NSS BP27 ULTRA MAXX User manual

BP27 ULTRA MAXX
IMPORTANT SAFETY INSTRUCTIONS
READANDUNDERSTANDALLINSTRUCTIONS
BEFORE OPERATING OR SERVICING MACHINE
DANGER ! Failure to Observe These Instructions Can Cause Personal Injury
to Machine Operator, By-Standers or Possible Machine Damage.
• ALWAYS wear eye protection and protective clothing when working with the batteries.
• The batteries contain ACID. Avoid contact with skin or clothing.
• Antidote: EYES - Flush with water 15 minutes. Call physician.
INTERNAL - Drink water or milk. Follow with Milk of Magnesia, beaten egg or vegetable oil. Call
physician.
• Service should be done only by authorized, trained personnel.
• Charge Batteries in a well ventilated area with Battery Compartment Open.
• Batteries generate explosive gasses - keep sparks, flames, burning cigarettes or other ignition sources away
at all times.
• Batteries are heavy - two (2) people are required for installation or removal.
• Never lay anything on top of batteries to prevent arcing.
• Turn off all switches during installation and service.
• To maintain machine balance, always slide batteries back into position as shown on battery installation decal.
• Connect batteries as shown on battery installation decal to avoid shorting out batteries and electrical system.
• Disconnect battery leads before performing any service or repairs.
• ALWAYS make sure battery charger is turned off when connecting/disconnecting to machine to prevent
sparking.
• ALWAYS operate this machine from the rear control panel, not from the side.
• NEVER operate machine in an explosive atmosphere (grain dust or gas vapor).
• NEVER use flammable liquids (gas, kerosene, solvents or thinners) to clean floor.
• ALWAYS turn off master switch when changing pads.
• NEVER operate machine with skirts or covers removed.
• NEVER leave machine unattended.
PERSONAL INJURY AND PROPERTY DAMAGE FROM MACHINE OVERTURNING, BATTERIES FALLING
OUT OF MACHINE OR BATTERIES LEAKING ACID CAN OCCUR IF YOU DO NOT FOLLOW THESE
PRECAUTIONS:
• NEVER attempt to operate machine unless you have been trained in its operation.
• Follow these rules when working on or near loading docks and ramps:
• ALWAYS be sure ramp is secured to vehicle before attempting to load/unload.
• ALWAYS use extreme caution when operating machine on a ramp or loading/unloading a machine into or out
of a truck. Use extreme caution if ramp is wet, oily or covered with cleaning chemicals.
• NEVER turn machine on an incline.
• NEVER stop machine on a ramp.
• NEVER attempt to climb a grade of more than 20 degrees.
• NEVER park machine near a dock or on ramps.
• NEVER leave machine unattended.
WARNING: Failure to observe these instructions can cause machine damage and possible personal
injury to machine operator.
• NEVER spray machine with water.
• NEVER allow battery charging plugs to get wet. Battery charging plugs will short out if wet.
• NEVER operate machine when charger is plugged in.
• NEVER store machine near furnaces, boilers or flame which may damage machine.
• NEVER store any item on the machine.
• ALWAYS protect machine from freezing temperatures.
SAVE THESE INSTRUCTIONS
https://harrissupplyind.com-ToOrderPartsCall608-268-8080

BATTERYINSTALLATIONINSTRUCTIONS
WET
STORAGE
BATTERY
• Contains ACID, Avoid Contact.
• Antidote: EYES - Flush with water 15
minutes.
• Internal - Drink water or milk. Follow with
Milk of Magnesia, beaten egg or vegetable oil.
•CallPhysician. POISON / DANGER
CAUSES SEVERE BURNS
WARNING
Read Service Manual before installing batteries or
using Charger. Failure to observe the following
instructions may result in damage to the machine
or injury to operator or bystanders.
BATTERYINSTALLATION
INSTRUCTIONS
• Only trained personnel should install batteries.
• Batteries are heavy use two (2) people to install.
• Weareyeprotectionandprotectiveclothing.
• Turn OFF all machine switches.
• Connect batteries as shown to the right (there is
also a decal in the battery compartment with this
picture). Machine will not turn on if batteries are
connectedimproperly.
• Do not lay anything on top of batteries.
• Disconnectbatteriesbeforeperformingany
service or repairs.
CHARGING INSTRUCTIONS
• Read instructions on charger.
• Use only 36 volt charger for 27BP Ultra Maxx.
• BEFORE charging check to insure battery water
level covers battery plates.
• Charge in well ventilated area.
• EXPLOSIVEGAS-DONOTSMOKE-STRIKEA
MATCH OR CAUSE A SPARK DURING
CHARGING.
AFTERcharging-ifneeded-fillbatterytobottom
of fill hole with distilled water.
DO NOT OVER FILL. Battery and machine
damage may result. Wipe any acid from top of
batteries clean with soap solution.
CORROSIVE
ACID
https://harrissupplyind.com-ToOrderPartsCall608-268-8080

FEATURES
https://harrissupplyind.com-ToOrderPartsCall608-268-8080

CONTROLS
https://harrissupplyind.com-ToOrderPartsCall608-268-8080

Before operating and/or attaching/detaching the pads, you must read these instructions:
• The machine can be lowered in the back, which raises up the front for ease of
transportation and pad attachment / detachment.
• The machine arrives in Position No. 1 (the operating position). To lower the back of the
machine to Position No. 3 (the pad changing position), hold operator handle with one hand
and move the Release Knob up with other hand. Lower the machine slowly. Let go of Release
Knob after machine begins to lower. The machine will stop in Position No. 2. Move Release
Knob up again and lower the machine slowly to floor (Position No. 3). Pad can now be easily
attached/detached.
• To raise machine to Position No. 2 (the transport position), lift up on Operator handle with
both hands. The machine will stop in Position No. 2. The machine can now be transported.
• To raise the machine back to Position No. 1, lift up on Operator handle with one hand and
Release Knob up with the other hand. Let go of Release Knob after machine starts to raise
up. The machine will stop in Position No. 1.
• After attaching a new pad and placing machine in Operating position, adjust Pad Pressure
Knob until the arrow (Below Left) points to the Release Knob.
• Push machine forward when starting to avoid possible damage to the floor.
• Increase or decrease Pad Pressure as needed, after machine starts.
Pad Installation
Remove the pad that is supplied in the battery compartment of the machine. Remove the center
hole of the pad and step on the center of the pad to compress the edges around the center hole.
This will allow easier installation of the pad holding cup.
With the machine in the pad changing position, No. 3, carefully center the pad on the driver.
Place pad grabber in the center hole of the pad. Holding the pad grabber, turn the pad driver
clockwise until the pad cup is tight and stops turning.
Caution: Pads must be installed concentric (evenly aligned) with the outside edge of the pad
driver. Failure to follow these precautions will cause excessive machine vibration, a reduction in
pad life and produce unsatisfactory burnishing results. Failure to install the
pad grabber tightly may allow the pad to be thrown from the driver. Never operate the
machine without a Flexiwall Shield in position over the pad.
Setting Pad Pressure
Pad pressure relates to buffing performance. Too much pad pressure will give uneven results and
may cause circuit breaker to blow. Too light pad pressure will also give poor results and no con-
tact with the floor. New pads are manufactured in different thickness; however, ALL pads will thin
down during use and require periodic adjustment of pad. Therefore, follow procedure below:
• ALWAYS Start with ALL pad pressure OFF the floor. Increase pad pressure on the floor in
small increments to prevent damage to the floor.
CAUTION: Too much pad pressure may permanently damage floor.
• The adjustment knob is a simple method of setting the pad pressure based on the
thickness of the pad.
• To increase pad pressure, turn the knob counter clockwise.
• To decrease pad pressure, turn the knob clockwise.
• If the circuit breaker blows on the machine, immediately reduce pad pressure by one full turn
or more on the adjustment knob clockwise. Reset circuit breaker and try machine.
NEW PADS - Always decrease pad pressure three turns after installing a new pad. Move
machine forward while starting machine and fine tune operating amps. Failure to decrease
pad pressure can cause an amp overload, blowing machine circuit breaker.
INSTRUCTIONS
https://harrissupplyind.com-ToOrderPartsCall608-268-8080

