iSMA iSMA-B-MAC36NL Installation manual

iSMA-B-MAC36NL User Manual
Version 1.6 www.globalcontrol5.com Page 2 / 50
Table of Contents
1Introduction............................................................................................................................... 3
1.1 Revision History................................................................................................................ 3
1.2 Safety Rules....................................................................................................................... 4
1.3 Overview............................................................................................................................. 4
1.4 Key Features:..................................................................................................................... 5
1.5 Technical Specification................................................................................................... 6
1.6 Software License Notice................................................................................................. 7
1.7 Dimensions........................................................................................................................ 8
2Hardware Specification .......................................................................................................... 9
2.1 Terminals and Internal Connection Diagram.............................................................. 9
2.2 Power Supply Connection ............................................................................................10
2.2.1 Earth Grounding ......................................................................................................10
2.3 Communication Bus Connection (RS485) ................................................................10
2.3.1 RS485 Grounding and Shielding ..........................................................................11
2.3.2 RS485 Network Termination and Biasing..........................................................11
2.3.3 M-Bus Connection ..................................................................................................14
2.4 Detection of the Device Extension ..............................................................................15
2.5 LED Indicators.................................................................................................................15
2.6 Mini USB...........................................................................................................................16
2.7 Local I/O...........................................................................................................................17
3Start-up ....................................................................................................................................17
3.1 Before the Start............................................................................................................... 17
3.2 SD Card.............................................................................................................................17
3.3 Factory Settings .............................................................................................................19
3.3.1 Factory Communication Settings........................................................................19
3.3.2 Factory Platform Credentials................................................................................19
3.4 First Login to the Controller Platform in Workplace................................................20
3.5 TCP/IP Configuration ....................................................................................................23
3.6 Connection to the Console...........................................................................................27
3.7 Controller System Update ............................................................................................28
3.8 Restore Controller to the Default State......................................................................31
3.9 Restore Controller to the Factory Default..................................................................32
3.10 Data Recovery Service............................................................................................34
3.11 HDMI Connection ....................................................................................................40
3.11.1 Preparation for HMI................................................................................................40
3.11.2 Update to Support HDMI Port ..............................................................................41
3.11.3 Module iSMA_HDMI................................................................................................42
3.11.4 Adding and Start-up of HDMI Service .................................................................45
3.11.5 User Fonts Support ................................................................................................49

iSMA-B-MAC36NL User Manual
Version 1.6 www.globalcontrol5.com Page 3 / 50
1Introduction
1.1 Revision History
Rev
Date
Description
1.0 01.10.2018 First edition
1.1 10.12.2018 Data Recovery Service, Support of the Niagara 4.6 and later
1.2 01.04.2019 HDMI Support, Restore to factory defaults
1.3 31.10.2019 Updated Universal Input supported sensor list
1.4 31.03.2020
Support of Niagara 4.8
Change of passphrase saving destination
User fonts support
Pop-up control for the HDMI display
Auto-detection of the device extension
Log saving to the Niagara home directory
M-Bus support
1.5 27.04.2020 Controller system update–Chapter 3.7
1.6 16.12.2020 Document updated with support of the Niagara 4.9 information
Chapter 3.11.4 updated with the Webservice configuration for HDMI Support
Table 1. Revision history

iSMA-B-MAC36NL User Manual
Version 1.6 www.globalcontrol5.com Page 4 / 50
1.2 Safety Rules
•Note: Incorrect wiring of this product can cause its damage and may result in other
hazards. Make sure the product has been correctly wired before turning the power ON.
•Before wiring or removing/mounting the product, be sure to turn the power OFF. Failure
to do so might cause electric shock.
•Do not touch electrically charged parts such as the power terminals. Doing so might
cause electric shock.
•Do not disassemble the product. Doing so might cause electric shock or faulty
operation.
•Use the product within the operating ranges recommended in the specification
(temperature, humidity, voltage, shock, mounting direction, atmosphere etc.). Failure to
do so might cause fire or faulty operation.
•Tighten the wires firmly to the terminal. Insufficient tightening of the wires to the
terminal might cause a fire.
1.3 Overview
iSMA-B-MAC36NL is a compact Master Application Controller with built-in different types of
I/O and operating in the Niagara Framework environment. Using the specific local I/O set 16x
UI, 8x AO, 4x DI and 8x DO allows to use the device in different applications. The controller
provides control, data logging, alarming, scheduling, integration, and visualisation.
To allow the IP connectivity there are 2x Fast Ethernet ports, which operate independently.
Built-in 1x RS485 can be used to expand the number of I/O by connecting MINI or MIX series
I/O modules or to integrate with other subsystems.
Dedicated microSD card stores real-time data, history logs, and alarms as well as the
operating system, Niagara Framework, and licenses.
There are 2x USB ports, one of them operates as a host port and the other one in the OTG
mode.

