ST ACEPACK DMT-32 User guide

Introduction
ACEPACK DMT-32 is an advanced power module designed to integrate power devices with different nature. Making use of
power module simplifies the design and increase reliability while optimizing PCB size and system costs.
This mounting instructions paper gives the main recommendations to appropriately handle, assemble and rework the ACEPACK
DMT-32 power module. It is necessary to follow some basic assembly rules either to limit thermal and mechanical stresses or
assure the best thermal conduction and electrical insulation.
Mounting instruction for STPOWER module ACEPACK DMT-32
TN1393
Technical note
TN1393 - Rev 2 - August 2023
For further information contact your local STMicroelectronics sales office.
www.st.com

1 Heat sink
When attaching a heat sink to a ACEPACK DMT-32 make sure not to apply excessive force to the device for
assembly. Drill holes for screws in the heat sink exactly as specified. Smooth the surface by removing burrs and
protrusions of indentations. Do not touch the heat sink when the ACEPACK DMT-32 is operational to avoid a burn
injury.
1.1 Basic guidelines
The following table gives designers basic guidelines.
Table 1. Mounting torque and heat sink flatness specifications
Item Condition Min. Typ. Max. Unit
Mounting torque Mounting screw:M3
Recommended 7 kgf•cm 4 7 10 Kgf.cm
Recommended 0.68 N•m 0.39 0.68 0.98 N•m
Device flatness See Figure 1. Device flatness specification 0 +120 μm
Heat sink flatness See Figure 2. Heat sink flatness specification -50 - +100 μm
Device and heat sink flatness are prescribed as seen in Figure 1. Device flatness specification and in
Figure 2. Heat sink flatness specification.
Increasing the contact pressure between package and heat sink will maximize the contact area between the two
surfaces. Increasing the mounting torque in the fastening screw, or using a clip with a high spring constant, will
increase the contact areas and provide solid conduction heat-flow paths, which are more effective than
conduction across an air gap. Applying the proper mounting torque is the key factor in obtaining adequate
pressure along the contact surfaces of the package and the heat sink, in order to minimize the contact thermal
resistance. If mounting torque is too low, the contact thermal resistance increases due to bad thermal contact
under insufficient contact pressure. If mounting torque is too high package crack may be occurring. Hence,
appropriate mounting torque must be applied to produce minimal thermal resistance and avoid damaging the
package or changing the device characteristics.
The thermal contact resistance depends on the force generated by the applied torque on the screw:
F=2
*
T
*
π
P+r
*
D
*
π
Where:
• 1108T is applied torque on the screw in N*m
• P is pitch in m
• D is screw diameter in m
• r is rubbing factor: # 0.12 for steel-steel with grease and # 0.2 for steel-aluminum
TN1393
Heat sink
TN1393 - Rev 2 page 2/18

Figure 1. Device flatness specification
Figure 2. Heat sink flatness specification
TN1393
Basic guidelines
TN1393 - Rev 2 page 3/18

1.2 Thermal conductive grease
To get the most effective heat dissipation, it is necessary to enlarge the contact area as much as possible, which
minimizes the contact thermal resistance. Properly apply thermal-conductive grease over the contact surface
between a module and heat sink, which is also useful for preventing the contact surface from corrosion. Ensure
that the grease has constant in time quality and long-term endurance within a wide operating temperature range.
Use a torque screwdriver to fasten up to the max specified torque rating. Exceeding the maximum torque
limitation might cause a module to be damaged or degraded. Pay attention not to have any dirt remaining on the
contact surface.
1.3 Screw tightening torque
Do not exceed the specified fastening torque. Over tightening the screws may cause ceramic or molding
compound crack, as shown in Figure 3. Molding compound crack, and heat-fin threaded hole destruction.
Tightening the screws beyond a certain torque can cause saturation of the contact thermal resistance.
Figure 3. Molding compound crack
Figure 4 shows the recommended fastening sequence for mounting screws.
STMicroelectronics recommends to temporary tight mounting screws with fixing torque set at 0.2/0.3N•m and
permanently tight mounting screws with the suggested torque of 0.68 N•m (0.98 N•m max.).
Use screwdriver temporary fastening
Use screwdriver permanent fastening
To reduce fastening process cycle time, two-steps permanently tightening is also possible:
Use screwdriver permanent fastening
If two-steps permanent tightening is applied, thermal grease may not evenly distribute in between the module and
external heat sink.
In case of use of electrical or pneumatic screwdriver, it is suggested to keep revolution at 200 rpm max. as quick
impact of screw may damage the module plastic body.
TN1393
Thermal conductive grease
TN1393 - Rev 2 page 4/18

Figure 4. Recommended fastening order of mounting screws
1.4 Recommended screws
All mounting screws should have washers and spring washer for best mounting results. It is recommended to use
SEMS screw (included spring/plain washer M3) as shown in the following figure.
Figure 5. SEMS screw (size M3, spring washer 5.0Φ, plain washer 7.5Φ)
TN1393
Recommended screws
TN1393 - Rev 2 page 5/18

