ABB RobotWare 6.02 Instructions for use

Application manual
Miller Ethernet I/P Interface and Weld
Editor

Trace back information:
Workspace R15-2 version a20
Checked in 2015-10-22
Skribenta version 4.6.081

Application manual
Miller Ethernet I/P Interface and Weld Editor
RobotWare 6.02
Document ID: 3HAC054885-001
Revision: -
© Copyright 2015 ABB. All rights reserved.

The information in this manual is subject to change without notice and should not
be construed as a commitment by ABB. ABB assumes no responsibility for any errors
that may appear in this manual.
Except as may be expressly stated anywhere in this manual, nothing herein shall be
construed as any kind of guarantee or warranty by ABB for losses, damages to
persons or property, fitness for a specific purpose or the like.
In no event shall ABB be liable for incidental or consequential damages arising from
use of this manual and products described herein.
This manual and parts thereof must not be reproduced or copied without ABB's
written permission.
Additional copies of this manual may be obtained from ABB.
The original language for this publication is English. Any other languages that are
supplied have been translated from English.
© Copyright 2015 ABB. All rights reserved.
ABB AB
Robotics Products
Se-721 68 Västerås
Sweden

Table of contents
7Overview of this manual ...................................................................................................................
8Product documentation, IRC5 ..........................................................................................................
10Safety ................................................................................................................................................
111 Overview of Auto-Axcess
111.1 Hardware ......................................................................................................... 131.2 Software .......................................................................................................... 141.3 Welding Processes ............................................................................................ 161.4 Auto-Axcess E Digital Control Panels ....................................................................
192 Installation and setup
192.1 Hardware ......................................................................................................... 192.1.1 Auto-Axcess E Welding Systems ............................................................... 212.1.2 Ethernet/IP ............................................................................................. 222.1.3 Auto-Axcess E Ethernet cable connection .................................................... 242.1.4 IRC5 Controller Ethernet cable connection ................................................... 252.2 Robot Controller Software ................................................................................... 262.3 Establishing a connection ................................................................................... 262.3.1 Overview ............................................................................................... 292.3.2 Setup Miller Ethernet/IP address in Miller Auto-Axcess .................................. 322.3.3 Setup the robot controller Ethernet/IP address .............................................. 342.3.4 Setup the Miller Ethernet/IP address in the robot controller .............................
373 Weld Editor Interface
373.1 About the Weld Editor Interface ........................................................................... 383.2 Widget screens ................................................................................................. 393.3 The Weld Editor Interface ................................................................................... 403.4 Ignition ............................................................................................................ 423.5 Heat ............................................................................................................... 443.6 Weld ............................................................................................................... 463.7 End ................................................................................................................
49Index
Application manual - Miller Ethernet I/P Interface and Weld Editor 5
3HAC054885-001 Revision: -
© Copyright 2015 ABB. All rights reserved.
Table of contents

This page is intentionally left blank

Overview of this manual
About this manual
This manual describes the options Miller Auto-Axcess E Ethernet/IP Interface and
Weld Editor and contains instructions to configure it.
Who should read this manual?
This manual is intended for:
• Personnel responsible for installations and configurations of fieldbus
hardware/software
• Personnel responsible for I/O system configuration
• System integrators
Prerequisites
The reader should have the required knowledge of:
• Mechanical installation work
• Electrical installation work
• System parameter configuration
References
Document IDReferences
3HAC032104-001Operating manual - RobotStudio
3HAC050988-001Application manual - Arc and Arc Sensor
3HAC050917-001Technical reference manual - RAPID Instructions, Functions
and Data types
3HAC050947-001Technical reference manual - RAPID overview
263 431A (www.miller-
welds.com)
Miller Axcess E Network Setup Guide
OM-251440A (www.miller-
welds.com)
Miller Auto-Axcess E Analog Welding Power Sources CE
Revisions
DescriptionRevision
New manual. Released with RobotWare 6.02.-
Application manual - Miller Ethernet I/P Interface and Weld Editor 7
3HAC054885-001 Revision: -
© Copyright 2015 ABB. All rights reserved.
Overview of this manual

Product documentation, IRC5
Categories for user documentation from ABB Robotics
The user documentation from ABB Robotics is divided into a number of categories.
This listing is based on the type of information in the documents, regardless of
whether the products are standard or optional.
All documents listed can be ordered from ABB on a DVD. The documents listed
are valid for IRC5 robot systems.
Product manuals
Manipulators, controllers, DressPack/SpotPack, and most other hardware is
delivered with a Product manual that generally contains:
• Safety information.
• Installation and commissioning (descriptions of mechanical installation or
electrical connections).
•Maintenance (descriptions of all required preventive maintenance procedures
including intervals and expected life time of parts).
• Repair (descriptions of all recommended repair procedures including spare
parts).
• Calibration.
• Decommissioning.
•Reference information (safety standards, unit conversions, screw joints, lists
of tools).
• Spare parts list with exploded views (or references to separate spare parts
lists).
• Circuit diagrams (or references to circuit diagrams).
Technical reference manuals
The technical reference manuals describe reference information for robotics
products.
•Technical reference manual - Lubrication in gearboxes: Description of types
and volumes of lubrication for the manipulator gearboxes.
•Technical reference manual - RAPID overview: An overview of the RAPID
programming language.
•Technical reference manual - RAPID Instructions, Functions and Data types:
Description and syntax for all RAPID instructions, functions, and data types.
•Technical reference manual - RAPID kernel: A formal description of the
RAPID programming language.
•Technical reference manual - System parameters: Description of system
parameters and configuration workflows.
Continues on next page
8 Application manual - Miller Ethernet I/P Interface and Weld Editor
3HAC054885-001 Revision: -
© Copyright 2015 ABB. All rights reserved.
Product documentation, IRC5

