Wega Concept User manual

ESPRESSO COFFEE MACHINE
Use and maintenance manual for the TECHNICIAN
- ENGLISH -
Wegaconcept


English

4
Wegaconcept
Technical manual
General warnings
The manufacturer of the equipment can not be held
responsible for damages caused by failure to oblige to
the requirements below.
Warnings for the installer
Read this manual carefully. It provides important•
information on safe installation, operation and main-
tenance of the equipment;
installation and maintenance of the equipment must•
be carried out by personnel qualied and authorized
by the manufacturer, in compliance with safety regu-
lations and instructions included in this manual;
identify the model of the equipment. The model is•
shown on the packaging and on the nameplate of
the machine;
install the equipment only on sites where there is•
good ventilation;
do not obstruct the ventilation and exhaust holes on•
the machine;
do not tamper with the equipment components.•
!
After installing the machine, the installer is
required to ll in the "Installation Form" that goes
with the machine.
On this form must be conrmed the hygiene and
safety requirements in force on the installation
site and must be reported any notes relating to
changes or interventions necessary for the proper
functioning of the equipment.
Filled copies of the Installation form must be kept
by the user and by the installer until the end of life
of the machine.
In case of withdrawal of the machine, the installer
must also provide for the withdrawal of the user's
Installation form.
Typographical conventions
!This symbol indicates that you must strictly follow
the instructions to which it refers in order to avoid
severe injury and/or damage to the machine.
iThissymbolprovidesadditionalinformation on the
operation of the machine and its components.

5
Wegaconcept
Technical manual
ENGLISH
Sections
Section I Operation....................................................... 7
Section II Programming................................................. 37
Section III Electrical/ hydraulic diagrams.......................... 51
Section IV Interfaces ...................................................... 61

6
Wegaconcept
Technical manual
Sections
Section I Operation....................................................... 7
1 Technical characteristics ................................................................ 8
1.1 External components .......................................................... 8
1.2 Internal components........................................................... 9
1.3 Specications...................................................................... 10
1.4 Push-buttons panels .......................................................... 10
2 Preparation ................................................................................... 11
2.1 Unpacking the machine ..................................................... 11
2.2 Equipment preparation ..................................................... 11
3 Machine installation...................................................................... 12
3.1 Positioning ........................................................................ 12
3.2 Hydraulic connection .......................................................... 13
3.3 Wiring................................................................................. 14
3.4 Turning on the machine...................................................... 14
3.5 External motor pump adjustment ..................................... 15
3.6 Machine tune-up ................................................................ 15
4 Boilers............................................................................................ 16
4.1 Coee boiler........................................................................ 16
4.2 Services boiler..................................................................... 16
4.3 Anti-ooding device ........................................................... 17
5 Delivery group ............................................................................... 17
6 Automatic Water Entry.................................................................. 18
7 Pumping system............................................................................ 18
8 Volumetric dosing.......................................................................... 18
9 Electric control unit........................................................................ 18
10 Cup heating device ........................................................................ 19
11 Illuminated side............................................................................. 19
11.1 Description.......................................................................... 19
11.2 Preparing the remote control.............................................. 19
11.3 Adjusting the brightness..................................................... 20
12 Softener......................................................................................... 20
12.1 Regeneration of the softener .............................................. 20
12.2 Regeneration request.......................................................... 21
13 Preparation of beverages............................................................... 22
13.1 Programming the coee doses............................................ 22
13.2 Coee preparation .............................................................. 22
13.3 Programming the hot water doses...................................... 22
13.4 Hot water delivery............................................................... 23
13.5 Regulation of the hot water temperature............................ 23
13.6 Steam delivery.................................................................... 23
14 Cappuccino maker ......................................................................... 24
14.1 installation.......................................................................... 24
14.2 Cleaning.............................................................................. 25
14.3 Cappuccino.......................................................................... 25
14.4 Warm milk .......................................................................... 25
15 Autosteamer (*)............................................................................. 25
15.1 Description.......................................................................... 25
15.2 Automatic heating and foaming ......................................... 26
15.3 Automatic heating .............................................................. 26
15.4 Manual heating and foaming.............................................. 26
15.5 Automatic Cleaning............................................................. 26
15.6 Autosteamer system operation ........................................... 27
16 Energy Saving ............................................................................... 28
16.1 Description.......................................................................... 28
16.2 Energy savings programming.............................................. 28
16.3 Programming of group stand-by ....................................... 28
17 Group washing .............................................................................. 28
18 Cleaning ........................................................................................ 29
19 Checks and maintenance............................................................... 30
20 Malfunctions and related solutions................................................ 32
21 Display indications......................................................................... 35
Section II Programming................................................. 37
22 USB drive ...................................................................................... 38
22.1 Data saving ......................................................................... 38
22.2 Restoring data..................................................................... 38
23 Programming ................................................................................ 38
23.1 Access to the programming................................................ 38
23.2 Browser key......................................................................... 38
23.3 Programming menu............................................................ 39
23.4 Boiler pressure adjustment. ................................................ 39
23.5 Adjustment of coee water temperature. ........................... 40
23.6 Adjustment of the groups temperature............................... 40
23.7 Adjusting the cup heater temperature ............................... 41
23.8 Programming of Energy Saving time and groups stand-by. ... 41
23.9 Conguration of groups proper use..................................... 42
23.10 Standby mode..................................................................... 43
23.11 Autosteamer option ............................................................ 44
23.12 Softener regeneration......................................................... 45
23.13 Display of the counters........................................................ 45
23.14 Setting the date.................................................................. 46
23.15 Setting the working days .................................................... 46
22.16 Setting the language .......................................................... 47
23.17 Delivery check..................................................................... 47
23.18 Programming group washing ............................................. 48
23.19 Setting the number of active groups................................... 49
23.20 Loading the default data..................................................... 49
24 Water meter................................................................................... 49
24.1 Viewing of the litres of water used...................................... 49
24.2 Resetting the Litres ofWater Used...................................... 49

7
Wegaconcept
Technical manual
ENGLISHOperation
Section I
Operation
25 Data reset ...................................................................................... 50
25.1 Resetting of selection counters ........................................... 50
25.2 Resetting of dosers alarm.................................................... 50
Section III Electrical/ hydraulic diagrams.......................... 51
26 Electric diagrams ........................................................................... 52
26.1 Electronic control unit diagram ........................................... 52
26.2 Power supply electronic diagram ....................................... 54
26.3 Connectors electric diagram................................................ 55
26.4 Control unit display / CPU diagram...................................... 59
27 Hydraulic diagram ......................................................................... 60
Section IV Interfaces ...................................................... 61
28 CREDIT - DEBIT / DEBIT - CREDIT system...................................... 62
28.1 CREDIT - DEBIT system with direct connection to the register..62
28.2 DEBIT - CREDIT system with direct connection to the register..62
28.3 DEBIT - CREDIT system with connection to the INTERFACE .. 64

8
Wegaconcept
Technical manual
1Technical characteristics
1.1 External components
Cup heater surface.1.
Push-button panel for coee selections.2.
Display and browser key.3.
Machine power switch.4.
Steam knob.5.
Anti-burn seal.6.
Steam nozzle.7.
Tray and cup support grille.8.
Pull-out cup support grille.9.
Lit up side.10.
Filter holder.11.
Hot water delivery nozzle.12.
Steam delivery nozzle / autosteamer13. (*).
Adjustable foot.
14.
Push-button panel for services/ autosteamer15. (*).
Dispensing spouts.
16.
Dispensing compartment light.17.
USB socket.18.
1 5 182
13
6
5
107 68 91514
11
12
4
16 1617
3
(*) optional.

