GEA VARIVENT A Quick guide

Translation of the Original Operating Instructions
VARIVENT®
Control Valve A
Edition 2016-06-07
English

2
Operating Instructions · Control Valve A
Edition 2016-06-07
Product Control Valve A
Document Translation of the Original Operating Instructions
Edition 2016-06-07
English
Manufacturer GEA Tuchenhagen GmbH
Am Industriepark 2-10
D-21514 Büchen
Phone:+49 4155 49-0
Fax: +49 4155 49-2423
Mail: sales.geatuchenhage[email protected]
Web: http://www.tuchenhagen.com
These Operating Instructions are the English translation of the original operating instruc-
tions in the sense of the EU Machinery Directive. This document is protected by copy-
right. All rights reserved. The document may not, in whole or in part, be copied,
reproduced, translated or reduced to an electronic medium of machine-readable form
without the express permission of GEA Tuchenhagen GmbH.
Wordmarks The designation VARIVENT®is a protected trademark of GEA Tuchenhagen GmbH.

3
Table of Contents
Table of Contents
Notes for the Reader ...................................................................................................................................... 6
Binding Character of These Operating Instructions ......................................................................................... 6
Notes on the Illustrations.................................................................................................................................. 6
Symbols and Highlighting................................................................................................................................. 7
Abbreviations and Terms ................................................................................................................................. 8
Safety............................................................................................................................................................. 10
Safety Note..................................................................................................................................................... 10
Operator's Duties............................................................................................................................................ 10
Qualification of Staff ....................................................................................................................................... 11
Supplementary Regulations ........................................................................................................................... 12
Instructions for the Safe Operation................................................................................................................. 13
•General Principles ...................................................................................................................................... 13
•Installation .................................................................................................................................................. 13
•Commissioning/Setup Mode ...................................................................................................................... 14
•Setting into Operation................................................................................................................................. 14
•Operation.................................................................................................................................................... 14
•Shutting Down ............................................................................................................................................ 15
•Maintenance and Repair ............................................................................................................................ 15
•Disassembly ............................................................................................................................................... 16
•Environmental Protection ........................................................................................................................... 16
•Electrical Equipment................................................................................................................................... 16
Signage .......................................................................................................................................................... 17
Residual Risk ................................................................................................................................................. 18
•Hazard Areas ............................................................................................................................................. 18
•Residual Dangers....................................................................................................................................... 19
•Declaration of Conformity........................................................................................................................... 20
Transport and Storage................................................................................................................................. 21
Scope of Supply ............................................................................................................................................. 21
Transport ........................................................................................................................................................ 21
Storage........................................................................................................................................................... 21
Intended Purpose ......................................................................................................................................... 22
Designated Use .............................................................................................................................................. 22
Requirements for the Operation ..................................................................................................................... 22
Pressure Equipment Directive........................................................................................................................ 22
ATEX Directive ............................................................................................................................................... 22
Improper Operating Conditions ...................................................................................................................... 23
Conversion Work............................................................................................................................................ 23
Design and Function.................................................................................................................................... 24
Design ............................................................................................................................................................ 24
Function.......................................................................................................................................................... 25
•Spring-to-close actuator (Z)........................................................................................................................ 25
•Spring-to-open actuator (A)........................................................................................................................ 25
Installation and Commissioning ................................................................................................................. 26
Notes on Installation....................................................................................................................................... 26
Fitting the Valve with Detachable Pipe Connection Elements........................................................................ 26

Table of Contents
4
Operating Instructions · Control Valve A
Edition 2016-06-07
Control Valve with Welding Ends ....................................................................................................................27
Pneumatic Connections ..................................................................................................................................29
Electrical Connections.....................................................................................................................................30
Commissioning................................................................................................................................................31
•Checks Prior to Commissioning..................................................................................................................31
•Testing the Valve Function Without Product...............................................................................................31
•Valve Stroke................................................................................................................................................32
•Tests During the Product Run.....................................................................................................................32
•Operation ....................................................................................................................................................32
Cleaning and Passivation.............................................................................................................................33
Cleaning..........................................................................................................................................................33
Cleaning Process Examples ...........................................................................................................................33
•Typical Cleaning Parameters in Dairy Operations ......................................................................................33
•Typical Cleaning Parameters in Breweries .................................................................................................33
•Cleaning Parameters ..................................................................................................................................34
•Passivation..................................................................................................................................................34
Malfunctions..................................................................................................................................................35
Maintenance ..................................................................................................................................................36
Inspections ......................................................................................................................................................36
•Product Contact Seals ................................................................................................................................36
•Pneumatic Connections ..............................................................................................................................36
•Electrical Connections ................................................................................................................................36
Maintenance Intervals.....................................................................................................................................37
Prior to Disassembly .......................................................................................................................................37
Disassembly....................................................................................................................................................38
Maintenance....................................................................................................................................................39
•Cleaning the Valve......................................................................................................................................39
•Replacing Seals ..........................................................................................................................................39
•Lubricating Seals and Threads ...................................................................................................................41
Assembly.........................................................................................................................................................42
Dismantling the Actuator Housing Cover ........................................................................................................43
Checking the Function ....................................................................................................................................43
•Setting the Stroke .......................................................................................................................................43
•Valve Stroke................................................................................................................................................44
Disposal ..........................................................................................................................................................44
•General Notes.............................................................................................................................................44
•Valve Actuator Disposal..............................................................................................................................44
Technical Data...............................................................................................................................................45
Type Plate .......................................................................................................................................................45
Technical Data ................................................................................................................................................46
Resistance of Sealing Materials......................................................................................................................47
Pipe Ends........................................................................................................................................................47
Tools ...............................................................................................................................................................48
Lubricants........................................................................................................................................................49
Weights ...........................................................................................................................................................49
Spare Parts Lists – Control Valves..............................................................................................................51
Control Valve A ...............................................................................................................................................51
Control Valve A...W.........................................................................................................................................53
Control Valve A...X..........................................................................................................................................55

Notes for the Reader
Notes on the Illustrations
6
Operating Instructions · Control Valve A
Edition 2016-06-07
Notes for the Reader
The present Operating Instructions are part of the user information for the valve. The
Operating Instructions contain all the information you need to transport, install, commis-
sion, operate and carry out maintenance for the valve.
Binding Character of These Operating Instructions
These Operating Instructions contain the manufacturer's instructions to the operator of
the valve and to all persons who work on or use the valve regarding the procedures to
follow.
Carefully read these Operating Instructions before starting any work on or using the
valve. Your personal safety and the safety of the valve can only be ensured if you act as
described in the Operating Instructions.
Store the Operating Instructions in such a way that they are accessible to the operator
and the operating staff during the entire life cycle of the valve. When the location is
changed or the valve is sold make sure you also provide the Operating Instructions.
Notes on the Illustrations
The illustrations in these Operating Instructions show the valve in a simplified form. The
actual design of the valve can differ from the illustration. For detailed views and dimen-
sions of the valve please refer to the design documents.

