gefran KFM LD User manual

.... Instruction manual
Door Drive
KFM LD

Information about this manual
Before using the product, read the safety instruction section carefully.
Keep the manual in a safe place and available to engineering and installation personnel during the product
functioning period.
SIEI-AREG GmbH has the right to modify products, data and dimensions without notice. The data can only be
used for the product description and they can not be understood as legally stated properties.
Thank you for choosing this Gefran product.
We will be glad to receive any possible information which could help us improving this manual. The e-mail
All rights reserved
2 KFM LD • Instruction manual

Table of contents
Information about this manual..................................................................................................................2
1. Safety ...................................................................................................................................................5
1.1. Warning notes ..........................................................................................................................................5
1.2. Symbols used in the manual ....................................................................................................................5
1.3. Safety requirements .................................................................................................................................5
1.3.1. Area of applicability...................................................................................................................................................5
1.3.2. Basic requirements for safety ...................................................................................................................................5
1.3.3. Obligationsoftheoperatingcompanyandinstallationrm ......................................................................................6
1.3.4. Duties of personnel ...................................................................................................................................................6
1.4. Warranty and liability................................................................................................................................6
1.4.1. Structuralmodicationoftheproduct .......................................................................................................................6
1.4.2. Use in line with intended use ....................................................................................................................................6
1.5. Personal protective equipment.................................................................................................................7
1.6. Disposal of the door drive ........................................................................................................................8
2. Description ..........................................................................................................................................9
2.1. KFM LD door drive, complete / Integrated ...............................................................................................9
2.2. KFM LD door drive, separated ...............................................................................................................10
2.3. Connection – Motor side ........................................................................................................................ 11
2.4. Connection options complete and separated.........................................................................................12
2.5. Control device KFM LD complete ..........................................................................................................13
2.5.1. Connection options ..................................................................................................................................................14
2.6. General description ................................................................................................................................15
2.7. Controller................................................................................................................................................15
2.8. Construction ...........................................................................................................................................15
2.8.1. Connection to elevator control unit ..........................................................................................................................15
2.9. Drive functions .......................................................................................................................................16
2.9.1. Approval inspection..................................................................................................................................................16
2.9.2. Function table ..........................................................................................................................................................16
2.9.3. Open / close.............................................................................................................................................................16
2.9.4. Running characteristic curve KFM LD not jerk-limited. ............................................................................................17
2.9.5. Behaviour after RESET............................................................................................................................................17
2.9.6. Stop function ............................................................................................................................................................18
2.9.7. Slip opening .............................................................................................................................................................18
2.9.8. Tripping ....................................................................................................................................................................18
2.9.9. Drive without torque .................................................................................................................................................18
2.9.10. Closing force monitoring ..........................................................................................................................................18
2.9.11. Opening force monitoring.........................................................................................................................................18
2.9.12. Trigger signal from the elevator control - trigger with 24V logic signals...................................................................19
2.9.13. Signals to the control system ...................................................................................................................................19
2.9.14. Door inspection switch .............................................................................................................................................19
2.9.15. Drive settings ...........................................................................................................................................................19
2.9.16. Error diagnosis and display options.........................................................................................................................20
2.9.17. Signal and fault display by means of light emitting diodes ......................................................................................20
3. Technology ........................................................................................................................................21
3.1. Technical data Drive...............................................................................................................................21
3.2. KFM LD dimensions, complete ..............................................................................................................22
3.3. KFM LD dimensions, separated.............................................................................................................22
4. Installation .........................................................................................................................................23
4.1. Car door drive ........................................................................................................................................23
4.1.1. Installation of car door drive.....................................................................................................................................23
4.1.2. Adjusting the belt tension.........................................................................................................................................24
KFM LD • Instruction manual 3

4.1.3. Resonance frequency measurement.......................................................................................................................24
4.1.4. Test sequence..........................................................................................................................................................24
4.2. Replacing F2/1, F5, F9 with KFM LD .....................................................................................................25
4.3. Connecting .............................................................................................................................................25
4.3.1. X2 for trigger signals with pin assignments..............................................................................................................25
4.3.2. Connection of the KFM LD door drive to conventional 24V logic level ....................................................................26
4.3.3. CAN bus connection (Not implemented in KFM LD)................................................................................................27
4.3.4. Power supply - KFM LD control complete and separated........................................................................................28
5. Commissioning .................................................................................................................................29
5.1. General ..................................................................................................................................................29
5.1.1. Commissioning the door drive .................................................................................................................................29
5.2. Learning the gear ratio (aipm)................................................................................................................30
5.3. Automatic ...............................................................................................................................................30
5.3.1. Automatic commissioning ........................................................................................................................................30
5.4. Manually with the service program.........................................................................................................33
5.5. Meaning of the LED indicator.................................................................................................................33
5.5.1. Error messages during automatic commissioning ...................................................................................................34
5.5.2. Explanation of the LED indicators............................................................................................................................35
5.6. Switch setting .........................................................................................................................................36
5.6.1. Switch and jumper settings during commissioning ..................................................................................................36
5.6.2. Setting of Switch J3 and Jumper J4.........................................................................................................................37
6. Maintenance ......................................................................................................................................38
6.1. Drive maintenance .................................................................................................................................38
6.1.1. Maintenance ............................................................................................................................................................38
6.2. Fault repair .............................................................................................................................................38
4 KFM LD • Instruction manual

