Wega Mininova User guide

MININOVA
EN ESPRESSO COFFEE MACHINE
Use and maintenance manual for the TECHNICIAN

NERO
C:0 M:0 Y:0 K:100
ROSSO
C:0 M:100 Y:100 K:0
VERDE
C:100 M:0 Y:100 K:0

3
Technical manual
ENGLISH
NERO
C:0 M:0 Y:0 K:100
ROSSO
C:0 M:100 Y:100 K:0
VERDE
C:100 M:0 Y:100 K:0
Index
A General Warnings ........................................................................... 5
B Warnings for the installer............................................................... 5
B.1 Power.................................................................................... 5
B.2 Materials to be used.............................................................. 5
B.3 Hydraulic connections........................................................... 5
B.4 Activation.............................................................................. 5
B.5 Maintenance and repairs....................................................... 6
C Typographical conventions............................................................. 6
Section I - OPERATION....................................................7
1 Technical characteristics ................................................................. 8
1.1 Internal components............................................................. 8
1.2 Internal components........................................................... 10
1.3 Push button panel Mininova 1GR Version EVD.....................12
1.4 Technical data ..................................................................... 12
2 Preparation ..................................................................................13
2.1 Unpacking the machine .....................................................13
2.2 Equipment preparation ......................................................14
3 Machine installation..................................................................... 15
3.1 Positioning..........................................................................15
3.2 Hydraulic connection
(with hydraulic connection available)
..16
3.3 Hydraulic connection (with inner tank)...............................17
3.4 Conversion from TANK to WATER MAINS 1GR Version..........19
3.5 Conversion from WATER MAINS to TANK 1GR Version..........20
3.6 Conversion from TANK to WATER MAINS 2GR Version..........21
3.7 Conversion from WATER MAINS to TANK 2GR Version..........22
3.8 Wiring................................................................................. 23
3.9 Machine start-up ................................................................23
3.10 External motor pump adjustment.......................................24
3.11 Machine tune-up ................................................................24
4 Boilers ..........................................................................................25
5 Control of the pressure in the boiler.............................................. 25
6 Automatic Water Entry .................................................................25
7 Coee delivery groups..................................................................26
8 Electronic control unit (version EVD).............................................26
9 Volumetric dosing (version EVD) ..................................................26
10 Pumping system...........................................................................27
11 Electronic push button panels (version EVD) ................................27
12 Pressure switch.............................................................................27
13 Thermostat...................................................................................27
14 Anti-ooding device.....................................................................28
15 Valve group ..................................................................................28
15.1 Valvola antidepressione ......................................................28
15.2 Safety or pressure relief valve..............................................28
15.3 Expansion-non return valve ................................................28
15.4 BY - PASS valve.................................................................... 28
16 Hot water dispensing nozzle.........................................................29
17 Steam dispensing nozzle..............................................................29
18 Softener .......................................................................................29
18.1 Description.......................................................................... 29
18.2 Measuring of the water hardness........................................29
18.4 Technical data ..................................................................... 30
18.3 Setting by-pass .................................................................. 30
19 Softener .......................................................................................31
20 Descaling......................................................................................32
20.1 1GR Version .........................................................................32
20.2 2GR Version .........................................................................33
21 Cleaning....................................................................................... 34
22 Checks and maintenance..............................................................35
23 Malfunctions and related solutions ..............................................37
24 List of hazards ..............................................................................40
Section II - ELECTRICAL/HYDRAULIC diagrams................ 41
25 Electrical schemes ........................................................................ 42
25.1 Electrical scheme versions1GR EMA-EPU............................. 42
25.2 Electrical scheme version 1GR EVD......................................43
25.3 Electrical scheme version 2GR.............................................44
26 Hydraulic schemes........................................................................45
26.1 Hydraulic scheme 1GR......................................................... 45
26.2 Hydraulic scheme 2GR......................................................... 46

4
NERO
C:0 M:0 Y:0 K:100
ROSSO
C:0 M:100 Y:100 K:0
VERDE
C:100 M:0 Y:100 K:0

5
Technical manual
ENGLISH
NERO
C:0 M:0 Y:0 K:100
ROSSO
C:0 M:100 Y:100 K:0
VERDE
C:100 M:0 Y:100 K:0
!
At the end of the installation, the installer has
to fill the "Installation Card" carryed out with
the machine. On this form must be confirmed
the conditions provided by hygiene and safety
regulations in the place of installation and must
be reported notes about changes and modication
due to a correct function of the machine.
Copies of "Installation Card" must be kept by
the user and installer until the end life of the
machine. In case of withdrawal of the machine,
the installer must provide for the withdrawal of the
"User's Installation Card".
B.1 Power
The water supply of the appliance must be carried out
with water which is suitable for human consumption, in
compliance with the regulations in force int the place
of installation. The owner / manager of the system must
conrm to the installer that the water meets the above
listed requirements.
B.2 Materials to be used
During the installation of the appliance the
components and materials that were provided with
the appliance are to be used. Should the use of other
components be necessary, the installer must verify their
suitability to be used in contact with water used for
human consumption.
B.3 Hydraulic connections
The installer must carry out the hydraulic connections
in accordance with the hygiene norms and the hydraulic
safety norms for environmental protection in force in the
place of installation.
B.4 Activation
When installation is complete, the appliance has to be
started, brought to the nominal working condition and
left for 30 minutes in the“ready to operate” condition.
Afterwards, the appliance has to be turned o and
emptied of the first water introduced in the whole
hydraulic circuit, to eliminate possible initial impurities.
Then the appliance must be once again loaded and
brought to the nominal working conditions.
After having reached the“ready to operate”condition,
the following deliveries have to be performed:
1. for each coee group make a continous erogation
to discharge all volume of water contained in each
coee tank combined;
2. release the whole volume of hot water inside the
boiler by performing a continuous delivery from the
appropriate nozzle. In the case of several dispensing
points, divide the volume on the base of the number
of the dispensing points;
3. continuously release steam for at least 1 minute for
each steam dispensing point.
AGeneral Warnings
The manufacturer of the equipment cannot be held
responsible for damage caused by failure to oblige to
the requirements below.
BWarnings for the installer
• Read this manual carefully. It provides important
information on safe installation, operation and main-
tenance of the equipment;
• Installation, conversion to other type of gas, and
maintenance of the equipment must be carried out
by personnel qualied and authorized by the manu-
facturer, in compliance with safety regulations and
instructions included in this manual;
• identify the model of the equipment. The model is
shown on the packaging and on the nameplate of
the machine;
• Install the equipment only on sites where there is
good ventilation;
• Do not obstruct the ventilation and exhaust holes on
the machine;
• Do not tamper with the equipment components.

