Cepex EXTREME Series Manual

EXTREME SERIES
BUTTERFLY VALVES
INSTALLATION AND
MAINTENANCE MANUAL
PVC-U (EPDM/FPM)
CPVC (EPDM/FPM)
PPH (EPDM/FPM)
PVDF (EPDM/FPM)
ABS (EPDM/FPM)
0045

2
Declaración de conformidad CE / EC Declaration of Conformity
El fabricante / the manufacturer: CEPEX S.A.U.
Avinguda Ramon Ciurans 40 ( Parcel.la 6) - P. I. Congost
08530 LA GARRIGA
Declara que nuestras vávulas / declares that our valves:
Tipo / Type: Válvulas de Mariposa / Buttery valves
Modelos / Models: INDUSTRIAL and EXTREME SERIES
Compuerta / Gate: PVC-U / CPVC / PPH / PVDF
Cumplen con los requisitos establecidos por la Unión Europea para EQUIPOS A
PRESIÓN según Directiva 2014/68/UE (PED), categoría II módulo A2, de acuerdo
con las normas harmonizadas:
- EN ISO 16136 VÁLVULAS INDUSTRIALES: Válvulas de mariposa de materiales
termoplásticos.
Meets the requirements established by the European Union for PRESSURE EQUIPMENT
according to Directive 2014/68/UE (PED), category II module A2, in accordance with
the harmonized standards:
- EN ISO 16136 INDUSTRIAL VALVES: Buttery valves of thermoplastic materials.
La marca CE sobre la válvula hace referencia a esta conformidad. Según la direc-
tiva 2014/68/UE solamente las válvulas mayores a DN25 pueden ir marcadas con
CE.
The CE marking on the valve refers to this conformity. According to Directive 2014/68/
UE only valves larger than DN25 can be marked with CE.
Organismo certicador / Notied Body: TÜV NORD Systems GmbH & Co. KG
Große Bahnstrasse 31 , D-22525 Hamburg / Germany
N.º de identicación / Identication number : 0045
Yasmin Fernández
Quality management
La Garriga, April 2017

3
ENGLISH PAGE 04
ESPAÑOL PAGE 09
FRANÇAIS PAGE 15
PORTUGUÊS PAGE 19
ITALIANO PAGE 24
DEUTSCH PAGE 29

4
ENGLISHEXTREME BUTTERFLY VALVE
1. DEFINITION
Buttery valve for isolating or regulating the ow in liquid handling systems. The liquid can ow in both directions.
Design based on the EN ISO 16136 Standard in accordance with the Pressure Equipment Directive.
The valve is available with PVC-U, PVC-C, PP-H, PVDF and ABS discs and EPDM and FPM sealing gaskets. The choice of material for
the disc and gasket depends on the type of liquid to be carried and on the working temperature of the liquid, in accordance with
the chemical resistance tables available on our website and the pressure/temperature chart in this Manual (G4.1).
2. WARNINGS
• Carefully read these instructions before handling the valve and observe their recommendations. Any damage caused by
failure to observe these instructions is not covered by the warranty.
• All connection and handling tasks must be performed by qualied personnel.
• The maximum service life of the valve is specied in EN ISO 16136. It is veried on the production plant by aging tests spe-
cied in the standard.
• Correct installation and handling of the valve, as well as adherence to the maximum pressure and temperature conditions
specied in this manual are essential for preserving the service life of the valve.
• The driven liquid must be compatible with the valve materials. Consult chemical resistance charts published by Cepex or
consult the technical department.
• Using tools for opening or closing the manual valve control is not recommended. This process must be done manually.
• Before carrying out any maintenance operations on the pipe or valve, ensure that the system is depressurised by releasing
the pressure and emptying the pipes, following the specic safety regulations of each product.
• Turning the handle when the safety lock is in place could damage the valve.
• Avoid shocks during transport, since they may damage the body and mechanism of the valve. Store the valve in the original
packaging, protected against humidity and direct sunlight.
• Before installation, check that the valve is undamaged and that it contains all the parts required for installation.
• After long periods of inactivity, check the grease on the gasket and follow the maintenance instructions set out in this ma-
nual. The grease must be compatible with the valve materials.
• It is important to avoid rapid closure of valves to eliminate the possibility of water hammer causing damage to the pipeline.
• When using the valve as the nal element of a installation, take into account the risks of the liquid and control the pressure
and temperature, according to the standards of safety of each product.

5
ENGLISH EXTREME BUTTERFLY VALVE
27
28
30
29
31
32
33
3. COMPONENTS (T3.1)
Fig. 1
N DESCRIPTION MATERIAL DN65-
DN200
DN250-
DN300
1Body PP-GR 1 1
2Sealing gasket EPDM / FPM 1 1
3Disc PVC-U/PPH/CPVC/PVDF/ABS 1 1
4Lower bearing POM 1 1
5Upper bearing POM 1 1
6Auxiliary bearing POM 1 1
7Shaft AISI 630 / AISI 316L / AISI 904L 1 1
8Cap PP 1 1
9Ring DIN-471 AISI-304 1 1
10 O-ring EPDM / FPM 2 4
11 O-ring EPDM / FPM 2 4
12 Lower washer POM (DN65: AISI-304) 1 1
13 O-ring EPDM / FPM 2 4
14 Screw DIN-912 AISI-304 1 1
15 Handle PP-GR 1 -
16 Washer AISI-304 1 -
17 Lever PP-GR 1 -
18 Pin AISI-304 1 -
19 Left spring AISI-304 1 -
20 Right spring AISI-304 1 -
21 Throttle plate PP-GR 1 -
22 Safety lock POM 1 -
23 Handle cap PP 1 -
24 Screw DIN-912 AISI-304 2 2
25 Nut DIN-934 AISI-304 2 2
26 Screw DIN-912 AISI-304 1 -
27 Gear box Aluminium (housing) - 1
28 Mounting clamp PP-GR - 1
29 Coupling bush AISI-303 - 1
30 Washer DIN-125 AISI-304 - 4
31 Nut DIN-934 AISI-304 - 4
32 Screw DIN-912 AISI-304 - 4
33 Screw DIN-912 AISI-304 - 4
Pressure / Temperature Chart. (G 4.1)
4. TECHNICAL SPECIFICATIONS
DN40 - DN200: PN 10 at 20 °C liquid temperature.
DN250 - DN300: PN 6 at 20 °C liquid temperature.
The working pressure of the valve reduces with increasing liquid temperature, as shown in the accompanying chart.
Maximum torque at the output of the gearbox = 500 Nm
(Ratio = 37:1).
4
Temperature
Pressure
psi bar
ºC
ºF
Temperature
Pressure
4
psi bar
ºC
ºF

6
ENGLISHEXTREME BUTTERFLY VALVE
Pressure loss chart (G 4.2)
Pressure loss table (T4.1)
Valve operating torque
Operating torque values at rated pres-
sure (PN) and 20 °C in as new direct
from the factory condition. Installa-
tion (flange tightening) and operating
(pressure and temperature) conditions
will affect these values.
The actuator that is required for an au-
tomatic operation must be calculated
according to some safety factors that
were determined in life tests carried
out in the factory.
(T4.3)Operating torque table (Nm)
Kv / % opening (G 4.3)
DN40 DN65 DN80 DN100 DN125 DN150 DN200 DN250 DN300
N·m 12 25 28 35 85 110 110 180 250
lbf·inch 106 221 248 310 752 974 974 1593 2213
D DN Kv (l/min) Cv (GPM)
50 (1 1/2”) DN40 600 42
63-75 (2 1/2”) DN65 1568 110
90 (3”) DN80 4980 349
110 (4”) DN100 7212 505
125-140 (5”) DN125 12320 863
160 (6”) DN150 25447 1134
200-225 (8”) DN200 35778 2505
250 (10”) DN250 65222 4567
315 (12”) DN300 94660 6629
L
A
B
G
S
E
C
H
E
F
K
DN
M
N
DN A B C C1 E F G H K L L1 M N E’ S HOLES
40 175 120 111 90 26 18 112 40 98-110 220 125 70 9 36 7 4
65-50 201 156 120 90 40 18 112 48 125-145 220 125 70 9 35 7 4
80 232 190 136 90 40 19 112 52 150-170 245 125 70 9 35 8 8
100 255 212 148 90 40 19 112 59 180-192 245 125 70 9 35 8 8
125 284 238 164 102 40 22 112 66 190-215 320 160 70 9 35 14 8
150 314 265 180 102 40 24 112 72 240 320 160 70 9 35 14 8
200 378 320 217 116 50 23 136 73 270-298 391 160 102 11 47 18 8
250 446 392 124 124 - 24 247 121 329-355 - 200 - - 51 18 12
300 535 470 124 124 - 28 297 121 384-427 - 200 - - 52 18 12
DN40-200 DN250-300
5. DIMENSIONS.
T 5.1
Fig. 2
Fig. 3
Valve design Flanged dimensions Valve connections Other connections Actuator coupling (optional)
ISO 16136: 2005 EN 558-1,ANSI B16.5 Class 150,JIS B2220, BS/E EN 1090-1 ISO15494, ISO15493, ISO10931 EN/ISO 5211

