WIKA TR10-A User manual

Operating instructions
Betriebsanleitung
Mode d‘emploi
Manual de instrucciones
EN
DE
FR
ES
Resistance thermometers (RTD) and thermocouples (TC)
Widerstandsthermometer (RTD) und Thermoelemente (TC)
Sondes à résistance (RTD) et thermocouples (TC)
Termorresistencias (RTD) y termopares (TC)
Examples/Beispiele/Exemples/Ejemplos

EN
DE
FR
ES
2
14150915.03 11/2018 EN/DE/FR/ES
WIKA operating instructions RTD and TC
Operating instructions models RTD and TC
Page
3 - 24
Betriebsanleitung Typen RTD und TC
Seite
25 - 46
Mode d'emploi types RTD et TC
Page
47 - 68
Manual de instrucciones modelos RTD y TC
Página
69 - 90
© 06/2010 WIKA Alexander Wiegand SE & Co. KG
All rights reserved. / Alle Rechte vorbehalten.
WIKA®is a registered trademark in various countries.
WIKA®ist eine geschützte Marke in verschiedenen Ländern.
Prior to starting any work, read the operating instructions!
Keep for later use!
Vor Beginn aller Arbeiten Betriebsanleitung lesen!
Zum späteren Gebrauch aufbewahren!
Lire le mode d‘emploi avant de commencer toute opération !
A conserver pour une utilisation ultérieure !
¡Leer el manual de instrucciones antes de comenzar cualquier trabajo!
¡Guardar el manual para una eventual consulta!

EN
Contents
Contents
14150915.03 11/2018 EN/DE/FR/ES
WIKA operating instructions RTD and TC
3
1. General information 4
2. Design and function 4
3. Safety 5
4. Transport, packaging and storage 9
5. Commissioning, operation 10
6. Additional notes for instruments with EHEDG and 3-A 18
7. Faults 19
8. Maintenance, cleaning and calibration 20
9. Dismounting, return and disposal 21
10. Specifications 23
11. Accessories 24

EN
1. General information / 2. Design and function
14150915.03 11/2018 EN/DE/FR/ES
WIKA operating instructions RTD and TC
4
1. General information
■
The thermometers described in the operating instructions have been manufactured
using state-of-the-art technology.
■
These operating instructions contain important information on handling the instrument.
Working safely requires that all safety instructions and work instructions are observed.
■
Observe the relevant local accident prevention regulations and general safety
regulations for the instrument's range of use.
■
Skilled personnel must have carefully read and understood the operating instructions
prior to beginning any work.
■
Subject to technical modifications.
■
Further information:
- Internet address: www.wika.de / www.wika.com
- Application consultant: Tel.: +49 9372 132-0
Fax: +49 9372 132-406
info@wika.com
2. Design and function
2.1 Description
These resistance thermometers and thermocouples are used for temperature
measurement in industrial applications.
This document describes instruments in standard version. For applications in hazardous
areas special instrument versions are required.
For further information for operation in hazardous areas, see the additional information for the
corresponding ignition protection type (separate document).
The instrument has been designed and built solely for the intended use described here,
and may only be used accordingly.
Ungrounded measuring point
The model TRxx or model TCxx thermometers consist of a welded tube, a mineral-
insulated sheathed cable or ceramic-insulated thermocouple wires in which the
temperature sensor is located.This is embedded in a ceramic powder, a temperature-
resistant sealing compound, cement compound or a heat transfer paste.

EN
2. Design and function / 3. Safety
14150915.03 11/2018 EN/DE/FR/ES
WIKA operating instructions RTD and TC
5
Thermocouples, non-insulated (grounded)
For special applications, for example surface temperature measurements, the sensors are
in direct contact with the protective sleeve, or the measuring points of thermocouples are
welded to the bottom.
Electrical connection
In terms of connection, the thermometer has a case and a plug or bare wire ends.The case
design will contain the connection terminals or certified transmitters. Optionally, separately
certified digital displays can be built into the cases.
2.2 Scope of delivery
Cross-check scope of delivery with delivery note.
3. Safety
3.1 Explanation of symbols
WARNING!
... indicates a potentially dangerous situation that can result in serious injury
or death, if not avoided.
CAUTION!
... indicates a potentially dangerous situation that can result in light injuries or
damage to equipment or the environment, if not avoided.
WARNING!
... indicates a potentially dangerous situation that can result in burns, caused
by hot surfaces or liquids, if not avoided.
Insulated measuring point (ungrounded) Non-insulated measuring point (grounded)
Thermocouple ThermocoupleMeasuring point Measuring point
Sheath Sheath