9
Wegaconcept
Technical manual
ENGLISHOperation
1.2 Internal components
Services boiler pressure switch.1.
Services boiler.2.
Coee boiler pressure switch.3.
Internal motor pump (if included).4.
Dispensing group.5.
Water inlet connection.6.
Hot water mixer.7.
Drain pad.8.
Volumetric dosing device.9.
Coee water container.10.
Coee water heating element.11.
Electronic control unit.12.
Services boiler heating element.13.
2
13
11
5
3
4
89
12
10
6
7
1

10
Wegaconcept
Technical manual
1.3 Specications
The specifications
indicated in the table
below correspond to
the plate located on
front of the machine.
specica-
tion plate
Technical data table
1.4 Push-buttons panels
Coee selections push button panel
The push button panel is connected to the electronic
control unit, and allows selection and programming of
coee doses.
Services push button panel
The services push button panel is included with
the machine, it is connected to the electronic control
unit and allows the delivery of hot water for making
beverages such as tea, etc...
Services push-button and autosteamer (*)
The autosteamer push-button panel is installed with
the homonymous device, and allows selection and
programming of milk-based beverages.
It also includes the services push button panel
Display and browser key.
All programming operations of the machine are
carried out using the selector as specied in the chapter
"23 Programming".
On the left of the selector there is a display which
shows the operating data of the machine and the
programming messages.
2Gr 3Gr 4Gr
Power supply
voltage V 230/400 240/415 230/400 240/415 230/400 240/415
Total power W 4.400 4.790 5.600 6.100 7.100 7.730
Power x group W 150x2 165x2 150x3 165x3 150x4 165x4
Coee water
tank heating
element power
per group
W 1,000x2 1,090x2 1,000x3 1,090x3 1,000x4 1,090x4
Steam boiler
power W 3.000 3.270 3.000 3.270 5.000 5.445
Steam boiler
capacity lt / UK gal 8 / 1,76 13 / 2.86 13 / 2.86
Coee water
tank capacity lt / UK gal (1.2/ 0.26)x2 (1.2/ 0.26)x3 (1.2/ 0.26)x4
Width mm / in 800 / 31.5 1040 / 40.9 1280 / 50.4
Depth mm / in 580 / 22.8 580 / 22.8 580 / 22.8
Height mm / in 590 / 23.2 590 / 23.2 590 / 23.2
Net weight kg / lb 95 / 209 117 / 257 142 / 312
Operating
conditions °C / °F 5 ÷ 40 / 41 ÷ 104
1 Espresso
1 Medium coee
1 Large coee
2 Espressos
2 Medium coees
2 Large coees
Stop / Programming /
Continuous
1.2 Bar Press 0.0
08:30 10-FEB-2011
Humidity 62% P 32%
Boiler pressure
Browser key
Pressure
hydraulic circuit
Absorbed power
indicator
Hour
Humidity
Date
Instantaneous
absorbed power
Hot water dose 2
Hot water dose 2
Hot water dose 1
Hot water dose 1
Small dose autosteamer
Large dose autosteamer
Automatic heating
Manual steam +
foaming
(*) optional.

11
Wegaconcept
Technical manual
ENGLISHOperation
2Preparation
2.1 Unpacking the machine
Open the packaging, ensuring not to damage the
machine.
Remove the machine protections and the equipment
contained in the package. Take the machine out.
If there is an external motor pump, the motor and the
pump are provided in a separate package.
Screw the steam nozzles to
the taps.
Motor pump
For the machines with an external motor, it is
necessary to prepare the pump and the motor.
Assemble the 3/8 gas connection with the inlet lter
(2) of the pump (arrow ) and the plain 3/8 outlet gas
connection (1) of the pump (arrow ).
Use the special washers (3) provided for sealing
purposes.
To correctly couple the pump and motor, use the
appropriate joint (4) and the spacer ring (5), lock
everything with the two clamps (6).
The pump and motor joint has to be installed also on
the machines with an internal motor pump.
2.2 Equipment preparation
Filter holder
In the housing of the lter holder(1), place the spring
to stop the lter (2).
Take the two cups (3) or one-cup (4) lter and press
it rmly into the lter holder.
Spouts
Complete the lter holder by installing the two-cup
(6) or one-cup (5) spout.
Softener
The softener is supplied by
default.
On request, an automatic resin
softener is supplied.
For further information, refer to
the chapter “12 Softener”.
1 2
3
6456
5
1
6
2
3 4
3
!Install the spout with related lter: one-cup spout
on one-cup lter lter holder, etc.
!Installtheconnection with the inlet lter (2) of the
pump (arrow ).

12
Wegaconcept
Technical manual
3Machine installation
3.1 Positioning
Prepare an ample support base for the machine that
is suitable to support its weight (3); it is important for all
terminals of the connections to the water supply (12) and
to the power supply (9) to be easily reachable and, in any
case, in the immediate vicinity of the machine.
Make sure that there is sucient space for placing
and correctly using the appliance. The grinding-dosing
machine (4) must be placed in the immediate vicinity
of the appliance in order to allow for comfortable use
of the machine.
5
4
3
2
1
12 14
13
11
15
10
9
8
6
7
It is advisable to equip the working base of the
machine with a drawer (1) for used coffee grounds,
preferably with a rubber device (2) for tapping the lter
holder.
!For correct operation, the machine must rest on a
perfectly horizontal surface. Any alignment of the
machine must be done by adjusting the feet (8).