7
6. INSTALLATION AND COMMISSIONING
Before starting the installation process, check that all the parts needed for the valve assembly are there, and that the materials,
connection type and nominal pressure are suitable for the installation.
For solvent or welded connections, ensure also that the parts to be connected are of the same material and that the correct solvent
or welding tools are used.
To install the valve, follow best installation practice recommendations provided on the Cepex website, paying specic attention to
thermal expansion and pipe alignment.
When lling the pipes with liquid, check that all the air has been purged from the system and that the initial pressure does not exceed
the nominal pressure of the valve, or of the system element with the lowest nominal pressure rating.
Valve assembly using standard ISO-DIN, ANSI, JIS and BS/E anges. Flat gaskets are not needed in the socket couplings, as they are
incorporated in the valve itself. Observe the tightening sequence of the screws on the anges (Fig. 6) and the maximum tightening
torque. All screws must be used in the ange in order to ensure proper operation of the valve.
The PP/PE sockets for butt welding must be chamfered as indicated in the diagram (Fig. 7) and table (T5.2), to ensure correct opening
and closing of the disc.
Install the valve once the sockets are solvent-bonded and dry, to avoid problems with the adhesive (entry of the latter into the valve).
Flanges must be well centred on the valve (pay special attention to measurements DN100-DN125 and DN200). Misalignment on
assembly could cause problems with the valve operation.
D DN inch Screws (A2) Torque
(N·m)
Torque
(inch·lbs)
40 50 - 4xM16x120 25 221
63 50 - 4xM16x120 25 221
75 65 2 1/2” 4xM16x140 25 221
90 80 3” 8xM16x150 25 221
110 100 4” 8xM16x160 30 265
125 125 - 8xM16x170 35 310
140 125 5” 8xM16x170 35 310
160 150 6” 8xM20x200 40 354
200 200 - 8xM20x210 50 442
225 200 8” 8xM20x230 50 442
250 250 - 12xM20x270 80 708
280 250 10” 12xM20x270 80 708
315 300 12” 12xM20x310 80 708
Screws and screw tightening torque
DN D min. x
40 31 30º
65 50.5 30º
80 70 30º
100 91.5 30º
125 113 30º
150 141 30º
200 191.5 20º
250 226 20º
300 296.5 20º
Fig. 4
Fig. 5
Fig. 6 Pipe and chamfer
measurements
PP/PE sockets
T 6.2
ENGLISH EXTREME BUTTERFLY VALVE
T 6.1

8
7.2 Assembling and Removing the Handle
To assemble the handle:
Fit the handle on the shaft while holding the lever. Place it so that, with the valve closed, the handle
indicator shows 90º on the throttle plate (21).
Fit the washer (16), screw (26) and cap (23).
To remove the handle:
Remove the round cap (23) from the handle, the screw (26) and the washer (16).
Press the lever (17) fully upwards so that its teeth are fully disengaged from the teeth on the
throttle plate (21). Remove the handle from the shaft (7).
7.1 Replacing the Sealing Gasket
Should it be necessary to replace the sealing gasket, proceed as follows:
· Ensure that the system is depressurised by releasing the pressure and emptying the pipes, fo-
llowing the specic safety regulations of each product. Also check the temperature of the liquid
and follow safety standards of temperature.
· Remove the valve from the installation.
· Remove the handle as per 7.2, screws (24), nuts (25) and throttle plate (21).
· Remove the ring (9). Take o the cap (8) and remove the screw (14).
· Tap on the shaft (7) with a rubber mallet until the bearing (14) is exposed from the bottom (Fig. 7).
· Once the bearing is out, remove the shaft (7), turn it and re-insert it (Fig. 8) from the bottom.
· Tap again until the bearings (5 and 6) emerge from the top. Remove the shaft again.
· Remove the disc by pressing in the direction of the uid.
· Remove the sealing gasket. Fit the new sealing gasket; it needs to be warped and placed so that it
lines up with the shaft, according to the indication tab of the gasket (Fig. 9).
WARNING: Before installing the new gasket, check the condition of the O-rings (10, 11 and 13).
Fig. 7 Fig. 8
7. OPERATION AND MAINTENANCE INSTRUCTIONS
It is recommended that the condition of the sealing gasket is checked regularly, since it may display signs of mechanical wear due
to pressure, handling and contact with the liquid. The sealing gasket should be greased in the disc contact area (the grease must
be compatible with the materials of the gasket and the disc). It is also advisable to check regularly that the ange xing nuts are
tightened correctly, as per the recommended torque values specied above (T6.1).
In long periods of inactivity, and in case that the installation allows it, maintain the valve slightly open. It is recommended to force a
periodic movement to avoid the lock of the valve in long periods of time in closed position. It is advisable to pass the liquid before
maneuvering the valve.
The manual gearbox is maintenance-free and greased for life.
To operate the valve, unlock the handle (13) removing the pin (16) and pulling the lever (15) upwards, releasing its teeth from the
throttle plate (15), then turning the handle in the appropriate direction.
To lock the valve, insert the pin (16) and, optionally, secure with a padlock.
Fig. 9
8. SOLUCIÓN DE PROBLEMAS T 8.1
FAULT POSSIBLE CAUSE FAULT CLEARANCE
The disc does not fully open or
close.
The sockets were not correctly bevelled. Disassemble the valve and bevel the sockets as indicated
in table T6.2.
Foreign materials in the compartment (adhesive, etc.). Disassemble the valve and check for obstructions in the
disc and gasket contact area.
Excessive opening or closing
torque.
The valve has been inactive for a long time. Operate with an auxiliary release key (not plastic handle).
Disassemble the valve and lubricate the sealing gasket.
Overtemperature or chemical attack cause damage to
the gasket.
Check the chemical compatibility of the liquid with the
disc and the working temperature. Replace the gasket.
Excessive ange torque. Tighten anges as indicated in section 6.
Misalignment between sockets and valve. Disassemble the valve and reassemble with concentric
alignment (observe the correct tightening sequence and
torque).
The valve is not fully watertight at
the sockets.
Misalignment between sockets and valve. Disassemble the valve and reassemble with concentric
alignment (observe the correct tightening sequence and
torque).
Flange screws not tight enough. Tighten anges as indicated in section 6.
The valve is not completely
watertight at the sealing gasket .
Inadequate chemicals.
Temperature out of range.
Excess pressure.
Conduction of abrasive elements.
Check compliance with the specications in this
document.
Damaged sealing gasket. Replace the gasket.
ENGLISHEXTREME BUTTERFLY VALVE

9
ESPAÑOL VÁLVULA DE MARIPOSA EXTREME
1. DEFINICIÓN
Válvula de mariposa para la interrupción o la regulación del caudal en los sistemas de conducción de líquidos. El líquido puede circu-
lar en los dos sentidos. Diseño basado en norma ISO EN 16136 según la Directiva de Equipos a Presión.
La válvula está disponible con compuertas fabricadas en PVC-U, PVC-C, PP-H, PVDF y ABS y con juntas de EPDM y FPM (FKM). La
elección del material de la compuerta y de la junta depende del tipo de líquido a transportar y de la temperatura y de trabajo del
líquido, de acuerdo con las tablas de resistencia química disponibles en nuestra web y el diagrama de presión / temperatura de este
mismo manual (G4.1).
2. ADVERTENCIAS
• Leer estas instrucciones antes de manipular la válvula y seguir las recomendaciones aquí mencionadas. Los daños causados por no
seguir estas instrucciones no estarán cubiertos por la garantía.
• Las operaciones de conexión y manipulación deberán ser realizadas por personal cualicado.
• La máxima vida útil de la válvula es la especicada en la norma EN ISO 16136. Se verica en la planta de producción mediante las
pruebas de envejecimiento especicadas en la norma.
• El cumplimiento de la vida útil está condicionado por la instalación y manipulación correcta de la válvula, y por el respeto a las
condiciones técnicas de presión y temperaturas máximas especicadas en este mismo manual.
• El líquido conducido debe ser compatible con los materiales de la válvula. Consultar tablas de resistencias químicas publicadas por
Cepex o consultar con el departamento técnico.
• No se recomienda la utilización de herramientas para la manipulación del mando manual de apertura y cierre de la válvula. Debe
realizarse de forma manual.
• Antes de realizar alguna operación de mantenimiento sobre el conducto o la válvula, asegurarse de que no existe presión en el
sistema, liberando la presión y vaciando los conductos, siguiendo las normativas de seguridad especícas para cada producto.
• Girar la maneta con el seguro posicionado podría provocar daños en la válvula.
• Evitar golpes durante el transporte que puedan dañar al cuerpo y al mecanismo. Mantener la válvula almacenada en el embalaje
original, protegido de la humedad y de la exposición directa al sol.
• Comprobar antes de la instalación que la válvula no ha sufrido daños y que contiene todos los elementos necesarios para su
instalación.
• Revisar el engrasado de la junta después de largos periodos de inactividad y seguir las instrucciones de mantenimiento de este
mismo manual. El lubricante debe ser compatible con los materiales de la válvula (consultar con el fabricante).
• Intentar evitar los golpes de ariete debidos a la maniobra brusca de la válvula, que podrían causar daños a la instalación.
• En caso de utilizar la válvula como nal de línea, tener en cuenta el riesgo del líquido según las normativas de seguridad del pro-
ducto y controlar la presión y la temperatura.

