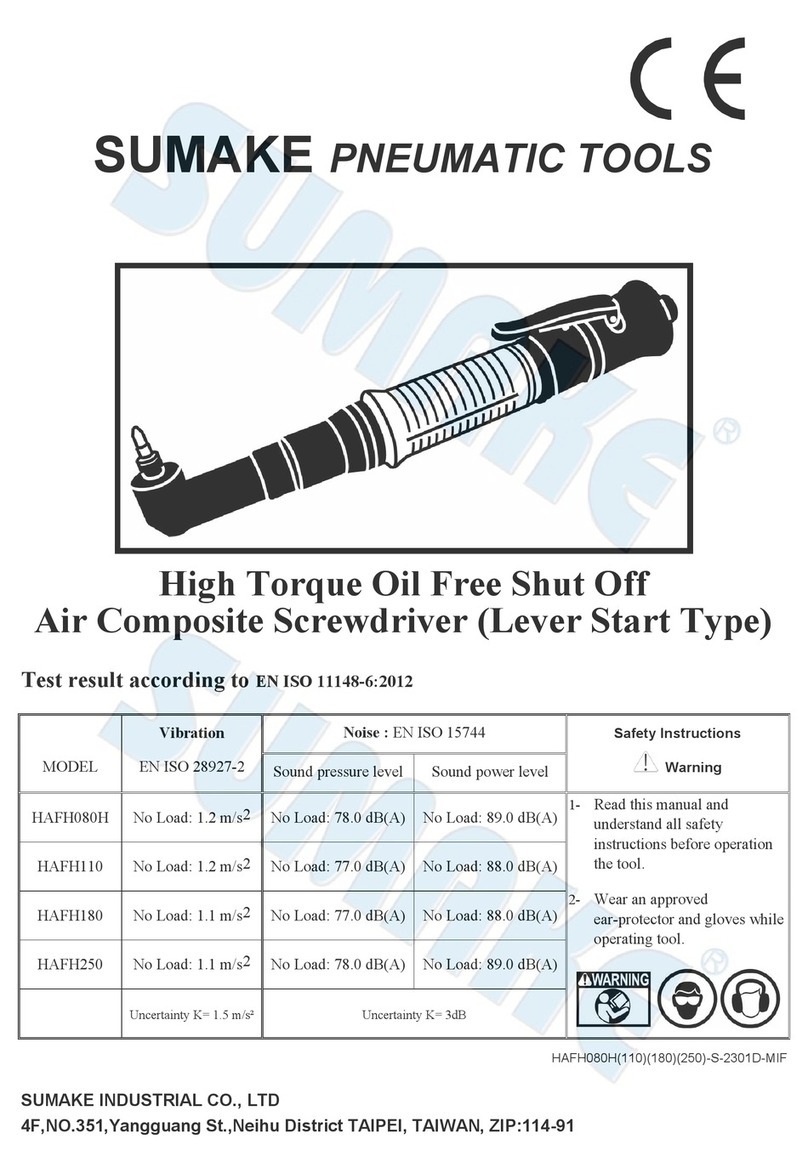
Sumake
Sumake HAFH080H User manual
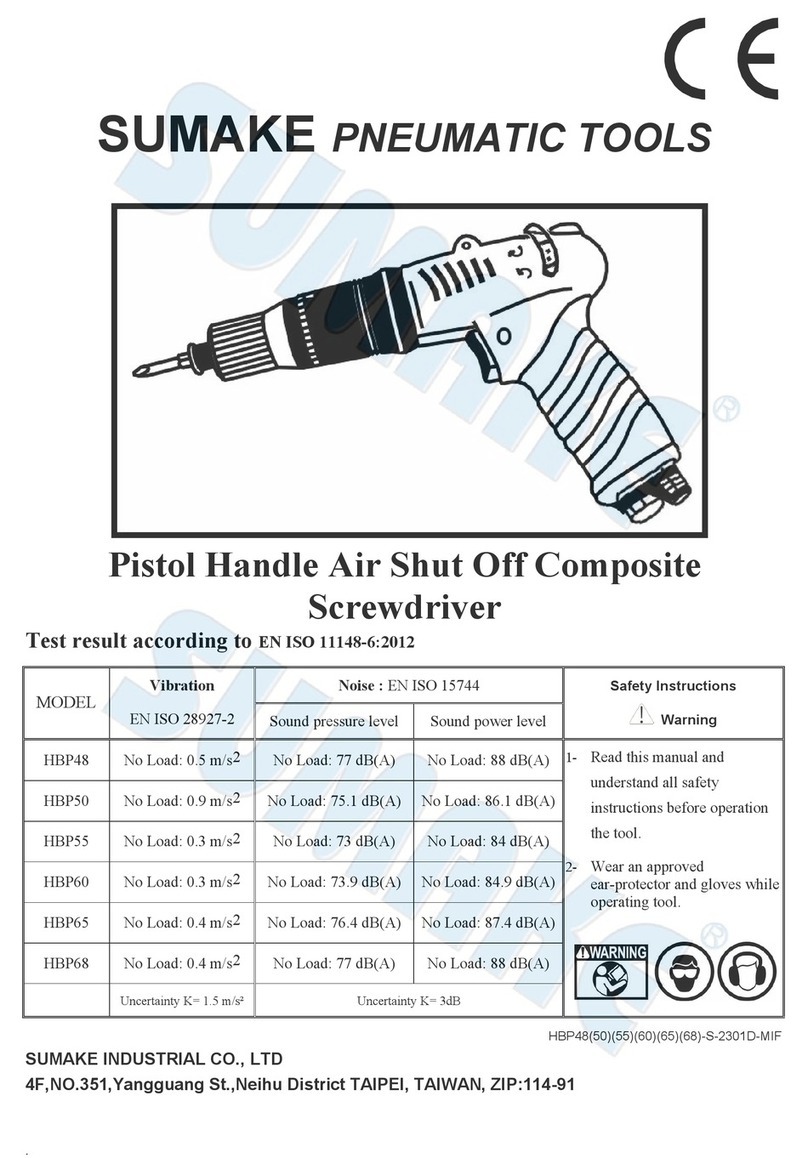
Sumake
Sumake HBP48 User manual