7
Notes for the Reader
Symbols and Highlighting
Symbols and Highlighting
In these Operating Instructions, important information is highlighted by symbols or
special formatting. The following examples illustrate the most important types of high-
lighting.
DANGER
Warning: Fatal Injuries.
Failure to observe the warning can result in serious damage to health, or even death.
The arrow identifies a precautionary measure you have to take to avoid the hazard.
EXPLOSION HAZARD
Warning: Explosions.
Failure to observe the warning can result in a severe explosion.
The arrow identifies a precautionary measure you have to take to avoid the hazard.
WARNING
Warning: Serious Injuries.
Failure to observe the warning can result in serious damage to health.
The arrow identifies a precautionary measure you have to take to avoid the hazard.
CAUTION
Warning: Injuries.
Failure to observe the warning can result in minor or moderate damage to health.
The arrow identifies a precautionary measure you have to take to avoid the hazard.

Notes for the Reader
Abbreviations and Terms
8
Operating Instructions · Control Valve A
Edition 2016-06-07
IMPORTANT NOTE
Warning: Damage to Property.
Failure to observe the warning can result in serious damage to the valve or in the vicinity
of the valve.
The arrow identifies a precautionary measure you have to take to avoid the hazard.
Carry out the following steps: = Start of a set of instructions.
1. First step in a sequence of operations.
2. Second step in a sequence of operations.
Result of the previous operation.
The operation is complete, the goal has been achieved.
NOTE
Further useful information.
Abbreviations and Terms
Abbreviation Explanation
BS British Standard
bar Unit of measurement of pressure [bar]
All pressure data expressed in [bar/psi] is assumed to be gauge pressure
[barg/psig] unless explicitly specified otherwise.
approx. approximately
°C Unit of measurement of temperature [degree Celsius]
dm3nUnit of measurement of volume [cubic decimetre]
Volume (litre) at standard temperature and pressure
DN DIN nominal width
DIN German standard issued by DIN (Deutsches Institut für Normung e.V,
German Institute for Standardization)
EN European Standard
EPDM Material designation
Short designation according to DIN/ISO 1629:
Ethylene Propylene Diene Rubber
°F Unit of measurement of temperature [degree Fahrenheit]
FKM Material designation, short designation according to DIN/ISO 1629:
Fluorine rubber
h Unit of measurement of time [hour]

9
Notes for the Reader
Abbreviations and Terms
HNBR Material designation
Short designation according to DIN/ISO 1629:
Hydrogenated Acrylonitrile Butadiene Rubber
IP Protection class
ISO International standard issued by the International Organization for Standardi-
zation
kg Unit of measurement of weight [kilogram]
kN Unit of measurement of force [kilonewton]
KVvalue Flow coefficient [m³/s]
1 KV= 0.86 x Cv
l Unit of measurement of volume [litre]
max. maximum
mm Unit of measurement of length [millimetre]
μm Unit of measurement of length [micrometre]
MMetric
Nm Unit of measurement of work [newton metre]
UNIT OF TORQUE 1 Nm = 0.737 lbft
Pound-Force (lb) + Feet (ft)
PA Polyamide
PE-LD Low-density polyethylene
psi Unit of measurement of pressure [psi]
All pressure data expressed in [bar/psi] is assumed to be gauge pressure
[barg/psig] unless explicitly specified otherwise.
PTFE Polytetrafluoroethylene
SET-UP Self-learning installation
During commissioning and maintenance, the SET-UP procedure carries out
all the necessary settings for the generation of messages.
a/f Indicates the size of spanners
width across flats
T.VIS Tuchenhagen Valve Information System
V AC Volt alternating current
V DC Volt direct current
W Unit of measurement of power [Watt]
TIG Welding method
Tungsten inert gas welding
Inch Unit of measurement of length in the Anglo-American language area
Inch OD Pipe dimension acc. to British standard
(BS), Outside Diameter
Inch IPS US pipe dimension
Iron Pipe Size
Abbreviation Explanation

Safety
Operator's Duties
10
Operating Instructions · Control Valve A
Edition 2016-06-07
Safety
Safety Note
The valve is operationally reliable. It was built according to state-of-the-art standards.
Nevertheless, the valve can pose dangers, especially if
•the valve is not used in accordance with its intended use,
•the valve is not used correctly,
•the valve is operated under impermissible operating conditions.
Operator's Duties
In your capacity as operator of the facility you bear a particular responsibility for the
proper and safe handling of the valve in your facility. Only use the valve when it is in
perfect condition to prevent danger to persons and property.
These Operating Instructions contain the information you and your staff need for the
safe and reliable operation during the entire service life of the valve. Be sure to read
these Operating Instructions carefully and ensure that the measures described here are
observed.
The operator's duty of care includes planning the necessary safety measures and moni-
toring that these measures are observed. The following principles apply:
•Only allow qualified staff to work on the valve.
•The operator must authorize the staff to carry out the relevant tasks.
•Working areas and the entire environment of the valve must be neat and clean.
•The staff must wear suitable work clothing and personal protective equipment. As
the operator of the facility make sure that work clothing and personal protective
equipment are used.
•Instruct the staff with regard to any properties of the product which might pose a
health risk and the preventative measures to be taken.
•Have a qualified first-aider on call during the operation, who can initiate the neces-
sary first-aid measures in case of an emergency.
•Clearly define processes, lines of authority and responsibilities associated with the
valve. Everybody must know what to do in case of an emergency. Instruct the staff
in this respect at regular intervals.
•The signs relating to the valve must always be complete and legible. Check, clean
and replace the signs as necessary at regular intervals.
NOTE
Carry out regular checks. This way you can ensure that these measures are actually
observed.

