Rotech Sentinel B17 User manual

Vehicle Access Control
Pedestrian Access Control
Safety & Security Equipment
Sentinel B17 Sliding Gate Operator
Installation Instructions (V03/22)

2
A
B
1
204
245
316
398
307
213
398
34mm
BULL.PI
(Optional)
40
318
204
70
180
2
3
B
F
T
4

3
V
R
5
MIN = 10 mm
MAX = 20 mm
MIN =120 mm
MAX = 140 mm
6
7
R
D
R
D

4
8
≈1 mm
9
P
S
M
C
10
A
OK
F
1 ÷ 3 cm
S
11
B CA
KMax 35 mm
X
K X
3 mm 74 mm
35 mm 63 mm
BULL 17 OMI.S
(optional MLS)

5
12 13
14
C
L
7
4
1
2
3
POWER
2 x 1,5
RG 58
5
4 x 0,25
4
6
5
2 x 0,25
3 x 0,25
15
BAR

6
16
JP1
Safety BAR
J7
SW1
F4
M
8k2
II°Ch. Radio
L
N
GND
GND
N
L
SCA
SERVICE LIGHT
-
+24 Vdc 0.5A
BRAKE
RESISTOR
PHOTO TEST
(fig.15) OPEN/CLOSE
JP1 BAR
Open
BAR N.C.
JP1 BAR
Close
BAR 8K2
U1
LD1
LD2
MOT
MOT
COM
15AT 250Vac
5A
P3
J6
J8
CON1
5A
/BAR OPEN
ANT
RG 58

7
OPEN
OPEN
OPEN
OPEN
18
COM
NCNO
RX2
TX2
24 Vdc
PHOTC
COM
PHOTO
TEST
COM
NCNO
RX1
TX1
24 Vdc
PHOTO
TST1:ON TST2:ON
COM
PHOTO
TEST
PHOTOTEST OPEN
PHOTOTEST CLOSE
+- +- +-+-
19
SCA 24Vac
AUX: 0
Aux: 1
L
N
Service Light
230V
SCA
24V
+
-
MAX 16A
250Vac
MAX 16A
250Vac
LOGIC MINV
SCA SERVICE LIGHT
OPEN
Open Safety Edge
COM PHOTO
Close Safety Edge
(8K2/N.O. Jumper)
BAR BAR
MOTOR
J3
Open
BAR N.C.
J3
Close
BAR 8K2
N.C.
21
bar:On
BAR LOGIC=ON
SCA 24Vac
AUX: 0
Aux: 1
L
N
Service Light
230V
SCA
24V
+
-
MAX 16A
250Vac
MAX 16A
250Vac
20
17
MINV:Off
MINV:On

8
log
nMan
v1.00
8888 PRG
PRG
PRG
PRG
PRG
PRG
PRG
PRG
PRG
PRG
PRG
PRG
PRG
PRG
tca
tped
tsmo
tsmc
fsto
sldo
sldc
pmo
pMc
seav
sear
40
20
20
20
45
fstc
25
25
85
85
60
60
blo 3
blc 3
45
PAR
Power ON
Display OFF
Firmware Ver. (3s)
Diagnostic
on PRG
OFF PRG
OFF PRG
OFF PRG
OFF PRG
LOG tca
IBL
IBCA
SCL
PP
OFF PRG
PRE
OFF PRG
off PRG
off PRG
OFF PRG
htr
ltca
pho1
pho2
PRG
tls 60
PRG
tacc 20
res PRG
OFF PRG
0012 3456
Nman
MACI
RES
0000 conf OK
CODE
par
9000 9C5a
AUTO OK
PUSH
RE-ENTER
CODE
Display OFF
2 Cycle
OPEN/CLOSE
PRG
PRG
PRG
PRG
mot 0 0
1
2
3
1
2
3
YAK 25
BISON 35
BULL 15OMI
230Vac
BULL 15OMAI
115Vac
_ _ _ _ _ _
0
PRG
PRG
PRG
PRG
tdec
tbr
50
4
spin 2
aux 0
tca
off PRG
off PRG
off PRG
off PRG
TCA
tst1
tst2
bar
minv
off PRG
Horm

9
Legenda
Premere il tasto (-) / Press key (-) / Die Taste (-) drücken
Appuyez sur la touche (-) / Presionar la tecla (-) / Wcisnąć przycisk (-)
Premere simultaneamente (+) e (-) / Press simultaneously keys (+) and (-)
Gleichzeitig (+) und (-) drücken / Presser simultanément (+) et (-)
Presionar simultáneamente (+) y (-) / Naciskać jednocześnie (+) i (-)
Premere il tasto (+) / Press key (+) / Die Taste (+) drücken
Appuyez sur la touche (+) / Presionar la tecla (+) / Wcisnąć przycisk (+)
Selezionare il valore desiderato con i pulsanti (+) e (-)
Increase/decrease the value with keys (+) and (-)
Mit den Tasten (+) und (-) kann man eingerichtete Werte ändern
Régler la valeur désirée avec les touches (+) et (-)
Establecer con las teclas (+) y (-) el valor deseado
Nastawia przyciskami (+) i (-) obraną wartoś
Premere il tasto (PG) / Press key (PG) / Die Taste (PG) drücken
Appuyez sur la touche (PG) / Presionar la tecla (PG )/ Wcisnąć przycisk
(PG)
Selezionare il pulsante del trasmettitore da associare alla funzione
Press the transmitter key, which is to be assigned to function
Taste des Sendegeräts drücken, dem diese Funktion zugeteilt werden soll.
Appuyer sur la touche du transmetteur qu’e l’on désire affecter à cette
fonction.
Presionar la tecla del transmisor que se desea asignar a esta función.
Wcisnąć przycisk nadajnika, który zamierza się skojarzyć z tą funkcją.
log
nMan
v1.00
8888 PRG
PRG
PRG
PRG
PRG
PRG
PRG
PRG
PRG
PRG
PRG
PRG
PRG
PRG
tca
tped
tsmo
tsmc
fsto
sldo
sldc
pmo
pMc
seav
sear
40
20
20
20
45
fstc
25
25
85
85
60
60
blo 3
blc 3
45
PAR
Power ON
Display OFF
Firmware Ver. (3s)
Diagnostic
on PRG
OFF PRG
OFF PRG
OFF PRG
OFF PRG
LOG tca
IBL
IBCA
SCL
PP
OFF PRG
PRE
OFF PRG
off PRG
off PRG
OFF PRG
htr
ltca
pho1
pho2
PRG
tls 60
PRG
tacc 20
res PRG
OFF PRG
0012 3456
Nman
MACI
RES
0000 conf OK
CODE
par
9000 9C5a
AUTO OK
PUSH
RE-ENTER
CODE
Display OFF
2 Cycle
OPEN/CLOSE
PRG
PRG
PRG
PRG
mot 0 0
1
2
3
1
2
3
YAK 25
BISON 35
BULL 15OMI
230Vac
BULL 15OMAI
115Vac
_ _ _ _ _ _
0
PRG
PRG
PRG
PRG
tdec
tbr
50
4
spin 2
aux 0
tca
off PRG
off PRG
off PRG
off PRG
TCA
tst1
tst2
bar
minv
off PRG
Horm