6
NERO
C:0 M:0 Y:0 K:100
ROSSO
C:0 M:100 Y:100 K:0
VERDE
C:100 M:0 Y:100 K:0
B.5 Maintenance and repairs
After ta maintenance and/or repair intervention, the
components used must ensure that the hygiene and
safety requirements initially foreseen for the appliance
are still met. These are met by using original spare parts
only.
After a repair or a substitution of components related
to parts in direct contact with water and food, a washing
procedure has to be carried out, as in the case of rst
installation.
!This symbol indicates that you must strictly follow the
instructions it refers to, in order to avoid damage to the
appliance or injury.
iThis symbol provides additional information on the
operation of the machine and its components.
CTypographical conventions
!
The user must be sufficiently informed to operate
the appliance correctly. It is recommended not
to carry out any operations on the machine
which may modify or alter its operation.
WHEN THE MACHINE IS OPERATING, THE BOILER
CONTAINS STEAM AND HOT WATER UNDER PRESSURE.
!Themachine'sinstallationandmaintenanceoperations
can onlybe carried outbyqualied technicalpersonnel.
Qualication can be provided by the builder through
participation in specic training courses.
!The installationand maintenance of the machine must
be carried out only by qualied service personnel with
knowledge and practical experience of the machine
itself, with particular attention to the safety aspects
and hygiene.

7
Technical manual
ENGLISH
NERO
C:0 M:0 Y:0 K:100
ROSSO
C:0 M:100 Y:100 K:0
VERDE
C:100 M:0 Y:100 K:0
Section I - OPERATION

8
NERO
C:0 M:0 Y:0 K:100
ROSSO
C:0 M:100 Y:100 K:0
VERDE
C:100 M:0 Y:100 K:0
1Technical characteristics
1.1 Internal components
1. Water tank.
2. Steam knob.
3. Pressure gauge.
4. Machine main switch.
5. Anti-burn rubber.
6. Coee dispensing lever.
7. Steam dispensing nozzle.
8. Boiler heating element indicator light
working.
9. Light water level boiler.
10. Coee dispensing spout.
11. Adjustable foot.
12. Hot water dispensing knob.
13. Hot water dispensing nozzle.
14. Hot water dispensing button.
15. Push button panel.
1
3
2
9
8
4
5
6
7
13 11
12 10
VERSION 1GR
5
2
2
5
2
E
R
O
A
D
F
P
M
M
A
E
S
T
V
P
E
R
U
A
V
A
P
A
U
C
A
W
Q
A
S
E
S
E
R
W
A
T
U
E
A
1
2
3
4
5
7
EMA
EVD
5
2
2
1
2
5
7
4
11
1013
15
EPU
14 13 11 10
4
3
14

9
Technical manual
ENGLISH
NERO
C:0 M:0 Y:0 K:100
ROSSO
C:0 M:100 Y:100 K:0
VERDE
C:100 M:0 Y:100 K:0
1. Water tank.
2. Steam Knob.
3. Hot water dispensing knob.
4. Coee dispensing lever.
5. Coee dispensing spout.
6. Hot water dispensing nozzle.
7. Steam dispensing nozzle.
8. Adjustable foot.
9. Anti-burn rubber.
10. Pressure gauge.
11. Machine main switch.
12. Warning light.
E
R
O
A
D
F
P
M
M
A
E
S
T
V
P
E
R
U
A
V
A
P
A
U
C
A
W
Q
A
S
E
S
E
R
W
A
T
U
E
A
5
2
2
1 2 3 4
11
12
10 9 7 6 58
VERSION 2GR EMA

10
NERO
C:0 M:0 Y:0 K:100
ROSSO
C:0 M:100 Y:100 K:0
VERDE
C:100 M:0 Y:100 K:0
1.2 Internal components
1. Boiler.
2. Electronic control unit.
3. Water tank
(*)
.
4. Volumetric dosing device.
5. Boiler pressure gauge.
6. Dispensing group.
7. Drain pad.
8. Internal vibration pump.
9. Internal motorpump
(*)
.
* optional
8
9
1
23
4
5
6
7
VERSIONS 1GR EMA-EPU-EVD

11
Technical manual
ENGLISH
NERO
C:0 M:0 Y:0 K:100
ROSSO
C:0 M:100 Y:100 K:0
VERDE
C:100 M:0 Y:100 K:0
VERSION 2GR EMA
1
8
6 5 4
3
2
1. Water tank.
2. Electronic control unit.
3. Boiler.
4. Dispensing group.
5. Drain pad.
6. Pressure gauge.
7. Vibration pump.
8. Solenoid valve.
7

12
NERO
C:0 M:0 Y:0 K:100
ROSSO
C:0 M:100 Y:100 K:0
VERDE
C:100 M:0 Y:100 K:0
1.3
Push button panel Mininova 1GR
Version EVD
1.4 Technical data
The nameplate of the machine is xed on the base of
the frame under the drain pan.
2
Large
coees
2
espressos
1 espresso
1
Large
coee
Stop/
Program.
PROG.
STOP
5
2
2
1GR 2GR
Boiler capacity (lt) 2 lt 4lt
Power supply voltage (V) 120 V 230 V 240 V 230/240
Power (W) 1270 W 1570 W 1710 W 2.850
Frequency (Hz) 50-60 Hz 50-60 Hz
Boiler pressure (bar) 1,4 bar MAX 1,4 bar MAX
Safety valve calibration (bar) 2 bar 2 bar
Supply water pressure (bar) 1,5 - 5 bar 1,5 - 5 bar
Coee dispensing pressure (bar) 8 - 9 bar 8 - 9 bar
Operational conditions ( °C / °F ) 5-40 / 41-104 °C / °F 5-40 / 41-104 °C / °F
Net weight with internal motorpump (kg) 30 kg n/a
Net weight with vibration pump (kg) 27 kg 46 kg
Internal water tank capacity (lt) 2 lt 4 lt
Widht (A) (mm) 335 mm 532 mm
Depht (B) (mm) 440 mm 445 mm
Height (C) (mm) Standard groups 430 mm 430 mm
Raised groups 470 mm n/a
C
A
B
E
R
O
A
D
F
P
M
M
A
E
S
T
V
P
E
R
U
A
V
A
P
A
U
C
A
W
Q
A
S
E
S
E
R
W
A
T
U
E
A
5
2
2
A
B
C

