GE MLJ1000 User manual

GGEEKK--105560105560
GE Power Management
“We bring good things to life”
MLJ
MLJ1000
DIGITAL SYNCHRONISM
CHECK RELAY

GEK - 105560
1
TABLE OF CONTENTS
1. DESCRIPTION ....................................................................................................................4
2. APPLICATION....................................................................................................................5
2.1 DESIGN CHARACTERISTICS ..........................................................................................5
2.2 APPLICATIONS..................................................................................................................7
3. OPERATION PRINCIPLES.............................................................................................11
3.1 CONFIGURATION UNIT.................................................................................................11
3.1.1 GENERAL Settings.......................................................................................................11
3.2 SYNCHRONISM CHECK UNIT......................................................................................11
3.2.1 Mode of Operation.......................................................................................................12
3.2.2 Settings.........................................................................................................................13
3.2.3 Failure of Closure Conditions .....................................................................................13
3.3 UNDERVOLTAGE UNIT.................................................................................................14
3.3.1 Mode of Operation.......................................................................................................14
3.3.2 Settings.........................................................................................................................14
3.4 INPUT UNITS....................................................................................................................15
3.5 SELF-CHECK UNIT..........................................................................................................15
3.5.1 Mode of Operation.......................................................................................................15
3.6 OUTPUT UNITS................................................................................................................16
3.6.1 Mode of Operation.......................................................................................................16
3.6.2 Settings.........................................................................................................................16
3.7 POWER SUPPLY ..............................................................................................................17
4. TECHNICAL CHARACTERISTICS..............................................................................18
4.1 MODEL LIST.....................................................................................................................18
4.2 TECHNICAL CHARACTERISTICS ................................................................................18
4.3 INSULATION ....................................................................................................................19
4.4 TYPE TESTS .....................................................................................................................20
5. DESCRIPTION OF HARDWARE...................................................................................21
5.1 CASE..................................................................................................................................21
5.2 INTERNAL CONNECTIONS ...........................................................................................21
5.3 IDENTIFICATION.............................................................................................................21
5.4 MLJ FRONT DEVICES.....................................................................................................21
6. OPERATION OF MLJ (KEYPAD AND DISPLAY) .....................................................23
6.1 READOUT SEQUENCE...................................................................................................24
6.1.1 F0: State of relay, error codes .....................................................................................25
6.1.2 F1, F2: VL, VB, Voltage in line and buses...................................................................25
6.1.3 F3:
∆
V Voltage difference module................................................................................25

GEK - 105560
2
6.1.4 F4:
∆θ
Phase angle......................................................................................................25
6.1.5 F5:
∆
f Frequency Slip ..................................................................................................25
6.1.6 F6, F7, F8, F9, and F10 Magnitudes recorded ...........................................................26
6.1.7 F11: TEST Display and inputs test ..............................................................................26
6.1.8 F12: VL VB State of Line and buses ............................................................................26
6.2 SEQUENCE OF SETTINGS .............................................................................................26
6.3 CALIBRATION SEQUENCE............................................................................................28
6.4 SUMMARY OF SETTINGS..............................................................................................29
7. ACCEPTANCE TESTS.....................................................................................................31
7.1 INTRODUCTION..............................................................................................................31
7.2 VISUAL INSPECTION......................................................................................................31
7.3 INSULATION ....................................................................................................................31
7.4 SYNCHRONISM UNIT.....................................................................................................31
7.4.1 Voltage unit test............................................................................................................32
7.4.2 Angle unit test...............................................................................................................32
7.5 UNDERVOLTAGE UNIT.................................................................................................32
7.6 CONTINUOUS AND MANUAL MODE TESTS.............................................................33
7.7 CALIBRATION .................................................................................................................33
7.8 GROUNDING....................................................................................................................33

GEK - 105560
3
List of Figures
FIGURE 1 LOGICAL DIAGRAM OF OPERATION (226B2202H2)..............................35
FIGURE 2 NAMEPLATE (226B1276H1).................................................................36
FIGURE 3 OUTLINE AND PANEL DRILLING (226B6086H1)....................................37
FIGURE 4 REAR TERMINAL PLATE (226B3205H1)................................................38
FIGURE 5 EXTERNAL CONNECTIONS (226B6265H1)............................................39
FIGURE 6 INTERNAL SETTINGS (301A7408H1) ....................................................40
FIGURE 7 BLOCK DIAGRAM (226B2201H1).........................................................41
The information provided herein does not intend to cover all details of variations of the
described equipment nor does it take into account the circumstances that may be present in
your installation, operating or maintenance activities.
Should you wish to receive additional information, or for any particular problem which cannot
be solved by referring to the information contained herein, please write to:
GENERAL ELECTRIC (USA) POWER MANAGEMENT, S.A.

