Pilz PNOZ ms4p User manual

PNOZ ms4p
Operating Manual 22109-EN-03
}Configurable safety systems PNOZmulti

Preface
This document is a translation of the original document.
All rights to this documentation are reserved by Pilz GmbH & Co. KG. Copies may be made
for internal purposes. Suggestions and comments for improving this documentation will be
gratefully received.
Source code from third-party manufacturers or open source software has been used for
some components. The relevant licence information is available on the Internet on the Pilz
homepage.
Pilz®, PIT®, PMI®, PNOZ®, Primo®, PSEN®, PSS®, PVIS®, SafetyBUS p®,
SafetyEYE®, SafetyNET p®, the spirit of safety® are registered and protected trademarks
of Pilz GmbH & Co. KG in some countries.
SD means Secure Digital

Contents
Operating Manual PNOZ ms4p
22109-EN-03 3
Section 1 Introduction 5
1.1 Validity of documentation 5
1.2 Using the documentation 5
1.3 Definition of symbols 5
Section 2 Overview 7
2.1 Scope 7
2.2 Unit features 7
2.3 Front view 8
Section 3 Safety 9
3.1 Intended use 9
3.2 System requirements 10
3.3 Safety regulations 10
3.3.1 Safety assessment 10
3.3.2 Use of qualified personnel 11
3.3.3 Warranty and liability 11
3.3.4 Disposal 11
3.3.5 For your safety 11
Section 4 Function description 12
4.1 Integrated protection mechanisms 12
4.2 Operation 12
4.3 Block diagram 12
4.4 Incremental encoders 12
4.4.1 Requirements of the incremental encoders 12
4.4.2 Adapter for incremental encoders 13
Section 5 Installation 14
5.1 General installation guidelines 14
5.2 Dimensions 14
5.3 Connecting the base unit and expansion modules 15
Section 6 Commissioning 16
6.1 General wiring guidelines 16
6.2 Pin assignment of RJ45 socket 16
6.3 Connecting the incremental encoder 17
6.3.1 Connect the signals from the incremental encoder to the speed monitor 17
6.3.2 Connect the incremental encoder to the speed monitor via an adapter 18
Section 7 Operation 20
7.1 LED indicators 20
Section 8 Technical details 21
8.1 Safety characteristic data 23

Contents
Operating Manual PNOZ ms4p
22109-EN-03 4
Section 9 Order reference 24
9.1 Product 24
9.2 Accessories 24
Section 10 Application examples 25
10.1 Example without position control 25
10.2 Example with position control 25

Introduction
Operating Manual PNOZ ms4p
22109-EN-03 5
1 Introduction
1.1 Validity of documentation
This documentation is valid for the product PNOZ ms4p. It is valid until new documentation
is published.
This operating manual explains the function and operation, describes the installation and
provides guidelines on how to connect the product.
1.2 Using the documentation
This document is intended for instruction. Only install and commission the product if you
have read and understood this document. The document should be retained for future ref-
erence.
1.3 Definition of symbols
Information that is particularly important is identified as follows:
DANGER!
This warning must be heeded! It warns of a hazardous situation that poses
an immediate threat of serious injury and death and indicates preventive
measures that can be taken.
WARNING!
This warning must be heeded! It warns of a hazardous situation that could
lead to serious injury and death and indicates preventive measures that can
be taken.
CAUTION!
This refers to a hazard that can lead to a less serious or minor injury plus
material damage, and also provides information on preventive measures
that can be taken.
NOTICE
This describes a situation in which the product or devices could be dam-
aged and also provides information on preventive measures that can be
taken. It also highlights areas within the text that are of particular import-
ance.

Introduction
Operating Manual PNOZ ms4p
22109-EN-03 6
INFORMATION
This gives advice on applications and provides information on special fea-
tures.

Overview
Operating Manual PNOZ ms4p
22109-EN-03 7
2 Overview
2.1 Scope
}Expansion module PNOZ ms4p
}Jumper
2.2 Unit features
Using the product PNOZ ms4p:
Speed monitor for connection to a base unit from the configurable control system
PNOZmulti
The product has the following features:
}Monitoring of 1 axis
}Connection: 1incremental encoder
}Measured variables:
– Standstill
– Speed (16 values can be set)
– Direction of rotation
}Axis types, start mode can be selected in the PNOZmulti Configurator
}Status indicators for
– Supply voltage
– Incremental encoder
– Axis status, standstill and excess speed
– Faults on the system
}Incremental encoder connection technology:
RJ45 female connector
}Function to deactivate speed monitoring
}Galvanic isolation between the connections X1 and X12
}Max. 4 speed monitors can be connected to the base unit