iSMA-B-MAC36NL User Manual
Version 1.6 www.globalcontrol5.com Page 5 / 50
1.4 Key Features:
•Niagara 4.4, 4.6, 4.7, 4.8, and 4.9
•Real-time programming
•2x Fast Ethernet (independent)
•1x RS485 (opto-isolated), optional extension as second RS485 port
•optional M-Bus extension
•2x USB (1x OTG, 1x Host)
•16x UI, 8x AO, 4x DI, and 8x DO
•HDMI to connect an external display
•Built-in web server provides graphical user interface available from the web browser
level
•SD card to collect real-time data, history logs, and alarms
•Hardware replacement by SD Card
•Different licensing models for various application types
Figure 1. iSMA-B-MAC36NL Key Features

iSMA-B-MAC36NL User Manual
Version 1.6 www.globalcontrol5.com Page 6 / 50
1.5 Technical Specification
Power Supply
Voltage
24 V AC/DC ± 20% isolated
Power consumption
14 W @ 24 V DC; 24 VA @ 24 V AC
Universal Inputs
Temperature input
•
Measurement with attached RTDs
•Accuracy ±0,1˚C
•For sensor Pt1000 and Ni1000 use 16-bit
resolution
Voltage input
•Voltage measurement from 0 - 10 V
•Input impedance 100 kΩ
•Measurement accuracy ±0,1%
•Measurement resolution 3 mV@12-bit and
1 mV@ 16-bit
Current input
•
Current measurement 0 - 20 mA
•Required external resistor 200 Ω
•Measurement accuracy ±1,1%
•Measurement resolution 15 µA @ 12-bit and 5 µA
@ 16-bit
Resistive input
•
Measurement of resistance from 0 to 1000 kΩ
•Measurement resolution for 20 kΩ load 20 Ω@12-
bit and 1 Ω@16-bit
•Measurement resolution for PT1000 and NI1000
0,1Ω@16bit
Resistance measurement method
The voltage divider
Dry contact input
Output current ~1 mA
Switching threshold: ON <5kΩ, OFF >8kΩ
Measurement resolution
12-bits (default) or 16-bits
Processing time
•10 ms/channel @ 12-bits
•140 ms/channel @ 16-bits
Digital Inputs
Type
Dry contact
Switching threshold
ON <5kΩ, OFF >8kΩ
Max input frequency
100 Hz
Analog Outputs
Voltage range
0 to 10 V DC
Max. load current
20 mA
Resolution
12-bits
Accuracy
±0.5%
Digital Outputs
(relays)
Contact material
AgSnO2
Resistive load
3 A @ 230 V AC/30 V DC
RS485 Interface
(base and optional)
RS485
Up to 128 devices
Half-duplex, Opto-isolated
Communication protocols
Modbus RTU/ ASCII, BACnet MS/TP

iSMA-B-MAC36NL User Manual
Version 1.6 www.globalcontrol5.com Page 7 / 50
Baud rate
From 2400 to 115,200
Address
1 to 247
M-Bus Interface
(optional)
Voltage
30 V
Max. current load
30mA
No. of devices
Up to 20
Baud rate
300-19200
Max. cable length
350 m
Niagara support
From N4.8 (OS .1147)
Ethernet
2x Fast Ethernet
independent mode
Baud rate
10/100 Mb/s
USB
2x USB
1x OTG, 1x Host
HDMI
1x HDMI
Standard type A
SD Card
1x microSD
2 GB system reserved / 2 GB user storage
Ingress protection
IP
IP30
Temperature
Storage
-40˚C to 85˚C (-40˚F to 185˚F)
Operating
0˚C to 50˚C (32˚F to 122˚F)
Humidity
Relative
5% to 95% RH
Connectors
Type
Removable screw terminals
Maximum cable size
2.5 mm
2
Housing
Construction
UL approved, self-extinguishing plastic (PC/ABS)
Mounting
DIN (DIN EN 50022 norm)
Dimension
Width
111 mm (4,4’’)
Length
160 mm (6,3’’)
Height
62 mm (2,45’’)
Table 2. Technical Specification
1.6 Software License Notice
This product contains the code covered by the GNU General Public License (GPL).
Note: This product contains open source software code, the Intellectual Property Rights to
which are the property of The Qt Company Ltd. with its registered office at Bertel Jungin aukio
D3A, 02600 Espoo, Finland.
The usage of abovementioned open source software code in the product is covered by the
GNU General Public License (GPLv3), which is available at:
https://www.gnu.org/licenses/gpl-3.0.en.html
.

iSMA-B-MAC36NL User Manual
Version 1.6 www.globalcontrol5.com Page 9 / 50
2Hardware Specification
2.1 Terminals and Internal Connection Diagram
The iSMA-B-MAC36NL controller is supplied by 24 V AC/DC. The power supply block is
separated. The grounding pin located next to power supply terminals must be connected to
the ground.
The device has 36x local IO on board:
•8x digital outputs (8DO), relay output with max. load 3 A @ 230 V AC/30 V DC;
•8x analog outputs (8AO), voltage output 0-10 V DC maximum load up to 20 mA;
•16x universal inputs (16UI), temperature, voltage, current, resistive, or dry contact;
•4x digital inputs (4DI), dry contact inputs or fast counter up to 100 Hz.
Figure 3. iSMA-B-MAC36NL Block Diagram

iSMA-B-MAC36NL User Manual
Version 1.6 www.globalcontrol5.com Page 10 / 50
2.2 Power Supply Connection
The device is designed to work with 24 V AC/DC separated power supply.
Figure 4. 24 V AC/DC power supply connection
2.2.1 Earth Grounding
Earth grounding protects from electrostatic discharge or other forms of EMI. Connecting the
controller’s ground spade lug to nearby earth ground is possible in hardware versions below
2.1.
2.3 Communication Bus Connection (RS485)
The device is equipped with an opto-isolated RS485 base port, which allows connecting the
device to the BMS in order to communicate with other devices in the network. The optional
controller version has an extension of a second RS 485 port. All rules are the same as in the
base port. The way of proper bus cable connection is shown in the figure below.

