BEKA BA507E-SS User manual

Issue: 2
4th May 2017
BA507E-SS & BA527E-SS
Rugged general purpose
loop-powered
panel mounting indicators
Issue 2

1. Description
2. Operation
2.1 Controls
3. Applications
3.1 Transmitter loops
3.2 Remote indication
4. Installation
4.1 Location
4.2 Installation procedure
4.3 Indicator earthing
4.4 EMC
4.5 Scale card
5. Configuration and Calibration
5.1 Summary of configuration
functions.
5.2 Indicator function
5.3 Resolution
5.4 Position of decimal point
5.5 Calibration using an external
current source.
5.6 Calibration using internal
reference.
5.7 Bargraph format and calibration
5.8 Function of the Ppush button
5.9 Tare function
5.10 Security code
5.11 Reset to factory defaults
5.12 Under and over-range
6. Lineariser
6.1 Lineariser calibration using an external
current source.
6.1.1 Example, adding break-points
to a new indicator.
6.2 Lineariser calibration using internal
reference.
6.2.1 Example, adding break-points
to a new indicator.
6.3 Under and over-range
6.4 Lineariser default configuration
7. Maintenance
7.1 Fault finding during commissioning
7.2 Fault finding after commissioning
7.3 Servicing
7.4 Routine maintenance
7.5 Guarantee
7.6 Customer comments
8. Accessories
8.1 Scale card
8.2 Tag information
8.3 Alarms
8.3.1 Solid state output
8.3.2 Configuration and adjustment.
8.3.3 Alarm enable
8.3.4 Setpoint adjustment
8.3.5 Alarm function
8.3.6 Alarm output status
8.3.7 Hysteresis
8.3.8 Alarm delay
8.3.9 Alarm silence time
8.3.10 Flash display when alarm
occurs.
8.3.11 Access setpoint in display
mode.
8.3.12 Adjusting alarm setpoints from
the display mode.
8.3.13 Displaying setpoints on
bargraph.
8.4 Display backlight
8.4.1 Loop powering the backlight
8.4.2 Separately powering the
backlight.
2222222222222222222222222222222222222222222222222
CONTENTS
The BA507E-SS & BA527E-SS are CE marked to show compliance with the European EMC Directive 2004/108/EC

1. DESCRIPTION
These rugged panel mounting, general purpose digital
indicators display the current flowing in a 4/20mA loop
in engineering units. They are loop powered but only
introduce a 1.2V drop which allows them to be
installed into almost any 4/20mA current loop. No
additional power supply or battery is required.
The two models are electrically similar, but have
different displays.
Model Display
BA507E-SS 4 digits 15mm high
BA527E-SS 5 digits 11mm high
and 31 segment bargraph.
This instruction manual supplements the instruction
sheet supplied with each instrument.
The main application of both models is to display a
measured variable or control signal in a process area.
The indicators have a rugged stainless steel case with
IP66 front of panel ingress and impact protection
allowing them to be installed in environments where
they are liable to be impacted. The zero and span of
the display are independently adjustable so that the
indicator can be calibrated to display any variable
represented by the 4/20mA input current, e.g.
temperature, flow, pressure or level.
2. OPERATION
Fig 1 shows a simplified block diagram of both
models. The 4/20mA input current flows through
resistor R1 and forward biased diode D1. The
voltage developed across D1, which is relatively
constant, is multiplied by a switch mode power
supply and used to power the instrument. The
voltage developed across R1, which is proportional
to the 4/20mA input current, provides the input
signal for the analogue to digital converter.
Each time a 4/20mA current is applied to the
instrument, initialisation is performed during which
all segments of the display are activated, after five
seconds the instrument displays the input current
using the calibration information stored in the
instrument memory. If the loop current is too low
to power the instrument the indicator will display
the error message ‘LPLo’.
Fig 1 Indicator block diagram
3

2.1 Controls
The indicators are controlled and calibrated via four
front panel push buttons located below the display.
In the display mode i.e. when the indicator is
displaying a process variable, these push buttons
have the following functions:
PWhile this button is pushed the indicator
will display the input current in mA, or as a
percentage of the instrument span
depending upon how the indicator has
been configured. When the button is
released the normal display in engineering
units will return. The function of this push
button is modified when optional alarms
are fitted to the indicator.
▼While this button is pushed the indicator
will display the numerical value and
analogue bargraph* the indicator has been
calibrated to display with a 4mAΦinput.
When released the normal display in
engineering units will return.
▲While this button is pushed the indicator
will display the numerical value and
analogue bargraph* the indicator has been
calibrated to display with a 20mAΦinput.
When released the normal display in
engineering units will return.
ENo function in the display mode unless the
tare function is being used.
P + ▼Firmware number followed by version.
P + ▲Direct access to the alarm setpoints when
optional alarms are fitted to the indicator
and the ‘ACSP’ access setpoints in display
mode function has been enabled.
P + E Access to configuration menu via optional
security code.
Note: * BA527E-SS only
ΦIf the indicator has been calibrated
using the CAL function, calibration
points may not be 4 and 20mA.
3. APPLICATIONS
3.1 Transmitter loops
Both models may be connected in series with any
4/20mA current loop and calibrated to display the
measured variable or control signal in engineering
units.
Figs 2 illustrate a typical application in which an
indicator is connected in series with a 2-wire
transmitter.
Fig 2 Indicator in a transmitter loop
Considering the example shown in Fig 2, the sum
of the maximum voltage drops of all the
components in the loop must be less than the
minimum power supply voltage.
Minimum operating voltage of 2-wire Tx 10.0
Maximum voltage drop caused by controller 5.0
Maximum voltage drop caused by BA507E-SS 1.3
Maximum voltage caused by cables 0.4
_____
16.7V
Therefore in this example the power supply must
have a minimum output of 16.7V at 20mA.
3.2 Remote indication
Both indicators may be driven from a 4/20mA
signal to provide a remote indication. Fig 3 shows
a typical application in which the 4/20mA output
from a gas analyser is connected to a BA507E-SS
loop powered indicator to provide a remote
indication of the analyser’s output. Again it is
necessary to ensure that the voltage capability of
the 4/20mA source is greater than the sum of the
voltage drops introduced by the indicator and the
cable resistance.
4

