Sullair Supervisor IE User manual

SUPERVISOR
INSTRUCTION MANUAL
IE
KEEP FOR
FUTURE
REFERENCE
Part Number 02250084---980
Sullair Corporation

AIR CARE
SEMINAR TRAINING
Sullair AirCare Seminars are 3---day courses thatprovide hands---on instruction
in the proper operation, maintenance and service of Sullair equipment.
Individual seminars on Industrial compressors and compressor electrical
systems are presented at regular intervals throughout the year at a dedicated
training facility at Sullair’s corporate headquarters in Michigan City, Indiana.
Instruction includes discussion of the function and installation of Sullair service
parts, troubleshooting of the most common problems, and actual equipment
operation. The seminars are recommended for maintenance and service
personnel.
For detailed course outlines, schedule and cost information contact:
Sullair Corporate Training Department
1---800---SULLAIR or 219---879---5451 (ext. 1816)
--- Or Write ---
Sullair Corporation
3700 E. Michigan Blvd.
Michigan City, IN 46360
Attn: Service Training Department

TABLE OF CONTENTS
Section 1 PAGE
SAFETY 11.1 GENERAL
11.2 ELECTRIC SHOCK
11.3 DECALS
Section 2
DESCRIPTION 32.1 INTRODUCTION
32.2 INSTRUMENTATION, FUNCTIONAL
DESCRIPTION
42.3 GENERAL
42.4 PURPOSE OF CONTROLS
52.5 AUTOMATIC OPERATION
52.6 SUPERVISOR IE OUTPUT RELAYS
52.7 SUPERVISOR IE SPECIAL FUNCTION INPUTS
62.8 SUPERVISOR IE AUXILIARY DIGITAL INPUTS
62.9 OPTIONAL FACTORY CONFIGURATIONS
72.10 SPECIAL SOFTWARE VERSION
Section 3
PROGRAMMING PROCEDURES
93.1 SUPERVISOR IE MICROCONTROLLER
PROGRAMMING
10 3.2 FACTORY PROGRAMMING
Section 4
START---UP PROCEDURES
12 4.1 MOTOR ROTATION DIRECTION CHECK
12 4.2 INITIAL START---UP PROCEDURE
12 4.3 SUBSEQUENT START---UP PROCEDURE
12 4.4 SHUTDOWN PROCEDURE
Section 5
MAINTENANCE AND
TROUBLESHOOTING 13 5.1 CONTROL SYSTEM ADJUSTMENT
13 5.2 MESSAGE DISPLAY DEFINITIONS
14 5.3 TROUBLE INDICATION SETPOINTS
15 5.4 TROUBLESHOOTING GUIDE

TABLE OF CONTENTS
Section 6 PAGE
CALIBRATION 21 6.1 CALIBRATION OF PRESSURE INPUTS
22 6.2 CALIBRATION OF TEMPERATURE INPUTS
Section 7
REPLACEMENT
PARTS 23 7.1 REPLACEMENT PARTS FOR SUPERVISOR
23 7.2 REPLACEMENT SENSORS
Section 8
WIRING
DIAGRAMS 24 8.1 WIRING DIAGRAM---MASTER CONTROL WATER---
COOLED COMPRESSOR
25 8.2 WIRING DIAGRAM---WYE---DELTA, AIRCOOLED
COMPRESSOR
26 8.3 WIRING DIAGRAM---FULL VOLTAGE, WATERCOOLED
COMPRESSOR
27 8.4 WIRING DIAGRAM---FULL VOLTAGE, AIRCOOLED
COMPRESSOR

Section 1
SAFETY
1
1.1 GENERAL
Sullair Corporation and its subsidiaries designs
and manufactures all of our products so they can
be operated safely. However, the responsibility for
safe operation rests with those who use and main-
tain these products. For safe machine operation it
is vitally important to review all safety precautions
noted in the Safety Section of your compressor’s
Operator’s Manual. The precautions listed there,
as well as those following, are offered as a guide
which, if conscientiously followed, will minimize the
possibility of accidents throughout the useful life of
this equipment.
The compressor should be operated only by those
whohavebeentrainedanddelegatedtodoso,and
who have read and understood their compressor’s
Operator’s Manual. Failure to follow the instruc-
tions, procedures and safety precautions listed
here and in the Operator’s Manual may result inac-
cidents and injuries.
NEVER start the compressor unless it is safe to do
so. DO NOT attempt to operate the compressor
with a known unsafe condition. Tag the compres-
sor and render it inoperative by disconnecting and
locking out all power at source or otherwise dis-
abling its primemover so others whomay notknow
ofthe unsafe condition cannot attempt tooperate it
until the condition is corrected.
Use and operate the air compressor only in full
compliance with all pertinent OSHA requirements
and/or all pertinent Federal, State, and Local codes
or requirements.
DO NOT modify the compressor and/or controls in
any way except with written factory approval.
1.2 ELECTRICAL SHOCK
A. Keep all parts of the body and any hand---held
tools or other conductive objects away from ex-
posed live parts of electrical system. Maintain dry
footing, stand on insulating surfaces and DO NOT
contact any other portion of the compressor when
making adjustments or repairs to exposed live
parts of the electrical system.
B. Attempt repairs only in clean, dry and well
lighted and ventilated areas.
C. Stay clear of the compressor during electrical
storms! It can attract lightning.
1.3 DECALS
SeeFigure1---1.TheSupervisorIEcontrol panel
contains several decals which contain necessary
information for safe performance. These decals
should never be removed. If adecal becomes dam-
aged, contact your nearest Sullair Distributor orthe
Sullair Corporation factory Service Department for
replacement parts (Note: When ordering new de-
cals, use part number printed on decal face.).

Section 1
SAFETY
2
Figure 1---1 Decals
* OSHA and FDA guidelines are superceded by any Federal, State or Local regulation whenever applicable.
*
*
!DANGER

Section 2
DESCRIPTION
3
2.1 INTRODUCTION
Your compressor is equipped with a Supervisor IE
microprocessor controller, replacing the standard
electro-mechanical control of pushbuttons,
switches and gauges. This manual explains the
functions and operation of the Supervisor control
as well as how to program its features for your par-
ticular application.
2.2 INSTRUMENTATION, FUNCTIONAL DESCRIP-
TION
Refer toFigure2-1.The Supervisor IEcontrol panel
consists of displays for pressure, temperature,
time (run hours), and a status message. Default
pressure isline pressure (P2) whichis normally dis-
played with pad selections for sump pressure, fluid
pressure, separator differential and fluid filterdiffer-
ential. Default temperature is unit discharge tem-
perature (T1) which is normally displayed with a
pad selection for injection fluid temperature. An
LED map provides a graphic illustration of the
points being monitored. Operator controls consist
of EMERGENCY STOP, ON/OFF, monitor display
pads and programming pads. All compressor con-
trol, pressure and temperature displays are pro-
vided in the Supervisor IE.
SThe line (terminal) pressure transducer (P2)is
connected to the dry side of the receiver down-
stream from the check valve and continually moni-
tors the plant air pressure.
SThe sump pressure transducer (P1) monitors
the sump/unit discharge pressure.
SInjection oil pressure (P3) monitors oil pressure
at the point of injection into the compressor down-
stream of the oil filter.
SFilter oil pressure (P4) monitors oil pressure
ahead of theoil filter and isused withP3tocalculate
oil filter differential; ”ΔP2”=P4-P3.
SThe discharge temperature probe (T1) moni-
tors the temperature ofthe airleaving the compres-
sorunit. Forboth air-cooled and water-cooled com-
pressors the normal reading is approximately
180_F(82
_C) based on 80_F(27
_C) ambient tem-
perature.
SThe injection temperature probe (T2)monitors
the temperature of the fluid just before it is injected
into the unit.
SThe air filter maintenance switch monitors the
condition of the air intake filter. When the Supervi-
sor displays the message “AIR FILTER MAINT
RQD”, filter service is required.
SThe ON/OFF pad turns the compressor on and
off.
Figure 2---1 Supervisor Control Panel
SYSTEM
GRAPHIC
DISPLAY
PRESSURE DISPLAY
TEMPERATURE DISPLAY MESSAGE DISPLAY
HOURS DISPLAY
KEYPADS