iSMA-B-MAC36NL User Manual
Version 1.6 www.globalcontrol5.com Page 11 / 50
Figure 5. RS485 communication bus connection
2.3.1 RS485 Grounding and Shielding
The device can be exposed to electromagnetic environment. The electromagnetic radiation
can induce electrical noise into both power and signal lines, as well as direct radiation into the
device causing negative effects to the device functioning. Appropriate grounding, shielding
and the other protective steps should be taken at the installation stage to prevent undesirable
effects. The preventions include making control cabinets grounding, cables shield grounding,
using protective elements for electromagnetic switching devices, using correct wiring as well
as appropriate cable types selection and cable cross-sections.
2.3.2 RS485 Network Termination and Biasing
The transmission line often creates communication problems. These problems include
reflections and signal attenuation.
To eliminate the presence of reflections at the ends of the bus cable, it must be terminated at
both ends with a resistor across the line. The resistor value has to be the same as a
characteristic impedance of the bus cable. Both ends must be terminated since the direction
of propagation is bidirectional. In case of an RS485 twisted pair cable, the termination is
typically 120 Ω.
In the iSMA-B-MAC36NL version there is a built-in 3-position switch on the back side of the
device (access after removing the back cover), which is dedicated to connecting termination
resistor and/or biasing resistors. In the iSMA-B-MAC36NL-RS version a 3-position switch is
installed below a terminal connector, as shown in the figure below on the right side.

iSMA-B-MAC36NL User Manual
Version 1.6 www.globalcontrol5.com Page 12 / 50
Figure 6. Switch for termination and biasing for the base (on left) and optional extension port (on right)
Table 3. Switch Termination and biasing
Switch position
Biasing
Termination 120 Ω +
Biasing
END OFF ON
BIA ON OFF
NONE
OFF
OFF

iSMA-B-MAC36NL User Manual
Version 1.6 www.globalcontrol5.com Page 13 / 50
If the switch is in the END position, it connects the termination resistor 120 Ω and biasing
resistors 680 Ω (pull-down to ground SG and pull-up to +5 V DC) to the RS485 bus.
Instead of using additional resistors, the termination and biasing can easily be done by a
simple switch activation.
Figure 7. RS485 network termination and biasing

iSMA-B-MAC36NL User Manual
Version 1.6 www.globalcontrol5.com Page 14 / 50
If the switch is in the BIA position, it connects the biasing resistors 680 Ω (pull-down to ground
SG and pull-up to +5 V DC) to the RS485 bus. The biasing is added to the RS485 bus in order
to reduce communication failures.
WARNING! Only one single device on the network can have biasing resistors connected.
Connecting biasing resistors on two or more devices on a single RS485 bus will take the
opposite effect–increase the number of communication problems.
Figure 8. RS485 network biasing
2.3.3 M-Bus Connection
M-Bus devices can be connected directly only to the iSMA-B-MAC36NL-M, the controller’s
hardware version with the M-Bus interface (max. 20 devices).
Figure 9. M-Bus connection

iSMA-B-MAC36NL User Manual
Version 1.6 www.globalcontrol5.com Page 15 / 50
2.4 Detection of the Device Extension
Starting from the iSMA-B-MAC36NL hardware version 2.1 and up, the device extension is
detected automatically and displayed for information in the Products field of the Workbench
platform.
2.5 LED Indicators
The device is equipped with LEDs for quick status checking and diagnostics:
Figure 10. LEDs on the front panel of iSMA-B-MAC36NL.
•The power LED ON lights up (green), and then turns the power supply on.
•The communication LED COM1 lights up (orange) for 20 ms in the transmit state for
sending each package through the main RS485 port. As long as the device sends
packages, the communication LED blinks continuously.
•The communication LED EXT lights up (orange) for 20 ms in the transmit state for
sending each package through the extension RS485 port. As long as the device sends
packages, the communication LED blinks continuously.
•The communication LEDs ETH1 and ETH2 light up (orange) in the transmit or receive
state when sending/receiving each package through the particular Ethernet port. As
long as the device sends/receives packages, the communication LEDs blink
continuously.
•The universal inputs LEDs U1-U16 indicate the statuses of the universal inputs. If the
LED is ON, the resistance value connected to the input is lower than the switching
threshold value (dry contact input is active).
Note: The LED also lights up if the voltage connected to the input has a very low potential.
•The digital inputs LEDs I1-I4 indicate the statuses of the digital inputs. If the LED is ON,
the input is active (resistance value connected to the input is lower than the switching
threshold value).
•The analog outputs LEDs A1-A8 indicate the statuses of the analog outputs. If the LED

