dacell DN-10 User manual

Ver 4.0
MODEL : DN-10
DIGITAL INDICATOR
User’s Manual
DACELL CO.,LTD.
Address : 681-1 Cheoksan -Ri ,Nami - Myeon ,
Cheongwon - Gun ,Chung-Buk,Korea
TEL : 82-43-260-2242
FAX : 82-43-260-2245
http://www.dacell.com
E-Mail : [email protected]

Contents
1. Features ⋅⋅⋅⋅⋅⋅⋅⋅⋅⋅⋅⋅⋅⋅⋅⋅⋅⋅⋅⋅⋅⋅⋅⋅⋅⋅⋅⋅⋅⋅⋅⋅⋅⋅⋅⋅⋅⋅⋅⋅⋅⋅⋅⋅⋅⋅⋅⋅⋅⋅⋅⋅⋅⋅⋅⋅⋅⋅⋅⋅⋅⋅⋅⋅⋅⋅⋅⋅⋅⋅⋅⋅⋅⋅⋅⋅⋅⋅⋅⋅⋅⋅⋅⋅⋅⋅⋅⋅⋅⋅⋅⋅⋅⋅⋅⋅⋅⋅⋅⋅⋅⋅⋅⋅⋅⋅⋅⋅⋅⋅ 2
1-1. Sigma-Delta Conversion System ⋅⋅⋅⋅⋅⋅⋅⋅⋅⋅⋅⋅⋅⋅⋅⋅⋅⋅⋅⋅⋅⋅⋅⋅⋅⋅⋅⋅⋅⋅⋅⋅⋅⋅⋅⋅⋅⋅⋅⋅⋅⋅⋅⋅⋅⋅⋅⋅⋅⋅⋅⋅⋅⋅⋅ 2
1-2. Calibration System ⋅⋅⋅⋅⋅⋅⋅⋅⋅⋅⋅⋅⋅⋅⋅⋅⋅⋅⋅⋅⋅⋅⋅⋅⋅⋅⋅⋅⋅⋅⋅⋅⋅⋅⋅⋅⋅⋅⋅⋅⋅⋅⋅⋅⋅⋅⋅⋅⋅⋅⋅⋅⋅⋅⋅⋅⋅⋅⋅⋅⋅⋅⋅⋅⋅⋅⋅⋅⋅⋅⋅⋅⋅⋅⋅⋅⋅⋅⋅⋅⋅⋅⋅⋅ 2
1-3. Relay Output (Hi, Lo) ⋅⋅⋅⋅⋅⋅⋅⋅⋅⋅⋅⋅⋅⋅⋅⋅⋅⋅⋅⋅⋅⋅⋅⋅⋅⋅⋅⋅⋅⋅⋅⋅⋅⋅⋅⋅⋅⋅⋅⋅⋅⋅⋅⋅⋅⋅⋅⋅⋅⋅⋅⋅⋅⋅⋅⋅⋅⋅⋅⋅⋅⋅⋅⋅⋅⋅⋅⋅⋅⋅⋅⋅ 2
1-4. Data Back-up Function ⋅⋅⋅⋅⋅⋅⋅⋅⋅⋅⋅⋅⋅⋅⋅⋅⋅⋅⋅⋅⋅⋅⋅⋅⋅⋅⋅⋅⋅⋅⋅⋅⋅⋅⋅⋅⋅⋅⋅⋅⋅⋅⋅⋅⋅⋅⋅⋅⋅⋅⋅⋅⋅⋅⋅⋅⋅⋅⋅⋅⋅⋅⋅⋅⋅⋅⋅⋅⋅⋅⋅⋅⋅⋅⋅⋅⋅ 2
1-5. Option (Analog OUT) ⋅⋅⋅⋅⋅⋅⋅⋅⋅⋅⋅⋅⋅⋅⋅⋅⋅⋅⋅⋅⋅⋅⋅⋅⋅⋅⋅⋅⋅⋅⋅⋅⋅⋅⋅⋅⋅⋅⋅⋅⋅⋅⋅⋅⋅⋅⋅⋅⋅⋅⋅⋅⋅⋅⋅⋅⋅⋅⋅⋅⋅⋅⋅⋅⋅⋅⋅⋅⋅⋅⋅⋅⋅⋅⋅ 2
1-6. Power Supply ⋅⋅⋅⋅⋅⋅⋅⋅⋅⋅⋅⋅⋅⋅⋅⋅⋅⋅⋅⋅⋅⋅⋅⋅⋅⋅⋅⋅⋅⋅⋅⋅⋅⋅⋅⋅⋅⋅⋅⋅⋅⋅⋅⋅⋅⋅⋅⋅⋅⋅⋅⋅⋅⋅⋅⋅⋅⋅⋅⋅⋅⋅⋅⋅⋅⋅⋅⋅⋅⋅⋅⋅⋅⋅⋅⋅⋅⋅⋅⋅⋅⋅⋅⋅⋅⋅ 3
1-7. Standard built-in product ⋅⋅⋅⋅⋅⋅⋅⋅⋅⋅⋅⋅⋅⋅⋅⋅⋅⋅⋅⋅⋅⋅⋅⋅⋅⋅⋅⋅⋅⋅⋅⋅⋅⋅⋅⋅⋅⋅⋅⋅⋅⋅⋅⋅⋅⋅⋅⋅⋅⋅⋅⋅⋅ 3
2. Cautions ⋅⋅⋅⋅⋅⋅⋅⋅⋅⋅⋅⋅⋅⋅⋅⋅⋅⋅⋅⋅⋅⋅⋅⋅⋅⋅⋅⋅⋅⋅⋅⋅⋅⋅⋅⋅⋅⋅⋅⋅⋅⋅⋅⋅⋅⋅⋅⋅⋅⋅⋅⋅⋅⋅⋅⋅⋅⋅⋅⋅⋅⋅⋅⋅⋅⋅⋅⋅⋅⋅⋅⋅⋅⋅⋅⋅⋅⋅⋅⋅⋅⋅⋅⋅⋅ 3
2-1. Set-up Cautions ⋅⋅⋅⋅⋅⋅⋅⋅⋅⋅⋅⋅⋅⋅⋅⋅⋅⋅⋅⋅⋅⋅⋅⋅⋅⋅⋅⋅⋅⋅⋅⋅⋅⋅⋅⋅⋅⋅⋅⋅⋅⋅⋅⋅⋅⋅⋅⋅⋅⋅⋅⋅⋅⋅⋅⋅⋅⋅⋅⋅⋅⋅⋅⋅⋅⋅⋅⋅⋅⋅⋅⋅⋅⋅⋅⋅⋅⋅⋅⋅⋅⋅⋅⋅ 3
2-2. Use Cautions⋅⋅⋅⋅⋅⋅⋅⋅⋅⋅⋅⋅⋅⋅⋅⋅⋅⋅⋅⋅⋅⋅⋅⋅⋅⋅⋅⋅⋅⋅⋅⋅⋅⋅⋅⋅⋅⋅⋅⋅⋅⋅⋅⋅⋅⋅⋅⋅⋅⋅⋅⋅⋅⋅⋅⋅⋅⋅⋅⋅⋅⋅⋅⋅⋅⋅⋅⋅⋅⋅⋅⋅⋅⋅⋅⋅⋅⋅⋅⋅⋅⋅⋅⋅⋅⋅⋅⋅⋅⋅⋅ 3
3. Specifications ⋅⋅⋅⋅⋅⋅⋅⋅⋅⋅⋅⋅⋅⋅⋅⋅⋅⋅⋅⋅⋅⋅⋅⋅⋅⋅⋅⋅⋅⋅⋅⋅⋅⋅⋅⋅⋅⋅⋅⋅⋅⋅⋅⋅⋅⋅⋅⋅⋅⋅⋅⋅⋅⋅⋅⋅⋅⋅⋅⋅⋅⋅⋅⋅⋅⋅⋅⋅⋅⋅⋅⋅⋅⋅⋅ 4
3-1 General Specifications ⋅⋅⋅⋅⋅⋅⋅⋅⋅⋅⋅⋅⋅⋅⋅⋅⋅⋅⋅⋅⋅⋅⋅⋅⋅⋅⋅⋅⋅⋅⋅⋅⋅⋅⋅⋅⋅⋅⋅⋅⋅⋅⋅⋅⋅⋅⋅⋅⋅⋅⋅⋅⋅⋅⋅⋅⋅⋅⋅⋅⋅⋅⋅⋅⋅⋅⋅⋅⋅⋅⋅⋅⋅⋅⋅ 4
4. Front Panel ⋅⋅⋅⋅⋅⋅⋅⋅⋅⋅⋅⋅⋅⋅⋅⋅⋅⋅⋅⋅⋅⋅⋅⋅⋅⋅⋅⋅⋅⋅⋅⋅⋅⋅⋅⋅⋅⋅⋅⋅⋅⋅⋅⋅⋅⋅⋅⋅⋅⋅⋅⋅⋅⋅⋅⋅⋅⋅⋅⋅⋅⋅⋅⋅⋅⋅⋅⋅⋅⋅⋅⋅⋅⋅⋅ 5
5. Back panel ⋅⋅⋅⋅⋅⋅⋅⋅⋅⋅⋅⋅⋅⋅⋅⋅⋅⋅⋅⋅⋅⋅⋅⋅⋅⋅⋅⋅⋅⋅⋅⋅⋅⋅⋅⋅⋅⋅⋅⋅⋅⋅⋅⋅⋅⋅⋅⋅⋅⋅⋅⋅⋅⋅⋅⋅⋅⋅⋅⋅⋅⋅⋅⋅⋅⋅⋅⋅⋅⋅⋅⋅⋅⋅⋅⋅⋅⋅⋅⋅⋅⋅⋅⋅⋅⋅⋅ 6
6. Setting Mode ⋅⋅⋅⋅⋅⋅⋅⋅⋅⋅⋅⋅⋅⋅⋅⋅⋅⋅⋅⋅⋅⋅⋅⋅⋅⋅⋅⋅⋅⋅⋅⋅⋅⋅⋅⋅⋅⋅⋅⋅⋅⋅⋅⋅⋅⋅⋅⋅⋅⋅⋅⋅⋅⋅⋅⋅⋅⋅⋅⋅⋅⋅⋅⋅⋅⋅⋅⋅⋅⋅⋅⋅⋅⋅⋅ 8