1.5 Electrical insulation: creepage and clearance
The electrical insulation is compliant with the IEC60664-1: the minimum creepage and clearance distances are
guaranteed according to the material class, pollution degree, altitude and voltage.
The creepage distance is defined as the shortest distance along the surface of a solid insulating material between
two conductive parts. Thanks to the grooves specifically designed on the molded surface, the DMT-32 ensure
higher creepage.
The figure below shows the minimum creepage of 12.85 mm, defined as the minimum distance guaranteed and to
be considered as a reference for the heat sink positioning. The creepage distance is depicted with the red line.
Figure 6. Creepage distance allowed
Heat sink
DBC
Creepage min= 12.85mm
The clearance distance is defined as shortest distance in air between two conductive parts. The clearance
distance, referred to the shoulder of the pin and the top of the groove is 3.30 mm, considered as typical value.
This represent the typical distance at which a generic heat sink can be located.
In the figure below it is highlighted the typical clearance can be guaranteed, considering the surface of a heat sink
on the top of the DBC substrate. This is represented by the solid arrow in blue. Additional clearance distance can
be achieved by specific design of the heat sink, that is as indicated in the figure below by the dashed green arrow.
Figure 7. Clearance distance allowed
Heat sink
DBC
Clearance= 3.3mm
TN1393
Electrical insulation: creepage and clearance
TN1393 - Rev 2 page 6/18

2 Package handling
2.1 ESD protective measures
Semiconductors are normally electrostatic discharge sensitive devices (ESDS) requiring specific precautionary
measures regarding handling and processing. Static discharges caused by human touch or by processing tools
may cause high-current and/or high-voltage pulses, which may damage or even destroy sensitive semiconductor
structures. On the other hand, integrated circuits (ICs) may also be charged by static during processing. If
discharging takes place too quickly (“hard” discharge), it may cause peak loads and damages, too. ESD
protective measures must therefore prevent contact with charged parts as well as charging of the ICs. Protective
measures against ESD include proper procedures for the handling, processing, and the packing of ESDS. A few
hints are provided below on handling and processing.
2.1.1 ESD protective measures in the workplace
• Standard marking of ESD-protected areas
• Access controls, with wrist strap and footwear testers
• Air conditioning
• Dissipative and grounded floor
• Dissipative and grounded working and storage areas
• Dissipative chairs
• Ground bonding point for wrist strap
• Trolleys with dissipative surfaces and wheels
• Suitable shipping and storage containers
• No sources of electrostatic fields
2.1.2 Equipment for personal
• Dissipative/conductive footwear or heel straps
• Suitable garments made of fabrics that do not generate excessive static electricity
• Wrist strap with safety resistor
• Volume conductive gloves or finger cots
2.1.3 Production installations and processing tools
• Machine and tool parts made of dissipative or metallic materials
• No materials having thin insulating layers for sliding tracks
• All parts reliably connected to ground potential
• No potential difference between individual machine and tool parts
• No sources of electrostatic fields
Our recommendations are based on the internationally applicable standards IEC 61340-5-1 and ANSI/ESD
S2020.
2.2 Packing of components
Please refer to product and package specifications and our sales department to get information about what
packaging is available for a given product.
Generally the following list of standards dealing with packing should be considered if applicable for a given
package and packing:
• IEC 60286-4 Packaging of components for automatic handling - Part 4: Stick magazines for dual-in-line
packages
• IEC 60286-5 Packaging of components for automatic handling - Part 5: Matrix trays
TN1393
Package handling
TN1393 - Rev 2 page 7/18

2.3 Storage and transportation conditions
Improper transportation and unsuitable storage of components can lead to a number of problems during
subsequent processing, such as poor solderability, delamination, and package cracking effects.
These relevant standards should be taken into account as appropriate:
• IEC 60721-3-0 Classification of environmental conditions: Part 3: Classification of groups of environmental
parameters and their severities; introduction
• IEC 60721-3-1 Classification of environmental conditions: Part 3: Classification of groups of environmental
parameters and their severities; Section 1: Storage
• IEC 60721-3-2 Classification of environmental conditions: Part 3: Classification of groups of environmental
parameters and their severities; Section 2: Transportation
• IEC 61760-2 Surface mounting technology - Part 2: Transportation and storage conditions of surface
mounting devices (SMD) - Application guide
• IEC 62258-3 Semiconductor Die Products - Part 3: Recommendations for good practice in handling,
packing and storage
• ISO 14644-1 Clean rooms and associated controlled environments Part 1: Classification of airborne
particulates
Table 2. General storage conditions, overview
Product Condition for storing
Wafer/die N2 or MBB(1) (IEC 62258-3)
Component - not moisture sensitive 1K2 (IEC 60721-3-1)
1. Moisture barrier bag
Maximum storage time
The conditions to be complied with in order to ensure problem-free processing of active and passive components
are described in standard IEC 61760-2.
Internet links to standards institutes
• American national standards institute (ANSI)
• Electronics industries alliance (EIA)
• Association connecting electronics industries (IPC)
2.4 Handling damage and contamination
Any mechanical damage during automatic or manual handling of components (in or out of the component
packing) that may harm package leads and/or body has to be avoided. In particular, unintentional bending of
leads may cause a loosening in the package body which can result in electrical malfunction.
Along with other factors, any contamination applied to a component or packing may cause:
• Solderability problems
• Corrosion
• Electrical shorts (due to conductive particles)
2.5 Component solderability
The final plating of most semiconductor packages are sufficiently thick and wettable to assure good solderability,
even after a long storage time. Note that the cut edges of the pins should be ignored in any assessment of
solderability. Suitable methods for the assessment of solderability can be derived from JESD22B 102 or
IEC6068-2-58.
Components are plated with pure Sn, or pre-plated with noble metals on a Ni carrier (e.g. NiAu, NiPdAu). Tin-
plated and pre-plated components are compatible with both SnPb and Pb-free soldering.
TN1393
Storage and transportation conditions
TN1393 - Rev 2 page 8/18