Application manuals
Specific applications (for example software or hardware options) are described in
Application manuals. An application manual can describe one or several
applications.
An application manual generally contains information about:
• The purpose of the application (what it does and when it is useful).
•What is included (for example cables, I/O boards, RAPID instructions, system
parameters, DVD with PC software).
• How to install included or required hardware.
• How to use the application.
• Examples of how to use the application.
Operating manuals
The operating manuals describe hands-on handling of the products. The manuals
are aimed at those having first-hand operational contact with the product, that is
production cell operators, programmers, and trouble shooters.
The group of manuals includes (among others):
•Operating manual - Emergency safety information
•Operating manual - General safety information
•Operating manual - Getting started, IRC5 and RobotStudio
•Operating manual - Introduction to RAPID
•Operating manual - IRC5 with FlexPendant
•Operating manual - RobotStudio
•Operating manual - Trouble shooting IRC5, for the controller and manipulator.
Application manual - Miller Ethernet I/P Interface and Weld Editor 9
3HAC054885-001 Revision: -
© Copyright 2015 ABB. All rights reserved.
Product documentation, IRC5
Continued

Safety
Safety of personnel
When working inside the robot controller it is necessary to be aware of
voltage-related risks.
A danger of high voltage is associated with the following parts:
• Devices inside the controller, for example I/O devices, can be supplied with
power from an external source.
• The mains supply/mains switch.
• The power unit.
• The power supply unit for the computer system (230 VAC).
• The rectifier unit (400-480 VAC and 700 VDC). Capacitors!
• The drive unit (700 VDC).
• The service outlets (115/230 VAC).
• The power supply unit for tools, or special power supply units for the
machining process.
• The external voltage connected to the controller remains live even when the
robot is disconnected from the mains.
• Additional connections.
Therefore, it is important that all safety regulations are followed when doing
mechanical and electrical installation work.
Safety regulations
Before beginning mechanical and/or electrical installations, ensure you are familiar
with the safety regulations described in Operating manual - General safety
information1.
1This manual contains all safety instructions from the product manuals for the manipulators and the controllers.
10 Application manual - Miller Ethernet I/P Interface and Weld Editor
3HAC054885-001 Revision: -
© Copyright 2015 ABB. All rights reserved.
Safety

1 Overview of Auto-Axcess
1.1 Hardware
Hardware features
Overview
Miller Auto-Axcess E welding systems are precise, digitally controlled and
software-driven. They are provided with Ethernet/IP communication for quick and
easy connection to the ABB IRC5 robot controller.
Miller Auto-Line
Miller® Auto-Line technology allows for any input voltage hook-up (190 – 630 V,
50 or 60 Hz) with no manual jumpers which assures rock-solid, consistent output
on fluctuating primary lines.
Fan-On-Demand
The Fan-On-Demand™ cooling system operates only when needed which reduces
the amount of airborne contaminants pulled through the machine.
Wind Tunnel Technology
The Wind Tunnel Technology™ feature circulates air over components that require
cooling, not over electronic circuitry, which reduces contaminants and improves
reliability in harsh welding environments.
1/4-turn steel connectors
1/4-turn steel connectors allow for faster installation of system and eliminates
thread stripping.
115 VAC duplex receptacle
The 115 VAC duplex receptacle provides 10-amp circuit-breaker-protected auxiliary
power regardless of primary power.
Dual removable lifting eyes
The dual removable lifting eyes are used for moving with overhead lifts.
Removability allows for flat-top feeder or storage on top.
Forklift slots
Forklift slots are slots cut into the frame for forklift transportation.
Small footprint
Miller Auto-Axcess models feature a small footprint, designed to minimize floor
space requirements.
Interface options
Several different wire feeding and operator interface options are available and
configurable to the desired application.
Connections for Ethernet
Two connections for Ethernet are provided to interface with any Auto-Axcess™ E
either directly or via the factory Ethernet network.
Continues on next page
Application manual - Miller Ethernet I/P Interface and Weld Editor 11
3HAC054885-001 Revision: -
© Copyright 2015 ABB. All rights reserved.
1 Overview of Auto-Axcess
1.1 Hardware

USB connections
USB connections allow USB flash drives can be used for loading code updates.
12 Application manual - Miller Ethernet I/P Interface and Weld Editor
3HAC054885-001 Revision: -
© Copyright 2015 ABB. All rights reserved.
1 Overview of Auto-Axcess
1.1 Hardware
Continued