Section 2
DESCRIPTION
4
SThe hour display records cumulative hours of
operation forthe compressor and is useful forplan-
ning and logging service operations. A selectable
display of “load” hours or “load” as a percent of
“run” hours is available by pressing “HR LOAD” or
“HR%” respectively.
SSeparator differential pressure can be dis-
played by pressing the “ΔP1” pad. When a differ-
ential of 10 PSID (0.7 bar) is reached, the message
“SEPARATOR MAINT RQD” is displayed and the
ΔP1 LED will flash.
SOil filter differential pressure can be displayed
by pressing the “ΔP2” pad. When a differential of
20PSID(1.4bar)isreached, themessage “OILFIL-
TER MAINT RQD” will be displayed and the ΔP2
LED will flash.
SThe “ON” LED indicates when the compressor is
running.
SThe amber light on the control panel indicates
when power to the compressor is supplied.
SThe green message display indicates the status
of the compressor.
2.3 GENERAL
While Sullair has built into this compressor a com-
prehensive array of controls and indicators to as-
sure you that it is operating properly, you will want
to recognize and interpret the reading which will
call for service or indicate the beginning of a mal-
function. Before starting your Sullair compressor,
read this section thoroughly and familiarize your-
self with the controls and indicators -their purpose,
location and use.
2.4 PURPOSE OF CONTROLS
CONTROL OR INDICATOR PURPOSE
ON/OFF PAD Depress to turn compressor ON. Depress again to
turn compressor OFF. If a fault shutdown occurs, or
EMERGENCY STOP, the ON/OFF button must be
pressed once to acknowledge the fault and silence
the alarm. Once the fault has been cleared, ON/OFF
must be pressed once to return to MANUAL SHUT-
DOWN in preparation for start.
HOUR DISPLAY Displays accumulated hours of compressor opera-
tion; useful for planning and logging service sched-
ules. Alternate displays by use of their respective
touchpads are - hours ON LOAD and percentage of
hours running when ON LOAD.
PRESSURE DISPLAY Continuously monitors service line air pressure (P2).
Located on dry side of receiver downstream of mini-
mum pressure/check valve. Selectable alternate dis-
plays via touchpad include:
SUMP PRESSURE (P1) displays sump/unit dis-
charge pressure.
SEPARATOR DIFFERENTIAL (ΔP1) displays the dif-
ferential pressure across the separator element/s. A
preset limit of 10 PSID (0.7 bar) will trigger the ΔP1
LED anda message will warn that a separator change
is required.
OIL FILTER DIFFERENTIAL (ΔP2) displays the dif-
ferential pressure across the fluid filter. A preset limit
of 20 PSID (1.4 bar) will trigger the ΔP2 LED and a
message will warn that a filter change is required.
TEMPERATURE DISPLAY Continuously monitors the temperature of theair leav-
ing the compressor unit (T1). The normal readings
should be approximately 180_F to 205_F(82
_Cto
96_C). An alternate display of injection fluid tempera-
ture (T2) is available from the touchpad. Normal read-
ings should be approximately 130_F to 160_F(54
_C
to 71_C).
AIR FILTER MAINTENANCE Indicates when the air filter change is required. The
LED shown onthe air filter ofthe graphic map willflash
and a message of “AIR FILTER MAINT RQD” will be
displayed.

Section 2
DESCRIPTION
5
2.4 PURPOSE OF CONTROLS (Cont’d.)
CONTROL OR INDICATOR PURPOSE
“POWER ENERGIZED” LIGHT Indicates when the control panel is receiving power.
“ON” LED Indicates when the compressor is running. If the ON
LED is flashing while the compressor is stopped, it is
indicating that the compressor was stopped by a re-
mote START/STOP contact and could be restarted
without notice.
2.5 AUTOMATIC OPERATION
For applications with varied periods of time when
there are no air requirements, Supervisor’s Auto-
matic mode allows the compressor to stop (time
delayed) when no compressed air requirement is
present and restart as compressed air is needed.
When needed, AUTOMATIC may also incorporate
an optional 0-30 second adjustable unloaded
STOP MODE feature which allows the motor to
stop froman unloaded condition when the ON/OFF
pad is pressed or after the timed stop period. If im-
mediate stop is required when operating in AUTO-
MATIC mode with optional unload STOP MODE
timing enabled, press the EMERGENCY STOPbut-
ton on the control panel.
2.6 SUPERVISOR IE OUTPUT RELAYS
PARAMETERS OPERATION
COMPRESSOR RUN Initiates starter controls and all auxiliary contacts that
operate simultaneously withthe mainstarter.Supervi-
sor assumes compressor is running if contact is
closed and P1 discharge pressure is at a satisfactory
level.
LOAD/UNLOAD SOLENOID VALVE Controls regulator bypass solenoid valve to load or
unload the compressor as demand varies.
COMMON FAULT ALARM Initiates to provide a common signal for remote indi-
cation of a fault shutdown.
WYE-DELTA TRANSITION Contact is used to control Wye-Delta starter transi-
tions logic. This contact is controlled by the Wye to
Delta timing function.
DRAIN SOLENOID VALVE Controlled by the drain time and drain interval timers,
this contact is used to control an optional condensate
drain solenoid valve.
2.7 SUPERVISOR IE SPECIAL FUNCTION INPUTS
PARAMETER OPERATION
REMOTE STOP/START (J1/1-16) Opening this contact initiates the STOP mode. Clos-
ing this contact permits a compressor start if permis-
sives are satisfied. Please note that AUTOMATIC/MA-
NUAL mode characteristics are maintained even
though remote STOP/START is used. The RUN LED
will flash if stopped with remote contact.
PARAMETERS SELECT With these contacts open, compressor operates
J1-13/16 (B) within pressure range P2A. With J1-13/16 contact
J1-15/16 (C) closed, compressor operates within pressure range
P2B. When J1-15/16 is closed, compressor oper-
ateswithinpressurerangeP2C.Suitablefor2or3
compressor base/load sequencing. The selected
range will be displayed in the status mode.

Section 2
DESCRIPTION
6
2.7 SUPERVISOR IE SPECIAL FUNCTION INPUTS (Continued)
PARAMETER OPERATION
RS 232 SERIAL PORT (J4) Full 2-way communication and control that provides
analog display transmission, signal status and com-
pressor status indication, as well as remote STOP/
START via computer. A great tool for preventive main-
tenance programs and customer DCS management
packages. Baud rates are factory settable from 1200
to 9600. Consult factory for communication protocol
(P/N 02250050-768).
2.8 SUPERVISOR IE AUXILIARY DIGITAL INPUTS
PARAMETERS OPERATION
MOTOR/OVERLOAD (J1/7-16) Monitors normally closed compressor motor over-
load contact. Will initiate compressor shutdown, flash
the motor LED on the graphic map and display the
message “MOTOR OVERLOAD” if the contact opens.
COOLING SYSTEM MONITOR (J1/9-16) Monitors cooler fan overload (AC), water pressure
switch (WC), and/or canopy fan motor overload. Nor-
mally closed signal when opened will initiate com-
pressor shutdown and display the message “FAN OL/
LOW WATER”
AUXILIARY FAULT (J1/11-16) An additional factory enabled digital input can be
(J1/11-12) used by the customer for an additional alarm/
shutdown parameter. During “factory programming”,
the user may select DISABLED, ALARM ONLY or
SHUTDOWN with alarm. Opening this contact when
enabled will affect the machine in the selected man-
ner; display the message “AUXILIARY FAULT” and
flash the LED just beneath the compressor graphic.
NOTE: All even numbered terminals of J1 connector are internally connected together.
2.9 OPTIONAL FACTORY CONFIGURATIONS
(Refer to section 3.2)
A. AUXILIARY DRY CONTACTS
With the addition of an extra 8-relay output board,
auxiliary dry contracts can be provided to remotely
indicate each annunciation point as listed on next
page.
B. REMOTE STOP/START
C. MACHINE NUMBER/BAUD RATE FOR SERIAL
COMMUNICATIONS.
D. 0-30 SECOND UNLOADED STOP MODE
E. SPARE DIGITAL SHUTDOWN INPUT
F. LOCKOUT OF ALL PARAMETER CHANGES
G. ADJUSTABLE T2 RELAY OUTPUT
H. SELECTABLE DISABLE OF FOURTH TEMPER-
ATURE (T4) INPUT FOR SINGLE-STAGE MA-
CHINES.
I. PROGRAMMABLE DELAYED AUTOMATIC RE-
START AFTER POWER FAILURE FROM 0 TO 120
SEC.
J. PROGRAMMABLE OFFSET OF PI (2 TO 30
PSID) TO PERMIT REMOTE MONITORING OF P2.

