TLV QuickTrap FX1 User manual

FX1
FX1
Trap Unit
X1
INSTRUCTION MANUAL
Keep this manual in a safe place for future reference
F46+F32
Copyright (C) 2019 by TLV CO., LTD. All rights reserved.
881 Nagasuna, Noguchi, Kakogawa, Hyogo 675-8511, Japan
Manufacturer
Tel: [81]-(0)79-422-1122 Fax: [81]-(0)79-422-0112
Option
BD2
( )
UNIVERSAL TEMPERATURE CONTROL STEAM TRAP

Introduction
Before beginning installation or maintenance, please read this manual to ensure correct use of
the product. Keep the manual in a safe place for future reference.
The FX1 temperature control steam trap (connector body unit F46 or former connector unit F32*
and steam trap unit X1) with built-in scale removal function is suitable for the accurate control of
condensate discharge temperatures for applications with operating pressures up to 2.1 MPaG
(300 psig).
DO NOT USE on any application except steam tracing lines, storage tank coils and instrument
enclosures.
Note: The FX1 can only control the temperature of condensate discharge from the trap; it cannot
control product temperature nor the temperature of condensate backing up in the system.
* Configuration of F32 differs slightly from that of F46
1 MPa = 10.197 kg/cm2, 1 bar = 0.1 MPa
For products with special specifications or with options not included in this manual, contact TLV
for instructions.
The contents of this manual are subject to change without notice.
Continued on next page
1. Safety Considerations
• Read this section carefully before use and be sure to follow the instructions.
• Installation, inspection, maintenance, repairs, disassembly, adjustment and valve
opening/closing should be carried out only by trained maintenance personnel.
• The precautions listed in this manual are designed to ensure safety and prevent equipment
damage and personal injury. For situations that may occur as a result of erroneous handling,
three different types of cautionary items are used to indicate the degree of urgency and the
scale of potential damage and danger: DANGER, WARNING and CAUTION.
• The three types of cautionary items above are very important for safety; be sure to observe
all of them, as they relate to installation, use, maintenance, and repair. Furthermore, TLV
accepts no responsibility for any accidents or damage occurring as a result of failure to
observe these precautions.
Indicates an urgent situation that poses a threat of death or serious injury.
Indicates a DANGER, WARNING or CAUTION item.
Indicates that there is a potential threat of death or serious injury.
WARNING
DANGER
CAUTION Indicates that there is a possibility of injury, or equipment/product
damage.
CAUTION
Install properly and DO NOT use this product outside the
recommended operating pressure, temperature and other specification
ranges. Improper use may result in such hazards as damage to the product
or malfunctions, which may lead to serious accidents. Local regulations
may restrict the use of this product to below the conditions quoted.
Take measures to prevent people from coming into direct contact
with product outlets. Failure to do so may result in burns or other injury
from the discharge of fluids.
Always wear heat-insulated gloves when handling products with high
body temperatures, such as when in operation. Failure to do so may
result in burns
.

A
D
H
F
C
B
E
B
I
C
G
E
H
J
D
A
F
CAUTION The pressure and temperature values displayed on the nameplate of
the connector body are the values for the connector body itself and
not for the entire trap.
Improper use may result in such hazards as damage to the product or
malfunctions that may lead to serious accidents.
DO NOT disassemble or remove this product or use the scale
removal function while it is under pressure. Allow internal pressure of
this product to equal atmospheric pressure and its surface to cool to
room temperature before disassembling, removing or using the scale
removal feature. Failing to do so could cause burns or other injury.
Be sure to use only the recommended components when repairing
the product, and NEVER attempt to modify the product in any way.
Failure to observe these precautions may result in damage to the product
or burns or other injury due to malfunction or the discharge of fluids.
Use under conditions in which no water hammer will occur. The
impact of water hammer may damage the product, leading to fluid
discharge, which may cause burns or other injury.
Use only under conditions in which no freeze-up will occur. Freezing
may damage the product, leading to fluid discharge, which may cause
burns or other injury.
2. Specifications
* Maximum allowable pressure (PMA) and maximum allowable temperature (TMA) are
PRESSURE SHELL DESIGN CONDITIONS, NOT OPERATING CONDITIONS.
** Valve No. is displayed for products with options. This item is omitted from the nameplate
when there are no options.
*** Set pressure and set temperature are the initial settings when shipped from the factory.
Refer to the product nameplate on the trap unit for detailed specifications.
A nameplate is also mounted on the F46 connector unit. The specifications displayed on the
nameplate are the values for the connector body itself. When a trap unit is installed, the
PMA/TMA and PMO/TMO are limited to the trap unit specifications.
To avoid malfunctions, product damage, accidents or serious injury,
install properly and DO NOT use this product outside the specification
range. Local regulations may restrict the use of this product to below the
conditions quoted.
CAUTION
A: Model
B: Nominal Diameter
C: Max. Allowable Press.*
D: Max. Allowable Temp.* (TMA)
E: Max. Operating Press.
F : Max. Operating Temp. (TMO)
G
: Valve No.**
H: Production Lot No.
I : Set Pressure***
J : Set Temperature***
Trap UnitConnector Unit (mounted only on F46)
2

3. Configuration
Replacement parts are available only in the following kits: M = Maintenance Parts, R = Repair Parts, T = Trap Unit
Description
Trap Body
Cover
Valve Stem
Adjusting Screw
Bimetal Element
Washer
Valve Seat
Valve Seat Gasket
Overexpansion Spring
Return Spring
Snap Ring
Spring Pin
RM T
No.
1
2
3
4
5
6
7
8
9
10
11
12
Description
Seal Ring
Screen
Locknut
Cap Nut
Cover Gasket
Nameplate
(Trap Unit)
Spring Guide
Thrust Plate
Cap Nut Gasket
Connector Flange
Snap Ring
RM T
No.
13
14
15
16
17
18
19
20
21
22
23
Description
Outer Connector Gasket
Inner Connector Gasket
Connector Body
Screen
Screen Holder Gasket
Screen Holder
Connector Bolt
Flange
Nameplate
(Connector Unit)
Caution Plate A
Caution Plate B
RM T
No.
24
25
26
27
28
29
30
31
32
A
B
Replacement parts for F32 differ from those for F46. When ordering replacement parts, please include the trap unit name,
size, connection type and also the connector unit name.
32
29
2826
9
22
8
11
6
10
19
1
20
6
14
2
12
21
7
16 15
4 A 3
13
B
17 18 23 24 25
27
5
30
31
3

