MKS SENTRY 1510A User manual

Instruction Manual #122162 1
SENTRYTM 1510A
and Tool Interface Module
with (Optional) Condenser
Installation & Operation Manual
Instruction Manual part number 122162
Revision E – February 2020
© 2020 MKS Instruments, Inc. All rights reserved.
Granville-Phillips® is a registered trademark of MKS Instruments, Inc.
SENTRYTM is a trademark of MKS Instruments, Inc. All other trademarks
and registered trademarks are the properties of their respective owners.

Instruction Manual #122162 2
Notice
This product is intended for use by industrial customers and should be
serviced only by MKS trained representatives. The service manuals and
related materials are provided in English at no charge and are intended for
use by experienced technicians. It is the responsibility of the user to obtain
and assure the accuracy of any needed translations of manuals. If you
require assistance, contact the MKS Customer Service group. Contact
information can be found on page 3 of this instruction manual and at
www.mksinst.com. The MKS Technical Support Group notifies users of
record if safety-related upgrades or new hazards associated with the product
are identified.
Record the Serial Numbers and Model Numbers
The model number, serial number and revision reference of each component may be found on
the SENTRY Controller and SENTRY Supervisor serial tags. The model number and revision
reference of the cables may be found as a label on each cable. For your convenience, record the
numbers below and retain this manual and information for future reference.
1) SENTRY Controller
Model Number:
Serial Number:
2) SENTRY Supervisor
Model Number:
Serial Number:
4) Tool/Host to SENTRY Supervisor
Interface Cable
Model Number:
-OR-
Stand-Alone Power Supply Cable
Model Number:
3) SENTRY Supervisor to SENTRY
Controller Cable
Model Number:
5) Serial Communication Cable
Model Number:
Other/Special:
SentryTM, Sentry 1510TM, Aerodynamic Resistor ValveTM, and Vacuum Regulation ValveTM
are trademarks of MKS Instruments, Inc.

Instruction Manual #122162 3
Damage Requiring Service
Disconnect the product from all power sources and refer servicing to Qualified Service Personnel under the
following conditions:
a. When any cable or plug is damaged.
b. If any liquid has been spilled onto, or objects have fallen into the product.
c. If the product has been exposed to rain or water.
d. If the product does not operate normally even if you follow the operating instructions. Adjust only those
controls that are covered by the operation instructions. Improper adjustment of other controls may result in
damage and will often require extensive work by a qualified technician to restore the product to its normal
operation.
e. If the product has been dropped or the enclosure has been damaged.
f. When the product exhibits a distinct change in performance. This indicates a need for service.
Service and Warranty Guidelines
Some minor problems are readily corrected on site. If the product requires service, contact the MKS Technical
Support Department at +1-833-986-1686. If the product must be returned to the factory for service, request a
Return Material Authorization (RMA) from MKS. Do not return products without first obtaining an RMA. In some
cases, a hazardous materials disclosure form may be required. The MKS Customer Service Representative will
advise you if the hazardous materials document is required.
When returning products to MKS, be sure to package the products to prevent shipping damage. Shipping damage
on returned products as a result of inadequate packaging is the Buyer's responsibility.
For Customer Service / Technical Support:
MKS Global Headquarters
2 Tech Drive, Suite 201
Andover MA, 01810 USA
Phone: +1-833-986-1686
Email: insidesales@mksinst.com
Visit our website at: www.mksinst.com
Warranty Information
MKS Instruments, Inc. provides an eighteen (18) month warranty from the date of shipment for new MKS products.
The MKS Instruments, Inc. general terms and conditions of sale provide the complete and exclusive warranty for
MKS products. This document is located on our web site at www.mksinst.com, or may be obtained by a contacting
an MKS customer service representative.
Proprietary Information
This document contains confidential proprietary information belonging to MKS Instruments, Inc. This information is
not for publication and has been provided to MKS on the condition that it not be copied, reproduced or disclosed,
either wholly or in part, to third parties without the expressed written consent of MKS Instruments, Inc.
The information contained in this document is subject to change without notice.
The SENTRY Supervisor and related SENTRY technology is covered by one or more of the following patents: U. S.
Pat Nos. 5,000,221; 5,220,940; 5,251,654; 5,255,709; 5,255,710; 5,320,124; 5,450,873; 5,456,280; 5,582,203;
5,597,011; 5,634,490; 5,655,562; and 5,664,600 and European Pat. No. 0 491 684. Other patents are pending.

