DEMA 693T FOAM STATION II User manual

DEMA®MODEL 693T FOAM STATION II
INSTALLATION INSTRUCTION
I-747 Page 1 of 8
Rev. E-40261 11/13/14
1. PARTS CHECKLIST:
ITEM DESCRIPTION QTY.
A. Foam Station Assembly 1
B. ¼” ID Tubing & Foot Strainer 1
C. 3/8” ID Tubing & Foot Strainer 1
D. Ceramic Weight (For ¼” ID Tubing) 1
E. Ceramic Weight (For 3/8” ID Tubing) 1
F. Metering Tip Kit 1
G. #10 Screw & Anchor Kit Set (Total: 4 Screws & 4 Anchors) 1
H. Label Card 1
2. INSTALLATION:
This product is designed only to be used as described in this instruction sheet. Adhere to all warnings and
cautions identified in this document.
WARNING: Installations must conform to all local and national plumbing codes and use
approved backflow prevention and pressure relief devices where required.
ALWAYS DISCONNECT DISPENSER FROM WATER SOURCE WHEN DISPENSER
IS NOT IN USE.
Always read SDS for all chemicals used and follow personal protective guidelines.
A. Mounting and Water Supply:
Locate mounting holes on a permanent vertical wall. Drill all holes into the drywall using a ¼” diameter bit for use with
the included #10 screw and anchor set. (If mounting unit to wood and you do not plan to use the included anchors, drill
1/8” diameter holes.) Insert the anchors into drilled holes and hammer them into the wall until they are flush with face
of wall. Assemble the #10 screws with a phillip screwdriver into the anchors for the keyhole slots so the screw heads are
sticking out of the wall approximately ½”. Mount the unit by inserting the screw heads through the keyhole slots and
tightening the screws. Secure the unit by inserting screws into the lower 2 holes.
The water inlet is equipped with a female garden hose fitting. The fitting may be removed to permit direct connection to
3/8” NPT pipe. Note: Apply pipe dope, hand tighten, and then turn 1-1/2 times with a wrench. DO NOT OVER
TIGHTEN.
WARNING: Do not use Teflon tape to seal internal plastic threads as the extra thickness of the tape may cause
the plastic to crack. Use non-welding liquid sealant instead.
WARNING: Water supply should not exceed 125 psi and water temperature must not exceed 150°F.
B. Outlet Connection:
Connect the discharge hose to the garden hose fitting. NOTE: Be sure to clamp garden hose onto wall
approximately 1 ft. below the unit, (Clamps, screws, & anchors are not supplied.) Attach shut-off valve to the
discharge end of the hose. See Table 1 for hose limitations.
C. Chemical Supply:
WARNING: USE CARE WHEN HANDLING HAZARDOUS CHEMICALS.
Place the chemical container in a convenient location not more than six feet below the Foam Station as greater lifts will
reduce injection capabilities. The top of the container should not be above the Foam Station. Cut the vinyl tube to any
convenient length that will allow the tubing to reach the bottom of the container. Drop the tubing end with the strainer

DEMA®MODEL 693T FOAM STATION II
INSTALLATION INSTRUCTION
I-747 Page 2 of 8
Rev. E-40261 11/13/14
into the chemical container. Push the other tubing end over the metering knob barb. Note: Remove ball valve knob
and Foam Station cover for chemical supply installation.
3. CHEMICAL ADJUSTMENT:
The chemical feed rate is controlled by metering tips screwed into the barb on the side of the Foam Station. The feed rates
can be changed using different metering tips. To select the proper metering tip size for the desired dilution ratio, refer to
Table 2 (Foamer) and Table 3 (P203 Injector).
1 cps (centipoise) is equal to the viscosity of water
75 cps is approximately equal to the viscosity of 10 weight motor oil
200 cps is approximately equal to the viscosity of most dishwashing detergents
Injection rate can be doubled with no tip by using ½” ID inlet tubing. Use a short piece of 3/8 in. ID tubing on
proportioner and foot valve barbs for a bushing.