EN
3. Safety
14150915.03 11/2018 EN/DE/FR/ES
WIKA operating instructions RTD and TC
6
Information
... points out useful tips, recommendations and information for efficient and
trouble-free operation.
3.2 Intended use
The thermometers described here are suitable for temperature measurement in industrial
applications.
Depending on design, these thermometers can be mounted directly into the process or
within a thermowell.The designs of the thermowells can be selected as desired, but the
operational process data (temperature, pressure, density and flow rate) must be taken into
account.
Neither repairs nor structural modifications are permitted, and any would void the
guarantee and the respective certification. The manufacturer shall not be responsible for
constructional modifications after delivery of the instruments.
The instrument has been designed and built solely for the intended use described here,
and may only be used accordingly.
The technical specifications contained in these operating instructions must be observed.
The manufacturer shall not be liable for claims of any type based on operation contrary to
the intended use.
3.3 Responsibility of the operator
The system operator is responsible for selecting the thermometer or thermowell, and for
the selection of their materials, so as to guarantee their safe operation within the plant or
machine.When preparing a quote, WIKA can only give recommendations which are based
on our experience in similar applications.
The safety instructions within these operating instructions, as well as the safety, accident
prevention and environmental protection regulations for the application area must be
maintained.
The operator is obliged to maintain the product label in a legible condition.

EN
3. Safety
14150915.03 11/2018 EN/DE/FR/ES
WIKA operating instructions RTD and TC
7
3.4 Personnel qualification
WARNING!
Risk of injury should qualification be insufficient
Improper handling can result in considerable injury and damage to
equipment.
▶
The activities described in these operating instructions may only be
carried out by skilled electrical personnel who have the qualifications
described below.
Skilled electrical personnel
Skilled electrical personnel are understood to be personnel who, based on their technical
training, know-how and experience as well as their knowledge of country-specific
regulations, current standards and directives, are capable of carrying out work on
electrical systems and independently recognising and avoiding potential hazards. The
skilled electrical personnel have been specifically trained for the work environment they
are working in and know the relevant standards and regulations.The skilled electrical
personnel must comply with current legal accident prevention regulations.
Operating personnel
The personnel trained by the operator are understood to be personnel who, based on their
education, knowledge and experience, are capable of carrying out the work described and
independently recognising potential hazards.
Special operating conditions require further appropriate knowledge, e.g. of aggressive
media.

EN
3. Safety
■
Product label for Tx10-A measuring insert
14150915.03 11/2018 EN/DE/FR/ES
WIKA operating instructions RTD and TC
8
3.5 Labelling, safety marks
Product labels (examples)
TR10-B
1 x Pt100 / B / 3 (F) -50 ... +250 °C
IEC 60751
Made in Germany
2015
11012345
T32 4 ... 20 mA -50 ... +250 °C
TR10-A
11012345
1 x Pt100 / B / 3
-50 ... +250 °C
D = 6 mm
525 mm
(F)
D-63911 Klingenberg
HART ®
TC10-B
1 x Type K / 1 / . 0 ... 1260 °C
IEC 60584
Made in Germany
2015
11012345
T32 4 ... 20 mA -50 ... +250 °C
D-63911 Klingenberg
HART ®
Made in Germany 2015
D-63911 Klingenberg
IEC 60751
TC10-A
11012345
1 x Type K / 1 / .
0 ... 1260 °C
D = 2 mm
Made in Germany 2015
D-63911 Klingenberg
IEC 60584
525 mm
TR10-B
1 x Pt100 / B / 3 (F) -50 ... +250 °C
IEC 60751
Made in Germany
2015
11012345
T32 4 ... 20 mA -50 ... +250 °C
TR10-A
11012345
1 x Pt100 / B / 3
-50 ... +250 °C
D = 6 mm
525 mm
(F)
D-63911 Klingenberg
HART ®
TC10-B
1 x Type K / 1 / . 0 ... 1260 °C
IEC 60584
Made in Germany
2015
11012345
T32 4 ... 20 mA -50 ... +250 °C
D-63911 Klingenberg
HART ®
Made in Germany 2015
D-63911 Klingenberg
IEC 60751
TC10-A
11012345
1 x Type K / 1 / .
0 ... 1260 °C
D = 2 mm
Made in Germany 2015
D-63911 Klingenberg
IEC 60584
525 mm
Model
Serial number
Information on version (measuring element, measuring range...)
Sensor in accordance with standard (resistance thermometer)
■
F = Thin-film measuring resistor
■
FT = Thin-film measuring resistor, sensitive tip
■
W = Wire-wound measuring resistor
Sensor in accordance with standard (thermocouple)
■
ungrounded
■
grounded
Transmitter model (only for design with transmitter)
Year of manufacture

