ADB Safegate ACE2 User manual

Advanced Control Equipment (ACE2)
User Manual
96A0357, Rev. G, 2019/11/08


A.0 Disclaimer / Standard Warranty
CE certification
The equipment listed as CE certified means that the product complies with the essential requirements concerning safety and
hygiene. The directives that have been taken into consideration in the design are available on written request to ADB
SAFEGATE.
ETL certification
The equipment listed as ETL certified means that the product complies with the essential requirements concerning safety and
FAA Airfield regulations. The directives that have been taken into consideration in the design are available on written request
to ADB SAFEGATE.
LED Product Guarantee
Where applicable, per FAA EB67 (applicable edition), ADB SAFEGATE L858(L) Airfield Guidance Signs are warranted against
electrical defects in design or manufacture of the LED or LED specific circuitry for a period of 4 years. ADB SAFEGATE LED light
fixtures (with the exception of obstruction lighting) are warranted against mechanical and physical defects in design or
manufacture for a period of 12 months from date of installation; and are warranted against electrical defects in design or
manufacture of the LED or LED specific circuitry for a period of 4 years per FAA EB67 (applicable edition).
Note
See your sales order contract for a complete warranty description. In some specific cases, deviations are (to be)
accepted in the contract, which will supersede the standard warranty.
Standard Product Guarantee
Products of ADB SAFEGATE manufacture are guaranteed against mechanical, electrical, and physical defects (excluding lamps)
which may occur during proper and normal use for a period of one year from the date of installation or 2 years from date of
shipment and are guaranteed to be merchantable and fit for the ordinary purposes for which such products are made. ADB
SAFEGATE L858 Airfield Guidance Signs are warranted against mechanical and physical defects in design or manufacture for a
period of 2 years from date of installation per FAA AC 150/5345-44 (applicable edition).
Note
See your sales order contract for a complete warranty description.
All Products Guarantee
LED Products of ADB SAFEGATE, manufactured and sold by ADB SAFEGATE or its licensed representatives, meets the
corresponding requirements of FAA, ICAO and IEC.
ADB SAFEGATE will correct by repair or replacement per the applicable guarantee above, at its option, equipment or parts
which fail because of mechanical, electrical or physical defects, provided that the goods have been properly handled and
stored prior to installation, properly installed and properly operated after installation, and provided further that Buyer gives
ADB SAFEGATE written notice of such defects after delivery of the goods to Buyer. Refer to the Safety section for more
information on Material Handling Precautions and Storage precautions that must be followed.
ADB SAFEGATE reserves the right to examine goods upon which a claim is made. Said goods must be presented in the same
condition as when the defect therein was discovered. ADB SAFEGATE furthers reserves the right to require the return of such
goods to establish any claim.
ADB SAFEGATE’s obligation under this guarantee is limited to making repair or replacement within a reasonable time after
receipt of such written notice and does not include any other costs such as the cost of removal of defective part, installation
of repaired product, labor or consequential damages of any kind, the exclusive remedy being to require such new parts to be
furnished.
96A0357, Rev. G, 2019/11/08 iii
Copyright © ADB Safegate, All Rights Reserved

ADB SAFEGATE’s liability under no circumstances will exceed the contract price of goods claimed to be defective. Any returns
under this guarantee are to be on a transportation charges prepaid basis. For products not manufactured by, but sold by ADB
SAFEGATE, warranty is limited to that extended by the original manufacturer.
This is ADB SAFEGATE’s sole guarantee and warranty with respect to the goods; there are no express warranties or warranties
of fitness for any particular purpose or any implied warranties of fitness for any particular purpose or any implied warranties
other than those made expressly herein. All such warranties being expressly disclaimed.
Liability
WARNING
Use of the equipment in ways other than described in the catalogue leaflet and the manual may result in personal
injury, death, or property and equipment damage. Use this equipment only as described in the manual.
ADB SAFEGATE cannot be held responsible for injuries or damages resulting from non-standard, unintended uses of its
equipment. The equipment is designed and intended only for the purpose described in the manual. Uses not described in the
manual are considered unintended uses and may result in serious personal injury, death or property damage.
Unintended uses includes the following actions:
•Making changes to equipment that have not been recommended or described in this manual or using parts that are not
genuine ADB SAFEGATE replacement parts or accessories.
•Failing to make sure that auxiliary equipment complies with approval agency requirements, local codes, and all applicable
safety standards if not in contradiction with the general rules.
•Using materials or auxiliary equipment that are inappropriate or incompatible with your ADB SAFEGATE equipment.
•Allowing unskilled personnel to perform any task on or with the equipment.
© ADB SAFEGATE BVBA
This manual or parts thereof may not be reproduced, stored in a retrieval system, or transmitted, in any form or by any means,
electronic, mechanical, photocopying, recording, nor otherwise, without ADB SAFEGATE BVBA’s prior written consent.
This manual could contain technical inaccuracies or typographical errors. ADB SAFEGATE BVBA reserves the right to revise this
manual from time to time in the contents thereof without obligation of ADB SAFEGATE BVBA to notify any person of such
revision or change. Details and values given in this manual are average values and have been compiled with care. They are not
binding, however, and ADB SAFEGATE BVBA disclaims any liability for damages or detriments suffered as a result of reliance
on the information given herein or the use of products, processes or equipment to which this manual refers. No warranty is
made that the use of the information or of the products, processes or equipment to which this manual refers will not infringe
any third party’s patents or rights. The information given does not release the buyer from making their own experiments and
tests.
Advanced Control Equipment (ACE2)
iv
Copyright © ADB Safegate, All Rights Reserved

