Taco Zone Sentry Series User manual

Application:
Taco Zone Sentry Zone Valves provide on-off, normally
open or normally closed control in both open and closed
hot or chilled water systems. The valves can be used in a
wide variety of heating and cooling applications, pri-
marily designed for use with fan coils, radiators, convec-
tors, air handlers, heat pumps and radiant applications.
Refer to the Product Specifications section for choosing
the correct style valve for your application.
Ease of Installation / Operation:
The Zone Sentry is the most technologically advanced
zone valve ever made. It’s also simple to install and oper-
ate. The valve can be installed in any direction, in any
orientation. We then went a step further, allowing the
operator to be mounted to the valve body in either direc-
tion (see Figure A), great for those tight baseboard jobs.
Snap-in quick connects on the back of the valve make
for a simple, secure and fast wiring hook-up. A green
LED light shows full functionality of the valve’s opera-
tion and thermostat status. Under a no power situation
the manual override button located on the top of the
valve allows the ball to be rotated up to 90° and is also
marked with a slot to indicate the position of the valve.
Valve Installation:
1. Valve body may be installed in any position, in
any orientation (see Figure A).
2. Before mounting the body, refer to Figure B for
any clearance requirements.
3. Use of a solder with a melting point below 600°F
is recommended. Do not overheat! Make sure the
ball valve is in the FULL OPEN position during sol-
dering. Direct flame tip away from the center of
the valve. Cool valve quickly with a wet rag.
4. Solder build-up on the ball valve may prevent
proper opening and closing of the valve. Rotate
the manual operation button several times to
loosen any possible build-up.
5. Valve body can be submerged for leak testing
before the operator is attached.
Operator Installation / Wiring:
1. Valve operator may be attached to the valve body
in either direction (see Figure A).
2. Operator Removal: Remove the valve operator
prior to soldering by pushing in and holding the
release clip at the front of the operator and lifting
upward approximately 3⁄4"(see Figure C).
3. To re-assemble the operator to the valve body:
Position operator such that the “D” shaped valve
stem aligns properly with the “D” shaped operator
drive cavity. (Note: The “D” shaped stem design
allows for correct insertion every time.) Next, slide
the valve stem into the operator cavity, push in
and hold the release clip until the operator slips
over the valve locking posts (see Figure C). Once
the operator is flush to the valve body, let go of
the release clip. Using very little force, try to take
Instruction Sheet
Zone Sentry Zone Valve
102-410
SUPERSEDES: November 1, 2009 EFFECTIVE: October 15, 2010
Plant ID# 001-3944
CAUTION: Operator must be removed from the
valve body before soldering (see Figure C). Ball
valve must be in the full open position before
soldering. Valve shipped in the closed position.
Two Position Head Placement.
Universal Body Placement.
May be installed in any position, any orientation.
AABB
Figure A
1
3
⁄
8
" CLEARANCE
3
⁄
4
" CLEARANCE
W
A
L
L
Figure B
NOTE: Some power robbing thermostats require
the use of a resistor (always use the resistor pro-
vided by the thermostat manufacturer with the
Zone Sentry). Consult the thermostat instructions
for the resistor installation.

the operator off of the valve body without using
the release clip. Both locking posts should be firm-
ly attached to the operator. If the operator slides
up the stem, repeat the assembly process.
4. Wire the operator in accordance with system
requirements (see Wiring Diagrams).
5. The plug-in quick connects can be disconnected
from the valve operator for ease of wiring. Insert the
corresponding wire into the quick connects (see
Wiring Diagrams) and tighten by turning the screw.
6. Caution: Do not jumper power/motor (24 VAC)
connection terminals, even temporarily. This may
cause damage to the thermostat’s heat anticipator.
Mode of Operation:
1. Upon initial field installation the capacitor
requires a full charge, up to 20 seconds, before the
valve starts to turn. Charging time will vary (typi-
cally less) during normal operation.
2. When the capacitor is charging the green LED
light will FLASH.
3. Once the capacitor is charged, the green LED will
stop flashing but remain ON. At this point the
valve’s operator will rotate the ball valve. The
green LED will remain ON as long as the thermo-
stat is calling (the unit is powered).
4. Once the thermostat is satisfied the green LED will
turn OFF and the valve will rotate 90° into its nor-
mal position or non-powered position. For exam-
ple: If the actuator is an NC (normally closed) ver-
sion, the operator would open the valve when the
thermostat calls. Once the thermostat is satisfied
the operator would then rotate the valve 90° to its
normally closed position.
A
D
C
F
E
B
G
VALVE SIZE Cv (Kv)/Ft.
of PIPE EQUIV.* CLOSE-OFF PSI (kPa)
1⁄2"4.9 (4.3) / 9.5 0-125 psi (0-862 kPa)
3⁄4"10.3 (8.9) / 8.4 0-125 psi (0-862 kPa)
1"8.9 (7.7) / 47.4 0-125 psi (0-862 kPa)
Dimensions (for reference purposes):
Flow Coefficients and Maximum Close-Off Pressure:
* At 4' per second (max.
recommended residential
flow rate).
WARNING: Do not use zone valves on indirect
water heaters without a tempering device.