1. Safety
1.1. Warning notes
• Safety notes are intended for the protection of persons and property.
• Safety notes must be read and observed by every person who works on the product.
• Warning notes precede activities that pose a hazard for people and the product.
1.2. Symbols used in the manual
Indicates a procedure, condition, or statement that, if not strictly observed, could result in personal injury or death.
Indicates a procedure, condition, or statement that, if not strictly observed, could result in damage to or destruc-
tion of equipment.
Indicates that the presence of electrostatic discharge could damage the appliance. When handling the boards,
always wear a grounded bracelet.
Indicates a procedure, condition, or statement that should be strictly followed in order to optimize these applications.
Note ! Indicates an essential or important procedure, condition, or statement.
1.3. Safety requirements
This document contains important information for safe operation of the product.
• Keep this document and all other applicable documents at the location of use for the entire working life of
the product.
1.3.1. Area of applicability
This document applies only to the product described here.
Other applicable documents
• International occupational health and safety regulations
1.3.2. Basic requirements for safety
• All existing safety devices are to be tested regularly in accordance with the maintenance schedule.
• This document, in particular the chapter entitled "Safety", together with the warnings and all other applicable
documents, must be followed by all persons who work with the product.
• In addition to this document, the rules at the location of use with regard to environmental protection and the
occupation health and safety and accident prevention regulations must be followed.
• All safety and hazard warnings on the installation must be kept in legible condition.
• Safety information and instructions required by law must be displayed to users in such a way that they are
clearly visible.
• A requirement for safe handling and non-disruptive operation of this product is knowledge of the fundamen-
tal safety regulations.
Warning
Caution
Important
KFM LD • Instruction manual 5

1.3.3. Obligations of the operating company and installation rm
• Only deploy trained and instructed qualied personnel.
• Provide personnel with the required personal protective equipment.
• Check personnel at regular intervals to ensure that they follow safety-conscious work practices and comply
with national provisions.
• Make all other applicable documents as well as this document available to personnel.
1.3.4. Duties of personnel
• Clearly establish all areas of responsibility prior to any activity.
• Always wear the personal protective equipment made available to you.
• Prior to work, make people aware of the dangers of electrical current.
1.4. Warranty and liability
The "General Terms of Sale and Delivery" of SIEI-AREG GmbH apply.
Warranty and liability claims in the event of injury or damage to property will be invalidated if attributable to at
least one of the following causes:
• Improper use that is not in line with the intended purpose of the product
• Improper installation, commissioning, operation and maintenance of the product
• Operation of the product with defective or inoperative safety devices, guards or protection devices
• Noncompliance with the information and instructions in the operating manual in respect of transport, stor-
age, installation, assembly, commissioning, operation and maintenance
• Structural modication to the product without agreement or approval
• Modication to product features without agreement or approval
• Decient monitoring of parts that are subject to wear
• Repairs that are carried out improperly
• Cases of catastrophe due to third-party interference or force majeure
• Use on non-approved auxiliary materials and operating uids.
1.4.1. Structural modication of the product
The product is congured in the factory and delivered ready for operation.
If changes are made to the product, the entire warranty of SIEI-AREG GmbH shall become null and void.
1.4.2. Use in line with intended use
The product has been constructed using state-of-the-art technology and in line with the recognised technical
safety regulations. It may only be used in accordance with its intended use and when the technical safety de-
vices are free from defects. Any other or additional form of use shall be regarded as non-compliant
with the intended use. SIEI-AREG GmbH shall not be liable for any damage arising from such use or for any
damage arising due to operator errors.
• In order to comply with the intended use of the product:
• Use the product as a Drive for elevator doors only
• Read and comply with the document, in particular the chapter entitled "Safety", together with the warnings
and all other applicable documents
• Comply with the commissioning instructions, the installation description as well as the required inspection
and maintenance work
• Do not make unnecessary runs; bear in mind that the elevator is a means of transport and not a toy.
6 KFM LD • Instruction manual