21
1) GENERAL FEATURES
Automation with single-phase power supply for sliding gates
2)GENERAL INFORMATION
For an efficient operation of the sliding automatic mechanism, the gate must have the following features:
- The guide rail and its wheels must be suitable in size and mantained to prevent gate from excessive sliding friction.
- When running, gate must not rock excessively.
- Opening and closing stroke must be regulated by a mechanical limit stop (to safety standard in force).
3) TECHNICAL DATA
BULL 17 OMI BULL 17 OMAI
Feed 230Vac 50/60Hz 115Vac 60Hz
Absorption 7 A 8 A
Torque 68 Nm 40 Nm
Inverter Yes Yes
Operating jogging 40% 40%
Protection degree IP44 IP44
Working temperature -20°C / +50°C -20°C / +50°C
Max. gate weight 1700 kg 1700 kg
Rack modulus M4 Z 18* M4 Z 18*
Opening speed 24 m/min MAX 24 m/min MAX
Noise level <70 dB <70 dB
Lubrication Oil Oil
Weight 21,3 kg 21,3 kg
*M6 Z13 (art. RI.P6 - optional)
4) INSTALLATION OF THE FOUNDATION PLATE
Dimensions of the foundation plate are shown in Fig. 2.
It is essential to keep the distance from the rack, in order to position and remove the actuator once the rack is fitted to the gate leaf.
The types of fittings of the foundation plate are mainly the following:
1 Installation without adjustment in height on the already existing base in concrete (Fig.2).
By using the plate as drilling template, drill 4 holes Ø10mm, and insert the steel threaded screw anchors, Ø10x120mm, similar to those shown in Fig. 2.
Lock the actuator directly to floor, as indicated in Fig.7.
1) GENERAL FEATURES .................................................................................21
2)GENERAL INFORMATION ............................................................................21
3) TECHNICAL DATA ......................................................................................21
4) INSTALLATION OF THE FOUNDATION PLATE...............................................21
5) RACK FIXING.............................................................................................22
6) LIMIT STOP FLASK POSITIONING (SEE FIG.10)...........................................22
7) HOW TO INSTALL THE MAGNETS(BULL 17 OMI.S/BULL 17 OMAI.S) FIG.11 22
8) MANUAL OPERATION (SEE FIG.12-13-14)..................................................22
9) WIRE DIAGRAM.........................................................................................22
10) CP.YAK OTI CONTROL UNIT......................................................................22
10.1) INPUT/OUTPUT FUNCTIONS........................................................... 22
10.2) HOW TO CHECK CONNECTIONS..................................................... 23
11) PROGRAMMING ......................................................................................23
12) TO ACCESS PROGRAMMING....................................................................23
12.1) RUN SELF-LEARNING AND ANTI-CRUSHING DEVICE SETTING ........ 23
13) PARAMETERS, LOGIC AND SPECIAL FUNCTIONS .....................................24
14) HOW TO ADJUST SPEED AND BRAKING...................................................26
15) AUTOSET ................................................................................................27
16) ERROR MESSAGES .................................................................................28
17) DISPLAY LCD ..........................................................................................28
18) DIAGNOSTICS .........................................................................................28
19) MAINTENANCE........................................................................................29
INDEX
QUICK PROGRAMMING
- Set the motor position by means of the menu MINV, by default the automation is set as LEFT MOTOR
- Enter the menu AUTO, confirm 2 times with <PG> and wait until the automation has carried out the autoset of the parameters
- By means of the menus PAR and LOG, select the parameters and the logic functions wanted according to the type of installation in object
IMPORTANT:After every change of the parameters FSTS. SLDO, SLDC, TSMO, TSMC, the automation executes an opening maneuver followed
by a closing one in order to acquire the new values of current and torque, on the screen will appear the message <PRG>
- To store the transmitter press the receiver button plug.

22
2 Installation with adjustment in height on the already existing base in concrete (Fig.3).
By using the plate as drilling template, drill 4 holes, and insert the Ø 10mm steel screw anchors for threaded bars.
Tighten the 4 threaded bars, M10/120mm, and anchor the screw anchors by tightening the nuts “B” to floor with the corresponding washers.
With reference to Fig. 3, position the foundation plate by means of the adjustment nuts “A”. After carrying out the required regulations, position the motor
as shown in Fig.6, and lock it, as indicated in Fig.7.
3 Installation with adjustment in height on concrete base.
With reference to Fig. 4, fit the stretcher bolts on the foundation plate and provide for a hole of adequate size.
Immerse the stretcher bolts in concrete, then remove the nuts “D” and the 11x30, large band washers “R”. Move them under the plate to allow for re-
gulations in height of the actuator (Fig. 5).
Carry out the regulations shown in Fig. 6 and lock the motor as indicated in Fig.7.
CAUTION: apart from the fitting modality used, carefully check that the actuator is steadily positioned and the materials are suited to the in-
tended use.
5) RACK FIXING
Iron rack, 12x30mm M4.
Position the spacers D by welding or fit them to the gate with screws at 130/150mm height from the centre line of the slot used for fitting to the base on
which the foundation plate is to be fixed.
Keep the pitch of teeth between the two parts of the rack; the joining with another piece of rack would make it easier to achieve (see Fig.8)
Secure the rack with the screws V making sure, once the actuator has been installed, that between rack and the drive gear there is always approx. 1mm
clearance (see Fig.9); to get this clearance use the slots on the rack.
6) LIMIT STOP FLASK POSITIONING (SEE FIG.10)
Open manually the gate and leave approximately of 1÷3cm, depending on gate weight, between gate and positive mechanical stop A; tighten the limit
stop flask S with the grains G to press the limit stop micro. Repeat the sequence with closing gate.
7) HOW TO INSTALL THE MAGNETS(BULL 17 OMI.S/BULL 17 OMAI.S) FIG.11
The magnets are housed in special supports (fig.11-”A”). These magnets are to be fitted to the limit switch brackets or the rack and cause the triggering
of sensors when they approach them.
Fitting onto the limit switch brackets
The bases are complete with hooking tongue allowing the fitting of the magnets to the limit switch bracket supplied with the operator, as shown in Fig.11-B.
This type of fitting allows to rapidly adjust the position of magnets. After calculating the correct distance, fix the support in the correct position by means
of a screw, so as to avert the moving of the bracket.
Fitting onto the rack
As an alternative, the supports can be fitted directly to the rack, by using the slots shown in Fig. 11-C. This fitting mode does not allow for subsequent
regulations. It is therefore advised to make some trials with temporarily fitted supports before carrying out the final fitting.
IMPORTANT: The correct distance of the magnet with respect to the sensor depends on the installation characteristics. This space cannot be preset
and must be adjusted on a trial basis.
The distances regarding the triggering of the sensor (value X) with respect to distance K of 3 and 35 mm, which are shown in Fig. 11 are only indicative.
In any case, distance K must not exceed 35 mm as a higher distance will not allow the triggering of the magnetic sensor.
8) MANUAL OPERATION (SEE FIG.12-13-14)
In the event of power failure or malfunction, to manually operate the gate proceed as follows:
- After inserting the customized key C, turn it anti-clockwise and pull the lever L.
- The geared motor is unlocked and the gate can be moved by hand.
- To return to the normal operating mode, close the lever L again and manually activate the gate until it is geared.
- Move the gate in one of the limit switches so that the next maneuver is at normal speed.
9) WIRE DIAGRAM
For the wire connections of the system and to adjust the operating modes, please refer to the Instruction Manual of the control unit.
In particular, the anti-crash device (encoder) should be adjusted according to regulations in force.
Please remember that the device should be earthed by means of the appropriate terminal.
10) CP.YAK OTI CONTROL UNIT
10.1) INPUT/OUTPUT FUNCTIONS
Terminals Function Description
L-N-GND Power supply
Power input of single-phase network.
L: Phase - N: Neutral - GND: Engine housing earth connection.
Please note that the ground must be connected as indicated in the diagram in Fig. 11.
U-V-W Three-phase engine U-V-W three-phase engine connection.
Lamp Flashing Flashing connection 230Vac 40W max or 115Vac 40W max (BULL 17 OMAI).
24 Vdc 24 Vdc Power supply output accessories 24Vdc/500mA max.
SCA SCA Voltage free N.O. contact for open gate light 24 Vac, 0.5 A max, configurable via the SCA logic
Phototest Phototest Phototest output for verified photocells, see figure 17
COM Common Common for all control inputs.
OPEN Opens OPEN button input (N.O. contact).
CLOSE Closes CLOSE button input (N.O. contact).
P.P. Step-step Step-step button input (N.O. contact)
PED Pedestrian Pedestrian button input (N.O. contact)
STOP Stop STOP button input (N.C. contact)
PHOTO Opening photocell Input for photocell active only in the opening phase
PHOTC Closing photocell Input for photocell active only in the closing phase