TABLE OF CONTENTS
1.0 Safety.........................................................................................................................................................................................1
1.1 Safety Messages.......................................................................................................................................................................................................... 1
1.1.1 Introduction to Safety...................................................................................................................................................................................2
1.1.2 Intended Use.................................................................................................................................................................................................... 2
2.0 Advanced Control Equipment.................................................................................................................................................3
2.1 About this manual.......................................................................................................................................................................................................3
2.2 How to work with the manual................................................................................................................................................................................3
3.0 Introduction..............................................................................................................................................................................5
3.1 Advanced Control Equipment................................................................................................................................................................................ 5
3.2 Wall Mount.................................................................................................................................................................................................................... 8
3.3 Internal-Mount.............................................................................................................................................................................................................8
3.4 Combo Box-Mount.....................................................................................................................................................................................................9
3.5 Main Circuit Board.......................................................................................................................................................................................................9
3.6 ACE2 Lamps-Out Monitoring Board..................................................................................................................................................................11
4.0 Modes of Operation...............................................................................................................................................................13
4.1 Stand-Alone Configuration...................................................................................................................................................................................13
4.2 Stand-Alone Push-button Description............................................................................................................................................................. 16
4.3 I/O Status display......................................................................................................................................................................................................17
4.3.1 Lamps-Out Calibration for Stand-Alone Mode................................................................................................................................18
5.0 Installation..............................................................................................................................................................................19
5.1 Introduction.................................................................................................................................................................................................................19
5.2 Wall-Mount Installation..........................................................................................................................................................................................19
5.2.1 ACE2 Cabling Entry......................................................................................................................................................................................20
5.3 Internal-Mount Installation...................................................................................................................................................................................23
5.4 Combo Box-Mount Installation...........................................................................................................................................................................23
5.4.1 ACE2 Cable Entry..........................................................................................................................................................................................25
6.0 Troubleshooting.....................................................................................................................................................................27
6.1 Troubleshooting Procedures.................................................................................................................................................................................27
6.2 Error Messages...........................................................................................................................................................................................................29
6.3 Wiring Schematics....................................................................................................................................................................................................30
6.3.1 Connectors......................................................................................................................................................................................................31
7.0 Parts.........................................................................................................................................................................................35
7.1 Parts List....................................................................................................................................................................................................................... 35
A.0 SUPPORT................................................................................................................................................................................ 37
A.1 ADB SAFEGATE website..........................................................................................................................................................................................37
A.2 Recycling......................................................................................................................................................................................................................38
A.2.1 Local authority recycling...........................................................................................................................................................................38
A.2.2 ADB SAFEGATE recycling.......................................................................................................................................................................... 38
96A0357, Rev. G, 2019/11/08 v
Copyright © ADB Safegate, All Rights Reserved

Advanced Control Equipment (ACE2)
TABLE OF CONTENTS
vi
Copyright © ADB Safegate, All Rights Reserved

1.0 Safety
Introduction to Safety
This section contains general safety instructions for installing and using ADB SAFEGATE equipment. Some safety instructions
may not apply to the equipment in this manual. Task- and equipment-specific warnings are included in other sections of this
manual where appropriate.
1.1 Safety Messages
HAZARD Icons used in the manual
For all HAZARD symbols in use, see the Safety section. All symbols must comply with ISO and ANSI standards.
Carefully read and observe all safety instructions in this manual, which alert you to safety hazards and conditions that may
result in personal injury, death or property and equipment damage and are accompanied by the symbol shown below.
WARNING
Failure to observe a warning may result in personal injury, death or equipment damage.
DANGER - Risk of electrical shock or ARC FLASH
Disconnect equipment from line voltage. Failure to observe this warning may result in personal injury, death, or
equipment damage. ARC Flash may cause blindness, severe burns or death.
WARNING - Wear personal protective equipment
Failure to observe may result in serious injury.
WARNING - Do not touch
Failure to observe this warning may result in personal injury, death, or equipment damage.
CAUTION
Failure to observe a caution may result in equipment damage.
Qualified Personnel
Important Information
The term qualified personnel is defined here as individuals who thoroughly understand the equipment and its safe
operation, maintenance and repair. Qualified personnel are physically capable of performing the required tasks, familiar
with all relevant safety rules and regulations and have been trained to safely install, operate, maintain and repair the
equipment. It is the responsibility of the company operating this equipment to ensure that its personnel meet these
requirements.
Always use required personal protective equipment (PPE) and follow safe electrical work practice.
96A0357, Rev. G, 2019/11/08 1
Copyright © ADB Safegate, All Rights Reserved

