AAQ AutoLift PP609 User manual

Advance AutoQuip
2 McDonald Crescent | Bassendean WA 6054
Ph: 08 9279 1663 | Fax: 08 9279 1667 | E: sales@aaq.net.au | W: www.aaq.net.au
-
READ THE ENTIRE CONTENTS OF THIS MANUAL BEFORE
INSTALLATION AND OPERATION. BY PROCEEDING YOU AGREE THAT
YOU FULLY UNDERSTAND AND COMPREHEND THE FULL CONTENTS
OF THIS MANUAL. FORWARD THIS MANUAL TO ALL OPERATORS.
FAILURE TO OPERATE THIS EQUIPMENT AS DIRECTED MAY CAUSE
INJURY OR DEATH.
Specifications subject to change without notice.
Note: While all due care and attention has been taken in the preparation of this document, Advance AutoQuip shall not be liable for any inaccuracies or omissions
which may occur therein
3 Car Stacker
AutoLift - PP609
2 Post 3 Car Stacker
2000Kg Lifting Capacity per platform
INSTALLATION MANUAL & OPERATION
INSTRUCTIONS
READ FIRST
DO NOT use the
machine until you read
and understand all the
dangers, warnings and
cautions in this manual.

2
Catalogue
1.Introduce................................................................................................................ 3
1.1 Summarize..................................................................................................... 3
1.2 Statement....................................................................................................... 3
2. Equipment introduction...........................................................................................4
2.1 Equipment description.............................................................................. 4
2.2 Equipment parameter...................................................................................4
3.Equipment transportation........................................................................................4
4.Assemble the lift ..................................................................................................... 5
4.1 Notice.............................................................................................................. 5
4.2Layout of the equipment ............................................................................. 6
4.3Tools for installing equipment:.................................................................. 7
4.4Installation procedure:................................................................................ 7
5.Introduction of control system..............................................................................22
5.1 Control principle.......................................................................................... 22
5.2Control issues that need attention............................................................ 22
5.3Control problem ..........................................................................................23
6.Electrical schematic............................................................................................... 24
7.Hydraulic schematic...............................................................................................24
8.Precautions for use................................................................................................ 25
8.1Announcements........................................................................................... 25
8.2 Parking cars.................................................................................................25
8.3 Take cars .................................................................................................... 26
9.Equipment maintenance....................................................................................... 26

3
1.Introduce
1.1 Summarize
The DTPP609 is a two-column hydraulic parking system. This manual should be read carefully
before installing and assembling equipment, which helps to assemble and use the equipment in the
right way to avoid risks and increase the reliability and service life of the equipment.
The operator should follow the instructions in this manual, otherwise the user will be
responsible for any loss and personal injury.
1.2 Statement
The operator shall operate the equipment in accordance with the instructions of the user manual
and the operator shall be responsible for any loss or personal injury.
If your equipment is damaged during transportation, the carrier shall be liable.
The equipment you purchase is safe in the first place of design and production, but to further
ensure safe use, equipment operators must be professionally trained and highly responsible. Do
not operate and service the equipment until you have read this manual thoroughly and without
carefully checking the safety of this equipment.
This warranty is the ultimate quality assurance of the product ,Product damage caused by bad
weather, natural disasters, damage during transportation, and failure to properly inspect the
maintenance is not covered by this warranty.

4
2.Equipment introduction
2.1 Equipment description
The DTPP609 is a hydraulic parking lift with three parking spaces for two parking plates.
This lift has the advantages of simple structure, convenient assembly and space saving, and is
well received by users. This lift is mainly composed of two side columns and a wave plate
platform.
2.2 Equipment parameter
Drive mode: cylinder drive
Maximum size of suitable vehicles: (can choose the size of the equipment)
(L×W×H)Ground Level :5200×2100×1900mm
Second Level:5000×2050×1550mm
Third level:5000×1950×1550mm
Maximum weight can parking:2000kg
Single equipment area: 12 square meters
3.Equipment transportation
Carefully remove the equipment and parts box. Note: When cutting the strap, the device may
be loose, so prevent the device from falling and hurting people.
Check the equipment for damage during transportation and whether it is short. Remember: If
the equipment is missing, it should be indicated on the relevant documents to prove whether it
is lost on the way to the transporter or the company is missing.

5
4.Assemble the lift
4.1 Notice
4.1.1 Read and understand the equipemt's safety alerts before using the equipment.
4.1.2 Pay attention to protect your hands and feet. The hands and feet must be removed from
the rotating parts. When the equipment falls, remove the feet to avoid being crushed.
4.1.3 Keeping the work site neat, clean, and chaotic workplaces can cause injury.
4.1.4Check the working environment of the equipment, do not expose the equipment to rain, do
not use the equipment in a humid environment, and the equipment area must be well ventilated
and illuminated.
4.1.5 This equipment should only be used by trained personnel. All untrained personnel should
stay away from the work area and do not allow untrained personnel to access and use the
equipment.
4.1.6 Use the quipment in the right way. Please do not modify the equipment with parts not
supplied by the factory.
4.1.7 When lifting or dropping the car, keep away from the working area of the equipment.
4.1.8 If the car on the platform is in a dangerous state, there must be enough shelter space.
4.1.9 Prevent electric shocks. In order to protect the operator, the grounding wire of the
equipment motor must be grounded reliably and must not be connected to other objects.
4.1.10 Warning! The power unit voltage on the equipment is very high. The power must be cut
off before servicing the electrical equipment on the power unit.。
4.1.11 Pay attention to maintenance. The equipment must be kept clean so that there is a safe
environment. Proper lubrication and maintenance contribute to the reliable use of the
equipment. Handle the machine carefully to prevent injury, especially to prevent it from being
crushed when the device is tipped over.
4.1.12Must keep a clear head. Be alert and alert when working.
4.1.13It is forbidden to remove any parts that involve safety.
4.1.14Maintain the safety locking device
4.1.15 When lifting the equipment, the guarantor is in a safe area.

