Oliver 4270 User manual

4270 16” Jointer
Owner’s Manual
Oliver Machinery M-4270 11/2003
Seattle, WA Copyright 2003
info@olivermachinery.net www.olivermachinery.net

Warranty
Thank you for your purchase of a genuine Oliver woodworking machine. Oliver Machinery has made
every attempt to provide a machine that is safe and durable.
All Oliver products are guaranteed, to the ORIGINAL RETAIL CUSTOMER, to be free from defects for
TWO YEARS FROM THE DATE OF PURCHASE. Oliver Machinery will repair or replace, at its option,
any component that fails under normal use. Please note that the customer is responsible for returning the
failed component to Oliver Machinery prepaid for inspection.
This warranty does not cover damages caused by misuse, accident, unauthorized repair, alteration or
improper maintenance.
Warning
Read this manual thoroughly before operating the machine. Oliver Machinery disclaims any liability for
machines that have been altered or abused. Oliver Machinery reserves the right to effect at any time,
without prior notice, those alterations to parts, fittings, and accessory equipment which they may deem
necessary for any reason whatsoever.
For More Information
Oliver Machinery is always adding new Industrial Woodworking products to the line. For complete, up-to-
date product information, check with your local Oliver Machinery distributor, or visit
www.olivermachinery.net
2

! WARNING
Read this manual completely and observe all warning labels on the machine. Oliver Machinery has made
every attempt to provide a safe, reliable, easy-to-use piece of machinery. Safety, however, is ultimately
the responsibility of the individual machine operator. As with any piece of machinery, the operator must
exercise caution, patience, and common sense to safely run the machine. Before operating this product,
become familiar with the safety rules in the following sections.
• Always keep guards in place and in proper operating condition.
• Never reach around or under the jointer.
1. If you are not properly trained in the use of a jointer do not use until the proper training has been
obtained.
2. Read, understand and follow the safety instructions found in this manual. Know the limitations and
hazards associated with this machine.
3. Electrical grounding: Make certain that the machine frame is electrically grounded and that a
ground lead is included in the incoming electrical service. In cases where a cord and plug are used,
make certain that the grounding plug connects to a suitable ground. Follow the grounding procedure
indicated in the National Electrical Code.
4. Eye safety: Wear an approved safety shield, goggles, or glasses to protect eyes. Common
eyeglasses are only impact-resistant, they are not safety glasses.
5. Personal protection: Before operating the machine, remove tie, rings, watch and other jewelry and
roll up sleeves above the elbows. Remove all loose outer clothing and confine long hair. Protective
type footwear should be used. Where the noise exceeds the level of exposure allowed in Section
1910.95 of the OSHA Regulations, use hearing protective devices. Do not wear gloves.
6. Guards: Keep the machine guards in place for every operation for which they can be used. If any
guards are removed for maintenance, DO NOT OPERATE the machine until the guards are
reinstalled.
7. Work area: Keep the floor around the machine clean and free of scrap material, saw dust, oil and
other liquids to minimize the danger of tripping or slipping. Be sure the table is free of all scrap,
foreign material and tools before starting to use the machine. Make certain the work area is well
lighted and that a proper exhaust system is used to minimize dust. Use anti-skid floor strips on the
floor area where the operator normally stands and mark off machine work area. Provide adequate
work space around the machine.
8. Jointer position: Position the jointer so that in case of material kick back the flying piece will not
injure workers.
9. Material condition: Do not attempt to joint boards with loose knots or with nails or other foreign
material.
10. Operator: Always use push blocks. Maintain a balanced stance and keep your body under control
at all times.
11. Before starting: Before turning on machine, remove all extra equipment such as keys, wrenches,
scraps, and cleaning rags away from the machine and off the table.
3

12. Careless acts: Give the work you are doing your undivided attention. Looking around, carrying on a
conversation, and “horseplay” are careless acts that can result in serious injury.
13. Disconnect all power sources: Before performing any service, maintenance, adjustments or when
changing blades. A machine under repair should be RED TAGGED to show it should not be used
until the maintenance is complete.
14. Job completion: If the operator leaves the machine area for any reason, the jointer should be
turned "off" and the cutter head should come to a complete stop before leaving.
15. Replacement parts: Use only genuine Oliver Machinery factory authorized replacement parts and
accessories; otherwise the warranty and guarantee are null and void.
16. Misuse: Do not use this Oliver jointer for other than its intended use. If used for other purposes,
Oliver disclaims any real or implied warranty and holds itself harmless for any injury or damage which
may result from that use.
17. Drugs, alcohol and medication: Do not operate this machine while under the influence of drugs,
alcohol, or any medication.
18. This machine is designed for planing wood products only. Do not use to cut any kind of metal or
substance other then wood.
19. Never start the jointer while a workpiece is in contact with the blade.
20. Raise or lower the tables only when the machine has been turned “off” and the cutter head has
come to a complete stop.
21. Make sure the cutter head is running in the proper direction. The knives should be turning toward the
infeed table.
22. Health hazards: Some dust created by power sanding, sawing, grinding, drilling and other
construction activities contains chemicals known to cause cancer, birth defects or other reproductive
harm. Some examples of these chemicals are:
• Lead from lead-based paint.
• Crystalline silica from bricks and cement and other masonry products.
• Arsenic and chromium from chemically-treated lumber.
Your risk from these exposures varies, depending on how often you do this type of work. To reduce
your exposure to these chemicals, work in a well-ventilated area, and work with approved safety
equipment, such as those dust masks that are specifically designed to filter out microscopic particles.
Familiarize yourself with the following safety notices used in this manual:
CAUTION: (This means that if precautions are not heeded, it may result in minor or moderate injury
and/or possible machine damage)
WARNING: (This means that if precautions are not heeded, it could result in serious injury or possibly
even death).
4