1.1.1 Introduction to Safety
CAUTION
Unsafe Equipment Use
This equipment may contain electrostatic devices, hazardous voltages and sharp edges on components
• Read installation instructions in their entirety before starting installation.
• Become familiar with the general safety instructions in this section of the manual before installing,
operating, maintaining or repairing this equipment.
• Read and carefully follow the instructions throughout this manual for performing specific tasks and
working with specific equipment.
• Make this manual available to personnel installing, operating, maintaining or repairing this
equipment.
• Follow all applicable safety procedures required by your company, industry standards and
government or other regulatory agencies.
• Install all electrical connections to local code.
• Use only electrical wire of sufficient gauge and insulation to handle the rated current demand. All
wiring must meet local codes.
• Route electrical wiring along a protected path. Make sure they will not be damaged by moving
equipment.
• Protect components from damage, wear, and harsh environment conditions.
• Allow ample room for maintenance, panel accessibility, and cover removal.
• Protect equipment with safety devices as specified by applicable safety regulations
• If safety devices must be removed for installation, install them immediately after the work is
completed and check them for proper functioning prior to returning power to the circuit.
Failure to follow this instruction can result in serious injury or equipment damage
Additional Reference Materials
Important Information
•IEC - International Standards and Conformity Assessment for all electrical, electronic and related technologies.
•IEC 60364 - Electrical Installations in Buildings.
•FAA Advisory: AC 150/5340-26 (current edition), Maintenance of Airport Visual Aid Facilities.
•Maintenance personnel must refer to the maintenance procedure described in the ICAO Airport Services Manual,
Part 9.
•ANSI/NFPA 79, Electrical Standards for Metalworking Machine Tools.
•National and local electrical codes and standards.
1.1.2 Intended Use
CAUTION
Use this equipment as intended by the manufacturer
This equipment is designed to perform a specific function, do not use this equipment for other purposes
• Using this equipment in ways other than described in this manual may result in personal injury, death
or property and equipment damage. Use this equipment only as described in this manual.
Failure to follow this instruction can result in serious injury or equipment damage
Advanced Control Equipment (ACE2)
Safety
2
Copyright © ADB Safegate, All Rights Reserved

2.0 Advanced Control Equipment
ACE2 Operations Manual
2.1 About this manual
The manual shows the information necessary to:
•Install
•Carry out maintenance
•Carry out troubleshooting on the Advanced Control Equipment.
2.2 How to work with the manual
1. Become familiar with the structure and content.
2. Carry out the actions completely and in the given sequence.
96A0357, Rev. G, 2019/11/08 3
Copyright © ADB Safegate, All Rights Reserved

Advanced Control Equipment (ACE2)
Advanced Control Equipment
4
Copyright © ADB Safegate, All Rights Reserved

3.0 Introduction
This section describes the L-827/ L-829 Advanced Control Equipment (ACE2™).
Note
ACE and ACE2 are trademarks of ADB Airfield Solutions.
The ACE2 operates either as the remote interface between the L-890 ALCMS and any controlled element in the airfield
lighting vault or as the stand-alone regulator/monitor performing all L-827/L-829 functions in accordance with FAA AC 150 /
5345-10F. The ACE2 is a universal device that can be used to control any type of CCR and/or controlled element regardless of
the manufacturer.
L-827/L-829 ACE2
The ACE2 can be physically packaged as a Combo Box-Mount (Figure 3), a Wall-Mount (Figure 1), or a CCR Internal-Mount
(Figure 2). The Combo Box Assembly is a wall-mount version, which houses the ACE2 controller board, the IRMS board, and
the CVM. The Remote-Mount is typically placed on top of the CCR. The Wall-Mount is usually bolted to a wall or can be
mounted on the front of a CCR. The internal-mount is mounted inside a ADB Airfield Solutions L-828 CCR. This combination is
called an L-829 CCR.
3.1 Advanced Control Equipment
Compliance with Standards
FAA: Monitoring: Certified to AC 150/5345-10 (Current Edition). ETL Certified.
Insulation Resistance: AC 150/5340-26 Chapter 3, Section 2, para. 27.
Overview
The ACE2 can operate either as the remote interface between the L-890 ALCMS and any controlled element in the airfield
lighting vault or as the stand-alone constant current regulator (CCR) monitor, performing all L-827/L-829 functions in
accordance with FAA AC 150 /5345-10. The ACE2 is a universal device that can be used to control any type of CCR and/or
controlled element regardless of the manufacturer.
The ACE2 can be packaged as a remote mount, wall mount, CCR internal mount, or Combo Box. A remote mount is typically
placed on top of the CCR. The wall mount is typically bolted to a wall or can be mounted on the front of a CCR. The internal
mount is mounted inside a ADB Safegate L-828 CCR (Also called a L-829 CCR). The Combo Box Assembly is a wall-mount
version, which houses the ACE controller board. The Combo Box Assembly also houses the IRMS board and the CVM, which
are normally mounted inside a ADB Safegate L-829 CCR.
Each CCR and controllable item is connected to an ACE2. The ACE2 is a microprocessor-based module that includes all of the
communication, control commands, input/output inter-face, and fail-safe functionality for the controlled element.
Note
For those applications that require:
•Connection with up to a four-circuit L-847
•Up to eight discrete input or outputs
Use ADB SAFEGATE's first generation ACE system. Request data sheet 2016 for more information.
96A0357, Rev. G, 2019/11/08 5
Copyright © ADB Safegate, All Rights Reserved

