GAGEMAKER RG-7000 User manual

R
RG
G-
-7
70
00
00
0
T
Th
hr
re
ea
ad
d
D
Di
ia
am
me
et
te
er
r
M
Me
ea
as
su
ur
re
em
me
en
nt
t
G
Ga
ag
ge
e
OPERATION MANUAL

R
RG
G-
-7
70
00
00
0
T
Th
hr
re
ea
ad
d
D
Di
ia
am
me
et
te
er
r
G
Ga
ag
ge
e
O
Op
pe
er
ra
at
ti
io
on
n
M
Ma
an
nu
ua
al
l
2
©2009 Gagemaker, LP
OMRG700010-00

R
RG
G-
-7
70
00
00
0
T
Th
hr
re
ea
ad
d
D
Di
ia
am
me
et
te
er
r
G
Ga
ag
ge
e
O
Op
pe
er
ra
at
ti
io
on
n
M
Ma
an
nu
ua
al
l
3
Contents
Introduction
Technical Support 7
Product Information and Updates 7
System Components
Component List 8
Setup Procedures
Setting Up the RG-7000 Gage 9
Zeroing the RG-7000 Gage Using Gage Blocks 11
Zeroing the RG-7000 Gage Using the MIC TRAC 15
Operating Procedures
Inspecting Parts 21
Care and Maintenance
Maintenance Tips 24
Warranty Information 24

R
RG
G-
-7
70
00
00
0
T
Th
hr
re
ea
ad
d
D
Di
ia
am
me
et
te
er
r
G
Ga
ag
ge
e
O
Op
pe
er
ra
at
ti
io
on
n
M
Ma
an
nu
ua
al
l
4

R
RG
G-
-7
70
00
00
0
T
Th
hr
re
ea
ad
d
D
Di
ia
am
me
et
te
er
r
G
Ga
ag
ge
e
O
Op
pe
er
ra
at
ti
io
on
n
M
Ma
an
nu
ua
al
l
5
Congratulations! Your decision to purchase a Gagemaker product above all others on the market
demonstrates your confidence in our quality and workmanship.
To ensure the high performance and operation of our product, we urge you to use the included reference
materials. They contain important information for proper installation, setup, and use of the equipment.
Also, we recommend that you follow the care and maintenance tips in this manual to keep the equipment
working in top condition.
If your questions have not been addressed in our reference materials, contact your local
representative or a customer service representative at 713-472-7360.

R
RG
G-
-7
70
00
00
0
T
Th
hr
re
ea
ad
d
D
Di
ia
am
me
et
te
er
r
G
Ga
ag
ge
e
O
Op
pe
er
ra
at
ti
io
on
n
M
Ma
an
nu
ua
al
l
6

R
RG
G-
-7
70
00
00
0
T
Th
hr
re
ea
ad
d
D
Di
ia
am
me
et
te
er
r
G
Ga
ag
ge
e
O
Op
pe
er
ra
at
ti
io
on
n
M
Ma
an
nu
ua
al
l
7
Introduction
The RG-7000 Series of the Thread Diameter Measurement Gages inspects the functional size of
external threads ranging from 1”-24”. The functional size of a thread is the size at which two parts will
screw together. To inspect functional size, the RG-7000 gages detect discrepancies in the cumulative
effects of thread element variations in flank angle, lead (including uniformity of helix) taper, and
roundness.
The RG-7000 gages use thread rolls that are precision ground in matched sets to ANSI specifications
to ensure maximum accuracy. The thread rolls seat in the thread form during inspection and reports
actual measurement readings on the gage’s indicator. Each set of thread rolls is designed to measure a
range of diameters for a specific thread form and pitch. The thread roll design allows them to make
rolling contact with the threaded part, causing minimal wear on thread rolls and eliminating damage to
parts.
Before inspecting parts, the RG-7000 gages must be preset to a nominal predetermined dimension. For
determining the gage’s setting dimensions, gauging tolerances, and specific type of thread roll for the
application, the Thread Disk for Windows program is available as an option. The RG-7000 gages can
be preset using gage blocks or the MIC TRAC MT-3000 measurement center.
To inspect parts, the thread rolls are placed in the threads of the part and the gage is properly
positioned by sweeping to obtain the largest indicator reading. Taking measurements in several
different locations along the entire length of the thread will detect any variations in functional size. It is
also recommended that the gage be zeroed periodically during use to maintain accurate readings.
Technical Support
Phone: 713-472-7360
Hours: Monday – Friday 8AM – 5PM (CST)
Product Information and Updates
Visit our web site at: www.gagemaker.com

