ASCO Valves EV8308G360 Installation and operating instructions
Other ASCO Valves Control Unit manuals

ASCO Valves
ASCO Valves 8210 Series Installation and operating instructions

ASCO Valves
ASCO Valves 8044 Series Installation and operating instructions
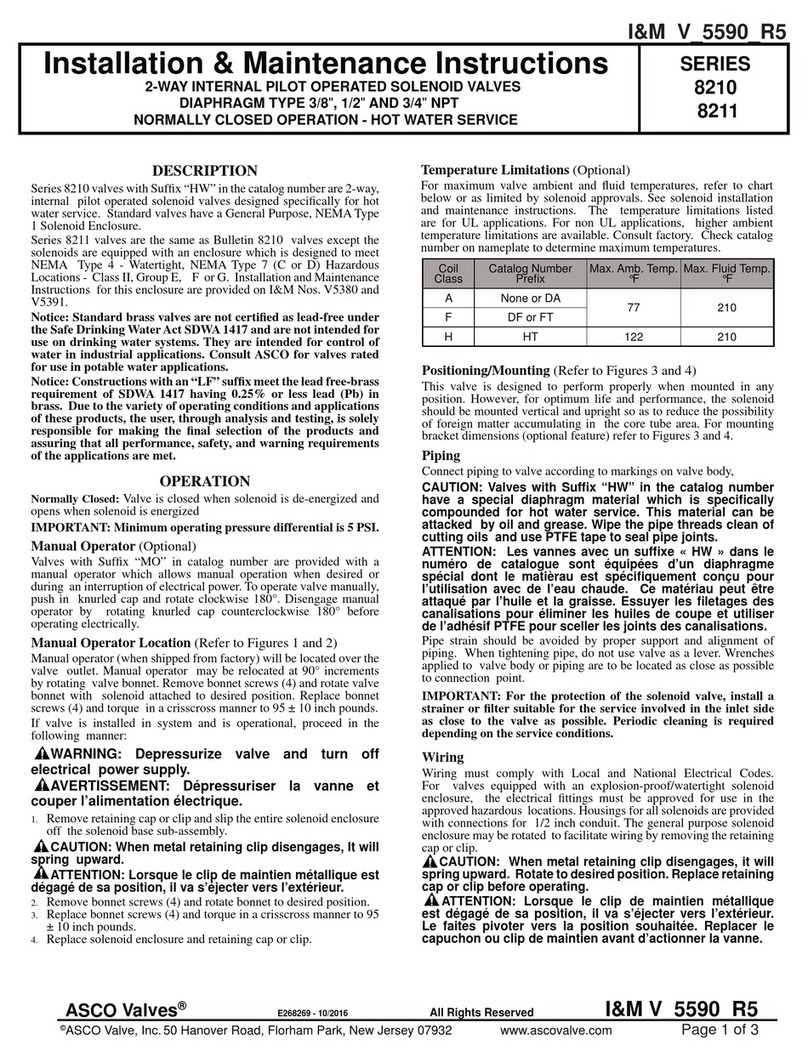
ASCO Valves
ASCO Valves 8210 Series Installation and operating instructions
