MKS 356 Micro-Ion Plus Series User manual

Series 356
Instruction Manual
Series 356 Micro-Ion®Plus
Vacuum Gauge Module
Instruction manual part number 356007-GP
Revision D - April 2018


Series 356
Instruction Manual
This Instruction Manual is for use with all Granville-Phillips
Series 356 Micro-Ion Plus Vacuum Gauge Modules. A list of
applicable catalog numbers is provided on the following page.
Series 356 Micro-Ion®Plus
Vacuum Gauge Module
© 2018 MKS Instruments, Inc. All rights reserved.
Granville-Phillips®and Micro-Ion®are registered trademarks, and mksinstTM is a
trademark of MKS Instruments, Inc. All other trademarks and registered trademarks
are the properties of their respective owners.
Customer Service / Technical Support:
MKS Pressure and Vacuum Measurement Solutions
MKS Instruments, Inc.
6450 Dry Creek Parkway
Longmont, Colorado 80503 USA
Tel: 303-652-4400
Fax: 303-652-2844
MKS Corporate Headquarters
MKS Instruments, Inc.
2 Tech Drive, Suite 201
Andover, MA 01810 USA
Tel: 978-645-5500
Fax: 978-557-5100
Email: [email protected]

Series 356 Micro-Ion®Plus Vacuum Gauge Module
Catalog numbers for Series 356 Micro-Ion Plus Vacuum Gauge Modules
Power supply and cable are not included.
Module with RS-485 interface, analog output, no display: 356001 - Y # - #
Module with RS-485 interface, analog output, digital display: 356002 - Y # - #
Ion Gauge Filaments:
Yttria-coated iridium Y
Flange/Fitting:
NW16KF D
NW25KF E
NW40KF K
1.33 inch (NW16CF) ConFlat-type F
2.75 inch (NW35CF) ConFlat-type G
1/2 inch VCR-type male H
NW16L M
40KFL L
Measurement Units:
Torr T
mbar M
pascal P
VCR and VCO are registered trademarks of Swagelock Company.

Micro-Ion®Module Instruction Manual - 356007-GP 5
Contents
Chapter 1 Introduction . . . . . . . . . . . . . . . . . . . . . . . . . . . . . . . . . . . . . . . . . 7
1.1 About These Instructions . . . . . . . . . . . . . . . . . . . . . . . . . . . 7
1.2 Caution and Warning Statements . . . . . . . . . . . . . . . . . . . . 7
1.3 System Grounding . . . . . . . . . . . . . . . . . . . . . . . . . . . . . . . 8
1.4 Explosion / Implosion . . . . . . . . . . . . . . . . . . . . . . . . . . . . . 8
1.5 Operation . . . . . . . . . . . . . . . . . . . . . . . . . . . . . . . . . . . . . . 9
1.6 Reading and Following Instructions . . . . . . . . . . . . . . . . . . 9
1.7 Customer Service . . . . . . . . . . . . . . . . . . . . . . . . . . . . . . . . 9
1.8 Definitions of Terms . . . . . . . . . . . . . . . . . . . . . . . . . . . . . . 10
1.9 Specifications . . . . . . . . . . . . . . . . . . . . . . . . . . . . . . . . . . . 10
Chapter 2 Installation . . . . . . . . . . . . . . . . . . . . . . . . . . . . . . . . . . . . . . . . . . 13
2.1 Module Components . . . . . . . . . . . . . . . . . . . . . . . . . . . . . 13
2.2 Installation Procedure . . . . . . . . . . . . . . . . . . . . . . . . . . . . . 13
Step 1 Install Pressure Relief Devices . . . . . . . . . . . . . . . 14
Step 2 Location of the Module . . . . . . . . . . . . . . . . . . . . 14
Step 3 Attach the Module to the Vacuum Chamber . . . . . 16
Step 4 Assemble and Connect the Cables . . . . . . . . . . . . 17
Step 5 Calibrate the Conductron Sensor . . . . . . . . . . . . . 23
2.3 Eliminating Radio Frequency Interference . . . . . . . . . . . . . . 23
Chapter 3 Operation . . . . . . . . . . . . . . . . . . . . . . . . . . . . . . . . . . . . . . . . . . . . 25
3.1 Preparing to Operate the Module . . . . . . . . . . . . . . . . . . . . 25
3.2 Theory of Operation . . . . . . . . . . . . . . . . . . . . . . . . . . . . . . 26
3.3 Set the Micro-Ion Gauge Emission Current Threshold . . . . . 29
3.4 Set the Micro-Ion Gauge Filament Mode . . . . . . . . . . . . . . . 29
3.5 Turn the Micro-Ion Gauge ON or OFF . . . . . . . . . . . . . . . . 31
3.6 Read Vacuum Pressure . . . . . . . . . . . . . . . . . . . . . . . . . . . . 32
3.7 Read the Analog Output . . . . . . . . . . . . . . . . . . . . . . . . . . . 33
3.8 Degas the Micro-Ion Gauge . . . . . . . . . . . . . . . . . . . . . . . . 34
3.9 Calibrate the Module at Atmosphere . . . . . . . . . . . . . . . . . . 35
3.10 Calibrate the Module at Vacuum . . . . . . . . . . . . . . . . . . . . 36
3.11 Process Control Relay Trip Points . . . . . . . . . . . . . . . . . . . . 36
3.12 RS-485 Operation and Commands . . . . . . . . . . . . . . . . . . . 40
3.13 RS-485 Physical Layer . . . . . . . . . . . . . . . . . . . . . . . . . . . . . 40
3.14 RS-485 Initial Setup . . . . . . . . . . . . . . . . . . . . . . . . . . . . . . 41
3.15 Data Timing and Response . . . . . . . . . . . . . . . . . . . . . . . . . 42
3.16 RS-485 Command Structure . . . . . . . . . . . . . . . . . . . . . . . . 44
3.17 RS-485 Command Sets . . . . . . . . . . . . . . . . . . . . . . . . . . . . 45
3.18 RS-485 Commands - Set 1 . . . . . . . . . . . . . . . . . . . . . . . . . 47
3.19 RS-485 Commands - Set 2 . . . . . . . . . . . . . . . . . . . . . . . . . 50
3.20 RS-485 Error Responses and Display Error Codes . . . . . . . . 57

