Zander Aachen SR3E User manual

H. ZANDER GmbH & Co. KG • Am Gut Wolf 15 • 52070 Aachen • Germany
Tel +49 (0)241 9105010 • Fax +49 (0)241 91050138 • info@zander-aachen.de • www.zander-aachen.de
1
Safety Relay for Elevators SR3E
N03
Ver. A
E61-421-00
Operating Instructions English translation
Errors and technical changes reserved
Automatic or manual start
Short-circuit monitoring and ground faultt monitoring
Up to PL e, SILCL 3, category 4
(EN ISO 13849-1 / EN 62061 / EN 61508)
Correct Use SR3E is an all-purpose emergency stop device with three safe
relay contacts for safe monitoring of one or two channel sensors.
The SR3E is specially designed for the use as safety component
in elevators according to EN 81-20 and EN 81-50, certified by
TÜV Rheinland.
Further applications for the SR3E include single or dual-channel
emergency stop circuits and guard monitoring on machines and
plants according to EN ISO 13849-1, EN 62061 and EN 61508.
3 non-delayed safety contacts
1 non-delayed auxiliary contact
Connection of:
- Emergency stop buttons
- Mechanical Safety switches
- Non-contact safety switches
- Safety components with OSSD-Outputs
Control: single or dual channel
Feedback loop for external contactors or extension
modules
Cyclical monitoring of the output contacts
LED indicator for power and status
Function The safety relay SR3E is designed for isolation of safety circuits according to EN 60204-1, stop-category 0 and can be used
in safety-related applications up to safety category 4, PL e (EN ISO 13849-1) SILCL 3 (EN 62061 / EN 61508) and as a safe-
ty component in elevators according EN 81-20.
Electrical
Connection
A safety transformer according to EN 61558-2-6 or a
power supply unit with electrical isolation from the mains
must be connected
Observe the instructions in the section “Tech. Data”
If the device does not function after commissioning, it
must be returned to the manufacturer unopened. Open-
ing the device will void the warranty
The auxiliary contact 41-42 may not be used as a safety
contact
Use adequate protective circuit for inductive loads (e.g.
free-wheeling diode)
Installation As per EN 60204-1, the device is intended for installation
in control cabinets with a minimum degree of protection of
IP54. The following should be noted:
Mounting on 35 mm rail according to EN 60715
Ensure sufficient heat dissipation in the control cabinet
Minimum distance to adjacent devices according to the
total current limit curve
Safety
Precautions
Fig. 1 Block diagram SR3E
Fig. 3 Mounting / Demounting
Fig. 4 Terminals
A1: Power supply
A2 : Power supply
S11: Control voltage
S10: Control line
S21: Start control line
S13: Control line
S14: Control line
S12: Control line
13-14: Safety contact 1
23-24: Safety contact 2
33-34: Safety contact 3
41-42: Auxiliary contact
to the device.
It is not allowed to open the device, tamper with the
device or bypass the safety devices.
All relevant safety regulations and standards are to be
observed.
The overall concept of the control system in which the
device is incorporated must be validated by the user.
Failure to observe the safety regulations can result in
death, serious injury and serious damage.
Note down the version of the product (see label “Ver.”)
and check it prior to every commissioning of a new de-
vice. If the version has changed, the overall concept of
the control system in which the device is incorporated
must be validated again by the user.
Installation and commissioning of the device must be
performed only by authorized personnel and who has
read and understood this operating instructions.
Observe the country-specific regulations when installing
the device.
The electrical connection of the device is only allowed to
be made with the device isolated.
The wiring of the device must comply with the instruc-
tions in this operating instructions, otherwise there is a
risk that the safety function will be lost.
It is not allowed to open the device, tamper with the
device or bypass the safety devices.
The contact protection and the insulation of the supply
cables must be designed for the highest voltage
Fig. 2 State diagram for SR3E with manual start

H. ZANDER GmbH & Co. KG • Am Gut Wolf 15 • 52070 Aachen • Germany
Tel +49 (0)241 9105010 • Fax +49 (0)241 91050138 • info@zander-aachen.de • www.zander-aachen.de
2
Safety Relay for Elevators SR3E
N03
Ver. A
E61-421-00
Operating Instructions English translation
Errors and technical changes reserved
Fig. 10:
Connecting to a safety PLC
(category 4, up to PL e / SIL 3)
Prerequisite:
Safe PLC output meets the
required safety level and short
circuit between PLC output and
SR3E can be excluded
(e.g. wiring inside an electrical
installation space - see EN ISO
13849-2; Tab D4).
Fig. 9:
Two channel emergency stop with
pnp-outputs/OSSD-outputs with
its own short circuit monitoring.