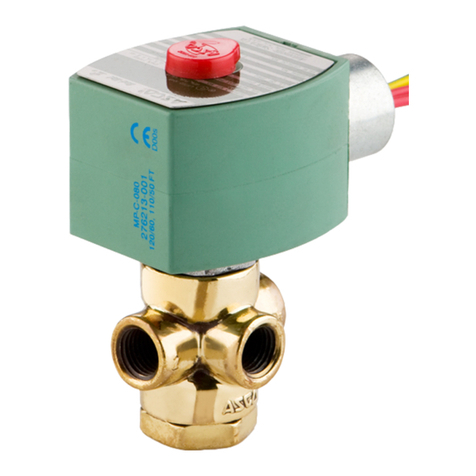
ASCO Valves
ASCO Valves 8320 Series Installation and operating instructions

ASCO Valves
ASCO Valves 8004 Series Installation and operating instructions
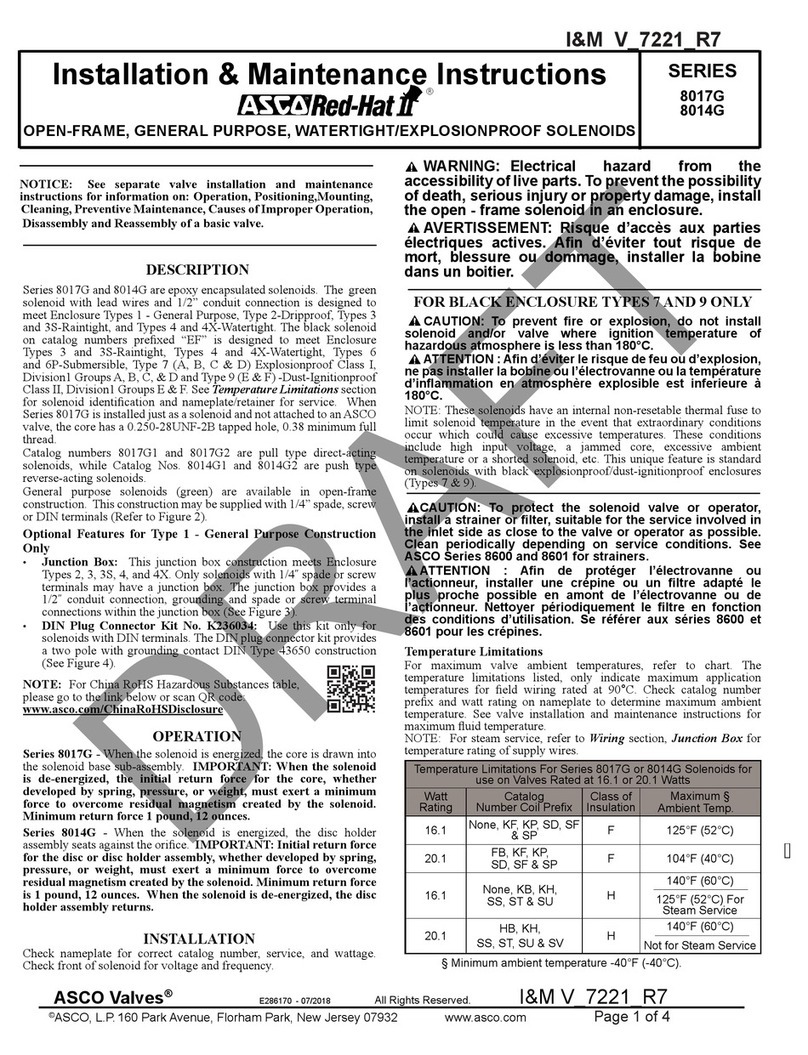
ASCO Valves
ASCO Valves Red-Hat II 8017G Series Installation and operating instructions
