autosen AI006 User manual

Operating principle of an inductive
proximity sensor
autosen AI001- AI065
autosen AI401- AI408
autosen AI801- AI816
autosen AI901- AI908
2502588 / 00 02 / 2019
Made in EU
UK

2
1. Operating principle of an inductive proximity sensor
The coil and capacitor form an LC circuit, also known as a basic sensor. Eddy current
losses in electrically conductive materials are used for a switching signal.
2. Terms:
Active zone / active
face
Space (room) above the sensing face in which the sensor reacts to the
approach of the damping material.
Output function Normally open: Object within the active zone
> Output switched.
Normally closed: Object within the active zone
> Output blocked.
Programmable: Normally closed or normally open can be freely selected.
Positive switching: Positive output signal (to L–).
Negative switching: Negative output signal (to L+).
Rated insulation
voltage
DC units with protection class II: 250 V AC
DC units with protection class III: 60 V DC
Rated short-circuit
current
For short-circuit-proof units: 100 A
Rated impulse with-
stand voltage
DC units with protection class II: 4 kV (≙overvoltage category III)
DC units with protection class III: 60 V DC: 0.8 kV (≙overvoltage
category II)
Power-on delay time The time the sensor needs to be ready for operation after application of
the operating voltage (in the millisecond range).
Operating voltage The voltage range in which the sensor functions safely. A stabilised and
smoothed direct voltage should be used!
Take into account residual ripple!
1: Connection
2: Housing
3: Downstream electronics
4: Capacitor
5: Pot core
6: Coil
7: Alternating electromagnetic eld = active face
8: Target = electrically conductive material

Current consumption Current for the internal supply of 3-wire DC units.
Degree of soiling Inductive proximity sensors are designed for degree of soiling 3.
Hysteresis Difference between the switch-on and the switch-off point.
Short-circuit pro-
tection
If autosen sensors are protected against excessive current by means of
a pulsed short-circuit protection, the short-circuit protection may cut in
with incandescent lamps, electronic relays and low resistance loads.
Standard target Square steel plate with a thickness of 1 mm and a side length identical
to the diameter of the sensing face or 3 x Sn, depending on which value
is greater.
Product standard IEC 60947-5-2
Repeatability = Repeat precision
Difference between any two Sr measurements. Max. 10% of Sr.
Switch point drift Shift in the switch point owing to changes in the ambient temperature.
Switching frequency Damping with standard target at half Sn. The ratio damped to undamped
(mark to space) = 1 : 2.

4
3. Sensing range (referred to the standard target)
Nominal sensing range Sn= characteristic value of the unit
Real sensing range Sr= individual deviation at room temperature between 90% and 110%
of Sn
Useful sensing range Su= switch point drift between 90% (Sumin = Sa) and 110% (Sumax)
of Sr
Safe sensing range =
operating distance Sa
= reliably switched between 0% and 81% of Sn
Safe switch-off distance = Sumax + max. hysteresis = 143% of Sn
4. Correction factors 5. Inuence of the standard target size
The sensor-specic values can be
found in the data sheet (exception
K1 units:
Same sensing range for all
X axis: Ratio between actual
target and the standard
target

6. Lateral approach and distances
7. Tips on ush and non-ush mounting in metal
Installation instructions for cylindrical designs
The principle of inductive sensor technology is based on an electromagnetic alternating eld created
via a copper coil embedded in an open pot core made of ferrite. An resonant circuit is created using
the capacitor. Thanks to an electrically conductive metal, located within a certain range in front of the
sensor, the eddy currents of the magnetic eld are strongly attenuated. These changes in the oscilla-
tion amplitude are detected by the sensor and the sensor is switched.
1. Typical switch-on curve (for slow approach)
2. Typical switch-off curve (for slow approach)
3. Poor repeatability
4. Good repeatability
The following applies for good repeatability of the
switch point: The closer the damping element is to
the sensor face the better. General recommendation:
a = 10% of the nominal sensing range.
1. Distance to the background
2. Recommended target distance
3. Recommended degree of coverage of
the sensing face
4. Recommended target size
The special feature of sensors which can be installed ush is the additional outer metal ring which
surrounds the coil. This shields the alternating eld and bundles it at the front.
non-ush mountable
sensor
Shielded coil with a ush
mountable sensor