6
4.1.16 Always check for damaged parts and check their activity and synchronization. If any
parts are not working properly, please do not use the equipment.
4.1.17 Warning! The work area should be non-flammable because there is an electric spark
when the switch is working.
4.2 Layout of the equipment
Before you install your lift, you should check the following items:
4.2.1 The work area should be designed and have enough space.
4.2.2 Avoid obstacles, such as the presence of wires in the installation area.
4.2.3 Carefully inspect the concrete floor where the equipment is to be installed for cracks and
check that the strength of the concrete meets the requirements. On the ground with a
compressive strength of not less than 25Mpa, the thickness of the ground concrete is not less
than 500mm, the number is not lower than C25, the newly poured concrete must be solidified
for at least 28 days, the ground error is not more than 3mm, and the expansion bolt size is
M19*160. Otherwise, the equipment will destroy the ground, which will cause damage to the
equipment and casualties.
4.2.4 The installation of the ground must ensure a certain level. The limit cannot exceed 5 mm.
Within this limit, it can be adjusted by a spacer. If the ground is severely uneven, it should be
repaired.
4.2.5 Installation of equipment on sloping floors or other non-concrete floors is prohibited.
4.2.6 It is forbidden to install equipment on cracked ground or inferior concrete floors.
4.2.7 Installation of equipment on the second floor or above is prohibited without the approval
of the architect.
4.2.8 If there is no protective measure, please do not install the equipment outdoors to avoid
damage to the motor in rainy weather.
4.2.9 Determine where the equipment is installed, then place the column and the platfrom in
their respective positions. Place the platfrom between the two columns
4.2.10 Confirm the position of the electrical control box and leave enough room for operation.
4.2.11 After confirming, draw the position of the bottom plate of the column with chalk to
ensure the error within 3mm, so as to avoid affecting the installation of the equipment.。
4.2.12 Check carefully to make sure the layout is correct。

7
4.3 Tools for installing equipment
Hammer, level, open end wrench, hex wrench, adjustable wrench, crowbar, chalk or colored
pen, flat head screwdriver, tape measure (5 m), needle-nosed pliers, etc.
4.4 Installation procedure :
FIG1 .Down position schematic

8
FIG2 Up position schematic

9
4.4.1Column front leg and additional plate install
FIG 3 Column front leg and additional plate installation diagram
4.4.2 Move the Stage 1 and Stage 2 carriage to the distance shown in Figure 4 and support
them with wooden or steel tubes of appropriate height to prevent the carriage from
falling.
additional plate
Front leg
Column
M16*50outer hexagon bolt 10pcs
M16 nut 10pcs
Ø16 plain washers 10pcs
Ø16 spring washer 10 pcs

10
FIG4 Cariage movement diagram
4.4.3Foundation diagram
FIG 5 Foundation diagram
Stage 1 carriage
Stage 2 carriage
500m
1000

11
4.4.4Column fixing and stage 1 carriage support tube installation
FIG 6 stage 1 carriage support tube installation
4.4.5Platfrom install ,the installation sequence is 1 layer first and then 2 layers.
Platfrom Install :First install the left and right side beams, followed by the rear beam and the tie
rods, then install the wave plates in sequence, and finally install the ramp. After installation,
adjust the diagonals on both sides to ensure that the diagonal distance between the two
diagonals is less than 20mm. The installation order of the 1st and 2nd floor plates is the same.
stage 1 carriage support tube
Here, Use 16 pieces of
M12*35 hex bolts, M12
nut, Ø12 flat washer,
Ø12 spring washer.
Note: The bolts are worn
from the outside to the
inside.

12
FIG 7 Platfrom frame Installation diagram
FIG 8 Ramp Installation diagram FIG 9 Pull rodInstallation diagram
M16X110 hex bolt, M16 nut Φ16 flat
pad, spring washer
M16*45 hex bolt, M16 nut Φ 16 flat
washer, spring washer
Lower platfrom right beam
Up platfrom right beam
Lower platfrom left beam
Up platform left beam
Lower platfrom left beam
Up platfrom
pull rod
Up platfrom rear beam
Lower platfrom rear beam
Up platfrom ramp
lower platfrom ramp

13
FIG 10 side beam Installation diagram FIG11 wave plate Installation diagram
FIG 12 1 level platfrom Installation completion diagram
M16X110 hex bolt, M16
nut Φ16 flat washer,
spring washer, bolts
are worn from the
outside to the inside.
M16X45 hex bolt, M16
nut Φ16 flat washer,
spring washer, bolts
are worn from inside
M8*20 bolt, M8
self-tightening nut Φ
8 flat washer

14
FIG 13 2-layer plate balance shaft installation diagram
FIG14 2-layer plate balance shaft installation diagram
Balance axis
Hexagon socket
head screw M8*20
Balance sprocket

15
FIG15 2-layer plate balance shaft installation diagram
FIG16 Plate diagram
Hexagon socket head
screw M8*20

16
4.4.6 Cylinder and chain installation
FIG17 Cylinder Installation Diagram
FIG 18 Cylinder fixing diagram
Cylinder fixing
bolt、M8 nut
Cylinder
Chain clip
Cylinder