11
Safety
Qualification of Staff
Qualification of Staff
This section contains information about the qualifications that staff working on the valve
must have.
Operating and maintenance staff must
•have the necessary qualification to carry out their tasks,
•be instructed with regard to possible dangers,
•know and observe the safety instructions given in the documentation.
Only allow qualified electricians to carry out work on the electrical equipment or have a
qualified electrician supervise the work.
Only allow specially trained staff to carry out any work on explosion-protected equip-
ment. When working on explosion-protected equipment observe the standards DIN EN
60079-14 for gases and DIN EN 50281-1-2 for dusts.
The following minimum qualifications are required:
•Vocational training as a specialist who can work on the valve independently.
•Sufficient instruction to work on the valve under the supervision and direction of a
qualified specialist.
Each member of staff must meet the following requirements to be allowed to work on the
valve:
•Personal qualification for the relevant task.
•Sufficient professional qualification for the relevant task.
•Instructed with regard to the function of the valve.
•Instructed with regard to the operating sequences of the valve.
•Familiar with the safety devices and their function.
•Familiar with these Operating Instructions, especially with the safety instructions and
the information which is relevant for the task on hand.
•Familiar with the basic regulations with regard to occupational health and safety and
accident prevention.
For work to be carried out on the valve the following user groups are distinguished:
User groups
Staff Qualifications
Operating staff Adequate instruction and sound knowledge in the following areas:
•Function of the valve
•Valve operating sequences
•What to do in case of an emergency
•Lines of authority and responsibilities with respect to the task

Safety
Supplementary Regulations
12
Operating Instructions · Control Valve A
Edition 2016-06-07
Supplementary Regulations
In addition to the instructions in this documentation the following also has to be
observed:
•pertinent accident prevention regulations,
•generally accepted safety rules,
•national regulations applicable in the country of use,
•work and safety instructions applicable in the facility,
•installation and operating regulations for use in potentially explosive areas.
Maintenance staff Adequate instruction as well as sound knowledge of the design and function
of the valve.
Sound knowledge in the following areas:
•Mechanical equipment
•Electrical equipment
•Pneumatic system
Authorization with regard to safety engineering standards to carry out the
following tasks:
•Setting devices into operation
•Earthing of devices
•Marking of devices
The relevant certificates of qualification must be submitted before work can
be carried out on ATEX certified machines.
User groups (Cont.)
Staff Qualifications

13
Safety
Instructions for the Safe Operation
Instructions for the Safe Operation
Dangerous situations during the operation can be avoided by safety-conscious and
proactive behaviour of the staff.
General Principles
To ensure the safe operation of the valve the following principles apply:
•The Operating Instructions must be kept ready to hand at the valve's place of use.
They must be complete and in clearly legible form.
•Only use the valve for its intended use.
•The valve must be functional and in good working order. Check the condition of the
valve before starting work and at regular intervals.
•Wear tight-fitting work clothing for all work on the valve.
•Ensure that nobody can get hurt on the parts of the valve.
•Immediately report any faults or noticeable changes on the valve to the person
responsible.
•Observe the accident prevention regulations and all local regulations.
Installation
For installation, the following principles apply:
•Only properly qualified staff is allowed to install, assemble and set the valve into
operation.
•Ensure that adequate working and traffic areas are available at the place of installa-
tion.
•Observe the maximum load-bearing capacity of the installation surface.
•Observe the transport instructions and markings on the part(s) to be transported.
•Remove any nails protruding from transport crates immediately after opening the
crate.
•Under no circumstances should anyone stand under a suspended load.
•During assembly, the valve safety devices might not be working effectively.
•Reliably secure machine parts which have already been connected against inadvert-
ently being switched on.

Safety
Instructions for the Safe Operation
14
Operating Instructions · Control Valve A
Edition 2016-06-07
Commissioning/Setup Mode
For commissioning, the following principles apply:
•Take protective measures against dangerous contact voltages in accordance with
pertinent regulations.
•The valve must be completely assembled and correctly adjusted. All screw connec-
tions must be securely tightened. All electrical cables must be installed correctly.
•Reliably secure machine parts which have already been connected against inadvert-
ently being switched on.
•Relubricate all lubricating points.
•Make sure lubricants are used properly.
•After conversion of the valve, residual risks must be reassessed.
Setting into Operation
For setting into operation, the following principles apply:
•Only allow properly qualified staff to set the valve into operation.
•Establish all connections correctly.
•The safety devices for the valve must be complete, fully functional and in perfect
condition. Check the function before starting any work.
•When the valve is switched on, the danger zones must be free.
•Remove any liquids that have escaped without leaving residues.
Operation
For operation, the following principles apply:
•Monitor the valve during the operation.
•Safety devices must not be changed, removed or taken out of service. Check all
safety devices at regular intervals.
•All guards and hoods must be fitted as intended.
•The place of installation of the valve must be adequately ventilated at all times.
•Structural alterations of the valve are not permitted. Immediately report any changes
on the valve to the person responsible.
•Always keep danger zones clear. Do not leave any objects in the danger zone. Only
allow persons to enter the danger zone when the machine is de-energized.
•Regularly check that all emergency stop devices are working correctly.

15
Safety
Instructions for the Safe Operation
Shutting Down
For shutting down, the following principles apply:
•Switch off the compressed air.
•Switch off the valve via the main switch.
•Padlock the main switch (if fitted) in the off position to prevent it from being switched
back on. The key to the padlock must be deposited with the person responsible until
the machine is restarted.
•For longer periods of standstill, observe the storage conditions, see Storage
(page 21).
Maintenance and Repair
Before starting any maintenance and repair work on the electrical devices of the valve,
carry out the following steps in accordance with the "5 safety rules":
•Isolate from the power supply
•Take appropriate measures to prevent switch on
•Test absence of voltage
•Earthing and short-circuiting
•Cover or safeguard any adjacent live parts.
For maintenance and repair, the following principles apply:
•Observe the intervals specified in the maintenance schedule.
•Only allow qualified staff to carry out maintenance or repair work on the valve.
•Before starting any maintenance or repair work, the valve must be switched off and
secured against being switched back on. Work may only be started once any
residual energy has been discharged.
•Block access for unauthorized persons. Put up notice signs which draw attention to
the maintenance or repair work going on.
•Do not climb on the valve. Use suitable access aids and working platforms.
•Wear suitable protective clothing.
•Only use suitable and undamaged tools to carry out maintenance work.
•When replacing parts only use approved, fully functional load lifting devices and
lifting accessories which are suitable for the intended purpose.
•Before setting the unit back into operation refit all safety devices as originally
provided in the factory. Then check that all safety devices are working correctly.
•Make sure lubricants are used properly.
•Check pipes are firmly secured, also check for leaks and damage.
•Check that all emergency stop devices are working correctly.