Contents
6Micro-Ion®Module Instruction Manual - 356007-GP
Chapter 4 Maintenance . . . . . . . . . . . . . . . . . . . . . . . . . . . . . . . . . . . . . . . . . 59
4.1 Customer Service . . . . . . . . . . . . . . . . . . . . . . . . . . . . . . . . 59
4.2 Troubleshooting . . . . . . . . . . . . . . . . . . . . . . . . . . . . . . . . . 60
4.3 Micro-Ion Gauge Continuity Test . . . . . . . . . . . . . . . . . . . . 63
4.4 Replacing the Gauge Assembly . . . . . . . . . . . . . . . . . . . . . . 66
4.5 Returning a Micro-Ion Module for Service . . . . . . . . . . . . . 66
Appendix A Filament Operation . . . . . . . . . . . . . . . . . . . . . . . . . . . . . . . . . . . 67
Index . . . . . . . . . . . . . . . . . . . . . . . . . . . . . . . . . . . . . . . . . . . . . . . . . . . . . . . . . . . . . . . . . . . . . . . . . . . . . 71

Micro-Ion®Module Instruction Manual - 356007-GP 7
Installation Operation MaintenanceIntroduction
Chapter 1 Introduction
1.1 About These Instructions These instructions explain how to install, operate, and maintain the
Granville-Phillips®Micro-Ion®Plus Vacuum Gauge Module. The module
contains a Micro-Ion ionization gauge and a Conductron®heat-loss sensor,
which working in combination provide pressure measurement from
1x10
–9 to atmosphere.
•This chapter explains caution and warning statements, which must be
adhered to at all times; explains your responsibility for reading and
following all instructions; defines terms that are used throughout this
manual; and tells you how to contact customer service.
•Chapter 2 explains how to install the module.
•Chapter 3 explains the theory of operation; module operating
procedures; how to read the analog output; and how to use the RS-485
interface.
•Chapter 4 explains troubleshooting; Micro-Ion gauge testing, removal
and replacement; and module return procedures.
•Appendix A explains filament operation modes of the Micro-Ion Gauge.
1.2 Caution and Warning
Statements
This manual contains caution and warning statements with which you must
comply to prevent inaccurate measurement, property damage, or personal
injury.
Caution and warning statements comply with American Institute of
Standards Z535.1-2002 through Z535.5-2002, which set forth voluntary
CAUTION
Caution statements alert you to hazards or unsafe
practices that could result in minor personal injury or
property damage.
Each caution statement explains what you must do to prevent or
avoid the potential result of the specified hazard or unsafe
practice.
WARNING
Warning statements alert you to hazards or unsafe
practices that could result in severe property damage or
personal injury due to electrical shock, fire, or explosion.
Each warning statement explains what you must do to prevent
or avoid the potential result of the specified hazard or unsafe
practice.

Chapter 1
8Micro-Ion®Module Instruction Manual - 356007-GP
practices regarding the content and appearance of safety signs, symbols,
and labels.
Each caution or warning statement explains:
a. The specific hazard that you must prevent or unsafe practice that you
must avoid,
b. The potential result of your failure to prevent the specified hazard or
avoid the unsafe practice, and
c. What you must do to prevent the specified hazardous result.
1.3 System Grounding Grounding, though simple, is very important! Be certain that ground circuits
are correctly used on your ion gauge power supplies, gauges, and vacuum
chambers, regardless of their manufacturer. Safe operation of vacuum
equipment requires grounding of all exposed conductors of the gauges, the
controller and the vacuum system. Lethal Voltages may be established
under some operating conditions unless correct grounding is provided.
Ion producing equipment, such as ionization gauges, mass spectrometers,
sputtering systems, etc., from many manufacturers may, under some
conditions, provide sufficient electrical conduction via a plasma to couple
a high voltage electrode potential to the vacuum chamber. If exposed
conductive parts of the gauge, controller, and chamber are not properly
grounded, they may attain a potential near that of the high voltage electrode
during this coupling. Potential fatal electrical shock could then occur
because of the high voltage between these exposed conductors and ground.
1.4 Explosion / Implosion Danger of injury to personnel and damage to equipment exists on all
vacuum systems that incorporate gas sources or involve processes capable
of pressuring the system above the limits it can safely withstand.
For example, danger of explosion in a vacuum system exists during
backfilling from pressurized gas cylinders because many vacuum devices
such as ionization gauge tubes, glass windows, glass belljars, etc., are not
designed to be pressurized.
Install suitable devices that will limit the pressure from external gas sources
to the level that the vacuum system can safely withstand. In addition, install
suitable pressure relief valves or rupture disks that will release pressure at a
level considerably below that pressure which the system can safely
withstand.
Suppliers of pressure relief valves and pressure relief disks can be located
via an online search, and are listed on ThomasNet.com under “Relief
Valves” and “Rupture Discs. Confirm that these safety devices are properly
installed before installing the Series 356 vacuum gauge module.
In addition, check that (1) the proper gas cylinders are installed, (2) gas
cylinder valve positions are correct on manual systems, and (3) the
automation is correct on automated systems.