6-1. Setting Method ⋅⋅⋅⋅⋅⋅⋅⋅⋅⋅⋅⋅⋅⋅⋅⋅⋅⋅⋅⋅⋅⋅⋅⋅⋅⋅⋅⋅⋅⋅⋅⋅⋅⋅⋅⋅⋅⋅⋅⋅⋅⋅⋅⋅⋅⋅⋅⋅⋅⋅⋅⋅⋅⋅⋅⋅⋅⋅⋅⋅⋅⋅⋅⋅⋅⋅⋅⋅⋅⋅⋅⋅⋅⋅⋅8
6-2. Setting Hi, Lo ⋅⋅⋅⋅⋅⋅⋅⋅⋅⋅⋅⋅⋅⋅⋅⋅⋅⋅⋅⋅⋅⋅⋅⋅⋅⋅⋅⋅⋅⋅⋅⋅⋅⋅⋅⋅⋅⋅⋅⋅⋅⋅⋅⋅⋅⋅⋅⋅⋅⋅⋅⋅⋅⋅⋅⋅⋅⋅⋅⋅⋅⋅⋅⋅⋅⋅⋅⋅⋅⋅⋅⋅⋅⋅⋅8
6-3. Setting Decimal Point ⋅⋅⋅⋅⋅⋅⋅⋅⋅⋅⋅⋅⋅⋅⋅⋅⋅⋅⋅⋅⋅⋅⋅⋅⋅⋅⋅⋅⋅⋅⋅⋅⋅⋅⋅⋅⋅⋅⋅⋅⋅⋅⋅⋅⋅⋅⋅⋅⋅⋅⋅⋅⋅⋅⋅⋅⋅⋅⋅⋅⋅⋅⋅⋅⋅⋅⋅⋅⋅⋅⋅⋅⋅⋅⋅ 8
6-4. Setting Round off ⋅⋅⋅⋅⋅⋅⋅⋅⋅⋅⋅⋅⋅⋅⋅⋅⋅⋅⋅⋅⋅⋅⋅⋅⋅⋅⋅⋅⋅⋅⋅⋅⋅⋅⋅⋅⋅⋅⋅⋅⋅⋅⋅⋅⋅⋅⋅⋅⋅⋅⋅⋅⋅⋅⋅⋅⋅⋅⋅⋅⋅⋅⋅⋅⋅⋅⋅⋅⋅⋅⋅⋅⋅⋅⋅ 9
6-5. Setting Peak Hold mode ⋅⋅⋅⋅⋅⋅⋅⋅⋅⋅⋅⋅⋅⋅⋅⋅⋅⋅⋅⋅⋅⋅⋅⋅⋅⋅⋅⋅⋅⋅⋅⋅⋅⋅⋅⋅⋅⋅⋅⋅⋅⋅⋅⋅⋅⋅⋅⋅⋅⋅⋅⋅⋅⋅⋅⋅⋅⋅⋅⋅⋅⋅⋅⋅⋅⋅⋅⋅⋅⋅⋅⋅⋅⋅⋅ 9
6-6. Setting Baud Rate ⋅⋅⋅⋅⋅⋅⋅⋅⋅⋅⋅⋅⋅⋅⋅⋅⋅⋅⋅⋅⋅⋅⋅⋅⋅⋅⋅⋅⋅⋅⋅⋅⋅⋅⋅⋅⋅⋅⋅⋅⋅⋅⋅⋅⋅⋅⋅⋅⋅⋅⋅⋅⋅⋅⋅⋅⋅⋅⋅⋅⋅⋅⋅⋅⋅⋅⋅⋅⋅⋅⋅⋅⋅⋅⋅10
6-7. Setting ID Number ⋅⋅⋅⋅⋅⋅⋅⋅⋅⋅⋅⋅⋅⋅⋅⋅⋅⋅⋅⋅⋅⋅⋅⋅⋅⋅⋅⋅⋅⋅⋅⋅⋅⋅⋅⋅⋅⋅⋅⋅⋅⋅⋅⋅⋅⋅⋅⋅⋅⋅⋅⋅⋅⋅⋅⋅⋅⋅⋅⋅⋅⋅⋅⋅⋅⋅⋅⋅⋅⋅⋅⋅⋅⋅⋅10
6-8. Setting DAC ZERO Scope ⋅⋅⋅⋅⋅⋅⋅⋅⋅⋅⋅⋅⋅⋅⋅⋅⋅⋅⋅⋅⋅⋅⋅⋅⋅⋅⋅⋅⋅⋅⋅⋅⋅⋅⋅⋅⋅⋅⋅⋅⋅⋅⋅⋅⋅⋅⋅⋅⋅⋅⋅⋅⋅⋅⋅⋅⋅⋅⋅⋅⋅⋅⋅⋅⋅⋅⋅⋅⋅⋅⋅⋅⋅⋅⋅11
6-9. Setting DAC CAPA Scope ⋅⋅⋅⋅⋅⋅⋅⋅⋅⋅⋅⋅⋅⋅⋅⋅⋅⋅⋅⋅⋅⋅⋅⋅⋅⋅⋅⋅⋅⋅⋅⋅⋅⋅⋅⋅⋅⋅⋅⋅⋅⋅⋅⋅⋅⋅⋅⋅⋅⋅⋅⋅⋅⋅⋅⋅⋅⋅⋅⋅⋅⋅⋅⋅⋅⋅⋅⋅⋅⋅⋅⋅⋅⋅⋅11
6-10. Setting the number of buffer ⋅⋅⋅⋅⋅⋅⋅⋅⋅⋅⋅⋅⋅⋅⋅⋅⋅⋅⋅⋅⋅⋅⋅⋅⋅⋅⋅⋅⋅⋅⋅⋅⋅⋅⋅⋅⋅⋅⋅⋅⋅⋅⋅⋅⋅⋅⋅⋅⋅⋅⋅⋅⋅⋅⋅⋅⋅⋅⋅⋅⋅⋅⋅⋅⋅⋅⋅⋅⋅⋅⋅⋅⋅⋅⋅12
6-11. Setting Auto Tracking Range ⋅⋅⋅⋅⋅⋅⋅⋅⋅⋅⋅⋅⋅⋅⋅⋅⋅⋅⋅⋅⋅⋅⋅⋅⋅⋅⋅⋅⋅⋅⋅⋅⋅⋅⋅⋅⋅⋅⋅⋅⋅⋅⋅⋅⋅⋅⋅⋅⋅⋅⋅⋅⋅⋅⋅⋅⋅⋅⋅⋅⋅⋅⋅⋅⋅⋅⋅⋅⋅⋅⋅⋅⋅⋅⋅12
6-12. Setting Auto Tracking Time ⋅⋅⋅⋅⋅⋅⋅⋅⋅⋅⋅⋅⋅⋅⋅⋅⋅⋅⋅⋅⋅⋅⋅⋅⋅⋅⋅⋅⋅⋅⋅⋅⋅⋅⋅⋅⋅⋅⋅⋅⋅⋅⋅⋅⋅⋅⋅⋅⋅⋅⋅⋅⋅⋅⋅⋅⋅⋅⋅⋅⋅⋅⋅⋅⋅⋅⋅⋅⋅⋅⋅⋅⋅⋅⋅13
7. Calibration ⋅⋅⋅⋅⋅⋅⋅⋅⋅⋅⋅⋅⋅⋅⋅⋅⋅⋅⋅⋅⋅⋅⋅⋅⋅⋅⋅⋅⋅⋅⋅⋅⋅⋅⋅⋅⋅⋅⋅⋅⋅⋅⋅⋅⋅⋅⋅⋅⋅⋅⋅⋅⋅⋅⋅⋅⋅⋅⋅⋅⋅⋅⋅⋅⋅⋅⋅⋅⋅⋅⋅⋅⋅⋅⋅14
7-1. Real-weight Calibration ⋅⋅⋅⋅⋅⋅⋅⋅⋅⋅⋅⋅⋅⋅⋅⋅⋅⋅⋅⋅⋅⋅⋅⋅⋅⋅⋅⋅⋅⋅⋅⋅⋅⋅⋅⋅⋅⋅⋅⋅⋅⋅⋅⋅⋅⋅⋅⋅⋅⋅⋅⋅⋅⋅⋅⋅⋅⋅⋅⋅⋅⋅⋅⋅⋅⋅⋅⋅⋅⋅⋅⋅⋅⋅⋅14
7-2. Sensor outout value Calibration ⋅⋅⋅⋅⋅⋅⋅⋅⋅⋅⋅⋅⋅⋅⋅⋅⋅⋅⋅⋅⋅⋅⋅⋅⋅⋅⋅⋅⋅⋅⋅⋅⋅⋅⋅⋅⋅⋅⋅⋅⋅⋅⋅⋅⋅⋅⋅⋅⋅⋅⋅⋅⋅⋅⋅⋅15
8. Setting KEY LOCK ⋅⋅⋅⋅⋅⋅⋅⋅⋅⋅⋅⋅⋅⋅⋅⋅⋅⋅⋅⋅⋅⋅⋅⋅⋅⋅⋅⋅⋅⋅⋅⋅⋅⋅⋅⋅⋅⋅⋅⋅⋅⋅⋅⋅⋅⋅⋅⋅⋅⋅⋅⋅⋅⋅⋅⋅⋅⋅⋅⋅⋅⋅⋅⋅⋅⋅⋅⋅⋅⋅⋅⋅⋅⋅⋅16
11. OPTION(OP-02, OP-03)
Option 02 (RS232C) ⋅⋅⋅⋅⋅⋅⋅⋅⋅⋅⋅⋅⋅⋅⋅⋅⋅⋅⋅⋅⋅⋅⋅⋅⋅⋅⋅⋅⋅⋅⋅⋅⋅⋅⋅⋅⋅⋅⋅⋅⋅⋅⋅⋅⋅⋅⋅⋅⋅⋅⋅⋅⋅⋅⋅⋅⋅⋅⋅⋅⋅⋅⋅⋅⋅⋅⋅⋅⋅⋅⋅⋅⋅⋅⋅⋅⋅⋅⋅⋅⋅⋅⋅⋅⋅⋅⋅⋅⋅⋅⋅⋅⋅⋅⋅⋅⋅⋅⋅⋅⋅ 17
1
Option 03 (RS485) ⋅⋅⋅⋅⋅⋅⋅⋅⋅⋅⋅⋅⋅⋅⋅⋅⋅⋅⋅⋅⋅⋅⋅⋅⋅⋅⋅⋅⋅⋅⋅⋅⋅⋅⋅⋅⋅⋅⋅⋅⋅⋅⋅⋅⋅⋅⋅⋅⋅⋅⋅⋅⋅⋅⋅⋅⋅⋅⋅⋅⋅⋅⋅⋅⋅⋅⋅⋅⋅⋅⋅⋅⋅⋅⋅⋅⋅⋅⋅⋅⋅⋅⋅⋅⋅⋅⋅⋅⋅⋅⋅⋅⋅⋅⋅⋅⋅⋅⋅⋅⋅⋅⋅ 19

