Enerpac SWE189DTTC-NBT User manual

Operation and Maintenance Manual
To reduce the risk of injury, user must read and understand this document before use.
Document Number: L4554
Document Revision: D
Issue Date: May, 2021
Language: English EN
Model No. SWE189DTTC-NBT (Pratt & Whitney PWA64005)
Sweeney Digital Turning Tool (DTT)

2L4554_d
ABOUT US
Enerpac is a global market leader in high pressure hydraulic
tools, controlled force products, portable machining, on-
site services and solutions for precise positioning of heavy
loads. As a leading innovator with over a 100 year legacy,
Enerpac has helped move and maintain some of the largest
structures on earth. When safety and precision matters, elite
professionals in industries such as aerospace, infrastructure,
manufacturing, mining, oil & gas and power generation rely
on Enerpac for quality tools, services and solutions. For
additional information, visit www.enerpac.com.
WARRANTY
Refer to the Enerpac Global Warranty document for terms and conditions of the product warranty. Such warranty
information can be found at www.enerpac.com.
NAMEPLATE
Refer to the controller nameplate for the product model number, serial number and other applicable information.
www.facebook.com/enerpac
www.youtube.com/enerpac
www.linkedin.com/company/enerpac
www.twitter.com/enerpac
Note: Nameplate appearance and details may vary.

L4554_d 3
1.0 SAFETY...................................................................................................................................................... 4
2.0 COMPLIANCE ........................................................................................................................................... 6
3.0 SPECIFICATIONS AND PRODUCT DATA ................................................................................................ 7
4.0 DESCRIPTION......................................................................................................................................... 11
5.0 FEATURES AND COMPONENTS ........................................................................................................... 12
6.0 POWER REQUIREMENTS ...................................................................................................................... 15
7.0 SET UP..................................................................................................................................................... 15
8.0 TURNING TOOL INSTALLATION............................................................................................................ 18
9.0 PENDANT SCREENS OVERVIEW .......................................................................................................... 18
10.0 BEGINNING THE INSPECTION.............................................................................................................. 20
11.0 MAINTENANCE....................................................................................................................................... 21
12.0 CIRCUIT BREAKER ................................................................................................................................ 22
13.0 CLEANING............................................................................................................................................... 22
14.0 PRODUCT DISPOSAL............................................................................................................................. 22
15.0 STORAGE ................................................................................................................................................ 22
16.0 TROUBLESHOOTING ............................................................................................................................. 23
17.0 ENGINE LIBRARY ................................................................................................................................... 24
18.0 REPLACEMENT PARTS LIST ................................................................................................................. 25
CONTENTS PAGE

4L4554_d
• Keep this manual for future reference in a place that
is accessible to all persons operating or servicing
the tool.
• Always perform a visual inspection of the tool before
placing it into operation. If any problems are found,
do not use the tool.
1.2 Electrical Shock Hazards
Risk of electric shock! Failure to observe the
following instructions and precautions may
result in serious personal injury or death.
• Connect the controller power cord only to a
grounded electrical outlet. Use only a power cord
with a ground pin.
• Unplug controller power cord from outlet before
performing cleaning, maintenance or repairs.
• The tool is intended for indoor use only.
• In the event that the tool is used outdoors, do not
expose it to rain, standing water or damp conditions.
In such cases, the tool should be brought indoors.
1.3 Electrical Safety
WARNING
Failure to observe and comply with the following
precautions may result in death or serious personal injury.
Property damage could also occur.
• High voltage is present inside the tool even when
tool drive motor is off. Before servicing the tool, be
sure that the controller power cord is disconnected
from the electrical outlet or other electrical power
source.
• Do not leave the tool unattended in the workplace
when the controller is connected to AC power
supply. Take all reasonable precautions to avoid
unauthorized use.
• If it is not possible to unplug the power cord from the
AC power outlet, the power must be turned off and
locked out at the AC power supply.
• Always disconnect the controller from AC power
before transporting it.
• Be sure that controller power is switched off before
connecting or disconnecting the motor cable.
• Make sure the controller cooling vents are
unobstructed and free of dirt or dust.
• Do not service or clean the tool while the tool is
operating and/or if controller is connected to AC
power supply.
WARNING
1.0 SAFETY
Read all instructions carefully. Follow all recommended
safety precautions to avoid personal injury as well as
damage to the product and / or damage to other property.
Enerpac cannot be responsible for any damage or injury
from unsafe use, lack of maintenance, or incorrect
operation. Do not remove warning labels, tags, or decals.
In the event that any questions or concerns arise, contact
Enerpac or a local Enerpac distributor for clarification.
Save these instructions for future use.
If you have never been trained on turbine engine turning
equipment and related safety precautions, consult your
distributor or service center for information about Enerpac
training courses.
This manual follows a system of safety alert symbols,
signals, words, and safety messages to warn the user of
specific hazards. Failure to comply with these warnings
could result in death or serious personal injury, as well as
damage to the equipment or other property.
The Safety Alert Symbol appears throughout
this manual. It is used to alert you to potential
physical injury hazards. Pay close attention
to Safety Alert Symbols and obey all safety
messages that follow this symbol to avoid the possibility
of death or serious injury.
Safety Alert Symbols are used in conjunction with certain
Signal Words that call attention to safety messages or
property damage messages and designate a degree or
level of hazard seriousness. The Signal Words used in this
manual are WARNING, CAUTION and NOTICE.
WARNING
Indicates a hazardous situation that, if not
avoided, could result in death or serious personal injury.
CAUTION Indicates a hazardous situation that, if not
avoided, could result in minor or moderate personal injury.
NOTICE
Indicates information considered important,
but not hazard related (e.g. messages related to property
damage). Please note that the Safety Alert Symbol will
not be used with the signal word.
1.1 General Safety Precautions
Failure to observe and comply with the following
precautions could result in death or serious personal
injury. Property damage could also occur.
• Read and completely understand the safety
precautions and instructions in this manual before
operating the tool or preparing it for use.
• Wear appropriate personal protective equipment
(such as safety glasses and face shield). The
operator must take precautions against injury due to
flying debris caused by possible failure of the tool or
workpiece.
• During operation, keep hands and fingers away from
the work area to avoid personal injury.
WARNING