4. Exploded View
CAUTION
DO NOT DISASSEMBLE OR REMOVE THIS
PRODUCT OR USE THE SCALE REMOVAL
FUNCTION WHILE IT IS UNDER PRESSURE.
Allow internal pressure of this product to equal
atmospheric pressure and its surface to cool
to room temperature before disassembling,
removing or using.
13
12
16
21
24
30
27
28
29
26
25
22
15
17
20
10
11
19
14
2
3
6
6
9
7
8
5
4
32
18
Cover Unit
Valve Unit
Cover Unit
Valve Unit
The X1 trap unit is designed for use with TLV
F46 and F32 connector units and TLV V1/V2/V1P/V2P
Series trap stations. It is not compatible with TLV F46J
connector unit. The connector unit
name is indicated on the connector body.
* Trap Unit X1
** Connector Body Unit
F46 or F32
*
*
*
*
*
*
*
*
*
*
1*
* *
23
* **
**
**
**
**
*
*
*
*
*
*
*
*
*
*
*
*
*
Do not remove snap ring used to fix the connector flange.
TLV
4

6. Proper Installation
• Installation, inspection, maintenance, repairs, disassembly, adjustment
and valve opening/closing should be carried out only by trained
maintenance personnel.
CAUTION
Note: For socket weld connections, use electric arc welding with a single pass. As internal
parts are not damaged by one pass welding, there is no need to remove them before welding.
1. In some instances, the trap unit and the connector body are sent as separate units. When
attaching them together, make sure the connector gaskets are still in place after having
removed their protective seal (See page 10 for details).
2. There are no restrictions on the installation direction beyond the following conditions:
a. The arrow on the connector body must point in the direction of condensate flow.
b. The connector body must be adjusted so that the connector flange face (for connecting
to the trap unit) is in the vertical plane.
c. The caution plates on the trap unit must face upward.
3. Before installation, be sure to remove all protective seals.
4. Before installing the trap, blow out the inlet piping to remove all dirt and oil.
5. Verify that piping is of a suitable diameter.
6. Support the pipes properly within 800 mm (2.5 ft) on either side of the trap.
7. Install in a place where caution plates (including cap) can clearly be seen during periods of
maintenance, in the lowest part of the pipeline so that condensate flows into the trap by
gravity.
8. Install inlet and outlet valves to isolate the product in event of trap failure or maintenance.
9. If the product is subject to back pressure, install a check valve.
10. Open the inlet valve gradually and make sure that the product functions properly.
• Take measures to prevent people from coming into direct contact with
product outlets.
• Install for use under conditions in which no freeze-up will occur.
• Install for use under conditions in which no water hammer will occur.
Installation Examples: Horizontal Piping
Correct
Caution plate is not facing upwards.
Universal Connector Flange is not
in the vertical plane.
Incorrect
Ground GroundGround GroundGround
5. Applications
• DO NOT USE on any application except steam tracing lines, storage tank coils and
instrument enclosures.
• SUITABLE for steam tracing lines or storage tank coils ONLY IF the required product
viscosity will be maintained when the condensate is sub-cooled at least 15 °C (27 °F), even to
the
point of the condensate having a lower temperature than the product temperature.
• SUITABLE for use on instrument enclosures ONLY IF the steam or condensate temperature
in the enclosures will NOT damage the instrument.
Caution
Plate
Connector
Flange

8. Adjusting Temperature Setting
• To prevent possible injury, always relieve pressure from trap before
opening to adjust the temperature setting.
• Always wear heat-insulated gloves and eye protection when handling pro-
ducts exposed to high temperatures. Failure to do so may result in burns.
CAUTION
The temperature setting can be easily adjusted.
7. Operational Check
A visual inspection can be carried out to aid in determining the necessity for immediate
maintenance or repair, if the trap is open to atmosphere. If the trap does not discharge to
atmosphere, use diagnostic equipment such as a stethoscope, thermometer, TLV Pocket
TrapMan or TrapMan (within its pressure and temperature measurement range).
(When conducting a visual inspection, flash steam is sometimes mistaken for steam leakage. For
this reason, the use of a steam trap diagnostic instrument such as TLV TrapMan is highly
recommended.)
Normal: Condensate is being discharged from the discharge outlet. (The surface temperature
of the trap should be about 10 to 20 °C (20 to 40 °F) lower than the set temperature.)
Blocked: No condensate is discharged and the surface temperature of the trap is low.
Blowing: Live steam continually flows from the outlet and there is a continuous hissing sound
of flow. The surface temperature of the trap is higher than the set temperature.
Instructions for Adjusting Temperature Setting
1. First close the external valve from which the steam and condensate flow to the trap (the
“inlet isolation valve”), followed by then closing the external valve to which the condensate
flows from the trap (the “outlet isolation valve”). Wait until the pressure between the inlet
isolation valve and the trap equals atmospheric pressure (when the trap body temperature
cools to room temperature). Do not remove the cap nut unless the trap is isolated from and
is not subjected to steam pressure.
2. Hold the cover with one wrench and use another wrench to slowly loosen and remove the
cap nut. Remove cap nut slowly to allow any residual pressurized steam to leak from the
trap interior through the threads of the adjustment screw and the cover.
3. Hold the adjusting screw in place with a flat-head screwdriver and remove the locknut
slowly in case of any additional steam leakage.
4. Use a flat-head screwdriver to turn the adjusting screw to adjust temperature. To raise the
temperature setting, turn the adjusting screw counterclockwise. To lower the temperature
setting, turn the adjusting screw clockwise. Refer to the set temperature adjustment chart
for the number of turns required from the "0" position to reach the desired temperature.
5. After completing the adjustment, replace the locknut. Hold the adjusting screw in place with
a flat-head screwdriver and tighten the locknut securely.
6. Replace the cap nut and tighten it to the proper torque (see page 10).
7. First fully open the outlet isolation valve, followed by then slowly opening the inlet isolation
valve – carefully checking for any steam leaks that might occur. In the event steam leaks are
detected, immediately close the inlet isolation valve, then the outlet isolation valve, and
repair the source of leakage.
8. Check the temperature setting by observing an inline temperature sensor or by measuring
the temperature at the wrench flat on the trap’s inlet side at least 30 minutes after supplying
steam with the new setting. The trap set temperature will be approximately 10 to 20 °C (20
to 40 °F) higher than the surface reading. If the resultant temperature is not as desired,
repeat procedure from step “1” above.
Caution
Plate
Connector
Flange
Installation Examples: Vertical Piping
Correct Incorrect
Caution plate is not facing upwards.
Ground Ground Ground
6