Overview
Operating Manual PNOZ ms4p
22109-EN-03 8
2.3 Front view
4
Fig.: Front view of PNOZ ms4p
Key:
}X12:
– Female connector for connecting an incremental encoder
}LEDs:
– POWER
– FAULT
– SHAFT
– X12

Safety
Operating Manual PNOZ ms4p
22109-EN-03 9
3 Safety
3.1 Intended use
The expansion module monitors standstill, speed and direction of rotation in accordance
with EN ISO 13849-1 up to PL e and EN IEC 62061 up to SIL CL 3.
The expansion module may only be connected to a base unit from the PNOZmulti system
(please refer to the document "PNOZmulti System Expansion" for details of the base units
that can be connected).
The configurable small control systems PNOZmulti are used for the safety-related interrup-
tion of safety circuits and are designed for use in:
}E-STOP equipment
}Safety circuits in accordance with VDE0113 Part 1 and EN60204-1
WARNING!
Users must take appropriate measures to detect or exclude errors (e.g. slip-
page or broken shearpin) which cause the frequency of the encoder signal
to no longer be proportional to the monitored speed.
Appropriate measures are:
– Using the monitored encoder to also control the drive
– Mechanical solutions
WARNING!
Encoder errors are detected and signalled via a diagnostic bit. This does
not bring the relevant axis to a safe condition.
To maintain safety (Category 3), the diagnostic bit (diagnostic bit 10) in the
user program must be evaluated in such a way that a shutdown occurs if
the axis is in operation (see examples in Chapter 9).
CAUTION!
If there are frequency differences between tracks A and B of the incre-
mental encoder, the track with the higher frequency will be evaluated. Differ-
ent directions of rotation will no longer be detected. The outputs Clockwise
and Anti-clockwise switch to a safe condition. The safe condition is cleared
again as soon as the error is remedied. Hazards that can arise through an
automatic restart must be excluded within the user program.

Safety
Operating Manual PNOZ ms4p
22109-EN-03 10
The following is deemed improper use in particular:
}Any component, technical or electrical modification to the product
}Use of the product outside the areas described in this manual
}Use of the product outside the technical details (see Technical details).
NOTICE
EMC-compliant electrical installation
The product is designed for use in an industrial environment. The product
may cause interference if installed in other environments. If installed in other
environments, measures should be taken to comply with the applicable
standards and directives for the respective installation site with regard to in-
terference.
3.2 System requirements
Please refer to the "Product Modifications PNOZmulti" document in the "Version overview"
section for details of which versions of the base unit and PNOZmulti Configurator can be
used for this product.
3.3 Safety regulations
3.3.1 Safety assessment
Before using a unit it is necessary to perform a safety assessment in accordance with the
Machinery Directive.
Functional safety is guaranteed for the product as a single component. However, this does
not guarantee the functional safety of the overall plant/machine. In order to achieve the re-
quired safety level for the overall plant/machine, define the safety requirements for the
plant/machine and then define how these must be implemented from a technical and organ-
isational standpoint.

Safety
Operating Manual PNOZ ms4p
22109-EN-03 11
3.3.2 Use of qualified personnel
The products may only be assembled, installed, programmed, commissioned, operated,
maintained and decommissioned by competent persons.
A competent person is someone who, because of their training, experience and current pro-
fessional activity, has the specialist knowledge required to test, assess and operate the
work equipment, devices, systems, plant and machinery in accordance with the general
standards and guidelines for safety technology.
It is the company’s responsibility only to employ personnel who:
}Are familiar with the basic regulations concerning health and safety / accident preven-
tion
}Have read and understood the information provided in this description under "Safety"
}And have a good knowledge of the generic and specialist standards applicable to the
specific application.
3.3.3 Warranty and liability
All claims to warranty and liability will be rendered invalid if
}The product was used contrary to the purpose for which it is intended
}Damage can be attributed to not having followed the guidelines in the manual
}Operating personnel are not suitably qualified
}Any type of modification has been made (e.g. exchanging components on the PCB
boards, soldering work etc.).
3.3.4 Disposal
}In safety-related applications, please comply with the mission time TM in the safety-re-
lated characteristic data.
}When decommissioning, please comply with local regulations regarding the disposal of
electronic devices (e.g. Electrical and Electronic Equipment Act).
3.3.5 For your safety
The unit meets all the necessary conditions for safe operation. However, you should always
ensure that the following safety requirements are met:
}This operating manual only describes the basic functions of the unit. The expanded
functions are described in the PNOZmulti Configurator's online help. Only use these
functions once you have read and understood the documentations.
}Do not open the housing or make any unauthorised modifications.
}Please make sure you shut down the supply voltage when performing maintenance
work (e.g. exchanging contactors).