Instruction Manual #122162 4
Table of Contents
1. Safety Information ................................................................................................... 5
2. General Description .............................................................................................. 10
2.1 Part Names and Description .............................................................................. 10
3. Quick Start Guide .................................................................................................. 15
3.1 SENTRY 1510 System Installation Checklist ..................................................... 15
4. Guidelines .............................................................................................................. 17
4.1 Installation Guidelines ....................................................................................... 17
4.2 Installation Layout ............................................................................................. 18
5. Installation & Power-Up ........................................................................................ 19
5.1 SENTRY 1510 ................................................................................................... 19
5.2 Drains and P-Traps ........................................................................................... 22
5.3 Process Pressure Sense Tube .......................................................................... 24
5.4 Nitrogen Supply to the SENTRY 1510 ............................................................... 25
5.5 TIM 100/120 Installation .................................................................................... 26
5.6 Power Supply .................................................................................................... 27
5.7 SENTRY Cable Installation ............................................................................... 28
5.8 System Start-Up ................................................................................................ 31
5.9 Condenser (Required for Wet Process) ............................................................. 33
6. Operation ............................................................................................................... 39
6.1 Introduction ....................................................................................................... 39
6.2 Operational Theory ............................................................................................ 39
6.3 Manual (“SINGLE”) Mode Sentry Controller with TIM-100/120 .......................... 41
6.4 Analog Interfaced Operation .............................................................................. 43
6.5 Serial Interfaced Operation ................................................................................ 43
7. Maintenance & Troubleshooting .......................................................................... 44
7.1 Maintenance ...................................................................................................... 44
7.2 Troubleshooting ................................................................................................. 44
8. Appendices ............................................................................................................ 50
8.1 Appendix A: Specifications and Facility Requirements ..................................... 50
8.2 Appendix B: SENTRY 1510 Menu ..................................................................... 51
8.3 Appendix C: Recommended System Grounding ............................................... 52
8.4 Appendix D: Tool/Host to Cable Matrix ............................................................. 53
8.5 Appendix E: Dimensional Drawings .................................................................. 54

Instruction Manual #122162 5
1. Safety Information
Be sure to read these important safety instructions and notes collected here for your
convenience and repeated with additional information at appropriate points throughout
this instruction manual.
These safety alert symbols in this manual or on the Product mean caution - personal safety,
property damage or danger from electric shock. Read these instructions carefully.
This product was designed and tested to offer reasonably safe service provided it is installed,
operated, and serviced in strict accordance with these safety instructions. These safety
precautions must be observed during all phases of operation, installation, and service of this
product. Failure to comply with these precautions or with specific warnings elsewhere in this
manual violates safety standards of design, manufacture, and intended use of the instrument.
MKS Instruments, Inc. disclaims all liability for the customer's failure to comply with these
requirements.
• Read Instructions – Read all safety and operating instructions before operating the product.
• Retain Instructions – Retain the Safety and Operating Instructions for future reference.
• Heed Warnings – Adhere to all warnings on the product and in the operating instructions.
• Follow Instructions – Follow all operating and maintenance instructions.
• Accessories – Do not use accessories not recommended in this manual as they may be
hazardous.

Instruction Manual #122162 6
General Hazards
Failure to review the Safety chapter and follow the safety
warnings can result in serious injury or death.
Do not attempt to perform installation, operation, or
maintenance procedures on the product until you have read and
understand the information in the Safety Chapter.
Read and understand each procedure before performing the
procedure.
Personal Responsibility
It is the responsibility of each person working on this product to
know the applicable regulatory safety codes as well as the
safety procedures, safety equipment, and contact information.
General Safety Considerations
Inappropriate Use
Use of this product in a manner or for purposes other than for
what it is intended may cause equipment damage or personal
injury.
Only use the product for its intended application.
Do not modify this product beyond its original design.
Always operate this product with the covers in place.
Damaged Components
The use of this product when components or cables appear to
be damaged may cause equipment malfunction or personal
injury.
Do not use this product if components or cables appear to be
damaged.
Place the product in a location where it will not get damaged.
Route cables and tubing so that they do not become damaged
and do not present a personal safety hazard.

Instruction Manual #122162 7
This equipment contains no user serviceable part. Refer all
repairs to MKS.
Do not operate this equipment without proper exhaust
connections.
Safety Alert Labels
Safety labels and identification labels are placed on the robot and controller to provide operators
with information. This section describes each label and identifies its location. For safety labels,
instructions are provided on how to avoid the hazard.
Warning Label – Hazardous Voltage
Location: On Power Supply Brick
Possible Injuries: Electric Shock or Burn
How to avoid hazard: Unplug and lockout before service.
Warning Label – Refer to manual
Location: TIM/Valve
Possible Injuries: Various
How to avoid hazard: Read and understand manual
before installation or use of equipment.
Disconnect Devices and Interlocks
Safety Interlocks
This product does not have an Emergency Off (EMO) circuit.
Using this product without an EMO may cause personal injury
or death.
The user must provide a disconnect device for the product
power that complies with local electrical codes.
Personnel servicing this product are responsible for disconnect
as specified by the facility Lockout/Tagout procedures.

