Servomex SERVOPRO k2001 User manual

Part Number: 02001001A
Revision: 3
Language: UK English
User Manual
SERVOPRO Plasma (k2001)
Trace N2Analyser
PROCESS ANALYSERS

This page intentionally blank

Copyright 2010
TABLE OF CONTENTS
1.0 CONCERNING THIS MANUAL..........................................................................................................................2
2.0 CAUTIONS AND WARNINGS............................................................................................................................3
2.1
Symbols description...................................................................................................................................3
2.2
Caution ......................................................................................................................................................3
2.3
Electrical shock hazard..............................................................................................................................3
2.4
Possible explosion hazard..........................................................................................................................3
2.5
General precautions for handling and storing high pressure cylinders.......................................................5
2.6
Gas hazard .................................................................................................................................................5
2.7
General safety instructions.........................................................................................................................6
4.0 SPECIFICATIONS ................................................................................................................................................8
5.0 DESCRIPTION....................................................................................................................................................10
5.1
General description..................................................................................................................................10
5.2
Sampling..................................................................................................................................................10
5.3
Power supply ...........................................................................................................................................10
5.4
Analysis section.......................................................................................................................................12
5.5
Electronics...............................................................................................................................................13
5.6 Description of controls and I/O ports............................................................................................................14
6.0 INSTALLATION.................................................................................................................................................15
6.1
Electrical..................................................................................................................................................15
6.2
Gas circuit................................................................................................................................................15
6.3
Analyzer cabinet installation....................................................................................................................16
7.0 OPERATION .......................................................................................................................................................26
7.1
Configuration...........................................................................................................................................26
7.2
Calibration...............................................................................................................................................27
7.2.1. Important facts concerning calibration...............................................................................................29
7.3
Diagnosis.................................................................................................................................................30
7.3.1 Error and Alarm Historic......................................................................................................................32
7.3.2 Ethernet info.........................................................................................................................................33
7.3.3 Serial number .......................................................................................................................................33
7.4
Run ..........................................................................................................................................................33
7.5
Special consideration about the 0 - 1 ppm range .....................................................................................35
7.6
Hidden Menu...........................................................................................................................................35
7.6.1 Starting Count ......................................................................................................................................35
7.6.2 Temperature Coefficient.......................................................................................................................36
7.6.3 Time and date setting ...........................................................................................................................38
7.6.4 System Gain .........................................................................................................................................39
7.6.5 PID values............................................................................................................................................40
7.6.6 Lock Range ..........................................................................................................................................40
7.6.7 Ethernet configuration 1.......................................................................................................................41
7.6.8 Ethernet configuration 2.......................................................................................................................42
7.6.9 Averaging Number...............................................................................................................................43
7.6.10 Calibration done parameters...............................................................................................................44
7.7
SERVOPRO PLASMA web interface.....................................................................................................44
8.0 START-UP...........................................................................................................................................................49
8.1
Routine and operational verification........................................................................................................50
8.2
Hints and tips...........................................................................................................................................50
9.0 MAINTENANCE AND TROUBLE SHOOTING...............................................................................................52
9.1
Maintenance.............................................................................................................................................52
9.2
Trouble-shooting .....................................................................................................................................52
9.3
Problem causes........................................................................................................................................53
APPENDIX 1 / HARDWARE AND TECHNIQUE...................................................................................................54
APPENDIX 2 / ANALOGUE AND DIGITAL OUTPUTS........................................................................................63

User Manual SERVOPRO Plasma Trace N2Analyser
APPENDIX 4 / RS-232C ............................................................................................................................................70
APPENDIX 5 / WEEE................................................................................................................................................74
Product disposal in accordance with the Waste Electrical and Electronic Equipment (WEEE) Directive 2002/96/EC75
APPENDIX 6 / APPLICATION NOTES ...................................................................................................................76
SAMPLING LINE SIZE, (AN-01)..............................................................................................................................77
THE IMPORTANCE OF REGULATOR PURGING, (AN-01).................................................................................79
LEAK FINDING PROCEDURE (AN-05)..................................................................................................................80
APPENDIX 7 / AUTO-CALIBRATION OPTION ....................................................................................................85
AUTOMATIC CALIBRATION OPTION..................................................................................................................86
1) Gas Circuit Description .................................................................................................................................86
2) System Operation...........................................................................................................................................86
2.1 Entering Zero and span gas values..........................................................................................................87
2.2 Manual Calibration..................................................................................................................................88
2.3 Automatic Calibration Mode...................................................................................................................89
APPENDIX 8 / TRACE NITROGEN IN HELIUM VERSION.................................................................................93
APPENDIX 9 / DUAL BACKGROUND ANALYZERS...........................................................................................95
APPENDIX 10/ COMPLIANCE AND STANDARDS INFORMATION………………………………………….100