TABLE 1: Outlet Garden Hose Connection
GARDEN HOSE SIZE AND
LENGTH MIN. PRESSURES
WATER AIR
25’ OF ¾” ID 40 PSI 40 PSI
50’ OF ¾” ID 50 PSI 40 PSI
25’ OF ½” ID 60 PSI 40 PSI
TABLE 2: Foamer Injection Rate
Metering
Tip Color
Injection Rate for Viscosities Shown
1 cps 75 cps 200 cps 500 cps
Oz/Gal Ratio Oz/Gal Ratio Oz/Gal Ratio Oz/Gal Ratio
Clear 0.84 152-1 0.65 197-1 0.45 284-1 0.30 427-1
Purple 1.35 95-1 1.10 116-1 0.90 142-1 0.60 213-1
Yellow 2.40 53-1 2.00 64-1 1.50 85-1 1.10 116-1
Green 4.20 30-1 3.40 38-1 2.65 48-1 2.10 61-1
Pink 5.25 24-1 4.50 28-1 3.45 37-1 2.60 49-1
Turquoise 9.40 14-1 7.25 18-1 5.45 23-1 3.70 35-1
Black 11.75 11-1 8.80 15-1 6.35 20-1 4.20 30-1
Gray 14.50 9-1 10.80 12-1 7.75 17-1 4.75 27-1
Red 18.00 7-1 13.20 10-1 8.30 15-1 5.00 26-1
Blue 20.60 6-1 14.70 9-1 8.65 14.8-1 5.20 25-1
Brown 24.10 5-1 16.15 8-1 9.30 14-1 5.50 23-1
White 27.50 4.7-1 17.80 7-1 9.70 13-1 5.70 22-1
Orange 30.00 4.3-1 18.50 6.9-1 10.10 12.7-1 5.85 21.9-1
Light Blue* 32.00 4-1 18.90 6.8-1 10.20 12.5-1 6.00 21-1
Tan* 32.50 3.9-1 19.25 6.6-1 10.40 12.3-1 6.25 20.5-1
None 34.25 3.7-1 20.45 6-1 10.60 12-1 6.50 20-1
All induction rates are based on 40 psi water pressure and 40 psi air pressure.
*The tips are not included in the standard tip pack.

DEMA®MODEL 693T FOAM STATION II
INSTALLATION INSTRUCTION
I-747 Page 3 of 8
Rev. E-40261 11/13/14
Table 3: P203CAM Injector Injection Rate
Metering
Tip Color
Injection Rate for Viscosities Shown
1 cps 75 cps 200 cps
Oz/Gal Ratio Oz/Gal Ratio Oz/Gal Ratio
Tan 0.40 320-1 0.25 512-1 0.20 640-1
Orange 0.50 256-1 0.35 366-1 0.25 512-1
Turquoise 0.75 171-1 0.45 284-1 0.35 366-1
Pink 0.95 135-1 0.65 197-1 0.45 284-1
Light Blue* 1.30 98-1 0.80 160-1 0.55 233-1
Brown 1.50 85-1 0.90 142-1 0.60 213-1
Red 1.90 67-1 1.00 128-1 0.70 183-1
White 2.25 57-1 1.30 98-1 0.80 160-1
Green 2.64 49-1 1.50 85-1 0.90 142-1
Blue 3.20 40-1 1.75 73-1 1.00 128-1
Yellow 4.85 26-1 2.25 57-1 1.10 116-1
Black 6.50 20-1 2.40 53-1 1.15 111-1
Purple 9.20 14-1 2.70 47-1 1.20 107-1
Gray 10.40 12-1 2.85 45-1 1.25 102-1
No Tip 12.80 10-1 3.50 37-1 1.55 83-1
* Metering tip color was formerly clear.
All injection rates are based on 40 PSI inlet water pressure and a water flow rate of 2.5 GPM.
4. OPERATION:
The 693T Foam Station permits the operator to select a chemical to foam (left hand lever), or a chemical to spray (right hand
lever) or a clear water rinse (middle lever) by opening and closing the appropriate valve with its lever. ONLY ONE
VALVE SHOULD BE OPEN AT ANY TIME. If two valves are opened simultaneously, the injector will not draw
chemical.