1. Features
We are grateful to you for picking up our product. If you experience problems while
using it, you may refer to the user manual or contact the Technical Support Department
of the company.
This product is an indicator which amplifies the minute voltage signals of each sensor
and converts themit into digital. It is mainly used in Physics quantity measurement for
strain gauge, pressure sensor, LVDT, and torque sensor, etc. It has the following
features.
1-1. Sigma-Delta Conversion System
A medium and high speed A/D conversion device is adopted to detect input signals
from the sensor. A D/A device at the same speed is adopted to detect analogue output
signals, which makes high-speed analog-digital converter, digital peak hold, sample
hold and section peak hold.
1-2. Calibration System
Two systems are adopted: calibration system based on real weight(standard weight);
calibration system based on the rated output of the sensor.
1-3. Relay Output
It is possible to set upper limit and lower limit from the keys on the front panel.
It is also possible to send the contact signals of the rear panel.
1-4. Data Back-up Function
As set value such as zero, span, upper limit and low limit, etc. is stored in FALSH
MEMORY, it is not necessary to reset the input data for they are stored in the memory
even when the electricity or power is cut off.
1-5. Option
It followed in External output signal and it did DC 0 ~10V with standard.
OP-01 : DC 4~20mA
2
OP-02 : RS232C

1. B
2. O
3. I
4. T
K
o
OP-03 : RS485
OP-04 : DAC Analog output
1-6. Power Supply
Power of this product did 220V(50~60Hz) with standard, 110V speaks when ordering,
1.7. Standard built-in product
ody
perating instructions
Terminal and Power Cable
he panel the parts for a fixation
2. Cautions
For optimum performance and safety, please read these instructions carefully.
Do not remodel this equipment at one's discretion.
2-1. Set-up Cautions
• Keep it out of wet places.
• Do not set it up near vibration & impulse, high temperature and humidity.
eep it out of the direct rays of the sun. Set it up where there is less dust, and Keep it
ut of direct air including salt and ion.
• Do not use when there is inflammable gas or heavy machinery, and smog.
• Ground earth-terminal(GN)
• Make wire separately from power system wiring and noise wiring.
• Make sure the use of 4 line sealed cable as a sensor cable. Too long cable leads to
measurement error due to wiring resistance.
2-2. Cautions
During calibration, Do not input free-load state and real-weight load until it becomes
stable. Pressing Enter Key in unstable condition leads to calibration error.
3
Do not press any Key in use at one's discretion. Please refer to 7. Setting-up mode for
the function and method of Key.

3. Specifications
• Available sensor
1) Micro-voltage output sensor(mV)
2) Strain gage sensor(Bridge 350Ω, 120Ω).
• Maximum display
Max 32676
• A/D conversion
100 time/sec
• Temperature characteristics (Amp characteristics)
Zero : 1µV/℃
Span : 100ppm/℃
• Front panel
Measured value display : 7 segment 5 LED, Character height 10mm
State display LED : Red LED 2 pieces
Key switch : 4 pieces
• Various function
Convert function
: Possible for setting Upper limit(H1) & Lower limit(LO)
Contact capacity is AC 250V, 0.5A and DC 50V 1A.
Analog output : DC 0 ~ 10V.
• Option
① OP-01 : DC 4~20mA
② OP-02 : RS232C
③ OP-03 : RS485
3-1 General Specifications
• Power Supply : AC 220V, 60Hz, 0.5A (Standard Specifications)
• Temperature Range : -10℃∼60℃, less than 85% RH (where there is no dewing.)
• Size : 72 × 72 × 111 mm(W × H × D)
4
• Weight : about 700 g

4. Front Panel
① HI, LO Indication
② Measured Value Indication
③ Function Key / ESC Key
④ Shift Key / ZERO Key /
HOLD RESET key
⑤ Up Key / CAL Key
⑥ Enter Key / HOLD Key
① Hi, Lo indicator
: Hi
value
Lo LE
② Measured Value indicator
or set point.
③
LED will be turned on when measured value is higher than or equal to the set Hi
.
D will be turned on when measured value is lower than or equal to the set Lovalue.
: indicates the measured data
: If y u o
push this key for more than 3 seconds, the machine will enter the setting mode.
If you
④
want to exit to escape from the setting mode, you may use the ESC key.
: If you want to change the number, you may use this key.
key adjusts the number to zero regardless of the current value.
This
This
⑤
And his t
key is used to set up SPAN MODE to calibrate.
key is used to cancel peak weight.
: If you push this key, it will increase the number by one.
u want to enter the calibration mode, you should hold this key for 3 seconds.
⑥
And f yo i
: If yo
This key is used to hold peak weight in PEAK MODE.
5
u are to store the set value, you may use the Enter key.

5. Back panel
Make sure the terminal site and its use, and wire separately from a lot of nosing
wiring.
Press protruded button on the top of terminal stand, and insert it into the hole on the
lower part of it to the end.
Then, pull it gently to make its certainty.
(Suitable cable is 0.5-1. Linking cable must be brazing or used with I terminal)
① PE : Ground Terminal (In other way independent ground connection )
② AC IN : Main Power Supply Wiring Terminal
③ COM : Relay Output lower limit and upper limit Common Terminal
④ LOW : Relay Output lower limit Connection Terminal
⑤ HIGH : Relay Output Upper Connection Terminal
ⓐ ZERO : ZERO KEY FOR External Input Mode Selection
The data is zero when connect –OUT Terminal.
This key does not work when is using HOLD DATA .
ⓑ HOLD : HOLD KEY FOR External Input Mode Selection
The data is held when connect –OUT Terminal.
(Peak Hold : Display is
display will be replaced w
Sample Hold : Display is key is pressed or command input is ON.)
The data is re
ⓒ +OUT : Analog O
Locked when HOLD key is pressed or command input is ON. But,
hen new peak data is entered.
Locked when HOLD
6
set when disconnect –OUT Terminal.
utput Terminal(+)

ⓓ -OU
nnection Terminal
e to earth the sensor-
ⓖ +SIG
ⓗ -SIG on Terminal
.0mV/V
um output value of sensor .)
. Turn it off when wiring(main power supply)
thick cable for GN(PE Terminal) to prevent it from having impulse voltage
T : Analog Ground Output Terminal (-) , GND
ⓔ +EXC : Sensor Supply Voltage + Co
ⓕ -EXC : Sensor Supply Voltage - Connection Terminal
[Sensor Shield Connection Terminal (Be sur
attached part and this terminal.)]
: Sensor Output Signal + Connection Terminal
: Sensor Output Signal - Connecti
ⓘ Amplification Adjustment Switch
SW1 : 3.0mV/V SW2 : 2.0mV/V
SW3 : 1.5mV/V SW4 : 1
(Set with the number which gets near to maxim
◀Caution▶
1
2. Please use
and trouble resulting from surge.
3. Make sure the function of terminal belows and connect required contact input and
output.
4. Operation of internal Circuit
discretion.
makes possible for 110V conversion but do not operate
at one's
EXC+
EXC-
SIG+
SIG-
GND
IND L/C
7

6. Setting Mode
6-1. Setting Method
If you push the key for about 3 seconds, will appear and then HL
will come out.
If you push the key at that time, the setting mode will change in the following
direction, and if you push the key at that time, the setting mode will change in the
opposite direction. If you push the key, the present mode will be chosen.
6-2. Setting Hi, Lo
You can set up the upper limit and lower limit of the relay output. HI will work if HI is
larger than the HI set value. LO will works if LO is smaller than the LO set value.
If you push the function key, the setting mode will come out.
If you push the Up key, you can choose ,
or (The upper limit -> , The lower limit -> )
If you push the ENT key, you choose HI or LO setting.
If you push the Shift key, you can choose the number location.
If you push the Up key, you can change the number as you wish.
….
You can save the setting value by pushing the ENT key.
-> -> or (In case it is not good, will come out.)
If you want to get out of the setting mode and return to the measurement mode,
you may have to push the Function key.
(Currently the value is indicated.)
6-3. Setting Decimal point
8
This product operates in a way of fixed decimal point, the decimal point must be
preset.