EN
3. Safety / 4. Transport, packaging and storage
14150915.03 11/2018 EN/DE/FR/ES
WIKA operating instructions RTD and TC
9
Sensor symbol
■
ungrounded = ungrounded welded
■
grounded = welded to the sheath (grounded)
■
quasi grounded = The thermometer is, due to its low isolation clearances between
sensor and sheath, to be considered as grounded.
Before mounting and commissioning the instrument, ensure you
read the operating instructions!
4. Transport, packaging and storage
4.1 Transport
Check the instrument for any damage that may have been caused by transport.
Obvious damage must be reported immediately.
CAUTION!
Damage through improper transport
With improper transport, a high level of damage to property can occur.
▶
When unloading packed goods upon delivery as well as during internal
transport, proceed carefully and observe the symbols on the packaging.
▶
With internal transport, observe the instructions in chapter 4.2 “Packaging
and storage”.
If the instrument is transported from a cold into a warm environment, the formation of
condensation may result in instrument malfunction. Before putting it back into operation,
wait for the instrument temperature and the room temperature to equalise.
4.2 Packaging and storage
Do not remove packaging until just before mounting.
Permissible conditions at the place of storage:
Storage temperature:
Instruments without built-in transmitter: -40 ... +80 °C
Instruments with built-in transmitter: see operating instructions of the transmitter in
question
Avoid exposure to the following factors:
■
Direct sunlight or proximity to hot objects
■
Mechanical vibration, mechanical shock (putting it down hard)
■
Soot, vapour, dust and corrosive gases
■
Hazardous environments, flammable atmospheres

EN
4. Transport, packaging ... / 5. Commissioning, operation
14150915.03 11/2018 EN/DE/FR/ES
WIKA operating instructions RTD and TC
10
Store the instrument in its original packaging in a location that fulfils the conditions listed
above. If the original packaging is not available, pack and store the instrument as described
below:
1. Place the instrument, along with the shock-absorbent material, in the packaging.
2. If stored for a prolonged period of time (more than 30 days), place a bag containing a
desiccant inside the packaging.
5. Commissioning, operation
WARNING!
Damage to the measuring instrument by operation outside the upper
or lower limits of the operating temperature
Failure to observe the permissible operating temperature, also taking
into account convection and radiation, can even cause damage to the
thermometer during mounting.
▶
The upper and lower limits of the specified operating temperature range
must not be exceeded.
5.1 Mechanical mounting
5.1.1 Multipoint assemblies
They are usually equipped with a case in which transmitters or terminal blocks are
mounted.
The transmitters/digital displays are fastened mechanically (e.g. rail system in case or
holder in connection head).
5.1.2 Cable probe
These are generally not fitted with a case.They can, however, be connected in an
additional case in which transmitter or terminal blocks are mounted.
5.1.3 Parallel threads
If the thermometer connecting head, neck tube, thermowell or process connection are
connected with parallel threads (e.g. G ½, M20 x 1.5 ...), these threads must be secured
using seals which prevent liquids from penetrating into the thermometer.
As standard, WIKA uses copper seals for the connection between the neck tube and the
thermowell, and a paper flat gasket for the connection of the connection head and the neck
tube or thermowell.
If the thermometer and the thermowell are already connected, the seals will already be
mounted (if ordered).The plant operator must check whether the seals are suitable for the
operating conditions and must replace them, if necessary, with suitable seals (see chapter
11 “Accessories”).
Seals must be replaced after dismounting!