1
3
⁄
8
" CLEARANCE
3
⁄
4
" CLEARANCE
W
A
L
L
VALVE SIZE A B C D E
(Sweat)
E
(Threaded) F G WEIGHT
(Valve + Actuator)
1⁄2"3"23⁄8"41⁄8"21⁄16"31⁄8"33⁄4"19⁄16"25⁄16"0.85 lbs
3⁄4"3"23⁄8"41⁄8"21⁄8"31⁄8"35⁄16"19⁄16"25⁄16"0.90 lbs
1"3"23⁄8"41⁄8"21⁄8"37⁄8"37⁄8"17⁄8"25⁄16"1.10 lbs
L
OCKING
POST
Step 1:
Push in and hold release clip
at the front of the operator.
Step 2:
Move operator upward
approximately 3⁄4" to
disengage Locking Posts.
Figure C: Operator
Removal

WARNING: Wiring connec-
tions must be made in
accordance with all applic-
able electrical codes.
CAUTION: To prevent elec-
trical shock, disconnect
electric power to system at
main fuse or circuit breaker
box until installation is
complete. When a service
switch is installed, more
than one disconnect switch
may be required to deener-
gize this device for servic-
ing.
Zone Sentry Zone Valve Wiring Diagrams
LED
Motor
Circuit
End Switch
c
w/y
Simplified Internal
Schematic:
Thermostats Transformer
To “T” Terminals
on Boiler Control
Transformer Relay
T
T
Up to 12 Valves per
40va Transformer
L1 (Hot)
L2
24 v
End Switch
Rh/Rc
w/y
Rh/Rc
w/y
Rh/Rc
w/y
w/y
c
End Switch
w/y
c
End Switch
w/y
c
L1 (Hot)
L2
Thermostat
To “T” Terminals
Motor
See Chart
See Chart
Red
Red End Switch
Motor Wire Color
Honeywell = Yellow
Erie = Black
Sparco = Orange/Yellow
Honeywell, Erie and Sparco Wire Leads
Wiring a Taco Zone Sentry Zone Valve to Replace a
Honeywell, Erie or Sparco Valve:
Honeywell and Erie Terminal Block
L1 (Hot)
L2
Thermostat
To “T” Terminals
Motor
End Switch
TH
TR
TR
TH
ES
ES
L1 (Hot)
L2
Thermostat
To “T” Terminals on Boiler
Control Transformer Relay
Taco Zone Sentry Zone Valve
c
End Switch
w/y
Wiring a Taco Zone Sentry Zone Valve to Replace a
Flair or Taco 3-Wire Valve:
Taco Zone Sentry Zone Valve
Taco 570 Series
L1 (Hot)
L2
Thermostat
To “T” Terminals
Motor
End Switch
1
2
3
Flair
L1 (Hot)
L2
Thermostat
To “T” Terminals
Motor
End Switch
1
2
3
45
L1 (Hot)
L2
Thermostat
To “T” Terminals on Boiler
Control Transformer Relay
c
End Switch
w/y
Wiring a Taco Zone Sentry Zone Valve to Replace a
White Rodgers Valve:
L1 (Hot)
L2
To “T” Terminals on Boiler
Control Transformer Relay
Taco Zone Sentry Zone Valve
46
5
L1 (Hot)
L2
To “T” Terminals
Motor End Switch
6
4
White-Rodgers (1311 or 1321)
4
56
Thermostat
5
2
3
1
Thermostat
c
End Switch
w/y
Typical Zone Sentry Zone Valve Wiring:
NOTE: Some power robbing thermostats require the use of a resistor (always use the resistor provided
by the thermostat manufacturer with the Zone Sentry). Consult the thermostat instructions for the
resistor installation.

Product Specifications:
Maximum Operating Pressure: 300 PSI (2,100 kPa)
Maximum Shutoff Pressure: 125 PSI (875 kPa)
Fluid Temperature Range: 20° to 240°F, (-7° to 115°C) @ 135°F (57°C) ambient
Service: Closed systems
Optional open system configuration
Up to 50% Glycol
Ball Rotation Speed: Full Open to Full Close (90° turn), 5 seconds (after charge time)
Full Close to Full Open (90° turn), 5 seconds (after charge time)
Seat Leakage: Drop-Tight Close-Off
Electrical Rating: 24 VAC, 60 HZ, 0.48 Amps
Do not exceed number of valves per transformer rating. Example:
Do not use more than 12 zone valves per 40VA transformer.
Power Consumption, Charging: 11.4 Watts, 0.48 Amps
Power Consumption, Power On: 1.44 Watts, 0.06 Amps
Heat Anticipator Setting: 0.5 Amps
End Switch Rating: 1 Amp @ 24 VAC
Materials of Construction, Actuator:
Body: High Performance Engineered Polymer
Gears: High Performance Internally Lubricated Engineered Polymer
Materials of Construction, Valve:
Body: Forged Bronze
Stem: Brass
Press Ring: Brass
Ball: Brass (Chrome Plated)
Seat: Modified Teflon®
O-rings: EPDM
Taco, Inc. will repair or replace without charge
(at the company’s option) any product or part
which is proven defective under normal use
within three (3) years from the date of start-up or
three (3) years and six (6) months from date of
shipment (whichever occurs first).