L4554_d 5
1.4 Grounding Instructions
Failure to observe the following instructions and
precautions may result in serious personal injury or death.
• The tool must be properly grounded. In the event
of malfunction or breakdown, grounding provides a
path of least resistance for electric current to reduce
the risk of electric shock. The controller is equipped
with a cord having an equipment grounding
conductor.
• A grounding plug is included with the cord. The plug
must be plugged into an appropriate outlet that is
properly installed and grounded in accordance with
all local codes and ordinances.
• Improper connection of the controller grounding
conductor can result in electric shock.
• If the cord and/or plug are damaged, do not connect
the controller to a live electrical outlet. Repair or
replace the damaged items as required and be
sure the grounding conductor is properly wired
before reconnecting the tool to the outlet. Consult
a qualified electrician if grounding conductor wiring
procedures are not completely understood or if
there is any doubt as to whether the tool is properly
grounded.
• Do not modify the plug provided with the controller.
If the plug will not fit in the outlet, have a proper
outlet installed by a qualified electrician.
• A qualified electrician should be consulted if there
is any doubt as to whether an outlet box is properly
grounded.
• The controller is equipped with an electric power
cord and plug specific to its rated single phase
voltage. No adapter should be used with the plug.
• If the controller must be reconnected for use on a
different type of electric circuit, the reconnection
should be made by a qualified electrician. After the
reconnection, the tool should comply with all local
codes and ordinances.
1.5 Use of Extension Cords
Failure to observe the following instructions and
precautions may result in serious personal injury or death.
• Use the proper size extension cord with the
controller power cord when use of an extension
cord is necessary. A qualified electrician should be
consulted to help specify and select the proper size
extension cord. The marked electrical rating of the
extension cord should be at least as great as the
electrical rating of the tool.
• A long extension cord should be arranged so that it
will not drape over any working area where it can be
tripped over, snagged, or pulled on unintentionally.
WARNING
WARNING
• If the tool is to be operated outdoors and an extension
cord is needed, use only an outdoor use extension
cord. An outdoor use extension cord will be clearly
marked with the suffix letter “W” and the statement
“Suitable for Use with Outdoor Appliances”.
1.6 Disconnecting Power
WARNING
Failure to observe and comply with the following
precautions could result in death or serious personal
injury. Property damage could also occur.
• Be sure that controller power is switched off before
disconnecting plug from electrical outlet.
• Do not unplug the controller by pulling on the cord.
To unplug, grasp the plug, not the cord.
• Disconnect plug from electrical outlet when the tool
is not in use and before servicing or cleaning the
tool.
1.7 Pendant Battery Safety
Precautions
Lithium ion batteries may explode or burn due to improper
use.
Failure to observe and comply with the following
precautions could result in death or serious personal
injury. Property damage could also occur.
• Always use the correct batteries for the pendant. Do
not attempt to use a non specified battery. Refer to
Section 3.3 for required battery type.
• Install the batteries in the proper polarity. Observe
(+) and (-) marks.
• Do not attempt to crush, incinerate, short circuit or
disassemble the batteries. Doing so may cause fire,
explosion and burns.
• Always store and transport rechargeable batteries
in a safe, non-conductive container (never keep
a spare battery loose in a pocket, purse, etc. and
always use protective cases).
• Keep batteries and pendant away from flames and heat.
• Do not probe the batteries or pendant with
conductive materials.
• Do not expose the batteries or pendant to wet
conditions or excessive humidity.
• Do not use any rechargeable battery if any visible
damage is present, or if known mishandling,
accidental or otherwise, has occurred
• Do not attempt to repair or modify the batteries.
• Store spare batteries in a cool, dry environment and
in a secured area, away from children and pets.
• Refer to battery manufacturer’s instructions for
complete battery safety information.
WARNING

6L4554_d
1.8 Pendant Battery First Aid
Failure to observe and comply with the following
precautions could result in death or serious personal
injury.
Although uncommon, electrolyte may be ejected from the
pendant batteries if damage, short-circuiting, overheating
or abuse occurs. Avoid contact with electrolyte. If contact
accidentally occurs, proceed as follows:
• If you get electrolyte in your eyes, flush with water
for 15 minutes without rubbing and immediately
contact a physician.
• If you get electrolyte on your skin, wash the area
immediately with soap and water. If irritation
continues, contact a physician.
If a battery is ingested, call your local poison control
center immediately.
Refer to battery manufacturer’s instructions for complete
battery first aid information.
2.0 COMPLIANCE
2.1 Compliance Statement
Sweeney Digital Turning Tool
Model SWE189DTTC-NBT
Enerpac declares that the Sweeney Model SWE189DTTC-
NBT Digital Turning Tool (DTT) has been tested, conforms
to applicable standards and is approved to carry the CE,
CSA and FCC certification marks.
NOTICE
Acopy of the EU Declaration of Conformity is
enclosed with each shipment of the product.
WARNING

L4554_d 7
3.1 Weights
Item Weight (all models)
lb kg
Controller *5.5 2.5
Foot Pedal ** 1.3 0.6
Pendant ** 1.8 0.8
Drive Motor ** 9.8 4.4
Transport Case 10.8 4.9
Total System
(all components) 29.2 13.2
* Includes AC power cord
** Includes connecting cable
3.2 Electrical Specifications
Item Specification
Voltage 100-240 Volts AC
(universal input)
Hertz 50/60 Hz
Watts 200 W
Circuit Breaker
Rating 10 Amps
NOTE: Mains supply voltage should be within ±
10% of the rated voltage.
3.3 Additional Specifications
Item Specification (all models)
Pollution Degree 2
Installation Category II
Max Altitude 6562 ft
[2000 m]
Relative Humidity 0 to 95%
(non condensing)
Operating Temp
Range
41°F to 104°F
[5°C to 40°C]
Environment For indoor use only
3.4 Operating Parameters
Item Operating Parameter
(all models)
Speed Continuously variable
20°/min - 360°/min
Direction Bidirectional
Adjustable backlash compensation
Torque 30 ft lbs - 150 ft lbs
User selectable
Acceleration/
Deceleration
0.2 sec - 5 sec
Incrementally adjustable
Dwell Timer 0 - 60 sec
Can be held indefinitely by user
Blade Counter Displays current blade number
Blade Flagging Maximum 999 flags per stage can be
flagged for re-inspection
Pendant
Displays engine, stage and blade
information
9-button interface
Pendant
Batteries
(rechargeable)
Liion Wholesale,
Model No. LGMJ1PCB
3.6V, 3500 mAh (each battery)
UL 2054 & IEC 62133 certified
Quantity: 2
Enerpac Part No. SWE189DTTAK10
3.0 SPECIFICATIONS AND PRODUCT DATA