GEK - 105560
4
1. DESCRIPTION
The main applications of the MLJ are:
• Connecting a generator to the system.
• Reestablishing the connection between two parts of the system.
• Manual closing of circuit breakers
• Automatic reclosing of a breaker after a relay trip.
The MLJ is a digital synchronism-checking relay that measures bus and line voltages. It tests:
• Voltage difference
• Frequency slip
• The phase angle between both voltages
The equipment provides an output to enable to close the circuit breaker when all of the values fall
within the set limits and remain there for the duration of time chosen for the setting. In the event that all
the conditions have not been met, after one minute the equipment gives off a signal showing a failure
of closing conditions.
The relay functions in two modes:
• Continuous mode: In this mode synchronism is checked continuously.
• Manual mode: This is activated when voltage is applied through a manually activated input, thus
beginning synchronism control when voltage applied through another digital input for initial
checking.
The function of synchronism (with voltage in the line and bus) can be controlled by two undervoltage
units, which allow the synchronism operation when both voltages are higher than the set value.
Additionally, it is equipped with DLDB dead line-dead bus, DLLB dead line-live bus, and LLDB live line-
dead bus, making it possible to select any combination thereof through independent settings.
The basic MLJ1000 equipment and the equipment linkable via RS-485 is mounted in a 2-inch module,
compatible with industrial MID systems, or in a 1/8 rack as an individual relay.
The equipment with communications added to the RS-485, through RS-232 and plastic or glass fiber
optics, models MLJ1006 MLJ1007, come with an additional 2-inch wide card, and is mounted in a 4-
inch module (also compatible with MID systems), or on a 1/4 rack as an individual relay.

GEK - 105560
5
2. APPLICATION
2.1 DESIGN CHARACTERISTICS
Measurement accuracy
The differential angle measurement of the MLJ is high precision and is limited solely by errors in
available voltage transformers .
The measurement of the angle is practically independent of the voltage.
In the MLJ the measurement is obtained via a numerical calculation done on digital voltage samples,
thus achieving high precision. This allows for a rating of 2º, which is clearly better than the possible
rating using other technologies.
Influence of harmonics
The pillar of the MLJ measurement calculation is the discrete Fourier transform, which is in essence a
harmonics filter. For this reason the voltage and line measurements are not affected by frequencies
other than the fundamental.
The rejection of harmonics is added to the independence of measurements, both magnitude and
phase, relative to frequency signal variations, which is very important in a synchronism checking relay
which, by its own nature, works in variable frequencies.
Given that in power systems, synchronization or synchronism checking is carried out in a steady state,
that is with voltage magnitudes near or equal to the rated value, close enable is not emitted for very low
voltages. Therefore, for voltage of less than 9 volts, the relay stops measuring phase and frequency,
not giving permission to close under such conditions.
The MLJ also offers additional insensitivity to frequency measurement concerning harmonics, since
this is done via a hardware circuit, a zero-cross detector, with an intrinsic harmonics filter. Furthermore,
it has a software filter which operates by double-period measurement, both between the rising and
falling edges, averaging them out and allowing for better performance of algorithm frequency
(improving security and response).
Closing time delay
The minimum closing time, set at 100 ms, is actually 160 ms, as it is necessary to add the time
required by the measurement units and the operation of the output relays to the set 100 ms. It should
be kept in mind that during the first cycles, from the time of a closure, the voltage is stabilizing both in
the line as well as in the buses and it is no desirable to allow a closure under these conditions. What is
more, it is necessary to take into consideration the response of both the high voltage transformers and
the internal transformers of the relay.

GEK - 105560
6
There is also a time for sustaining the permission signal, which always has a fixed value of some 130
ms., being the result of a prefixed delay of 100 ms. added to the dropout time of the measurement
units (one cycle = 20 ms. at 50 Hz.) and the deactivation of the output relay (10 ms.).
Minimum settings
Barring any special requirements, it is not recommended to use settings that near the minimum limits
for the relays, (2 V for the voltage difference, 2º for the angle difference), so as to avoid being too
restrictive in close enabling, given the real characteristics of accuracy in the installations, measurement
transformers, etc.
Close enable
Close enable is defined by three conditions in the system:
• The difference in amplitude of the two voltage signals to be synchronized defines a circle shifted
from the axis of abscissa a distance equal to the magnitude of the minimum vector and having a
maximum radius equal to the difference ∆V.
• The angular difference, allowed either in positive or negative, between the two approaching vectors,
forms a cone on which the close enable takes place.
• The frequency slip, ∆f = f1- f2, which has to be less than that specified, configures a third and
basic condition of closure, optimum for carrying out closure procedures in ideal conditions, with
similarity between signals.
∆V
V
1
V
2
θ1θ2
CLOSE ENABLE
∆f =
f1- f2