If the decimal point is changed after presetting, displaying value does not increase
according to the decimal point.
Press Function key and then Up key to become
->
Press ENT key to choose decimal point setting.
Press Shift key to choose the required number.
Press ENT key to store the number.
-> -> (In case it is not good, will come out.)
If you want to get out of the setting mode and return to the measurement mode,
you may have to push the Function key.
(Currently the value is indicated.)
6-4. Setting Round off
It is to set the variations of display number. When the value varies considerably, you
can set it properly. It is possible to set 1, 2, 5, 10, 20, 50, 100.
Press Function key and then Up key to be
->
Press ENT key to choose round off setting.
Press Shift key to choose the required number.
Press ENT key to store the number.
-> -> (In case it is not good, will come out.)
If you want to get out of the setting mode and return to the measurement mode,
you may have to push the Function key.
(Currently the value is indicated.)
6-5. Setting Peak Hold, Sample Hold
This Product also has Peak Hold Function. So if you need this function, you can use
this, with operating as follows. When you are in this mode. You can reset the value by
pressing key.
Press Function key and then Up key to be
9
->

Press ENT key to choose Hold setting.
Press Up key to choose Peak Hold or Sample Hold setting.
Press ENT key to store it.
-> -> (In case it is not good, will come out.)
If you want to get out of the setting mode and return to the measurement mode,
you may have to push the Function key.
6-6. Setting Baud Rate
This mode is designed to set up Baud Rate when you engage in serial
communication.
You can set up 2400, 4800, 9600, 19200 bps.
Press Function key and then Up key to be
->
Press ENT key to choose baud rate setting.
Press Shift key to choose what you want.
Press ENT key to store it.
-> -> (In case it is not good, will come out.)
If you want to get out of the setting mode and return to the measurement mode,
you may have to push the Function key.
(Currently the value is indicated.)
6-7. Setting ID Number
In RS485 or RS232C Command mode, it is used for giving product specific number.
Press Function key and then Up key to be
->
Press ENT key to choose ID number setting.
Press Up key to change the required number.
(When it presses Up key, the number increases. When it presses Shift key, the
number decrease)
…….
Press ENT key to store it.
10
-> -> (In case it is not good, will come out.)

If you want to get out of the setting mode and return to the measurement mode,
you may have to push the Function key.
(Currently the value is indicated.)
6-8. Setting DAC Zero Scope
When using analog output, it sets Zero scope of output value. By Display setting
Analog output control is possible.
Press Function key and then Up key to be
->
Press ENT key to choose DAC Zero scope setting.
Press Shift key to choose what you want.
Press Up key to change the required number.
….
Press ENT key to store it.
-> -> (In case it is not good, will come out.)
If you want to get out of the setting mode and return to the measurement mode,
you may have to push the Function key.
(Currently the value is indicated.)
ex) When DAC Zero value sets at 500.0, analog output voltage will be 0V.
(When take goods out of a warehouse, sets )
6-9. Setting DAC Capa Scope
When using analog output, it sets scope of output value. By Display setting Analog
output control is possible.
Press Function key and then Up key to be
->
Press ENT key to choose DAC CAPA scope setting.
Press Shift key to choose what you want.
Press Up key to change the required number.
11
….

Press ENT key to store it.
-> -> (In case it is not good, will come out.)
If you want to get out of the setting mode and return to the measurement mode,
you may have to push the Function key.
(Currently the value is indicated.)
ex) When DAC CAPA value sets at 500.0, analog output voltage will be 10V.
6-10. Setting the number of buffer
As setting Display speed and the number of A/D Sampling , it can set up 1~32.
According to 6-1, Press Function key and then Up key to be .
->
Press ENT key to choose the number of buffer.
Press Up key to change the required number.
…….
Fast --------------------------- Slow
Press ENT key to store it.
-> -> (In case it is not good, will come out.)
If you want to get out of the setting mode and return to the measurement mode,
you may have to push the Function key.
(Currently the value is indicated.)
6-11. Setting Auto Tracking Range
As setting ZERO Operation Range (Auto zero), it set up 0, 1, 2, 5, 10, 20, 50, 100.
※ This function must use 6-12 Time Mode at the same time.
According to 6-1, Press Function key and then Up key to be .
->
Press ENT key to choose Auto zero.
Press Up key to change the required number.
…….
Press ENT key to store it.
12
-> -> (In case it is not good, will come out.)

If you want to get out of the setting mode and return to the measurement mode,
you may have to push the Function key.
(Currently the value is indicated.)
6-12. Setting Auto Tracking Time
As setting time to operate Auto zero, it set up 0.1~5.0 second.
According to 6-1, Press Function key and then Up key to be .
->
Press ENT key to choose time mode.
Press Up key to change the required number.
…….
Press ENT key to store it.
-> -> (In case it is not good, will come out.)
If you want to get out of the setting mode and return to the measurement mode,
you may have to push the Function key.
(Currently the value is indicated.)
Ex) After setting Zero Tracking range and Auto Tracking time , when do
not change input signal, and then, Display is or , after 0.2 second,
Display is .
13

7. Calibration
Before calibration, You should select Dip switch to the most near thing in sensor
output value and make .
7-1. Real-weight Calibration
Standard weight is necessary. When being used Multiple sensor at one Indicator, It
calibtrate certainly at Real-weight.
1) Real-weight Calibration Mode Setting
Press Function key about 3 seconds to return to Setup mode.
Press Up key to be
->
Press ENT key to choose calibration setting mode.
Preess Up key to be
Press ENT key to store it.
-> -> (In case it is not good, will come out.)
If you want to get out of the setting mode and return to the measurement mode,
you may have to push the Function key.
(Currently the value is indicated.)
2) Zero and Span Setting
Press Up key about 3 seconds to return to Real-weight Calibration mode.
->
Leave the sensor free-load and press ENT key to set Zero.
-> -> ->
Press Up key to be
Press ENT key, It uses Shift key and Up Key and it inputs Real-weight
value.
(Standard weight value it was prepared).
Press ENT key , put counterweight on.
Press ENT key to set SPAN value.
14
-> -> ->

If you want to get out of the setting mode and return to the measurement mode,
you may have to push the Function key.
※ If, when is indicated or with Real-weight value different case, to repeat the
above statement.
7-2. Sensor output value Calibration
Sensor CAPA and Output value are necessary. (When the sensor purchasing, it is
becoming marking in Calibration sheet.)
It considers a sensor quality and a circumference condition, use Real-weight
calibration for precision measuring.
1) Sensor output mode setting
Press Function key about 3 seconds to return to setup mode
Press Up key to be
->
Press ENT key to choose calibration setting mode.
Preess Up key to choose GAIN(The choosing number of Amplification Adjustment
Switch)
Press ENT key to store it.
-> -> (In case it is not good, will come out.)
If you want to get out of the setting mode and return to the measurement mode,
you may have to push the Function key.
(Currently the value is indicated.)
※ Please set up the choosing number of Amplification Adjustment Switch
2) CAPA setting and Sensor output setting
Set it with reference to Calibration sheet, enclosed with the sensor.
Press Up key about 3 seconds to return to CAPA mode.
Press ENT key, It uses Shift key and Up Key and it inputs Sensor CAPA
value.
Press ENT key to store it.
15
-> -> (In case it is not good, will come out.)

Press Up key to be
Press ENT key, It uses Shift key and Up Key and it inputs Sensor output
value.
Press ENT key to store it.
-> -> (In case it is not good, will come out.)
If you want to get out of the setting mode and return to the measurement mode,
you may have to push the Function key.
(Currently the value is indicated.)
8. Setting KEY LOCK
This can be used as two function.
If you choose , Span Calibration does not operate.
If you choose , Span Calibration is possible.
Press Function key and Power on.
Select
After selecting or , press ENT key to store it.
If you choose -> Setting is impossible. You only use hi, low and zero key.
If you choose -> Setting is possible.
16

#Option-02 (RS232C)
Make wire separately from power system wiring and noise wiring.
Make sure the use of sealed cable as a sensor cable.
Indicator Host PC
TX(Transmitting Data) RXD(Receiving Data), Number 2 Pin
RX(Receiving Data) TXD(Transmitting Data), Number 3 Pin
GN(Ground) GND(Ground), 5 Pin
1. TYPE : EIA-232C
2. Method : half duplex, asynchronous system
3. Baud-rate : Selection in 2400, 4800, 9600, 19200bps
4. Parity : No Parity
5. Data bit : 8 bit, No Parity
6. Stop bit : 1bit
7. Stream mode (Ex. Data +1234.5 transmission)
Data format (code : ASCII)]
CODE BYTE1 BYTE2 BYTE3 BYTE4 BYTE5 BYTE6 BYTE7 BYTE8
ASCII S T , N T , + 0
HEX 53H 54H 2CH 4EH 54H 2CH 2BH 30H
CODE BYTE9
BYTE10 BYTE11 BYTE12 BYTE13 BYTE14 BYTE15 BYTE16
ASCII 1 2 3 4 . 5 CR LF
HEX 31H 32H 33H 34H 2EH 35H 0DH 0AH
1) BYTE
. DATA S
1, BYTE2
TABLE: S T . DATA UnSTABLE
. DATA L
2) BYTE
: U S
OVERFLOW : O L . DATA UNDERFLOW : U
3 ~ BYTE6 : f ed
3) BYTE
4) BYTE CARR
5) BYTE LINE
ix character (, N T ,)
7 ~ BYTE14 : DATA 8 BYTE(+/-)
15 : IAGE RETURN
16 : FEED
17
8. Command mode : Please set to RS485 mode(OP-03:RS485 )

