GE AV-Line Instruction Manual

Table
of
Contents
PAGE
DESCRIPTION
AV
-
LINE
Switchboard
Construction
Receiving
,
Handling
and
Storage
Installing
the
Bus
Stub
For
LVD
Stubs
For
Armor
Clad
Stubs
Short
Circuit
Cable
Bracing
MAIN
CABLE
AV
-
1
,
AV
-
2
,
AV
-
5
Switchboards
utilizing
cord
for
Short
Circuit
Protection
.
AV
-
3
,
AV
-
4
Switchboards
utilizing
cord
for
Short
Circuit
Protection
.
LOAD
CABLE
AV
-
3
,
AV
-
4
Switchboards
utilizing
cord
for
Short
Circuit
Protection
.
Installing
the
Switchboard
Switchboard
Maintenance
3
4
5
5
5
6
6
7
8
9
,
10
,
11
11
,
12
)
2
Courtesy of NationalSwitchgear.com

AV
-
Line
®
Switchboard
Construction
These
instructions
do
not
purport
to
cover
ail
de
-
tails
or
variations
in
equipment
nor
do
they
pro
-
vide
for
every
possible
contingency
to
be
met
in
connection
with
installation
,
operation
or
mainte
-
nance
.
Should
further
information
be
desired
,
or
should
particular
problems
arise
which
are
not
covered
sufficiently
for
the
purchaser
’
s
purpose
,
the
matter
should
be
referred
to
the
General
Electric
Company
.
-
I
m
N
i
051
-
i
=
*
r
'
0
$
n
a
M
3
a
c
a
tin
C
3
Q
*
QD
c
!
Li
»
f
c
«
55
A
Spa
\
FIGURE
1
Typical
group
mounted
distribution
construction
.
FIGURE
2
Typical
individually
mounted
distribution
construction
.
?
3
Courtesy of NationalSwitchgear.com

Receiving
,
Handling
and
Storage
RECEIVING
45
°
MINIMUM
Before
leaving
the
factory
,
the
switchboard
is
given
a
final
in
-
spection
and
packed
by
workmen
experienced
in
the
proper
handling
and
packing
of
electrical
equipment
.
Upon
receipt
of
any
apparatus
,
an
immediate
inspection
should
be
made
for
any
damage
sustained
in
transit
.
If
damage
is
noted
,
or
indication
of
rough
handling
is
visible
,
a
claim
for
damage
should
be
filed
with
the
carrier
.
Information
as
to
damaged
parts
,
part
number
,
case
number
,
requisition
number
,
etc
.
,
should
accompany
the
claim
.
In
regard
to
claims
for
damaged
shipments
,
shortages
and
incor
-
rect
material
,
the
following
is
an
excerpt
from
the
Published
Supplemental
Terms
and
Conditions
of
Sale
for
products
of
the
Distribution
Equipment
Division
,
General
Electric
Company
.
“
Title
and
risk
of
loss
shall
pass
upon
delivery
of
the
products
to
the
carrier
at
the
f
.
o
.
b
.
point
and
invoices
shall
be
payable
with
-
out
deduction
for
losses
in
shipment
.
It
is
the
Purchaser
’
s
re
-
sponsibility
to
file
claims
with
the
carrier
for
loss
or
damage
in
transit
.
”
-
“
Claims
for
shortages
or
incorrect
material
must
be
made
in
writing
within
30
days
after
receipt
of
the
shipment
by
the
Pur
-
chaser
,
and
the
failure
to
give
the
Company
such
written
notice
within
the
30
-
day
period
shall
be
unqualified
acceptance
of
the
products
and
a
waiver
by
the
Purchaser
of
all
claims
for
short
-
ages
or
incorrect
material
.
”
HANDLING
FIGURE
4
FIGURE
3
Using
lifting
slings
,
spreader
Using
lifting
plates
,
angles
or
and
blocking
are
not
furnished
beams
which
are
furnished
with
equipment
.
Equipment
may
be
moved
into
position
by
means
of
construction
rollers
under
the
shipping
skids
.
Remove
all
outer
packaging
.
Lifting
by
crane
or
other
hoisting
methods
done
as
shown
in
Figures
3
and
4
.
To
remove
the
AV
-
LINE
Switchboard
from
the
skids
after
taking
out
the
shipping
bolts
,
carefully
slide
the
equipment
so
that
the
rear
side
is
off
the
skids
,
resting
on
the
floor
(
see
Fig
.
5
)
.
Tit
the
entire
equipment
slightly
to
the
rear
to
release
the
skids
.
Caution
is
advised
in
sliding
and
tilting
this
equipment
due
to
its
height
and
weight
.
It
can
become
top
heavy
if
tilted
too
far
.
Slide
the
switchboard
into
place
by
pushing
on
the
frame
.
Blow
out
any
dust
or
loose
particles
of
packing
material
which
may
have
col
-
lected
on
the
device
parts
.
Remove
all
protective
blocking
on
relays
,
devices
or
breakers
.
with
equipment
.
LIFTING
INSTRUCTIONS
1
.
Do
not
pass
cables
or
ropes
through
support
holes
.
2
.
Always
use
load
rated
shackles
or
safety
hooks
in
support
holes
.
3
.
Rig
so
that
legs
of
sling
(
Figs
.
3
and
4
)
are
no
less
than
45
°
from
horizontal
.
REMOVE
STORAGE
1
X
-
/
If
it
is
necessary
to
store
the
equipment
for
any
length
of
time
,
the
following
precautions
should
be
taken
to
prevent
corrosion
or
breakage
:
1
.
Uncrate
equipment
.
2
.
Store
in
a
clean
,
dry
,
rodent
-
free
area
in
moderate
tempera
-
ture
.
Cover
with
a
suitable
canvas
to
prevent
deposits
of
dirt
or
other
foreign
material
on
movable
parts
and
electrical
con
-
tact
surfaces
.
(
Heavy
duty
plastic
covers
are
recommended
.
)
3
.
If
stored
in
cool
or
damp
areas
,
heat
should
be
provided
to
keep
the
equipment
dry
.
On
outdoor
switchboards
this
may
be
accomplished
by
making
a
temporary
power
connection
to
the
heaters
installed
in
the
equipment
.
On
indoor
switch
-
boards
,
two
standard
120
volt
lamps
rated
at
100
watts
can
be
used
inside
each
vertical
section
.
-
m
.
r
T
REMOVE
i
mm
mm
FIGURE
5
Remove
lag
bolts
.
Slide
unit
off
skid
and
remove
skid
.
CAUTION
:
Remove
all
cartons
and
other
miscellaneous
pack
-
ing
material
from
inside
the
units
before
energizing
any
heaters
.
4
Courtesy of NationalSwitchgear.com

Installing
The
Bus
Stub
STUB
STUB
1
2
3
STUB
COVER
STUB
COVER
FLANGE
ADAPTER
6
REMOVABLE
FRAME
MEMBER
w
r
a
REMOVE
REAR
COVER
<
D
-
n
5
:
'
A
a
4
-
mi
-
C
FIGURE
6
For
LVD
stubs
.
FIGURE
7
For
Armor
-
Clad
stubs
.
INSTALLATION
PROCEDURES
2
J
Slide
flange
adapters
together
to
close
up
slot
.
If
access
to
switchboard
bus
at
point
of
connection
to
busway
stub
is
limited
by
wall
or
other
obstruction
,
stub
must
be
installed
before
board
is
placed
in
final
location
.
3
.
)
Loosely
fasten
bus
stub
flange
to
stub
cover
with
hardware
furnished
with
stub
.
(
4
j
)
Bolt
stub
bus
to
switchboard
bus
(
see
Fig
.
7
A
)
.
(
£
)
Bolt
neutral
splice
bus
(
if
required
)
to
stub
neutral
with
hard
-
ware
furnished
with
the
neutral
splice
bus
.
(
6
?
)
After
stub
and
switchboard
bus
is
properly
aligned
and
bolted
,
tighten
down
flange
screws
.
