Oliver 4260 User manual

Warranty
Oliver makes every effort possible to assure that its equipment meets the highest possible
standards of quality and durability. All products sold by Oliver are warranted to the original
customer to be free from defects for a period of 2 (two) years on all parts, excluding electronics
and motors, which are warranted for 1 year. Oliver’s obligation under this warranty shall be
exclusively limited to repairing or replacing (at Oliver’s option) products which are determined by
Oliver to be defective upon delivery F.O.B. (return freight paid by customer) to Oliver, and on
inspection by Oliver. This warranty does not apply to defects due, directly or indirectly, to misuse,
abuse, negligence, accidents, unauthorized repairs, alterations, lack of maintenance, acts of
nature, or items that would normally be consumed or require replacement due to normal wear. In
no event shall Oliver be liable for death, personal or property injury, or damages arising from the
use of its products.
Warning
Read this manual thoroughly before operating the machine. Oliver Machinery disclaims any
liability for machines that have been altered or abused. Oliver Machinery reserves the right to
effect at any time, without prior notice, those alterations to parts, fittings, and accessory
equipment which they may deem necessary for any reason whatsoever.
For More Information
Oliver Machinery is always adding new Industrial Woodworking products to the line. For
complete, up-to-date product information, check with your local Oliver Machinery distributor, or
visit www.olivermachinery.net

1
Table of Contents
SAFETY INSTRUCTIONS ................................................................................................................... 2
Uncrating the Machine.......................................................................................................................... 5
Machine Preparation and Setup.......................................................................................................... 5
Dust Collection....................................................................................................................................... 5
Electrical Connections .......................................................................................................................... 6
Grounding Instrctions............................................................................................................................ 6
On/Off Switch ......................................................................................................................................... 7
Control Box............................................................................................................................................. 7
Cutterhead Guard Installing & Removal ............................................................................................ 7
Cutterhead .............................................................................................................................................. 8
Cutterhead Removal ............................................................................................................................. 8
Fence....................................................................................................................................................... 9
Hand Safety and Placement.............................................................................................................. 10
Jointing .................................................................................................................................................. 10
Direction of the Grain .......................................................................................................................... 10
Edging ....................................................................................................................................................11
Facing.....................................................................................................................................................11
Beveling .................................................................................................................................................11
Rabbeting.............................................................................................................................................. 12
Adjusting the Infeed Table Height..................................................................................................... 12
Adjusting V-Belts ................................................................................................................................. 12
Coplaner Adjusting ...............................................................................................................................13
Coplaner Adjusting Continued .......................................................................................................... 14
Basic Operations ................................................................................................................................ 15
Push Blocks.......................................................................................................................................... 15
Trouble shooting .................................................................................................................................. 18
PARTS DIAGRAMS ............................................................................................................................ 19
PARTS LIST......................................................................................................................................... 22
Lubrication............................................................................................................................................ 13

2
SAFETY INSTRUCTIONS
For Your Safety Read Instruction Manual Before Operating Jointer
As with all machines, there is a certain amount of hazard involved with the use of this jointer. Use the
machine with the respect and caution demanded where safety precautions are concerned. When normal
safety precautions are overlooked or ignored, personal injury to the operator can result.
Wear eye protection.
Never make jointing , planning, or rabbeting cut deeper than 1/8 in.
Always use hold-down/push blocks for jointing material narrower than 3 inches, or planning material
thinner than 3inches.
Never perform jointing. Planning, or rabbeting cuts on pieces shorter than 8 inches (203 mm) in
length.
Keep guards in place and in working order.
Remove adjusting keys and wrenches. Form habit of checking to see that keys and adjusting
wrenches are removed from tool before turning it on .
Keep work area clean. Cluttered areas and benches invite accidents.
Don’t use in dangerous environment. Don’t use power tools in damp or wet locations, or expose them
to rain. Keep work area well lighted.
Keep children away. All visitors should be kept safe distance from work area.
Make workshop kid proof with padlocks, master switches, or by removing starter keys.
Don’t force tool. It will do the job better and safer at the rate for which it was designed.
Use right tool. Don’t force tool or attachment to do a job for which it was not designed.
Use proper extension cord. Make sure your extension cord is in good condition. When using an
extension cord, be sure to use one heavy enough to carry the current your product will draw. An
undersized cord will cause a drop in line voltage resulting in loss of power and overheating Table
(see Figure 9) shows the correct size to use depending on cord length and nameplate ampere rating.
If in doubt, use the next heavier gage. The smaller the gage number, the heavier the cord.
Wear proper apparel. Do not wear loose clothing, gloves, neckties, rings, bracelets, or other jewelry
which may get caught in moving parts. Nonslip footwear is recommended. Wear protective hair
covering to contain long hair.
Always use safety glasses. Also use face or dust mask if cutting operation is dusty. Everyday
eyeglasses only have impact resistant lenses, they are NOT safety glasses.
Secure work. Use clamps or a vise to hold work when practical. It’s safer than using your hand and it
frees both hands to operate tool.
Don’t overreach. Keep proper footing and balance at all times.

3
Maintain tools with care. Keep tools sharp and clean for best and safest performance. Follow
instructions for lubricating and changing accessories.
Disconnect tools before servicing; when changing accessories, such as blades, bits, cutters, and the
like.
Reduce the risk of unintentional starting. Make sure switch is in off position before plugging in.
Use recommended accessories. Consult the owner’s manual for recommended accessories. The use
of improper accessories may cause risk of injury to persons.
Never stand on tool. Serious injury could occur if the tool is tipped or if the cutting tool is
unintentionally contacted.
Check damaged parts. Before further use of the tools, a guard or other part that is damaged should
be carefully checked to determine that it will operate properly and perform its intended function –
check for alignment of moving parts, binding of moving parts, breakage of parts, mounting , and any
other conditions that may affect its operation. A guard or other part that is damaged should be
properly repaired or replaced.
Direction of feed. Feed work into a blade or cutter against the direction of rotation of the blade or
cutter only.
Never leave tool running unattended. Turn power off. Don’t leave tool until it comes to a complete stop.
Do not perform jointing operation on material shorter than 10 in , narrower than 3/4 in, or less than 1/4
in thick.
Maintain the proper relationships of infeed and outfeed table surfaces and cutter head knife path.
Support the work piece adequately at all times during operation; maintain control of the work at all
times.
Do not back the work toword the infeed table.
Do not attempt to perform an abnormal or a little-used operation without study and the use of adequate
hold-down/push blocks, jigs, fixtures, stops and the like.