13
Technical manual
ENGLISH
NERO
C:0 M:0 Y:0 K:100
ROSSO
C:0 M:100 Y:100 K:0
VERDE
C:100 M:0 Y:100 K:0
technical
data
plate
2Preparation
2.1 Unpacking the machine
Open the packaging, ensuring not to damage the
machine.
Remove the machine protections and the equipment
contained in the package. Take the machine out.
If there is an external motor pump, the motor and the
pump are provided in a separate package.
!Handling operations must be performed by at
least 2 persons or with the aid of suitable lifting
accessories.
!Considering the significant weight of the
equipment, use extreme caution in handling and
use safety gloves.
iAll technical data are indicated on the technical
data plate.
The detais of the equipment are also reported on
the label located on the packaging of the machine.
E
R
O
A
D
F
P
M
M
A
E
S
T
V
P
E
R
U
A
V
A
P
A
U
C
A
W
Q
A
S
E
S
E
R
W
A
T
U
E
A
5
2
2

14
NERO
C:0 M:0 Y:0 K:100
ROSSO
C:0 M:100 Y:100 K:0
VERDE
C:100 M:0 Y:100 K:0
2.2 Equipment preparation
Softener
On request, an automatic resin softener is supplied.
For further information, refer to chapter "Softeners".
Motor pump (only for version 1GR)
For the machines with an external motor, it is
necessary to prepare the pump and the motor.
Assemble the 3/8 gas connection with the inlet lter
(2) of the pump (arrow ) and the plain 3/8 outlet gas
connection (1) of the pump (arrow ).
Use the special washers (3) provided for sealing
purposes.
To correctly couple the pump and motor, use the
appropriate joint
(4)
and the spacer ring
(5),
lock
everything with the two clamps
(6).
The pump and motor joint has to be installed also on
the machines with an internal motor pump.
Filter holder
In the housing of the lter holder (1) place the spring
to stop the lter (2).Take the two cups (3) or one-cup (4)
lter and press it rmly into the lter holder.
Spouts
Complete the lter holder by installing the 2 cups (6)
or one-cup (5) spout. !Install the connection with the inlet lter (2)of
the pump (arrow ).
iInstall the spout with relative lter: one-cup spout
onone-cup lterholderorwithone-cuplter,etc...
6
3
2
3
1
456
5
4
1
2
3
6

15
Technical manual
ENGLISH
NERO
C:0 M:0 Y:0 K:100
ROSSO
C:0 M:100 Y:100 K:0
VERDE
C:100 M:0 Y:100 K:0
3Machine installation
3.1 Positioning
Prepare an ample support base for the machine that
is suitable to support its weight
(13);
It is important for
all terminals of connections to the water mains
(8)
and
to the electrical mains
(15)
to be easily reachable and in
any case in the immediate vicinity of the machine
.
Make sure that there is sucient space for placing
and correctly using the appliance
. When positioning the
machine close to the wall, you have to ensure a minimum
distance of 20 cm between the machine and the wall.
The grinding-dosing machine
(14)
must be placed
in the immediate vicinity of the appliance in order to
allow for comfortable use of the machine
.
It is advisable
to equip the working base of the machine with a drawer
(11)
for used coee grounds, preferably with a rubber
device for tapping the lter holder.
Place the motor pump (10)(only for version 1GR) in a
protected area with no humidity and away from accidental
contact with the operator.
!For correct operation, the machine must rest on a
perfectly horizontal surface. Any alignment of the
machine must be done by adjusting the feet (5).
!In case of installation of the machine in motion
environments (ships, trains, etc.) it's necessary
to use special feet, to be anchored on the support
base, available from the manifacturer.
5
2
2
1
2
3
5
8
6
7
10 9
11
12
13
14
15
4

16
NERO
C:0 M:0 Y:0 K:100
ROSSO
C:0 M:100 Y:100 K:0
VERDE
C:100 M:0 Y:100 K:0
3.2 Hydraulic connection (version with
hydraulic connection available)
If the machine is available to be connected up to the
water, follow the instructions below:
1. Connect the water supply
(10) to the softener inlet
(7)
using the provided exible hose
;
2. connect the softener outlet
(6)
to the external motor
pump inlet
(8)
;
3. connect the outlet of the motor pump
(9)
to the
inlet of the machine
(4)
;
4. connect the drain pad of the machine
(2)
to the
sewer discharge
(3)using the special hose provided,
avoiding overly tight bends or kinks, and making
sure that there is sucient inclination for water to
drain
.
Warnings
1. The water supply must provide cold water for
human consumption (potable water) at a pressure
between 1,5 and 5 bars. If the pressure is higher than
5 bar, connect a pressure reducer before the pump.
2. add a tap (11) to the water supply so as to stop water
from owing to the machine;
3. in order to prevent damage, it is advisable to install
the softener where it will be protected from accidental
blows;
4. to prevent water from freezing, install the softener
inside a premise with a room temperature higher
than 5°C;
5. if there is no softener, connect the water supply (10)
directly to the inlet of the external motor pump (8);
6. if there is an internal motor pump, connect the outlet
of the softener (6)(if there is one)or the water supply
(10) directly to the machine inlet (4);
7. when connecting the pad of the machine to the sewer
drain, avoid overly tight curves or kinks, and make
sure that there is sucient inclination for water to
ow out of the drain;
8. the drain must be connected to an inspectable siphon
that can be periodically cleaned, in order to avoid
bad odours;
9. to avoid oxidization and damage to the machine over
time, do not use iron connections for the hydraulic
system, even if galvanized.
iAll lling connections are 3/8 male gas type. The
drain pan is connected to a tube with an internal
diameter of 16 mm.
i
All of the machine are equipped with a "Time-out"
device that allows filling of water in the boiler
within a maximum time.
This function keeps water
from owing out of the boiler's valve (ooding)
and keeps the motor pump from overheating. If
the time limit is not enough for the boiler to ll
up completely (such as for the machines installed
with 3 or 4 groups), turn the machine o and then
back on, and repeat the operations listed above.
5
2
2
2
3
5
10
6
7
9 8
11 4