Theory of Operation
The Advanced Control Equipment (ACE2™) represents the heart of ADB SAFEGATE's airfield lighting distributed control
system. Distributed control technology has many advantages over traditional central control, including but not limited to:
cost-effectiveness, system expandability, ease of maintenance, ease of installation, interchangeable parts, and ease of
troubleshooting. In a distributed control scenario, each ACE2 unit is locally installed at or near a controllable item (CCR,
Generator, ATS, etc.). Each ACE2 would, in turn, talk with the airfield lighting control network and execute remote lighting
commands. Multiple ACE2 units can be daisy-chained together, making system expansion very easy.
The ACE2 is a universal device that can be used to control any type of CCR and/or controlled element regardless of the
manufacturer. The printed circuit boards are mounted inside a small and rugged environmental enclosure that can be
mounted on top of the CCR, wall mounted or directly attached to the door of an ADB Safegate L-828 CCR.
The ACE2 consists of a microprocessor-based module(s) that includes all of the communication, control commands, input/
output interface, and fail-safe functionality for the controlled element.
The ACE2 is ADB SAFEGATE' second generation distributed control/monitor system. ACE2 network communications are
compatible with ADB SAFEGATE's first generation system simply called ACE. Thus ACE and ACE2 units can be connected on
the same distributed network.
Communication
Each of the ACE2 units connected to a CCR or other controllable device will have a unique factory set number and a field
programmable communication address. This address is used by the ADB SAFEGATE L-890 ALCMS to direct lighting
commands to the corresponding ACE2, which in turn executes the commands and returns the operational status of the
element back to the ALCMS.
Each ACE2 is connected to redundant communication networks via two RS-422 serial communication ports located on the
main printed circuit board. The ACE network is comprised of a communications server and all the daisy-chained ACE2 and
ACE (if present) units in the lighting vault. Both the ACE2 and ACE devices can be connected to the same network. The
communications server stays in constant communication with all the ACE2 and ACE units in both of the networks while at the
same time staying in constant contact with the main ALCMS network. This communications protocol dictates that the local
ACE2 store all data and parameters specific to the controlled element. This characteristic frees up the ALCMS computers from
having to store the parameters for each of the controlled elements. The result of this is real-time communication between all
of the ACE2 and ACE units and the rest of the ADB SAFEGATE L-890 ALCMS, even if a network connection fails in one of the
ACE2 or ACE units.
Input/Output Interface
The ACE2 incorporates an input/output interface that supports full FAA L-827/L-829 CCR control monitoring capabilities. The
pluggable terminal blocks provide an easy-to-service point of connection.
The latching output relays can be configured to control CCR brightness steps or simple ON/OFF control as required by the
controlled element. The input lines can be configured to monitor any external event that is determined by a discrete dry
contact closure. Some examples include generator monitoring, monitoring of Automatic Transfer Switch position, and control
of Circuit Selector Switch loops. In addition, the ACE2 can be optionally expanded to perform CCR input voltage and current
monitoring as well as airfield circuit cable Insulation Resistance Monitoring.
Fail-safe Functionality
Each ACE2 unit provides a self-contained fail-safe feature. This feature insures default airfield lighting operation in the event
of an L-890 ALCMS component failure or even a complete ALCMS failure. In addition, each ACE2 can monitor its output and
verify that the proper command is executed. The fail-safe system also permits maintenance of portions of the control system
without changing the operational status of the lighting system. The fail-safe system is by definition only used in the ALCMS
modes, and must be set up by a qualified ADB SAFEGATE technician.
The fail-safe mode of each ACE2 unit is defined per requirements of the airport/owner. The fail-safe modes are as follows:
Latching Fail-safe Mode:
This mode is executed as follows:
•If the CCR was switched ON before the failure, it will remain ON at the same brightness level.
•If the CCR was switched OFF before the failure, it will remain OFF.
Simple Fail-safe Mode:
Advanced Control Equipment (ACE2)
Introduction
6
Copyright © ADB Safegate, All Rights Reserved

This mode is executed as follows:
•After a failure occurs, the CCR will switch ON to a predeter-mined brightness level without regard to the current step.
Smart Fail-safe Mode:
This mode is executed as follows:
•If the CCR was switched ON before the failure, it will remain ON at the same brightness level.
•If the CCR was switched OFF before the failure, it will switch ON to a predetermined brightness level.
Graphics User Interface (GUI)
The ACE2 graphic user interface (GUI) consists of the 128 x 64 pixel monochrome LCD display and four momentary switch
buttons. In typical modes of operation, the upper half of the LCD displays a monitored parameter or in the stand-alone mode
a configuration menu. The first string of the LCD lower half is reserved for warning and alarm messages in “reverse color”.
Reverse color means that the background is white and the text is blue. The second string is split to indicate several fields and
displays:
•Brightness step. Reverse color means protective shutdown, blank – OFF.
•Remote (“Rmt”)/Local (“Lcl” reverse color)
•Primary power present (“PP”) / loss of power (“LoP” reverse color)
•RS422 channel A message received ('A')
•RS422 channel B message received ('B')
•IRMS response received (small 'W'), megging has been reported (large 'W')
Specifications
Input Voltage: 85 to 256 VAC, 12 VA, 50/60 Hz
Input Power: 12VA maximum
Operating Conditions: -10 to +55 °C (+14 to +131 °F)
Altitude: Sea Level to 10,000 feet
Dimensions
Remote Mount: 13.3 × 10.4 × 3.9 in
(33.8 × 26.4 × 9.9 cm)
Wall Mount: 13.2 × 11.3 × 4.2 in
(33.5 × 28.7 × 10.7 cm)
Internal Mount: 13.2 × 10.3 × 2.7 in
(33.5 × 26.2 × 6.9 cm)
Combo Box: 20.0 × 20.0 × 8.7 in
(50.8 × 50.8 × 22.1 cm)
96A0357, Rev. G, 2019/11/08 7
Copyright © ADB Safegate, All Rights Reserved