1.2 Software
Software features
Multi-MIG capability
Multi-MIG® capability includes common carbon steel, aluminum and stainless
welding programs, including Accu-Pulse®, Accu-Curve™, standard or adaptive
pulse, conventional MIG, Metal-Cored, and RMD® (Regulated Metal Deposition)
programs using the most popular wire diameters and gas combinations.
SureStart
SureStart™ provides consistent arc starts by electronically assuring a ball is not
left on the wire when welding is stopped. This provides a predictable condition for
the next arc start and combines this with precisely tuned arc starting routines.
Arc Control
Arc Control offers a simple way to tailor factory pulse weld programs by adjusting
the arc plasma cone to accommodate a variety of welding applications without the
need for any reprogramming or changing any hardware.
Arc Adjust
Arc Adjust allows a simple method that controls arc length for pulse processes
and wetting action for RMD.
Remote/trigger program select
Remote/trigger program select allows changing weld programs to take advantage
of up to eight programs of Multi-MIG welding process capabilities.
Software updates
Note
As new and improved software features are developed, they can be added to
the existing Auto-Axcess E systems for free. Code transfer is accomplished via
a USB memory stick plugged directly into USB connection on the Auto-Axcess
E.
Application manual - Miller Ethernet I/P Interface and Weld Editor 13
3HAC054885-001 Revision: -
© Copyright 2015 ABB. All rights reserved.
1 Overview of Auto-Axcess
1.2 Software

1.3 Welding Processes
Accu-Pulse
Accu-Pulse® is standard on all Auto-Axcess™ E models.
The Accu-Pulse process allows for precise control of the pulse arc. Accu-Pulse
provides optimum molten puddle control and has power to increase wire feed
speeds and deposition 20 to 25 percent in many applications. In most cases, slightly
different ratios of gas mixtures will perform well using a similar program and
adjusting arc length or the appropriate arc control for the selected process. Contact
Miller for more information on less common materials and gas combinations.
Benefits (compared to conventional pulse):
• Shorter arc lengths possible
• Better puddle control
• More tolerant of contact tip to work variation
• Less audible noise
• No arc wandering in tight corners
• Narrow arc plasma column
• Allows weld to fill in at toes increasing travel
• speed and deposition
• More tolerant of poor fit up and gaps
• (compared to standard pulse)
• Ideal for robot seam tracking applications
xx1500000807
Accu-Curve
Accu-Curve™ is standard on all Auto-Axcess™ E models.
Accu-Curve is a variation of the Accu-Pulse process. The transitions from peaks
to background voltage are “curved”. The curved transitions provide a “softer” feel
Continues on next page
14 Application manual - Miller Ethernet I/P Interface and Weld Editor
3HAC054885-001 Revision: -
© Copyright 2015 ABB. All rights reserved.
1 Overview of Auto-Axcess
1.3 Welding Processes

without sacrificing the tight arc lengths that allow for better puddle control and
have become the hallmark of the Accu-Pulse process.
Benefits:
• "Softer” arc feel than Accu-Pulse
• Maintains tight arc lengths
• Maintains better puddle control
RMD
RMD® (Regulated Metal Deposition) is standard on all Auto-Axcess™ E models.
The RMD process is a precisely controlled short-circuit transfer. It is a method of
detecting when the short is going to clear and then rapidly reacting to this data
changing the current levels. Features proactive dynamic puddle control.
Benefits:
• Well suited to thin materials
• Can replace TIG process in some applications
• Gap filling
• Spatter reduction
• Provides less heat into work piece
• Excellent performance on stainless steel
• Can be combined with other Axcess®-related programs
• Minimize distortion
• Use larger diameter wire on thin materials
xx1500000808
Application manual - Miller Ethernet I/P Interface and Weld Editor 15
3HAC054885-001 Revision: -
© Copyright 2015 ABB. All rights reserved.
1 Overview of Auto-Axcess
1.3 Welding Processes
Continued

1.4 Auto-Axcess E Digital Control Panels
Front Panel
xx1500000809
USB Connection A (Host)1
Voltage/Arc Adjust Display Meter2
Program Display3
Program # Select4
Power Switch5
Process Setup Button6
Control Knob7
Wire Speed/Amperage Display Meter8
Purge Pushbutton9
Jog Forward Pushbutton10
Jog Retract Pushbutton11
Wire Feed/Amperage Select12
Arc Control13
Continues on next page
16 Application manual - Miller Ethernet I/P Interface and Weld Editor
3HAC054885-001 Revision: -
© Copyright 2015 ABB. All rights reserved.
1 Overview of Auto-Axcess
1.4 Auto-Axcess E Digital Control Panels

Rear Panel
xx1500000810
Wire Feed Speed Sensor Connection (Optional)14
Gas Flow Sensor Connection (Optional)15
Peripheral Connector16
Circuit Breakers17
Motor Connector18
DeviceNet Connector19
Ethernet Connector A20
Ethernet Connector B21
E-Stop22
115 VAC, 10 A Duplex Receptacle23
Capabilities
Remote Program Select
Remote Program Select allows changing weld programs from the robot controller
to take advantage of up to eight programs or Multi-MIG® welding process
capabilities.
Continues on next page
Application manual - Miller Ethernet I/P Interface and Weld Editor 17
3HAC054885-001 Revision: -
© Copyright 2015 ABB. All rights reserved.
1 Overview of Auto-Axcess
1.4 Auto-Axcess E Digital Control Panels
Continued