6
Free zones
Free zones refer to areas around the sensor which must be kept free of metallic materials in order not
to compromise with the operating principle of the device.
With inductive sensors, a distance of at least three times the nominal sensing range must be main-
tained between a metallic material and the sensing face. The correct installation of non-ush mounta-
ble sensors also requires that there is no interference material within a distance less than the diameter
of the detection face. The sensing face projects out of the metallic environment by twice the length of
the nominal sensing range of the sensor.
d d≥ d d d≥ 2 x d
d = diameter of the
sensing face
(details in data sheet)
Sn = Nominal sensing range
(details in data sheet)
≥ d
≥3 x Sn
≥2 x Sn
≥3 x Sn
non-flush
mountable sensor
flush
mountable sensor
Flush and non-ush mountable
In principle, “ush” and “non-ush” mounting are only of relevance in metal environments. All non-met-
als such as plastics, wood and glass have no inuence on the mounting.
With ush mountable sensors, the sensing face of the sensor may be aligned level with the metal
installation environment. Needless to say, these sensors can also be mounted in a non-ush manner.
Sensors which are non-ush mountable, on the other hand, must not be installed level with the sur-
rounding metal surface. The metallic installation environment would cancel out the sensor’s alternating
eld and cause the sensor to switch continuously.

d = diameter of the
sensing face
(details in data sheet)
Mutual inuence
In applications in which two inductive sensors must be installed opposite each other, they should be
spaced out at a distance of at least eight times that of the nominal sensing ranges. With series connec-
tion, the spacing between the units must be observed.
≥8 x Sn
8. Installation instructions for rectangular designs AI006-AI009, AI407, AI408
ush: AI006, AI008, AI407
h=any
non-ush: AI007, AI009, AI408

8
Align the sensing face
flush
non-flush
Sn = Nominal sensing range

Art. no. Mounting Sensing range /
frequency
Switching
output
Structural
shape
Connectors
AI006 Flush 20 mm / 100 Hz Normally open Cubic M12
AI007 Non-flush 35 mm / 80 Hz Normally open Cubic M12
AI008 Flush 20 mm / 100 Hz Antivalent Cubic M12
AI009 Non-flush 40 mm / 60 Hz Antivalent Cubic M12
AI050 Flush 2 mm / 5000 Hz Normally open M8 thread M8
AI051 Non-flush 4 mm / 5000 Hz Normally open M8 thread M8
AI052 Flush 2 mm / 5000 Hz Normally closed M8 thread M8
AI053 Non-flush 4 mm / 5000 Hz Normally closed M8 thread M8
AI054 Flush 4 mm / 2000 Hz Normally open M12 thread M12
AI055 Non-flush 8 mm / 2000 Hz Normally open M12 thread M12
AI056 Flush 4 mm / 2000 Hz Normally closed M12 thread M12
AI057 Non-flush 8 mm / 2000 Hz Normally closed M12 thread M12
AI058 Flush 8 mm / 2500 Hz Normally open M18 thread M12
AI059 Non-flush 12 mm / 2000 Hz Normally open M18 thread M12
AI060 Flush 8 mm / 2500 Hz Normally closed M18 thread M12
AI061 Non-flush 12 mm / 2000 Hz Normally closed M18 thread M12
AI062 Flush 15 mm / 200 Hz Normally open M30 thread M12
AI063 Non-flush 20 mm / 200 Hz Normally open M30 thread M12
AI064 Flush 15 mm / 200 Hz Normally closed M30 thread M12
AI065 Non-flush 20 mm / 200 Hz Normally closed M30 thread M12
9. Classication of inductive sensors
autosen inductive sensors - standard class
for standard applications & factory automation in the standard designs M8, M12, M18, M30 & cubic
Find a wealth of technical information, incl. engineering data and suitable genuine accessories, at:
autosen.com/standard-class

10
autosen inductive sensors - high resistance class
Can be used in machine tool manufacture, resistant to oils & coolants.
Find a wealth of technical information, incl. engineering data and suitable genuine accessories, at:
autosen.com/high-resistance
Art. no. Mounting Sensing range /
frequency
Switching
output Structural shape Connectors
AI001 Flush 2 mm / 800 Hz Normally open M8 thread M8
AI002 Flush 2 mm / 800 Hz Normally open M8 thread M12
AI003 Flush 4 mm / 700 Hz Normally open M12 thread M12
AI004 Flush 8 mm / 400 Hz Normally open M18 thread M12
AI005 Flush 15 mm / 100 Hz Normally open M30 thread M12
AI024 Flush 2 mm / 1300 Hz Normally closed M8 thread M8
AI025 Flush 4 mm / 700 Hz Normally closed M12 thread M12
AI026 Flush 8 mm / 400 Hz Normally closed M18 thread M12
AI027 Flush 15 mm / 100 Hz Normally closed M30 thread M12
AI034 Flush 2 mm / 800 Hz Normally open Ø 6.5mm, smooth M8
AI035 Non-flush 4 mm / 700 Hz Normally open Ø 6.5mm, smooth M8
AI038 Flush 4 mm / 700 Hz Normally open M12 thread M12
Art. no. Mounting Sensing range /
frequency
Switching
output
Structural shape Cable
AI901 Flush 2 mm / 5 kHz Normally open M8 thread 5 m cable
AI902 Non-flush 4 mm / 5 kHz Normally open M8 thread 5 m cable
AI903 Flush 2 mm / 5 kHz Normally closed M8 thread 5 m cable
AI904 Non-flush 4 mm / 5 kHz Normally closed M8 thread 5 m cable
AI905 Flush 4 mm / 5 kHz Normally open M12 thread 5 m cable
AI906 Non-flush 8 mm / 5 kHz Normally open M12 thread 5 m cable
AI907 Flush 4 mm / 5 kHz Normally closed M12 thread 5 m cable
AI908 Non-flush 8 mm / 5 kHz Normally closed M12 thread 5 m cable