©
Remove
shipping
screws
holding
bus
stub
flange
adapter
to
stub
cover
.
Slide
adapter
apart
to
allow
stub
to
enter
through
slot
in
cover
.
When
space
is
limited
,
the
top
rear
frame
mem
-
ber
may
be
removed
so
that
the
stub
with
stub
cover
may
be
installed
horizontally
instead
of
vertically
.
SWITCHBOARD
BUSBAR
BUS
STUB
FLAT
WASHER
V
2
-
13
BOLT
OPEN
SLOT
LOCK
WASHER
DO
NOT
FILL
IN
OPEN
SLOT
WITH
HARDWARE
FIGURE
7
A
For
Armor
-
Clad
stubs
.
5
Courtesy of NationalSwitchgear.com

WARNING
:
Short
Circuit
Cable
Bracing
Required
s
:
\
LOAD
CABLE
BRACING
MAIN
CABLE
BRACING
Load
cable
short
circuit
bracing
is
required
for
each
component
installed
in
an
AV
-
3
or
AV
-
4
switchboard
section
with
available
short
circuit
currents
of
65
,
000
rms
symmetrical
amperes
and
above
.
Main
cable
bracing
is
required
when
five
cables
per
phase
or
less
feed
a
switchboard
at
available
short
circuit
currents
of
100
,
000
and
150
,
000
rms
symmetrical
amperes
,
and
eight
cables
per
phase
or
less
at
an
available
short
circuit
current
of
200
,
000
rms
symmetrical
amperes
.
Assembly
,
purchasing
and
maintenance
instructions
for
main
cable
short
circuit
bracing
can
be
found
on
pages
6
and
7
.
Assembly
,
purchasing
and
maintenance
instructions
for
load
cable
short
circuit
bracing
can
be
found
on
page
8
.
Installing
The
Main
Cable
AV
-
1
,
AV
-
2
AND
AV
-
5
SWITCHBOARDS
UTILIZING
CORD
FOR
SHORT
CIRCUIT
PROTECTION
PRIOR
TO
INSTALLATION
minimum
,
making
6
revolutions
around
the
"
A
”
and
“
B
,
?
phase
main
cables
and
6
revolutions
around
the
“
B
"
and
“
C
”
phase
main
cables
.
Now
,
with
the
remaining
cord
,
wrap
the
main
cable
lashing
to
the
cable
braces
in
between
phases
with
4
to
5
revolu
-
tions
,
tieing
a
knot
to
the
cable
braces
as
you
complete
your
last
revolution
.
All
revolutions
should
be
made
as
tight
as
possible
so
as
to
prevent
whipping
during
short
circuits
.
Before
any
installation
work
is
performed
,
study
all
drawings
furnished
by
the
General
Electric
Company
for
the
particular
installation
.
These
include
arrangement
drawings
(
front
,
end
and
plan
view
)
,
connection
diagrams
and
schedule
of
equip
-
ment
.
Any
material
external
to
the
equipment
which
may
be
required
to
meet
any
local
codes
(
railings
,
etc
.
)
is
not
furnished
.
INSPECTION
AFTER
MAIN
CABLE
INSTALLATION
CABLE
BRACE
4
To
prevent
heating
,
there
should
be
no
closed
loop
of
steel
around
a
single
conductor
or
group
of
conductors
which
does
not
include
all
the
conductors
(
including
the
neutral
)
of
the
circuit
.
If
the
conductors
must
pass
through
separate
holes
in
a
piece
of
steel
,
slots
should
be
cut
between
the
holes
.
Do
not
allow
cables
carrying
heavy
current
to
come
near
instruments
or
meters
as
this
may
affect
their
accuracy
.
Use
the
minimum
amount
of
cable
necessary
to
accomplish
the
connections
.
The
increased
resist
-
ance
of
longer
cables
generates
unnecessary
heat
.
Main
cable
lashing
should
be
checked
bi
-
monthly
.
-
3
)
f
•
s
fol
[
s
-
i
-
MAIN
CABLE
TERMINALS
FIGURE
7
B
INSTALLATION
PROCEDURES
FOR
MAIN
CABLE
WITH
SHORT
CIRCUIT
PROTECTION
Align
conduit
holes
in
a
linear
orientation
directly
over
or
as
close
as
possible
to
the
braces
.
Consideration
should
be
given
to
installing
conduits
or
sleeves
which
might
be
required
for
future
connections
.
Run
and
bend
the
main
cable
in
a
most
convenient
orientation
,
making
sure
the
main
cable
has
been
located
directly
up
against
the
cable
braces
before
it
connects
to
the
main
cable
terminals
.
Lash
the
main
cable
according
to
Figure
7
B
above
,
using
a
polyester
braided
rope
having
a
tensile
strength
of
2000
lbs
.
)
6
Courtesy of NationalSwitchgear.com

Installing
The
Main
Cable
f
AV
-
3
,
AV
-
4
SWITCHBOARDS
UTILIZING
CORD
FOR
SHORT
CIRCUIT
PROTECTION
A
A
ft
g
*
CABLE
BRACE
|
oT
o
B
Cal
[
o
;
FIGURE
7
C
FIGURE
7
D
PRIOR
TO
INSTALLATION
INSPECTION
AFTER
MAIN
CABLE
INSTALLATION
Before
any
installation
work
is
performed
,
study
all
drawings
furnished
by
the
General
Electric
Company
for
the
particular
installation
.
These
include
arrangement
drawings
(
front
,
end
and
plan
view
)
,
connection
diagrams
and
schedule
of
equip
-
ment
.
Any
material
external
to
the
equipment
which
may
be
required
to
meet
any
local
codes
(
railings
,
etc
.
)
is
not
furnished
.
To
prevent
heating
,
there
should
be
no
closed
loop
of
steel
around
a
single
conductor
or
group
of
conductors
which
does
not
include
all
the
conductors
(
including
the
neutral
)
of
the
circuit
.
If
the
conductors
must
pass
through
separate
holes
in
a
piece
of
steel
,
slots
should
be
cut
between
the
holes
.
Do
not
allow
cables
carrying
heavy
current
to
come
near
instruments
or
meters
as
this
may
affect
their
accuracy
.
Use
the
minimum
amount
of
cable
necessary
to
accomplish
the
connections
.
The
increased
resis
-
tance
of
longer
cables
generates
unneccessary
heat
.
Main
ca
-
ble
lashing
should
be
checked
bi
-
monthly
.
INSTALLATION
PROCEDURES
FOR
MAIN
CABLE
WITH
SHORT
CIRCUIT
PROTECTION
Align
conduit
holes
in
a
linear
orientation
a
distance
equal
to
the
radius
bend
of
the
cable
.
Consideration
should
be
given
to
in
-
stalling
conduits
or
sleeves
which
might
be
required
for
future
connections
(
see
Figure
7
D
)
.
Run
and
bend
the
main
cable
in
a
most
convenient
orientation
,
making
sure
the
main
cable
has
been
located
directly
up
against
cable
braces
before
it
connects
to
the
main
cable
terminals
(
see
Figure
7
C
)
.
Lash
the
main
cable
according
to
Figure
7
C
above
,
using
a
polyester
braided
rope
having
atensile
strength
of
2000
lbs
.
minimum
,
making
6
revolu
-
tions
around
the
“
A
”
and
“
B
”
phase
main
cables
and
6
revolu
-
tions
around
the
“
B
”
and
“
C
”
phase
main
cables
.
Now
with
the
remaining
cord
,
wrap
the
main
cable
lashing
to
the
cable
brace
in
between
phases
with
4
to
5
revolutions
,
and
tie
a
knot
to
the
cable
brace
as
you
complete
your
last
revolution
.
All
revolutions
should
be
made
as
tight
as
possible
so
as
to
prevent
whipping
during
short
circuits
.
