Lenze MCS 09 Guide

Geared servo motors
g500-H / MCS helical geared servo motor
Mounng and switch-on instrucons EN


Contents
About this document 5
Document descripon 5
Further documents 5
Notaons and convenons 6
Safety instrucons 7
Basic safety instrucons 7
Applicaon as directed 7
Residual hazards 8
Product informaon 10
Idencaon of the products 10
Nameplates 10
Product codes 11
Equipment 14
Transport 15
Storage 17
Mechanical installaon 18
Important notes 18
Preparaon 18
Installaon 19
Mounng posions 19
Venlaon 20
Dimensions 24
Mounng 24
Electrical installaon 25
Important notes 25
Preparaon 25
Motor connecon 26
Connecon via terminal box 26
Connecon via ICN connector 29
Commissioning 36
Important notes 36
Before inial switch-on 36
Funconal test 37
Maintenance 38
Maintenance intervals 39
Maintenance work 41
Repair 47
Diagnoscs and fault eliminaon 48
Malfuncons 48
Contents
3

Technical data 49
Standards and operang condions 49
Conformies and approvals 49
Protecon of persons and device protecon 49
EMC data 49
Environmental condions 50
Motor data 51
Rated data 51
Inverter power supply 400 V, self-venlated motors 51
Inverter power supply 400 V, forced venlated motors 57
Inverter power supply 230 V, self-venlated motors 61
Environmental notes and recycling 64
Contents
4

About this document
WARNING!
Read this documentaon carefully before starng any work.
▶Please observe the safety instrucons!
Document descripon
This document is intended for skilled personnel who work with the products described.
The data and informaon compiled in this document serve to support you in the electrical and
mechanical installaon and commissioning.
•The document is only valid together with the complete documentaon of the product!
•For safety-rated aachments observe the enclosed operang instrucons of the
manufacturer!
•The document includes safety instrucons which must be observed.
•All persons working on and with the drives must have the documentaon at hand during
work and observe the informaon and notes relevant for it.
•The documentaon must always be complete and in a perfectly readable state.
Further documents
Informaon and tools with regard to the Lenze products can be found on the
Internet:
www.Lenze.com à Downloads
About this document
Document descripon
5

Notaons and convenons
Convenons are used in this document to disnguish between dierent types of informaon.
Numeric notaon
Decimal separator Point Generally shown as a decimal point.
Example: 1 234.56
Warnings
UL Warnings UL Are used in English and French.
UR warnings UR
Text
Engineering Tools " " Soware
Example: "Engineer", "EASY Starter"
Icons
Page reference ¶Reference to another page with addional informaon.
Example: ¶ 16 = see page 16
Documentaon reference ,Reference to other documentaon with addional informaon.
Example: , EDKxxx = see documentaon EDKxxx
Layout of the safety instrucons
DANGER!
Indicates an extremely hazardous situaon. Failure to comply with this instrucon will result
in severe irreparable injury and even death.
WARNING!
Indicates an extremely hazardous situaon. Failure to comply with this instrucon may result
in severe irreparable injury and even death.
CAUTION!
Indicates a hazardous situaon. Failure to comply with this instrucon may result in slight to
medium injury.
NOTICE
Indicates a material hazard. Failure to comply with this instrucon may result in material
damage.
About this document
Notaons and convenons
6

Safety instrucons
Basic safety instrucons
Disregarding the following basic safety instrucons and safety informaon may lead to severe
personal injury and damage to property!
•Only use the product as directed.
•Never commission the product in the event of visible damage.
•Never modify the product technically.
•Never commission the product before assembly has been completed.
•Never operate the product without the required covers.
•Connect/disconnect all pluggable connecons only in deenergized condion!
•Only remove the product from the installaon in the deenergized state.
•The product can – depending on their degree of protecon – have live, movable or
rotang parts during or aer operaon. Surfaces can be hot.
•Observe all specicaons of the corresponding documentaon supplied. This is the
condion for safe and trouble-free operaon and the achievement of the specied
product features.
•The procedural notes and circuit details given in the associated documentaon are
suggesons and their transferability to the respecve applicaon has to be checked. The
manufacturer of the product does not take responsibility for the suitability of the process
and circuit proposals.
•All work with and on the product may only be carried out by qualied personnel.
IEC 60364 and CENELEC HD 384 dene the qualicaons of these persons:
-They are familiar with installing, mounng, commissioning, and operang the product.
-They have the corresponding qualicaons for their work.
-They know and can apply all regulaons for the prevenon of accidents, direcves, and
laws applicable at the place of use.
Applicaon as directed
•The product is a professional equipment intended for use by trades, specic professions or
industry and not for sale to the general public. IEC 60050 [IEV 161‑05‑05]
•To prevent personal injury and damage to property, higher-level safety and protecon
systems must be used!
•All transport locks must be removed.
•Mounted eye bolts on the motor are not suitable for transporng geared motors.
•The product may only be operated under the specied operang condions and in the
specied mounng posions.
•The product may only be operated on the inverter.
•Built-in brakes must not be used as safety brakes.
•The product must not be operated in private areas, in potenally explosive atmospheres
and in areas with harmful gases, oils, acids and radiaon.
Safety instrucons
Basic safety instrucons
7