autosen inductive sensors - full-metal housing
Have protection rating IP 67, IP 68, IP 69 K and are up to 100 °C and 100 bar temperature & pressure
resistant.
Find a wealth of technical information, incl. engineering data and suitable genuine accessories, at:
autosen.com/ganzmetall-sensoren
Art. no. Mounting Sensing range /
frequency
Switching
output Structural shape Connectors
AI039 Non-flush 7 mm / 700 Hz Normally open M12 thread M12
AI040 Flush 4 mm / 700 Hz Normally closed M12 thread M12
AI041 Non-flush 7 mm / 700 Hz Normally closed M12 thread M12
AI042 Flush 8 mm / 400 Hz Normally open M18 thread M12
AI043 Non-flush 12 mm / 300 Hz Normally open M18 thread M12
AI044 Flush 8 mm / 400 Hz Normally closed M18 thread M12
AI045 Non-flush 12 mm / 300 Hz Normally closed M18 thread M12
AI046 Flush 15 mm / 100 Hz Normally open M30 thread M12
AI047 Non-flush 22 mm / 100 Hz Normally open M30 thread M12
AI048 Flush 15 mm / 100 Hz Normally closed M30 thread M12
AI049 Non-flush 22 mm / 100 Hz Normally closed M30 thread M12
Art. no. Mounting Sensing range /
frequency
Output Structural shape Connectors
AI016 Flush 3 mm / 100 Hz Normally open M12 thread M12
AI017 Non-flush 6 mm / 500 Hz Normally open M12 thread M12
AI018 Flush 5 mm / 100 Hz Normally open M18 thread M12
AI019 Non-flush 12 mm / 500 Hz Normally open M18 thread M12
AI020 Flush 10 mm / 50 Hz Normally open M30 thread M12
AI021 Non-flush 25 mm / 250 Hz Normally open M30 thread M12

12
autosen inductive sensors - miniature sensors
Inductive sensors with a short overall length and small diameters up to 3 mm are also used in very
conned conditions. This makes them the ideal solution for robotics, mounting and handling technolo-
gy. These sensors achieve switching frequencies of up to 7000 Hz across a high temperature range.
Find a wealth of technical information, incl. engineering data and suitable genuine accessories, at:
autosen.com/miniatursensoren
Art. no. Flush/Non-flush Sensing range /
frequency
Output Structural shape Cable
AI801 Flush 0.6 mm / 3000 Hz Normally open Ø3mm, smooth 2 m cable
AI802 Non-flush 1 mm / 3000 Hz Normally open Ø3mm, smooth 2 m cable
AI803 Flush 0.6 mm / 3000 Hz Normally closed Ø3mm, smooth 2 m cable
AI804 Non-flush 1 mm / 3000 Hz Normally closed Ø3mm, smooth 2 m cable
AI805 Flush 0.8 mm / 5000 Hz Normally open Ø4mm, smooth 2 m cable
AI806 Non-flush 1.5 mm / 5000 Hz Normally open Ø4mm, smooth 2 m cable
AI807 Flush 0.8 mm / 5000 Hz Normally closed Ø4mm, smooth 2 m cable
AI808 Non-flush 1.5 mm / 5000 Hz Normally closed Ø4mm, smooth 2 m cable
AI809 Flush 0.8 mm / 5000 Hz Normally open M5 thread 2 m cable
AI810 Non-flush 1.5 mm / 5000 Hz Normally open M5 thread 2 m cable
AI811 Flush 0.8 mm / 5000 Hz Normally closed M5 thread 2 m cable
AI812 Non-flush 1.5 mm / 5000 Hz Normally closed M5 thread 2 m cable
AI813 Flush 1.5 mm / 7000 Hz Normally open Ø6.5mm, smooth 2 m cable
AI814 Non-flush 2 mm / 7000 Hz Normally open Ø6.5mm, smooth 2 m cable
AI815 Flush 1.5 mm / 7000 Hz Normally closed Ø6.5mm, smooth 2 m cable
AI816 Non-flush 2 mm / 7000 Hz Normally closed Ø6.5mm, smooth 2 m cable

