VPro BR Series User manual

OSRBR208-EN
1/14
Instruction manual
Electric
Actuated B
all
Valve
B
R
VR
GS
T
R
L
R
L
3
SP-1384
Please read this manual before installation and use.
GENERAL
It composed of flange-end ball valve and high-power electric actuator.
(proportional control)
Actuator
PDX : For AC / DC power. It corresponds to various control input
signals.
PHX : For AC / DC power.
Valve
BR type For various fluids and general use.
VR type For control
GS type For Wafer. (JIS 10K / 20K)
TR type For mixing / dividing.
LR type For mixing / dividing.
L3 type Trunnion structure. (L)
PRODUCT CODE
BR type (JIS 10K) B R 1 - - -
(JIS 20K) B R 3 T T - - -
VR type (V-port) V R 1 U U - - -
(Reduced port) V R 1 U U R 0 1 5 - -
GS type (V-port) G S 3 U U V - -
(Full port) G S 3 U U - - -
(Standard port) G S 3 U U R - -
TR type T R 1 T T P - - -
LR type L R 1 T T P - - -
L3 type L 3 1 T T G - - -
(1) (2) (3) (4) (5) (6) (7) (8) (9) (10) (11)
(1) Actuator
PDX PHX
(2)
Valve
BR
VR
GS
TR LR L3
(3)
Voltage
1 : 100 / 110 V AC
2 : 200 / 220 V AC
0 : 24 V DC
3 : 24 V AC
(4) Sizing code
0 : Standard
1 : Light
2 : Heavy
(5) Connection
1 : JIS 10K
3 : JIS 20K
(6) Body material
T : SCS13A
U : SCS14A
(7) Ball material
T : SUS304 / SCS13A
U : SUS316 / SCS14A
(8) Seat material
F : F-PTFE
G : R-PTFE
R : R-F-PTFE
K : PEEK
I : API
C : R-PEEK
M : SUS316 + Stellite
P : R-PTFE
(9) Size [mm]
ex. 25 A 025
(10) Option
L: Auxiliary limit switch
EA : Alarm output board
EI : 4 to 20 mA
Indication signal board
(11) Operation mode
Nil : Mode A
J : Mode B
TR LR / L3
BR / VR GS

OSRBR208-EN
2/14
VALVES SPECIFICATIONS
Water Oil Air, Gas Steam Chemicals Sea water Slurry Negative pressure
BR
VR
type
Valve type BR VR
Design 2-way, Full port 2-way, V-port
Connection JIS10K Flanged-end JIS20K Flanged-end JIS10K Flanged-end
Fluid
Max pressure 1 MPa 2 MPa 1 MPa
Size [mm] 015 to 100 015 to 150 015 to 080 015 to 080
Material Body SCS14A SCS13A SCS13A SCS14A
Ball SCS14A SCS13A SCS13A SUS316 / SCS14A
Seat F-PTFE R-PTFE R-F-PTFE R-PTFE R-F-PTFE
Stem seal Packing R-PTFE R-PTFE
O-ring FKM FKM
The optional for steam fluids.
Valve type Option code O-ring
BR
VR
ST Replace (Steam resistant FKM)
PRESSURE & TEMPERATURE RATING
BR (JIS 10K) BR (JIS 20K) VR
Note) Insulation options are required for use with fluids more than 150 °C.
INHERENT FLOW CHARACTERISTIC
VR
Cv value (%)
Valve opening (%)
Range ability
V
R-1UUG - 015 to 080
V
R-1UUG R 015
50:1
100:1

OSRBR208-EN
3/14
VALVES SPECIFICATIONS
Water Oil Air, Gas Steam Chemicals Sea water Slurry Negative pressure
GS type
Valve type GS
Design 2-way, Wafer
Connection JIS Flanges 10K / 20K
Fluid
Max pressure 2 MPa
Size [mm] 015 to 150
Material Body SCS14A
Ball SCS14A (HCr PLTD)
Seat R-PTFE PEEK API R-PEEK SUS316 + Stellite
Stem seal Packing R-PTFE
PRESSURE & TEMPERATURE RATING
Note) Option for use in fluid temperature more than 170 °C.
SEAT LEAKAGE VOLUME
Seat material Leakage rate Remarks
G R-PTFE We prefer to K seat depends on pressure or
environmental conditions. please consult us
for your specifications.
API cannot be used with steam fluid.
K PEEK Bubble-tight
I API
C R-PEEK Less than 0.00001 % of rated Cv.
(V-ported type is 5 to 8 times the above.)
1/1000 of ANSI B16.104 Class IV.
M SUS316 + Stellite Less than 0.01 % of rated Cv.
(V-ported type is 5 to 8 times the above.)
ANSI B16.104 Class IV.
Note) M seat can also be manufactured at ANSI B16.104 Class V.
INHERENT FLOW CHARACTERISTIC
Cv
value (%)
Valve opening (%)
Range ability
GS-3UU V 015 to 032
GS-3UU - 015 to 080
GS-3UU R 040 to 150
50:1
200:1
100:1