17
FIG19 Lifting sprocket installation Diagram
Note: Install the lifting sprocket guard after the chain is installed.
After above cylinders and other components are installed, start to install chain.
FIG20 Chain Installation
Lifting sprocket guard
Lifting sprocket
Cross countersunk head bolt M5*12
Cylinder
Chain
Balance sprocket

18
FIG22 Chain Installation
FIG23 Chain wrapping diagram
Chain Clip
Chain

19
FIG 24 Chain plate seat installation Diagram
Chain balance adjustment:When the same tooth on both sides of the balance sprocket is hung on
the same chain, the device is in equilibrium.
4.4.7 The anti-dropper and the limit switch are installed. This equipment has a total of 4
anti-droppers and 3 limit switches. 2 anti-droppers are installed on the left column, and 2
anti-droppers and 3 limit switches are installed on the right column.
FIG25 Left column anti-dropper installation diagram
Left column
Anti-dropper
device cover
Anti-dropper
M16*6 5Hex bolts,
Ø16 flat gasket,
spring washer
Chain plate seat, Hex
bolts M10*30, Ø10
flat gasket, Spring
washer

20
FIG 26 Right column anti-dropper installation diagram
Note: The installation procedure of the right column anti-dropper is to first place the limit switch
on the anti-dropper joint shield, and then fix the anti-dropper on the column. The limit switch
mounting is fixed by 4 cross countersunk head bolts M5*12.
FIG27 Lower limit installation diagram
Limit switch adjustment: The 1st and 2nd layer upper limits are adjusted according to the drawing
requirements(1 & 2 layer height). The lower limit position is adjusted to the position when the 1st
floor plate falls to the bottom.
Right Column
Anti-dropper joined
cover
Limit Switch
Anti-Dropper
M16*65 Hex bolts, Ø16
flat gasket, spring
washer
Right Column
Limit switch cover,Hexagon
socket head bolt M6*12 ,
Ø6 flat gasket, spring
washer
Limit switch,Cross
countersunk head
bolt M5*12
Table of contents
Other AAQ Lifting System manuals

AAQ
AAQ AL-6254A User manual
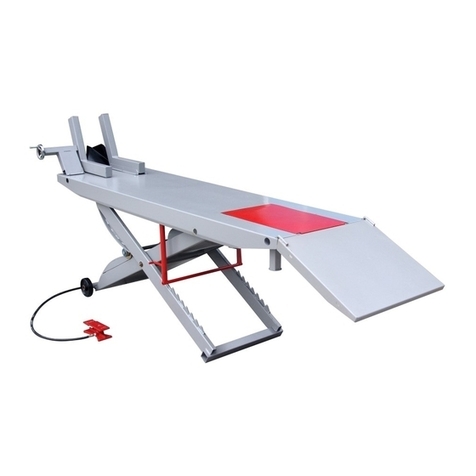
AAQ
AAQ AutoLift 243612 User manual