17
Technical manual
ENGLISH
NERO
C:0 M:0 Y:0 K:100
ROSSO
C:0 M:100 Y:100 K:0
VERDE
C:100 M:0 Y:100 K:0
!
The water supply of the appliance must be carried
out with water which is suitable for human
consumption, in compliancewith the regulationsin
force in the place of installation. The installer must
receive, from the owner/manager of the system,
conrmation that the water meetsthe above listed
requirements.
Incaseofsupplyfromthetank,don'tusecarbonated
water or other liquids.
!
During the installation of the appliance, only
the
components and materials supplied with
the appliance are to be used. Should the
use of other components be necessary, the
installer must verify their suitability to be
used in contact with water used for human
consumption. The installer must carry out the
hydraulic connections in accordance with the
hygiene norms and the hydraulic safety norms
for environmental protection in force in the
place of installation.
!
The hydraulic connection must be made in
compliance with local national standards. In case
of use of an external tank: the connection hose
between the machine and the tank can't be longer
than 150 cm. For the European Community: both
for the hydraulic connection to the water supply,
and for the connection to an external tank, it is
necessary to place a non-return valve (10) on the
machine as set forth by EN 1717 standards.
!
FOR THE U.S.A.
The water connections and discharges must be
made in accordance with the 2003 International
Plumbing Code of the International Code Council
(ICC), or with the 2003 Uniformed Hydraulic Code of
the IAPMO. Themachine must be installed together
with an adequate non-return valve, as required by
national regulations.
3.3 Hydraulic connection (version with
inner tank)
In inner tank version the operations
of connection to the aqueduct are not
necessary as the water is supplied from
the tank inside the machine.
The possible lack of water in the
tank is indicated by the ashing led
of the STOP/PROG. (A) button for
EVD model or by the warning light in
specic patterns EPU (B) and EMA (C).
If the machine is ready to connect
to the aqueduct, follow the instructions
below:
1. Connect the water supply
(10) to the entrance of
the water depuration lter
(7)
using the supplied
exible hose;
2. connect the output of the water filter
(6) to the
entrance of the external motorpump
(8)
;
3. connect the exit of the motorpump
(9)
alto the
entrance of the machine
(4)
;
4. connect the drain pain of the machine llegare la
vaschetta di scarico della macchina
(2) to the sewage
system
allo scarico fognario
(3)
using the supplied
hose, taking care to avoid sharp bends or kinks and
keeping a sucient slope to drain water discharge.
PROG.
STOP
A
5
2
2
B
5
2
E
R
O
A
D
F
P
M
M
A
E
S
T
V
P
E
R
U
A
V
A
P
A
U
C
A
W
Q
A
S
E
S
E
R
W
A
T
U
E
A
C

18
NERO
C:0 M:0 Y:0 K:100
ROSSO
C:0 M:100 Y:100 K:0
VERDE
C:100 M:0 Y:100 K:0
To restore the level of liquid is sucient to remove
the tank cover and add water.
It is recommended to clean the tank periodically as
follow:
1. Extract the tank from its housing
;
2. carefully wash the tank with lukewarm water
;
3. ll the tank with potable water
;
4. place the tank correctly in place.
!
Fill the tank only with cold potable water. Do not
use other types of liquids or carbonated beverages.
Operating without water may damage the machine
.
5
2
2

19
Technical manual
ENGLISH
NERO
C:0 M:0 Y:0 K:100
ROSSO
C:0 M:100 Y:100 K:0
VERDE
C:100 M:0 Y:100 K:0
3.4 Conversion fromTANK toWATER MAINS
1GR Version
Through this procedure you can change the type
of water supply of the machine, from internal Tank to
Water Mains.
All operations must be performed by technical
personnel only.
• Unplug the machine from the power supply.
• remove the water tank;
• remove the screws, and then remove the top cover
and the body of the machine;
• set switch (A) placed on the right side of the machine
to "0";
• turn the knob (B) clockwise to end of stroke, so that
its direction is the one shown in the picture;
• replace the body of the machine using the screws;
• replace the water tank;
• hook the hose (C) supplied to the quick coupling
placed under the machine;
• connect the hose to the water supply and open the
tap (D), make sure that the system pressure is about
1 bar;
• connect the cable to the power supply and turn on
the machine.
A
B
C CD
A

20
NERO
C:0 M:0 Y:0 K:100
ROSSO
C:0 M:100 Y:100 K:0
VERDE
C:100 M:0 Y:100 K:0
3.5 Conversion fromWATER MAINS toTANK
1GR Version
Through this procedure you can change the type
of water supply of the machine, from Water Mains to
internal Tank.
All operations must be performed by technical
personnel only.
• Unplug the machine from the power supply.
• close the tap (D) and disconnect the hose from the
water supply;
• unhook the hose (C) from the quick coupling placed
under the machine;
• remove the water tank;
• remove the screws, and then remove the top cover
and the body of the machine;
• turn the knob (B) counter-clockwise to end of stroke,
so that its direction is the one shown in the picture;
• set switch (A) placed on the left side of the machine
to "1";
• replace the body of the machine using the screws;
• replace the water tank;
• ll the internal tank with potable water;
• connect the cable to the power supply and turn on
the machine.
A
B
C CD
A
Other manuals for Mininova
3
Table of contents
Other Wega Coffee Maker manuals