R
RG
G-
-7
70
00
00
0
T
Th
hr
re
ea
ad
d
D
Di
ia
am
me
et
te
er
r
G
Ga
ag
ge
e
O
Op
pe
er
ra
at
ti
io
on
n
M
Ma
an
nu
ua
al
l
8
System Components
Take some time to become familiar with all the parts that make up the RG-7000 gage by
reviewing the labeled diagram below. The part names are important for understanding the
operating instructions.
1
2
3
4
5
6
7
8
9
10
11
12
13
14
15
16
17
18
19
10
11
13
Component List
Item
Description
Qty
Item
Description
Qty
1
#¼-20 X 5/16” X 3/8” Lower adjuster arm lock bolt 2 11 #10 washer 2
2
Lower adjuster arm clamp plate 1 12 Upper thread roll 1
3
Lower adjuster arm 13 Thread roll pin 2
4
Gage frame assembly 1 14 Gage lever 1
5
Nameplate 1 15 Lower thread roll 1
6
Retraction lever 1 16 Indicator protector 1
7
Indicator clamp 1 17 # 4-40 X ½” cap screw 2
8
Indicator 1 18 1/8” hex wrench 1
9
Indicator bushing 1 19 5/32” hex wrench 1
10
#10-32 X ¼” button head lock screw 2

R
RG
G-
-7
70
00
00
0
T
Th
hr
re
ea
ad
d
D
Di
ia
am
me
et
te
er
r
G
Ga
ag
ge
e
O
Op
pe
er
ra
at
ti
io
on
n
M
Ma
an
nu
ua
al
l
9
Setup Procedures
The accuracy and repeatability of your RG-7000 gage depends on the correct attachment and
set up of the components. Each of the procedures on the following pages will help you to set
up your RG-7000 gage properly.
Setting Up the RG-7000 Gage
Materials Needed:
•
RG-7000 gage
•1/8” hex wrench (supplied with gage)
•Thread rolls (proper pitch) •Cloth
•Thread Disk for Windows software
Setting up the RG-7000 gage, involves determining the thread roll type for your application and installing
them on the gage. Entering some minimal thread information into the Thread Disk for Windows program
will provide you with the proper type thread rolls, gage setting dimensions, and the gauging tolerances
for your application.
1. Start the Thread Disk for Windows program.
2. Select the Thread Type and Thread Class.
3. Type the Nominal Diameter and Threads per
Inch.
4. Select the Number of Thread Starts.
5. Click the Calculate button.
6. Click the Gagemaker tab.
7. Based on the Roll # displayed on the
Gagemaker screen, select the proper thread
roll.
8. Print the Gagemaker screen for future
reference in determining gage settings and
product tolerances.

R
RG
G-
-7
70
00
00
0
T
Th
hr
re
ea
ad
d
D
Di
ia
am
me
et
te
er
r
G
Ga
ag
ge
e
O
Op
pe
er
ra
at
ti
io
on
n
M
Ma
an
nu
ua
al
l
10
Setting Up the RG-7000 Gage (continued)
9. Using the 1/8” hex wrench, remove the lock
screw and washer from each roll pin.
10. Clean the thread rolls and the roll pins
on the gage to ensure they are free
from debris.
11. Slide a thread roll on each of the gage’s roll
pins. The face of the thread roll that is marked
with lines and the thread roll type should face
outward.
Note: Be sure there is no dirt between the thread
roll and the roll pin, to enable the thread
rolls to spin freely.

R
RG
G-
-7
70
00
00
0
T
Th
hr
re
ea
ad
d
D
Di
ia
am
me
et
te
er
r
G
Ga
ag
ge
e
O
Op
pe
er
ra
at
ti
io
on
n
M
Ma
an
nu
ua
al
l
11
Setting Up the RG-7000 Gage (continued)
12. Place the washer and lock screw on each roll
pin.
13. Using the 1/8” hex wrench, tighten the lock
screw. Eliminate any side to side movement of
the thread roll, but make sure that the thread
roll still rotates.
DO NOT over tighten the lock screw. This
will prevent the gage from operating
properly.