Section 2
DESCRIPTION
7
AUXILIARY DRY CONTACTS:
ON EXISTING RELAY CONTACTS K6 -T2 reference reached (factory configured
J10 Slot #7) option) non-latching with a 20_F(11
_C) deadband.
Adjustable setpoint
K7 - P1/T1 Prealarm
Indicates at 98% of Max Press P1 shutdown.
Does not latch. High Temp T1 Prealarm
Indicates at 225_F 107_C. Does not latch.
K8 - Full Load/Modulate relay for sequencing.
ON ADDITIONAL 8 RELAY OUTPUT BOARD K1- MaxPressP1shutdown,P1orP2sensor
(J11 Slot #8) failure.
K2- MinPressP3shutdown,P3orP4sensor
failure.
K3- HighTempT1,T3,T4shutdown,T1or
T2 sensor failure.
K4 - Compressor Motor Overload.
K5 - Fan Overload/Low Water Pressure.
K6 - Oil Filter Maintenance Required.
K7 - Separator Maintenance Required.
K8 - Inlet Filter Maintenance Required.
2.10 SPECIAL SOFTWARE VERSION — MASTER CONTROL
A special version of this control (IC p/n
02250057-714) is available for use in systems
where the STOP/START and LOAD/UNLOAD func-
tions are to be controlled by an external control de-
vice. All safeties are still active within the supervi-
sor. When enabled, the status message will always
indicated ”Master Control”. Relay K8 is utilized to-
remotely indicate MASTER CONTROL is enabled.
PARAMETER OPERATION
J1-11 Aux input is the LOCAL/MASTER input.
Contact open - LOCAL or normal operation
Contact closed - MASTER CONTROL or remote op-
eration.
Relay K8 Relay K8 is used to indicate LOCAL or MASTER CON-
TROL Supervisor setting.
Deenergized - normal or LOCAL control. (contact
open)
Energized - REMOTE START/STOP enabled and
armedaswellasAUXINPUTenabled.(contact
closed)
CONTROL LOGIC With REMOTE ENABLE/DISABLE disabled - all Su-
pervisor controls will operate normally except K8. Se-
rial and dry contact remote stop/start will be ignored.
Input J1-11 will be ignored. K8 will be deenergized.
Normal status messages will be used.
WithREMOTE ENABLE/DISABLE enabled -REMOTE
STOP/START input and LOCAL/MASTER CONTROL
input J1-11 will be active. Power failure restart is ac-
tive. Only Automatic mode will be used.

Section 2
DESCRIPTION
8
PARAMETER OPERATION
CONTROL LOGIC (Cont’d.) After REMOTE STOP/START is armed (pressing ON/
OFF key), relay K8 will energize to indicated REMOTE
enabled forMASTER CONTROL. Thisrelaywill deen-
ergize if the compressor is stopped manually or on a
fault.
With B and C true:
LOCAL/MASTER input closed (LOCAL) - Standard
Supervisor control in Automatic mode. Normal status
messages. REMOTE STOP/START is ignored. Run-
ning status messages are STANDBY, ON LOAD and
OFF LOAD unless shut down.
LOCAL/MASTER input open (MASTER) - Energize
relay K2 (UNLOAD/LOAD) upon machine start. Ig-
nore P2 as a start permissive and as UNLOAD/LOAD
control. the master controller will perform all UN-
LOAD/LOADfunctions external tothe Supervisor. The
RUN LED blinks in this mode if the machine is armed
but not running. (Just like normal REMOTE STOP/
START). Standard status messages of LOAD, UN-
LOAD and STANDBY are replaced with “MASTER
CONTROL”. All manual stop and fault shutdown logic
is still active.
REMOTE STOP/START logic is only valid if LOCAL/
MASTER input is closed. This input logic istobeopen
to stop and close to start.

Section 3
PROGRAMMING PROCEDURES
9
3.1 SUPERVISOR IE MICROCONTROLLER PRO-
GRAMMING
Several display and operational functions are user
programmable from the Supervisor keypad. Re-
peatedly pressing the “PROG” pad will scroll the
message display through the various program-
mable parameters. The cursor pad (Y)isusedto
change parameter values. A built---in timed delay
feature returns the message display to operation
mode after 5 seconds of inactivity.
PARAMETER (IN SEQUENTIAL ORDER) OPERATION
LANGUAGE Press the cursor pad for 2 seconds to change to next
language for the message display. Languages in or-
der are: French, German, Italian, Spanish and En-
glish.
AUTOMATIC/MANUAL The controller default state is AUTOMATIC operation.
If line pressure is adequate and/or the sump pressure
is greater than 5 to 10 PSIG (0.3 to 0.7 bar), pressing
the ON/OFF pad will put the control in STANDBY
mode until line pressure drops to the programmed
differential value and the sump pressure is low
enough to permit a START. AUTOMATIC mode pro-
vides a timed STOP with automatic restart operation.
AUTOMATIC RESTART AFTER POWER failure isalso
included in AUTOMATIC mode.
MANUAL mode ignores the line pressure permissive
of AUTOMATIC and starts the compressor with ON/
OFFas long as the minimum sump pressure and oth-
er fault conditions are satisfied. The compressor is
only stopped manually, remotely, or serially with no
time stop and no automatic restart after power failure.
PRESSURE UNITS Selects bar or PSIG; use cursor key to select. 1 bar =
14.5 PSIG.
TEMPERATURE UNITS _COR_F; use cursor key to select.
MAXIMUM PRESSURE P1 Displays factory set high discharge pressure shut-
down value (not adjustable).
MAXIMUM PRESSURE P2A Use the cursor key to set the OFF LOAD pressure set-
ting. Depressing the cursor pad for more than 2 sec-
onds will initiate a fast scrolling mode to quickly reach
the desired setpoint forall programmable setpoints. A
wraparound feature (on all functions) returns the val-
ue to its lowest limit if scrolling exceeds the high limit.
Typically set for 110 PSIG (7.6 bar).
PRESSURE DIFFERENTIAL P2A Selects the ON LOAD setting bysubtracting thediffer-
ential from P2A. Normally set for 10 PSIG (0.7 bar).
MAXIMUM PRESSURE P2B Same as P2A, but provides a second OFF LOAD set-
ting for base/load operation.
PRESSURE DIFFERENTIAL P2B Same as P2A, but provides a second ON LOAD set-
ting for base/load operation.
MAXIMUM PRESSURE P2C Same as P2A, but provides a third OFF LOAD setting
for base/load operations.
PRESSURE DIFFERENTIAL P2C Same as P2A, but provides a third ON LOAD setting
for base/load operation.
MINIMUM PRESSURE P3 Displays factory set minimum oil pressure value (not
adjustable).