GEK - 105560
7
2.2 APPLICATIONS
Synchronism
In general, synchronism check is intended primly for application where the two parts of a system to be
joined by the closure of a circuit breaker are interconnected at other points throughout the system.
Usually, performing synchronism check measurements is done with relatively long times in order to
make sure the voltages are synchronized. Nevertheless, this long timer, which can be on the order of
10 to 20 seconds, is not appropriate when both ends of the line are to be reclosed at high speed. If the
measurement time is lower, then the synchronism check can be done faster, although this means that
the reclosing could be done under no-synchronism conditions, with greater frequency slip than for ideal
condition.
It is essential to point out the intrinsic relation that invariably exists between time, frequency slip and
angle of closure, in such a way that, for constant slip, the following expression is carried out:
SDT
=**
1000
180
Where: D= angle of closure in degrees
S= Frequency slip in mHz
T= Total time in seconds
For applications where a preferred value for frequency slip does not exist, it is recommended to use
the maximum. This way the behavior of other synchronism relays which do not have this feature can
be reproduced.
If a preferred value for the voltage difference does not exist, it is recommended to use the maximum
rating; in doing so closure is permitted monitoring only conditions of phase, slip and time.
If the time of the circuit breaker closure is known, the maximum angle difference can be estimated by
applying the above expression; it will be obtained during closure of the circuit breaker.
For example, let us take: a setting of 30º for the angle, a setting of 167 ms for the time,
and that the time of operation of the circuit breaker to be 83 ms.
From the above equation we obtain the value of 1 Hz (360º/s) for frequency slip S. If we
had frequency slip greater than 1 Hz, we would not have close enable.
If we adjust the maximum frequency slip to 330 mHz, then:
330 mHz ≅120º/s ⇒120º/s * 167 ms = 20º
and the movement in the difference of the angle during the circuit breaker closure will be:
83 ms * 120º/s = 10º
20º+10º=30º, which is the fixed phase setting, and therefore the closure occurs at the
optimum moment, when the voltages in the line and bus are completely in phase.

GEK - 105560
8
In a large majority of cases, the typical slip can be set at around 20 to 40 mHz. This is the situation for
short lines.
In lines with short “dead times”, that is, immediate reclosing in the remote end, with very similar
operation in case of internal faults in both circuit breakers and channel transmission times less than 25
ms, the slip setting may be set at 200 to 250 mHz.
In any case, the order and operating times of the different elements involved should be observed;
these are the elements with which the synchronism check relay must be coordinated, and whose
typical magnitudes are shown on the following page.

GEK - 105560
9
t1t2t3t4t5t6t7t8t9t10 t11 t12
t1 = Moment of detection of the fault in protections A and B.
t2 = Tripping order of circuit breakers A and B (it may not happen at the same time).
t3 = Opening of circuit breakers A and B (it may not happen at the same time).
t4 = Spark quenching of the arcs in circuit breakers A and B.
t5 = End of safety waiting period, in order to compensate error clear up discrepancies between circuit
breakers A and B, and order reclosing of circuit breaker B.
t6 = Closure of circuit breaker B and initiation of stabilization of relay signals of synchronism relay A.
t7 = Initiation of the set time in synchronism relay A.
t8 = End of synchronism relay time delay and internal output of synchronization enable.
t9 = Reclose order of circuit breaker A.
t10 = Closure of circuit breaker A.
t11 = Resetting of synchronism relay A.
t12 = End of output enable of synchronism relay A.
∆1 = Opening time of circuit breakers = 60 ms.
∆2 = Spark quenching time = 20 ms.
∆3 = Additional waiting time for discrepancies in opening of circuit breakers A and B.
∆4 = Closure time of circuit breaker B = 80 ms.
∆5 = Stabilization time of synchronism relay signals = 30 ms.
∆6 = Time set in the synchronism relay for voltage checking (setting).
∆7 = Time for action of output unit of the synchronism relay = 30 ms.
∆8 = Closure time of circuit breaker A = 80 ms.
∆9 = Reset time of the synchronism relay = 130 ms.
∆10 = Sustained time of synchronism enable = 130 ms.
Λ3
Λ1Λ2Λ4Λ6
Λ5Λ7Λ8Λ9Λ10
AB

GEK - 105560
10
Application of voltage
As the MLJ is equipped with instantaneous undervoltage monitoring in two inputs (line and bus), and
with undervoltage and overvoltage levels (live and dead), it can be used as a relay in a large number of
applications such as:
• Undervoltage
• Overvoltage
• Voltage within the limits
• Voltage outside of limits
• Instantaneous or time delayed
In order to do so, the following should be set:
1. The desired settings for the presence or absence of voltage in line and bus (3-1 to 3-4).
2. The enable settings of the undervoltage unit (4-2 to 4-4).
3. The control setting for voltage in line and bus (2-2).
4. The enables for the synchronism unit and synchronism control (4-2 and 2-1).
5. The configured function for auxiliary relays (5-1 and 5-2).
6. The output contact jumpers (normally open or closed).