NOTE: When using the spray wand, make sure that the shut-off valve at the end of the hose is in the fully open position in
order to draw chemical product.
To Foam:
First: Open the left hand lever all the way. Water rushing through the foamer will draw up soap and send soapy water
through the hose.
Next: Pull out on the air regulator knob above the air gage. Set the air regulator to 40psi. Open the air valve on the left side
of the 693T. Adjust the air regulator upwards gradually until you obtain the thickness of foam you desire. Push the air
regulator knob back in to lock the setting in place. This operation must be repeated in the same order each time the 693T is
shut down and restarted (water first then gradually build up air pressure).
TABLE 4: Water Flow & Air Flow Setting.
PRESSURE (PSI)
40 50 60 80
WATER FLOW (GPM) 1.4 1.6 1.7 2.1
AIR FLOW (SCFM) 3.5 4.2 4.8 6.1

DEMA®MODEL 693T FOAM STATION II
INSTALLATION INSTRUCTION
I-747 Page 4 of 8
Rev. E-40261 11/13/14
5. SERVICING:
CAUTION: TURN OFF WATER SUPPLY BEFORE SERVICING. WHEN SERVICING UNIT, BE SURE THAT
REPLACEMENT PARTS HAVE BEEN INSTALLED ACCORDING TO DRAWING. BE CERTAIN CHECK
VALVE PARTS ARE IN PLACE.
PROBLEM SEE SITUATION:
Unit will not draw or stops drawing chemical 1, 2, 3, 5, 6, 10, 11, 12, 13, 15, 16, 17
Poor foam quality 1, 2, 3, 5, 6, 10, 11, 12, 13, 15, 16
Foam surges 1, 2, 3, 4, 5, 6, 8, 9, 10, 11, 12, 13, 15, 16
Foam output is too wet 1, 3, 4, 5, 6, 7, 8, 9, 10, 11, 13, 16
Foam output is too dry 2
Water is flowing into chemical container 12
Foam does not clean adequately 4, 8, 11, 14
POSSIBLE SITUATIONS
Situation Cause Solution
1 Chemical tube not immersed in chemical
or chemical depleted. Immerse tube in chemical or replace.
2 Air pressure is too high for water. Adjust air regulator down.
3 Water pressure is too low. At least 30 psi is required. Increase if possible, or decrease air pressure.
4 Chemical to water ratio is too low. Change metering tip to one that is larger.
5 Foam hose is kinked. Straighten hose.
6 Foam hose is too long or wrong size. See Table 1.
7 Air supply is inadequate. Increase air pressure by regulating up.
8 Detergent is wrong. Use a more effective detergent, and be sure that product is
recommended for foaming.
9 Using an oiler on the airline may
deteriorate the quality of the foam. Use only clean, dry air.
10 Holes or cuts are in chemical inlet tube. Replace the tube.
11 Strainer and/or metering tip are blocked. Remove, clean or replace.
12 Solution check valve is not working. Remove, clean or replace.
13 Air regulator is not working. Remove, clean or replace.
14 Soil has hardened on surface. Reapplication may be necessary. Be sure to rinse foam off before it
dries.
15 Rust or build-up is clogging the foamer
aspirator. Disconnect water from unit and remove injector from unit. Visually
inspect. Remove blockage.
16 Water scale or chemical build-up may
have formed in the water jets. Place the chemical tube in descaling acid and completely open the shut-
off valve. Let unit run until the chemical tube is filled with acid, then
close shut-off valve and water supply. Elevate the chemical tubing and
outlet hose until acid has had enough time to descale. Repeat if
necessary. For severe cases, disassemble unit and soak foamer body in
descaling acid.
17 More than one valve is open. Close the rinse valve and the injector valve that is not in use.

DEMA®MODEL 693T FOAM STATION II
INSTALLATION INSTRUCTION
I-747 Page 5 of 8
Rev. E-40261 11/13/14
Return Policy
No merchandise may be returned for credit without DEMA Engineering Company’s written permission. Return Merchandise
Authorization (RMA) number required in advance of return.