23
COM Common Common for limit switch.
SWC Closing Limit Switch CLOSING limit switch input (N.C. contact)
SWO Opening Limit Switch OPENING limit switch input (N.C. contact)
BAR Sensing safety edge
Sensing edge contact input
Resistive safety edge (8K2): JP1 "BAR" closed
Mechanical safety edge (N.C.): JP1 "BAR" open
The intervention of the safety edge stops the movement of the gate and reverses for approximately 3s.
Note: this entry is connected the safety transformer mounted on the hand release lever that prevents
any maneuver if the motor released.
The sensitive edge must be connected in series to this Microswitch, as shown in Figure 21
RADIO Radio receiver Quick connector for plug radio receiver.
2CH Second channel N.O. output of the second radio channel of the radio receiver. (max 24Vac/dc 1A)
BRAKE Brake Resistance Input for braking current dissipation resistance
The resistance is only used on 230V BULL 17 OMI
P3 Not used
CON1 Not used
J7 Not used
J8 Not used
SW1 Dip1, Dip2 Keep it ON
U1 CONFIGURATION
MEMORY
E-Eprom extractable memory. it contains all the configurations of the unit (logical, parameters, etc.),
excluding radio transmitters. In case of failure it is possible to extract the E-Eprom and insert it in a
different unit, thus avoiding reprogramming.
10.2) HOW TO CHECK CONNECTIONS
1) Cut off power supply.
2) Manually release the door/gate and push it for about half stoke. Lock the door again.
3) Restore power supply.
4) Send a step-by-step command through push-button <-> on the control unit (LCD display off). To stop the door/gate press <-> once more.
5) The door/gate should open. If not, set the MINV logics to change the opening direction (default MINV=OFF) Engine installed to the left.
11) PROGRAMMING
The programming of the various functions of the control unit is carried out using the LCD display on the control unit and setting the desired values in
the programming menus described below.
The parameters menu allows you to assign a numerical value to a function, in the same way as a regulating trimmer.
The logic menu allows you to activate or deactivate a function, in the same way as setting a dip-switch.
Other special functions follow the parameters and logic menus and may vary depending on the type of control unit or the software release.
12) TO ACCESS PROGRAMMING
1 - Press the button <PG>, the display goes to the first menu, Parameters “PAR”.
2 - With the <+> or <-> button, select the menu you want.
3 - Press the button <PG>, the display shows the first function available on the menu.
4 - With the <+> or <-> button, select the function you want.
5 - Press the button <PG>, the display shows the value currently set for the function selected.
6 - With the <+> or <-> button, select the value you intend to assign to the function.
7 - Press the button <PG>, the display shows the signal “PRG” which indicates that programming has been completed.
12.1) RUN SELF-LEARNING AND ANTI-CRUSHING DEVICE SETTING
When operator assembly and wiring is completed, parameters and logic are programmed, self learning allows the operator to learn the stroke and torque.
Enter menu Auto and press the button < PG >, PUSH will be displayed.
Press again the button < PG >: self-learning is beginning: PRG will be displayed, and the control panel completes some opening/closing cycles.
When the procedure is completed OK will be displayed.
This procedure can be followed from any position of the gate/door leaf and can be stopped at any moment by pressing keys <+> and <-> at the same
time, or through the activation of STOP/PHO/PHA/BAR/PP/PED inputs.
If the procedure is not successful, the wording ERR appears. Check that no obstacles or frictions are present.
After the AUTOSET procedure it is necessary to check the value of the operating forces according to the European Standards EN12445 and EN12453.
If the value of the force is too high it is mandatory to install a safety edge which complies to the standard EN12978.
Check the value of the operative forces in accordance with EN12445 and EN12453 at the end of the autoset phase. If the value of the force is too high
install an edge compliant with EN12978.
Notes:
Pressing <-> with the display turned off means an impulse of P.P.
Simultaneously pressing <+> and <-> from inside a function menu allows you to return to the previous menu without making any changes.
Hold down the <+> key or the <-> key to accelerate the increase/decrease of the values.
After waiting 30s the control unit quits programming mode and switches off the display.