GEK - 105560
11
3. OPERATION PRINCIPLES
The MLJ can be described as the function of a group of different units, each being responsible for one
part of the overall operation.
3.1 CONFIGURATION UNIT
The configuration unit allows us to select and change the following parameters:
• Frequency (50 or 60 Hz).
• Unit number.
• Communication speed.
3.1.1 GENERAL Settings
The configuration unit has the following settings:
0-1: f Operation frequency
Range: 50 or 60
Units: Hz
Default value: 50
6-1: COM. ID Unit number (relay identifier)
Range: 1-255
Default value: 1
6-2: COM. kbauds Serial port baud rate
Range: 0.3, 0.6, 1.2, 2.4, 4.8, 9.6, 14.4, 19.2, 38.4
Units: kilobauds
Default value: 9.6
NOTE
:Settings 6-1 and 6-2 are the only ones that do no restart the protection since they only affect
communications. The rest of the protection settings restart the protection.
3.2 SYNCHRONISM CHECK UNIT
The main function of the MLJ is that of providing synchronism conditions for circuit breaker closures.
The synchronism check unit analyzes the voltage magnitudes at both side of the circuit breaker, and
the status of inputs and the settings, giving a synchronism signal if the conditions are met.
Depending on the status of the Manual input, this unit has two modes of operation: Manual mode and
Continuous mode. They are both described below.

GEK - 105560
12
3.2.1 Mode of Operation
Using an analog to digital converter, samples of line and bus voltages are acquired. From the samples,
and applying the discrete Fourier transform (DFT), the module and argument of both magnitudes are
obtained, and from them, the voltage and angle differences. With the measurement of the period, the
frequency slip is obtained.
Once the basic fundamental magnitudes and their derivatives have been obtained, they are compared
to the settings (see figure 7). The status of the external digital inputs is checked as well: circuit breaker
52b input, Manual mode input and Enable input. For the checking to begin, input 52b must be
activated, showing that the circuit breaker is open.
If all the synchronism conditions are met, a time delay mechanism will be tripped and when the time
limit is reached the synchronism signal SYNC will finally be obtained.
There are two different settings for the time delay mechanism:
• If Manual input is not activated, it will remain in Continuous mode and the time delay mechanism
will work based on the first setting (setting 1-4 t cont). If, on the other hand, Manual input is
activated, it will work in Manual mode and the setting of the time delay mechanism will be the
second setting (setting 1-5 t man).
• If the relay is in Manual mode, checking synchronism will begin when the Enable input is activated.
However, in Continuous mode, the Enable input will not effect the relay.
The synchronism signal can be obtained in the Enable and Closure output relays, as well as in the
auxiliary relays, if they have been configured for this purpose.

GEK - 105560
13
3.2.2 Settings
The synchronism unit is assigned the following settings:
1-1: ∆V: Voltage difference (modulus of vector difference).
Range: from 2 to 90 in steps of 0.5
Units: volts
Default value: 15
1-2: ∆θ:Angle
Range: from 2 to 60º in steps of 1
Units: degrees
Default value: 10
1-3: ∆f; Difference in frequencies (frequency slip).
Range: from 10 to 500 in steps of 10
Units: mHz
Default value: 20
1-4:t cont: Time delay in continuous mode.
Range: from 0.1 to 99.0 steps of 0.1
Units: seconds
Default value: 0.1
1-5: t man: Time delay in manual mode.
Range: from 0.1 to 99.0 steps of 0.1
Units: seconds
Default value: 10.0
2-1: SUP 27 ON-OFF: Undervoltage supervision enable
Range: Enabled or disabled
Units: --
Default value: OFF (Disabled)
2-2: SUP 27 V: Undervoltage threshold supervision.
Range: from 10 to 180 in steps of 1
Units: volts
Default value: 40
4-1: 25 ON-OFF: Activation of the synchronism check unit.
Range: Enabled or disabled
Units: --
Default value: OFF (Disabled)
3.2.3 Failure of Closure Conditions
In order to make possible certain applications, the MLJ can provide a signal indicating Synchronism
Failure if synchronism conditions have not been achieved 1 minute from having activated the Enable
input or the Manual mode input.
This signal showing a failure in closure conditions may be obtained via a suitable configuration of the
auxiliary contacts. This unit does not have its own setting.