Art. no. Flush/Non-flush Sensing range /
frequency
Output Structural
shape
Connectors
AI028 Flush 4 mm / 2000 Hz Normally open M12 thread M12
AI029 Non-flush 10 mm / 2000 Hz Normally open M12 thread M12
AI030 Flush 8 mm / 2000 Hz Normally open M18 thread M12
AI031 Non-flush 15 mm / 2000 Hz Normally open M18 thread M12
AI032 Flush 15 mm / 2000 Hz Normally open M30 thread M12
AI033 Non-flush 30 mm / 2000 Hz Normally open M30 thread M12
AI036 Flush 3 mm / 2000 Hz Normally open M8 thread M8
AI037 Non-flush 6 mm / 2000 Hz Normally open M8 thread M8
autosen inductive sensors - Factor 1
Have protection rating IP 67, IP 68, IP 69 K, are magnetic-eld immune and detect all metals with the
same sensing range (correction factor = 1).
A transmitter and receiver coil system on a circuit board forms a transformer.
Electrically conductive materials in the near eld inuence the coupling factor of the transformer.
The change of the coupling factor is used by downstream electronics for a switching signal.
By omitting the ferrite core, the inductive F1 sensors are less sensitive to interference from strong
magnetic elds.
Find a wealth of technical information, incl. engineering data and suitable genuine accessories, at:
autosen.com/faktor1
1: Connection
2: Housing
3: Downstream electronics
4: Circuit board with transmitter and receiver coil
5: Alternating electromagnetic eld = active face
6: Target = electrically conductive material

14
autosen inductive sensors with IO-Link
Enable a reliable transmission of the distance as a linearised process value using IO-Link. The normal-
ly closed / normally open functions and PNP/NPN can be adjusted via IO-Link.
Representation of the process value with measuring range and adjustment range for
frontal damping
500
1000
1500
2000
2500
3000
3500
4095
8184
3800
400
-8184
3
4
6
7
5
1
2
[mm]
① ⑤
② ⑥
③ ⑦
④
Process data value
Adjustment range PDV (ProcessDataVariable)
Near range
Adjustment range
Distance to sensing face
LED IO-Link
LED SIO (on delivery)

SP1
4095
SP1+H
SP1
H
ON OFF
0
teach
PDV
SSC
SP1
4095
SP1+H
SP1
H
0
teach
PDV
SSC
ONOFF
Switch point denition IO-Link
Switch-on point
SP1
SP1 + H Switch-on point
Switch-off point
Switch-off point
Normally closed (switch point logic = 1)
Normally open (switch point logic = 0)
Single point mode (presence detection) to smart sensor prole 2
SP1
SP1 + H

16
SP2
SP2
SP2-H
H
OFF
0
teach
SSC
SP1
4095
SP1+H
SP1
H
teach
PDV
ON OFF
SP2
SP2
SP2-H
H
ON
0
teach
SSC
SP1
4095
SP1+H
SP1
H
teach
PDV
OFF ON
Switch-on point
Switch-on point
Switch-on point
Switch-on point
SP1
SP1
SP2
SP2
SP1 + H
SP1 + H
SP2 - H
SP2 - H
Switch-off point
Switch-off point
Switch-off point
Switch-off point
Normally closed (switch point logic = 1)
Normally open (switch point logic = 0)
Window mode (presence detection) to smart sensor prole 2

SP2
4095
SP1
SP2
H
ON
0
teach
PDV
SSC
SP1
OFF
SP2
4095
SP1
SP2
H
NOFFO
0
teach
PDV
SSC
SP1
SP
H
SSC
PDV
Switch-on point
Switch-on point
SP1
SP1
SP2
SP2
Switch-off point
Condition:
Switch point
Hysteresis
Switching signal channel
Process data variable
SP1 > SP2 + 3% and SP1 between 400 and 3800 and SP2 between 388 and 3686
Switch-off point
Normally closed (switch point logic = 1)
Normally open (switch point logic = 0)
Two point mode (presence detection) to smart sensor prole 2

18
Art. no. Flush/
Non-flush
Sensing range /
frequency
Output Connec-
tors
Structural shape
AI401 Flush 0.375...3.75 mm / 600 Hz NO/NC prog. M12 M12 thread
AI402 Non-flush 0.7...7 mm / 600 Hz NO/NC prog. M12 M12 thread
AI403 Flush 0.75...7.5 mm / 300 Hz NO/NC prog. M12 M18 thread
AI404 Non-flush 1.3...13 mm / 300 Hz NO/NC prog. M12 M18 thread
AI405 Flush 1.3...13 mm / 100 Hz NO/NC prog. M12 M30 thread
AI406 Non-flush 2.3...23 mm / 100 Hz NO/NC prog. M12 M30 thread
AI407 Flush 2.1...21 mm / 100 Hz NO/NC prog. M12 cubic design
AI408 Non-flush 2.6...26 mm / 100 Hz NO/NC prog. M12 cubic design
autosen inductive sensors with IO-Link
Inductive sensors with IO-Link interface and protection rating IP 65; IP 66; IP 67; IP 68; IP 69K.
Find a wealth of technical information, incl. engineering data and suitable genuine accessories, at:
autosen.com/induktive-IO-Link