10
ESPAÑOLVÁLVULA DE MARIPOSA EXTREME
27
28
30
29
31
32
33
3. COMPONENTS (T3.1)
Fig. 1
N DESCRIPCIÓN MATERIAL DN65-
DN200
DN250-
DN300
1 Cuerpo PP-GR 1 1
2 Junta EPDM / FPM 1 1
3 Compuerta PVC-U/PPH/CPVC/PVDF/ABS 1 1
4 Casquillo inferior POM 1 1
5 Casquillo superior POM 1 1
6 Casquillo auxiliar POM 1 1
7 Eje AISI 630 / AISI 316L / AISI 904L 1 1
8 Tapón PP 1 1
9 Anillo DIN-471 AISI-304 1 1
10 Junta tórica EPDM / FPM 2 4
11 Junta tórica EPDM / FPM 2 4
12 Arandela inferior POM (DN 65 AISI-304) 1 1
13 Junta tórica EPDM / FPM 2 4
14 Tornillo DIN-912 AISI-304 1 1
15 Maneta PP-GR 1 -
16 Arandela DIN-
6798 AISI-304 1 -
17 Gatillo PP-GR 1 -
18 Pasador AISI-304 1 -
19 Muelle izquierda AISI-304 1 -
20 Muelle derecha AISI-304 1 -
21 Divisor PP-GR 1 -
22 Seguro POM 1 -
23 Tapón maneta PP 1 -
24 Tornillo DIN-912 AISI-304 2 2
25 Tuerca DIN-934 AISI-304 2 2
26 Tornillo DIN-912 AISI-304 1 -
27 Reductor manual Aluminio (carcasa) - 1
28 Soporte actuador PP-GR - 1
29 Conexión AISI-303 - 1
30 Arandela DIN-125 AISI-304 - 4
31 Tuerca DIN-934 AISI-304 - 4
32 Tornillo DIN-912 AISI-304 - 4
33 Tornillo DIN-912 AISI-304 - 4
Diagrama de Presión / Temperatura. (G 4.1)
4. CARACTERÍSTICAS TÉCNICAS
DN40 - DN200: PN 10 a 20 ºC de temperatura del líquido.
DN250 - DN300: PN 6 a 20ºC de temperatura del líquido.
La presión de servicio de la válvula se reduce cuando aumenta la temperatura del líquido, según los dos grácos adjuntos.
Par máximo a la salida del reductor manual = 500 N·m
(Reducción = 37:1).
4
Temperatura
Presión
psi bar
ºC
ºF
Temperatura
Presión
4
psi bar
ºC
ºF

11
ESPAÑOL VÁLVULA DE MARIPOSA EXTREME
Par de maniobra de la válvula.
Valores de par de maniobra a PN y 20
ºC en condiciones de salida de fábrica.
Las condiciones de instalación (apriete
de las bridas) y de servicio (presión y
temperatura) harán variar estos valores.
El actuador requerido para automatizar
el giro debe ser calculado teniendo en
cuenta ciertos coeficientes de segu-
ridad que han sido determinados en
pruebas de fatiga realizadas en fábrica.
(T4.3)
DN40 DN65 DN80 DN100 DN125 DN150 DN200 DN250 DN300
N·m 12 25 28 35 85 110 110 180 250
lbf·inch 106 221 248 310 752 974 974 1593 2213
D DN Kv (l/min) Cv (GPM)
50 (1 1/2”) DN40 600 42
63-75 (2 1/2”) DN65 1568 110
90 (3”) DN80 4980 349
110 (4”) DN100 7212 505
125-140 (5”) DN125 12320 863
160 (6”) DN150 25447 1134
200-225 (8”) DN200 35778 2505
250 (10”) DN250 65222 4567
315 (12”) DN300 94660 6629
L
A
B
G
S
E
C
H
E
F
K
DN
M
N
DN A B C C1 E F G H K L L1 M N E’ S HOLES
40 175 120 111 90 26 18 112 40 98-110 220 125 70 9 36 7 4
65-50 201 156 120 90 40 18 112 48 125-145 220 125 70 9 35 7 4
80 232 190 136 90 40 19 112 52 150-170 245 125 70 9 35 8 8
100 255 212 148 90 40 19 112 59 180-192 245 125 70 9 35 8 8
125 284 238 164 102 40 22 112 66 190-215 320 160 70 9 35 14 8
150 314 265 180 102 40 24 112 72 240 320 160 70 9 35 14 8
200 378 320 217 116 50 23 136 73 270-298 391 160 102 11 47 18 8
250 446 392 124 124 - 24 247 121 329-355 - 200 - - 51 18 12
300 535 470 124 124 - 28 297 121 384-427 - 200 - - 52 18 12
DN40-200 DN250-300
T 5.1
Fig. 2
Fig. 3
Diseño de
válvula
Dimensiones embridado Conexiones para
válvulas
Otras conexiones Acoplamiento actuador
(opcional)
ISO 16136: 2005 EN 558-1,ANSI B16.5 Class 150,JIS B2220, BS/E EN 1090-1 ISO15494, ISO15493, ISO10931 EN/ISO 5211
Diagrama de pérdidas de cargas (G 4.2)
Tabla de pérdidas de carga (T4.1)
Tabla de par de maniobra
Kv / grado apertura (G 4.3)
5. DIMENSIONES.

12
ESPAÑOLVÁLVULA DE MARIPOSA EXTREME
6. INSTALACIÓN Y PUESTA EN SERVICIO
Antes de iniciar la instalación de la válvula, verique que tiene disponibles todos los elementos necesarios para su montaje y que
los materiales, el tipo de conexión y la presión nominal son los adecuados para la instalación. En caso de unión por encolado o por
soldadura, certique también que los materiales a unir son iguales y que la cola o las herramientas de soldadura son las adecuadas.
Para la jación de la válvula, siga las recomendaciones de buenas prácticas de instalación disponibles en la web de Cepex, con
especial atención a las dilataciones térmicas y en la alineación de los tubos.
En el momento de llenar las tuberías del líquido a transportar, verique que se purgue todo el aire de la instalación y que la presión
inicial no supera la PN de la válvula o del elemento de menor presión nominal de la instalación.
Montaje de la válvula mediante bridas normalizadas ISO-DIN, ANSI, JIS y BS/E. En el acoplamiento no son necesarias juntas planas
para los manguitos, por llevarlas incorporadas la misma válvula. Tener en cuenta el orden de apriete (Fig. 5) de los tornillos en las
bridas y el par máximo de apriete (T6.1). Es imprescindible instalar la totalidad de los tornillos para asegurar el correcto funcionamiento
de la válvula.
Los manguitos de PP / PE de soldadura a tope se deben achaanar según el esquema (Fig. 6) y la tabla T6.2 para garantizar un buen
cierre y apertura de la compuerta.
Instalar la válvula una vez que los manguitos de unión estén encolados y secos para evitar problemas con el adhesivo (introducción
del mismo adhesivo en la válvula).
Las bridas deben estar bien centradas en la válvula (sobre todo atención a las medidas DN100-DN125 y DN200). Una mala alineación
del conjunto podría provocar problemas en el funcionamiento de la válvula.
D DN inch Screws (A2) Torque
(N·m)
Torque
(inch·lbs)
40 50 - 4xM16x120 25 221
63 50 - 4xM16x120 25 221
75 65 2 1/2” 4xM16x140 25 221
90 80 3” 8xM16x150 25 221
110 100 4” 8xM16x160 30 265
125 125 - 8xM16x170 35 310
140 125 5” 8xM16x170 35 310
160 150 6” 8xM20x200 40 354
200 200 - 8xM20x210 50 442
225 200 8” 8xM20x230 50 442
250 250 - 12xM20x270 80 708
280 250 10” 12xM20x270 80 708
315 300 12” 12xM20x310 80 708
DN D min. x
40 31 30º
65 50.5 30º
80 70 30º
100 91.5 30º
125 113 30º
150 141 30º
200 191.5 20º
250 226 20º
300 296.5 20º
Fig. 4
Fig. 5
Fig. 6
T 6.2
Tornillos y par de apriete de tornillos
Manguitos PP/PE Medida del tubo
y chaanes
T 6.1

13
ESPAÑOL VÁLVULA DE MARIPOSA EXTREME
7.2 Montaje y desmontaje de la maneta
Para montar la maneta:
•Montarlamanetaenelejemientrassemantienepresionadoelgatillo.Orientarlademaneraque,
con la válvula cerrada, el indicador de la maneta indique 90º en el divisor (21).
•Montarlaarandela(16),eltornillo(26)yeltapón(23).
Para desmontar la maneta:
•Extraereltapónredondo(23)delamaneta,eltornillo(26)ylaarandela(16).
•Presionarelgatillo(17)almáximohaciaarribadeformaquelosdientesdeésteliberentotalmente
los dientes del divisor (21) y sacar la maneta del eje (7).
7.1 Operaciones para el recambio de la junta de la compuerta
En caso de que fuera necesario cambiar la junta de la válvula, se procederá de la siguiente
manera:
•Asegurarse de que no existe presión en el sistema, liberando la presión y vaciando los conduc-
tos, siguiendo las normativas de seguridad especícas para cada producto. Controlar también
la temperatura del líquido y seguir la normas relativas a la temperatura.
•Desmontarlaválvuladelainstalación.
•Extraerlamanetasegún7.2,lostornillos(24),lastuercas(25)yeldivisor(21).
•Quitarelanilloelástico(9).Sacareltapón(8)yextraereltornillo(14).
•Golpearsobreeleje(7)conunamazadenylonhastaquesalgaelcasquillo(14)pordebajo
(Fig.7).
•Conelcasquillofuera,sacareleje(7),rotarloyreintroducirlo(Fig.8)porlaparteinferior.
•Picardenuevohastaquesalganloscasquillos(5y6)porencima.Volverasacareleje.
•Extraerlacompuertapresionandoenelsentidodeluido.
• Extraer la junta. Montar la nueva junta; debe entrar deformada y colocarla de manera que
quede centrada con el eje.
ATENCIÓN: antes de montar la nueva junta, revisar el estado de las juntas tóricas (10, 11 y 13).
Fig. 7 Fig. 8
7. INSTRUCCIONES DE OPERACIÓN Y MANTENIMIENTO
Es recomendable revisar el estado de la junta de forma regular, ya que se produce un desgaste mecánico debido a las presiones, a la
manipulación y al contacto con el líquido. Se recomienda el engrasado de la junta en la zona de contacto con la compuerta (con grasa
compatible con los materiales de la junta y la compuerta). También se recomienda revisar periódicamente el apriete de las tuercas de
jación de las bridas según el par recomendado con anterioridad en este mismo manual (T6.1).
En largos periodos de inactividad, y siempre que la instalación lo permita, mantener la válvula ligeramente abierta. Se recomienda
hacer un movimiento de compuerta periódico para no trabar la vàlvula en estados de larga duración en posición de válvula cerrada.
Es recomendable hacer pasar el líquido antes de maniobrar la válvula.
El reductor manual está exento de mantenimiento y está engrasado de por vida.
Para accionar la válvula, se procederá a desbloquear la maneta (13) extrayendo el pasador (16) y presionando la palanca (15) hacia
arriba, liberando los dientes de la misma del divisor (17) y girando la maneta en el sentido conveniente.
Para bloquear la válvula, colocar el pasador (16) y, opcionalmente, asegurar con un candado.
Fig. 9
8. GUÍA DE PROBLEMAS MÁS COMUNES T 8.1
PROBLEMA CAUSA SOLUCIÓN
La compuerta no abre o cierra
completamente.
Los manguitos PE-100 no han sido achaanados
correctamente o no son del mismo DN.
Desmontar la válvula y achaanar los manguitos según
T6.2. Comprobar estado de la compuerta y DN de los
manguitos.
Elementos extraños en el compartimento (adhesivo,
etc.).
Desmontar la válvula y comprobar obstrucciones en la
zona de contacto de la compuerta con la junta.
Excesivo par de apertura o cierre. La válvula ha estado mucho tiempo sin maniobrar. Accionamiento con una llave auxiliar (no la maneta).
Desmontar la válvula y lubricar la junta.
Deterioro de la junta por exceso de temperatura o por
ataque químico.
Revisar compatibilidad química del líquido con la
compuerta y temperatura de trabajo. Cambiar la junta.
Par de embridado excesivo. Embridar según apartado 6.
Desalineación entre manguitos y válvula. Desmontar la válvula y volver a montar con alineación
concéntrica (respetar el orden y el par de apriete).
La válvula no presenta una
completa estanqueidad en los
manguitos de unión.
Desalineación entre manguitos y válvula. Desmontar la válvula y volver a montar con alineación
concéntrica (respetar el orden y el par de apriete).
Falta de apriete de los tornillos de embridado. Embridar según apartado 6.
La válvula no presenta una
completa estanqueidad en la junta.
Elementos químicos inapropiados.
Temperatura fuera de valores.
Exceso de presión.
Conducción de elementos abrasivos.
Comprobar el cumplimiento de las características técnicas
de este documento.
Junta dañada. Sustituir la junta.