OSRBR208-EN
4/14
VALVES SPECIFICATIONS
Water Oil Air, Gas Steam Chemicals Sea water Slurry Negative pressure
TR LR L3 type
Valve type TR / LR L3
Design 3-way, Full port 3-way, Full port
Connection JIS10K Flanged-end JIS10K Flanged-end
Fluid
Max pressure 1 MPa 1 MPa
Size [mm] 020 to 040 050 to 100 025 to 150
Material Body SCS13A SCS13A
Ball SUS304 SCS13A SCS13A
Seat R-PTFE R-PTFE
Stem seal Packing R-PTFE PTFE
O-ring FKM -
The optional for steam fluids.
Valve type Option code O-ring
TR LR ST Replace
L3 ST-VF Add
O-ring: Steam resistant FKM
PRESSURE & TEMPERATURE RATING
TR / LR L3
Note) Insulation options are required for use with fluids more than 150 °C. (L3: 170 °C)
INHERENT FLOW CHARACTERISTIC (TR / LR)
020 mm 025 mm 040 mm 050 to 100 mm
Cv
value (%)
Cv value (%)
Cv value (%)
Cv value (%)
Valve opening (%)
Valve opening (%)
Valve opening (%
)
Valve opening (%)
Range ability
20:1
INHERENT FLOW CHARACTERISTIC (L3)
025 mm 040 to 150 mm
Cv value (%)
Cv value (%)
Valve opening (%)
Valve opening (%)
Range ability
30:1
FLOW PATHS (Position / P1) (Position / P2)
P1 P2
Note) When a closed path is exposed to high pressure, it may leak slightly to an open path. (TR / LR)

OSRBR208-EN
5/14
ELECTRIC ACTUATOR SPECIFICATIONS
3 way valve: SHUT / Position , OPEN / Position
PDX type
Actuator type
(:Voltage code) PDX-300- PDX-700- PDX-02K- PDX-06K-
Voltage 100 / 110 V AC ±10 % 50/60 Hz (Code: 1)
200 / 220 V AC ±10 % 50/60 Hz (Code: 2)
24 V AC ±10 % 50/60 Hz (Code: 3)
24 V DC (Code: 0)
Rated torque [Nm] 21 50 140 400
Operation time [s] 6 to 20, Variable 15 to 50, Variable 30 to 100, Variable 90 to 300, Variable
Power consumption
(Max) [VA]
AC power 100
DC power 80
AC power 150
DC power 120
Motor DC motor (VIC: voltage, current control)
Overload protection Current limiter
Method of operation Proportional control
Input signal 4 to 20 mA 1 to 5 V (Input resistance: 250 ) (Standard)
0 to 5 V 0 to 10 V 2 to 10 V (Input resistance: more than 1 M )
0-135 to 0-1 k Potentiometer input (Applied voltage: 5 V DC)
Operation *¹ [Mode A]
[Mode B]
SHUT by decreased signal OPEN by increased signal
SHUT by increased signal OPEN by decreased signal
[Forced open / shut] It takes priority over the input signal.
C-S is ON SHUT C-O is ON OPEN Common in mode A / B
Indication signal 0 mA : SHUT 1 mA : OPEN (External load resistance: less than 3 k)
Common in mode A / B
Override switch It takes priority over the input signal. Common in mode A / B
Dry contact / Transistor, Open collector. (Input signal current: 6 mA 15V DC)
Operating range SHUT: 0 to 40% OPEN: 50 to 100%
Resolution Less than 0.5 % Less than 0.2 %
Duty cycle 50% 30 min.
Ambient
temperature -20 to 55 °C
Space heater 3 W
Manual operation Manual over-ride with clutch. (Direct operation / 06K: Operation by manual shaft.)
Enclosure Equivalent to IP65 (IEC 60529)
Housing material Aluminum alloy die cast (acrylic resin baking finish)
Wire connection Terminal Block: M3, Ground terminal: M3
Conduct port 2-G1/2 Attachments: Cable gland (for 6 to 12 mm cable), plug.
*¹ Change by DIP switch. (Standard Potentiometer input or 0 to 5 V 0 to 10 V 2 to 10 V)
*² Change by DIP switch. (Standard Mode B)