Fig 3 Indicator providing a remote display
4. INSTALLATION
4.1 Location
Both indicators have a robust stainless steel case with
a 10mm thick toughened glass window. The case
provides 7J and the window 4J front of panel impact
protection. The captive silicone gasket, which seals
the joint between the instrument and the panel
enclosure, ensures IP66 front of panel ingress
protection. Both indicators have IP20 rear protection.
Although the front of the indicators have IP66
protection, they should be shielded from continuous
direct sunlight and severe weather conditions.
The BA507E-SS and BA527E-SS may be located in
any panel providing that the operating temperature is
between –40°C and +70°C. For most industrial
applications the rear of the panel enclosure in which
the indicator is mounted should provide additional
protection to prevent the ingress of moisture into the
rear of the instrument.
4.2 Installation Procedure
a. Cut the aperture specified in Fig 4 in the panel
enclosure. Ensure that the edges of aperture
are de-burred.
b. Inspect the indicator's captive gasket and
ensure that it is not damaged before inserting
the indicator into the panel enclosure aperture.
c. If the enclosure panel is less than 1.0mm thick,
or is non-metallic, an optional BEKA stainless
steel support plate should be slid over the rear
of the indicator before the panel clamps are
fitted to evenly distribute the clamping force and
prevent the enclosure panel being distorted or
creeping.
d. Slide a panel clamp into the two grooves at
each corner of the indicator housing with the
M3 stud protruding through the hole at the
rear of the clamp. Fit the stainless steel spring
washer over the stud and secure with the
stainless steel wing nut.
Fig 4 Dimensions
e. Evenly tighten the four clamps to secure the
instrument. The recommended minimum
tightening torque for each wing nut is 22cNm
(1.95 lbf in).
f. Connect the panel enclosure wiring to the
rear terminal blocks. To simplify installation,
the terminals are removable so that wiring
can be completed before the instrument is
installed.
g. Finally, fit a silicone rubber push-on cap to
the end of each M3 threaded rod.
Fig 4 show the overall dimensions of the indicators
together with the recommended panel enclosure
cut-out dimensions.
5

Fig 5 Installation procedure
4.3 Indicator earthing
Both indicators have an M4 earth stud on the rear
panel which should be electrically connected to the
panel enclosure in which the indicator is mounted, or
to the plant equipotential conductor.
4.4 EMC
Both instruments comply with the requirements of the
European EMC Directive 2004/108/EC. For specified
immunity all wiring should be in screened twisted
pairs, with the screens earthed in the safe area.
Fig 6 Rear terminals
4.5 Scale card
The indicator’s units of measurement are shown
on a printed scale card in a window at the right
hand side of the display. The scale card is
mounted on a flexible strip that is inserted into a
slot at the rear of the instrument as shown in Fig 7.
Thus the scale card can easily be changed without
dismantling the indicator or removing it from the
panel enclosure in which it is mounted.
New indicators are supplied with a printed scale
card showing the requested units of measurement,
if this information is not supplied when the indicator
is ordered a blank card will be fitted.
A pack of self-adhesive scale cards printed with
common units of measurement is available as an
accessory from BEKA associates. Custom printed
scale cards can also be supplied.
To change a scale card, unclip the protruding end
of the flexible strip by gently pushing it upwards
and pulling it out of the rear panel of the indicator.
Peel the existing scale card from the flexible strip
and replace it with a new printed card, which
should be aligned as shown in Fig 7. Do not fit a
new scale card on top of an existing card.
Install the new scale card by gently pushing the
flexible strip into the slot at the rear of the indicator,
when it reaches the internal end-stop secure it by
pushing the end of the flexible strip downwards so
that the tapered section is held by the rear panel of
the indicator.
6

Align the self-adhesive printed
scale card onto the flexible strip
and insert the strip into the
indicator as shown below.
Fig 7 Inserting flexible strip carrying scale card
into slot at the rear of indicator.
7

5. CONFIGURATION AND CALIBRATION
Indicators are configured and calibrated via the four
front panel push-buttons. All the configuration
functions are contained in an easy to use intuitive
menu that is shown diagrammatically in Fig 8.
Each menu function is summarised in section 5.1 and
includes a reference to more detailed information.
When the indicator is fitted with alarms additional
functions are added to the menu which are described
in section 8.3
Throughout this manual push buttons are shown as P,
E,▼or ▲, and legends displayed by the indicator
are shown within inverted commas e.g. 'CAL' and '
ALr2'.
Access to the configuration menu is obtained by
operating the Pand Epush buttons simultaneously. If
the indicator security code is set to the default 0000
the first parameter 'FunC' will be displayed. If a
security code other than the default code 0000 has
already been entered, the indicator will display 'CodE'.
Pressing the Pbutton will clear this prompt allowing
each digit of the code to be entered using the ▲and
▼push buttons and the Pbutton to move control to
the next digit. When the correct four digit code has
been entered pressing Ewill cause the first parameter
'FunC' to be displayed. If the code is incorrect, or a
button is not pressed within twenty seconds, the
indicator will automatically return to the display mode.
Once within the configuration menu the required
parameter can be reached by scrolling through the
menu using the ▲and ▼push buttons as shown in
Fig 8. When returning to the display mode following
recalibration or a change to any function, the indicator
will display ‘dAtA’ followed by ‘SAVE’ while the new
information is stored in non-volatile memory.
All new indicators are supplied calibrated as
requested at the time of ordering. If calibration is not
requested, indicators will be configured as follows:
BA507E-SS BA527E-SS
Access code ‘CodE’ 0000 0000
Function ‘FunC’ Std Std
Display at 4mA ‘Zero’ 0.0 0.00
Display at 20mA ‘SPAn’ 100.0 100.00
Resolution ‘rESn’ 1 digit 1 digit
Bargraph start ‘BarLo’ ----- 0.00
Bargraph finish ‘BarHi’ ----- 100.00
Pbutton in display mode ‘C—P’ % %
Tare ‘tArE’ Off Off
Default configuration can easily be changed on-site.
5.1 Summary of configuration functions
This section summarises each of the main
configuration functions and includes a cross
reference to a more detailed description. Fig 8
illustrates the location of each function within the
configuration menu. The lineariser and the
optional factory fitted alarms are described
separately in sections 6 and 8.3 of this manual.
Display Summary of function
'FunC' Indicator function
Defines the relationship between the
4/20mA input current and the indicator
display. May be set to:
‘Std’ Standard linear relationship
‘root’ Square root extraction
‘Lin’ 16 segment adjustable
lineariser – see section 5.
See section 5.2
'rESn' Display resolution
Defines the resolution of the least
significant display digit. May be set to
‘1’, ‘2’, ‘5’ or ‘10’ digits.
See section 5.3
'dP' Decimal point
Positions a dummy decimal point
between any of the digits or turns it off.
See section 5.4
'CAL' Calibration of the digital display
using an external current source.
Enables the zero and span of the
indicator to be adjusted using an
external current source such as a
calibrator. When used with an accurate
traceable current source this is the
preferred method of calibration.
See section 5.5
'SEt' Calibration of display using internal
references.
Enables the zero and span of the
indicator to be adjusted without the
need for an accurate input current or
disconnection from the 4/20mA loop.
See section 5.6
'bAr' Bargraph format and calibration
Only the BA327E -SS has a bargraph
The bargraph may be conditioned to
start from left, right or centre of the
display, or it may be disabled. When
optional alarms are fitted it can also
display both alarm setpoints and the
measured value.
The bargraph may be calibrated to start
and finish at any value within the
indicator’s calibrated digital display.
See section 5.7
8