Table of Contents Page Number
Warranty........................................................................................................................................................ 2
Warnings ....................................................................................................................................................3-4
Table of Contents.......................................................................................................................................... 5
Specifications ................................................................................................................................................ 5
Contents of the Shipping Containers ............................................................................................................ 6
Uncrating the Machine .................................................................................................................................. 6
Machine Preparation and Setup ................................................................................................................... 6
Dust Collection .............................................................................................................................................. 7
Electrical Connections................................................................................................................................... 7
Stop/Start Switch........................................................................................................................................... 7
Fence............................................................................................................................................................ 8
Installation of the Fence ................................................................................................................................ 8
Fence Legend ............................................................................................................................................... 8
Adjustment of he 90 Degree Stop................................................................................................................. 8
Fence Operation ........................................................................................................................................... 8
Knives........................................................................................................................................................... 9
Installation of the Knives ............................................................................................................................... 9
Adjusting the Outfeed Table ....................................................................................................................... 10
Operation ................................................................................................................................................... 10
Hand Safety and Placement ....................................................................................................................... 10
Jointing ........................................................................................................................................................ 11
Direction of the grain ................................................................................................................................... 11
Edging ......................................................................................................................................................... 11
Facing.......................................................................................................................................................... 11
Beveling....................................................................................................................................................... 12
Rabbeting.................................................................................................................................................... 12
Adjusting the Infeed Table Height............................................................................................................... 12
Maintenance .............................................................................................................................................. 13
V-Belts......................................................................................................................................................... 13
Lubrication................................................................................................................................................... 13
Knives.......................................................................................................................................................... 13
Table Leveling............................................................................................................................................. 13
Troubleshooting........................................................................................................................................ 14
Specifications
Model No................................................................................................................................................. 4270
Stock No (5HP, 1PH, 220 Volt) ........................................................................................................ 4270.001
Stock No.(7.5HP, 3PH, 220/440 Volt, pre-wired 220 Volt) .............................................................. 4270.002
Stock No.(5HP, 1PH, 220 volt, spiral head).................................................................................... 4270.101
Stock No (7.5HP, 3PH, 220/440 volt, pre-wired 220 Volt, spiral head) ........................................... 4270.102
Infeed Table Travel (in.) ................................................................................................................................ 1
Cutterhead speed (RPM) ........................................................................................................................ 6000
Number of Knives (Straight).......................................................................................................................... 4
Numbe of Knives (Spiral) .............................................................................................................................. 3
Rabbeting Capacity (in.)............................................................................................................................. 3/4
Dust Port Diameter (in.) ................................................................................................................................ 6
Table Dimensions (L x W/in.) ............................................................................................................ 102 x 17
Table Height (In.) ........................................................................................................................................ 32
Fence Dimensions (L x H/in.)....................................................................................................68-1/2 x 5-1/2
Fence Tilts (deg.) .................................................................................................................................90 - 45
Positive Stops (deg.) ....................................................................................................................... 90 and 45
Shipping Dimension (L x W x H/in.) .......................................................................................... 104 x 36 x 39
Overall Dimensions ................................................................................................................... 102 x 45 x 40
Gross Weight (lbs.) ................................................................................................................................. 1750
CFM............................................................................................................ 884CFM at 4500FPM air velocity
5

Oliver 4270 – 16” Jointer
Contents:
1. 16” Jointer
2. Two push blocks
3. Knife setting jig
4. Allen keys
5. Wrenches
Uncrating the Machine
Uncrate the machine and inspect the unit for
signs of shipping damage. If damage is found,
contact your dealer immediately. Unbolt the
machine from the pallet Retain all packaging
materials in case it becomes necessary to ship
the machine to another site.
Tool Box Contents
Machine Preparation and Setup
! WARNING
The equipment used to lift this machine
must have a rated capacity at, or above the
weight of the jointer. Failure to comply
may cause serious injury!
The jointer must be positioned on a smooth,
level surface. The area must be well lit and
have plenty of room to maneuver with large
pieces of wood.
Level the jointer front to back and side to side
using a level placed on the table. Use shims
under the corners, if necessary, but make sure
the jointer is stable before being placed into
service.
Clean all rust protected surfaces with a
commercial solvent. Do not use acetone,
gasoline, lacquer thinner or any type of
flammable solvent, or a cleaner that may
damage paint. Cover cleaned surfaces with
WD-40 or a 20W machine oil.
6

Dust Collection
Figure 1
The 6” dust collection port (A, Figure 4) is
located below the outfeed table. Typically flex
hose is used to run from this point to a central
trunk line.
Note: Do not operate the jointer without dust
collection.
Electrical Connections
! WARNING
Electrical connections and wiring must be
performed by a certified electrician. The
machine must be properly grounded.
Failure to comply may cause serious
injury!
Figure 2 (3 Phase)
This jointer can be 1 or 3-Phase based on
your order and is wired for 220 volt. If on 3
phase you need to switch from 220V to 440V,
have a certified electrician make the changes.
Make sure the voltage of your power supply
matches the specifications on the motor plate
of the machine.
With 3-Phase power verify the cutter head is
turning in the proper direction. If rotation is
incorrect, swap two of the phases to reverse.
Note: If running from a phase converter
ensure the ‘high leg’ of the converter does not
feed the control circuit.
Stop/Start Switch
Attach the Stop/Start switch (Figure 3) to holes
‘A’ using the supplied bolts
Figure 3
7

Fence
Figure 4
! WARNING
Never make any adjustments with the
machine running!
Installation of the Fence
The fence, although completely assembled,
requires bolting to the machine as well as
alignment.
1. Mount the fence (Figure 5) to the machine
base (Figure 4) lining up the holes (A),
using the allen bolts provided.
Fence Legend
The various adjustments, locks and handles
are shown in Figure 5.
A. 90 degree adjust bolt.
B. Angle lock handle.
Figure 5
C. 90 degree flip stop.
D. Width adjustment handle.
E. 45 degree adjust bolt.
F. Width lock handle.
G. Fence angle adjust handle.
Adjustment of the 90 Degree Stop
1. Lay a square on the infeed table as shown
in Figure 6.
2. Loosen the angle lock handle (B, figure 5).
3. Ensure the 90 degree flip stop (C, Figure
5) is in the 90 degree position.
4. Loosen the jam nut on the 90 degree
adjusting bolt (A, figure 5) and adjust the
bolt against the flip stop until the fence
becomes true with the square.
Figure 6
5. Tighten the jam nut while holding the bolt
in position.
Fence Operation
To tilt the fence, see Figure 5. Loosen angle
lock handle ‘B’, flip up the stop ‘C’, and tilt the
fence with the fence angle adjusting handle ‘G’
to the desired angle. Use a protractor or
adjustable triangle to set the angle. A 45
degree stop, ‘E’ is provided for quick set-up at
this angle.
To adjust the cutting width loosen the lock
handle ‘F’ and turn the width adjustment
handle ‘D’ to move the fence toward or away
from the rabbeting ledge.
Once any adjustments are made be sure to
lock them into place.
8