1.5. Personal protective equipment
Danger Cause Risks Remedy Equipment
Unprotected shaft Fall Safety harness
Warning
Do not walk underneath
suspended loads
Head injury Head protection
• Falling tool
• Transport of heavy load
• Sharp-pointed objects
Warning
Do not walk underneath
suspended loads Danger of crushing in the foot area
Cut or stab injury in the foot area Foot protection
• Falling tool
• Transport of heavy load
• Sharp-pointed objects
• Sharp objects
• Mechanical parts
• Sharp-pointed objects
• Caustic substances
Danger of crushing in the hand
area
Cut or stab injury in the hand area
Acid / alkali burns
Hand protection
• Severe noise pollution Noise damage Ear protection
• Flying parts
• Flying particles
• Laser beams
• Optical beams
Eye injury
Loss of sight/ blinding Eye protection
• Electrical Voltage Electric shock Enable source of energy
Tab. 1 Warning pictograms
KFM LD • Instruction manual 7

1.6. Disposal of the door drive
• Please dispose of this unit with care as an industrial waste and according to your required local regulations.
• The capacitors of inverter main circuit and printed circuit board are considered as hazardous waste and
must not be burned.
• The Plastic enclosure and parts of the inverter such as the top cover board will release harmful gases if
burned.
Pursuant to Article 26 of Italian Legislative Decree no. 49 of 14 March 2014 “Implementation of Directive
2012/19/EU on waste electrical and electronic equipment (WEEE)”
The symbol showing a crossed-out wheeled bin on equipment or its packaging indicates that the product must
be collected separately from other waste at the end of its useful life.
The manufacturer is responsible for organising and managing the separate collection of this piece of equipment
at the end of its useful life.
Users wishing to dispose of the equipment must therefore contact the manufacturer to obtain instructions from
the same on how to have the equipment collected separately at the end of its useful life.
By collecting the disused equipment separately, it can be recycled, treated or disposed of in an environmentally
friendly manner, thus helping to prevent the environment and public health from being aected negatively and
enabling reuse and/or recycling of the materials forming the same equipment.
Caution
8 KFM LD • Instruction manual

2. Description
2.1. KFM LD door drive, complete / Integrated
1
2
3 4 5
6
7
8
9
10
Fig. 1
Item Designation Item Designation
1 Drive bearing 6 Connection of motor + controller
2 V-groove belt on motor side 7 Tightening screw
3 Door drive motor 8 Header
4 Inspection switch 9 Toothed belt on coupler side
5 Control device 10 Anti-vibrating damper
Tab. 2 Parts of door drive
1
2
3
4
Fig. 2
Item Designation Item Designation
1 V-groove washer 3 Housing
2 Motor 4 Controller
Tab. 3 Parts of KFM LD compact
KFM LD • Instruction manual 9

2.2. KFM LD door drive, separated
In the KFM LD door drive there is an insulation paper over the electronic parts to protect the technician from
contact with live parts during commissioning. For this reason, the insulating paper must not be removed and after
commissioning, the cover must be mounted on the housing and screwed tight!
123
4
5
Fig. 3
Item Designation Item Designation
1 Drive shaft 4 Connecting line, 7 wires
Impulses / temperature
2 Door drive motor 5 Control device
3 Connecting line, 4 wires
Motor line
Tab.4 Parts of KFM LD Separate Version
Warning
10 KFM LD • Instruction manual

2.3. Connection – Motor side
4
3
2
1
5
6
7
Fig. 4
Item Designation Item Designation
1 Fastening - impulses / temp. line 5 Connection for Pulse encoder
2 Fastening - motor line 6 Housing of control device
3 Motor connection 7 Inspection switch
4 Connection for Temperature sensor
Tab.5 Connectors of KFM LD
KFM LD • Instruction manual 11

2.4. Connection options complete and separated
15
9
6
X6 RS232
S1 S2
T1
J4
J3
H4H3 H2 H1
X5 CAN
Diagnose SY9
Diagnostic
N
PEL1
X7
Netz / Line
F1 / F3 Sicherung
Fuse 5A T
X2 Eingang / Input
aktiv
inaktiv
Terminator
123456 1234
12345
1
4
X4 Lichtvorhang
/ light curtain
X3 Ausgang
/ Output
Netz / Line
230 V / 50 Hz
X1 RJ45
CAN
Fig. 5
X1 CAN-Connector (not implemented)
Pin Assignment
1 CAN-L
2 CAN-H
3 GND
4 Not used
5 GND
6 Not used
7 CAN-L
8 CAN-H
Tab.6 Connector X1
X2 RM3.81 Input
Pin Signals
1 +24V
2 0V
3 TU
4TO
5 TUL (default)
6 Inspection approval
Tab.7 Connector X2
X3 RM3.81 Output
Pin Signals
1 TSU (default)
2 TSO (default)
3 >150N (default)
4 n.c.
Tab.8 Connector X3
X3 RM3.81 Output
Pin Assignment Connection
1 +24V X2:1
2LT X3:4
3 0V X2:2
4 0V X2:2
5 n.c. -
Tab.9 Connector X4
12 KFM LD • Instruction manual