8L4554_d
CONTROLLER
DRIVE MOTOR
3.5 Dimensions - Controller and Drive Motor
Dimension in mm
A9.93 252.2
B4.79 121.8
C5.76 146.2
E6.55 166.4
F9.43 239.4
G3.13 79.4
H3.13 79.4
Dimension ft m
D6.0 1.8
I20.0 6.1

L4554_d 9
3.6 Dimensions - Pendant and Foot Pedal
Dimension in mm
A8.99 228.3
B3.90 99.0
C2.52 64.1
E3.52 89.5
F2.63 66.7
G0.79 20.0
Dimension ft m
D16.0 4.9
H20.0 6.1
PENDANT
FOOT PEDAL

10 L4554_d
3.7 Dimensions - Transport Case (Travel Size)
Dimension in mm
A
B
C
A21.96 557.8
B13.97 354.8
C8.85 224.8

L4554_d 11
4.0 DESCRIPTION
The Sweeney Digital Turning Tool (DTT) provides a highly accurate way of rotating components of a turbine engine to
facilitate inspection of the engine with the use of a borescope. The system controls a motor and gear assembly that
turns the turbine engine at a controlled rate of rotation by a controlled number of degrees forward or reverse to position
engine turbine blades for inspection by the operator.
There are three major components of the DTT system: the controller, the pendant and the drive motor.
The controller acts as the heart of the system to which the pendant, drive motor and foot pedal are connected.
The pendant features a custom membrane keypad with marked, easy to reach buttons. It is connected to the controller
via a 16 foot [4.9 m] USB cable. The pendant’s graphic display features wide angle viewing and all light readability
characteristics. A clip is included to suspend the pendant for ease of use and clear vision. All movement commands
and adjustments to settings and options are communicated through the pendant display.
The drive motor unit consists of a small electric motor and a custom engineered gearbox which can be coupled to
various aircraft engine drive pad adaptors. Output torque is adjustable from 30 to 150 ftlbs. Speed is adjustable from
20°/min to 360°/min.
The foot pedal is provided as a convenience and is not required to operate the tool.
Figure 1: Digital Turning Tool

12 L4554_d
1
5.0 FEATURES AND COMPONENTS
Figure 2: Controller
2 3 4 5 6
Key:
1. Pendant USB Connection
2. Drive Motor Cable Connector
3. Foot Pedal Cable Connector
4. AC Power Inlet Connector (NEMA C14)
5. Power On-O Switch and Circuit Breaker
6. Power Indicator Light

L4554_d 13
Key:
1. Adjustable Clip
2. LCD Screen Display
3. Function Buttons
4. Up Arrow Button
5. Flag Button
6. Counter-Clockwise (CCW)
Rotation Button
7. Clockwise (CW) Rotation Button
8. Down Arrow Button
9. Stop Button
10. Pendant On-O Button
11. Wrist Strap
12. Pendant USB Connection
(under protective cover)
13. Pendant USB Cable
10
11
12
9
8
4
7
5
3
6
2
1
13
Figure 3: Pendant

14 L4554_d
Figure 4: Drive Motor and Connecting Cable
Figure 5: Foot Pedal Figure 6: Transport Case
NOTICE
To prevent damage to
controller electrical circuits, be sure
power switch is in the OFF ( o) position
before connecting or disconnecting
drive motor cable.

L4554_d 15
5.1 Drive Motor
The drive motor consists of a small electric motor with a
custom gearbox capable of coupling to various aircraft
engine drive pad adaptors.
Output torque is adjustable from 30 to 150 ft lbs. Speed
is adjustable from 20°/min to 360°/min.
5.2 Pendant
A remote control pendant is provided with the DTT. The
back of the pendant contains an adjustable clip capable
of accepting ¾ inch diameter tubing for placement on
non magnetic surfaces.
The pendant is connected to the controller via a standard
16 ft [4.9 m] USB Type A cable.
Tool operation is controlled using the 9 button interface
on the pendant. Operational status is communicated via
the pendant LCD screen.
5.3 Controller
The controller consists primarily of a housing, cover, power
supply and printed circuit boards capable of tracking and
executing all communications between the pendant and
drive motor. Refer to Section 6.0 for power requirements.
The top of the controller features unique connectors to
ensure that the drive unit, foot pedal, AC power cord and
pendant are connected in the proper locations.
One USB type A port is provided for the pendant USB
cable. This port also supplies power for charging the
pendant batteries. In addition, it can be used to apply
periodic system level firmware updates via a USB drive.
5.4 Foot Pedal
The foot pedal consists of a switch unit and cable
assembly, which is connected to the pedal connector
located on the front panel of the controller. When in
MANUAL mode, the foot pedal is used to control engine
rotation. When in AUTO mode, the foot pedal provides a
hands-free way to flag blades during the inspection.
5.5 Transport Case
A Pelican™ brand transport case is provided for safely
moving and storing the tool. The tool can be operated
while leaving the controller in the case if the lid is open.
This travel size case is supplied with most DTT units.
However, if the tool is ordered with attachments, a special
larger size transport case may be provided.
6.0 POWER REQUIREMENTS
The controller is AC powered. It features auto-voltage
sensing circuitry and can be operated at 100-240 VAC,
50/60 Hz. The power inlet on all models is aNEMA C14
connection.
A 6 foot [1.8 m] power cord with a North American style
120V NEMA 5-15R plug is supplied with the controller.
Before connecting electric power to the controller, be
certain that the power supply being used is the proper
voltage and Hz. Refer to the controller data plate.
Also refer to sections 1.4 and 1.5 of this manual for
important electrical safety information and precautions.
WARNING Failure to follow the electrical safety
precautions contained in sections 1.4 and 1.5 of this
manual could result in electric shock. Death or serious
personal injury could occur.
7.0 SET UP
7.1 Delivery and Handling
Upon delivery, all components must be inspected for
damage incurred during shipping. If damage is found, the
carrier should be notified at once. Shipping damage is not
covered by the Enerpac warranty.
7.2 Before Start-up
• Be sure that the shipment includes all components
and that there is no obvious damage.
• Read the following sections of this manual to become
familiar with DTT features and safety devices.
• Verify that the AC power supply is of the correct
specifications and capacity to power the tool.
7.3 Cable Connections
Ensure that all cables are properly connected to the
controller before using the tool. Each connector is
labelled with the corresponding cable icon to help prevent
improper connections.
1. Be sure that the controller power switch is in the
OFF ( o) position.
NOTICE
Be certain that controller power is off before
connecting the drive motor cable in the following steps.
Connecting or disconnecting the drive motor cable when
power is on may result in permanent damage to controller
electrical circuits. Such damage is not covered under the
product warranty.
2. Connect the drive motor cable to the control box by
lining up the bosses on the male connector with the
notches in the female connector.
3. Push the male connector into the female connector.
With the connector fully inserted, turn the locking
ring a quarter turn to lock the connectors together.