7
Courtesy of NationalSwitchgear.com

Installing
The
Load
Cable
•
V
AV
-
3
AND
AV
-
4
SWITCHBOARDS
UTILIZING
CORD
FOR
SHORT
CIRCUIT
PROTECTION
•
I
re
SF
a
\
E
^
2
CABLE
BRACE
I
O
1
1
im
(
CD
|
'
FIGURE
7
F
FIGURE
7
E
INSPECTION
AFTER
LOAD
CABLE
INSTALLATION
PRIOR
TO
INSTALLATION
Before
any
installation
work
is
performed
,
study
all
drawings
furnished
by
the
General
Electric
Company
for
the
particular
installation
.
These
include
arrangement
drawings
(
front
,
end
and
plan
view
)
,
connection
diagrams
and
schedule
of
equip
-
ment
.
Any
material
external
to
the
equipment
which
may
be
required
to
meet
any
local
codes
(
railings
,
etc
.
)
is
not
furnished
.
To
prevent
heating
,
there
should
be
no
closed
loop
of
steel
around
a
single
conductor
or
group
of
conductors
which
does
not
include
all
the
conductors
(
including
the
neutral
)
of
the
circuit
.
If
the
conductors
must
pass
through
separate
holes
in
a
piece
of
steel
,
slots
should
be
cut
between
the
holes
.
Do
not
allow
cables
carrying
heavy
current
to
come
near
instruments
or
meters
as
this
may
affect
their
accuracy
.
Use
the
minimum
amount
of
cable
necessary
to
accomplish
the
connections
.
The
increased
resis
-
tance
of
longer
cables
generates
unnecessary
heat
.
Load
cable
lashing
should
be
checked
bi
-
monthly
.
INSTALLATION
PROCEDURES
FOR
LOAD
CABLE
WITH
SHORT
CIRCUIT
PROTECTION
Locate
the
load
cable
braces
which
can
be
found
every
18
"
on
the
back
of
the
switchboard
.
Run
and
bend
the
load
cable
in
the
most
convenient
manner
,
making
sure
that
the
load
cable
is
up
against
the
load
cable
brace
closest
to
the
component
’
s
load
terminals
(
see
Figure
7
E
)
and
to
every
load
cable
brace
above
or
below
,
depending
if
the
load
cable
will
exit
the
switchboard
on
top
or
bottom
(
see
Figure
7
F
)
.
After
running
the
load
cable
up
against
the
load
cable
braces
and
using
a
polyester
braided
rope
having
a
tensile
strength
of
2000
lbs
.
minimum
,
lash
the
load
cable
to
the
load
cable
brace
,
making
4
revolutions
around
the
cable
and
the
brace
.
Tie
a
knot
to
the
cable
brace
after
completion
of
the
last
revolution
.
All
revolutions
should
be
made
as
tight
as
possible
so
as
to
prevent
whipping
during
short
circuits
.
8
Courtesy of NationalSwitchgear.com

Installing
The
AV
-
Line
Switchboard
PRIOR
TO
INSTALLATION
Before
any
installation
work
is
performed
,
study
all
drawings
furnished
by
the
General
Electric
Company
for
the
particular
installation
.
These
include
arrangement
drawings
(
front
,
end
,
and
plan
view
)
,
connection
diagrams
and
schedule
of
equip
-
ment
.
Any
material
external
to
the
equipment
which
may
be
required
to
meet
any
local
codes
,
(
mats
,
screens
,
railings
,
etc
.
)
,
is
not
furnished
.
gn
,
nu
LOCATION
In
locating
the
switchboard
,
consideration
should
be
given
to
the
aisle
space
required
.
The
space
at
the
front
must
be
sufficient
to
permit
the
opening
of
doors
,
and
the
insertion
and
withdrawal
of
removable
breakers
.
The
space
at
the
rear
must
be
sufficient
for
opening
of
doors
as
well
as
the
cables
,
inspection
,
and
mainte
-
nance
.
Check
local
codes
for
special
aisle
space
requirements
.
FIGURE
8
Bolting
the
switchboard
directly
to
the
floor
—
indoor
construction
.
FRONT
\
FOUNDATION
REQUIREMENTS
Indoor
Equipment
—
The
floor
or
foundation
must
be
strong
enough
to
prevent
sagging
from
the
weight
of
the
switchboard
structure
.
If
the
foundation
is
subject
to
vibrations
,
special
mounting
must
be
provided
to
prevent
the
transmittal
of
vibra
-
tions
to
the
equipment
.
Because
of
its
high
structural
strength
,
the
AV
-
LINE
Switchboard
may
be
bolted
directly
to
the
floor
(
see
Fig
.
8
)
.
The
floor
must
be
entirely
level
without
any
high
spots
which
might
cause
misalign
-
ment
.
If
the
floor
is
not
level
it
is
recommended
that
floor
channels
be
used
.
The
steel
floor
channels
when
used
should
be
embedded
in
a
level
concrete
slab
with
the
top
surface
of
the
channels
flush
with
the
finished
floor
.
To
avoid
distortion
of
the
structure
,
it
is
essen
-
tial
that
the
steel
channels
be
level
and
aligned
with
each
other
prior
to
the
final
anchoring
.
The
recommended
foundation
con
-
struction
and
method
of
mounting
the
switchboard
to
the
founda
-
tion
is
shown
in
Fig
.
9
.
Channels
should
be
grouted
after
installation
.
i
ur
r
FIGURE
9
Switchboard
mounted
on
floor
channels
—
indoor
construction
.
FRONT
\
j
I
Outdoor
Equipment
—
Outdoor
equipment
is
usually
installed
on
a
concrete
pad
with
a
level
and
smooth
surface
.
Channel
sills
are
supplied
with
the
switchboard
,
two
with
the
non
-
walk
-
in
type
and
three
for
the
walk
-
in
type
as
shown
in
Figs
.
10
and
11
.
Channels
should
set
on
the
pad
and
be
filled
with
grout
.
Conduits
—
At
the
time
the
foundation
channels
are
being
in
-
stalled
,
any
conduits
or
sleeves
required
for
power
and
control
cables
that
are
to
enter
the
equipment
from
underneath
should
be
located
and
installed
within
the
available
space
shown
on
the
floor
plan
drawings
.
Consideration
should
be
given
to
installing
conduits
or
sleeves
which
might
be
required
for
future
connec
-
tions
.
Conduit
stubs
should
extend
above
the
floor
just
enough
to
prevent
the
entrance
of
water
.
Consideration
should
be
given
to
the
location
of
components
in
the
switchboard
and
space
should
be
allowed
for
swinging
cables
after
they
leave
the
conduit
.
The
lowest
live
metal
part
in
the
switchboard
will
be
approximately
8
"
minimum
above
the
bottom
of
the
switchboard
(
not
including
floor
sills
)
.
It
should
be
noted
that
the
switchboard
must
be
lifted
over
the
conduit
stubs
.
The
conduits
should
terminate
at
the
switchboard
with
the
appropriate
conduit
connectors
.
Conduits
may
require
grounding
or
electrical
connection
to
the
switch
-
board
enclosure
.
If
1
%
"
z
FIGURE
10
Non
-
walk
in
type
switchboard
—
outdoor
construction
.
FRONT
\
FIGURE
11
Walk
-
in
type
switchboard
—
outdoor
construction
.
9
Courtesy of NationalSwitchgear.com

Installing
The
AV
-
Line
Switchboard
3
-
PHASE
4
WIRE
SUPPLY
N
G
.
V
1
2
3
©
L
©
SERVICE
ENTRANCE
MAIN
BREAKER
))
)
FIELD
CONNECTIONS
AND
TESTING
OF
GROUND
-
FAULT
PROTECTION
SYSTEMS
(
7
)
In
the
service
-
entrance
section
,
the
neutral
conductor
shall
be
bonded
to
the
switchboard
ground
bus
by
a
“
main
bonding
jumper
”
(
ground
strap
)
(
NEC
250
-
5
;
UL
-
891
,
Para
.
23.8
and
23.12
)
.