X5 RM2.54 CAN
Pin Signals Connection
1 Connected X5:2
2 Connected X5:1
3 CAN-L
4 CAN-H
Tab.10 Connector X5
X2 RM3.81 Input
Pin Assignment
1 L1 (230V/50Hz)
2 PE
3 N
Tab.11 Connector X7
2.5. Control device KFM LD complete
F1/F3
X4
X5
X1
X2 J4 H1 - 4 X3X7 J3S1 S2 T1X6F1/F3
X4
X5
X1
X2 J4 H1 - 4 X3X7 J3S1 S2 T1X6
Fig. 6
X7 F1 F3 X6
S1
X2
S2
T1
J3
H1...H4
X3
J4
X1
X5
S11
X4
Fig. 7
Item Designation Item Designation
F3 Equipment fuse (5 A) X5 CAN connection (Not implemented)
H1-4 Status display LED X6 Diagnostic connection (RS232)
J3 Switch for CAN resistor (Not implemented) X7 Power supply 230V
J4 Jumper (bridge) for reset S1 Operating mode switch
X1 CAN interface (RJ45) (Not implemented) S2 Speed switch
X2 Input for control signals S11 Inspection switch
X3 Output for Control signals T1 Button for commissioning
X4 Light curtain connection
Tab. 12 Controls of KFM LD
KFM LD • Instruction manual 13

2.5.1. Connection options
1. The control device is actuated via an interface with 24-V logic level at connections X2 / X3. The control
system is connected via two separate connecting lines.
2. The connection via CAN bus by means of a CAN bus line to connections X2 / X5 is based on a special
thyssenkrupp CAN bus specication and requires an elevator control unit from SIEI-AREG GmbH as pre-
requisite (Not implemented).
3. Connectors X2:5 and X3:4 can be occupied as input 1 and 2. The function is set via parameters ase1 and
ase 2. Pins X3:1-3 are only used as outputs. The function is dened via parameters aas1 – aas3.
4. The pin connector socket X4 light grid is used to connect an external light grid. At pin 1 + 24V and pin 3 / pin
4 GND, the supply of the light grid can be tapped. These pins are directly connected to connector X2. The
signal (24V logic) of the light curtain is routed to pin 2 which is internally connected to pin 4 of connector X3.
The function of the light curtain must be activated in the software via a parameter.
5. In the CAN connection X5, pins 1and 2 interconnected. The CAN signals are simultaneously on the connec-
tions X5 and X1.
Connection information, program updates and further details from the manufacturer are available from SIEI-AR-
EG GmbH.
14 KFM LD • Instruction manual

2.6. General description
The contents of these instructions refer to the current software version. The KFM LD door drive is intended
standard for the drive of the dierent car door, with unknown ratios. It simultaneously replaces control device
and drive of types F2/1 and F5 during replacement and conversion work.
Function: A frequency-controlled motor drives the coupler (widening cam) of the driven door panel via a
V-groove belt.
The drive speed is controlled in a path-dependent manner via an encoder built into the drive. This supplies the
necessary information with respect to position and speed. No switch is therefore needed for detecting the door
position.
At the end positions, an adjustable end-of-travel moment holds the door in position. A parking brake is not
required.
Note ! The travel control requires a linear relationship between motor speed and door movement. This means that the drive may only be
used on linear-operated doors. (Not on doors with crank drive!)
Application limits of the drive: The drive path is limited to max. 100 motor revolutions or 51200 impulses
(1 rotation corresponds to 512 impulses). The eective diameter of the shrunk-on drive pinion is 26 mm. This
corresponds to a path of 81.7 mm per motor revolution. The door mechanics must be designed so that the
gear ratio for the fast door panel moves between 60 and 310 impulses / cm travel. The drive software cannot
process values outside of this tolerance range.
Motor: The drive motor is a frequency-controlled asynchronous motor with built-in encoder. It stands vertically
on a console that is vibration-protected with rubber insulators and fastened to the suspension gear. Horizontal
mounting is also possible via an optionally available adapter bracket. (See special versions)
Control device: The KFM LD drive is available in two types:
1. Together with the motor, the control electronics form a structural unit. The controller and motor connections
are permanently connected to one another.
The printed circuit board with the connections, light indicators, adjustment switches and start switches for
commissioning can be accessed by removing the rear housing cover on the control device attachment. (See
Fig. 2 and Fig. 6).
2. The door motor and the controller are separated. The printed circuit board with the connections, light indica-
tors, adjustment switches and start switches for commissioning can be accessed by removing the housing
cover on the control device. (See Fig. 3 and Fig. 7).
2.7. Controller
The control device of the KFM LD drive operates according to the V/f-characteristic curve method. The encoder
installed in the motor provides all of the information required for this purpose.
2.8. Construction
The control consists of a printed circuit board with the functional groups:
1. Power electronics with input lter and PFC circuit for reduction of the harmonic waves: Frequency inverter.
Power pack with all required lter measures.
2. Microprocessor electronics: Processor in which the setpoint is calculated and regulation is performed with
the interfaces for elevator control and settings devices.
3. Program Flash EPROM: integrated in the microprocessor with rmware w (download via serial interface x6).
2.8.1. Connection to elevator control unit
The following connection options are provided on the motor:
1. Interface with conventional 24-V logic levels (controller input X2; controller output X3)
2. (A CAN bus connection is present for SIEI-AREG GmbH control systems (NOT IMPLEMENTED)).
KFM LD • Instruction manual 15