What Floor System Works Best With The Ultra Maxx 27BP
.
Dry polishing or burnishing works best with the Ultra Maxx 27BP. Use mop on restorers rather
than spray buff systems to restore the shine. Spray buffing is time consuming, uses more pads
because they become loaded with floor finish, and can cause overloading of the machine’s
circuit breaker.
HOW THE Ultra Maxx 27BP WORKS
The Ultra Maxx 27BP utilizes a 3 HP permanent magnet motor to drive the 27" pad. The pad
pressure is adjustable by turning a knob on the top of the machine, which will either increase or
decrease the pad pressure. The level of pad pressure is indicated on the dial on the right-hand
side of the control panel. The pad is adjusted properly when the arrow on average stays in or on
the green arrow indicating proper amps. Due to imperfections in the floor, the amps will change
slightly. Periodic adjustment may be necessary to keep the dial running in the green. Too much
pad pressure (meter pointing in the red) may cause the circuit breaker to disconnect the circuit to
the motor. If this happens, reduce the pad pressure, push the black button that says “70” and
continue running the machine.
To Begin Operation
Make sure that the correct pad (7/8" to 1") x 27" has been properly installed on the pad driver
with pad grabber and ring in place. You are now ready to run the machine.
WARNING: MACHINE MUST BE MOVING AT ALL TIMES WHEN PAD IS
ROTATING OR FLOOR MAY BE DAMAGED.
Turn the master switch to “I”, check the level of battery work range (put machine on “charge” if not
in the high range). Push the machine forward slightly and squeeze the deadman switch lever to
activate pad driving motor. With the machine moving forward, watch the amp meter for the
average needle position on the meter. Adjust the black knob in the center of the control panel
counter clockwise to increase the pad pressure. It will move the amp indicator needle more
toward the right, or the red area. Adjust the knob clockwise to decrease the pad pressure,
decreasing the amps which moves the needle to the left. Adjust until the amp meter needle
averages in the area of the green arrow, indicating proper amps.
WARNING: NEVER OPERATE MACHINE WITH THE NEEDLE IN THE RED AREA OF
THE METER, OR DAMAGE TO THE MACHINE FROM OVERLOAD MAY RESULT.
Floors that have high or low spots will cause the amp meter to enter into the red area
occasionally. This is to be expected and will cause no harm to the machine. If you operate the
machine continuously in the red area, the circuit breaker, in the rear panel, can and will blow,
indicating too much pad pressure or load. Push the button to reset, decrease pad pressure by
2 or 3 turns or more on the adjustment knob, change or turn the pad; otherwise, damage to the
machine will result. Operating the machine with higher than recommended pad pressure in the
red area will shorten the operating time per battery charge. Maximum operating time can be
achieved by adjusting pad pressure throughout the buffing cycle.
Battery Meter Gauge
Turn the switch to the “I” position. Check to see that light near switch is lit. With master switch on,
check battery meter for charge indication. If needle is in the red area on the left side, marked
“recharge”, the batteries are too low to operate and should be recharged. The middle, green
area, indicates whether or not the batteries are in the high or low range. The right side of the
gauge indicates (when the battery charger is connected and charging and switch is on) the level
of the charge in the batteries, whether high, low or in between. When needle is in the far right,
red area, shown as high, charging of the batteries is complete.
OPERATION
https://harrissupplyind.com-ToOrderPartsCall608-268-8080

MOTOR - The motor used on the Ultra Maxx 27BP requires very little service. Using compressed air,
blow the entire motor every 60 days. Pay close attention to the carbon brush area. Accumulated dirt
will cause excessive carbon brush arcing, reduced brush life, poor machine performance and possible
damage.
CARBON BRUSHES - Inspect every 1000 hours of use for uneven wear and pitting. Replace carbon
brushes when they have worn to a length of 3/8". Failure to replace carbon brushes will cause poor
machine performance and possible motor damage.
WHEELS/CASTER - Every 30 days, lubricate the wheels/caster with an industrial grade bearing
grease. Failure to lubricate wheels/caster will cause the machine to maneuver with difficulty and
premature failure of the wheels/caster and bearing.
PAD PRESSURE/PIVOT LINKAGE - Every 60 days, inspect ALL connections in the pad pressure
adjustment and pivot linkage assembly. All linkage must move freely and smoothly to ensure proper
machine operation. Lubricate each part as required with small amount of grease such as Lubriplate.
Failure to lubricate these components may make it impossible to adjust the pad pressure or place the
machine into all three positions.
DUST CONTROL SYSTEM - Weekly, check the vac hose for connection to the Flexiwall Shield and
filter bag. When filter bag is more than one-half (1/2) full, dispose of old bag and replace with a new
bag. Inspect flexiwall Shield for dents, cracks and wear. A damaged Flexiwall Shield will greatly
reduce the burnishing and dust control capabilities. Dirt build up on the brush should be removed.
POLYETHYLENE BODY - Weekly, clean with aerosol cleaner, “Armorall” type protector or wipe with a
damp cloth. Never Spray machine with water.
NOTES:
MAINTENANCE
https://harrissupplyind.com-ToOrderPartsCall608-268-8080

BASEASSEMBLY
ITEM PART NO.DESCRIPTION QUANTITY
101 64-9-111-3 CONTROL FRAME WELDMENT 1
102 91-2-139-0 11/32 I.D. X 11/16 O.D. X .051/.080 THICK SAE FLAT WASHER (5/16) 2
103 91-2-145-0 5/16-18 HEX NUT WITH NY-LOK INSERT 2
104 64-9-078-3 BASE ASSEMBLY 1
105 91-2-139-0 11/32 I.D. X 11/16 O.D. X .051/.080 THICK SAE FLAT WASHER (5/16) 2
106 91-2-152-0 5/16 SPLIT LOCK WASHER 2
107 91-2-164-0 5/16-18 X 3/4 HEX BOLT 2
108 91-2-100-0 1/4-20 X 5/8 TRUSS HEAD PHILLIPS MACHINE SCREW 2
109 91-2-097-0 1/4 EXTERNAL STAR LOCK WASHER 2
110 23-9-291-1 HOSE/WIRE TIE DOWN 2
111 64-9-070-1 CATCH ASSEMBLY 1
112 91-2-164-0 5/16-18 X 3/4 HEX BOLT 4
113 91-2-152-0 5/16 SPLIT LOCK WASHER 4
114 91-2-139-0 11/32 I.D. X 11/16 O.D. X .051/.080 THICK SAE FLAT WASHER (5/16) 4
115 44-9-534-3 LEFT SUPPORT BRACKET 1
116 44-9-533-3 RIGHT SUPPORT BRACKET 1
117 26-9-258-1 4" GRAY SOFT CASTER COMPLETE 1
44-9-049-1 WHEEL/AXLE ASSEMBLY REPLACEMENT 4" CASTER 1
118 91-2-218-0 13/32 I.D. X 13/16 O.D. X .051/.080 THICK SAE FLAT WASHER (3/8) 4
119 91-2-226-0 3/8-16 X 1 HEX BOLT 4
120 44-9-520-3 FRAME ASSEMBLY 1
121 64-9-020-1 SHAFT COLLAR LEG SUPPORT 2
122 91-2-254-0 1/2-13 X 1 1/4 HEX BOLT 2
123 91-2-242-0 1/2 SPLIT LOCK WASHER 2
124 91-2-245-0 17/32 I.D. X 1 1/16 O.D. X .074/.121 THICK SAE FLAT WASHER (1/2) 2
125 64-9-069-1 LIFT ARM 2
126 44-9-514-6 LIFT ARM SPACER 2
127 91-2-245-0 17/32 I.D. X 1 1/16 O.D. X .074/.121 THICK SAE FLAT WASHER (1/2) 2
128 91-2-242-0 1/2 SPLIT LOCK WASHER 2
129 91-2-254-0 1/2-13 X 1 1/4 HEX BOLT 2
130 44-9-279-6 BUSHING, PIVOT 2
131 91-2-226-0 3/8-16 X 1 HEX BOLT 2
132 91-2-210-0 3/8 SPLIT LOCK WASHER 2
133 91-2-218-0 13/32 I.D. X 13/16 O.D. X .051/.080 THICK SAE FLAT WASHER (3/8) 2
134 44-9-051-1 WHEEL - 8" 2
44-9-048-1 WHEEL BEARING (TWO REQUIRED PER WHEEL) 2
135 64-9-221-1 BASE ASSEMBLY LEG EXTENDER 2
136 64-9-222-1 AXLE, BASE PLATED 1
137 91-2-249-5 1/2-13 THIN HEX NUT WITH N-LOK INSERT 2
138 44-9-279-6 BUSHING, PIVOT 2
139 44-9-516-3 PIVOT WELDMENT 1
140 91-2-254-0 1/2-13 X 1 1/4 HEX BOLT 2
141 91-2-245-0 17/32 I.D. X 1 1/16 O.D. X .074/.121 THICK SAE FLAT WASHER (1/2) 2
142 91-2-147-0 5/16-18 X 1 FLAT HEAD PHILLIPS MACHINE SCREW 2
143 91-2-145-0 5/16-18 HEX NUT WITH NY-LOK INSERT 2
144 91-2-139-0 11/32 I.D. X 11/16 O.D. X .051/.080 THICK SAE FLAT WASHER (5/16) 2
145 91-2-147-0 5/16-18 X 1 FLAT HEAD PHILLIPS MACHINE SCREW 2
https://harrissupplyind.com-ToOrderPartsCall608-268-8080