OSRBR208-EN
6/14
ELECTRIC ACTUATOR SPECIFICATIONS
3 way valve: SHUT / Position , OPEN / Position
WIRING
PDX Setting with DIP SW
• Operation
Mode A Mode B
• Input signal
4 to 20 mA / 1 to 5 V
0-135 to 0-1 k
Potentiometer input / 0 to 5 V
0 to 10 V 2 to 10 V
Note) Input signal circuit is non-isolated. Do not connect DC (minus) wire to other DC (minus) common.
ADJUSTMENT OF ACTUATOR
PDX Dead band
Turn the trimmer clockwise for wide the dead band
as necessary. It is useful to prevent the hunting
reaction of actuator. *Each trimmer on a built-in
control board.
Operating range
Turn clockwise and adjust valve/damper to open
side.
• Adjust the closed position by SHUT trimmer.
• Adjust the open position by OPEN trimmer.
Operating speed (Speed control)
Slow by turn the S.C. trimmer counterclockwise.
Fast by turn the S.C. trimmer clockwise.
Note) The operation time is the time when it is operated
by the override switch.
Operation time with the override switch cannot be
adjusted with S.C. trimmer.
At factory shipment, the S.C trimmer is set to the
fastest position.
M
S.LS
O.LS
DIPSW
4
321
ON
OFF
ZERO SPAN
D.B. S.C.
SHUT OPEN
0〜40% 50〜100%
T2
T1
-
+
O
S
C
B
R
W
+
-
-
+
+
-
+
-
R
W
B
R
W
C
B
R
〜
AL(AlarmLED)
Groundterminal(M3)
Motor
(Indicationsignal)
Dead
band Speed
control
(Operationrange)
Potentiometer
1KΩ
Indication
signal
0to1mA
Voltage
100/110VAC
200/220VAC
24VAC
24VDC
OverrideSW
OPEN
SHUT
Positionerboard
Inputsignal
4to20mA
1to5V
Inputsignal
0to5V
0to10V
2to10V
Resistance
input
0-135Ω
to
0-1KΩ
(100/110VAC)
(200/220VAC)
(Rcore
transformer)
4321
ON
OFF
4321
ON
OFF
4321
ON
OFF
4321
ON
OFF
4321
ON
OFF
4321
ON
OFF
ZERO SPAN
SHUT OPEN
D.B.
AL
S.C.
D.B. S.C.
SHUT OPEN
SPANZERO
ON
OFF
(S2) (S3)DIPSW(S1)
1 2 3 4
T1T2WRBCSO+-
Deadband
wide
Speedcontrol
fast
Operatingrange
open open
Indicationsignal
decrease increase
Positionerboard
PDX
SHUT
LED
OPEN
LED

OSRBR208-EN
7/14
ELECTRIC ACTUATOR SPECIFICATIONS
3 way valve: SHUT / Position , OPEN / Position
PHX type
Actuator type
(:Voltage code) PHX-300- PHX-700- PHX-02K- PHX-06K-
Voltage 100 / 110 V AC ±10 % 50/60 Hz (Code: 1)
200 / 220 V AC ±10 % 50/60 Hz (Code: 2)
24 V AC ±10 % 50/60 Hz (Code: 3)
24 V DC (Code: 0)
Rated torque [Nm] 21 50 140 400
Operation time [s] AC: 1.2 to 2.5
DC: 2 to 2.5
(Max 8)
AC: 3.5 to 7
DC: 4.5 to 7
(Max 22)
AC: 11 to 23
DC: 15 to 23
(Max 78)
AC: 35 to 70
DC: 45 to 70
(Max 230)
The operation time is the time when it is operated by the override switch.
Operation time with the override switch cannot be adjusted with S.C. trimmer.
At factory shipment, the S.C trimmer is set to the fastest position.
Power consumption
(Max) [VA] 120
Motor Brushless DC motor (PWM Control)
Overload protection Current limiter
Method of operation Proportional control
Input signal 4 to 20 mA / 1 to 5 V (Input resistance: 250 )
Operation *¹ [Mode A]
[Mode B]
SHUT by decreased signal OPEN by increased signal (Standard)
SHUT by increased signal OPEN by decreased signal (Option: J)
[Forced open / shut] It takes priority over the input signal.
C-S is ON SHUT C-O is ON OPEN Common in mode A / B
Indication signal 0 mA : SHUT 1 mA : OPEN (External load resistance: less than 3 k)
Common in mode A / B
Override switch It takes priority over the input signal. Common in mode A / B
Dry contact / Transistor, Open collector. (Input signal current: 6 mA 15V DC)
Operating range SHUT: 0 to 40 % OPEN: 50 to 100 %
Resolution Less than 0.2 %
Duty cycle 100 %
Ambient
temperature -20 to 55 °C
Space heater 3 W
Manual operation Manual over-ride with clutch. (Direct operation / 06K: Operation by manual shaft.)
Enclosure Equivalent to IP65 (IEC 60529)
Housing material Aluminum alloy die cast (acrylic resin baking finish)
Wire connection Terminal Block: M3, Ground terminal: M3
Conduct port 2-G1/2 Attachments: Cable gland (for 6 to 12 mm cable), plug.
*¹ Change by DIP switch. (Standard Mode B)

OSRBR208-EN
8/14
ELECTRIC ACTUATOR SPECIFICATIONS
3 way valve: SHUT / Position , OPEN / Position
WIRING
PHX Setting with DIP SW
• Mode setup
Mode A Mode B
• AC / DC mode change
ON AC power OFF DC power
Note) AC / DC mode change is
Factory-adjusted.
Note) Input signal circuit is non-isolated. Do not connect DC (minus) wire to other DC (minus) common.
ADJUSTMENT OF ACTUATOR
PHX Dead band
Turn the trimmer clockwise for wide the dead band
as necessary. It is useful to prevent the hunting
reaction of actuator. *Each trimmer on a built-in
control board.
Operating range
Turn clockwise and adjust valve/damper to open
side.
• Adjust the closed position by SHUT trimmer.
• Adjust the open position by OPEN trimmer.
Operating speed (Speed control)
Slow by turn the S.C. trimmer counterclockwise.
Fast by turn the S.C. trimmer clockwise.
Note) The operation time is the time when it is operated
by the override switch.
Operation time with the override switch cannot be
adjusted with S.C. trimmer.
At factory shipment, the S.C trimmer is set to the
fastest position.
-
+
O
S
C
I+
I-
T2
T1
1
DIPSW
OFF
2 3
ON
ZERO SPAN
D.B. S.C.
SHUT OPEN
0〜40% 50〜100% S.LS
O.LS
M
+
-
-
+
+
-
AL(AlarmLED)
Dead
band Speed
control
Potentiometer
1KΩ
Brushless
DCmotor
Groundterminal(M3)
(Indicationsignal)
(Operationrange)
Indication
signal
0to1mA
Voltage
100/110VAC
200/220VAC
24VAC
24VDC
Inputsignal
4to20mA
1to5V
OverrideSW
SHUT
OPEN
Positionerboard
(100/110VAC)
(200/220VAC)
(Rcore
transformer)
1
OFF
2 3
ON 1
OFF
2 3
ON
1
OFF
2 3
ON 1
OFF
2 3
ON
DIPSW
1
ON
OFF
T1T2I-I+CSO+-
2 3
ZERO SPAN
SHUT OPEN
D.B.
AL
S.C.
D.B. S.C.
SHUT OPEN
SPANZERO
Deadband
wide
Speedcontrol
fast
Operatingrange
open open
Indicationsignal
decrease increase
Positionerboard
PHX