Setting: Initial operation of the drive setting is possible in several dierent ways:
1. Automatic commissioning via push-button T1. Description in Chap.5.2 on page 30.
2. With the help of a PC or laptop in combination with E@syDrives, a special software program from the door
drive manufacturer that can be accessed at the Gefran intranet and on the CDROM that is included at every
KFM LD Door drive.
Note ! For the procedure during commissioning, further details and technical data, please refer to the following descriptions of the drive
or the adjustment instructions in chapter "Commissioning".
2.9. Drive functions
Function principle: The KFM LD door drive responds according to the applied trigger signals. (See function
table).
Trigger signals:
Trigger signal for function
TO Open door
TU Close door
TL Close door slowly or nudge
Tab. 13 Control Signals
2.9.1. Approval inspection
Function table, trigger signals (commands). Specied responses depending on trigger signals.
2.9.2. Function table
TO TU TL Response of the drive
1 1 X Stop function
1 0 1 Slip opening
1 0 0 Open
0 1 0 Close
0 X 1 Nudge / close slowly
0 0 0 Drive without torque
Tab. 14 Function table
Explanations:
"1" → Signal applied (signal is "true");
"0" → Signal is not applied (signal is "not true");
"X" → Any signal
2.9.3. Open / close
A running characteristic curve is generated by the control electronics depending on the door path to be trav-
elled. This is congured in such a way that the door always moves at the optimal speed (long creepage is not
required). The running characteristic curve contains a special prole for operation of the door cam by the door
drive. The generation of the prole for widening cam operation can be switched o via E@syDrives.
The running characteristic curve of the KFM LD drive is not jerk-limited. (Thus, the speed curve is not rounded
– see Fig. 8). All parameters of the running characteristic curve for opening, closing, nudging and re-opening
can be set independent of one another.
In the following sketches, the curve of the speed reference value for a normal, complete door movement with
KFM LD drive is shown.
16 KFM LD • Instruction manual

V
Widening cam
speed
Widening cam
operation can
be deactivated
Widening cam
operation can
be deactivated
Maximum
speed
Maximum
speed
Acceleration
Acceleration
Deceleration
Deceleration
Approach speed
Widening cam
speed
Approach
speed
VClose
Open
t
t
Fig. 8
2.9.4. Running characteristic curve KFM LD not jerk-limited.
When a door end position is reached, this is recognised automatically by the drive and a corresponding end
position signal (TSU / TSO) is sent to the elevator control. The door drive now presses the door against the end
position with an adjustable torque as long as the corresponding trigger signal (TO, TU, TUL) is applied.
The end position signal applied to the elevator control remains valid until the door is located within a certain
denable environment ("Drawing from end position" window) around each end position, independent of whether
the corresponding trigger signal is being applied or not. The behaviour is similar to that of a real end position
switch.
2.9.5. Behaviour after RESET
Following a RESET, on opening/closing the door initially moves at low speed over the entire door width until the
entire door path has been run through once in a single motion. The door then moves at normal speed again.
KFM LD • Instruction manual 17