BASEASSEMBLY
https://harrissupplyind.com-ToOrderPartsCall608-268-8080

SHIELDANDPADDRIVERASSEMBLY
ITEM PART NO.DESCRIPTION QUANTITY
201 64-9-205-1 RUBBER STUD TERMINAL BOOT 2
202 64-9-225-1 MOTOR 36 VOLT, 1500 RPM, 3 HP 1
203 52-9-341-1 1 1/4 X .770 X .082 WASHER 2
204 44-9-266-3 MOTOR MOUNT 1
205 44-9-261-3 FORK 1
206 91-2-139-0 11/32 I.D. X 11/16 O.D. X .051/.080 THICK SAE FLAT WASHER (5/16) 3
207 91-2-152-0 5/16 SPLIT LOCK WASHER 3
208 91-2-164-0 5/16-18 X 3/4 HEX BOLT 3
209 44-9-516-3 PIVOT WELDMENT 1
210 65-9-255-2 BUMPER STRAP 27 1
211 91-2-035-0 10-24 HEX NUT WITH NY-LOK INSERT 1
212 44-9-553-1 END CUFF - 2" 1
213 44-9-554-1 HOSE, 2" DIAMETER X 3 FEET LONG 1
214 44-9-544-1 HOSE CLAMP, 1 9/16" - 2 1/2" DIAMETER 1
215 91-2-045-0 10-24 X 1 ROUND HEAD PHILLIPS MACHINE SCREW 1
216 65-9-253-1 BUMPER/BRUSH 27 1
217 65-9-137-9 FLEXIWALL SHIELD 27 ASSEMBLY 1
218 44-9-289-1 MOTOR KEY 1
219 65-9-030-8 PAD DRIVER 27 ASSEMBLY 1
220 52-9-354-1 MOTOR WASHER 1" O.D., STAINLESS 1
221 91-2-152-0 5/16 SPLIT LOCK WASHER 1
222 91-2-149-0 5/16-24 X 7/8 HEX BOLT 1
223 91-2-081-0 10 X 1/2 SHEET METAL SCREW 3
224 59-9-072-1 SPRING CLIP PAD HOLDER SET 1
59-9-060-1 BIG MOUTH PAD GRABBER ASSEMBLY 1
59-9-061-1 BIG MOUTH - MALE THREAD PORTION 1
225 65-9-270-1 27" LUST LITE BURN PAD - CASE (5) 1
226 91-2-098-0 1/4-20 X 1 SOCKET HEAD CAP SCREW 3
227 91-2-088-0 1/4 SPLIT LOCK WASHER 3
228 91-2-095-0 1/4 FENDER WASHER 3
229 57-9-609-9 PAPER BAG - 6 PACK 1
230 91-2-164-0 5/16-18 X 3/4 HEX BOLT 6
231 91-2-152-0 5/16 SPLIT LOCK WASHER 6
232 91-2-139-0 11/32 I.D. X 11/16 O.D. X .051/.080 THICK SAE FLAT WASHER (5/16) 6
https://harrissupplyind.com-ToOrderPartsCall608-268-8080

SHIELDANDPADDRIVERASSEMBLY
https://harrissupplyind.com-ToOrderPartsCall608-268-8080

CONTROLFRAMEASSEMBLY
ITEM PART NO. DESCRIPTION QUANTITY
301 44-9-052-1 LOAD ADJUST KNOB (INCLUDES SET SCREW) 1
302 91-2-245-0 17/32 I.D. X 1 1/16 O.D. X .074/.121 THICK SAE FLAT WASHER (1/2) 2
303 52-9-457-1 1/2" BOWED WASHER 1
304 64-9-061-1 ADJUSTMENT ROD 1
305 64-9-062-1 ADJUSTMENT ROD COLLAR 1
306 91-2-218-0 13/32 I.D. X 13/16 O.D. X .051/.080 THICK SAE FLAT WASHER (3/8) 1
307 44-9-056-1 INSULATED STANDOFF 1
308 91-2-097-1 1/4 EXTERNAL STAR LOCK WASHER 1
309 91-2-121-0 1/4-20 X 5/8 HEX BOLT 1
310 44-9-101-1 SOLENOID, 36 VOLT 1
311 91-2-093-0 9/32 I.D. X 5/8 O.D. X .051/.080 THICK SAE FLAT WASHER (1/4) 2
312 91-2-088-0 1/4 SPLIT LOCK WASHER 2
313 91-2-117-0 1/4-20 X 1/2 HEX BOLT 2
314 44-9-092-1 1/4-20 X 2 1/2 HEX BOLT GR. 8 1
315 27-9-128-6 BUSHING SPACER 2
316 27-9-128-6 BUSHING SPACER 2
317 91-2-093-0 9/32 I.D. X 5/8 O.D. X .051/.080 THICK SAE FLAT WASHER (1/4) 2
318 91-2-090-0 1/4-20 HEX NUT WITH NY-LOK INSERT 2
319 64-9-060-1 ADJUSTMENT BRACKET WELDMENT 1
320 44-9-532-6 SWITCH BRACKET 1
321 91-2-037-0 7/32 I.D. X 1/2 O.D. X .032/.065 THICK SAE FLAT WASHER (10) 2
322 91-2-032-0 10 SPLIT LOCK WASHER 2
323 91-2-046-0 10-24 X 1 1/4 ROUND HEAD PHILLIPS MACHINE SCREW 2
324 44-9-107-1 SNAP SWITCH 1
325 91-2-013-0 #6 EXTERNAL STAR LOCK WASHER 2
326 91-2-009-0 6-32 X 7/8 PAN HEAD PHILLIPS MACHINE SCREW 2
327 91-2-090-0 1/4-20 HEX NUT WITH NY-LOK INSERT 2
328 44-9-060-1 KNOB, RAISE/LOWER ROD 1
329 64-9-010-1 LATCH HANDLE 1
330 64-9-009-3 LATCHASSEMBLY 1
331 44-9-063-1 COMPRESSION SPRING 1
332 91-2-245-0 17/32 I.D. X 1 1/16 O.D. X .074/.121 THICK SAE FLAT WASHER (1/2) 2
333 44-9-535-6 SPACER GUIDE 4
334 91-2-032-0 #10 SPLIT LOCK WASHER 2
335 91-2-041-0 10-24 X 1/2 ROUND HEAD PHILLIPS MACHINE SCREW 2
336 64-9-070-1 CATCHASSEMBLY 1
337 64-9-227-3 COUNTERPOISE 1
338 64-9-078-3 BASEASSEMBLY 1
339 91-2-088-0 1/4 SPLIT LOCK WASHER 4
340 50-9-430-1 1/4-20 X 2 HEX BOLT 4
341 91-2-152-0 5/16 SPLIT LOCK WASHER 2
342 91-2-164-0 5/16-18 X 3/4 HEX BOLT 2
343 91-2-139-0 11/32 I.D. X 11/16 O.D. X .051/.080 THICK SAE FLAT WASHER (5/16) 2
344 44-9-103-1 SHUNT 1
345 91-2-097-1 1/4 EXTERNAL STAR LOCK WASHER 2
346 91-2-092-0 1/4-20 HEX NUT 2
347 27-9-267-1 WIRE TIE 5 1/2" LONG 6
348 64-9-111-3 CONTROL FRAME WELDMENT 1
349 91-2-097-1 1/4 EXTERNAL STAR LOCK WASHER 2
350 91-2-127-0 1/4-20 X 1 HEX BOLT 2
351 44-9-280-3 TOP SUPPORT BRACKET 1
352 91-2-164-0 5/16-18 X 3/4 HEX BOLT 2
353 91-2-152-0 5/16 SPLIT LOCK WASHER 2
354 91-2-139-0 11/32 I.D. X 11/16 O.D. X .051/.080 THICK SAE FLAT WASHER (5/16) 2
355 91-2-140-0 3/8 I.D. X 7/8 O.D. X .064/.104 THICK WROUGHT WASHER (5/16) 2
356 91-2-148-0 5/16-18 X 1 ROUND HEAD PHILLIPS MACHINE SCREW 2
357 91-2-116-0 1/4-20 X 3/8 HEX BOLT 1
358 91-2-088-0 1/4 SPLIT LOCK WASHER 4
359 91-2-031-0 COTTER PIN 1/8 X 3/4 2
360 91-2-064-0 10-32 X 1/4 SET SCREW - CUP POINT 1
https://harrissupplyind.com-ToOrderPartsCall608-268-8080