EN
5. Commissioning, operation
14150915.03 11/2018 EN/DE/FR/ES
WIKA operating instructions RTD and TC
11
5.1.4 Tapered threads
With NPT or other tapered threads, it should be checked whether it may be necessary
to seal them additionally with PTFE tape or hemp.The threads must be lubricated with a
suitable lubricant before fitting.
5.1.5 Mounting instructions for electrical thermometers with ceramic protection tube
Ceramic thermowell materials withstand changes in temperature only to a limited extent. A
temperature shock can therefore easily result in stress cracks and consequently in damage
to the protection tube.
For this reason, preheat thermocouples with ceramic or sapphire protection tubes before
installation, and then slowly immerse them into the hot process.
In accordance with DIN 43724, an insertion speed of 1 cm/min is recommended for protec-
tion tubes with a diameter of 24/26 mm. For smaller diameters of 10/15 mm, the speed can
be increased to 50 cm/min. As a basic principle, higher process temperatures require a
lower insertion speed.
In addition to the protection from thermal stress, ceramic protection tubes must also be
protected from mechanical loads.The reason for these harmful stresses are bending forces
in case of a horizontal mounting position. As a consequence, an additional support must
be provided in case of a horizontal mounting position depending on the diameter, greater
nominal lengths and the design.
In principle, the deflection problem also occurs for metal protection tubes, particularly
for insertion lengths > 500 mm. For process temperatures > 1,200 °C, vertical mounting
should be preferred.
5.2 Electrical mounting
Using a transmitter/digital display (option):
Observe the contents of the operating instructions for the transmitter/digital display (see
scope of delivery).
Cable glands
Requirements for meeting ingress protection:
■
Only use cable glands within their indicated clamping range (cable diameter suitable for
the cable gland).
■
Do not use the lower clamping area with very soft cable types.
■
Only use round cables (if necessary, slightly oval in cross-section).
■
Do not twist the cable.
■
Repeated opening/closing is possible; however only if necessary, as it might have a
detrimental effect on the ingress protection
■
For cable with a pronounced cold-flow behaviour the gland must be fully tightened.

EN
5. Commissioning, operation
14150915.03 11/2018 EN/DE/FR/ES
WIKA operating instructions RTD and TC
12
3160629.06
red
1 x Pt100, 2-wire 1 x Pt100, 3-wire 1 x Pt100, 4-wire
white white
red
red
red
red
white
white
white white white
white
red
red red
red
red
2 x Pt100, 2-wire 2 x Pt100, 3-wire 2 x Pt100, 4-wire
red
white white red
red
white
black
yellow
yellow
yellow
black
black
white
white
red
red
red
red
black
black
black
black
yellow yellow
yellow
red
white
black
yellow
white
5.3 Electrical connection
CAUTION!
Danger of short circuit
Damage to cables, wires and connection points can lead to malfunction of
the instrument.
▶
Avoid damaging the cables and wires. Fine-stranded leads with bare ends
must be finished with end splices.
5.3.1 Resistance thermometers
■
With terminal block

EN
5. Commissioning, operation
14150915.03 11/2018 EN/DE/FR/ES
WIKA operating instructions RTD and TC
13
Without connector
Lemosa connector
3366036.02
1 x Pt100
2-wire
1 x Pt100
3-wire
1 x Pt100
4-wire
2 x Pt100
2-wire
2 x Pt100
3-wire
red
red
red
red
red
red
red
red
white
white
white
white
Connector (male)
Front view
Socket (female)
Front view
white
white
black
black
black
yellow
yellow
3160629.06
1 x Pt100
2-wire
1 x Pt100
3-wire
1 x Pt100
4-wire
2 x Pt100
2-wire
■
With cable or connector
2 x Pt100
3-wire

EN
5. Commissioning, operation
14150915.03 11/2018 EN/DE/FR/ES
WIKA operating instructions RTD and TC
14
Binder
Series 680
Series 423 (shielded)
Binder
Series 680
Series 423 (shielded)
Binder
Series 680
Series 423 (shielded)
Binder
Series 680
Series 423 (shielded)
Binder
Series 692
Screw-in plug (Binder, Amphenol)
3366142.05
View of the connector contacts View of the socket contacts
Connector (male) Socket (female)
Amphenol
C16-3
1 x Pt100
2-wire
1 x Pt100
3-wire
1 x Pt100
4-wire
2 x Pt100
2-wire
2 x Pt100
3-wire
2 x Pt100
4-wire

EN
5. Commissioning, operation
14150915.03 11/2018 EN/DE/FR/ES
WIKA operating instructions RTD and TC
15
5.3.2 Thermocouples
■
With terminal block
Single thermocouple Dual thermocouple
The colour coding
at the positive poles
of the instrument
decides the
correlation of polarity
and terminal.
3166822.03
Type of sensor Standard Positive Negative
KIEC 60584 Green White
JIEC 60584 Black White
EIEC 60584 Violet White
NIEC 60584 Pink White
Colour code of cable strands
■
With cable or connector
3171966.01
3374896.01
Lemosa connector,
male on the cable
Binder connector,
male on the cable
(screw-in plug)
Single
thermocouple
For the marking
of the cable ends,
see table
Cable
Dual
thermocouple
Positive and negative terminal are marked.
Two thermo connectors are used with dual
thermocouples.
Thermo connector
3374900.01a