13
Wegaconcept
Technical manual
ENGLISHOperation
3.2 Hydraulic connection
Remove any rubber plugs which may be inserted in•
the tap xtures of the softener;
connect the water supply (• 12) to the softener inlet
(10) using the provided exible hose;
rinse the resins from the softener and check that the•
water, which initially comes out yellowish, comes
out clean;
connect the softener outlet (• 11) to the external motor
pump inlet (13);
connect the outlet of the motor pump (• 14) to the inlet
of the machine (7);
connect the drain pad of the machine (• 6) to the sewer
discharge (5) using the special hose provided, avoid-
ing overly tight bends or kinks, and making sure that
there is sucient inclination for water to drain.
Warnings
The water supply must provide cold water for1.
human consumption (potable water) at a pressure
between 1,5 and 5 bars If the pressure is higher
than 5 bar, connect a pressure reducer before the
pump.
add a tap (
2. 15) to the water supply so as to stop water
from owing to the machine;
in order to prevent damage, it is advisable to
3.
install the softener where it will be protected from
accidental blows;
to prevent water from freezing, install the softener
4.
inside a premise with a room temperature higher
than 5°C;
if there is no softener, connect the water supply
5.
(12) directly to the inlet of the external motor
pump (13);
if there is an internal motor pump, connect the
6.
outlet of the softener (11) (if there is one) or the
water supply (12) directly to the machine inlet
(7);
when connecting the pad of the machine to the
7.
sewer drain, avoid overly tight curves or kinks, and
make sure that there is sucient inclination for
water to ow out of the drain.
the drain must be connected to an inspectable
8.
siphon that can be periodically cleaned, in order
to avoid bad odours;
to avoid oxidization and damage to the machine
9.
over time, do not use iron connections for the
hydraulic system, even if galvanized.
!All filling connections are of the 3/8 male gas
type. The drain pan is connected to a tube with an
internal diameter of 16mm.
!
The water supply of the appliance must be carried
out with water which is suitable for human
consumption, in compliance withthe regulationsin
force in the place of installation.The installer must
receive, from the owner/manager of the system,
conrmationthat the watermeetsthe abovelisted
requirements.
!
During the installation of the appliance, only
the components and materials supplied with the
appliance are to be used.
Should the use of other components be necessary,
the installer must verify their suitability to
be used in contact with water used for human
consumption.
The installer must carry out the hydraulic
connections in accordance with the hygiene norms
and the hydraulic safety norms for environmental
protection in force in the place of installation.
!
The hydraulic connection must be made in
compliance with local national standards. In case
of use of an external tank: the connection hose
between the machine and the tank can't be longer
than 150 cm. For the European Community: both
for the hydraulic connection to the water supply,
and for the connection to an external tank, it is
necessary to place a non-return valve (15) on the
machine as set forth by EN 1717 standards.
!
The machines are equipped with a time-limit
switch that allows the water to ll the boiler only
for a limited time. This function keeps water from
flowing out of the boiler's valve (flooding) and
keeps the motor pump from overheating. If the
time limit is not enough for the boiler to ll up
completely(such as for the machines installed with
3 or 4 groups), turn the machine o and then back
on, and repeat the operations listed above.

14
Wegaconcept
Technical manual
3.4 Turning on the machine
Before turning on the machine, make sure the drain
pad (2) located under the cup support grid is correctly
connected to the sewer.
Turn on the machine using the main switch (1) and
follow the indications on the display of the machine.
C Motor pump power cable
MP Motor pump terminal
B Blue
M Brown
GV Yellow-green
C
MP
BB
MM
GV GV
3.3 Wiring
It is necessary to link a safety main
switch (A) on the electric panel, as
required by standard regulations.
Machine with INTERNAL MOTOR PUMP
In case of internal motor pump connect the power
cable as set forth in the chapter "Electrical diagrams" (the
cable has a cross-section and number of wires based on
the power and voltage of the machine).
Machine with EXTERNAL MOTOR PUMP
In case of external motor pump, proceed as follows:
Connect the motor pump cable (with smaller cross
1.
section) to the connector of the external motor as
shown in the diagram below.
Connect the machine power cable (with larger
2.
cross section) as set forth in the "Wiring diagrams"
chapter.
A
1
2
When the machine
is turned on, it performs
the functional test and
reports information
regarding the software
installed.
XX-XX-XX : revision date•
Rx : software revision number;•
D.Board x.xx: display card version.•
If the result is O.K.
the machine is working
correctly.
In case of negative
result, check the
message on the
display.
FUNCTIONAL TEST
DELNEW xx-xx-xx Rx
D.BOARD x.xx
TEST
-O.K.-
!
To avoidthe risk of burns,it is advisable to keep•
hands away from the hot water nozzle, steam
nozzleanddeliverygroupsduringthemachine's
heating phase.
Before using the machine, run deliveries dry•
with the lterholder attachedfor a few seconds
to release any air which may be in the circuit.
Before using the machine, dispense a few•
servings of coee to test the grinding and to
check the operating pressure of the machine.
!
Always connect the motor pump cable before the
machine power supply cable, in accordance with
the diagram provided. Failure to comply with
the instructions given above may cause serious
damage to the machine and/or motor pump and
will invalidate the warranty. Carry out the electrical
connections only whenthemachine is disconnected
from the power supply.

15
Wegaconcept
Technical manual
ENGLISHOperation
3.5 External motor pump adjustment
To adjust operating pressure proceed as follows:
press the "• PROG/STOP" button for continuous coee
delivery;
adjust the pressure by turning the screw located on•
the pump (1) so as to
obtain a value between
8 and 9 bar: tightening
the screw increases the
pressure, and loosening
it reduces the pressure.
check the pressure on
the display (2);
end the delivery press-•
ing the "PROG/
STOP" button
again.
3.6 Machine tune-up
When installation is complete, the appliance has to be
started, brought to the nominal working condition and
left in the "ready to operate" condition for 30 minutes.
Afterwards, the appliance has to be turned o and
emptied of the first water introduced in the whole
hydraulic circuit, to eliminate possible initial impurities.
Then the appliance must be once again loaded and
brought to the nominal working conditions.
After reaching the "ready to operate" condition, the
following deliveries have to be performed:
for each coee unit, carry out a continuous delivery,1.
in order to release the whole volume of water
contained in each associated coffee tank (1.2
litres);
release the whole volume of hot water inside
2.
the boiler (8 litres for 2GR, 13 litres for 3GR and
4GR), by performing a continuous delivery from
the appropriate nozzle. In case of several delivery
points, divide the volume based on the number of
the delivery points;
continuously release steam for at least 1 minute for
3.
each steam delivery point;
When installation is complete, the installer must write
a report about the performed operations.
1
When the machine
is turned on, it will
activate the motor
pump installed and
begin to ll the services
boiler and the water
heaters for the coee (equal to the number of delivery
groups installed on the machine.)
0.0 Bar Press 3.5
08:30 14-APR-2010
COFFEE
WATER FILLING
In order to remove
the air from the
heaters, each time the
machine is turned on
the solenoid valves
of the groups will be
activated, making water and steam come out from the
perforated disk of each group for about 10 seconds.
When the heating
phase of the delivery
groups has finished
(after about 10
minutes), signaled by
the disappearance of
the “PLEASE WAIT” indication, it will be possible to
make the coee selections. For the delivery of hot water
and steam, it will be necessary to wait for the complete
heating of the services boiler.
During the heating
phase of the services
boiler (from 95°C to
98°C), the machine will
execute a light delivery
of water and steam
from the hot water nozzle.
Thedeliveryofsteam
and hot water, and
thus the full operation
of the machine, will
be possible only at a
pressure higher than
0.6 bar.
0,0 Bar Press 3,5
PLEASE WAIT
Humidity 38% P 85%
0.7 Bar Press 3.5
08:30 14-APR-2010
Humidity 38% P 85%
0,0 Bar Press 3,5
STEAM ESCAPE
Humidity 38% P 85%
0.0 Bar Press 3.5
08:30 14-APR-2010
MAKE ATTENTION
WATER/STEAM ESCAPE
0,0 Bar Press 3,5
08:30 14-APR-2010
2
!To avoid the risk of burns, it is advisable to keep
hands away from the hot water nozzle, steam
nozzle and delivery groups during the machine's
heating phase.

