Zander Aachen SR3C Operation manual

User Information
H. ZANDER GmbH & Co. KG • Am Gut Wolf 15 • D52070 Aachen • Tel +49 (0)241 9105010 • Fax +49 (0)241 91050138
info@zander-aachen.de • www.zander-aachen.de
1
B01
B101
E61-137-00
•
2 start behaviors possible:
- Monitored manual start
- Automatic start
•
Short circuit and earth fault monitoring
•
Up to PL e, SILCL 3, category 4
•
Version with higher DC breaking capacity possible
•
It is not allowed to open the device, tamper with the de-
vice or bypass the safety devices.
•
All relevant safety regulations and standards are to be
observed.
•
The overall concept of the control system in which the
device is incorporated must be validated by the user.
•
Failure to observe the safety regulations can result in
death, serious injury and serious damage.
Correct Use
The SR3C is a universal emergency stop safety switching device
with three safe relay outputs that can quickly and safely stop the
moving parts of a machine or system in case of danger.
Applications for the SR3C include single or dual-channel emer-
gency stop circuits and guard monitoring on machines and sys-
tems.
Features
•
3 safe, redundant relay outputs
1 auxiliary contact (signaling contact)
•
Connection of:
- Emergency stop buttons
- Safety switches
- Non-contact safety switches
- OSSD-Outputs
•
Single and dual-channel operation possible
•
Feedback loop for monitoring downstream contactors or
expansion modules
•
Cyclical monitoring of the output contacts
•
Indication of the switching state via LED
Function
The emergency stop safety switching device SR3C is de-
signed for safe isolation of safety circuits according to EN
60204-1 and can be used up to safety category 4, PL e
according to EN ISO 13849-1.
The internal logical system closes the safety contacts when
the start button is pressed.
If the safety switch is opened, the positively driven safety
contacts are opened and safely switch the machine off. It is
ensured that a single fault does not lead to a loss of the
safety function and that every fault is detected by cyclical
self-monitoring no later than when the system is switched off
and switched on again.
Electrical
Connection
•
When the 24V version is used, a control transformer
according to EN 61558-2-6 or a power supply unit with
electrical isolation from the mains must be connected.
•
External fusing of the safety contacts (6A slow-blow or
8A quick-action or 10 A gG) must be provided.
•
A maximum length of the control lines of 1000 meters
with a line cross section of 0.75 mm
2
must not be ex-
ceeded.
•
The line cross section must not exceed 2.5 mm
2
.
•
If the device does not function after commissioning, it
must be returned to the manufacturer unopened. Ope-
ning the device will void the warranty.
Installation
As per EN 60204-1, the device is intended for installation in
control cabinets with a minimum degree of protection of
IP54. It is mounted on a 35-mm DIN rail according to DIN
EN 60715 TH35.
Safety
Precautions
•
Installation and commissioning of the device must be
performed only by authorized personnel.
•
Observe the country-specific regulations when installing
the device.
•
The electrical connection of the device is only allowed to
be made with the device isolated.
•
The wiring of the device must comply with the instruc-
tions in this user information, otherwise there is a risk
that the safety function will be lost.
Fig. 1 Block diagram SR3C
SR3C, Order no. 472173
Germanischer Lloyd
certificate 32915-06HH
Fig. 2 Installation / removal
Fig. 3 Connections
A1: Power supply
A2 : Power supply
S11: DC 24V control voltage
S10: Control line
S21: Start control line
S13: Control line
S14: Control line
S12: Control line
13-14: Safety contact 1
23-24: Safety contact 2
33-34: Safety contact 3
41-42: Auxiliary contact
Emergency Stop Safety Relay SR3C AC/DC24V
(not for plug-in terminals)
English translation

User Information
H. ZANDER GmbH & Co. KG • Am Gut Wolf 15 • D52070 Aachen • Tel +49 (0)241 9105010 • Fax +49 (0)241 91050138
info@zander-aachen.de • www.zander-aachen.de
2
B01
B101
E61-137-00
Note: The items listed under “Electrical connection” must be observed during commissioning.
Commissioning
Procedure
1. Wiring emergency stop circuit:
Wire the emergency stop circuit according to the required
Performance Level determined (see Fig. 1 to Fig. 5).
2. Wiring start circuit:
Wire the start circuit according to Fig. 6 or Fig. 7 to set the
starting behavior.
Warning:
If “Automatic start” is set, bear in mind that the safety con-
tacts will switch immediately after the power supply is
connected. If “Monitored manual start” is set, the start
button must be opened after wiring.
3. Wiring feedback loop:
If your application provides for external contactors or ex-
pansion modules, connect them to the device according to
Fig. 8 or Fig. 9.
4. Wiring power supply:
Connect the power supply to terminals A1 and A2 (Fig. 10).