Function description
Operating Manual PNOZ ms4p
22109-EN-03 12
4 Function description
4.1 Integrated protection mechanisms
The relay conforms to the following safety criteria:
}The circuit is redundant with built-in self-monitoring.
}The safety function remains effective in the case of a component failure.
4.2 Operation
The speed monitor can monitor an axis for standstill, speed and direction of rotation. The
speed monitor signals the status of the monitored values to the base unit. Depending on
the implemented safety circuit, the values may be transferred from the base unit to a relay
output on the safety system, for example. Incremental encoders may be used to record the
values.
The configuration of the speed monitor is described in detail in the PNOZmulti Configur-
ator's online help.
4.3 Block diagram
Interface
to previous
module
Interface
to next
module
X12
X1
4.4 Incremental encoders
4.4.1 Requirements of the incremental encoders
}Only incremental encoders with a differential output of the following type are permitted
– Sin/Cos
– TTL (RS 422)
– HTL (24 V)
}Please note the values stated in the technical details

Function description
Operating Manual PNOZ ms4p
22109-EN-03 13
4.4.2 Adapter for incremental encoders
The adapter records the data between the encoder and drive and makes it available to the
PNOZ ms4p via the RJ45 socket.
Pilz supplies complete adapters as well as ready-made cable with RJ45 connector, which
can be used when making your own adapter. The range of products in this area is con-
stantly being expanded. Please contact us about the range of adapters that is currently
available.

Installation
Operating Manual PNOZ ms4p
22109-EN-03 14
5 Installation
5.1 General installation guidelines
}The control system should be installed in a control cabinet with a protection type of at
least IP54. Fit the control system to a horizontal mounting rail. The venting slots must
face upward and downward. Other mounting positions could destroy the control system.
}Use the notches on the rear of the unit to attach it to a mounting rail. Connect the con-
trol system to the mounting rail in an upright position, so that the earthing springs on the
control system are pressed on to the mounting rail.
}The ambient temperature of the PNOZmulti units in the control cabinet must not exceed
the figure stated in the technical details, otherwise air conditioning will be required.
}To comply with EMC requirements, the mounting rail must have a low impedance con-
nection to the control cabinet housing.
CAUTION!
Damage due to electrostatic discharge!
Electrostatic discharge can damage components. Ensure against discharge
before touching the product, e.g. by touching an earthed, conductive sur-
face or by wearing an earthed armband.
5.2 Dimensions
94 (3.70")
45
(1.77")
121 (4.76")

Installation
Operating Manual PNOZ ms4p
22109-EN-03 15
5.3 Connecting the base unit and expansion modules
Connect the base unit and the expansion modules as described in the operating manuals
for the base modules.
}The terminator must be fitted to the last expansion module
}Install the expansion module in the position configured in the PNOZmulti Configurator.
The position of the expansion modules is defined in the PNOZmulti Configurator. The ex-
pansion modules are connected to the left or right of the base unit, depending on the type.
Please refer to the document "PNOZmulti System Expansion" for details of the number of
modules that can be connected to the base unit and the module types.

Commissioning
Operating Manual PNOZ ms4p
22109-EN-03 16
6 Commissioning
6.1 General wiring guidelines
The wiring is defined in the circuit diagram of the PNOZmulti Configurator.
Details of the input type, axis type and reset mode, plus the values for standstill, speed
monitoring and direction of rotation are also defined in the PNOZmulti Configurator.
Please note:
}Information given in the Technical details must be followed.
}Use copper wiring with a temperature stability of 75 °C.
CAUTION!
The configurable switch-off delay when overspeed is reached increases the
reaction time of the system comprising base unit and speed monitor by the
stated value (see technical details). This must not delay the transfer to a
safe condition by more than the permitted time. The configuration of the
switch-off delay must be considered in the risk assessment as regards haz-
ards, reaction time and safety distance.
6.2 Pin assignment of RJ45 socket
RJ45 socket
8-pin PIN Track
8 1
1 5 V
2 0 V
3 T
4 A
5 /A
6 /Z
7 B
8 /B

Commissioning
Operating Manual PNOZ ms4p
22109-EN-03 17
6.3 Connecting the incremental encoder
Proceed as follows when connecting the incremental encoder:
}The incremental encoder may be connected via an adapter (e.g. ) or directly to the
speed monitor.
}The incremental encoder on connector X12 monitors the axis
}Use only shielded cables for all connections
}0 V from the incremental encoder and speed monitor should always be connected.
}Position the terminating resistors of the signal lines as close as possible to the speed
monitor input.
6.3.1 Connect the signals from the incremental encoder to the speed
monitor
Encoder types: 1 Vss, 5 V-TTL
}Apply 5 VDC to incremental encoder only
}Do not terminate incremental encoder with Z0=120 Ohm
X12
X22
Speed monitor
5 V DC
0 V
2
4
5
7
8
A
/A
B
/B
5 V
0 V
Zo
Zo
Incremental
encoder
Fig.: Connection to incremental encoder type 1 Vss, 5 V-TTL
Encoder types: 24 V-HTL
}Apply 24 VDC supply voltage to incremental encoder only
}Do not terminate incremental encoder with Z0=120 Ohm
X12
X22
Speed monitor
24 V DC
0 V
2
4
5
7
8
A
/A
B
/B
24 V
0 V
Incremental
encoder
Fig.: Connection to incremental encoder type 24 V-HTL