16
Wegaconcept
Technical manual
4Boilers
There are two kinds of boilers inside the machine:
4.1 Coee boiler
Each delivery group is
equipped with a coffee
boiler (1) of limited capacity
(1,2 litres).
These boilers provide
hot water for the coee.
Heat is provided by an
electric heating element
(2).
For each boiler are
installed: a temperature
sensor (3), a safety thermostat (4), and a pressure
switch.
4.1.1 Security systems:
Coee boiler pressure switch.
Each coee boiler is equipped with a safety
switch to control the pressure.
Calibration is set to 5 Bar and can be
distinguished by the GREEN seal.
Expansion - non-return valve
This is a valve consisting of an expansion
valve and a non-return valve.
expansion valve (• 5): the cold water sent from the
pump to the heat exchangers is heated. This heating
causes an increase in the volume of
water.To limit pressure increases in
the hydraulic circuit, the valve lim-
its the maximum internal pressure
of the circuit to 12 Bar.
non-return valve (• 6): its function is
that of preventing the back ow of
water from the exchangers in the
hydraulic circuit.
Temperature sensor (3).
Turns o the resistance when 130° C are reached and
displays an alarm.
Temperature sensor (4).
Turns o the resistance when 150° C are reached.
CPU Control.
Turns o the resistance if using 100% of its max power
for 45 minutes.
4.2 Services boiler
Inside the coee machine, there is a services boiler
(7).
This boiler provides steam and hot water for tea.
Heat is provided by an electric heating element (8).
The boiler includes a temperature sensor (10), a safety
valve (11), a level probe (9a) and a safety probe (9b).
9a
8
7
9b
10
11
4 3
2
1
4.2.1 Security systems:
Services boiler pressure switch.
Also the boiler is equipped with a safety switch to
control the pressure.
Calibration is set to 1.5 Bar and can be distinguished
by the red seal.
Pressure limitation safety valve
The pressure relief valve guarantees that
the pressure in the boiler does not go above
2 Bar. If there is a malfunction, the valve can
eliminate all the excess pressure from the
boiler.
Temperature sensor (10).
Turns o the resistance when 130° C are reached and
displays an alarm.
CPU Control.
Turns o the resistance if using 100% of its max power
for 60 minutes.
5
6

17
Wegaconcept
Technical manual
ENGLISHOperation
Safety thermostat.
Located inside the boiler,
turns off the resistance if the
temperature reaches 169° C.
The thermostat allows you to
avoid damage to the electrical
resistance in case of lack of
water in the boiler.
The thermostat bulb (12) is
located inside a sheath placed
at the center of resistance.The contacts of the thermostat
(13) are connected to the electrical resistance (8).
If the electrical resistance is exposed due to failure to
load water to the boiler, the temperature of the resistance
increases dramatically. At this point, the thermostat
interrupts the power supply to the resistance thus
preventing damage.
5Delivery group
The delivery group is composed as follows :
the group body (• 1) is made up of a metallic block
which is hooked onto the coee boiler (2);
the activation of the motor pump and solenoid valve•
(3) located on the side of the group allows the cold
water to enter the boiler (4), consequently the hot
water in the boiler is carried towards the delivery
group (5);
the electrical cartridge heating element (• 6) installed
in the group is controlled by an electronic control unit
and allows the group to be heated at a programmed
temperature;
the temperature sensor (• 7) detects the value of the
temperature of the group and sends it to the elec-
tronic control unit;
the activation of the safety thermostat (• 8) prevents
risks if there is a failure in the electronic system.
12
13
14
8
2
3
1
3
7
1
6
4
5
!Do not replace the heating element with a more
powerful one. Before making any modications,
contact the manufacturer.
!The valves must be checked on a regular basis
as described in the chapter "Controls and
maintenance".
iTo reset the thermostat, press the center button
(14). However, before trying to operate the
machine, verify the causes of the blockade of the
water feeding the boiler
4.3 Anti-ooding device
The cover installed on the
pressure relief valve makes it
possible to collect any water
which may leak from the boiler
due to malfunction and channel
it to the drain pad, by means of a
special hose.

18
Wegaconcept
Technical manual
6Automatic Water Entry
The Automatic Water Entry system is for checking the
boiler level. It is composed of:
level probe (short) (• 1) and safety probe (long) (2)
inserted in the boiler, composed of a stainless steel
rod;
electronic control unit (• 3) ;
hydraulic circuit controlled by a motor pump and•
solenoid valve controlled by the electronic control
unit.
When, during the normal operation of the machine,
the water level drops down, the level probe (1) sends a
signal to the electronic control unit (3), which activates
the motor pump and the lling solenoid valve, thus
restoring the level of water in the boiler.
If the level is very low or there is no water in the
boiler (during the machine's installation or due to a
failure), the safety probe (2) sends a signal to the control
unit which de-activates the heating element to keep it
from overheating and activates the motor pump and
the solenoid valve to restore the level of water in the
boiler.
To avoid possible flooding due to machine
malfunctions or leaks in the hydraulic circuit, the
electronic control unit includes a timing device that cuts
o automatic lling after a maximum operating time
(roughly 30 seconds). During the installation of machines
with three or four groups the initial water lling time
may exceed the established time limit. In this event,
just switch the machine o and then back on to restore
normal operating conditions.
1
1
2
8Volumetric dosing
The volumetric dosing device serves the purpose of
measuring the quantity of water sent to the group of
espresso delivery.
The dosing device generates an electrical impulse
which is sent to the electronic control unit.
This impulse is read by the control unit and memorized
during the programming of
the dose.
The ashing of the LED (1)
indicates that the electrical
impulse has been sent from
the dosing device to the
control unit.
1
7Pumping system
This is a component that feeds
the machine, raising the water
pressure to 8-9 bar for coffee
delivery and automatic lling of
the boiler.
9Electric control unit
The electronic control unit (1) is the core of the
machine. It monitors and controls all operation of the
unit.
Among its functions, it electronically manages the
dose of coffee through the passage of water in the
dispenser and controls the entry of water into the
boiler.
It is set up to be connected to the delivery accounting
systems by means of a specic interface.
The information concerning the installed software
(date and version) can be seen on the display when the
machine is turned on.
The information concerning the installed software
(date and version) can be seen on the display when the
machine is turned on.
i
The unit includes a button lithium battery. When
it needs replacing, disconnect the machine from
the power outlet and open the central unit placed
inside the equipment.
Dispose of the battery in compliance with the
collection regulations of the country of use.
3

19
Wegaconcept
Technical manual
ENGLISHOperation
DATA
REGISTER RESET
!When the software is updated, as soon as the
machine is started the system loads the default
data. In this case you will need to set the machine
parameters again.
10 Cup heating device
The cup heating device is for heating cups before
they are used.
Place the cups to be heated on the
appropriate surface (1).
To turn on the cup heater, press
the () navigator button (it is not
necessary to insert an USB drive); an
asterisk will appear on the rst line on
the far right of the display, indicating
thatthe cup heater is ON.
To turn it off, press the ()
navigator button again, the asterisk
will disappear.
To change the temperature of
the cup heater, proceed as listed in
chapter "23-Programming".
1
RESS 3.5 *
14-APR-2010
% P 85%
Cup heater
ON/OFF
!
For safety reasons, it is advisable not to place cloths
or other objects on the cup heater (1).
!If the cup heater is set to a temperature lower than
70 °C in the adjustment menu, it will remain o,
even if switched ON ( * symbol on the display).
11 Illuminated side
11.1 Description
Within each side of the body, there is a drowned strip
with LEDs.
They provide uniform and adjustable lighting along
the perimeter on the same side, which can be activated
at user's discretion.
This chapter provides instructions for adjusting and
turning on/o one or both lit sides.
To activate and deactivate the lighting
of the delivery compartments, as well as
of the sides of the machine, press the ()
navigator button repeatedly.
The lights will switch on sequentially,
depending on how many times the
button is pressed.
The table below shows the
correspondence between the number of
presses and the switching on of the lights.
no. of presses on the
button ()
Dispensing
compartment light Sides light
1 ON OFF
2ONON
3 OFF ON
4 OFF OFF
!Dispose of the batteries in compliance
with the environmental regulations in
use. Donot dispose of themtogether with
the household waste.
iThe ON/OFF lights button works as a main switch.
The internal dimmerand the remotecontrol cannot
switch on the sides if these were set to OFF by the
main switch.
ON/OFF
Lights
11.2 Preparing the remote control
Open the battery cover on the back of the•
remote control.
Insert two AAA batteries. Make sure the polar-•
ity (+ and -) is aligned correctly.
Put the battery cover back in place.•