2.9.6. Stop function
The door delays with redirection speed until it is stationary and then adjusts the position achieved when sta-
tionary. Moving the door by force, e.g., by hand, results in the door moving back to the original position when
released. Intentional changing of the stop door position is only possible via the TO, TU and TUL trigger signals.
The stop function can be cancelled by entering altered trigger signals.
2.9.7. Slip opening
(Partial opening of the door that can be dened within the opening width.) The slip opening function makes it
possible to adjust the door drive in such a way that the door only opens partially in certain cases (e.g., after
interruption of the light barrier). The set value (TSSOE) up to which the door can be opened lies between 100%
and 900% of the door width. The setting is made using a service program.
2.9.8. Tripping
Slip opening is tripped under the following conditions: The TO and TUL trigger signals (nudging) are applied
simultaneously, TU is inactive and the slip function on the control device of the KFM LD door drive is activated.
(Activated by entering the % value.) The door travels to the door position set for slip opening (TSSOE).
As long as the signals for slip opening are applied, the drive regulates to this set position (same as stop func-
tion). If the TO and TUL control signals (nudging) are applied simultaneously and the slip function is not acti-
vated, the drive behaves as with the stop function. The slip opening function can only be activated if a value for
the desired door position is set. With slip opening, the door behaves as follows depending on the door position:
1. The door is located between TSSOE and TSO. If the slip opening command is now issued, the door stops
at reopening speed and remains at a standstill in stop mode (i.e., the door drive regulates to position) until
another door command is applied.
2. The door is located between TSU and TSSOE; door opens. If the command for slip opening is issued now,
the door opens up to the TSSOE position and then stops at reopening speed. The door remains at a stand-
still in the stop mode until another door command is pending.
3. The door is located between TSU and TSSOE; the door does not open. If the slip opening command is now
issued, the door reopens if necessary and moves directly to the TSSOE position. The door remains at a
standstill in the stop mode until another door command is pending.
2.9.9. Drive without torque
The drive is without torque, but not switched o. The door movement is monitored by the drive. If the door
closes at excessively high speed, the drive brakes the door. This prevents the landing door from closing at ex-
cessive speed. Below the speed threshold and in the "OPEN" direction, the door can be moved easily by hand.
The door drive monitors the changed door position and takes it into account in a subsequent door movement.
The "Drive without torque" state must be cancelled by entering altered trigger signals.
2.9.10. Closing force monitoring
The KFM LD door drive can learn a certain force as the maximum door closing force (150 N limitation). The
door drive can be set in such a way that it automatically reopens and then recloses when the learned maximum
door closing force is reached.
2.9.11. Opening force monitoring
The requirements for glass doors are ensured with automatic commissioning in hex switching position S2 = 7,
8, or 9. This means force limitation during complete opening and a reduction of the kinetic energy. Upon reach-
ing 150N, the drive stops immediately and is then torque-free. By changing the control command, the control
system can again immediately access the drive.
This option must not be activated on re service elevators, as the elevator control system is not notied of the
behaviour of the door drive.
Note ! The reopening of the door occurs by the elevator control unit. Trigger signal from the elevator control - trigger with 24V logic
signals.
Caution
18 KFM LD • Instruction manual

2.9.12. Trigger signal from the elevator control - trigger with 24V logic signals
The elevator control unit must provide the following:
1. +24V reference potential for all signals sent to the control electronics on
2. 0V isolated inputs / outputs.
3. TO signal "Open door"
4. TU signal "Close door"
5. TUL signal "Nudge" (close door slowly) (optional)
6. Approval inspection
Activation: +24V DC – The inputs on the control electronics are isolated. Activation with 230V AC can only
take place if the trigger signals are converted externally to 24V DC. The input signals can be applied as 0 Volt
switching or 24 Volt switching. Codication is performed via the polarity of the 24 Voltage supply.
Mixed operation of 0 Volt switching / 24 Volt switching of the input signals between one another is not possible.
The trigger signals are processed by the control electronics depending on the state, i.e., the corresponding
action is only performed while the respective signal is applied. If all the trigger signals are inactive, the KFM LD
door drive switches to a state without torque.
Note ! If a stop switch is used, a TO and TU signal must be sent to the door drive parallel to the main switch. (stop function).
The KFM LD door drive has no CAN interface that can be used in combination with elevator control !
2.9.13. Signals to the control system
The following output signals are output as status signals (acknowledgements):
Default TSU – door connected
Default TSO – door open
Default >150N – indicator indicating closing force exceeded
The status signals are switched by transistors which, depending on the connection version, act either as tran-
sistor with open commutator or as transistor with open emitter. These connections are short-circuit-protected.
The outputs can be programmed via the function (aoes) (dF96) “Selection TSU/TSO as break contact/ make
contact” in such a way that in the case of a pending acknowledge signal of the transistor
• blocked corresponds to 0 = break contact,
or
• switched through – corresponds to 1 = make contact.
The acknowledge signals are isolated. Reference potential is +24V DC, and/or 0V, maximum current: 50 mA. If
relays are switched with the signals, external freewheeling diodes must be tted. The acknowledge signals can
be output as 0 Volt switching or 24 Volt switching. Codication is performed via the polarity of the 24 Voltage
supply.
Mixed operation of 0 Volt switching / 24 Volt switching of the acknowledge signals between one another is not
possible. Mixed logic is, however, possible for the trigger and output signals of the door drive.
2.9.14. Door inspection switch
There is a door inspection switch on the KFM LD door drive. If the "Approval inspection" signal is active, the
door can be opened and closed by pressing the button.
The door inspection switch switches this signal internally to the TU or TO inputs.
2.9.15. Drive settings
All parameter settings, such as speed, acceleration, etc., can be changed with the service programs E@
syDrives and diagnostic unit 6. The program steps and parameters to be entered are described in the instruc-
tions for the programs.
KFM LD • Instruction manual 19