Residual hazards
Even if notes given are taken into consideraon and protecve measures are implemented,
the occurrence of residual risks cannot be fully prevented.
The user must take the residual hazards menoned into consideraon in the risk assessment
for his/her machine/system.
If the above is disregarded, this can lead to severe injuries to persons and damage to
property!
Product
Observe the warning labels on the product!
Dangerous electrical voltage:
Before working on the product, make sure there is no voltage applied to the power terminals!
Aer mains disconnecon, the power terminals will sll carry the hazardous electrical voltage
for the me given next to the symbol!
High leakage current:
Carry out xed installaon and PE connecon in compliance with:
EN 61800‑5‑1 / EN 60204‑1
Hot surface:
Use personal protecve equipment or wait unl the device has cooled down!
Protecon of persons
•The power terminals may carry voltage in the switched-o state or when the motor is
stopped.
-Before working, check whether all power terminals are deenergized.
•Voltages may occur on the drive components (e.g. capacive, caused by inverter supply).
-Careful earthing in the marked posions of the components must be carried out.
•There is a risk of burns from hot surfaces.
-Provide protecon against accidental contact.
-Use personal protecve equipment or wait unl the device has cooled down.
-Prevent contact with ammable substances.
•There is a risk of injury due to rotang parts.
-Before working on the drive system, ensure that the motor is at a standsll.
•There is a risk of accidental start-up or electric shock.
Motor protecon
•Installed temperature sensors are no full protecon for the machine.
-If necessary, limit the maximum current. Parameterize the inverter so that it will be
switched o aer some seconds of operaon with I > Irated, especially if there is a risk
of blocking.
-Integrated overload protecon does not prevent overloading under all condions.
•The fuses are no motor protecon.
-Use a current-dependent motor protecon switch.
-Use the built-in temperature sensors.
Safety instrucons
Residual hazards
8

Gearbox protecon
•Excessive vibraon acceleraons and resonances will damage the gearbox.
-Do not operate the gearbox at vibraon acceleraons > 2 g (20 m/s2) of the machine.
-Do not operate the gearbox in the resonance range of the machine.
•Excessive torques will damage the gearboxes.
-Do not exceed the output torques specied on the nameplate.
•Excessive input speeds lead to increased temperatures.
-Do not exceed the input speeds specied on the nameplate.
•Avoid excessive lateral forces on the gearbox sha.
-Align the shas of the gearbox and driven machine exactly with each other.
•Machine elements can be damaged by a lack of lubricant.
-Mount the gearbox only in the mounng posion indicated on the nameplate.
-When changing the lubricant, use the lubricant type and quanty specied on the
nameplate.
Safety instrucons
Residual hazards
9

Product informaon
Idencaon of the products
Nameplates
The nameplate is aached to the motor.
l
DE
2
10.1
8.2
10.2
7.7
10.3
7.8
10.4 8.3
9
10
8.1
18
14
3 7.6
12.1
4
13
7.3
7.4 7.5
16
11.1
11
7.2
15
19
1
12.2
12.3
11.2 11.3
7.1
17
5.7
5.9 5.8 5.4
Pos. Contents Pos. Contents
1Manufacturer/producon locaon 9 Encoder type designaon
2 Motor type/standard 10 Brake data
3 Gearbox type 10.1 Brake type
4 Motor type 10.2 AC/DC brake voltage
5.4 Rao (gearbox) 10.3 Performance
5.7 Load capacity (gearbox) 10.4 Braking torque
5.8 Output speed (geared motor) 11 Fan specicaons
5.9 Output torque (geared motor)t 11.1 AC/DC fan voltage
7.1 Rated voltage/motor voltage 11.2 Rated frequency
7.2 Rated current/motor current 11.3 Electrical power input
7.3 Rated power/motor power 12.1 Material number
7.4 Output torque (motor) 12.2 Serial number
7.5 Motor speed [rpm] 12.3 Year of manufacture/week of manufacture
7.6 Motor code for controller parameterizaon (C86 Y 1.
Frequency)
13 Bar code
7.7 Rated frequency 14 Permissible ambient temperature
7.8 Cos phi 1. Frequency 15 Weight
8.1 Temperature class (motor) 16 UL le number
8.2 Degree of protecon (motor) 17 Conformity/approvals
8.3 Motor protecon 18 Connuous standsll torque M0 [Nm]
19 Addional customer data
Product informaon
Idencaon of the products
Nameplates
10