3 Soldering
ACEPACK DMT-32 is parts THD packages that are typically soldered by wave soldering.
3.1 Selective wave soldering
Wave soldering is a large-scale soldering process by which electronic components are soldered to a PCB to form
an electronic assembly. The name is derived from the fact that the process uses a tank to hold a quantity of
molten solder; the components are inserted into or placed on the PCB and the loaded PCB is passed across a
pumped wave or cascade of solder. The solder wets the exposed metallic areas of the board (those not protected
with solder mask), creating a reliable mechanical and electrical connection.
For THD, only the leads that extend through the drill holes in the PCB contact the hot solder. The body of the
package is heated by the hot leads. This has two consequences:
1. The package body is cooler than in the case of reflow soldering
2. The temperature gradient between leads and body and inside the package is greater than in the case of
reflow soldering.
Therefore, for wave-solderable THD packages the heat resistance is tested according to JESD22-B106 and
IEC668 2-20 (typically 260 °C, 10 s).
Note: immersion of the whole package body into the molten solder is not recommended since THD packages are not
designated for such a harsh temperature shock.
There are many types of wave-soldering machines, but their basic components and principles are the same. A
standard wave-soldering machine consists of three zones: the fluxing zone, the preheating zone, and the
soldering zone. A fourth zone, the cleaning zone, may be used depending on the type of flux applied.
Dual-wave soldering is the most commonly used wave-soldering method (see Figure 8. Typical dual-wave
soldering profile). The peak temperatures, ramp rates, and times that are used depend on the materials and the
wave-soldering equipment.
The first wave has a turbulent flow and therefore guarantees a wetting of nearly all shapes of leads and board
pads, but also creates an increased number of unwanted solder bridges. These solder bridges have to be
removed by the second, laminar wave.
When using lead-free solder alloys, a nitrogen atmosphere is recommended.
Selective wave soldering is used when only a few THD packages have to be soldered onto the board. Generally
this is done after the other components are already soldered by reflow soldering. This requires effective protection
of these components undergoing the selective wave soldering. This protection can be achieved either by using
special fixtures and deflectors for the PCB or/ and a small wave shape achieved by using special wave-guiding
tubes or covers.
TN1393
Soldering
TN1393 - Rev 2 page 9/18

Figure 8. Typical dual-wave soldering profile
3.2 Other soldering techniques
Beside wave and reflow soldering, other techniques are used in special applications. Examples include selective
wave soldering, laser welding and laser soldering, hot bar soldering, and manual soldering with solder irons and
hot air guns.
For this broad group of soldering techniques, which cannot be tested for every component, some general
guidelines should be followed:
• The maximum temperature of the package body and leads must not exceed the maximum allowed
temperature for reflow or wave soldering.
• The maximum allowed time at high temperatures must not exceed the maximum allowed time for reflow or
wave soldering.
• If heat is applied to the leads, the maximum temperatures in the package and of the package body must
not exceed the maximum allowed temperatures during reflow or wave soldering.
• For details and special arrangements, please refer to the product data sheet and/or qualification report.
If long contact and heating times are unavoidable, the resulting temperatures on different leads near the package
body should be measured and compared to the temperatures and duration achieved during wave or reflow
soldering, which must not be exceeded.
Please ask to your local sales, quality, or application engineer to provide you the evaluation report for further
information if needed.
3.3 Heat sink mounting by reflow soldering
In special applications the heat sinks of high-power THD packages can be mounted to the board by solder paste
printing, pick and place, and reflow soldering. In this case, the packages undergo a reflow profile.
Note: THD packages are qualified for wave soldering and not for reflow soldering. Therefore, reflow soldering should
not be used for heat sink mounting for THD packages.
TN1393
Other soldering techniques
TN1393 - Rev 2 page 10/18

4 Cleaning
After the soldering process, flux residues can be found around the solder joints. However, if the solder joints have
to be cleaned, the cleaning method (e.g. ultrasonic, spray, or vapor cleaning) and solution have to be selected
with consideration of the packages to be cleaned, the flux used (rosin-based, water-soluble, etc.), and
environmental and safety aspects.
Removing/drying even of small residues of the cleaning solution should also be done very thoroughly.
TN1393
Cleaning
TN1393 - Rev 2 page 11/18

