Collamat 9100 Release Note

CCollamatollamat®91009100
Technical handbook
Collamat Stralfors AG CH-4147 Aesch Pfeffingerring 201 Tel +41 61 756 28 28 Fax +41 61 756 29 29
5999.555-01A

Index
Page
Important warnings 3
Danger notes 3
Explanation of symbols 4
Introduction 5
General informations 5
The monitor 5
The labeller 6
The Collamat®9100 Labeller 7
Prevention of accidents 7
Assemblies 8
Installation examples 9
Traction unit 10
Pinch roller 11
Exchange of the pinch roller 12
Parallel adjustment of the pinch roller 13
Traction roller 14
Rewinder and unwinder 15
Arrangement and mechanical adjustment of rewinder 18
Installation and mechanical adjustment of unwinder 20
Electrical settings 21
Midi-unwinder 23
Flap adapter 24
Support 24
Flap 25
Exchange of mirror 26
Roller dispenser edge (option) 27
Optical label scanner 28
THE MONITOR 9100 29
Construction 29
The control panel 30
Construction 31
Firmware memory IC6, EPROM 128 Kbytes 32
The LCD-Display 32
The back panel 33
The mains filter p.c.board 34
The interface p.c.board 35
The power supply 35
Fuses 36
Terminals and connectors 37
The motor driver 38
The connector box 9100 39
Fuse F1, 5A slow blowing 40
Control signals for external units 40
5999.555-01A 20.08.98 WM Page 1/ 64

Index
Page
Signals and connector pin assignments 41
Inputs 41
Photocoupler inputs 41
Comparator inputs 42
Functional description of inputs 42
Outputs 44
Isolated outputs 44
Open collector outputs 45
Description of output function 46
Connection of a signalisation to the monitor 46
Monitor C9100 pin assignment 48
Connector X3, LABELLER 48
Connector X5, GSC 49
Connector X7, CONTROL SIGNALS 49
How to connect the goods scanner 50
Nonstop labelling 51
Incremental encoder 53
Measuring goods scanner 53
Motor and motor cable 54
Control of a hotstamp printer with the IFEED signal 55
Control of flap adapter 56
Testing the monitor with the diagnosis connector 57
Cabling and putting into operation 57
Fuses 59
Glossary 59
Technical data 61
Trouble shooting checklist 64
5999.555-01A 20.08.98 WM Page 2/ 64

Important warnings
Before installing and operating the Collamat®9100 read the following
safety instructions.
The Collamat®9100 labeller is exclusively intended for labelling goods. It must
exclusively be controlled and driven by a C9100 monitor.
Install the Collamat®9100 only by a trained specialist considering the national
specific regulations of
prevention of accidents
mechanical stability
construction of electrical and mechanical systems
noise suppression
Take notice of the technical data of the Collamat®9100. Especially the environ-
ment conditions must be observed.
Operate the Collamat®9100 only by trained personnel.
In case of non-authorized modifications the guarantee will become void.
Before connecting non-standard products, ask your competent technical
supporter.
Danger notes
The safety symbols and danger advices on the Collamat®9100 and in this ma-
nual must strictly be observed.
Switch the monitor C9100 off before connecting or disconnecting the labeller
to or from the monitor C9100.
Only authorized personnel may open the monitor and the connector box.
Disconnect the monitor from the mains before opening the connector box.
Danger of pinching hair, jewelry, ties, clothes etc. into the traction unit !
Danger of injury by cutting fingers in the paper zone !
Danger of injury in the dancer roller zone of the Collamat®9100 rewinder and
unwinder !
Danger of injury in the case of non-expert use of the Collamat®9100 paper
stock control !
When operating the labeller, the operating personnel must keep to a safe loca-
tion to prevent injury by the products being labeled.
5999.555-01A 20.08.98 WM Page 3/ 64

Symbol descriptions
ATTENTION
Danger to damage the Collamat®9100 or other system compo-
nents, with a potential consequential danger of injuries.
DANGER
Imminent hazard for persons.
DANGER
Shock hazard due to high voltage at component.
DANGER
Hazard of contact injury due to high component temperature.
ATTENTION
ESD (ElectroStatic Discharge) warning. The p.c.boards or other
components may only be touched in an electrostatically pro-
tected environment.
NOTE
Important or additional information to Collamat®9100 or its
documentation.
5999.555-01A 20.08.98 WM Page 4/ 64