4
Hand safety. It is good practice to move the hands
in an alternate motion from back to front as the
work continues through the cut. Never pass the
hands directly over the cutter knife. As one hand
approaches the knives remove it from the stock in
an arc motion and place it back on the stock in a
position beyond the cutterknife.
Three inch rule. When working a piece of wood on
the jointer, follow the 3 inch radius rule. The hands
must never be closer than 3 inches to the cutter
head.
Health hazards. Some dust created by power
sanding, sawing, grinding, drilling and other construction activities contains chemicals known to cause
cancer, birth defects or other reproductive harm. Some examples of these chemicals are:
*Lead from lead-based paint.
*Crystalline silica from bricks and cement and other masonry products.
* Arsenic and chromium from chemically-treated lumber.
Your risk from these exposures varies, depending on how often you do this type of work. To reduce
your exposure to these chemicals, work in a well-ventilated area, and work with approved safety
equipment, such
as those dust masks that are specifically designed to filter out microscopic particles.
Familiarize yourself with the following safety notices used in this manual:
CAUTION: (This means that if precautions are not heeded, it may result in minor or moderate injury
and/or possible machine damage)
WARNING: (This means that if precautions are not heeded, it could result in serious injury or
!
possibly even death).
!

5
Uncrating the Machine
Uncrate the machine and inspect the unit for
signs of shipping damage. If damage is found,
contact your dealer immediately. Unbolt the
machine from the pallet. Retain all
packaging materials in case it becomes
necessary to ship the machine to another site.
Moving the Machine into Place
Do not lift the jointer by the tables
from the
pallet to the shop position. This may change
coplanar alignment and will need to be
corrected before use. See page 13 for
coplanar adjustments.
To move the machine, use the supplied 3/4”
lifting bars by placing them through the stand
and securing with properly rated straps on
each side.
WARNING: The equipment used to lift this
machine must have a rated capacity at or
above the weight of the jointer. Failure to
comply may cause serious damage and injury.
Machine Preparation and Setup
The jointer must be positioned on a smooth,
level surface. The area must be well lit and
have plenty of room to maneuver with large
pieces of wood.
Level the jointer front to back and side to side
using a level placed on the table. Use shims
under the corners, if necessary, but make sure
the jointer is stable before being placed into
service.
Clean all rust protected surfaces with a
commercial solvent. Do not use acetone,
gasoline, lacquer thinner or any type of
flammable solvent, or a cleaner that may
damage paint. Cover cleaned surfaces with
WD-40 or a 20W machine oil.
Dust Collection
The 6” dust collection port (A, Fig. 1) is located
below the outfeed table. Typically flex hose is
used to run from this point to a central trunk
line.
Note: Do not operate the jointer without
dust collection.
Fig. 1
Fig. 1
A

6
Electrical Connections
Depending on how this jointer was ordered it could be
made to operate at 220V single phase or 220V/440V
three phase. Be sure to confirm the correct operating
rating before connecting to power.
The jointer is supplied with a power cord, but no plug.
It may be hardwired to the service in accordance with
local electrical code. If a plug is used it must be
properly rated for the motor and match the outlet used.
Never use an adapter between plug and outlet and
always ground the machine.
To convert from 220V three phase to 440V three
phase new parts are required. Contact Oliver
Machinery for details.
With three phase power make sure the cutter head
rotation is in the proper direction.
All wiring and electrical connection must be done by a
qualified electrician and meet local electrical codes.
Grounding Pin

7
Control Switch
The control switch comes mounted to the infeed table
as shown Fig. 1
The control switch features an on and an off switch.
The off switch features a lock that must be twisted
clockwise to reset before the machine can be started.
This machine features magnetic motor controls. In
the event of power loss, the machine will not start
when power is restored until the on switch is pressed.
WARNING: Ensure that your workplace is
inaccessible to children by closing and locking all
entrances when you are away. NEVER allow
untrained visitors in workplace when assembling ,
adjusting or operating equipment.
Cutterhead Guard Installing & Removal
1. Disconnect jointer from power source.
2. Turn knob (A) counterclockwise to create tension
on spring, and hold it there Fig 3.
3. Insert guard post (B) down through hole in front of
ledge.
4. Slightly turn set (A), if necessary, until the guard
seats itself, and the spring engages the slot at the
end of the guard post.
5. Check the guard for proper tension. If guard does
not spring back into place when pulled back from
cutterhead, remove guard and adjust spring
tension by repeating steps 1-3 until correct tension
is achieved. NEVER run the jointer without the
guard.
WARNING: Use the jointer guard for all
operations except rabbeting.
Fig. 1
Fig. 2
Fig. 3
!