3.2 Wall Mount
Figure 1: ACE2 Wall-Mount Assembly
1. Enclosure
2. ACE2 Front Display
3. ACE Control Keys
3.3 Internal-Mount
Figure 2: Internal-Mount Assembly
1. Constant Current Regulator
2. ACE2 Display
3. ACE2 Control Keys
4. Rotary Step Switch
Refer to Figure 2. The ACE2 is a universal device that is used to control most types of CCRs and/or controlled elements
regardless of the manufacturer. The ACE2 printed circuit boards are mounted inside a small and rugged environmental
enclosure that can be:wall-mounted, placed on a CCR, or enclosed in the CCR itself. The ACE2 consists of microprocessor-
based module(s) that process communication, control commands, input/ output interface, and failsafe functionality for
controlled elements in the airfield lighting vault.
Advanced Control Equipment (ACE2)
Introduction
8
Copyright © ADB Safegate, All Rights Reserved

3.4 Combo Box-Mount
Figure 3: ACE2 Combo Box-Mount Assembly
1. Enclosure
2. ACE2 Front Display
3. ACE2 Control Keys
3.5 Main Circuit Board
The Main Printed Circuit Board (Figure 4) is the central part of the design. It includes a micro-controller core that implements
main logic and provides calculating functions. A communication circuit provides the interface for the redundant
communication network (RCN), which is how ACE2 receives and transmits data to the ALCMS vault computer. It contains a
fiber optic interface connection for the Current Voltage Monitor (CVM), optional Insulation Resistance Monitoring System
(IRMS), and an RS-232 local configuration interface. The watchdog jumper (J2) is used to select whether the watchdog timer is
On or Off. Connecting pins 1 and 2 enables the watchdog timer. Connecting pins 2 and 3 disables watchdog timer, and
removing the jumper also disables watchdog timer. The normal setting for the watchdog timer is On. The watchdog timer
should only be set by qualified ADB Airfield Solutions personnel. The reset switch (SW1) is used during the design and test
phase, and has no application for the user. The keypad switches and an LCD connector provides a Graphic User Interface (GUI)
for local control and monitoring for all controllable functions. The display is connected to the main board by a ribbon cable.
The two-position DIP switch (SW2), is not currently used, but allows for future upgrades. The DIP switch must remain with
both selectors in the On position for proper operation. The Power Supply circuitry provides all ACE2 equipment with a
regulated and isolated power source.
96A0357, Rev. G, 2019/11/08 9
Copyright © ADB Safegate, All Rights Reserved

The Power Supply circuitry can be turned On and Off via the main power switch in the lower right corner of Figure 4.
Figure 4: ACE2 Main Circuit Board
1. Ribbon connector to display board 3. SW1 5. SW7 7. Relay Fuses
2. Main PCB 4. SW2 6. RY7
Table 1: Main Board Description
Feature Function Description
Ribbon connector to display
board
Main PCB
SW1 Reset switch - Press to reset the processor
SW2
Two-position DIP switch
•Not used
•Keep in On position
SW7 On/Off power switch to ACE2
RY7 RY7 general fault relay
Relay Fuse
ACE2 Power Supply Circuit
The ACE2 Power Supply circuitry is integrated into the Main Circuit Board (shown in Figure 5). It provides the internal system
with a regulated and isolated power source.
ACE2 Input/Output
Advanced Control Equipment (ACE2)
Introduction
10
Copyright © ADB Safegate, All Rights Reserved

The Discrete Input/Output circuitry provides an interface for all control and monitoring connections. It contains seven latching
relay outputs and, one proper operation, mono-stable relay output normally used for the Fault Alarm indication. The I/O
circuit contains eight Optically-isolated input lines.
3.6 ACE2 Lamps-Out Monitoring Board
The ACE2 lamps-out monitoring (LOM) board (Figure 5) consists of a processor communicating over a fiber optic serial
communications link, with up to three Current and Voltage Modules (CVM). In addition to RMS voltage, RMS current,
apparent power (VA), and true power (WATTS), the LOM Board also calculates the number of lamps burned out at each
brightness level. The Lamps-out function can detect up to 16 burned out lamps.
If the CCR is controlling multiple circuits through circuit selectors, each of the circuits may have a CVM monitoring voltage,
current, watts, VA, and the number of lamps out on the circuit.
The setting of the two-position DIP switch (SW1) depends on the number of circuits monitored and the number of Lamps-Out
boards used. If the ACE2 contains only one Lamps- Out board, the settings are:
•Switch 1 - Off
•Switch 2 - Off
If the ACE2 contains a second Lamps-Out board, the SW1 settings on the second board are:
•Switch 1 - Off
•Switch 2 - On
If the ACE2 contains a third Lamps-Out board, the SW1 settings on the third board are
•Switch 1 - Off
•Switch 2 - On
The third Lamps-Out board also has a 4-port jumper with a jumper on pins 1 and 2.
Figure 5: Lamps-Out Monitoring Module
1. Switch (SW2)
2. SW1 Switch Positions for Monitoring Additional Lamps-Out Boards
3. IC Chip Sets
4. Fiber Optic Sockets (one shown installed)
96A0357, Rev. G, 2019/11/08 11
Copyright © ADB Safegate, All Rights Reserved