1. Start at the standard factory setting (point A) (100 °C at 0.9 MPaG, 9 barg; 212 °F at 130 psig).
2. Move up or down vertically to the desired set temperature (point B).
3. Follow the set temperature line in either direction to the vertical line corresponding to the
actual operating steam pressure (point C).
4. Follow the horizontal line to where it meets the left side of the chart (point D), indicating the
number and direction of turns required. (- turn: clockwise, + turn: counterclockwise)
Set Temperature Adjustment Chart
The trap can be set to open at any temperature between 50 °C and 200 °C (120 °F and 390 °F)
provided the set temperature is at least 15 °C (27 °F) below saturated steam temperature.
To determine the number and direction of adjusting screw turns required for the desired set
temperature, refer to the charts below.
-
turn: clockwise, + turn: counterclockwise
Standard "0" position = 100
˚
C at 0.9 MPaG, 9 barg; 212
˚
F at 130 psig
1 MPa = 10.197 kg/cm2= 10 bar
Adjusting
Screw
Adjuster Slot
Cover
A
B
Standard Factory Setting ("0" Position):
The standard "0" position is the position where point (A), the
bottom of the adjusting screw slot is even with point (B), the
top surface of the cap.
FX1
100 °C at 0.9 MPaG (9 barg),
212 °F at 130 psig
Temperature Setting Range
1 MPa = 10.197 kg/cm2= 10 bar
Set Temperature (˚F)
Operating pressure (psig)
Set Temperature (˚C)
Operating Pressure (MPaG)
0.20.1 0.3 0.5 0.7 1 2.1
200
150
100
50 15 20 30 50 100 200 300
390
300
200
120
15 ˚C below saturated
steam temperature
27 ˚F below saturated
steam temperature
Operating Pressure (psig)
Number of Turns of Adjusting Screw
Operating Pressure (MPaG)
Number of Turns of Adjusting Screw
Set Temperature (˚C)
Set Temperature (˚F)
200
190
180
170
160
150
140
130
120
110
100
90
80
70
60
50
0.20.1 0.3 0.5 0.7 1.51 2.1
B
A
C
D
B
A
C
D
10 30 50 100 150 200 300
390
380
360
340
320
300
280
260
240
220
210
200
180
160
140
120
B
A
CD
B
A
CD
-21/2
+21/2
+31/2
+41/2
-11/2
+11/2
-1/2
+1/2
-2
-1
+1
+2
+3
+4
+5
0
+
-
-21/2
+21/2
+31/2
+41/2
-11/2
+11/2
-1/2
+1/2
-2
-1
+1
+2
+3
+4
+5
0
+
-