Instruction Manual #122162 8
Grounding
The power source to which this product is connected must be properly grounded in accordance
with all electrical codes pertaining to high voltage electrical equipment in an industrial
environment.
See Grounding in the following documentation for more detailed requirements regarding gauge
and system grounding.
Electrical Shock
Improper electrical connection or connection to an improper
electrical supply can result in electrical shock, burns, fire, and
damage to the equipment and death or serious injury.
Always use proper power and proper electrical compliant
connections in accordance with local electrical code.
Fire and Explosion Hazards
The Product provides no direct fire or explosion hazard.
Explosive Environment
Do not use the product in an environment of explosive or
combustible gases or gas mixtures. Operation of any electrical
instrument in such an environment constitutes a definite safety
hazard. Do not use the product to measure the pressure of
explosive gases or gas mixtures.
Damaged Components
This equipment has not been evaluated for use in exhaust lines
containing flammable gases at concentrations at, or in excess
of their Lower Explosive Limit (LEL), or for hazardous locations
and environments.
Responsibility
It is the responsibility of the Customer to comply with all local, state, and federal ordinances,
regulations, and laws applicable to the installation, operation and service of this equipment.
It is the responsibility of the end user to provide sufficient lighting at work to meet local
regulations.
Operation and Service of this equipment in strict accordance with the methods and procedures
supplied by MKS is the responsibility of the Customer.

Instruction Manual #122162 9
MKS Instruments, Inc. assumes no liability, whatsoever, for any personal injuries or damages
resulting from the operation or service of this equipment in any manner inconsistent or contrary
to the methods supplied in MKS literature including, but not limited to, manuals, instructions,
bulletins, communications, and recommendations.
For emergencies and for product safety related matters, contact MKS.
Notice
Do not substitute parts or modify the instrument. Because of the danger of
introducing additional hazards, do not install substitute parts or perform any
unauthorized modification to the product.
Return the product to a service facility designated by MKS for service and
repair to ensure that safety features are maintained. Do not use this product
if it has unauthorized modifications.
Notice
Safety Check - Upon completion of any service or repairs to this product, ask
the Qualified Service Person to perform safety checks to determine that the
product is in safe operating order.
Notice
Finite Lifetime - After ten years of normal use or even non-use, the electrical
insulation in this product may become less effective at preventing electrical
shock. Under certain environmental conditions which are beyond the
manufacturer’s control, some insulation material may deteriorate sooner.
Therefore, periodically inspect all electrical insulation for cracks, crazing, or
other signs of deterioration. Do not use if the electrical insulation has
become unsafe.

Instruction Manual #122162 10
2. General Description
2.1 Part Names and Description
SENTRY 1510 is a mechanical-based process pressure exhaust controller. It is a pressure
regulator designed to respond to static exhaust pressure changes and process flow gas
changes in order to maintain a constant process pressure at the tool.
Nitrogen Supply Port accepts the Nitrogen supply from the tool or facilities required for
proper operation of the SENTRY 1510. A fitting accepting ¼” OD tube or pipe is provided.
Drain Port (plugged) provides a means for connecting a drain line to the SENTRY 1510
when a vertical upward flow configuration is installed. A ¼” FNPT port with plug is provided.
SENTRY 1510 Input Port provides a means for connecting the SENTRY 1510 to the
process exhaust output from the tool.
Flow Direction Arrow indicates the process exhaust flow direction and points from the tool
process exhaust to the facility exhaust.
Mounting Holes provide a means for installing the SENTRY 1510 to a support structure or
the process equipment. Four 10-32 thread holes are provided.
Interface Port accepts the TIM-100/120 to SENTRY 1510 interface cable which supplies the
appropriate power and signal communications to the SENTRY 1510 controller.
Sense Line Port accepts the sense line included with the SENTRY 1510. The tool process
pressure is measured by the internal pressure transducer. A Nitrogen purge is provided to
ensure long-term reliability.
Notice
Do NOT block the Sense Line Port when Nitrogen is turned ON.
Reference Port this port is not currently used on models supplied with this manual. A
limited number of models are available with the reference port operational to allow for differential
pressure control relative to a pressure other than atmosphere.
SENTRY 1510 Output Port provides a means for connecting the SENTRY 1510 to the
facility exhaust.
4
3
2
1
5
6
7
9
10
8

Instruction Manual #122162 11
2.1.1 (Optional) CD-20 Condenser
The optional CD-20 Condenser is designed to work with the SENTRY 1510 as an integrated
system. The CD-20 is designed to remove moisture from wet processing such as steam
oxidation or steam cleaning. Whenever a SENTRY 1510 will see a wet process, a BAI or OEM
comparable condenser is required. See section 5.9 for the “AVP” condenser information. Water
is the only cooling medium approved for the use with the CD-20 Condenser.
CD-20 Input Port provides a means for connecting the CD-20 to the process exhaust output
from the tool.
Cooling Water Input Port accepts a ¼” OD water supply line. The water does not have to
be chilled. Any flow metering device intended to control the water flow must be installed prior to
the input port.
Lower Mounting Bracket is used for mounting the CD-20 to the process tool or other
support structure.
Lexan Outer Wall is an enclosure that provides some impact protection to the internal
quartz tube.
Cooling Water Outlet accepts a ¼” OD water return line. Any flow metering must not be
incorporated on the return line.
Tie Rods secure the condenser tubes and lower mounting bracket with the upper mounting
bracket. No user serviced parts are included The tie rods must not be disconnected.
Upper Mounting Bracket is used for mounting the CD-20 to the process tool or other
support structure.
Connecting Rods are used to secure the SENTRY 1510 to the CD-20 to provide an
integrated pressure and moisture control system.
1
2
4
8
5
3
9
7
6