16 L4554_d
AC POWER CORD
FOOT PEDAL
DRIVE MOTOR
PENDANT
USB CABLE
DRIVE MOTOR CABLE
Figure 7: Connections Overview
4. At the drive motor end, connect the drive motor cable
by aligning the bosses with the notches and pushing
the male connector into the female connector. With
the connector fully inserted, turn the locking ring a
quarter turn to lock the connectors together.
5. (OPTIONAL) If the foot pedal is being used, connect
the foot pedal cable by aligning the bosses with the
notches and pushing the male connector into the
female connector.
6. Connect the AC power cord to the controller power
inlet connection and to an electrical power source of
the correct specifications. Refer to Section 6.0 for
AC power requirements.
7. Connect the pendant to the controller using the
provided USB cable.
NOTICE
The USB cable connectors can be inserted only
one way. Before inserting, align protruding tab on USB
connector with matching notch in USB socket. To prevent
damage, do not force USB connector into socket if it
does not fit.
NOTICE
As part of the initial setup process, the pendant
must be connected and paired to the controller using the
USB cable. Refer to detailed instructions in Section 7.5.1.

L4554_d 17
7.4 Powering Up
1. To power-up the controller: Press the ON ( I) half of
the power switch located on the top of the controller.
The controller power indicator will illuminate with a
white light, indicating that the unit is on.
2. To power-up the pendant: Press and hold the power
button on the side of the pendant housing until the
pendant emits two audible beeps. Then, release
the button. The pendant screen will illuminate
approximately 3 seconds after the power button is
pressed.
NOTICE
If the pendant screen will not illuminate, or if the
pendant low battery alert appears, charge the pendant
batteries. Refer to Sections 11.1 and 11.2 for instructions.
7.5 Pendant Setup
After the initial power-up of a new DTT unit, the pendant
must be connected to the controller via the supplied
USB cable. Then, the pendant must be paired with the
controller as described in Section 7.5.1.
This wired pairing process must be performed for complete
new DTT systems or whenever a new (replacement)
pendant or controller is being used.
7.5.1 Pendant Pairing
NOTICE
If this is the first time the pendant and controller
have been paired, the pendant must be paired with the
pendant USB cable connected, as described in the
following steps.
1. Using the provided USB cable, connect the pendant
to the controller USB port.
NOTICE
The USB cable connectors can be inserted only
one way. Before inserting, align protruding tab on USB
connector with matching notch in USB socket. To prevent
damage, do not force USB connector into socket if it
does not fit.
2. Upon pendant power-up, a screen will display
indicating that the pendant is searching for a
controller to pair to.
3. A confirmation screen indicating the controller has
been found will appear.
4. Press PAIR to confirm the pairing.
5. The boot-up screen will appear with the current
software revision displayed.
PAIRING PENDANT
Searching for controller
PAIR
Controller Found
PAIRING PENDANT
7.5.2 Pendant Lost Signal Alarm
If the pendant USB cable is disconnected while pendant
power is on, the pendant will emit a “lost signal” alarm,
alerting the user that communication to the pendant has
been lost.
When the alarm sounds, both controller power and
pendant power must be cycled off and on to reset the
alarm and restore normal operation.
Before power is cycled, be sure that pendant is connected
to the controller via the USB cable. Cycle the controller
power first. Then, cycle the pendant power.
After pendant power has been cycled, re-pair the pendant
with the controller as described in Section 7.5.1.

18 L4554_d
8.0 TURNING TOOL
INSTALLATION
Always follow the steps in this section in sequential order
when installing the tool.
8.1 Mount the Engine Adaptor
Mount the engine interface adaptor on the respective
drive pad of the engine gearbox.
Captive screws are included with each adaptor for
mounting. However, mounting methods will vary and
may include hex bolts, studs, captive screws, or clamps
(user-supplied). Ensure the proper mounting fasteners are
being used for the engine being inspected.
8.2 Attach Drive Motor to Engine
Adaptor
1. Ensure the controller is powered on, the pendant is
paired, and the drive motor is properly connected to
the controller. The square alignment screen will be
visible after pairing is completed.
EXIT
Use CW arrow and CCW arrow
to align the ears of the motor to
the adapter. Use the UP and
DOWN arrows to adjust the
speed
SPEED = 360 deg./min.
SQUARE ALIGNMENT
2. To install the drive motor on the engine interface
adaptor, first line up the square drive and the flange
bolt pattern.
3. Use the CCW or CW buttons on the pendant to
change the direction of the motor so the drive motor
flange bolts line up with the engine interface adaptor.
4. After the ears of the motor are aligned to the adaptor,
secure the drive motor to the adaptor.
5. Torque by hand or wrench to set.
6. After securing the drive motor, press EXIT.
8.3 Calibrate Backlash
NOTICE
Backlash calibration is recommended before
starting any borescope inspection in order to remove all
clearance in the gear train between the DTT drive motor
and the engine requiring inspection. This ensures that
when the motor rotates, the engine blades are in sync
with motor input.
8.3.1 If Rotating Clockwise
1. Press and hold the CW key until the engine rotates.
Then immediately release the CW key.
2. Press SET to designate the Blade 1 location.
3. Backlash is now calibrated. You are ready to begin
your engine inspection.
8.3.2 If Rotating Counter Clockwise
1. Press and hold the CCW key until the engine rotates
and release the CCW key.
2. Press SET to designate the Blade 1 location.
3. Backlash is now calibrated. You are ready to begin
your engine inspection.
SETMENU
Push CW arrow for 5 sec. to drive
motor until it rotates smoothly
then release. Then push SET for
blade 1
TORQUE= 50 ft./lbs.
ELIMINATE BACKLASH
9.0 PENDANT SCREENS
OVERVIEW
9.1 Splash Screen
Upon successful calibration of backlash, a splash screen
will display the Enerpac logo as well as the current
firmware version of the tool.
Digital Turning Tool
Version XX.YY.ZZ
• XX is the pendant version
• YY is the controller version
• ZZ is the engine library version
When applying firmware updates provided by Enerpac,
this numerical sequence will update to correspond with
the numerical sequence of the applied firmware update.