9

Display Summary of function
'C - - P' Function of P push-button
The indicator may be configured to display
the input current in milliamps, or the input
current as a percentage of the 4/20mA
input when the Ppush button is operated
in the display mode.
See section 5.8
'tArE' Tare function
When enabled the tare function sets the
indicator display to zero when the Epush
button is operated in the display mode.
See section 5.9
'CodE' Security code
Defines a four digit numeric code that must
be entered to gain access to the
configuration menu. Default code 0000
disables this security function and allows
unrestricted access to all conditioning
functions.
See section 5.10
'rSEt' Reset
Contains two sub-functions, ‘ConF’ which
returns the indicator to the default
conditions and ‘LtAb’ which returns the
lineariser to the default conditions. To
prevent accidental use both resets must
be confirmed by entering ‘5urE’ before
they will be executed.
See section 5.11
5.2 Indicator function: ‘FunC’
This configuration function defines the relationship
between the indicator’s 4/20mA input current and
the indicator’s display. Three alternatives are
available:
‘Std’ Standard linear relationship
‘root’ Square root extraction
‘Lin’ 16 segment adjustable
lineariser.
To reveal the existing indicator function select
'FunC' from the configuration menu and press P.
If the function is set as required, press Eto return
to the menu, or press the ▲or ▼button to change
the setting, followed by the Ebutton to return to the
configuration menu.
‘Std’ Linear
Provides a linear relationship between the
4/20mA indicator input current and the
indicator display.
‘root’ Square root extraction
Primarily intended to linearise the square
law 4/20mA output from differential
flowmeters.
For reference, the following table shows
the output current from a non-linearised
differential flowmeter.
% of full flow Current output mA
2.5 4.01
10.0 4.16
25.0 5.00
50.0 8.00
75.0 13.00
100.0 20.00
When the root function is selected the
indicator will display flow in linear units.
‘Lin’ 16 segment adjustable lineariser
Enables non linear variables to be
displayed by the indicator in linear
engineering units. Use of the lineariser is
described in section 6 of this instruction
manual.
5.3 Resolution: rESn
This function defines the resolution of the least
significant display digit. Decreasing the display
resolution can improve the readability of a noisy
signal. Select ''rESn' from the menu and press P
which will reveal the current display resolution. To
change the resolution press the ▲or ▼button to
select 1, 2, 5 or 10 digits, followed by the Ebutton
to enter the selection and return to the
configuration menu.
10

5.4 Position of the decimal point: ‘dP’
A dummy decimal point can be positioned between
any of the digits or it may be absent. To position the
decimal point select 'dP' from the menu and press P.
The decimal point can be moved by pressing the ▲or
▼push button. If a decimal point is not required it
should be positioned beyond the most or least
significant digit. When positioned as required press
the Ebutton to enter the selection and return to the
configuration menu.
5.5 Calibration using an external
current source: ‘CAL’
This function enables the zero and span of the
indicator to be adjusted using an external calibrated
current source. When used with an accurate
traceable current source this is the preferred method
of calibration.
Zero is the indicator display with 4mA input
Span is the indicator display with 20mA input
To calibrate the indicator select 'CAL' from the
configuration menu and press P.The indicator will
display 'ZEro' which is a request for a 4mA input
current. Adjust the external current calibrator to
4.000mA and again press Pwhich will reveal the
current zero display. The flashing digit of the
indicator display can be changed by pressing the ▲or
▼buttons, when set as required pressing Pwill
transfer control to the next digit. When all the digits
have been adjusted, press Eto enter the new zero
and return to the 'ZEro' prompt.
Pressing the ▲button will cause the indicator to
display 'SPAn' which is a request for a 20mA input
current. Adjust the external current calibrator to
20.000mA and again press Pwhich will reveal the
existing span display. The flashing digit of the
indicator display can be changed by pressing the ▲or
▼buttons, when set s required pressing Pwill
transfer control to the next digit. When all the digits
have been adjusted press Eto enter the new span
and return to the 'SPAn' prompt. Finally press Eagain
to return to the configuration menu.
Notes:
a. The indicator input current must be adjusted to the
required value before the zero and span functions
are entered by pressing the P button.
b. Indicators may be calibrated at currents other than
4 and 20mA, withiin the range 3.8 to 21.0mA
providing the difference between the two currents
is greater than 4mA. If these conditions are not
complied with, the indicator displays ‘FaiL’ and
aborts the calibration.
c. If the zero current is greater than the span current
the instrument will be reverse acting i.e. an
increasing input current will cause the display to
decrease.
5.6 Calibration using internal reference: ‘SEt’
Using the ‘SEt’ function the indicator can be
calibrated without the need for an accurate
external current source and without the need to
disconnect the indicator from the 4/20mA
measuring loop.
The indicator’s internal reference is used to
simulate a 4mA and 20mA input current, so the
actual indicator input input current does not have
to be known during calibration.
Zero is the display with a simulated 4mA input
Span is the idisplay with a simulated 20mA input
To calibrate the indicator display select 'SEt' from
the configuration menu and press P. The indicator
will display 'ZEro', pressing Pagain will reveal the
current display at 4mA. The flashing digit can be
adjusted by pressing the ▲or ▼buttons, when
the flashing digit is correct pressing Pwill transfer
control to the next digit. When all the digits have
been adjusted, press Eto return to the 'ZEro'
prompt.
To adjust the display at 20mA, press the ▲button
which will cause the indicator to display 'SPAn',
pressing Pwill then reveal the indicator’s existing
display at 20mA. The flashing digit can be
adjusted by pressing the ▲or ▼buttons, when
the flashing digit is correct pressing Pwill transfer
control to the next digit. When all the digits have
been adjusted press Eto return to the 'SPAn'
prompt followed by Eto return to the ‘SEt’ prompt
in the configuration menu.
5.7 Bargraph format and calibration: ‘bAr’
Only the BA527E-SS has a bargraph
In addition to a five digit numerical display the
BA527E-SS has a 31 segment analogue bargraph
which may be configured to start and finish
anywhere within the indicators numerical display
range.
To configure the bargraph select 'bAr' from the
configuration menu and press P. The indicator will
display 'tYPE', pressing Pagain will reveal the
existing bargraph justification which can be
changed to one of the following four or five options
using the ▲or ▼button:
Bargraph starts from
‘LEFt’ Left end of display
‘CEntr’ Centre of display
‘riGHT’ Right end of display
‘AlrSP’ Only with alarms – see section 9.3.14
‘oFF’ Bargraph disabled
When set as required press Eto return to the
‘tYPE’ sub-function prompt.
11