Instruction Manual #122162 12
Reference Port this port is not currently used on models supplied with this manual. A
limited number of models are available with the reference port operational to allow for differential
pressure control relative to a pressure other than atmosphere.
CD-20 Output Port provides a means for connecting the CD-20 to the facility exhaust.
2.1.2 SENTRY TIM-100/120
Notice
A TIM-100 is shown above. Except for items 3 and 4, the descriptions listed
also apply to the TIM-120. Access to the display and keypad on a TIM-120 is
provided through the use of a Program Module available separately.
SENTRY TIM-100/120 is a microprocessor-based interface used in conjunction with the
Sentry 1510. The TIM-100/120 provides the user with the ability to interface with the SENTRY
1510 controller through direct keypad input or through electronic communication from the
process equipment.
Mounting Brackets are used to mount the TIM-100/120 to the process equipment.
Display provides a real time read-back of pressure control. It also allows the user to view
and change the menu parameters.
Keypad contains the four keys used to navigate and change the menu tree and parameters.
Contrast Knob allows the user to adjust the display contrast.
Power/Interface Port accepts the power cable (power supply) or power and interface cable.
RS 422/485 Port accepts the optional serial communication cable.
On/Off Switch is an on/off rocker connected to a fuse. The fuse acts as a safety cut-off
device by detecting over-current situations and cutting power to the TIM-100/120.
SENTRY Port accepts the TIM-100/120 to SENTRY 1510 controller cable.
Address Switches are used to set the base address of the TIM-100/120 when using the RS
422/485 communication port.

Instruction Manual #122162 13
2.1.3 Display TIM-100/200
Selection Indicator An asterisk symbol [*] will appear in the selection indicator box when a
menu item is chosen by pressing the asterisk key [*] on the keypad.
Menu Item Name Display indicates the current menu item available for modification. The
user can scroll the menu by using of the arrow keys on the keypad.
Exhaust Set Point indicates the currently active (desired) set point. This value indicates
pressure with an implied decimal point (1700 = 17.00 mm H2O).
Menu Item Value Display indicates the current stored value for the menu item displayed.
Process Exhaust (Actual) Read-Back indicates the currently achieved (actual) process
exhaust read-back. This value indicates pressure with an implied decimal point (1700 = 17.00
mm H2O).
Graphical Display The graphical display provides a real-time plot of the process exhaust
read-back.
Full Scale Process Exhaust The full-scale process exhaust indicates the factory configured
full-scale range of the unit being operated. Depending on the SENTRY 1510 model, this value
will indicate 2540 or 5080 for 1” H2O and 2” H2O (25.4 and 50.8 mm H2O) full-scale
configurations respectively.
StptMode
Single
Pres
S
1700
Pres
1713
2540
0

Instruction Manual #122162 14
2.1.4 Keypad (TIM-100/200)
Asterisk Key [*] enables a menu item to be modified. When the star key is depressed on the
keypad. An [*] will appear in the selection indicator box.
& Up Arrow [] and Down Arrow [] Keys allow the user to scroll through the menu
items. Once a menu item is chosen using the asterisk key, the arrow keys allow the user to
select a value or option available under the individual menu item.
Enter Key [ENT] enters into memory the selected menu item value. A change made to a
menu item is only activated after the enter key is pressed.

Instruction Manual #122162 15
3. Quick Start Guide
If you are familiar with the SENTRY 1510 system and have previously installed the same model, you
may wish to make an additional photocopy of this checklist on clean-room paper and refer to it during the
installation. Review the notes and cautions located throughout the manual prior to installation. However,
if you have not previously installed a SENTRY 1510 system or may have installed a different model, it is
recommended that you read through the installation manual in its entirety first and use the checklist
during actual installation.
3.1 SENTRY 1510 System Installation Checklist
[ ] 1. General
[ ] 1.1. Unpacking: Verify that none of the contents are missing or damaged
[ ] 1.2. Part Names: Review the part names prior to installation.
[ ] 2. Installation Checklist
[ ] 2.1. Copy this checklist onto cleanroom paper and refer to it during installation.
[ ] 3. Guidelines
[ ] 3.1. Review Installation Guidelines
[ ] 3.2. Review Installation Layout
[ ] 4. Installation & Power-Up
[ ] 4.1. SENTRY 1510
[ ] 4.1.1. Mount the SENTRY 1510 to the Process Tool
[ ] 4.1.2. Connect the Furnace Exhaust (No BAI Condenser)
[ ] 4.1.3. Connect the Facilities Exhaust to the SENTRY 1510
[ ] 4.2. Drains and P-Traps
[ ] 4.2.1. Install Drains (as required)
[ ] 4.2.2. Install P-Traps or Tubing Loops (as required)
[ ] 4.2.3. Install Isolation Valves (as required)
[ ] 4.3. Process Pressure Sense Tube
[ ] 4.3.1. Connect the Process Pressure Sense Tube to the Furnace
[ ] 4.3.2. Connect the Proess Pressure Sense Tube to the SENTRY 1510
Care should be taken to avoid pinching or blocking of the sense
line as damage to the SENTRY 1510 Transducer may occur.
[ ] 4.4. SENTRY 1510 Nitrogen Supply
[ ] 4.4.1. Connect the Nitrogen Supply Line to the SENTRY 1510
[ ] 4.5. TIM 100/120
[ ] 4.5.1. Attach the Mounting Brackets to the TIM 100/120
[ ] 4.5.2. Mount the TIM 100/120 to the Tool
[ ] 4.5.3. Ground the TIM 100/120
[ ] 4.6. SENTRY Cable Installation
[ ] 4.6.1. Connect the TIM 100/120 to the SENTRY 1510 Cable
[ ] 4.6.2. Connect the TIM 100/120 Power and/or Tool Interface
[ ] 4.6.3. Connect the Serial Communication Cable (Optional)
[ ] 4.7. System Start-Up
[ ] 4.7.1. Power ON the SENTRY TIM-100/120
[ ] 4.7.2. Select Communication Operating Mode
[ ] 4.7.3. Save Operating Parameter Data
[ ] 4.8. Condenser (Required for Wet Process)