(category 4, up to PL e / SIL 3)
Prerequisite:
Signal generator meet require-
ments for PL e / SIL 3, too.
Fig. 5:
Dual channel emergency stop
with short circuit and ground fault
monitoring.
(category 4, up to PL e / SIL 3)
Advice: Follow the guidelines in „Electrical Connection“ during the start-up.
Commissioning
Procedure 1. Input circuit:
Depending on the risk evaluation choose one of the wiring
diagrams in „Applications“ (Fig. 5 to Fig. 10).
2. Choose start mode:
Connect the start button with S11 and S21 for monitored
manual start or connect S21 with S12 directly for automatic
start (Fig. 11 or Fig. 12).
Warning:
If “Automatic start” is set, bear in mind that the safety
contacts will switch immediately after the power supply is
connected. If “Monitored manual start” is set, the start
button must be opened after wiring.
3. Feedback loop:
If external contactors or extension modules are used,
connect them according to Fig. 13 or Fig. 14.
4. Power supply:
Connect the power supply to A1 and A2 (Fig. 13).
Caution: Power must not yet be activated.
5. Starting the device:
Switch on the operating voltage.
Warning:
If the “Automatic start” starting behaviour is set, the safety
contacts will close immediately.
If the “Monitored manual start” starting behaviour is set,
close the start button to close the safety contacts.
LEDs Pwr, K1 and K2 are lit.
6. Triggering safety function:
Open the emergency stop circuit by actuating the connect-
ed safety switch. The safety contacts open immediately.
7. Reactivation:
Close the emergency stop circuit. If “Automatic start” is
selected, the safety contacts will close immediately.
If the “Monitored manual start” starting behaviour is set,
close the start button to close the safety contacts.
Fig. 11:
Monitored manual start.
It is monitored that the start button
has been opened before the
safety switch is closed.
Prerequisite:
Power supply may not be inter-
rupted
Fig. 12:
Automatic start.
Maximum allowable delay when
closing the safety switches at
S12 and S13/S14:
S12 before S13/S14: 200ms
S13/S14 before S12: no limit
Warning:
Safety contacts will be
activated immediately at
power-on.
Depending on the application or the result of the risk assessment according to EN ISO 13849-1, the device must be wired as
shown in Fig. 5 to Fig. 16.
Applications
Fig. 7:
Single channel emergency stop
with ground fault monitoring.
(category 1, up to PL c / SIL 1)
Note:
Not suitable for applications in
elevators according to EN 81-20
Fig. 6:
Dual channel emergency stop
with ground faultt monitoring.
(category 3, up to PL d / SIL 2)
Note:
For applications according EN
81-20 a fault exclusion for short
circuit between S12 and S14 is
required
Fig. 8:
Dual channel safety guard
monitoring with short circuit and
ground fault monitoring.
(category 4, up to PL e / SIL 3)
Emergency Stop
Circuit
Start Behaviour
Fig. 13:
Feedback loop for monitored
manual start.
The feedback loop monitors
contactors or the expansion
modules .
Feedback Loop Fig. 14:
Feedback loop for automatic
start.
The feedback loop monitors
contactors or the expansion
modules .
Power supply
and
Safety contacts
Fig. 15:
Power supply A1 and A2.
Fig. 16:
Connecting load to safety con-
tacts. Voltage „+V“ according to
techn. Data.
ATTENTION:
Inductive loads should have
adequate protection circuit such
as a free-wheeling diode.
ATTENTION: Loss of functional safety!
For the applications according Fig. 9 and Fig. 10 the following is to be noted:
Make sure that the ground potential of the signal generator and the SR3E is the same
It must be ensured that any switch-on pulses (light test) sent by the signal generator do not lead to a
short activation of the safety relay and should therefore basically be deactivated.

H. ZANDER GmbH & Co. KG • Am Gut Wolf 15 • 52070 Aachen • Germany
Tel +49 (0)241 9105010 • Fax +49 (0)241 91050138 • info@zander-aachen.de • www.zander-aachen.de
3
Safety Relay for Elevators SR3E
N03
Ver. A
E61-421-00
Operating Instructions English translation
Errors and technical changes reserved
Check and Mainte-
nance
Technical Data In compliance with EN 60204-1; EN ISO 13849-1; IEC 62061; IEC 61508
Parts 1-2 and 4-7; EN 81-20; EN 81-50
Operating voltage DC 24 V +/- 10 %
Power consumption 2.6 W
Inrush current 5 A (approx. 250 µs)
Pulse suppression (A1 / S12 / S14)
Switch-Off pulse / dark test max. 3 ms (Pulse width) / 500 ms (Pulse rate)
Switch-On pulse / light test max. 1 ms (Pulse width) / 500 ms (Pulse rate)
Note: It must be ensured that any switch-on pulses (light
test) sent by the signal generator do not lead to a short
activation of the safety relay and should therefore basically
be deactivated.