Knives
Figure 7
! WARNING
The knives are extremely sharp. Use
caution when handling.
Installation of the Knives
1. To expose the cutterhead, move the fence
all the way back.
2. Back down both the infeed and outfeed
tables to their lowest position. Be sure to
loosen the lock on the outfeed table
before doing so.
3. Now turn the cutterhead by hand until one
of the knives is exposed and accessible.
Use gloves or a rag to prevent injury.
4. Using a 10mm wrench on the knife lock
bolt, release the pressure on the knife by
turning the bolt into the cutterhead as
show in Figure 7. To prevent injury, hold
the wrench with one hand while tapping
the top of the wrench with the other hand
as shown. Do this for all six bolts.
Figure 8
5. Once all the bolts have been turned in, the
knife should pop up from the spring
pressure. Remove the knife and
immediately place the new knife in the slot
to prevent loss of the springs.
Note: It is not only important to set the height
of the knife with respect to the cutterhead it is
also important that the outside edge of the
knives be aligned with the rabbeting ledge.
6. With the knife in the slot use a straight
edge on the rabbeting ledge as shown in
Figure 8 to push the knife into alignment
with the edge.
7. Next use the supplied knife guage as
shown to carefully push down on the knife
until it is position as shown in Figure 9.
Make sure the knife makes contact within
the indent as shown by ‘A’ in Figure 9.
8. With the knife held firmly into place back
the knife lock bolts out into the cutterhead
in order to put pressure onto the knife.
Work from the center bolts outward. Do
this in two steps. First loosely, then firmly
the second time.
9. Repeat the above for all knives.
Note: The supplied guage sets the knives to
the cutterhead however it is always best to set
the knives to the outfeed table. Many
aftermarket devices are available to do this. If
using this method the knife should be no more
than 1/8” out of the cutterhead (not including
the bevel)
Figure 9
9

Adjusting the Outfeed Table
1. Once the knives are set it is now time to
set the outfeed table. For proper
operation the height of the outfeed table
must be set to the highest point of the
cutting circle. To do this, set a straight
edge on the outfeed table as shown in
Figure 10.
2. Carefully watch the height of the straight
edge as you gently rock the cutterhead
back and forth as shown by the arrows in
figure 10. Stop when the knife is at its
highest position.
3. At this point it is time to ‘dial in’ the outfeed
table to the knife. To do this, slowly turn
up or down the table with the table height
adjusting wheel (B, Figure 11) until there
is no light between the table and the
bottom of the straight edge.
Figure 10
4. Once set, lock into place with the height
lock knob (A, Figure 11).
Note: Failure to adjust the outfeed table will
result in either a curved or sniped work piece.
Operation
! WARNING
Keep all guards in place. Keep hands away
from the cutterhead! Always use push
stick when possible. Failure to comply
may cause serious injury.
Figure 11
Hand Safety and Placement
Never pass the hands directly over the cutter
knife. As one hand approaches the knives
remove it from the stock in an arc motion and
place it back on the stock in a position beyond
the cutter knife. See figure 12.
When feeding the work piece, pressure is
applied not only toward the cutterhead but
against the fence and down to the table as
well. At the start of the cut, the left hand holds
the material down and toward the fence while
the right hand pushes toward the cutterhead.
As the material crosses he cutterhead the left
hand comes up and over as in Figure 12 to
continue the pressure but now on the outfeed
table. As the right hand approaches the
cutterhead it is time to move it up and over the
cutterhead in the same fashion as the left in
Figure 12 all the while continuing pressure as
stated above.
Figure 12
10

Jointing
In order to craft a good woodworking project, it
is necessary to have a square piece of wood
to start with. The way to do this is with a
jointer. You need one straight edge and one
flat face. After you have these, you can plane
to thickness and rip to width and the resulting
piece will be square and true on all four sides.
At this point you can begin building your
project.
Direction of the Grain
To avoid tear out, always feed the material in
the direction of the grain. If the direction of the
grain changes half way through the board, try
taking lighter cuts at a slower feed rate. If the
results are still unsatisfactory, try turning the
material around and feeding the other way.
(Figure 13)
Figure 13
Edging (Figure 14)
To give a good straight edge for gluing or
joining, set the fence square with the table.
Remove the least amount of material required
to obtain a straight edge. Hold the best face
of the piece firmly against the fence
throughout the feed. When finished you will
have a perfect starting point for your project.
Figure 14
Facing (Figure 15)
Once you have a good edge it is time to
eliminate any warp or cup on the board. Keep
in mind the outfeed table is the reference point
and once the material is past the cutterhead,
downward pressure should be applied to the
outfeed table only. Putting downward
pressure on the board over the infeed table
will bend any cup or warp prior to hitting the
cutterhead and after the pressure is released,
the cup will spring back. At the same time try
keeping a constant feed rate in order to give a
good smooth cut with no burn marks.
Figure 15
11

Beveling
Figure 16
For beveling (Figure 16), set the fence to the
desired angle using a protractor and lock into
place. Feed the material through pressing
firmly against the fence and tables. Several
passes may be necessary for the desired
result.
Rabbeting
! WARNING
Rabbeting requires removal of the blade
guard. Use extreme caution and replace
the guard after completion.
1. Adjust the fence so that the distance
between the edge of the knife and the
fence is equal to the width of the desired
rabbet (figure 17).
2. Lower the infeed table to the depth of the
rabbet required. If the rabbet is quite
deep it may be necessary to do it in
increments.
Adjusting the Infeed Table Height
The height of the infeed table with respect to
the cutting circle will determine the amount of
material to be removed from the work piece.
To raise or lower the table turn the height
adjusting wheel (A, Figure 18) on the back of
the infeed table to the desired height indicated
by the guage (B, Figure 18).
Figure 17
Figure 18
12

Maintenance
V-Belts
After the first 20 hours of operation it is
necessary to check the tension on of the V-
belts. To do this, open the access door (A,
Figure 19). With medium finger pressure the
belt should push in approximately ½” about
midway between the pulleys. If there is too
much play, remove the three belt cover bolts
(B, Figure 19) and pull the guard off. Adjust
the tension by loosening the bottom jam nut
on the bracket (A, Figure 20) and then turn
down the top nut until the desired tension is
achieved.
Lubrication
Figure 19
Periodically apply a light grease to the tables
up/down lead screw. As well, apply a light oil
to the dovetail ways from time to time to allow
ease of movement.
The cutterhead bearings are permanently
greased for life and do not require care.
Knives
When knives become gummed up with pitch
carefully clean them with a strong solvent. A
knife in this condition will not only give a poor
cut it will allow heat to build up quickly thus
putting undue stress on the machine.
Dull knives can be replaced or sharpened.
Check in your local yellow pages for a
sharpening service. It may be more cost
effective to replace rather than sharpen.
Note; Do not run the machine with dull knives.
Not only will they give a bad cut, the put undue
stress and vibration on the machine thereby
decreasing the life of the machine and
damaging the cutterhead bearings.
Figure 20
Table Leveling
The tables have been leveled at the factory
and should not require leveling. However, if
needed it can be done using the adjusting
bolts as seen in Figure 21. There are 6 sets
each consisting of a locking bolt and an
adjusting bolt with jam nut. It should only be
necessary to adjust one table leaving the other
table as is. Keep in mind that leveling a table
can easily turn into a long project therefore it is
best to determine what part of the table needs
adjusting before turning a bolt and to turn only
a little at a time. Also understand that
changing the position of one bolt affects all
others and that the other bolts will have to be
‘zeroed’ out. To adjust the table loosen all
lock nuts and jam nuts, adjust the appropriate
bolts and lock into place. Note: Use a good
known 4’ straight edge such as by Starrett.
Figure 21
13