Section 3
PROGRAMMING PROCEDURES
10
3.1 SUPERVISOR IE MICROCONTROLLER PROGRAMMING (Continued)
PARAMETER (IN SEQUENTIAL ORDER) OPERATION
UNLOAD TIME Adjusts timed stop function if compressor is running
unloaded for 0 to 60 minutes.
WYE TO DELTA TIME Adjusts transition timer for Wye---Delta starters from 0
to 30 seconds. ON LOAD function is delayed by the
value ofWye toDelta time. A separate relay contact is
provided with this function. It is recommended that a
transition time of 8 seconds not be exceeded.
DRAIN TIME AND DRAIN INTERVAL A timed contact is furnished to control a condensate
(OPTIONAL) removal solenoid valve. Both drain dura-
tion time (1 to 10 seconds) and time interval between
drains (1 to 10 minutes) may be set from these
modes.
3.2 FACTORY PROGRAMMING
Additional programming functions are available for
customizing the control for a particular application.
“FACTORY PROGRAMMING” is accessed by
pressing the PROG key until the AUTOMATIC/
MANUAL selection isdisplayed. Once there, press
andholdthenP1 and PROG keys simultaneously
for 3 seconds. In addition to the preceding setting,
the following parameters may be programmed:
PARAMETER (IN SEQUENTIAL ORDER) OPERATION
MACHINE NUMBER Select 1thru 32. Allows multiple machines on acom-
mon serial network. Default is 1.
BAUD RATE Select 1.2k, 2.4k, 4.8k, or9.6k. The correct baud rate
must be selected to match monitoring equipment for
serial communications. Default is 9.6K.
MAXIMUM PRESS P1 Adjustable from 50 to 200 PSI. Default is 135psi. In-
crease this value only if the sump tank is rated for the
increased pressure. This value must be set to trip be-
forethe tank pressure relief valve setting less itstoler-
ance range.
STOP MODE TIME Adjustable from 0 to 30 sec. Runs the compressor
unloaded for the time programmed when a normal
stop is initiated. E-Stop and fault shutdowns always
override this timer.. Default is 0.
VIEW T3/T4 ON/OFF A service function, when ON is selected, displays for
T3 and T4 replace the normal displays for T1 and T2
respectively. (Note: T1 and T2 LED’S are not active in
this display mode.) Be sure to turn this function OFF
before releasing this machine to the user. Default is
OFF.
REMOTE ENABLE ON/OFF Select ON for Remote STOP/START function. Select
OFF to disable this function. Default is OFF.
SETPOINT T2 ADJ. Adjust from 100 to 235_F. Resets at 20_Fbelowthe
setpoint. Not a shutdown function unless wired tothe
auxiliary input. Useful for operating remote devices
when oil temperature has elevated to operating tem-
peratures. Default is 167.
AUX INPUT SelectDIS= disabled, ALM= alarm only, SHT=alarm
and shutdown . Default is DIS. The LED below the
compressor on the graphic map will flash and AUX-
ILIARY INPUT will be displayed when contact
J1-11/J1-16 is opened and function is ALM or SHT.

Section 3
PROGRAMMING PROCEDURES
11
3.2 FACTORY PROGRAMMING (Continued)
PARAMETER (IN SEQUENTIAL ORDER) OPERATION
ENABLE DEFAULT When OFF is selected, the analog display selected
will remain until that key is pressed again. the 5 se-
cond time out is defeated. Default is OFF.
ENABLE USER Default is OFF. This overrides certain programmable
features in the user programming mod. Change to
ON to enable. Protected parameters are:Language
Units
Max Press P2 A,B,C
Diff Press P2 A,B,C
UNLOAD TIME
WYE DELTA TIME
DRAIN TIME
INTERVAL TIME
RESTART TIME Adjustable from 0 to 120 sec. Default time is 0 sec.
Select a different value to delay auto-restart of com-
pressor following a sustained power loss. Useful for
staggering the startup ofmachines set in abase/load
configuration.
ENABLE T4 Select ON if machine is a tandem, otherwise select
OFF. When OFF, the fourth temperature input is ig-
nored. Default is OFF.
DPI OFFSET Adjustable from 2.14bar to 30psid 2.1 bar. Normally
setat2,ifP2istobesensed downstream ofadditional
pressure drops, determine the difference by measur-
ing the full load pressure at both points. Change the
offset by this measured differential. this will allow
proper monitoring of separator condition even
though P2 is sensed at a remote location.

Section 4
START---UP PROCEDURES
12
4.1 MOTOR ROTATION DIRECTION CHECK
After the electrical wiring has been done, it is nec-
essary to check the direction of the motor rotation.
With the control system in MANUAL mode, press
the ON/OFF pad twice in succession to bump start
the compressor. When looking at the motor from
the end opposite the compressor unit, the shaft
should be turning counterclockwise for direct drive
packages and clockwise forgear driven packages.
If the motor shaft is not turning in the proper direc-
tion, disconnect the power to the starter and ex-
change any two of the three motor leads, then re---
check rotation. A “Direction of Rotation” decal is lo-
cated on the coupling guard between the motor
and compressor to show proper motor/compres-
sor rotation.
4.2 INITIAL START---UP PROCEDURE
The following procedure should be used to make
the initial start---up of the compressor:
1. Read the preceding pages of this manual thor-
oughly.
2. Be sure that all preparations and checks de-
scribed in the Installation Section have been
made.
3. Crack open the shut off valve to the service line.
4. Set the compressor in MANUAL mode and start
the compressor by pressing the ON/OFF pad.
5. Check for possible leaks in piping.
6. Slowly close the shut---off valve and check that
the maximum pressure (P2)and pressure differ-
ential (P2) are correctly programmed.
7. Observe the operating temperature. If the oper-
ating temperature exceeds 205_F(96
_C), the
cooling system or installation environment
should be checked.
8. Observe return line sight glasses and mainte-
nance indicators.
9. Open shut---off valve to service line.
10. Reinspect the compressor for temperature and
leaks the following day.
4.3 SUBSEQUENT START---UP PROCEDURE
On subsequent start---ups, check that the proper
level is visible in the fluid sight glass and simply
press the ON/OFF pad. When the compressor is
running, observe the control panel for mainte-
nance indications.
4.4 SHUTDOWN PROCEDURE
To shut the compressor down, simply press the
ON/OFF pad. If STOP MODE TIME is enabled, a 0
--- 30 sec. delay before shutdown will occur when
ON/OFF pad is pressed. This may be overriden by
pressing “EMERGENCY STOP”.

Section 5
MAINTENANCE AND TROUBLESHOOTING
13
5.1 CONTROL SYSTEM ADJUSTMENT
RefertoFigure 2---1.Before starting the compres-
sor, but with power applied, press the PROG pad
on the Supervisor panel three times to enter the
PROGRAMMING mode. Continue pressing the
PROG pad until “MAX PRESS P2A” is displayed.
Use the cursor (UP arrow) pad to set the desired
UNLOAD pressure (110 PSIG [7.6 bar]). Note that
pressing the pad for over 2 seconds will initiate fast
scrolling of the value being set.
Once thecorrect value is selected, press the PROG
pad to proceed to thedisplay “PRES DIF P2A”. This
value is used to set the LOAD pressure where the
compressor will begin building pressure (10 PSID
[0.7 bar]). This will provide LOAD/UNLOAD opera-
tion at 100 to 110 PSIG [6.7 to 7.6 bar]). These val-
ues will be entered when the display is returned to
operating mode condition by continuing to press
PROG through the end of the PROGRAMMING
menu or allowing the display to automatically re-
turn to operating mode status after 5 seconds ofin-
activity.While scrolling with the PROGpad, all exist-
ing user programmable values will be displayed.
5.2 MESSAGE DISPLAY DEFINITIONS
In addition to programming prompts, the 20---char-
acter electro---luminescent display provides infor-
mation regarding machine status and trouble con-
ditions. These messages can be displayed in any
one of five languages; English, French, Spanish,
German or Italian. The following table explains
what each message means asit relates tothe com-
pressor.
MESSAGE DISPLAY DEFINITIONS
MACHINE STATUS MESSAGES EXPLANATION
MANUAL SHUTDOWN The machine is ready to be started. Machine
control is powered up; permissives are made;
machine has been stopped via the ON/OFF
pad, the remote start/stop contact (if the
RUNNING LED is flashing), or acomputer com---
mand through the RS232 port.
STANDBY The machine is in AUTOMATIC mode and a
start was initiated, but either the line pressure
P2 is higher than the LOAD setpoint or sump
pressure P1is higher than 14.5 PSIG (1 bar). Ma-
chine start will occur when these pressures are satis---
fied.
ON LOAD The compressor is running and P2 is less than
the UNLOAD setpoint. The LOAD/UNLOAD
solenoid valve relay (output J10/50---51) is en---
ergized. The compressor is attempting to meet
the system air demand.
OFF LOAD The compressor is running and P2 has exceed---
ed UNLOAD setpoint, but has not dropped
below the LOAD setpoint (DIFF PRESS P2). The
UNLOAD solenoid valve relay is deenergized
and the compressor is unloading.
STOP MODE (OPTIONAL) The machine is in AUTOMATIC or MANUAL
mode and a stop command has been initiated
either via the ON/OFF pad or the remote
STOP/START contact (J1/1---2). This mode runs
the compressor for 0 to 30 seconds with the
LOAD/UNLOAD valve relay deenergized before
stopping.