Integrated 80 V Touch Sensor
Integrated 80 V Touch Sensor is used with external circuitry or peripheral equipment
when touch sensing.
Front Panel Features
• Weld Process Selection
• Wire Size and Type
• Gas Type
• Wire Jog Forward Button
• Wire Jog Reverse Button
• Purge Button
• Digital Display Meters:
- Voltage / Arc Adjust (Trim)
- Wire Feed Speed /Amperage
• Program Number
• Arc Control (SharpArc® and Inductance)
Digital Outputs
• Voltage
• Current
Digital Inputs
• Voltage/Arc Adjust (Trim)
• Wire Feed Speed
Auto Setup
• Robot Specific
Sequence
• Preflow: 0 – 9.9 seconds
• Start Power: 0 – 2.5 seconds
• Start Ramp
• Voltage: 10 – 44
• IPM: 50 –1400
• Crater: 0 – 2.5 seconds
• Crater Ramp
• Retract
• Postflow: 0 – 9.9 seconds
18 Application manual - Miller Ethernet I/P Interface and Weld Editor
3HAC054885-001 Revision: -
© Copyright 2015 ABB. All rights reserved.
1 Overview of Auto-Axcess
1.4 Auto-Axcess E Digital Control Panels
Continued

2 Installation and setup
2.1 Hardware
2.1.1 Auto-Axcess E Welding Systems
Description
Miller Auto-Axcess E welding systems are extensively used in robotic arc welding
applications.
Auto-Axcess E uses Ethernet/IP, a well established industrial Ethernet
communication system with good real-time capabilities.
Compatible equipment
The Miller Auto-Axcess E Ethernet/IP Interface may be used with any Auto-Axcess
E weld power supply manufactured by Miller Electric. This list includes, but is not
limited to, the following units:
• Auto-Axcess E 675 Digital
• Auto-Axcess E 450 Digital
• Auto-Axcess E 300 Digital
Continues on next page
Application manual - Miller Ethernet I/P Interface and Weld Editor 19
3HAC054885-001 Revision: -
© Copyright 2015 ABB. All rights reserved.
2 Installation and setup
2.1.1 Auto-Axcess E Welding Systems

xx1500000814
20 Application manual - Miller Ethernet I/P Interface and Weld Editor
3HAC054885-001 Revision: -
© Copyright 2015 ABB. All rights reserved.
2 Installation and setup
2.1.1 Auto-Axcess E Welding Systems
Continued
Table of contents
Other ABB Network Hardware manuals
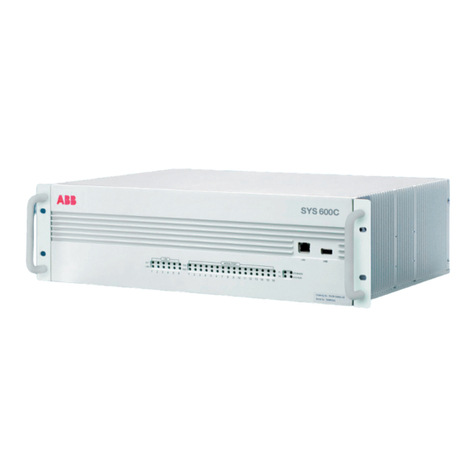
ABB
ABB MicroSCADA Pro SYS 600 Parts list manual
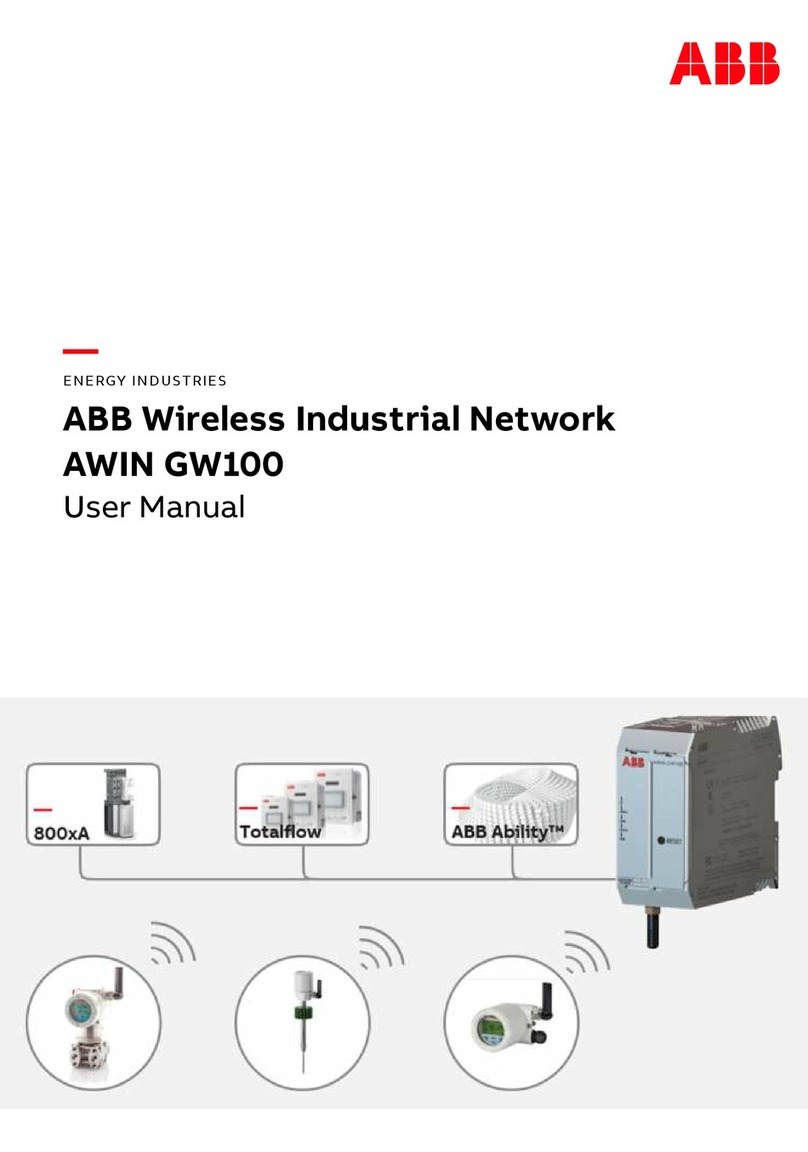
ABB
ABB AWIN GW100 User manual
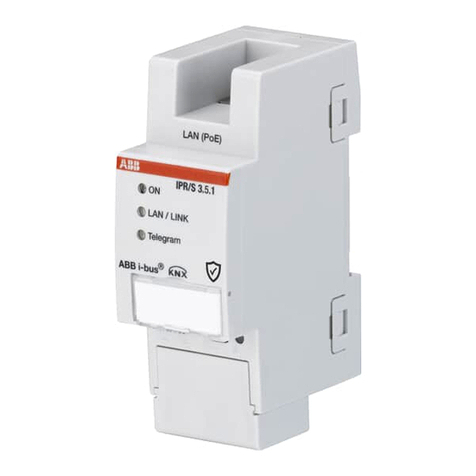
ABB
ABB i-bus KNX IPR/S 3.5.1 User manual