The indicator’s digital display at which the bargraph
starts is defined by the ‘bArLo’ sub-function which is
selected by pressing the ▲button followed by the P
button which will reveal the current indicator display at
which the bargraph starts. The flashing digit can be
adjusted by pressing the ▲or ▼buttons, when set as
required pressing Pwill transfer control to the next
digit. When all the digits have been adjusted, press E
to return to the 'bArLo' prompt from which ‘bArHi’
which defines the finishing point of the bargraph can
be selected by pressing the ▲button. ‘bArHi’ is
adjusted in the same way as ‘bArLo’. When set as
required, pressing Etwice will return the display to the
‘bAr’ prompt in the configuration menu.
Note: ‘bArLo’ must be set lower than ‘bArHi’, incorrect
setting is indicated by the bargraph scale flashing with
a single bargraph segment activated.
5.8 Function of the Ppush button: ‘C - - P’
When the indicator is in the display mode, operating
the Ppush button will display the input current in
milliamps, or the displayed value as a percentage of
the difference between the displayed values at 4mA
and 20mA inputs.
To check or change the function of the Ppush button
select 'C - - P' from the configuration menu and press
Pto reveal the current setting. Pressing the ▲or ▼
button will toggle the setting between '4-20' the
current display in milliamps and 'PC' the percentage
display. When set as required press Eto return to
the ‘C - - P’ prompt in the configuration menu.
5.9 Tare function: ‘tArE’
The tare function is primarily intended for use with
weighing system. When the indicator is in the display
mode and the tare function is activated, pressing the
Ebutton for more than three seconds will zero the
indicator’s digital display and activate the tare
annunciator. On the BA527E-SS the bargraph
remains linked to the digital display when the tare
function is activated. Subsequent operation of the E
push button for less than 3 seconds will return the
indicator to the gross display and deactivate the tare
annunciator.
To check or change the tare function select 'tARE'
from the configuration menu and press Pto reveal the
current setting. Pressing the ▲or ▼button will
toggle the setting between 'on' and 'oFF'. When set
as required press Eto return to the ‘tARE’ prompt in
the configuration menu.
5.10 Security code: ‘CodE’
Access to the instrument configuration menu may be
protected by a four digit security code which must be
entered to gain access. New instruments are
configured with the default security code 0000 which
allows unrestricted access to all configuration
functions.
To enter a new security code select 'CodE' from
the configuration menu and press Pwhich will
cause the indicator to display the existing security
code with one digit flashing. The flashing digit can
be adjusted using the ▲and ▼push-buttons,
when set as required operating the Pbutton will
transfer control to the next digit. When all the
digits have been adjusted press Eto return to the
‘CodE’ prompt. The revised security code will be
activated when the indicator is returned to the
display mode. Please contact BEKA associates
sales department if the security code is lost.
5.11 Reset to factory defaults: ‘rSEt’
This function enables the indicator and the
lineariser to be quickly returned to the factory
default configurations shown in sections 5 and 6.
To reset the indicator or lineariser select ‘rSEt’ from
the configuration menu and press P, the indicator
will display one of the reset options ‘ConF’ or
‘LtAb’.
‘ConF’ Resets the indicator to defaults
‘LtAb’ Resets the lineariser to defaults
Using the ▲or ▼push button select the required
sub-function and press P. To prevent accidental
resetting the request must be confirmed by
entering ‘5urE’. Using the ▲button set the first
flashing digit to ‘5’ and press Pto transfer control to
the second digit which should be set to ‘u’. When
‘5urE’ has been entered pressing the Ebutton will
reset the selected configuration menus and return
the display to the ‘rSEt’ function in the
configuration menu.
5.12 Under and over-range
If the numerical display range of the indicator is
exceeded, all the decimal points will flash as
shown below:
BA507E-SS BA527E-SS
Underrange -9.9.9.9 -9.9.9.9.9
Overrange 9.9.9.9 9.9.9.9.9
Although not guaranteed, most indicators will
continue to function normally with an input current
between 1.8mA and 4mA, at lower currents the
instrument will display ‘LPLo’ before it stops
functioning.
Under or overrange of the BA527E-SS bargraph is
indicated by an activated arrow at the appropriate
end of the bargraph and a flashing bargraph scale.
12

6. LINEARISER
A sixteen segment, seventeen break-point (0 to 16)
lineariser may be selected in the ‘FunC’ section of the
configuration menu. The position of each break-point
is fully adjustable so that the slope of the straight line
between break-points can be set to compensate for
input non-linearity, thus allowing the indicator to
display a non-linear process variables in linear
engineering units. Each break-point must occur at a
current greater than the preceding break-point and
less than the following break-point, in the range 3.8 to
21.0mA. If this requirement is not observed when
configuring the lineariser the indicator will display
'FaiL' and the configuration adjustment which
produced the error message will be ignored. Fig 9
shows a typical linearised indicator characteristic.
Fig 9 shows a typical linearising characteristic
Selecting ‘Lin’ in the ‘FunC’ section of the
configuration menu activates the lineariser, this does
not change the configuration menu shown in Fig 8, but
the 'CAL' and 'SEt' functions are extended as shown
in Fig 10. As with a linear indicator, calibration of the
lieariser may be performed with an external current
source using the 'CAL' function, or with the internal
reference using the 'SEt' function.
The lineariser calibration is retained irrespective of
how the indicator function ‘FunC’ is subsequently
changed. It is therefore possible to select and
deselect the lineariser without having to reconfigure it
each time.
The lineariser calibration may be reset to the factory
default settings without changing the indicator
configure using the 'LtAb' function described in section
5.11.
6.1 Lineariser calibration using an external
current source.
This method allows direct calibration of the
lineariser with an external current source and is the
preferred method when traceability is required. If
the exact system non-linearity is unknown, this
method also allows direct calibration from the
variable to be displayed. e.g. the output from a
level sensor in an irregular tank may be displayed
in linear volumetric units by filling the tank with
known incremental volumes and calibrating the
indicator to display the sum of the increments at
each break-point.
The number of break-point required should first be
entered using the 'Add' and 'dEL' functions. In
both these sub-functions the indicator initially
displays the current break-point and the total
number of break-points being used as shown
below.
Display Description of function
'Add' Add a break-point
Adds a new break-point before the
displayed break-point. The calibration
of existing break-points is not changed,
but the identification number of all
subsequent break-points is increased
by one.
'dEL' Remove a break-point
Removes the displayed break-point and
joins the preceding break-point to the
following break-point with a straight
line. The identification number of all
subsequent break-points is decreased
by one.
To add a break-point use the ▲or ▼button to
select 'CAL' from the configuration menu and press
Pwhich will result in the 'Add' sub-function prompt
being displayed. To enter the sub-function press P
which will reveal the current break-point and the
total number of break-points which have already
been entered. When adding a break-point the
insertion position can be selected using the ▲and
▼push buttons followed by Ppush button to
insert the additional break-point. In previously
uncalibrated linearisers each new break-point
should be added in front of the highest existing
break-point, if this sequence is not followed a 'FaiL'
message will occur in the 'Pt5' function. See
example in section 6.1.1.
13