Product codes
Gearbox product code
Example G 50 A H 045 M V C R 2 C 1A
Product type Gearboxes G
Product family 50
Generaon A
B
Gearbox type Helical gearbox H
Output torque 45 Nm 045
100 Nm 110
140 Nm 114
210 Nm 121
320 Nm 132
450 Nm 145
600 Nm 160
850 Nm 185
1500 Nm 215
3000 Nm 230
5000 Nm 250
8000 Nm 280
14000 Nm 314
Type of construcon Geared motor M
Gearboxes N
Sha type Solid sha with featherkey V
Solid sha without featherkey G
Housing type Foot mounng + centering A
Foot mounng B
With centering C
Flange mounng Without ange R
Flange with through holes K
Reinforced ange with through
holes P
Number of stages 2-stage 2
3-stage 3
4-stage 4
Motor mounng Integrated motor C
IEC adapter with jaw coupling N
T
IEC adapter with plug-in hollow
sha
H
NEMA adapter with jaw coupling A
NEMA adapter with plug-in
hollow sha
B
Servomotor adapter with plug-in
hollow sha
S
Servomotor adapter with jaw
coupling
E
D
G
Drive size
1A
...
□H
08
...
82
Product informaon
Idencaon of the products
Product codes
11

Product code of MCS synchronous servo motor
Example M C S 06 C 41 - RS0 B0
Meaning Variant Product code
Product family Motor M
Type Compact servo motors C
Version Synchronous S
Motor frame size Square dimension 62 mm 06
Square dimension 89 mm 09
Square dimension 116 mm 12
Square dimension 142 mm 14
Square dimension 192 mm 19
Overall length C
...
P
Rated speed rpm x 100 11
...
60
Inverter mains connecon 3 x 230 V L
3 x 400 V -
Feedback SinCos absolute value encoder, single-turn, EnDat
AS2048-5V-E
ECN
Digital absolute value encoder, mul-turn,
Hiperface DSL®
AM20-8V-D
EKM
SinCos absolute value encoder, mul-turn, EnDat
AM32-5V-E
EQI
SinCos absolute value encoder, mul-turn, EnDat
AM2048-5V-E
EQN
Digital safety absolute value encoder, mul-turn,
Hiperface DSL®
AM20-8V-D2
EVM
Resolver p=1 RS0
Safety resolver, p=1
RV03
RV0
SinCos absolute value encoder, mul-turn,
Hiperface®
AM128-8V-H
SKM
SinCos absolute value encoder, mul-turn,
Hiperface®
AM1024-8V-H
SRM
SinCos absolute value encoder, single-turn,
Hiperface®
AS1024-8V-H
SRS
SinCos safety absolute value encoder, mul-turn,
Hiperface®
AM128-8V-K2
SVM
SinCos safety absolute value encoder, mul-turn,
Hiperface®
AM1024-8V-K2
SVM
SinCos safety absolute value encoder, single-turn,
Hiperface®
AS1024-8V-K2
SVS
Brake Without brake B0
Permanent magnet brake DC 24V P1
Permanent magnet brake DC 24V, reinforced P2
Product informaon
Idencaon of the products
Product codes
12

Product code feedbacks
Example AS 1024 - 8 V - K 2
Meaning Variant Product code
Product family Resolver RS
Resolver for safety funcon RV
Incremental encoder IG
Incremental encoder with commutaon
signal
IK
Absolute value encoder, singleturn AS
Absolute value encoder, multurn AM
Number 2-pole Resolver for servo motors 0
2-pole Resolver for three-phase AC
motors
1
Number of pole pairs for resolvers 2
3
4
...
Number of bits, steps or increments per
revoluon
20
32
128
512
1024
2048
...
Supply voltage 5 V
8 V
15 V
24 V
...
Interface or signal level Standard
TTL T
HTL (for incremental encoders) H
Hiperface (for absolute value encoders) H
EnDat E
SinCos 1 Vss S
Digital D
For safety funcon
TTL U
HTL (for incremental encoders) K
Hiperface (for absolute value encoders) K
EnDat F
SinCos 1 Vss V
Digital D
Safety Integrity Level (SIL) 1
2
3
4
Product informaon
Idencaon of the products
Product codes
13