EN
5. Commissioning, operation
14150915.03 11/2018 EN/DE/FR/ES
WIKA operating instructions RTD and TC
16
5.4 Temperature carry-over from the process
A heat reflux from the process that exceeds the operating temperature of the transmitter
(digital display) or case is not permitted and must be prevented by installing suitable heat
insulation or a respectively long neck tube.
Increasing the distance of the connection components to hot surfaces
The neck length (N) is defined as the distance between the lower edge of the connection
head or case and the heat-emitting surface.The expected temperature at the lower edge
of the connection head or case should be a maximum of 80 °C.The conditions for built-in
transmitters or displays must be considered, and if needed, the neck length should be
increased.
3160670.07
tapered threadparallel thread
To help select the minimum neck length, the following standard values have been
determined.
Maximum medium temperature Recommendation for
dimension N
Recommendation for
dimension X
100 °C - -
135 °C 20 mm 20 mm
200 °C 50 mm 50 mm
> 200 °C ≤ 450 °C 100 mm 100 mm
For thermometers fitted with a connecting cable, the temperature at the interface with the
connecting cable is restricted.The maximum is 150 °C.To ensure that the permissible
temperature is not exceeded, the dimension X must be selected accordingly.

EN
5. Commissioning, operation
14150915.03 11/2018 EN/DE/FR/ES
WIKA operating instructions RTD and TC
17
Increasing the distance of the connection components to hot surfaces
The length X is defined as the distance between the transition point from the cable to
the heat-emitting surface.The expected temperature at the transition point should be a
maximum of 120 °C.
▶
If necessary, the X length should be increased.
11355647.01
Thread Thread(NPT)

EN
6. Additional notes for instruments with EHEDG and 3-A
14150915.03 11/2018 EN/DE/FR/ES
WIKA operating instructions RTD and TC
18
6. Additional notes for instruments with EHEDG and 3-A
6.1 Compliance with the conformity in accordance with 3-A
For a 3-A compliant connection for milk thread fittings per DIN 11851, suitable profile
sealings have to be used (e.g. SKS Komponenten BV or Kieselmann GmbH).
Note:
To maintain the 3-A certification, one of the 3-A-approved process connections must be
used.These are marked with the logo in the data sheet.
6.2 Compliance with EHEDG conformity
For an EHEDG conform connection, sealings in accordance with the current EHEDG policy
document must be used.
Manufacturers of sealings
■
Sealings for connections per ISO 2852, DIN 32676 and BS 4825 part 3:
e.g. Combifit International B.V.
■
Sealings for connections per DIN 11851: e.g. Kieselmann GmbH
■
VARIVENT®sealings: e.g. GEA Tuchenhagen GmbH
■
Neumo BioControl®sealings: e.g. Neumo GmbH & Co. KG
6.3 Mounting instructions
Observe the following instructions, especially for EHEDG certified and 3-A conform
instruments.
■
To maintain the EHEDG certification, one of the EHEDG-recommended process
connections must be used.These are marked with the logo in the data sheet.
■
To maintain the conformity to the 3-A standard, a 3-A conform process connection must
be used.These are marked with the logo in the data sheet.
■
Mount the electrical thermometer including thermowell with minimal dead space and
able to be cleaned easily.
■
The mounting position of the electrical thermometer including thermowell, welding
socket and instrumentation T-piece should be designed to be self-draining.
■
The mounting position must not form a draining point or cause a basin to be formed.
6.4 Cleaning in place (CIP) cleaning process
■
When cleaning from outside (“wash down”), observe the permissible temperature and
ingress protection.
■
Only use cleaning agents which are suitable for the seals used.
■
Cleaning agents must not be abrasive nor corrosively attack the materials of the wetted
parts.
■
Avoid thermal shocks or fast changes in the temperature.The temperature difference
between the cleaning agent and rinsing with clear water should be as low as possible.
Negative example: Cleaning with 80 °C and rinsing at +4 °C with clear water.