14

The delete break-point sub-function 'dEL' operates in
exactly the same way as the 'Add' sub-function
described above. Once within the ‘dEL’ sub-function
each time the Pbutton is pressed a break-point is
removed. When deleting a break-point from a
calibrated indicator, the break-point to be deleted can
be selected using the ▲and ▼push buttons. The
minimum number of break-point is 2, break-points
'0:1' and '1:1'.
When the required number of linearising break-points
has been entered, return to the linearisation sub-menu
by pressing E. The indicator will display the 'Add' or
'dEL' prompt depending upon the last function used.
Using the 'Pts' sub-function the input current at which
each break-point occurs and the corresponding
indicator display may now be defined.
Using the ▲or ▼button select the 'PtS' function in
the sub-menu and press Pto enter the function
which will display the first break-point '0:n', where n is
the total number of linearising break-points entered –
see Fig 9. The selected linearising break-point can be
changed using the ▲and ▼buttons. When the
required linearising break-point has been selected set
the indicator input current to the exact value at which
the break-point is required and press P*. Using the
▲and ▼buttons and the Pbutton to move between
digits, enter the required indicator display at this
break-point. When set as required, press the Epush
button to enter the required indicator display and
return to the sub-menu from which the next beak-point
can be selected.
When all the break-points have been calibrated
pressing Etwice will return the indicator to the ‘CAL’
function in the configuration menu.
Note: * The indicator input current must be
adjusted to the required value before the P
button is operated to enter the required
indicator display.
Error message
If during calibration the indicator displays a
'FAiL' error message the current at which the
selected break-point is being set is not above the
proceeding break-point or is not below the
following break-point.
6.1.1 Example
Adding break-points to a new indicator
When adding break-points to a new indicator, or to a
lineariser following resetting to the factory defaults
using the 'LtAb' function described in section 5.11,
each additional break-point should be added before
the highest existing breakpoint. The first additional
break-point should be added before the default break-
point '1:1' which will result in a display of '1:2'. If
more new break-points are required, using the ▲
button select the new highest break-point '2:2' and
add the second additional break-point by operating
the Ppush button which will result in a display of
'2:3'. Repeat the sequence until the required
number of break-points has been entered.
The input current and at which each break-point
occurs and the corresponding indicator display
may now be entered as described above.
6.2 Lineariser calibration using the internal
reference.
The ‘SEt’ function enables the lineariser to be
calibrated without the need for an accurate
external current source. Throughout the calibration
the indicator input current may be any value
between 4 and 20mA.
The ‘SEt’ functions contains four sub-functions.
Display Description of function
'Add' Add a break-point
Adds a new break-point before the
displayed break-point. The calibration
of existing break-points is not changed,
but the identification number of all
subsequent break-point is increased by
one.
'dEL' Remove a break-point
Removes the displayed break-point
and joins the preceding segment to the
following segment with a straight line.
The identification number of all
subsequent break-points is decreased
by one.
'in' Defines the current at which break-
point occurs.
Enables the required current at each
break-point to be defined without
having to input an accurate input
current to the indicator.
'diSP' Defines indicator display at break-
point.
Enables the indicator display at each
break-point to be defined.
The number of break-point required should first be
entered using the 'Add' and 'dEL' sub-functions.
In both these sub-functions the indicator initially
displays the current break-point and the total
number of break-point being used as shown below.
15

To add a break-point using the ▲or ▼button select
'SEt' from the configuration menu and press Pwhich
will result in the 'Add' sub-function prompt being
displayed. To enter the sub-function press Pwhich
will reveal the current break-point and the total
number of break-points which have already been
entered. When adding a break-point the insertion
position can be selected using the ▲and ▼push
buttons followed by Ppush button to insert the
additional break-point. In previously uncalibrated
linearisers each new break-point should be added in
front of the highest existing break-point, if this
sequence is not followed a 'FaiL' message will occur
when the breakpoints are calibrated. See example in
section 6.2.1.
The delete break-point, sub-function 'dEL' operates in
exactly the same way as the 'Add' sub-function
described above. Once within the ‘dEL’ function each
time the Pbutton is pressed a break-point is removed.
When deleting a break-point from a calibrated
indicator, the break-point to be deleted can be
selected using the ▲and ▼push buttons. The
minimum number of break-point is 2, break-points
'0:1' and '1:1'.
When the required number of linearising break-point
has been entered, return to the linearisation sub-menu
by pressing E. The indicator will display the 'Add' or
'dEL' prompt depending upon the last sub-function
used. The indicator input current and corresponding
indicator display at each break-point can now be
entered using the ‘in’ and ‘diSP’ sub-functions.
Using the ▲or ▼button select 'in' from the sub-menu
and press Pwhich will reveal the starting point for the
first segment '0:n', where n is the total number of
break-point entered. Press Pand use the ▲and ▼
buttons and the Pbutton to move between digits, to
enter the input current in milliamps at which the first
break-point is required, usually 4.000mA. When set
as required, press Eto return to the ‘0:n’ prompt from
which the next break-point can be selected using the
▲and ▼buttons. When the required break-point has
been selected press Pand enter the indicator input
current at which this break-point is required using the
▲and ▼buttons and the Pbutton to move between
digits,. Repeat this procedure until the indicator input
current at all the break-points has been defined and
then return to the ‘in’ sub-function by pressing the E
button.
The corresponding indicator display at each of the
break-points can now be defined using the ‘diSP’ sub-
function Using the ▲and ▼buttons select the
‘diSP’ sub-function and press Pwhich will reveal the
starting point for the first break-point '0:n', where n
is the total number of break-points entered. Press P
and use the ▲and ▼buttons and the Pbutton to
move between digits, to enter the required indicator
display at the first break-point. When set as required,
press Eto return to the ‘0:n’ prompt from which the
next break-point can be selected using the ▲or ▼
buttons. When the required break-point has been
selected press Pand set the required indicator
display at this break-point.
Repeat this procedure until the indicator display at
all the break-points has been defined and then
return to the ‘SEt’ function in the configuration
menu by pressing the Ebutton twice.
Error message
If during calibration the indicator displays a
'FAiL' error message the current at which the
selected break-point is being set is not above
the proceeding break-point or is not below the
following break-point.
6.2.1 Example
Adding break-points to a new indicator
When adding break-points to a new indicator, or to
a lineariser following resetting to the factory
defaults using the 'LtAb' function described in
section 6.11, each additional break-point should be
added before the highest existing breakpoint.
The first additional break-point should be added
before the default break-point '1:1' which will result
in a display of '1:2'. If more new break-points are
required, using the ▲button select the new
highest break-point '2:2' and add the second
additional break-point by operating the Ppush
button which will result in a display of '2:3'. Repeat
the sequence until the required number of break-
points has been entered.
6.3 Under and over-range
The lineariser does not change the under and
over-range indication described in section 6.12.
At input currents below that specified for the first
break-point '0:n', the indicator will continue to use
the specified slope of the first segment.
At input currents above that specified for the last
break-point 'n:n', the indicator will continue to use
the slope specified for the last lineariser segment.
6.4 Lineariser default configuration
When the lineariser is reset to the factory defaults
using the ‘LtAb’ function described in section 5.11,
the defaults conditions are:
Indicator display
BA507E-SS BA527E-SS
First break-point '0:1' 4mA 0.0 0.00
Second break-point '1:1' 20mA 100.0 100.00
16