14
FRANÇAISVANNE PAPILLON EXTREME
1. DÉFINITION
Robinet à membrane pour l'arrêt ou la régulation du débit dans les systèmes de conduite de uides. Le liquide peut circuler dans
les deux sens. Conception basée sur la norme ISO EN 16136 selon la Directive.
Le robinet est disponible avec des corps fabriqués en PVC-U, PVC-C, PP-H, PVDF et ABS, ainsi qu'avec des joints en EPDM et FPM
(FKM). Le choix du matériau du corps et du joint dépend du type de uide à transporter et de la température de travail du uide,
selon les tableaux de résistance chimique disponibles sur notre site Internet ainsi que le diagramme de pression / température
de ce manuel (G4.1).
2. MISES EN GARDE
• Lisez attentivement ces instructions avant de manipuler le robinet et respectez les recommandations de ce manuel. Les dom-
mages provoqués par un éventuel non-respect des recommandations ne sont pas couverts par la garantie.
• Seul du personnel qualié est autorisé à raccorder et manipuler le produit.
• La durée de vie utile maximale du robinet est conforme à celle indiquée dans la norme EN ISO 16136. Elle est vériée en usine
de production par les tests de vieillissement spéciés dans la norme.
• La durée de vie utile est soumise à l'installation et à la manipulation correcte du robinet, ainsi qu'au respect des conditions
techniques de pression et de température maximales spéciées dans ce manuel.
• Le uide conduit doit être compatible avec les matériaux du robinet. Consulter les tableaux de résistances chimiques publiés par
Cepex ou consulter le département technique.
• Nous vous déconseillons d'utiliser des outils pour manipuler la commande manuelle d'ouverture et de fermeture du robinet. Vous devez le faire de
façon manuelle.
• Avant toute opération de maintenance sur le conduit ou le robinet, veuillez vérier l'absence de pression dans le système, en
libérant la pression et en vidangeant les conduits, selon les normes de sécurité spéciques pour chaque produit.
• Veillez à ne pas faire tourner la manette lorsque le dispositif de verrouillage est enclenché pour éviter tout dommage sur le
robinet.
• Pendant le transport, évitez tout choc susceptible d'endommager le corps et le mécanisme. Conservez le robinet dans son em-
ballage d'origine, à l'abri de l'humidité et des rayons directs du soleil.
• Avantde procéder à l'installation, vériez soigneusement que le robinet n'a pas été endommagé et que l'emballage contient bien tous les éléments
nécessaires.
• Vériez le graissage du robinet après de longues périodes d'inactivité et suivez les instructions de maintenance de ce manuel. Le
lubriant doit être compatible avec les matériaux du robinet.
• Veillez à éviter les coups de bélier dus à une manipulation brusque du robinet, qui pourraient endommager l'installation.
• Si vous utilisez le robinet comme n de ligne, tenez compte du risque lié au uide selon les normes de sécurité du produit et
contrôler la pression et la température.

15
FRANÇAIS VANNE PAPILLON EXTREME
27
28
30
29
31
32
33
(T3.1)
Fig. 1
N DESCRIPTION MATERIAL DN65-
DN200
DN250-
DN300
1Corps PP-GR 1 1
2Joint EPDM / FPM 1 1
3Disc PVC-U/PPH/CPVC/PVDF/ABS 1 1
4Douille POM 1 1
5Douille POM 1 1
6Douille auxiliaire POM 1 1
7Axe AISI 630 / AISI 316L / AISI 904L 1 1
8Chapeau PP 1 1
9Anneau DIN-471 AISI-304 1 1
10 Joint torique EPDM / FPM 2 4
11 Joint torique EPDM / FPM 2 4
12 Rondelle POM (DN65: AISI-304) 1 1
13 Joint torique EPDM / FPM 2 4
14 Vis DIN-912 AISI-304 1 1
15 Manette PP-GR 1 -
16 Rondelle AISI-304 1 -
17 Cliquet d’arrêt PP-GR 1 -
18 Goujon AISI-304 1 -
19 Ressort gauche AISI-304 1 -
20 Ressort droite AISI-304 1 -
21 Répartiteur PP-GR 1 -
22 Dispositif de verrouillage POM 1 -
23 Chapeau manette PP 1 -
24 Vis DIN-912 AISI-304 2 2
25 Écrou DIN-934 AISI-304 2 2
26 Vis DIN-912 AISI-304 1 -
27 Réducteur manuel Aluminium (housing) - 1
28 Bride de xation PP-GR - 1
29 Douille de raccordment AISI-303 - 1
30 Rondelle DIN-125 AISI-304 - 4
31 Écrou DIN-934 AISI-304 - 4
32 Vis DIN-912 AISI-304 - 4
33 Vis DIN-912 AISI-304 - 4
4. CARACTÉRISTIQUES TECHNIQUES
DN65-DN200 (2½”-8”) : PN10 (150 psi) à une température du uide de 20 ºC.
DN250 - DN300 (10”-12”) PN6 (90 psi) à une température du uide de 20 ºC.
La pression de service du robinet diminue lorsque la température du uide augmente, selon les deux graphiques joints.
Couple maximum à la sortie du réducteur manuel = 500 N·m
(Ratio = 37:1).
4
Temperature
Pressure
psi bar
ºC
ºF
Temperature
Pressure
4
psi bar
ºC
ºF
3. COMPOSANTS
Diagramme de pression / température. (G 4.1)

16
FRANÇAISVANNE PAPILLON EXTREME
Couple de manipulation du ro-
binet.
Valeurs de couple de manipulation
à PN et 20 ºC dans des conditions de
sortie d’usine. Les conditions d’instal-
lation (serrage des brides) et de service
(pression et température) feront varier
ces valeurs. En cas de besoin d’automa-
tisation de la manipulation, consultez le
fabricant.
DN40 DN65 DN80 DN100 DN125 DN150 DN200 DN250 DN300
N·m 12 25 28 35 85 110 110 180 250
lbf·inch 106 221 248 310 752 974 974 1593 2213
D DN Kv (l/min) Cv (GPM)
50 (1 1/2”) DN40 600 42
63-75 (2 1/2”) DN65 1568 110
90 (3”) DN80 4980 349
110 (4”) DN100 7212 505
125-140 (5”) DN125 12320 863
160 (6”) DN150 25447 1134
200-225 (8”) DN200 35778 2505
250 (10”) DN250 65222 4567
315 (12”) DN300 94660 6629
L
A
B
G
S
E
C
H
E
F
K
DN
M
N
DN A B C C1 E F G H K L L1 M N E’ S HOLES
40 175 120 111 90 26 18 112 40 98-110 220 125 70 9 36 7 4
65-50 201 156 120 90 40 18 112 48 125-145 220 125 70 9 35 7 4
80 232 190 136 90 40 19 112 52 150-170 245 125 70 9 35 8 8
100 255 212 148 90 40 19 112 59 180-192 245 125 70 9 35 8 8
125 284 238 164 102 40 22 112 66 190-215 320 160 70 9 35 14 8
150 314 265 180 102 40 24 112 72 240 320 160 70 9 35 14 8
200 378 320 217 116 50 23 136 73 270-298 391 160 102 11 47 18 8
250 446 392 124 124 - 24 247 121 329-355 - 200 - - 51 18 12
300 535 470 124 124 - 28 297 121 384-427 - 200 - - 52 18 12
DN40-200 DN250-300
5. DIMENSIONS.
T 5.1
Fig. 2
Fig. 3
Conception du
robinet
Dimensions bridage Connexions pour
robinets
Autres connexions Raccord actionneur (en
option)
ISO 16136: 2005 EN 558-1,ANSI B16.5 Class 150,JIS B2220, BS/E EN 1090-1 ISO15494, ISO15493, ISO10931 EN/ISO 5211
Diagramme de pertes de charge (G 4.3)
Tableau des pertes de charge (T4.1) Kv / Degré d'ouverture. (G 4.2)
(T4.3)Tableau de couple de manœuvre