OSRBR208-EN
9/14
ELECTRIC ACTUATOR SPECIFICATIONS
3 way valve: SHUT / Position , OPEN / Position
OPTIONAL PARTS
Specifications Code No. PDX PHX Remarks
Input signal 4 to 20 mA or 1 to 5 V Nil Mode A (Standard)
and J Mode B
operation 0-135 to 0-1 k Potentiometer input or 0 to 5 V F Mode A
K Mode B
0 to 10 V G Mode A
N Mode B
2 to 10 V H Mode A
M Mode B
Auxiliary limit switch L0 For standard signal
(Select limit switch depending on the load) L2 For micro load signal
Alarm output board EA EI and EA
4 to 20 mA Indication signal board EI cannot be used together.
*Auxiliary limit switch: Please refer to the specifications.
WIRING (OPTION)
L0 / L2 Auxiliary limit switch EA Alarm output board EI 4 to 20 mA Indication signal board
At CLOSE side, LC and LS is ON.
At OPEN side, LC and LO is ON.
ON point can be reset by adjusting
the cam.
NO : Normally open
NC : Normally closed
Alarm SW will be ON, when
overload protector works.
Error 11 and 12 is ON.
Normal 11 and 13 is ON.
Cannot be used with EI option.
The angle range of 4 to 20 mA can be
adjusted by ZERO / SPAN trimmer on
control board. Output signal (0 to 1 mA)
cannot be used together.
com.
LO
LS
OLS
SLS
LC
SHUToutput
OPENoutput
Actuatorwiring
OLSSLS
OFF
ON
SHUT OPEN
13
12
11com.
NO
NC
Actuatorwiring
Alarmoutput
board
-
+
12
11
-
+
ZERO SPAN
+
-
+
-
4〜20mA
Actuatorwirin:PDX,PHX
Actuator
Positionerboard
4〜20mA
EIOption
Unavailable
0〜1mA

OSRBR208-EN
10/14
ELECTRIC ACTUATOR SPECIFICATIONS
3 way valve: SHUT / Position , OPEN / Position
DIMENSIONS
Parts name
1 Body 5 Terminal block 9 Transformer 13 Rubber packing
2 Motor cover 6 Limit switch 10 Drive shaft
3 Motor 7
SW setting cam
11 Manual clutch
4 Control board 8 Potentiometer 12 Manual shaft (For 06K)
11
58
7
6
9
12
13
2
3
4
1
10
PDX-300, 700 PDX-02K PDX-06K
PHX-300, 700 PHX-02K PHX-06K 175
220
115
217.5
156
2-G1/2
105
175
160
92.5
189
115
2-G1/2
105
175
160
92.5
167
115
2-G1/2
3 8
13
5
9
6
7
1
11
10
1
11
10
2
4
3 8
13
5
9
6
7
2
4