7. MAINTENANCE
7.1 Fault finding during commissioning
If an indicator fails to function during commissioning
the following procedure should be followed:
Symptom Cause Solution
No display Incorrect wiring Check wiring
There should be 0.6 to
1.2V between
terminals 1 & 3 with
terminal 1 positive.
With an optional loop
powered backlight,
there should be 3.4 to
5V between terminals
3 & 12 with terminal 12
positive.
No display
0V between
terminals 1 & 3.
Incorrect wiring
or no power
supply.
Check supply voltage
and voltage drop
caused by all the
instruments in the
loop.
All decimal points
flashing.
Underrange if
–ve sign
displayed or
overrange.
Recalibrate the
numerical display.
Unstable display 4/20mA input is
noisy.
Reduce ripple on
4/20mA power supply
and/or decrease
indicator resolution.
Unable to enter
configuration
menu.
Incorrect
security code
entered.
Enter correct security
code, or contact BEKA
if the code has been
lost.
7.2 Fault finding after commissioning
ENSURE PLANT SAFETY BEFORE
STARTING MAINTENANCE
If an indicator fails after it has been functioning
correctly follow the procedure shown in section 7.1. If
this does not reveal the cause of the fault, it is
recommended that the instrument is replaced. This
can be done without disconnecting power, but while
the indicator is disconnected the 4/20mA loop will be
open circuit.
7.3 Servicing
All BA507E-SS and BA527E-SS loop powered
indicators are interchangeable if the required
optional backlight and alarms are fitted. A single
spare instrument may quickly be recalibrated to
replace any instrument that is damaged or fails.
No attempt should be made to repair instruments
at component level.
We recommend that faulty instruments
are returned to BEKA associates or to
your local BEKA agent for repair.
7.4 Routine maintenance
The mechanical and electrical condition of the
instrument should be regularly checked. Initially
annual inspections are recommended, but the
inspection frequency should be adjusted to suit the
environmental conditions.
7.5 Guarantee
Indicators which fail within the guarantee period
should be returned to BEKA associates or your
local agent. It is helpful if a brief description of the
fault symptoms is provided.
7.6 Customer comments
BEKA associates is always pleased to receive
comments from customers about our products and
services. All communications are acknowledged
and whenever possible, suggestions are
implemented.
17

8. ACCESSORIES
8.1 Scale card
Both models have a window on the right hand side of
the display through which to view a scale card
showing the units of measurement such as oC, mBar,
RPM. New indicators are fitted with a scale card
showing the units of measurement specified when the
indicator was ordered, if the units are not specified a
blank scale card will be fitted. A pack of scale cards
pre-printed with common units of measurement is
available as an accessory. These can easily be fitted
on-site to the indicator without opening the indicator
enclosure or removing it from the panel, See section
4.5 of this instruction manual.
Custom scale cards for applications requiring less
common units of measurement are also available.
8.2 Tag information
New indicators are supplied with tag or application
information laser etched onto the rear panel adjacent
to the terminals, legend as specified when the
indicator was ordered. This tag information is not
visible from the front of the instrument after
installation.
8.3 Alarms
CAUTION
These alarms outputs should not be used for
critical safety applications such as an emergency
shut down system.
Both models can be supplied with factory fitted dual
solid state, single pole alarm outputs. Each alarm
output may be independently conditioned as a high or
low alarm with a normally open or normally closed
output in the non-alarm condition.
When the 4/20mA current powering the indicator is
removed both alarm outputs will open irrespective of
configuration. The open circuit condition should
therefore be chosen as the alarm condition when
designing an alarm system. Fig 11 illustrates the
conditions available and shows which are fail safe.
When an alarm occurs an alarm annunciator on the
indicator front panel is activated and if required the
numerical display can alternate between the
measured value and the alarm channel identification
‘ALr1’ or ‘ALr2’.
CAUTION
The alarms are activated by the indicator’s
numerical display. Use of the Tare Function
‘tArE’ will change the numerical display, the
alarms will continue to function at the original
displayed value, but this will correspond to a
different input current.
Fig 11 Alarm outputs
Configurable functions for each alarm include
adjustable setpoint, hysteresis, alarm delay and
alarm accept.
8.3.1 Solid state output
Each alarm has a galvanically isolated single pole
solid state switch output which as shown in Fig 12.
The output is polarised and current will only flow in
one direction.
Ron = less than 5Ω+ 0.7V
Roff = greater than 1MΩ
Fig 12 Equivalent circuit of each alarm output
The solid state output of each alarm may be used
to switch any dc circuit with parameters equal to or
less than:
V=30V
I=200mA
18

19

Fig 14 Typical alarm application
(Shown without recommended screened cables)
8.3.2 Configuration and adjustment
When optional alarms are fitted to a loop powered
indicator the configuration menu is extended as
shown in Fig 13. The additional functions appear
between the ‘SEt’ and the ‘C- - P’ functions for the
BA507E-SS and and between ‘bAr’ and ‘C- -P’ for the
BA527E-SS indicators. For simplicity, Fig 13 only
shows the additional functions for alarm 1, but alarm 2
has identical functions.
The following table summaries each of the alarm
configuration functions and includes a cross reference
to more detailed information. Again only the functions
on alarm 1 are listed, but alarm 2 has identical
facilities.
Summary of alarm configuration functions
Display Description of function
'EnbL’ Alarm enable
Enables or disables the alarm without
changing the alarm parameters.
See section 8.3.3
'SP1' Alarm setpoint 1
Adjusts the alarm setpoint. The alarm
is activated when the indicator display
equals the setpoint.
See section 8.3.4
'Hi.Lo' Alarm function
Defines the alarm function as High or
Low.
See section 8.3.5
'no.nC' Normally open or normally closed
output
Sets the alarm output open or closed in
the non-alarm condition.
See section 8.3.6
'HStr' Hysteresis
Adjusts the alarm hysteresis.
See section 8.3.7
'dELA' Alarm delay time
Introduces adjustable delay between
the display equalling the setpoint and
the alarm output being activated.
See section 8.3.8
'SiL' Alarm silence time
Defines the time that the alarm output
remains in the non-alarm condition
following acceptance of an alarm.
See section 8.3.9
‘FLSH’ Flash display when alarm occurs
When enabled, alternates the
numerical display between process
value and alarm reference, ‘ALr1’ or
‘ALr2’, when an alarm output is
activated.
See section 8.3.10
'ACSP' Access setpoint
Sub-menu which enables direct access
to the alarm setpoints from the indicator
display mode, and defines a separate
security code.
See section 8.3.11
20
This manual suits for next models
1
Table of contents
Other BEKA Measuring Instrument manuals