Introduction
Micro-Ion®Module Instruction Manual - 356007-GP 9
Installation Operation MaintenanceIntroduction
1.5 Operation It is the installer's responsibility to ensure that the automatic signals
provided by the process control module are always used in a safe manner.
Carefully check manual operation of the system and the setpoint
programming before switching to automatic operation. Where an
equipment malfunction could cause a hazardous situation, always provide
for fail-safe operation. As an example, in an automatic backfill operation
where a malfunction might cause high internal pressures, provide an
appropriate pressure relief device.
1.6 Reading and Following
Instructions
You must comply with all instructions while you are installing, operating,
or maintaining the module. Failure to comply with the instructions violates
standards of design, manufacture, and intended use of the module. MKS
Instruments, Inc. disclaims all liability for the customer's failure to comply
with the instructions.
•Read instructions – Read all instructions before installing or operating the
product.
•Retain instructions – Retain the instructions for future reference.
•Follow instructions – Follow all installation, operating and maintenance
instructions.
•Heed warnings and cautions – Adhere to all warnings and caution
statements on the product and in these instructions.
•Parts and accessories – Install only those replacement parts and
accessories that are recommended by Granville-Phillips. Substitution of
parts is hazardous.
1.7 Customer Service If the product must be returned to the factory for service, request a Return
Material Authorization (RMA) from MKS, which can be completed at
https://www.mksinst.com/service/servicehome.aspx. Do not return
products without first obtaining an RMA. In most cases a hazardous
materials disclosure form is required. The MKS Customer Service
Representative will advise you if the hazardous materials document is
required.
When returning products to MKS, be sure to package the products to
prevent shipping damage. Shipping damage on returned products as a result
of inadequate packaging is the Buyer's responsibility.
For Customer Service / Technical Support:
MKS Pressure and Vacuum Measurement Solutions
MKS Instruments, Inc.
6450 Dry Creek Parkway
Longmont, Colorado 80503 USA
Tel: 303-652-4400
Fax: 303-652-2844

10 Micro-Ion®Module Instruction Manual - 356007-GP
MKS Corporate Headquarters
MKS Instruments, Inc.
2 Tech Drive, Suite 201
Andover, MA 01810 USA
Tel: 978-645-5500
Fax: 978-557-5100
Email: [email protected]
1.8 Definitions of Terms • Table 1-1 lists terms describing the Micro-Ion Plus Module and its
components.
1.9 Specifications
Measurement Range for Air and N2
Measurements will change with different gases and gas mixtures. Micro-Ion
Plus gauges are not intended for use with flammable or explosive gases.
Atmospheric pressure value is based on calibration at time of use.
Torr 1 x 10–9 Torr to atmosphere (“At”)
mbar 1 x 10–9 mbar to atmosphere (“At”)
pascal 1 x 10–7 pascal to atmosphere (“At”)
Micro-Ion Gauge Emission Current
Emission current 0.1 and 4 mA, autoranging
Micro-Ion gauge auto on 2 x 10–2 Torr, 2.66 x 10–2 mbar, 2.66 pascal, with decreasing pressure
Micro-Ion gauge auto off 3 x 10–2 Torr, 3.99 x 1–2 mbar, 3.99 pascal, with increasing pressure
Micro-Ion gauge degas Electron bombardment, 3.75 W with 2-minute timer
Default switch to high (4.0 mA) 5.0 x 10–6 Torr, 6.6 x 10–6 mbar, 6.6 x 10–4 pascal, with decreasing pressure
Default switch to low (0.1 mA) 1 x 10–5 Torr, 1.3 x 10–5 mbar, 1.3 x 10–3 pascal, with increasing pressure,
adjustable, 50% hysteresis (automatically set)
Table 1-1 Terms Describing the Micro-Ion Plus Module and Components
Term Description
Module The Micro-Ion Plus Module, which contains a hot filament Micro-Ion gauge
(Bayard-Alpert type ionization gauge) and a Conductron heat-loss sensor.
Micro-Ion gauge The Bayard-Alpert type ionization gauge, which indicates pressure by producing
a current that is proportional to gas density.
Conductron sensor The heat-loss sensor, which measures pressure as a function of heat loss through
the gold-plated tungsten sensing wire.