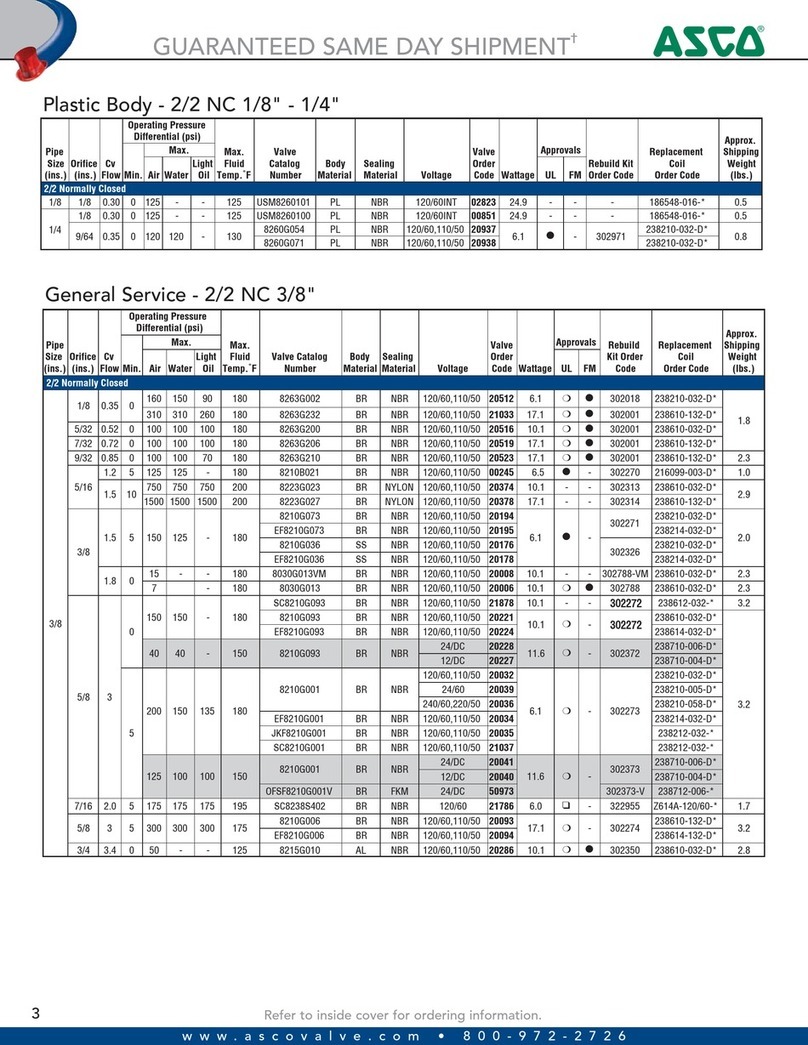
ASCO Valves
ASCO Valves USM8260101 Installation and operating instructions
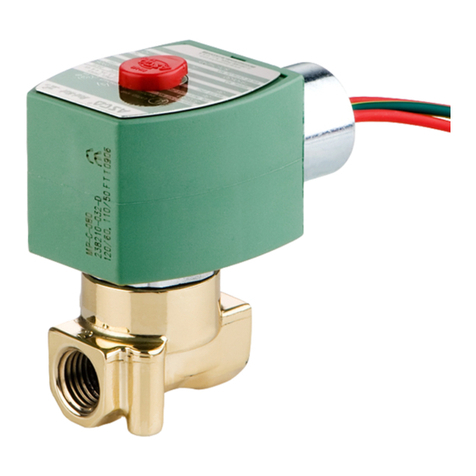
ASCO Valves
ASCO Valves 8262 Series Installation and operating instructions
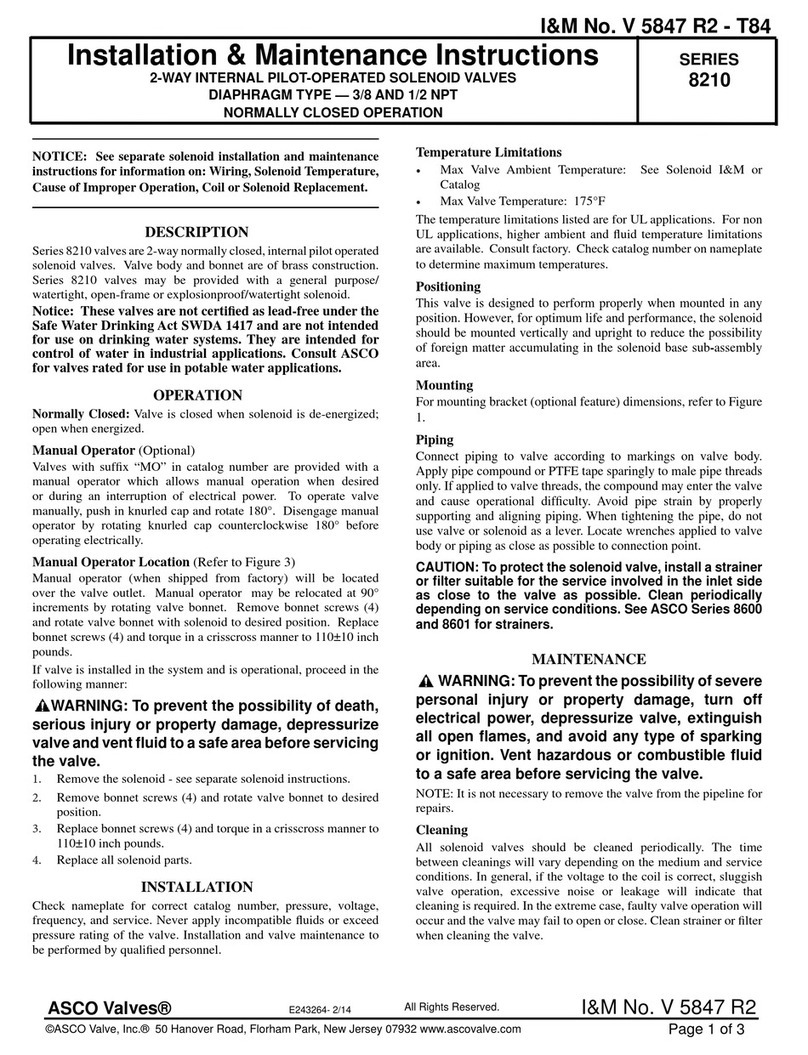
ASCO Valves
ASCO Valves 8210 Series Installation and operating instructions