ABB
ABB M4M 30 User manual
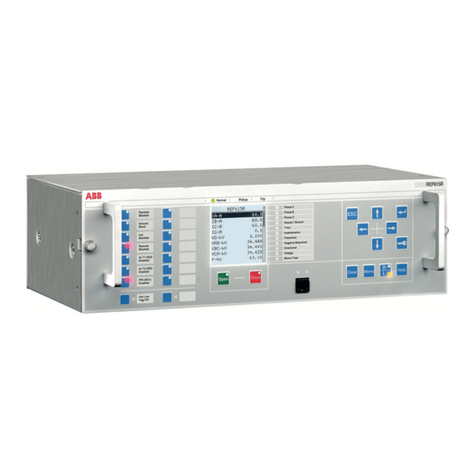
ABB
ABB RELION REF615R User manual
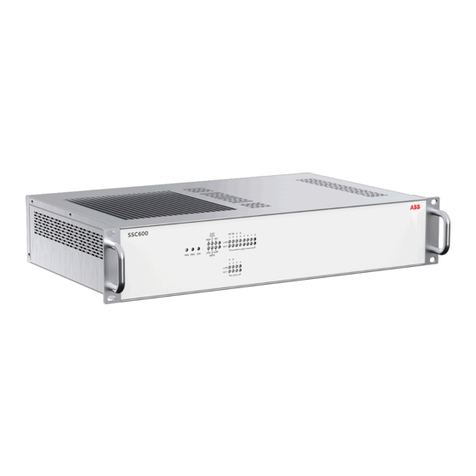
ABB
ABB ABILITY SSC600 User manual
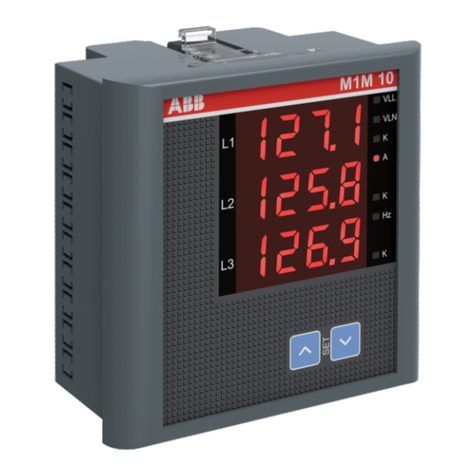
ABB