Introduction
Micro-Ion®Module Instruction Manual - 356007-GP 11
Installation Operation MaintenanceIntroduction
Filament selection Alternating, automatic, or manual modes
• For a Micro-Ion gauge with yttria-coated iridium filaments, the default is
alternating
Outputs and Indicators
Analog output Logarithmic, 0.50 Vdc/decade, where 1000 Torr = 7 Vdc
Digital RS-485 output
Interface RS-485 two-wire, half-duplex
Communications format ASCII format, eight data bits, no parity, one stop bit
Baud rates 1200, 2400, 4800, 9600, 19200 (default), or 38400 baud
Address 0 to 63, selected by using address switch and RS-485 SA command
LED status indicator Module status indicator lights up to indicate module status.
Pressure display (optional) X.X±Y display format includes two significant digits, a 1-digit exponent, and
a ± sign for the exponent.
Trip point indicators (optional) LED indicator for relay 1 or relay 2 is solid green when corresponding relay
is activated or blinks green when corresponding relay is being configured.
Trip point relays
Relay type Two single-pole, double-throw relays (SPDT)
Relay contacts are silver alloy-gold clad, rated for 1 A at 30 Vdc. The relays
can handle resistive or non-inductive loads.
Relay contact ratings 1 A at 30 Vdc resistive or non-inductive
Minimum hysteresis 5%
Range 1.0 x 10–9 to 100 Torr
1.0 x 10–9 to 133 mbar
1.0 x 10–7 to 1.33 x 104pascal
Default activation pressure Default activation pressures are set to 0.0.
Micro-Ion Plus Module
Micro-Ion gauge sensitivity
At 4 mA emission (high) 18/Torr, 13.5/mbar, .135/pascal
At 0.1 mA emission (low) 20/Torr, 15/mbar, .15/pascal (± 15% variation)
X-ray limit < 3 x 10–10 Torr, < 3.99 x 10–10 mbar, < 3.99 x10–8 pascal
The x-ray limit is the absolute lowest indication from the gauge. It is not

Chapter 1
12 Micro-Ion®Module Instruction Manual - 356007-GP
practical to make repeatable measurements near the x ray limit
Micro-Ion gauge filament material Yttria-coated iridium
Conductron sensing wire material Gold-plated tungsten
Internal volume 10.8 cm3, (0.67 in.3) to the port screen
Physical Characteristics
Weight 567 gm (20 oz.) with NW16KF fitting
Power required +24 Vdc ±15% external power supply. Power supply must provide 1.5 A
current at 24 Vdc. Inrush current can momentarily exceed the 1.5 A peak.
+24 Vdc±15% external power supply must be certified to IEC standard with
a safety extra-low voltage classified output.
Operating environment +10 °C to +40 °C ambient, non-condensing, indoor use only, ordinary
protection for moisture, maximum altitude 3000 meters
Operating conditions Suitable for continuous operation. Category 1 for installation over voltage.
Pollution degree 2, Class 1
Non-operating temperature –40 °C to +85 °C (–40 °F to +185 °F)
Case material Aluminum extrusion
Connectors 15-pin subminiature D connector for module power supply, analog
outputs, and RS-485 outputs
Materials exposed to gas Yttria-coated iridium, gold-plated tungsten, 304 stainless steel, tantalum,
tungsten, nickel iron alloy, nickel, borosilicate glass
Compliance
Product Safety IEC/EN 61010-1
IP Rating IP20

Micro-Ion®Module Instruction Manual - 356007-GP 13
Installation Operation MaintenanceBefore You Begin
Chapter 2 Installation
2.1 Module Components The Micro-Ion Plus Module contains a Micro-Ion gauge (Bayard-Alpert type
ionization gauge) and a Conductron heat-loss sensor.
2.2 Installation Procedure The module installation procedure includes the following steps:
1. Install the appropriate pressure relief devices in the vacuum system.
2. Determine the best for the module on the vacuum chamber.
3. Attach the module vacuum chamber fitting to its mate on the vacuum
chamber.
4. Assemble and connect the module wiring.
5. Calibrate the Conductron sensor at atmosphere.
This chapter also explains what to do if radio frequency interference (RFI)
from the module disrupts operation of other electronic devices.
WARNING
Using the module to measure the pressure of flammable
or explosive gases can cause a fire or explosion resulting
in severe property damage or personal injury.
Do not use the module to measure the pressure of
flammable or explosive gases.
WARNING
Exposing the module to moisture can cause fire or
electrical shock resulting in severe property damage or
personal injury.
To avoid exposing the module to moisture, install the
module in an indoor environment. Do not install the module
in any outdoor environment.

Chapter 2
14 Micro-Ion®Module Instruction Manual - 356007-GP
Step 1 Install Pressure Relief Devices
Before you install the module, install appropriate pressure relief devices in
the vacuum system.
MKS Instruments, Inc./Granville-Phillips does not supply pressure relief
valves or rupture disks. Suppliers of pressure relief valves and pressure relief
disks can be located via an online search, and are listed on ThomasNet.com
under “Relief Valves” and “Rupture Discs. Confirm that these safety
devices are properly installed before installing and operating the product.
Ensure the following precautions are complied with at all times:
(1) the proper gas cylinders are installed,
(2) the gas cylinder valve positions are correct on manual systems,
(3) and the automation is correct on automated gas delivery systems.
Step 2 Location of the Module
To determine the best location on the vacuum system for module, refer to
Figure 2-1 and Table 2-1, and the guidelines below.
• For proper operation of the module at atmosphere, orient the module
vertically (see Figure 2-1). Although the Micro-Ion gauge will read
correctly below 100 Torr with the module mounted in any position,
inaccurate readings will result at pressures above 100 Torr if the module
is not in the vertical position as illustrated in Figure 2-1.
• For greatest accuracy and repeatability, locate the module in a stable,
room-temperature environment. Ambient temperature should never
exceed 40 °C (104 °F) operating, non-condensing, or 85 °C (185 °F)
non-operating.
• Locate the module away from internal and external heat sources and in
an area where ambient temperature remains reasonably constant.
• Do not locate the module near the pump, where gauge pressure might be
lower than normal vacuum chamber pressure.
CAUTION
Operating the module above 1000 Torr (1333 mbar,
133 kPa) true pressure could cause vacuum system
rupture or product failure.
To avoid vacuum system rupture or product failure due to
overpressurization, install pressure relief valves or rupture
disks in the system if pressure exceeds 1000 Torr
(1333 mbar, 133 kPa).