9. Cleaning Function
Rust, scale and other buildup on the valve seat may hinder the sealing ability of the steam trap
and cause steam leakage and resultant higher product temperature; or block the valve seat
opening - thereby preventing condensate discharge and resultant lowered product temperature.
The FX1 contains a built-in cleaning device that can be used without removing the trap from the
line. Follow the steps below to remove contaminant accumulation from around the valve opening.
• To prevent possible injury, always relieve pressure from trap before
opening to clean the trap.
• Always wear heat-insulated gloves and eye protection when handling pro-
ducts exposed to high temperatures. Failure to do so may result in burns.
CAUTION
Cleaning Function Instructions
1. First close the inlet isolation valve, followed by then closing the outlet isolation valve. Wait
until the pressure between the inlet isolation valve and the trap equals atmospheric pressure
(when the trap body temperature cools to room temperature). Do not remove the cap nut or
the cover unless the trap is isolated from and is not subjected to steam pressure.
2. Hold the cover with one wrench and use another wrench to slowly loosen and remove the
cap nut. Remove cap nut slowly to allow any residual pressurized steam to leak from the trap
interior through the threads of the adjustment screw and the cover. If steam leakage occurs
while loosening cap nut or locknut, disassemble the trap and replace both the
seal ring and the cover gasket (see chapter 10).
3. Hold the adjusting screw in place with a flat-head screwdriver and remove the locknut slowly
in case of any additional steam leakage.
4. Check the current set position of the adjusting screw. Check and record the number of turns
required to return to the standard factory setting (when points (A) and (B) are even with each
other as shown on page 7).
5. Use a flat-head screwdriver to slowly turn the adjusting screw clockwise (to tighten) until it
stops. (This causes the cleaning edge of the stem to reach the valve seat and loosen debris).
6. Slowly turn the adjusting screw counterclockwise (to loosen) until it stops. (This will allow
flushing once the steam is safely turned on using the instructions that follow).
7. Replace the cap nut and tighten it to the proper torque (see page 10).
8. First fully open the outlet isolation valve, and then slowly and carefully open the inlet isolation
valve – checking for any steam leaks. In the event steam leaks are detected, immediately
close the inlet isolation valve, then the outlet isolation valve, and repair the source of leakage.
9. Wait 10 seconds to allow any loose scale to be flushed internally. Be aware of any external
steam leak – including the outlet connection if opened to atmosphere. Be careful to not come
in contact with any steam that is discharging from an open outlet connection. If any steam
leaks are detected elsewhere on the trap or piping, immediately close the inlet isolation valve,
then the outlet isolation valve, and repair the source of leakage.
10. Next, prepare to set the trap temperature again by first isolating the trap and safely relieving
all steam pressure from the trap as follows.
11. First close the inlet isolation valve, followed by then closing the outlet isolation valve. Wait
until the inlet pressure equals atmospheric pressure. (When the trap body temperature cools
to room temperature)
12. Hold the cover with one wrench and use another wrench to slowly remove the cap nut as in
step 2 above.
13. Slowly turn the adjusting screw clockwise (to tighten) to return to the original position
checked in step 4 above.
14. Replace the locknut. Hold the adjusting screw in place with a flat-head screwdriver and
tighten the locknut securely.
15. Replace the cap nut and tighten it to the proper torque (see page 10).
16. First fully open the outlet isolation valve, followed by then slowly opening the inlet isolation
valve – carefully checking for any steam leaks. In the event steam leaks are detected,
immediately close the inlet isolation valve, then the outlet isolation valve, and repair the
source of leakage.
17. Check the temperature setting by observing an inline temperature sensor or by measuring the
temperature at the trap inlet wrench flat at least 30 minutes after supplying steam with the
new setting. The trap set temperature will be approximately 10 to 20 °C (20 to 40 °F) higher
than the temperature reading on the trap body surface. If the resultant temperature is not as
desired, use the above instructions for adjusting temperature settings (see page 9).

Disassembly/Reassembly (to reassemble, follow procedures in reverse)
Disassembly Reassembly
Remove with a socket wrench Consult the table of tightening torques
and tighten to the proper torque
Remove and clean sealing
surfaces
Replace with a new gasket if warped or
damaged
Remove with a spanner or socket
wrench
Reattach and tighten
Remove with a spanner or socket
wrench
Line up spring pin in valve stem with
grooves cut into the adjusting screw as
cover is placed onto the body; consult
the table of tightening torques and
tighten to the proper torque
Remove and clean sealing
surfaces
Replace with a new gasket; coat
surfaces with anti-seize
Locknut 15
Cover 2
Cover Gasket 17
Screw in by using a flat-head
screwdriver
Be careful not to damage the seal ring
during reassembly
Adjusting Screw 4
Remove
Replace with a new seal ring if damaged;
coat with heat resistant silicon grease
Seal Ring 13
Remove from the valve stem Reattach to the valve stemSnap Ring 11
Lift up and off from the valve stem Slide onto the valve stemWasher 6
Remove from the valve stem Place on the valve stemReturn Spring 10
Remove from the valve stem by
lifting up and off
Slide onto the valve stemThrust Plate 20
Lift up and off from the valve stem Slide onto the valve stemWasher (5 sets) 6
Remove the bimetal element from
the valve stem by lifting up and off
Reassemble the bimetal elements,
paying special attention to the proper
orientation (the TLV marks on the
outside, see Exploded View, p. 4)
Bimetal Element
(5 sets of 2 discs) 5
Cap Nut Gasket 21
Part & No.
Connector Bolt
See separate instruction 10.1 See separate instruction 10.1Connector Gaskets
Gasket(s)
Seal Ring
Valve Stem
Bimetal Element
Over-expansion and Return Springs
Check for warping and damage
Check for scratches and wear
Check for scratches and wear
Check for wear and deformation
Check for wear
Check for clogging, corrosion or damage
Check for rust, scale, oil film wear or damage
Check inside for rust and scale
Parts Inspection Procedure
Screen
Valve Seat
Body, Cover
Operational inspections should be performed at least twice per year, or as called for by trap
operating conditions. Steam trap failure may result in temperature drop in the equipment, poor
product quality or losses due to steam leakage.
10. Inspection and Maintenance
CAUTION
Continued on next page
• Installation, inspection, maintenance, repairs, disassembly, adjustment
and valve opening/closing should be carried out only by trained
maintenance personnel.
• Before attempting to open the trap, close the isolation valves and wait
until the trap has cooled completely. Failure to do so may result in burns.
• Be sure to use the proper components and NEVER attempt to modify the
product.
9