Warning: Wiring only in de-energized state.
5. Starting the device:
Switch on the operating voltage.
Warning:
If the “Automatic start” starting behavior is set, the safety
contacts will close immediately.
If the “Monitored manual start” starting behavior is set, close
the start button to close the safety contacts.
LEDs K1 and K2 are lit.
6. Triggering safety function:
Open the emergency stop circuit by actuating the connec-
ted safety switch. The safety contacts open immediately.
7. Reactivation:
Close the emergency stop circuit. If “Automatic start” is
selected, the safety contacts will close immediately.
If the “Monitored manual start” starting behavior is set, close
the start button to close the safety contacts.
Fig. 6:
Monitored manual start.
It is monitored that the start
button was opened before the
emergency stop button closes.
(Prerequisite: operating voltage
must not be interrupted.)
Fig. 7:
Automatic start.
Max perm. delay during closing
of the safety switches on S12
and S13:
S12 before S13: 300 ms
S13 before S12: any
Warning:
Safety contacts switch
immediately when the
power supply is connected.
Depending on the application or the result of the risk assessment according to EN ISO 13849-1, the device must be wired as
shown in Fig. 1 to Fig. 11.
Applications
Fig. 3:
Single-channel emergency stop
circuit with earth fault monitor-
ing.
(category 1, up to PL c)
Fig. 2:
Two-channel emergency stop
circuit with earth fault monitoring.
(category 3, up to PL d)
Fig. 1:
Two-channel emergency stop
circuit with short circuit and earth
fault monitoring.
(category 4, up to PL e)
Fig. 4:
Two-channel sliding guard
monitoring with short circuit and
earth fault monitoring.
(category 4, up to PL e)
Emergency Stop
Circuit
Starting Behavior
Emergency Stop Safety Relay SR3C AC/DC24V
Fig. 8:
Feedback loop for monitored manual
start:
The feedback loop monitors contactors
or the expansion modules .
Feedback Loop
Fig. 9:
Feedback loop for automatic start:
The feedback loop monitors contac-
tors or the expansion modules .
Power supply
and
Safety contacts
Fig. 10:
Power supply A1 and A2.
(Power supply according to techn.
Data )
Fig. 11:
Connecting load to safety contacts.
(Figure shows example.
Voltage „+V“ according to techn.
Data)
Warning only for the 24V version:
In order to activate earth fault monitoring, the PE must be
connected only to the power supply unit in accordance with
EN60204-1.
Fig. 5:
Two-channel emergency stop
with pnp-outputs/OSSD-outputs
with short circuit monitoring.
(category 4, up to PL e)

User Information
H. ZANDER GmbH & Co. KG • Am Gut Wolf 15 • D52070 Aachen • Tel +49 (0)241 9105010 • Fax +49 (0)241 91050138
info@zander-aachen.de • www.zander-aachen.de
3
B01
B101
E61-137-00
Maintenance
The device must be checked once per month for proper
function and for signs of tampering and bypassing of the
safety function.
Techn. Data
Corresponds to the standards EN 60204-1; EN ISO 13849-1 ; EN 62061
Operating voltage AC/DC 24V
Reted supply frequency 50-60 Hz
Permissible deviation + / - 10%
Power consumption DC 24V AC 24V
approx. 2.3W approx. 4.5VA
Control voltage at S11 DC 24V
Control current S11...S14 approx. 60mA
Safety contacts 3 NO contacts
Auxiliary contacts 1 NC contact
Max. switching voltage AC 250V
Version 472172 AC: 250V, 2000VA, 8A for ohmic load,
Safety contact breaking capacity (13-14, 23-24, 33-34) 250V, 3A for AC-15
DC: 24V, 48W, 2A for DC-13
Max. total current 15A (13-14, 23-24, 33-34)
Version 472172 AC: 250V, 500VA, 2A for AC-12
Auxiliary contact breaking capacity (41-42) DC: 50V, 30W, 1.25A for ohmic load
Version 472173 High DC breaking capacity AC: 250V, 2000VA, 8A for ohmic load
Safety contact breaking capacity (13-14, 23-24, 33-34) 250V, 3A for AC-15
DC: 50V, 400W, 8A for ohmic load
24V, 3A, for DC-13
Max. total current through all 3 contacts:
15A (13-14, 23-24, 33-34)
Version 472173 High DC breaking capacity AC: 250V, 500VA, 2A for AC-12
Auxiliary contact breaking capacity (41-42) DC: 50V, 100W, 2A for ohmic load
Minimum contact load 24V, 20mA
Min. Contact fuses 6A slow-blow or 8A quick-action or 10A gG
Max. line cross section 0.14 - 2.5mm
2
Max. length of control line 1000m with 0.75mm
2
Contact material AgNi
Contact service life mech. approx. 1 x 10
7
, electr. 1 x 10
5
operating cycles
Test voltage 2.5kV (control voltage/contacts)
Rated impulse withstand voltage, leakage path/air gap 4kV (DIN VDE 0110-1)
Rated insulation voltage 250V
Degree of protection IP20
Temperature range -15°C to +40°C
Degree of contamination 2 (DIN VDE 0110-1)
Overvoltage category 3 (DIN VDE 0110-1)
Weight approx. 230g
Mounting DIN rail according to EN 60715TH35
Note: Additional data can be requested from the manu-
facturer for applications that deviate from these conditions.