Installation
Micro-Ion®Module Instruction Manual - 356007-GP 15
Installation Operation MaintenanceBefore You Begin
• Do not locate the module near a gas inlet or other source of
contamination, where inflow of gas or particulates causes atmospheric
pressure to be higher than system atmosphere.
• Do not locate the module where it will be exposed to corrosive gases
such as mercury vapor or fluorine.
Figure 2-1 Dimensions
9.8
(3.8)
7.4
(2.8)
9.2
(3.5)
Dim H.
Dimensions in cm
(in.)

Chapter 2
16 Micro-Ion®Module Instruction Manual - 356007-GP
Step 3 Attach the Module to the Vacuum Chamber
Attach the module vacuum chamber fitting to its mate on the vacuum
chamber.
CAUTION
Twisting the module to tighten the fitting to the vacuum
chamber can damage the module’s internal connections.
• Do not twist the module to tighten the fitting.
• Use appropriate tools to tighten the fitting.
Table 2-1 Fittings for the Micro-Ion Plus Module
Fitting
Dim. H
cm in.
½–inch VCR-type male 5.8 2.3
1.33–inch (NW16CF) ConFlat type 4.3 1.7
2.75–inch (NW35CF) ConFlat type 4.3 1.7
NW16KF 2.0 0.8
NW25KF 2.0 0.8
NW40KF 2.0 0.8
NW16KF extended 4.2 1.65
NW25KF extended 4.2 1.65
NW40KF extended 4.6 1.8

Installation
Micro-Ion®Module Instruction Manual - 356007-GP 17
Installation Operation MaintenanceBefore You Begin
VCR-type fitting a. Remove the plastic or metal bead protector cap from the fitting.
b. If a gasket is used, place the gasket into the female nut.
c. Assemble the components and tighten them finger-tight.
d. While holding a back-up wrench stationary, tighten the female nut 1/8
turn past finger-tight on 316 stainless steel or nickel gaskets, or 1/4 turn
past finger-tight on copper or aluminum gaskets. Do not twist the
module to tighten the fitting.
ConFlat flange To minimize the possibility of leaks with ConFlat flanges, use high strength
stainless steel bolts and a new, clean stainless steel with OFHC copper
gasket. Avoid scratching the seal surfaces.
a. Finger tighten all bolts.
b. Use a wrench to continue tightening 1/8 turn at a time in crisscross
order (1, 4, 2, 5, 3, 6) until flange faces make contact. Further tighten
each bolt about 1/16 turn.
NW flange The NW mounting system requires O-rings and centering rings between
mating flanges.
Tighten the clamp to compress the mating flanges together and seal the
O-ring.
Step 4 Assemble and Connect the Cables
Connecting Cables The cables are user-supplied. Granville-Phillips does not supply cable.
• Use externally shielded cable.
• Connect the wiring to the 9-pin trip point connector and the 15-pin
subminiature D connector. On the User Interface connector, Pin 1 must
be connected to pin 5 for the Micro-Ion gauge to turn ON. See Figure 2-2.

Chapter 2
18 Micro-Ion®Module Instruction Manual - 356007-GP
Figure 2-2 9-pin Trip Point and 15-pin User Interface Subminiature D Wiring Connectors
Module Power Supply Connect the module power supply to terminals 5 and 8 on the 15-pin I/O
wiring connector.
• Pin 5 (ground) is negative (–).
• Pin 8 (power input) is positive (+).
The module requires a +24 Vdc ±15% external power supply. The power
supply must provide a 1.5 A current at 24 Vdc. Inrush current can
momentarily exceed the 1.5 A peak.
Typical module operating power is 18 W for 4 mA emission when the
Micro-Ion gauge is ON.
Power inputs are reverse-bias protected.
The Micro-Ion gauge will not activate and an emission error will occur if
insufficient power is supplied during Micro-Ion gauge activation.
Analog and RS-485
Output Wiring
Connect wiring for analog and RS-485 outputs to the 15-pin
subminiature-D connector, as illustrated in Figure 2-3.
Figure 2-3 Wiring Terminals for Analog and RS-485 Wiring
9-pin subminiature D
trip points wiring
connector
15-pin subminiature
D user interface
connector
Pin 1 must be
connected to pin 5
for the Micro-Ion
gauge to turn ON