Section 5
MAINTENANCE AND TROUBLESHOOTING
14
5.3 TROUBLE INDICATION SETPOINTS
CONDITION/DISPLAY CAUSE
P1 High Discharge Pressure Shutdown Default is 135 PSIG (9.3 bar), factory settable for
HIGH PRESSURE P1 high pressure machines.
50 (3.5 bar) --- 200 PSIG (13.8 bar)
Machine will shut down and must be cleared
and reset by pressing ON/OFF once before
restart is possible.
P1 High Discharge Pressure Prealarm Indicates at 98% of Max Press P1.
HIGH PRESSURE P1
Failure to Run, P1 Pressure Loss Since no run contact is used to indicate run
PRESSURE LOSS status, the Supervisor examines P1 pressure
to see if a minimum of 14.5 PSIG (1 bar) is being
produced when the RUN output is energized.
Reading is overridden for 1 minute at startup.
Low Oil Pressure P3 Shutdown Min PressP3 isfactory preset at 10PSIG. (.7bar)
(Injection Oil Pressure) Factory adjustable 3 (.2 bar) --- 145 PSIG (10
bar). Requires
LOW PRESSURE P3 clearing of shutdown by pressing ON/OFF once
to reset.
Low Oil Pressure P3 Prealarm Set for 5 PSIG (.3 bar) above Min Press P3. Not
LOW PRESSURE P3 latching.
High Temperature T1 Shutdown Pre---programmed shutdown at 235_F (113_C).
(Compressor Discharge Temperature) Requires ON/OFF reset to clear.
HIGH TEMPERATURE T1
High Temperature T1 Prealarm Pre---programmed indication at 225_F (107_C).
HIGH TEMPERATURE T1 Not latching.
High Temperature T2 Shutdown Pre---programmed shutdown at 235_F (113_C).
(Injection Oil Temperature)
HIGH TEMPERATURE T2
High Temperature T3 Shutdown Pre---programmed indication at 225_F (107_C).
(Dry---side Discharge Temperature) Not latching.
HIGH TEMPERATURE T3
High Temperature T4 Shutdown Pre---programmed shutdown at 235_F (113_C).
(Tandem Interstage Temperature)
HIGH TEMPERATURE T4
P1 --- P4 Shorted Sensor Shutdown Signal voltage > 4.82 volts (196 PSIG) 13.5 bar.
SHORT CIRC Px SENDER
P1 --- P4 Open Sensor Shutdown Signal voltage < 0.15 volts.
OPEN CIRC Px SENDER
T1 --- T4 Shorted Sensor Shutdown Resistance < 81 ohms (---45_C).
SHORT CIRC Tx SENDER
T1 --- T4 Open Sensor Shutdown Resistance >176 ohms (200_C).
OPEN CIRC Tx SENDER
Inlet Filter Maintenance Required Vacuum Switch connected to J1/5---6 and
AIR FILTER MAINT RQD preset for 22” (56cm) WC. Indicates when inlet
filter is too dirty for proper air flow. Not
latched and not a shutdown condition.
Separator Maintenance Required Calculated: P1 --- P2 --- 2PSIG (.14bar)onlyafter
1 minute SEPARATOR MAINT RQD of sustained high differential.
Preset to warn at 10 PSIG (.7 bar). Warning will
occur. Offset differential is programmable. Not
latched and not a shutdown condition.

Section 5
MAINTENANCE AND TROUBLESHOOTING
15
5.3 TROUBLE INDICATION SETPOINTS (Cont’d.)
CONDITION/DISPLAY CAUSE
Oil Filter Maintenance Required Calculated: P4 --- P3. Preset at 20 PSIG. (1.38
bar) P4
OIL FILTER MAIN RQD is located on the high pressure side of the
oil filter. P3 is the injection oil pressure on the
low pressure side of the oil filter. Not latched,
not a shutdown condition.
Emergency Stop Indicates if Emergency Stop button is depress---
EMERGENCY SHUTDOWN ed or if optional sensors wired in series with
the E---Stop button and its master control relay
are open. Must be cleared and reset by press---
ing ON/OFF once.
Fan Overload/Low Water Pressure Shutdown of canopy or cooler fan motor
FAN OL/LOW WATER overload as well as water pressure switch for
water---cooled machines. Normally closed
contact wired to J1/9---10. (Water pressure
switch is normally open and closes with 10
PSIG (.7 bar) minimum water pressure. Fault
must be cleared and reset by pressing ON/OFF pad
once.
5.4 TROUBLESHOOTING
The information contained in the Troubleshooting
chart has been compiled from field report data and
factory experience. It contains symptoms and
usual causes for the described problems. Howev-
er, DO NOT assume that these are the only prob-
lems that may occur. Consult factory forsymptoms
and resolutions to other problems. All available
data concerning the trouble should be systemati-
cally analyzed before undertaking any repairs or
component replacement procedures.
A detailed visual inspection is worth performing for
almost all problems and may avoid unnecessary
additional damage to the compressor/controller.
a. Check for loose wiring.
b. Check for damaged piping.
c. Check forparts damaged by heat or anelectrical
short circuit, usually apparent by discoloration
or a burnt odor.
Should your problem persist after making the rec-
ommended check, consult your nearest Sullair Dis-
tributor or the Sullair Corporation factory Service
Department.

Section 5
MAINTENANCE AND TROUBLESHOOTING
16
5.4 TROUBLESHOOTING GUIDE
SYMPTOM PROBABLE CAUSE REMEDY
COMPRESSOR WILL NOT
START Main Disconnect Switch Open
Line Fuse Blown
Control Transformer Fuse Blown
Motor Starter Overloads Tripped
Low Incoming Line Voltage
Supervisor Panel Fuse is Blown
Close switch.
Replace fuse.
Replace fuse.
Reset. Should trouble persist, check whether mo-
tor starter contacts are functioning properly.
Check voltage. Should voltage check low, con-
sult power company.
Replace fuse.
Replace Supervisor controller if no display or er-
ratic display.
COMPRESSOR SHUTS DOWN
WITH AIR DEMAND PRESENT Loss of Control Voltage
Low Incoming Voltage
Excessive Operating Pressure
“High Temp T1“ or “T3” Message Dis-
played
Reset. If trouble persists, check thatline pressure
does not exceed maximum operating pressure of
the compressor (specified on nameplate).
Consult power company. The Sullair Supervisor
will provide indication of most maintenance prob-
lems if control power has not been lost. Shut-
downs will occur upon a faulty condition or abad
sender condition.
Check maximum P2 pressure setting.
“High Press P1” display; Max P1 pressure may
be set too low. Consult factory for recalibration.
Defective solenoid valve; solenoid valve should
cause control lever to move to unload stop when
the load/unload relay contact opens. Repair if de-
fective.
Defective blowdown valve; blowdown valve
should exhaust sump pressure to 40 to 50 PSIG
(2.8 bar to 3.4 bar) when maximum operating
pressure is reached. Repair if defective.
Open or shorted P1, P2, P3 or P4 sender mes-
sage; replace sender indicated.
Cooling watertemperature toohigh; increase wa-
ter flow (water---cooled only).
Cooling water flow insufficient; check water lines
and valves (water---cooled only).
Cooler plugged; clean tubes. If plugging per-
sists, install water conditioner (water---cooled
only).
Cooling air flow restricted; clean cooler and
check for proper ventilation.
Ambient temperature is too high; provide suffi-
cient ventilation.
Low fluid level; add fluid.
Clogged filter; change the fluid filter element as
indicated by Supervisor control.
Thermal valve not functioning properly; replace
element (air---cooled only).
Water flow regulating valve not functioning prop-
erly; change (water---cooled only).
Open or shorted T1 or T2 sender; check for a
short or open circuit to probe and correct wiring.
Table of contents
Other Sullair Controllers manuals