R
RG
G-
-7
70
00
00
0
T
Th
hr
re
ea
ad
d
D
Di
ia
am
me
et
te
er
r
G
Ga
ag
ge
e
O
Op
pe
er
ra
at
ti
io
on
n
M
Ma
an
nu
ua
al
l
12
Zeroing the RG-7000 Gage Using Gage Blocks
Materials Needed:
•RG-7000 gage •5/32” hex wrench (supplied with gage)
•Gage block(s)
To ensure consistent and accurate readings, the RG-7000 gage should be zeroed on a gage
block once during each shift, at a minimum.
1. Locate the gage setting dimensions previously
printed from the Gagemaker screen in the
Thread Disk for Windows software.
2. Stack the proper size gage block(s) for the
desired setting dimension.
3. Using the 5/32” hex wrench, loosen the lower
adjuster arm lock bolts. Slide the adjuster arm
open enough to fit over the gage block(s).
4. Place the gage block(s) between the thread
rolls and slide the adjuster arm until the thread
rolls contact the gage block(s).
5. Remove the gage block(s).
Slide Arm Open

R
RG
G-
-7
70
00
00
0
T
Th
hr
re
ea
ad
d
D
Di
ia
am
me
et
te
er
r
G
Ga
ag
ge
e
O
Op
pe
er
ra
at
ti
io
on
n
M
Ma
an
nu
ua
al
l
13
Zeroing the RG-7000 Gage Using Gage Blocks (continued)
6. Slide the adjuster arm approximately .050”
closer to the upper thread roll to give the gage
the proper preload.
7. Using the 5/32” hex wrench, tighten the
adjuster arm lock bolts to lock the arm in place.
8. Press the retraction lever on the RG-7000 and
insert the gage block(s) between the thread
rolls.

R
RG
G-
-7
70
00
00
0
T
Th
hr
re
ea
ad
d
D
Di
ia
am
me
et
te
er
r
G
Ga
ag
ge
e
O
Op
pe
er
ra
at
ti
io
on
n
M
Ma
an
nu
ua
al
l
14
Zeroing the RG-7000 Gage Using Gage Blocks (continued)
9. Turn the indicator dial on the RG-7000 to align
the needle with zero.
10. Tighten the indicator clamp.
11. Press the retraction lever and remove the RG-
7000 from the gage block(s). Reposition the
gage between the gage block(s) to verify the
zero setting.
Note: Note the position of the small revolution
counter on the indicator before removing
the gage. Place a piece of masking tape on
the backside of the indicator and record the
dial setting of the small revolution counter
to eliminate incorrect indicator readings.
12. Press the retraction lever and remove the RG-
7000 from the gage block(s).
13. Set a frequency for verifying the zero setting of
all gages. As a minimum, the RG-7000 gage
should be zeroed on a gage block once during
each shift to ensure accurate readings.

R
RG
G-
-7
70
00
00
0
T
Th
hr
re
ea
ad
d
D
Di
ia
am
me
et
te
er
r
G
Ga
ag
ge
e
O
Op
pe
er
ra
at
ti
io
on
n
M
Ma
an
nu
ua
al
l
15
Zeroing the RG-7000 Gage Using the MIC TRAC
Materials Needed:
•RG-7000 gage •MIC TRAC MT-3000, CPU, and flat face anvils
•5/32” hex wrench (supplied with gage)
•Setting dimensions (Thread Disk for Windows software)
To ensure consistent and accurate readings, the RG-7000 gage should be zeroed on the MT-
3000 once during each shift, at a minimum.
1. Turn the coarse adjust knob counterclockwise
to bring the flat face anvils together.
2. If necessary for documentation purposes,
press the PRINT pad on the CPU to record
the starting location of the anvils.
3. Press the EXT pad on the CPU to change to
external measurement mode.
4. Locate the gage setting dimensions previously
printed from the Gagemaker screen in the
Thread Disk for Windows software.
5. Turn the coarse adjust knob on the MT-3000
to display a measurement that is close to the
desired setting dimension.
6. Secure the coarse adjust lock.
7. Turn the fine adjust knob until the CPU
displays the exact setting dimension.
8. Secure the fine adjust lock.
9. If necessary for documentation purposes,
press the PRINT pad on the CPU to record
the actual setting dimension.