OSRBR208-EN
11/14
INSTALLATION, OPERATION & MAINTENANCE INSTRUCTIONS
HANDLING & STORAGE
HANDLING
Proper care in handling the valve should be taken to
prevent damage. Do not drop or throw it.
STORAGE
Store the valve in the protected area from dust,
moisture, and direct sunlight. If possible, should be
kept in the original packaging.
CHECKING
• Check the product code, power supply, and voltage
before installation.
• Make sure that the bolts are not loose.
• DIP switch be sure perform set up before a power
supply injection.
Should not change an unnecessary switch.
INSTALLATION
PRECAUTIONS
Before installing, clean pipe and valve ends.
Make sure they are free of dirt, dust and etc.
PIPING FLANGES
• GS / VR type has a flow direction. Install the valve
accordingly.
• Specify the ST option if a steam fluid. Flow direction is
restricted by ST option. (BR)
• Gasket should be selected appropriately to suit the
fluid, pressure and temperature.
Use spring washer to prevent from decreasing surface
pressure gasket when the temperature change
happens frequently.
• Tighten all bolts using crossover method to load the
joint evenly.
• Wafer type ball valve is put between two seats of
flanged-end and tightened with long bolts. (GS)
• In the TR / LR type, when the flow path is subjected to
a high pressure from arrow, it may leak slightly to the
low pressure port.
ENVIRONMENT
• Do not install in place where corrosive gas is present
or where vibration is heavy (0.5 G or more).
• When radiant heat causes the surface temperature of
the control unit to exceed 55 °C, provide an
appropriate shielding plate.
• If there is a possibility that the fluid and drive part
freeze, please take measures to prevent freezing.
POSITIONING
• Should be positioned through 90° upward from
horizontal. Provide space around the product to allow
manual operation, inspection and replacement work.
• Maintenance space more than 120 mm upward from
the actuator is required.
OTHER NOTES
Until the wiring is completed there must be no
condensation or flooding in the interior of the actuator,
after piping. Protective caps on the cable gland are
not waterproof.
CAUTIONS FOR MAINTENANCE (GS / L3)
Do not keep warm for maintenance of the valve gland.
GS L3
TIGHTEN THE GLAND NUTS (GS / L3)
• Check that there is no leakage from the gland
packing.
• If it leakage, tighten gland nuts by alternately.
Do not over-tighten the gland nuts.
GS L3
Recommended torques [Nm]
Valve size [mm]
Torque
GS L3
V-port Full port Standard port
015 to 020 015 to 020 - - 2
025 to 032 025 to 032 040 025 3.5
- 040 to 050 050 to 065 040 to0 50 7
- 065 to 080 080 to 100 065 to 080 10
- - 125 to 150 100 to 125 14
- - - 150 20
Gland nut
Gland plate
Stem
Packing
Gland nut

OSRBR208-EN
12/14
INSTALLATION, OPERATION & MAINTENANCE INSTRUCTIONS
WIRING
PRECAUTIONS
• Remove the actuator cover before wiring.
• Two G1/2 electrical connections are provided with a
cable gland and plug. Usable cable size is 6 to 12
mm.
• When using a flexible tube, dew condensation may
occur inside the actuator due to respiration from the
inside of the tube and malfunction may result. Seal the
flexible tube connector part with a sealant.
• Sealants that affect the electrical contacts should not
be used inside the electric actuator.
• If long distance wiring or low voltage operation, check
that terminal voltage is in the proper range.
• Input signal circuit is non-isolated.
Do not connect DC (minus) wire to other DC (minus)
common.
CONNECTION
• Do not wiring outdoors on a rainy day.
• Check the power supply and voltage.
Connect the signal as shown in the wiring diagram.
Do not connect unnecessarily terminal.
• Check whether the MODE change DIP SW on a
circuit board substrate is set up correctly.
• When wiring, if wiring of a signal is mistaken, it will not
operate correctly. Contact us when you use two valve
or more by one controller or indicator.
• Actuator should be electrically grounded.
Use the terminal marked ( ) inside the actuator.
PREVENT DEW CONDENSATION
• When installing the cover after wiring, perform the bolt
by the temporary tightening procedure and the
permanent tightening procedure to tightly and
securely tighten the rubber packing so that water does
not enter from the outside.
• Tighten the cable gland nut so that there is no leakage
from the wire entrance.
CONTROL
INPUT SIGNAL
• Use shielded wire for signal wiring where high level
noise is generated or when the wiring distance is long.
• Control with a 1 to 5 V input signal becomes an input
resistance 250 . Provide a voltage that can safely
20mA or more than.
DC POWER SUPPLY
• Battery or full wave rectification can be used.
• Consider an inrush current of motor.
(It is 1.5 to 3 times of consumed current.)
• When using a DC voltage, be selected the wire
thickness by the wiring distance.
• Do not use power supply that require more than
1 second with rise and fall time.
INPUT SIGNAL AND OPERATION MODE
The input signal and operation mode are set as
follows. (Factory shipped)
Input signal 4 to 20 mA or 1 to 5 V
Operation mode Mode A
Operation SHUT by decreased signal.
OPEN by increased signal.