5 Inspection
After component placement:
A visual inspection after component placement can be done by AOI. It is used to check if the mounting is done
completely and if severe misplacements have occurred. Sometimes the correct orientation of the component can
also be checked.
After soldering:
The solder joint meniscus of the leads of THD packages can be inspected by optical microscope or AOI.
Acceptable solder joints are described in international standards such as IPC-A-610.
Figure 9. Example of THD package pin that is soldered into the hole is well wetted and do not show any sign of
defects: shows a THD lead with optimal wetting. It has to be assured that a metallized via is filled properly. This
cannot be detected by visual inspection, but can be done by x-ray and/or cross sectioning.
Figure 9. Example of THD package pin that is soldered into the hole is well wetted and do not show any
sign of defects
Automatic X-ray Inspection (AXI) is the only reasonable method for efficient inline control. AXI systems are
available as 2D and 3D solutions. They usually consist of an X-ray camera and the hardware and software
needed for inspection, controlling, analysing, and data-transfer routines. These systems enable the user to
reliably detect soldering defects such as poor soldering, bridging, voiding, and missing parts. For the acceptability
of electronic assemblies, please refer also to the IPC-A-610C standard.
Cross sectioning of a soldered package as well as dye penetration analysis can serve as tools for sample
monitoring only, because of their destructive character. Nonetheless, these analysis methods must be used during
engineering of new products at customers’ production sites to get detailed information about the solder-joint
quality.
Lead-free (SnAgCu) solder joints typically do not have a bright surface. Lead-free solder joints are often dull and
grainy. These surface properties are caused by the irregular solidification of the solder, as the solder alloys are
not exactly eutectic .This means that SnAgCu-solders do not have a melting point but a melting range of several
degrees. Although lead-free solder joints have this dull surface, this does not mean that lead-free joints are of
lower quality or weak. It is therefore necessary to teach the inspection staff what these lead-free joints look like,
and/or to adjust optical inspection systems to handle lead-free solder joints.
TN1393
Inspection
TN1393 - Rev 2 page 12/18

6 Rework
If a defective component is observed after board assembly, the device can be removed and replaced by a new
one. Repair of single solder joints is generally possible, but requires proper tools. For example, repairing the
solder joint of an exposed die pad cannot be done with a soldering iron.
Whatever rework process is applied, it is important to recognize that heating a board and components above 200
°C may result in damage. As a precaution, every board with its components has to be baked prior to rework. For
details, please refer to the international standard J-STD-033.
In any case, mechanical, thermal or thermo-mechanical overstress has to be avoided, and rework has to be done
according to JEDEC J-STD-033A, IPC-7711 and IPC-7721.
6.1 Device removal
If a defective component is going to be sent back to the supplier, no further defects must be caused during the
removal of this component, because this may hinder the failure analysis by the supplier.
The following recommendations should be considered:
• Temperature profile: during the de-soldering process it should be assured that the package peak
temperature is not higher and temperature ramps are not steeper than for the standard assembly wave
process.
• Mechanics: be careful not to apply high mechanical forces for removal. Otherwise failure analysis of the
package can be impossible, or PCB can be damaged. For large packages, pipettes can be used
(implemented on most rework systems); for small packages, tweezers may be more practical.
6.2 Site redressing
After removing the defective component, the pads on the PCB have to be cleaned to remove solder residues.
This may be done by vacuum desoldering or wick.
Don’t use steel brushes because steel residues can lead to bad solder joints. Before placing a new component, it
may be necessary to apply solder paste on PCB pads by printing (special micro-stencil) or dispensing.
6.3 Reassembly and reflow
After preparing the site, the new package can be placed onto the PCB and the leads are to be inserted into the
holes. Regarding placement accuracy and placement force, the process should be comparable to the (automatic)
pick and place process.
During the soldering process, it should be assured that the package peak temperature is not higher and
temperature ramps are not steeper than for the standard assembly process. Soldering wire can be used to
resolder the leads. Use only no-clean solder paste, solder wire, and flux for repair.
TN1393
Rework
TN1393 - Rev 2 page 13/18

7 Coating of assembled PCB’s
In some applications, coatings are used to prevent damage due to external influences such as:
• Mechanical abrasion
• Vibration
• Shock
• Humidity
• Hand perspiration
• Chemicals and corrosive gases
These influences may cause:
• Electrical leakage due to humidity.
Corrosion that leads to degradation of conductor paths, solder joints, and any other metallized areas; and/or
formation of electrical leakage paths. These can eventually result in electrical shorts (electrical leakage) or open
contacts.
• Mechanical damage to conductor paths, solder joints, and components. This damage can lead to electrical
failures.
Coatings act as electrically isolating and impervious covers that adhere well to the different PCB materials.
A wide variety of different coatings is available on the market. They differ in:
• Price
• Simple processability (spray, dip, casting, curing, etc.)
• Reparability
• Controllability
• Homogeneity
In any case, please be aware of the chemical, electrical, mechanical and thermo-mechanical interaction between
the coating and the PCB and its components. Coatings can affect component reliability.
TN1393
Coating of assembled PCB’s
TN1393 - Rev 2 page 14/18

Contents
1Heat sink ..........................................................................2
1.1 Basic guidelines ...............................................................2
1.2 Thermal conductive grease ......................................................4
1.3 Screw tightening torque .........................................................4
1.4 Recommended screws ..........................................................5
1.5 Electrical insulation: creepage and clearance ......................................6
2Package handling..................................................................7
2.1 ESD protective measures........................................................7
2.1.1 ESD protective measures in the workplace .....................................7
2.1.2 Equipment for personal ....................................................7
2.1.3 Production installations and processing tools ...................................7
2.2 Packing of components .........................................................7
2.3 Storage and transportation conditions .............................................8
2.4 Handling damage and contamination ..............................................8
2.5 Component solderability.........................................................8
3Soldering..........................................................................9
3.1 Selective wave soldering ........................................................9
3.2 Other soldering techniques .....................................................10
3.3 Heat sink mounting by reflow soldering ...........................................10
4Cleaning..........................................................................11
5Inspection ........................................................................12
6Rework ...........................................................................13
6.1 Device removal ...............................................................13
6.2 Site redressing................................................................13
6.3 Reassembly and reflow ........................................................13
7Coating of assembled PCB’s ......................................................14
Revision history .......................................................................15
List of figures..........................................................................17
TN1393
Contents
TN1393 - Rev 2 page 16/18