Commissioning
Operating Manual PNOZ ms4p
22109-EN-03 18
6.3.2 Connect the incremental encoder to the speed monitor via an adapter
}The adapter is connected between the incremental encoder and the drive. The output
on the adapter is connected to the RJ-45 female connector on the speed monitor.
}The adapter can also be used without connecting to a drive. The signal lines can then
be terminated directly at the adapter with ZO = 120 Ohm.
}If the signal lines in the drive are already terminated with ZO = 120Ohm, the incre-
mental encoder may no longer be terminated.
}The signals relevant for the speed monitor are utilised in parallel by the adapter. The in-
formation stated under "Connect incremental encoder signals to the speed monitor" and
in the adapter operating manual must be observed when connecting the supply voltage.
}Supply only incremental encoder with 5 VDC. 24V-HTL signals may not be terminated.
CAUTION!
Communication errors may occur if the adapter cable is too long or there
are any external sources of interference. The length of the adapter cable
should be <5 m. Lay the adapter cable separately from any potential
sources of interference, such as drive cables leading to the motor, for ex-
ample.
Incremental
encoder
A
/A
B
/B
Zo
Zo
X12
Speed monitor
Adapter
5 V
0 V
5 V DC
0 V
18
Fig.: Connection via adapter

Commissioning
Operating Manual PNOZ ms4p
22109-EN-03 19
Incremental
encoder
A
/A
B
/B
Zo
Zo
X12
Speed monitor
Drive
Adapter
5 V
0 V
5 V DC
0 V
1 8
Fig.: Connection via adapter and drive

Operation
Operating Manual PNOZ ms4p
22109-EN-03 20
7 Operation
When the supply voltage is switched on, the PNOZmulti safety system copies the configur-
ation from the chip card.
The LEDs “POWER”, “DIAG”, “FAULT”, “IFAULT” and “OFAULT” will light up on the base
unit.
The PNOZmulti safety system is ready for operation when the "POWER" and "RUN" LEDs
on the base unit and the "READY" LED on the PNOZ ms4p are lit continuously.
7.1 LED indicators
Legend
LED on
LED flashes
LED flashes briefly
LED off
LED LED status Meaning
POWER Supply voltage is present.
FAULT External fault leading to a safe condition; the fault is at the in-
cremental encoder inputs whose LEDs are flashing, e.g. short
across the contacts
Internal fault leading to safe condition
SHAFT Encoder or wiring fault
Axis is in the normal range (no standstill, no overspeed)
Axis is signalling standstill
Axis is signalling overspeed
X12 Incremental encoder on terminal X12 is connected correctly
Table of contents
Other Pilz Control Unit manuals