Installation
Micro-Ion®Module Instruction Manual - 356007-GP 19
Installation Operation MaintenanceBefore You Begin
(a) 15K pull-up to 12 Vdc, (LOW) 0 Vdc at 0.80 mA. See Figure 2-4.
(b) Open Collector, no pull-up, 40 Vdc, 50 mA. See Figure 2-4.
(c) Pin must be held LOW for at least 2 msec to activate calibration.
Table 2-2 Connections to 15-pin Subminiature D Connector
Pin # Function Input or Output Description
Pin 1 Micro-Ion gauge
ON/OFF
Input Must be continuously connected to Pin 5 (LOW) to turn gauge ON (a)
• Removing ground connection turns gauge OFF
Pin 2 Analog output Output • 0.5 Vdc/decade, 7 Vdc maximum
• Ground reference to pin 12
Pin 3 Filament status Output (LOW) Indicates an inoperable filament (b)
Pin 4 Gauge status Output (LOW) Indicates Micro-Ion gauge is ON (b)
Pin 5 Ground (–) Input Power supply ground
Pin 6 Degas status Output (LOW) Indicates Micro-Ion gauge degas is ON (b)
Pin 7 Degas ON/OFF Input • Continuous LOW will activate 2-minute degas (a)
• Pressure must be < 5 x 10–6 Torr (6.66 x 10–6 mbar,
6.66 x 10–4 pascal) for degas to start
Pin 8 +24 Vdc power Input +20.4 Vdc to +27.6 Vdc, 26 W nominal
Pin 9 Calibration Input LOW sets atmospheric or vacuum calibration point (a) (c)
Pin 10 Not used Not used
Pin 11 Keyboard lock Input Continuous LOW locks keyboard (a)
Pin 12 Signal common Output Signal ground (analog output)
Pin 13 RS-485+ Input/output RS-485+
Pin 14 RS-485 – Input/output RS-485 –
Pin 15 Chassis ground Input Chassis ground (cable shield)

Chapter 2
20 Micro-Ion®Module Instruction Manual - 356007-GP
Control Inputs The module provides an internal 15 K pull-up resistor to 12 Vdc, as
illustrated in Figure 2-4.
Figure 2-4 Input Circuit Wiring
Status Outputs The module provides an open collector output with no pull-up, as
illustrated in Figure 2-5.
Figure 2-5 Output Circuit Wiring
User interface input pin
(pins 1, 7, 9, and 11)
Internal to μP input port
Active HIGH
Pin must be held LOW
(< 3.0 V at 1.2 mA) for at
least 20 msec
User interface output pin
(pins 3, 4, and 6)
Internal command
from μP (5 Vdc)
Active HIGH User must provide a
pull-up of 40 Vdc,
50 mA maximum
Table of contents
Other MKS Control Unit manuals