20
Wegaconcept
Technical manual
12 Softener
Mains water contains insoluble salts, which cause the
build-up of lime scale deposits in the boiler and other
parts of the machine. The softener makes it possible
to eliminate or substantially reduce the presence of
these mineral salts. The resin softener has the property
of retaining the calcium contained in the water. For
this reason, the resins become saturated after a certain
period and must be regenerated with coarse kitchen salt
(NaCl, sodium chloride) or special water softening salt.
It is very important to regenerate the softener within
the established times. The regeneration is to be done
regularly every 15 days. However, in locations where
water is very hard, it will be necessary to regenerate
it more frequently. The same rule can be applied to
locations where there is a large consumption of hot water
for tea or other uses.
12.1 Regeneration of the softener
Proceed as follows:
move levers (• B) and (E)
from left to right;
remove the lid by loosen-•
ing the knob (A);
release enough water•
through the pipe (C) to
make room for the salt to
be added, based on the
model (see the table on
the following page);
clean any salt or resin residues from•
the gasket located on the cover;
put the cover back in place by screw-•
ing the knob (A) down securely and
move the lever (B) back from right
to left;
let the salt water drain from the little•
hose (D) until the water is no longer
salty (about 30-60 minutes). The salt
allows the accumulated mineral
salts to be released;
switch the lever (• E) from right to
left back to its initial position.
B
E
A
C
D
Softener model Amount of salt
8 litres 1.0 kg
12 litres 1.5 kg
16 litres 2.0 kg
11.3 Adjusting the brightness
11.3.1 Adjustment by remote control
You can adjust the brightness of the body
sides, using the supplied remote control. Proceed
as follows:
Point the remote at the machine;•
briey press the button (< 1 sec) to turn on/•
o the side;
holding the button (> 1 sec) increases/de-•
creases the brightness of the side.
button no. 1 (red) operates the right side,•
while button no. 2 (green) operates the left
side.
11.3.2 Adjustment by internal regulator
Should the remote control not work properly, you can
make the adjustment by the regulator installed inside
the machine.
To access it, proceed as follows:
remove the left side of the body (• A), after disconnect-
ing the LED connector;
open the unit compartment to access the machine;•
once the regulator (• B) has been detected, operate the
appropriate trimmers.
Right side
Left side
A
B
1
2
3
4
!Never operate the electronic apparatus when the
machine is wired.
Shutdownthemachinecompletelybydisconnecting
it from the power outlet before carrying out any
operation.
R
G
B
+-
Table of contents
Other Wega Coffee Maker manuals
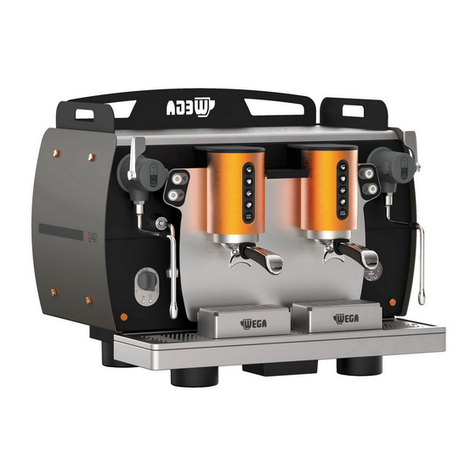
Wega
Wega WBAR EVD User manual
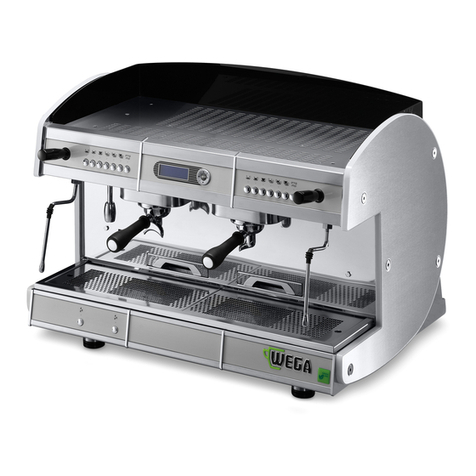
Wega
Wega Wegaconcept User manual
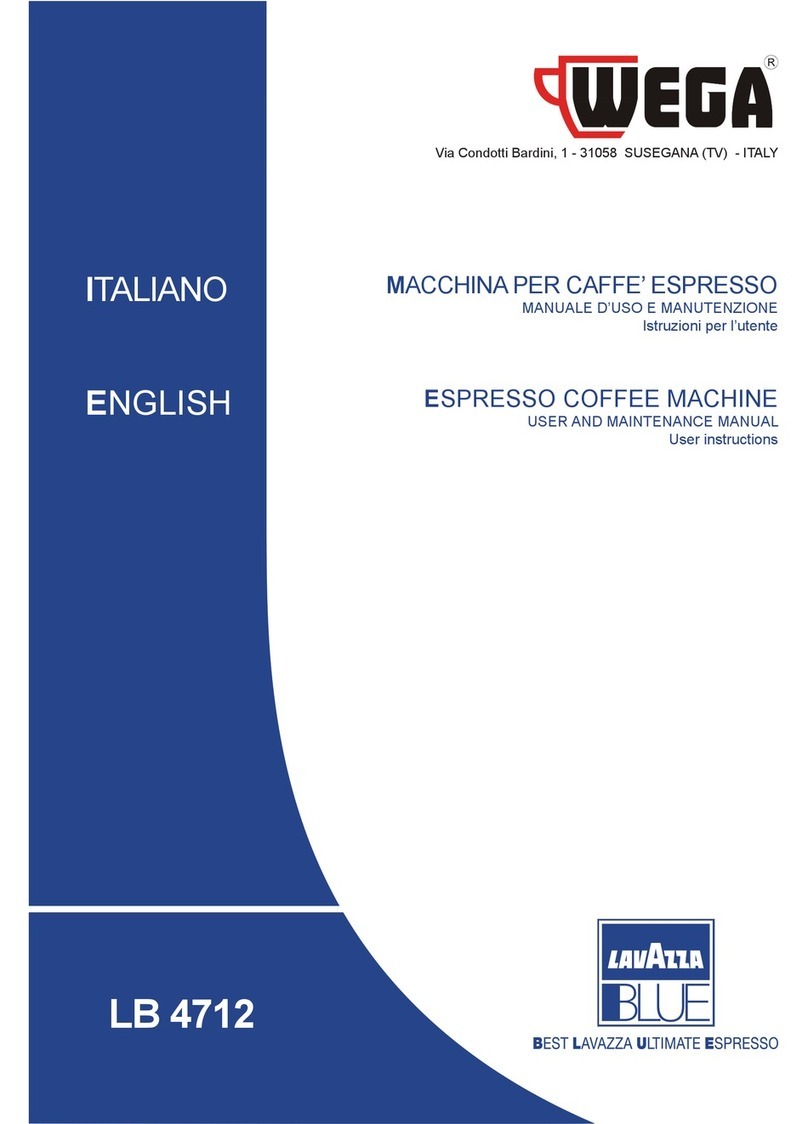
Wega
Wega LB 4712 Operating instructions
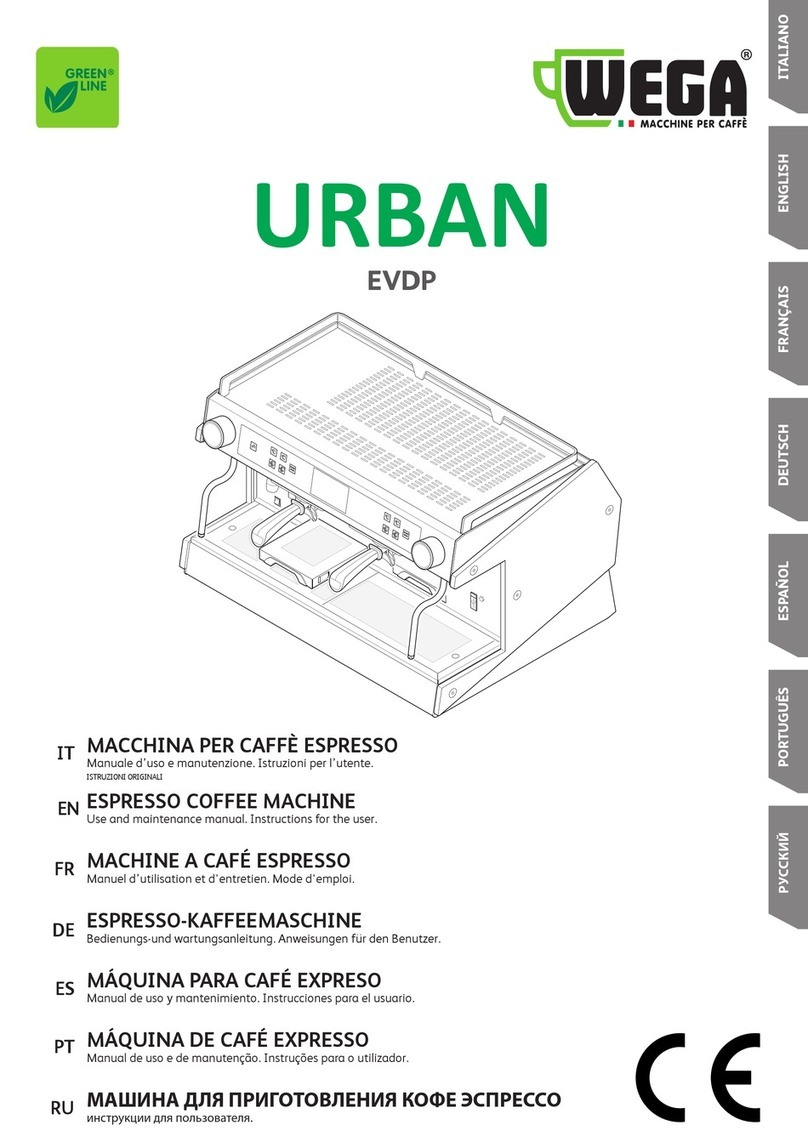
Wega
Wega URBAN EVDP User manual