Pilz
Pilz mc1p coated User manual
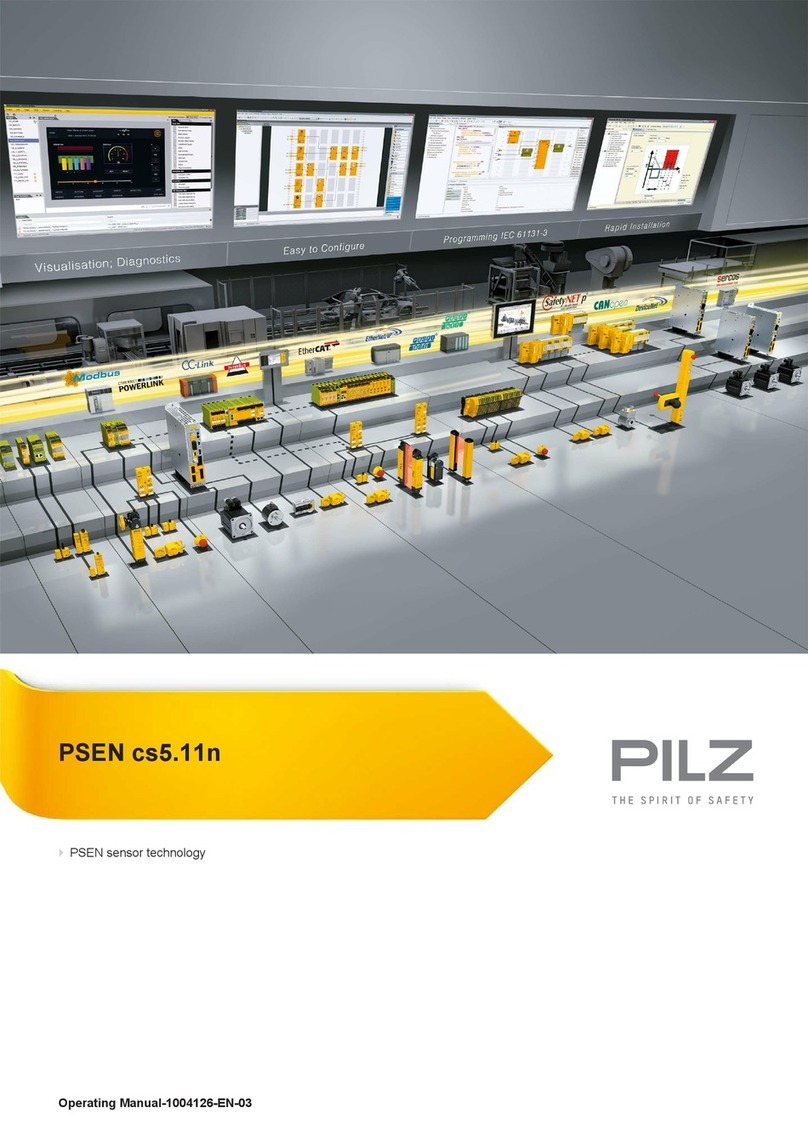
Pilz
Pilz PSEN cs5.11n User manual
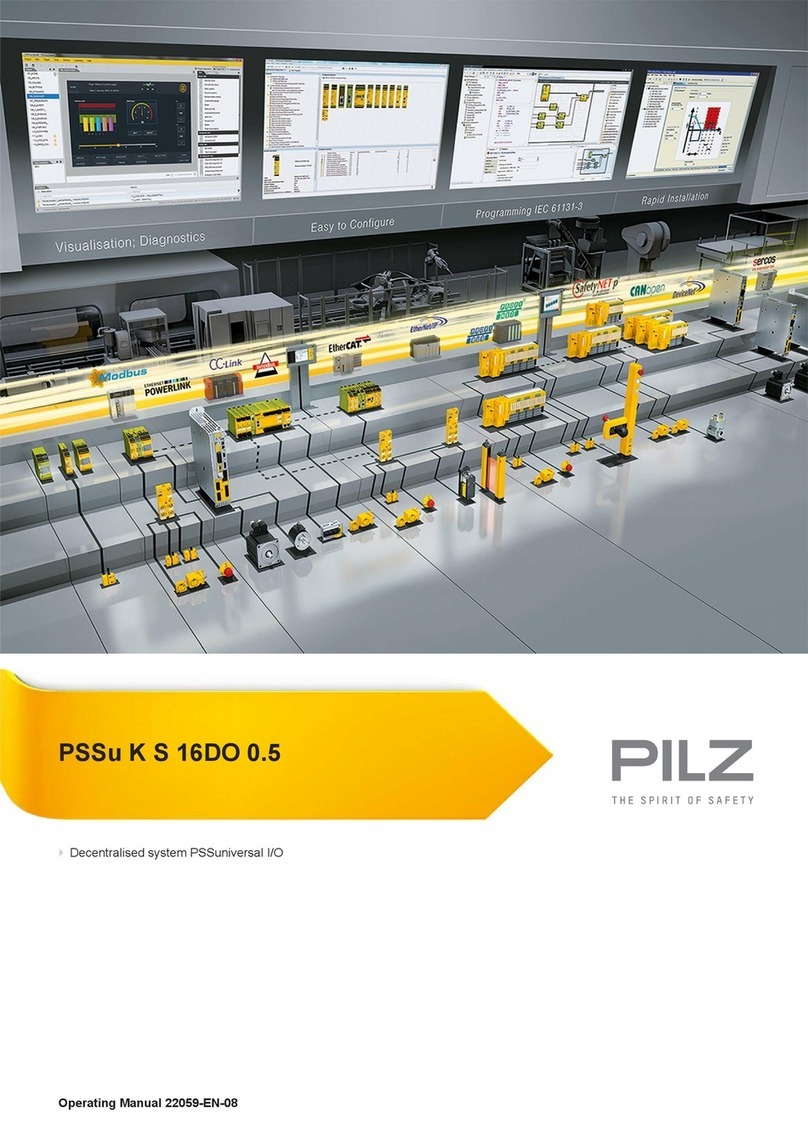
Pilz
Pilz PSSu K S 16DO 0.5 User manual