Contact configuration 3 NO (Safety contacts) / 1 NC (Auxiliary contact)
Max. switching voltage AC 250 V
Contact rating of safety contacts (13-14, 23-24, 33-34) AC: 250 V, 2000 VA, 8 A for resistive load
6 switching cycles/ min 250 V, 3 A for AC-15
DC: 30 V, 240 W, 8 A for resistive load
24 V, 3 A for DC-13
Thermal current Ith Max. 5 A per contact (see total current limit curve)
Contact rating of auxiliary contact (41-42) AC: 250 V, 500 VA, 2 A for resistive load
DC: 30 V, 60 W, 2 A for resistive load
Minimum contact load 5 V, 10 mA
External fuses 10 A gG (NO); 6 A gG (NC)
Max. switch-on delay < 50 ms
Max. switch-off delay Via A1: < 40 ms; Via S12 or S13/S14 < 20 ms
Recovery time < 500 ms
Wire width 0.14 - 2.5 mm2
Tightening moment (Min. / Max.) 0.5 Nm / 0.6 Nm
Contact material AgSnO2
Service Life mech. approx. 1 x 107
Rated impulse withstand voltage 2.5 kV (control voltage / contacts)
Dielectric strength 4 kV (DIN VDE 0110-1)
Rated insulation voltage 250 V
Degree of pollution / Overvoltage category 2 / 3 (DIN VDE 0110-0)
Protection IP20
Temperature range Ambient -15 °C to +55 °C
Temperature range Storage -15 °C to +85 °C
Max. altitude ≤ 2000 m (above sea level)
Weight approx. 150g
Mounting DIN rail according to EN 60715 TH35
Safety Character-
istics according to
EN ISO 13849-1
Device cannot be switched on after an emergency stop:
Emergency stop circuit was closed again.
Was the start button opened before closing of the emer-
gency stop circuit (manual start)?
Is the feedback loop closed?
If the fault still exists, perform the steps listed under
“Commissioning Procedure”. If these steps do not remedy
the fault either, return the device to the manufacturer.
Device does not switch on:
Check the wiring by comparing it to the wiring diagrams.
Check the safety switch for correct function and adjustment.
Check whether the emergency stop circuit is closed.
Check whether the start button (manual start) is closed.
Check the operating voltage at A1 and A2.
Is the feedback loop closed?
What to do in
Case of a Fault?
Safety Character-
istics according to
EN 62061 /
EN 61508 -
High Demand
No maintenance is required for the device itself.
But the following checks are regularly required to ensure
proper and continuous functioning:
Check the switch function
Check for signs of manipulation and safety function
bypassing
Check if the device is mounted and connected securely
Check for soiling
Check if the safety device is working properly, in particular:
Every time after initial commissioning
Every time after replacing a component
After every fault in the safety circuit
According to CNB / M / 11.050, a request for the safety function is recommended at the following intervals:
Once a month for applications up to PL e with Cat. 3 or Cat. 4 or SIL CL3, SIL 3 with HFT = 1
Once a year for applications up to PL d with Cat. 3 or SIL CL 2, SIL 2 with HFT = 1
Load per contact <= 1 A <= 2A <= 3A
Use duration T10d [years] 20 20 20
Category 4 4 4
PL e e e
PFHd [1/h] 1.2E-08 1.2E-08 1.2E-08
nop [Cycles per year]
AC-15 / DC-13 ≤ 55,000 / ≤ 350,000 ≤ 42,500 / ≤ 100,000 ≤ 42,500 / ≤ 15,000
Load per contact <= 1 A <= 2A <= 3A
Use duration T10d [years] 20 20 20
Proof-Test-Intervall [years] 20 20 20
PFH [1/h] 1.2E-10 1.2E-10 1.2E-10
SIL(CL) 333
nop [Cycles per year]
AC-15 / DC-13 ≤ 55,000 / ≤ 350,000 ≤ 42,500 / ≤ 100,000 ≤ 42,500 / ≤ 15,000

H. ZANDER GmbH & Co. KG • Am Gut Wolf 15 • 52070 Aachen • Germany
Tel +49 (0)241 9105010 • Fax +49 (0)241 91050138 • info@zander-aachen.de • www.zander-aachen.de
4
Safety Relay for Elevators SR3E
N03
Ver. A
E61-421-00
Operating Instructions English translation
Errors and technical changes reserved
Dimension
Drawing
Variants Order No. 472292 SR3E, DC 24 V fixed screw terminals
Order No. 474292 SR3E, DC 24 V incl. plug-in screw terminals
Order No. 475292 SR3E, DC 24 V incl. push-in twin spring connector
Order No. 472596 Spacer for a defined minimum distance between two safety relays (see derating)
Total current limit
curve
Fixed
Terminals
Plug-In
Terminals
Fig. 17: Total current limit depending on the ambient temperature
The max. permissible total current is shown in Fig. 17.