NOTE: - Coat all threaded portions with anti-seize.
- If drawings or other special documentation were supplied for the product, any torque
given there takes precedence over values shown here.
Tightening Torque and Distance Across Flats
Part Name & No.
Screen
Holder
(F32) 29
Screwed,
Socket Welded
Flanged
Cap Nut 16
Cover 2
Connector Bolt 30
Valve Seat 7
Screen Holder F46 (all connections and sizes) 29
15, 20 mm ( ”, ”)
25 mm ( 1”)
15 – 25 mm ( ” - 1”)
Torque
(lbf.ft)
(26)
(185)
(28)
(22)
(73)
(43)
(110)
(43)
N.m
35
250
39
30
100
60
150
60
1 N.m 10 kg.cm
〜
〜
Disassembly/Reassembly (to reassemble, follow procedures in reverse)
Disassembly ReassemblyPart & No.
Remove from the valve stem only
if damaged
Replace with new if damagedSpring Pin 12
Remove without bending Reinsert without bendingScreen 14
Remove from the trap body Reinsert
Overexpansion Spring 9
Remove from the trap body Reinsert in the proper orientationSpring Guide 19
Remove with a socket wrench,
being careful not to scratch the
sealing surfaces
Consult the table of tightening torques
and tighten to the proper torque; be
careful not to scratch seating surfaces
Valve Seat 7
Remove and clean sealing
surfaces
Replace with a new gasket; coat
surfaces with anti-seize
Valve Seat Gasket 8
2
1
/
4
3
/
2
1
/
Distance Across Flats
mm
24
46
14
19
30
22
38
22
(in)
( )
(1 )
( )
( )
(1 )
( )
(1 )
( )
4
3
/
16
15
/
16
3
/
16
9
/
16
13
/
8
7
/
2
1
/
8
7
/
10.1 Separating/Attaching Trap and Connector Bodies
1. Loosen and remove the connector bolts, remove the entire trap unit from the connector body
and take it to a repair area where it can be supported in a vise during disassembly.
2. A When reinstalling the original trap:
a. Using a small screwdriver, remove the old gaskets from their housings in the trap body,
then clean the housings.
b. New connector gaskets must be installed.
c. To facilitate assembly and prevent loosening of the gaskets, apply a small amount of
suitable adhesive at 120˚ intervals around the outer edge of the gaskets.
d. Holding the trap body so that the gasket housings are horizontal, place the gaskets into
the housings.
2. B When installing a replacement trap:
a. Be sure to remove all protective seals, making sure the connector gaskets are still in place
after having removed their seal.
b. Before installation, scrape the mounting surface of the connector body clean using a soft
tool.
3. Align the bottom edge of the trap body with that of the connector body (see Fig. A), making
sure the gasket housings on the trap body align with the corresponding recesses in the
connector body. Maintaining the proper alignment, close the tops together until the two
faces are flush, making sure that connector gaskets remain in position.
4. Insert the connector bolts and finger-tighten, keeping
trap and connector bodies flush. Tighten the connector
bolts to the proper torque.
Figure A
Coat threads with anti-seize, then
tighten to the proper torque
Replace with a new gasket, apply anti-
seize to both surfaces
Insert without bending
Screen Holder
Gasket 28
Screens 14 & 27
Screen Holder 29
Remove without bending
Use a socket wrench to
remove
Remove the gasket and
clean the sealing surface
10

11.
Instructions for Plug / Holder Disassembly and Reassembly
Gasket
Do not pinch gasket
in thread recesses
Coat with anti-seize
Gasket Surface
Replace with a new bimetal element
Correct the assembly of the bimetal
elements
Clean the bimetal elements
Use cleaning function
Clean parts
Readjust the screw
Use cleaning function
Replace with a new valve stem
Replace with a new valve seat
Tighten to the proper torque
Replace with a new gasket
Readjust the screw
Replace with a new gasket or seal
ring
Replace with a new seal ring
Replace with a new gasket
A bimetal element is damaged or broken
The assembly (orientation) of the bimetal
elements is incorrect
There is a build-up of foreign matter in the spaces
between the bimetal elements
The valve seat is clogged with rust and scale
The screen or piping are clogged with rust and scale
The adjusting screw is not correctly positioned
There is a build-up of dirt or scale on the valve
stem or seating surfaces of the valve seat
The valve stem is worn or sealing surfaces are damaged
The valve seat is worn or sealing surfaces are damaged
The valve seat is loose
The valve seat gasket is damaged
The adjusting screw is not correctly positioned
Leakage from the cap nut gasket: the gasket or
the seal ring is damaged or deteriorated
Leakage from the adjusting screw: the seal ring is
damaged or deteriorated
Leakage from the cover gasket: the cover gasket
is damaged or deteriorated
CauseProblem Remedy
No condensate
is discharged or
temperature
does not rise to
the set
temperature
Steam is blowing
or the
temperature
rises above the
set temperature
There is leakage
to the outside of
the trap
NOTE: When replacing parts with new, use the parts list on page 3 for reference, and replace with parts from
the Maintenance Kit and/or Repair Kit. Please note that replacement parts are only available as part
of a replacement parts kit.
The seal on the threaded plugs/holders found on TLV products is formed by a flat metal gasket.
There are various installation orientations for the gaskets, such as horizontal, diagonal and
downward, and the gasket may be pinched in the thread recesses during assembly.
Instructions for Disassembly and Reassembly
Remove the plug/holder using a tool of the specified size
(distance across flats).
The gasket should not be reused. Be sure to replace it with a
new gasket.
Clean the gasket surfaces of the plug/holder and the product
body using a rag and/or cleaning agents, then check to
make sure the surfaces are not scratched or deformed.
Coat both the gasket surface of the plug/holder and the
threads of the plug/holder with anti-seize, then press the
gasket onto the center of the gasket surface of the
plug/holder, making sure the anti-seize affixes the gasket
tightly to the plug/holder. Check to make sure the gasket is
not caught in the recesses of the threads.
Hold the plug/holder upside down to make sure that the anti-
seize makes the gasket stick to the plug/holder even when
the plug/holder is held upside down.
Screw the plug/holder by hand into the product body while
making sure that the gasket remains tightly affixed to the
center of the gasket surface of the plug/holder. Make sure
the entire gasket is making contact with the gasket surface
of the product body. It is important at this point to make sure
the gasket is not pinched in the thread recesses of the
plug/holder.
Tighten the plug/holder to the proper torque.
Next, begin the supply of steam and check to make sure
there is no leakage from the part just tightened. If there is leakage, immediately close the inlet valve
and, if there is a bypass valve, take the necessary steps to release any residual pressure. After the
surface of the product cools to room temperature, repeat the procedure beginning from step .
12. Troubleshooting
If the expected performance is unachievable after installation of the steam trap, read chapters 5
and 6 again and check the following points to take appropriate corrective measures.