EN
7. Faults
14150915.03 11/2018 EN/DE/FR/ES
WIKA operating instructions RTD and TC
19
7. Faults
CAUTION!
Physical injuries and damage to property and the environment
If faults cannot be eliminated by means of the listed measures, the instrument
must be taken out of operation immediately.
▶
Ensure that there is no longer any signal present and protect against being
put into operation accidentally.
▶
Contact the manufacturer.
▶
If a return is needed, please follow the instructions given in chapter 9.2
“Return”.
WARNING!
Physical injuries and damage to property and the environment caused
by hazardous media
Upon contact with hazardous media (e.g. oxygen, acetylene, flammable
or toxic substances), harmful media (e.g. corrosive, toxic, carcinogenic,
radioactive), and also with refrigeration plants and compressors, there is a
danger of physical injuries and damage to property and the environment.
Should a failure occur, aggressive media with extremely high temperature
and under high pressure or vacuum may be present at the instrument.
▶
For these media, in addition to all standard regulations, the appropriate
existing codes or regulations must also be followed.
▶
Wear the required protective equipment (depending on the application; the
thermometer itself is basically not dangerous).
For contact details, please see chapter 1 “General information” or the back
page of the operating instructions.
Faults Causes Measures
No signal/cable break Mechanical load too high or
overtemperature
Replace probe or measuring insert
with one of a suitable design
Erroneous measured
values
Sensor drift caused by
overtemperature
Replace probe or measuring insert
with one of a suitable design
Sensor drift caused by chemical
attack
Use a suitable thermowell.
Erroneous measured
values (too low)
Entry of moisture into cable or
measuring insert
Replace probe or measuring insert
with one of a suitable design
Erroneous measured
values and response
times too long
Wrong mounting geometry, for
example mounting depth too
deep or heat dissipation too high
The temperature-sensitive
area of the sensor must be
inside the medium, and surface
measurements must be ungrounded
Deposits on the sensor or
thermowell
Remove deposits