Left: SR3E with 5 mm clearance to adjacent devices, heated with same load
Right: SR3E with no clearance to adjacent devices, heated with same load
Nominal voltage DC 24 V
Overvoltage up to DC 26,4 V
Total current: ∑ Ith² = I1² + I2² + I3² (I1, I2, I3: Current in contact paths 13-14, 23-24, 33-34)
This manual suits for next models
4
Other Zander Aachen Relay manuals
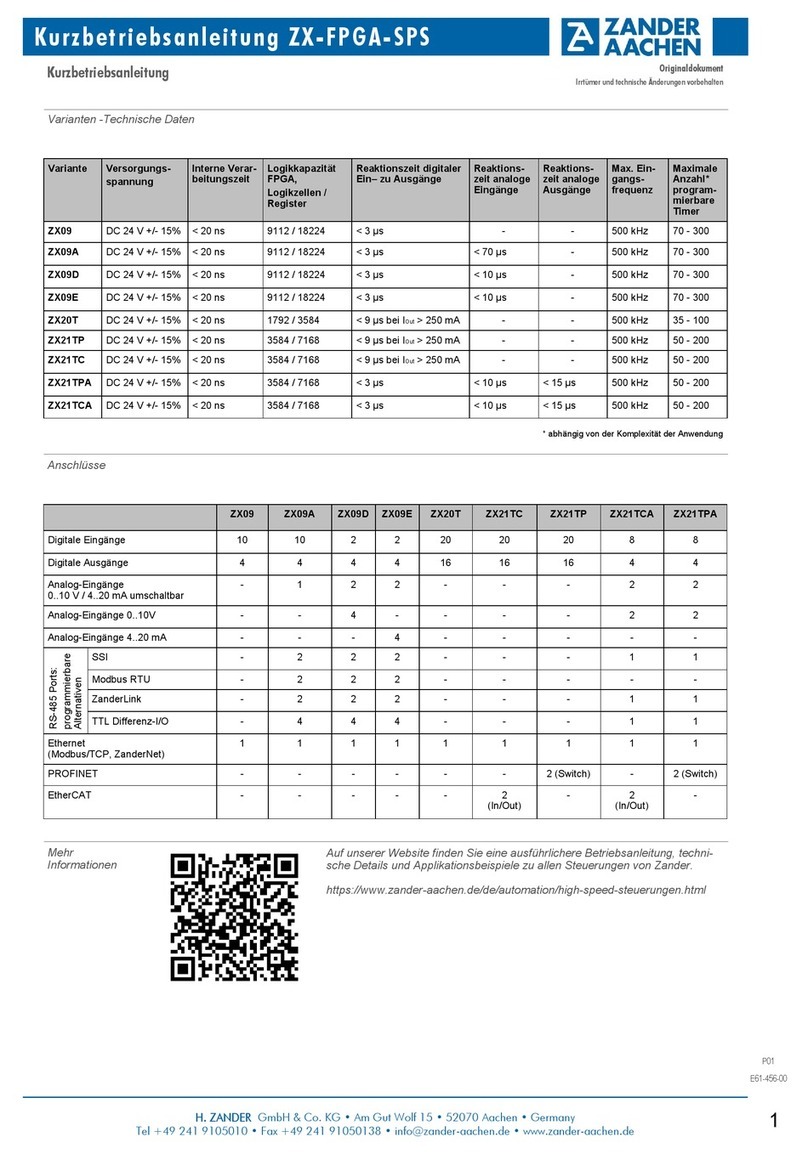
Zander Aachen
Zander Aachen ZX09 Series User manual
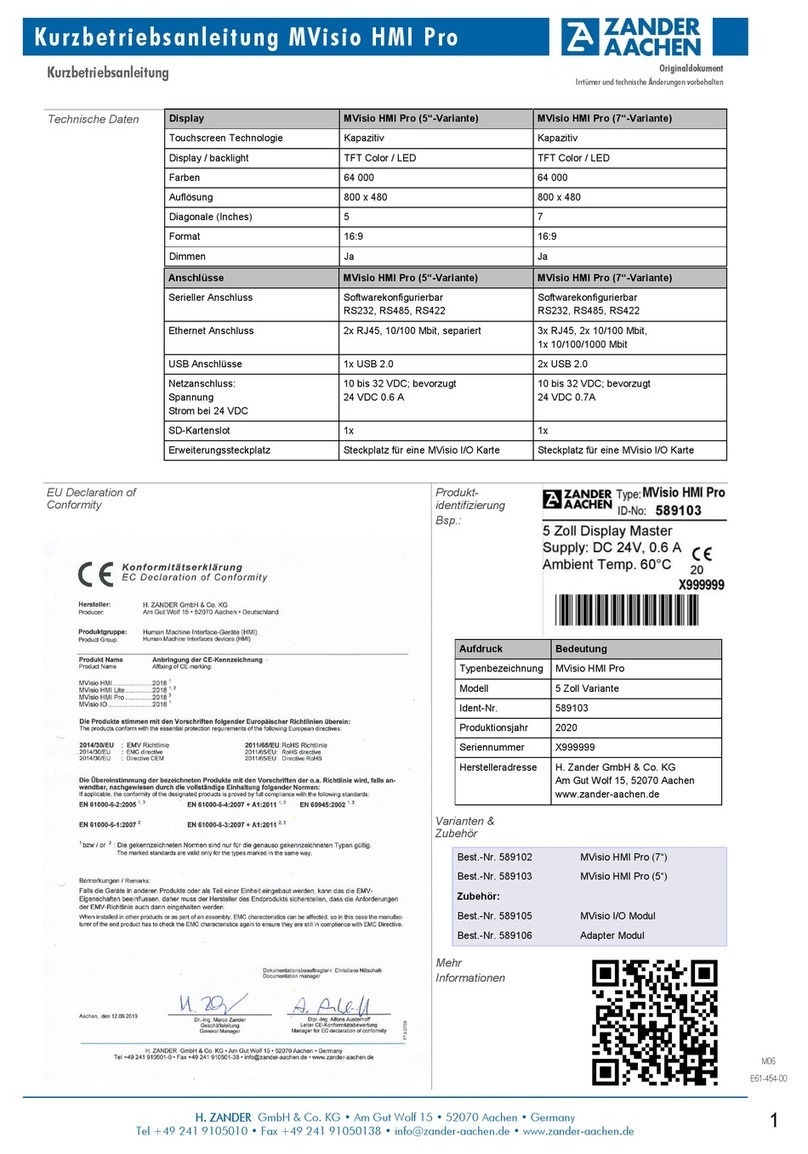