Advanced Control Equipment (ACE2)
Introduction
12
Copyright © ADB Safegate, All Rights Reserved

4.0 Modes of Operation
Only qualified ADB Safegate personnel select modes of operations. There are 3 ways to handle the ACE2 operation:
1. L-827 stand-alone (external to the CCR).
2. L829 stand-alone (integrated with the CCR).
3. L-890 ALCMS.
4.1 Stand-Alone Configuration
The ACE2 is only set up for stand-alone operation by qualified ADB Safegate personnel. In this mode, configuration of the
ACE2 is performed through the local menu and alternative functions of the buttons listed in Figure 7:
1. Modify, execute (Output Monitoring button).
2. Go to the next item (Auxiliary Monitoring button).
3. Enter, exit (Select/Config button).
4. No Function (Software Version button).
Figure 6: Functional Buttons
The stand-alone mode configuration menu is presented in Table 2 and Figure 7 below.
Table 2: ACE2 Stand-Alone Configuration Short Reference
Button Action
2 ↓ , 3 2 ↓ , 3 ←, 1
modify
Menu Item Parameter Possible value Description
CCR Config
Menu
CCR Type Generic, Heavy
Duty
Heavy Duty is an older brand name, which requires an additional output line
(B1, B10) to turn on and off the regulator. If this regulator is not in use adjust
setting to Generic.
CCR Class 6.6A, 20A ADB Safegate sells two regulator output types. 6.6A and 20A output. Based on
the regulator choose the correct current output.
CCR Style 3 steps, 5 steps ADB Safegate sells two regulator step types, 5 step and 3 step. Based on the
regulator choose the correct Step Configuration.
Line Frequency 50Hz, 60Hz Depending on the location, the input voltage frequency may be 50Hz or 60Hz.
Set the ACE2 to the correct frequency for the area.
Ramp Interval 0.5s, 1s, 2s, 5s
When adjusting the steps of a regulator it is necessary to have a slight delay
between steps. The Ramp Interval sets the amount of time the regulator stays
at a step before moving on to the next step.
96A0357, Rev. G, 2019/11/08 13
Copyright © ADB Safegate, All Rights Reserved