R
RG
G-
-7
70
00
00
0
T
Th
hr
re
ea
ad
d
D
Di
ia
am
me
et
te
er
r
G
Ga
ag
ge
e
O
Op
pe
er
ra
at
ti
io
on
n
M
Ma
an
nu
ua
al
l
16
Zeroing the RG-7000 Gage Using the MIC TRAC (continued)
10. Using the 5/32” hex wrench, loosen the lower
adjuster arm lock bolts. Slide the adjuster arm
open enough to fit over the MT-3000 flat face
anvils.
11. Position the gage over the flat face anvils and
slide the adjuster arm until the thread rolls
contact the flat face anvils.
12. Remove the RG-7000 gage from the MT-3000.
13. Slide the adjuster arm approximately .050”
closer to the upper thread roll to give the gage
the proper preload.
Slide Arm Open

R
RG
G-
-7
70
00
00
0
T
Th
hr
re
ea
ad
d
D
Di
ia
am
me
et
te
er
r
G
Ga
ag
ge
e
O
Op
pe
er
ra
at
ti
io
on
n
M
Ma
an
nu
ua
al
l
17
Zeroing the RG-7000 Gage Using the MIC TRAC (continued)
14. Using the 5/32” hex wrench, tighten the
adjuster arm lock bolts to lock the arm in place.
15. Press the retraction lever on the RG-7000 gage
and place the thread rolls over the flat face
anvils on the MT-3000.
16. Release the retraction lever and allow the
thread rolls to contact the flat face anvils. Be
sure that only the thread rolls contact the flat
face anvils and that the lower adjuster arm is
clear of all surfaces.

R
RG
G-
-7
70
00
00
0
T
Th
hr
re
ea
ad
d
D
Di
ia
am
me
et
te
er
r
G
Ga
ag
ge
e
O
Op
pe
er
ra
at
ti
io
on
n
M
Ma
an
nu
ua
al
l
18
Zeroing the RG-7000 Gage Using the MIC TRAC (continued)
17. While maintaining pressure between the lower
thread roll and flat face anvil, sweep the upper
thread roll up and down to locate the smallest
indicator reading.
18. Turn the indicator dial on the RG-7000 to align
the needle with zero.
19. Tighten the indicator clamp.
20. Press the retraction lever and remove the RG-
7000 from the MT-3000. Reposition the gage
on the flat face anvils to verify the zero setting.
Note: Note the position of the small revolution
counter on the indicator before removing
the gage. Place a piece of masking tape on
the backside of the indicator and record the
dial setting of the small revolution counter
to eliminate incorrect indicator readings.

R
RG
G-
-7
70
00
00
0
T
Th
hr
re
ea
ad
d
D
Di
ia
am
me
et
te
er
r
G
Ga
ag
ge
e
O
Op
pe
er
ra
at
ti
io
on
n
M
Ma
an
nu
ua
al
l
19
Zeroing the RG-7000 Gage Using the MIC TRAC (continued)
21. Press the retraction lever on the RG-7000 gage
and remove it from the MT-3000.
22. Set a frequency for verifying the zero setting of
all gages. As a minimum, the RG-7000 gage
should be zeroed on the MT-3000 once during
each shift to ensure accurate readings.

R
RG
G-
-7
70
00
00
0
T
Th
hr
re
ea
ad
d
D
Di
ia
am
me
et
te
er
r
G
Ga
ag
ge
e
O
Op
pe
er
ra
at
ti
io
on
n
M
Ma
an
nu
ua
al
l
20
Table of contents
Other GAGEMAKER Measuring Instrument manuals