10. General information on connection systems
Series connection (AND) Parallel connection (OR)
11. Conguration of cables and connectors
3-wire series connection
Max. 4 units Power-on delay times, voltage
drops and current consumption add up. UB
min (sensor) and UHIGH min (load) must
remain unchanged.
2. negative switching / 3. positive switching / 4. sensor 1 / 5. sensor n
Colour coding:
BK: black, BN brown, BU: blue, WH: white
3-wire parallel connection
The current consumption of all non-switched
units adds up. The units can be used in
combination with mechanical switches.
3-wire technology
(negative or positive
switching)
4-wire technology
(positive switching, normally closed
and normally open)

20 www.autosen.com
Technical data and further information at:
We reserve the right to make technical changes without prior notice.
This manual suits for next models
71
Other autosen Accessories manuals
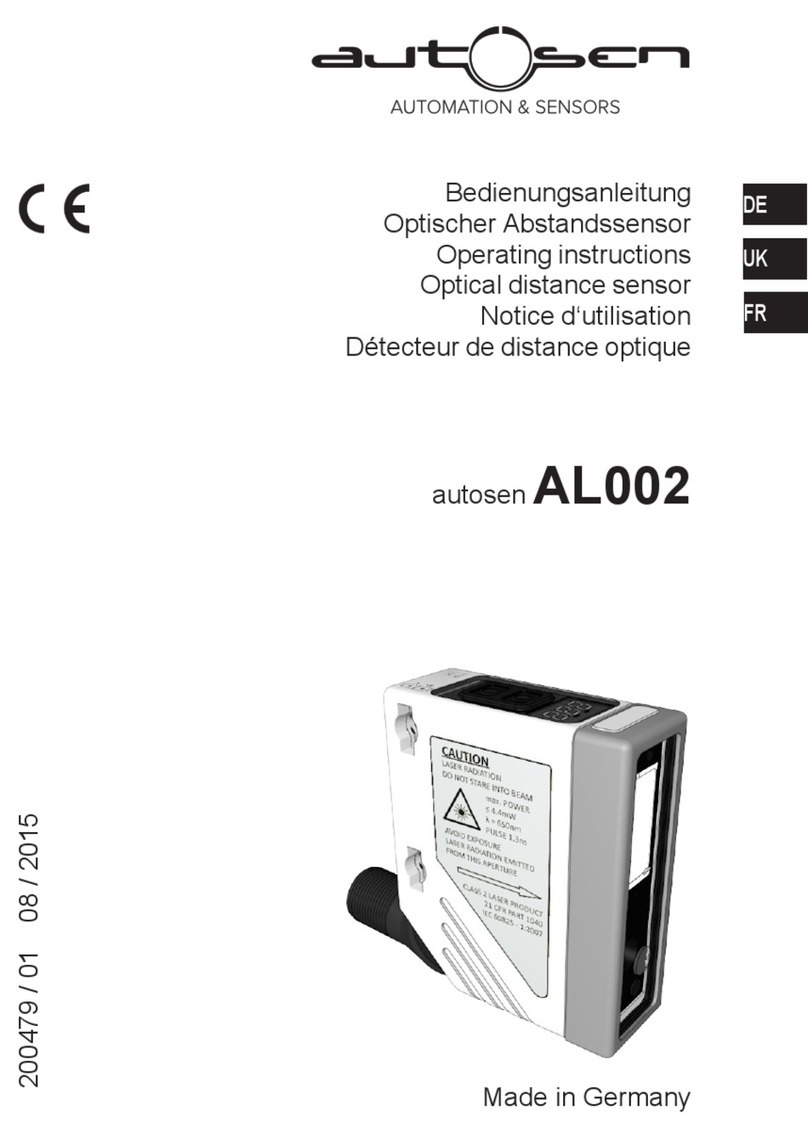
autosen
autosen AL002 User manual

autosen
autosen AU001 User manual
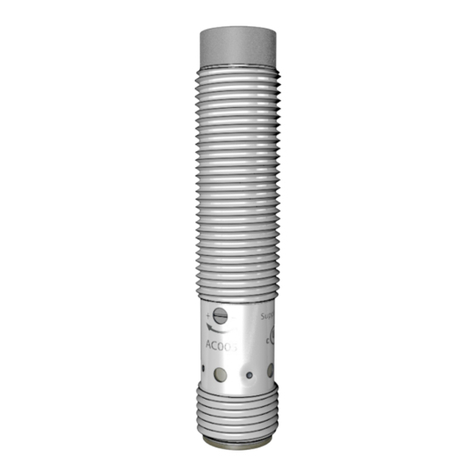
autosen
autosen AC005 User manual