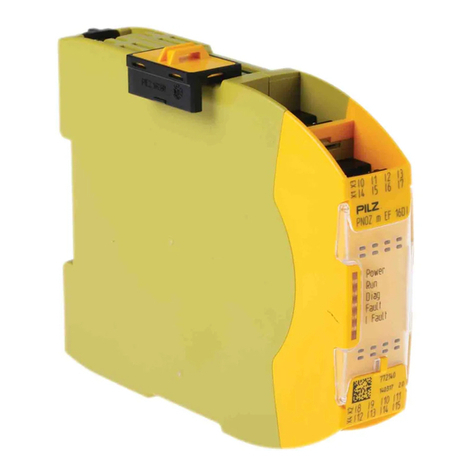
Pilz
Pilz PNOZ m EF 16DI User manual
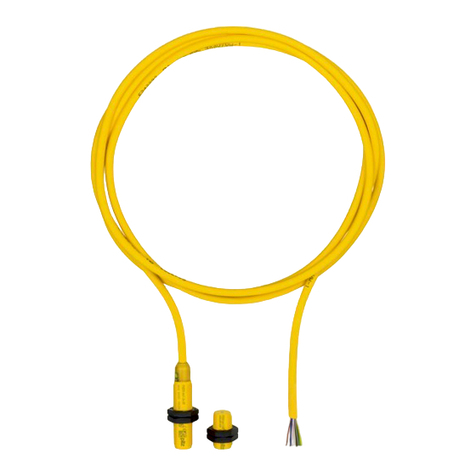
Pilz
Pilz PSEN ma1.3a/b-22 User manual
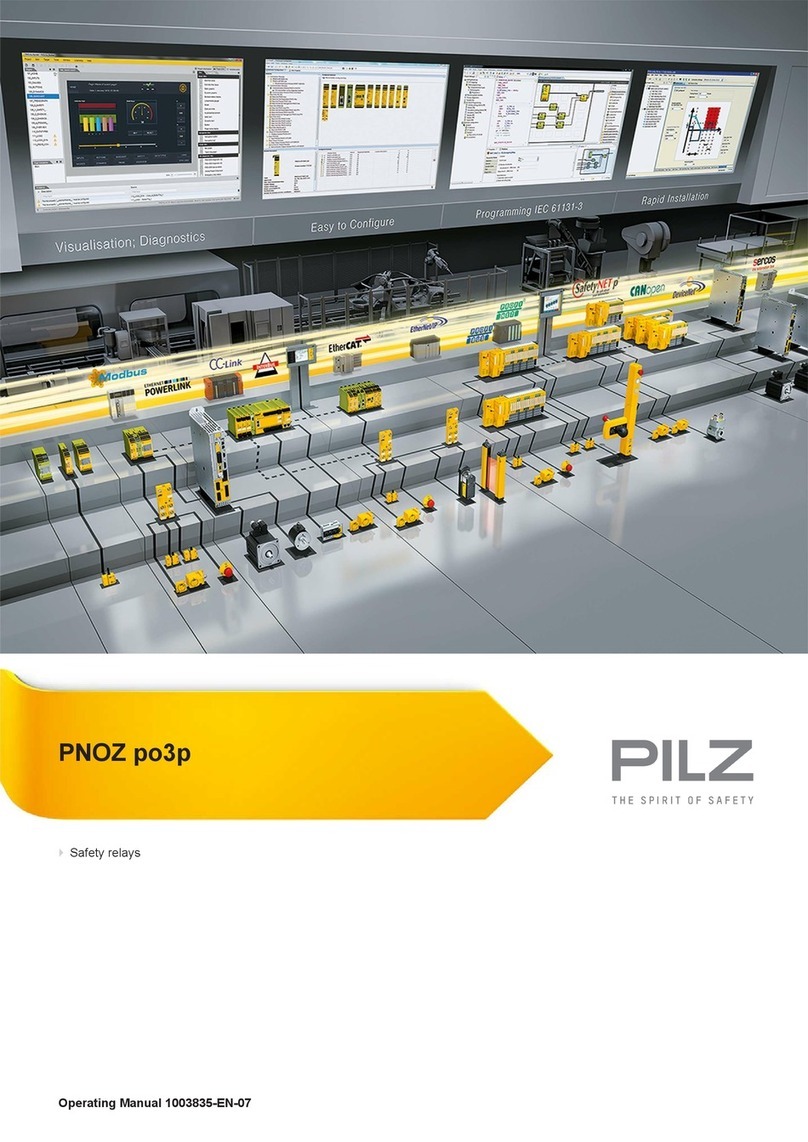
Pilz
Pilz PNOZ po3p User manual