GAGEMAKER
GAGEMAKER PD-8000-RSC User manual
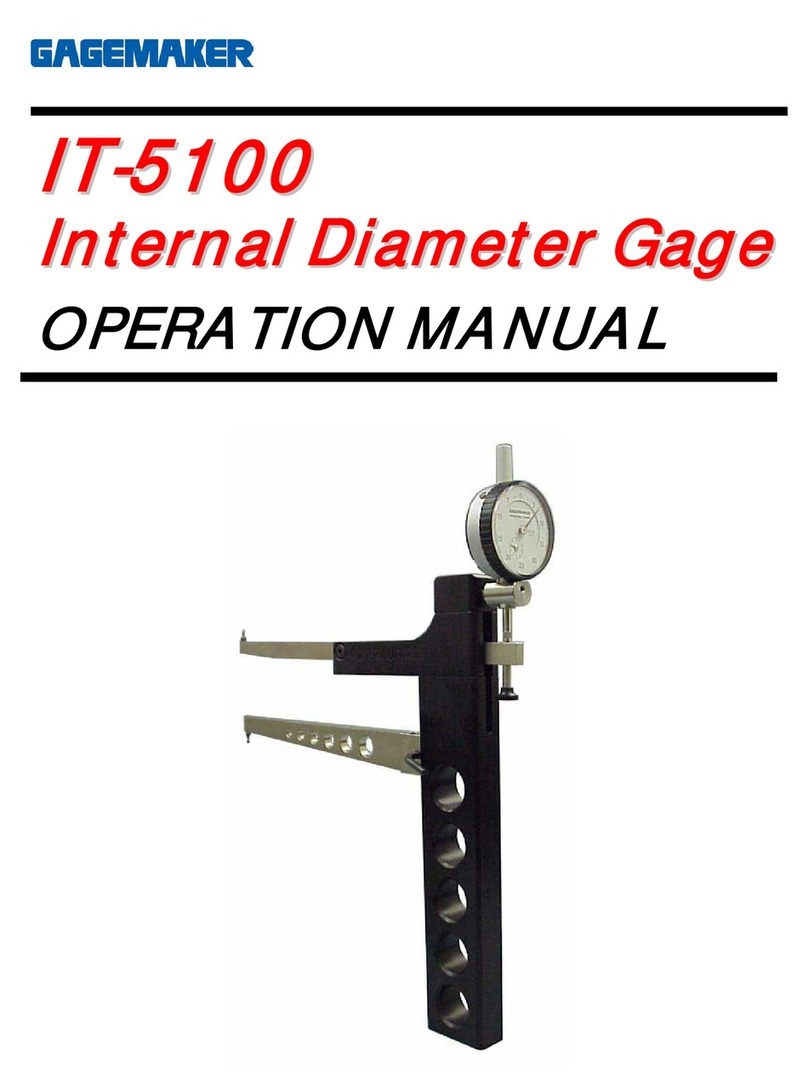
GAGEMAKER
GAGEMAKER IT-5100 User manual
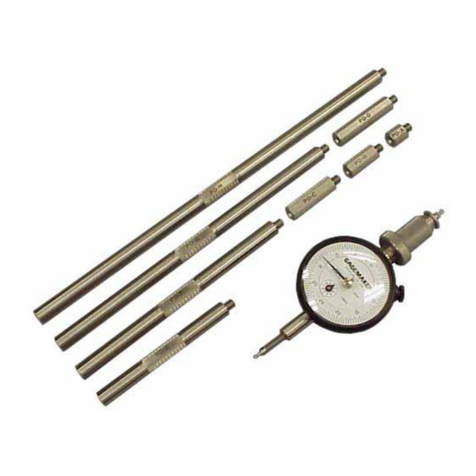
GAGEMAKER
GAGEMAKER PD-6001 User manual
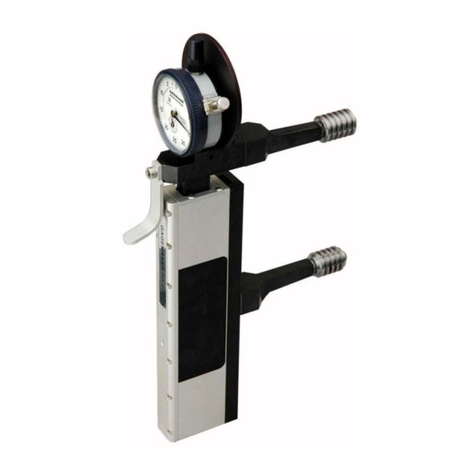
GAGEMAKER
GAGEMAKER PG-6000 User manual
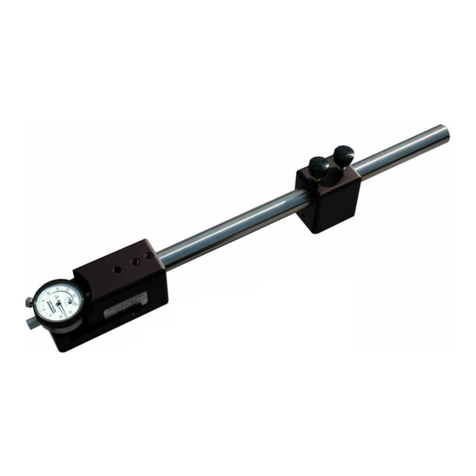
GAGEMAKER
GAGEMAKER BXG-1000 User manual