13.2 Operation Instructions for BD2
BD2
Coat with
Anti-Seize
Torque (T) and Distance Across Flats (D)
BD2 Valve ①
Screen Holder Gasket
Discharge Hole
Valve Stopper Pin
BD2 Valve Seat
(Screen Holder)
Screen
②
BD2 Valve
BD2
Valve Seat
(Screen
Holder)
F46
F32
Screwed & Socket Weld
25 mm (1")
All connections and sizes
Screwed & Socket Weld
Flanged 15 - 25 mm ( "-1")
2
1
/
15, 20 mm ( ", ")
2
1
/
4
3
/
②
①
①
②
(T): 30 N・m (22 lbf・ft)
(D): 17 mm
( ")
32
21
/
(T): 100 N・m (73 lbf・ft)
(D): 30 mm
(1 ")
16
3
/
(T): 60 N・m (43 lbf・ft)
(D): 22 mm
( ")
8
7
/
(T) : 150 N・m (110 lbf・ft)
(D) : 38 mm (1
")
2
1
/
Note: Do not leave the vicinity while the blowdown valve is in the open position.
CAUTION • Always wear eye protection and heat-resistant gloves when operating the
blowdown valve. Failure to do so may result in burns or other injury.
• When operating the blowdown valve, stand to the side well clear of the
outlet to avoid contact with internal fluids that will be discharged. Operate the valve slowly and
surely, taking care to avoid the area from which internal fluids are discharged and any fluids
deflected off piping or the ground etc. Failure to do so may result in burns or other injury.
• Do not excessively loosen the BD2 valve when opening the blowdown valve. The valve stopper
pin installed to prevent the BD2 valve from being removed may break and internal pressure may
result in the BD2 valve being blown off, leading to injuries, damage and fluid discharge, causing
burns.
1. With two wrenches, firmly hold the BD2 valve seat (screen holder) ②(22 mm, ") in place
while slowly opening the BD2 valve ①(17 mm, "). Be careful to avoid contact with fluid that
will be discharged through the hole in the center of the blowdown valve as the valve opens.
2. Close the BD2 valve ①and tighten to a torque of 30 N·m (22 lbf·ft), and confirm that there is
no leakage. If leakage continues, dirt or scale may prevent the valve from sealing. Open and
blow out again, then try to close once more.
32
21
/
8
7
/
13.1 Reassembly of Blowdown Valve
13. Optional Blowdown Valve BD2
The BD2 blowdown valve, installed in place of the screen holder, uses internal pressure to blow
out condensate/steam, dirt and scale to the atmosphere.
CAUTION • Installation, inspection, maintenance, repairs, disassembly, adjustment
and valve opening/closing should be carried out only by trained
maintenance personnel.
•When disassembling or removing the product, wait until the internal pressure equals
atmospheric pressure and the surface of the product has cooled to room temperature.
• Do not tighten the BD2 valve or the BD2 valve seat in excess of the appropriate tightening
torque. Over-tightening may cause breakage to threaded portions, which may cause burns,
other injuries or damage.
1. Clean the trap, BD2 threads, and sealing surfaces, and
apply a small amount of anti-seize.
2. Replace gasket.
3. Carefully place the gasket over the threaded portion,
and position carefully so that it does not
become off-center.
4. Fasten to the steam trap with the proper torque.
12

14.
Express Limited Warranty
Subject to the limitations set forth below, TLV Corporation, a North Carolina corporation (“TLV”)
warrants that products which are sold by it or TLV International, Inc., a Japanese corporation
(“TII”), which products (the “Products”) are designed and manufactured by TLV Co., Ltd., a
Japanese corporation (“TLVJ”), conform to the specifications published by TLV for the
corresponding part numbers (the “Specifications”) and are free from defective workmanship
and materials. With regard to products or components manufactured by unrelated third parties
(the “Components”), TLV provides no warranty other than the warranty from the third party
manufacturer(s).
Duration Of Warranty
This warranty is effective for a period of the earlier of: (i) three (3) years after delivery of Products
to the first end user in the case of sealed SST-Series Products for use in steam pressure service
up to 650 psig; (ii) two (2) years after delivery of Products to the first end user in the case of
PowerTrap
®
units; or (iii) one (1) year afterdelivery of Products to the first end user in the case of
all other Products. Notwithstanding the foregoing, asserting a claim under this warranty must be
brought by the earlier of one of the foregoing periods, as applicable, or within five (5) years after
the date of delivery to the initial buyer if not sold initially to the first end user.
ANY IMPLIED WARRANTIES NOT NEGATED HEREBY WHICH MAY ARISE BY OPERATION OF
LAW, INCLUDING THE IMPLIED WARRANTIES OF MERCHANTABILITY AND FITNESS FOR A
PARTICULAR PURPOSE AND ANY EXPRESS WARRANTIES NOT NEGATED HEREBY, ARE
GIVEN SOLELY TO THE INITIAL BUYER AND ARE LIMITED IN DURATION TO ONE (1) YEAR
FROM THE DATE OF SHIPMENT BY TLV.
Exclusive Remedy
THE EXCLUSIVE REMEDY UNDER THIS WARRANTY, UNDER ANY EXPRESS WARRANTY OR
UNDER ANY IMPLIED WARRANTIES NOT NEGATED HEREBY (INCLUDING THE IMPLIED
WARRANTIES OF MERCHANTABILITY AND FITNESS FOR A PARTICULAR PURPOSE), IS
REPLACEMENT; PROVIDED: (a) THE CLAIMED DEFECT IS REPORTED TO TLV IN WRITING
WITHIN THE APPLICABLE WARRANTY PERIOD, INCLUDING A DETAILED WRITTEN
DESCRIPTION OF THE CLAIMED DEFECT AND HOW AND WHEN THE CLAIMED DEFECTIVE
PRODUCT WAS USED; AND (b) THE CLAIMED DEFECTIVE PRODUCT AND A COPY OF THE
PURCHASE INVOICE IS RETURNED TO TLV, FREIGHT AND TRANSPORTATION COSTS
PREPAID, UNDER A RETURN MATERIAL AUTHORIZATION AND TRACKING NUMBER ISSUED
BY TLV. ALL LABOR COSTS, SHIPPING COSTS, AND TRANSPORTATION COSTS
ASSOCIATED WITH THE RETURN OR REPLACEMENT OF THE CLAIMED DEFECTIVE
PRODUCT ARE SOLELY THE RESPONSIBILITY OF BUYER OR THE FIRST END USER. TLV
RESERVES THE RIGHT TO INSPECT ON THE FIRST END USER'S SITE ANY PRODUCTS
Exceptions To Warranty
This warranty does not cover defects or failures caused by:
1. improper shipping, installation, use, handling, etc., by other than TLV or service
representatives authorized by TLV; or
2. dirt, scale or rust, etc.; or
3. improper disassembly and reassembly, or inadequate inspection and maintenance by other
than TLV or service representatives authorized by TLV; or
4. disasters or forces of nature; or
5. abuse, abnormal use, accidents or any other cause beyond the control of TLV; or
6. improper storage, maintenance or repair; or
7. operation of the Products not in accordance with instructions issued with the Products or
with accepted industry practices; or
8. use for a purpose or in a manner for which the Products were not intended; or
9. use of the Products in a manner inconsistent with the Specifications; or
10. failure to follow the instructions contained in the TLV Instruction Manual for the Product.