AAQ
AAQ AL-6214A Guide
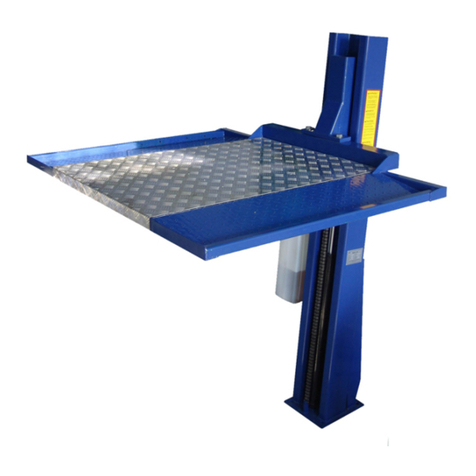
AAQ
AAQ AutoLift AL-167261 User manual
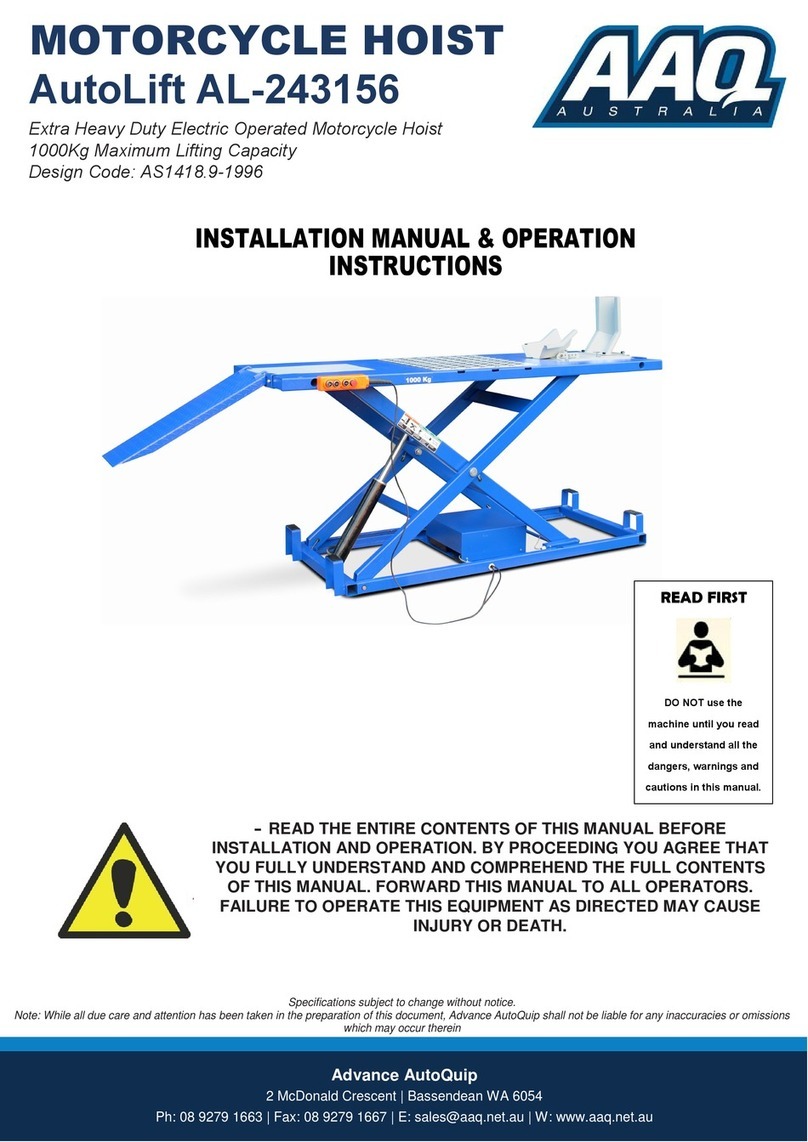
AAQ
AAQ AutoLift AL-243156 User manual
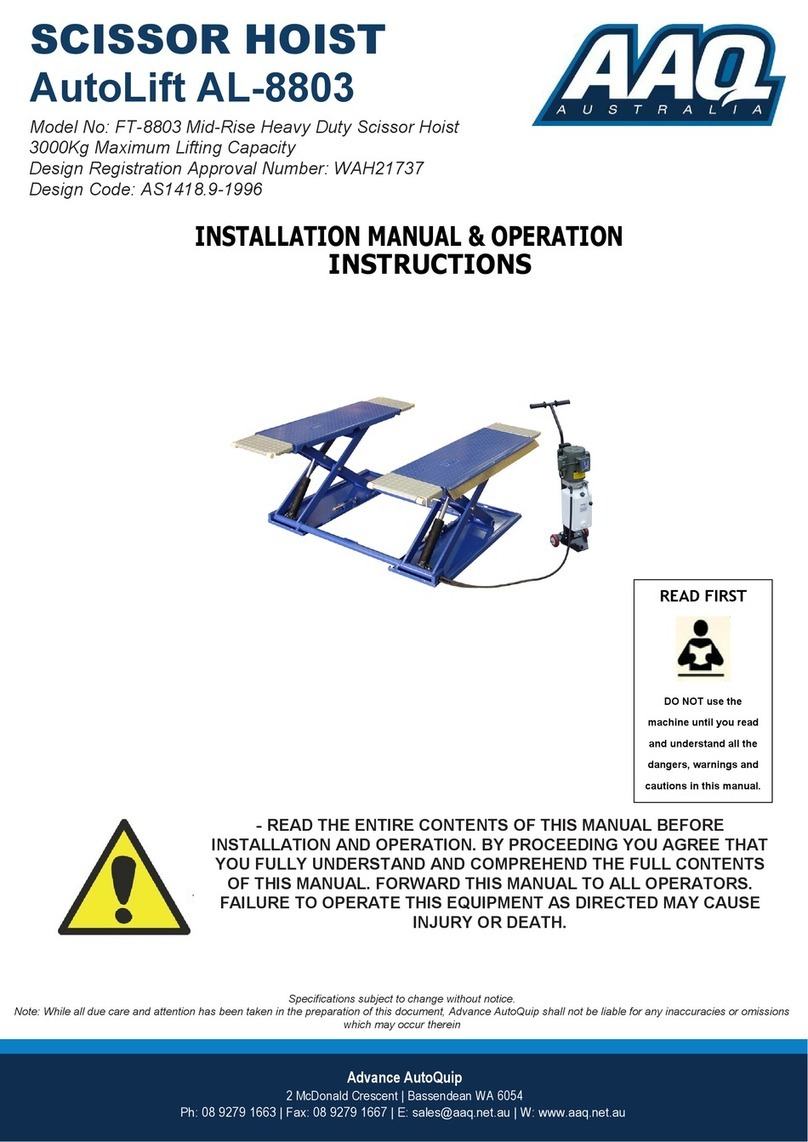
AAQ
AAQ AutoLift AL-8803 User manual
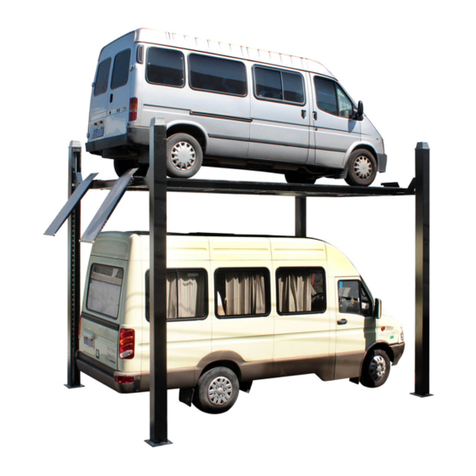
AAQ
AAQ AutoLift 163027 User manual