Sullair
Sullair 02250160-842 User manual
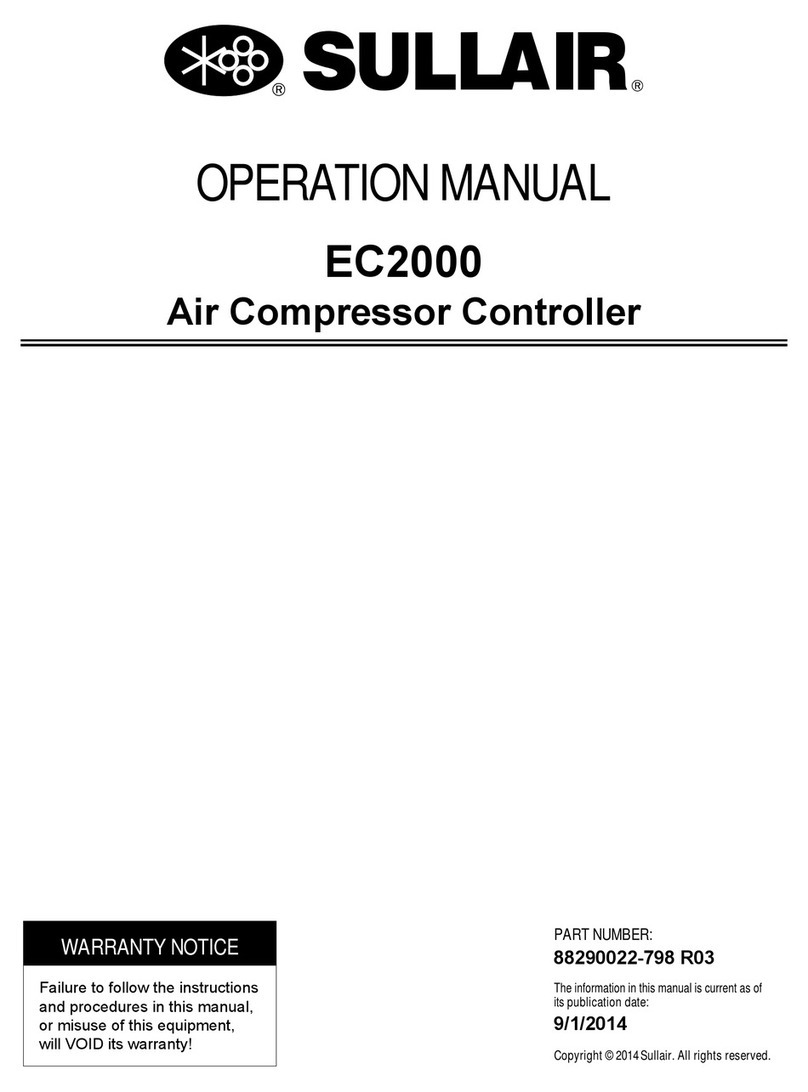
Sullair
Sullair EC2000 User manual
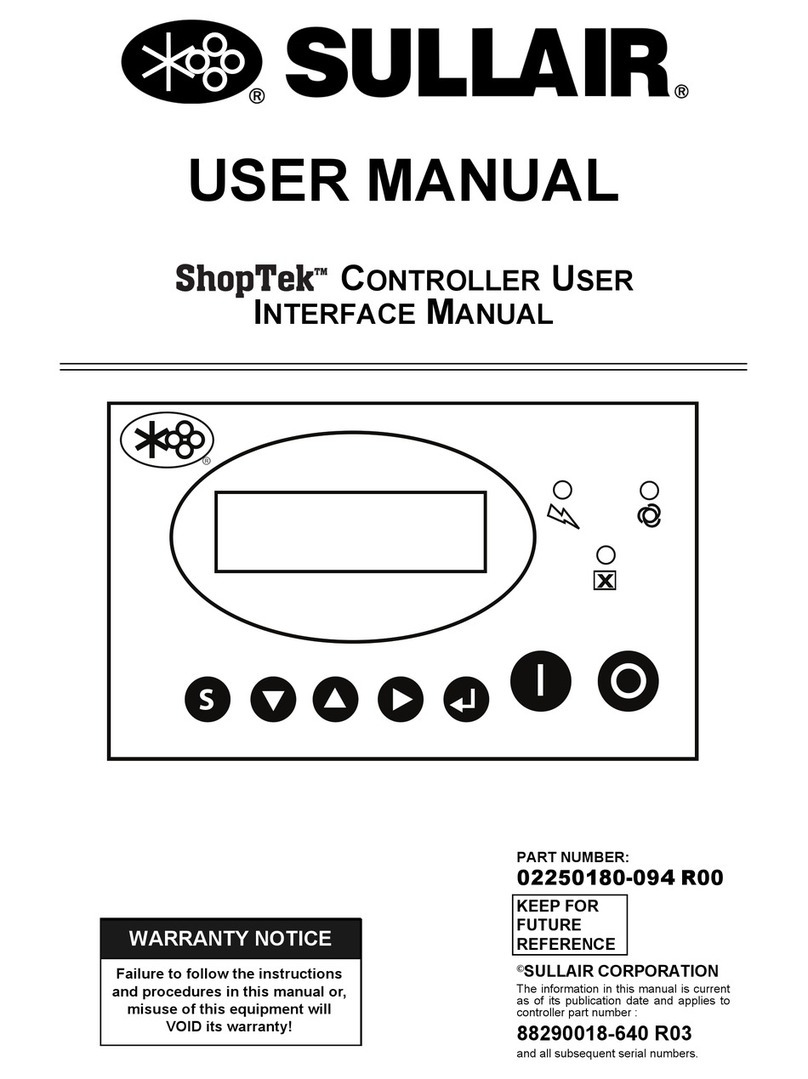
Sullair
Sullair ShopTek User manual