GAGEMAKER
GAGEMAKER MIC TRAC MT-3000 User manual
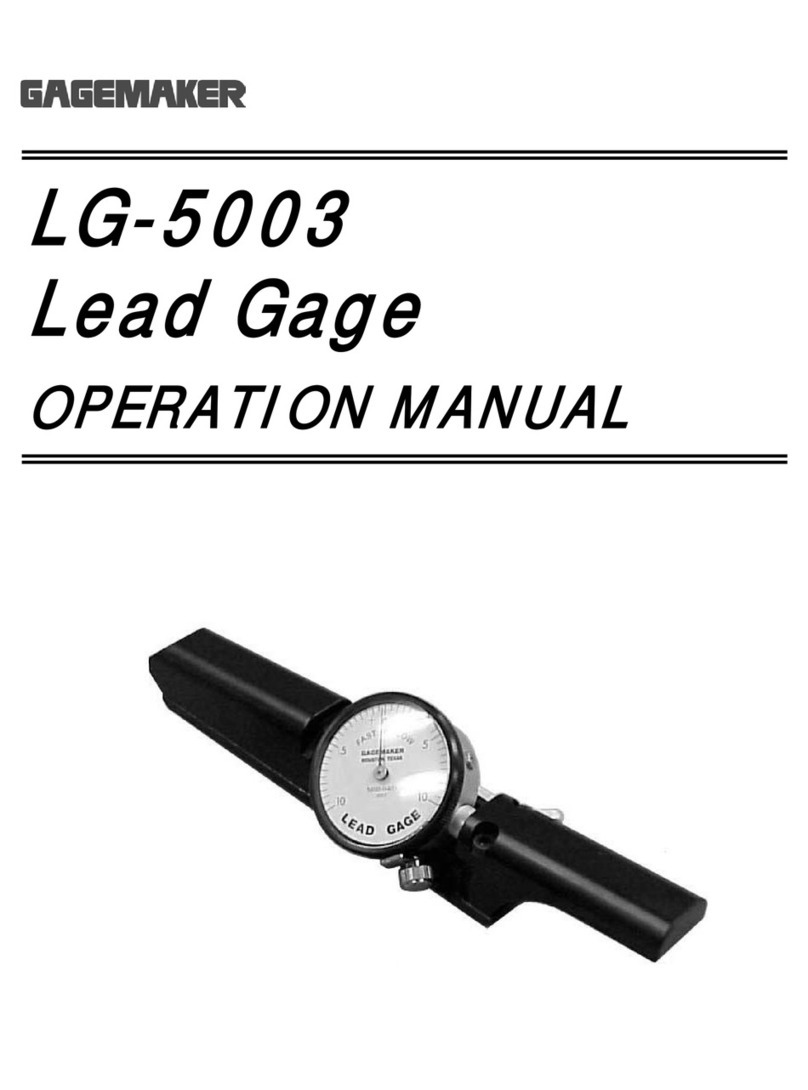
GAGEMAKER
GAGEMAKER LG-5003 User manual
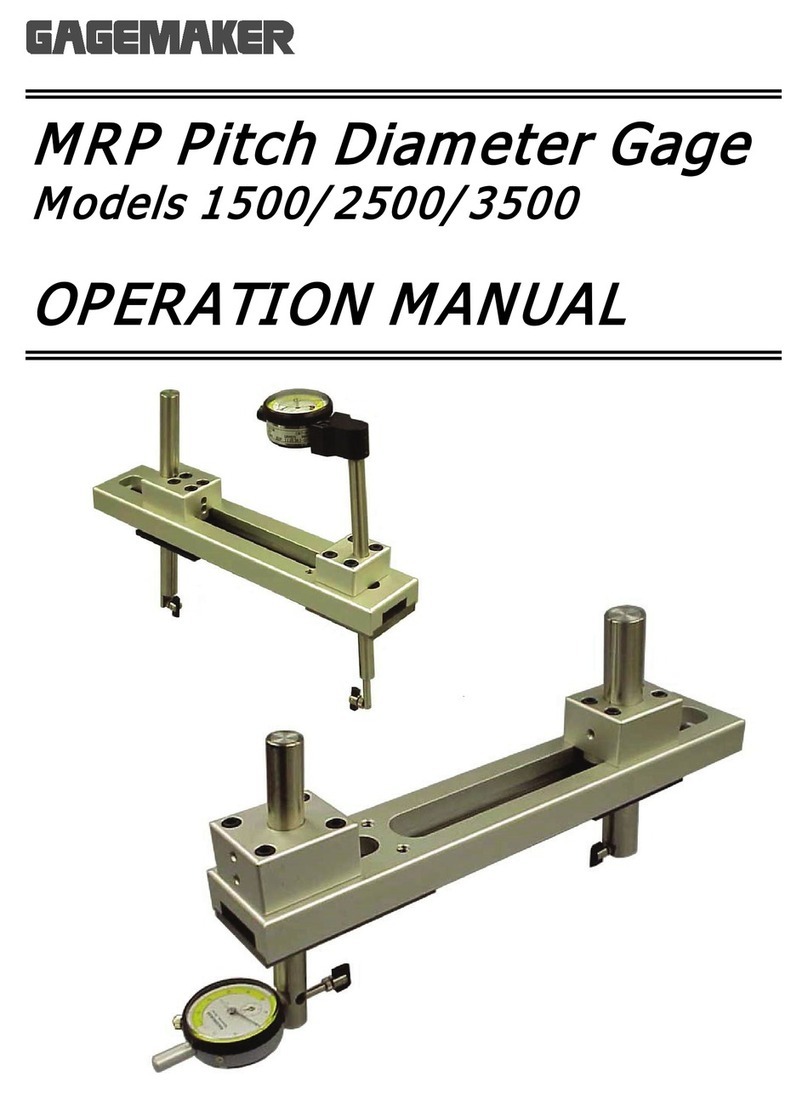
GAGEMAKER
GAGEMAKER MRP-1500 User manual