Wega
Wega EVDS io User manual
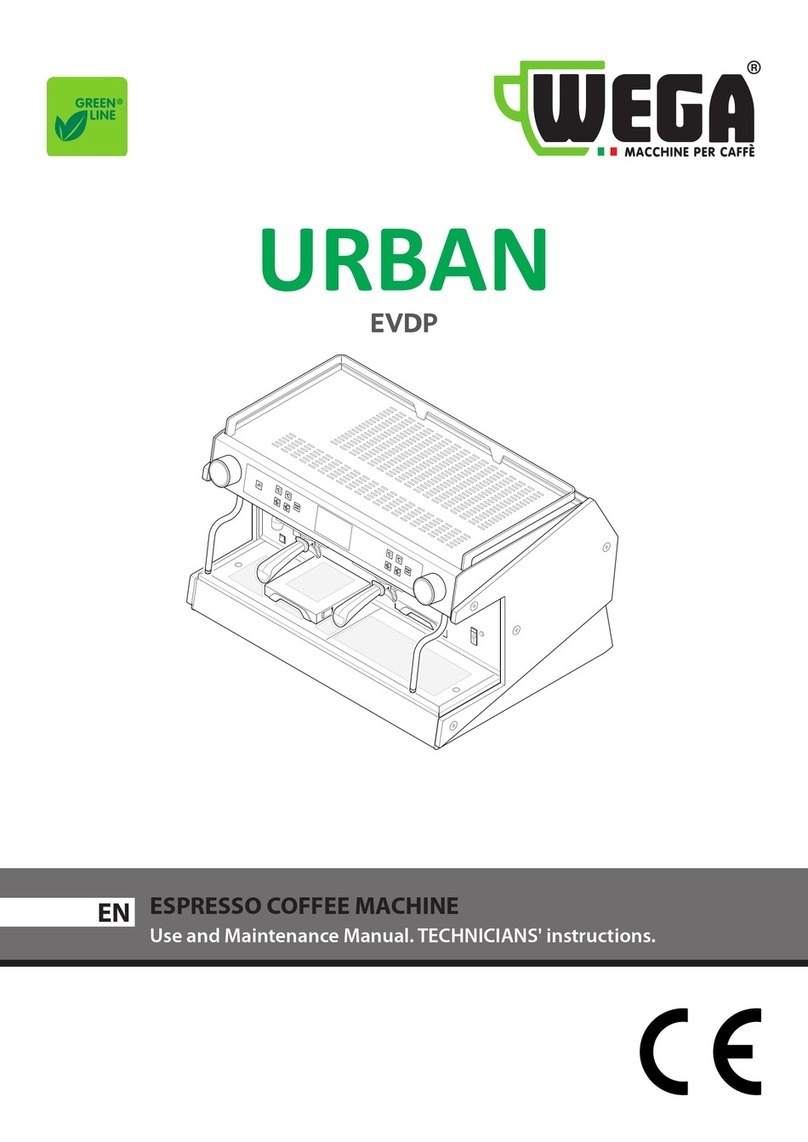
Wega
Wega URBAN EVDP User manual