Zander Aachen
Zander Aachen MVisio HMI Pro User manual
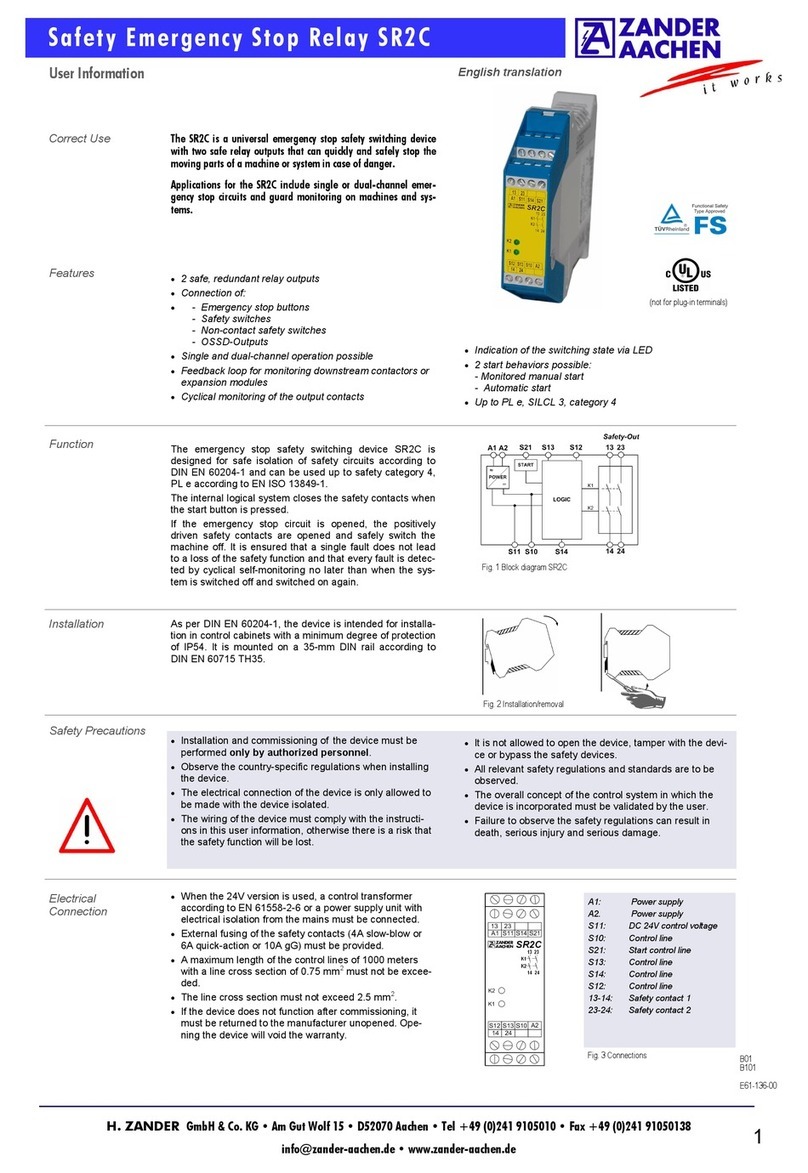
Zander Aachen
Zander Aachen SR2C User manual
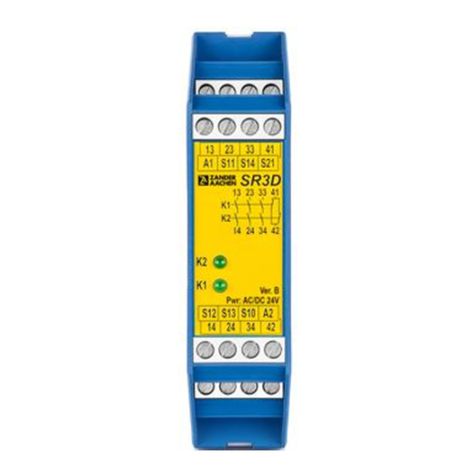
Zander Aachen
Zander Aachen SR3D Operation manual