Safety
Characteristics
According to
EN ISO 13849-1
The device is certified according to EN ISO 13849-1 up to a
Performance Level of PL e.
Device cannot be switched on again after an emergency
stop:
•
Check whether the emergency stop circuit was closed
again.
•
Was the start button opened before closing of the emer-
gency stop circuit (with manual start)?
•
Is the feedback loop closed?
If the fault still exists, perform the steps listed under
“Commissioning Procedure”.
If these steps do not remedy the fault either, return the
device to the manufacturer for examination.
Opening the device is impermissible and will void the
warranty.
Device does not switch on:
•
Check the wiring by comparing it to the wiring diagrams.
•
Check the safety switch used for correct function and
adjustment.
•
Check whether the emergency stop circuit is closed.
•
Check whether the start button (with manual start) is
closed.
•
Check the operating voltage at A1 and A2.
•
Is the feedback loop closed?
What to do in
Case of a Fault?
The device is otherwise maintenance free, provided that it
was installed properly.
Emergency Stop Safety Relay SR3C AC/DC24V
Safety characteristics according to EN ISO 13849-1 for all variants of SR3C
Load (DC13; 24V) <= 0,1A <= 1A <= 2A
T10d [years] 20 20 20
Category 4 4 4
PL e e e
PFHd [1/h] 1,2E-08 1,2E-08 1,2E-08
nop [cycle / year] <= 500.000 <= 350.000 <= 100.000

User Information
H. ZANDER GmbH & Co. KG • Am Gut Wolf 15 • D52070 Aachen • Tel +49 (0)241 9105010 • Fax +49 (0)241 91050138