Troubleshooting
Description of Symptoms Possible Cause Corrective Action
Machine will not start
1. Fuse blown or circuit breaker
tripped
2. Cord Damaged
3. Faulty switch
4. Not connected to power
source
5. No power to machine
6. Emergency stop button
pressed
1. Replace fuse or reset circuit
breaker
2. Have cord replaced
3. Replace switch
4. Check connection
5. Check voltage
6. Rotate emergency stop button
clockwise until it pops out
Cutterhead does not come up to
speed
1. Cable too light or too long
2. Low current
3. Motor not wired for correct
voltage
1. Replace with adequate size
cable
2. Contact local electric
company
3. Refer to motor nameplate for
correct voltage
Unsatisfactory finish 1. Dull Knives
2. Gum or pitch on knives
1. Sharpen or replace knives
2. Clean or replace knives
Excessive vibration
1. Machine not level.
2. Damaged knives
3. Bad V-belts
4. Bent pulley
5. Improper motor mounting
6. Loose hardware
1. Reposition on flat, level
surface
2. Replace knives
3. Replace V-belts
4. Replace pulley
5. Check and adjust motor
6. Tighten hardware
Adjustments do not move freely. Sawdust and debris in
mechanisms Clean and regrease
Finished stock is concave on the
end
Knife is higher than the
outfeed table
Adjust the outfeed table to the
highest point of the cutting
circle
Back end of the stock is thicker
than the front end
Knife is higher that the outfeed
table
Adjust the outfeed table to the
highest point of the cutting
circle
Finished stock is concave or
convex in the middle
Tables are not level with each
other.
Level one of the tables to the
other.
14
Table of contents
Other Oliver Power Tools manuals

Oliver
Oliver 4705 User manual
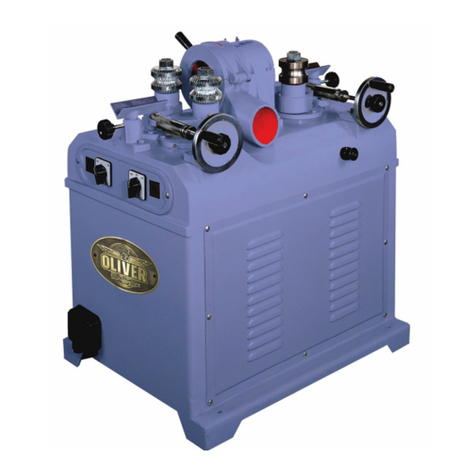
Oliver
Oliver 7660.002 User manual
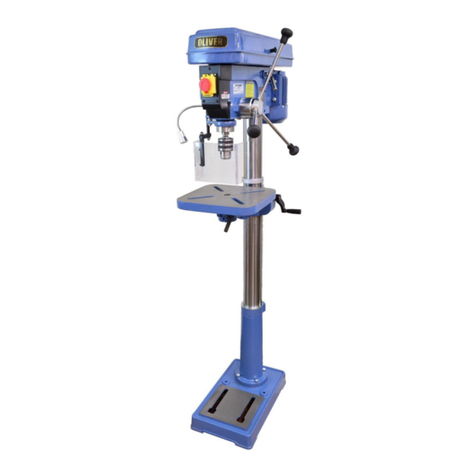
Oliver
Oliver 10062 User manual