OSRBR208-EN
13/14
INSTALLATION, OPERATION & MAINTENANCE INSTRUCTIONS
OPERATION
TESTING
• Make sure that power supply voltage is correct. Also
check operating position, wiring, speed and signals.
• During trial operation, check that valve movement and
output signal are correct.
CONFIRM THE OPERATING CONDITION
• Adjust fluid condition, controller setting, sensor etc. so
that stable control is achieved.
• When used in an unstable control state, the life of the
actuator and the valve will be shortened.
• The desired control state is stable at the target value.
Adjust the PID setting value of the controller when
overshooting the target value greatly, when not
converging for a long time or hunting operation. Also,
when the time delay is large, please consider the
sensor position.
DUTY CYCLE (PDX)
Confirm that the operation frequency is within the
specified duty cycle.
Use beyond the load time rate range will affect
product life. Also, it may cause burnout.
Duty cycle is a value that regulates the opening /
closing frequency of the actuator.
The meaning of 50 % 30 minutes for Duty cycle is
that 15 minutes (50 % of 30 minutes) operation is
possible. The calculated value obtained by dividing
15 minutes by the operation time is the number of
times of operation within 30 minutes.
ATTENTION
• Do not change an unnecessary dip switch.
• Keep power supplied for built-in space heater to
prevent condensation inside actuator.
• Do not touch the moving parts of actuator in
operation.
• Never put anything on the actuator or make it into a
foothold.
MANUAL OPERATION
PRECAUTIONS
• Be sure to turn off the power before manual operation.
• Operate manually with reference to the opening
degree label. Do not turn beyond the fully open / fully
closed position. Operation failure may occur during
automatic operation.
THE WAY OF OPERATION
PDX / PHX PDX / PHX (06K)
Manual operation can be possible by pulling down
manual clutch knob. Set the knob to manual
position and operate the joint by using an
adjustable wrench in the SHUT/OPEN direction.
When it becomes in the position besides the range
of operation in the case of manual operation, it may
stopped automatic moving.
In case the manual clutch knob is not easy to pull
down, try moving joint or manual shaft to the
opposite direction by wrench. For automatic
operation, reset the knob to automatic position.
Be sure to confirm that knob is reset completely.
Before automatic operation, be sure to remove
wrench.
MAINTENANCE
• To prevent electric shock, be sure to turn off the power
when removing the actuator cover.
• Do the routine maintenance at least once in half a
year.
Inspection items
• Confirm operation of opening and closing.
• Confirm that an actuator is not hot excessively.
• Confirm existence of abnormal noise and
vibration during operation.
• Confirm whether screws are loose or not.