CONTROLFRAMEASSEMBLY
https://harrissupplyind.com-ToOrderPartsCall608-268-8080

HOUSINGASSEMBLY
ITEM PART NO.DESCRIPTION QUANTITY
401 64-9-226-1 RUBBER MOTOR COVER 1
402 44-9-554-1 HOSE 2" DIAMETER X 3 FEET LONG 1
403 64-9-176-1 BATTERY WARNING LABEL 1
404 64-9-117-1 SOFT DRAW LATCH WITH CONCEALED KEEPER 1
405 64-9-251-1 BP 27 ULTRA MAXX SIDE DECAL 2
406 91-2-140-0 3/8 I.D. X 7/8 O.D. X .064/.104 THICK WROUGHT WASHER (5/16) 2
407 91-2-148-0 5/16-18 X 1 ROUND HEAD PHILLIPS MACHINE SCREW 2
408 91-2-064-0 10-32 X 1/4 SET SCREW - CUP POINT 1
409 44-9-052-1 LOAD ADJUST KNOB (INCLUDES SET SCREW) 1
410 44-9-104-1 AMP METER 1
411 64-9-113-1 SLIDE RAIL, RIGHT 1
412 44-9-109-1 INDICATOR LIGHT - RED LENS/48VDC 1
413 44-9-110-1 TOGGLE SWITCH, MOTOR 1
414 07-9-882-1 5/8 HEX NUT 1
415 10-9-987-1 STAINLESS FLAT WASHER 1
416 06-9-185-1 LOCK WASHER 1
417 64-9-029-1 DASH PANEL DECAL 1
418 44-9-290-1 SWITCH PLATE - RIGHT 1
419 91-2-127-0 1/4-20 X 1 HEX BOLT 2
420 44-9-288-1 SWITCH PLATE - LEFT 1
421 91-2-218-0 13/32 I.D. X 13/16 O.D. X .051/.080 THICK SAE FLAT WASHER (3/8) 2
422 44-9-105-1 BATTERY METER 36VOLT 1
423 44-9-107-1 SNAP SWITCH 1
424 91-2-004-0 #6 INTERNAL STAR LOCK WASHER 2
425 91-2-009-0 6-32 X 7/8 PAN HEAD PHILLIPS MACHINE SCREW 2
426 27-9-128-6 BUSHING SPACER 2
427 44-9-062-1 3/8 SPRING WASHER 4
428 91-2-090-0 1/4-20 HEX NUT WITH NY-LOK INSERT 2
429 91-2-093-0 9/32 I.D. X 5/8 O.D. X .051/.080 THICK SAE FLAT WASHER (1/4) 2
430 91-2-051-0 10-24 X 1/2 TRUSS HEAD PHILLIPS MACHINE SCREW 4
431 44-9-304-6 HANDLE 1
432 91-2-036-0 10-24 HEX NUT WITH STAR LOCK WASHER 1
433 91-2-037-0 7/32 I.D. X 1/2 O.D. X .032/.065 THICK SAE FLAT WASHER (10) 1
434 91-2-048-0 10-24 X 1 3/4 ROUND HEAD PHILLIPS MACHINE SCREW 1
435 91-2-009-0 6-32 X 7/8 PAN HEAD PHILLIPS MACHINE SCREW 2
436 44-9-190-1 CHARGER PLUG ONLY - GRAY 36 VOLT 1
64-9-082-1 WIRE ASSEMBLY, ANDERSON TO SOLENOID/STANDOFF 36 VOLT 1
437 91-2-079-0 #10 X 5/8 PAN HEAD PHILLIPS SHEET METAL SCREW 8
438 64-9-109-1 LABEL PAD POSITION 1
439 44-9-064-1 EXTENSION SPRING 1
440 91-2-035-0 10-24 HEX NUT WITH NY-LOK INSERT 1
441 44-9-070-1 CIRCUIT BREAKER - 70 AMP/ETA - 2500 BP 1
442 91-2-002-0 6-32 HEX NUT WITH STAR LOCK WASHER 2
443 64-9-027-3 REAR COVER PANEL 1
444 64-9-095-1 1/4 MIPT PLUG 2
445 64-9-189-1 WIRING DIAGRAM DECAL 1
446 64-9-001-1 HOUSING WITH SLIDE RAILS 1
447 91-2-079-0 #10 X 5/8 PAN HEAD PHILLIPS SHEET METAL SCREW 10
448 64-9-224-3 RIGHT FENDER 1
64-9-223-3 LEFT FENDER 1
449 64-9-252-1 BP 27 ULTRA MAXX SIDE LABEL 2
450 91-2-103-7 1/4-20 X 5/8 FLAT HEAD PHILLIPS HEAD PHILLIPS MACHINE SCREW 6
451 64-9-121-1 TAPPING PLATE 2
452 64-9-117-1 SOFT DRAW LATCH WITH CONCEALED KEEPER 1
453 64-9-119-3 HOOD STOP / SUPPORT BRACKET 2
454 91-2-093-0 9/32 I.D. X 5/8 O.D. X .051/.080 THICK SAE FLAT WASHER (1/4) 4
455 91-2-088-0 1/4 SPLIT LOCK WASHER 4
456 91-2-127-0 1/4-20 X 1 HEX BOLT 4
457 44-9-553-1 END CUFF - 2" 1
458 57-9-609-9 PAPER BAG - 6 PACK 1
459 59-9-032-1 WASHER, 5/32 I.D. STEEL 4
460 91-2-093-0 9/32 I.D. X 5/8 O.D. X .051/.080 THICK SAE FLAT WASHER (1/4) 6
461 91-2-090-0 1/4-20 HEX NUT WITH NY-LOK INSERT 6
462 91-2-103-9 1/4-20 X 1 1/2 ELEVATOR BOLT - ZINC PLATED 4
463 91-2-092-0 1/4-20 HEX NUT 4
464 64-9-114-1 SLIDE RAIL, LEFT 1
465 64-9-074-1 HOUSING, HOOD ONLY 1
466 59-9-032-1 WASHER, 5/32 I.D. STEEL 4
467 59-9-031-1 POP RIVET, 5/32 I.D. 4
468 64-9-035-1 HOOD DECAL 1
469 59-9-031-1 POP RIVET, 5/32 I.D. 4
https://harrissupplyind.com-ToOrderPartsCall608-268-8080