Safety
Instructions for the Safe Operation
16
Operating Instructions · Control Valve A
Edition 2016-06-07
Disassembly
For disassembly, the following principles apply:
•Only allow qualified staff to disassemble the valve.
•Before starting disassembly, the valve must be switched off and secured against
being switched back on. Work may only be started once any residual energy has
been discharged.
•Disconnect all power and utility lines.
•Markings, e.g. on lines, must not be removed.
•Do not climb on the valve. Use suitable access aids and working platforms.
•Mark the lines (if unmarked) prior to disassembly to ensure they are not confused
when re-assembling.
•Protect open line ends with blind plugs against ingress of dirt.
•Pack sensitive parts separately.
•For longer periods of standstill, observe the storage conditions, see Storage
(page 21).
Environmental Protection
Harm to the environment can be avoided by safety-conscious and proactive behaviour
of the staff.
For environmental protection the following principles apply:
•Substances harmful to the environment must not be discharged into the ground or
the sewage system.
•Always observe the pertinent regulations relating to waste avoidance, disposal and
utilization.
•Substances harmful to the environment must be collected and stored in suitable
containers. Clearly mark the containers.
•Dispose of lubricants as hazardous waste.
Electrical Equipment
For all work on electrical equipment, the following principles apply:
•Access to electrical equipment should only be allowed to qualified electricians.
Always keep unattended switch cabinets locked.
•Modifications of the control system can affect the safe and reliable operation. Modifi-
cations are only permitted with the express permission of the manufacturer.
•After completion of all work, check that the protective devices are fully functional.

17
Safety
Signage
Signage
Dangerous points on the valve are indicated by warning signs, prohibition signs and
mandatory signs.
The signs and notes on the valve must always be legible. Any illegible signs must be
replaced immediately.
Signs on the valve
Sign Meaning
General hazard warning
Warning Crushing
Explosive atmosphere hazard warning

Safety
Residual Risk
18
Operating Instructions · Control Valve A
Edition 2016-06-07
Residual Risk
Hazard Areas
Please observe the following notes:
•In the event of malfunctions, shut down the valve (disconnect from the power and air
supply) and secure it against being used.
•When the valve is switching, never reach into the valve housing (391), the lantern
(9) or into the valve inlet X (on pneumatic actuators). Fingers can be crushed or cut
off.
•When releasing the grooved cap nut (252) of the non-actuated valve (spring-to-close
version) there is a risk of the bellows and the round thread of the grooved cap nut
being damaged. Before releasing the grooved cap nut (252) therefore relieve the
spring tension by pressurizing the actuator with compressed air. The valve is
opened.
•The housing sockets have very sharp edges. When transporting and assembling the
valve therefore be sure to wear suitable protective gloves.
•Before starting any service, maintenance or repair work, disconnect the valve from
the power supply and secure it against inadvertently being switched back on again.
•Only allow a qualified electrician to carry out any work on the electrical power
supply.
•Check the electrical equipment of the valve at regular intervals. Immediately remedy
loose connections and molten cables.
•If work on live parts cannot be avoided, call in a second person, who can operate
the main switch in case of an emergency.

19
Safety
Residual Risk
Residual Dangers
Dangerous situations can be avoided by safety-conscious and proactive behaviour of
the staff and by wearing personal protective equipment.
Residual dangers on the valve and measures
Danger Cause Measure
Danger to life Inadvertent switch-on of the
valve Effectively disconnect all components, effectively prevent switch-
on.
Electric power Observe the following safety rules:
1Isolate from the power supply.
2Take appropriate measures to prevent switch on.
3Test absence of voltage.
4Earthing and short-circuiting.
5Cover or safeguard any adjacent live parts.
Spring tension in the actuator Danger to life caused by compression spring in the actuator. Do not
open actuators but return them to GEA Tuchenhagen for proper
disposal.
Danger of injury Danger presented by moving
or sharp-edged parts The operator must exercise caution and prudence.
For all work:
•Wear suitable work clothing.
•Never operate the machine if the cover panels are not correctly
fitted.
•Never open the cover panels during the operation.
•Never reach into openings.
As a precautionary measure, wear personal protective equipment in
the vicinity of the valve:
•Protective gloves
•Safety shoes
Environmental
damage Operating materials with prop-
erties which are harmful to the
environment
For all work:
•Collect lubricants in suitable containers.
•Dispose of lubricants in accordance with the pertinent regula-
tions.