• Confirm that water or condensation no remains
in the actuator.
• Confirm the fluid temperature or pressure.
• Confirm the leak from valve stem.
• Confirm the bolt tightening torque.

OSRBR208-EN
Document is subject to change without notice.
NIPPON VALVE CONTROLS, INC.
1-21-19 Meieki minami, Nakamura-ku, Nagoya 450-0003 JAPAN
TEL: 81-52-582-6435 FAX: 81-52-582-6439
14/14
INSTALLATION, OPERATION & MAINTENANCE INSTRUCTIONS
TROUBLE SHOOTING
Problem Cause Solution
Actuator
does not
move.
Faulty wiring. Correct the wiring.
Voltage and
input signal are
not coming.
Check the voltage and
input signal.
Incorrect
voltage.
When it's burned out by
excess voltage, replace
the actuator.
Connection or
wiring is not
correct.
Correct the miswiring
and misconnection.
Be careful not to
mistake the plus and
minus of wiring.
Short the
circuit, contact
failure.
Review wires and
connection.
Motor is too
old.
Replace the actuator.
Repair in our factory.
LED lamp (S or O) on
the board is lit, but the
motor does not move.
(PDX)
Operation is
unstable.
Excess surge
or voltage was
applied.
• Replace the control
board or limit switch.
(Repair in our factory)
• Replace the actuator.
Rainwater
entered the
actuator.
• Dry the inside.
• Replace the actuator.
Added high
harmonics
noise from an
inverter.
Attachment a filter for
each inverter maker
option.
Effect of high
level noise.
Use the shielded wire
and ground the wiring.
Separate signal wire
from power line.
Problem Cause Solution
Stop in the
mid position.
(Input signal
1 to 5 V)
Signal voltage
source
capacity
shortage.
Use a voltage source
that can be made to
flow more than 20 mA.
Please contact us.
Stop in the
mid position.
• Biting of
valve seat.
• The scale
has adhered
to the valve
ball.
Remove a foreign
object.
Overload
protector runs
because of
over-torque.
Motor protection circuit
returns by the signal of
operation of an
opposite direction. Turn
on the power again.
Alarm LED
is lit.
Stop
automatic
moving after
manual
operation.
Manual clutch
knob is not
reset.
Reset manual clutch
knob.
Out of
operating
range. (06K)
Reset by manual
operation.
Leakage
from
valve body
• Valve cap
get loose.
• Valve body is
damaged.
Replace the valve.
Leakage
from
valve seat
Seat is worn
or damaged.
Replace the valve.
Replace the valve seat.
Leakage
from
valve stem
Stem packing
is worn or
distorted.
Replace the valve.
Replace the packing.
Leakage
from
valve gland
(GS L3)
Gland packing
is worn or
distorted.
Tighten the gland nut.
Replace the gland
packing.
For more information contact
NIPPON VALVE CONTROLS, INC. for consultation.
Other manuals for BR Series
1
This manual suits for next models
9
Table of contents
Other VPro Control Unit manuals
Popular Control Unit manuals by other brands
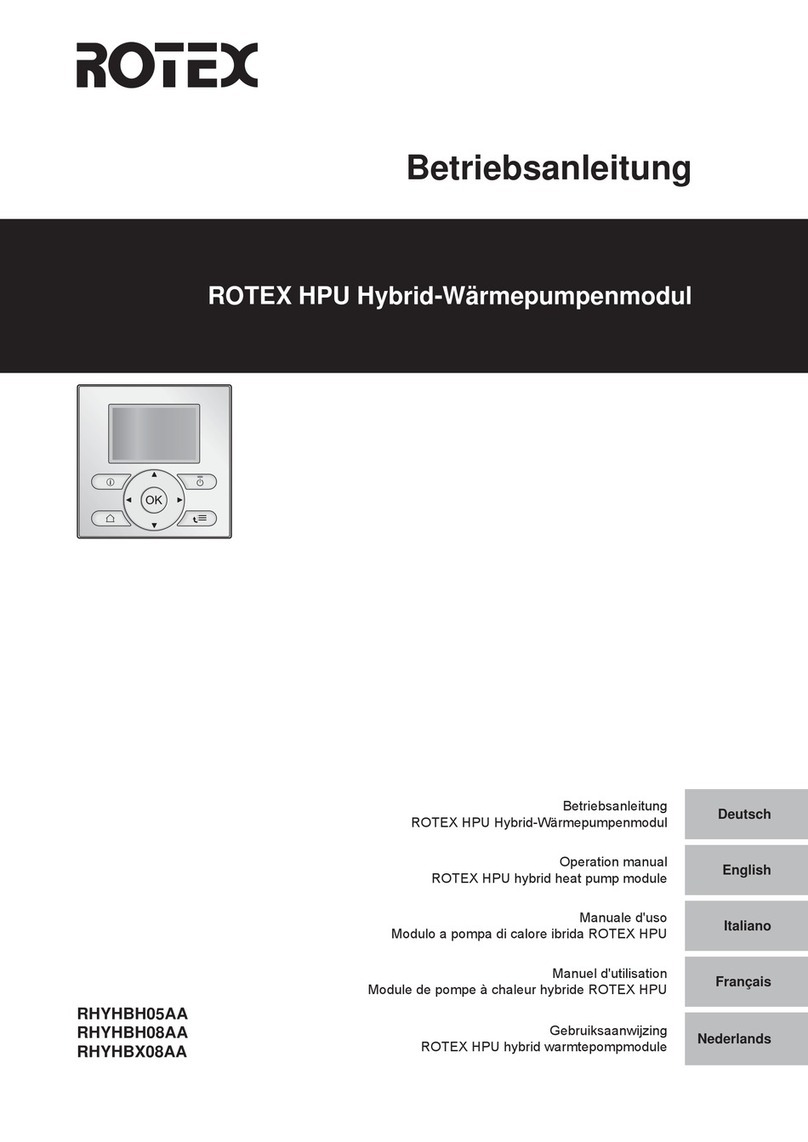
Rotex
Rotex RHYHBH05AA Operation manual