17
FRANÇAIS VANNE PAPILLON EXTREME
6. INSTALLATION ET MISE EN SERVICE
Avant d’installer le robinet, vériez que vous disposez bien de tous les éléments nécessaires et que les matériaux, le type de
raccordement et la pression nominale correspondent bien à l’installation. En cas de raccordement par collage ou soudure, assurez-
vous que les matériaux à raccorder sont identiques et que la colle ou les outils de soudure sont appropriés.
Pour xer le robinet, appliquez les recommandations de bonnes pratiques disponibles sur le site Web de Cepex, en faisant
particulièrement attention aux dilatations thermiques et à l’alignement des tuyauteries.
Lors du remplissage des tuyauteries du uide à transporter, vériez la purge de tout l’air de l’installation et veillez à ce que la pression
initiale ne soit pas supérieure à la pression nominale du robinet ou de l’élément de plus faible pression nominale de l’installation.
Montage du robinet au moyen des brides normalisées ISO-DIN, ANSI, JIS et BS/E. Dans le raccord, aucun joint plat n’est nécessaire
pour les manchons, car ils sont intégrés dans le robinet lui-même. Tenez compte de l’ordre de serrage (Fig. 5) des vis sur les brides
et du couple maximum de serrage. Il est indispensable d’installer la totalité des vis pour garantir le bon fonctionnement du robinet.
Les manchons de PP / PE de soudure en bout doivent être biseautés selon le schéma (Fig. 6) et le tableauT6.2 pour garantir une bonne
fermeture et ouverture du corps.
Installez le robinet une fois que les manchons de raccordement sont collés et secs pour éviter tout problème avec l’adhésif
(introduction du même adhésif dans le robinet).
Les brides doivent être bien centrées dans le robinet (surtout, attention aux mesures DN100-DN125 et DN200). Un mauvais alignement
de l’ensemble pourrait provoquer des problèmes de fonctionnement du robinet.
D DN inch Screws (A2) Torque
(N·m)
Torque
(inch·lbs)
40 50 - 4xM16x120 25 221
63 50 - 4xM16x120 25 221
75 65 2 1/2” 4xM16x140 25 221
90 80 3” 8xM16x150 25 221
110 100 4” 8xM16x160 30 265
125 125 - 8xM16x170 35 310
140 125 5” 8xM16x170 35 310
160 150 6” 8xM20x200 40 354
200 200 - 8xM20x210 50 442
225 200 8” 8xM20x230 50 442
250 250 - 12xM20x270 80 708
280 250 10” 12xM20x270 80 708
315 300 12” 12xM20x310 80 708
Vis et couple de serrage de vis
DN D min. x
40 31 30º
65 50.5 30º
80 70 30º
100 91.5 30º
125 113 30º
150 141 30º
200 191.5 20º
250 226 20º
300 296.5 20º
Fig. 4
Fig. 5
Fig. 6 Dimensions
du tube et des
biseaux
Manchons PP/PE
T 6.2
T 6.1

18
FRANÇAISVANNE PAPILLON EXTREME
Fig. 7 Fig. 8
Fig. 9
7. CONSIGNES DE FONCTIONNEMENT ET DE MAINTENANCE
Il est recommandé de réviser régulièrement l'état du joint puisqu'il est soumis à une usure mécanique provoquée par les pressions,
la manipulation et le contact avec le uide. Il est recommandé de graisser le joint dans la zone de contact avec le corps (avec de
la graisse compatible avec les matériaux du joint et du corps). Il est également conseillé de réviser régulièrement le serrage des
écrous de xation des brides pour vérier que le couple correspond bien à la valeur indiquée dans ce manuel (T6.1).
Pendant de longues périodes d'inactivité, et à condition que l'installation le permette, laissez le robinet légèrement ouvert.
Le réducteur manuel n'a besoin d'aucune maintenance et il est graissé à vie.
Pour actionner le robinet, on débloquera la manette (13) en enlevant le goujon (16) et en appuyant sur la poignée (15) vers le haut,
ce qui libèrera les dents du répartiteur (17) et on tournera la manette dans le sens approprié.
Pour bloquer le robinet, placer le goujon (16) et, en option, sécuriser avec un verrou.
7.2 Montage et démontage de la manette
Pour monter la manette :
•Monterlamanettedansl'axetoutenappuyantsurlecliquetd'arrêt.L'orientezdefaçonàceque,avecle
robinet fermé, l'indicateur de la manette indique 90º sur le répartiteur (17).
•Montezlarondelle(14),lavis(22)etlechapeau(19).
Pour démonter la manette :
•Enlevezlechapeau(19)delamanette,lavis(22)etlarondelle(14).
•Appuyezsurlecliquetd'arrêt(15)aumaximumverslehautdesortequesesdentslibèrenttotalement
les dents du répartiteur (17) et enlevez la manette de l'axe (6).
7.1 Opérations pour le changement de joint du corps
Au cas où il serait nécessaire de changer le joint du robinet, procédez de la façon suivante :
•Veillez à ce qu'il n'y ait pas de pression dans le système, en libérant la pression et en vidangeant les
conduits, selon les normes de sécurité spéciques à chaque produit. Contrôler aussi la température
du uide et suivez les normes de sécurité.
•Démontezlerobinetdel'installation.
•Enlevezlamanetteselon7.2,lesvis(20),lesécrous(21)etlerépartiteur(17).
•Retirezl'anneauélastique(8).Enlevezlechapeau(7)etretirezl'anneau(12).
•Tapezsurl'axe(6)avecunemasseennylonjusqu'àcequeladouille(4)sorteparlebas(Fig.7).
•Unefoisladouillesortie,retirezl'axe(6),faites-letourneretréintroduisez-le(Fig.8)danslapartiein-
férieure.
•Tapezdenouveaujusqu'àcequelesdouilles(4et5)sortentlehaut.Retirezànouveaul'axe.
•Enlevezlecorpsenappuyantdanslesensduuide.
•Enlevezlejoint.Montezlenouveaujoint;ildoitentrerdéformé,etplacez-ledefaçonàcequ'ilsoit
centré avec l'axe, en utilisant l'onglet d'indication du matériel (Fig. 9.
ATTENTION : avant de monter le nouveau joint, révisez l'état des joints toriques (9 et 11).
9. GUIDE DES PROBLÈMES LES PLUS FRÉQUENTS T 9.1
PROBLÈME CAUSE SOLUTION
Le corps ne s'ouvre pas ou ne
se ferme pas complètement.
Les manchons n'ont pas été correctement
biseautés.
Démonter le robinet et biseauter les manchons
selon T6.2. Vérier l'état du corps.
Corps étrangers dans le compartiment (adhésif,
etc.).
Démonter le robinet et vérier les obstructions
dans la zone de contact du corps avec le joint.
Couple d'ouverture ou de
fermeture excessif
Le robinet a été trop longtemps inactif. Actionnement avec une clé auxiliaire (pas la
manette).
Démonter le robinet et lubrier le joint.
Détérioration du joint par excès de température ou
par attaque chimique.
Réviser la compatibilité chimique du uide avec le
corps et la température de travail. Changer le joint.
Couple de bridage excessif. Brider selon le paragraphe 6.
Défaut d'alignement entre manchons et robinet. Démonter le robinet et le remonter avec
alignement concentrique (respecter l'ordre et le
couple de serrage).
Le robinet ne présente pas
une étanchéité complète
au niveau des manchons de
raccordement.
Défaut d'alignement entre manchons et robinet. Démonter le robinet et le remonter avec
alignement concentrique (respecter l'ordre et le
couple de serrage).
Absence de serrage des vis de bridage. Brider selon le paragraphe 6.
Le robinet ne présente pas
une étanchéité complète au
niveau du joint.
Éléments chimiques inappropriés.
Température hors valeurs.
Excès de pression.
Conduite d'éléments abrasifs.
Vérier le respect des caractéristiques techniques
de ce document.
Joint endommagé. Changer le joint.