List of figures
Figure 1. Device flatness specification...........................................................3
Figure 2. Heat sink flatness specification .........................................................3
Figure 3. Molding compound crack .............................................................4
Figure 4. Recommended fastening order of mounting screws...........................................5
Figure 5. SEMS screw (size M3, spring washer 5.0Φ, plain washer 7.5Φ) ..................................5
Figure 6. Creepage distance allowed ...........................................................6
Figure 7. Clearance distance allowed ...........................................................6
Figure 8. Typical dual-wave soldering profile ..................................................... 10
Figure 9. Example of THD package pin that is soldered into the hole is well wetted and do not show any sign of defects . 12
TN1393
List of figures
TN1393 - Rev 2 page 17/18

IMPORTANT NOTICE – READ CAREFULLY
STMicroelectronics NV and its subsidiaries (“ST”) reserve the right to make changes, corrections, enhancements, modifications, and improvements to ST
products and/or to this document at any time without notice. Purchasers should obtain the latest relevant information on ST products before placing orders. ST
products are sold pursuant to ST’s terms and conditions of sale in place at the time of order acknowledgment.
Purchasers are solely responsible for the choice, selection, and use of ST products and ST assumes no liability for application assistance or the design of
purchasers’ products.
No license, express or implied, to any intellectual property right is granted by ST herein.
Resale of ST products with provisions different from the information set forth herein shall void any warranty granted by ST for such product.
ST and the ST logo are trademarks of ST. For additional information about ST trademarks, refer to www.st.com/trademarks. All other product or service names
are the property of their respective owners.
Information in this document supersedes and replaces information previously supplied in any prior versions of this document.
© 2023 STMicroelectronics – All rights reserved
TN1393
TN1393 - Rev 2 page 18/18
Table of contents
Other ST Control Unit manuals
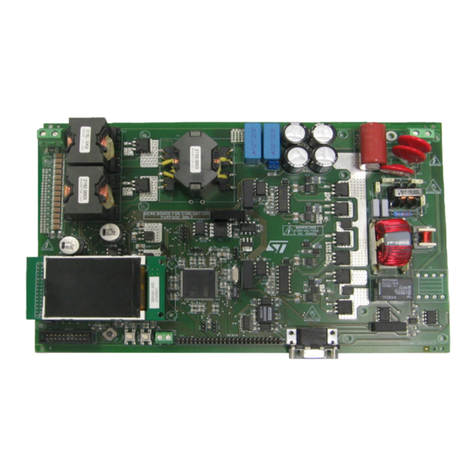
ST
ST AN4070 Installation and operating instructions
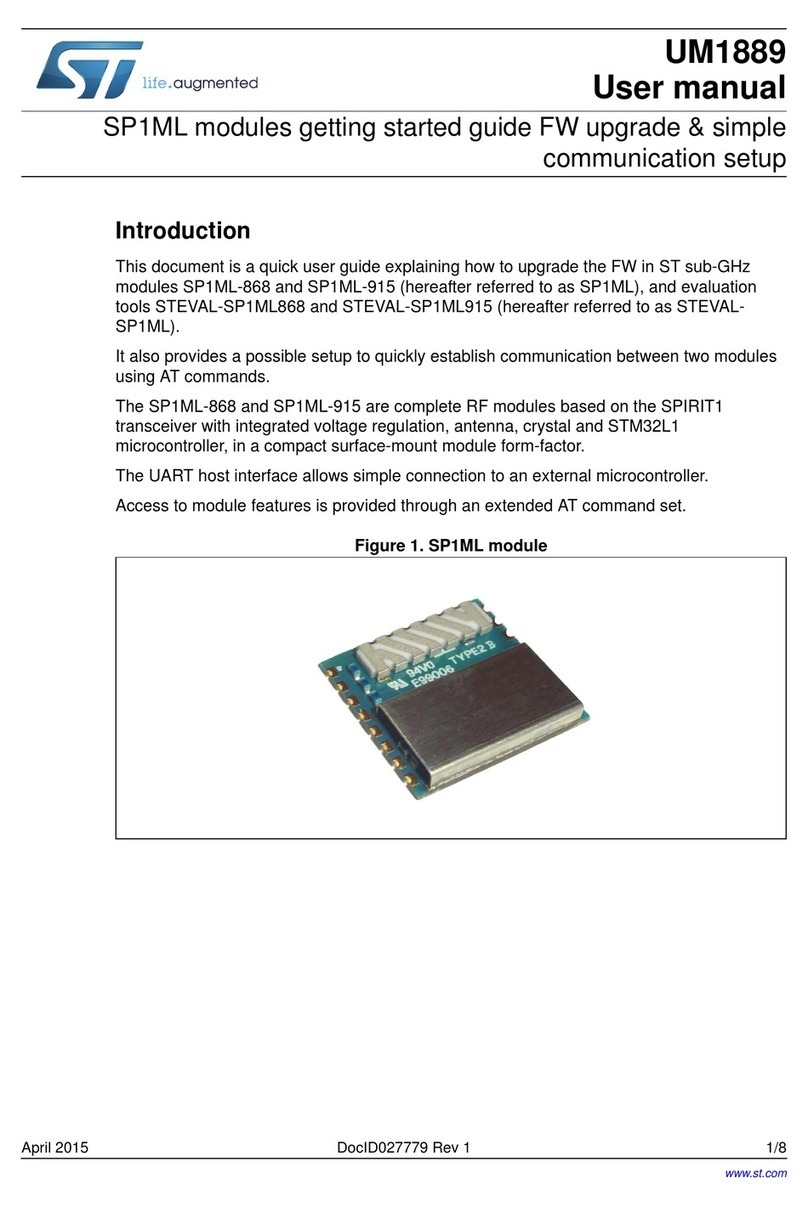
ST
ST SP1ML-915 User manual
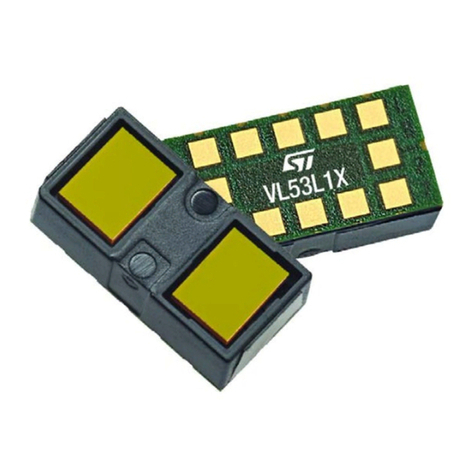
ST
ST VL53L1X API User manual