CLAIMED TO BE DEFECTIVE BEFORE ISSUING A RETURN MATERIAL AUTHORIZATION.
SHOULD SUCH INSPECTION REVEAL, IN TLV’S REASONABLE DISCRETION, THAT THE
CLAIMED DEFECT IS NOT COVERED BY THIS WARRANTY, THE PARTY ASSERTING THIS
WARRANTY SHALL PAY TLV FOR THE TIME AND EXPENSES RELATED TO SUCH ON-SITE
INSPECTION.
Exclusion Of Consequential And Incidental Damages
IT IS SPECIFICALLY ACKNOWLEDGED THAT THIS WARRANTY, ANY OTHER EXPRESS
WARRANTY NOT NEGATED HEREBY, AND ANY IMPLIED WARRANTY NOT NEGATED
HEREBY, INCLUDING THE IMPLIED WARRANTIES OF MERCHANTABILITY AND FITNESS
FOR A PARTICULAR PURPOSE, DO NOT COVER, AND NEITHER TLV, TII NOR TLVJ WILL IN
ANY EVENT BE LIABLE FOR, INCIDENTAL OR CONSEQUENTIAL DAMAGES, INCLUDING,
BUT NOT LIMITED TO LOST PROFITS, THE COST OF DISASSEMBLY AND SHIPMENT OF
THE DEFECTIVE PRODUCT, INJURY TO OTHER PROPERTY, DAMAGE TO BUYER’S OR THE
FIRST END USER’S PRODUCT, DAMAGE TO BUYER’S OR THE FIRST END USER’S
PROCESSES, LOSS OF USE, OR OTHER COMMERCIAL LOSSES. WHERE, DUE TO
OPERATION OF LAW, CONSEQUENTIAL AND INCIDENTAL DAMAGES UNDER THIS
WARRANTY, UNDER ANY OTHER EXPRESS WARRANTY NOT NEGATED HEREBY OR
UNDER ANY IMPLIED WARRANTY NOT NEGATED HEREBY (INCLUDING THE IMPLIED
WARRANTIES OF MERCHANTABILITY AND FITNESS FOR A PARTICULAR PURPOSE)
CANNOT BE EXCLUDED, SUCH DAMAGES ARE EXPRESSLY LIMITED IN AMOUNT TO THE
PURCHASE PRICE OF THE DEFECTIVE PRODUCT. THIS EXCLUSION OF CONSEQUENTIAL
AND INCIDENTAL DAMAGES, AND THE PROVISION OF THIS WARRANTY LIMITING
REMEDIES HEREUNDER TO REPLACEMENT, ARE INDEPENDENT PROVISIONS, AND ANY
DETERMINATION THAT THE LIMITATION OF REMEDIES FAILS OF ITS ESSENTIAL
PURPOSE OR ANY OTHER DETERMINATION THAT EITHER OF THE ABOVE REMEDIES IS
UNENFORCEABLE, SHALL NOT BE CONSTRUED TO MAKE THE OTHER PROVISIONS
UNENFORCEABLE.
Exclusion Of Other Warranties
THIS WARRANTY IS IN LIEU OF ALL OTHER WARRANTIES, EXPRESS OR IMPLIED, AND ALL
OTHER WARRANTIES, INCLUDING BUT NOT LIMITED TO THE IMPLIED WARRANTIES OF
MERCHANTABILITY AND FITNESS FOR A PARTICULAR PURPOSE, ARE EXPRESSLY
DISCLAIMED.
Severability
Any provision of this warranty which is invalid, prohibited or unenforceable in any jurisdiction
shall, as to such jurisdiction, be ineffective to the extent of such invalidity, prohibition or
unenforceability without invalidating the remaining provisions hereof, and any such invalidity,
prohibition or unenforceability in any such jurisdiction shall not invalidate or render
unenforceable such provision in any other jurisdiction.
13901 South Lakes Drive, Charlotte, NC 28273-6790, U.S.A.
Tel: [1]-704-597-9070 Fax: [1]-704-583-1610