BEKA
BEKA BA374NG User manual
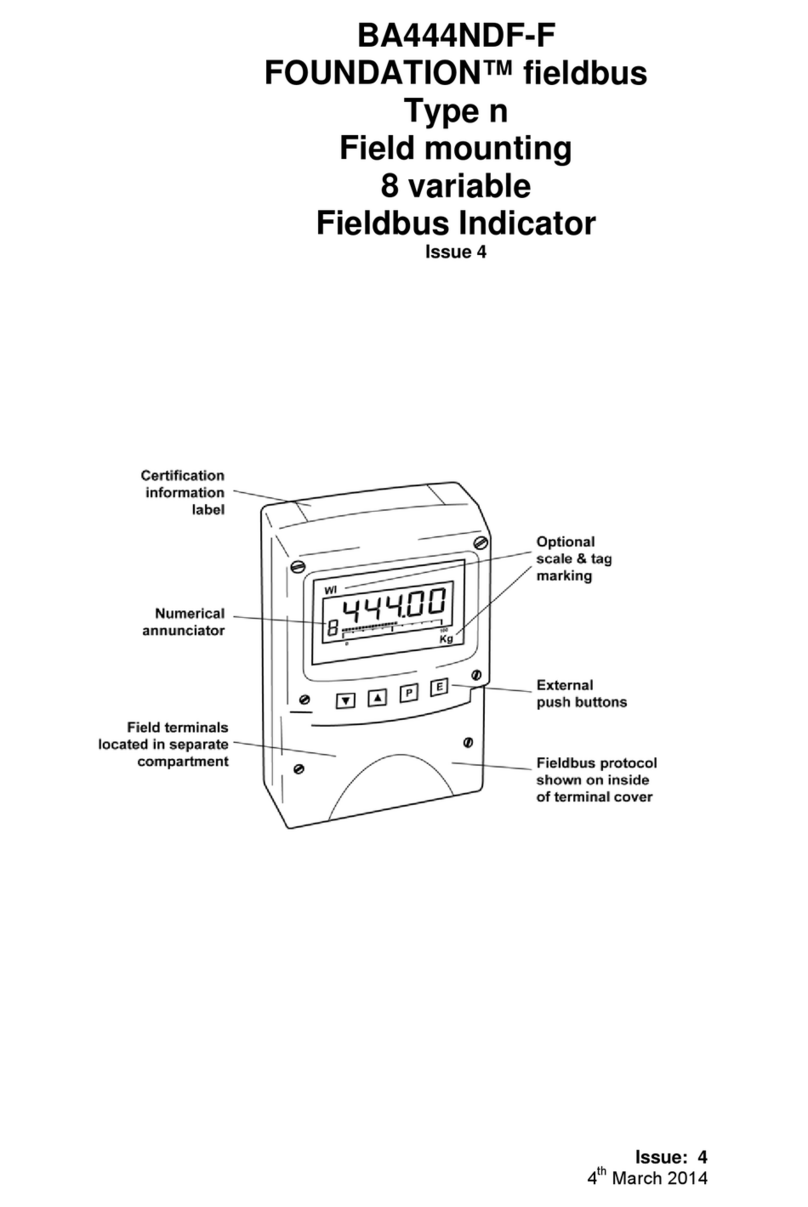
BEKA
BEKA FOUNDATION BA444NDF-F User manual
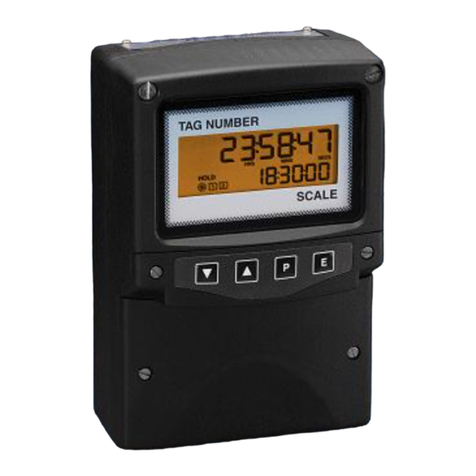
BEKA
BEKA BA364ND User manual
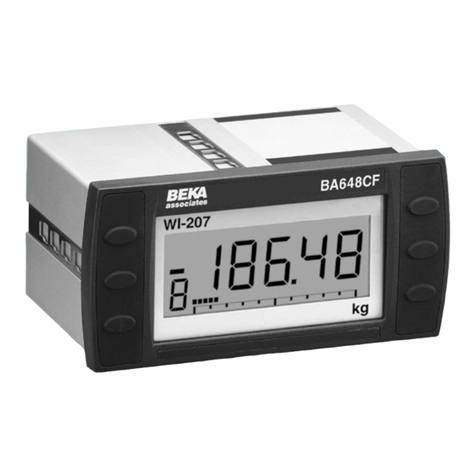
BEKA
BEKA BA648CF-F User manual
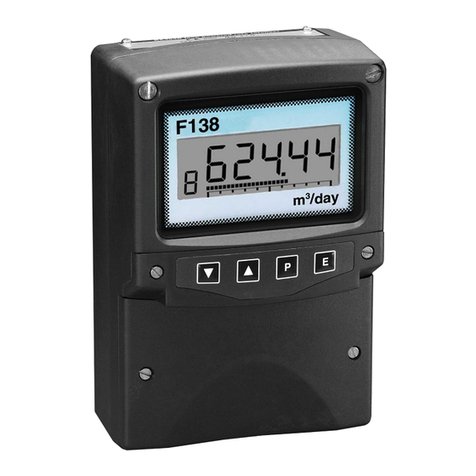
BEKA
BEKA PROFIBUS PA BA444DF-P User manual
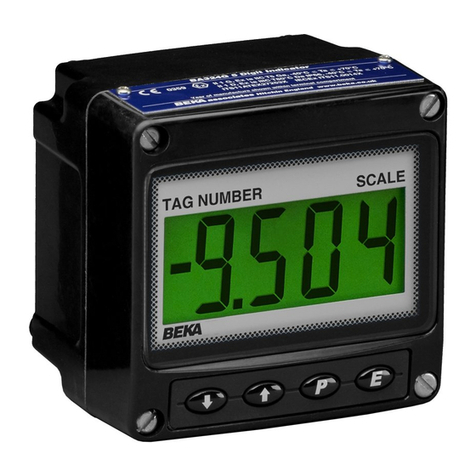
BEKA
BEKA BA504G User manual

BEKA
BEKA BA307C User manual

BEKA
BEKA BA444NDF-P Installation and operating instructions
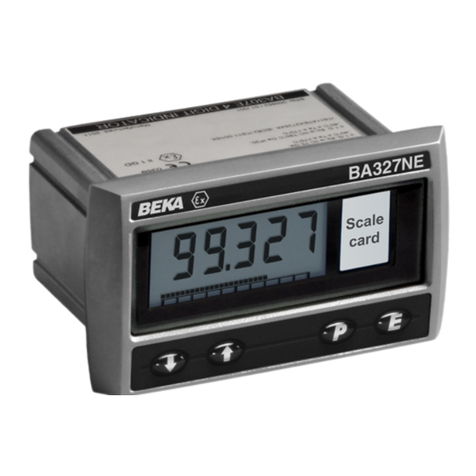
BEKA
BEKA BA327NE User manual