This
grounding
point
on
the
neutral
conductor
shall
be
located
on
the
supply
side
of
any
ground
-
fault
sensors
in
-
volving
the
neutral
conductor
(
UL
-
891
,
Para
.
15.4
and
15.5
)
.
Grounding
connections
shall
not
be
made
to
the
neutral
con
-
ductor
on
the
load
side
of
the
service
disconnecting
means
(
NEC
250
-
23
a
;
UL
-
891
,
Para
.
15.4
)
.
(
?
)
On
load
feeders
,
run
all
phase
conductors
(
and
neutral
if
used
)
through
the
sensor
window
(
s
)
,
with
all
in
the
same
direction
with
respect
to
sensor
polarity
.
(
J
)
Do
not
run
equipment
ground
conductors
through
ground
-
fault
sensors
.
Connect
them
directly
to
the
switchboard
ground
bus
(
not
to
the
neutral
bus
)
(
UL
-
891
,
Para
.
38.39
)
.
(
71
)
Connect
the
service
grounding
electrode
(
water
pipe
,
etc
.
)
to
the
lug
provided
on
the
switchboard
ground
bus
for
this
pur
-
pose
(
NEC
250
-
26
c
;
UL
-
891
,
Para
.
23.6
)
.
(
J
)
Whenever
a
service
is
derived
from
a
grounded
neutral
sup
-
ply
,
the
grounded
neutral
conductor
must
be
brought
into
the
service
-
entrance
equipment
,
even
if
the
grounded
conductor
is
not
needed
for
the
load
supplied
by
the
service
(
NEC
250
-
23
b
)
.
This
is
required
to
provide
a
low
-
impedance
ground
-
fault
current
return
path
to
the
neutral
to
assure
operation
of
the
overcurrent
device
,
for
safety
to
personnel
and
property
.
(
&
)
Refer
to
GEI
-
48907
for
instructions
for
conducting
perfor
-
mance
tests
of
new
installations
of
ground
-
fault
protection
systems
,
as
required
by
NEC
230
-
95
(
c
)
.
4
WIRE
IGF
NEUTRAL
-
1
N
«
-
N
aus
-
o
-
&
;
T
)
)
)
)
)
)
FDR
¥
1
FDR
#
2
iE
-
yi
IGF
=
INTEGRAL
GROUND
FAULT
PROTECTION
3
WIRE
IGF
GHD
^
rr
8
US
©
y
V
'
'
t
1
2
3
'
'
©
'
i
'
V
V
2
3
.
N
vj
.
©
v
V
I
I
I
I
II
I
I
I
1
I
2
3
I
I
I
1
N
G
J
I
2
3
G
|
3
PHASE
—
3
WIRELOAD
~
~
|
|
3
-
PHASE
—
4
WIRE
LOAD
|
TYPICAL
SINGLE
-
SOURCE
GROUND
FAULT
PROTECTION
USING
INTEGRAL
GROUND
FAULT
TRIPS
FIGURE
13
FUSE
SELECTION
The
proper
fuses
for
each
circuit
should
be
selected
based
on
load
characteristics
(
see
Ambient
Temperatures
and
Circuit
Loading
)
and
available
short
-
circuit
current
at
the
line
terminals
of
the
switchboard
.
Select
a
fuse
for
which
the
rating
of
the
combination
fuse
and
switch
equals
or
exceeds
the
available
short
-
circuit
current
.
Removable
link
-
type
fuses
are
not
recommended
.
TESTING
AND
INSPECTION
After
the
equipment
has
been
installed
and
all
connections
made
,
it
should
be
tested
and
inspected
BEFORE
ENERGIZING
.
Although
the
equipment
and
devices
have
been
inspected
at
the
factory
,
a
final
field
test
should
be
made
to
be
certain
that
the
equipment
has
been
properly
installed
and
that
all
connections
are
correct
and
have
not
become
loose
in
transportation
.
It
is
recommended
that
the
switchboard
be
completely
wire
checked
,
and
all
bolts
and
terminals
double
checked
for
tightness
.
Check
all
Kirk
key
interlocking
schemes
to
insure
desired
performance
.
The
incoming
line
should
be
completely
de
-
energized
while
the
tests
are
in
progress
.
In
addition
to
these
mechanical
checks
the
switchboard
should
be
meggered
.
Meggering
should
be
performed
with
all
switchboard
devices
in
the
open
position
and
all
instrumentation
and
control
fuses
removed
.
A
megger
(
megohmmeter
)
developing
500
volts
should
be
used
.
As
a
guide
switchboards
tested
when
leaving
the
factory
have
shown
typical
minimum
values
of
100
megohms
.
Any
switchboards
job
tested
under
the
above
conditions
showing
values
considerably
below
this
should
be
inspected
for
possible
tracking
on
insulation
or
insulation
breakdown
.
All
scraps
of
wire
,
plaster
,
dust
and
other
foreign
material
must
be
removed
.
Vacuum
cleaning
is
the
recommended
method
of
removal
.
After
thorough
cleaning
and
inspection
,
if
the
megger
reading
is
still
low
,
it
may
still
be
safe
to
energize
the
equipment
.
When
restoring
flooded
or
wet
equipment
to
service
,
for
example
,
it
is
accepted
maintenance
prac
-
tice
to
require
a
minimum
of
one
megohm
before
energizing
.
Under
damp
or
humid
conditions
it
is
considered
good
practice
to
operate
the
equipment
at
lower
-
than
-
rated
voltage
for
a
short
time
,
if
possible
,
to
improve
the
low
megger
reading
.
Instructions
for
inspection
and
testing
of
low
voltage
power
circuit
\
breakers
are
given
in
the
applicable
individual
instruction
book
.
Direc
-
tions
for
testing
devices
such
as
relays
,
instruments
and
meters
are
given
in
the
instruction
book
furnished
for
each
device
.
Protective
relays
must
be
coordinated
with
other
relays
in
the
system
,
therefore
these
relays
are
to
be
set
by
the
purchaser
.
General
instructions
on
setting
the
relays
are
given
in
the
relay
instruction
books
.
3
-
PHASE
4
WIRE
SUPPLY
1
2
3
N
G
ALTERNATE
SENSOR
ARRANGEMENTS
I
t
2
3
N
I
ALTERNATE
SENSORS
FOR
MAIN
BREAKER
GFP
c
X
>
t
©
I
ZERO
SEQUENCE
GROUND
RETURN
SENSOR
)
)
SERVICE
ENTRANCE
MAIN
BREAKER
12
3
N
GFR
I
x
>
-
(
(
I
I
ZERO
-
SEQUENCE
OR
RESIDUAL
SENSOR
RESIDUAL
2
3
N
NEUTRAL
N
BUS
(
XXX
^
I
RESIDUAL
1
!
>
~
Epl
)
)
>
-
-
)
))
GFR
-
GROUND
FAULT
RELAY
FDR
01
GFR
FDR
02
GRD
c
sus
©
''
'
'
\
'
>
t
\
r
1
2
3
N
1
2
3
i
i
:
r
I
i
i
©©
L
1
1
1
1
2
3
N
G
I
I
I
I
I
1
2
3
G
I
I
I
I
|
3
PHASE
—
4
WIRE
LQAD
~~
|
|
3
PHASE
—
3
WIRE
LOAD
|
TYPICAL
SINGLE
-
SOURCE
GROUND
FAULT
PROTECTION
USING
GROUND
FAULT
RELAYS
FIGURE
12
10
Courtesy of NationalSwitchgear.com

GROUND
FAULT
PROTECTION
When
ground
fault
protection
is
furnished
,
it
is
important
that
all
field
connections
shall
be
made
correctly
so
that
the
ground
fault
protection
system
will
function
properly
.
Observe
the
following
rules
,
illustrated
in
Figs
.
12
,
13
.
ELECTRICAL
CLEARANCES
BOLTING
The
following
minimum
clearances
should
be
maintained
except
at
terminals
of
circuit
breakers
and
switches
:
AV
-
Line
switchboards
are
furnished
with
medium
carbon
steel
hardware
having
a
high
tensile
strength
.