In order to obtain service under this warranty, it
is the responsibility of the purchaser to promptly
notify the local Taco stocking distributor or Taco
in writing and promptly deliver the subject prod-
uct or part, delivery prepaid, to the stocking dis-
tributor. For assistance on warranty returns, the
purchaser may either contact the local Taco
stocking distributor or Taco. If the subject prod-
uct or part contains no defect as covered in this
warranty, the purchaser will be billed for parts
and labor charges in effect at time of factory
examination and repair.
Any Taco product or part not installed or operat-
ed in conformity with Taco instructions or which
has been subject to misuse, misapplication, the
addition of petroleum-based fluids or certain
chemical additives to the systems, or other
abuse, will not be covered by this warranty.
If in doubt as to whether a particular substance
is suitable for use with a Taco product or part, or
for any application restrictions, consult the
applicable Taco instruction sheets or contact
Taco at [401-942-8000].
Taco reserves the right to provide replacement
products and parts which are substantially simi-
lar in design and functionally equivalent to the
defective product or part. Taco reserves the right
to make changes in details of design, construc-
tion, or arrangement of materials of its products
without notification.
TACO OFFERS THIS WARRANTY IN LIEU OF
ALL OTHER EXPRESS WARRANTIES. ANY
WARRANTY IMPLIED BY LAW INCLUDING
WARRANTIES OF MERCHANTABILITY OR FIT-
NESS IS IN EFFECT ONLY FOR THE DURATION
OF THE EXPRESS WARRANTY SET FORTH IN
THE FIRST PARAGRAPH ABOVE.
THE ABOVE WARRANTIES ARE IN LIEU OF ALL
OTHER WARRANTIES, EXPRESS OR STATU-
TORY, OR ANY OTHER WARRANTY OBLIGA-
TION ON THE PART OF TACO.
TACO WILL NOT BE LIABLE FOR ANY SPE-
CIAL, INCIDENTAL, INDIRECT OR CONSE-
QUENTIAL DAMAGES RESULTING FROM THE
USE OF ITS PRODUCTS OR ANY INCIDENTAL
COSTS OF REMOVING OR REPLACING
DEFECTIVE PRODUCTS.
This warranty gives the purchaser specific