HOUSINGASSEMBLY
https://harrissupplyind.com-ToOrderPartsCall608-268-8080

WIRING DIAGAM
ITEM PART NO.DESCRIPTION QUANTITY
164-9-080-1 WIRE ASSEMBLY, BREAKER TO SHUNT 1
264-9-081-1 WIRE ASSEMBLY, SOLENOID TO BREAKER 1
364-9-082-1 WIRE ASSEMBLY, ANDERSON TO SOLENOID / STANDOFF 1
464-9-083-1 WIRE ASSEMBLY, SHUNT TO MOTOR 1
564-9-084-1 WIRE ASSEMBLY, MOTOR TO STANDOFF 1
664-9-085-1 WIRE ASSEMBLY, SOLENOID TO MAIN SWITCH 1
764-9-086-1 WIRE ASSEMBLY, SOLENOID/LIGHT/VOLT METER TO STANDOFF 1
864-9-087-1 WIRE ASSEMBLY, SAFETY SWITCH TO VOLT METER / MAIN SWITCH TO LIGHT1
964-9-088-1 WIRE ASSEMBLY, HANDLE SWITCH TO SAFETY SWITCH 1
10 64-9-089-1 WIRE ASSEMBLY, SOLENOID TO HANDLE SWITCH 1
11 64-9-182-1 WIRE ASSEMBLY, ANDERSON TO POSITIVE/NEGATIVE BATTERY 1
17 64-9-183-1 WIRE ASSEMBLY, ANDERSON TO SOLENOID/STANDOFF 1
97 23-9-198-1 BATTERY JUMPER 3/8" RING #97 2
—27-9-267-1 WIRE TIE, 5 1/2" LONG 6
—44-9-056-1 INSULATED STANDOFF 1
—44-9-070-1 CIRCUIT BREAKER - 70 AMP/ETA 1
—44-9-101-1 SOLENOID, 36 VOLT 1
—44-9-103-1 SHUNT 1
—44-9-104-1 AMP METER 1
—44-9-105-1 BATTERY METER 36 VOLT 1
—44-9-106-1 BATTERY, 205 AMP/HR, 12 VOLT 3
—44-9-107-1 SNAP SWITCH 2
—44-9-109-1 INDICATOR LIGHT - RED LENS/48VDC 1
—44-9-110-1 TOGGLE SWITCH, MOTOR 1
—44-9-190-1 CHARGER PLUG ONLY - GRAY 36 VOLT 1
—44-9-562-1 BATTERY, 185 AMP/HR, 12 VOLT, DRY 3
—64-9-225-1 MOTOR 36 VOLT - 1500 RPM, 3 HP 1
—64-9-184-1 175 AMP ANDERSON WITH CONTACTS GRAY 36 VOLT 2
https://harrissupplyind.com-ToOrderPartsCall608-268-8080

WIRING DIAGRAM
https://harrissupplyind.com-ToOrderPartsCall608-268-8080

MOTOR
ITEM PART NO.DESCRIPTION QTY.
164-9-228-1 1/4-20 X 9 1/2 HEX HEAD BOLT (A-100016-04) 2
291-2-088-0 1/4 SPLIT LOCK WASHER 2
3————- PLUG (NOT AVAILABLE) 1
464-9-205-1 RUBBER BOOT, STUD TERMINAL 2
544-9-162-1 5/16-18 THIN HEX NUT, BRASS 2
644-9-163-1 5/16-18 HEX NUT, BRASS 2
791-2-152-0 5/16 SPLIT LOCK WASHER 2
891-2-139-0 11/32 I.D. X 11/16 O.D. X .051/.080 THICK SAE FLAT WASHER (5/16) 2
944-9-164-1 INSULATION WASHER 2
10 44-9-165-1 INSULATION SPACER 2
11 44-9-166-1 TOP END BELL 1
12 44-9-164-1 INSULATION WASHER 2
13 91-2-139-0 11/32 I.D. X 11/16 O.D. X .051/.080 THICK SAE FLAT WASHER (5/16) 2
14 ————- LEAD HARNESS ASSEMBLY (NOT AVAILABLE) 2
15 44-9-167-1 5/16-18 X 1 3/4 HEX BOLT, BRASS 2
16 ————- 10-32 X 3/8 SCREW, BRASS BINDING HEAD (NOT AVAILABLE) 4
17 44-9-169-1 CARBON BRUSH 4
18 44-9-168-1 BRUSH RING ASSEMBLY 1
19 44-9-170-1 BRUSH SPRING 4
20 91-2-074-0 10-32 X 3/8 TRUSS HEAD PHILLIPS MACHINE SCREW 2
21 64-9-229-1 COMPLETE STATOR ASSEMBLY WITH BAFFLE 1
22 53-9-344-1 THRUST WASHER 1
23 50-9-204-1 TOP BEARING 1
24 64-9-230-1 COMPLETE ARMATURE ASSEMBLY W1-9005 1
25 44-9-173-1 VENT FAN 1
26 44-9-289-1 KEY 1
27 44-9-175-1 RETAINING RING 1
28 44-9-084-1 BOTTOM BEARING 1
29 44-9-174-1 BOTTOM END BELL 1
https://harrissupplyind.com-ToOrderPartsCall608-268-8080

TROUBLE SHOOTING
PROBLEM CAUSE SOLUTION
Pad Does Not Turn Low Battery Charge. Recharge Batteries.
Loose Battery Cable. Tighten & Clamp battery Cables.
Circuit Breaker Has Tripped. Reduce Pad Pressure/Change Pad
Reset Breaker.
Worn Motor Carbon Brushes. Change Carbon Brushes.
Pad Load Adjustment Knob Adjust Knob Until Motor Will
Out Of Adjustment. Turn On.
Micro-switch Not Engaged. Adjust Mounting Bracket.
Machine Pushes Hard Worn Wheel Or Caster. Grease Wheels Or Replace.
Uneven Floor Buffing Worn Pad. Change pad.
Motor out of Alignment. Call NSS Service Center For
Repair.
Machine Vibrates Pad Is Torn Or Not Centered. Center pad.
Change Pad. Use Correct Pad.
Check Pad Driver For Damage
& Replace If Necessary.
Circuit Breaker Trips Pad Pressure Too Heavy. Reduce Pad Pressure. Run
Machine In Green Area of AMP
Meter.
Spray Buffing. Do Not Spray Buff With
BP27 ULTRA MAXX.
Pad Rubbing On Flexiwall Realign Pad On Driver Or
Shield Replace with new pad.
Check Pad size.
Short Running Time Dead Cell In Battery Test Batteries And Replace.
On Battery Charge Excessive Pad Pressure. Reduce Pad Pressure.
Incorrect Pad. Use NSS Pads Or
Recommended Equivalent.
Battery Charger Does Connection Not Made Between Check Anderson Connecters For
Not Turn On Battery Charger And Machine Proper Contact On Both Charger
And Machine.
Improper Charger Sequence. Read Instructions On Battery
Charger Or In Instruction Manual.
https://harrissupplyind.com-ToOrderPartsCall608-268-8080