8
Helical Cutterhead
Knife inserts are dangerously
sharp. Use extreme caution when inspecting,
removing, or replacing knife inserts.
The knife inserts on the Jointer are four-sided.
When dull, simply remove each insert, rotate it 90°
for a fresh edge, and re-install it. No further
adjustment is necessary. Use the two provided torx
wrench to remove the knife insert screw. Use one
of the torx wrenches to help hold the cutterhead in
position, and the other to remove the screw. See
Fig. A. It is advisable to rotate all inserts at the
same time to maintain consistent cutting. However,
if one or more knife inserts develops a nick, rotate
only those inserts that are affected.
Each knife insert has an etched reference mark so
you can keep track of the rotations.
IMPORTANT: When removing or rotating inserts,
clean saw dust from the screw, the insert, and the
cutterhead platform. Dust accumulation between
these elements can prevent the insert from seating
properly, and may affect the quality of the cut.
Before installing each screw, lightly coat the screw
threads with machine oil and wipe off any excess.
Securely tighten each screw which holds the knife
inserts before operating the jointer!
Make sure all knife insert screws are tightened
securely. Loose inserts can be propelled at high
speed from a rotating cutterhead, causing injury.
Fig. A
Cutterhead Removal
If removal of the cutterhead is necessary, do the
following:
WARNING: Disconnect jointer from power
source.
1. Remove the entire fence assembly by releasing
lock handle and removing hex nuts. Lift the
fence off the machine.
2. Loosen the bolts connecting the motor to the
motor mount and remove the drive belt from
cutterhead pulley.
3. Lower bothinfeed andoutfeed tables to expose
the cutterhead.
4. Remove the two bolts and spring washers which
secure the cutterhead to thebase, as shownin
Fig. B.
5. Remove the cutterhead as sembly, with studs
attached, by lifting cutterhead straight up from
base. Thebelt pulley maybe left on
cutterhead to assist in raising the cutterhead.
6. Remove pulley andboth bearing housings with
attached studs from thecutterhead.
NOTE: You maywish to keep on hand an
extra cutterhead in order to maintainshop
productivity.
7. When mounting newcutterhead to base, make
sure thecurved seats of thebasearecleaned and
free of dust andgrease.
Fig B
!

9
Fence
The fence is assembled and comes mounted
to the jointer. If it needs to be removed, take
off by removing the bolts as shown Fig, 4
The width adjustment handwheel (D, Fig. 5)
will need to be installed.
WARNING: Never make any adjustments to
the fence when the machine is running. All
machine adjustments should be made with
the power off or machine unplugged.
Fence Legend
The various adjustments, locks and handles
are shown in Fig.5.
A. 90 degree adjust bolt.
B. Angle lock handle.
C. 90 degree flip stop.
D. Width adjustment handwheel.
E. 45 degree adjust bolt.
F. Width lock handle.
G. Fence angle adjust handle.
Adjustment of the 90 Degree Stop
1. Lay a square on the infeed table as shown
in Fig. 6
2. Loosen the angle lock handle (B, Fig. 5).
3. Ensure the 90 degree flip stop
(C, Fig. 6) is in the 90 degree position.
4. Loosen the jam nut on the 90 degree
adjusting bolt (A, Fig.6) and adjust the bolt
against the flip stop until the fence becomes
true with the square.
5. Tighten the jam nut while holding the bolt
in position.
Fence Operation
To tilt the fence, see Fig.5. Loosen angle
lock handle ‘B’, flip up the stop ‘C’, and tilt
the fence with the fence angle adjusting
handle ‘G’ to the desired angle. Use a
protractor or adjustable triangle to set the
angle. A 45 degree stop, ‘E’ is provided for
quick set-up at this angle.
To adjust the cutting width loosen the lock
handle ‘F’ and turn the width adjustment
handlwheel ‘D’ to move the fence toward
or away from the rabbeting ledge.
Once any adjustments are made be sure
to lock them into place.
Fig. 4
Fig. 5
Fig. 6

10
Fig. 7
Hand Safety and Placement
Never pass the hands directly over the cutter
knife. As one hand approaches the knives
remove it from the stock in an arc motion and
place it back on the stock in a position beyond
the cutter knife. See Fig 7.
When feeding the work piece, pressure is
applied not only toward the cutterhead but
against the fence and down to the table as well.
At the start of the cut, the left hand holds the
material down and toward the fence while the
right hand pushes toward the cutterhead. As
the material crosses the cutterhead the left
hand comes up and over as in Fig 7 to
continue the pressure but now on the outfeed
table. As the right hand approaches the
cutterhead it is time to move it up and over the
cutterhead in the same fashion as the left in
Fig 7 all the while continuing pressure as
stated above.
WARNING: Keep all guards in place. Keep hands
away from the cutterhead! Always use push stick
when possible.
Failure to comply may cause serious injury.
Jointing
In order to craft a good woodworking project, it
is necessary to have a square piece of wood to
start with. The way to do this is with a jointer.
You need one straight edge and one flat face.
After you have these, you can plane to
thickness and rip to width and the resulting
piece will be square and true on all four sides.
At this point you can begin building your
project.
Direction of the Grain
To avoid tear out, always feed the material in
the direction of the grain. If the direction of the
grain changes half way through the board, try
taking lighter cuts at a slower feed rate. If the
results are still unsatisfactory, try turning the
material around and feeding the other way. Fig. 8
(Fig. 8)

11
Edging
To give a good straight edge for gluing or
joining, set the fence square with the table.
Remove the least amount of material required
to obtain a straight edge. Hold the best face
of the piece firmly against the fence throughout
the feed. When finished you will have a perfect
starting point for your project. (Fig. 9)
Facing
Once you have a good edge it is time to
eliminate any warp or cup on the board. Keep
in mind the outfeed table is the reference point
and once the material is past the cutterhead,
downward pressure should be applied to the
outfeed table only. Putting downward pressure
on the board over the infeed table will bend any
cup or warp prior to hitting the cutterhead and
after the pressure is released, the cup will
spring back. At the same time try keeping a
constant feed rate in order to give a good
smooth cut with no burn marks
.
(Fig. 10)
Beveling
For beveling (Fig 11), set the fence to the
desired angle using a protractor and lock into
place. Feed the material through pressing
firmly against the fence and tables. Several
passes may be necessary for the desired result.
Fig. 9
Fig. 10
Fig. 11