ITT
ITT FABRI-VALVE XS150 Installation and maintenance instructions

ZIEHL-ABEGG
ZIEHL-ABEGG UNIcon CTG-150AV operating instructions
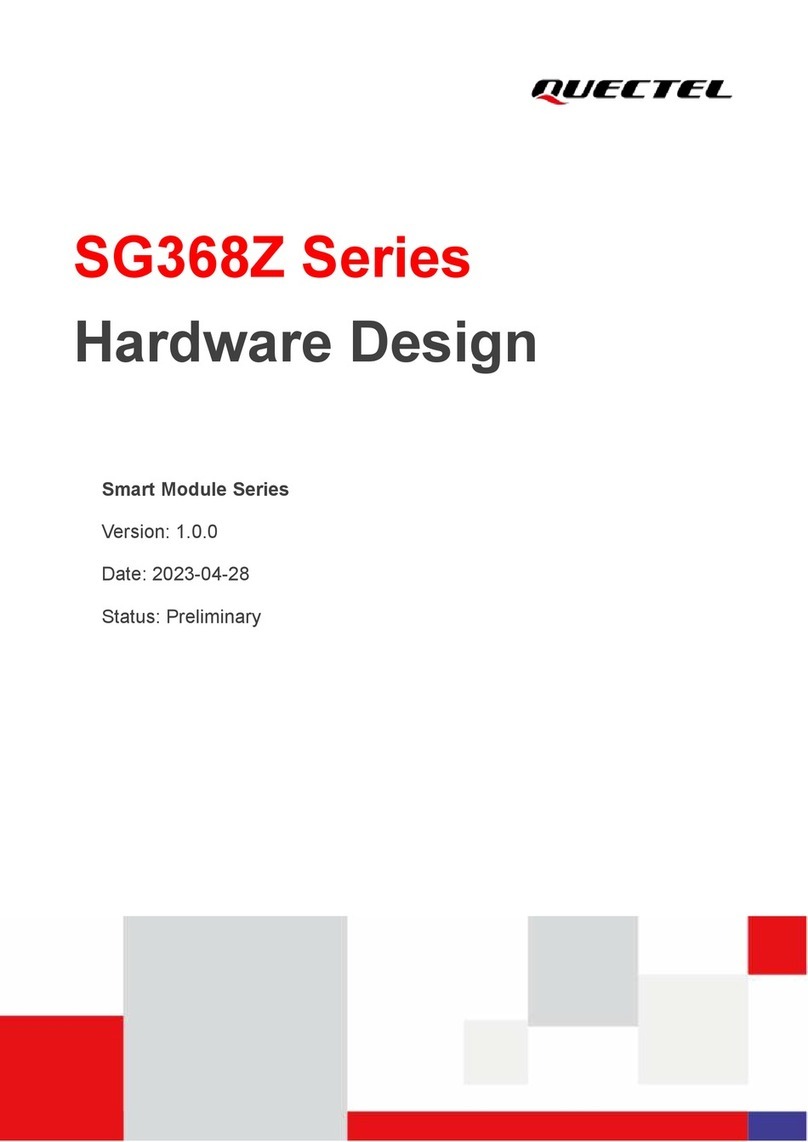
Quectel
Quectel SG368Z Series Hardware design
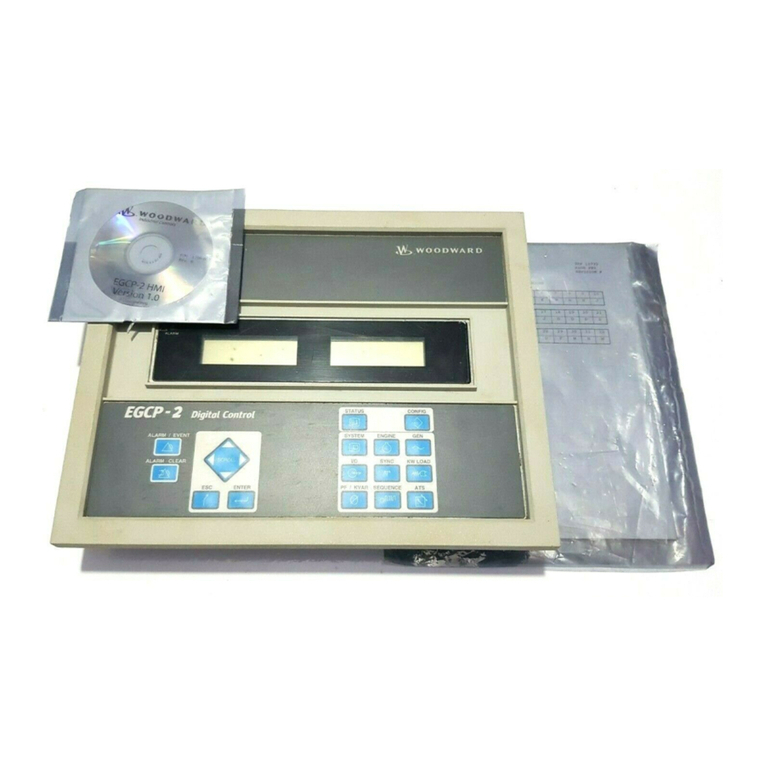
Woodward
Woodward EGCP-2 Installation and operation manual
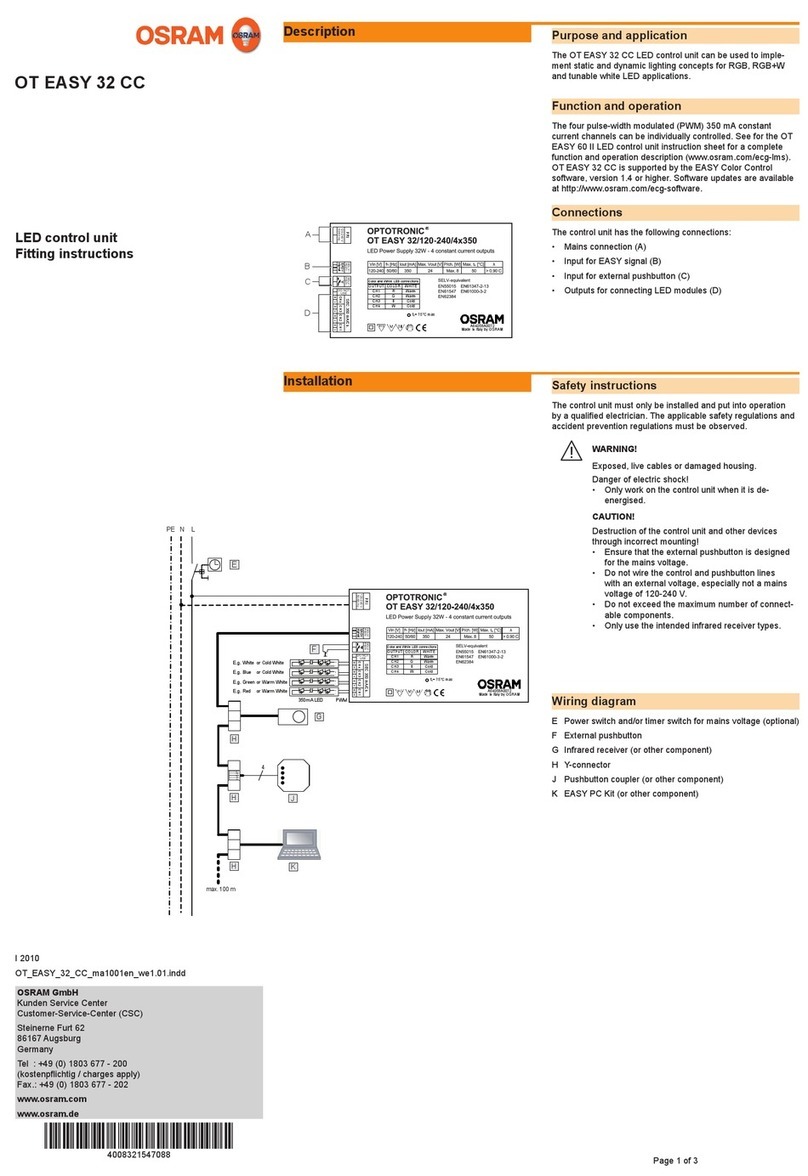
Osram
Osram OT EASY 32 CC Fitting instructions