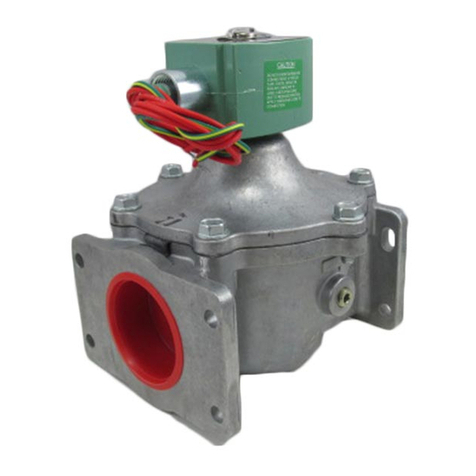
ASCO Valves
ASCO Valves 8214 Series Installation and operating instructions
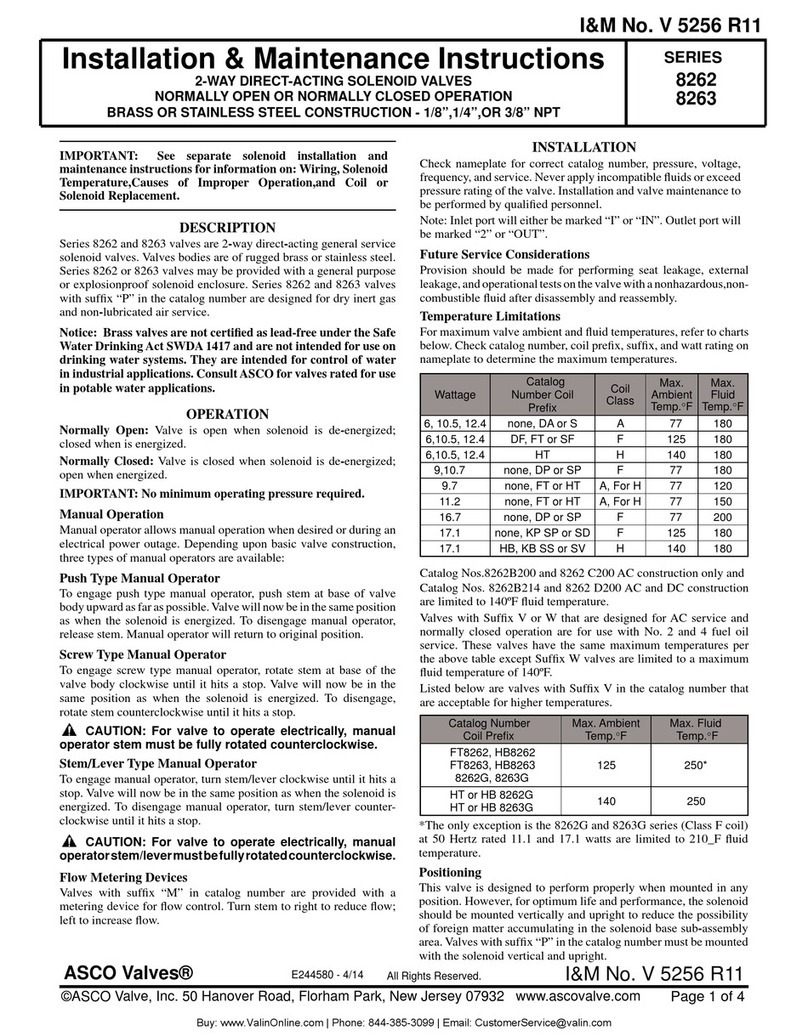
ASCO Valves
ASCO Valves 8263 Series Installation and operating instructions
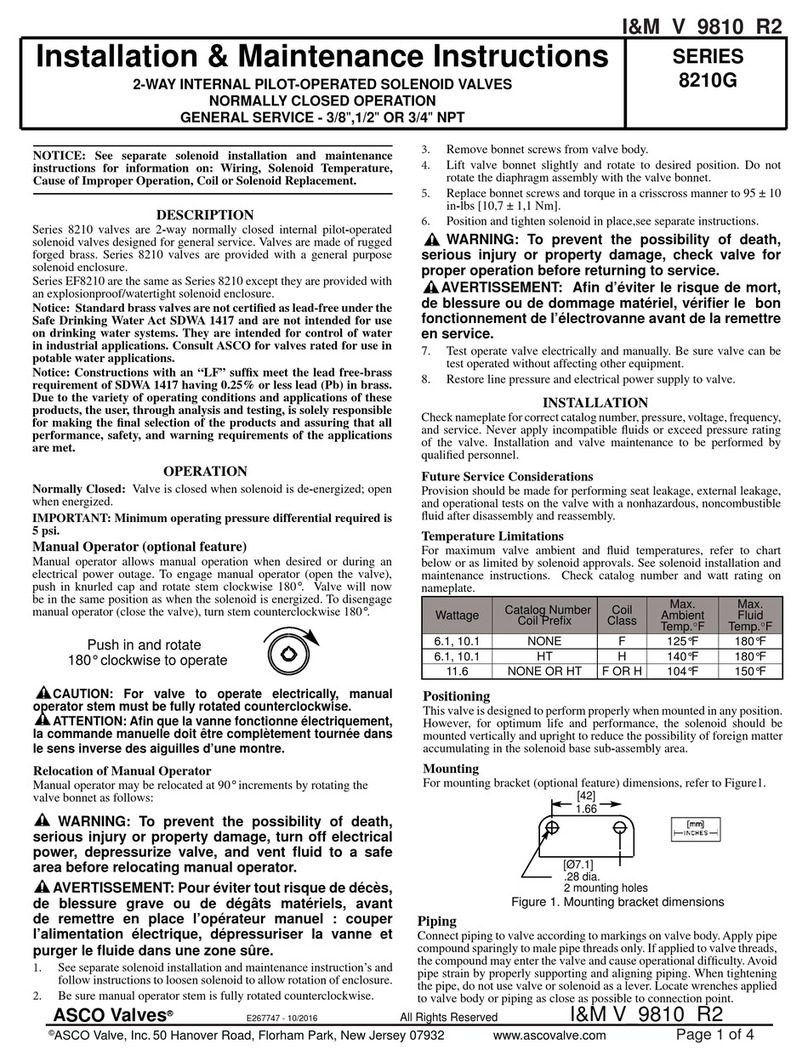
ASCO Valves
ASCO Valves 8210G Series Installation and operating instructions