Wega
Wega URBAN EVDP User manual
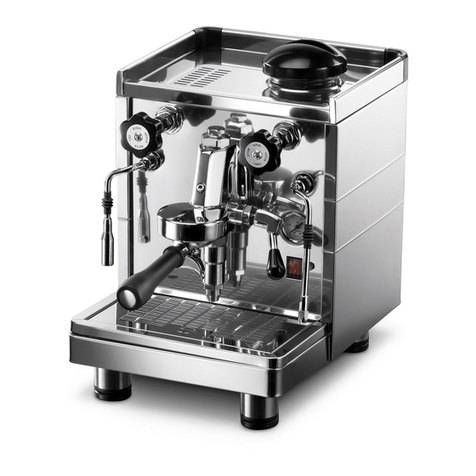
Wega
Wega MININIVA CLASSIC DUO User manual
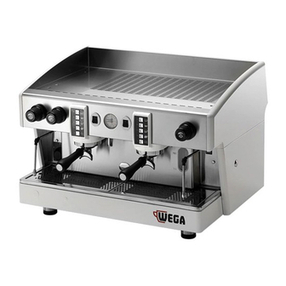
Wega
Wega ALE User manual

Wega
Wega MININOVA CLASSIC DUO User guide
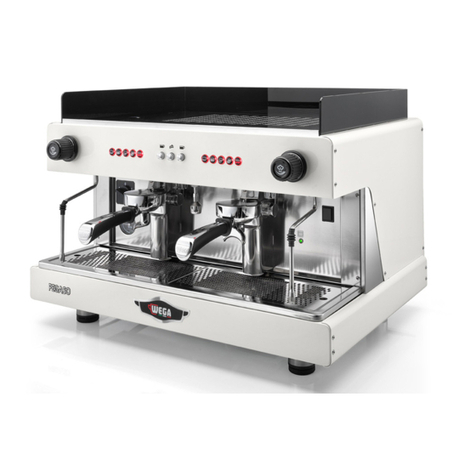
Wega
Wega Atlas 2010 User guide
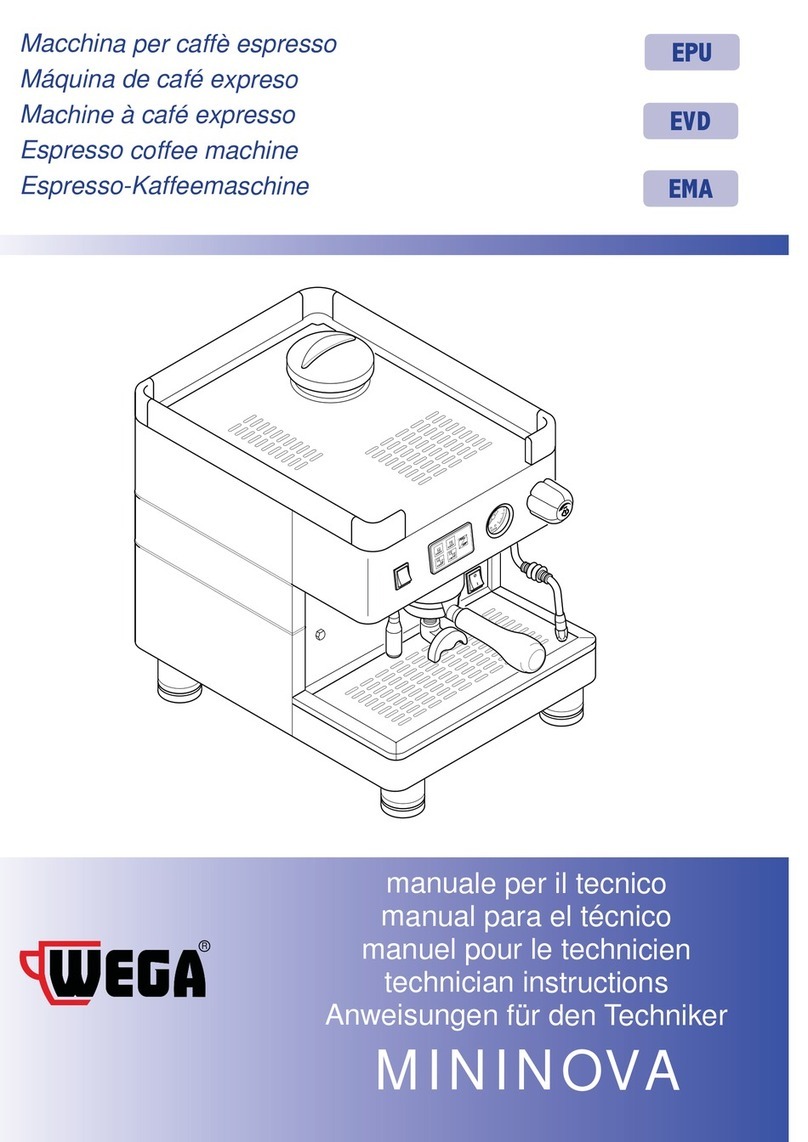
Wega
Wega Mininova User manual
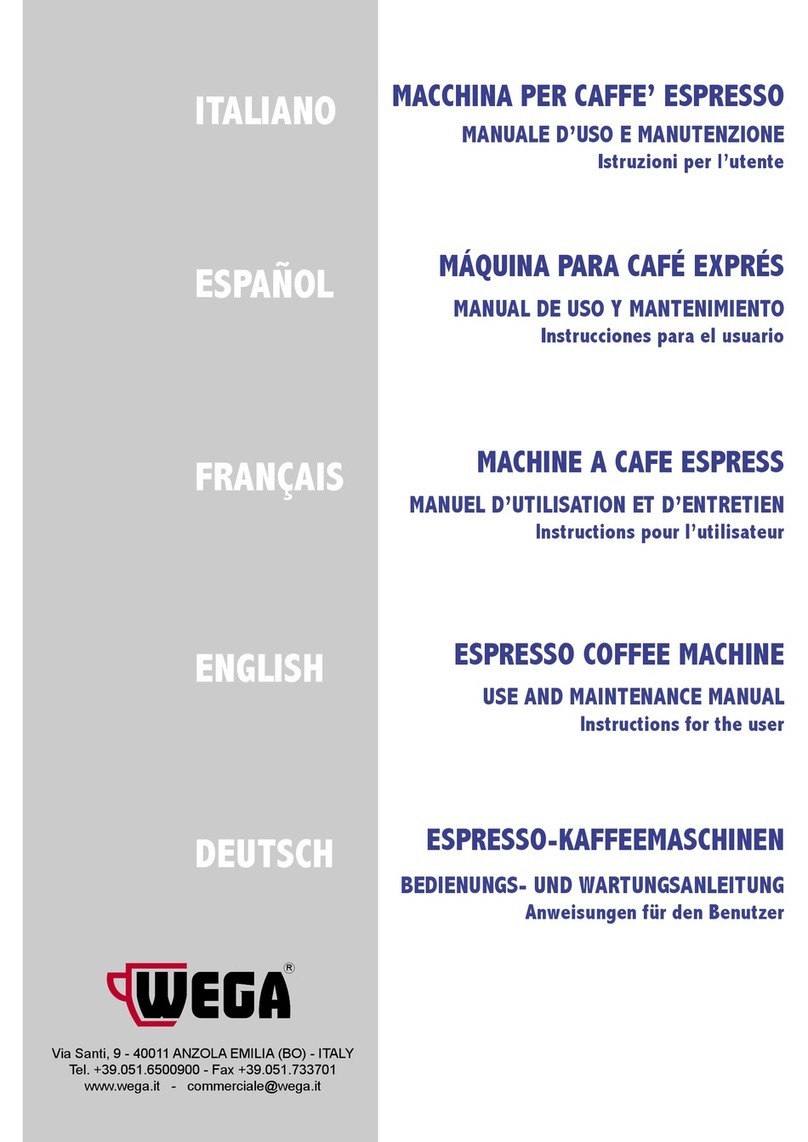
Wega
Wega Espresso Coffee Machine User guide