Warranty
DEMA products are warranted against defective material and workmanship under normal use and service for one year from the date
of manufacture. This limited warranty does not apply to any products which have a normal life shorter than one year or failure and
damage caused by chemicals, corrosion, improper voltage supply, physical abuse or misapplication. Rubber and synthetic rubber
parts such as “O”-rings, diaphragms, squeeze tubing and gaskets are considered expendable and are not covered under warranty. This
warranty is extended only to the original buyer of DEMA products. If products are altered or repaired without prior approval of
DEMA, this warranty will be void.
Defective units or parts should be returned to the factory with transportation prepaid. If inspection shows them to be defective, they
will be repaired or replaced without charge. F.O.B. factory DEMA assumes no liability for damages. Return merchandise
authorization number to return units for repair or replacement must be granted in advance of return.

DEMA®MODEL 693T FOAM STATION II
INSTALLATION INSTRUCTION
I-747 Page 6 of 8
Rev. E-40261 11/13/14
NO. PART NO. DESCRIPTION
1 100-38 Strainer Washer
2 65-10 Swivel Coupling
3 65-14 Hose Fitting – Medium Long
4 69-8-2 Top Manifold
5 66-153 Pipe Plug & O-Ring Assy.
6 99-8-2 Valve
7 69-2 Adapter
8 30-5-14 O-Ring (EP)
9 58-83-1 Pipe Adapter (3/8”)
10 69-9-1 Adapter
11 69-4 Bottom Manifold
12 65-18-1 Outlet Fitting
13 93-15-2 Pressure Gauge
14 25-137-12 ¼” NPT Nipple X 1 ½ Lg.
NO. PART NO. DESCRIPTION
15 16-11 ¼” NPT Ball Valve
16 24-11L Foot Strainer (For 3/8” ID Tubing)
17 24-11MP Foot Strainer (For 1/4” ID Tubing)
18 61-107 Ceramic Weight (3/8” ID Tubing)
19 61-107-2 Ceramic Weight (1/4” ID Tubing)
20 100-12 Vinyl Tubing (1/4” ID X 8’ Lg.)
21 100-12L Vinyl Tubing (3/8” ID X 8’ Lg.)
ACCESSORIES
NO. PART NO. DESCRIPTION
22 93-18 Plastic Foam Wand
23 93-14 3/4” ID X 25’ Lg. Outlet Hose
ACCESSORY
13
8
14
20 21
15
16 17
1
FOAMER ASSEMBLY
(SHOWN EXPLODED
ON PAGE 8)
1918
6
9
8
7
23
6
4
23
22
12
11
8
P203CTC
(SHOWN EXPLODED
ON PAGE 7)
8
10
6
5

DEMA®MODEL 693T FOAM STATION II
INSTALLATION INSTRUCTION
I-747 Page 7 of 8
Rev. E-40261 11/13/14
NO. PART NO. DESCRIPTION
1 24-67 Screw (4 Req’d)
2 100-15- Metering Tip (Specify Color)
3 24-62-SP Metering Knob Kit
4 24-25S O-Ring (Silicone)
5 24-24P Check Valve Ball
6 24-23-2 Check Valve Spring – Hasteloy
7 24-37-7 Check Valve Core
8 25-29S O-Ring (Silicon)
9 24-68 Injector Body
ACCESSORIES
NO. PART NO. DESCRIPTION
10 100-15K Metering Tip Kit
BREAKDOWN OF P203CTC INJECTOR
8
7
2
10
6
5
4
1
9
3

DEMA®MODEL 693T FOAM STATION II
INSTALLATION INSTRUCTION
I-747 Page 8 of 8
Rev. E-40261 11/13/14
NO. PART NO. DESCRIPTION
1 29-18-4 7/16 Internal Snap Ring
2 29-17-2 Washer (S.S.) – Air Nozzle
3 29-7 O-Ring (Viton)
4 29-5P Ball 11/32” Dia. (Teflon)
5 29-16 Nozzle
6 29-11 Diffuser
7 29-15-2 Pin
8 69-3 Adapter
9 29-12 Check Valve Repair Kit
10 25-29V Metering Knob O-Ring (Viton)
11 23-34-3 Check Valve Core
12 23-9-2 Check Valve Spring – Hasteloy
13 23-10 Ball (9/32” Dia.) – (S.S.)