Introduction
General information
This Technical Manual describes design and function of the Collamat®9100. In addition
to the Operating Instructions, it contains the settings and notes necessary to get opti-
mum use of the Collamat®9100. The descriptions of each electrical or mechanical as-
sembly also help for quick error analysis and trouble-shooting.
We recommend to replace p.c.boards always as complete units returning them to Colla-
mat Stralfors AG or its representative for repair to be sure that the high quality standard
of the Collamat®9100 can also be guaranteed after any repair.
Special characteristics of the Collamat®9100:
resistant to wear, no clutch/brake-system
rugged
easy installation and operation due to modular design
easy to operate due to up-to-date menu operated software
quick change-over to other labelling tasks
high performance
high reliability and accuracy
latest SMD-technology
high precision 3-phase steppermotor
The Monitor
The power supply and the electronic control are built into a stable metal casing. All peri-
pherals are connected to a connector box connected to the monitor back panel by one
single D-sub-connector. A large heatsink allows to operate the monitor without additio-
nal fan. The control (monitor) can be mounted in various positions.
The monitor contains the following assemblies:
Noise filter with voltage selector
The noise filter keeps EMI outside to prevent any interference with the electronic
control and also prevents EMI to be transmitted to the mains supply. The voltage se-
lector allows versatile adaptation of the power supply to different mains voltages.
Transformer
Supplies the power for all components of the Collamat®9100.
Interface p.c.board
The interface p.c.board connects the motor driver to the power supply and to the
controller. The electronic part of the power supply is also installed on the interface
p.c.board which shapes all input and output signals to and from the controller.
5999.555-01A 20.08.98 WM Page 5/ 64

Motor Driver
The 3-phase motor driver is a standard assembly of a leading stepper motor. It ener-
gizes the stepper motor. The step rate is adjustable from 200 up to 1000 steps per
revolution. Standard setting is 500 steps per revolution.
Controller p.c.board
The controller p.c.board comprises a Hitachi H8/532 microcontroller, EPROM with
software, LC-display and short-stroke keyboard. The controller p.c.board controls all
labelling sequences, the LC-display, the keyboard and the nonvolatile memory.
The LC-display has four lines with 20 characters each and a background illumination.
The controller p.c.board combines front panel and controller in one component.
The software
The controlling software of the Collamat®9100 is stored in the EPROM (firmware) and
has the following features:
Modern user guidance
6 digits preselection and batch counter
Adjustable label length dependent suppression of label scanner signal to detect
transparent or preprinted labels
Adjustable goods speed and length dependent scanner signal suppression after
labelling
Programmable adjustment of labelling position on the goods
Programmable adjustment of predispensing
Multiple labelling with electronic setting of gap between labels
Automatic adaptation of dispensing speed by measuring the goods speed by light
barrier or incremental encoder
Storage of 20 labelling programs
Memory protection by access password
Two user levels
Monitoring of label stock and out-of-label, end of paper web, open roller in traction
unit, motor driver OK-signal
Nonstop mode with two Collamat®9100 systems
Multilingual user display
Automatic label scanner adjustment
Full operability during labelling
All peripherals program-controlled - no potentiometers and switches necessary
The Dispenser
The traction unit as well as the other peripherals are mounted on a module rail. All parts
are surface treated to protect from corrosion. The special coating of the traction unit rol-
ler affords permanent torque transmission to the paper web without slip. The force of
the paper web brake is adjustable. The traction roller can be easily turned by hand du-
ring Power OFF for easy threading and installing the paper web.
5999.555-01A 20.08.98 WM Page 6/ 64