24
13) PARAMETERS, LOGIC AND SPECIAL FUNCTIONS
The tables below describe the individual functions available in the control unit.
PARAMETERS (PAR)
MENU FUNCTION MIN-MAX-(Default) MEMO
TCA Automatic closure time. It is activated only with “TCA” logics :ON
At the end of the preset time, the control unit starts a new closing operation. 1-240-(40s)
Tped The passage left open by the door/gate leaf during the partial opening controlled by the
pedestrian inoput, is adjusted.
The value is expressed in percentage on the aggregate value of the stroke. 5-100-(20%)
tsmo It adjusts the duration of the OPENING slowdown phase.
The value is expressed as a percentage of the total value of the stroke.
See section “How to adjust speed and braking”. 10-100-(20%)
Tsmc It adjusts the duration of the CLOSING slowdown phase.
The value is expressed as a percentage of the total value of the stroke.
See section “How to adjust speed and braking”. 10-100-(20%)
FSTo
The opening and closing speed is adjusted.
IMPORTANT: Change the values of this parameter only by keeping to the weight limits
shown in Table 1.
See section “How to adjust speed and braking”.
20-120-(45)
fstc
The opening and closing speed is adjusted.
IMPORTANT: Change the values of this parameter only by keeping to the weight limits
shown in Table 1.
See section “How to adjust speed and braking”.
20-120-(45)
sldo Speed during braking is adjusted.
See section “How to adjust speed and braking”. 10-40-(25)
sldc Speed during braking is adjusted.
See section “How to adjust speed and braking”. 10-40-(25)
PMO The torque applied to motor 2 in the opening* phase is adjusted. 1-99-(85%)
PMC The torque applied to motor 2 in the closing* phase is adjusted. 1-99-(85%)
sEav
The trigger time of the anti-crash device (Encoder) is adjusted during the normal speed phase*.
0:Off-99: maximum sensibility - 1: minimum sensitivity Ø-90-(60%)
sEar The trigger time of the anti-crash device (Encoder) is adjusted during the braking phase*.
0:Off-99: maximum sensibility - 1: minimum sensitivity Ø-90-(60%)
blo Stop space is adjusted after reaching the opening and closing limit switch. This value is
expressed in centimetres.
See section “How to adjust speed and braking”. 1-10-(3)
blc Stop space is adjusted after reaching the opening and closing limit switch. This value is
expressed in centimetres.
See section “How to adjust speed and braking”. 1-10-(3)
TLS It is activated with AUX parameter only, preset to value 1.
The activation time of the service light is adjusted. 1-240-(60s)
TACC Ramp during acceleration. Value expressed in tenths of seconds.
See section “How to adjust speed and braking”. 1-25-(20)
TDEC Ramp during deceleration. 50-99-(50)
Tbr Emergency braking, after the activation of PHOT/BAR/STOP inputs,the value is expressed in
tenths of seconds (for adjustment see table 1). 1-20-(7)
spin
It adjusts the reversal distance that the gate travels following the intervention of the sensing
edge (SAFETY EDGE). During the reversal phase, further interventions of the sensing edge
are ignored, the intervention of the sensing edge causes stopping. If during reversal (in the
OPEN and CLOSE direction) a related photocell (PHOTO or PHOTC) is active, the parameter
is ignored and the reversal space must be minimal (10 cm).
The minimum value 1 equals approximately 20 cm, the maximum value 4 equals approxima-
tely 60 cm.
1-4-(1)
AUX
It selects the operating mode of the SCA output:
0: SCA
1: Service light. The contact closes for the time preset with TLS parameter. The countdown
starts at the inception of the opening operation.
2: Area light. The contact closes in the opening phase and remains closed for the entire TCA
time. It opens only with closed door.
See wiring shown in figure 17.
Ø-2-(Ø)

25
LOGIC (LOG)
MENU FUNCTION ON-OFF-(Default) MEMO
TCA Enables or disables automatic closing
On: automatic closing enabled
Off: automatic closing disabled
(ON)
IBL
Enables or disables multi-flat function.
On: multi-flat function enabled. The step-by-step and perdestrian commands have no effect
during the opening phase.
Off: multi-flat function disabled.
(OFF)
IBCA During the TCA phase, the PP controls are enabled or disabled.
On: PP controls are disabled.
Off: PP controls are enabled.
(OFF)
SCL
The rapid closure is enabled or disabled. It can be activated only if TCA:ON
On: enabled rapid closure. With open gate, the photocell activation causes the automatic
closure after 3 s.
If the photocell is activated during the opening phase, the operation is completed and
closure starts after 3s
Off: disabled rapid closure.
(OFF)
PP The operating mode of “P.P. Push button” and of the transmitter are selected.
On: Operation : OPEN > CLOSE > OPEN >
Off: Operation: OPEN > STOP > CLOSE > STOP >
(OFF)
PRE Forewarning flashing light enabled or disabled.
On: enabled forewarning flashing light. The flashing light is activated 3 s before the starting of the motor.
Off: disabled forewarning flashing light.
(OFF)
HTR
The Service Man function is enabled or disabled.
On: Service Man operation. The OPEN/CLOSE push buttons should be kept pressed for the
entire operating time.
Off: Automatic operation.
(OFF)
LTCA During the TCA time, the blinker is enabled or disabled.
On: Enables blinker.
Off: Disables blinker.
(OFF)
Pho1 The PHOT O input is enabled or disabled in the opening phase.
On: Photocell 1 activated only in the closing phase.
Off: Photocell 1 activated in both opening and closing phases.
(OFF)
Pho2 The PHOT C input is enabled or disabled in the opening phase.
On: Photocell 1 activated only in the closing phase.
Off: Photocell 1 activated in both opening and closing phases.
(OFF)
tst1
The check on the photocell connected to PHOTO input is activated or deactivated
Before operation, the control unit checks the switching of the photocell contact.
The test shall be carried out following any command (PP, OPEN, CLOSE, radio, TCA) with engine
off before performing the manoeuvre (even partial manoeuvres). The test is not carried out when
the engine already in motion must stop and then reverse following the SAFETY EDGE or PHOT
intervention. If the checks are not successful, the door/gate will not move.
On: activated check on photocell.
Off: deactivated check on photocell.
(OFF)
tst2 As for TST1, but referred to PHOTC input (OFF)
bar
It changes the mode of operation of the PHOTO inputs (photocell in OPEN) and BAR in case
the sensitive safety edges are installed in the mobile opening and closing edges.
On: The PHOTO input takes on a similar function to the BAR input but inverts the motion for the
distance set with the SPIN parameter if the sensing edge to which it is connected is pressed
during the opening phase (if the photocells in CLOSE are busy, it reverses for 10 cm). The safety
edge connected to the BAR input is only active during the CLOSING phase.
Off: The intervention of the sensing safety edge connected to the BAR input stops the movement
of the gate and inverts the motion for the distance set with the SPIN parameter (if the photocell
in the inversion direction is busy it reverses for 10cm) , both in OPENING and CLOSING.
The PHOT OPEN input resumes the operation of the photocell active in opening.
(OFF)
MINV The opening direction of the motor is selected (see Fig. 4):
On: Right side motor mount
Off: Left side motor mount
(OFF)
horm
Enable or disable the transition from Automatic to Man Present mode.
The logic is associated with the state of the PED input.
On: If at least one of the inputs: DAS, PHOTO or PHOTC remains active (open contact) for at le-
ast 10 seconds, regardless of the position of the door, the unit switches to Man Present mode
(only the OPEN/ CLOSE/ SWO/ SWC inputs are active), after activating the PED command.
For further safety purposes, it is necessary that during the OPEN/CLOSE command, the
PED input is closed. Use an N.O. key for this function, with automatic release.
Off: Automatic switch disabled.
The logic also works with PHOTOTEST enabled. (OFF)
(OFF)