AAQ
AAQ AutoLift AL-2525 User manual

AAQ
AAQ AutoLift FP-VRC User manual
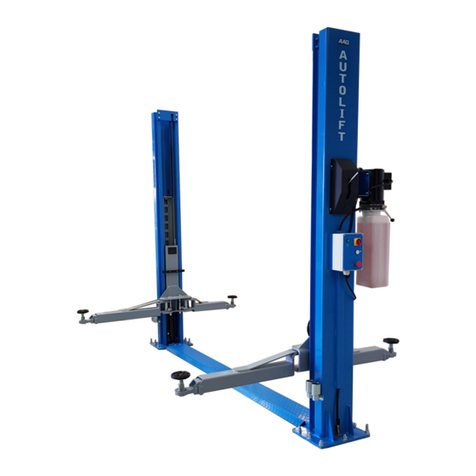
AAQ
AAQ AutoLift AL-900DD Technical Document
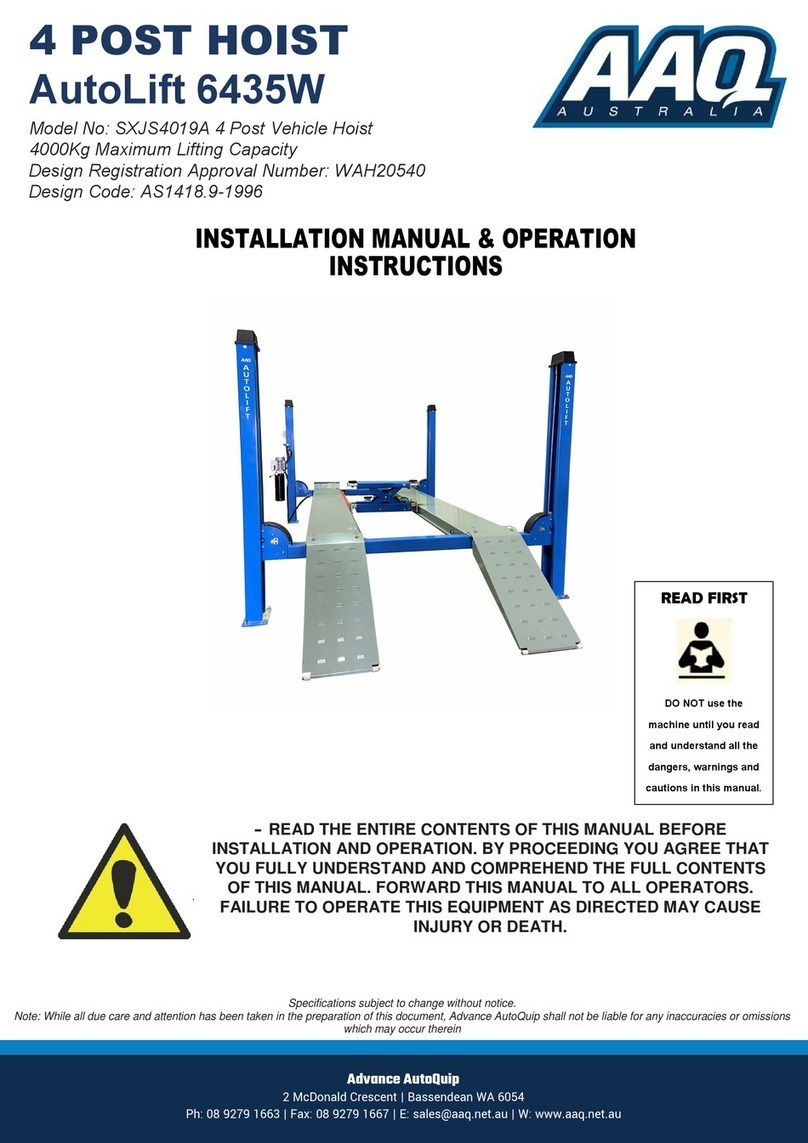
AAQ
AAQ SXJS4019A User manual