The Collamat®9100 Labeller
The Collamat®9100 must be installed by trained personnel considering the following
national specific regulations:
Prevention of accidents
Noise suppression
Mechanical stability
Construction of electrical and mechanical systems
Prevention of accidents
When installing and connecting the C9100 monitor and labeller pay attention that the
signal and power cables cannot become stumble obstacles. Lay the cables according to
the national safety regulations. Signal cables must not be placed in close proximity to
power cables.
Noise suppression
For radio interference suppression the C9100 labeller and monitor are shielded accor-
ding to the CE directives. Only cables approved by Guhl & Scheibler are allowed to be
used to connect the monitor to labeller and mains. Additional peripherals have to be
connected only to the mains socket of the monitor. These devices must be approved by
Guhl & Scheibler.
Mechanical stability
If the Collamat®9100 is used on a movable stand, this stand must be capable to be til-
ted by 10° in each direction. See Figure 1:
Figure 1: Mechanical stability of C9100 labeller stand
10° 10°
5999.555-01A 20.08.98 WM Page 7/ 64

Assemblies
In the following the various assemblies, their adjustment and maintenance are descri-
bed. First an overall view of the labeller.
The assemblies are mounted on a module rail. Figure 2 shows these assemblies with
their designations on the module rail:
Figure 2: Assemblies
Legend for assemblies
1. Rewinder
2. Unwinder
3. Modular rail
4. Connector box
5. Traction unit
6. Support
7. Flat printing unit (optional)
8. Adapter (optional with magnet)
1 2 3 6 7 8
45
5999.555-01A 20.08.98 WM Page 8/ 64

Installation examples
Due to the modular design of the Collamat®9100 there is nearly no limit in variations of
the installation. But for best results in labelling, the following figures show installation
examples of constructions which do their work successfully:
Figure 3: 1st example
Figure 4: 2nd example
Figure 5: 3rd example
The threading of the paper web, the adjustment of the paper brake and
adapter are described in the Operating Instructions of the Collamat®
9100 labeller.
5999.555-01A 20.08.98 WM Page 9/ 64

Traction unit
General information
The traction unit can be used both for right- and left-hand versions of the labeller.
Figure 6: Traction unit
Legend for traction unit
1. Paper break
2. Pinch roller
3. Traction roller
4. Stepper motor
5. Paper web guide
6. Module rail
The direction of rotation of the traction roller is set by programming the monitor.
More information see Operating Instructions MONITOR C8600/C9100,
chapter CONFIGURATION, menu DIRECTION OF ROTATION.
Install the paper web guides in position Afor right-hand version, in position Bfor left-
hand version.
B
A
1
4 23
5
6
5999.555-01A 20.08.98 WM Page 10 / 64

Pinchroller
Direction of tension force
The direction of the tension force of the left- and right-hand version are opposite to
each other. If the direction of the tension force is not correct, hits of the rewinder to the
paper web may open the traction unit.
Procedure
Slacken locking screw (2), remove, turn, reengage and screw down knurled washer (1).
Letter 'L' or 'R' defines left- or right-hand version, respectively. Standard version is 'R'.
Figure 7: Direction of the tension force
Legend
1. Knurled disk
2. Locking screw
3. Eccentric pinch roller shaft
4. Pinch roller
5. Adjustment flange
6. Traction roller
1
2
3
4
5
6
5999.555-01A 20.08.98 WM Page 11 / 64

Exchange of pinch roller
The pinch roller is a part subject to wear. Its wearing time is stress-dependent. It is good
practice to select a paper web wider than the pinch roller to avoid wear when the pinch
roller runs directly on the traction roller.
Procedure
Disassemble and remove front panel (1) together with eccentric pinch roller shaft (2).
Do not slacken fixing screw (3). Slacken locking screw (4) and pull off pinch roller (5).
Attach new pinch roller (5), tighten locking screw (4), slide in and reassemble front pa-
nel (1). Then check parallelism with pinch roller.
Figure 8: Pinchroller
Legend
1. Front panel
2. Eccentric pinch roller shaft
3. Fixing screw of knurled knob
4. Locking screw with hexagon socket
5. Pinch roller
6. Traction roller
The parallelism adjustment of the pinch roller is described in the follo-
wing chapter.
1
2
3
45
6
5999.555-01A 20.08.98 WM Page 12 / 64