L4554_d 19
9.2 Main Menu
The main menu contains user adjustable settings which
allow the user to tailor the DTT to specific engine rotation
requirements and user inspection preferences.
ENGINE: < JT8D-200(H) >
ROTATE: < CW >
STAGE: < HPC7 >
MODE: < AUTO >
SPEED: < 180 DEG/MIN >
DELAY: < 0 >
MAIN MENU
START
BLADE 1: < NOT SET >
REVIEW FLAGS :
STOP MODE: < ON >
TORQUE LIMIT: < 150 FT/LBS >
ACCELERATION: < 0.2 SEC >
TOGGLE DIRECTION: < STD >
RESET BLADE 1 :
SOUND: < OFF >
SCREEN BRIGHTNESS: < >
BLUETOOTH: < ON >
9.2.1 Engine
Select to scroll through all engines that are in memory.
9.2.2 Rotate
Select to change the direction of rotation,CW (clockwise)
or CCW (counter-clockwise).
9.2.3 Stage
Select to change the selected engine stage.
9.2.4 Mode
Select to change between MANUAL or AUTO mode:
• MANUAL mode enables engine turning by pressing
and holding the CW or CCW button, or depressing
the foot pedal.
• AUTO mode cycles the blade automatically,
stopping at each blade for the time specified in the
DELAY menu.
9.2.5 Speed
Select to determine the number of degrees per minute
the engine will rotate, adjustable from 20 to 360 degrees
per minute.
9.2.6 Delay
Select to change the length of time of the pause at each
blade when in AUTO mode.
9.2.7 Set Blade
To set the blade one position, select this option. Blade1
must be set in order to track blade numbers on the
pendant screen. If Blade 1 is not set, “?” will appear
instead of a number.
9.3 Review Flags
After inspection, use this option to review all flagged
blades (up to 999 blades can be flagged per engine).
To select review flags, press the flag button.
If you want to rotate to a flagged blade, press the GOTO
button and the engine will automatically rotate to that
blade.
Continue until all blades that you want to review have
been reviewed. Press EXIT to return to the main inspection
menu.
NOTICE
If the user selects the review flags option and
presses the start button, the inspection screen will appear
(not the review flags screen).
9.3.1 Stop Mode
Select to turn stop mode on or off. This is a YES or NO
selection. When in stop mode, rotation stops at Blade 1
after 360 degrees of rotation have been achieved. Stop
Mode is on by default.
9.3.2 Torque Limit
Select to determine the torque level at which the engine
will be rotated. If this limit is exceeded, the drive motor
will slip and a SLIP ERROR message will appear.
INCREASEBACK DECREASE
A slip error has occurred. Increase
torque and acceleration time to fix this
error. Use UP arrow
to increase torque
and INCREASE to increase
acceleration.
TORQUE LIMIT: “30-150”
ACCELERATION: “.2-5 SEC.”
SLIP ERROR
9.3.3 Acceleration
Select to set the acceleration/deceleration at which the
motor will perform before it reaches next blade.
9.3.4 Toggle Direction
Select to change the direction of the engine between
NORMAL and REVERSE. When in REVERSE mode, the
drive motor will rotate CCW even though the pendant
will still display CW. On engines with space constraints
where mounting to the front of the gearbox is required,
this allows the engine to be turned CW and for the display
to say CW.