rights, and the purchaser may have other rights
which vary from state to state. Some states do
not allow limitations on how long an implied war-
ranty lasts or on the exclusion of incidental or
consequential damages, so these limitations or
exclusions may not apply to you.
LIMITED WARRANTY STATEMENT
COMFORT MADE EASY.®
TACO, INC., 1160 Cranston Street, Cranston, RI 02920 Telephone: (401) 942-8000 FAX: (401) 942-2360.
TACO (Canada), Ltd., 8450 Lawson Road, Unit #3, Milton, Ontario L9T 0J8. Telephone: 905/564-9422. FAX: 905/564-9436.
Visit our web site at: http://www.taco-hvac.com
Printed in USA
Copyright 2010
TACO, Inc.
Other Taco Control Unit manuals
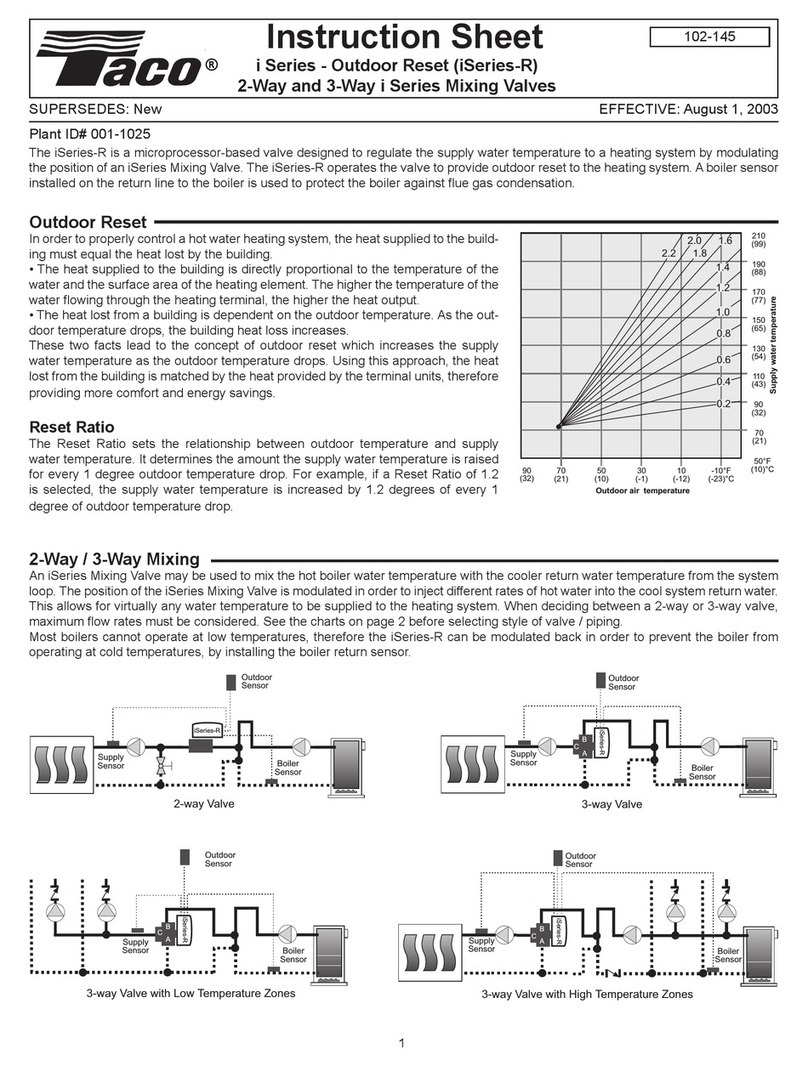
Taco
Taco i Series User manual

Taco
Taco Comfort Solutions 5000-3 Series User manual
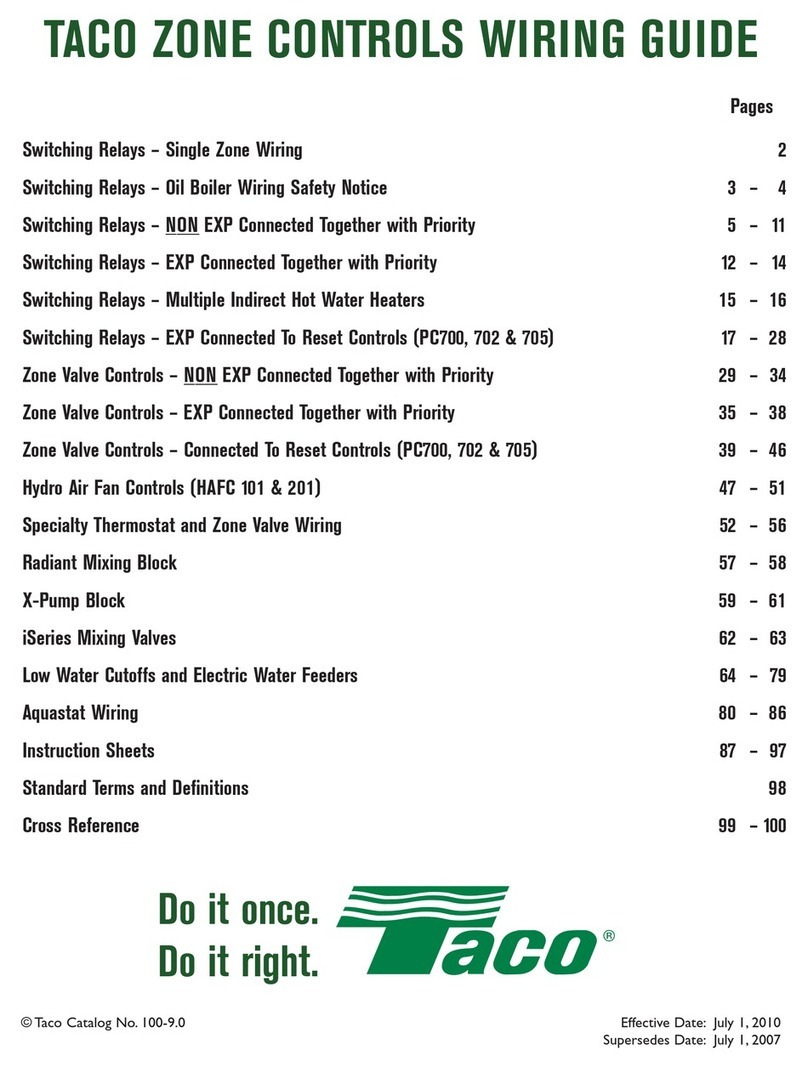
Taco
Taco SR501 User manual
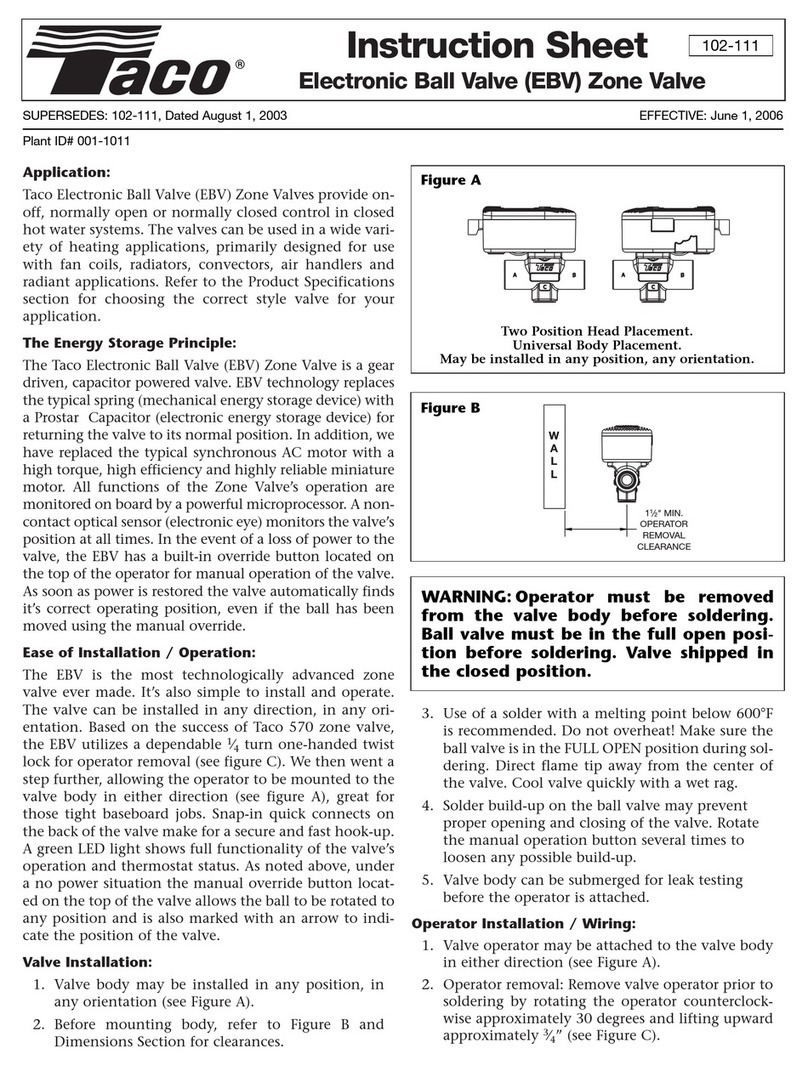
Taco
Taco 102-111 User manual
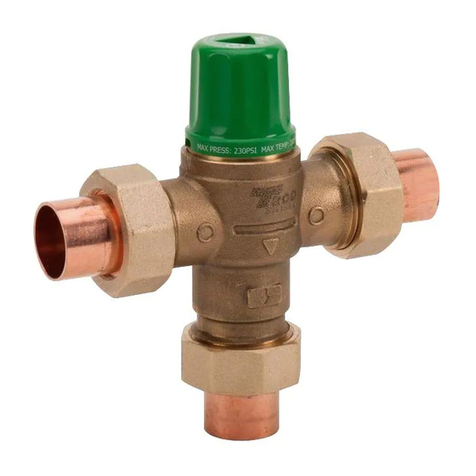
Taco
Taco 5000-2 User manual
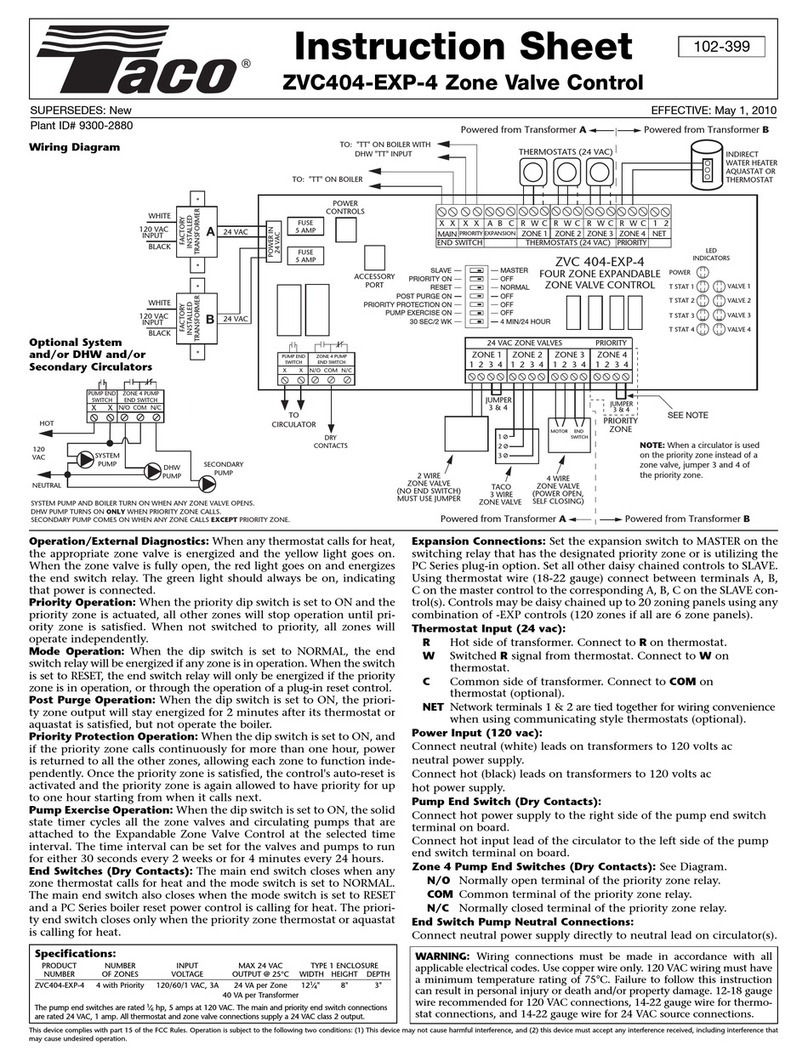
Taco
Taco ZVC404-EXP-4 User manual
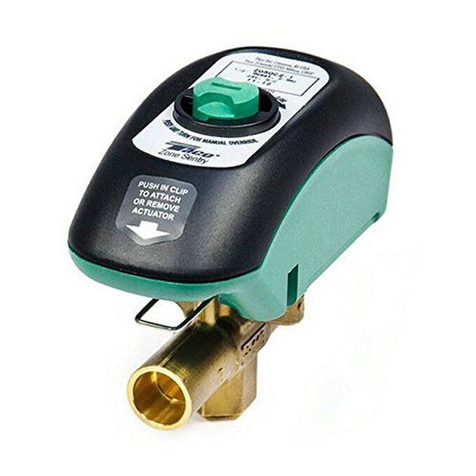
Taco
Taco Zone Sentry User manual
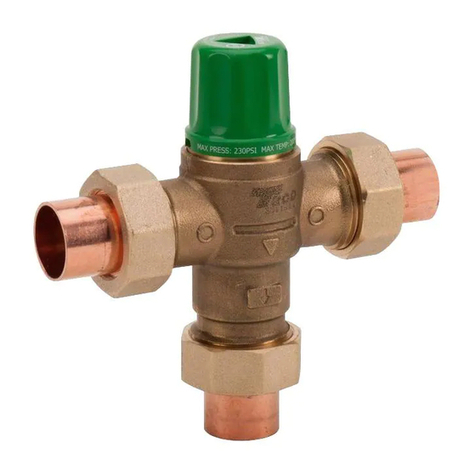
Taco
Taco 5000-HX Series User manual
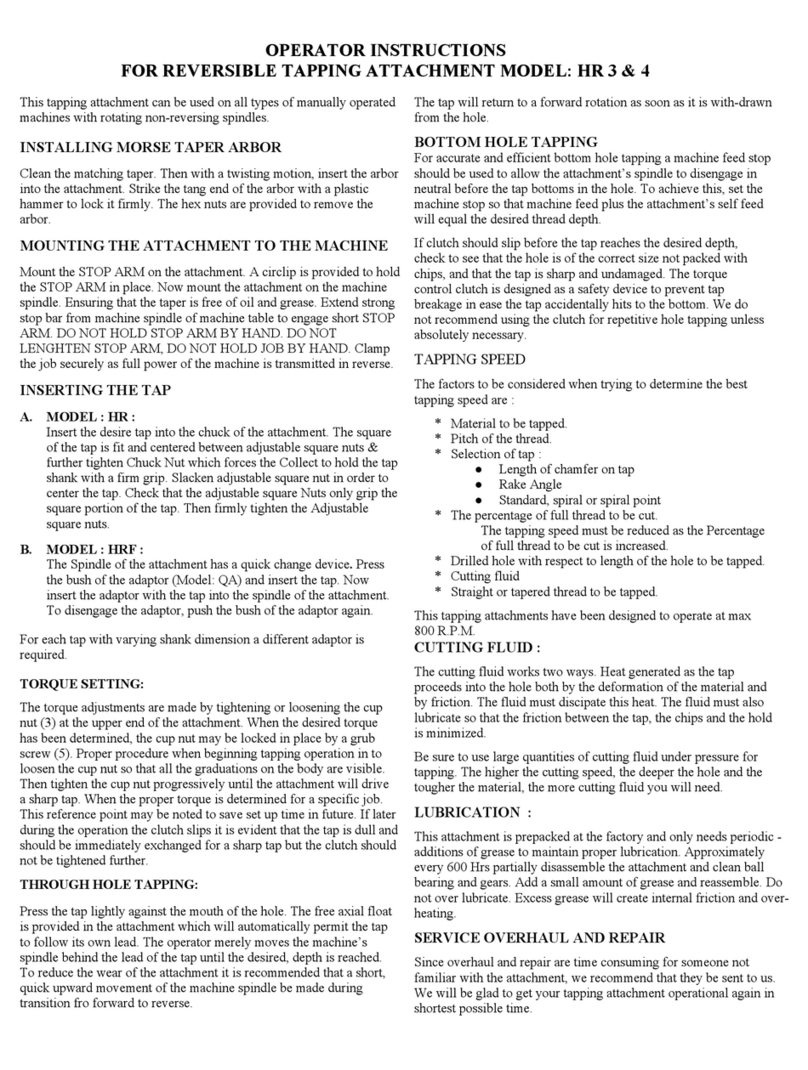
Taco
Taco HR Series Specifications