Safety
Residual Risk
20
Operating Instructions · Control Valve A
Edition 2016-06-07
Declaration of Conformity
Declaration of Conformity
in accordance with the EC Machinery Directive 2006/42/EC
We hereby declare that the machine designated as follows, based on its design and
type as well as in the version brought by us to market, complies with the basic safety
and health protection requirements of the EU- machine directive.
This declaration will become invalid if any alterations are made to the machine which
have not been agreed with us.
Authorised representative for compilation Authorised representative - CE
of the technical documentation documentation
GEA Tuchenhagen GmbH
At Industriepark 2-10
21514 Büchen
Büchen, 16/02/2015
Franz Bürmann i.V. Matthias Südel
Managing Director Team Leader Product Development
Designation of the machine: Valve with drive
Machine type: VARIVENT®
Relevant EU directives 2006/42/EC
Applicable harmonized standards: DIN EN ISO 12100
Table of contents
Other GEA Control Unit manuals
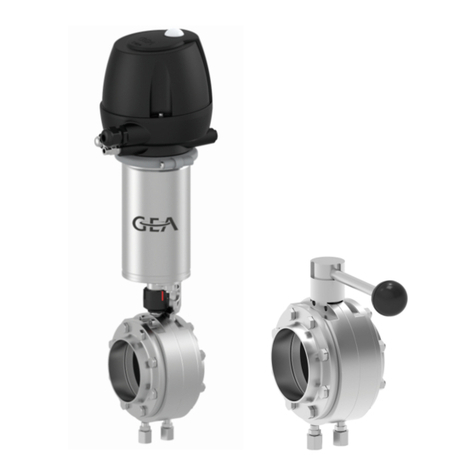
GEA
GEA ECOspace User manual
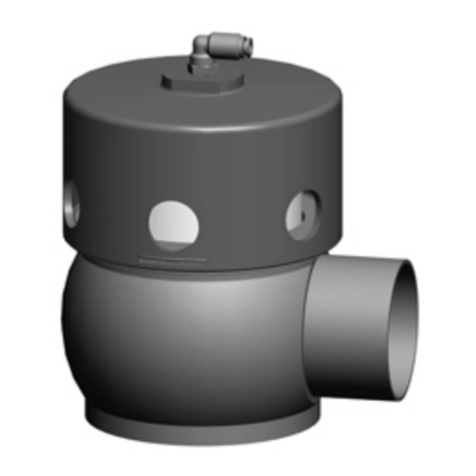
GEA
GEA DHV User manual
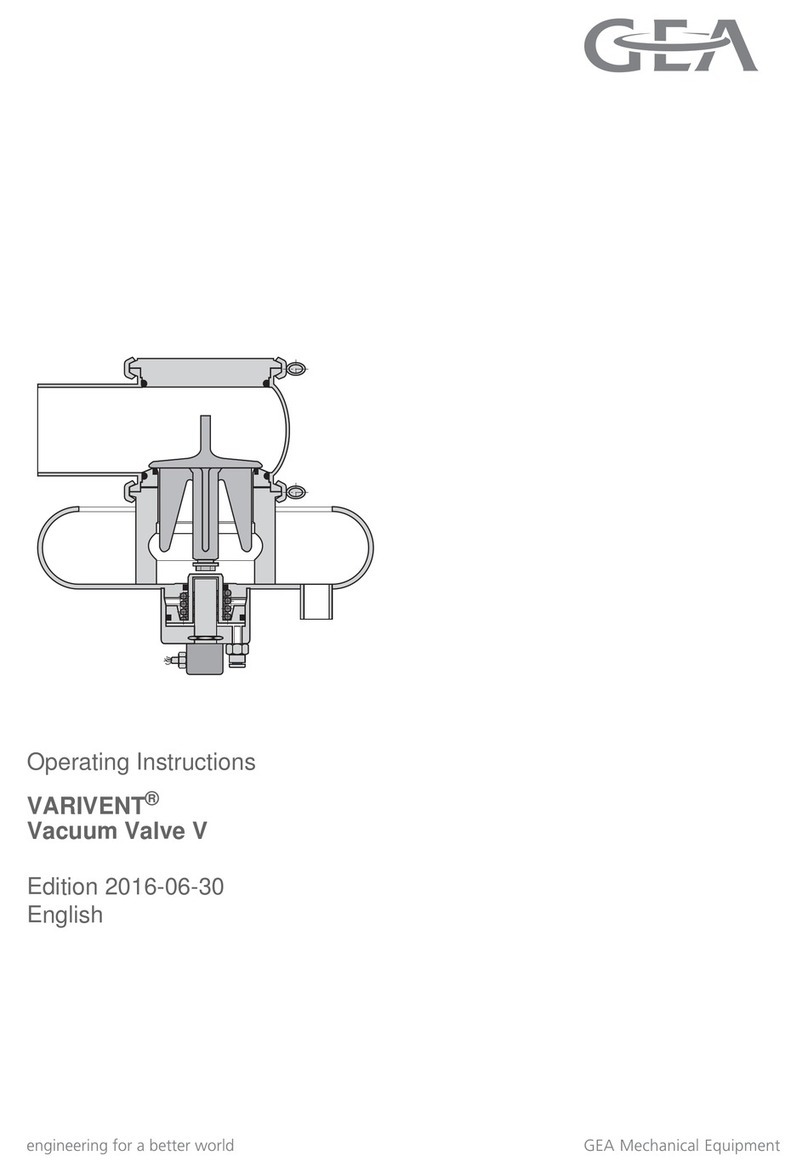
GEA
GEA VARIVENT Vacuum Valve V User manual
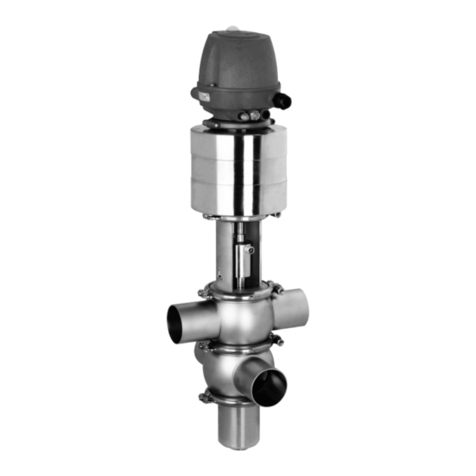
GEA
GEA VARIVENT DN 25 User manual
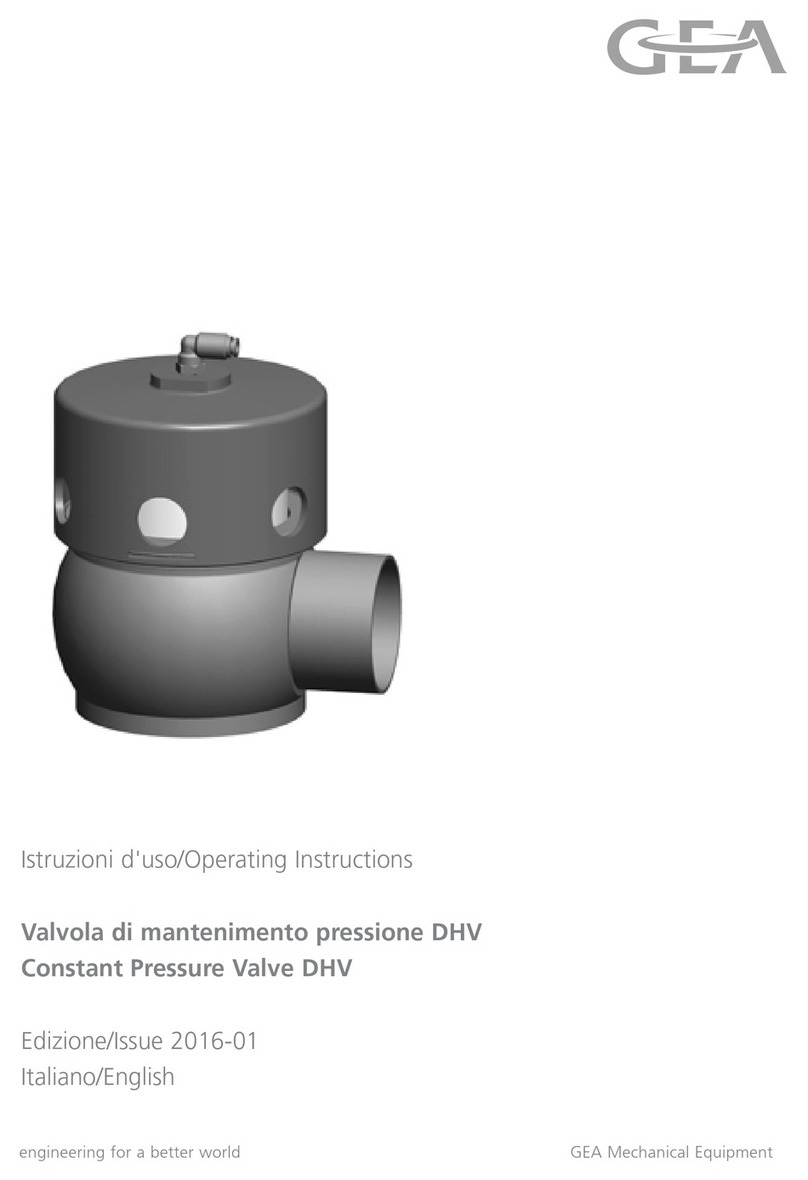
GEA
GEA DHV User manual