autosen
autosen AL004 User manual

autosen
autosen AL005 User manual
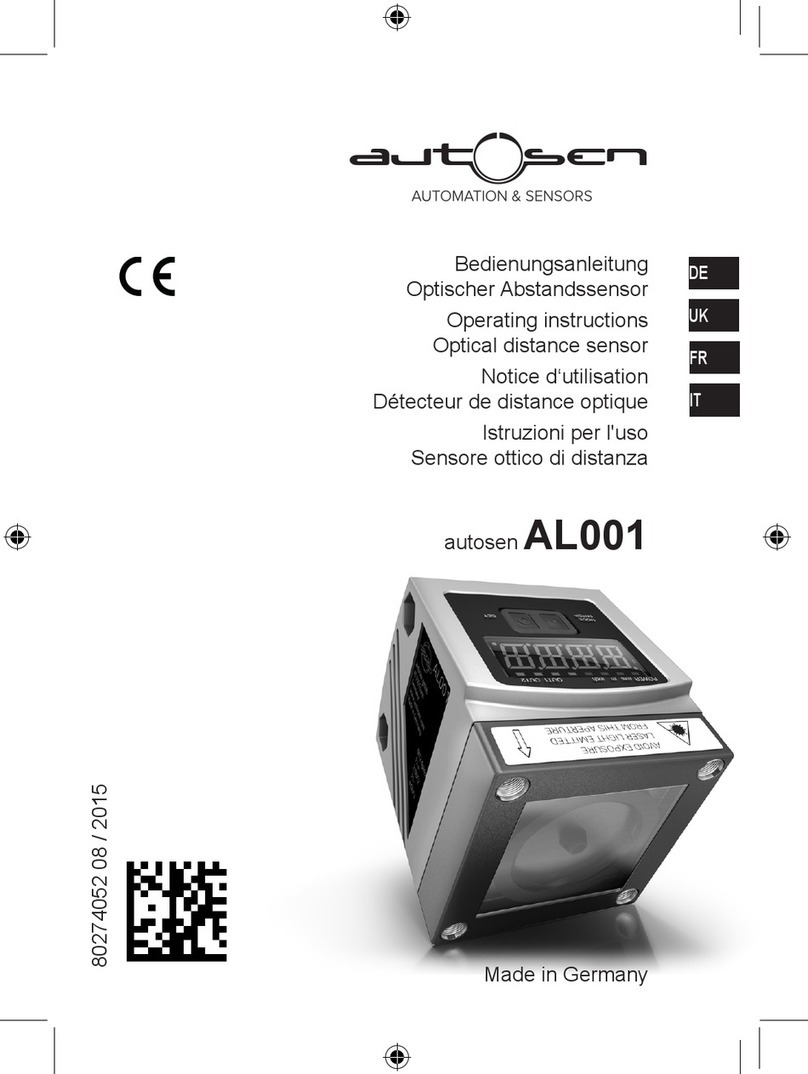
autosen
autosen AL001 User manual
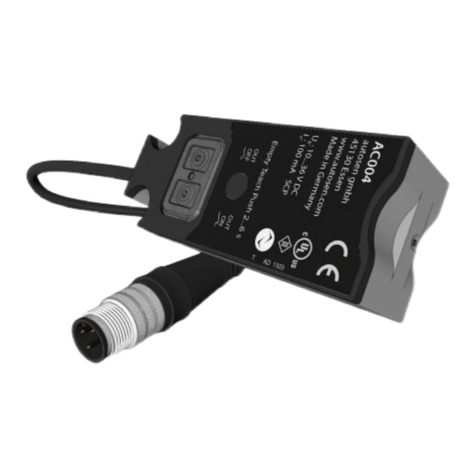
autosen
autosen AC004 Manual

autosen
autosen AU011 User manual

autosen
autosen AL006 User manual
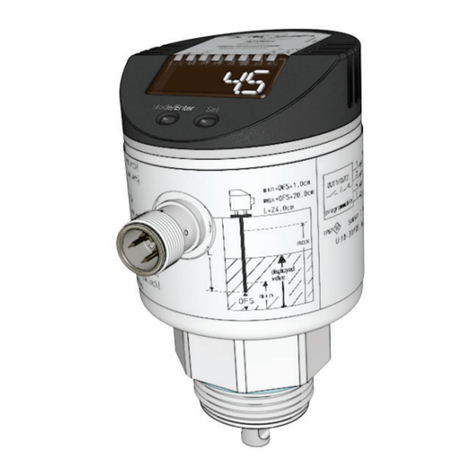
autosen
autosen AF003 User manual
Popular Accessories manuals by other brands
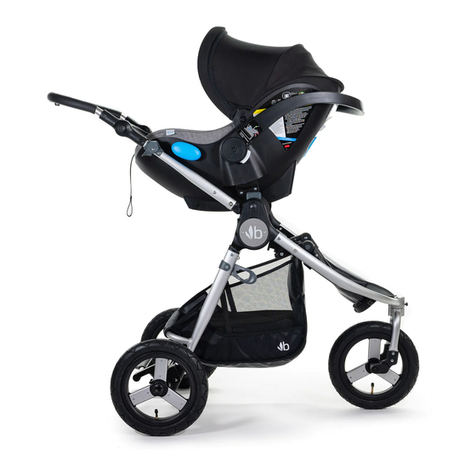
Bumbleride
Bumbleride Indie & Speed Car Seat Adapter owner's manual