Table 2: ACE2 Stand-Alone Configuration Short Reference (continued)
Button Action
2 ↓ , 3 2 ↓ , 3 ←, 1
modify
Menu Item Parameter Possible value Description
IRMS Config
Menu
Meg Voltage Disabled, 50V,
500V, 1000V
Select the Meg Voltage based on the regulator. The smaller regulators voltage
protection triggers if higher Meg Voltages are used, but the higher the Meg
Voltage, the more accurate the reading.
Meg Period 5min, Hourly,
Daily, Weekly Set how often to Meg the field circuit
Resistance
Warning
Disabled, 100K,
300K,1M, 3M,
10M, 30M,
100M
Select a resistance value to be notified at depending on the field circuit, it may
vary.
Resistance Alarm
Disabled, 100K,
300K,1M, 3M,
10M, 30M,
100M
Select a resistance value to be notified at depending on the field circuit, it may
vary.
LOM Config
Menu
LO Warning Disabled, 1-15 Select a Lamp out value to be notified at depending on the field circuit, it may
vary.
LO Alarm Disabled, 1-15 Select a Lamp out value to be notified at depending on the field circuit, it may
vary
Command
Menu
Meg Now N/A Perform a Meg right now
Meg Timer Reset N/A Reset the current Meg timer to start over with the count.
LO Calibration N/A See Lamps-Out Calibration for Stand-Alone Mode for instructions.
Exit N/A N/A
Note
VA refers to the Volt-Amps in an airfield load and is measured by reading the RMS voltage, measuring the RMS
current, and multiplying these two numbers together.
Watts corresponds to the amount of power actually consumed by an airfield load. These two numbers are only equal in the
case of a purely resistive load. In systems with reactance (capacitance or inductance), power from the source enters the
reactive portions of the load, and returns to the source, un-used. This additional unused energy is the difference between the
VA and Watts delivered to a system. The power factor of a load is the ratio of the power (watts) used by a load, to the volts
and amps (VA) that are delivered to the load. This is always less than or equal to 1.
It is important to remember that all electrical components in a power system are designed to deliver the necessary VA the
system needs in order for it to consume the watts it needs.
CCR sizes are actually designed to deliver a kVA value because it is impossible to account for the different power factors in
airfield loads. If an airfield load has open-circuited transformers, signs, etc. it requires more VA to deliver the watts needed.
For instance, if a 30kW CCR delivered 30kVA into a load with a power factor of 0.5 the resultant watts would be 15kW.
Advanced Control Equipment (ACE2)
Modes of Operation
14
Copyright © ADB Safegate, All Rights Reserved
Table of contents
Other ADB Safegate Control System manuals
Popular Control System manuals by other brands
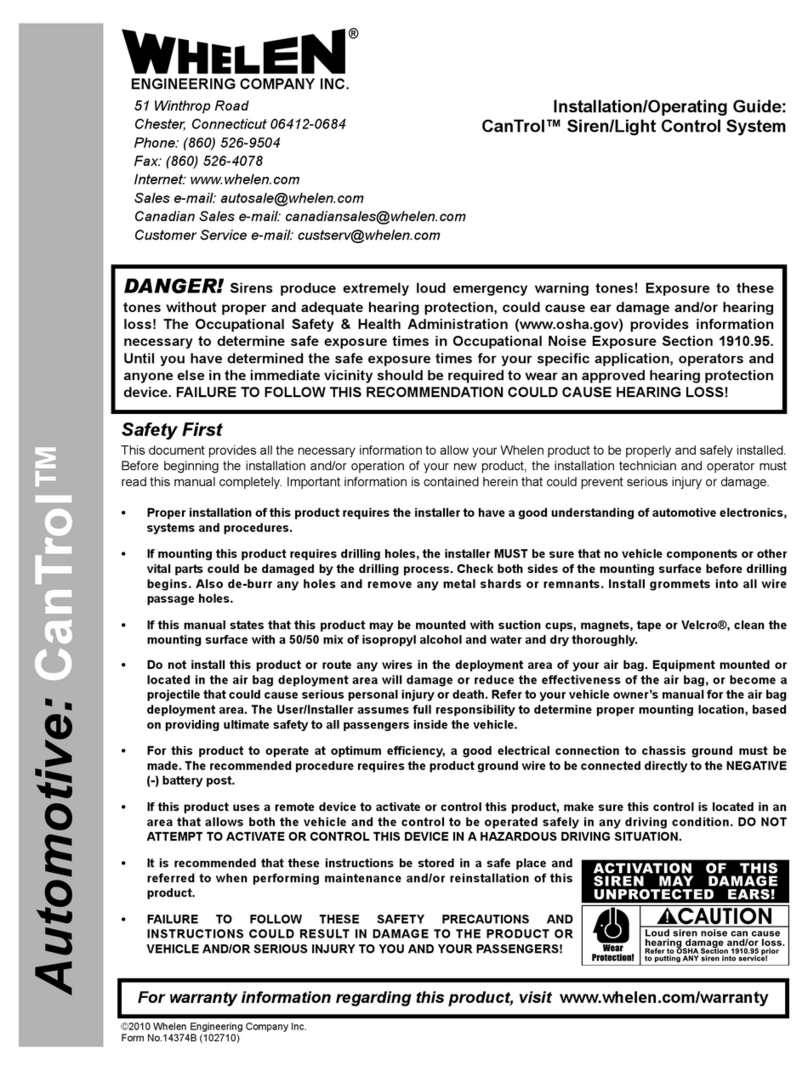
Whelen Engineering Company
Whelen Engineering Company CanTrol Installation & operating guide
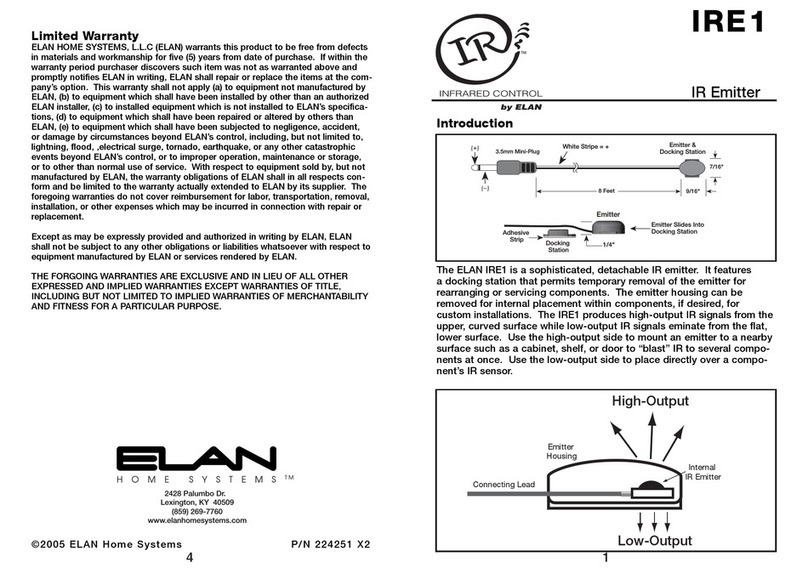
Elan
Elan IRE1 quick start guide