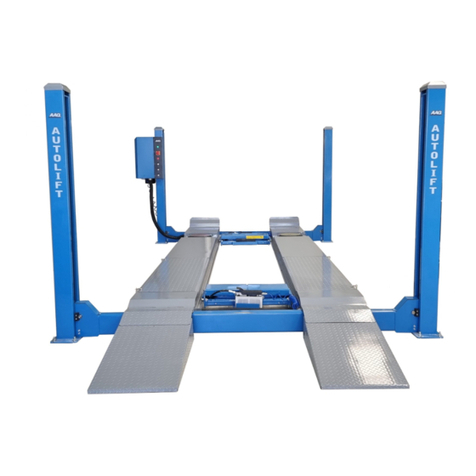
AAQ
AAQ AutoLift AL-6000S2 User manual
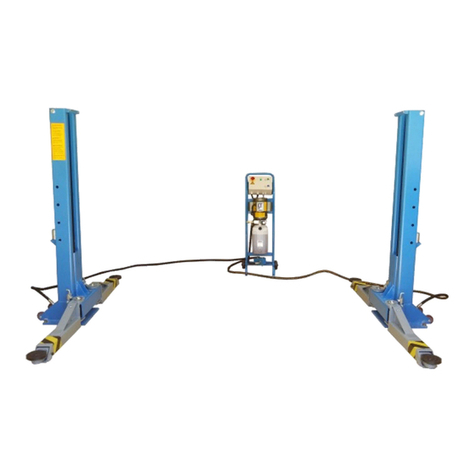
AAQ
AAQ 167212E User manual
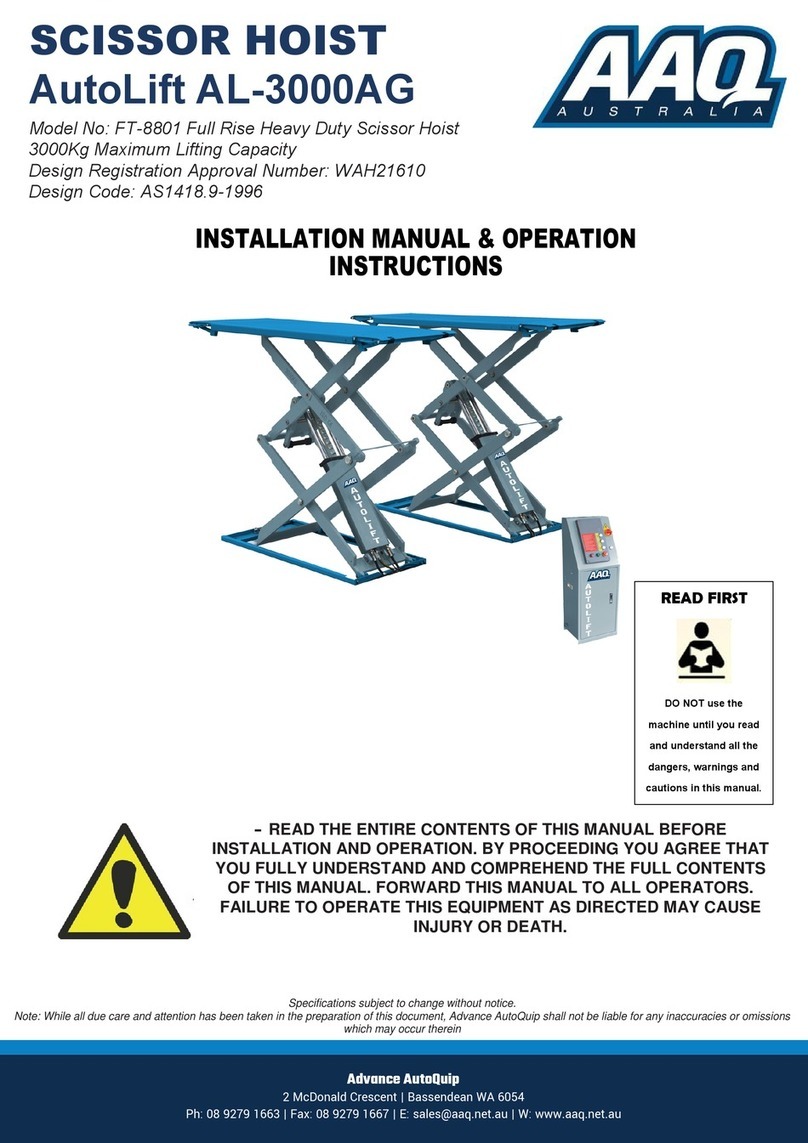
AAQ
AAQ AutoLift AL-3000AG User manual