ST
ST L6472 User manual
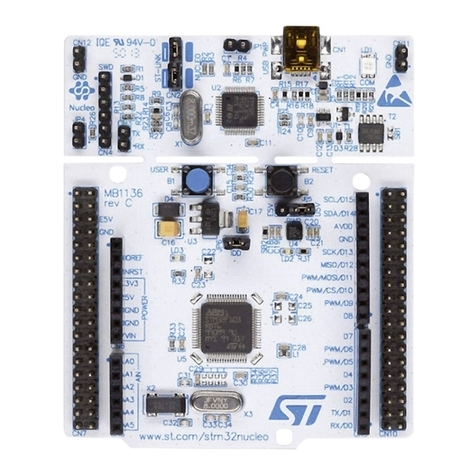
ST
ST STM32 Nucleo User manual
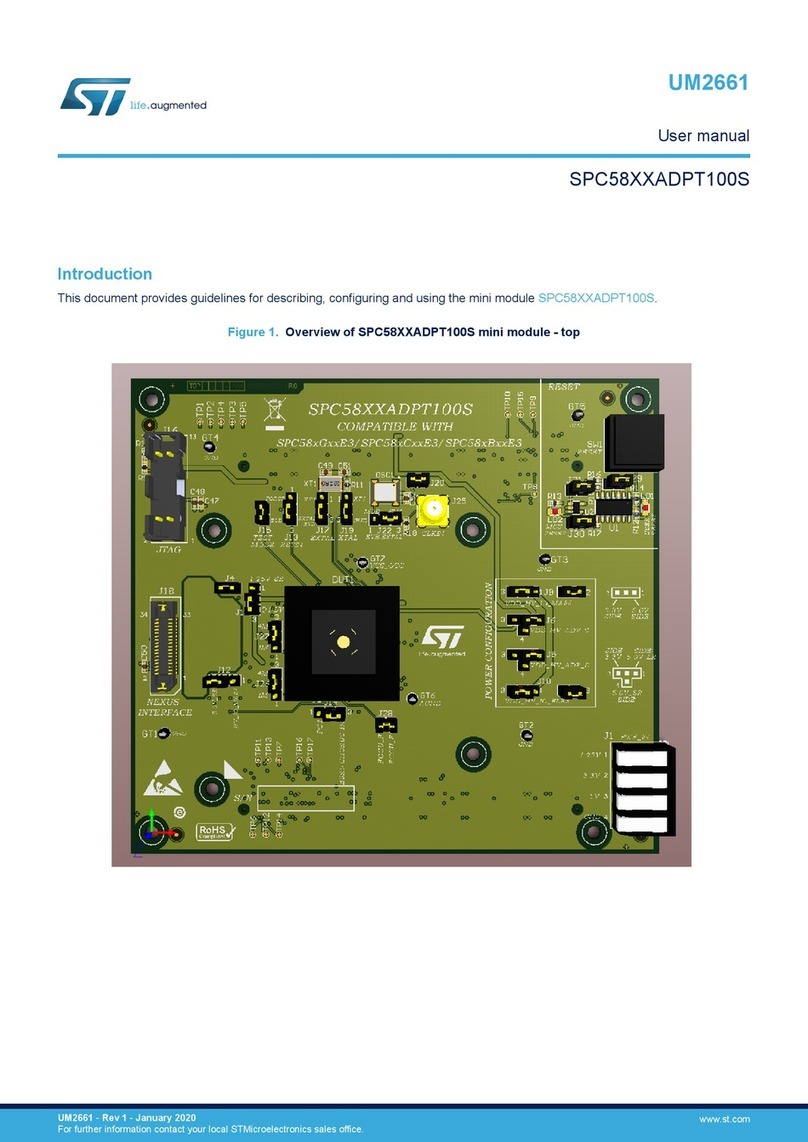
ST
ST SPC58XXADPT100S User manual
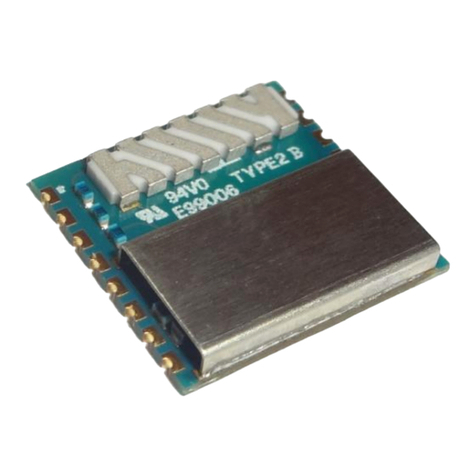