19
PORTUGUÊS VÁLVULA DE BORBOLETA EXTREME
1. DEFINIÇÃO
Válvula de borboleta para interrupção ou regulação do caudal nos sistemas de condução de líquidos. Permite que o líquido circule em
ambos os sentidos. Desenhada com base na norma ISO EN 16136 em conformidade com a Diretiva.
A válvula está disponível com comportas fabricadas em PVC-U, PVC-C, PP-H, PVDF e ABS e com juntas de EPDM e FPM (FKM). A escolha
do material da comporta e da junta depende do tipo de líquido a transportar e da temperatura de funcionamento, de acordo com as
tabelas de resistência química disponíveis no nosso site e o esquema de pressão/temperatura do presente manual (G4.1).
2. ADVERTÊNCIAS
• Ler estas instruções antes de manipular a válvula e seguir as recomendações aqui mencionadas. Os danos causados pelo não segui-
mento destas instruções não estarão cobertos pela garantia.
• As operações de conexão e manipulação deverão ser realizadas por pessoal qualicado.
• A vida útil máxima da válvula é a especicada na norma EN ISO 16136. É testada em fábrica através de testes de envelhecimento
especicados na norma.
• O cumprimento da vida útil está condicionado pela instalação e manipulação correta da válvula, e pelo seguimento das condições
técnicas de pressão e temperaturas máximas especicadas neste mesmo manual.
• O líquido conduzido deverá ser compatível com os materiais da válvula. Consultar as tabelas de resistência químicas publicadas pela
Cepex ou consultar o departamento técnico.
• Não se recomenda a utilização de ferramentas para a manipulação do comando manual de abertura e fecho da válvula. Esta operação
deve ser realizada manualmente.
• Antes de realizar alguma operação de manutenção sobre a conduta ou válvula, assegurar-se de que não existe pressão no sistema,
libertando a pressão e esvaziando as condutas, seguindo as normas de segurança especícas para cada produto.
• Rodar a alavanca com o encravamento posicionado poderá provocar danos na válvula.
• Evitar golpes durante o transporte que possam danicar o corpo e o mecanismo. Manter a válvula armazenada na embalagem origi-
nal, protegida da humidade e da exposição direta ao sol.
• Antes da instalação, vericar que a válvula não sofreu danos e que contém todos os elementos necessários para a instalação.
• Após longos períodos de inatividade, examinar a lubricação da junta e seguir as instruções de manutenção contidas no presente