BP27 ULTRA MAXX ORIG. 01-00 9096431
NSS® Enterprises,Inc.European DistributionCentre
Unit II, Pinfold Trading Estate 55 Nottingham Road
STAPLEFORD, NOTTINGHAM NG9 8AD ENGLAND U.K.
PHONE: (44) 0115 939 1568 FAX: (44) 0115 949 0615
NSS Enterprises, Inc.
3115 Frenchmens Road, Toledo, Ohio 43607
PHONE (419) 531-3761•FAX (419) 531-3761
https://harrissupplyind.com-ToOrderPartsCall608-268-8080
Table of contents
Other NSS Floor Machine manuals
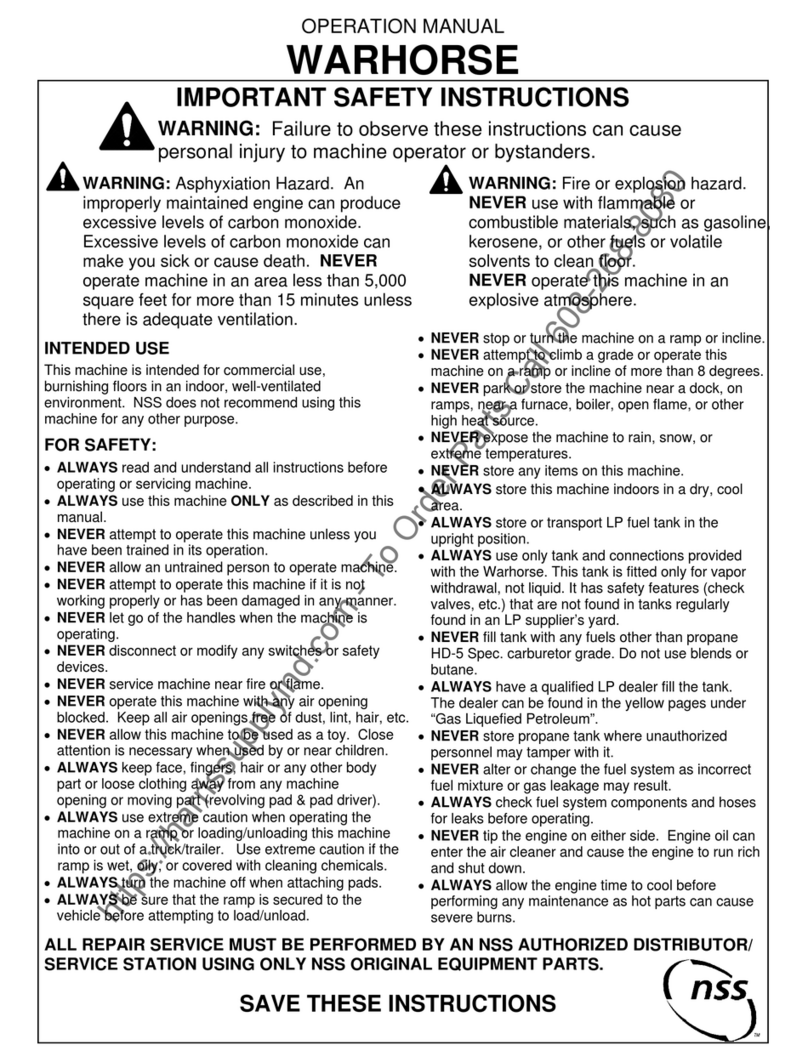
NSS
NSS WARHORSE User manual
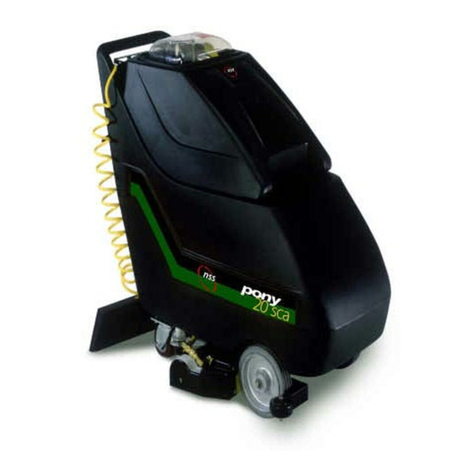
NSS
NSS PONY 20 SCA User manual
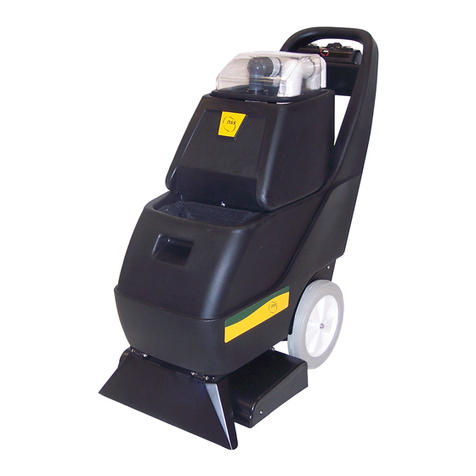
NSS
NSS STALLION 818 SC User manual
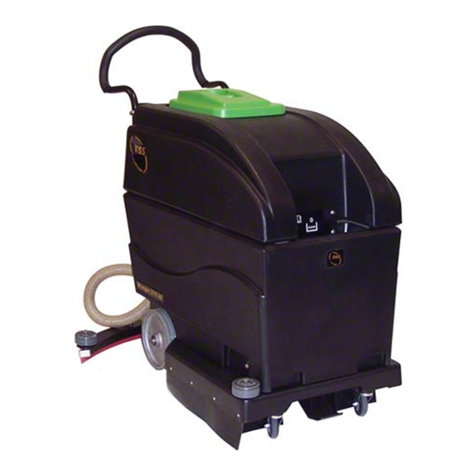
NSS
NSS WRANGLER 1710 AB User manual
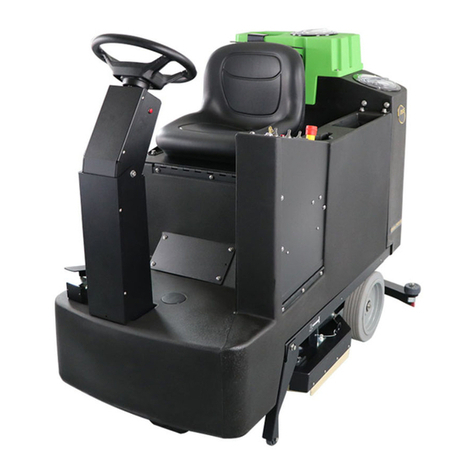
NSS
NSS champ 2929 rb User manual
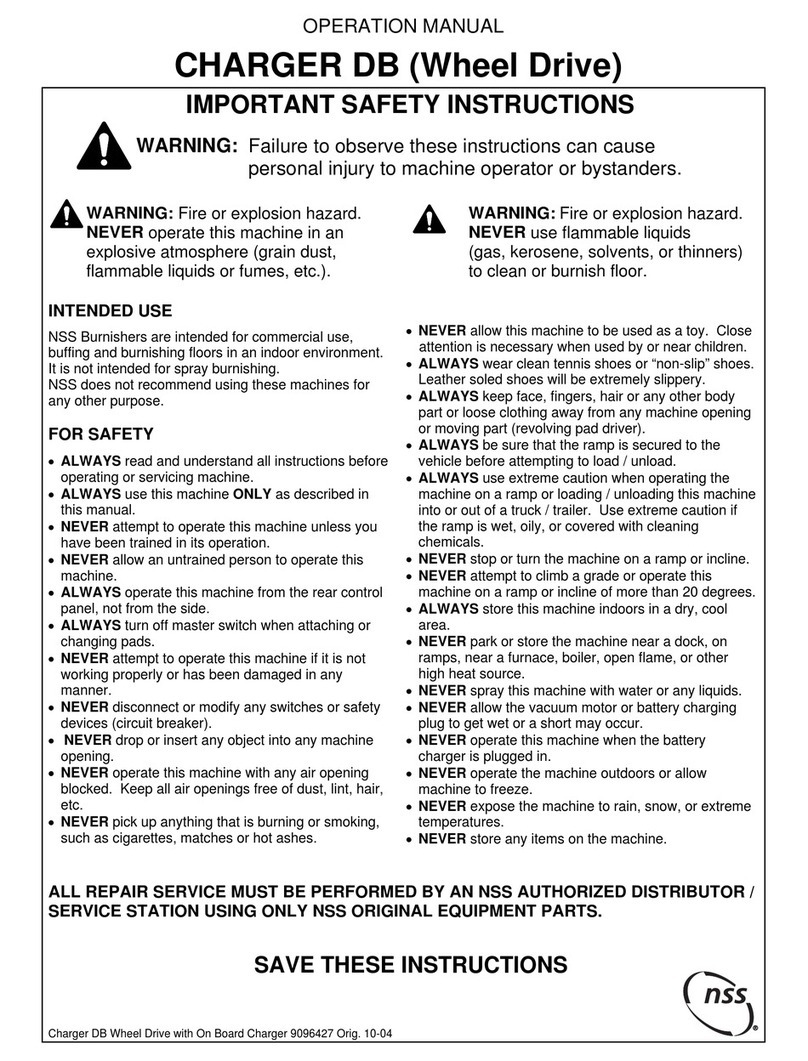
NSS
NSS CHARGER DB User manual
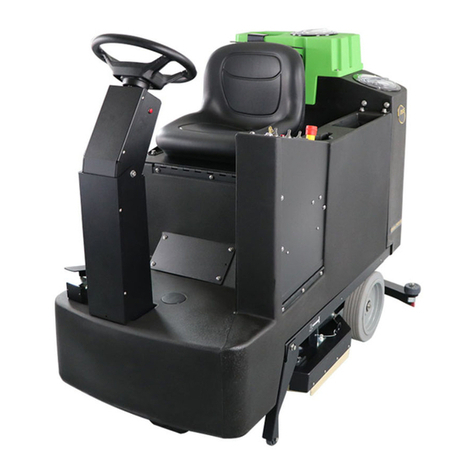
NSS
NSS champ 2929 rb User manual
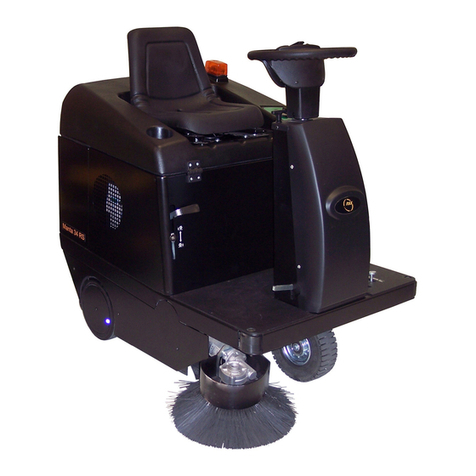
NSS
NSS MANTA 34 RS Manual
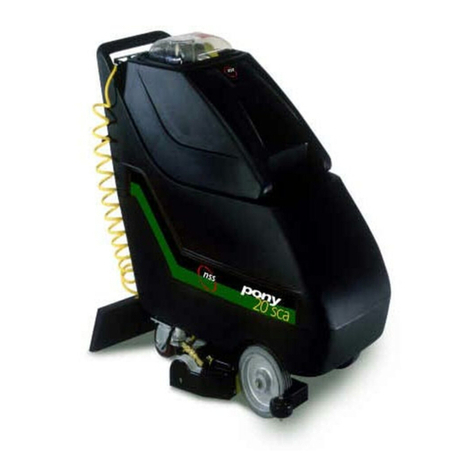
NSS
NSS PONY 20 SCA User manual
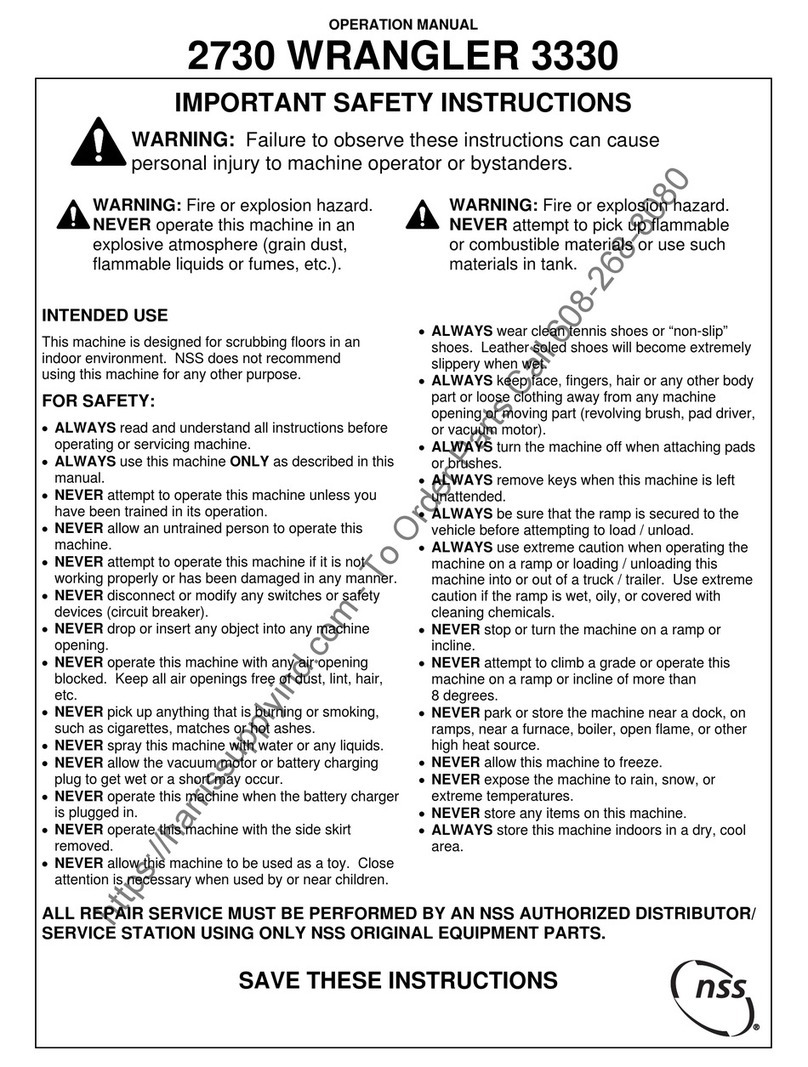
NSS
NSS WRANGLER 2730 User manual