Vaisala
Vaisala WINDCAP WMT700 Series user guide
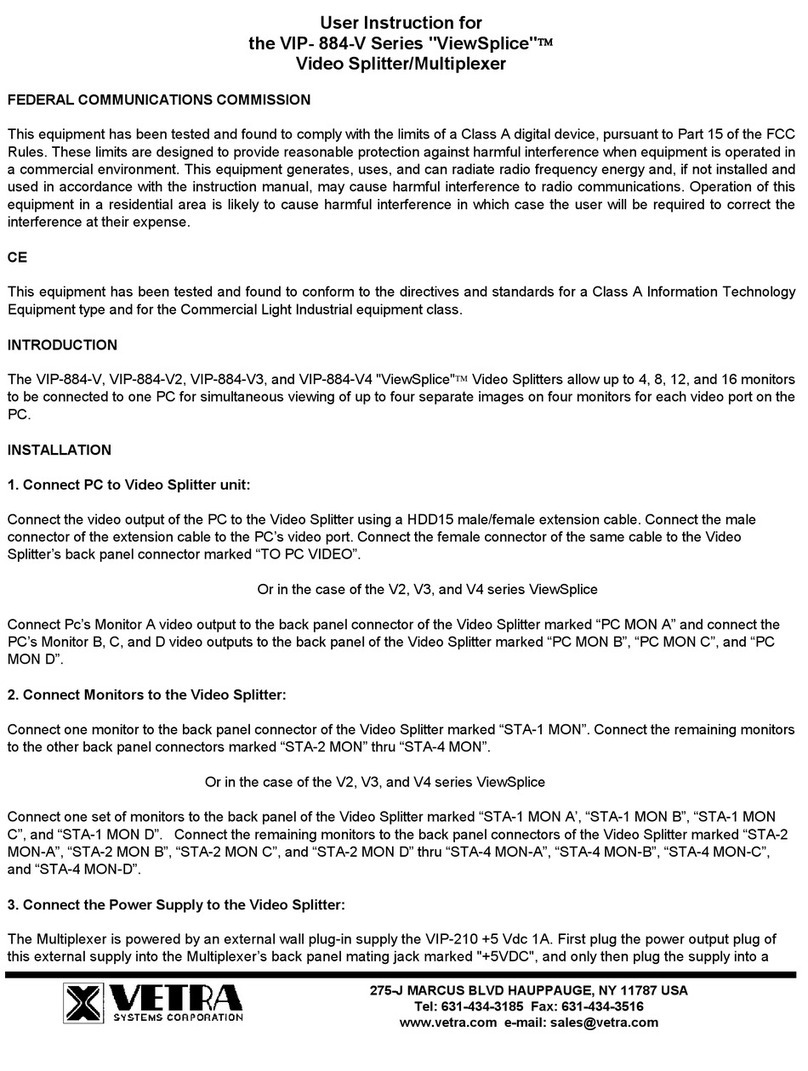
Vetra
Vetra ViewSplice VIP- 884-V Series User instruction
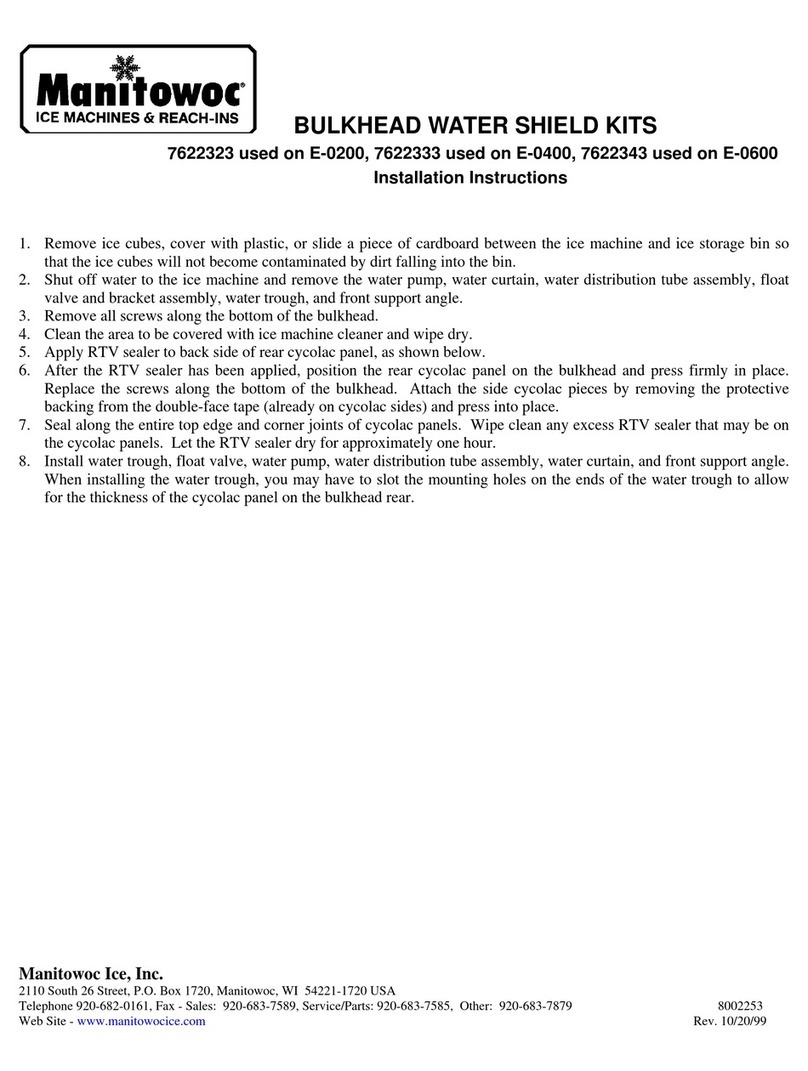