ABB M1M 10 User manual
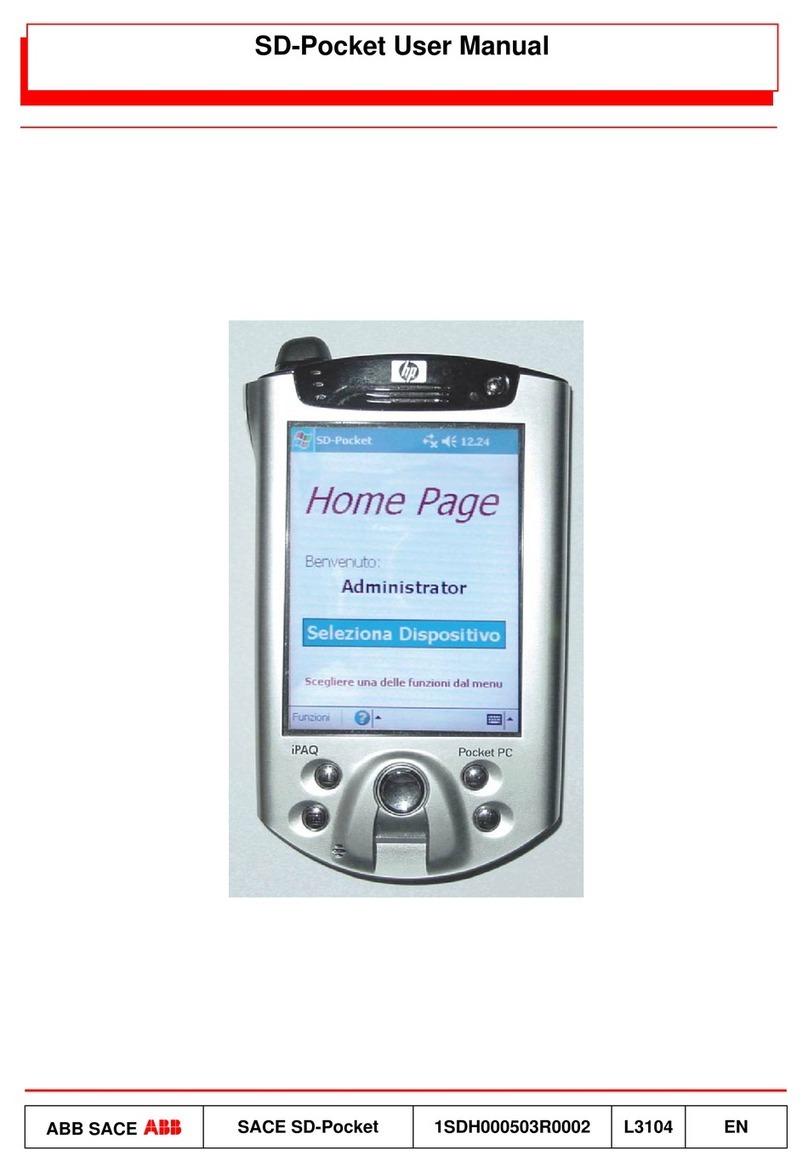
ABB
ABB iPAQ User manual
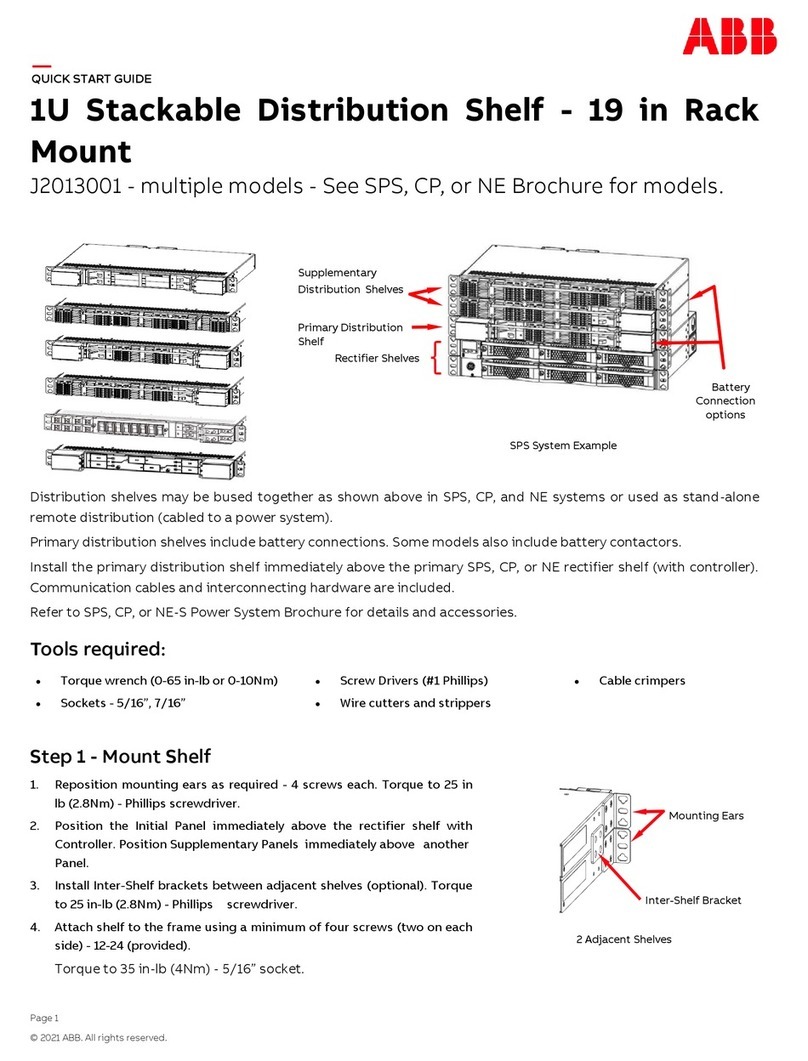
ABB
ABB J2013001 User manual
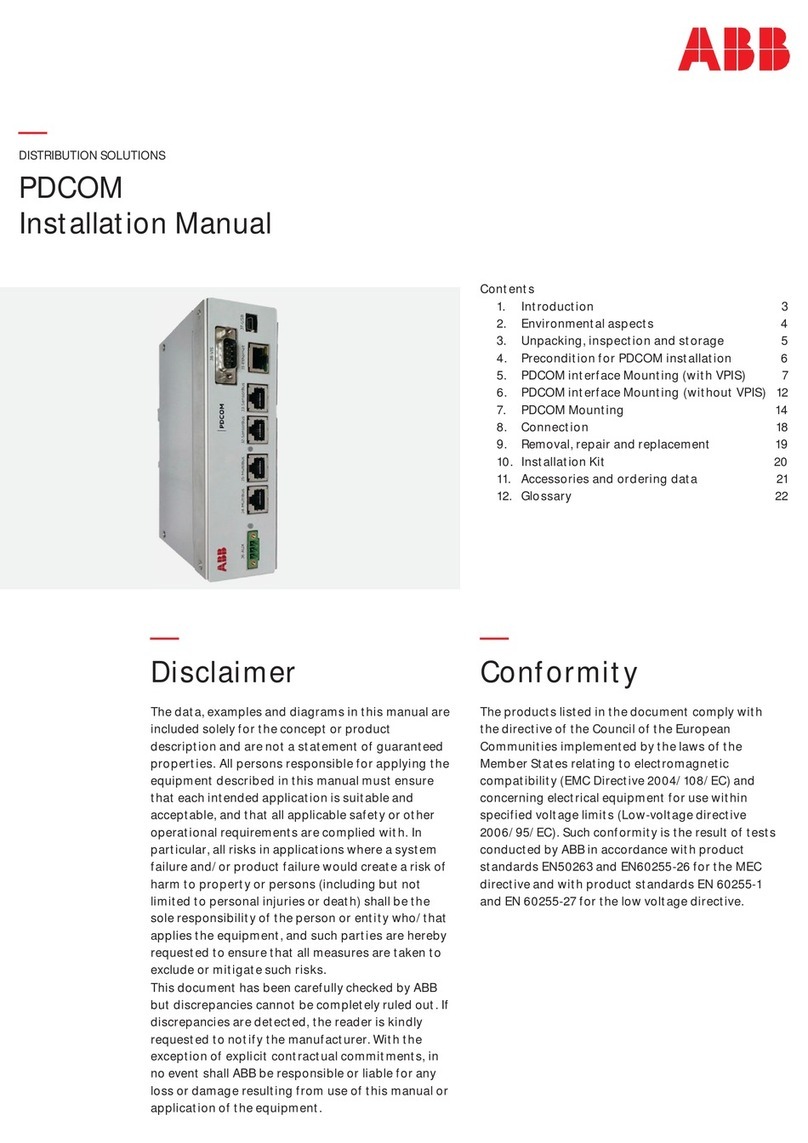
ABB
ABB PDCOM User manual