User Manual SERVOPRO Plasma Trace N2Analyzer
1.0 CONCERNING THIS MANUAL 2
1.0 CONCERNING THIS MANUAL
This analyzer was designed for simple use, according to the "Plug and play" principle and so was
this manual. For the benefits of clarity, all electronics, software and physical details not necessary
for the operation of the unit are omitted. It is the way we want it.
We understand that you want to put your new analyzer to use as soon as possible. To achieve this
goal, take the time to read all this manual in its entirety. Every section is based on the
assumption that you have read and understood the preceding one, and every section has important
comments for the user. This analyzer is very simple to install and to use; also, it is maintenance-
free. No special technical knowledge is required to operate the unit.
We hope that you will enjoy working with the SERVOPRO PLASMA Trace Nitrogen Analyzer.
In the spirit of progress and continuous improvement, we would appreciate any comments you
may have, negative or positive - as long they are constructive.
Servomex believes that the information in this manual is accurate. The document has been
carefully reviewed for technical accuracy. If there should be any error, Servomex reserves the
right to make changes to subsequent editions of this document without prior notice to holders of
this edition. The reader should contact Servomex if errors are suspected. In no event shall
Servomex be liable for any damages arising out of or related to this document or the information
contained in it.

User Manual SERVOPRO Plasma Trace N2Analyzer
2.0 CAUTIONS AND WARNINGS 3
2.0 CAUTIONS AND WARNINGS
2.1 Symbols description
2.2 Caution
Improper installation, operation or service of this analyzer may cause damage to the analyzer and
void the manufacturer’s warranty.
2.3 Electrical shock hazard
Do not operate unless the cabinet is securely closed. Servicing this instrument
implies possible exposure to shock hazard level voltages which can cause
death or serious injury.
For both safety and proper performance, this instrument must be connected to a properly
grounded three-wire source of electrical power.
Both alarm switching relay contacts and digital output contacts wired to a separate power source
must be disconnected before servicing.
Tampering or unauthorized substitution of components may adversely affect the safety of this
product. Use only factory-approved components for repair.
2.4 Possible explosion hazard
Never introduce other gases than argon in this analyzer. If explosive,
flammable or corrosive gases or mixtures are allowed to flow in the analyzer,
fire or explosion may result. This analyzer is not designed to be used in
hazardous areas.

User Manual SERVOPRO Plasma Trace N2Analyzer
2.0 CAUTIONS AND WARNINGS 4
This analyzer must be installed in laboratory environments: moisture- and vibration-free, with
stable temperatures.

User Manual SERVOPRO Plasma Trace N2Analyzer
2.0 CAUTIONS AND WARNINGS 5
2.5 General precautions for handling and storing high pressure cylinders
This analyzer is frequently applied to verify the contents of high-pressure cylinder gases.
Mishandling of gas cylinders could result in death, serious injury or property damages. Handle
gas cylinders with extreme care. Refer to general precautions for handling and storing high-
pressure cylinders. Here are some precautions from the COMPRESSED GAS ASSOCIATION'S
HANDBOOK.
1.
Never drop cylinders or permit them to strike each other violently.
2. Cylinders may be stored in the open, but in such cases, should be protected against extreme
weather. To prevent rusting, keep away from the dampness of the ground.
3.
The valve protection cap should be left on each cylinder until it has been secured against a
wall or a bench, or placed in a cylinder stand until it is ready to be used.
4. Avoid dragging, rolling, or sliding cylinders, even for a short distance; they should be moved
by using a suitable hand-truck.
5. Never tamper with safety devices in valves or cylinders.
6. Do not store full and empty cylinders together. Serious suck back can occur when an empty
cylinder is attached to a pressurized system.
7. No part of a cylinder should be subjected to a temperature higher than 125
o
F (52
o
C). A
flame should never be permitted to come in contact with any part of a compressed gas
cylinder.
8. Do not place cylinders where they may become part of an electric circuit. When electric arc
welding, precautions must be taken to prevent striking an arc against the cylinder.
Edited from selected paragraphs of the Compressed Gas Association's
"Handbook of Compressed Gases" published in 1981.
Compressed Gas Association
1235 Jefferson Davis Highway
Arlington, Virginia 22202
2.6 Gas hazard
Argon and helium are member of the rare gas family which consist of helium, argon, krypton,
xenon or neon.
All of these gases are monoatomic and are characterized by their extreme chemical inactivity.
They are colorless, odorless, tasteless and NON TOXIC.
However, these gases can act as a simple asphyxiate by displacing the necessary amount of
oxygen to support life. Proper ventilation must be done to provide safe area.