Oliver
Oliver 10047VS User manual
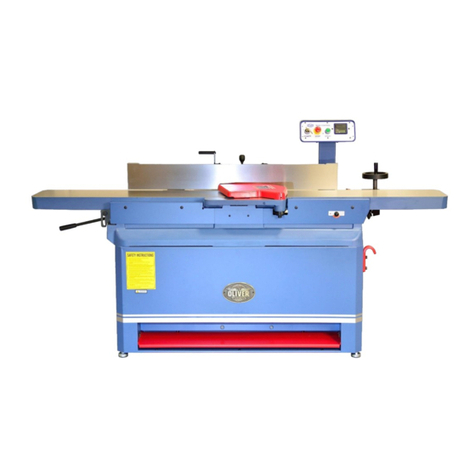
Oliver
Oliver 4275C User manual
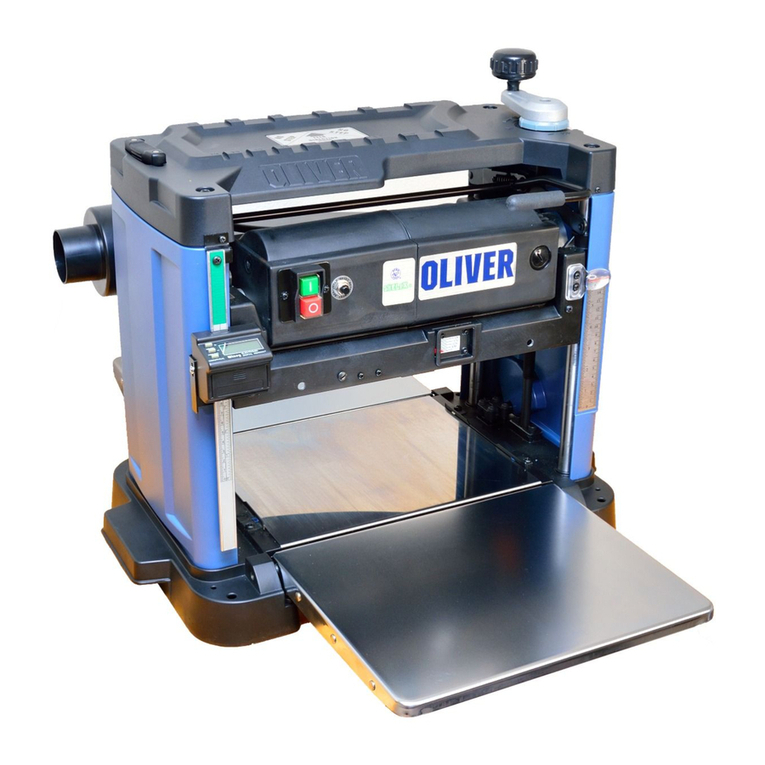
Oliver
Oliver 10044 User manual
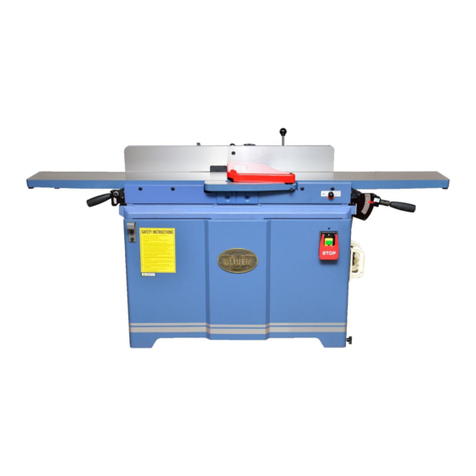
Oliver
Oliver 4235 User manual
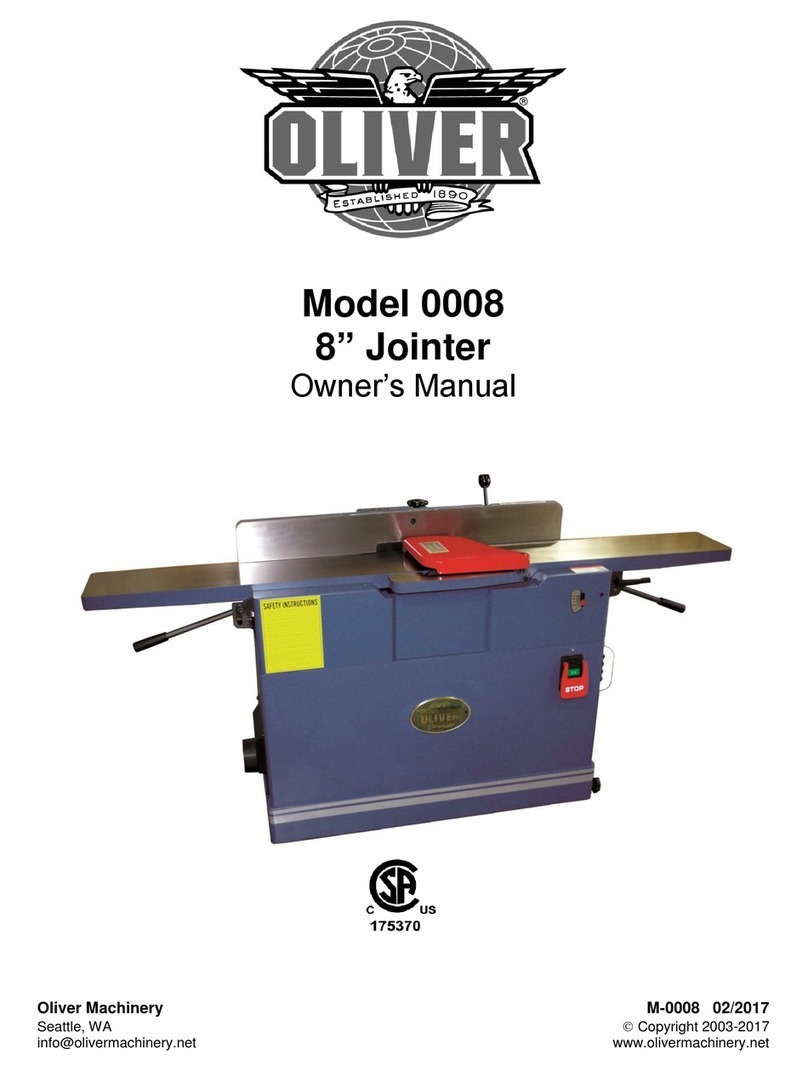
Oliver
Oliver 0008 User manual
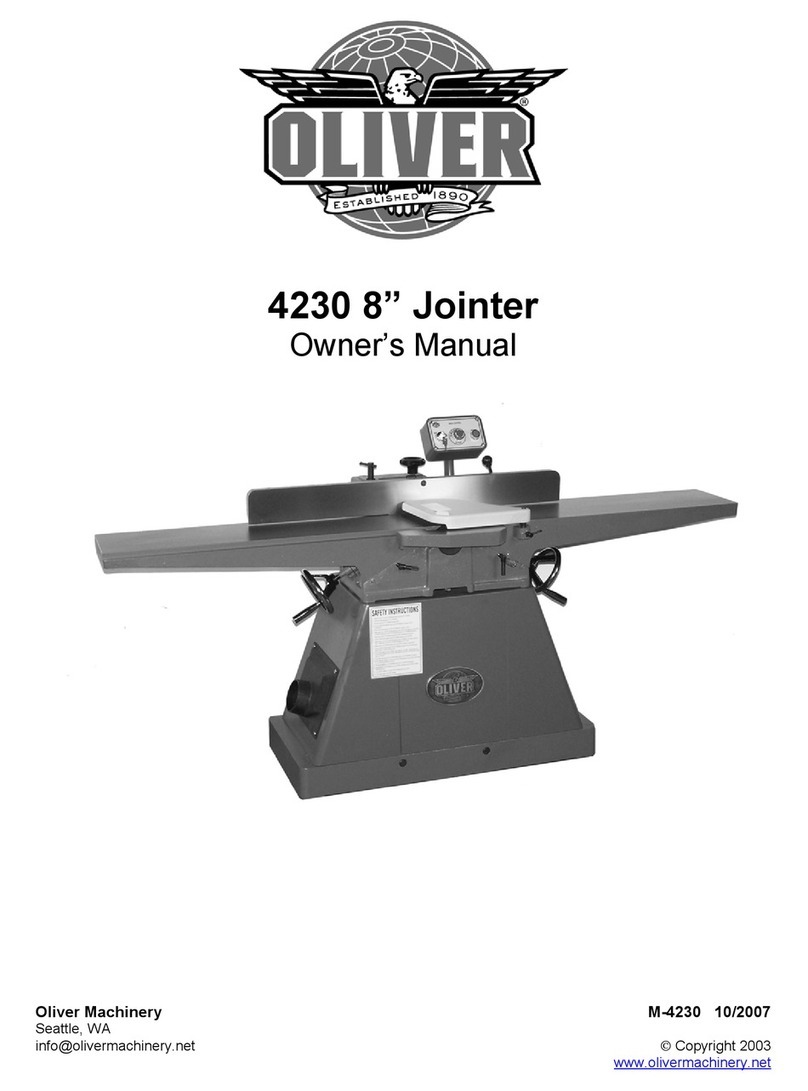
Oliver
Oliver 4230 User manual