Sullair
Sullair 900 User manual
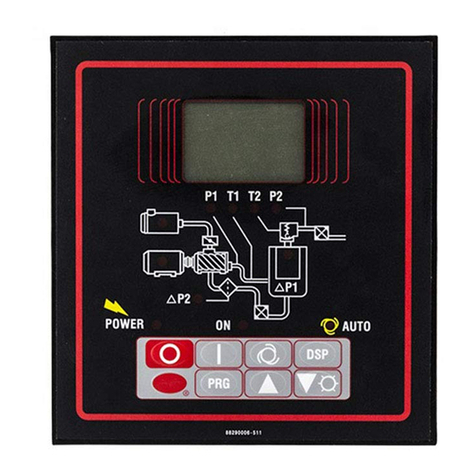
Sullair
Sullair SUPERVISOR CONTROLLER User manual
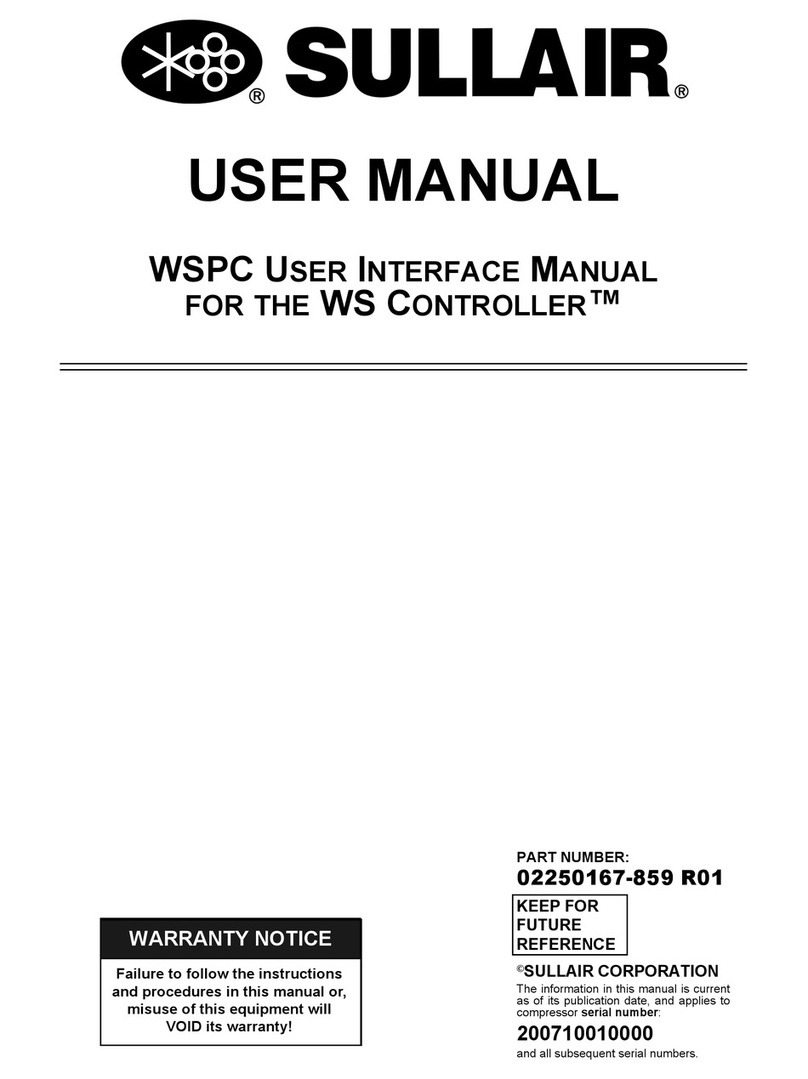
Sullair
Sullair WSPC User manual
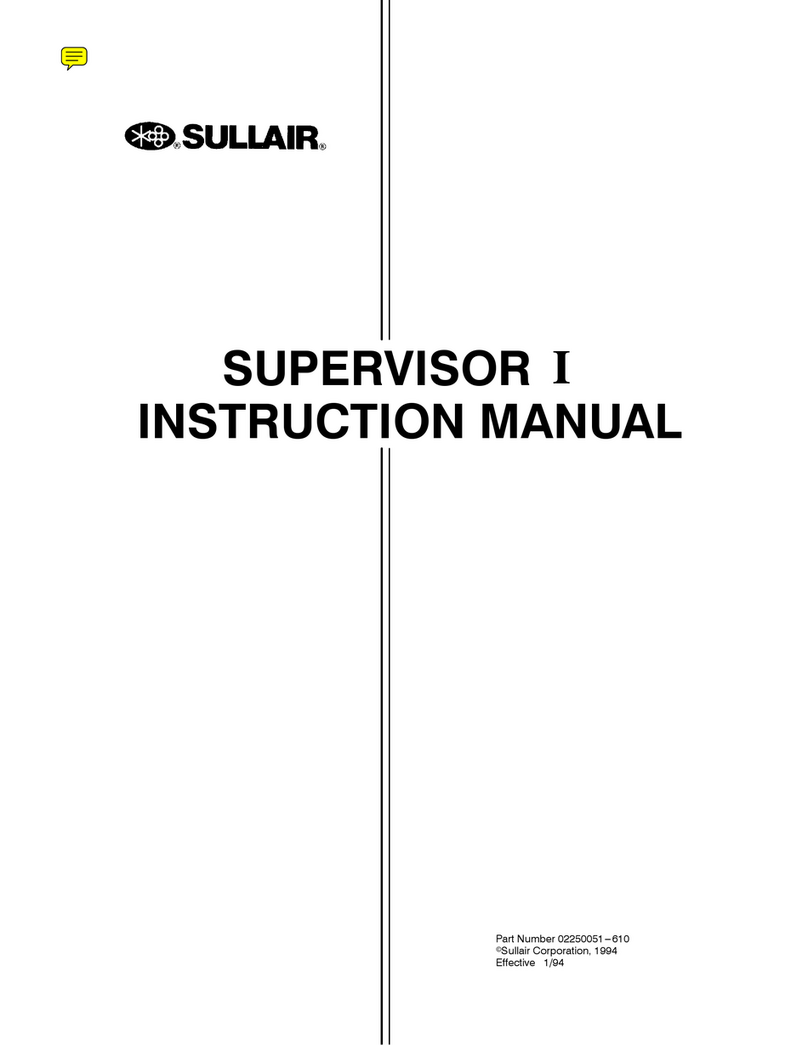
Sullair
Sullair SUPERVISOR I User manual
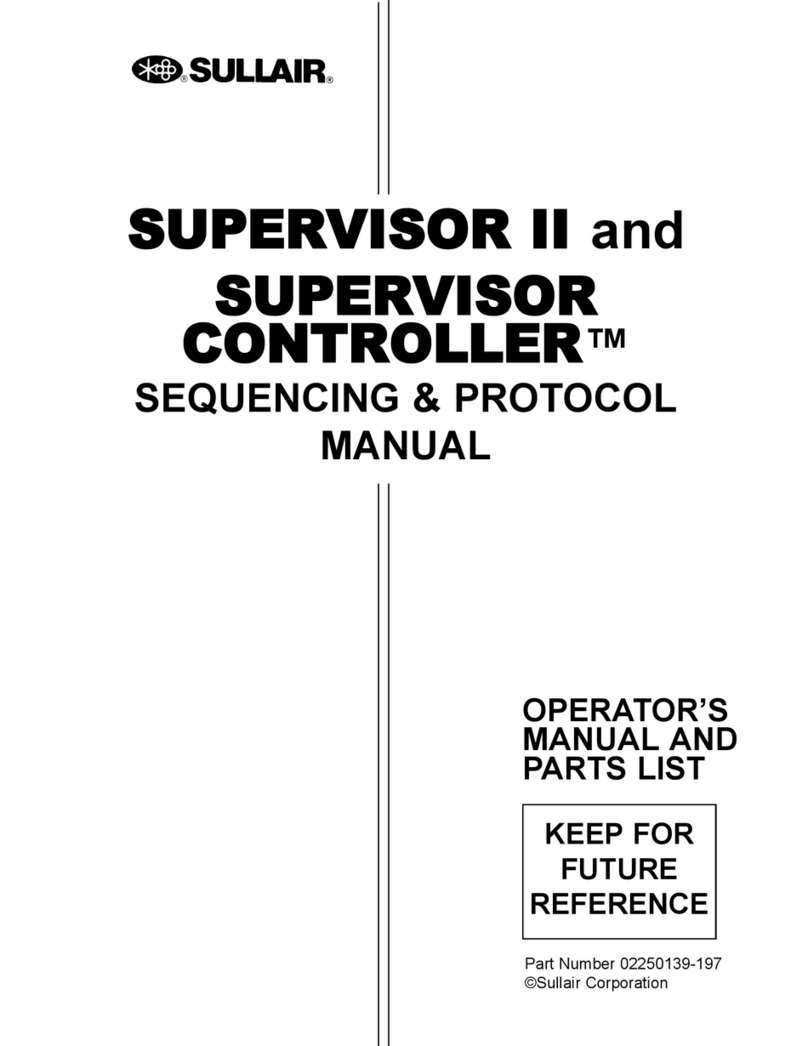
Sullair
Sullair SUPERVISOR II Series User manual
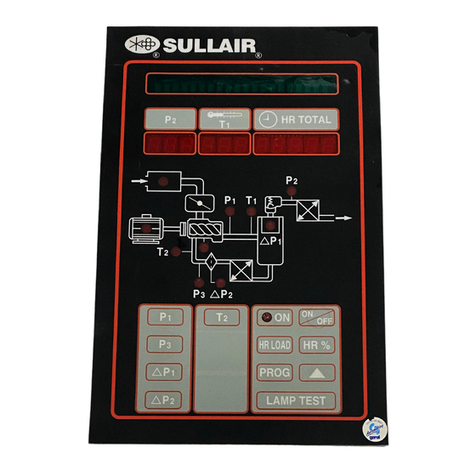
Sullair
Sullair SUPERVISOR CONTROLLER User manual