12
Rabbeting
1. Adjust the fence so that the distance
between the edge of the knife and the
fence is equal to the width of the desired
rabbet (Fig 12).
2. Lower the infeed table to the depth of the
rabbet required. If the rabbet is quite deep
it may be necessary to do it in increments.
WARNING :
Rabbeting requires removal of
the blade guard. Use extreme caution and
replace the guard after completion.
Adjusting the Infeed Table Height
The height of the infeed table with respect to
the cutting circle will determine the amount of
material to be removed from the work piece.
To raise or lower the table, turn the height
adjusting wheel (A, Fig 13) on the back of
the infeed table to the desired height indicated
by the guage (B, Fig 13).
Infeed Table Lock
The 4260 jointer is equipped with an infeed
table lock that will limit the maximum depth of
cut to 1/8” unless released by the operator.
The lock must be released during any infeed
table adjustment to prevent damage to the
raising mechanism.
Adjusting V-Belts
After the first 20 hours of operation it is
necessary to check the tension on of the V-
belts. To do this, loosen the knob A open the
pulley cover (C, Fig. 14). With medium finger
pressure the belt should push in approximately
½” about midway between the pulleys. If there
is too much play, remove the four screws (B,
Fig. 14) and take the cover off. Adjust the
tension by loosening the bottom jam nut on
the bracket (A, Figure 15) and then turn down
the top nut until the desired tension is
achieved.
Fig. 12
Fig. 13
Fig. 14
.
Fig. 15

13
Lubrication
Periodically apply a lightgrease to the tables up/
down lead screw. As well, apply a light oil to the
dovetail ways from time to time to allow ease of
movement.
The cutterhead bearings are permanently
greased for life and do not require care.
Setting Table Coplanar
To achieve optimal results from your jointer, the
infeed and outfeed tables must be parallel front
to back and side to side, coplanar. If they are
not, the finished workpiece may have a slight
taper to it.
The tables have been properly aligned at the
factory and the results are on an inspection
sheet included with the new product. However,
during handling and normal use, the tables can
come out of adjustment. This alignment should
be checked periodically or when the finished
workpiece shows a taper.
The following steps should be followed to set the
tables coplanar. It is the same procedure to set
both infeed and outfeed tables. A steel straight
edge is needed to properly complete this
adjustment.
Disconnect the jointer from the power source. If
hardwired turn the breaker off at the service
panel.
Remove the cutter head guard. Be extremely
careful around the cutter inserts, they are very
sharp.
Slide the fence as far back as possible or
remove it from the machine.
Loosen the table locks on the front of the
machine.
Adjust the outfeed table above the cutter head.
Lock the outfeed table in this position.
Place the steel straight edge across the edge of
the outfeed table and extending over the infeed
table.
Raise the infeed table until it just comes in
contact with the steel straight edge. Lock the
infeed table in this position.

The machinist straight edge should lie evenly
across the infeed and outfeed tables without a
gap between the straight edge and tables. Move
the straight edge across the tables and check for
gaps at any position from front to back.
If the steel straight edge does not lie evenly and
gaps are found one or both tables may need to be
adjusted to make the tables coplanar.
Both tables are adjusted in the same manner.
Adjust one table and then the other if needed.
Proceed as follows with the outfeed table first if
both need to be adjusted.
Each table has four cam adjusting nuts, two in the
front and two in the back (A, Fig. 16). One front
adjusting nut is located behind the table raising
handwheel and one back adjusting nut is located
inside covers B (Fig. 17).
Now that the four cam adjusting nuts are exposed
you will need to loosen the set screws before any
adjustment. Above each cam adjusting nut is a
plastic cap, pry out the cap and remove the set
screw below the cap.
With a 32mm wrench (not included) adjust the
cam nuts to raise or lower that portion of the table
as needed until the table coplanar is properly
aligned with no gaps between the straight edge
and tables. Repeat at each point until all are
aligned.
Retighten each set screw and replace the plastic
caps.
Replace the cover of back adjusting nut.
Adjust the outfeed table even with the cutter head
and the infeed table to the desired cutting depth.
14
Fig. 17
Fig. 16

15
Basic Operations
Before making anycutson the stock, makeafew
practice cuts by raising the infeed table to “0" and
with the power disconnected. In this manner you will
acquaint yourself withthefeel of jointer operations.
SURFACING
Twohanded
pushblock
Adjust depth of cut. It is better to makecuts of ap-
proximately 1/64 inch. This will enable youto have
bettercontrol overthematerial being surfaced. Make
several passes if necessary to obtain proper stock
removal.
Never surface pieces shorter than12 inches or thin-
nerthan3/8 inchwithout the useof aspecial work
holding fixture. Never surface pieces thinner than3
inches without the use of apush block. On stock 8"
to 12"longuseasingle two-handed push block (Fig.
18). On stock longer than12 inches usetwo push
blocks (Fig. 19). Withnarrow stock usethetype
push block shown in Fig.20.Whensurfacing short
stock over 4inches wide, use two (2) push blocks to
guide material over cutterhead (Fig. 21).
L-shaped push block
for narrow stock
Two push
blocks forstock
longer than 12
inches
Fig. 18
Fig. 19
Twopush blocks
with dowels
forshort stock
over 4inches wide
Fig. 20
Fig. 21

15
SURFACING: LONGBOARDS
Theuseof pushblocks willhelpto insure against
hands coming in contact with cutterhead in the event
of akickback andas trailing endof boardpasses over
cutterhead.
When surfacing longstock, place push block near
thefront of piece andstart feeding woodwiththe right
hand until guard hasopened andcutis started (Fig.
21). Place second pushblock nearthe rearof infeed
table and continue feeding stock using the hand over
hand method (Fig. 22). Before the left hand is in the
3inch areaof the cutterhead moveit over to theoutfeed
side(Fig. 23). As soon as possible follow with the
right hand over to theoutfeed sideandcontinue through
with cut(Fig. 24).
Begin by feeding stockwithright hand andapply pres-
sure to front of stock with push block.
When the stock is longer thantwice the length of the
infeed andoutfeed tables, another helper or support
table mustbe usedto support thestock.
Left hand pushes
downtoward fence
as right hand
starts feed
F
Fig. 21
Near cutter,
feedhand
over hand
1
F
ig. Fig. 22
Left hand is
moved to
outfeed
side
Fig. 23
Fig. 24
On outfeed
Side both hands
pull stock through