14 23-11V Check Valve O-Ring (Viton)
15 23-32T Metering Knob
NO. PART NO. DESCRIPTION
16 61-9- Metering Tip (Specify Color)
17 30-5V-14 O-Ring (Viton)
18 29-14 Air Nozzle
19 93-6-2 Air Check Valve Spring - Hasteloy
20 26-49P Ball 3/16” (Teflon)
21 90-35V Air Check Valve O-Ring (Viton)
22 29-17-3 Washer (S.S.) – Foamer Inlet
23 29-18-2 5/16” Internal Snap Ring
24 93-1 Pressure Regulator
25 29-10 Hi Lo Screw (4 Req’d)
ACCESSORIES
NO. PART NO. DESCRIPTION
26 61-9K Metering Tip Kit
24 23 20 18
14
15
26 16
25
19
22 21
13
12
9
10
17
11
4
2
1
6
8
7
5
3
Other DEMA Dispenser manuals
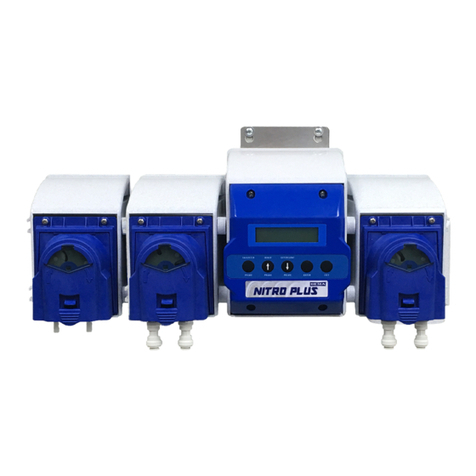
DEMA
DEMA Nitro Plus User manual
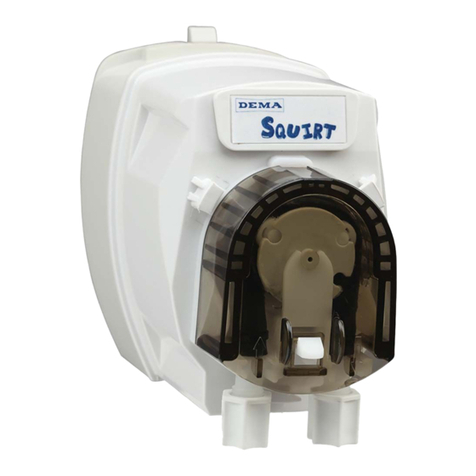
DEMA
DEMA SQUIRT DRAIN UNIT User manual

DEMA
DEMA Nitro User manual
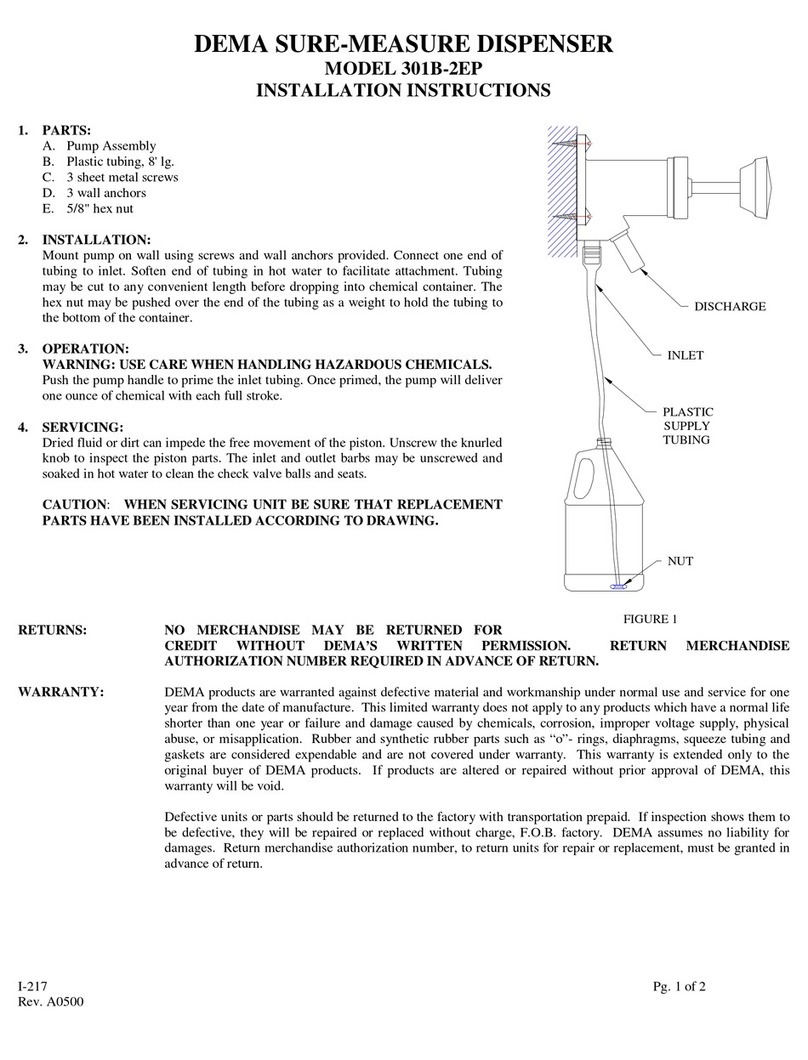
DEMA
DEMA 301B-2EP User manual