Parallel adjustment of pinch roller
The parallelism of the pinch roller with the traction roller is decisive for the stability of
the paper transport. If the rollers are not in parallel the paper web will be transported
obliquely through the traction unit resulting in a lateral force on the paper web which for-
ces the web to shift on the dispensing edge and the labels to be dispensed obliquely.
Procedure
Release and shift pinch roller (2) to the left, slacken screw (7) on right adjusting flange
(6), turn adjustment flange (6) by means of 3 mm mandrel (9) appropriately.
Retighten screw (7) and shift pinch roller (2) to the right. Slacken clamping screw (7) on
left adjusting flange (5) and adjust it with the same pressure as the right adjusting flan-
ge (6). Tighten screw (7), reposition and lock pinch roller (2) in center position of tracti-
on roller (8).
Figure 9: Parallelism of pinch roller with traction roller
Legend
1. Front panel 6. Adjusting flange, right
2. Pinch roller 7. Clamping screw
3. Eccentric pinch roller shaft 8. Traction roller
4. Support plate 9. Mandrel
5. Adjusting flange, left
In new traction units the parallelism of the pinch roller to the traction
roller is already correctly adjusted by Guhl & Scheibler.
7
9
152364
8
5999.555-01A 20.08.98 WM Page 13 / 64

Traction roller
Replacement of traction roller and damping disk
Procedure
Remove front panel (1) together with pinch roller (9). Unscrew stud bolt (7) and remove
traction roller (3) from stepper motor-shaft (5). Remove securing ring (8). Remove tracti-
on roller (3) from roller shaft (4) and replace the damping disk (6).
Reassemble the traction unit in reverse order. Tighten stud bolt only after assembly of
front panel.
Figure 10: Replacement of traction roller
Legend
1. Front panel 6. Damping disk
2. Suport plate 7. Stud bolt
3. Traction roller 8. Securing ring
4. Roller shaft 9. Pinch roller
5. Stepper motor 10. Ball bearing
It is important that the traction roller is adjusted with an axial play of
0.3 - 0.4 mm between ball bearing (10) and collar of roller shaft (4).
0.3-0.4
7 6 9 8 10
14325
5999.555-01A 20.08.98 WM Page 14 / 64

Rewinder and unwinder
General information
The motor driven rewinder and unwinder (= winders) are intended to automatically
rewind and unwind the backing paper web. Each winder is supplied with a DC voltage
of 18.....30 Volt. Any deviation of the dancer roller starts the motor automatically. De-
pending on the dancer roller position the electronic system controls the motor current
and thus the rewinding speed. At the end of the backing paper web or if it tears, the mo-
tor will stop automatically after a few rotations in order to avoid an uncontrollable rotati-
on of the motor. The winding force and the dancer roller action direction can be
adjusted with jumpers on the p.c.board of the winder. The direction of rotation can be
changed from outside by a switch. Rewinder and unwinder distinguish themselves only
by dancer roller and winding mandrel.
Construction
Legend
1. Support plate
2. Clamping piece
3. Rotation direction chan-
geover switch
4. DC-motor
5. Brake
6. Winding mandrel
7. Lateral Disk
8. Winder p.c.board
9. Knurled knob
10. Rewinder dancer roller
11. Unwinder dancer roller
12. Cover
Figure 11: Winder
Support plate
The assembly is mounted on a sturdy aluminum support plate (1) guaranteeing a solid
fixing of the winder on the module rail. A cover (12) with a rubber gasket protects the
electronic system and mechanical parts from dirt and humidity.
1
2
3
4
5
6
7
8
9
10
11
12
5999.555-01A 20.08.98 WM Page 15 / 64