User Manual SERVOPRO Plasma Trace N2Analyzer
2.0 CAUTIONS AND WARNINGS 6
The nitrogen is a diatomic molecule and is colorless, odorless and non toxic. However, nitrogen
can also act as a simple asphyxiate by displacing the necessary amount of oxygen to support life.
Proper ventilation must be done to provide safe area.
2.7 General safety instructions
To avoid the risk of electric shock, do not remove the casing or open the back. There are no user
serviceable parts inside. Leave servicing to the experts!
To prevent fire or the risk of electric shock, keep this unit out of the rain and away from
moisture. The lightning symbol inside an equilateral triangle means that there are live,
uninsulated parts inside this unit that may give you a dangerous electric shock if touched.
1. Instructions: Read all the safety instructions and all the operation instructions thoroughly
before using the unit for the first time. Keep these safety instructions and operating
instructions somewhere safe in case you need to refer to them again in the future.
2. Safety warnings: In your own interest pay heed to all the safety warnings on the unit and in
the operating instructions. Follow the instructions on operation and use of the unit in every
respect.
3. Water and moisture: Never use the unit near water, for example near a bath, a wash basin, a
sink a washing machine, in a damp cellar or near a swimming pool.
4. Ventilation: Wherever you put the unit, always ensure there is sufficient ventilation. Never
put the unit on a bed, for example, or a sofa. a carpet or similar surface that might block the
vents. Make sure there is proper ventilation to avoid overheating.
5. Effects of heat: Do not put the unit anywhere near sources of heat, such as radiators, hot-air
shafts, ovens, etc.
6. Power source: Connect the unit only to the power source indicated on the operating
instructions or on the unit.
7. Protecting the power cord: Run the power cord so that no one can step on it and nothing can
rest on or against it. The power cord is particularly at risk in the area of the plug, the socket
and where it comes out of the unit.
8. Cleaning: Follow the manufacturer’s recommendations for cleaning the unit.
9. Unit not in use: If you are not going to use the unit for some time, remove the plug from the
socket.
10. Foreign bodies: Take great care to ensure that no liquids or other foreign bodies can find
their way inside the unit through the openings in the casing.
11. Repair in the event of damage: The unit should only be repaired by qualified personnel.
Never try to do more in the way of maintenance to your unit than the operating instructions
allow. Beyond that, always consult an expert for repair work.

User Manual SERVOPRO Plasma Trace N2Analyzer
3.0 WARRANTY, SERVICE POLICY, REPAIR SERVICES 7
RETURNING A PRODUCT FOR REPAIR
Upon determining that repair services are required, the customer must :
1. Obtain an RMA (Return Material Authorization) number.
2. Supply a purchase order number or other acceptable information.
3. Include a list of problems encountered along with your name, address and telephone, and
RMA number.
4. Ship the analyzer in its original packaging or equivalent. Failure to properly
package the analyzer will automatically void the warranty.
5. Every gas connection must be capped with appropriate metal caps. Failure to do so
will automatically void the warranty.
6. Write RMA number on the outside of the box.
7. Use a Servomex approved carrier. The delivery must be sent to the regional Servomex
Repair Centre. Servomex will not accept airport to airport delivery.
8. Servomex will not cover transport fees.
Other conditions and limitations may apply to international shipments.
NOTE: Seller applies to SERVOMEX and/or authorized distributors.
PROPRIETARY RIGHTS
Buyer agrees that any Servomex software, firmware and hardware products ordered or included
in the goods ordered are proprietary of Servomex. No change, modification, defacement,
alteration, reverse engineering, software decompilations nor reproduction of such software or
hardware products, or disclosures of programming content to other parties is authorized without
the express written consent of Servomex.
To maintain Servomex trade secret and other proprietary protection of such software and
firmware, such items are not sold hereunder but are licensed to buyer.
Servomex reserves the right to interrupt all business relationship and warranty or service if there
is any tentative from any customers to reverse engineering any of Servomex products or to
tamper with any sealed module.
Trademarks and product identification as Servomex are the property of Servomex and shall be
used only in connection with Servomex products. No third party could remove or deface any
model number or marks.

User Manual SERVOPRO Plasma Trace N2Analyzer
(1) The accuracy may be decreased by an additional 4% full scale at some frequencies under the influence of
radiated RF fields specified for industrial environments.
(2) The analyzer is supplied configured for operation with one of these voltage ranges. You must specify the voltage
range when you order the analyzer.
4.0 SPECIFICATIONS 8
4.0 SPECIFICATIONS
Detector type: Plasma Emission Detector (PED).
Material: Quartz, single element, vacuum tight to 69 kPa (10
Psig)
Range: X1: 0 – 1 ppm display resolution to 10 ppb
X10: 0 – 10 ppm display resolution to .1 ppm
X100: 0 – 100 ppm display resolution to 1 ppm
Accuracy: ±1% full scale
(1)
Drift: ±1% over 24 hours
Noise: ≤2 ppb
Sample flow requirements: 25 ml min
-1
to 150 ml min
-1
Recommended calibration
gas:
for 0 – 1 ppm range:
for 0-10, 0-100 ppm range:
- Zero: purified gas with a heated purifier (ex: GP-200)
- Span: 0.7 to 0.9 ppm
- 20 % for zero and 80% of full scale you will be using.
Flow accuracy: 0 to 200 ml min
-1
±1% full scale
Operating pressure: Sample pressure: 27.6 to 55.2 kPa gauge (max)
(5 to 10 Psig(max))
Operating temperature: +5°C to +40°C
Sample and vent connections: 1/8’’ Swagelok tube fittings
Supply: Electrical Supply:
Voltage: 100 to 120 Vac or 220 to 240 Vac
(2)
Frequency: 50 to 60 Hz
Maximum power consumption:
Power: 45 W
Fuses: Two fuses 1 amp / 250 V, Littelfuse type “F”, fact-acting
miniature fuses 5 x 20 mm
Response time: - X10 and X100: 20 sec. for 90% of a step change at
75 ml min
-1
- X1: 40 sec. for 90% of a step change 75 ml min
-1
Dimensions (Height x width x
Depth): 133 mm x 483 mm x 457 mm (5.25 ins x 19 ins x 18 ins)
Weight: 15 kg (33 lbs)
Operating altitude: 2000 m (max)
Operating ambient humidity
range: 0 to 95% RH non-condensing
Ingress protection: IP20