16
JOINTING (orEDGING)
Never edge aboard that is less than 3inches wide,
less than1/4 inchthick, or12 inches long,without
using apush block.
Movefenceforward
to expose onlyamount
of cutterhead required
CAUTION: When workpiece is twice the
length of the jointer infeed or outfeed
table usean infeed or outfeed support.
Begin by feeding stockwithright hand andapply pres-
sure to front of stock withpush block. Whenedging,
make cuts of approximately 1/16inch forhardwood
and1/8 inchfor softwood.
When edging woodwider than3inches lapthefin-
ersover the top of thewood, extending themback
over the fence such that they will act as astop for the
hands in the event of akickback. Keep stock against
thefence (Fig. 25).
BEVELING
When beveling never makecut deeper than1/16inch.
Makecertain material being beveled is over 12 inches
long, morethan 1/4 inchthick and1inchwide.
Setfence to desired angle.
CAUTION: Although fence may be tilted in or
out for bevel cut, we recommends for safety
reasons the fence be tilted in, if possible,
making a cradled cut (Fig. 26).
F
Fig. 25
F
Fig. 26
For wood wider than 3inches, hold with fingers close
together nearthe top of thestock, lapping over the
board andextending overthefence. Whenbeveling
material less than 3inches wide, usebeveled push
blocks andapply pressure toward the fence. Keep
fingers neartop of push block (Fig. 27).
When beveling short material useonebevel hold down
andapplypressure toward thefence. Keepthumb
above the ledge on hold downblock (Fig.28).
CROSS GRAIN
NOTE: Whenbeveling round fouredges of a
workpiece, make cross grain cuts first.This will help
clean up anychipping or splintering whenbeveling
theend grain.
Forlong boards, follow thesame hand-over-hand pro-
cedure used for surfacing long boards, (page 15).
Fig. 27
Fig. 28

17
Push Blocks
Push blocks are simple, yet necessary toolsto
assist the operator especially when jointing thin
or short stock. Illustrated in Figure 30 are three
types of push blocks commonly used in jointing.
Pushblocks may be obtained commercially or
easily constructed.
NOTE: The Jointer is supplied with two push
block Figure 29 for feeding stock.
Fig. 29
Fig. 30
Table of contents
Other Oliver Power Tools manuals
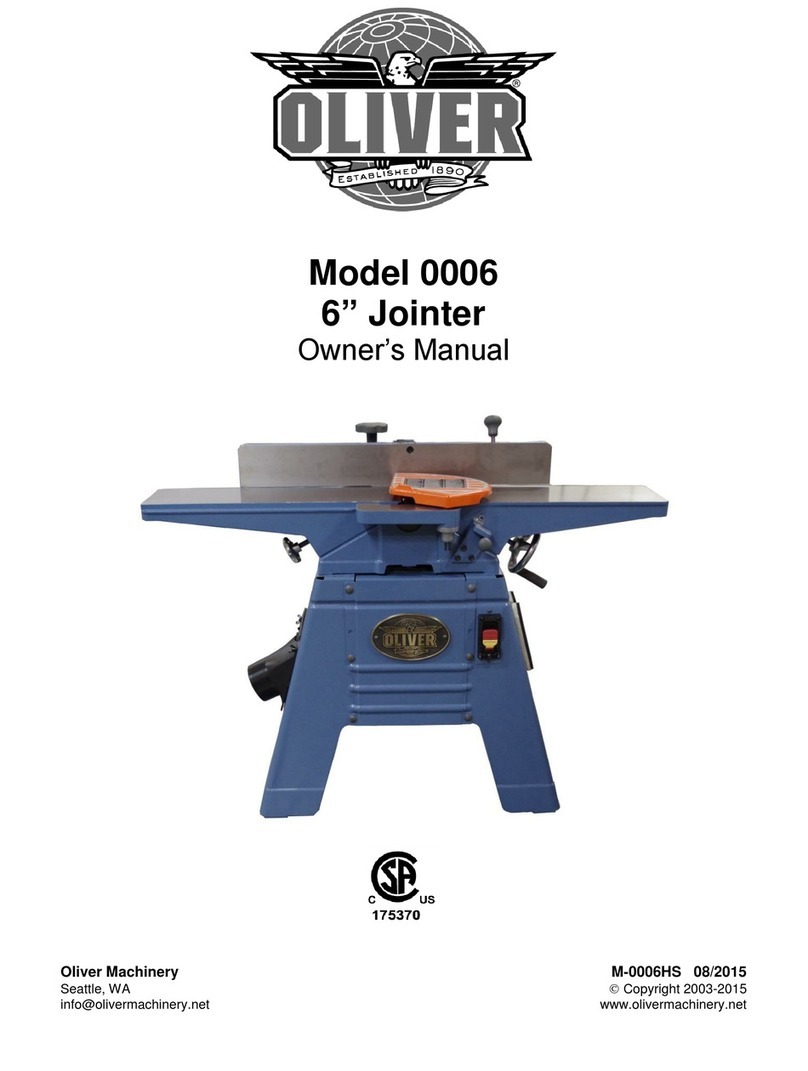
Oliver
Oliver 0006 User manual