2.9.16. Error diagnosis and display options
The KFM LD door drive has an event stack that stores errors and warnings in non-volatile form, for example,
overtemperature of the heat sinks, etc. The error stack can only be read out with one of the service programs.
2.9.17. Signal and fault display by means of light emitting diodes
One possibility for error diagnosis during commissioning is provided by the display of the 4 LEDs on the control
device. Details on the function and meaning can be found in Chap. 5.5 on page 33.
Also see about this the Chap. 4.3 on page 25.
20 KFM LD • Instruction manual
Table of contents
Other gefran DC Drive manuals
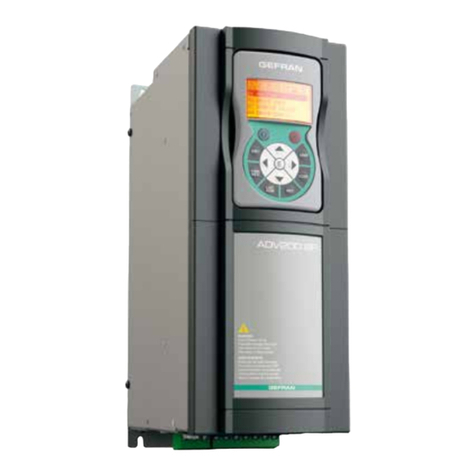
gefran
gefran ADV200 SP Series User manual
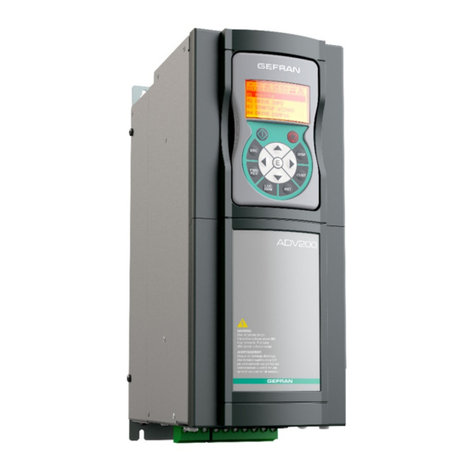
gefran
gefran ADV200-SI Series User manual
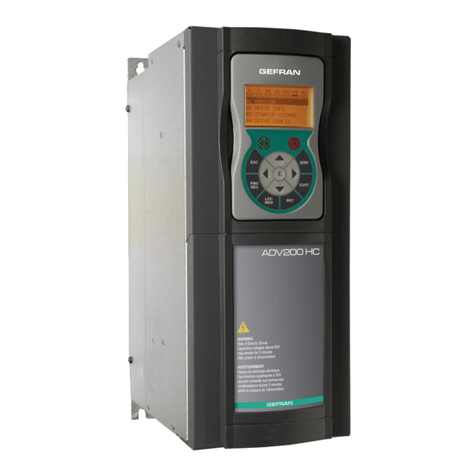
gefran
gefran ADV200-HC User manual
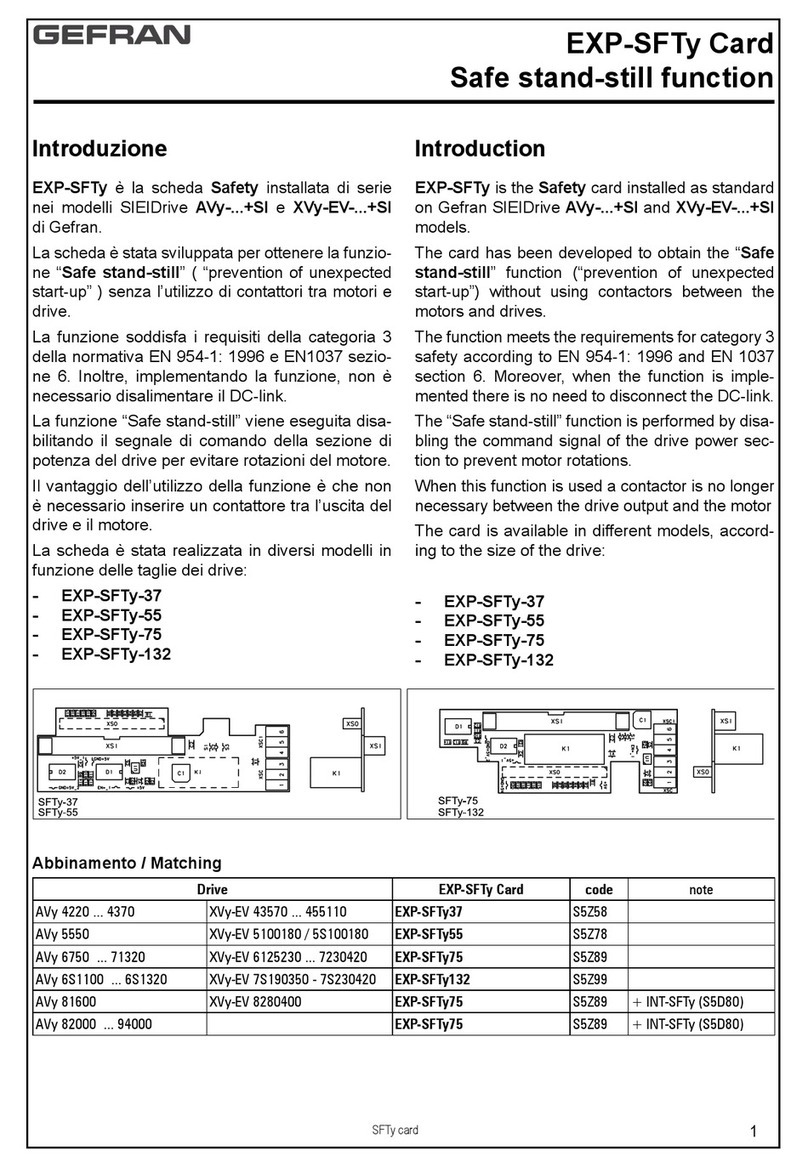
gefran
gefran EXP-SFTy User manual
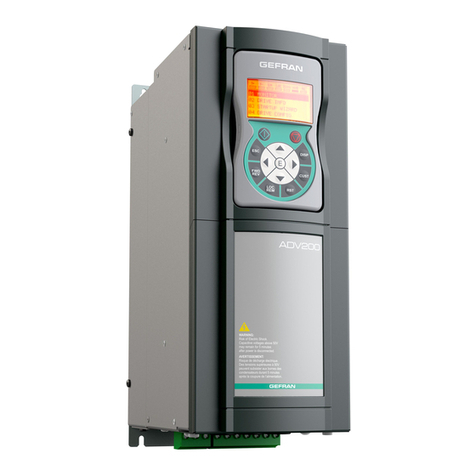
gefran
gefran ADV200 WA Parts list manual