GEA
GEA Aseptomag AV User manual
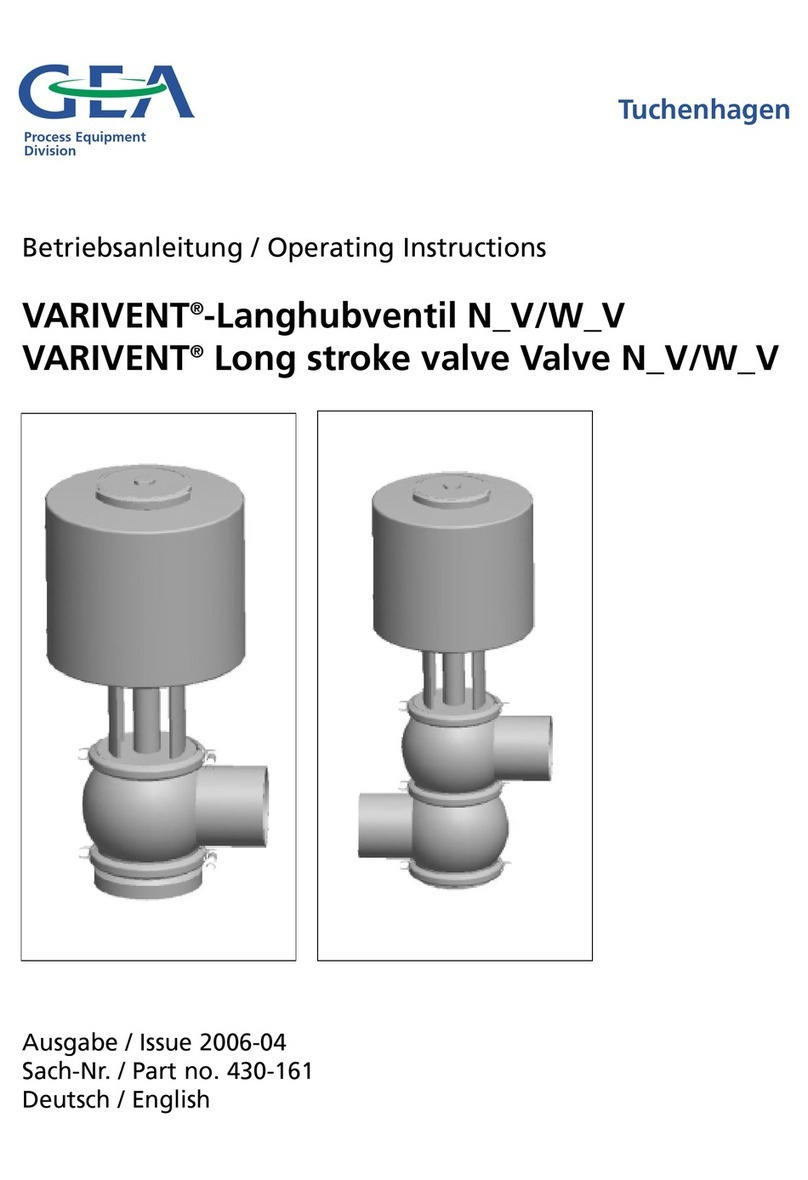
GEA
GEA VARIVENT N V User manual