User Manual SERVOPRO Plasma Trace N2Analyzer
4.0 SPECIFICATIONS
9
•Fully microprocessor-controlled, with 4 x 40 LCD display
•Self-diagnostic system software
•Auto-zero, auto-span calibration system (optional).
Provides maintenance-free system
•Digital output:
4 digital outputs: 3 are for range indication and1 for system status monitoring
Relay contact rating: 30 Vrms, 42.4 V peak or 60 Vdc
•Alarm output:
2 digital outputs for a specified value chosen by the user
Relay contact rating: 30 Vrms, 42.4 V peak or 60 Vdc
•4-20 mA isolated output
Maximum load impedance: 600 Ωat 20 mA DC
Isolation: 750 VDC or AC peak maximum
•Serial port: RS-232 (optional)
•Custom options: contact factory
•CE and Y2000 compliant
•CSA approval on demand
-The analyzer is rated in accordance to Over Voltage Category II, Pollution Degree 2
-Ingress protection: IP20.
The SERVOPRO PLASMA analyzer is only suitable to measure nitrogen in helium and argon.

User Manual SERVOPRO Plasma Trace N2Analyzer
5.0 DESCRIPTION 10
5.0 DESCRIPTION
5.1 General description
The SERVOPRO PLASMA Trace Nitrogen in argon Analyzer is an instrument for measuring 0
to 100 ppm nitrogen in argon. This analyzer is designed to work with pure gas. Avoid
introduction of air into the sampling system. If this happens, let clean gas flow in it: the unit will
recover and normally will not require recalibration. The overall functions of the analyzer are
controlled by the microprocessor boards. Different functions are accessed by selecting the proper
menu items on the display with the help of the membrane keypad.
PLEASE READ THE ENTIRE MANUAL BEFORE OPERATING THE ANALYZER.
You will find important comments in all sections of this manual.
5.2 Sampling
The argon sample is introduced through a 1/8" tube Swagelok fitting at the rear of the cabinet.
The sample is directed to a particle filter and goes through a thermofluidic flow control valve.
From there, the argon sample gas is introduced into the plasma cell. The sample coming out from
the cell passes through an electronic mass flow transducer before it is vented into the atmosphere.
The mass flow transducer gives flow information to the microprocessor system. This information
is used to control the intensity of signal to be sent to the thermofluidic flow control valve. The
microprocessor executes a P.I.D. algorithm (proportional - integral - derivative) to maintain the
flow at the set point value. Never block the vent, or permanent damage will result to flow
transducer. Leave vent at atmospheric pressure.
5.3 Power supply
The utility power supply must be stable and transient-free for a reliable operation of the analyzer.
The system has two fuses.
The analyzer has one power supply module delivering D.C. regulated voltage to the signal
conditioning module, the microprocessor system display and the flow control module. If you
have a built-in option, the power supply module may also be connected to it, depending on the
option installed.