Zander Aachen
Zander Aachen SPEEDY ZX8T Operation manual
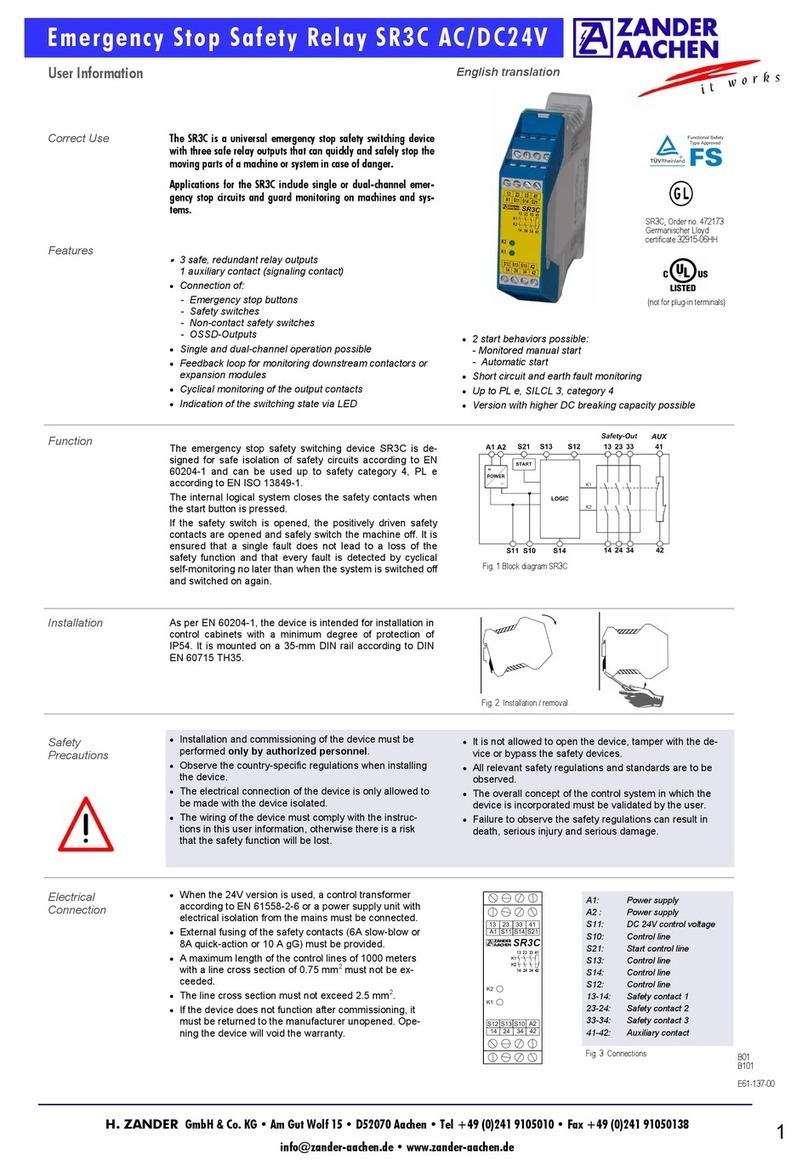
Zander Aachen
Zander Aachen SR3C Operation manual
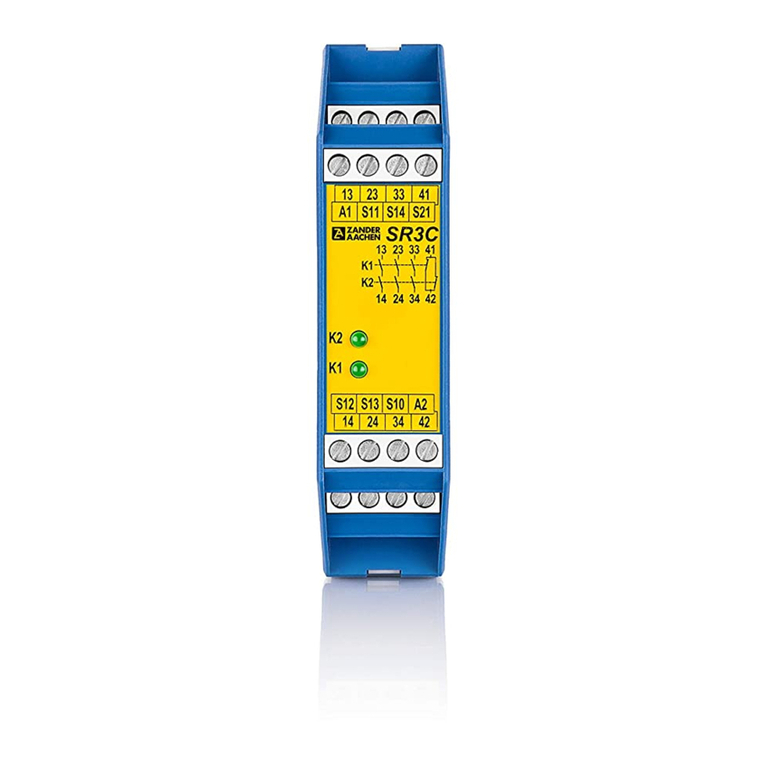
Zander Aachen
Zander Aachen SR3C User manual