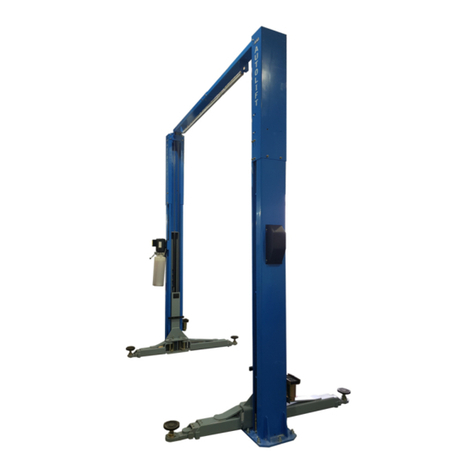
AAQ
AAQ AutoLift AL-9500HD User manual
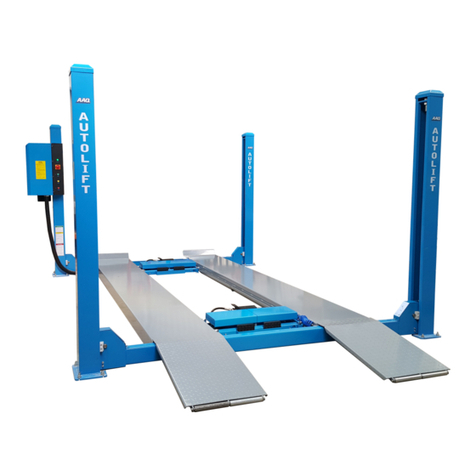
AAQ
AAQ AL-4000A User manual
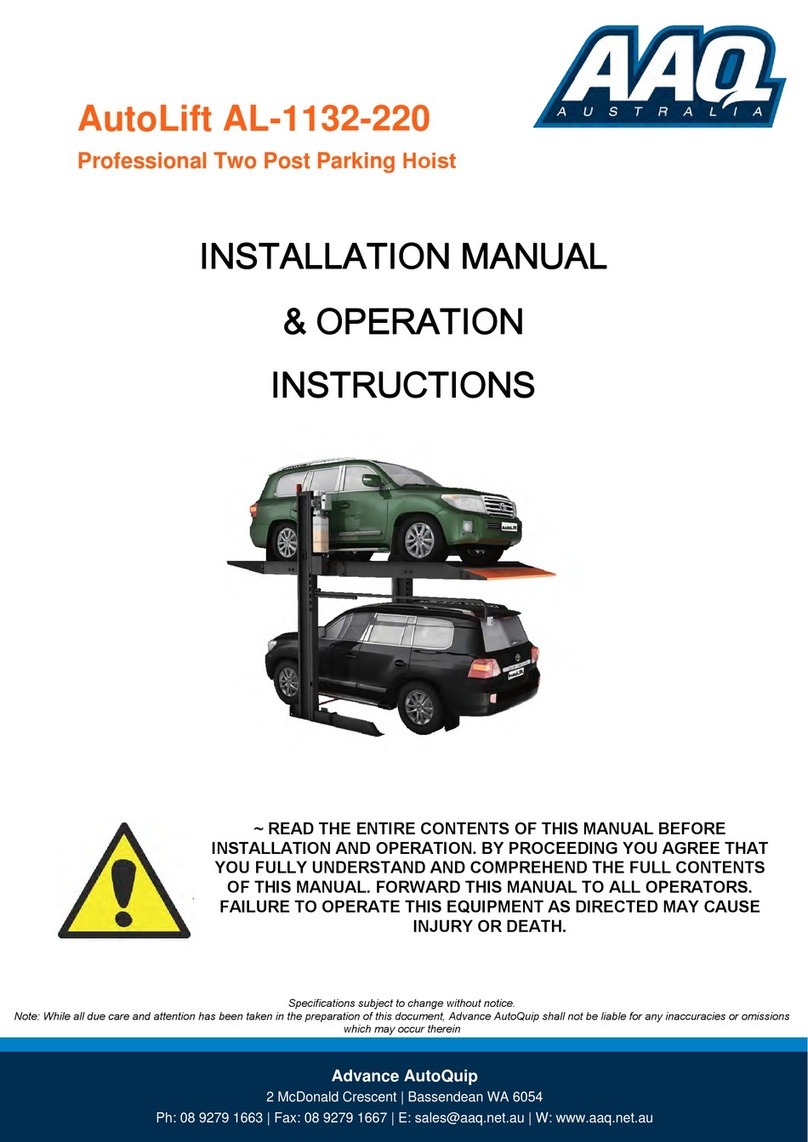
AAQ
AAQ AutoLift AL-1132-220 User manual