26
NUMBER OF CYCLES (Nman)
The number of cycles (open+close) completed by the system is displayed.
When the push-button <PG> is pressed once, the first 4 digits are displayed, if the push-button is pressed once more, the last 4 digits are displayed.
E.g. <PG> 0012 >>> <PG> 3456: 123.456 cycles were performed.
MAINTENANCE (maci)
This function allows to activate the indication of maintenance required after a certain number of operations, preset by the installer.
To activate and select the number of operations, proceed as follows:
Press the <PG> button, OFF is displayed, indicating that the function is disabled (default).
Select one of the numbers shown (from OFF to 100) by using the <+> and <-> keys . The figures express the value of hundreds of cycles (e.g.: the
number 50 means 5000 operations).
Press OK to activate the function. The PROG message is displayed.
When the flashing light flashes for around 10 sec at end of operation, this means that maintenance operations are needed.
RESET (RES)
RESET of the control unit. WARNING: Returns the control unit to the default values.
When the <PG> push-button is pressed once, the RES wording begins to flash, if the push-button<PG> is pressed once more, the control unit is reset.
Note: neither the transmitter codes nor the position and stroked of the gate leaf will be erased from the receiver.
AUTOSET (AUTO)
The automatic system stroke is self learned. See section “STROKE SELF-LEARNING”
PASSWORD (CODE)
It allows to type in an access protection code to the programming of the control unit.
A four-character alphanumeric code can be typed in by using the numbers from 0 to 9 and the letters A-B-C-D-E-F.
The default value is 0000 (four zeros) and shows the absence of a protection code.
While typing in the code, this operation can be cancelled at any moment by pressing keys + and – simultaneously. Once the password is typed in, it
is possible to act on the control unit by entering and exiting the programming mode for around 10 minutes in order to allow adjustments and tests on
functions.
By replacing the 0000 code with any other code, the protection of the control unit is enabled, thus preventing the access to any other menu. If a protecg-
tion code is to be typed in, proceed as follows:
- select the Code menu and press OK.
- the code 0000 is shown, also in the case a protection code has been previously typed in.
- the value of the flashing character can be changed with keys + and -.
- press OK to confirm the flashing character, then confirm the following one.
- after typing in the 4 characters, a confirmation message “CONF” appears.
- after a few seconds, the code 0000 appears again
- the previously stored protection code must be reconfirmed in order to avoid any accidental typing in.
If the code corresponds to the previous one, a confirmation message “OK” appears.
The control unit automatically exits the programming phase. To gain access to the Menus again, the stored protection code must be typed in.
IMPORTANT: TAKE NOTE of the protection code and KEEP IT IN A SAFE PLACE for future maintenance operations. To remove the code from
a protected control unit, enter the programming mode with the password and reset the code to the 0000 default value.
IF YOU LOOSE THE CODE, PLEASE CONTACT THE AUTHORISED SERVICE CENTER FOR THE TOTAL RESET OF THE CONTROL UNIT.
ENGINE TYPE SELECTION (mot)
It allows for selecting the configuration of the unit for the type of engine used.
Normally the correct value is factory preset and does not need any intervention on the part of the installer.
Only in case of replacement of the unit, it is necessary to set the correct value, each digit corresponding to a given engine model, as per the list below.
0: YAK25/BISON35
1: BULL 17 OMI 230Vac
2: BULL 17 OMAI 115Vac
3: NOT USED
The display always shows the abbreviation MOT followed by the engine number currently set (example MOT.1,MOT.2).
14) HOW TO ADJUST SPEED AND BRAKING
The door/gate stroke is shown in the following scheme:
V
T
FSTS
slds
BLc
TAcc Tdec
TSM
SWO (SWC) SWC (SWO)
The V axis is the gate/door speed, T axis is the time required by the door/gate to move from a limit switch to the other. The parameters govern both the
opening and the closing phases.
At gate/door stopped on any SWO (SWC) limit switch, when a control key is pressed the gate/good starts moving and reaches the standard operating
speed, which can be adjusted by FSTSO/FSTSC parameter.
The TACC time sets how rapidly the gate/door should reach the standard speed.

27
Before meeting the SWX (SWO) stop limit switch, braking preset by TSM time will start.
Braking leads the gate/door from standard speed (FSTSO/FSTSC) to braking speed, adjusted by SLDS parameter.
The TDEC time sets how rapidly the gate/door should reach the braking speed.
The TDEC time is theoretical by reason of the fact that as soon as the speed reaches the value preset by SLDS, braking at constant speed starts until
reaching the SWC (SWO) limit switch.
Once the limit switch is reached, the gate/door continues its movement for a period of time adjusted by BLC parameter, until entire stop.
The following diagram graphically represents the stroke of the gate in case of intervention of a safety input (STOP/PHOT/BAR):
V
T
FSTo/fstc
sldo/SldC
BLo/blc
TAcc Tdec
TSMo/tsmc
SWO (SWC) SWC (SWO)
V
T
tbr
stop
phot
bar
The intervention of the safety input causes an immediate slowing of the gate, the time in which the gate switches from standard speed to a complete
stop is adjustable through the TBR value and must respect the values indicated in Table 1.
IMPORTANT:
- For the correct operation of parameters it is mandatory that the AUTOSET be carried out correctly (see STROKE LEARNING).
- If the FSTo(FSTc) speed is increased, TSMo(TSMc), TACC and TDEC values must be increased proportionally in order to avert any mechanical stress
to the gear motor.
-
The TBR value must be set according to those indicated in table 1, setting a TBR that is too short on a gate with strong inertia may damage the automation.
A TSMo (TSMc) value, which is too short, combined with a TDEC value, which is too high, might result in the cancellation of the SLDo (SLDc) braking
phase due to the gate leaf friction and the triggering of the limit switches when the speed is still high.
This situation must be absolutely avoided.
- The AUTO function does not change the default values of the above-mentioned parameters. The latter must be preset by the installer according to
the gate/door specifications.
- An NC contact that opens whenever the engine is unlocked or the casing is removed will also be serially wired in the BAR input with the SAFETY
EDGE (or the SAFETY EDGES). Thus, in situation 1. unit powered, 2. Engine stopped, 3. SWO and SWC not engaged (i.e. engine out of limit switches),
if the BAR input is activated and then reactivated (engine locked and carter inserted, ready to restart), upon the subsequent PP/OPEN/CLOSE
command (also by radio) it is necessary to force a slow manoeuvre.
TABLE 1 BULL 17 OMI / BULL 17 OMAI
WEIGHT
Kg
FSTO/FSTC
Max
TBR
Min
TSMO/TSMC
Min
V
m/1'
1700 85 2 30 17
1000 100 3 35 20
500 120 4 50 24
Depending on the actuator model and the weight of the gate, set the speed value in opening and closing (FSTO/FSTC), the minimum value of the TBR
braking and the minimum value of the TSMO/TSMC slowdown distance.
At each combination we obtain the value of the speed of the gate (Column V) expressed in meters/minute.
Exceeding the recommended values may cause damage and malfunction, the manufacturer does not assume any responsibility arising from improper
FSTO/FSTC/TBR/TSMO/TSMC value settings.
The values reported are indicative and referred to a standard installation, the installer must nevertheless ensure compliance with the limits set by the
EN 12453, EN 12445 standards.
15) AUTOSET
For a correct operation of braking it is essential that the stroke is memorised. This can be performed either using the above described AUTO function or
when the first operation is completed (then carried out without interruptions) from SWO to SWC (or viceversa).
The engine starts in SLOW mode to search for SWO, it stops, then reverses still in SLOW manoeuvre to search for SWC (determining the stroke). Then
first FAST manoeuvre from SWC to SWO (ramps, speed, slowdowns determined by the TSMo/TSMc/FSTo/FSTc/SLDo/SLDc parameters set) and se-
cond fast manoeuvre from SWO to SWC.
However, these values can be manually modified at a second time.
If you manually change a parameter that requires a new acquisition, the unit will perform a complete opening and closing manoeuvre, the message
"PRG” will be displayed. At the end the operation will return to normal.
It is not possible to carry out the autoset with logic HTR:ON