Instruction Manual #122162 16
[ ] 4.8.1. Mount the Condenser to the Process Tool
[ ] 4.8.2. Install the SENTRY 1510 on the Condenser
[ ] 4.8.3. Connect the Furnace & Facilities Exhaust to the CD-20 Condenser
[ ] 4.8.4. Connect the “AVP” Condenser to the Furnace & Facilities
[ ] 4.8.5. Connect Facilities Water Supply to the Condenser

Instruction Manual #122162 17
4. Guidelines
4.1 Installation Guidelines
Before beginning the design and installation lay out, consider the following general installation
features, guidelines and limitations.
1. The SENTRY 1510 controller must remain free of all moisture. For installation on wet
process a condenser must be installed in the exhaust path prior to the SENTRY 1510.
2. The SENTRY 1510 is equipped with four 10-32 threaded mounting holes located at the base
of the unit. These four holes should be used for mounting the SENTRY 1510 to the process
tool. Use caution not to over tighten mounting hardware.
3. An arrow in the Teflon portion of the SENTRY 1510 indicates the direction of flow. The
arrowhead must point towards house exhaust.
4. The SENTRY 1510 should be mounted in an accessible location on or in close proximity of
the process tool.
5. The process sense tube is shipped in a 10-foot length. Any extra length should be loosely
coiled.
Care should be taken to avoid pinching or blocking of the sense
line as damage to the SENTRY 1510 Transducer may occur.
6. Mounting configuration:
(a) Horizontal configured SENTRY 1510’s must be installed within 3 degrees of level in the
horizontal plane.
(b) Vertical configured SENTRY 1510’s must be installed within 3 degrees of level in the
vertical plane.
7. To maintain CE certification, if applicable, the Tool Interface Module must be installed at a
height above the floor greater than 24” (0.6 meter).
8. The Tool Interface Module requires that the analog ground and the power ground be
common on the tool side (refer to page 24 and Appendix C).
9. The minimum static exhaust required for proper operation of the SENTRY 1510 at least 10
mm H2O more negative than set point (vary by installation).
10. The SENTRY 1510 requires an input of house grade or better Nitrogen regulated to 40 - 100
PSI.

Instruction Manual #122162 18
Guidelines
4.2 Installation Layout
The SENTRY 1510 can be ordered as horizontal of vertical installation configuration. Verify
you have the correct configuration for your installation and follow the appropriate installation
diagrams throughout this manual.

Instruction Manual #122162 19
5. Installation & Power-Up
5.1 SENTRY 1510
The SENTRY 1510 is available in a horizontally mounted configuration and a vertically
mounted configuration. Both versions will be illustrated throughout this manual. Before
beginning your installation verify the part number is the appropriate number for your
installation.
5.1.1 Mounting the SENTRY 1510 to the Process Tool
1. Selected a location for the SENTRY 1510 and mount the SENTRY 1510 Controller to the
support structure using 10-32 hardware in the threaded holes located at the base of the
unit.
Notice
Do not to over-tighten the 10-32 screws, as this could result in damage to the
internal threads.
2. For horizontal configurations be sure the 1510 Controller is within 3 degrees of horizontal.
For vertical installations be sure the unit is mounted to within 3 degrees of vertical.
3. Be sure the arrow indicating the direction of flow is pointing towards the house exhaust.