Wega
Wega URBAN EVDP User manual
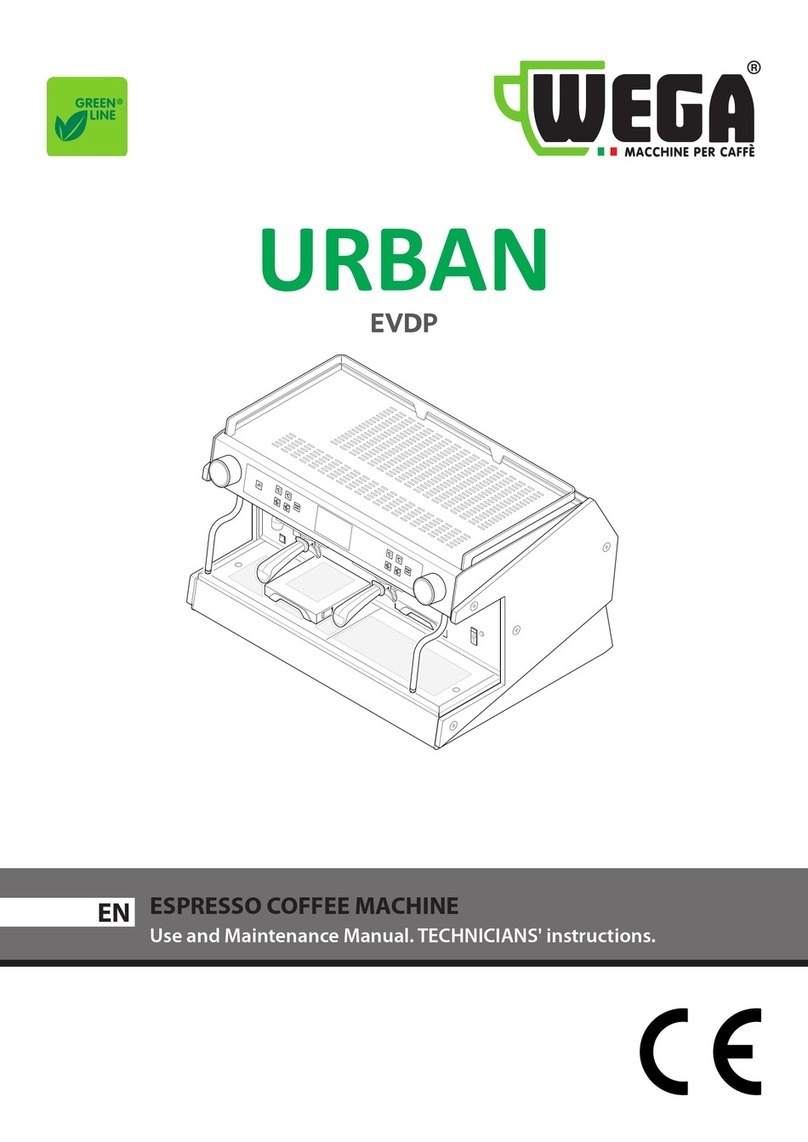
Wega
Wega URBAN EVDP User manual
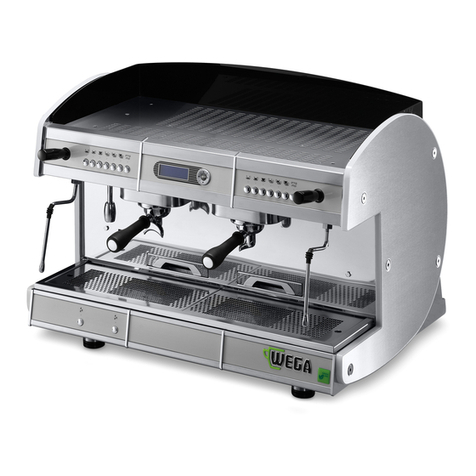
Wega
Wega Wegaconcept User manual