28
16) ERROR MESSAGES
Some messages that are displayed in the event of malfunctions are shown hereunder:
err Error N.O inputs (autoset) If the error occurs during self-learning, check the PP/PED/OPEN/CLOSE inputs.
Err1 STOP error (autoset) STOP intervention during the autoset.
Err2 Error, photocells (Autotest) PHOTO/PHOTC intervention during the autoset.
Err4 Error, sensitive edge (autoset) BAR intervention during autoset.
Err5 Error, phototest Check the operation and correct connection of the photocells.
amp
Triggering of the amperometric sensor
An obstacle or a point of friction has caused the triggering of the amperometric sensor. Remove
the obstacle or check the door stroke.
F01 The brake connected absorbs too much.
F02 Short circuit on the engine. Check the impedance of the windings and the insulation between
each phase of the motor and the ground.
F04 At power-on the bus voltage is not within the specifications. Check the supply voltage, or the
correct selection of the engine according to the menu Mot.
F05 Over temperature detected in the unit.
F06 Instantaneous current threshold exceeded. Unlock the engine and check that the pinion is free
to turn. If necessary, contact technical assistance.
F07
Instantaneous current threshold exceeded. Unlock the engine and verify that there are no
excessive loads (difficulty moving) along the entire travel of the gate. If necessary, contact
technical assistance.
F08
Exceeded maximum allowed voltage on the power bus. Check the supply voltage. Cary out the
following actions in the order indicated:
1. Increase TDEC and TSMO/TSMC parameters, check intermediate stops with STOP/PP/PHOT/
BAR commands, if the problem recurs, go to the following point:
2. Increase parameter TBR, check intermediate stops with STOP/PP/PHOT/BAR commands, if
the problem recurs go to the following point:
3. Connect braking resistance, check intermediate stops with STOP/PP/PHOT/BAR commands,
if the problem recurs go to the following point:
4.
Decrease the parameters FSTO/FSTC, check intermediate stops with STOP/PP/PHOT/BAR commands.
F09
The values set are incorrect and the gate goes past the limit switch.
Act by modifying the following parameters in order:
-blo /blc (decrease)
-tsmo / tsmc (increase)
-sldo / sldc (decrease)
-fsto / fstc (decrease)
17) DISPLAY LCD
The LCD display can be turned by 180°.
- Cut off mains power supply
- Press PGM
- While keeping PGM pressed, reset the mains power supply
- Keep PGM pressed (around 5 sec) until the software version appears, turned by 180°.
Normally proceed with programming.
18) DIAGNOSTICS
In the event of operating anomalies the status of all inputs (stop command and safety) can be displayed. One segment of the display is linked to each
input. In the event of failure it switches on according to the following scheme.
PHOTO
SWC
STOP
SWO
PHOTC BAR
P.P. PED
OPEN
CLOSE
LD1 LED: Mains power present.
LD2 LED: PRESENT + 5V
PHOTO: PHOT1/TST1
PHOTC: PHOT2/TST2
F4: Power supply line protection fuse 15AT.