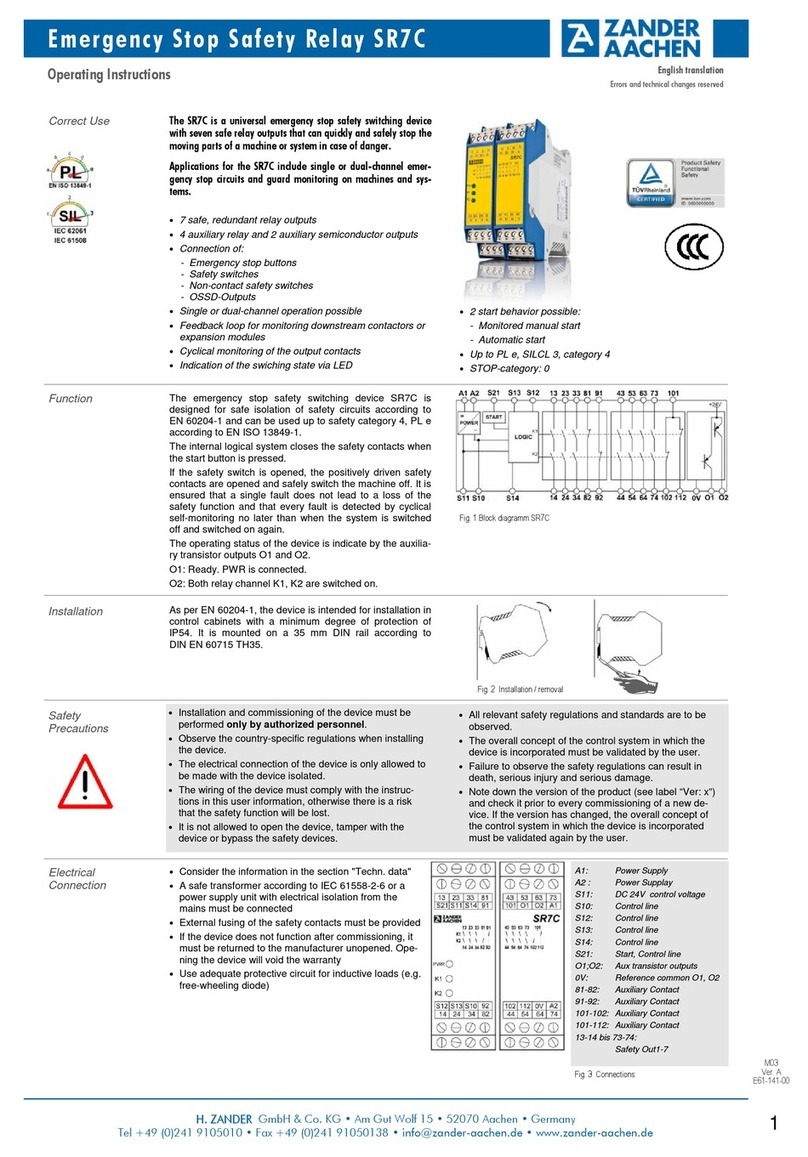
Zander Aachen
Zander Aachen SR7C User manual
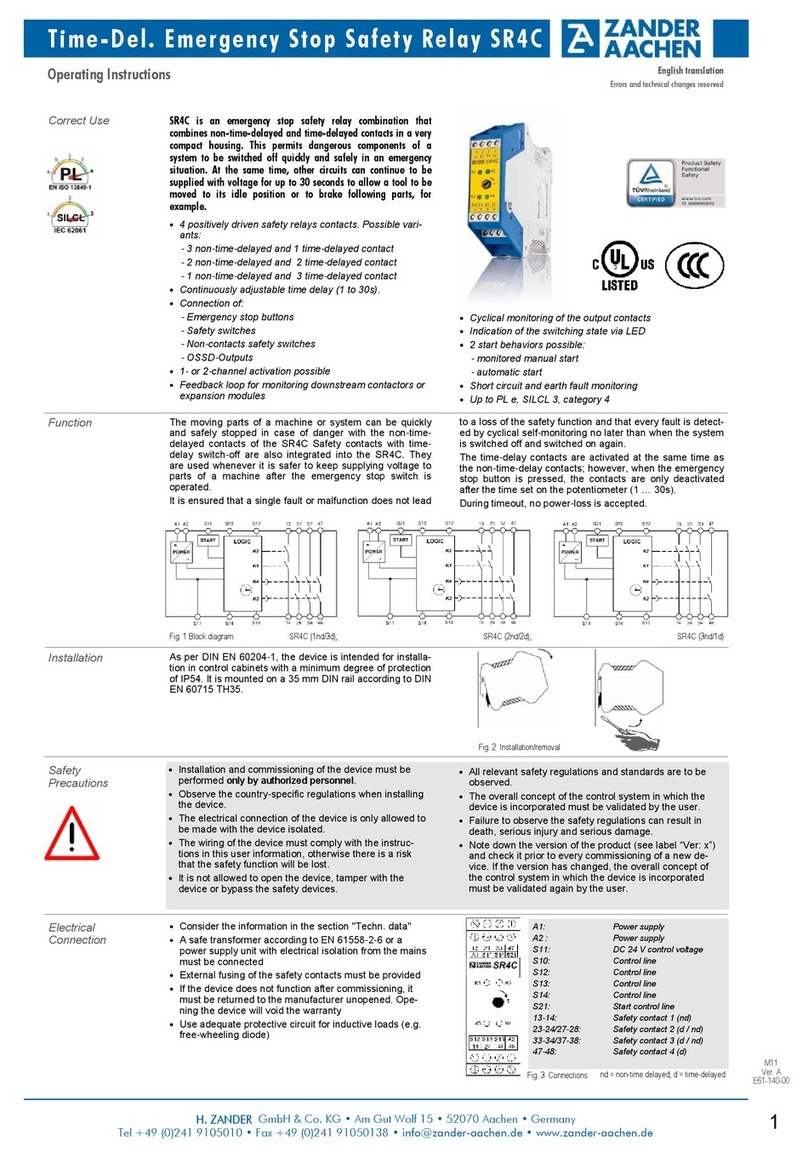
Zander Aachen
Zander Aachen SR4C User manual
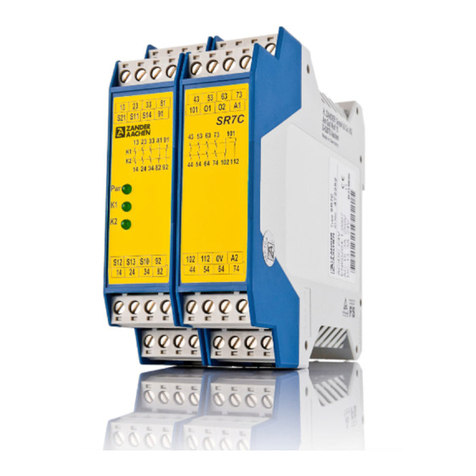
Zander Aachen
Zander Aachen SR7C Operation manual