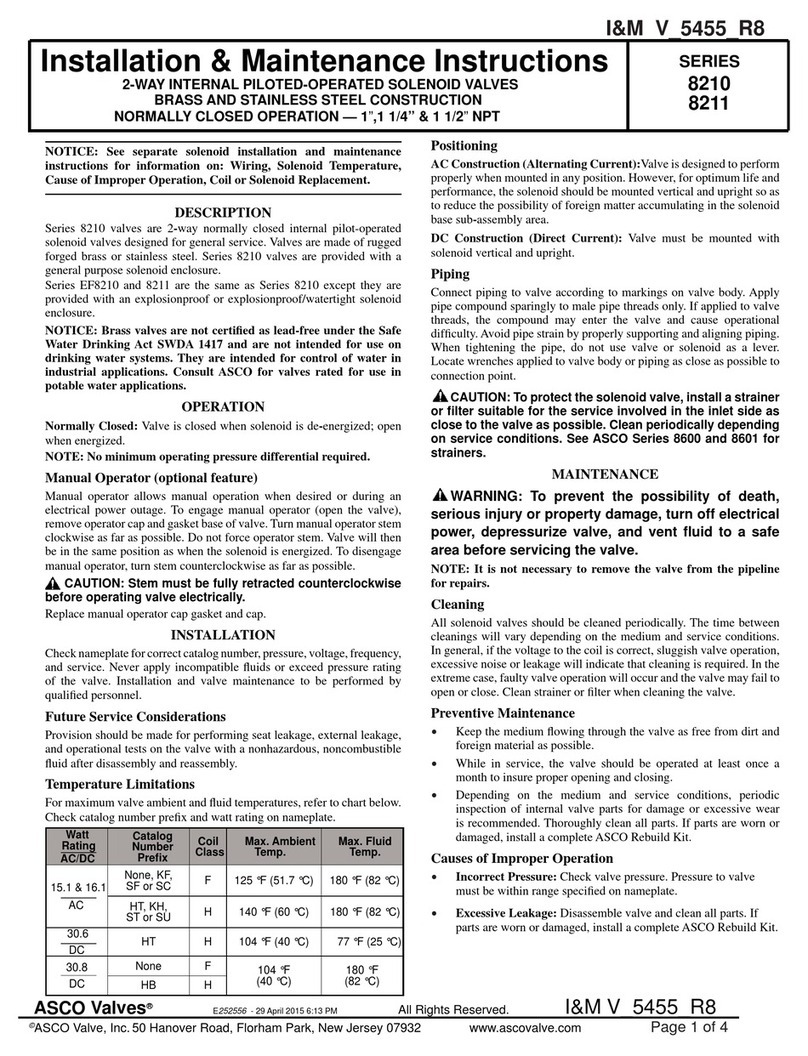
ASCO Valves
ASCO Valves 8210 Series Installation and operating instructions
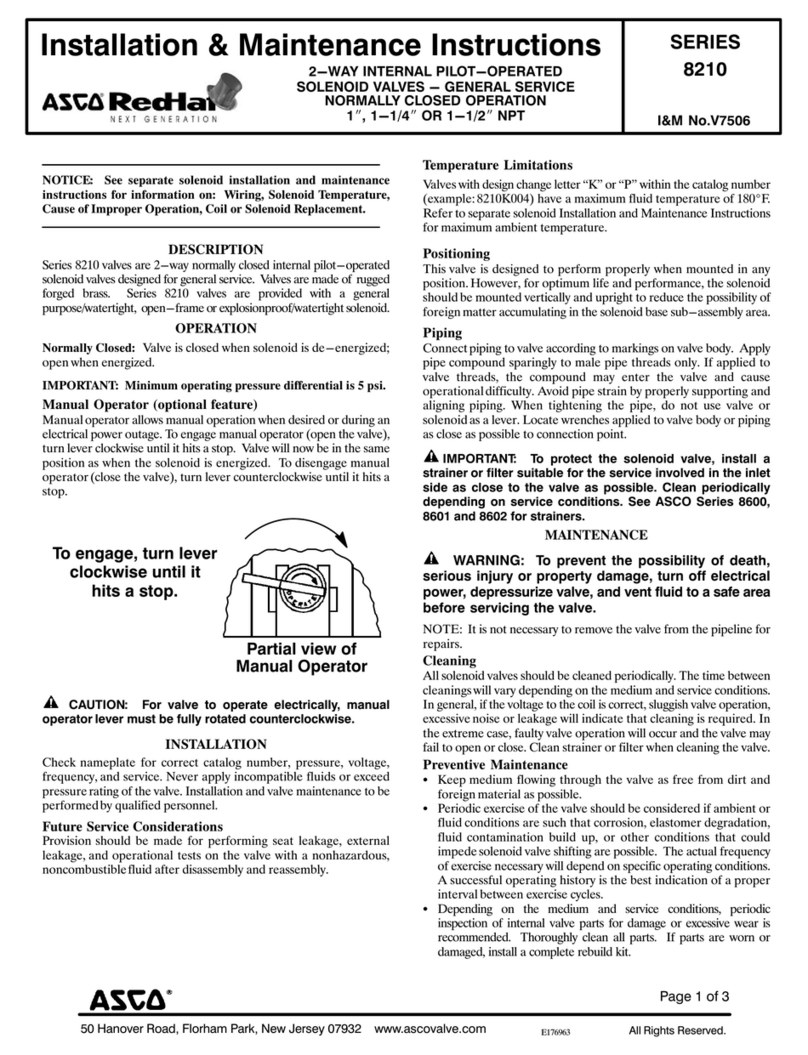
ASCO Valves
ASCO Valves 8210 Series Installation and operating instructions
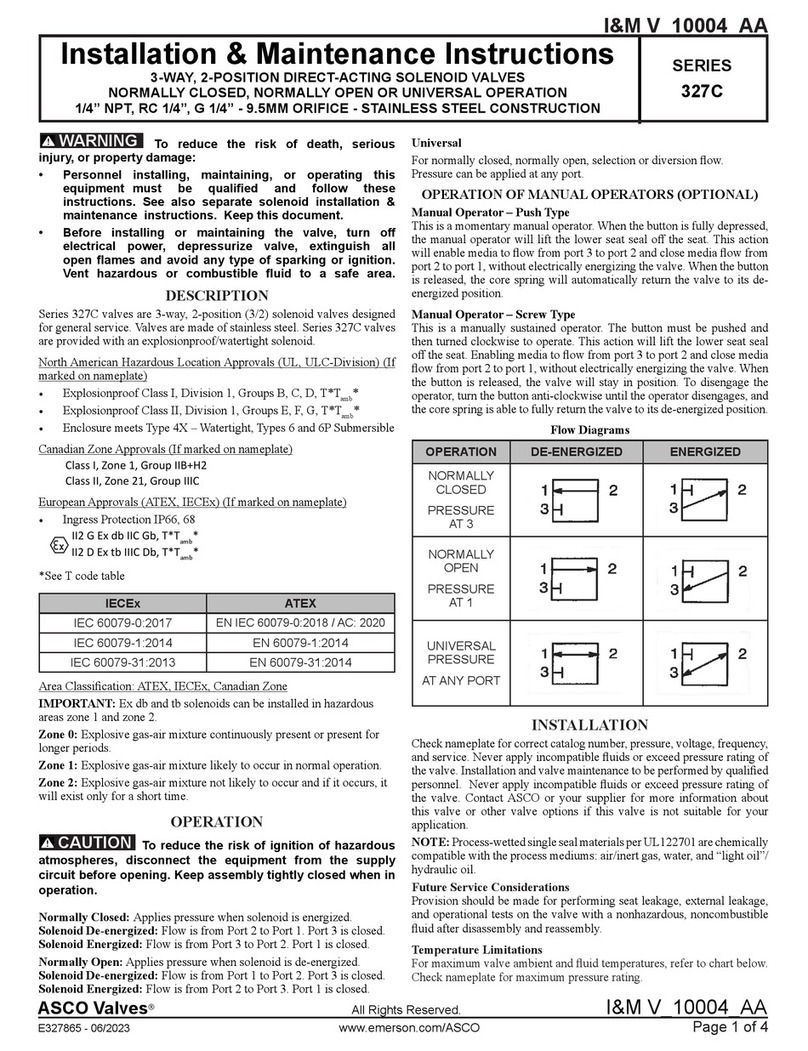
ASCO Valves