NSS
NSS WRANGLER 2016 AB User manual
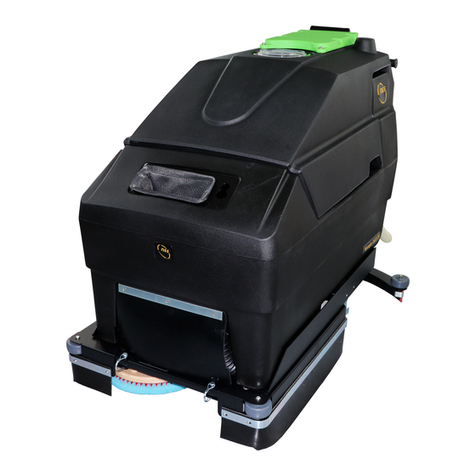
NSS
NSS WRANGLER 26 User manual
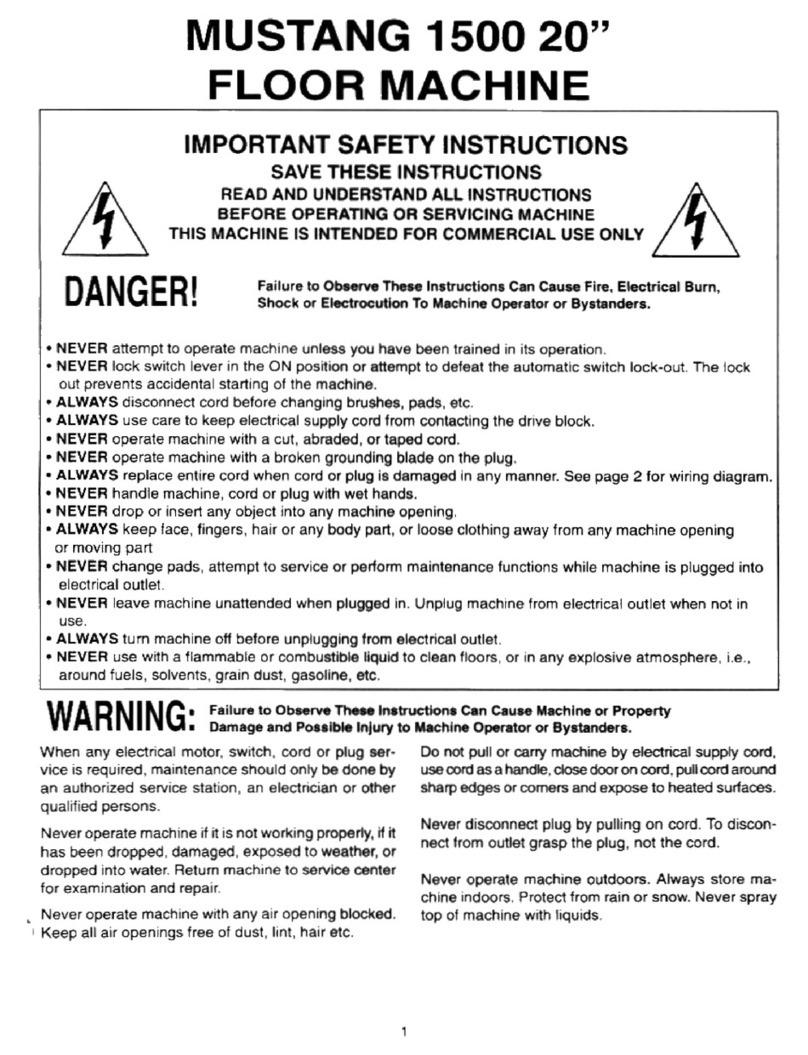
NSS
NSS mustang 1500 User manual