GEK - 105560
14
3.3 UNDERVOLTAGE UNIT
Besides the undervoltage described in and linked with the synchronism unit, there is an independent
unit which has various undervoltage and overvoltage functions to allow for the closure of the circuit
breaker in dead lines and/or bus situations (see figure 1).
3.3.1 Mode of Operation
The modulus are calculated from the line and bus voltage phasors and then compared with the
settings. For each voltage two different levels can be set.
If the voltage is below the set undervoltage level, the corresponding line or bus is said to be dead. If the
voltage is above the set overvoltage level, the line or bus is said to be live.
There can be three different situations of undervoltage: live line and bus (LLLB), dead line and live bus
(DLLB), or dead bus and live line (LLDB). By choosing settings we are able to make the undervoltage
unit operate in any of these situations.
Similar to what has been stated in the case of the synchronism unit, if the Manual input is activated, in
order for the undervoltage units to operate, it is necessary to also activate the Enable input. However,
as opposed to the synchronism check unit, this undervoltage unit has no time delay whatsoever.
3.3.2 Settings
The undervoltage unit has the following assigned settings:
3-1: VL↑:Level of voltage present in line (live line: LL).
Range: from 40 to 245 in steps of 1.
Units: volts
Default value: 50
3-2: VL↓:Level of voltage absent in line (dead line: DL).
Range: from 10 to 180 in steps of 1.
Units: volts
Default value: 30
3-3: VB↑:Level of voltage present in bus (live bus: LB).
Range: from 40 to 245 in steps of 1.
Units: volts
Default value: 50
3-4: VB↓:Level of voltage absent in bus (dead bus: DB).
Range: from 10 to 180 in steps of 1.
Units: volts
Default value: 30
4-2: DLDB ON-OFF: Activation condition: dead line and bus (DLDB).
Range: Enabled or disabled.
Units: --
Default value: OFF (Disabled)
4-3: DLLB ON-OFF: Activation condition: dead line with live bus
(DLLB).
Range: Enabled or disabled.
Units: --
Default value: OFF (Disabled)

GEK - 105560
15
4-4: LLDB ON-OFF: Activation condition: live line with dead bus
(LLDB).
Range: Enabled or disabled.
Units: --
Default value: OFF (Disabled)
NOTE
: The relay does not check to see if the live line setting (3-1) is greater than the dead line setting
(3-2). This is also applied to the bus settings (3-3 and 3-4). This allows for protection schemes
for under or overvoltage, as well as inhibiting close enable in overvoltage situations.
3.4 INPUT UNITS
The three digital inputs are activated with D.C. voltages and with the same range of values as those of
the auxiliary voltage.
The input unit not only reads the state of the inputs, but also filters the possible bounce or noise which
may be present.
Input 52b indicates the state of the circuit breaker. If it is active it means that the circuit breaker is
open. In this case the synchronism unit can give synchronism if the rest of the set conditions are met. If
it is not used, voltage must be applied to this input in order to enable the synchronism unit.
The Manual mode input changes the time of the delay mechanism of the synchronism unit and gives
way to the Enable input; if that input is not active, neither the synchronism nor the undervoltage will be
activated.
When Manual mode is not desired, simply disconnect the Manual and Enable inputs, leaving the
terminals corresponding to these two inputs free.
3.5 SELF-CHECK UNIT
While operating the synchronism and undervoltage units, the MLJ continuously carries out internal
checks to verify the integrity of its components.
3.5.1 Mode of Operation
During startups and regular operation, the MLJ monitors the following parameters without interfering
with normal operation:
• Program memory (ROM).
• Work memory (RAM).
• Non-volatile setting memory (EEPROM).
• Setting validity.
• Analog measurement circuits.
A WATCHDOG internal system diagnosis the program sequences using task chaining - which provides
a high level of security of the internal operation.
During startup, a thorough check is carried out, during which the message “tSt” appears on the relay
display.
This unit indicates possible failures detected using codes on the display. It also generates an Alarm
signal, which can be obtained on an alarm contact (programmable) as well as an auxiliary contact..
Upon detection of a system failure, the outputs are deactivated in order to avoid misoperation of the
relay.