ASCO Valves 327C Series Installation and operating instructions
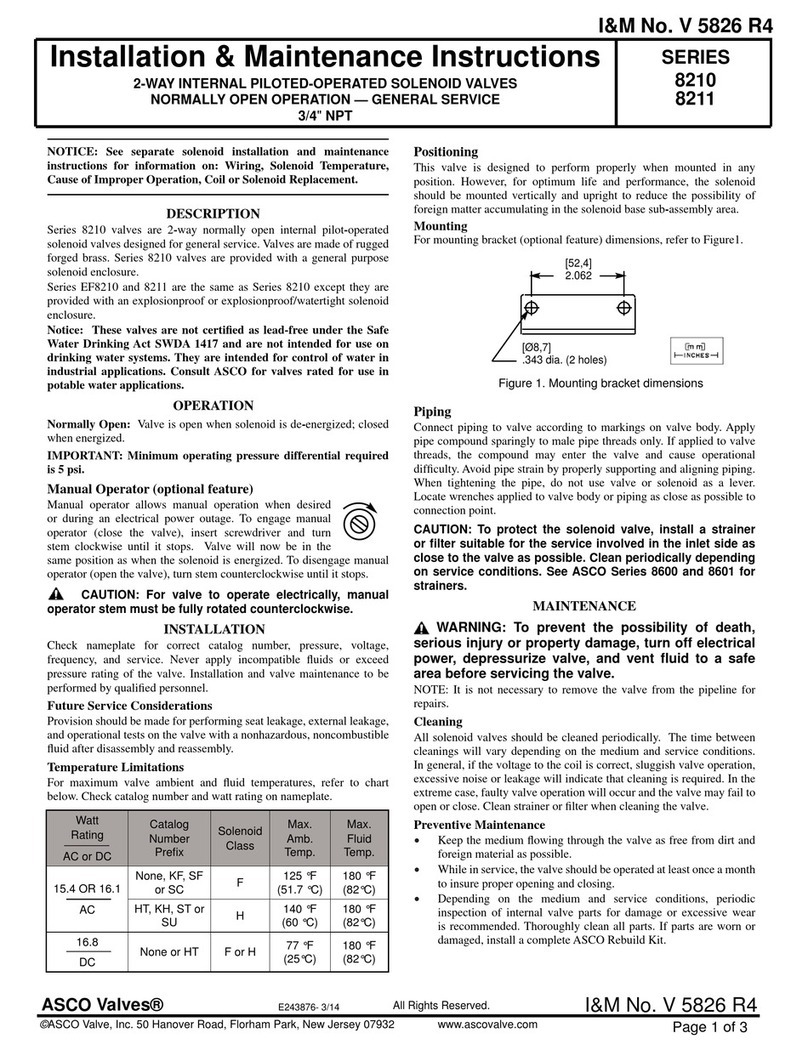
ASCO Valves
ASCO Valves 8210 Series Installation and operating instructions
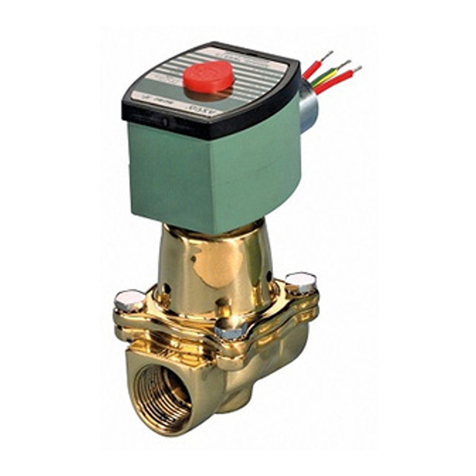
ASCO Valves
ASCO Valves 8222 Series Installation and operating instructions

ASCO Valves
ASCO Valves 8214(200) Series Installation and operating instructions