Drive
The winding mandrel (6) is driven by a current controlled DC-motor (4) with belt trans-
mission. To avoid an after-running of the winder, an electronic brake (5) is energized as
soon as the motor stops. Therefore a definite start-stop function is guaranteed.
Dancer roller
The dancer roller has two functions: firstly, it represents a paper buffer to quickly supply
or take up the paper web, secondly, to signalize its position via an electro-optical scan-
ner to the electronic control. Due to the adjustable spring force, the paper web tension
can be kept constant (adjustment of the spring force, see Collamat®9100 Operating In-
structions ). The cooperation of dancer roller and electronic control guarantees constant
paper tension for both the unwinder and rewinder. Two different dancer rollers are
available for rewinder and unwinder.
Winding mandrel
Rewinder and unwinder distinguish themselves also by the winding mandrel. The man-
drel of the rewinder is fitted with a clamping bow utilized for a secure and quick detach-
able connection between paper and mandrel.
The unwinder mandrel is additionally equipped with a clamping core for use on paper
rolls with 3" core diameter. The clamping core serves for a reliable transmission of the
torque to the paper roll. Clamping cores with other diameters are also available.
Electronic control unit of winder
This electronic control unit controls the complete unwinding/rewinding process powering
the motor with current as a function of the dancer roller position. The position is optically
measured and electrically decoded. The brake is automatically energized when the mo-
tor stands still.
Adjustments
In the following description of the winder adjustments pay attention to the following
items:
Dancer roller: Motor:
Spring force
Direction of pulling force
Direction of action
Direction of rotation
Pull force (torque)
5999.555-01A 20.08.98 WM Page 16 / 64

Spring tension of dancer roller
Set the spring tension so that the dancer roller can be moved back by the tension force
of the backing paper web. For adjustment push and turn the knurled knob (9) of the
dancer roller shaft with open winder housing to obtain the necessary force. Lock knob in
nearest snap-in hole.
Attention there are two different types of springs namely right-hand and left-hand
spring differing by the direction of rotation and force transmission direction. Choosing
the wrong spring type may cause faults because the spring is not subject to tension but
to pressure, so it might jump out of the snap-in hole. This can generally be noticed after
a few dancer roller deviations. For further information see Collamat®9100 Operating
Instructions.
Pulling direction of dancer roller
Concerning the pull direction two different types of winders are to be distinguished. The
rewinder has to be set so that the paper is always under tension whilst the unwinder
must provide for a full loop. Furthermore, depending on the available space, both win-
ders may be mounted in a different way. In principle, the dancer roller has to be adju-
sted so that the paper web can never be stretched. This applies both for empty and fully
wound mandrels. Furthermore, the direction of action of the rewinder motor has to be
opposed to the direction of the spring tension direction allowing a more exact posi-
tioning of the dancer roller with empty winder mandrel. Set the direction of unwinder
motor rotation, depending on inside or outside wound label roll.
Direction of dancer roller action
The direction of dancer roller action is adjusted on the p.c.board with jumper J1. Nor-
mally, the jumper is already correctly set in factory, but there is a difference between
rewinder and unwinder.
The rewinder motor must start when the dancer roller is released
The unwinder motor must stop when the dancer roller is free
Attention:
If the dancer roller is freely swung out , the free-wheeling limitation be-
comes active and stops the motor after eight revolutions. Therefore eit-
her stop the winder or do not let the dancer roller swing completely
back.
5999.555-01A 20.08.98 WM Page 17 / 64

Direction of motor rotation
Select the direction of motor rotation with change-over switch (3) (Fig.11, page 15) loca-
ted on the support plate (1) behind the lateral disk (7).
Motor torque
The motor torque depends on the kind of winder.
The acceleration of the rewinder must not be high but its pull force acting on the pa-
per web must be constant.
The acceleration of the unwinder must be high and its response time low, but it has
to stop immediately after unwinding.
Adjust the pull force torque on the electronic control unit with jumper J2.
Arrangement and mechanical adjustment of rewinder
The rewinder is placed behind the traction unit on the module rail.
Legend
1. Module rail
2. Traction unit
3. Rewinder
4. Dancer roller
5. Rotation direction chan-
ge-over switch
6. Paper web
Figure 12
The winder is mounted 'under' the module rail (1). The dancer roller (4) pulls the paper
web downwards and the motor turns anticlockwise. Adjust the dancer roller with the
spring so that the force in top position does not become too high. (See Collamat®9100
Operating Instructions.) The dancer roller must not hit the paper web when labelling
with high speed. The direction of action of the dancer roller (4) is the same as that of
the spring force, i.e. when the dancer roller moves downwards, the motor has to start.
The direction of motor rotation is adjusted with the change-over switch (5) behind the
lateral disk.
For LEFT-HAND versions the same instructions apply, however
inverted !
2
1
3
4
56
5999.555-01A 20.08.98 WM Page 18 / 64