User Manual SERVOPRO Plasma Trace N2Analyzer
5.0 DESCRIPTION 11

User Manual SERVOPRO Plasma Trace N2Analyzer
5.0 DESCRIPTION 12
5.4 Analysis section
The sample gas, which at atmospheric pressure, flows through a proprietary design; a pure quartz
cell is submitted to a high-frequency, high-intensity electromagnetic field.
The SERVOPRO PLASMA Analyzer is based on a spectroscopic emission cell, which in itself is
not a new technique. On the other hand, the characteristics which make this system stable and
selective are the frequency, the intensity, the regulation, as well as the coupling technique and
focusing (stabilizing) electrodes used to keep the plasma stable.
Under these conditions, the plasma becomes the center of a luminous phenomenon
(electroluminescence). In fact, the plasma is electromagnetically induced. Plasma is a collection
of charged particles; In this case, the plasma consists of a stream of sample gas. This process
being an emission technique, it is very useful for quantitative analysis. This is not a new
technique. These recent advances make the development of new instruments based on plasma
technology easier; this without the cost normally associated with this category of analytical
instruments.
Once the sample gas is ionized (charged), many spectral lines are emitted.
Here, we think a few words regarding the technique used to create the plasma are necessary.
There are many ways of producing light from a gas stream for analytical purposes. The
electroluminescence phenomenon includes luminescence from all kinds of electrical discharges,
such as sparks, arcs or tubes of different kinds, operating on direct or alternating current of low
or high frequency. Recently, some experiments were conducted in the microwave range by
surface-wave-induced plasma.
Excitation, in these cases, results mostly from electron or ion collisions; that is, the kinetic
energy of electrons or ions accelerated in an electric field in which the atoms or molecules of a
gas are subjected that causes the emission of light.
By any of the above mentioned methods, a characteristic emission spectra can be obtained for the
plasma gas and each substance in it. The emission usually varies for a given substance,
depending on the mode of excitation.
We developed our plasma generator and plasma cell in such a way as to minimize the heat
generation inside the cell to get a clear spectral line for the substance of interest, i.e. nitrogen.
Once the intense line is identified, we must use a system to filter it out. In our case, instead of
using a defraction grating, prism or tunable filter, we use an custom made optical filter with a
special coating that lessens background noise considerably and reduces spectral interference.
This filter shows an exceptional blocking range. The filter's main characteristic is its great
stability: temperature and humidity and time will not affect its performance. The filter is coupled
with a special lens that focuses the optical beam.

User Manual SERVOPRO Plasma Trace N2Analyzer
5.0 DESCRIPTION 13
The resulting light is directed to a special photodiode, where an electrical current is generated.
This current is proportional to the nitrogen level in the argon stream.
By regulating the power of the plasma and having close control of plasma position with the
focusing electrodes; we can optimize the sensitivity for a particular spectral ray.
5.5 Electronics
The current from the photodiode is directed to a low bias current switched integrator, followed by
a precision floating-point programmable gain amplifier, and ending with an analog to digital
converter. This data is read by the microprocessor circuit, where a digital signal processing
algorithm is executed to determine the equivalent parts per million value.
The microprocessor board converts this value back into an analog one; then an optional
4-20 mA isolator transmits it to a remote PLC, computer or recorder.
The microprocessor board also manages operator interventions and validates data input from the
keypad. The data is displayed on a LCD of 4 lines x 40 characters. Also, the microprocessor
board controls flow with a P.I.D. algorithm.
The microprocessor board uses a multitasking kernel to control the operation of the analyzer.
On option, the analyzer may be equipped with digital output, for remote range indication. Also, a
serial port may be installed with the appropriate protocol for remote data transmission.

User Manual SERVOPRO Plasma Trace N2Analyzer
5.0 DESCRIPTION 14
5.6 Description of controls and I/O ports
Key Description
1. Keypad
2. LCD display
3. Power inlet
4. Gas connections
5. Ethernet port
6. RS-232 port
7. IO Connector
1
2
3
4
5
6
7

User Manual SERVOPRO Plasma Trace N2Analyzer
6.0 INSTALLATION 15
6.0 INSTALLATION
6.1 Electrical
Connect the line cord to the proper line voltage according to the model you have
(i.e. Voltage: 100 to 120 Vac or 220 to 240 Vac; Frequency: 50 to 60 Hz).
For optimum unit performance this voltage must be stable, transient-free and have a stable
frequency. Also, the unit must be properly grounded.
Check the earth (ground) continuity between your electrical supply outlet earth (ground) and the
functional earth (ground) terminal on the rear of the analyzer.
6.2 Gas circuit
For all gas line connections (including calibration gas and sample gas), we recommend the use of
1/8" stainless steel tubing in full length, with no fittings. You must avoid pipe thread
connections: they are usually sealed with Teflon tape and some particles can get into the lines. By
using compression-type tube fittings, the venturi aspiration of outside contaminants is virtually
eliminated.
If you suspect occasional contamination with air, it is a good idea to install a small molecular
sieve trap (50 cc to 100 cc) at the sample inlet. This minimizes pollution with moisture. Moisture
or air will not damage the cell, but will give noise and instability. Again, this analyzer is designed
to operate with clean gas.
Tube quality is often overlooked. For a 1/8" O.D. tube, use a minimum wall thickness of .028".
The tube must be purchased to meet ASTM69 specifications. Inferior quality tubes may have
irregularities on their circumference, causing inadequate sealing with compression tube fittings.
Install a by-pass rotometer on your sample line. Install the rotometer near the analyzer and close
to the stream selection valve. This increases gas velocity and allows a faster purging of the
sample line, before selection. You will also get a faster response time this way. Also adjust your
sample line pressure to a value which will bring proper flow into the system: higher sample line
pressure results in longer response time.
All lines must be cleaned and purged to remove any trace of moisture or particles. Particles can
damage your stream selection valves. Also, particles in the inlet filter will trap moisture.
After all these precautions are taken, the pressure regulator on the calibration cylinder must also
have a S.S. diaphragm and compression tube fitting on the low pressure side, and CGA fitting on
the high pressure side. A regulator with discharge pressure adjustable from 0 to 207 kPa (30 PSI)
is recommended. Apply equal pressure for the zero, the span gas, and the sample gas.