29
19) MAINTENANCE
The following table is used to record maintenance operations, improvement or repair works carried out by the expert engineer.
Date _ _ _ _ _ _ _ _ _ _ _ _ _ _ _ _ _ _ _ _ _ _ _ _ _ _ _ _ _ _ _ _ Engineer's Signature _ _ _ _ _ _ _ _ _ _ _ _ _ _ _ _ _ _ _ _ _ _ _ Stamp
Description of operation
_ _ _ _ _ _ _ _ _ _ _ _ _ _ _ _ _ _ _ _ _ _ _ _ _ _ _ _ _ _ _ _ _ _ _ _ _ _ _ _ _ _ _ _ _ _ _ _ _ _ _ _ _ _ _ _ _ _ _ _ _ _ _ _ _ _ _ _ _ _ _ _ _
_ _ _ _ _ _ _ _ _ _ _ _ _ _ _ _ _ _ _ _ _ _ _ _ _ _ _ _ _ _ _ _ _ _ _ _ _ _ _ _ _ _ _ _ _ _ _ _ _ _ _ _ _ _ _ _ _ _ _ _ _ _ _ _ _ _ _ _ _ _ _ _ _
Date _ _ _ _ _ _ _ _ _ _ _ _ _ _ _ _ _ _ _ _ _ _ _ _ _ _ _ _ _ _ _ _ Engineer's Signature _ _ _ _ _ _ _ _ _ _ _ _ _ _ _ _ _ _ _ _ _ _ _ Stamp
Description of operation
_ _ _ _ _ _ _ _ _ _ _ _ _ _ _ _ _ _ _ _ _ _ _ _ _ _ _ _ _ _ _ _ _ _ _ _ _ _ _ _ _ _ _ _ _ _ _ _ _ _ _ _ _ _ _ _ _ _ _ _ _ _ _ _ _ _ _ _ _ _ _ _ _
_ _ _ _ _ _ _ _ _ _ _ _ _ _ _ _ _ _ _ _ _ _ _ _ _ _ _ _ _ _ _ _ _ _ _ _ _ _ _ _ _ _ _ _ _ _ _ _ _ _ _ _ _ _ _ _ _ _ _ _ _ _ _ _ _ _ _ _ _ _ _ _ _
Date _ _ _ _ _ _ _ _ _ _ _ _ _ _ _ _ _ _ _ _ _ _ _ _ _ _ _ _ _ _ _ _ Engineer's Signature _ _ _ _ _ _ _ _ _ _ _ _ _ _ _ _ _ _ _ _ _ _ _ Stamp
Description of operation
_ _ _ _ _ _ _ _ _ _ _ _ _ _ _ _ _ _ _ _ _ _ _ _ _ _ _ _ _ _ _ _ _ _ _ _ _ _ _ _ _ _ _ _ _ _ _ _ _ _ _ _ _ _ _ _ _ _ _ _ _ _ _ _ _ _ _ _ _ _ _ _ _
_ _ _ _ _ _ _ _ _ _ _ _ _ _ _ _ _ _ _ _ _ _ _ _ _ _ _ _ _ _ _ _ _ _ _ _ _ _ _ _ _ _ _ _ _ _ _ _ _ _ _ _ _ _ _ _ _ _ _ _ _ _ _ _ _ _ _ _ _ _ _ _ _
Date _ _ _ _ _ _ _ _ _ _ _ _ _ _ _ _ _ _ _ _ _ _ _ _ _ _ _ _ _ _ _ _ Engineer's Signature _ _ _ _ _ _ _ _ _ _ _ _ _ _ _ _ _ _ _ _ _ _ _ Stamp
Description of operation
_ _ _ _ _ _ _ _ _ _ _ _ _ _ _ _ _ _ _ _ _ _ _ _ _ _ _ _ _ _ _ _ _ _ _ _ _ _ _ _ _ _ _ _ _ _ _ _ _ _ _ _ _ _ _ _ _ _ _ _ _ _ _ _ _ _ _ _ _ _ _ _ _
_ _ _ _ _ _ _ _ _ _ _ _ _ _ _ _ _ _ _ _ _ _ _ _ _ _ _ _ _ _ _ _ _ _ _ _ _ _ _ _ _ _ _ _ _ _ _ _ _ _ _ _ _ _ _ _ _ _ _ _ _ _ _ _ _ _ _ _ _ _ _ _ _
Date _ _ _ _ _ _ _ _ _ _ _ _ _ _ _ _ _ _ _ _ _ _ _ _ _ _ _ _ _ _ _ _ Engineer's Signature _ _ _ _ _ _ _ _ _ _ _ _ _ _ _ _ _ _ _ _ _ _ _ Stamp
Description of operation
_ _ _ _ _ _ _ _ _ _ _ _ _ _ _ _ _ _ _ _ _ _ _ _ _ _ _ _ _ _ _ _ _ _ _ _ _ _ _ _ _ _ _ _ _ _ _ _ _ _ _ _ _ _ _ _ _ _ _ _ _ _ _ _ _ _ _ _ _ _ _ _ _
_ _ _ _ _ _ _ _ _ _ _ _ _ _ _ _ _ _ _ _ _ _ _ _ _ _ _ _ _ _ _ _ _ _ _ _ _ _ _ _ _ _ _ _ _ _ _ _ _ _ _ _ _ _ _ _ _ _ _ _ _ _ _ _ _ _ _ _ _ _ _ _ _
Date _ _ _ _ _ _ _ _ _ _ _ _ _ _ _ _ _ _ _ _ _ _ _ _ _ _ _ _ _ _ _ _ Engineer's Signature _ _ _ _ _ _ _ _ _ _ _ _ _ _ _ _ _ _ _ _ _ _ _ Stamp
Description of operation
_ _ _ _ _ _ _ _ _ _ _ _ _ _ _ _ _ _ _ _ _ _ _ _ _ _ _ _ _ _ _ _ _ _ _ _ _ _ _ _ _ _ _ _ _ _ _ _ _ _ _ _ _ _ _ _ _ _ _ _ _ _ _ _ _ _ _ _ _ _ _ _ _
_ _ _ _ _ _ _ _ _ _ _ _ _ _ _ _ _ _ _ _ _ _ _ _ _ _ _ _ _ _ _ _ _ _ _ _ _ _ _ _ _ _ _ _ _ _ _ _ _ _ _ _ _ _ _ _ _ _ _ _ _ _ _ _ _ _ _ _ _ _ _ _ _
Date _ _ _ _ _ _ _ _ _ _ _ _ _ _ _ _ _ _ _ _ _ _ _ _ _ _ _ _ _ _ _ _ Engineer's Signature _ _ _ _ _ _ _ _ _ _ _ _ _ _ _ _ _ _ _ _ _ _ _ Stamp
Description of operation
_ _ _ _ _ _ _ _ _ _ _ _ _ _ _ _ _ _ _ _ _ _ _ _ _ _ _ _ _ _ _ _ _ _ _ _ _ _ _ _ _ _ _ _ _ _ _ _ _ _ _ _ _ _ _ _ _ _ _ _ _ _ _ _ _ _ _ _ _ _ _ _ _
_ _ _ _ _ _ _ _ _ _ _ _ _ _ _ _ _ _ _ _ _ _ _ _ _ _ _ _ _ _ _ _ _ _ _ _ _ _ _ _ _ _ _ _ _ _ _ _ _ _ _ _ _ _ _ _ _ _ _ _ _ _ _ _ _ _ _ _ _ _ _ _ _
Date _ _ _ _ _ _ _ _ _ _ _ _ _ _ _ _ _ _ _ _ _ _ _ _ _ _ _ _ _ _ _ _ Engineer's Signature _ _ _ _ _ _ _ _ _ _ _ _ _ _ _ _ _ _ _ _ _ _ _ Stamp
Description of operation
_ _ _ _ _ _ _ _ _ _ _ _ _ _ _ _ _ _ _ _ _ _ _ _ _ _ _ _ _ _ _ _ _ _ _ _ _ _ _ _ _ _ _ _ _ _ _ _ _ _ _ _ _ _ _ _ _ _ _ _ _ _ _ _ _ _ _ _ _ _ _ _ _
_ _ _ _ _ _ _ _ _ _ _ _ _ _ _ _ _ _ _ _ _ _ _ _ _ _ _ _ _ _ _ _ _ _ _ _ _ _ _ _ _ _ _ _ _ _ _ _ _ _ _ _ _ _ _ _ _ _ _ _ _ _ _ _ _ _ _ _ _ _ _ _ _
Date _ _ _ _ _ _ _ _ _ _ _ _ _ _ _ _ _ _ _ _ _ _ _ _ _ _ _ _ _ _ _ _ Engineer's Signature _ _ _ _ _ _ _ _ _ _ _ _ _ _ _ _ _ _ _ _ _ _ _ Stamp
Description of operation
_ _ _ _ _ _ _ _ _ _ _ _ _ _ _ _ _ _ _ _ _ _ _ _ _ _ _ _ _ _ _ _ _ _ _ _ _ _ _ _ _ _ _ _ _ _ _ _ _ _ _ _ _ _ _ _ _ _ _ _ _ _ _ _ _ _ _ _ _ _ _ _ _
_ _ _ _ _ _ _ _ _ _ _ _ _ _ _ _ _ _ _ _ _ _ _ _ _ _ _ _ _ _ _ _ _ _ _ _ _ _ _ _ _ _ _ _ _ _ _ _ _ _ _ _ _ _ _ _ _ _ _ _ _ _ _ _ _ _ _ _ _ _ _ _ _

71
BULL
User’s handbook
Safety measures
• Do not stand within the gate movement area.
• Children must not play with controls and near the gate.
• In the event of malfunctions, do not attempt to repair the failure but contact the specialised personnel.
Manual and emergency manoeuvre
In the event of power failure or malfunction, to manually operate the gate proceed as follows:
• After inserting the customized key C, turn it anti-clockwise and pull the lever L.
• The geared motor is unlocked and the gate can be moved by hand.
• T
o return to the normal operating mode, close the lever L again and manually activate the gate until it is geared.
Maintenance
• Every month check the good operation of the emergency manual release.
• It is mandatory not to carry out extraordinary maintenance or repairs as accidents may be caused.These
operations must be carried out by qualified personnel only.
• The operator is maintenance free but it is necessary to check periodically if the safety devices and the other
components of the automation system work properly. Wear and tear of some components could cause dan-
gers.
Waste disposal
If the product must be dismantled, it must be disposed according to regulations in force regarding the differenti-
ated waste disposal and the recycling of components (metals, plastics, electric cables, etc..). For this operation
it is advisable to call your installer or a specialised company.
Warning
All Benincá products are covered by insurance policy for any possible damages to objects and persons caused
by construction faults under condition that the entire system be marked CE and only Benincá parts be used.
CL