EN
7. Faults / 8. Maintenance, cleaning and calibration
14150915.03 11/2018 EN/DE/FR/ES
WIKA operating instructions RTD and TC
20
Faults Causes Measures
Erroneous measured
values
(of thermocouples)
Parasitic voltages (thermal
voltages, galvanic voltage) or
wrong equalisation line
Use suitable compensating cable
Display of measured
value jumps
Cable break in connecting cable
or loose contact caused by
mechanical overload
Replace probe or measuring insert
with a suitable design, for example
equipped with a strain relief or a
thicker conductor cross-section
Corrosion Composition of the medium not
as expected or modified or wrong
thermowell material selected
Analyse medium and then select a
more suitable material or replace
thermowell regularly
Signal interference Stray currents caused by electric
fields or earth loops
Use shielded connecting cables,
and increase the distance to
motors and power cables
Earth loops Eliminate potential differences by
using galvanically isolated barriers
or transmitters
8. Maintenance, cleaning and calibration
For contact details, please see chapter 1 “General information” or the back
page of the operating instructions.
8.1 Maintenance
The thermometers described here are maintenance-free.
Repairs must only be carried out by the manufacturer.
8.2 Cleaning
CAUTION!
Physical injuries and damage to property and the environment
Improper cleaning may lead to physical injuries and damage to property and
the environment. Residual media in the dismounted instrument can result in a
risk to persons, the environment and equipment.
▶
Carry out the cleaning process as described below.
This manual suits for next models
40
Table of contents
Languages:
Other WIKA Thermometer manuals
Popular Thermometer manuals by other brands
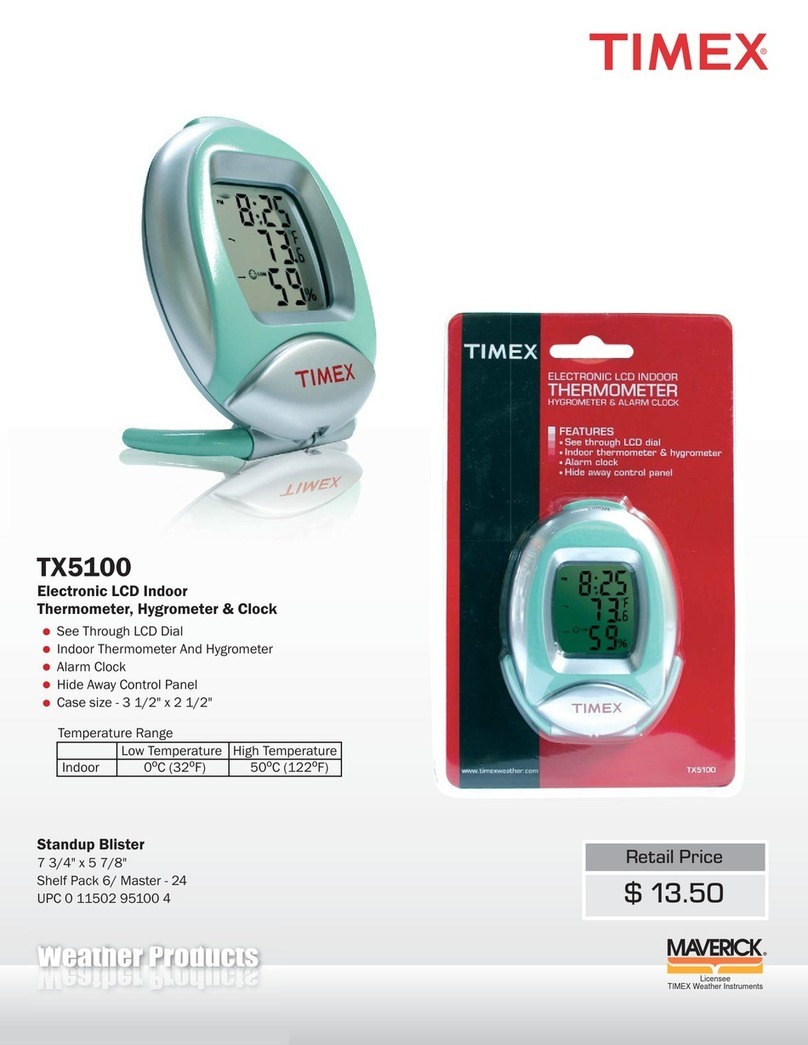
Timex
Timex TX-5100 Specification sheet
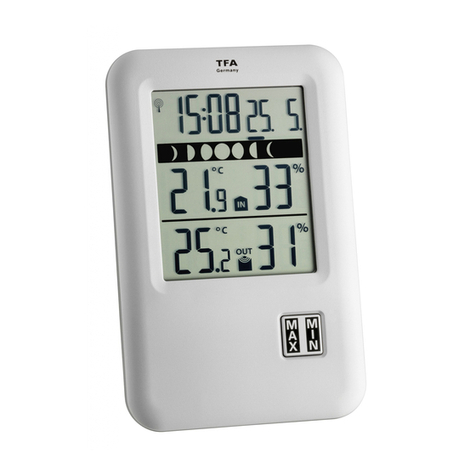
TFA
TFA 30.3044.IT instruction manual
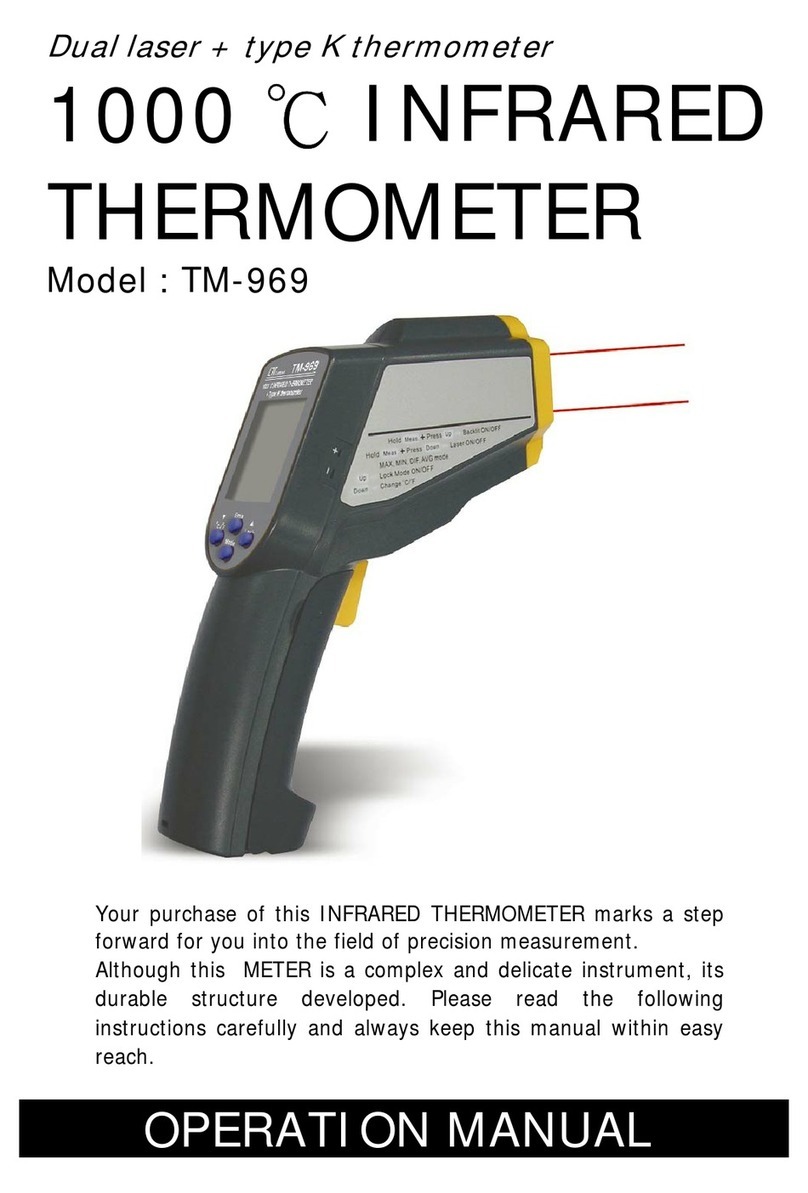
Sechang Instruments
Sechang Instruments TM-969 Operation manual
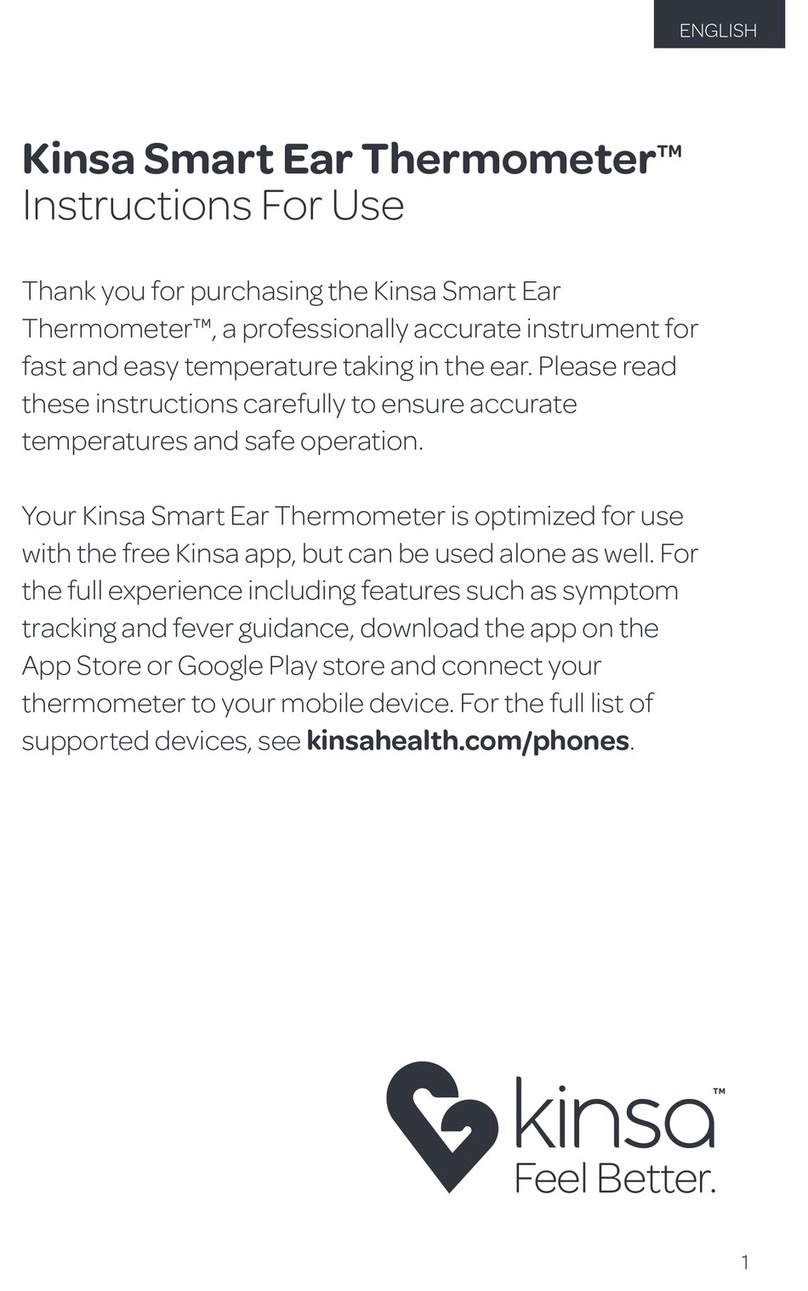
Kinsa
Kinsa Smart Ear Thermometer A-10240 Instructions for use

TaiDoc Technology Corporation
TaiDoc Technology Corporation TD-1242 Operation instructions
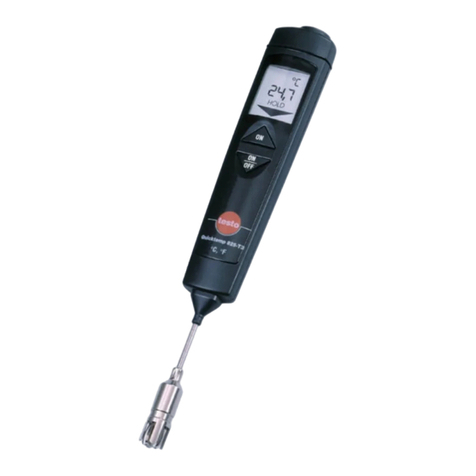
TESTO
TESTO 825-T1 instruction manual