#Option-03 (RS485)
Make wire separately from power system wiring and noise wiring because is sensitive to
electrical noise noise.
Cable uses by Shield Cable certainly.
1. TYPE : RS485
2. Method : half duplex, asynchronous system
3. Baud-rate : Selection in 2400, 4800, 9600, 19200bps
4. Parity : No Parity
5. Data bit : 8 bit
6. Stop bit : 1bit
Please refer INDICATOR manual and establish ID_NO.( 1 ~ 32 channel)
ID_NO t must establish other number with COMMAND code certainly
7. Command form (PC -> INDICATOR)
CODE BYTE1 BYTE2 BYTE3 BYTE4 BYTE5
ASCII I D 0 1 P
HEX 49H 44H 30H 31H 50H
1) BYTE
2) BYTE
3) BYTE
1, BYTE2 : fixed character (ID)
3, BYTE4 : equipment number (1 ~ 32)
5 : Command (P, H, R, Z)
8. Commend DESCRIPTION
Command
ASCII HEX Command explanation
P 50H Present Value Transmission
H 48H Command to set to HOLD
R 52H Command to cancel HOLD
Z 5AH Command to set zero
18

9. Transmisssion DATA Form (INDICATOR -> PC)
CODE BYTE1 BYTE2 BYTE3 BYTE4 BYTE5 BYTE6 BYTE7 BYTE8
ASCII I D 0 0 1 , + 0
HEX 53H 54H 30H 30H 31H 2CH 2BH 30H