GAGEMAKER
GAGEMAKER CA-9001 User manual
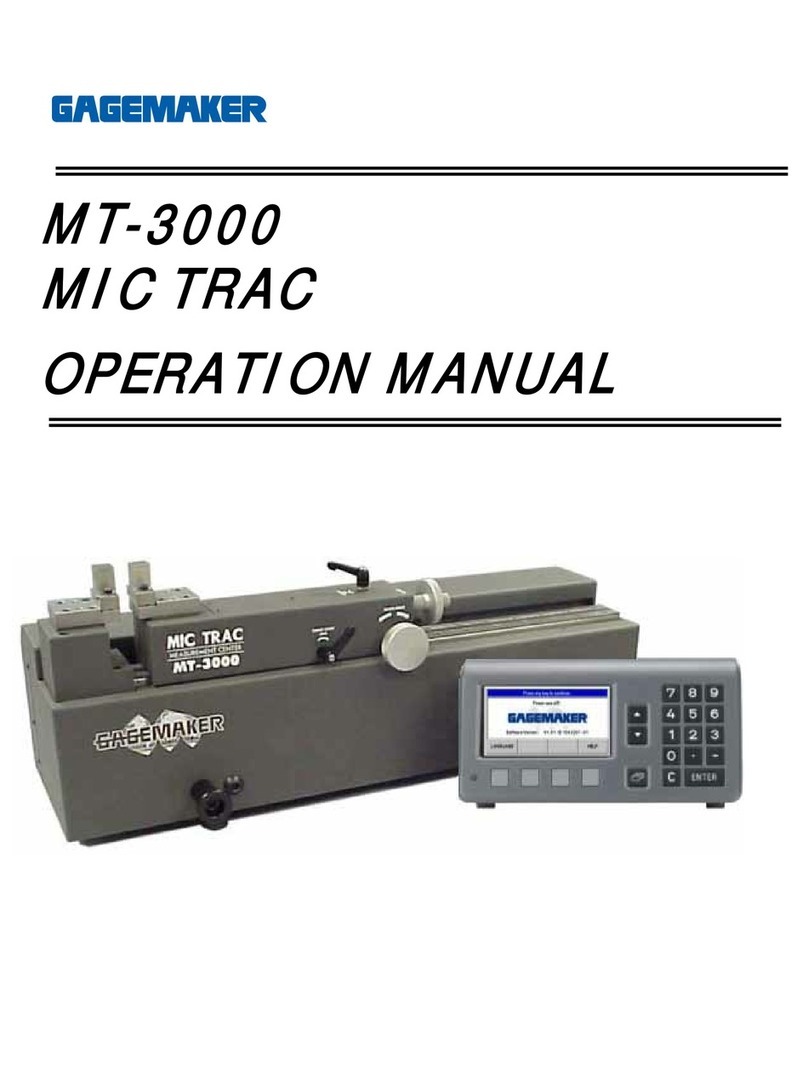
GAGEMAKER
GAGEMAKER MIC TRAC MT-3000 User manual