Manitowoc
Manitowoc 7622323 installation instructions
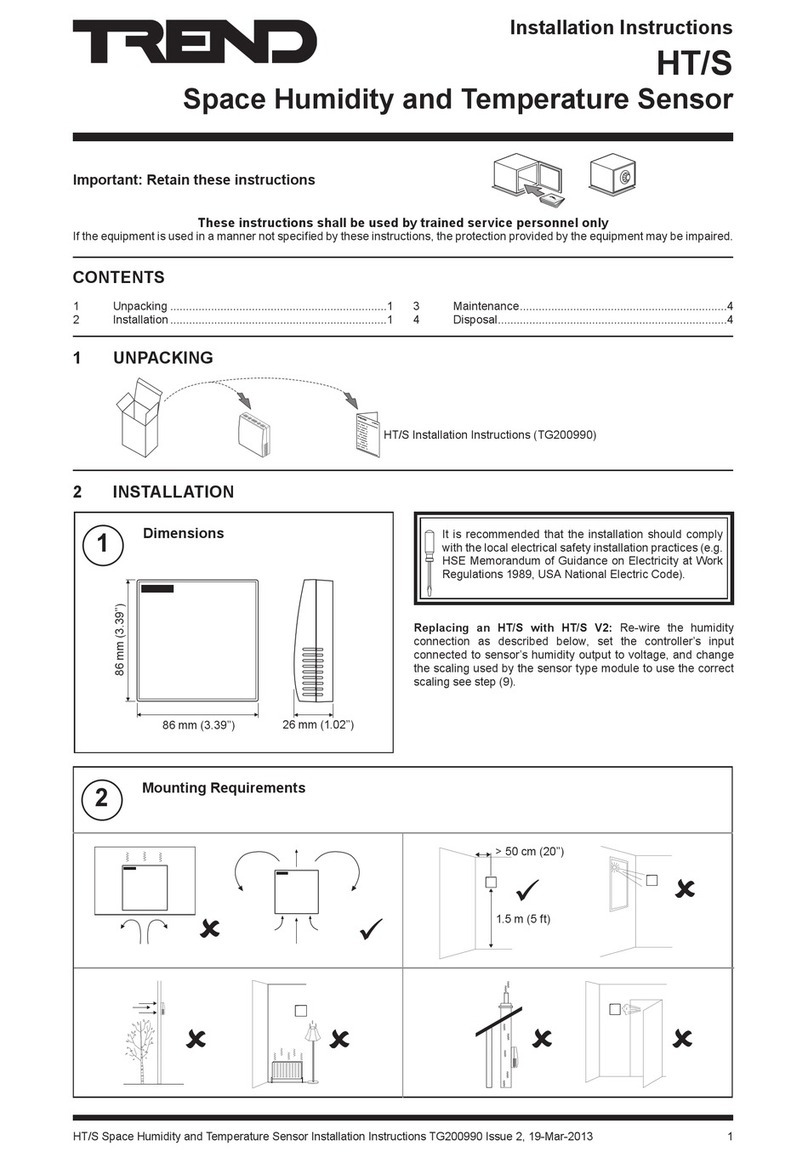
TREND
TREND HT/S installation instructions

COUGAR
COUGAR POSEIDON LT ARGB 240 user manual