Popular Control Unit manuals by other brands
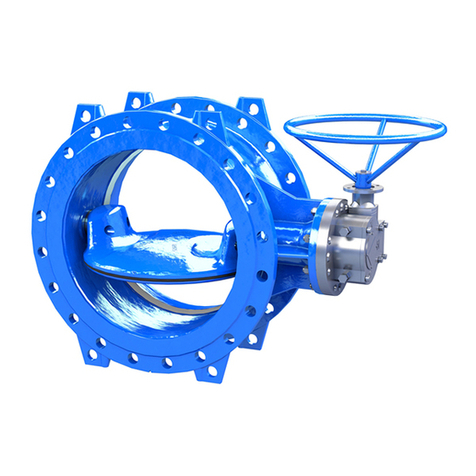
Vag
Vag EKN H-Series Operation and maintenance instructions
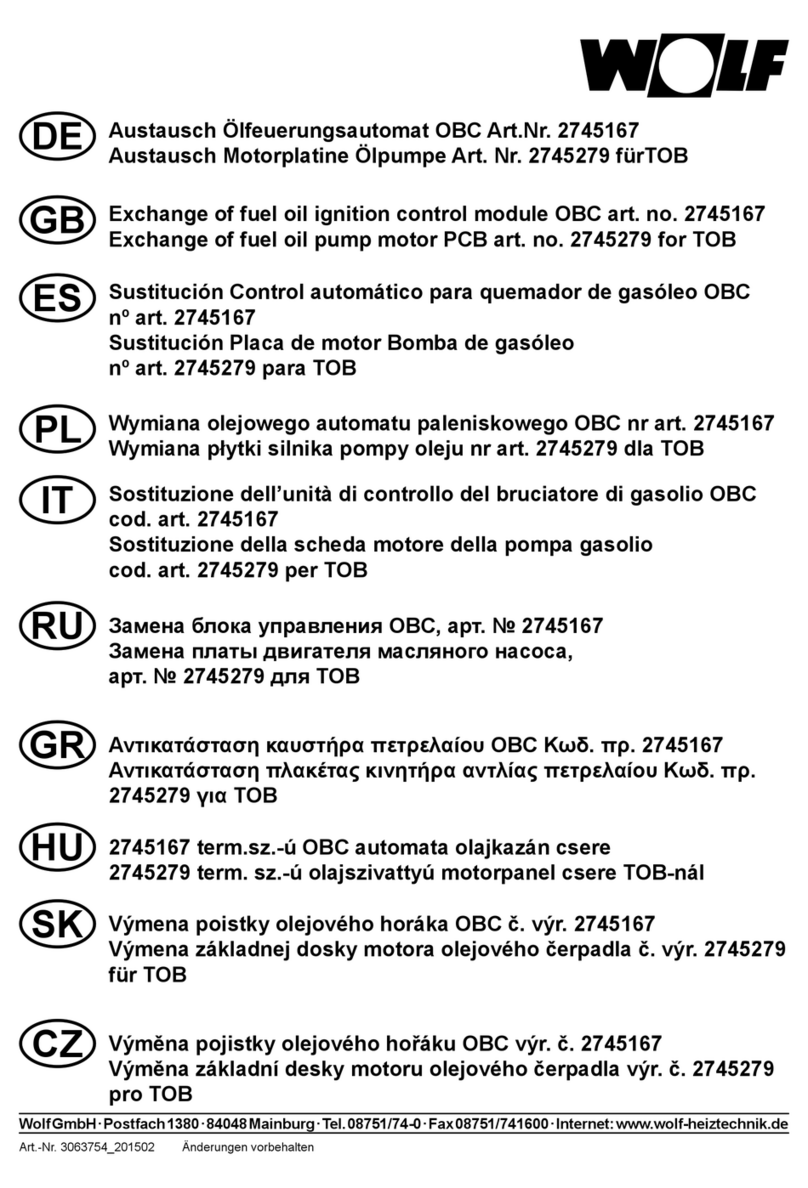
Wolf
Wolf OBC manual

S&S Northern
S&S Northern Merlin 1000S Installation, operating and maintenance guide
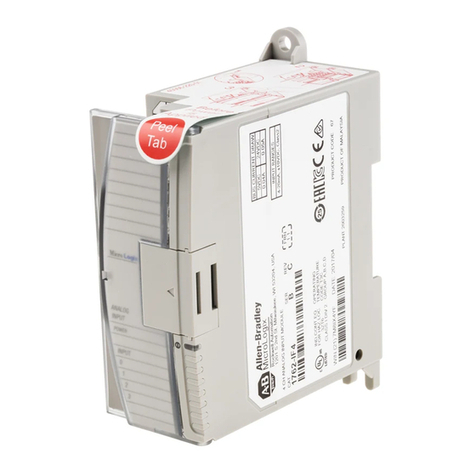