User Manual SERVOPRO Plasma Trace N2Analyzer
6.0 INSTALLATION 16
Regulator purging is critical. When you connect the regulator to a cylinder, it is full of air (790
000 ppm of N
2
). If you open the valve on the cylinder and leave it open even for a short period of
time, the air inside the regulator will diffuse into the cylinder. It is impossible to know exactly
how much nitrogen you may have in your cylinder. Naturally, because this cylinder has no more
correspondence to its analyzed certificate, it must not be used as a reference.
Very often (too often!!), problems related to this type of analyzer (and this applies also for trace
oxygen analyzers) occur from an inefficient purge of the pressure regulator, resulting in a bad
calibration gas. Regulator purging is an operation that is not always given the attention it
deserves when using calibration gases.
The end user should understand that what happens to the gas between the cylinder and its end use
is controlled by the quality of connecting lines and the efficiency of the purging procedures.
Please refer to appendix 1 for more details about sampling system and regulator purging.
This is what we recommend and this is what we approve. Our performances are
guaranteed if installation is done as per drawing CAI-4003. Nothing else will be better
than this.
The vent of the analyzer must be at atmospheric pressure. If you suspect vent blocking, install a
back-pressure regulator or a relief valve with a pressure setting of 7 kPa (1 PSI). This will
prevent over pressurization of the system. Remember, the analyzer will perform better if the vent
is working at atmospheric pressure. You may use 1/8" S.S. tubing for a length of 10 feet. At this
point use 1/4" - or bigger - tubing to vent the analyzer.
6.3 Analyzer cabinet installation
This unit is designed for a rack mounted cabinet. If you install it in a different type of cabinet
without side support bracket,
you must install a metal bracket to support the rear
side of the cabinet.
Like every analytical equipment, it must be installed properly. The unit should not be installed in
direct sunlight and exposed to any vibrations. The ideal room temperature is around 25
o
C and,
most important of all, the temperature must be stable; it is essential to avoid excessive excursion
in temperature swings.
Never install the analyzer in an area where a strong electromagnetic field is present. Never use
radio transmitters near the analyzer. Also, it is a good idea to eliminate fluorescent lights near
sensitive electronic circuits.