Oliver
Oliver 4705 User manual
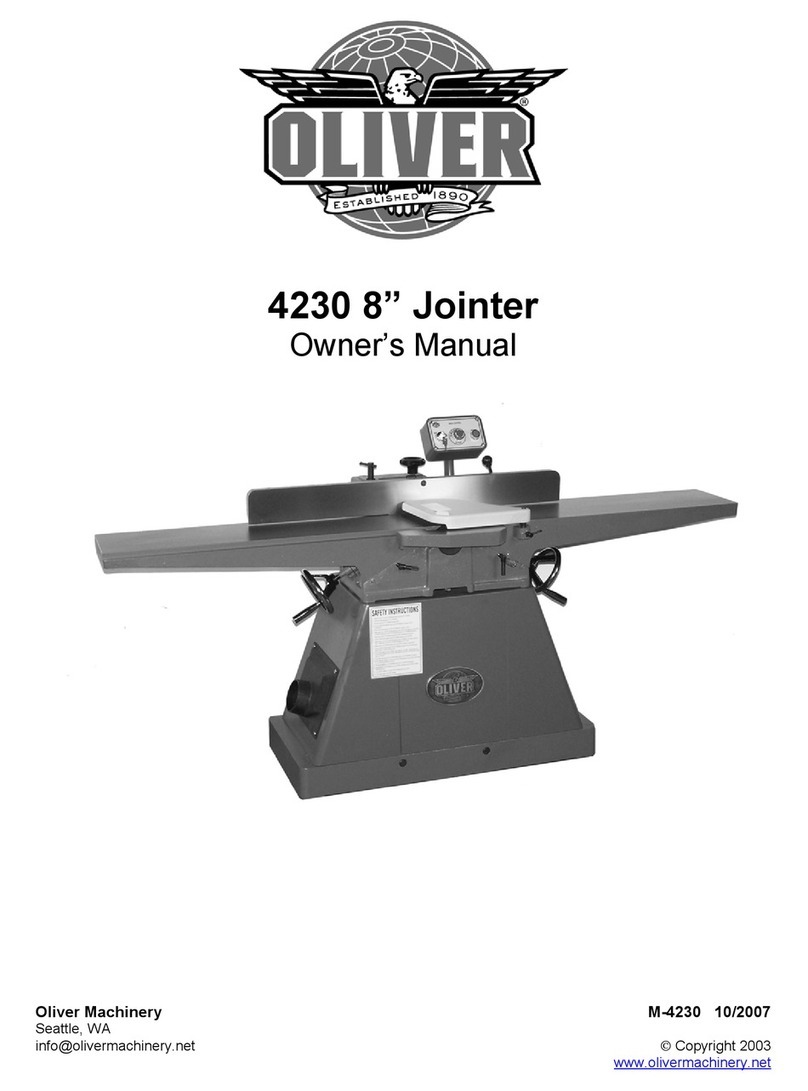
Oliver
Oliver 4230 User manual

Oliver
Oliver 10047VS User manual
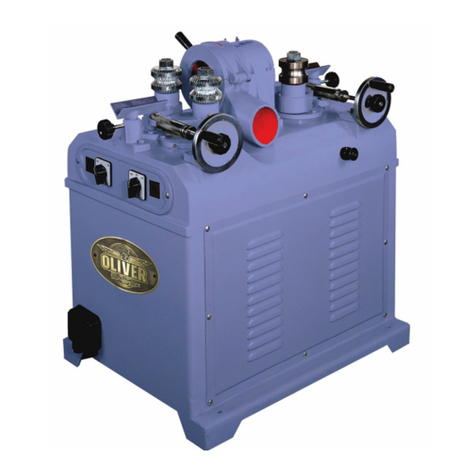
Oliver
Oliver 7660.002 User manual