ATTENTION:
Adjust dancer roller into top position so that the paper web is never
completely stretched. Otherwise hits on the paper web may open the
traction unit. Best results are obtained when the angle between winder
mandrel and traction unit is an obtuse one. See also Figure 12. A
straight / stretched paper web will cause problems !
Figure 13 shows a second version to mount the rewinder. The rewinder is mounted he-
re 'above' the module rail. Use this kind of mounting only if that according to Figure 12
is not possible for lack of space reasons.
Figure 13
Adjust the spring tension of the dancer roller so that it can carry the paper web up to the
upper stop. The dancer roller must move automatically completely upwards (left stop)
when there is no paper. The motor turns clockwise. Be careful that the paper is never
fully stretched.
For LEFT-HAND versions the same instructions apply, however
inverted !
Right stop = clockwise
5999.555-01A 20.08.98 WM Page 19 / 64
Other manuals for 9100
3
Table of contents
Other Collamat Label Maker manuals

Collamat
Collamat 8600 User manual
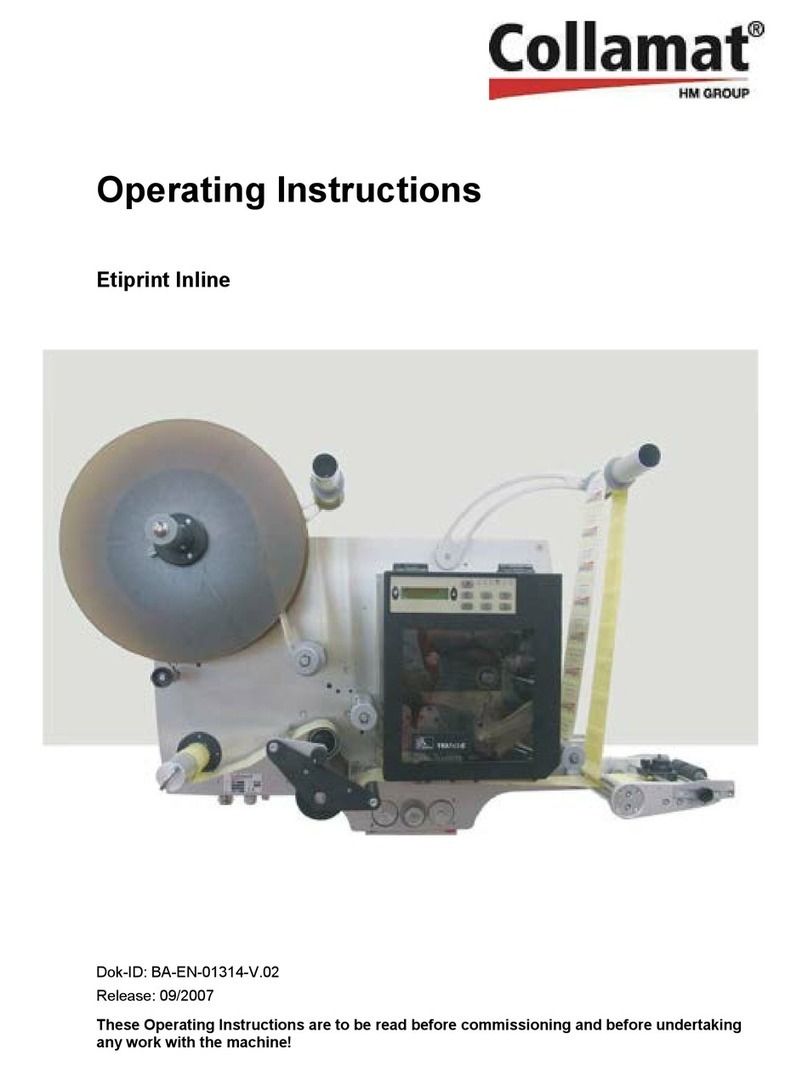
Collamat
Collamat Etiprint Inline User manual
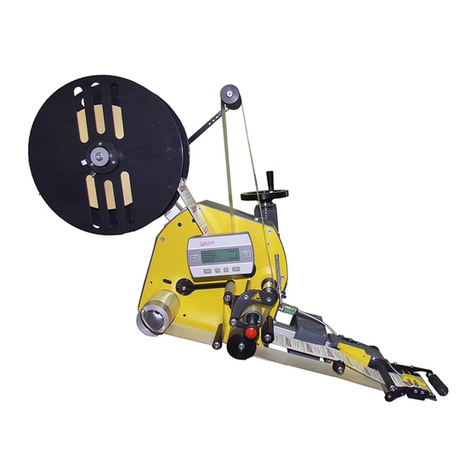
Collamat
Collamat S Series Release Note