Wega
Wega ALE Series User manual
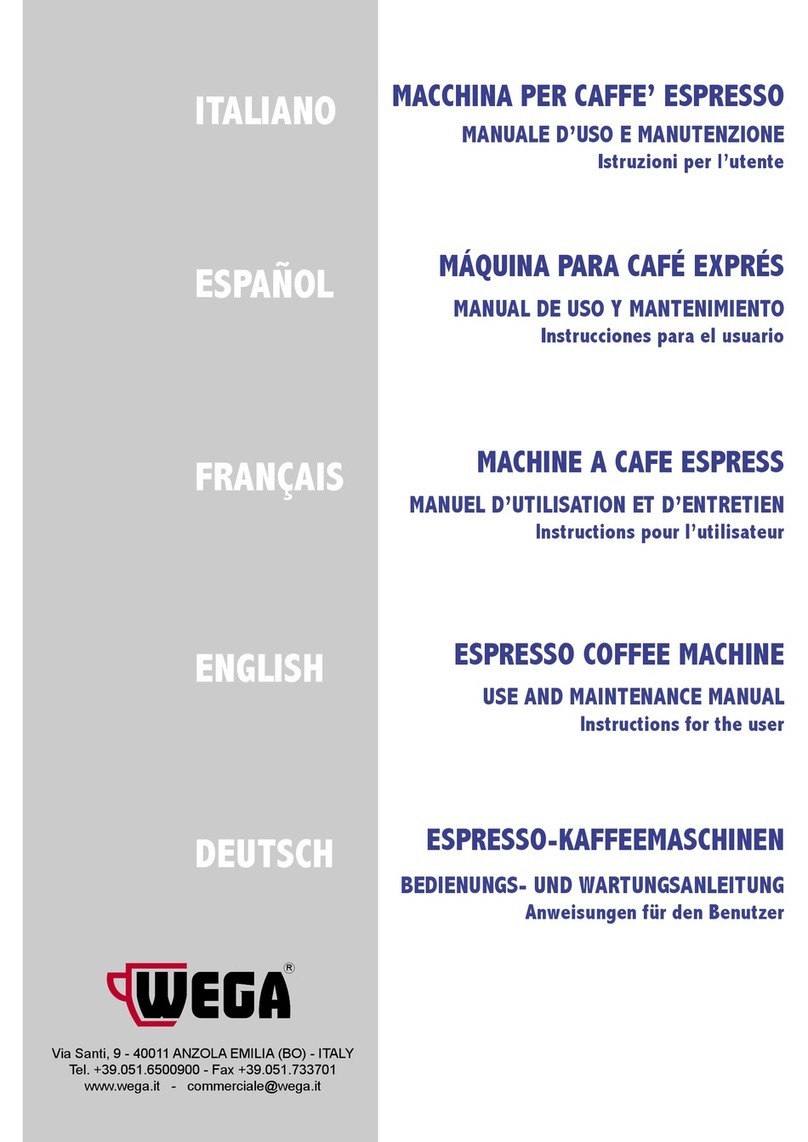
Wega
Wega Espresso Coffee Machine User guide
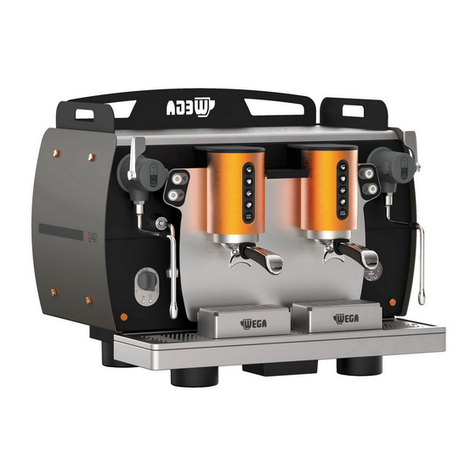
Wega
Wega WBAR EVD User manual
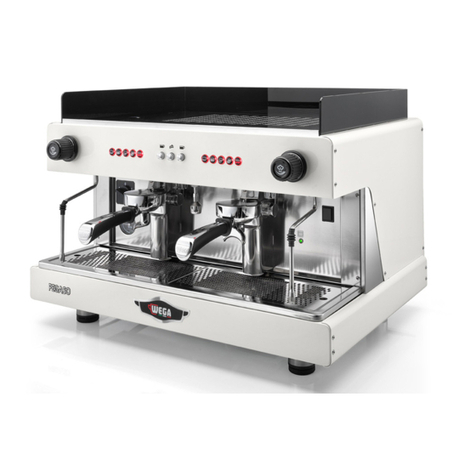
Wega
Wega Atlas 2010 User guide
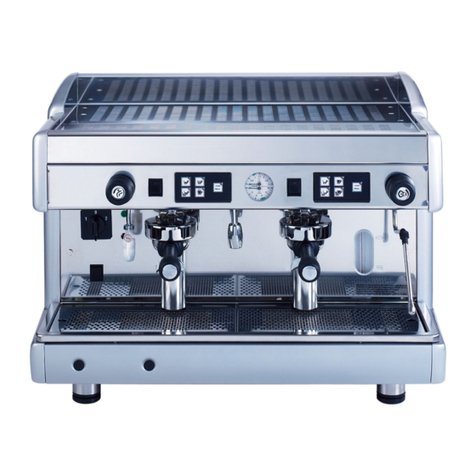
Wega
Wega LB 4700 User manual
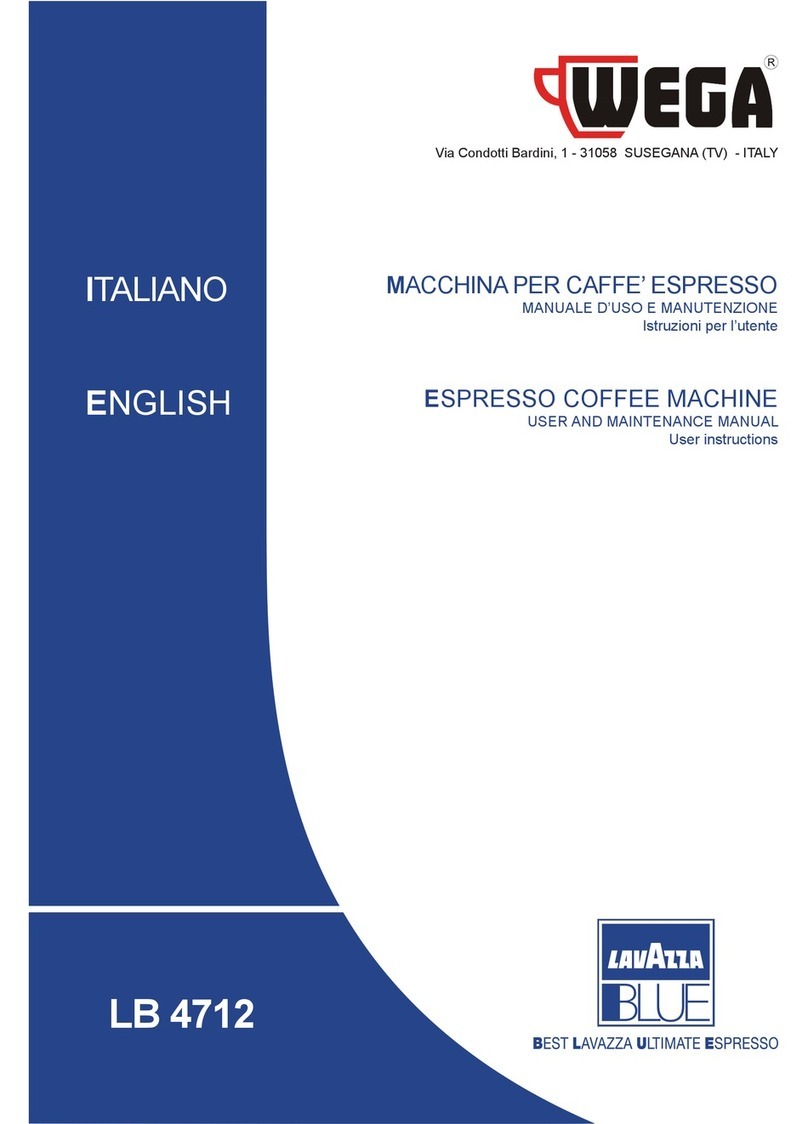
Wega
Wega LB 4712 Operating instructions
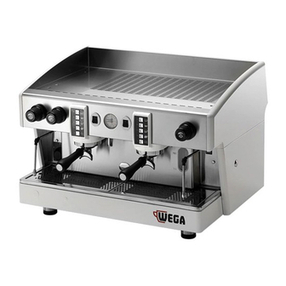
Wega
Wega ALE User manual
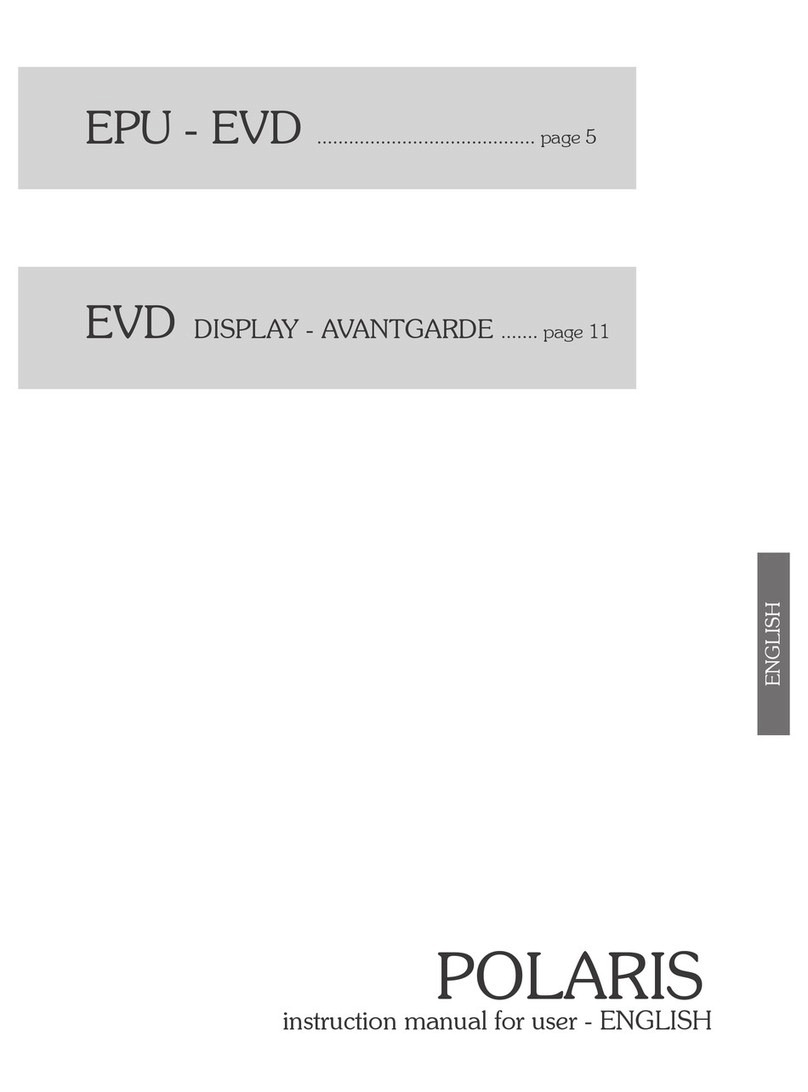
Wega
Wega Polaris EPU User manual