info@zander-aachen.de • www.zander-aachen.de
4
B01
B101
E61-137-00
Dimension
Drawing
114
99
22,5
Variants
Order no. 472172 SR3C, AC/DC 24V, fixed screw terminals
Order no. 472173 SR3C, AC/DC 24V (high DC breaking capacity), fixed screw terminals
Order no. 473172 SR3C, AC/DC 24V, plug-in terminals
Order no. 473173 SR3C, AC/DC 24V (high DC breaking capacity), plug-in terminals
Order no. 472592 EKLS4, set of plug-in screw terminals
Order no. 472593 EKLZ4, set of plug-in tensile spring terminals
Emergency Stop Safety Relay SR3C AC/DC24V
Table of contents
Other Zander Aachen Relay manuals
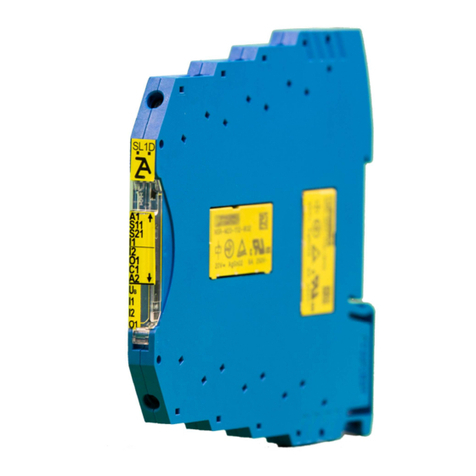
Zander Aachen
Zander Aachen MINOS SD1E User manual
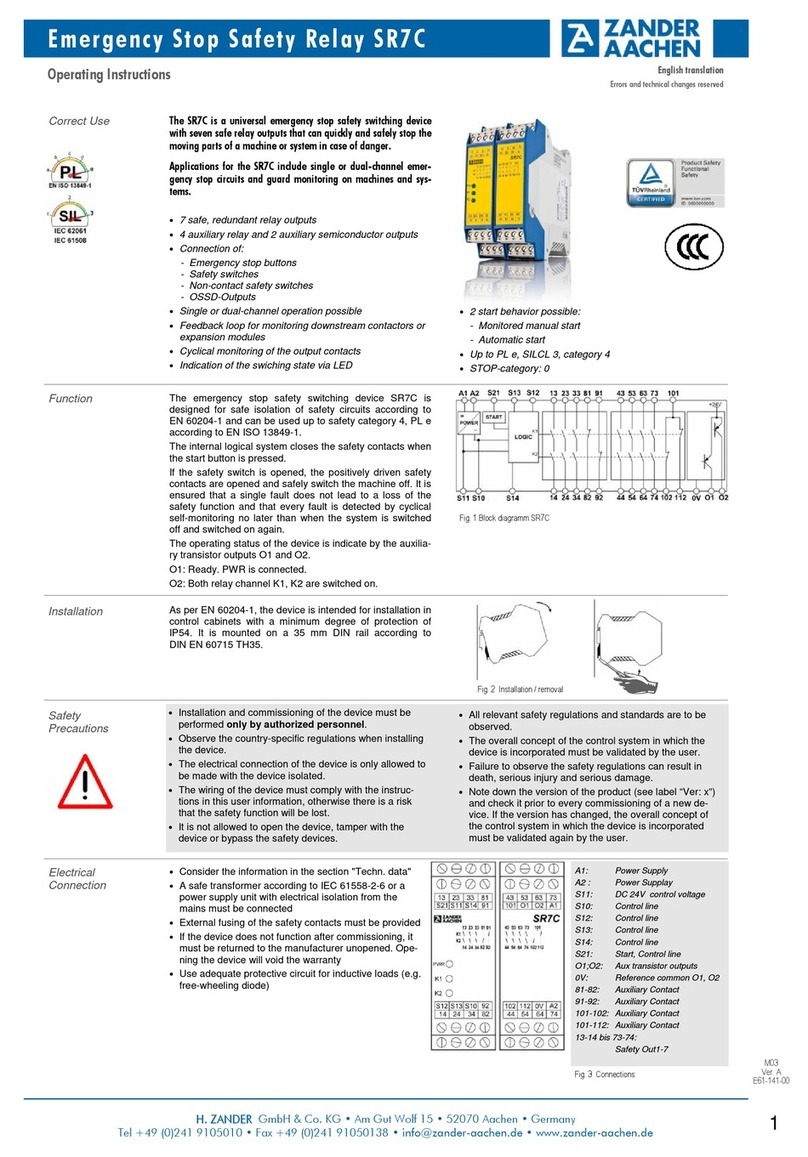
Zander Aachen
Zander Aachen SR7C User manual
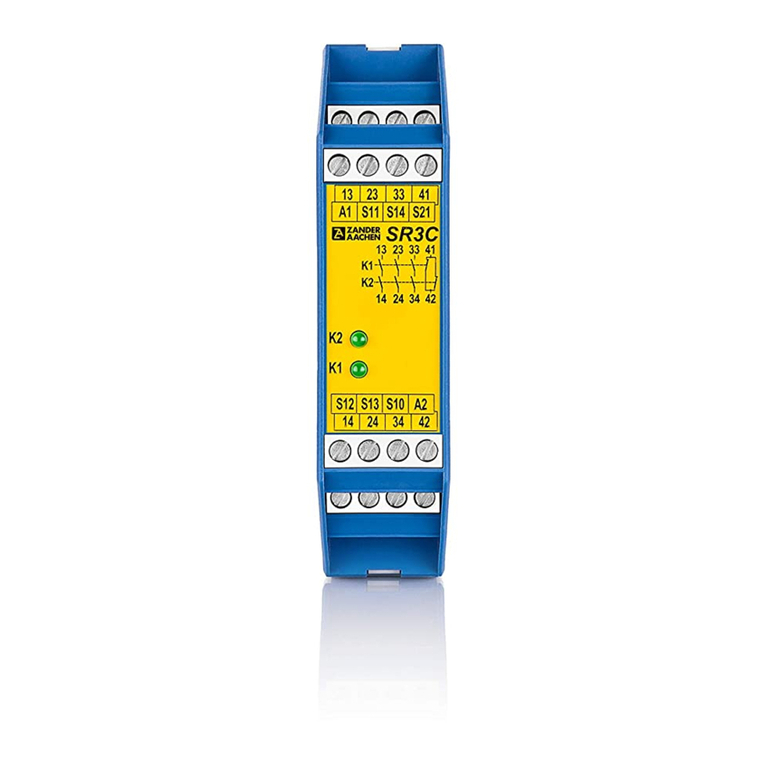
Zander Aachen
Zander Aachen SR3C User manual
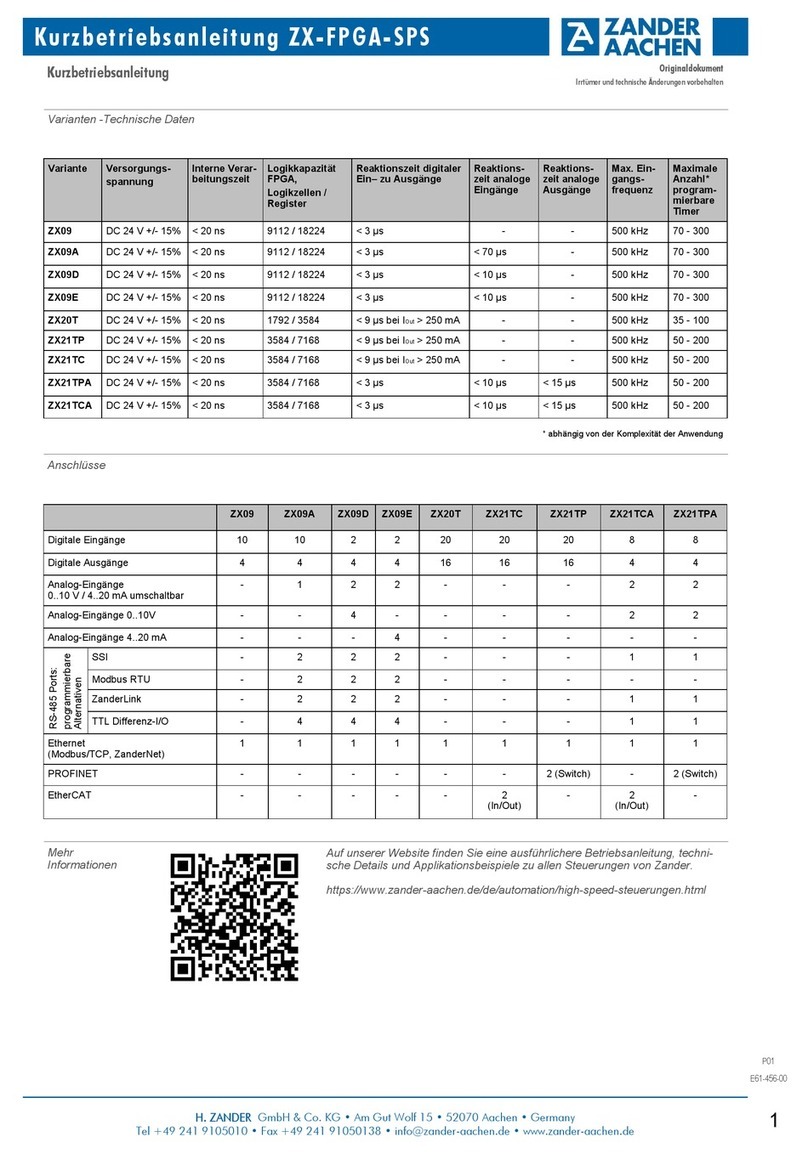
Zander Aachen
Zander Aachen ZX09 Series User manual
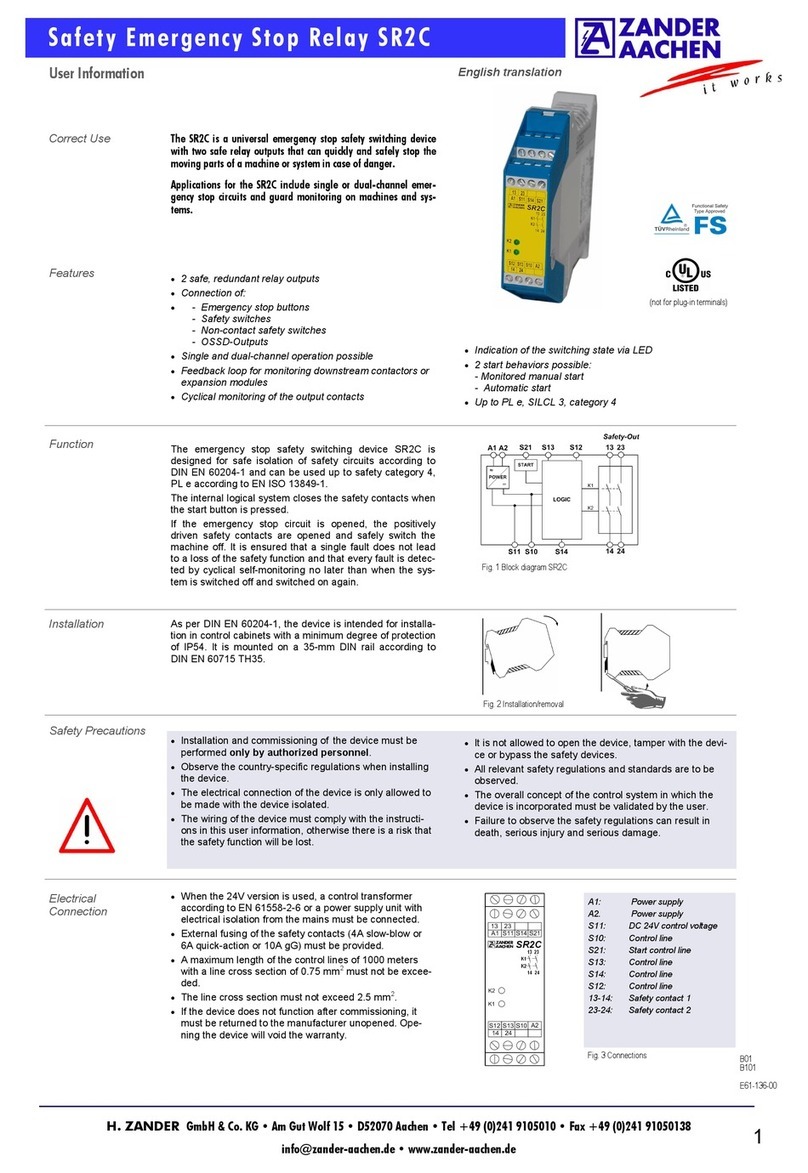