Popular Network Hardware manuals by other brands
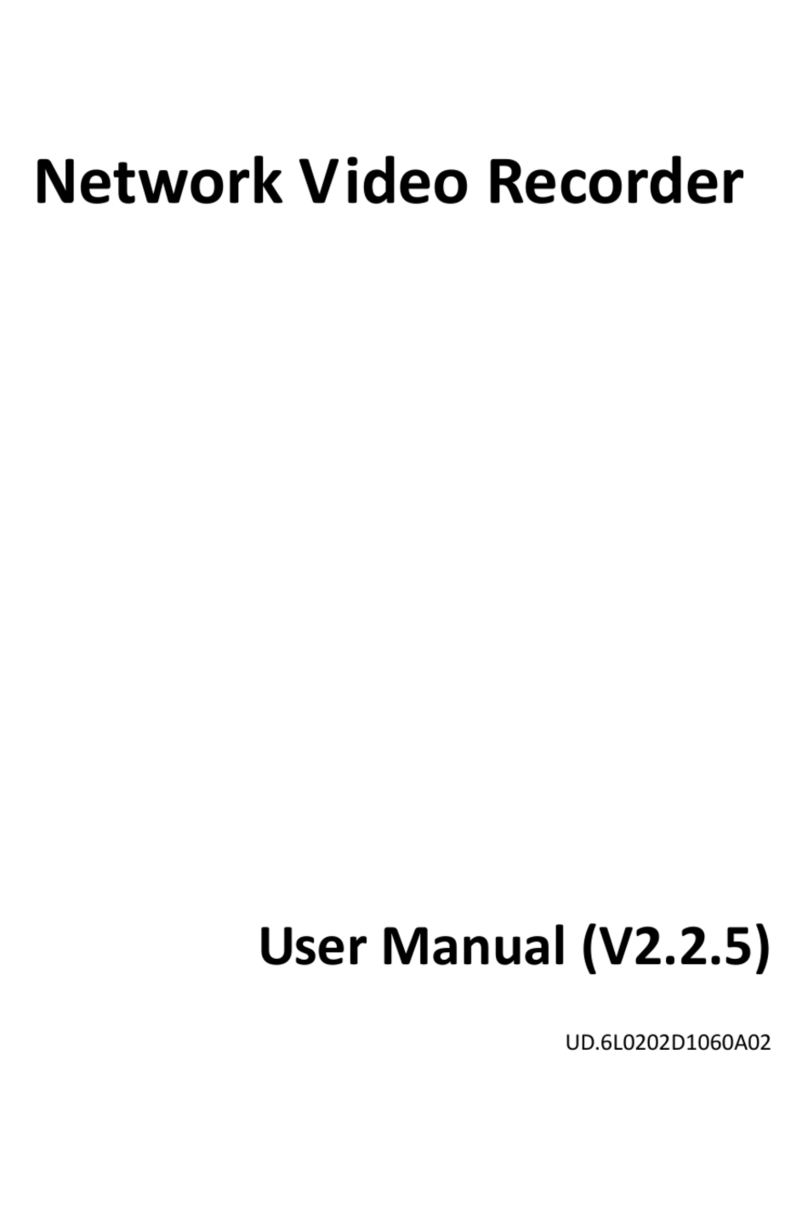
Dahua
Dahua NVR2 Series VR2104 user manual
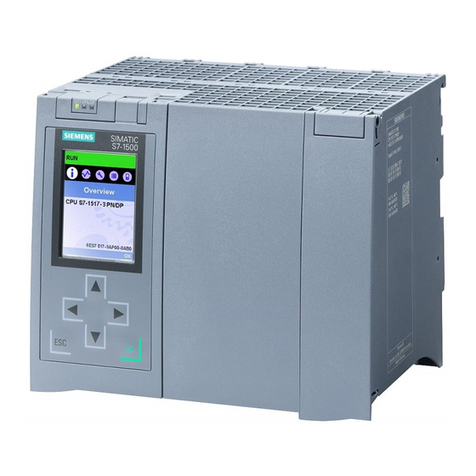
Siemens
Siemens SIMATIC NET S7-1500 operating instructions