GEA
GEA VARIVENT X User manual

GEA
GEA DHV DN65/50 KVS 16 User manual
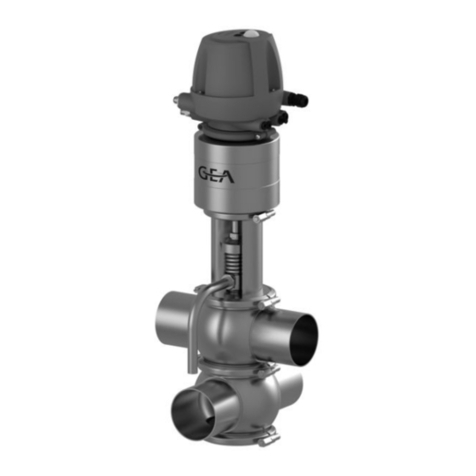
GEA
GEA VARIVENT K User manual
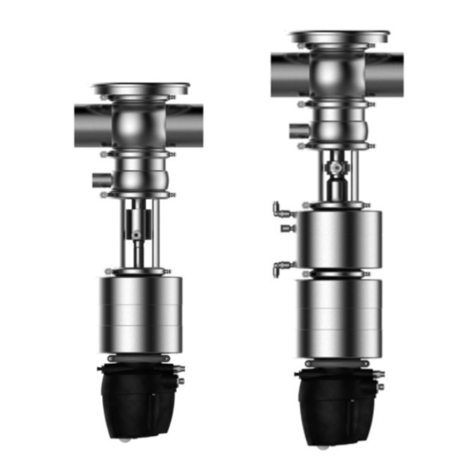
GEA
GEA VARIVENT T R Series User manual
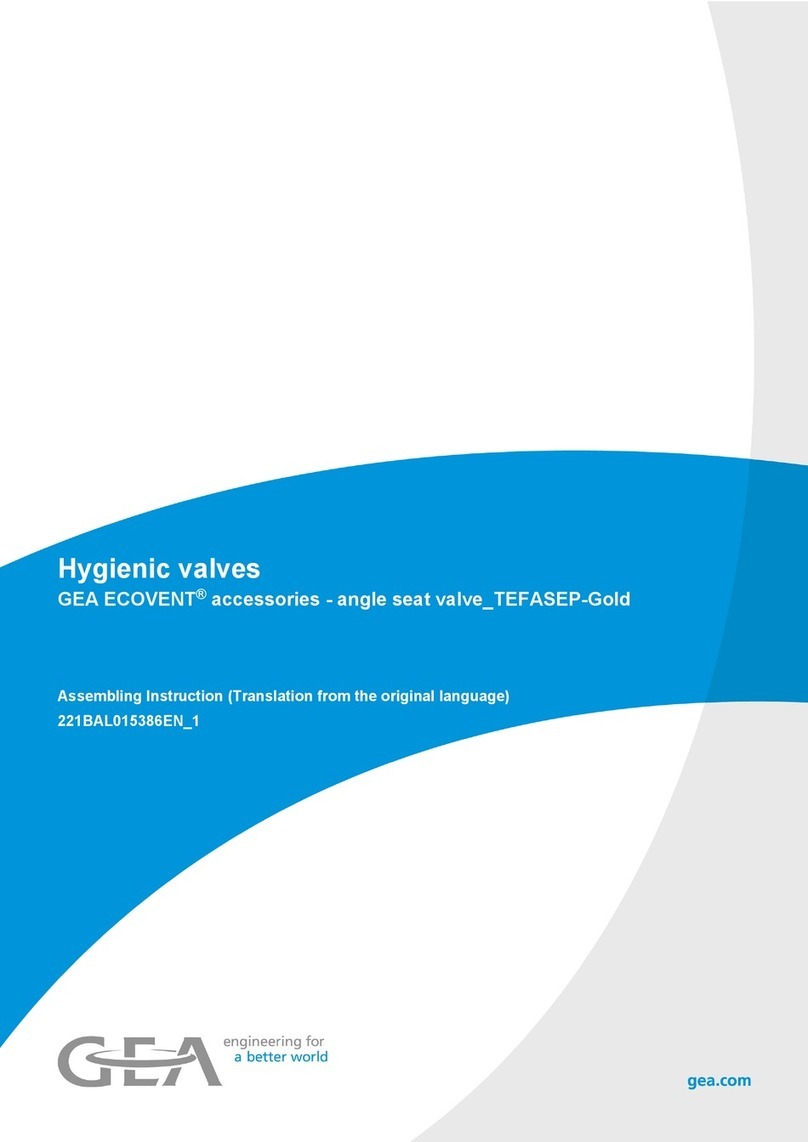
GEA
GEA ECOVENT TEFASEP-Gold ECO E User manual
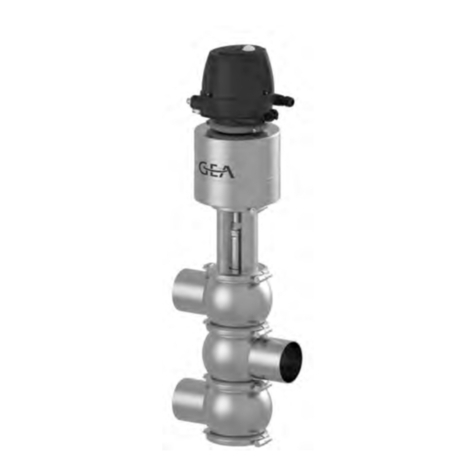
GEA
GEA VARIVENT X R Series User manual
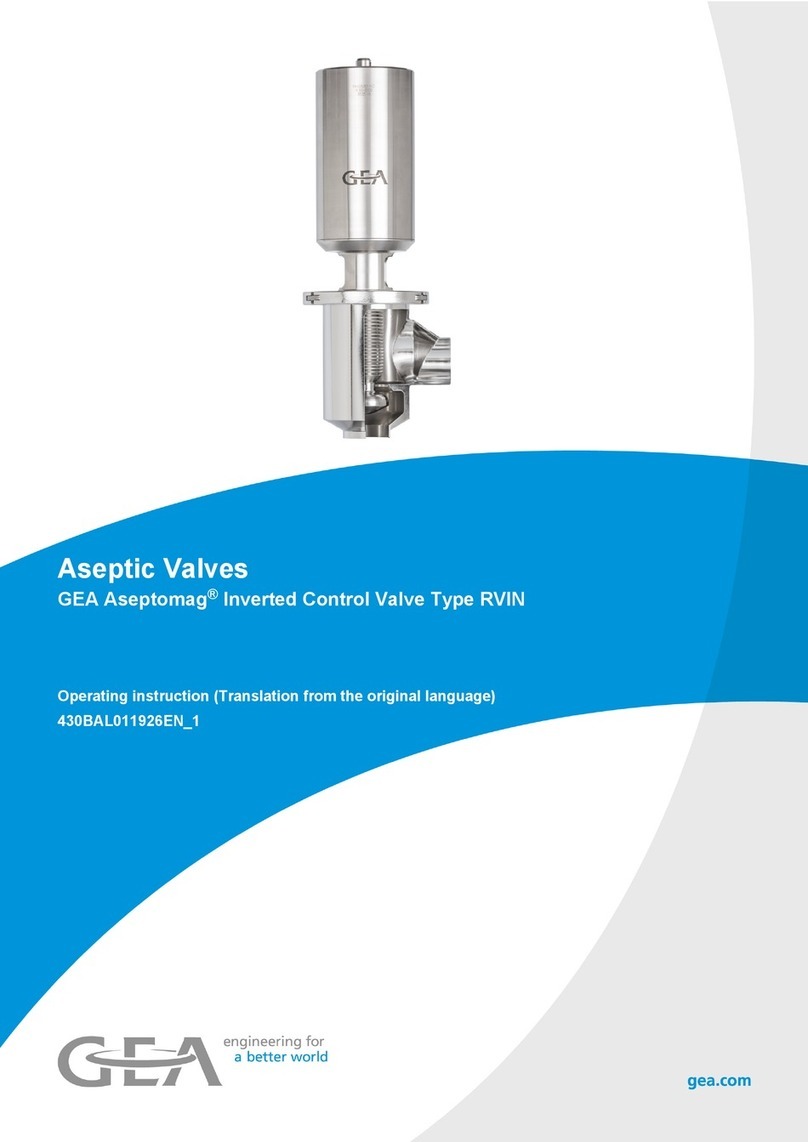
GEA
GEA Aseptomag RVIN User manual