Oliver
Oliver 4240 User manual
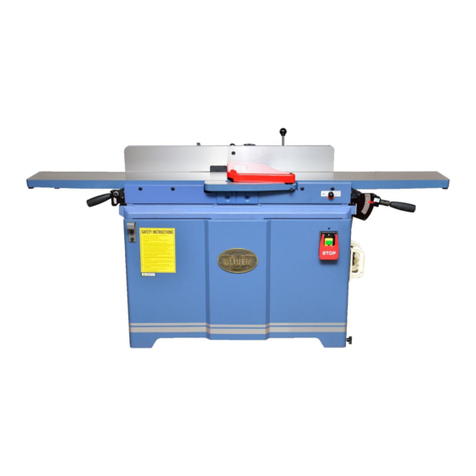
Oliver
Oliver 4235 User manual
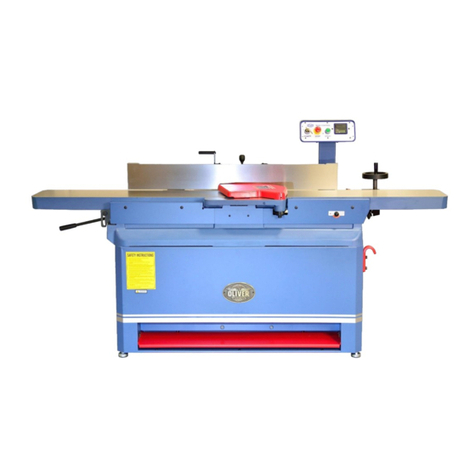
Oliver
Oliver 4275C User manual
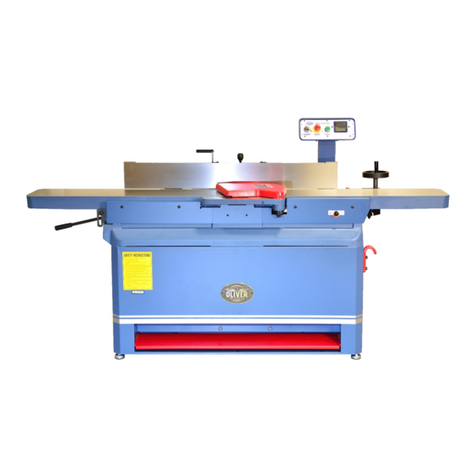
Oliver
Oliver 4265C Instruction Manual
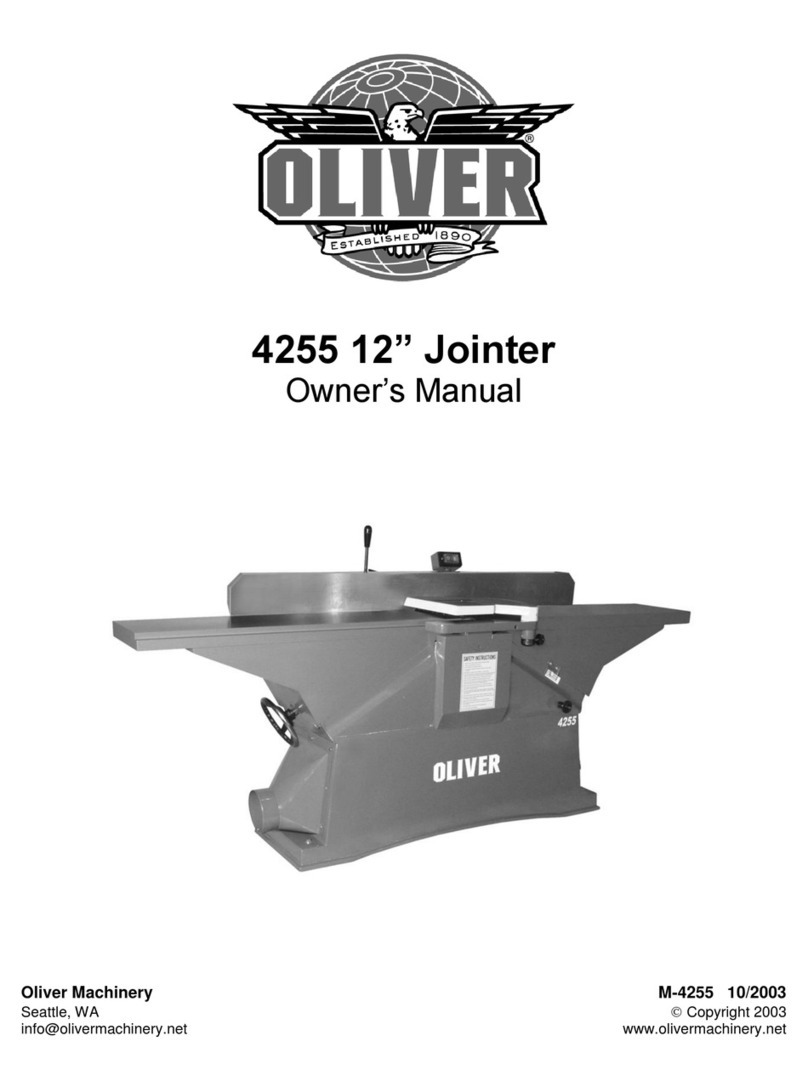
Oliver
Oliver 4255 User manual
Popular Power Tools manuals by other brands
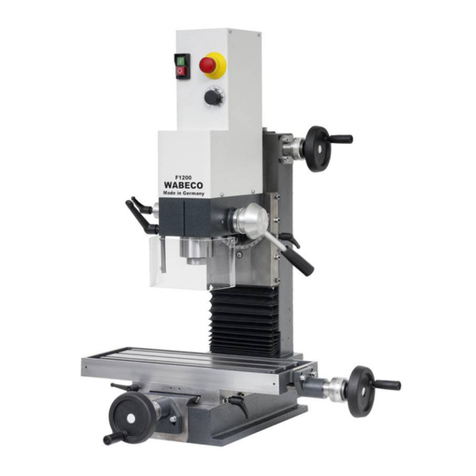
WABECO
WABECO F1200 high speed operating instructions