CODE BYTE9 BYTE10 BYTE11 BYTE12 BYTE13 BYTE14 BYTE15 BYTE16
ASCII 1 2 3 4 . 5 CR LF
HEX 31H 32H 33H 34H 2EH 35H 0DH 0AH
1) BYTE
2) BYTE
3) BYTE ed
4) BYTE
5) BYTE CARR
6) BYTE LINE
1, BYTE2 : fixed character (ID)
3 ~ BYTE5 : equipment number (1 ~ 32)
6 : fix character (,)
7~BYTE14 : DATA 8byte (+/- )
15 : IAGE RETURN
16 : FEED
19
Table of contents
Other dacell Measuring Instrument manuals
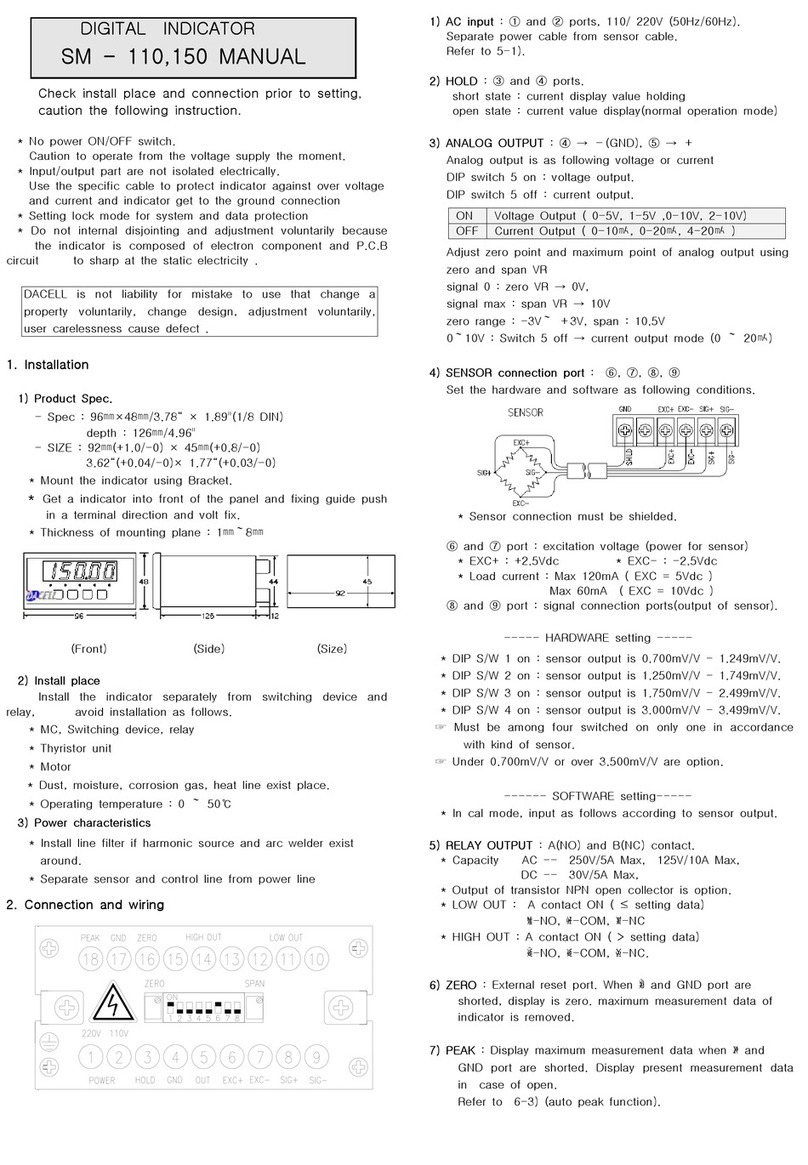
dacell
dacell SM110 User manual
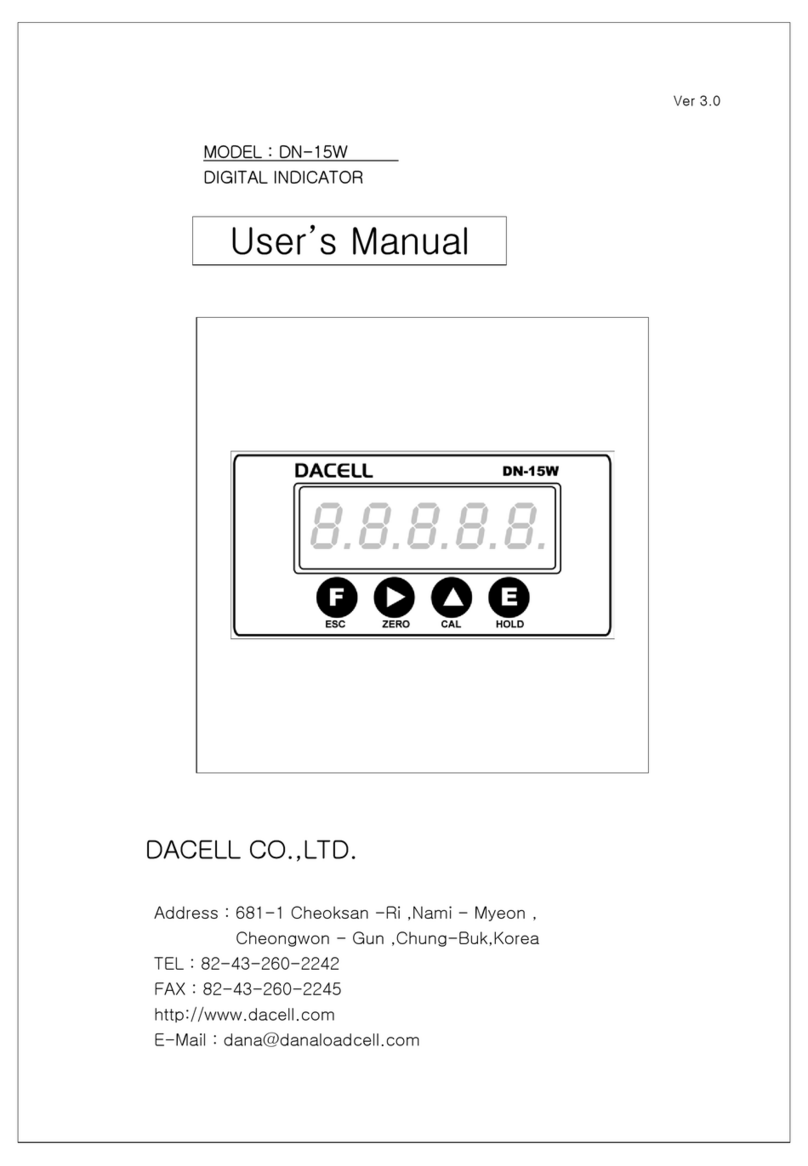
dacell
dacell DN-15W User manual
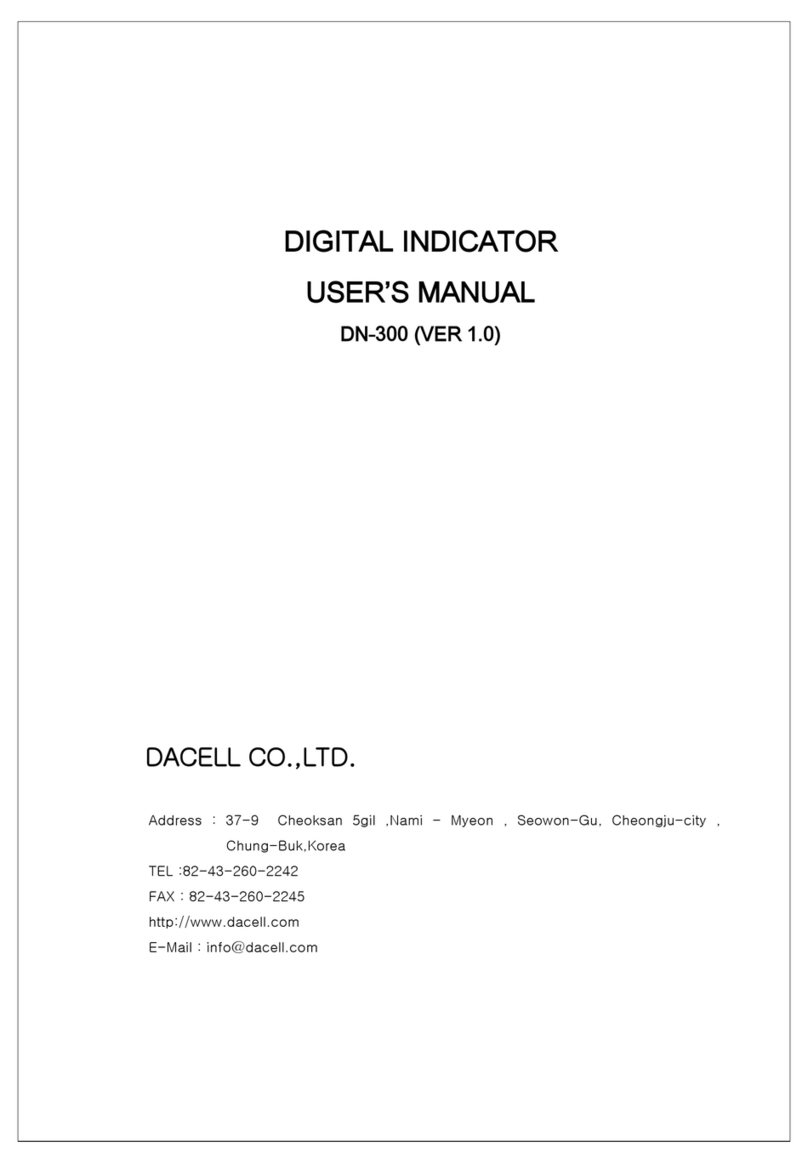
dacell
dacell DN-300 User manual
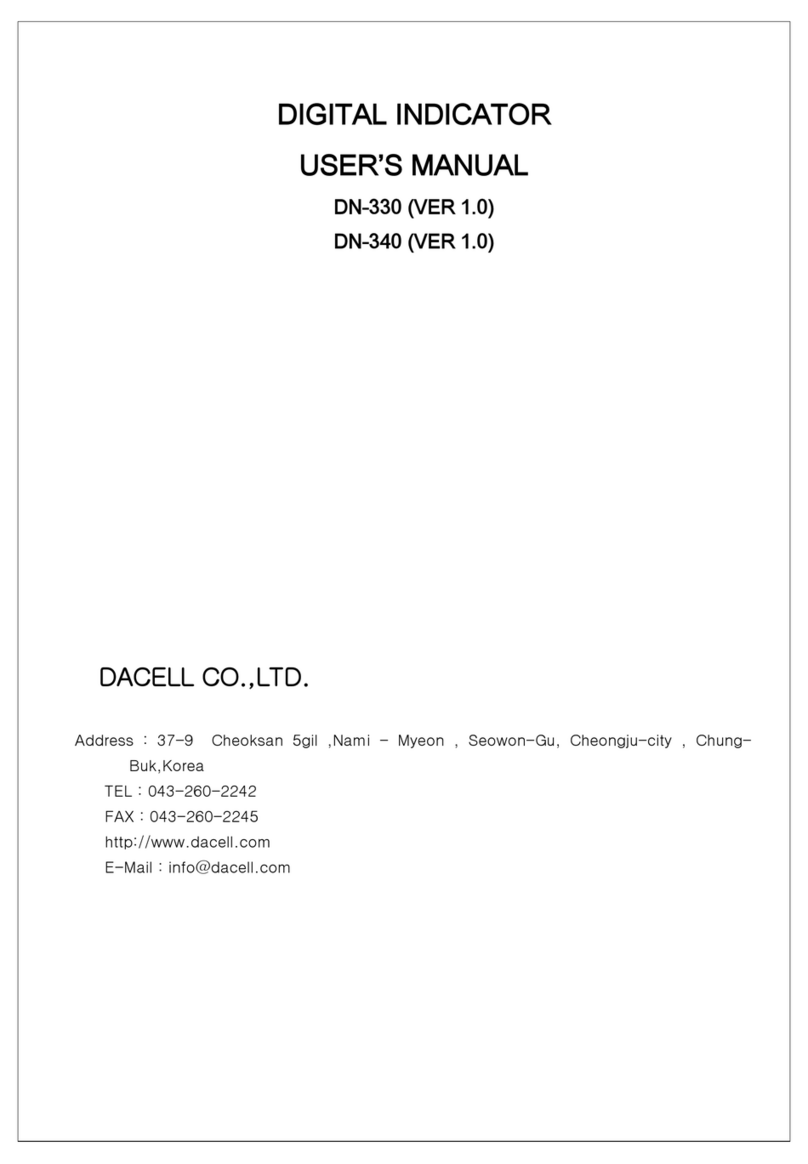
dacell
dacell DN-330 User manual
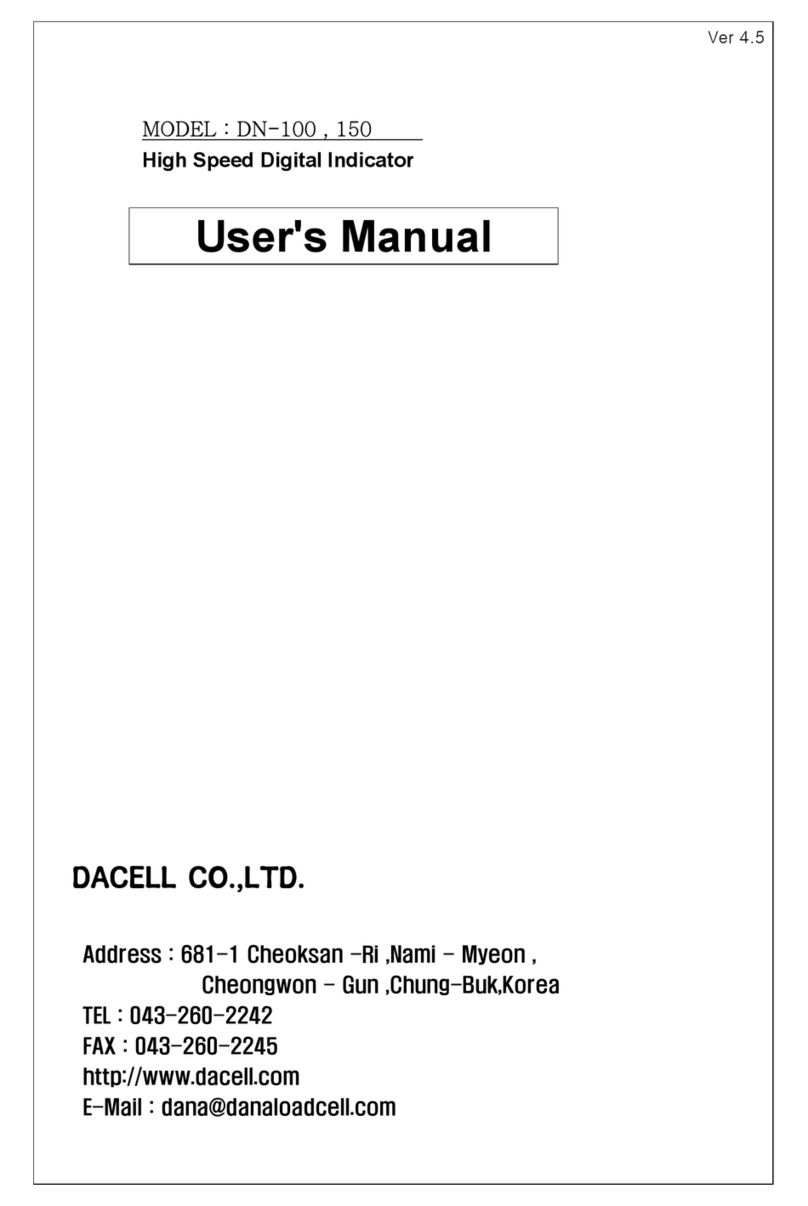
dacell
dacell DN-100 User manual
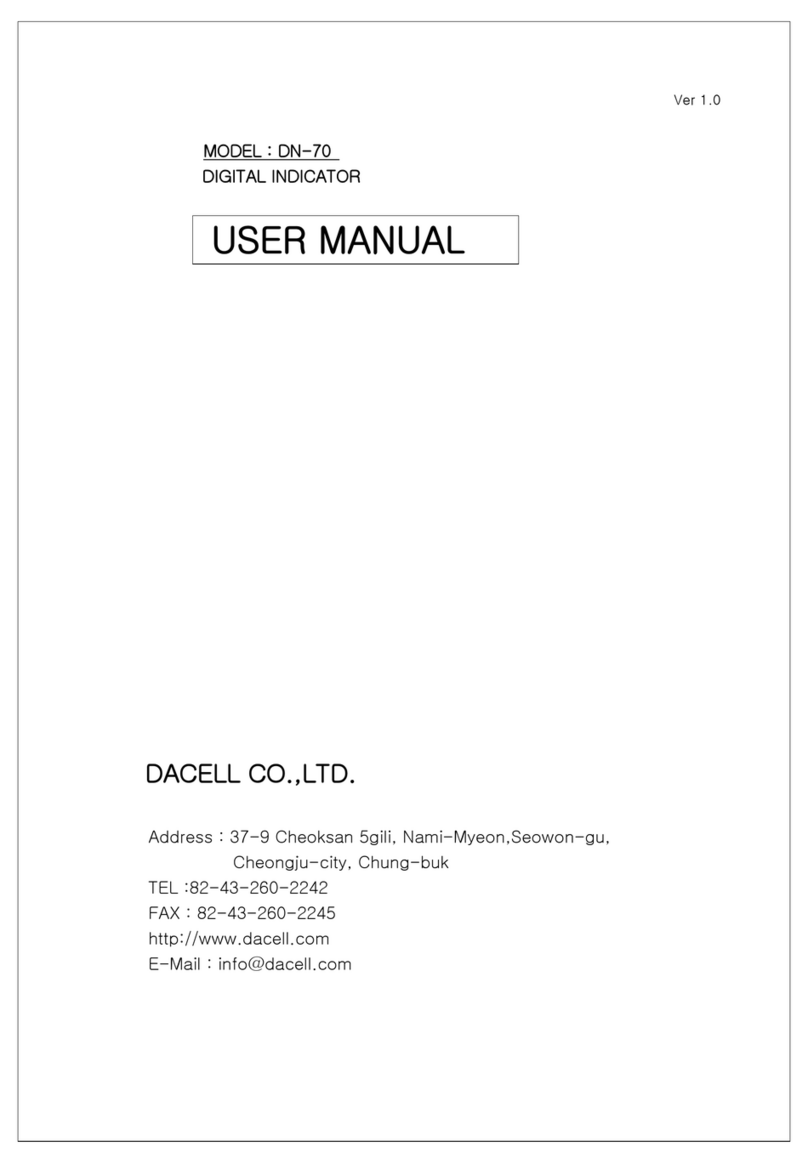
dacell
dacell DN-70 User manual
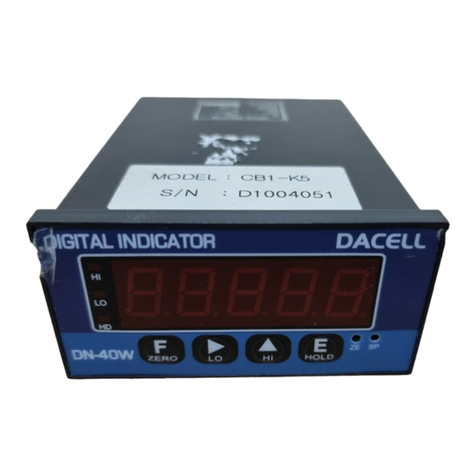
dacell
dacell DN-40W User manual
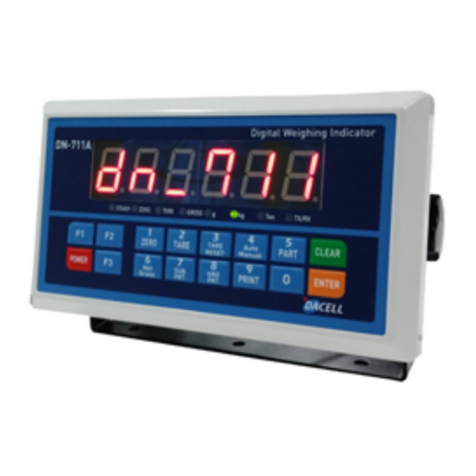
dacell
dacell DN-711A User manual
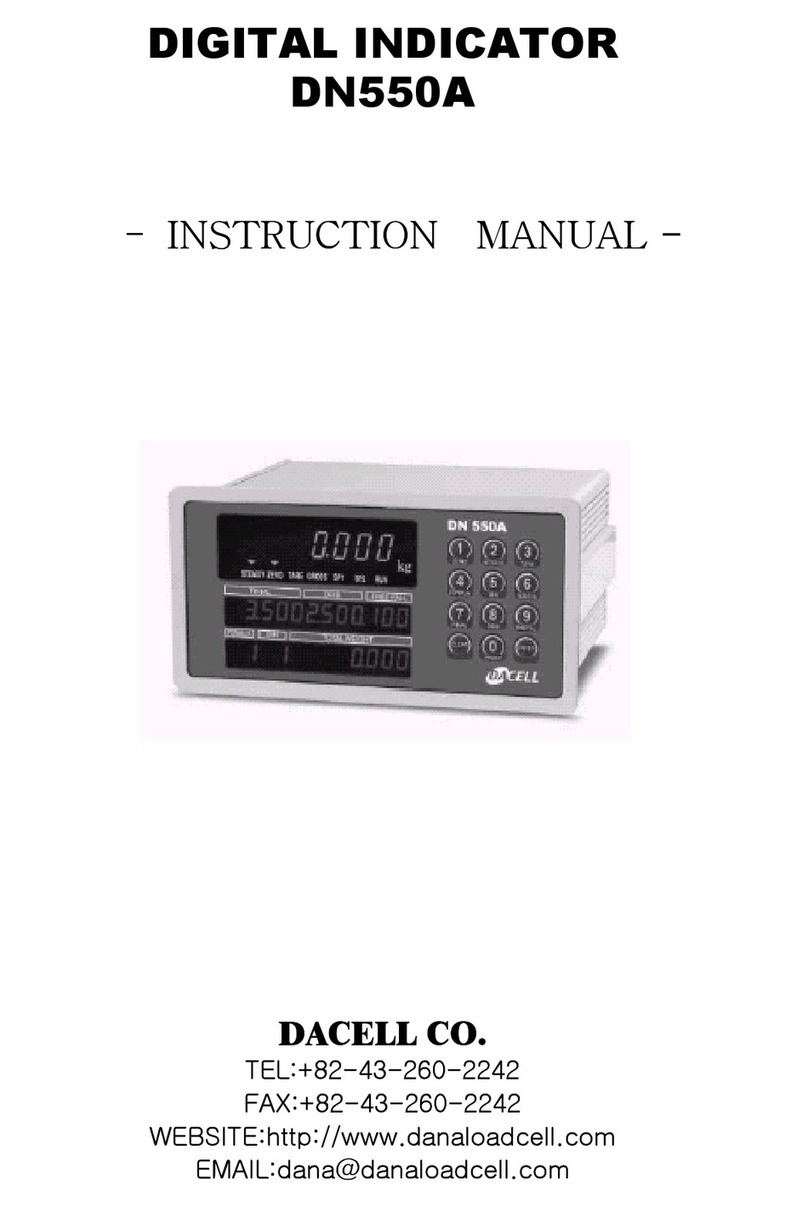
dacell
dacell DN550A User manual