BEKA
BEKA BA527C User manual
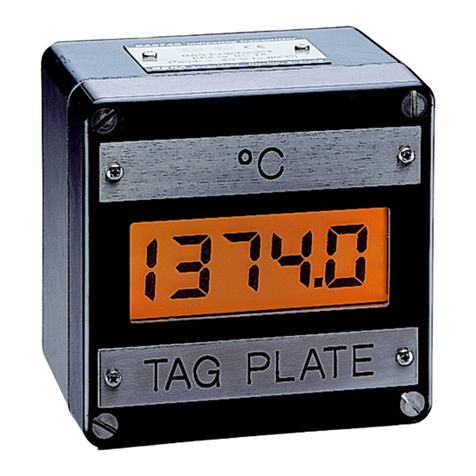
BEKA
BEKA BA304C User manual
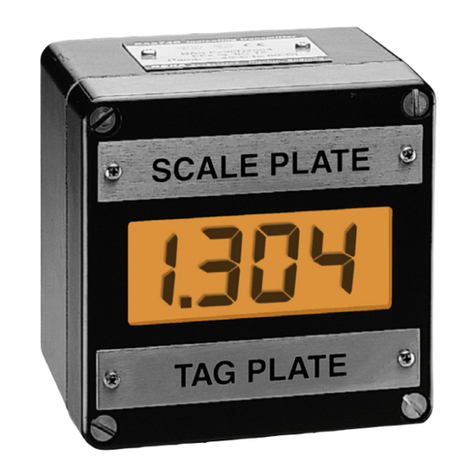
BEKA
BEKA BA304NC User manual
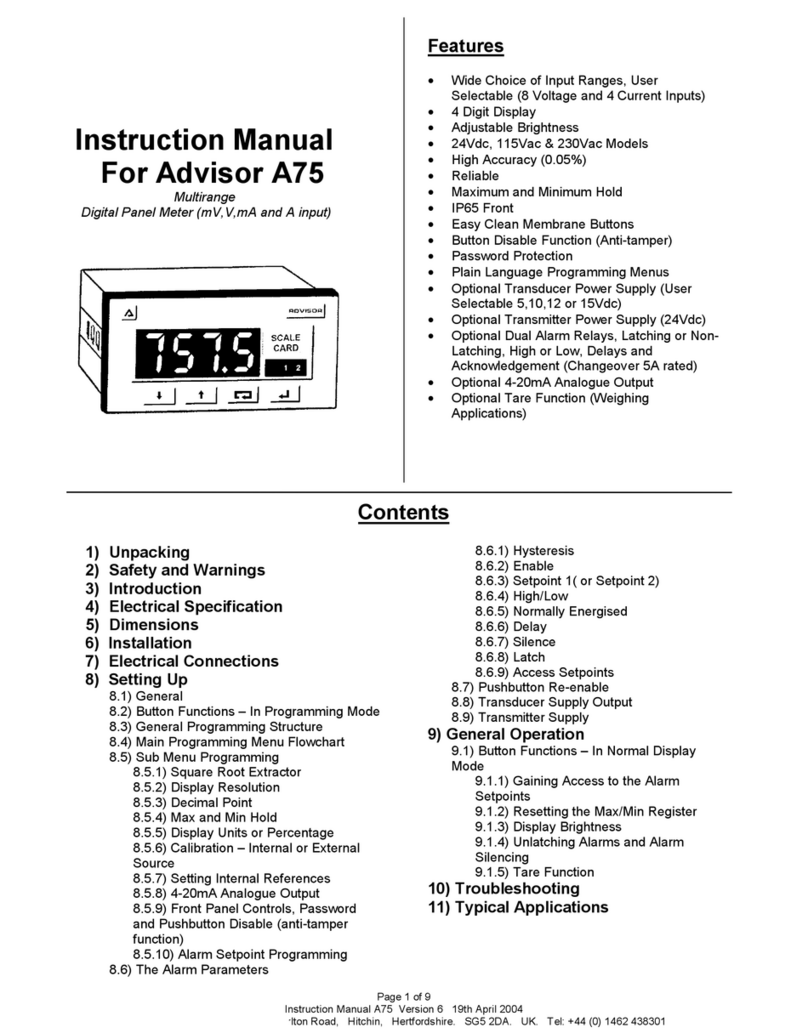
BEKA
BEKA Advisor A75 User manual

BEKA
BEKA BA504E User manual

BEKA
BEKA BA304G User manual

BEKA
BEKA BR323AL User manual
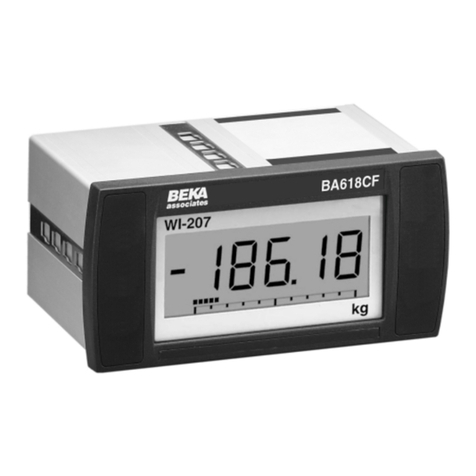
BEKA
BEKA FOUNDATION BA618CF-F User manual

BEKA
BEKA BA327E-SS User manual
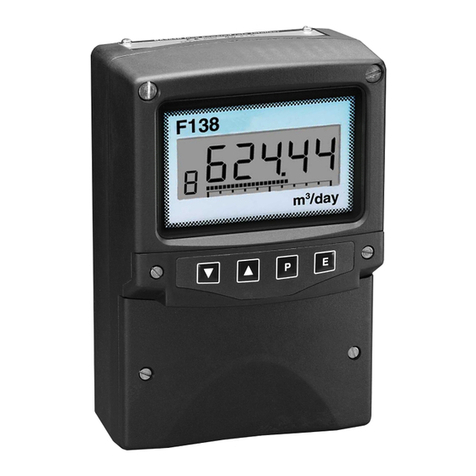
BEKA
BEKA FOUNDATION BA444DF-F User manual
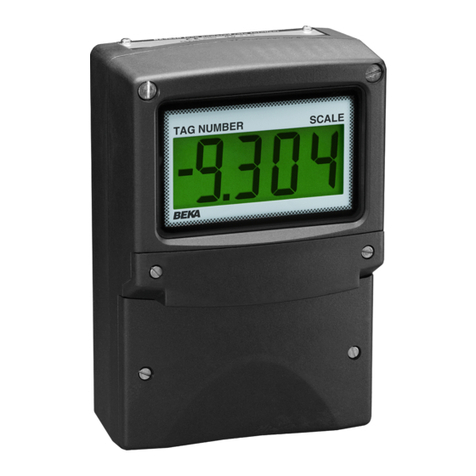
BEKA
BEKA BA304D User manual