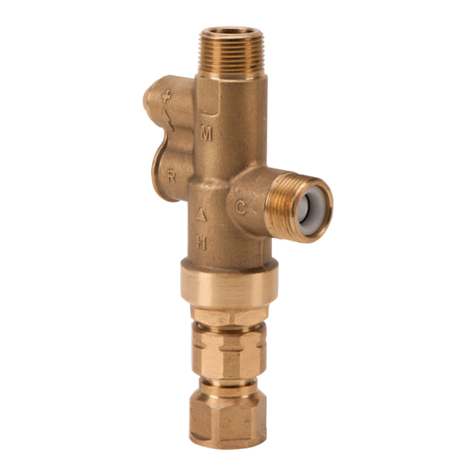
Taco
Taco 5123-WH-N User manual
Popular Control Unit manuals by other brands
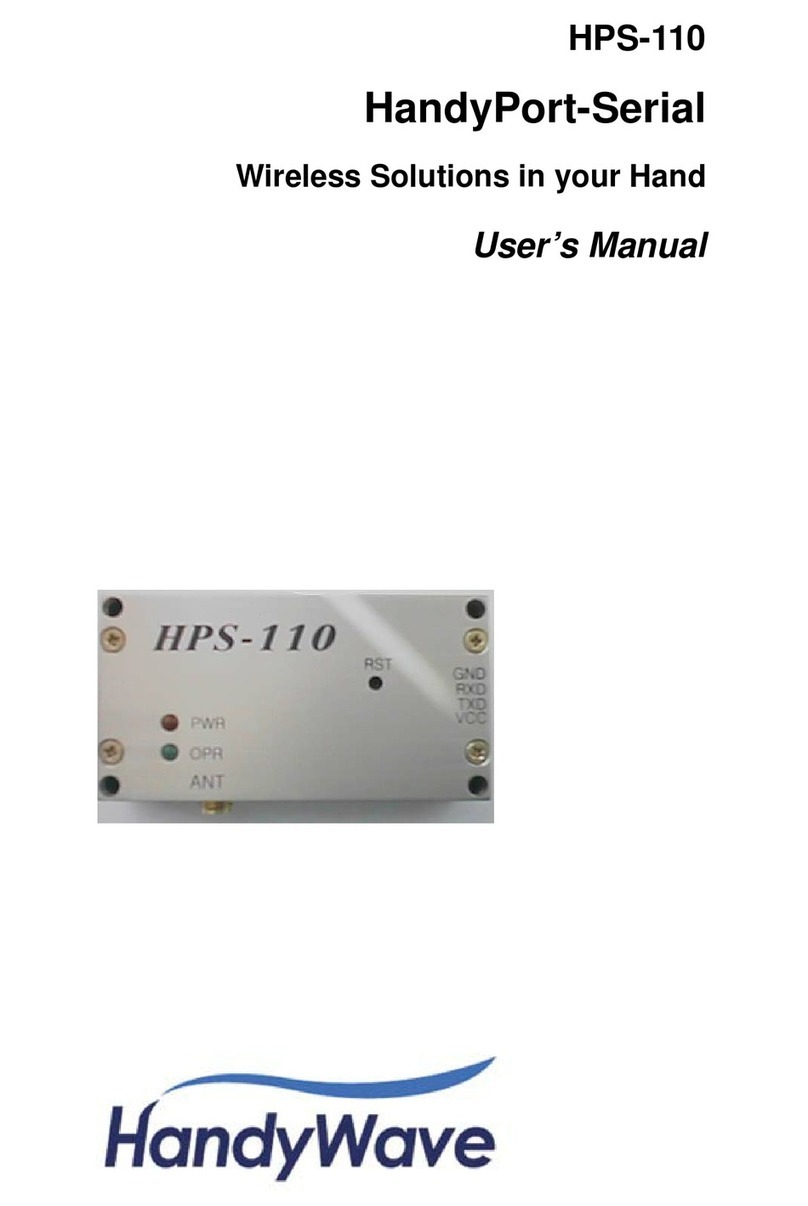
HandyWave
HandyWave HandyPort Series user manual
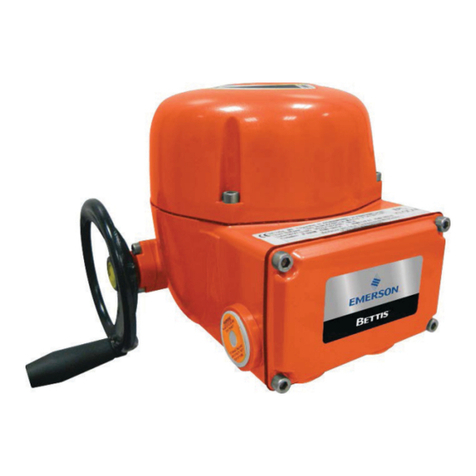
Emerson
Emerson Bettis OM13-SCE300 Installation, operation and maintenance manual
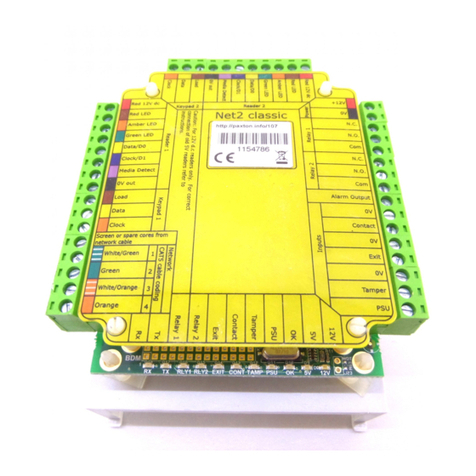
Paxton
Paxton Ins-30000 Net2 classic quick start guide
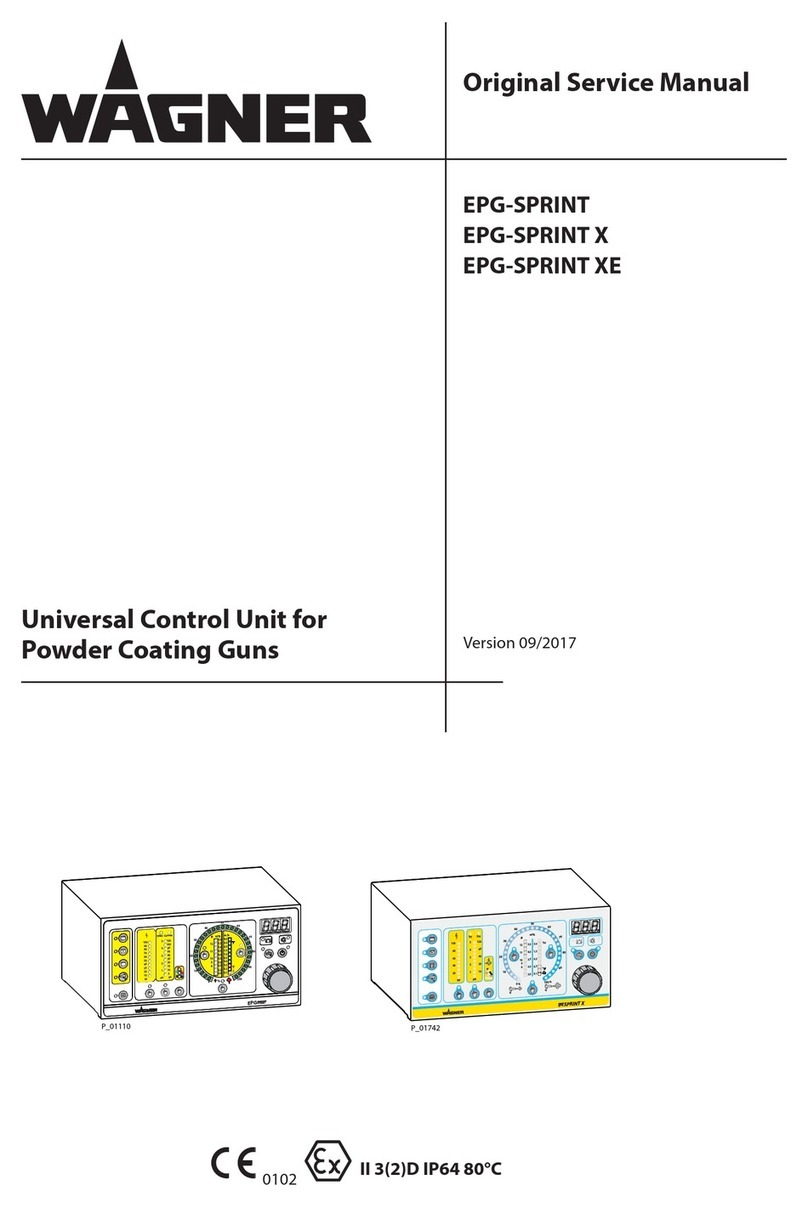
WAGNER
WAGNER EPG-SPRINT Original service manual
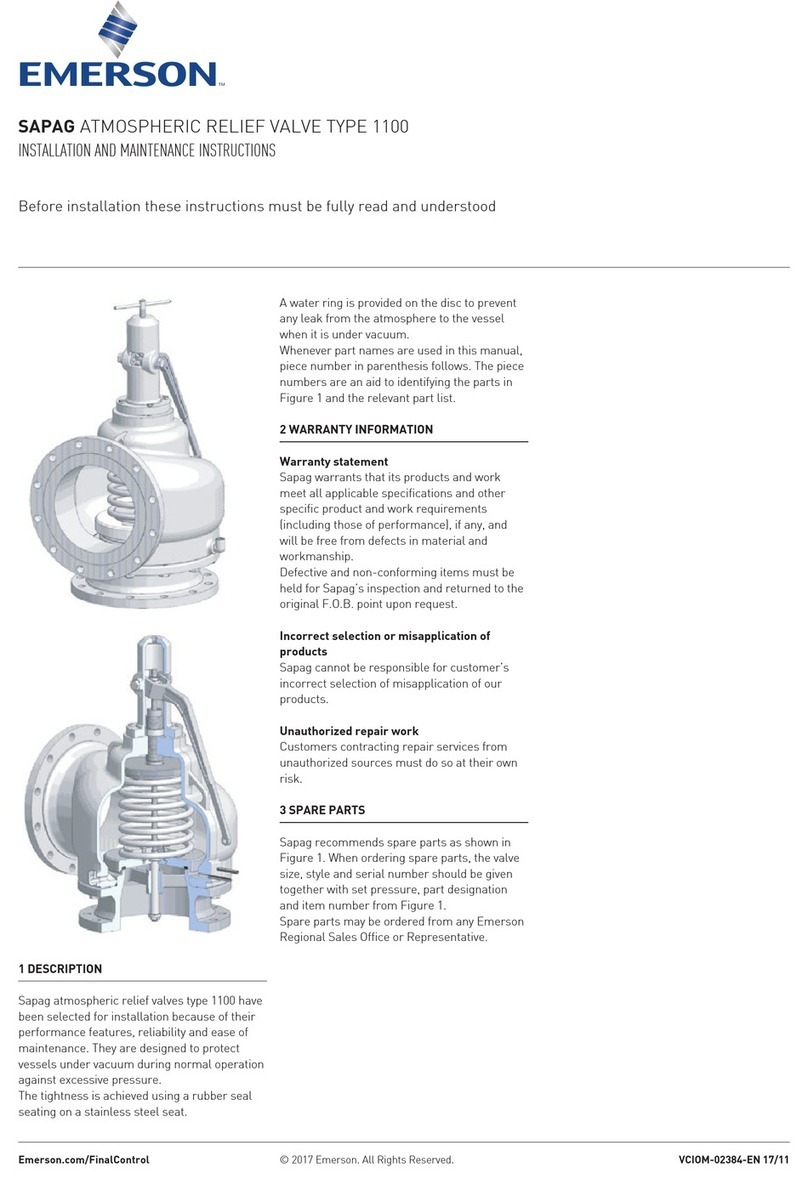
Emerson
Emerson Sapag 1100 Installation and maintenance instructions

TECO
TECO Foxtrot C-WG-0503S Basic documentation