dacell
dacell DN500N User manual
Popular Measuring Instrument manuals by other brands
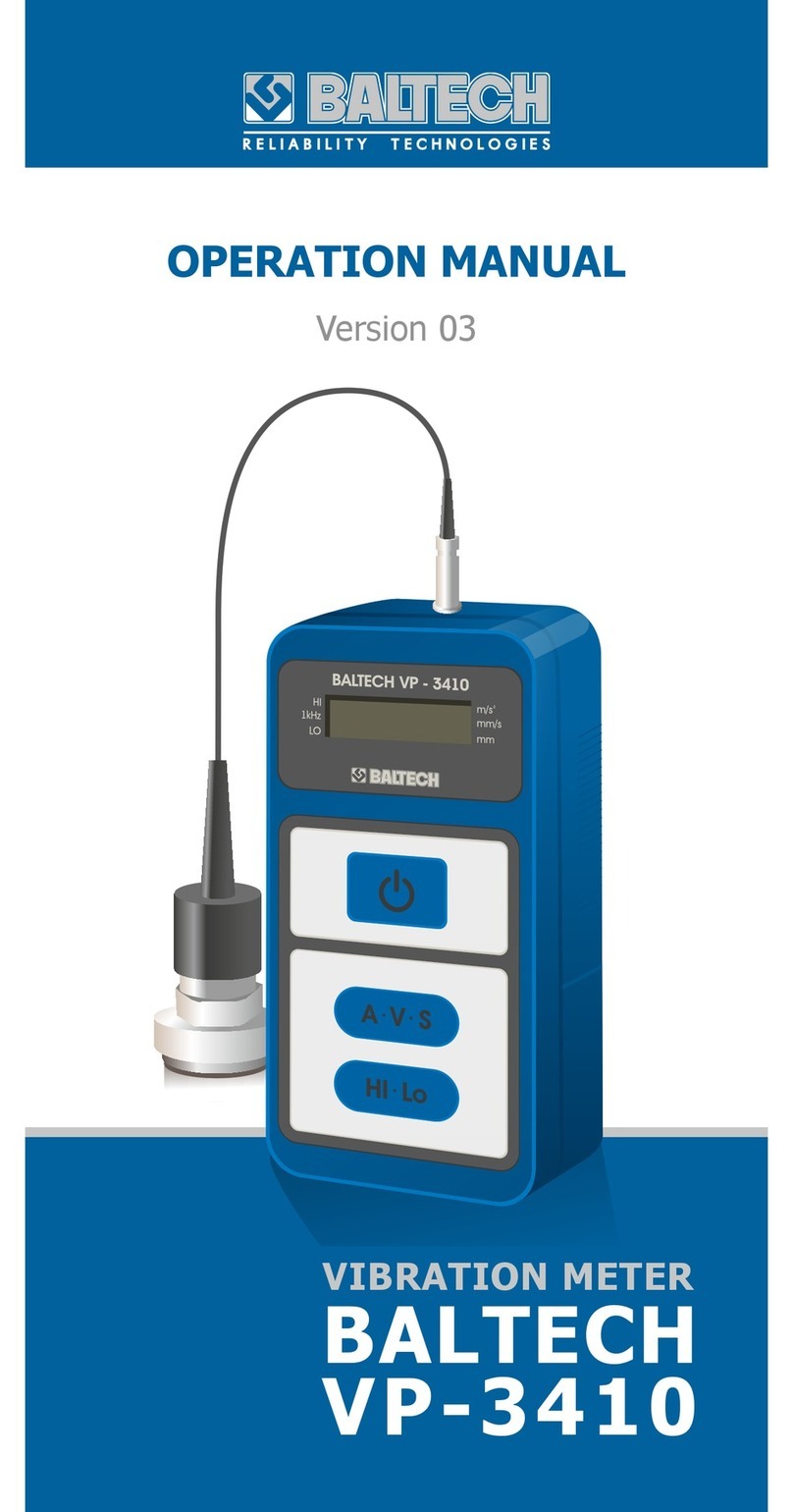
Baltech
Baltech VP-3410 Operation manual
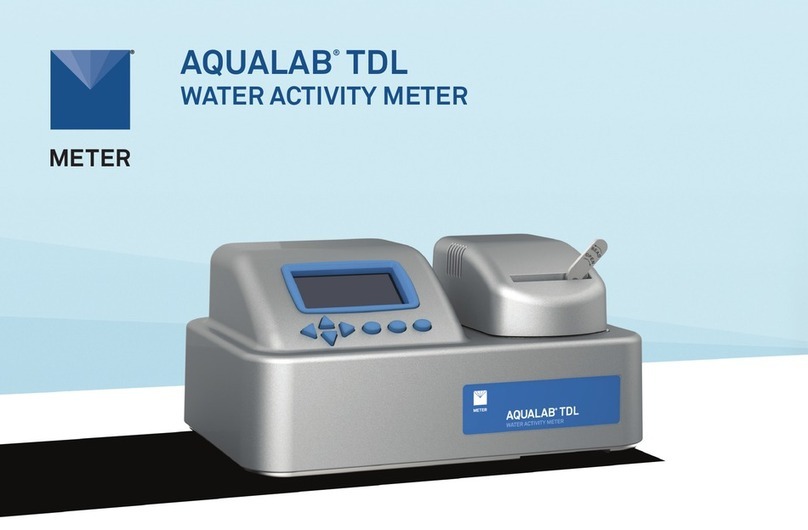
METER
METER AQUALAB TDL quick start
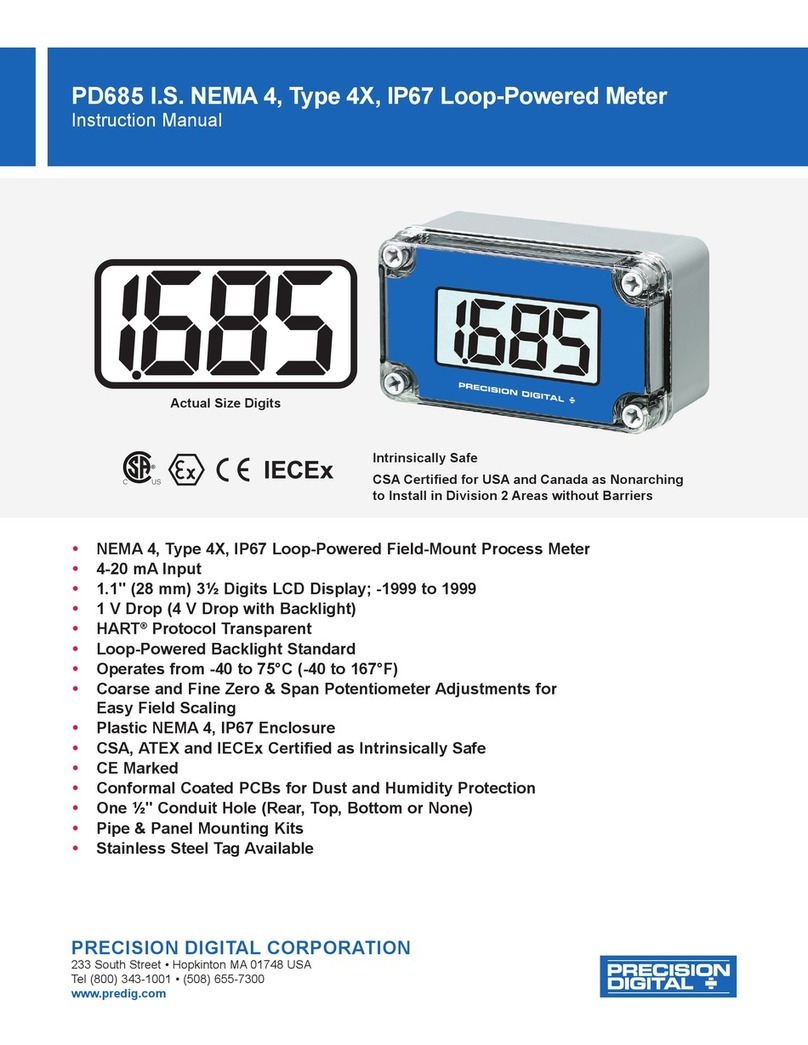
Precision Digital Corporation
Precision Digital Corporation PD685 instruction manual