User Manual SERVOPRO Plasma Trace N2Analyzer
6.0 INSTALLATION 17
1. TO AVOID DAMAGE TO ANALYZER, ALWAYS LEAVE THE
PROTECTION CAPS ON GAS CONNECTIONS UNTIL CLEAN GAS
IS READY TO FLOW IN THE ANALYSER.
2. THE VENT CONNECTION OF THE ANALYZER MUST BE AT
ATMOSPHERIC PRESSURE ALL THE TIME. PRESSURIZING
THE VENT SIDE OF ANALYZER COULD CAUSE THE QUARTZ
CELL TO CRACK AND ALSO DAMAGE THE FLOW MODULE.
FOR EXAMPLE, IF YOU HAVE TO CHECK YOUR SAMPLE LINES
FOR LEAKS, DON’T DO IT WITH THE ANALYZER CONNECTED
TO SAMPLE LINE WHILE THE VENT PROTECTION CAP IS STILL
INSTALLED. SO PLEASE DO YOUR LEAK TEST AND CONNECT
YOUR SAMPLE LINE TO SAMPLE INLET ONLY AFTER ALL
LEAK TESTS ARE DONE. ANY FAILURE TO FOLLOW THESE
RECOMMENDATIONS WILL VOID THE WARRANTY.
3. THE ANALYZER CABINET IS NOT DESIGNED TO BE
SUPPORTED BY FRONT PANEL ONLY. A BRACKET
SUPPORTING THE REAR OF THE ANALYZER CABINET MUST