manual. O lubricante deverá ser compatível com os materiais da válvula.
• Tentar evitar os golpes de aríete causados por um manuseamento brusco da válvula, que poderão provocar danos na instalação.
• Caso se utilize a válvula como nal de linha, dever-se-á ter em consideração o risco do líquido, consoante as normas de segurança do
produto e controlar a pressão e a temperatura.

20
PORTUGUÊS
VÁLVULA DE BORBOLETA EXTREME
27
28
30
29
31
32
33
(T3.1)
Fig. 1
NDESCRIÇÃO MATERIAL DN65-
DN200
DN250-
DN300
1 Corpo PP-GR 1 1
2 Junta EPDM / FPM 1 1
3 Comporta PVC-U/PPH/CPVC/PVDF/ABS 1 1
4 Casquilho POM 1 1
5 Casquilho POM 1 1
6 Casquilho auxiliar POM 1 1
7 Eixo AISI 630 / AISI 316L / AISI 904L 1 1
8 Tampão PP 1 1
9 Anel DIN-471 AISI-304 1 1
10 Junta tórica EPDM / FPM 2 4
11 Junta tórica EPDM / FPM 2 4
12 Anilha POM (DN 65 AISI-304) 1 1
13 Junta tórica EPDM / FPM 2 4
14 Parafuso DIN-912 AISI-304 1 1
15 Alavanca PP-GR 1 -
16 Anilha AISI-304 1 -
17 Trava PP-GR 1 -
18 Filtro AISI-304 1 -
19 Mola izquierda AISI-304 1 -
20 Mola derecha AISI-304 1 -
21 Separador PP-GR 1 -
22 Encravamento POM 1 -
23 Tampão da alavanca PP 1 -
24 Parafuso DIN-912 AISI-304 2 2
25 Porca DIN-934 AISI-304 2 2
26 Parafuso DIN-912 AISI-304 1 -
27 Reducor manual Aluminio (carcasa) - 1
28 Flange de xação PP-GR - 1
29 Casquilho união AISI-303 - 1
30 Anilha DIN-125 AISI-304 - 4
31 Porca DIN-934 AISI-304 - 4
32 Parafuso DIN-912 AISI-304 - 4
33 Parafuso DIN-912 AISI-304 - 4
4. CARACTERÍSTICAS TÉCNICAS
DN65-DN200 (2½”-8”): PN10 (150 psi) a 20 ºC de temperatura do líquido.
DN250-DN300 (9”-12”): PN6 (90 psi) a 20 ºC de temperatura do líquido.
A pressão de serviço da válvula reduz-se quando a temperatura do líquido aumenta, tal como ilustrado pelos dois grácos em anexo.
Binário máximo à saída do redutor manual = 500 N·m
(Redução = 37:1).
4
Temperatura
Presión
psi bar
ºC
ºF
Temperatura
Presión
4
psi bar
ºC
ºF
3. COMPONENTES
Esquema de Pressão/Temperatura. (G 4.1)
Other manuals for EXTREME Series
3
Table of contents
Languages:
Other Cepex Control Unit manuals
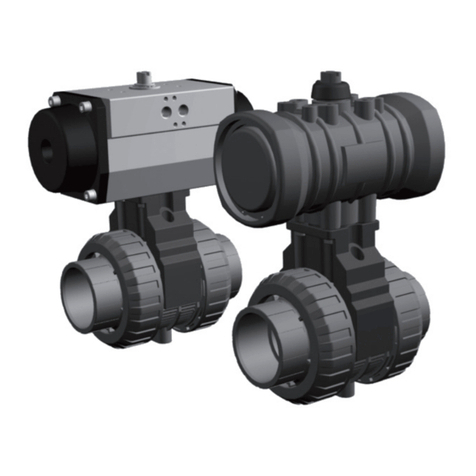
Cepex
Cepex EXTREME Series Manual
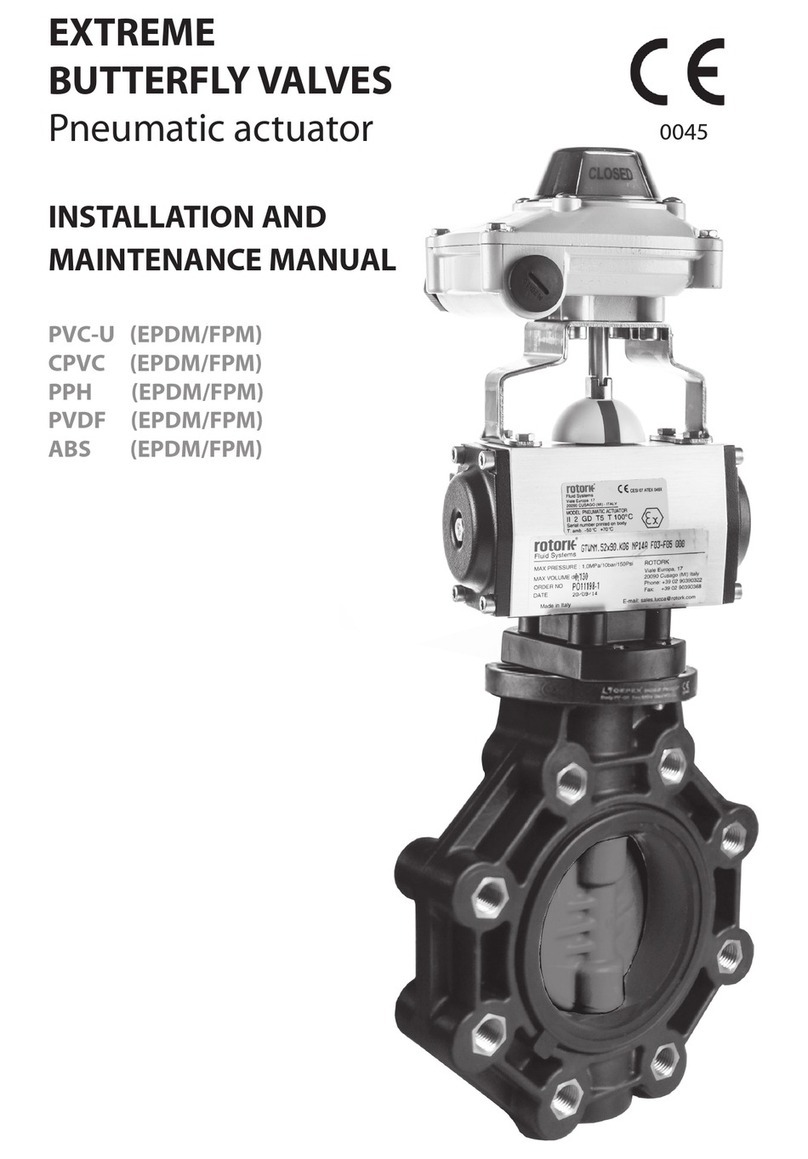
Cepex
Cepex EXTREME Series Manual
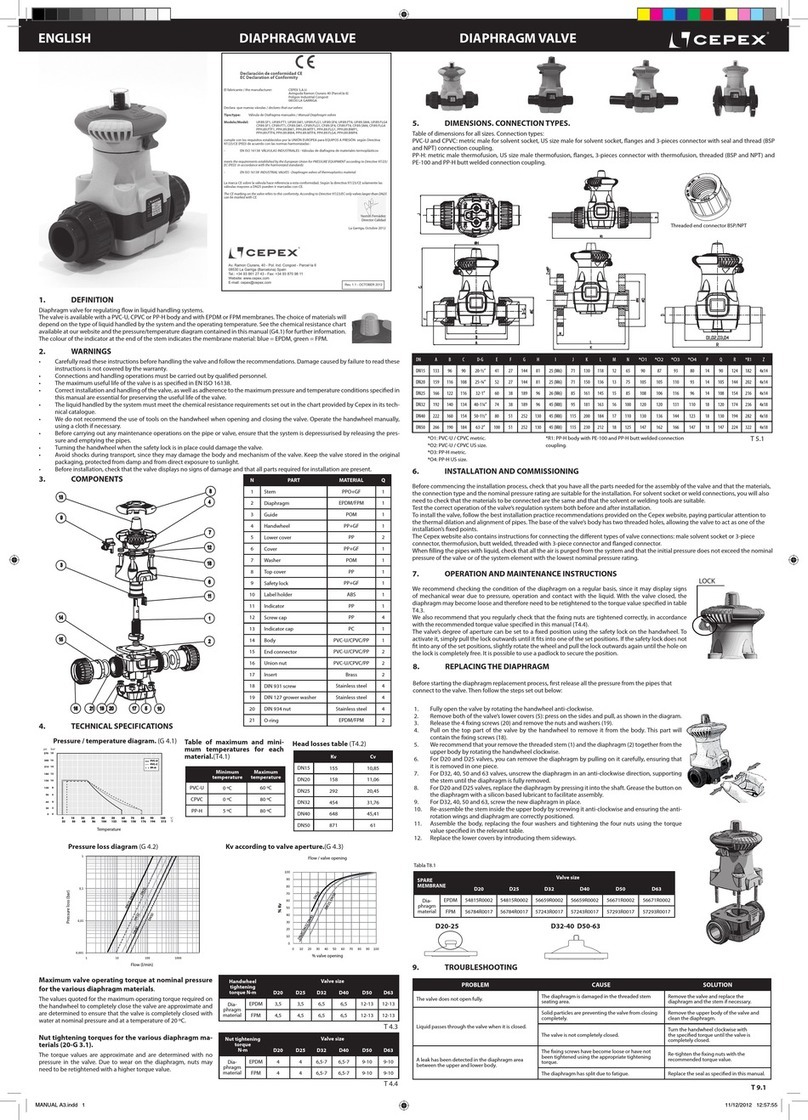
Cepex
Cepex DN15 User manual
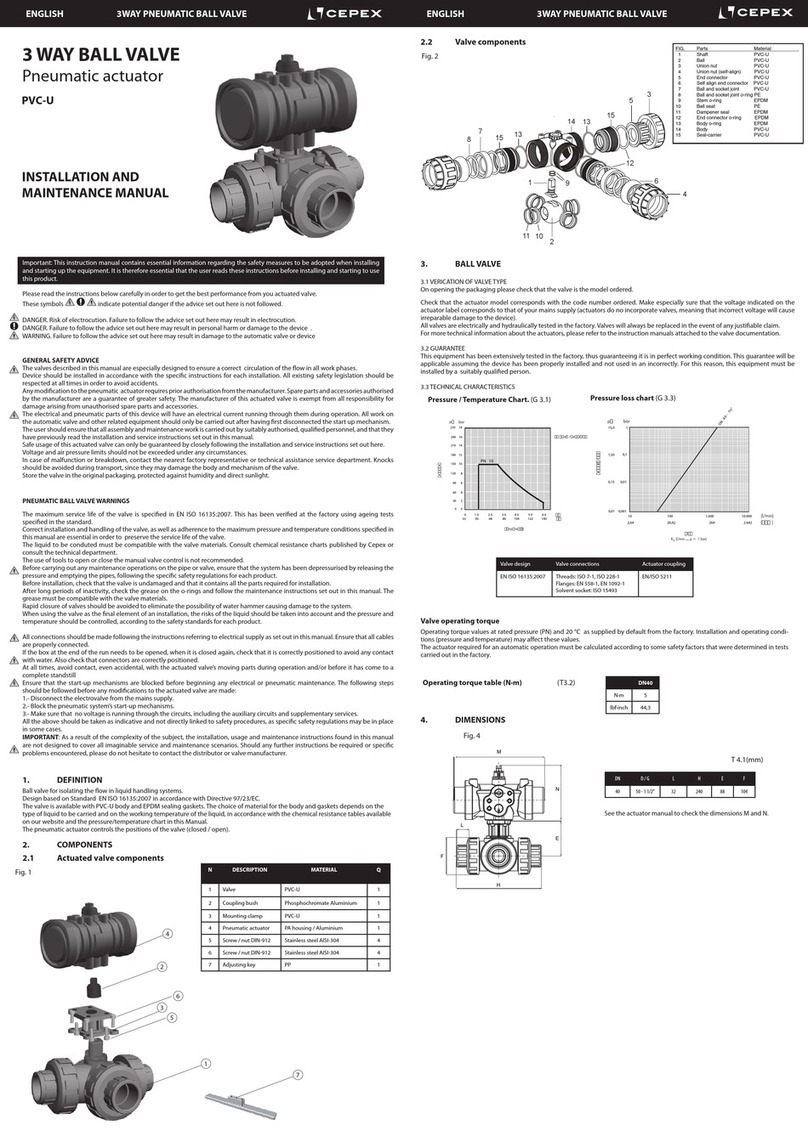
Cepex
Cepex PVC-U Manual
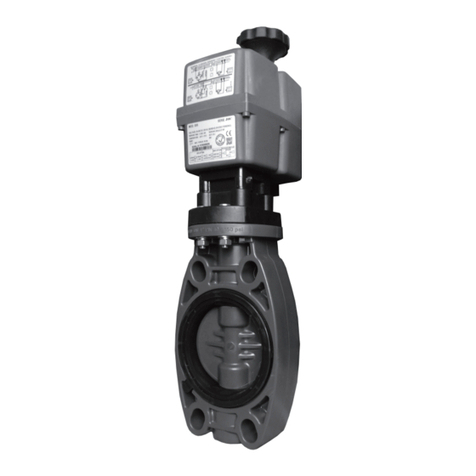
Cepex
Cepex STD Manual
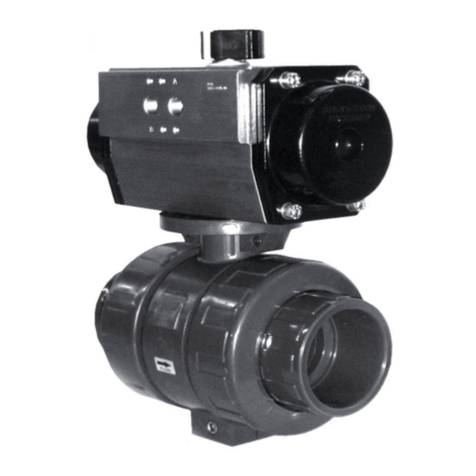
Cepex
Cepex PVC-U Series Manual