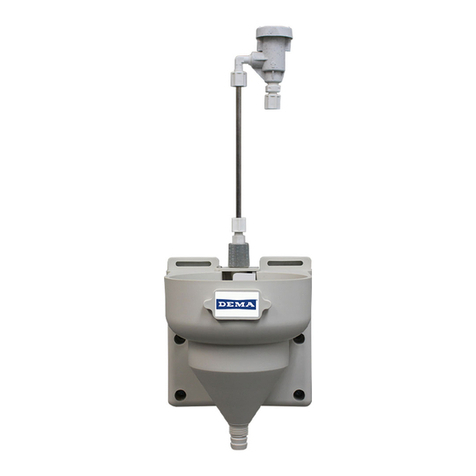
DEMA
DEMA 5800V.BV User manual
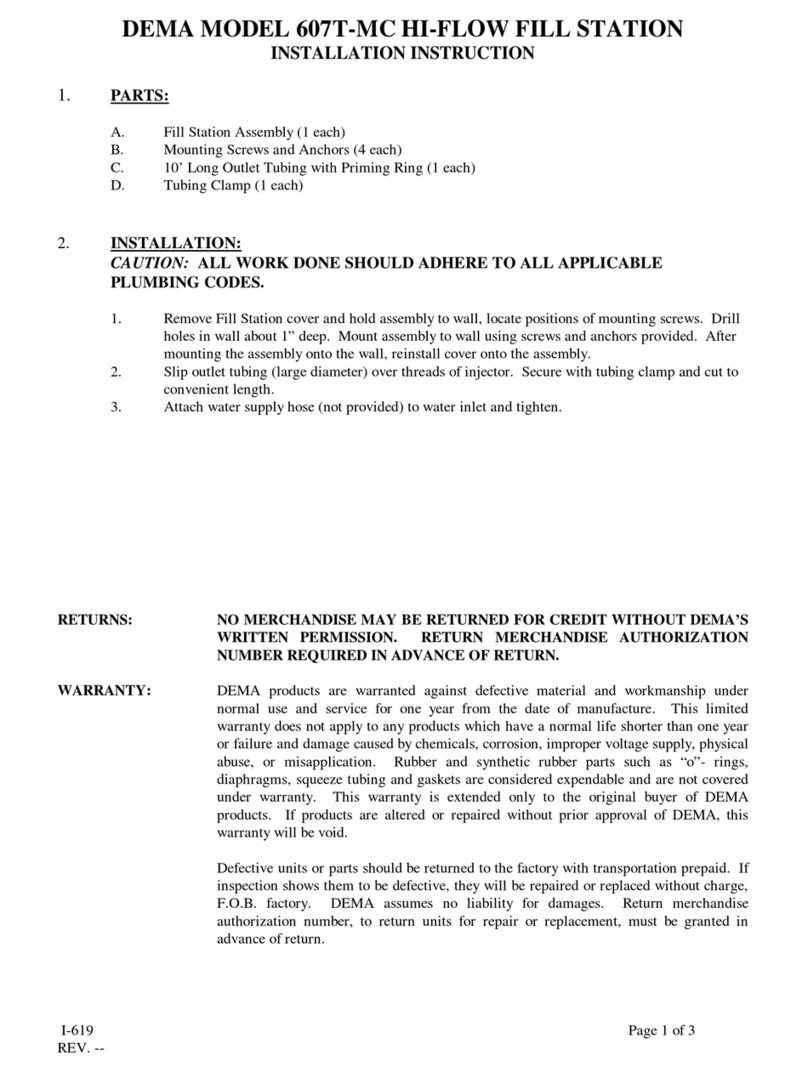
DEMA
DEMA 607T-MC User manual
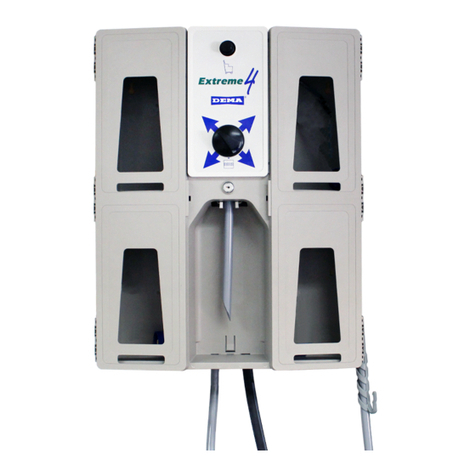
DEMA
DEMA 665 Series User manual
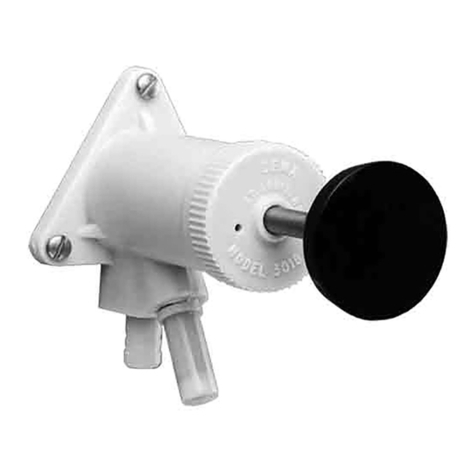
DEMA
DEMA 301B-C User manual

DEMA
DEMA Laundry Master 830 User manual
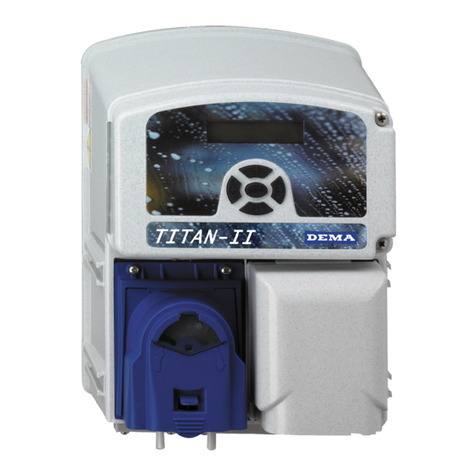
DEMA
DEMA TITAN II User manual
Popular Dispenser manuals by other brands