Printed on recycled paper.
Tel: [81]-(0)79-422-1122
Fax: [81]-(0)79-422-0112
Rev. 8/2019 (M)PAC-65502-a
881 Nagasuna, Noguchi, Kakogawa,
Hyogo 675-8511, Japan
Manufacturer:
Other manuals for QuickTrap FX1
1
This manual suits for next models
1
Table of contents
Other TLV Control Unit manuals
Popular Control Unit manuals by other brands
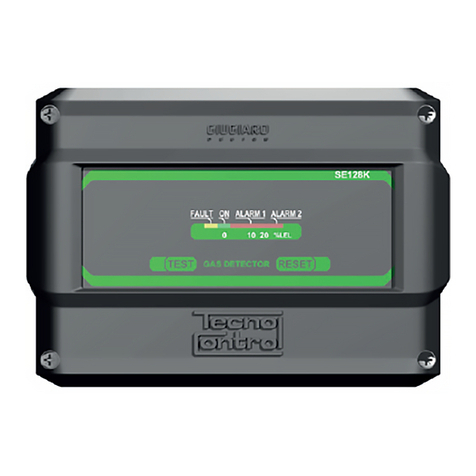
Tecnocontrol
Tecnocontrol SE128K user manual

Sys Tec Electronic
Sys Tec Electronic CANopen ChipF40 System manual
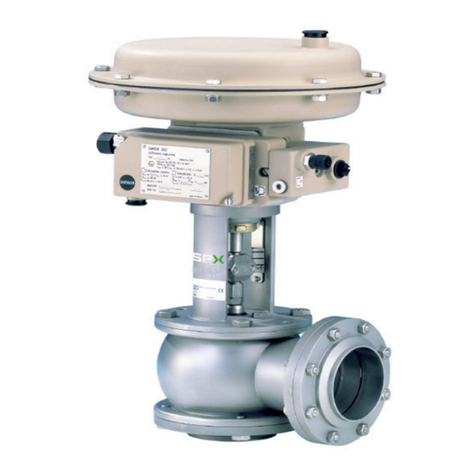
SPX FLOW
SPX FLOW APV DELTA RG4 instruction manual
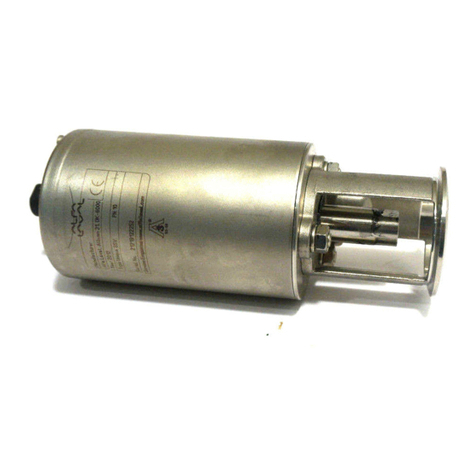
Alfalaval
Alfalaval SMP-BC instruction manual
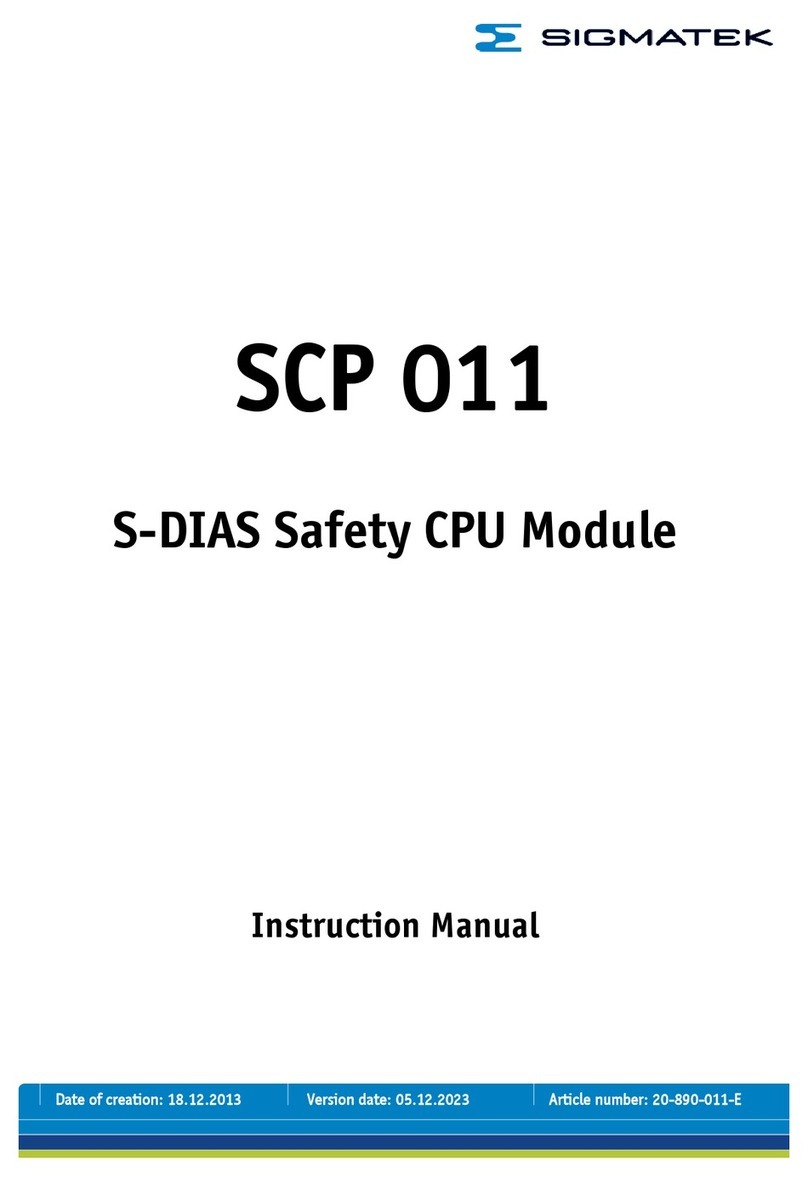
SIGMA TEK
SIGMA TEK SCP 011 instruction manual

Krom Schroder
Krom Schroder valVario VAA 1 operating instructions