Knight
Knight UMP Hospitality instruction manual

MBW
MBW CH104 Series Installation & user manual
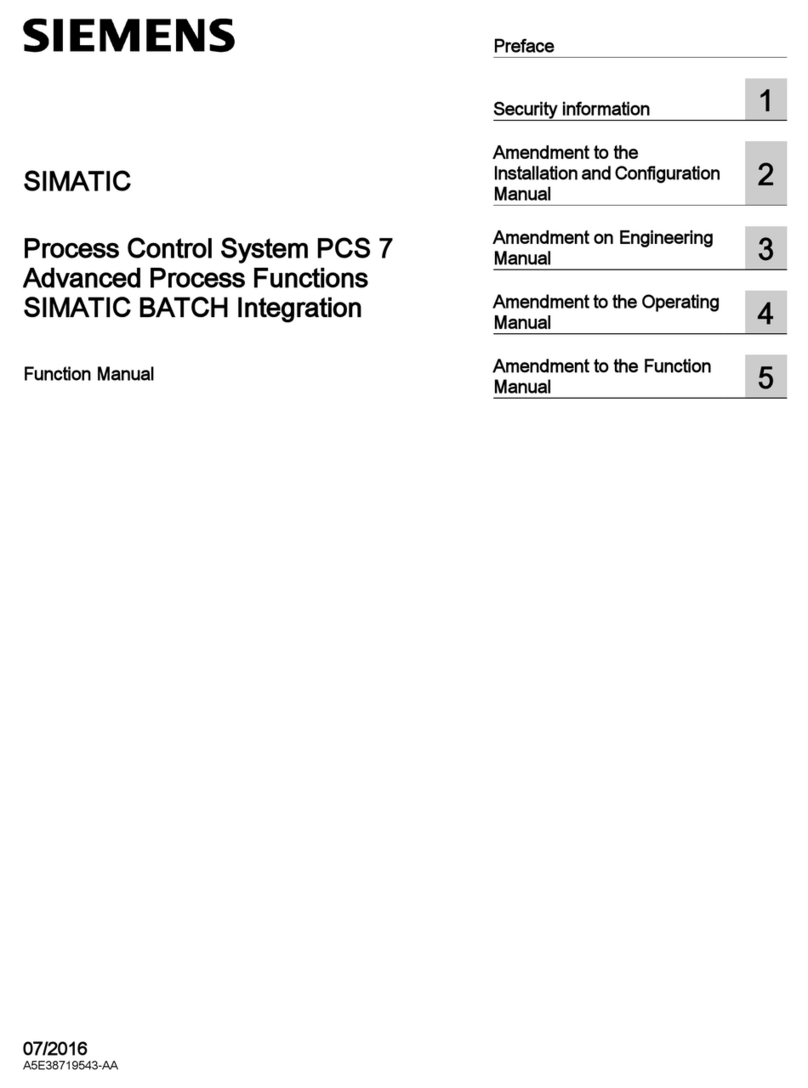
Siemens
Siemens SIMATIC PCS 7 Function manual
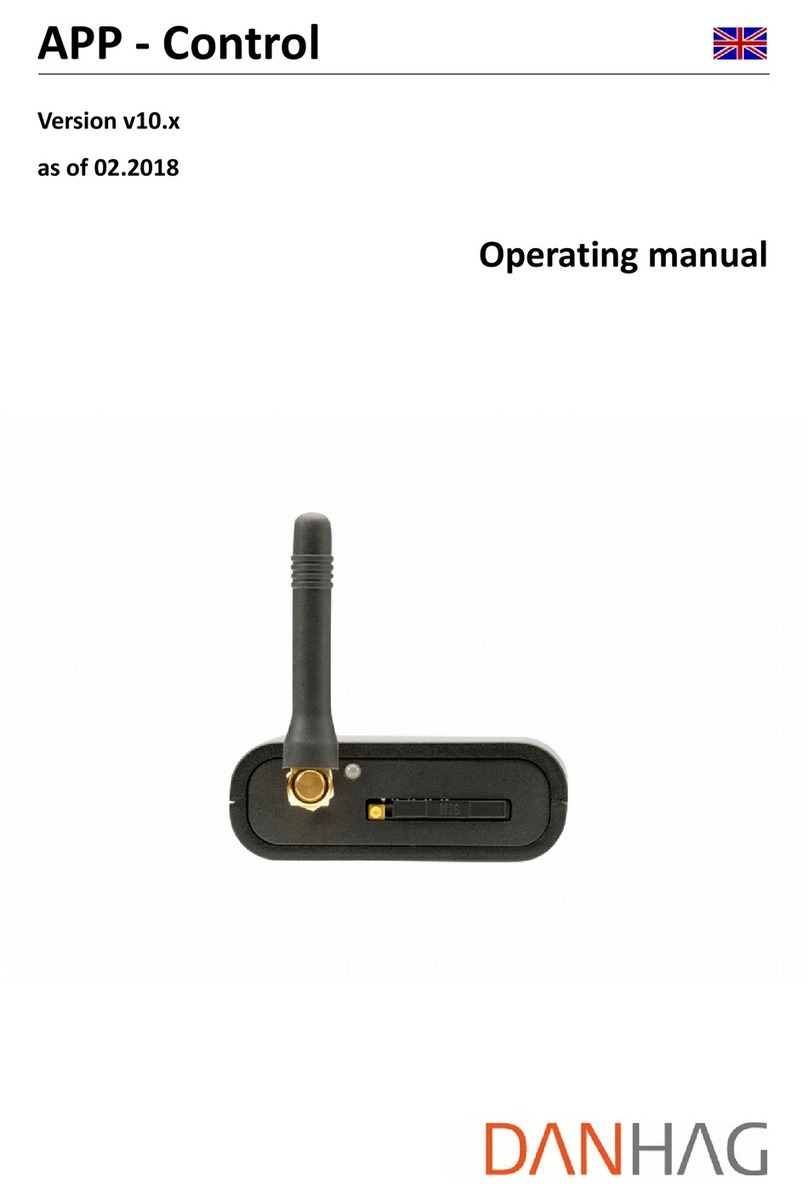
DANHAG
DANHAG APP-control operating manual