Instruction Manual #122162 20
5.1.2 Connecting the Furnace Exhaust (No BAI Condenser)
After the SENTRY 1510 is securely mounted, the process tool exhaust can be plumbed to the
input side of the SENTRY 1510. If your installation includes a BAI factory condenser please
follow the installation guidelines located in the CD-20 condenser section 4.9 of this manual.
Notice
The process exhaust should not be dampened. Fully Open ALL dampers
between the process tube and the SENTRY 1510.
1. The input of the 1510 is designed to accept 1” male NPT threads.
2. Using thread seal tape install a 1” male NPT compression or other suitable fitting into the
input side of the SENTRY 1510 controller.
3. Install a transition fitting to transition from the quartz output to 1” OD. Tubing. The transition
fitting should provide a fitting for the SENTRY 1510 process pressure sense line. The length
of the transition should not exceed 10”. Transitions that exceed this length may result in a
pressure differential preventing the SENTRY 1510 from accurately controlling the pressure
inside the process tube.
4. Using 1” OD. Tubing plumb from the Teflon transition fitting installed in step 2 to the Teflon
fitting installed at the input of the 1510 controller. If your installation is using a non BAI
condenser plumb 1” OD. Tubing from the output of the condenser to the 1” male NPT fitting
installed at the input of the SENTRY 1510.
5. For wet processing drain requirements refer to section 4.2
Table of contents
Other MKS Control Unit manuals