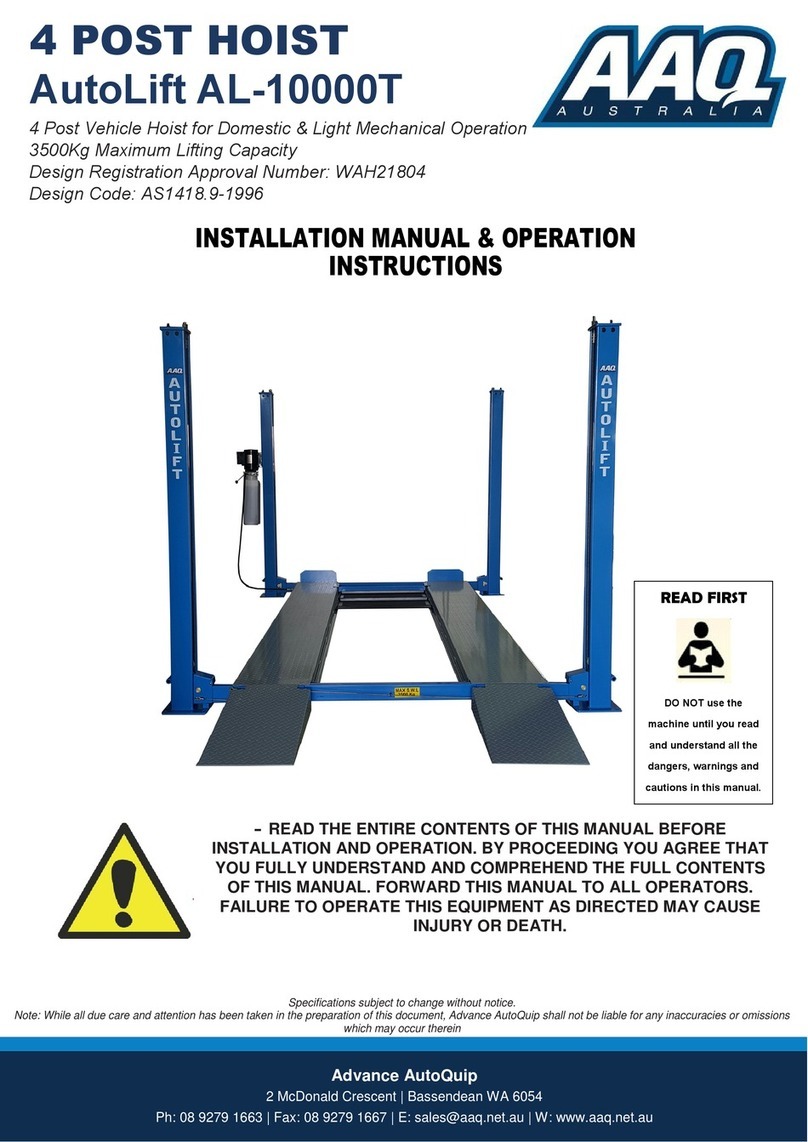
AAQ
AAQ AutoLift AL-10000T User manual
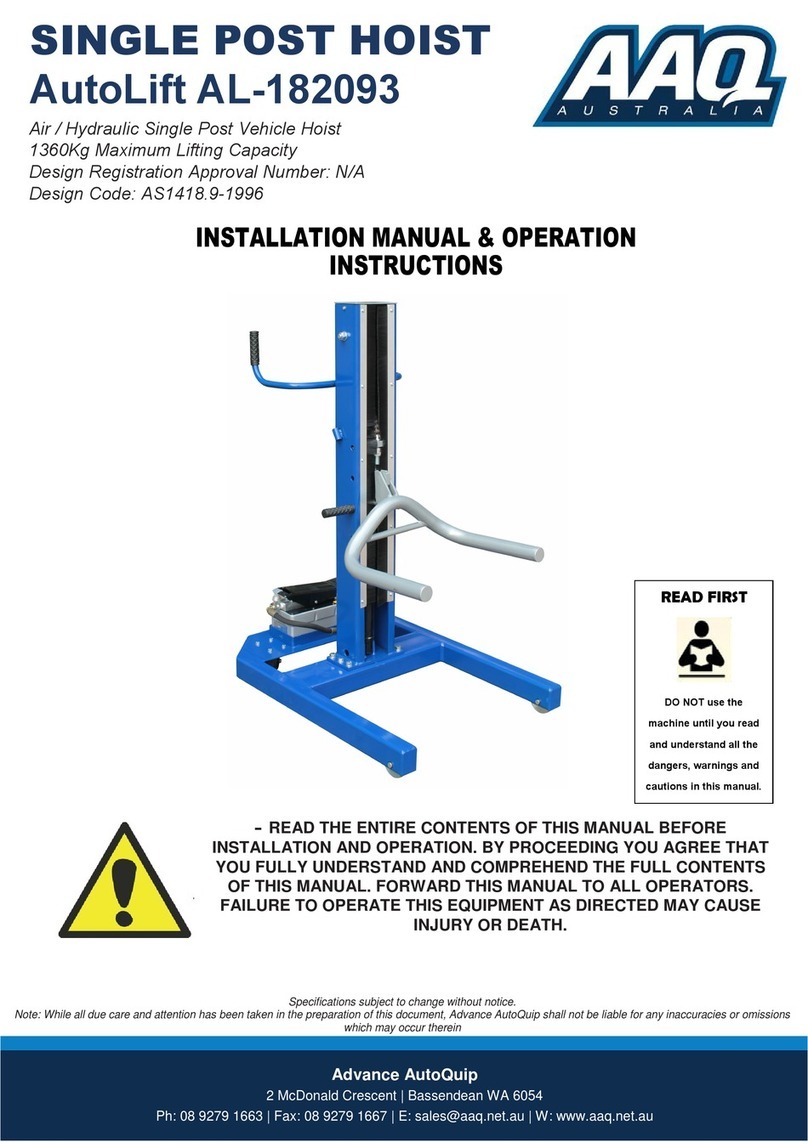
AAQ
AAQ AutoLift AL-182093 User manual
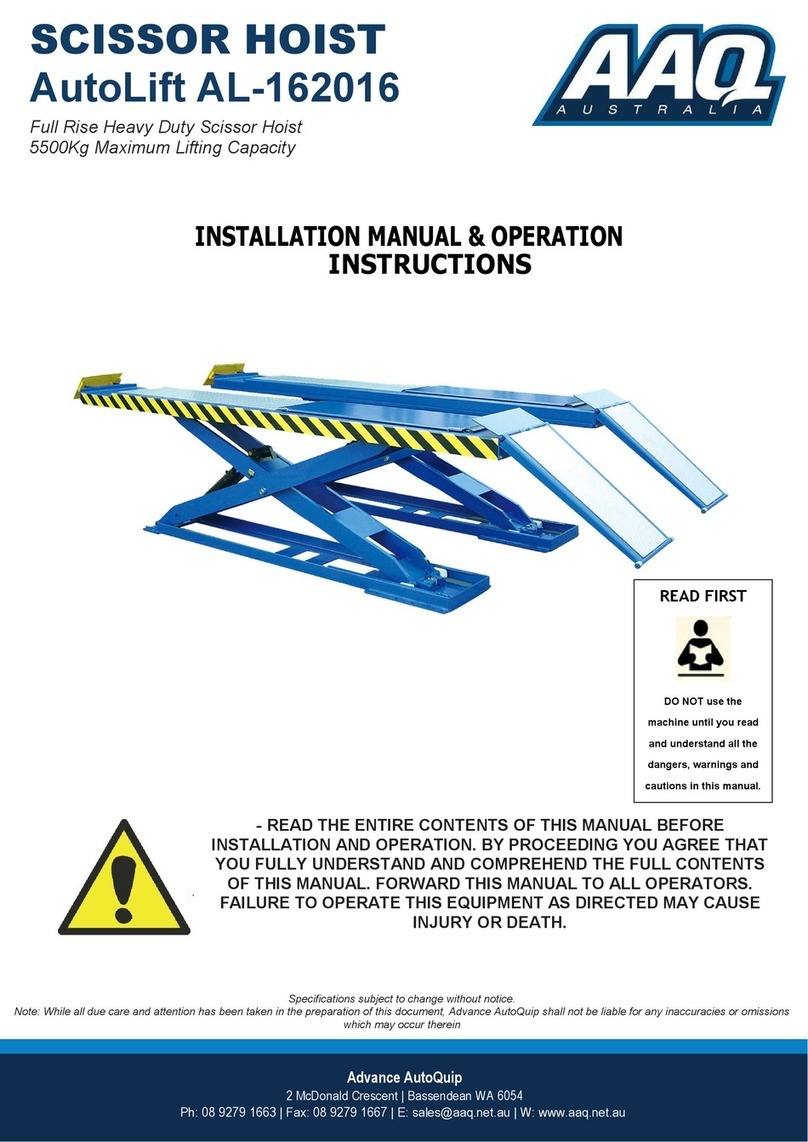
AAQ
AAQ AutoLift AL-162016 User manual