20 L4554_d
9.3.5 Reset Blade 1
Press to reset the Blade 1 position. To set blade one from
the main menu, highlight “Blade 1” and then press the
flag button.
9.3.6 Sound
Select to mute or unmute pendant sounds. When sound is
on, the icon appears at the upper right of the pendant
screen. When sound is muted, the icon appears.
Note that the pendant “lost signal” alarm will be activated
if the USB cable is disconnected, even when the sound
is muted.
9.3.7 Screen Brightness
Select to adjust the screen brightness.
10.0 BEGINNING THE
INSPECTION
After all options have been set to the appropriate values
in the main menu screen, it is time to begin the inspection
Use the left most function key to press START.
ENGINE: < JT8D-200(H) >
ROTATE: < CW >
STAGE: < HPC7 >
MODE: < AUTO >
SPEED: < 180 DEG/MIN >
DELAY: < 0 >
MAIN MENU
START
BLADE 1: < NOT SET >
REVIEW FLAGS :
STOP MODE: < ON >
TORQUE LIMIT: < 150 FT/LBS >
ACCELERATION: < 0.2 SEC >
TOGGLE DIRECTION: < STD >
RESET BLADE 1 :
SOUND: < OFF >
SCREEN BRIGHTNESS: < >
BLUETOOTH: < ON >
Upon pressing START, you will be taken to the main
inspection screen.
START MENU
INSPECTION
FLAGS CW
JT8D-200(H)
HPC7
AUTO
DIRECTION:
MODE:
5 FLAG
• If in manual mode, press and hold the CW or CCW
button to start rotating the engine. Release the
button to make the engine come to a controlled stop.
• If in AUTO mode, the controller will cycle the blade