V
4
"
to
Vs
"
bolts
have
a
tensile
strength
of
120
,
000
psi
,
and
W
to
5
/
s
"
bolts
have
a
strength
of
60
,
000
psi
.
Similar
hardware
should
be
used
for
any
additional
bolting
.
The
use
of
a
torque
wrench
is
recommended
to
assure
the
following
torques
.
These
torques
apply
to
alumi
-
num
or
copper
connections
.
When
torquing
bolts
the
following
values
are
nominal
:
0
-
125
V
126
-
250
V
251
-
600
V
Between
live
parts
of
opposite
polarity
:
Through
air
Over
surface
Between
live
parts
and
grounded
metal
through
air
or
over
surface
GROUNDING
Where
required
,
the
ground
bus
is
bolted
to
the
uprights
of
the
rear
frame
structure
.
It
is
arranged
so
that
connections
to
the
station
ground
can
be
made
in
any
unit
.
A
ground
lug
is
included
in
each
complete
equipment
for
tying
the
switchboard
to
the
station
ground
.
IT
IS
VERY
IMPORTANT
THAT
THE
EQUIPMENT
BE
ADEQUATELY
GROUNDED
,
TO
INSURE
THAT
ALL
PARTS
OF
THE
EQUIPMENT
,
OTHER
THAN
LIVE
PARTS
,
ARE
AT
GROUND
POTENTIAL
.
Ground
sensor
relays
are
recommended
for
protection
of
the
switchboard
.
V
2
"
3
/
4
"
1
"
2
"
3
/
4
"
11
/
4
"
8
-
10
lb
.
ft
.
16
-
19
lb
.
ft
.
23
-
27
lb
.
ft
.
35
-
40
lb
.
ft
.
45
-
50
lb
.
ft
.
1
/
4
"
—
20
bolts
5
/
i
6
w
—
18
bolts
—
16
bolts
1
/
2
"
—
13
bolts
s
/
s
"
—
16
bolts
Flat
washers
and
spring
washers
should
be
used
for
all
connec
-
tions
.
Washers
should
not
be
included
under
the
heads
of
car
-
riage
bolts
.
V
2
"
V
2
"
1
"
Switchboard
Maintenance
CAUTION
!
De
-
energize
this
equipment
before
performing
any
work
.
A
periodic
maintenance
schedule
should
be
established
to
ob
-
tain
the
best
service
from
the
switchboard
.
An
annual
check
and
overall
maintenance
procedure
for
the
switchboard
devices
and
all
connections
,
should
be
followed
as
a
minimum
requirement
.
Equipment
subject
to
highly
repetitive
operation
may
require
more
frequent
maintenance
.
A
permanent
record
of
all
maintenance
work
should
be
kept
.
The
record
should
include
a
list
of
periodic
checks
and
tests
made
,
the
date
they
were
made
,
the
condition
of
the
equipment
,
and
any
repairs
or
adjustments
that
were
performed
.
Maintenance
employees
should
follow
all
recognized
safety
practices
,
such
as
those
contained
in
the
National
Electrical
Code
,
OSHA
and
in
company
or
other
safety
regulations
during
maintenance
.
For
specific
information
regarding
the
maintenance
of
devices
,
such
as
circuit
breakers
,
relays
,
meters
,
etc
.
,
refer
to
the
sepa
-
rate
instruction
book
furnished
for
each
device
.
1
.
Periodically
inspect
switchboard
,
while
under
load
to
deter
-
mine
if
there
is
any
indication
of
overheating
.
If
overheating
or
any
other
unsatisfactory
condition
is
found
,
completely
de
-
energize
switchboard
and
investigate
.
Particularly
look
for
loose
bolts
and
connections
,
or
overloading
.
Remove
any
accumulation
of
dirt
or
other
foreign
matter
in
enclosure
.
Do
not
touch
live
parts
while
switchboard
is
energized
.
2
.
Plated
parts
may
become
dark
over
a
period
of
time
due
to
oxidation
.
Do
NOT
remove
this
discoloration
,
as
it
will
reduce
the
thickness
of
the
plating
.
3
.
Retighten
lugs
and
joints
to
eliminate
possible
heating
points
.
Transmittal
of
vibration
through
building
structure
and
conduit
to
switchboard
may
loosen
lugs
and
joints
.
Turning
load
off
and
on
causes
expansion
and
contraction
between
lug
and
cable
tending
to
loosen
lug
.
4
.
Do
not
open
sealed
breaker
or
trip
units
as
calibration
may
be
disturbed
.
Return
to
factory
for
any
replacement
.
AMBIENT
TEMPERATURES
AND
CIRCUIT
LOADING
Switchboards
are
designed
for
installation
where
average
ambi
-
ent
temperature
will
not
exceed
40
°
C
(
104
°
F
)
.
For
higher
tem
-
peratures
,
derating
may
be
required
.
The
conductor
temperatures
within
the
enclosure
may
be
as
high
as
80
°
C
(
176
°
F
)
.
Some
parts
of
breakers
,
switches
and
fuses
may
run
hotter
.
In
accordance
with
NEC
Art
.
384
-
16
(
c
)
it
is
recommended
that
thermal
-
magnetic
molded
-
case
breakers
in
switchboards
not
be
loaded
in
excess
of
80
%
of
rating
where
load
will
continue
for
three
hours
or
more
,
even
with
ambient
-
compensated
breakers
.
SHORT
CIRCUITS
Normally
,
the
overcurrent
protective
device
on
the
circuit
will
prevent
any
electrical
damage
except
at
the
actual
point
of
short
-
circuit
.
A
thorough
inspection
of
the
entire
system
after
any
large
fault
current
should
be
made
to
insure
that
there
has
been
no
mechanical
damage
to
conductors
,
insulation
or
equipment
.
In
addition
,
the
individual
overcurrent
protective
device
or
de
-
vices
which
performed
the
short
-
circuit
interruption
must
be
in
-
spected
for
possible
arcing
damage
to
contacts
,
arc
chutes
and
/
or
insulation
.
Do
not
open
sealed
devices
such
as
breaker
trip
units
or
150
A
frame
breakers
.
If
there
is
any
possibility
that
sealed
units
may
have
been
damaged
,
they
should
be
replaced
.
For
additional
details
on
the
particular
device
involved
,
refer
to
the
applicable
individual
instruction
book
.
ARCING
DAMAGE
TO
INSULATION
Some
organic
insulating
materials
carbonize
when
subjected
to
the
heat
of
an
electrical
arc
and
lose
their
insulating
qualities
.
Any
insulation
found
to
be
carbon
-
tracked
must
be
replaced
before
applying
power
.
(
Continued
on
Page
12
)
11
Courtesy of NationalSwitchgear.com

Switchboard
Maintenance
WATER
-
SOAKED
EQUIPMENT
1
.
Completely
de
-
energize
switchboard
.
2
.
Carefully
clean
and
dry
all
parts
of
the
switchboard
.
When
using
heaters
,
do
not
exceed
180
degrees
F
.
3
.
Replace
all
fuses
.
4
.
Individual
devices
should
be
inspected
for
the
possible
en
-
trance
of
water
,
dirt
or
foreign
matter
.
5
.
Do
not
open
sealed
devices
such
as
breaker
trip
units
or
150
A
.
frame
breaker
.
Replace
them
.
6
.
Prior
to
re
-
energizing
the
switchboard
it
should
be
meggered
.
Refer
to
testing
and
inspection
section
on
page
10
.
7
.
If
assistance
or
guidance
is
required
contact
your
local
Gen
-
eral
Electric
service
engineer
.
General
Electric
Service
Shops
have
facilities
for
reconditioning
.
SPARE
PARTS
A
spare
parts
stock
for
the
components
of
the
AV
-
Line
Switch
-
board
,
such
as
bus
,
insulators
,
etc
.
is
not
recommended
.