Servend
Servend MD 150 Replacement manual
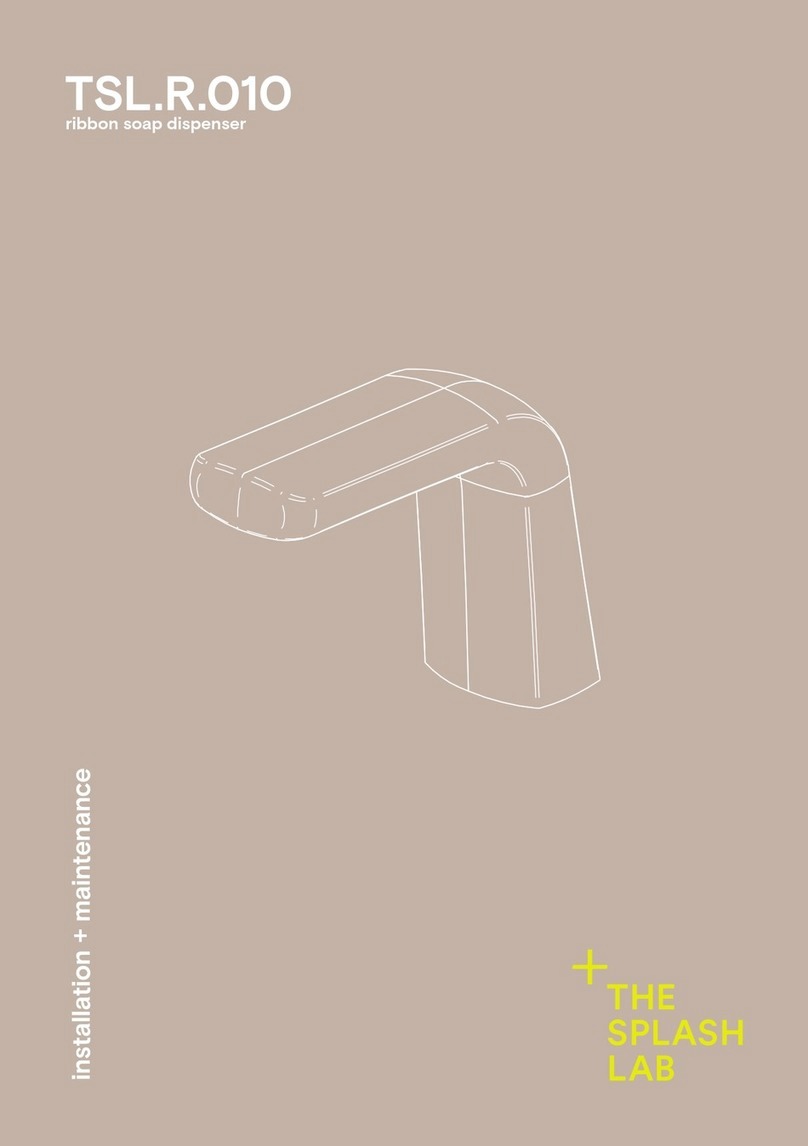
The Splash Lab
The Splash Lab TSL.R.010 Series Installation & maintenance

Presto
Presto 52043 installation guide

Hilti
Hilti HDE 500-22 Original Operating Instruction
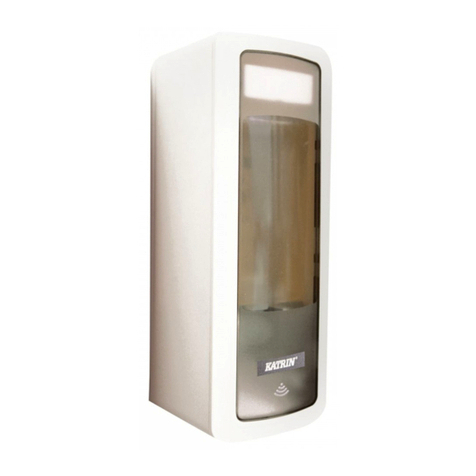
KATRIN
KATRIN 44672 Measurements and installation instructions

U-Line
U-Line H-1131 installation instructions