NSS
NSS charger 2000 User manual
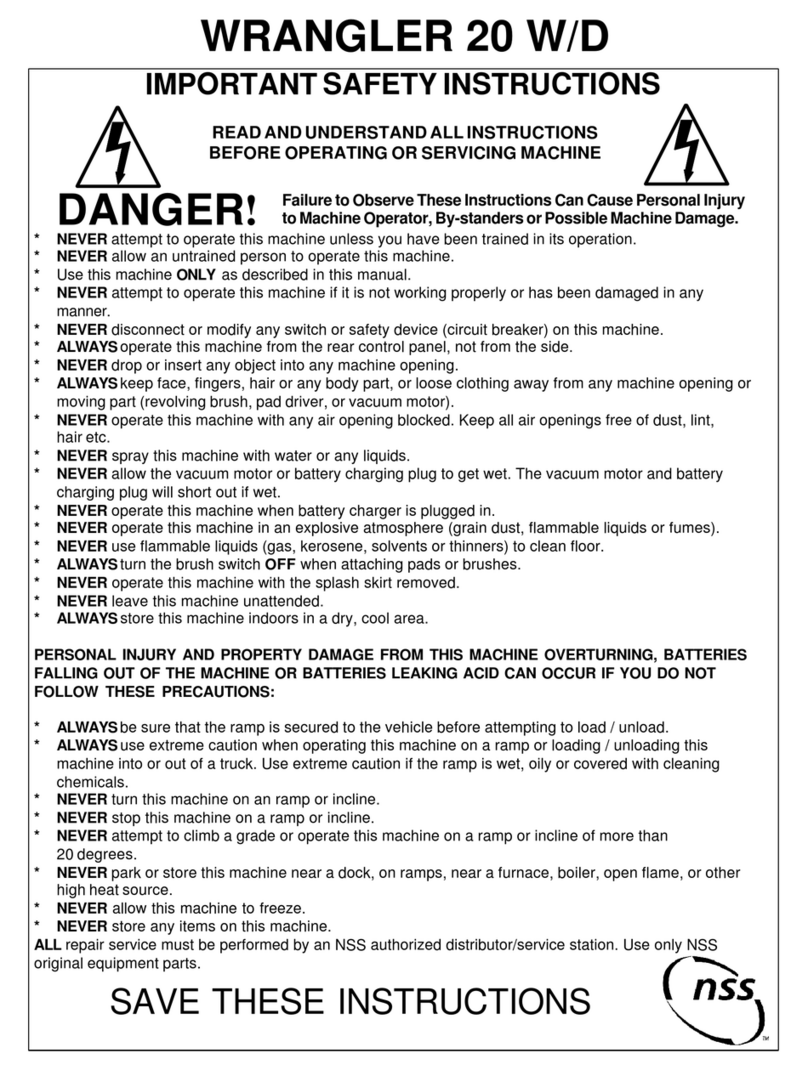
NSS
NSS WRANGLER 20W/D User manual
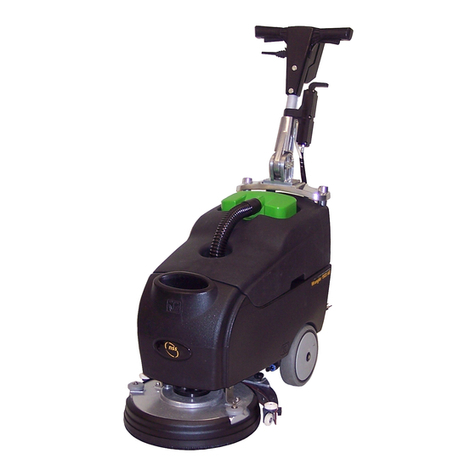
NSS
NSS WRANGLER 1503 AE Operating instructions
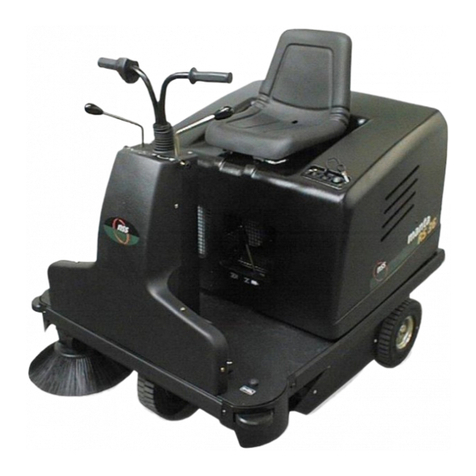
NSS
NSS Manta RS 36 Manual
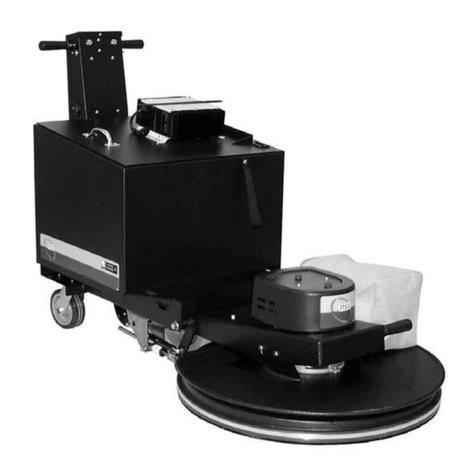
NSS
NSS CHARGER 2717 DB User manual
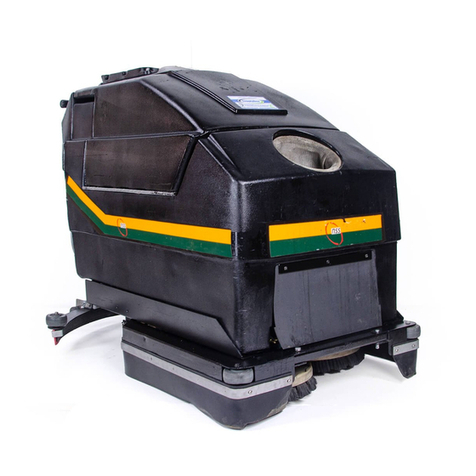
NSS
NSS WRANGLER 2625 DB User manual
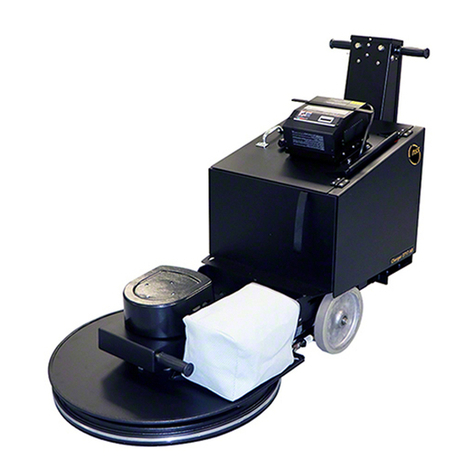
NSS
NSS CHARGER 2717 AB User manual