Sullair
Sullair 02250165-411 R01 User manual
Popular Controllers manuals by other brands
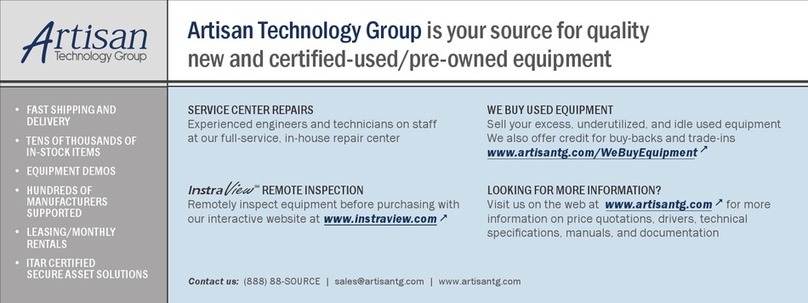
YASKAWA
YASKAWA MotionSuite MP940 Hardware manual
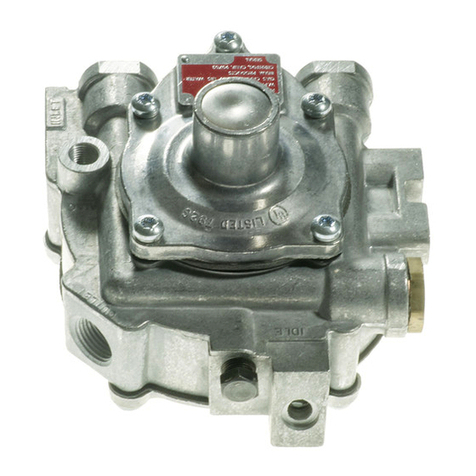
Impco
Impco T60 Repair instructions
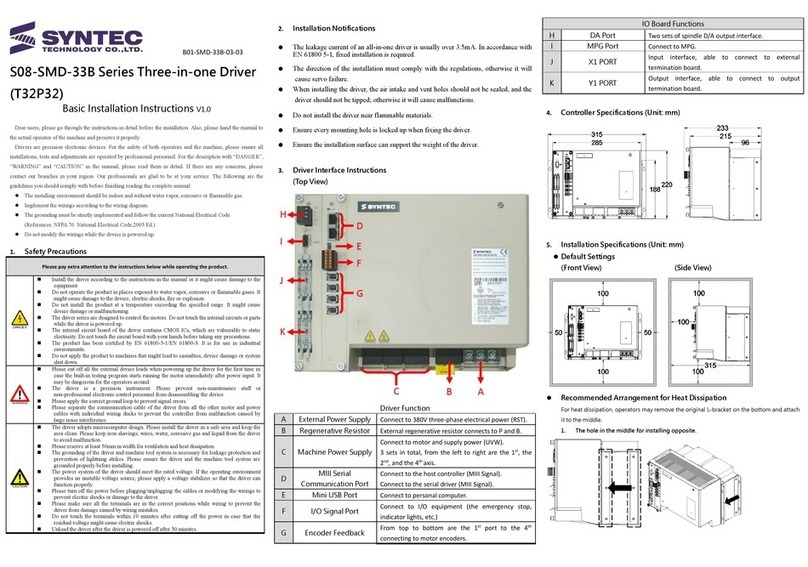
Syntec
Syntec S08-SMD-33B Series installation instructions

Omron
Omron CQM1H - 08-2005 Replacement guide
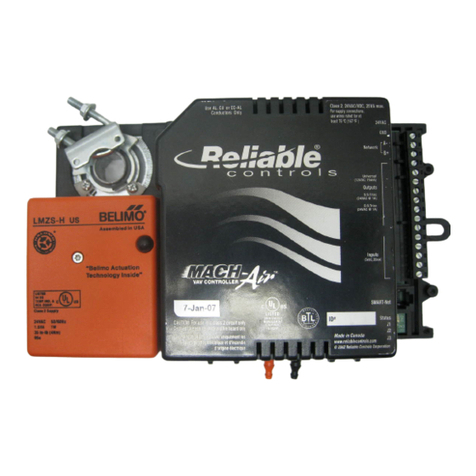
Reliable Controls
Reliable Controls MACH-Air quick start guide
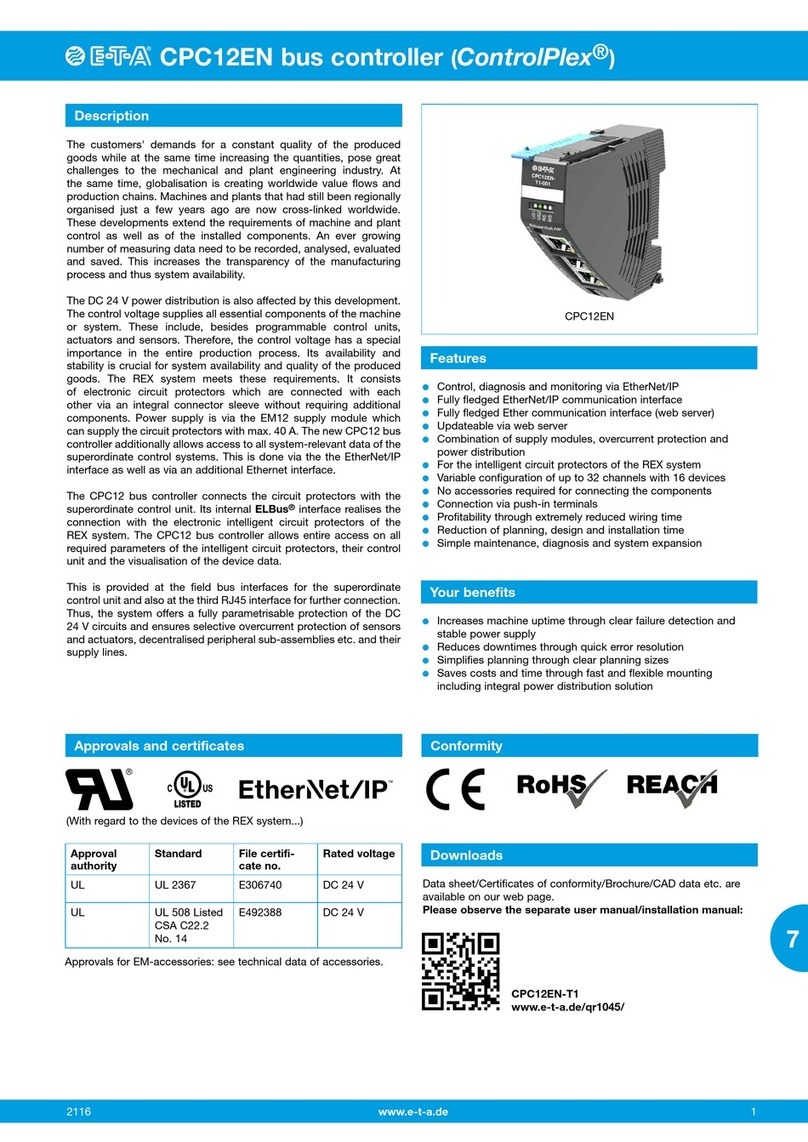
E-T-A
E-T-A EtherNetIP ControlPlex CPC12EN quick start guide