Pilz
Pilz PIT gb LLLE User manual
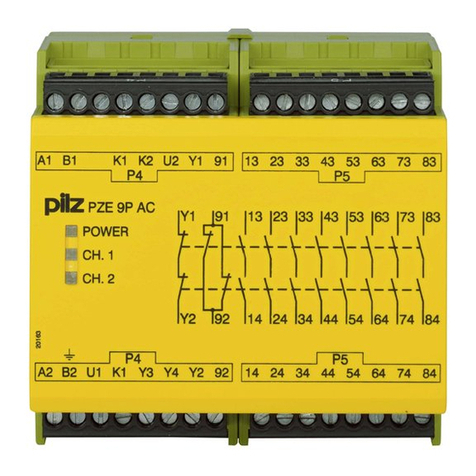
Pilz
Pilz PZE 9P User manual

Pilz
Pilz PNOZ mc1p User manual

Pilz
Pilz PMCtendo SZ User manual
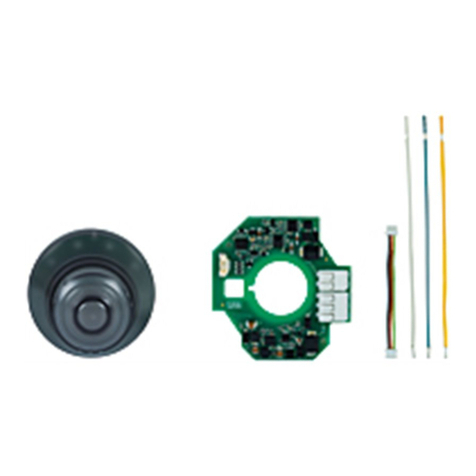
Pilz
Pilz PIT es Set10u-5c PCB User manual
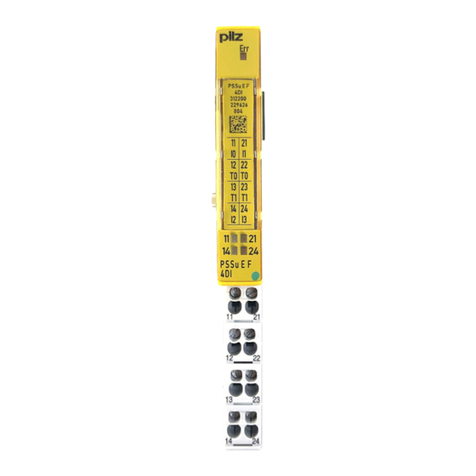
Pilz
Pilz PSSu E F 4DI User manual

Pilz
Pilz PNOZ m EF 2MM User manual
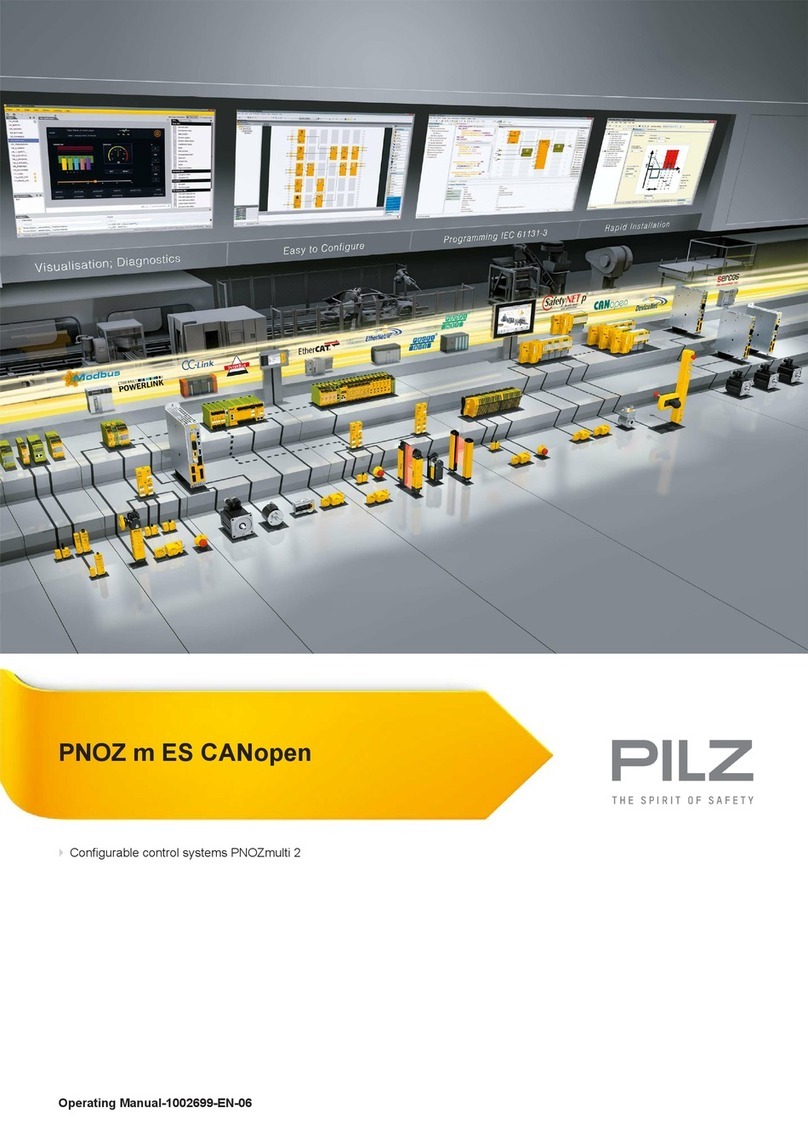
Pilz
Pilz PNOZ m ES CANopen User manual