Zander Aachen
Zander Aachen SR2C User manual
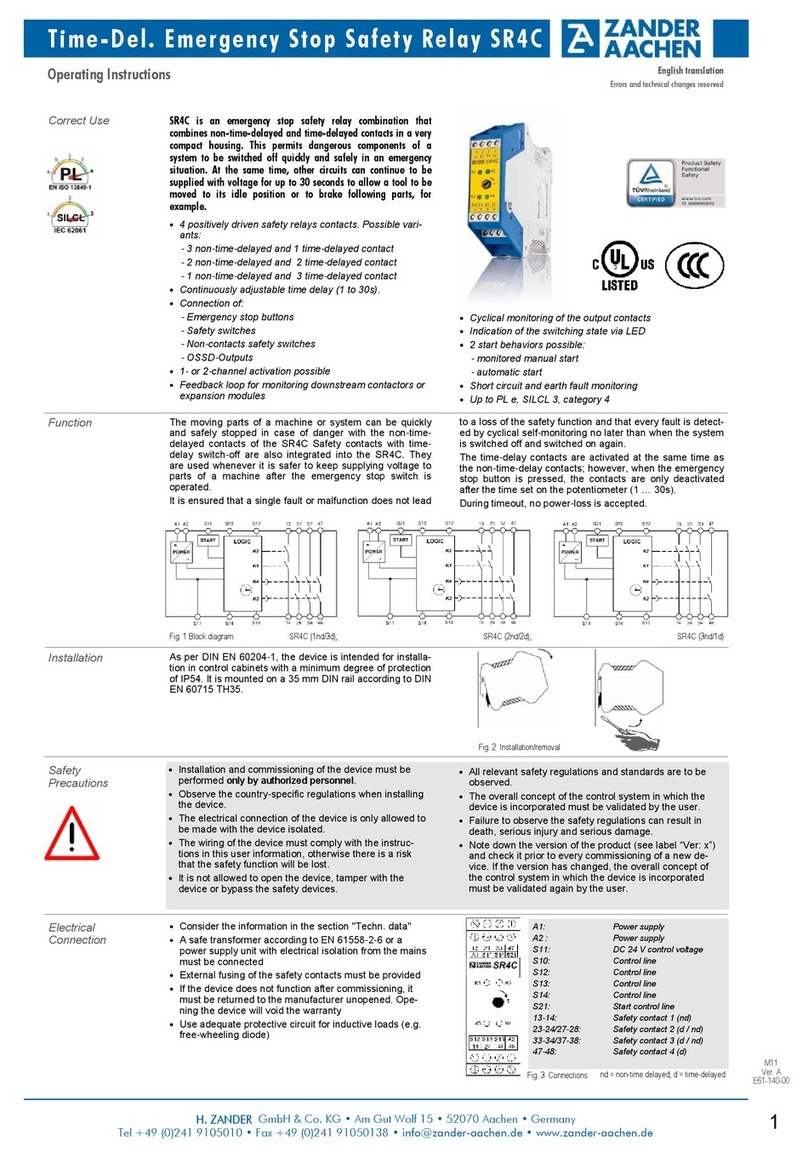
Zander Aachen
Zander Aachen SR4C User manual
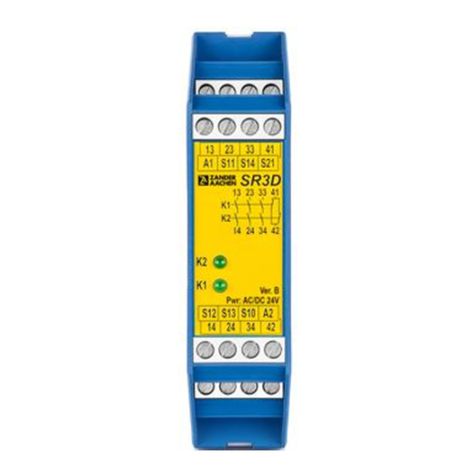
Zander Aachen
Zander Aachen SR3D Operation manual
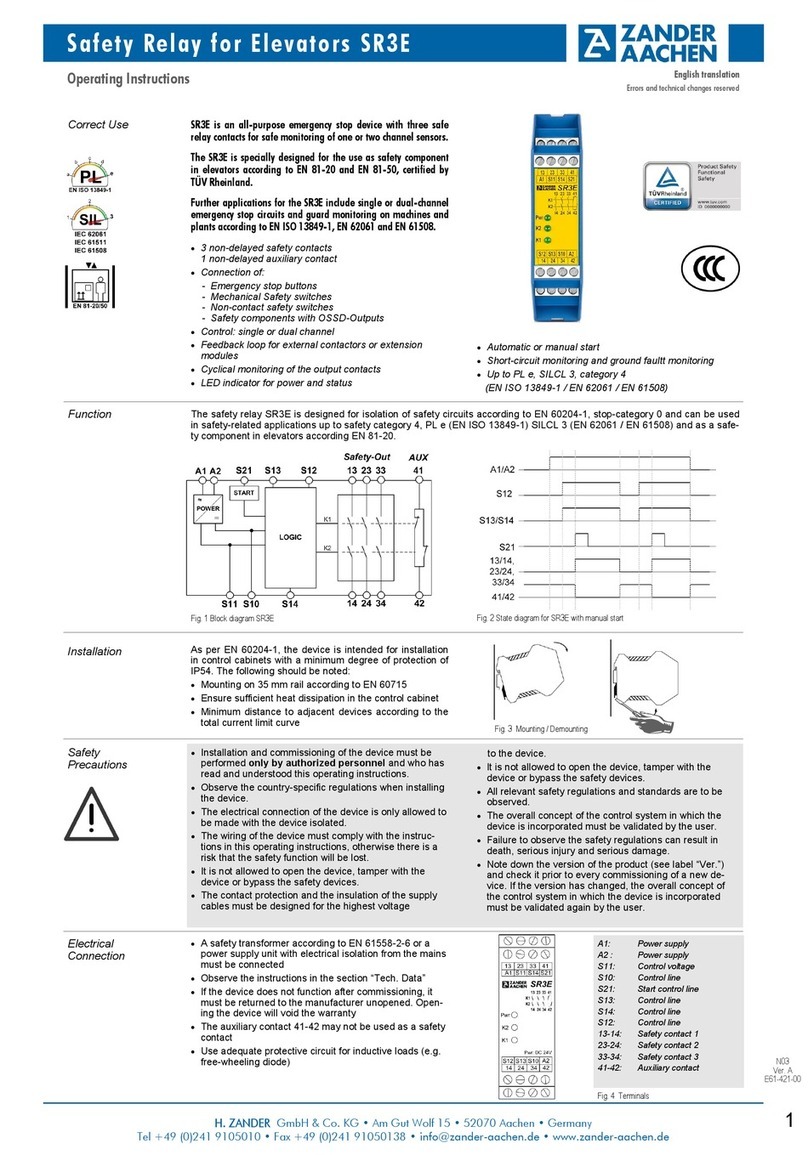
Zander Aachen
Zander Aachen SR3E User manual
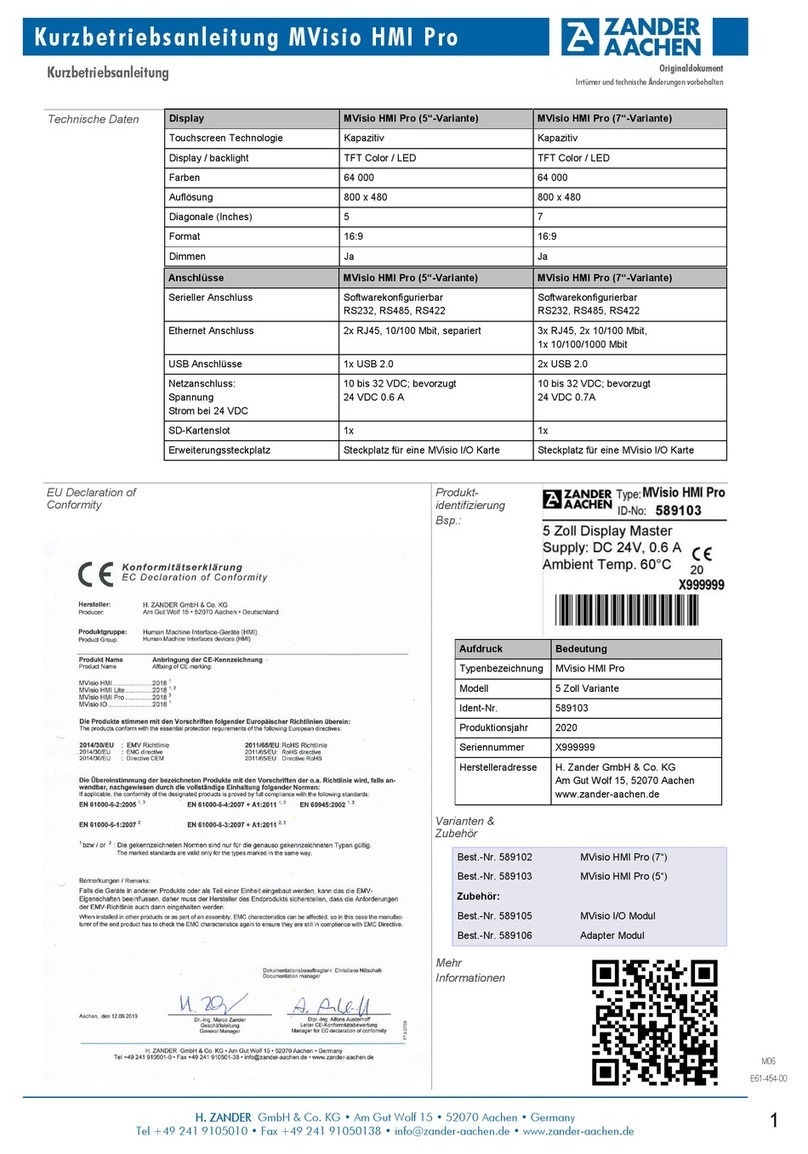
Zander Aachen
Zander Aachen MVisio HMI Pro User manual
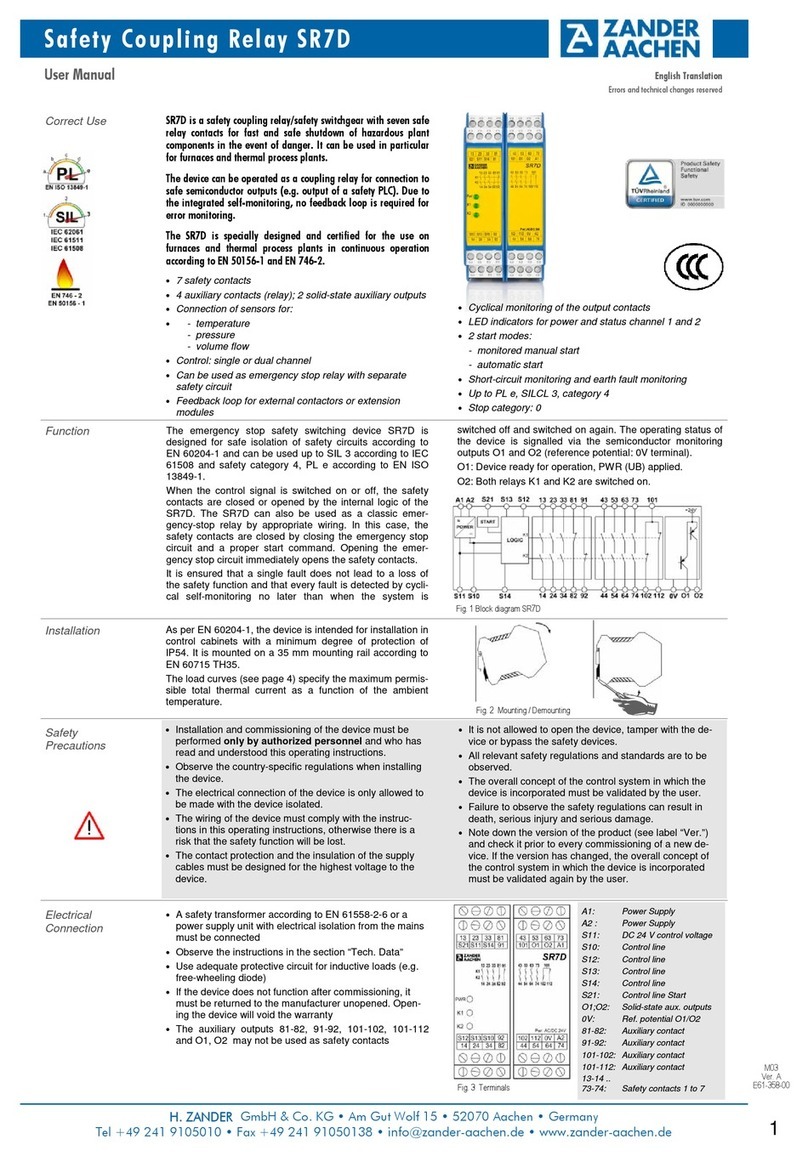
Zander Aachen
Zander Aachen SR7D User manual