When
components
need
to
be
reordered
,
please
refer
to
the
nameplate
marking
,
shop
drawing
number
,
and
order
by
description
.
A
spare
parts
stock
of
devices
such
as
circuit
breakers
,
meters
,
switches
,
etc
.
will
vary
due
to
the
variety
of
installations
.
Your
General
Electric
Sales
Engineer
will
be
glad
to
assist
you
in
the
proper
selection
for
a
device
stock
list
.
For
further
information
call
or
write
your
local
General
Electric
Sales
Office
o r
.
.
.
Distribution
Equipment
Division
41
Woodford
Avenue
Plainville
,
CT
06062
is
V
ELECTRIC
GENERAL
GEH
2621
A
4
/
81
10
M
Courtesy of NationalSwitchgear.com
Table of contents
Other GE Switch manuals
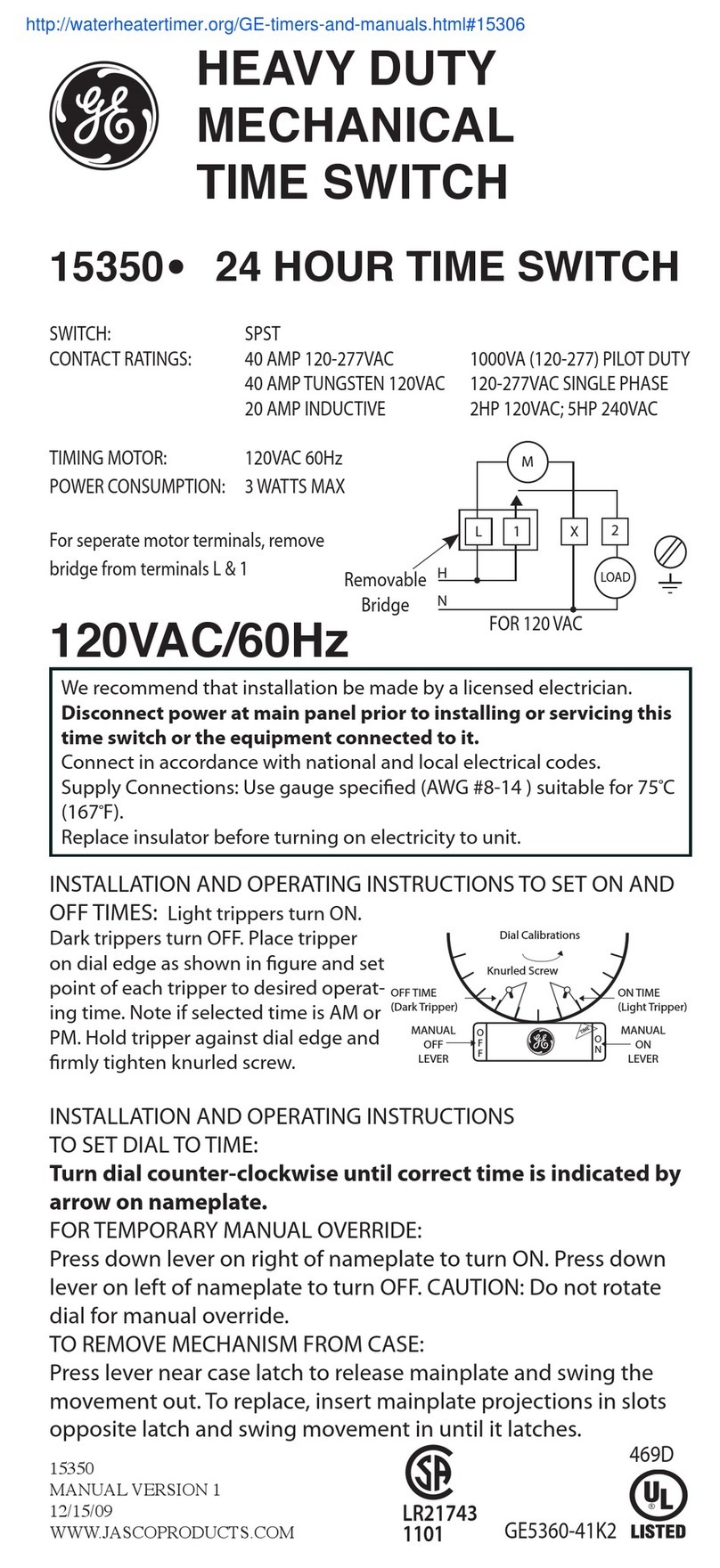
GE
GE 15350 User manual
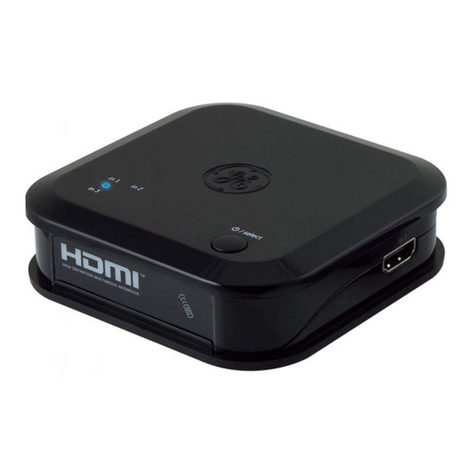
GE
GE 3-Device HDMI Switch User manual
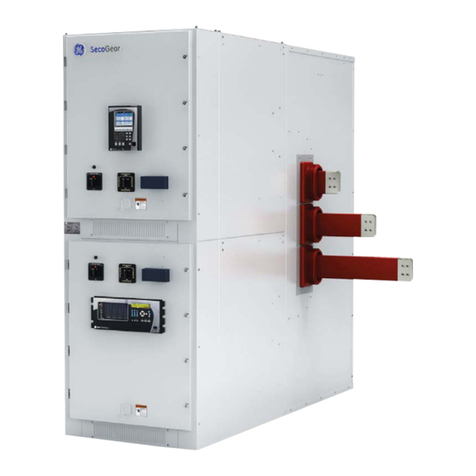
GE
GE SecoGear User guide
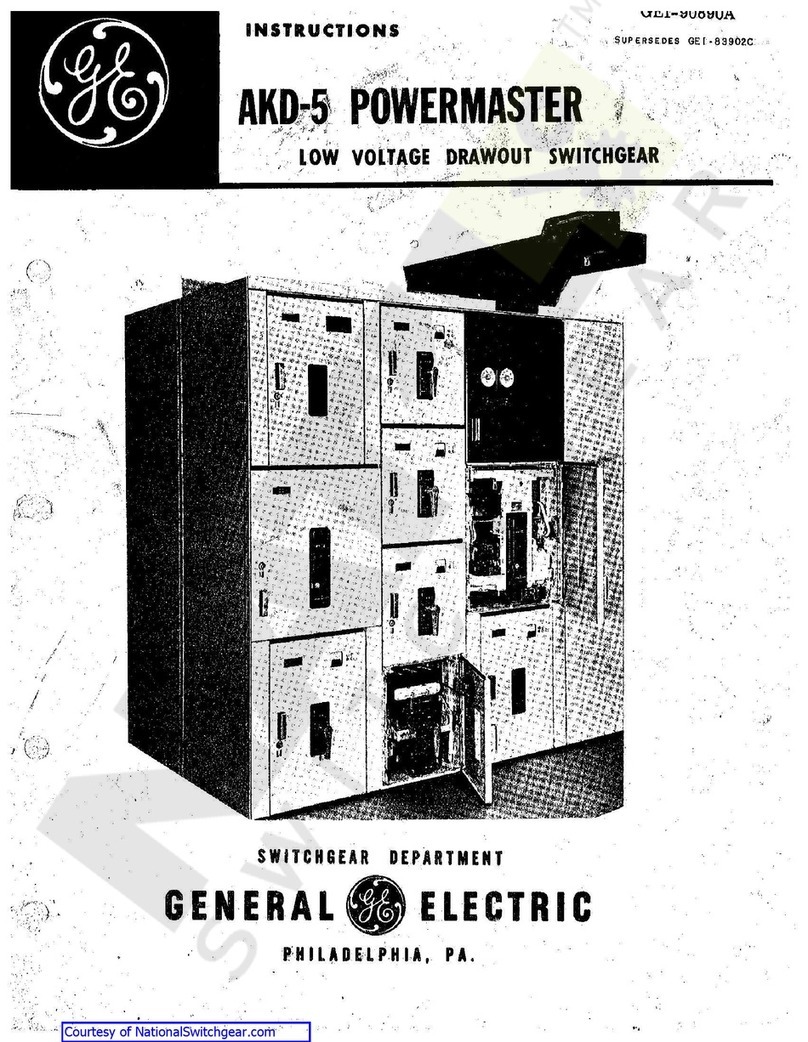
GE
GE POWERMASTER AKD-5 User manual

GE
GE ZTS Series Installation guide
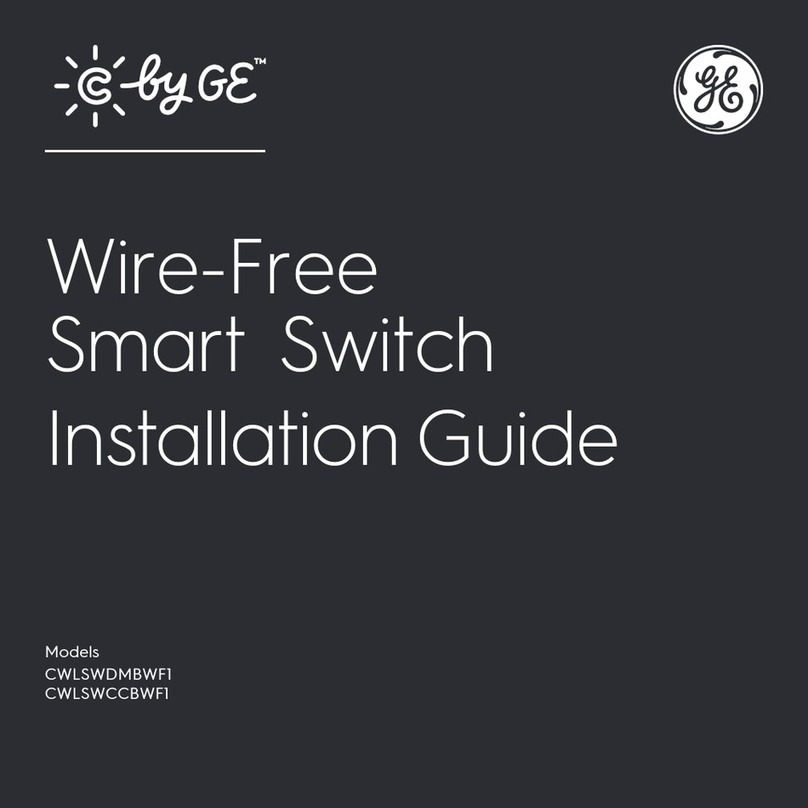
GE
GE CWLSWDMBWF1 User manual

GE
GE Digital Energy STS-230-25-2-RM User manual
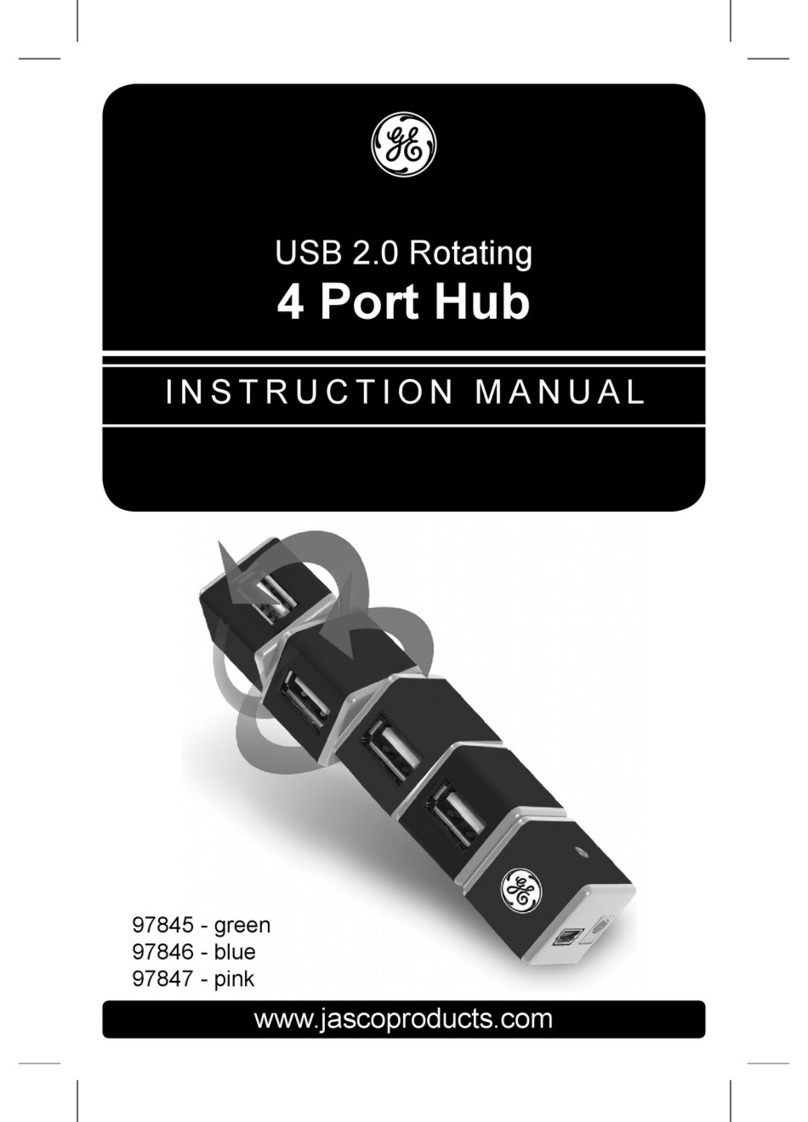
GE
GE 97845 User manual
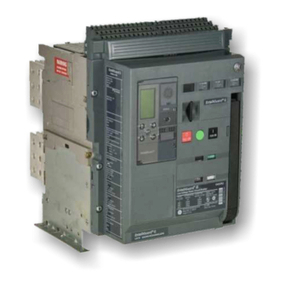
GE
GE EntelliGuard G Technical Document