automatically, stopping at each blade for the time
specified in the DELAY menu.
• At any time, press the FLAG button to flag a blade.
This allows you to return to potentially damaged
blades for further review after the inspection is
complete. Upon flagging a blade, the blade number
flagged will appear on screen; this list will build with
each blade number flagged.
START MENU
INSPECTION
FLAGS
DRIVING
CW
JT8D-200(H)
HPC7
AUTO
DIRECTION:
MODE:
5 FLAG
5
• If for any reason you need to change any of the
preset values, press STOP and then EXIT to return to
the main menu. After any changes are made, press
START and START again to continue the inspection
where you left off.
• After the inspection is complete, you can review
flagged blades.
START MENU
FLAG REVIEW
GOTO CW
JT8D-200(H)
HPC7
AUTO
DIRECTION:
MODE:
1
INSPECTION
This manual suits for next models
2
Table of contents
Other Enerpac Tools manuals
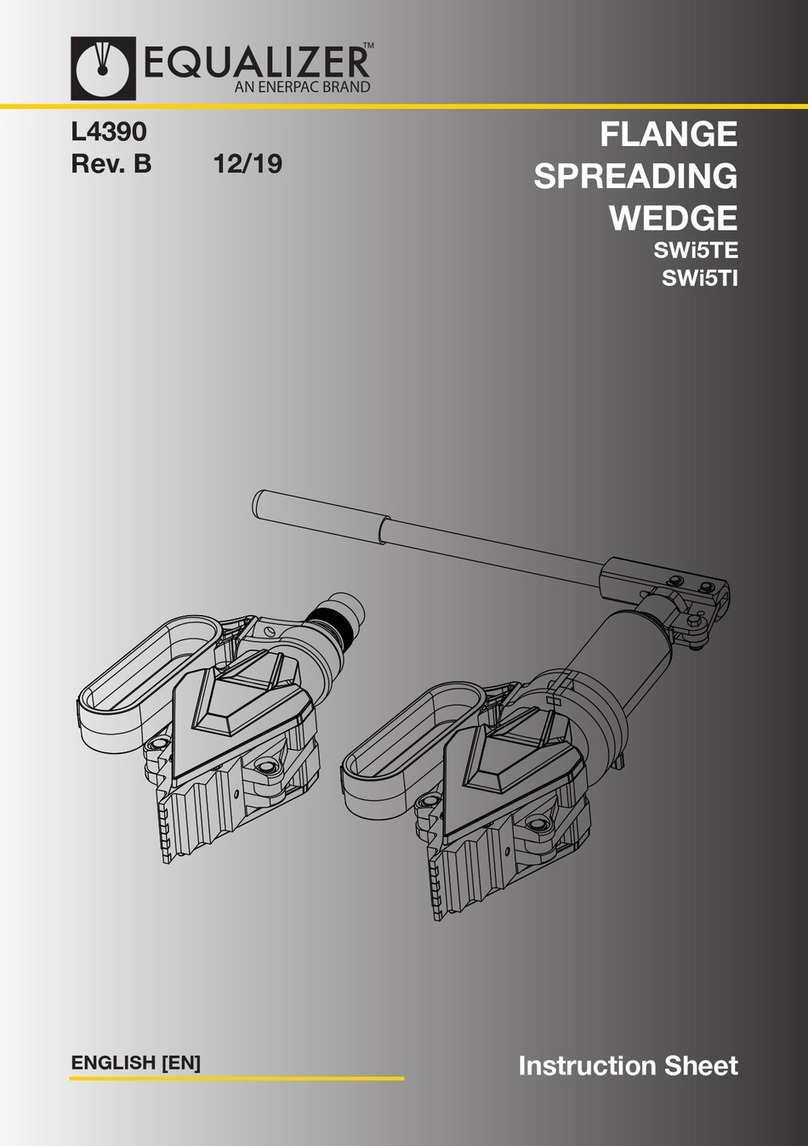
Enerpac
Enerpac EQUALIZER SWi5TE User manual
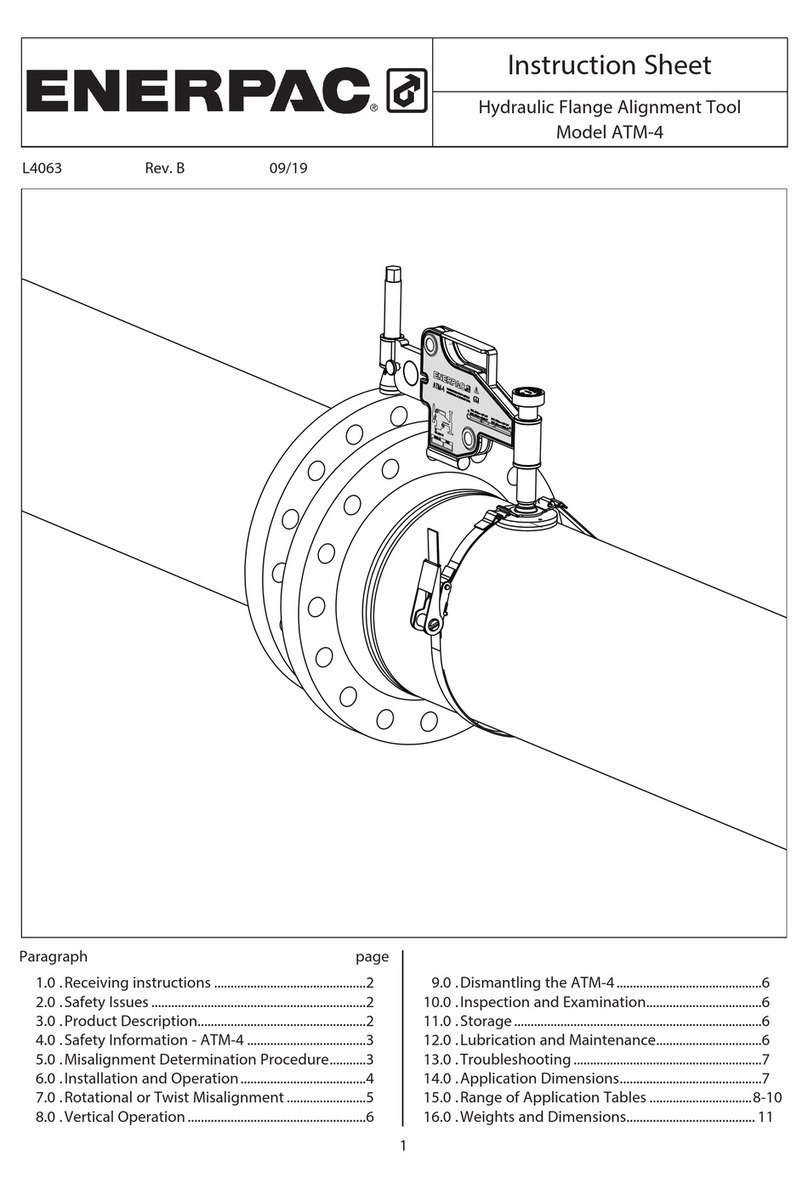
Enerpac
Enerpac ATM-4 User manual
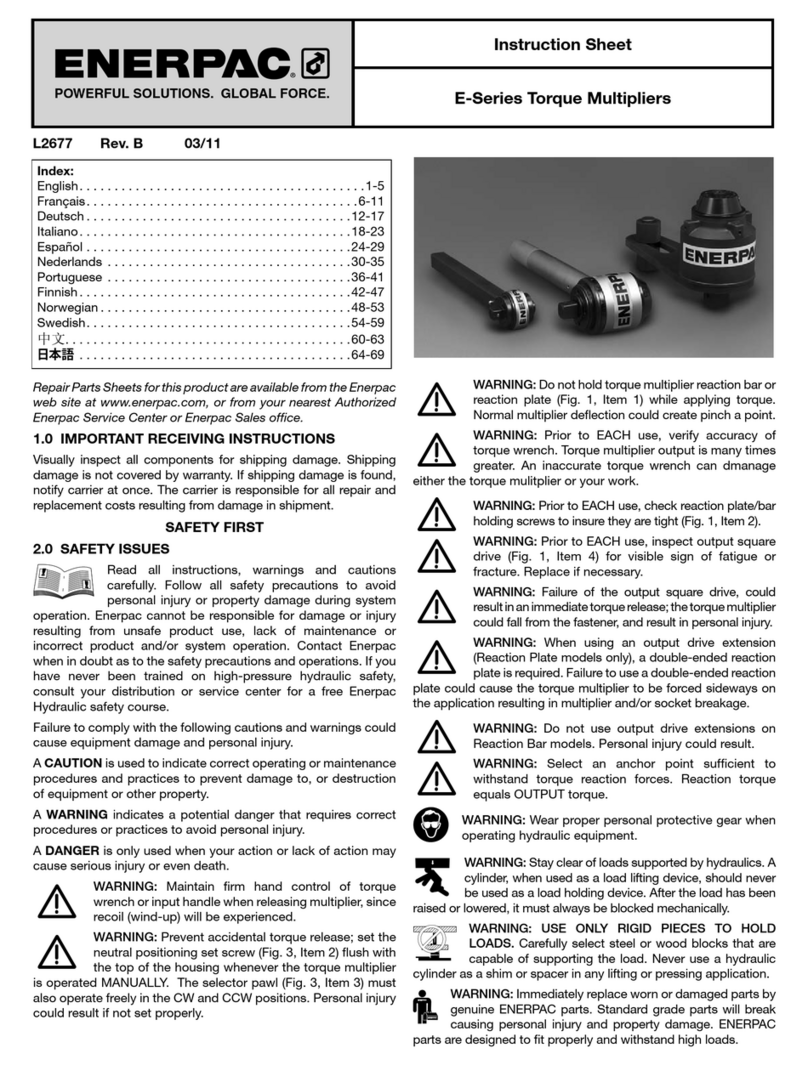
Enerpac
Enerpac E Series User manual
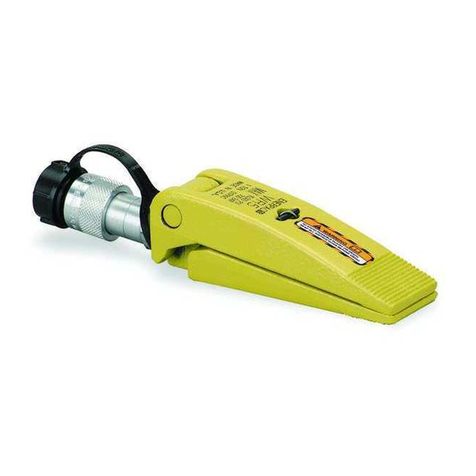
Enerpac
Enerpac WR-5 User manual
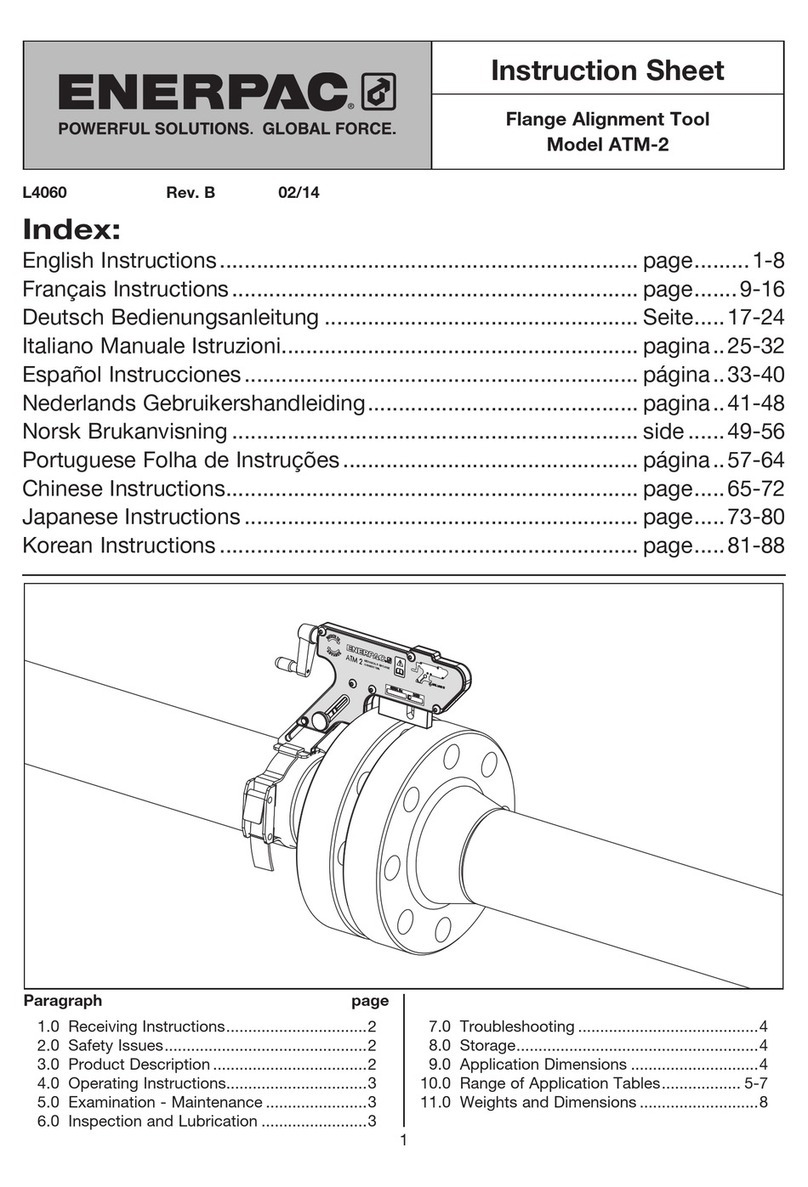
Enerpac
Enerpac ATM-2 User manual
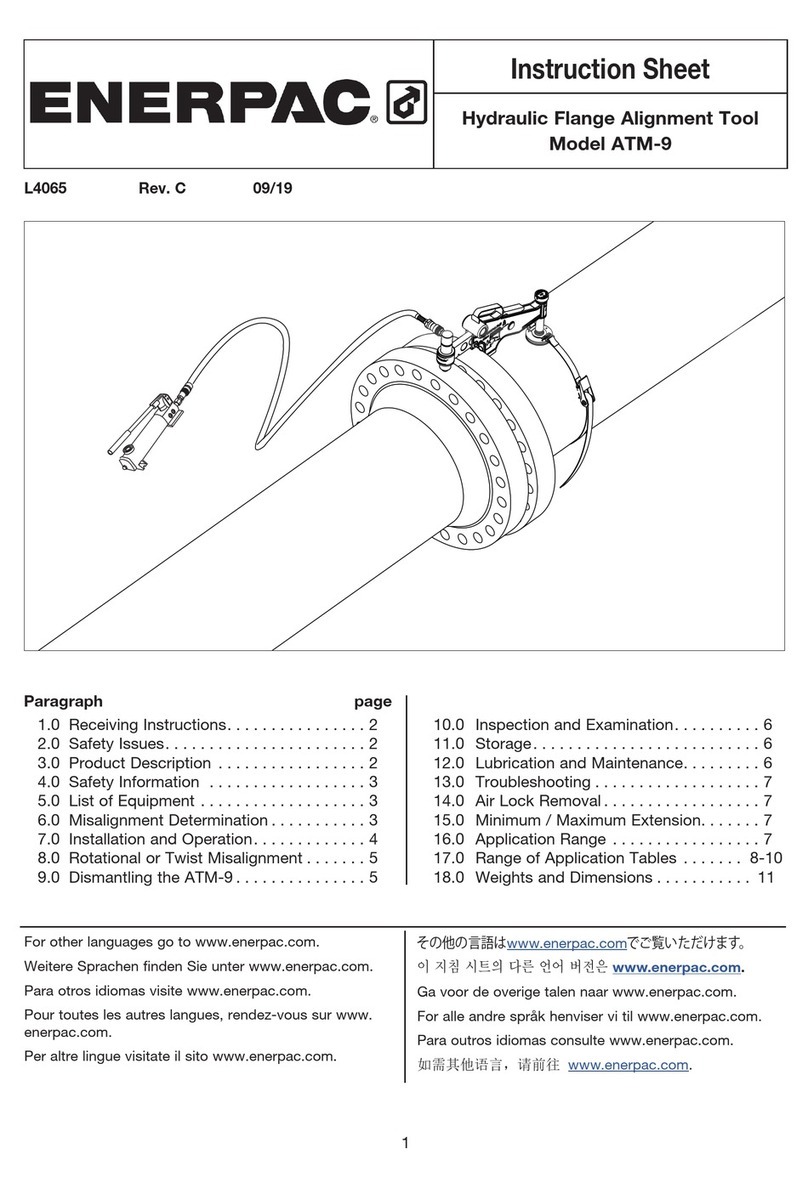
Enerpac
Enerpac ATM-9 User manual