iSMA-B-MAC36NL User Manual
Version 1.6 www.globalcontrol5.com Page 16 / 50
is ON, the output voltage or PWM factor is different than 0.
•The digital outputs LEDs O1-O8 indicate the statuses of the digital outputs. If the LED
is ON, the output is active (closed circuit).
•The status LED RUN does not light if the power is connected. After the operating
system (Linux) has started up, the LED RUN lights up continuously (green). Next, after
the Platform has started up, the LED RUN also flashes very quickly. If a station exists
in the controller, after the station has been started up and it operates correctly, the LED
RUN flashes slowly (1Hz).
•The alarm LED ∆(triangle with an exclamation mark) lights up in red color if there is no
SD card inserted, or there is a problem with the SD card connection/reading/writing.
•With Niagara 4.9 and up, the alarm LED ∆ supports a station fault, removal, and
stopping state, and indicating these station states with in red color.
2.6 Mini USB
The mini USB port is dedicated to debugging connection through the console.
A description, how to connect to the system console, is included in Chapter 3.6 Connection to
the Console.
Figure 11. LEDs on the front panel of iSMA-B-MAC36NL.

iSMA-B-MAC36NL User Manual
Version 1.6 www.globalcontrol5.com Page 17 / 50
2.7 Local I/O
The iSMA-B-MAC36NL has built-in different types of I/O. The specific local I/O set 16x UI, 8x
AO, 4x DI,and 8x DO allows to use the device in different applications. For the detailed
description of the local I/O set please refer to the Local IO User Manual, available at the
support.gc5.pl.
3Start-up
3.1 Before the Start
To be able to operate normally, the device needs to have:
1. its SD card fitted in SD card box, and
2. its license assigned.
The hardware itself is only the base for the SD card, which consists of all the software parts
necessary for hardware management.
The SD card is not assigned to a particular hardware unit. It can be moved to another
controller. This function allows for easy hardware replacement. Together with the SD card all
the parameters, such as the communication settings, station, Niagara, JVM, and operation
system, are moved.
The license file provides a limited number of points, which can be used to build the application.
Without the license file, the user is not allowed to run the station on the device.
3.2 SD Card
Without the microSD card the device cannot operate properly.
The microSD Card contains all main software parts, which are crucial for the device
functioning:
1. Linux operating system;
2. Java Virtual Machine;
3. Niagara N4.
The card slot is placed on the left side of the device, as it is shown in the figure below.

iSMA-B-MAC36NL User Manual
Version 1.6 www.globalcontrol5.com Page 18 / 50
The microSD card must be inserted into the unit prior to the mounting process. However, it is
possible to move the SD card from one unit to another (the microSD card is not assigned to
the particular hardware iSMA-B-MAC36NL unit). For example, the SD card may be removed
from a unit that suffered a hardware failure and used it in a replacement unit.
How to remove the SD card:
•All power to the controller needs to be shut down before inserting/removing the micro
SD card; otherwise equipment damage may occur.
•The controller needs to be unmounted from any DIN rail or screw tab mounting, as
accessing the card requires access to the space behind the mounting base.
•Discharge any static electricity, which may have been accumulated, by touching a
known, securely grounded object.
Figure 12. SD Card Mounting
•Insert the micro SD card by sliding the card into the card socket, label side down, until
the spring catch engages.
•Remove the micro SD card by pushing the card in, until the spring release pushes the
card partially out of the card socket. Grasp the card, and pull it completely out of the
unit. Store the micro SD card in a static-free protective case.

iSMA-B-MAC36NL User Manual
Version 1.6 www.globalcontrol5.com Page 19 / 50
3.3 Factory Settings
Out of the box, the SD card image has the factory settings. Whenever the controller is restored
via clean or update distribution file, the default settings are restored. Please refer to Chapter
Controller System Update for more details.
WARNING! The cleaning deletes the station–please save it before update!
The factory settings can be divided into two groups:
3.3.1 Factory Communication Settings
•ETH1 IP Address: 192.168.1.123;
•ETH2 IP Address: Disabled;
•Subnet Mask: 255.255.255.0;
•Default Gateway: 192.168.1.1;
•Nameserver (DNS): 192.168.1.1;
•Host Name : MACNL.
3.3.2 Factory Platform Credentials
•User: tridium;
•Password: Niagara.
Out of the box, the controller has no default station installed.
Note:In Niagara 4.6 and later versions, the user is requested to change the factory platform
credentials at the first platform logging.
Note: Starting from the iSMA-B-MAC36NL hardware version 2.1, the passphrase is saved on
the SD card. For controllers firstly commissioned in the Niagara 4.4 version, once the Niagara
Framework is upgraded to 4.8 version or later, the passphrase resets to default “niagara”;
therefore, the station will not restart automatically, and it is required to re-enter the passphrase
and manually restart the station.