MKS
MKS 390 Series User manual

MKS
MKS Granville-Phillips 274 Series User manual

MKS
MKS 248A User manual
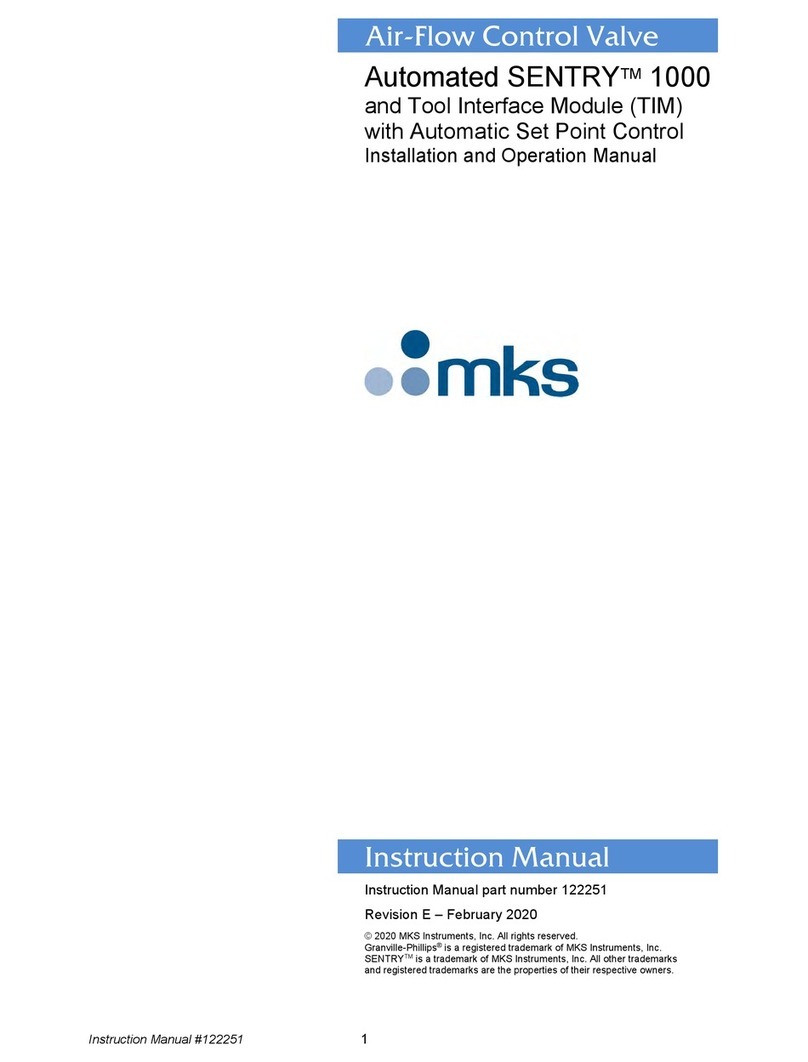
MKS
MKS Automated SENTRY 1000 User manual
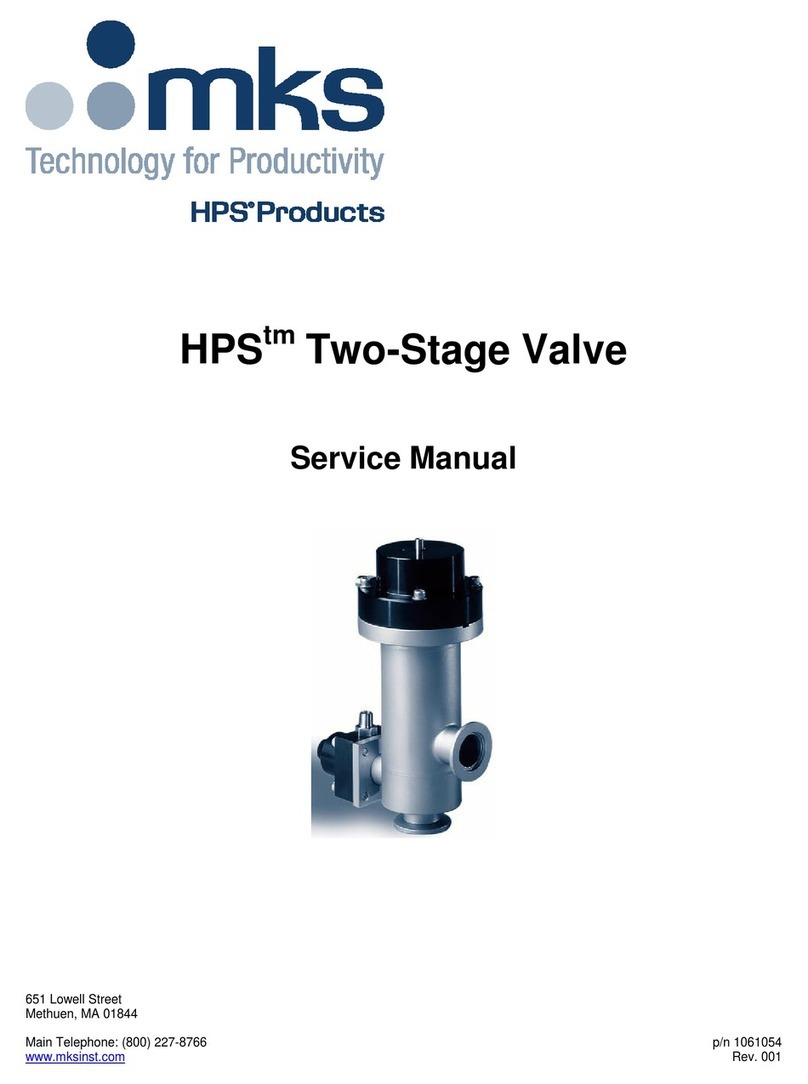
MKS
MKS HPS User manual
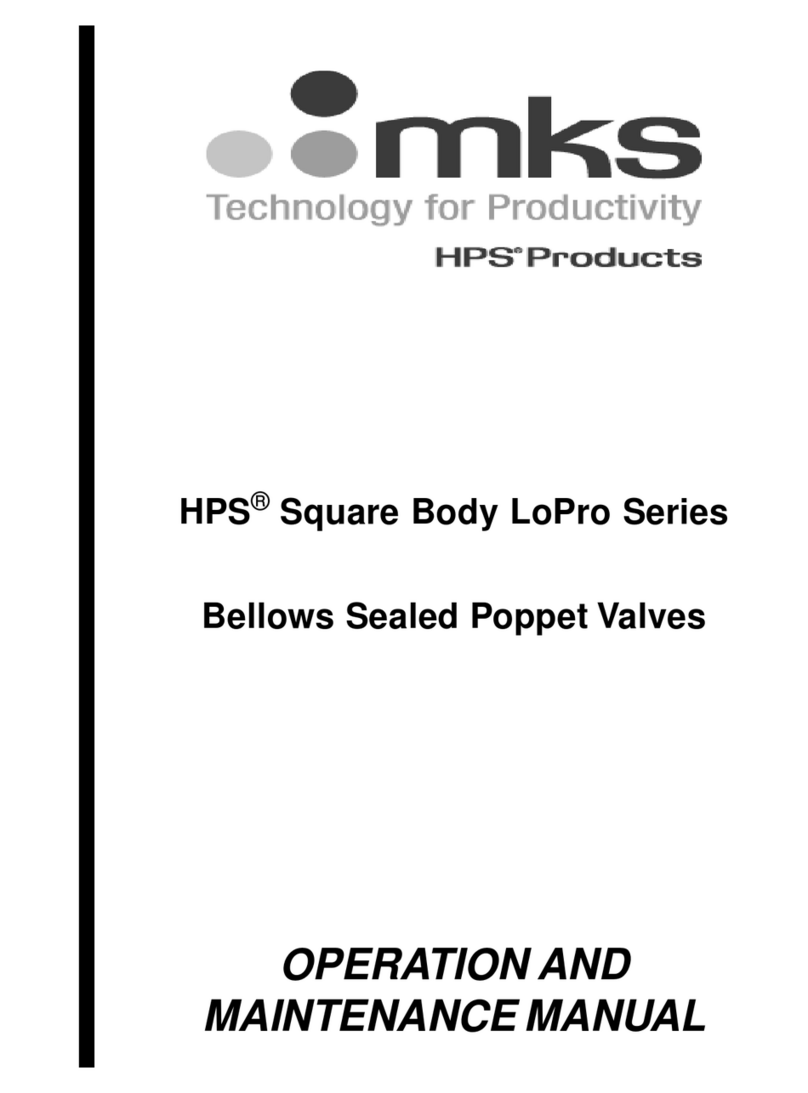
MKS
MKS HPS Square Body LoPro Series User manual
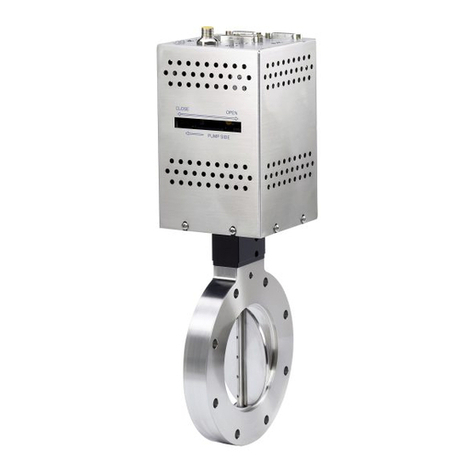
MKS
MKS T3B Series Owner's manual