Equipment
The following gure provides an overview of the elements and connecons on the product.
Their posion, size and appearance may vary.
(depending on the mounting position)
Oil level check
(depending on the mounting position)
Oil drain plug
(depending on the mounting position)
Oil filler plug
(depending on the mounting position)
Ventilation
Housing type
Output flange
Output shaft
Temperature monitoring
Permanent magnet brake
Feedback
Motor connection
Cooling
Product informaon
Equipment
14

Transport
•Ensure appropriate handling.
•Make sure that all component parts are securely mounted. Secure or remove loose
component parts.
•Only use safely xed transport aids (e.g., eye bolts or support plates).
•Do not damage any components during transport.
•Avoid electrostac discharges on electronic components and contacts.
•Avoid impacts.
•Check the carrying capacity of the hoists and load handling devices. The weights can be
found in the shipping documents.
•Secure the load against pping and falling down.
•Standing beneath suspended loads is prohibited.
The transport weights can be found in the shipping documents!
The motors mounted on the gearbox are somemes equipped with ears. These
are exclusively intended for mounng the motor on/removing the motor from
the gearbox and must not be used for the complete geared motor!
CAUTION!
Danger from pping or falling loads!
Standing beneath suspended loads is prohibited!
▶Use addional appropriate liing aids, if required, to achieve a direcon of loading which is
as vercal as possible (highest load carrying capacity). Secure liing aids against shiing!
▶Screw in the transport aids completely. They must have even and full-surface contact!
▶Transport aids must be loaded vercally in the direcon of the screw axis! Diagonal or
lateral tension reduces the load carrying capacity! Observe data in standard DIN 580!
The thread in the output sha can be used with smaller drives. Larger gearboxes have a
transport thread for eye bolts in accordance with DIN 580 in the gearbox housing as standard.
The eye bolt is not included in the scope of supply!
The posion of the transport thread can be seen in the following representaons.
Transport
15

Posion of the eye bolt
G50AH045 ... G50BH114 G50BH121 ... G50BH230
1. 2.
Thread M6 M8 M10 M12 M16 M20 M24
Load carrying
capacity
kg 80 140 230 340 700 1200 1800
Transport
16

Storage
Storage up to one year:
•Observe the climac condions according to the technical data
-4Environmental condions ^ 50
•Store in a dry, low-vibraon environment (Ve < 0.2 mm/s) without aggressive atmosphere
in the interior
•Protect from dust, shocks and sunlight
•Avoid temperature changes with condensate formaon.
•Store gearboxes with a venlaon unit with the venlaon element on top.
•Do not acvate venlaon unit, in order to prevent air exchange with the ambient air.
•Treat damaged corrosion protecon on shas and bare surfaces subsequently
Storage for more than one year, up to two years:
•Apply a long−term corrosion prevenve (e.g. Ancorit BW 366 from the Fuchs company) to
the shas and uncoated surfaces before storing the motor away.
•Do not acvate venlaon element
•Install gearbox in mounng posion M1 (A)
•Fill gearbox with the lubricant type lled in (see nameplate) up to the lling/venng bore
for mounng posion M1 (A)
-4Nameplates ^ 10
-4Venlaon ^ 20
Storage
17

Mechanical installaon
Important notes
•Install the product according to the informaon in the chapter "Standards and operang
condions".
4Standards and operang condions ^ 49
•The technical data and the data regarding the supply condions can be found on the
nameplate and in this documentaon.
•Ambient media − especially chemically aggressive ones − may damage sha sealing rings,
lacquers and plascs.
•Lenze oers special surface and corrosion protecon in this case.
•Only install the gearbox in the mounng posion shown.
4Mounng posions ^ 19
Preparaon
•Protect sha sealing rings from contact with solvents.
•Remove protecon covers from shas.
•Thoroughly remove ancorrosion agents from the sha and from ange faces.
•Draw the transmission elements onto the output sha only by using the centering thread.
•Align the output sha and transmission elements exactly to avoid tensions.
•Mount belt pulleys, sprockets, or gear wheels as close as possible to the sha shoulder in
order to keep the bending load of the sha and the bearing forces at a minimum level.
•Tighten all screw connecons with the specied torques and secure them with standard
screw locking adhesive.
•Check paint for damage and repair professionally.
Mechanical installaon
Important notes
18