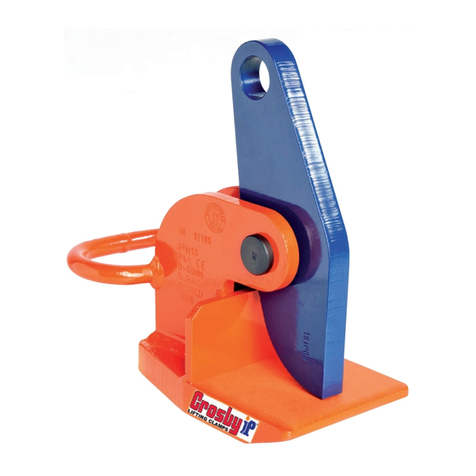
Crosby
Crosby IPH10 user manual
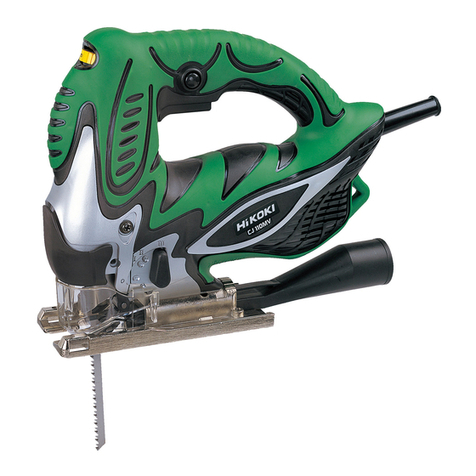
HIKOKI
HIKOKI CJ 110MV Handling instructions
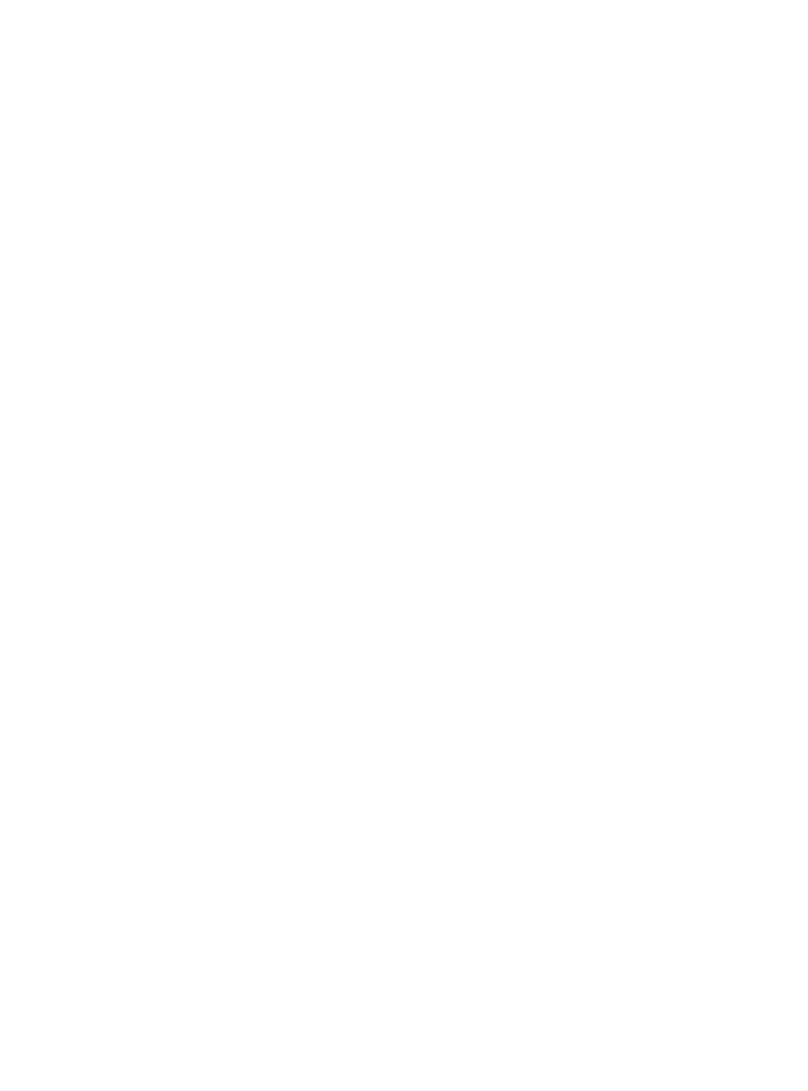
Swordfish
Swordfish Ikon operating instructions
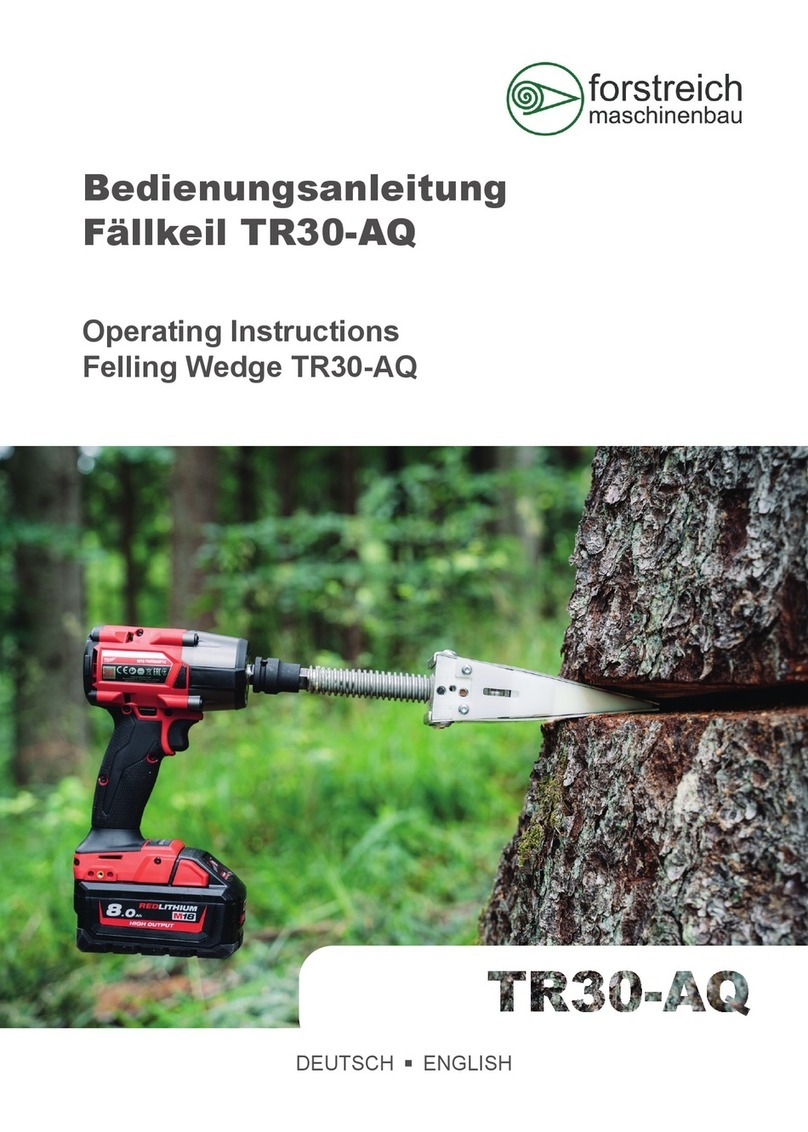
Forstreich Maschinenbau
Forstreich Maschinenbau TR30-AQ operating instructions
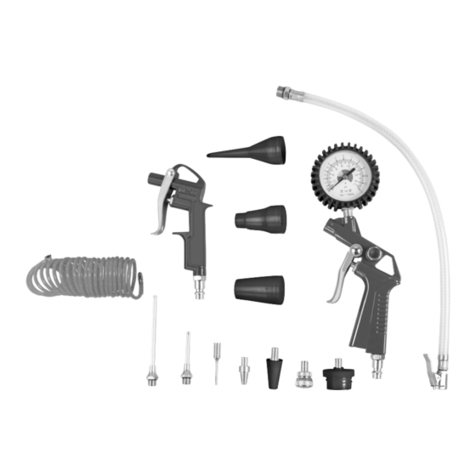
Scheppach
Scheppach 7906100735 Translation of the original instructions