Wega
Wega AIRY 1 User manual
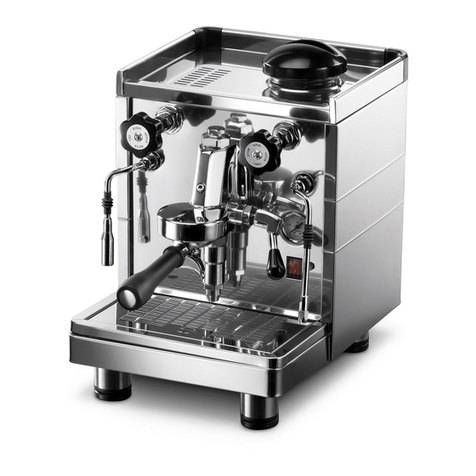
Wega
Wega MININIVA CLASSIC DUO User manual
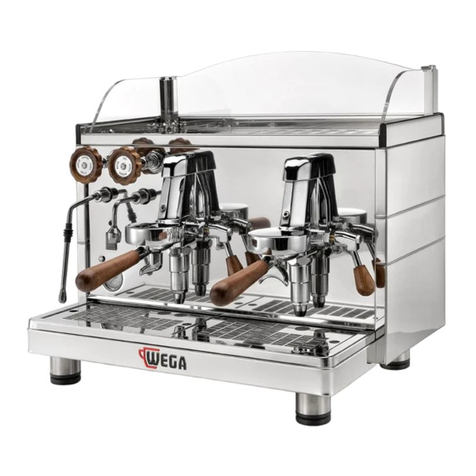
Wega
Wega Mininova Classic EMA 2GR User manual
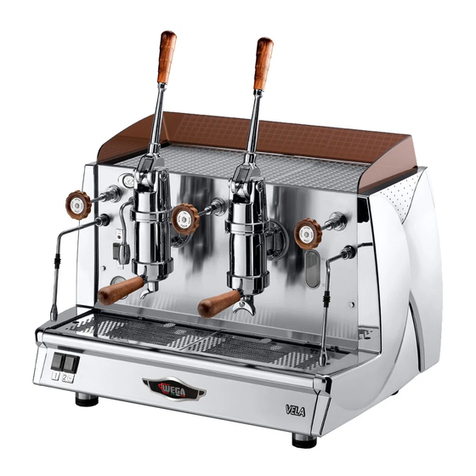
Wega
Wega EMA User manual
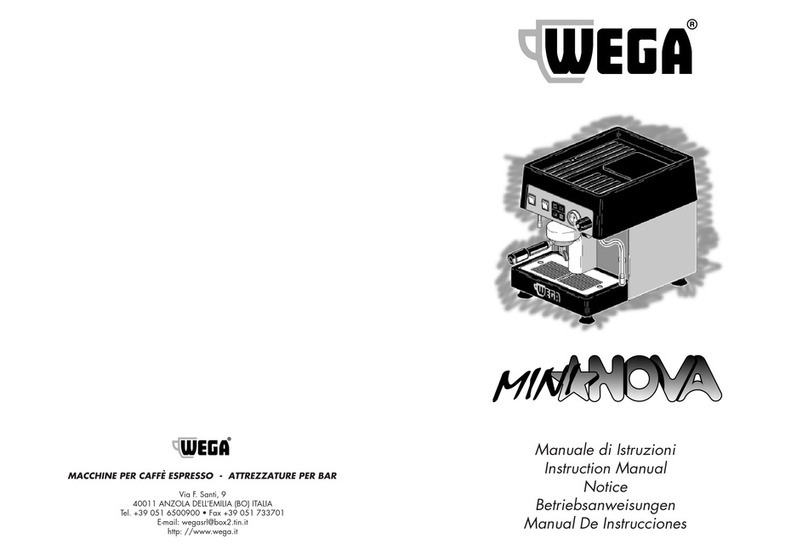
Wega
Wega Mininova User manual
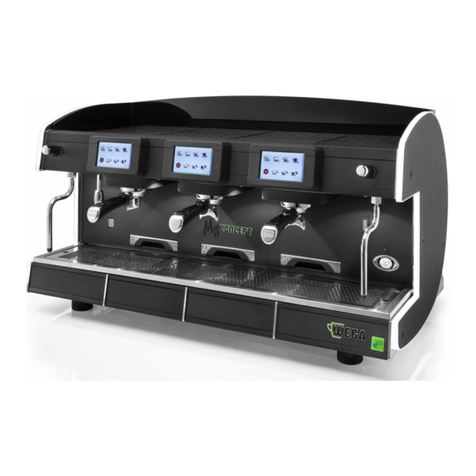
Wega
Wega WEGACONCEPT Series User manual