Oliver
Oliver 4235 User manual
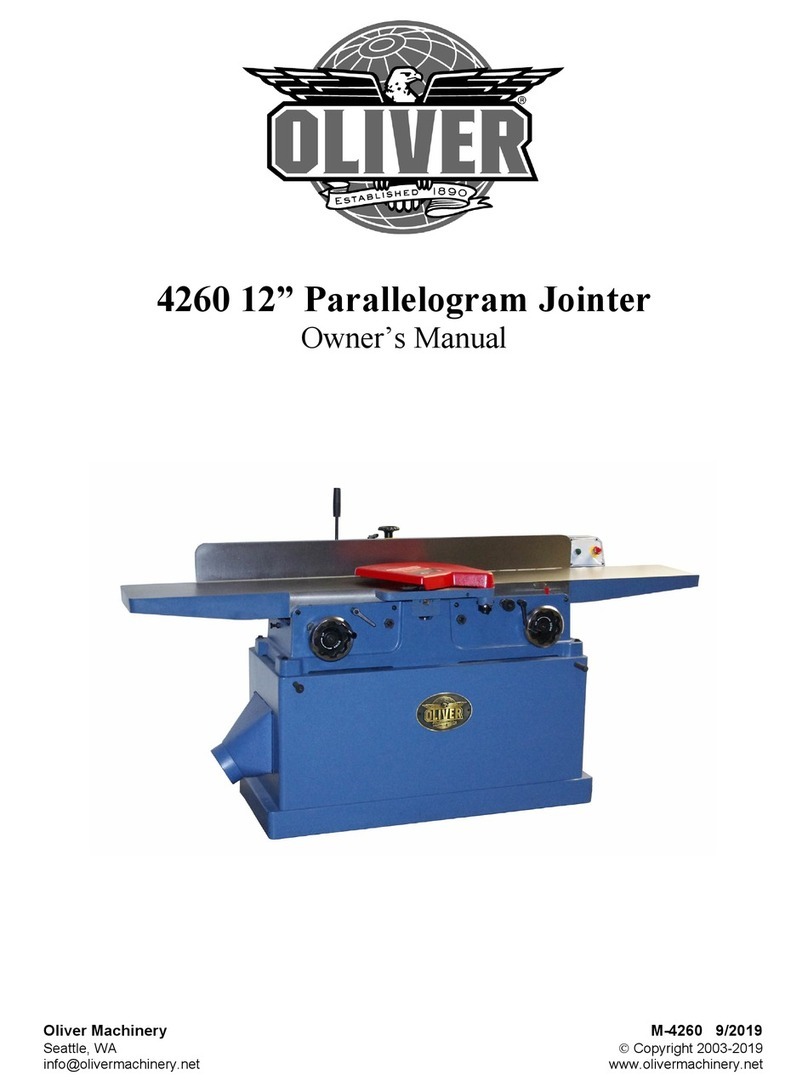
Oliver
Oliver 4260 User manual
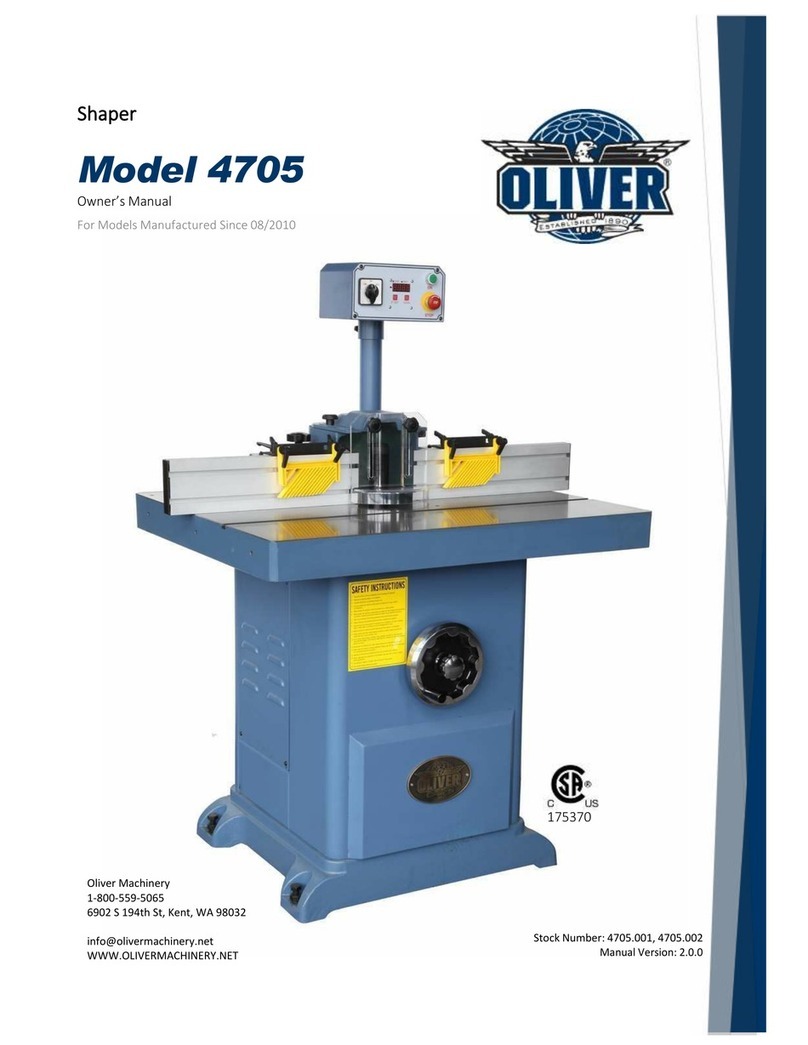
Oliver
Oliver 4705 User manual
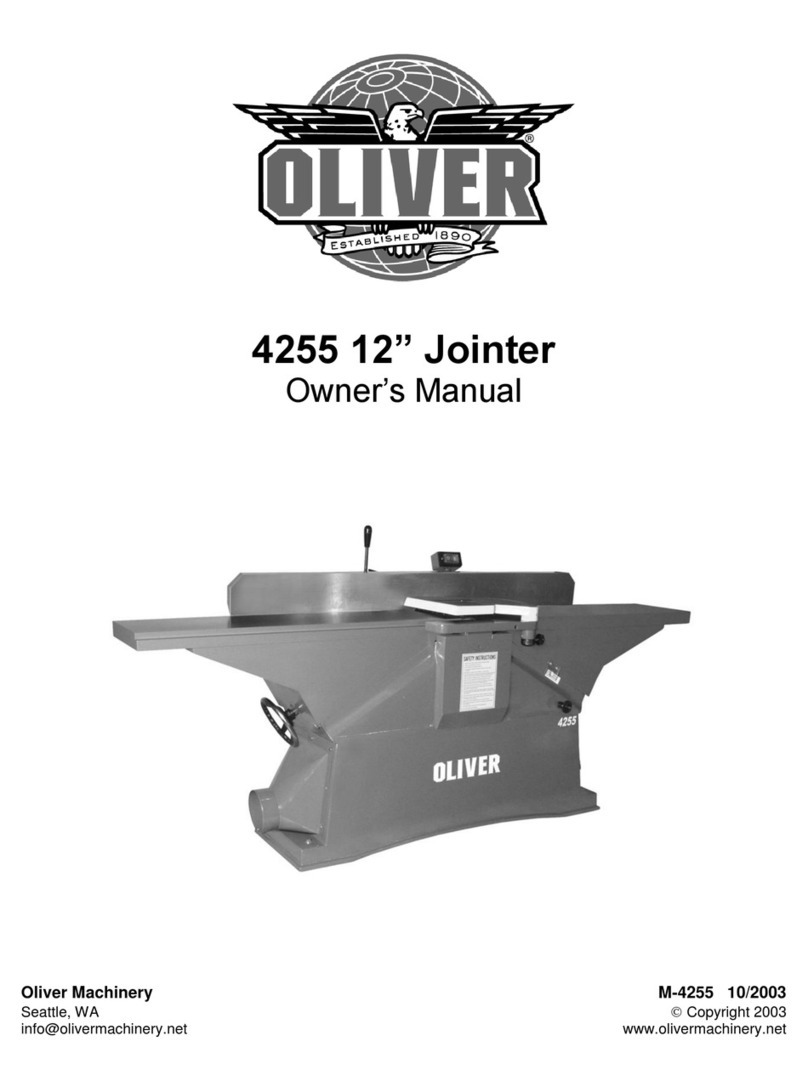
Oliver
Oliver 4255 User manual
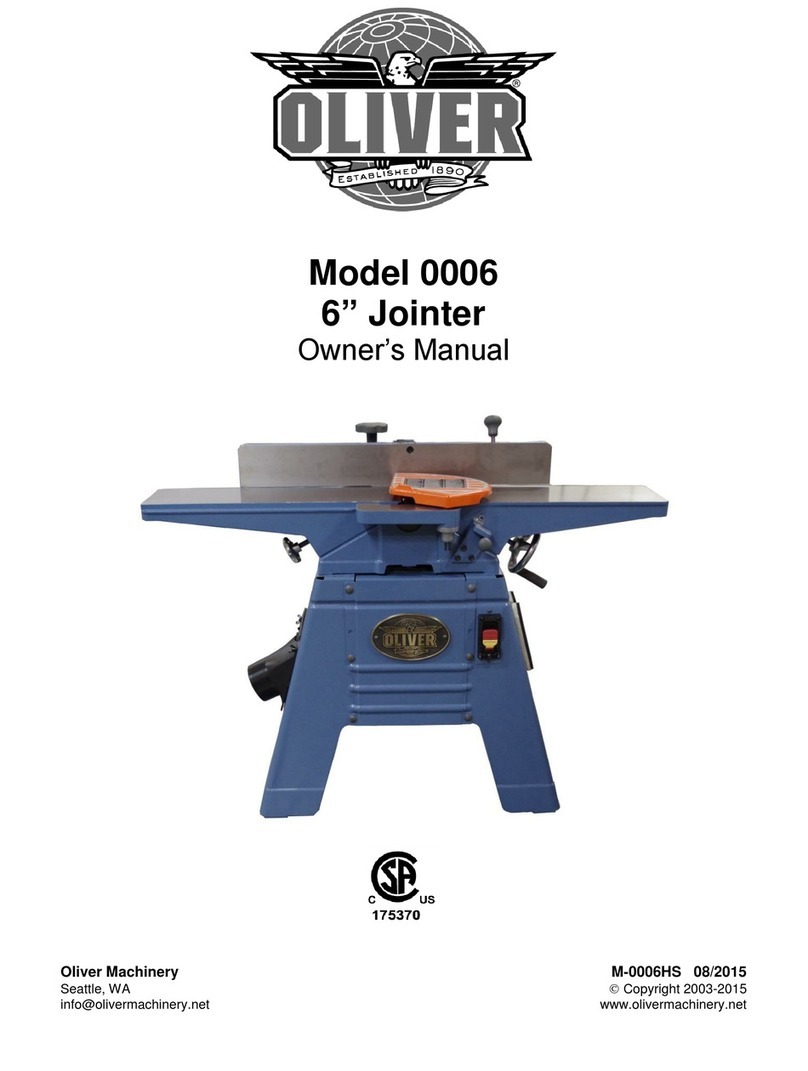