BE INSTALLED. SEE USER MANUAL FOR DRAWING OF SUCH
INSTALLATION.
Table of contents
Other Servomex Analytical Instrument manuals
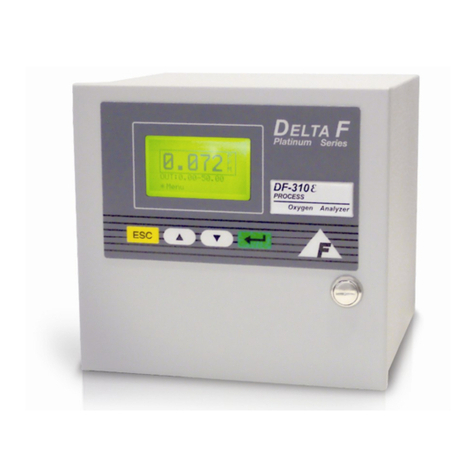
Servomex
Servomex DF-310E User manual
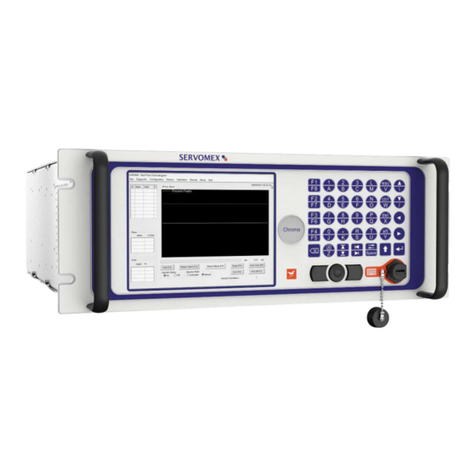
Servomex
Servomex SERVOPRO Chroma User manual
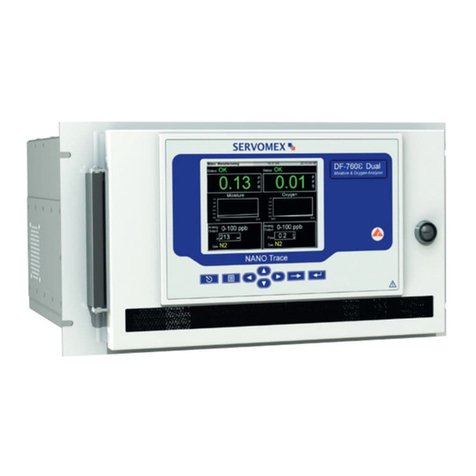
Servomex
Servomex NanoTrace DF-760E User manual
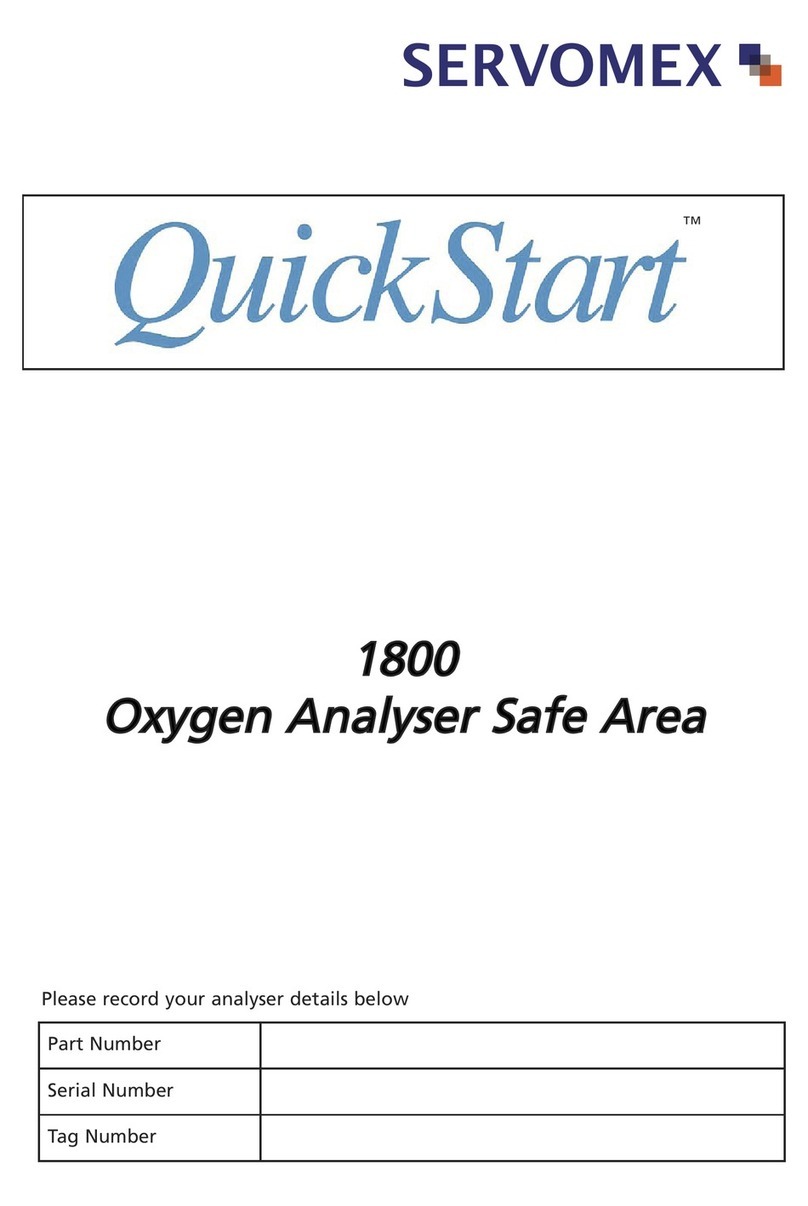
Servomex
Servomex xendos 1800 Series User manual
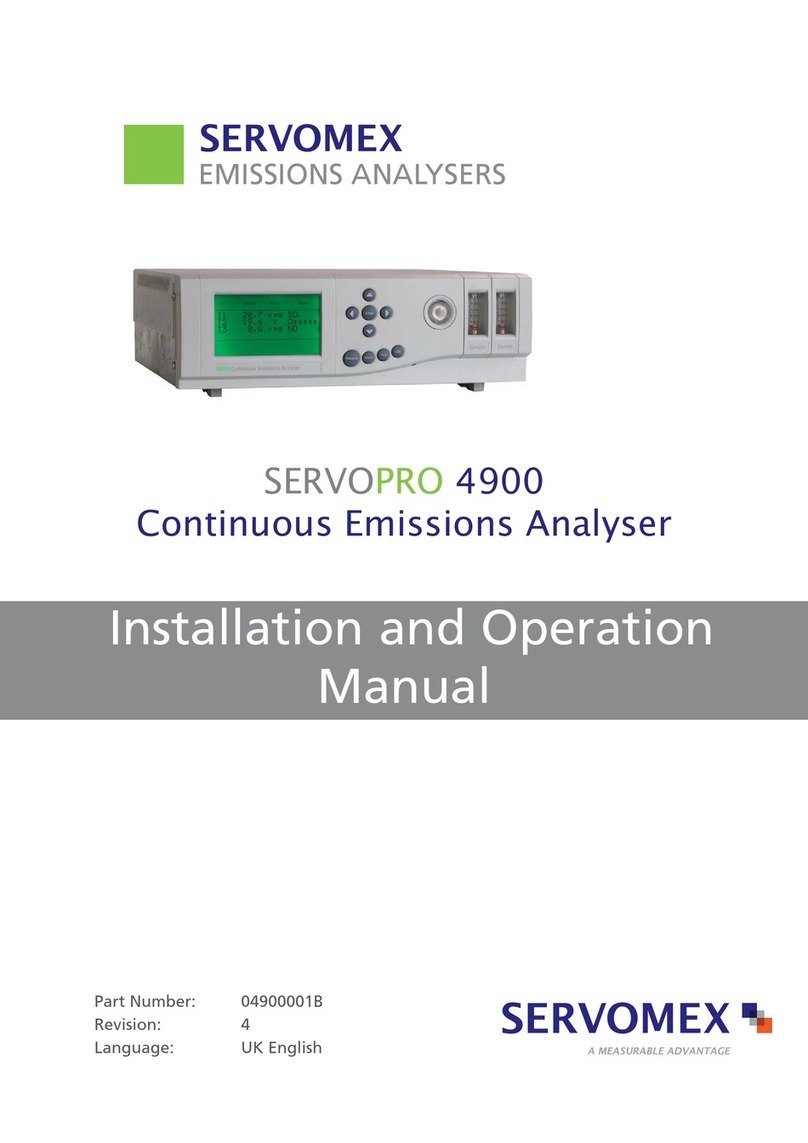
Servomex
Servomex SERVOPRO 4900 User manual
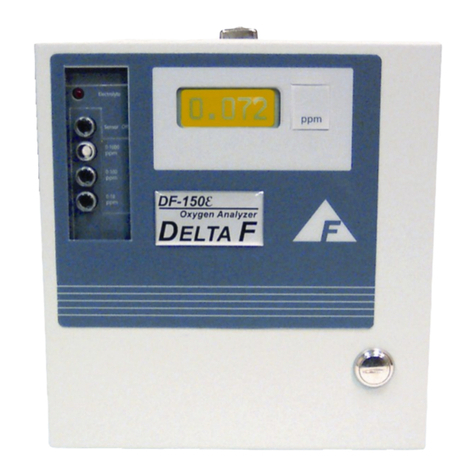
Servomex
Servomex DF-150E User manual
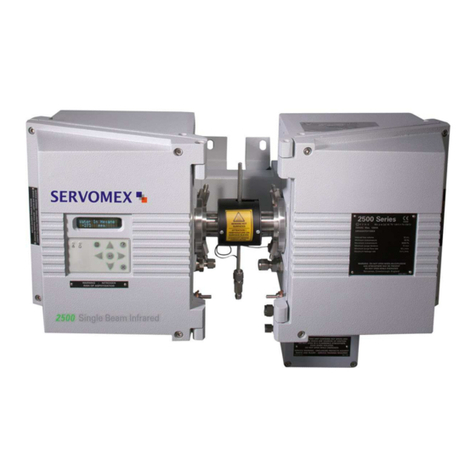
Servomex
Servomex SERVOTOUGH SpectraExact 2500 Instruction manual

Servomex
Servomex 700B User manual
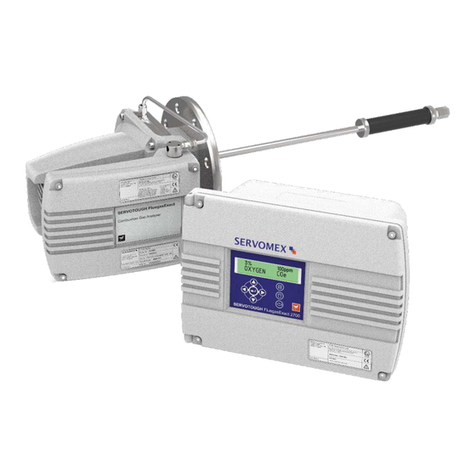
Servomex
Servomex 2700 User manual