GEK - 105560
16
The codes for failures are:
0.0. No defects
8.0. ROM failure. The program memory has failed.
8.1. Writing failure to EEPROM
8.2. RAM program failure
0.1. Setting failure. The settings stored are incorrect. This error is also shown when the
EEPROM memory is new (in which case the settings are stored by default).
0.4. Measurement error (defect in the analog circuits).
If there are multiple failures, only the one with top priority is shown. The above is listed from most to
least important.
3.6 OUTPUT UNITS
The MLJ has 5 outputs which are relay contacts. The contacts can be configured as normally opened
(N.O.) or normally closed (N.C.), by means of internal jumpers (solded in the printed circuit board). The
contacts included are:
2 close enable contacts. Set in the factory as normally opened (N.O.) (non-configurable).
1 alarm contact. Set in the factory as normally closed (N.C.) (non-configurable).
1 auxiliary contact. Set in the factory as normally opened (N.O.) and configured in factory as function
25.
1 auxiliary contact. Set in the factory as normally opened (N.O.) and configured in factory as function
27.
3.6.1 Mode of Operation
Internally, the MLJ reads the signals sent from the following units: the synchronism and synchronism
failure signals supplied by the synchronism unit; the undervoltage, dead bus and line signals supplied
by the undervoltage unit; and, finally, the alarm signal given by the self-check unit.
If there is a synchronism or undervoltage signal, this unit will activate the Close enable relays.
If there is an Alarm signal, or if the power fails, the Alarm relay will be deactivated. For this reason this
contact is always configured as normally closed (N.C.) contact.
The auxiliary relays are activated depending on how they have previously been configured. The
configuration is individual for each of them, and is done by selection using the following menu:
− Close enable (PEr)
− Synchronism (25)
− Undervoltage (27)
− Dead line (_dL)
− Dead bus (db_)
− Failure of closure conditions (F25)
− Alarm (ALA)
NOTE
:the message that appears on the screen is shown in parenthesis.
The selection of the outputs as normally opened (N.O.) or normally closed (N.C.) can be done
withdrawing the MLJ from its case and changing the jumpers to C for closed and A for opened,
respectively (a solder gun is required for this operation).
3.6.2 Settings
There are two settings, one for each of the auxiliary outputs:
5-1 1: Configuration: first auxiliary output
Range: PEr, 25, 27, _dL, db_, F25, ALA
Units: --

GEK - 105560
17
Default value: 25 (synchronism)
5-2 2: Configuration: second auxiliary output
Range: PEr, 25, 27, _dL, db_, F25, ALA
Units: --
Default value: 27 (undervoltage)
3.7 POWER SUPPLY
The power supply circuit of the MLJ generates, from the auxiliary voltage, the internal voltages
necessary for the operation of the relay.
The power supply isolates the internal circuitry from external perturbations, for both industrial and high
frequencies.
The power supply is effective over a wide range and is a switching type power supply.

GEK - 105560
18
4. TECHNICAL CHARACTERISTICS
4.1 MODEL LIST
Here is the information required to completely define the MLJ models. (See chart below):
MLJ 100 _A010 _00 _
Communications Auxiliary and inputs voltage Case
0 - No communications F - 24/ 48 Vdc C - In individual case
5 - RS-485 H - 110/ 250 Vdc S - In MID system
6 - RS-485, 232, plastic optic fiber
7 - RS-485, 232, glass optic fiber
4.2 TECHNICAL CHARACTERISTICS
• FREQUENCY
50 and 60 Hz, programmable by user.
• NOMINAL VOLTAGE
63 to 220 Vac.
• AUXILIARY POWER
24 - 28 Vdc ±20%
110 - 250 Vdc ±20%
• MAXIMUM VOLTAGE ALLOWABLE
Continuous: 440 Vac.
• TEMPERATURE RANGES
Operating: -25ºC to +55ºC
Storage: -40ºC to +65ºC
Comply with IEC standard 255-6 (for the -25º to +55ºC interval) and ANSI C37.90 (specifying the -
25º to +55ºC interval).
• AMBIENT HUMIDITY
Up to 95% without condensation.
• CLOSURE ENABLE CONTACTS
Break capacity: 4000 VA
Maximum continuous voltage: 300 Vdc
Maximum alternating voltage: 440 Vac
Carry continuously: 16 A
Make and carry: 30 A