ST
ST SPLML-868 Instruction Manual
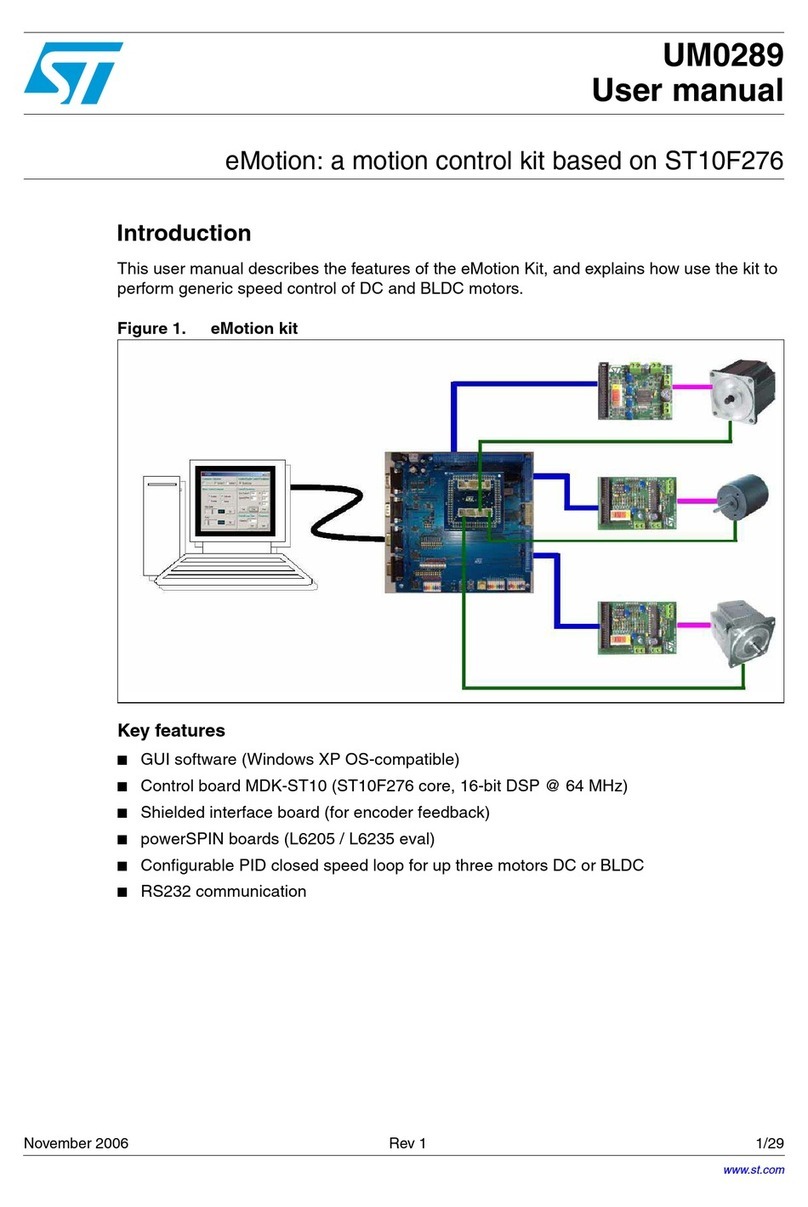
ST
ST eMotion User manual
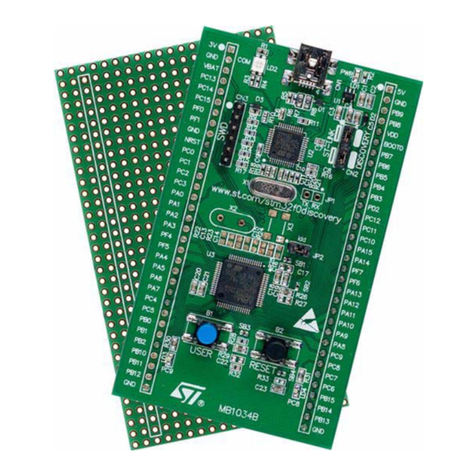
ST
ST STM32F051R8T6 User manual