iSMA-B-MAC36NL User Manual
Version 1.6 www.globalcontrol5.com Page 20 / 50
Figures 13 and 14. Passphrase reset
3.4 First Login to the Controller Platform in Workplace
WARNING! It is highly advisable to install the Data Recovery Service with the first
commissioning of the controller. See more in the point 3.10.
After opening the Workplace software, to log into the controller for the first time, please do the
following steps:
•Click File > Open > Open Platform in the menu bar.
•The Open Platform dialog window appears.
•Fill the fields in the Open Platform dialog window as follows:
•Type: select Image Platform Connection, if not already selected.
Note:Workbench may by default be set to a secure image platform TLS connection. If so, for
any new controller change the type to a regular (non-TLS) platform connection. After
conversion, the recommended TLS platform connection should always be used.
•Host: leave at default IP, and type in the default IP address of the new controller (the
default IP address is 192.168.1.123);
•Port: leave the default 3011 port number.
•Credentials:
oUsername: type in the factory default username (tridium);
oPassword: type in the factory default password (niagara);
•Click the OK button to accept all settings.
Other manuals for iSMA-B-MAC36NL
4
This manual suits for next models
3
Table of contents
Other iSMA Controllers manuals
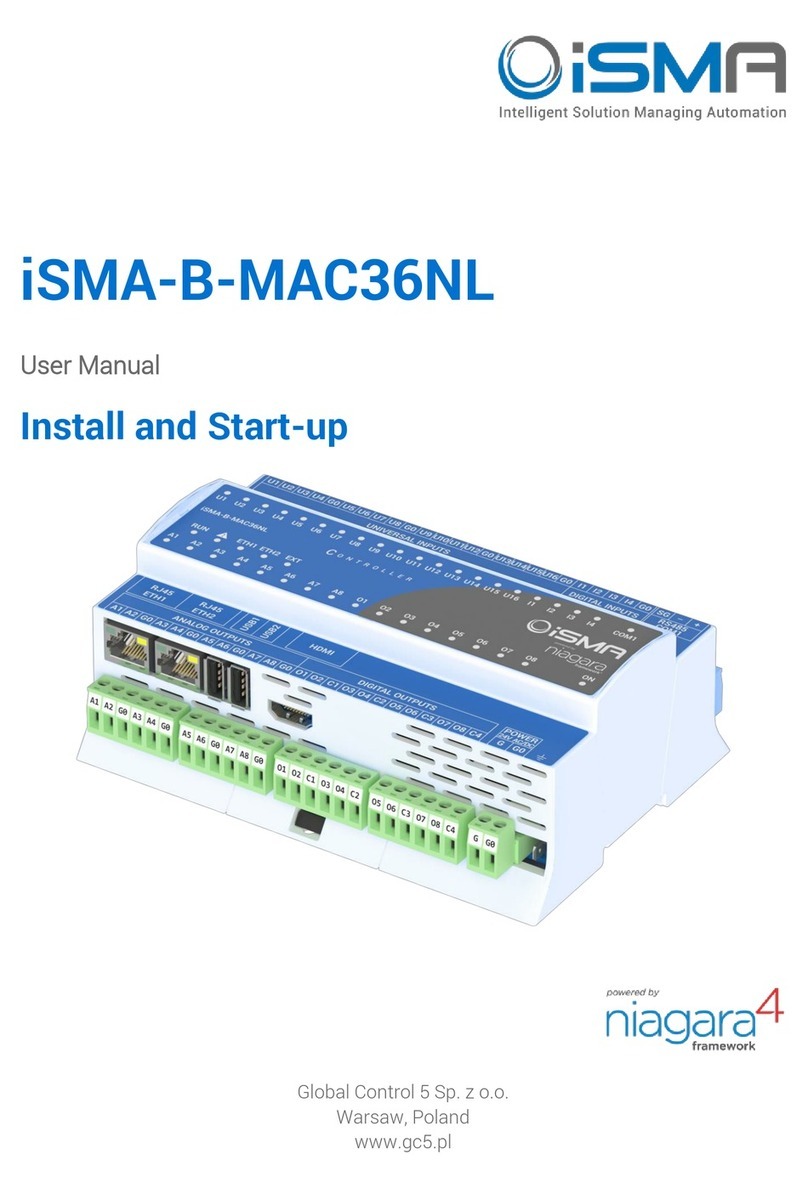
iSMA
iSMA iSMA-B-MAC36NL User manual
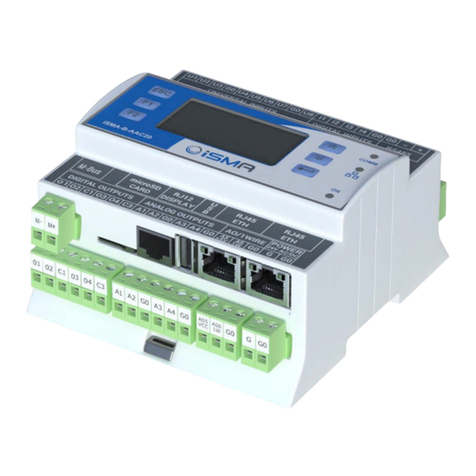
iSMA
iSMA B-AAC20 User manual
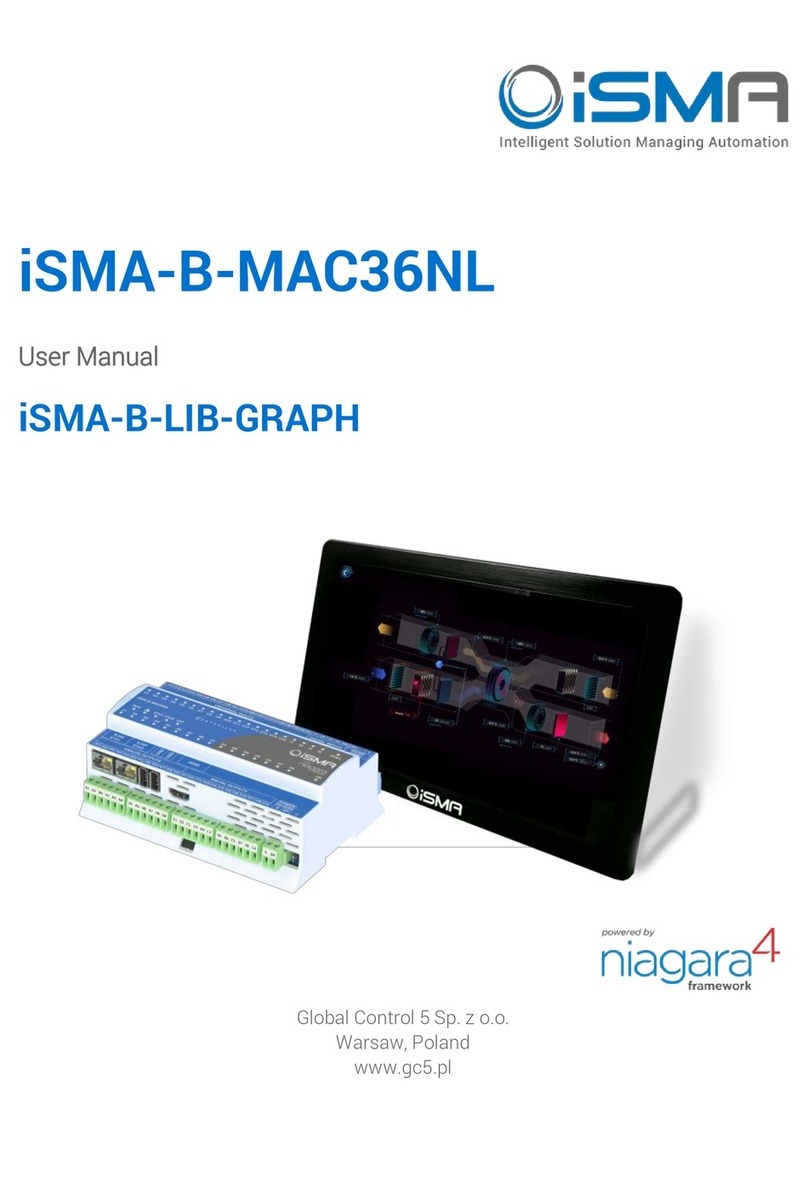
iSMA
iSMA iSMA-B-MAC36NL User manual