GEA
GEA VARIVENT Y User manual
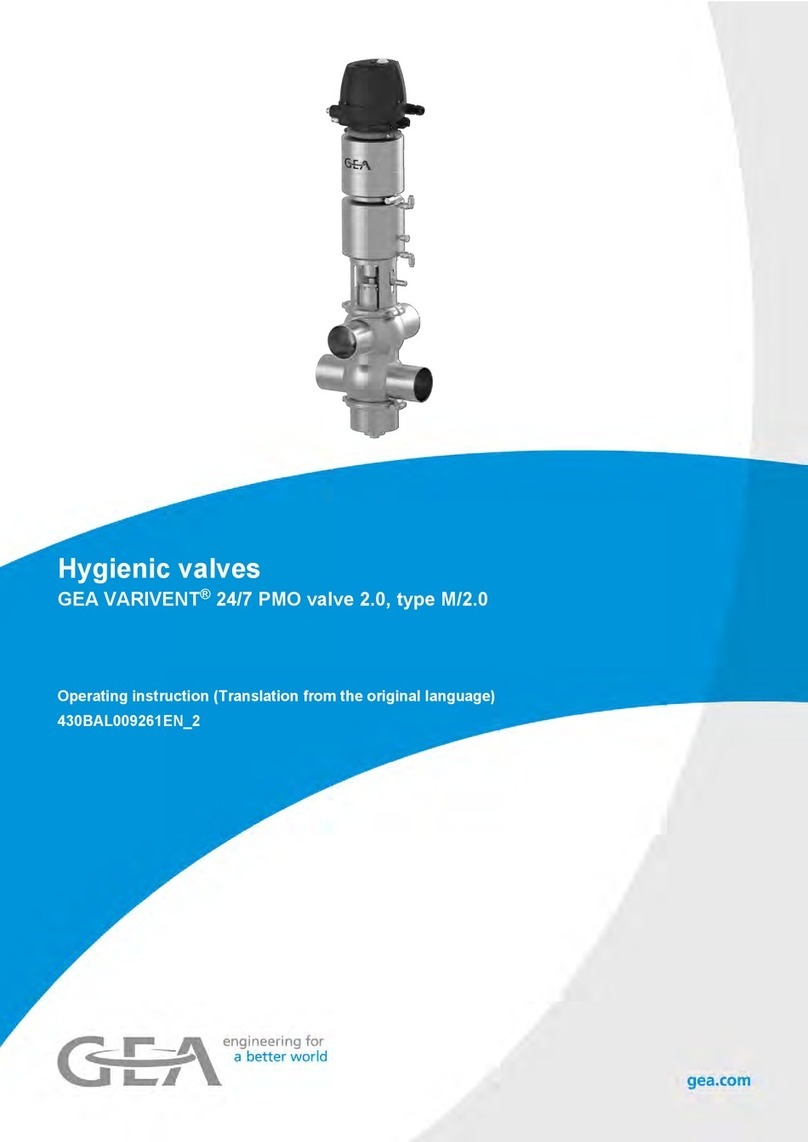
GEA
GEA VARIVENT 24/7 PMO User manual
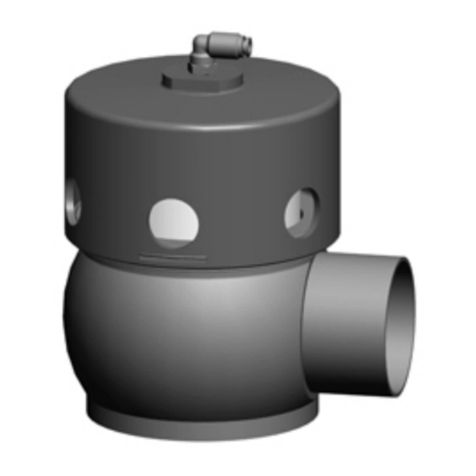
GEA
GEA DHV DN65/50 KVS 16 User manual

GEA
GEA VARIVENT T R User manual
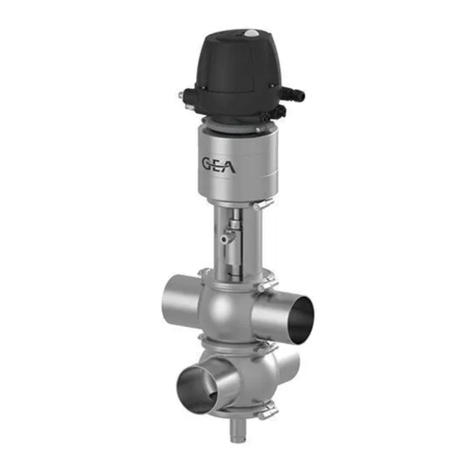
GEA
GEA VARIVENT User manual

GEA
GEA H A/T Series User manual