Oliver
Oliver 0006 User manual
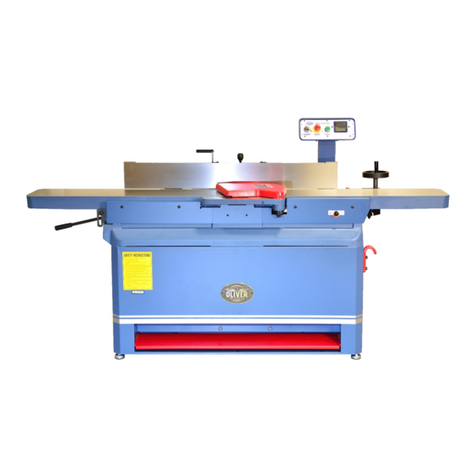
Oliver
Oliver 4265C Instruction Manual
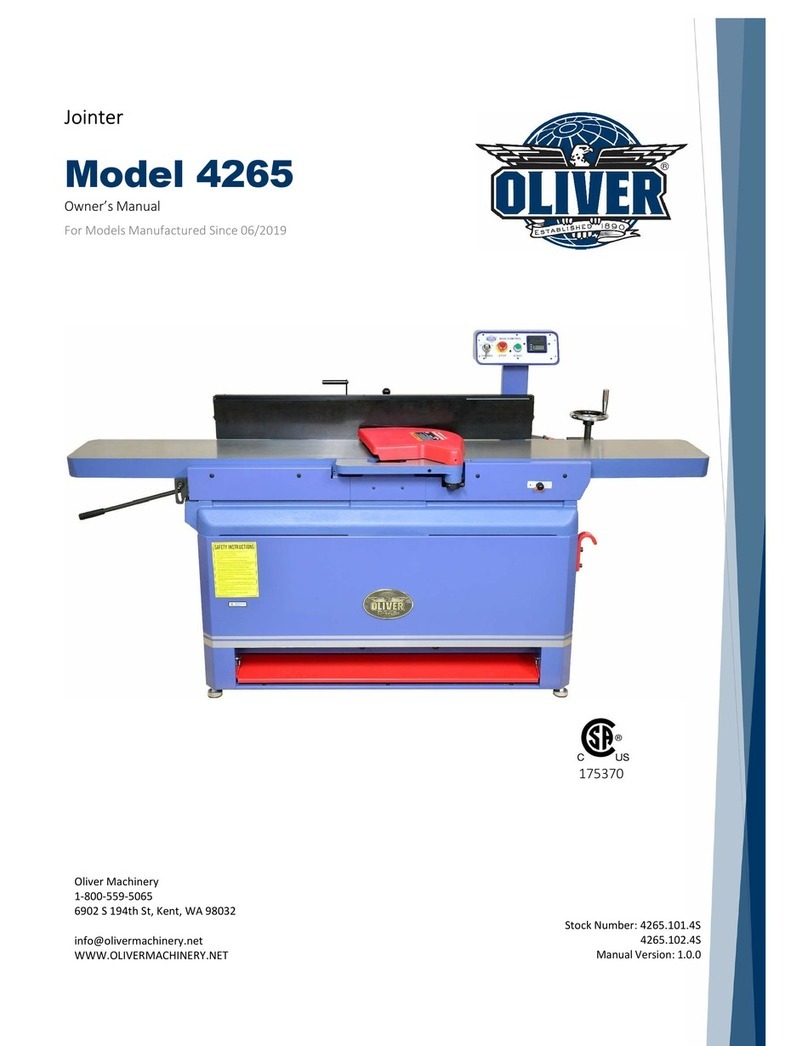
Oliver
Oliver 4265 User manual
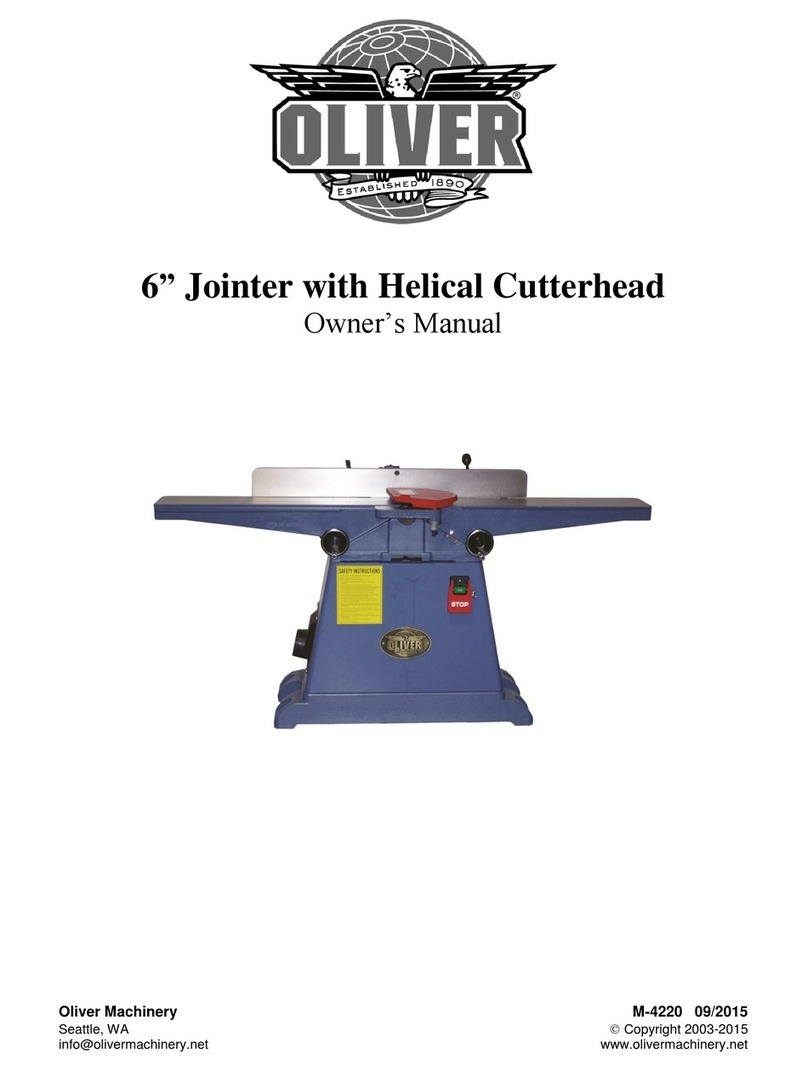
Oliver
Oliver 4220 User manual