Wega
Wega LavAzza BLUE LB 4722 User manual
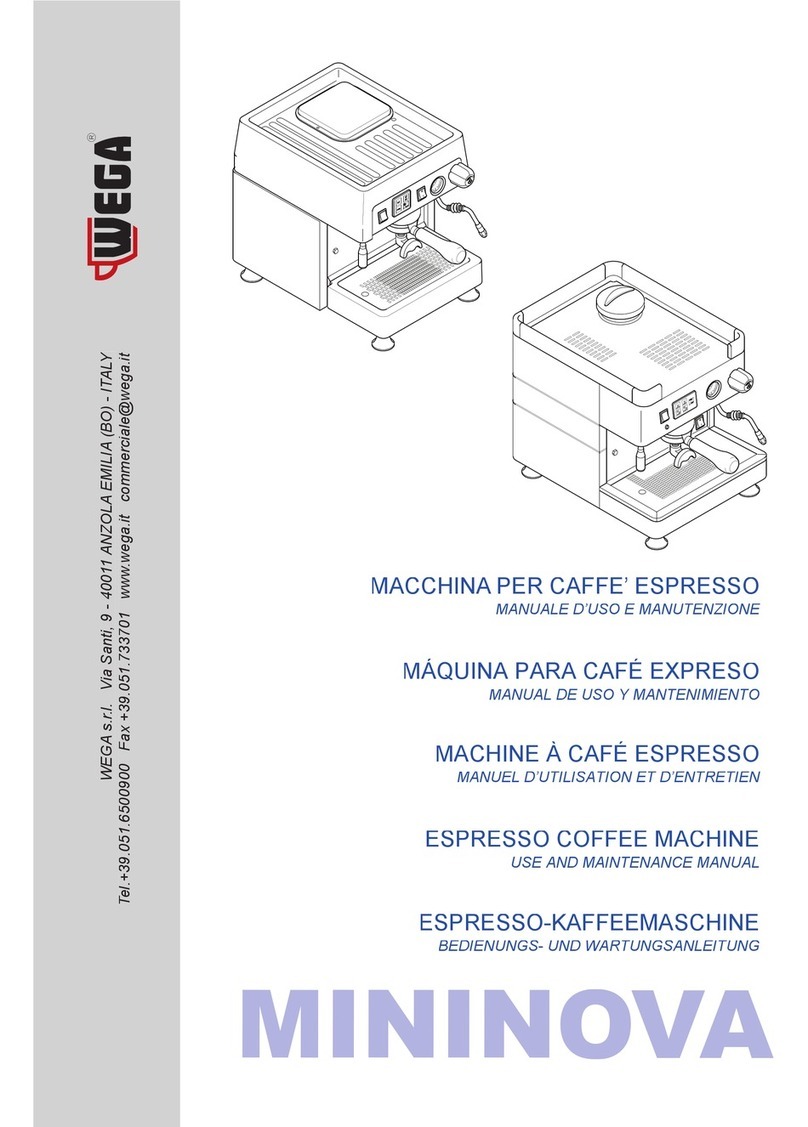
Wega
Wega Mininova User manual
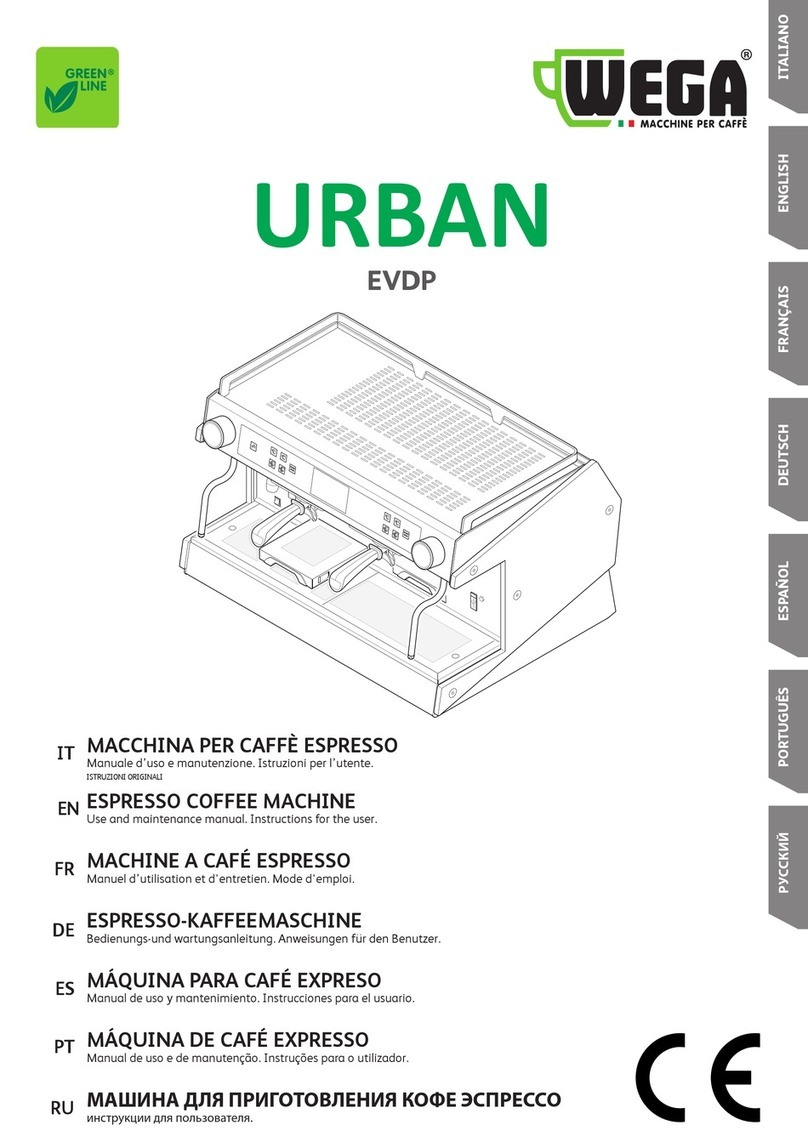
Wega
Wega URBAN EVDP User manual