Funkwerk
Funkwerk elmeg hybrid 300 installation guide
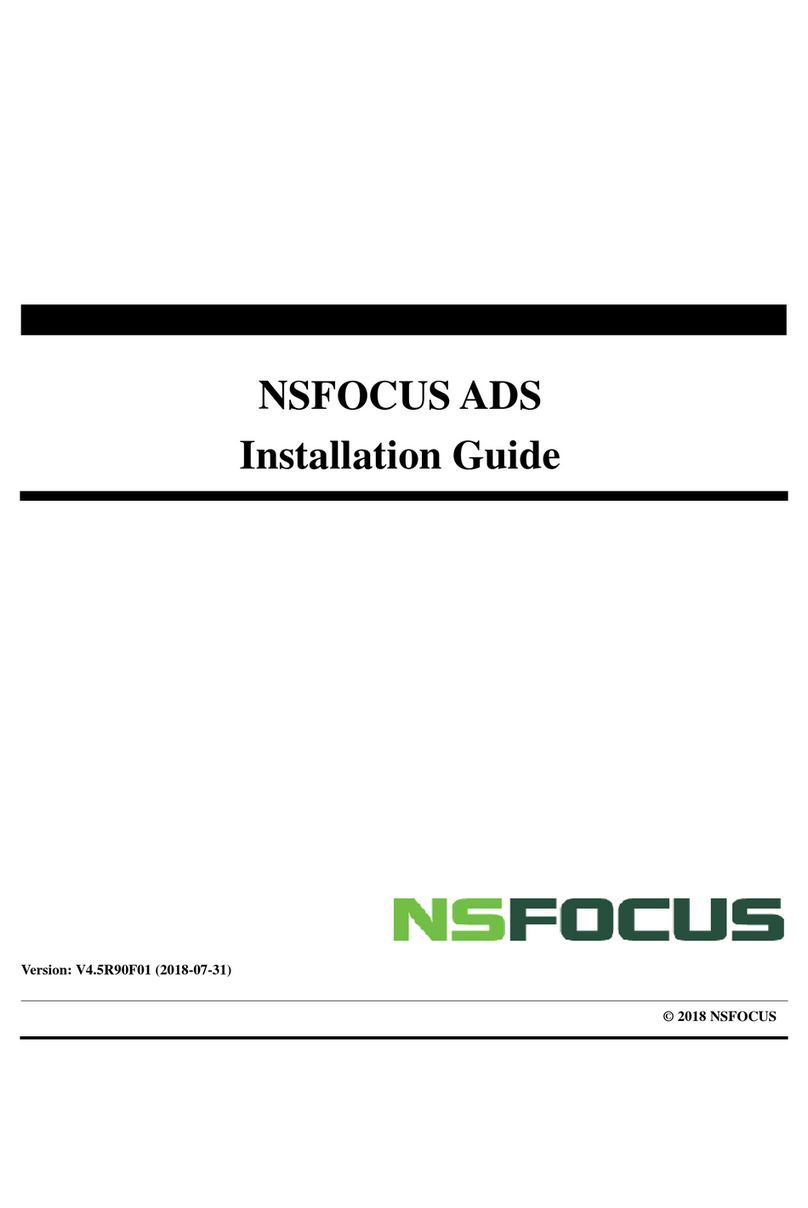
NSFOCUS
NSFOCUS ADS installation guide
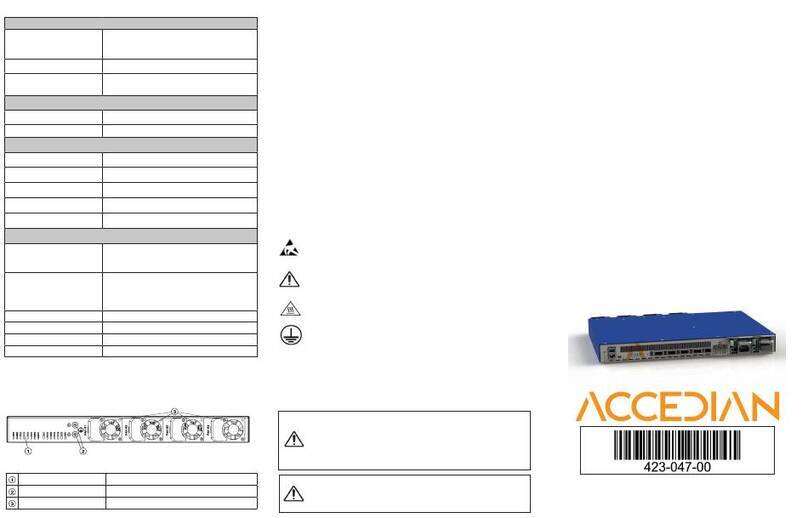
Accedian
Accedian Skylight Flex 100 Hardware installation guide

Cornick
Cornick VIP Vision NVRPRO Series quick start guide