Oliver
Oliver 4240 User manual
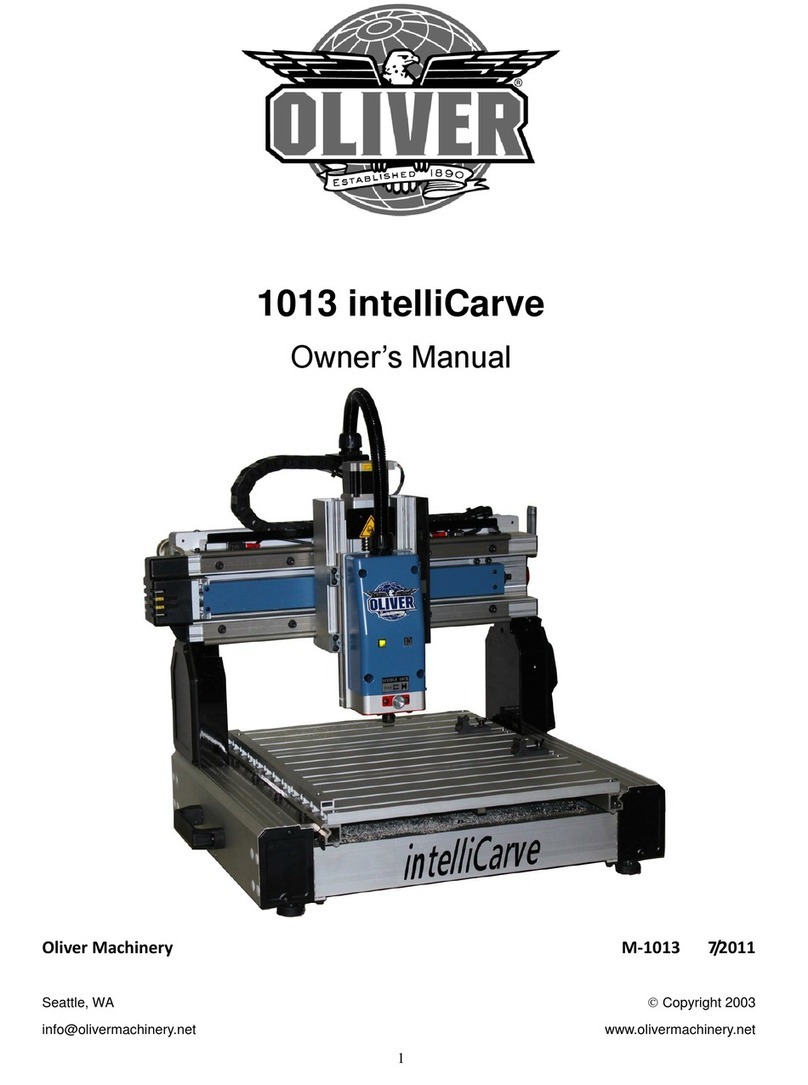
Oliver
Oliver M1013 User manual
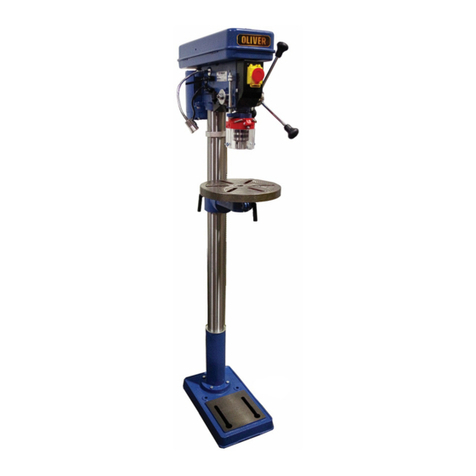
Oliver
Oliver 10060.001 User manual