76
11
12
1
8
9
3
2
7
6
4
10
13
15
5
14
16
Ref. BULL 17 OMI
230 V Code
BULL 17 OMAI
115 V Code Note
1
9688344 9688349
2
9688348 9688348
3
9688319 9688319
4
9686337 9686337
5
9686694 9686694
6
9686032 9686032
7
9686335 9686335
8
9688317 9688317
9
9688270 9688270
10
9688102 9688102 BULL_S
11
9686329 9686329
12
9688335 9688335
13
9688336 9688336
14
9688318 9688318
15
9686094 9686094
16
9688350 - -
This manual suits for next models
2
Table of contents
Other Rotech Gate Opener manuals
Popular Gate Opener manuals by other brands
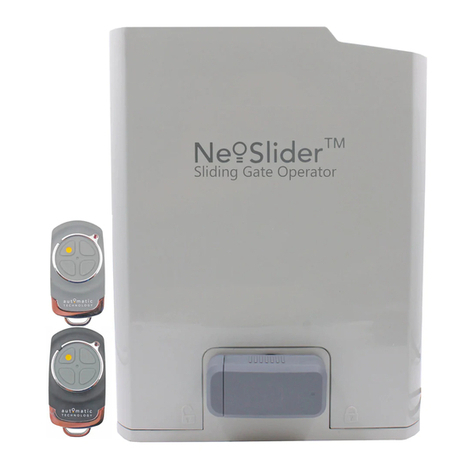
Automatic Technology
Automatic Technology NeoSlider NES-500 manual
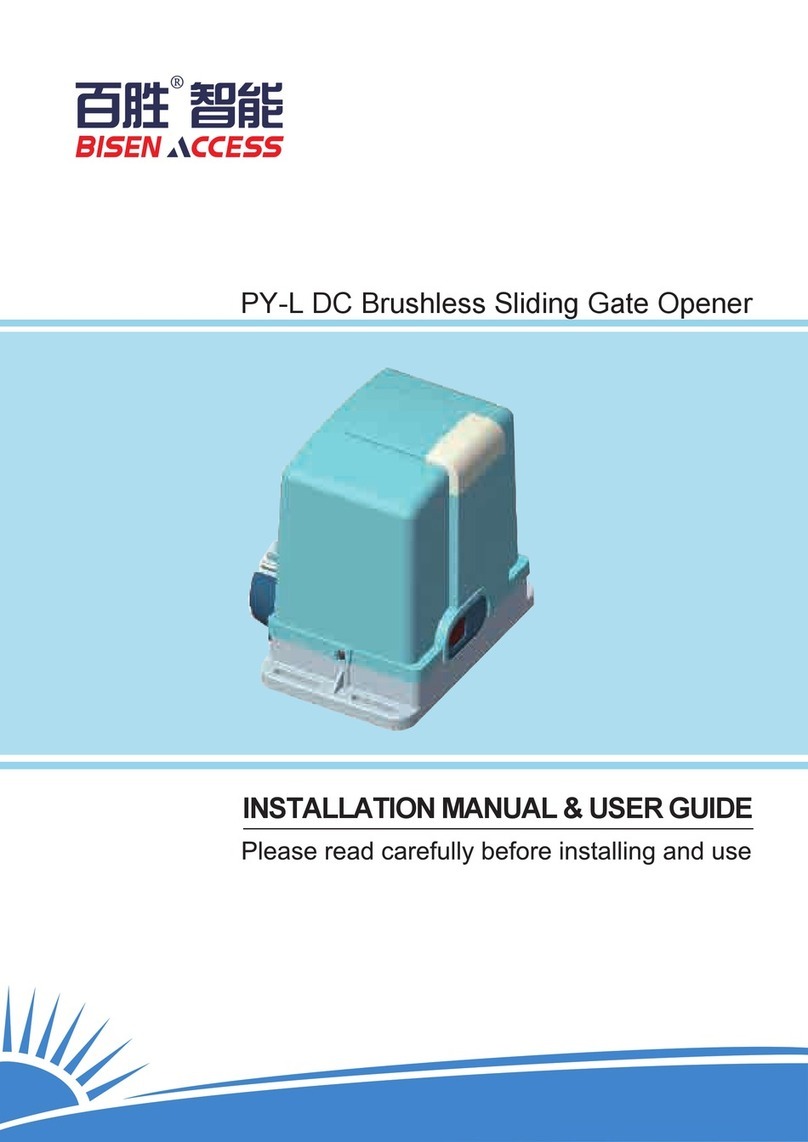
BISEN
BISEN PY-L Installation manual & users guide
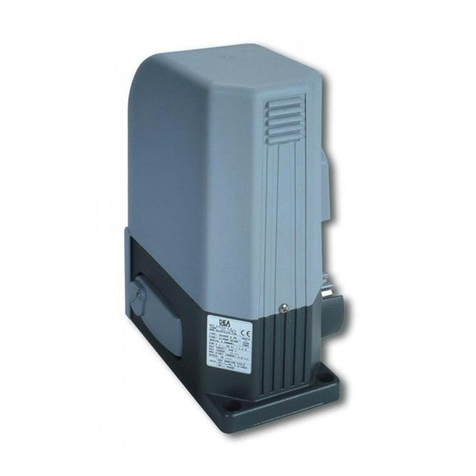
Dea
Dea LIVI 403E Operating instructions and warnings
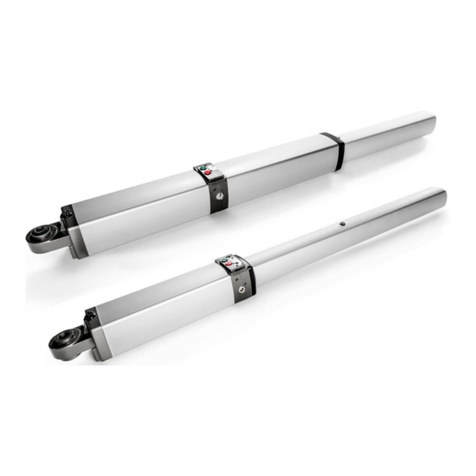
HYDOM
HYDOM 3LC33 250A3A Series installation manual
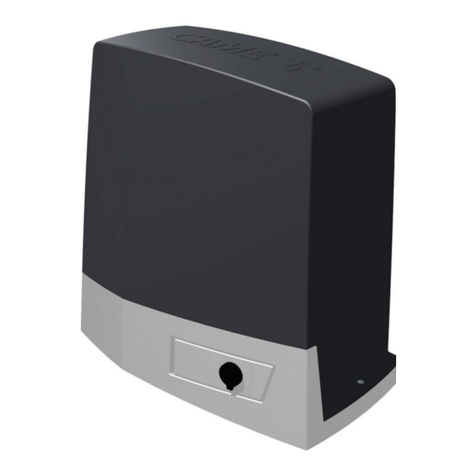
CAME
CAME BKV15AGE installation manual

Dea
Dea ANGOLO Operating instructions and warnings