Collamat
Collamat 8600 Release Note

Collamat
Collamat 6600 Release Note

Collamat
Collamat 2600 User manual
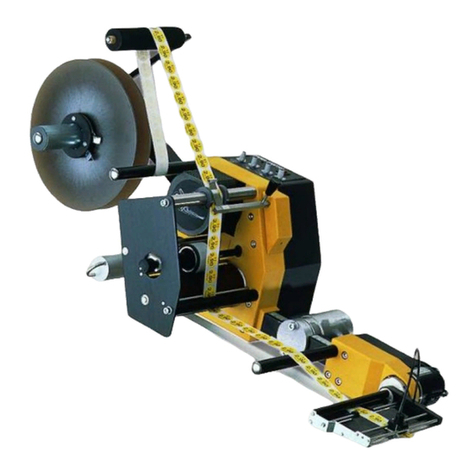
Collamat
Collamat C4300 Series Release Note
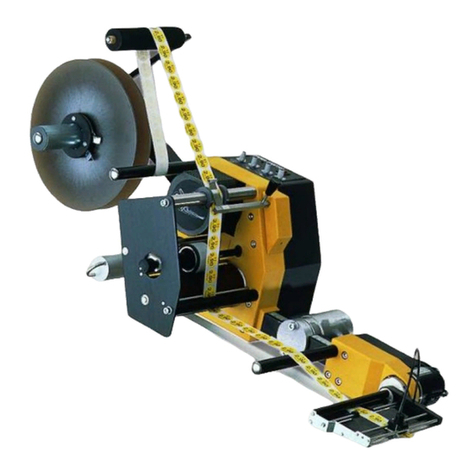
Collamat
Collamat C4300 Series User manual
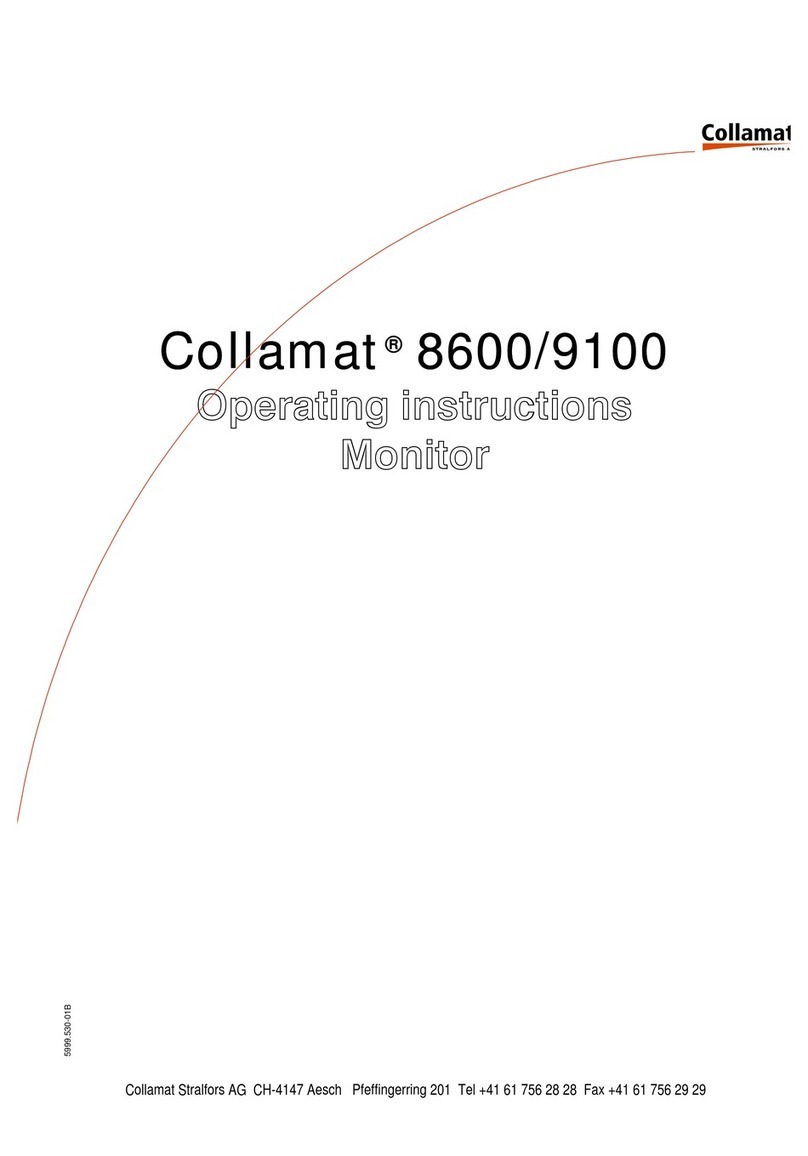
Collamat
Collamat 8600 User manual
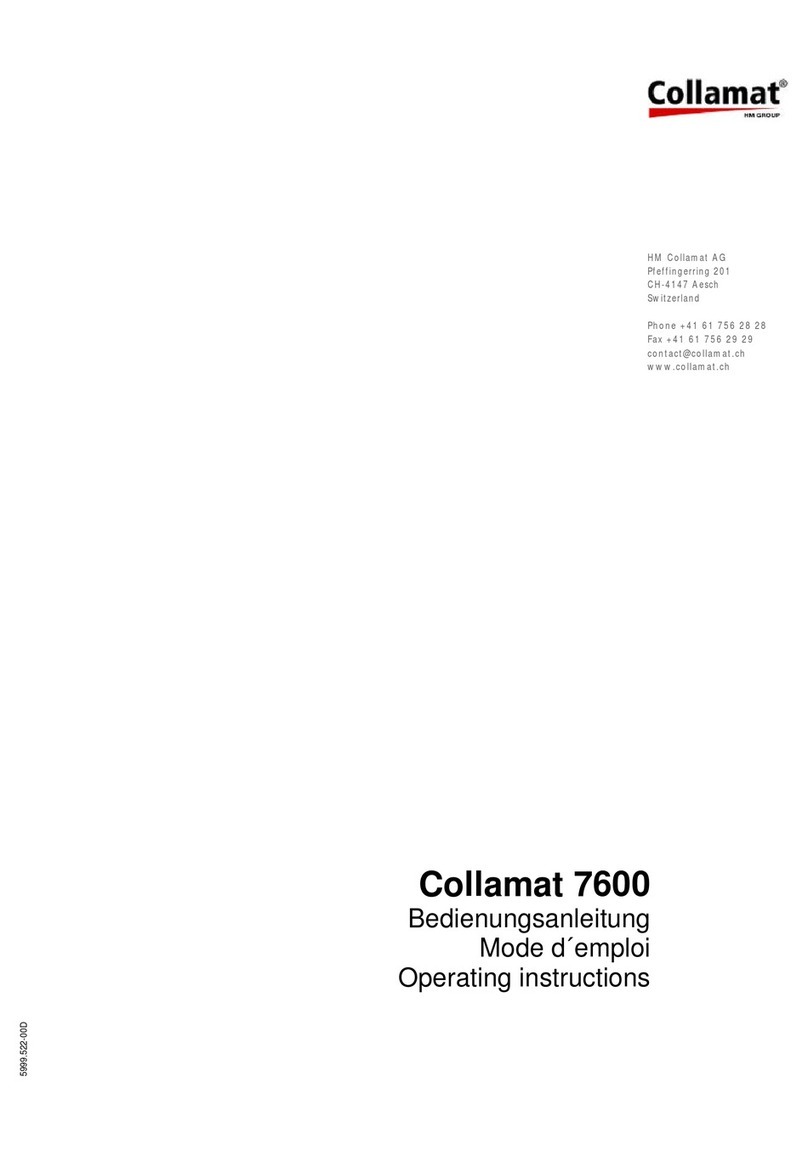
Collamat
Collamat 7600 User manual