CHK Power Quality
CHK Power Quality Miro PCM Technical notes
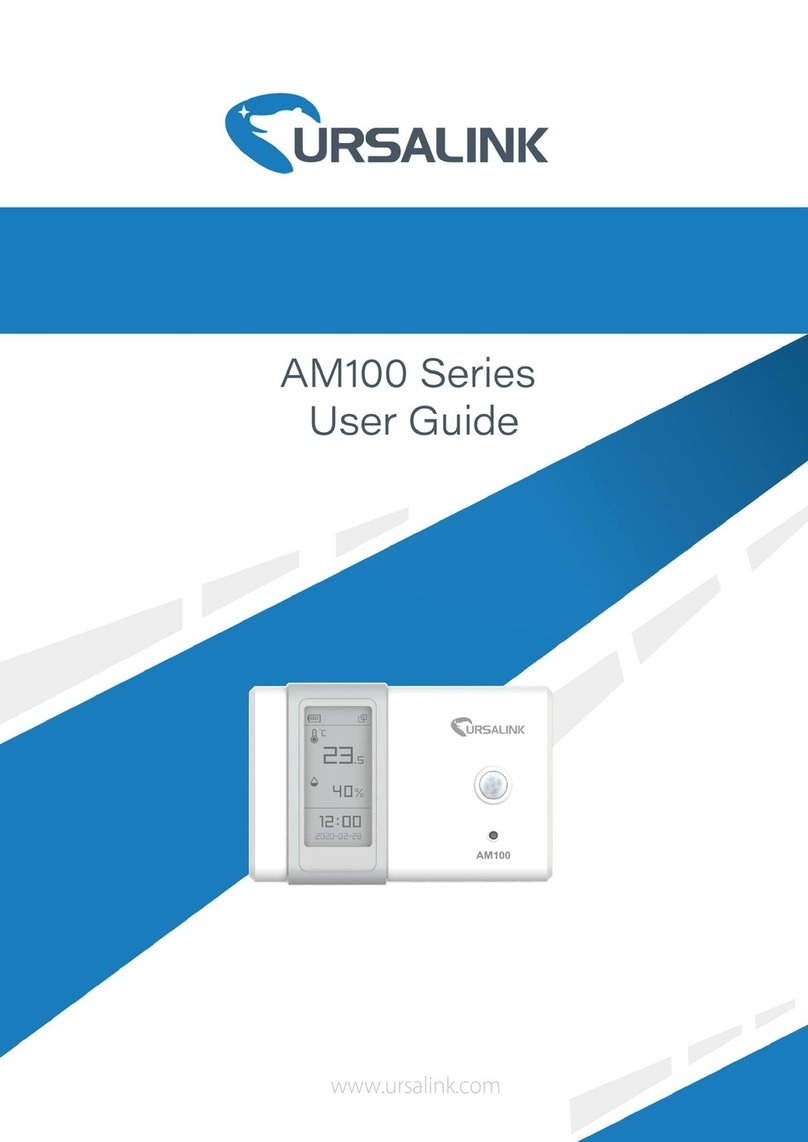
Ursalink
Ursalink AM100 Series user guide
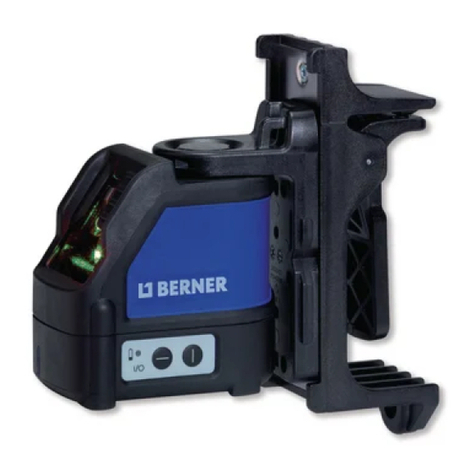
Berner
Berner BCLL TOP Instruction manual/safety instructions