MKS
MKS HPS 145 Vacuum Sentry Series User manual
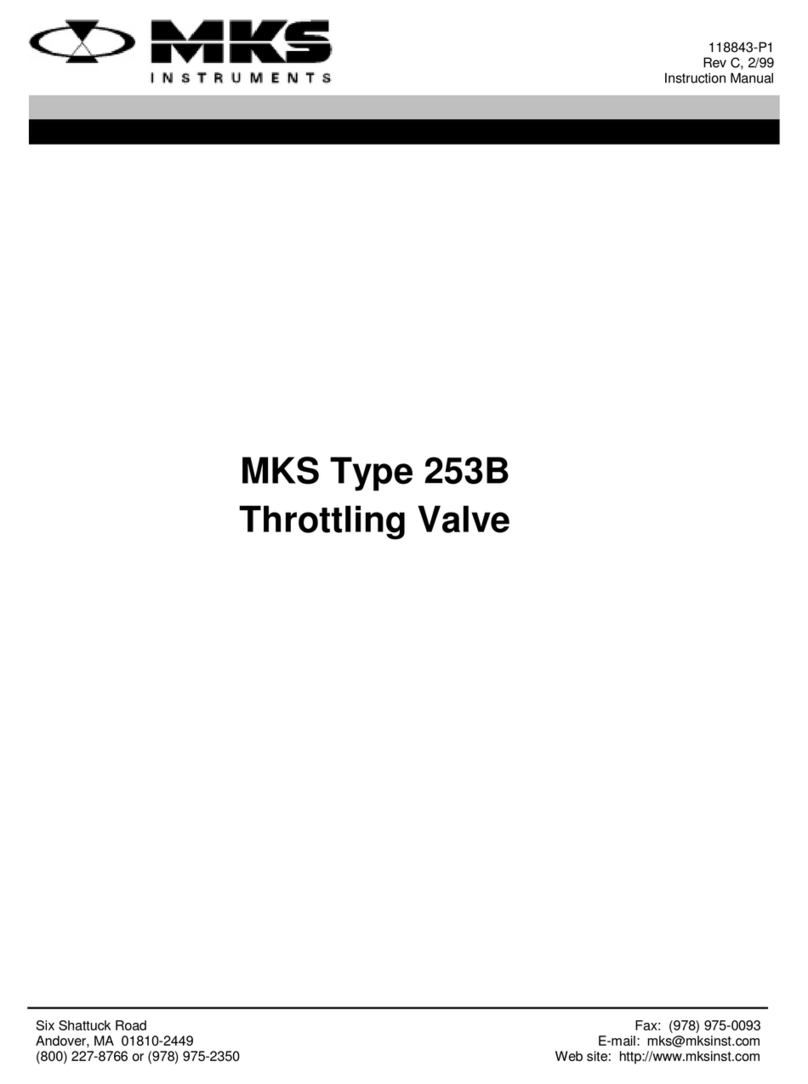
MKS
MKS 253B-2-2-2 User manual
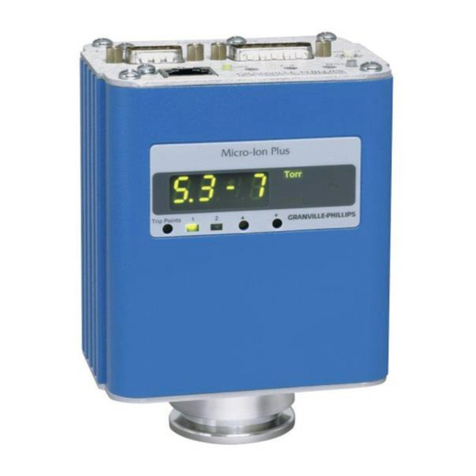
MKS
MKS 356 Micro-Ion Plus Series User manual
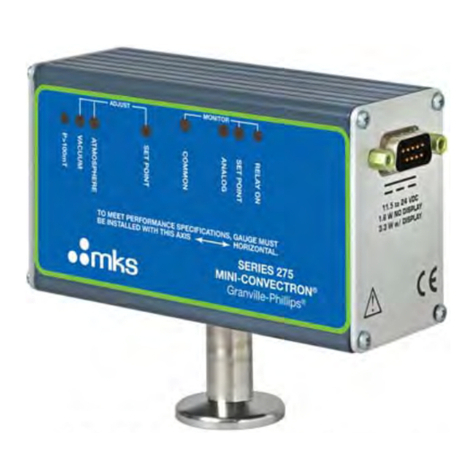
MKS
MKS Series 275 MiniConvectron User manual
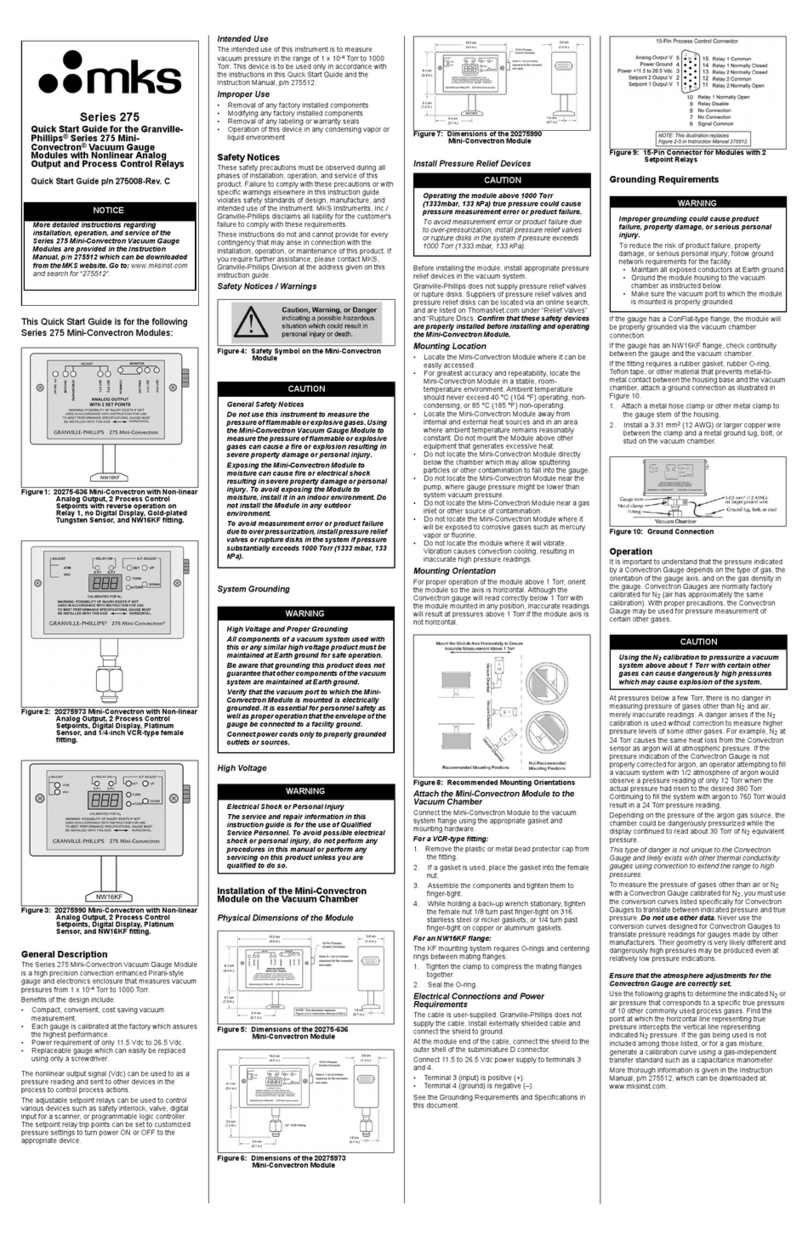
MKS
MKS Series 275 MiniConvectron User manual
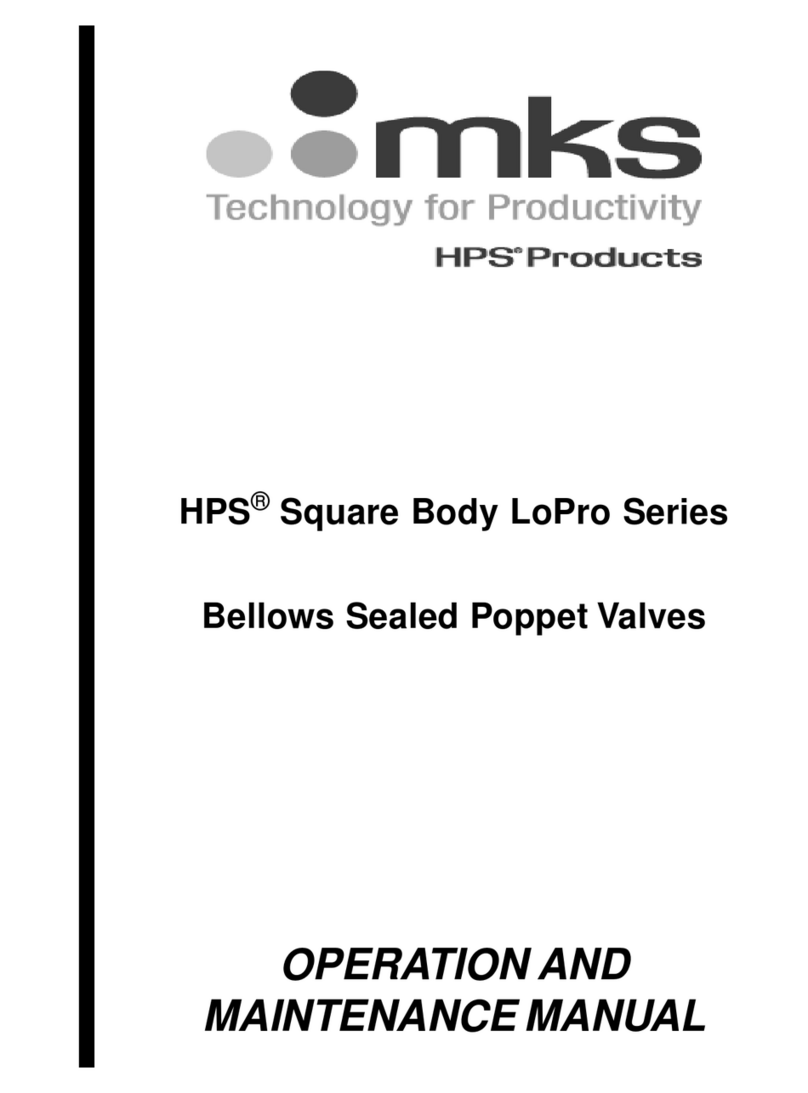
MKS
MKS HPS Square Body LoPro Series User manual