Installaon
•The mounng surfaces must be plane, torsionally rigid and free from vibraons.
•The mounng areas must be suited to absorb the forces and torques generated during
operaon.
•Ensure an unhindered venlaon.
•For versions with a fan, keep a minimum distance of 10 % from the outside diameter of the
fan cover in intake direcon.
Mounng posions
M1 [ A ]
M2 [ D ]
M5 [ F ]
M3 [ B ]
M4 [ C ]
M6 [ E ]
Mechanical installaon
Installaon
Mounng posions
19

Venlaon
No venlaon is required for the gearboxes G50AH045 …BH121.
The gearbox G50BH121 can oponally be ed with venlaon units.
From G50BH132onwards, the gearboxes are supplied with venlaon units as
standard.
Gearboxes that are delivered with a venlaon unit are provided with a label.
Remove the transport locking device on the vent valve before inial commissioning.
Loosely enclosed vent valves must be mounted in accordance with the mounng posion.
G50BH121 ... BH145
Mounng posion M1 (A) Mounng posion M2 (D) Mounng posion M3 (B)
Filling and venlaon
+
+
+
Control
Drain
Mechanical installaon
Installaon
Venlaon
20
This manual suits for next models
11
Table of contents
Other Lenze Engine manuals
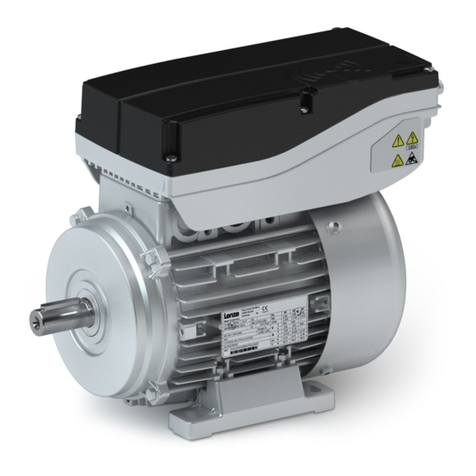
Lenze
Lenze Smart Motor m300 Technical manual