Pilz
Pilz PZE 7 User manual
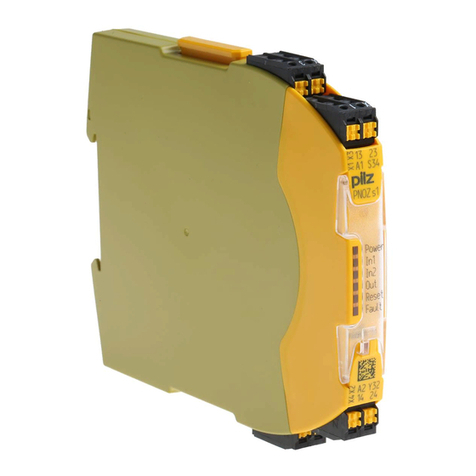
Pilz
Pilz PMCprotego S1--2 User manual

Pilz
Pilz Motion Control PMC User manual
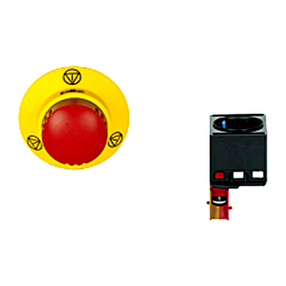
Pilz
Pilz PIT es Set/1 User manual

Pilz
Pilz PSEN ma1.4-51 M12/8-0.15m User manual
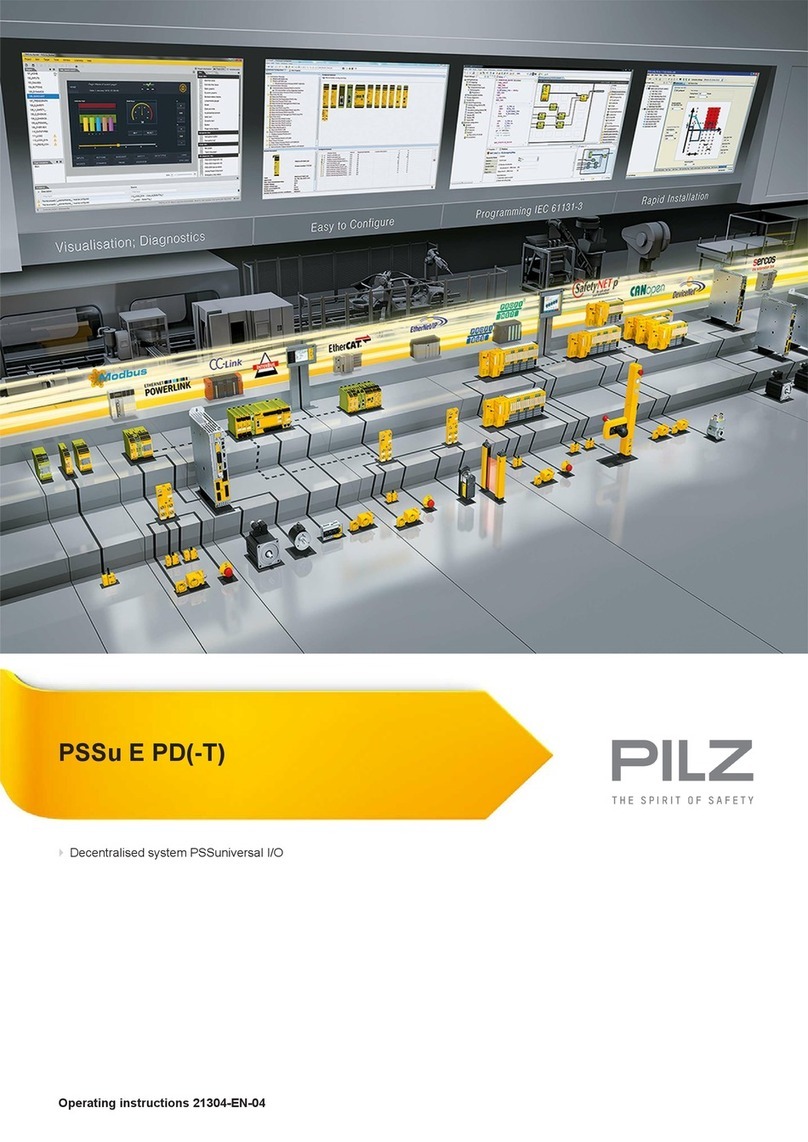
Pilz
Pilz PSSu E PD User manual