MKS
MKS Automated SENTRY 1000-300 User manual
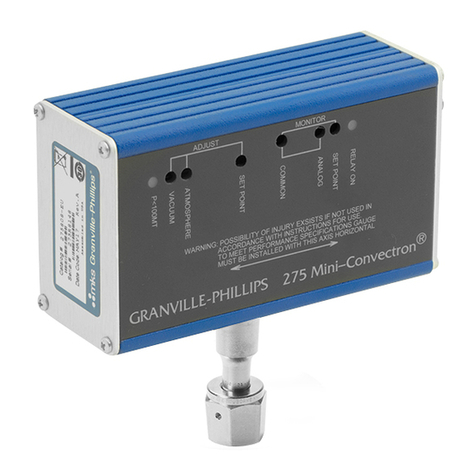
MKS
MKS Granville-Phillips Series 275 User manual
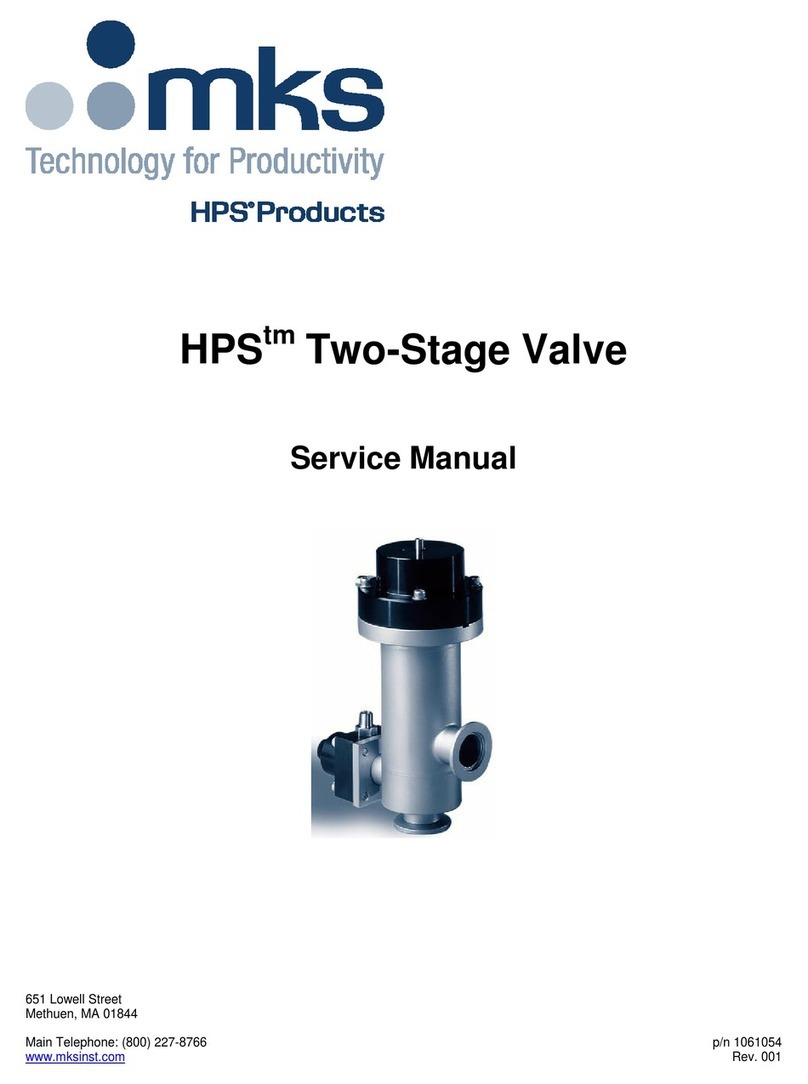
MKS
MKS HPS User manual

MKS
MKS 390 Series User manual