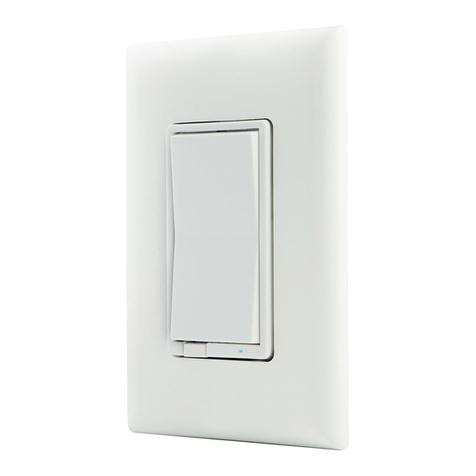
GE
GE In-wall WirelessSmart Switch User manual
Popular Switch manuals by other brands
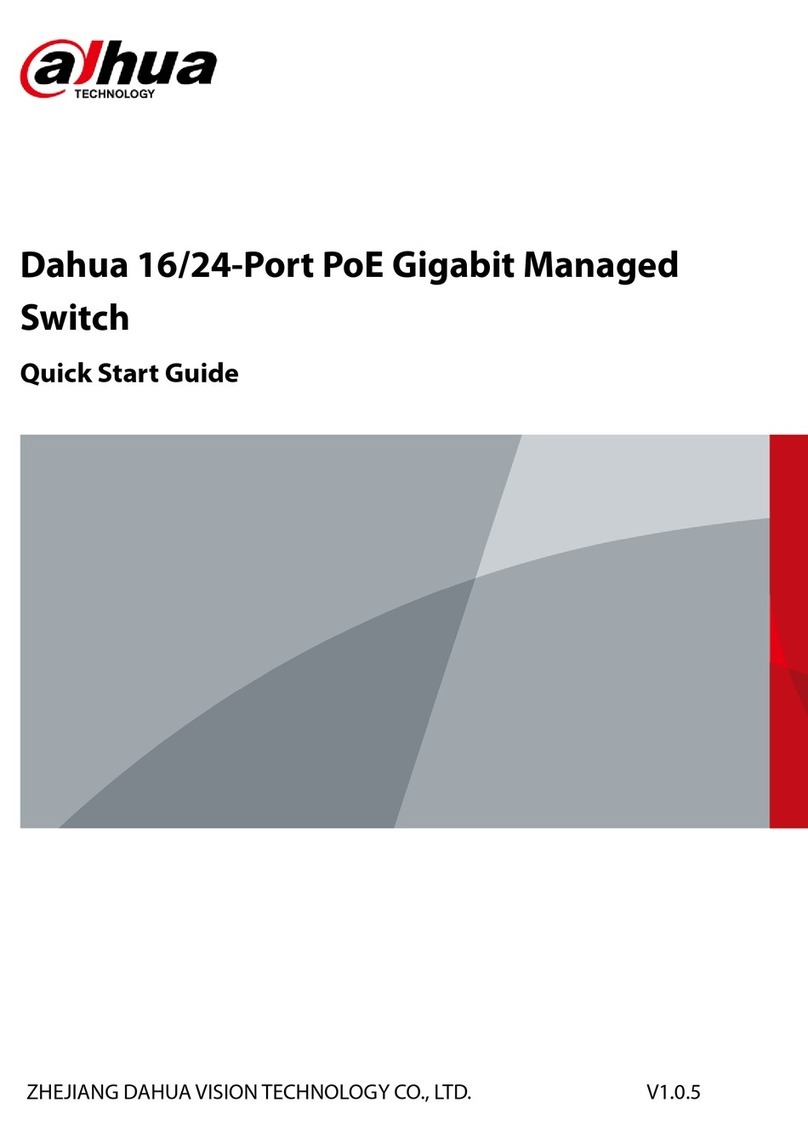
Dahua
Dahua DH-PFS4218-16GT-190 quick start guide
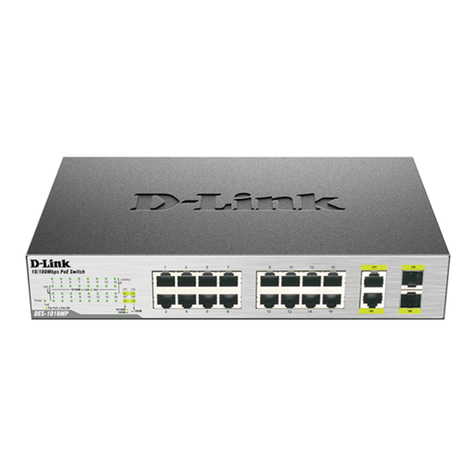
D-Link
D-Link DES-1018MP Quick installation guide
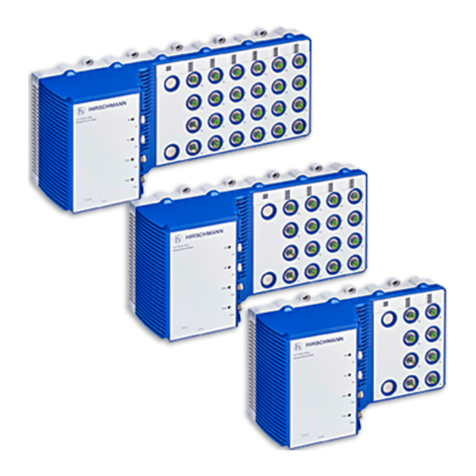
Belden
Belden HIRSCHMANN OCTOPUS OS3 user manual
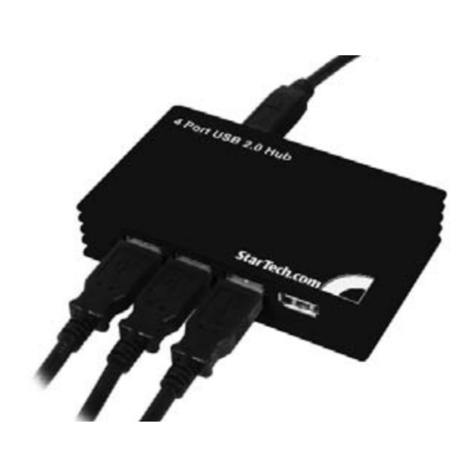
StarTech.com
StarTech.com ST7202USBGB instruction manual
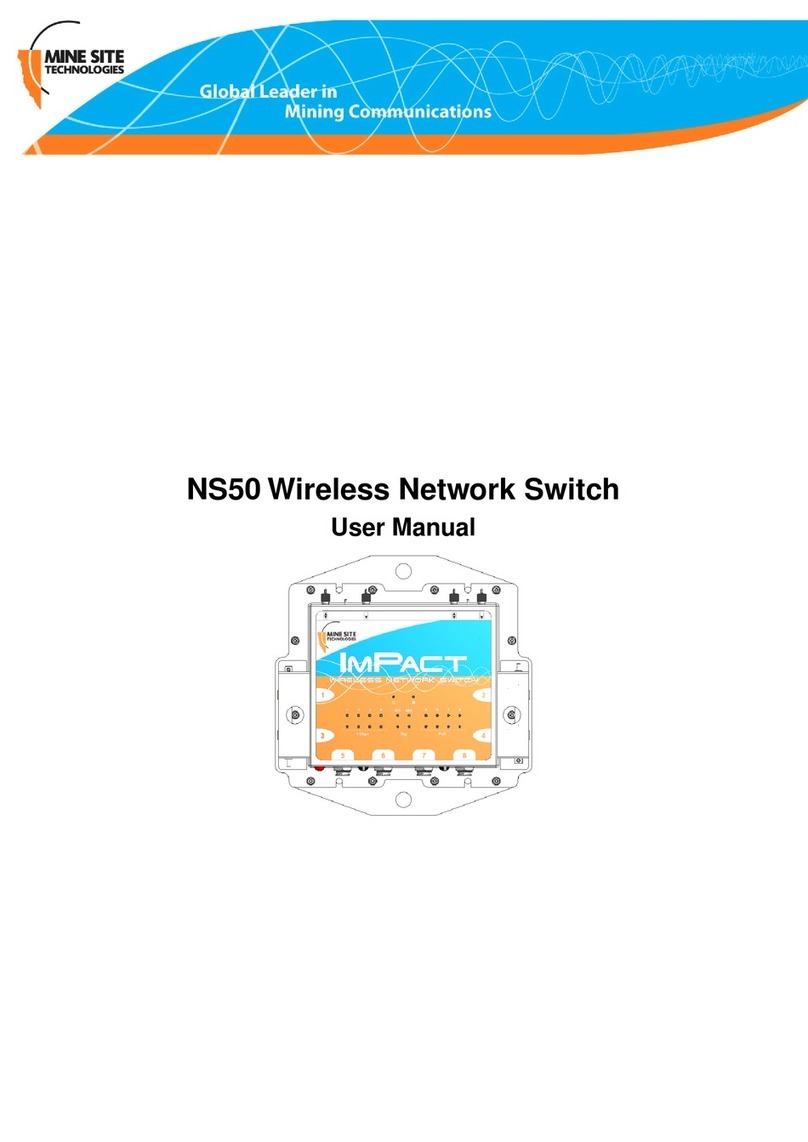
Mine Site Technologies
Mine Site Technologies NS50 user manual

Ubiquiti
Ubiquiti UniFi USW-Industral Quck Start Guide