Cepex
Cepex EXTREME Series Manual
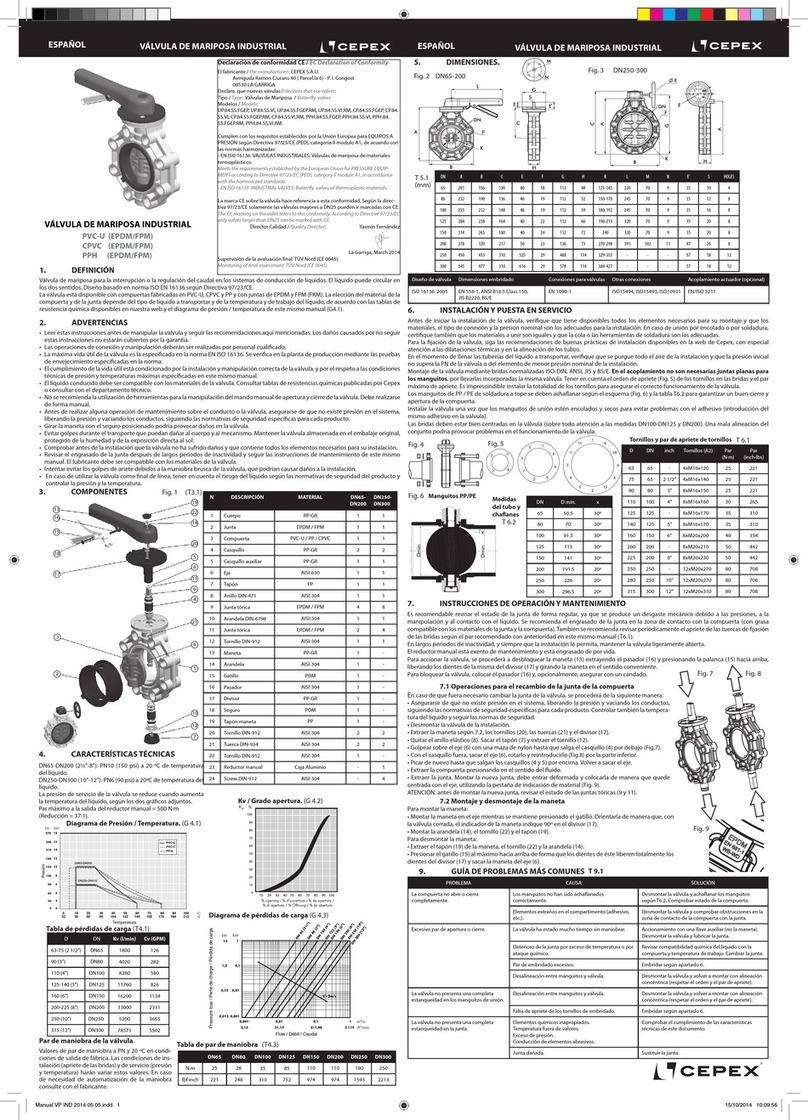
Cepex
Cepex PVC-U Series User manual
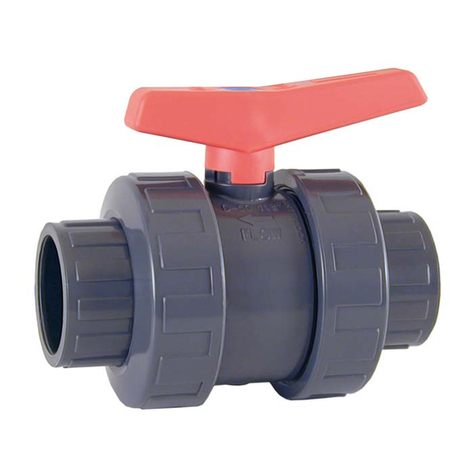
Cepex
Cepex Industrial Series User manual
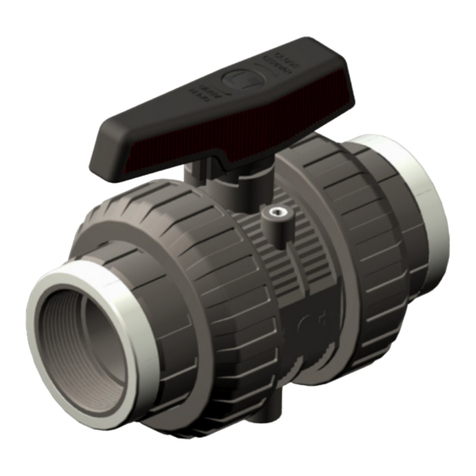
Cepex
Cepex PVC-U User manual
Popular Control Unit manuals by other brands
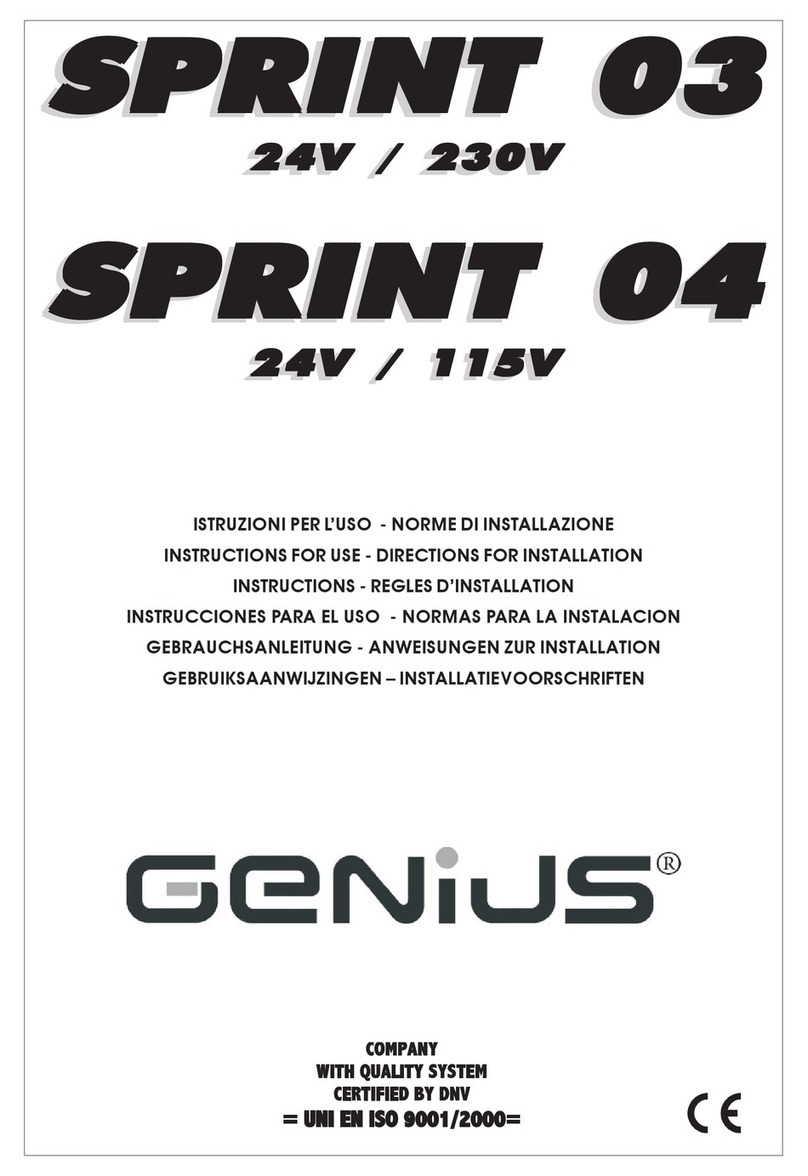
Genius
Genius SPRINT 03 Instructions for use
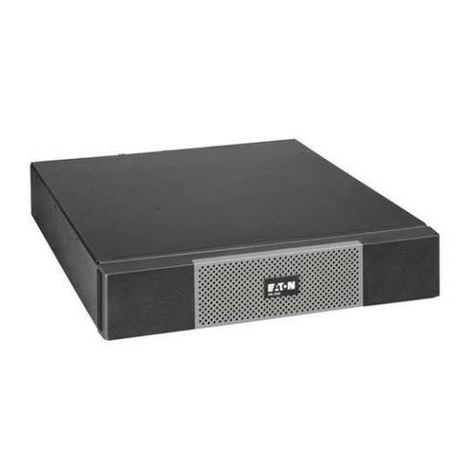
Eaton
Eaton 5PX EBM 72V RT2U installation manual
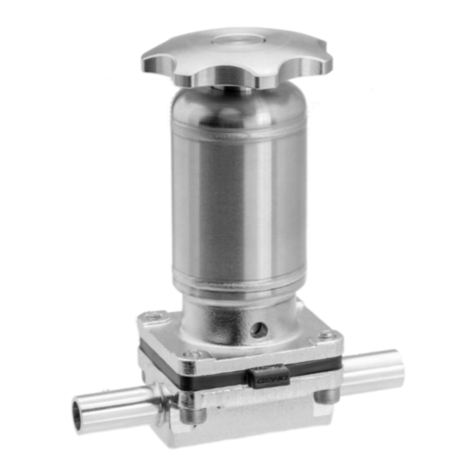
GEM
GEM 616 operating instructions
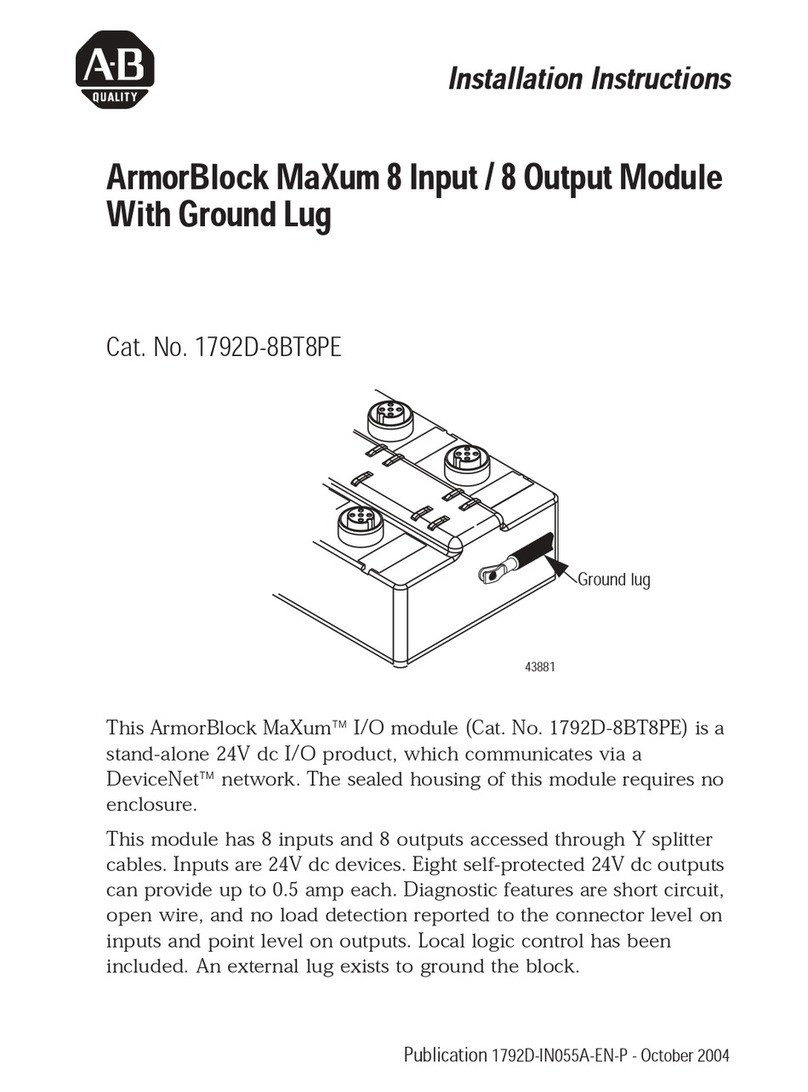
Rockwell Automation
Rockwell Automation ArmorBlock MaXum 1792D-8BT8PE installation instructions
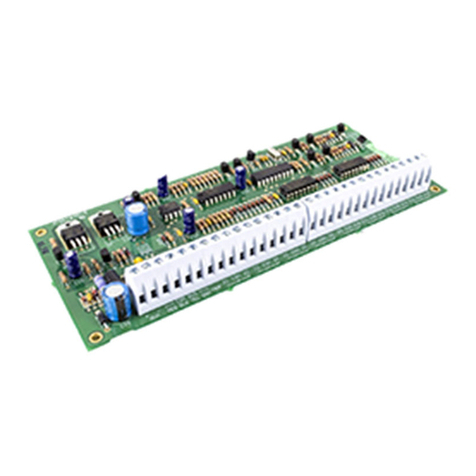
DSC
DSC Maxsys PC4116 installation instructions
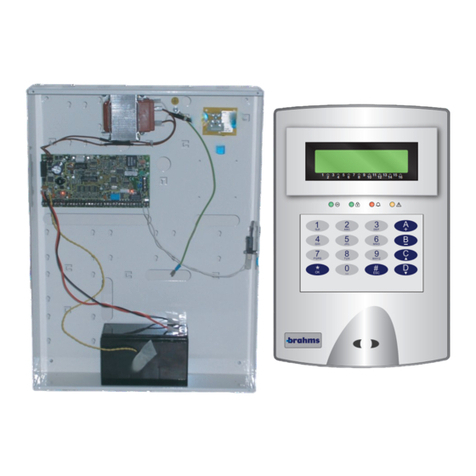
Bra
Bra Proxinet 36-76-192 installation manual