GEK - 105560
19
• ALARM AND AUXILIARY CONTACTS
Break: 1760 VA
Maximum continuous voltage: 250 Vdc
Maximum alternating voltage: 380 Vac
Make and carry: 8 A
Carry continuously: 8 A
• ACCURACY
Voltage: 2% or 0.5 V
Voltage difference: 3% or 1 V
Angle difference: 1º (voltages between 20 and 220 Vac)
2.5º (voltages between 10 and 20 Vac and between 220 and
300 Vac)
Frequency slip: 5 mHz (range of 45 to 65 Hz)
Time: 1% or 30 ms (*)
The slip measurement unit may require up to 60 ms, which will be added to the time delay
introduced by setting; this is typical behavior.
• VOLTAGE CIRCUIT BURDEN
Less than 0.15 VA at 110 V and 50 Hz or at 120 V and 60 Hz.
• DIGITAL INPUTS BURDEN
24 to 48 Vdc model: 30 kOhm
110 to 220 Vdc model: 136 kOhm
• AUXILIARY POWER SUPPLY BURDEN
Idle: 3W (NC alarm relay activated only)
Tripped: 6W (all relays activated)
• WEIGHTS
Net: 3 kg.
Shipping: 4 kg.
4.3 INSULATION
According to IEC 255-5.
Between each terminal and ground: 2000 Vac for 1 minute at industrial frequency.
Between independent circuits: 2000 Vac for 1 minute at industrial frequency.
This manual suits for next models
1
Table of contents
Other GE Relay manuals
Popular Relay manuals by other brands
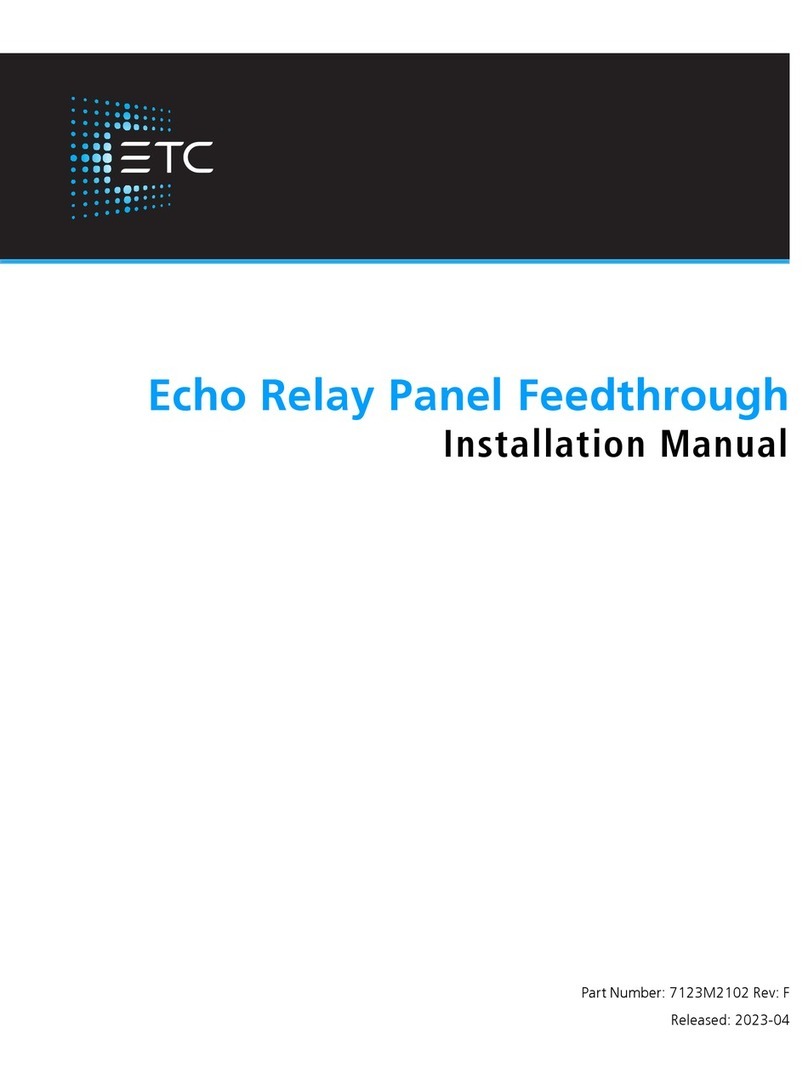
ETC
ETC Echo Relay Panel Feedthrough installation manual
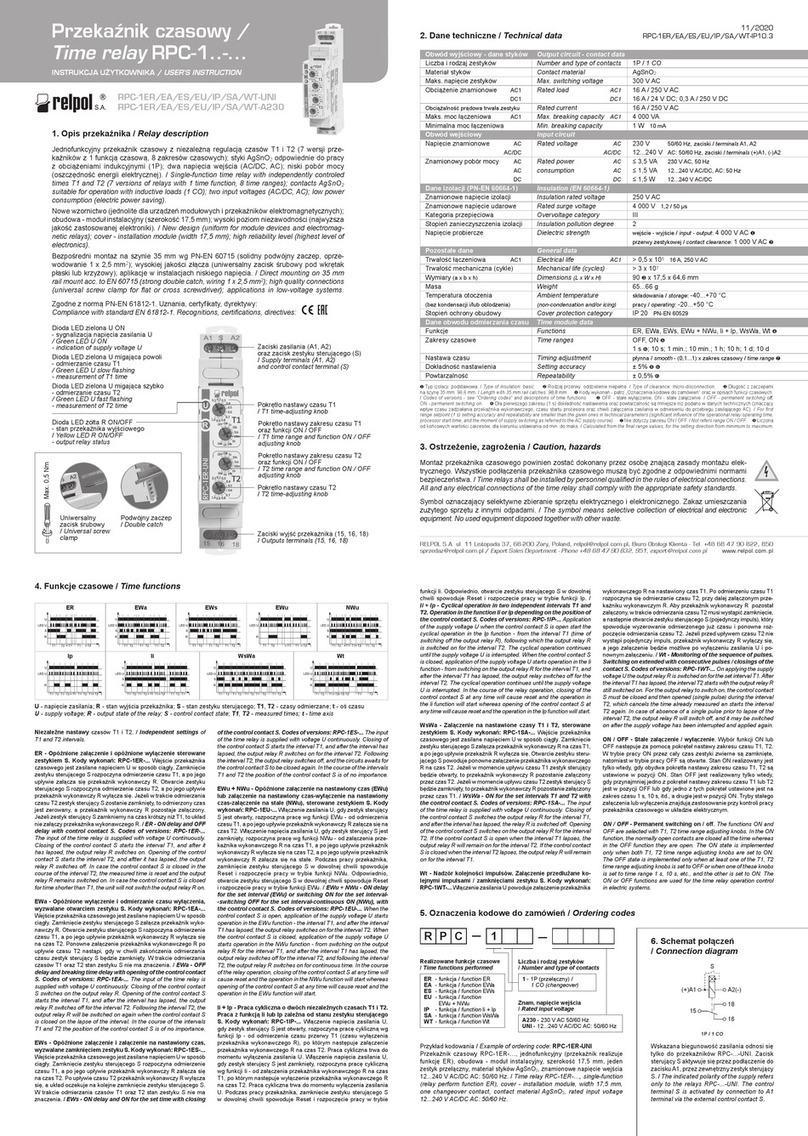
Relpol
Relpol RPC-1 Series User instruction