MKS
MKS HPS 145 Vacuum Sentry Series User manual
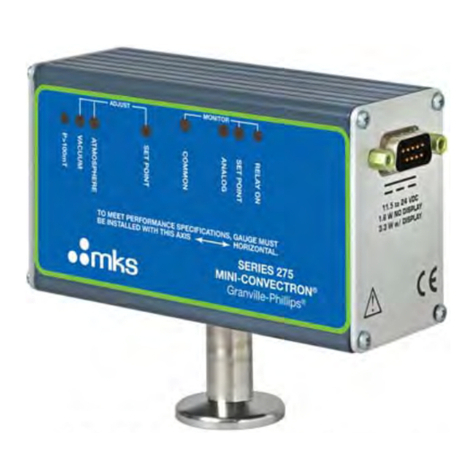
MKS
MKS Series 275 MiniConvectron User manual
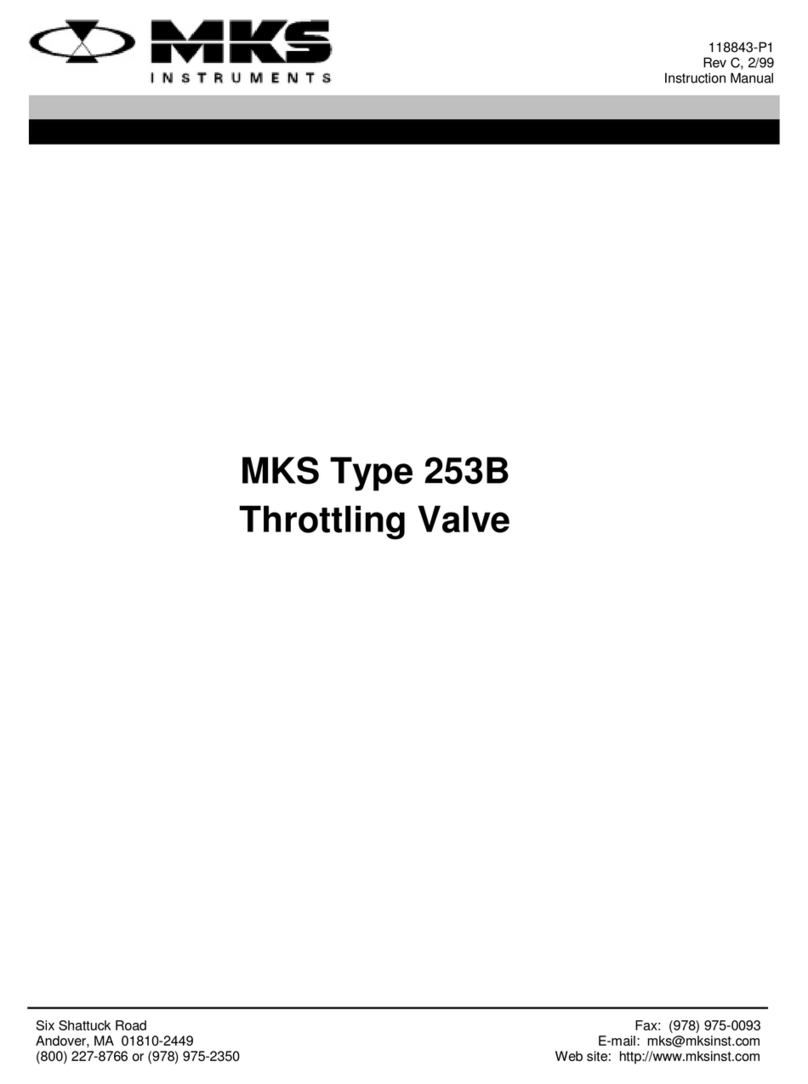
MKS
MKS 253B-2-2-2 User manual