Lenze
Lenze SDSGA User manual

Lenze
Lenze g500 Series User manual

Lenze
Lenze MD KS Series User manual
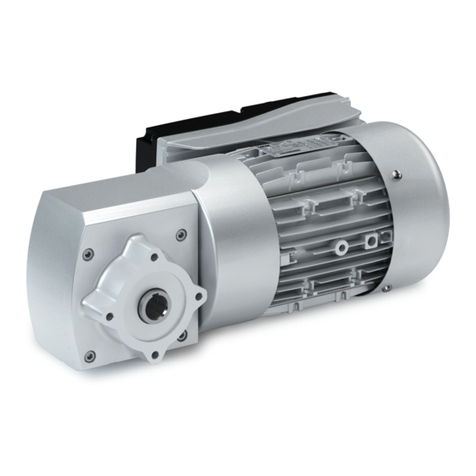
Lenze
Lenze MSEMA 080-32 Series Guide
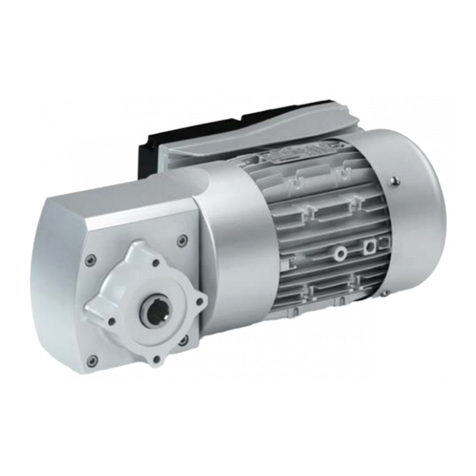
Lenze
Lenze MSEMA Series Technical manual
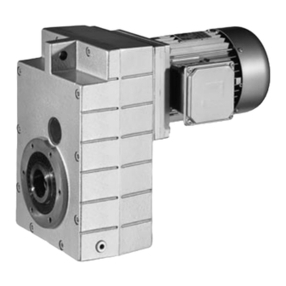
Lenze
Lenze L-force GST User manual
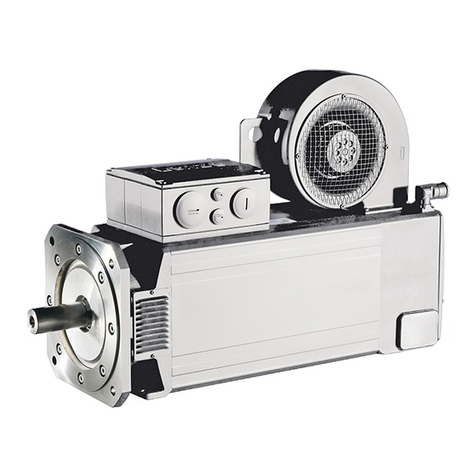
Lenze
Lenze MQA Series Guide
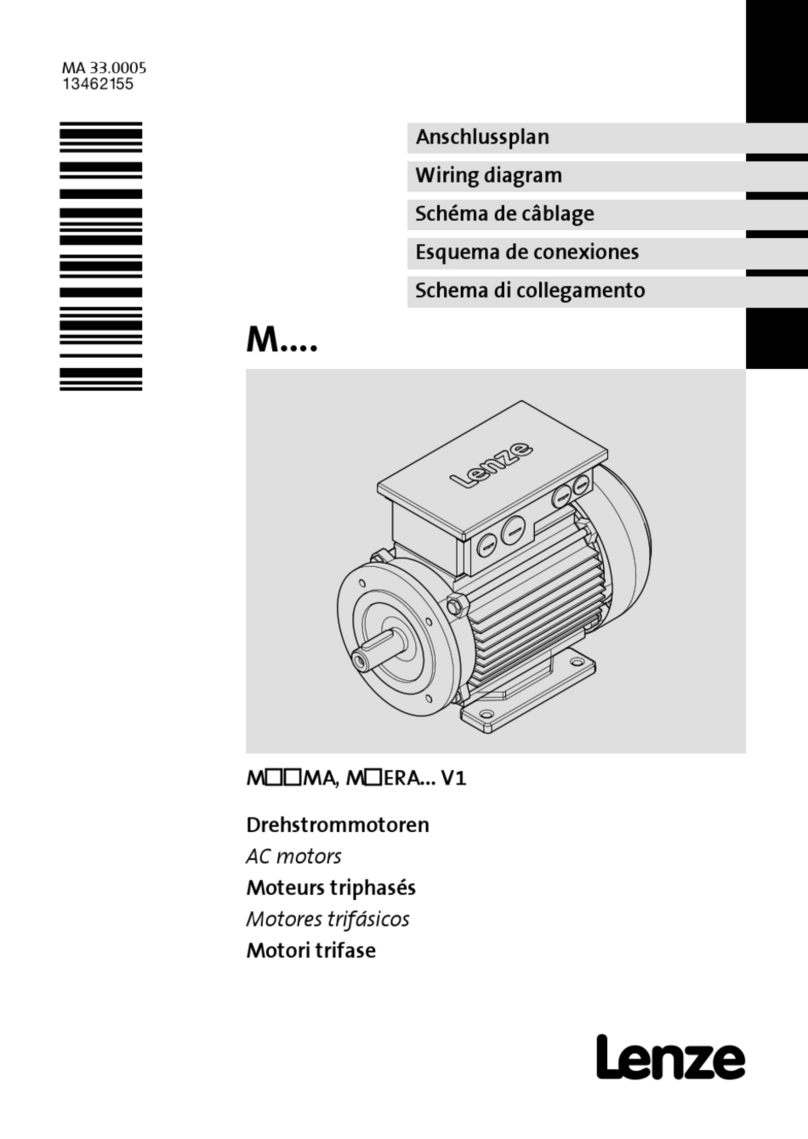
Lenze
Lenze MDERA 056 V1 Series Quick start guide
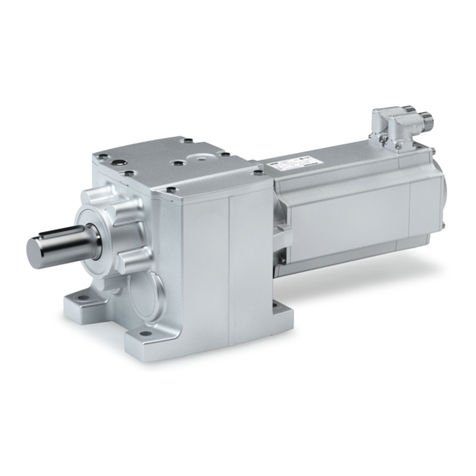
Lenze
Lenze g500-H45 Technical manual