Woodward
Woodward WIC1 Series Original Technical Manual
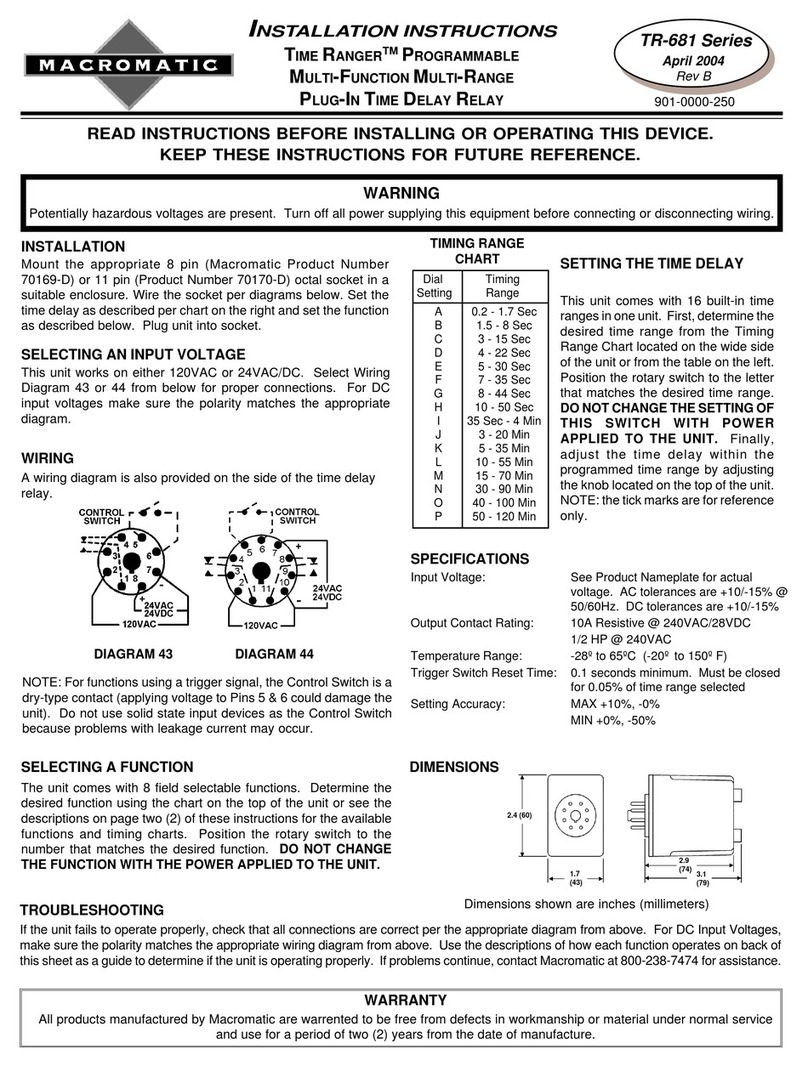
macromatic
macromatic Time Ranger TR-681 Series installation instructions
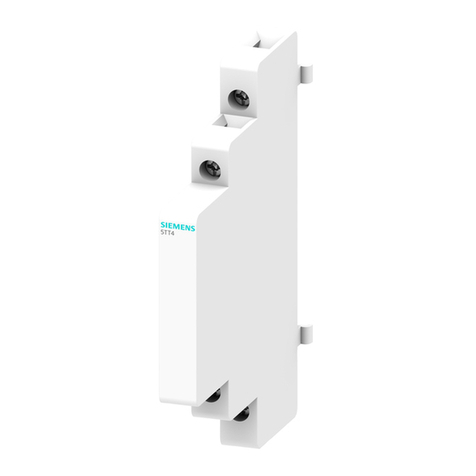
Siemens
Siemens 5TT4930 operating instructions

Siemens
Siemens Solkor 7PG2113 manual