gefran
gefran ADV200-...-DC Series Troubleshooting guide
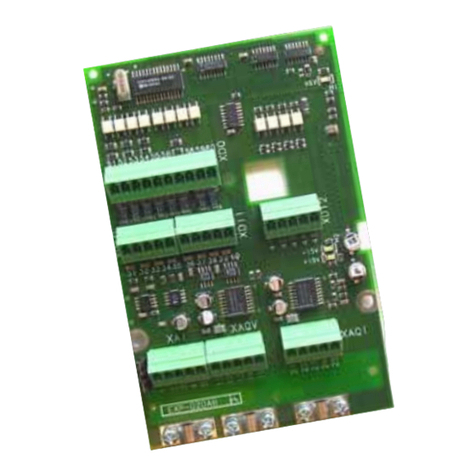
gefran
gefran EXP-D20A6 User manual
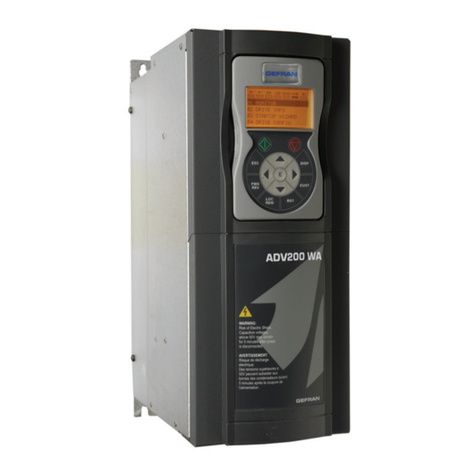
gefran
gefran ADV200 WA User manual
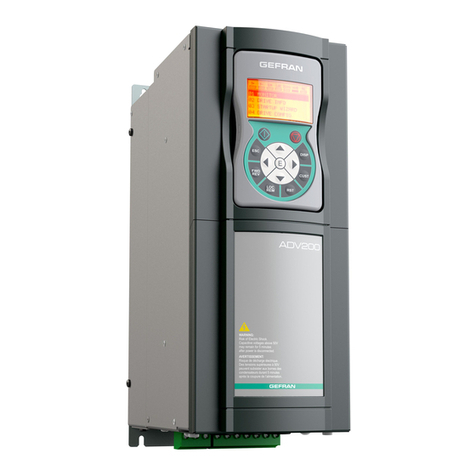
gefran
gefran ADV200 Series Troubleshooting guide
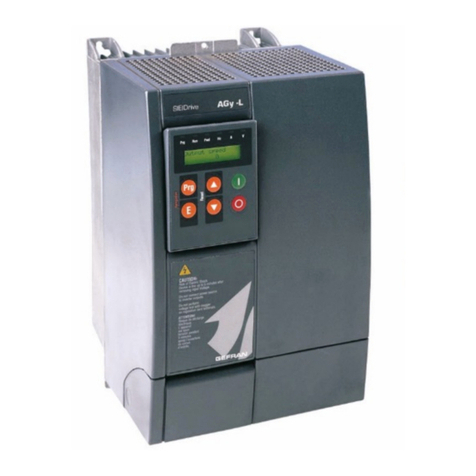
gefran
gefran AGy-L Series Guide