Wega
Wega LavAzza BLUE LB 4722 User manual
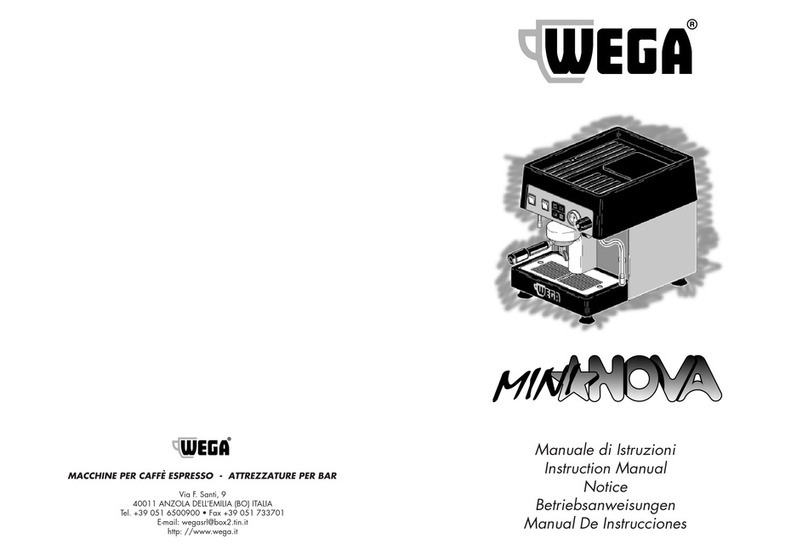
Wega
Wega Mininova User manual
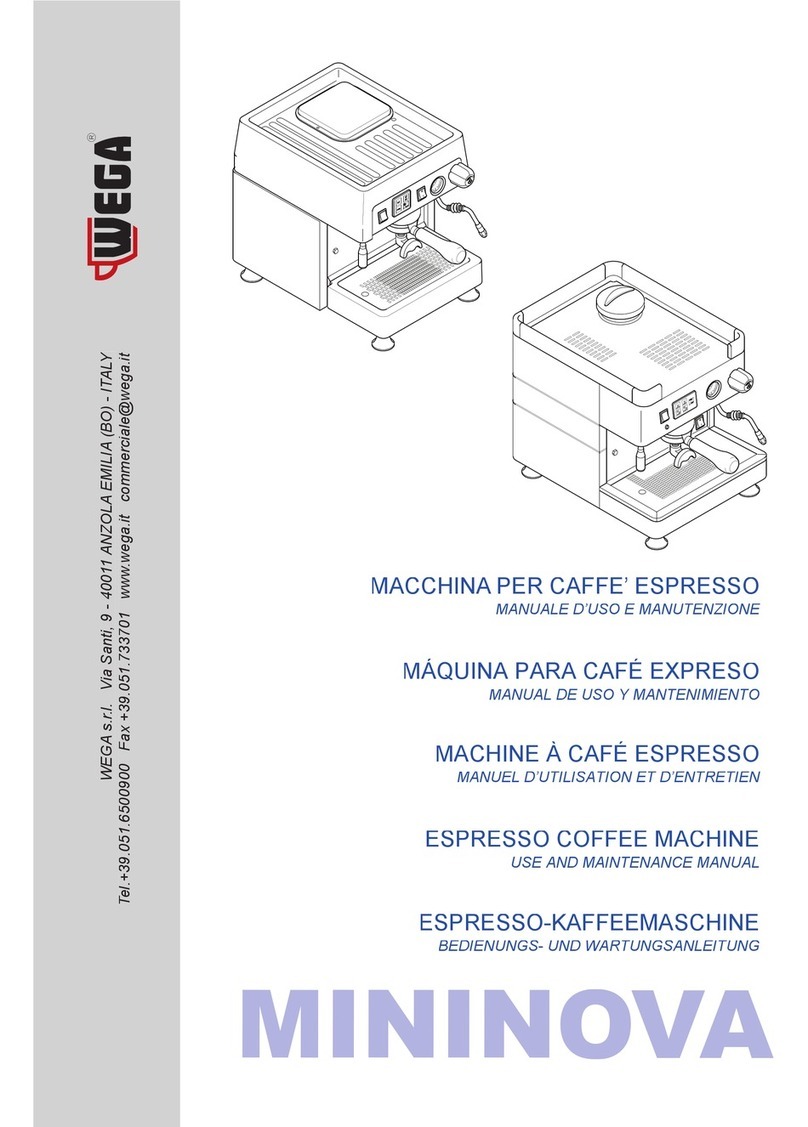
Wega
Wega Mininova User manual
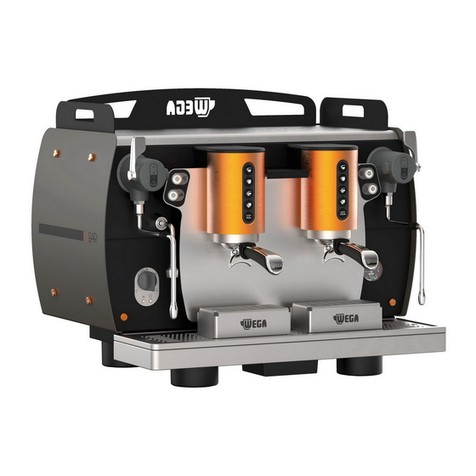
Wega
Wega WBAR EVD User manual

Wega
Wega AIRY 1 User manual
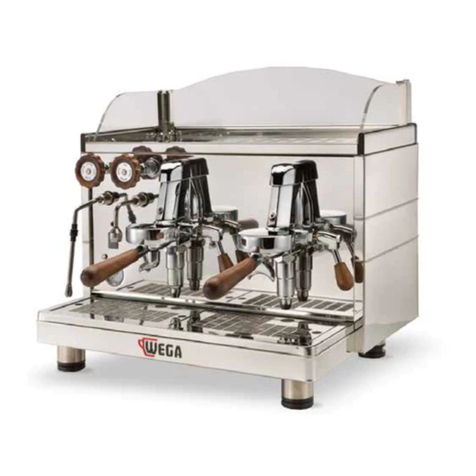
Wega
Wega MININOVA CLASSIC DUO 2GR User manual
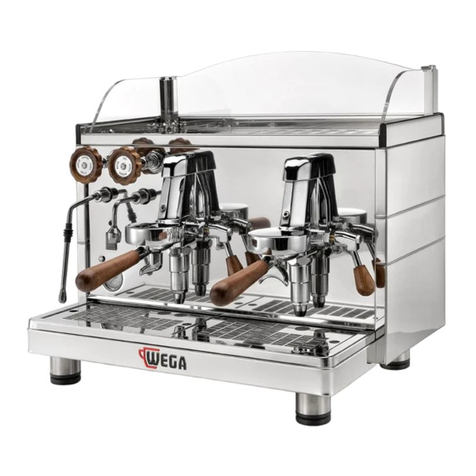
Wega
Wega Mininova Classic EMA 2GR User manual