Enerpac
Enerpac HPH14 User manual

Enerpac
Enerpac SWE189DTTA User manual
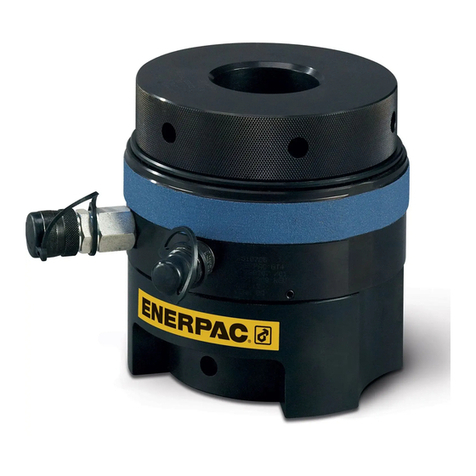
Enerpac
Enerpac GT Series User manual
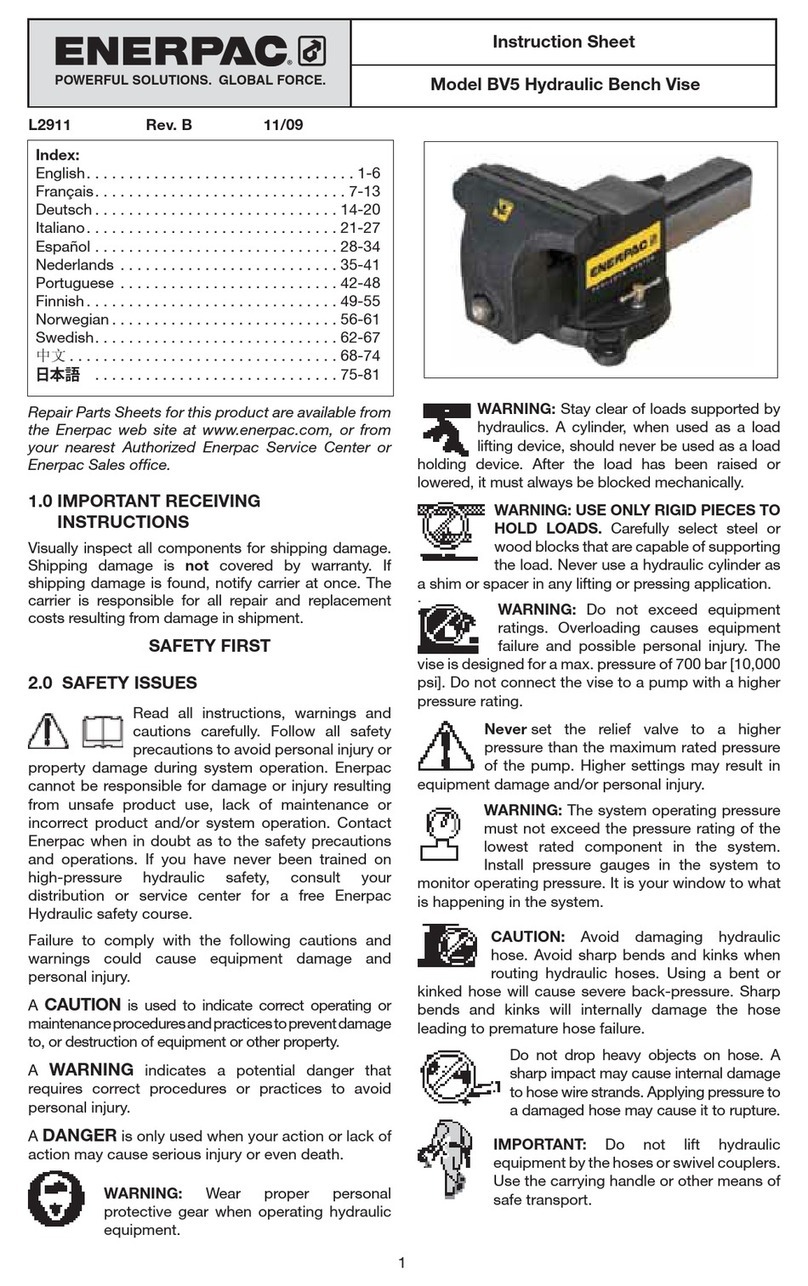
Enerpac
Enerpac BV5 User manual