ST
ST Teseo-LIV4FM User manual
Popular Control Unit manuals by other brands

Metso
Metso Neles R series Installation maintenance and operating instructions
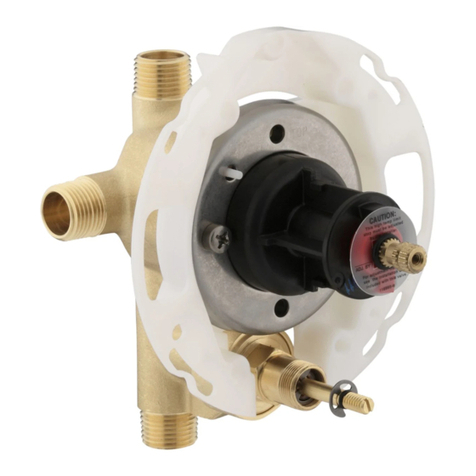
Kohler
Kohler K-304 Installation and care guide

Solem
Solem BL-IS Quick installation guide
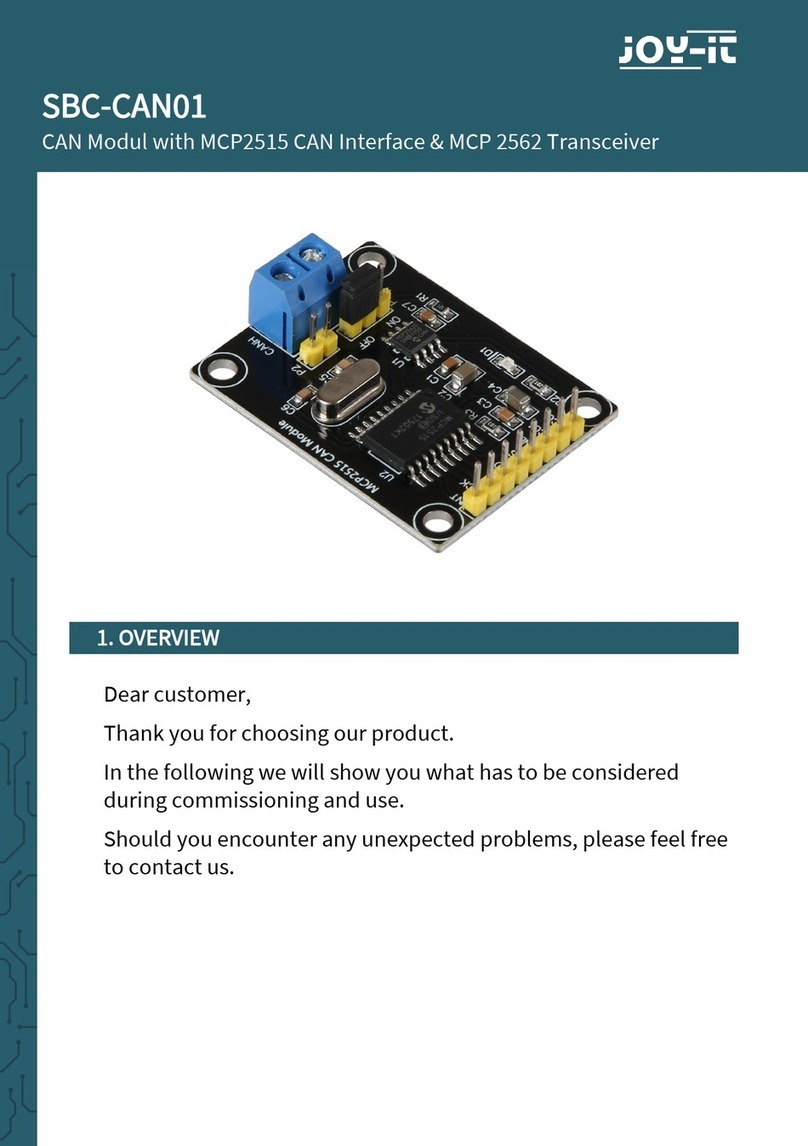
Joy-it
Joy-it SBC-CAN01 quick start guide
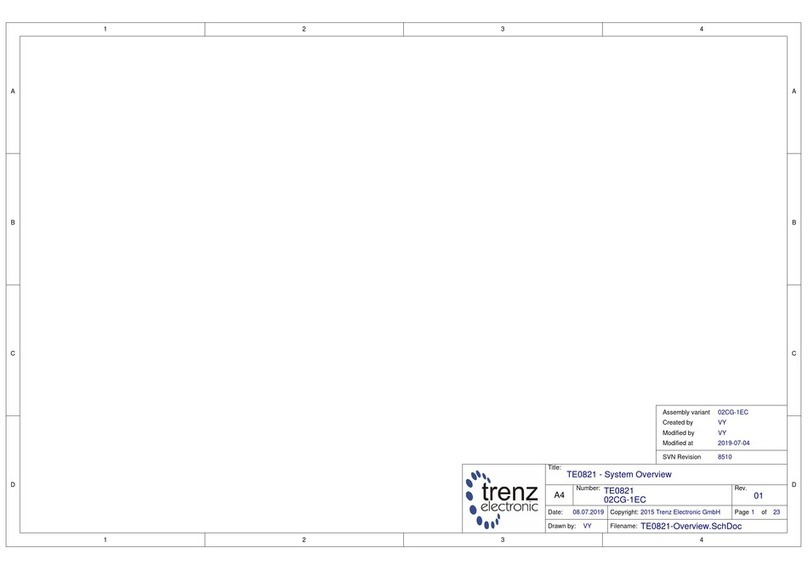
Trenz Electronic
Trenz Electronic TE0821 02CG-1EC Series Schematics
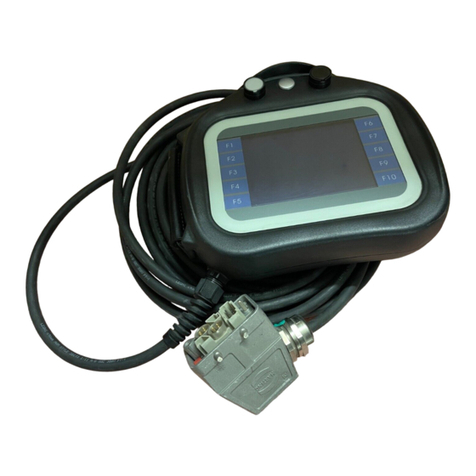
Lenze
Lenze Digitec EPM-H605 operating instructions