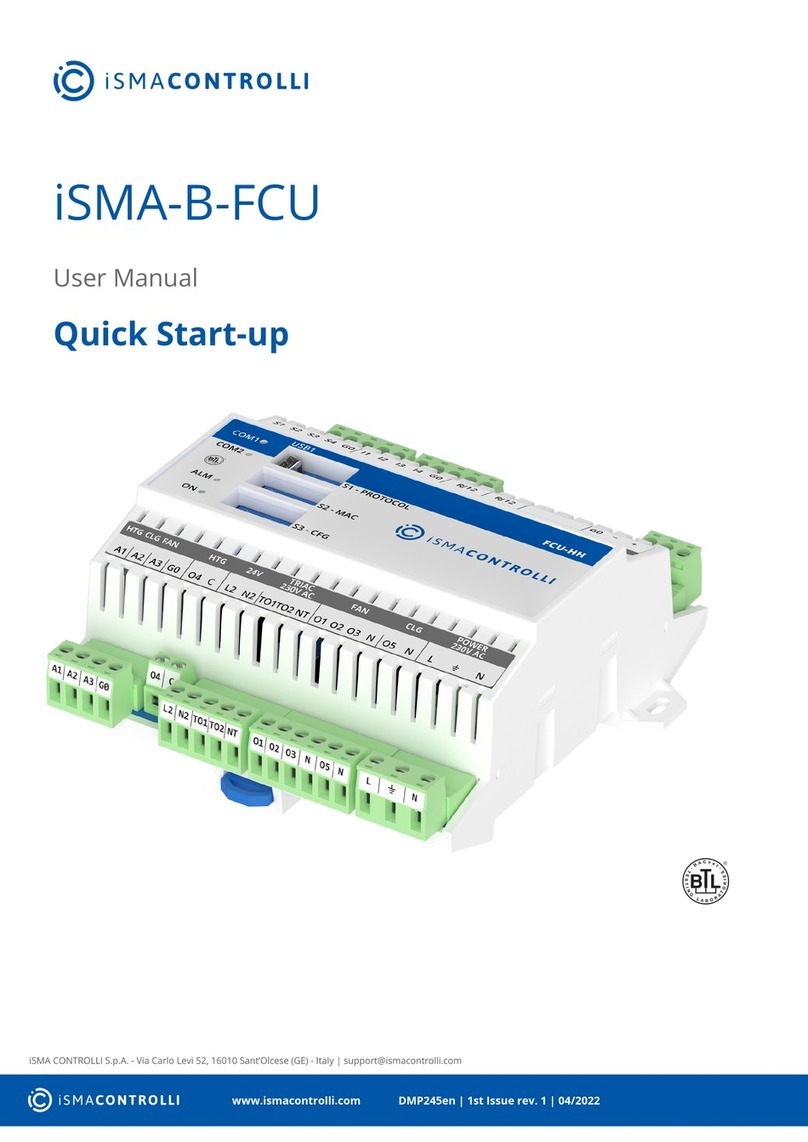
iSMA
iSMA B-FCU User manual
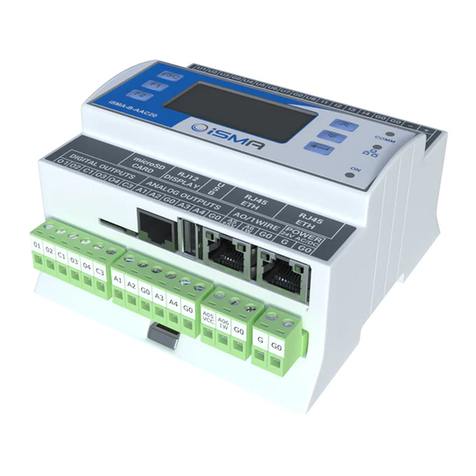
iSMA
iSMA iSMA-B-AAC20 User manual
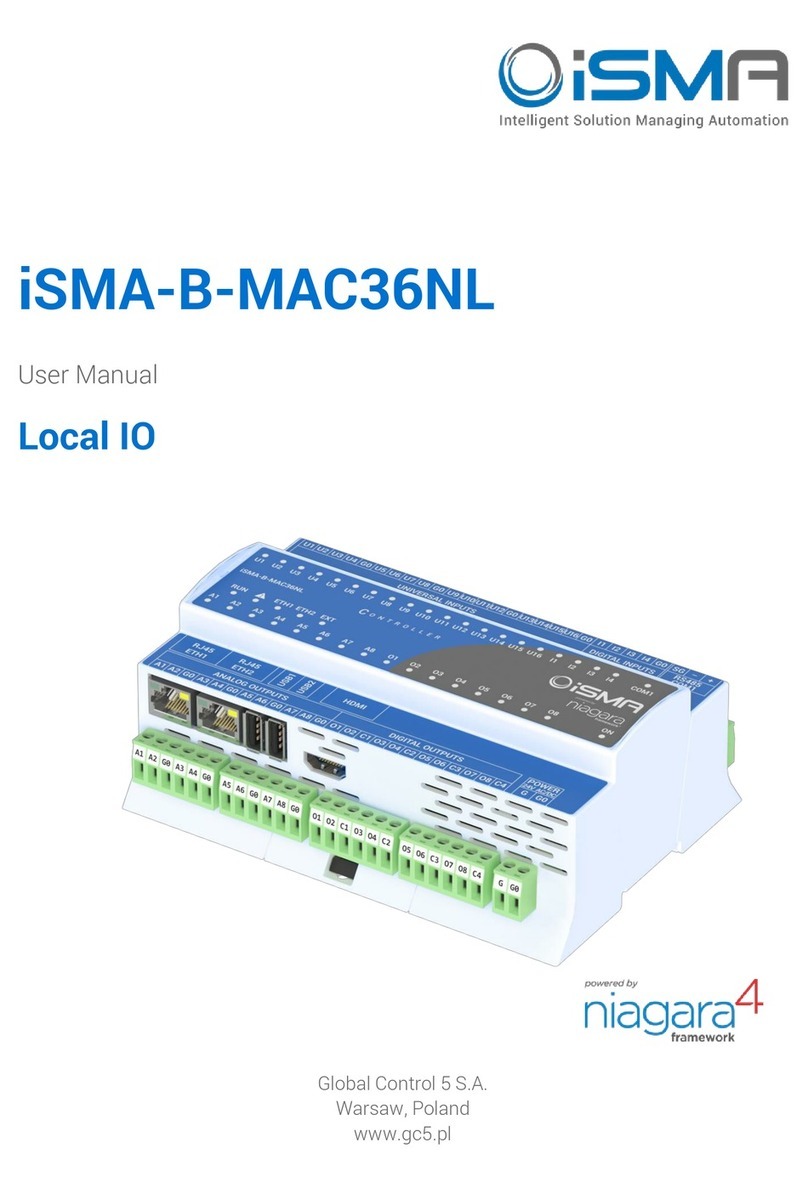
iSMA
iSMA iSMA-B-MAC36NL User manual
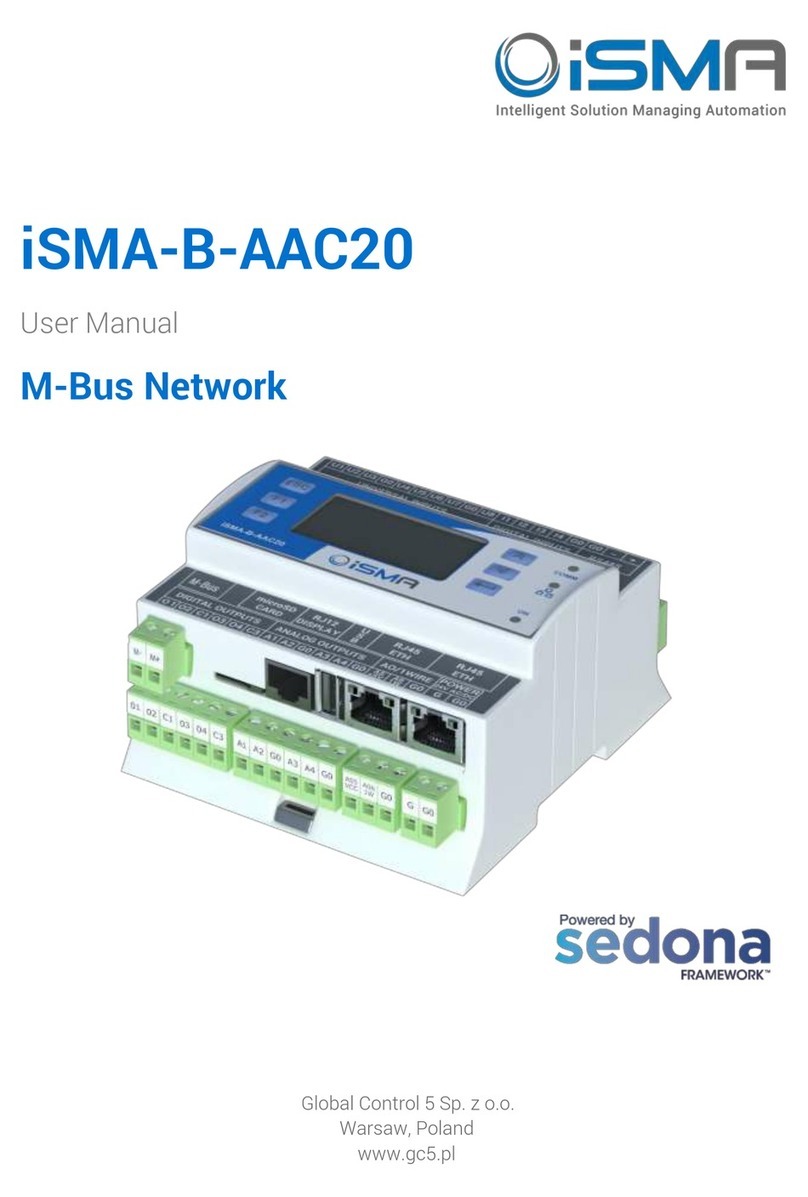
iSMA
iSMA iSMA-B-AAC20 User manual
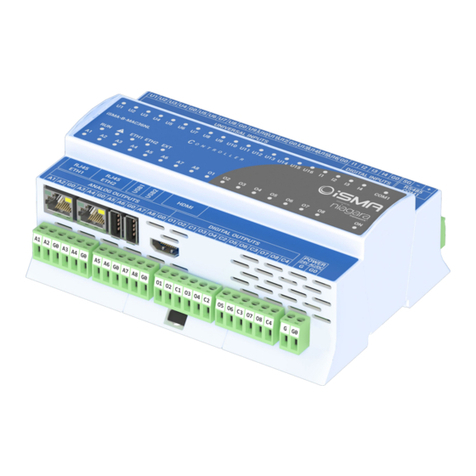
iSMA
iSMA iSMA-B-MAC36NL User manual
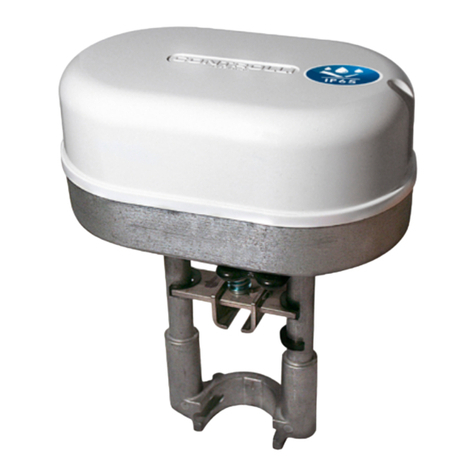
iSMA
iSMA MVE2 Series User manual
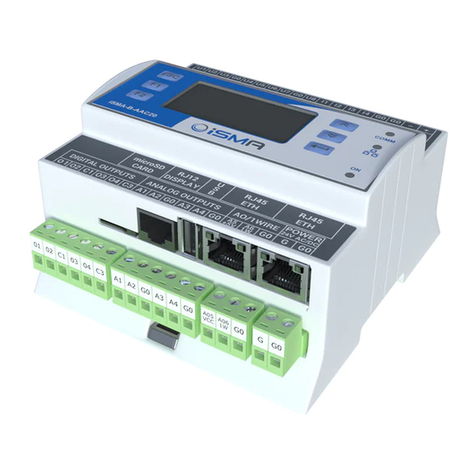
iSMA
iSMA iSMA-B-AAC20 User manual