Allen-Bradley
Allen-Bradley MicroLogix 1762-IF4 installation instructions

Nevco
Nevco MPCX2 Football Operator instructions
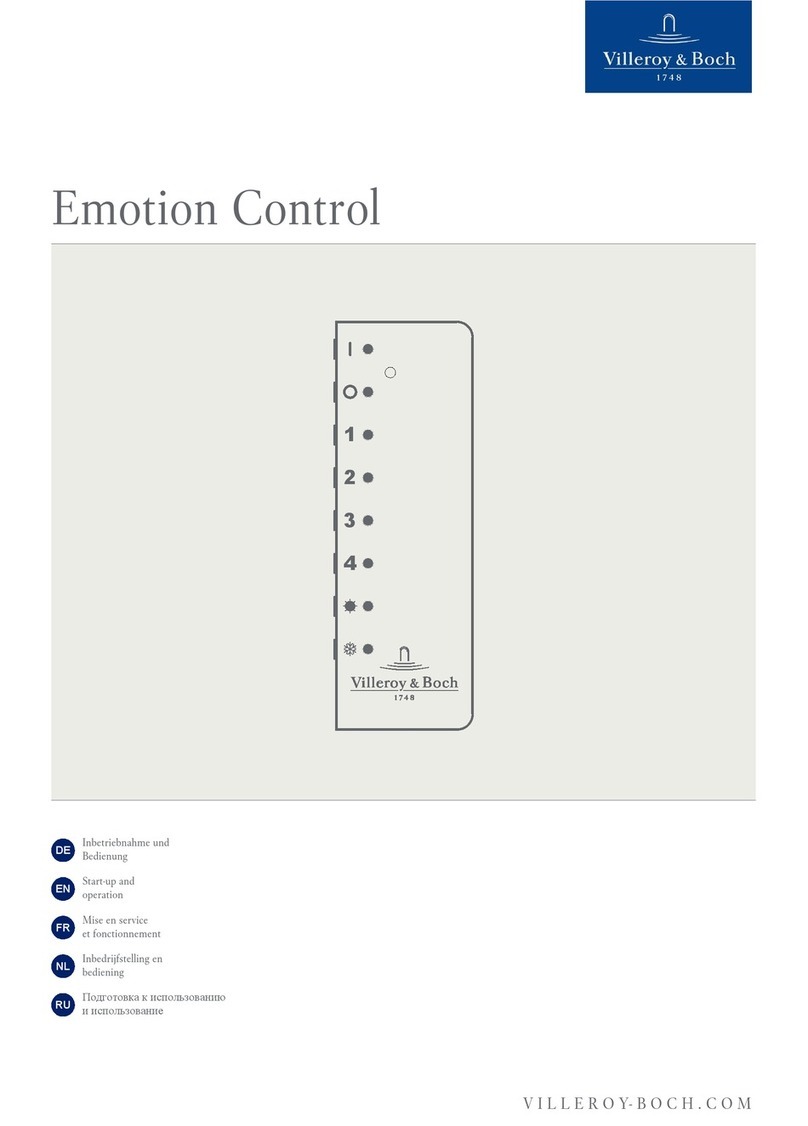
Villeroy & Boch
Villeroy & Boch Emotion Control Start-up and operation
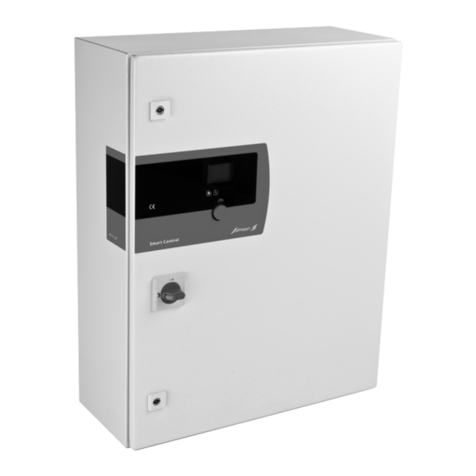
salmson
salmson SC-L Installation and starting instructions
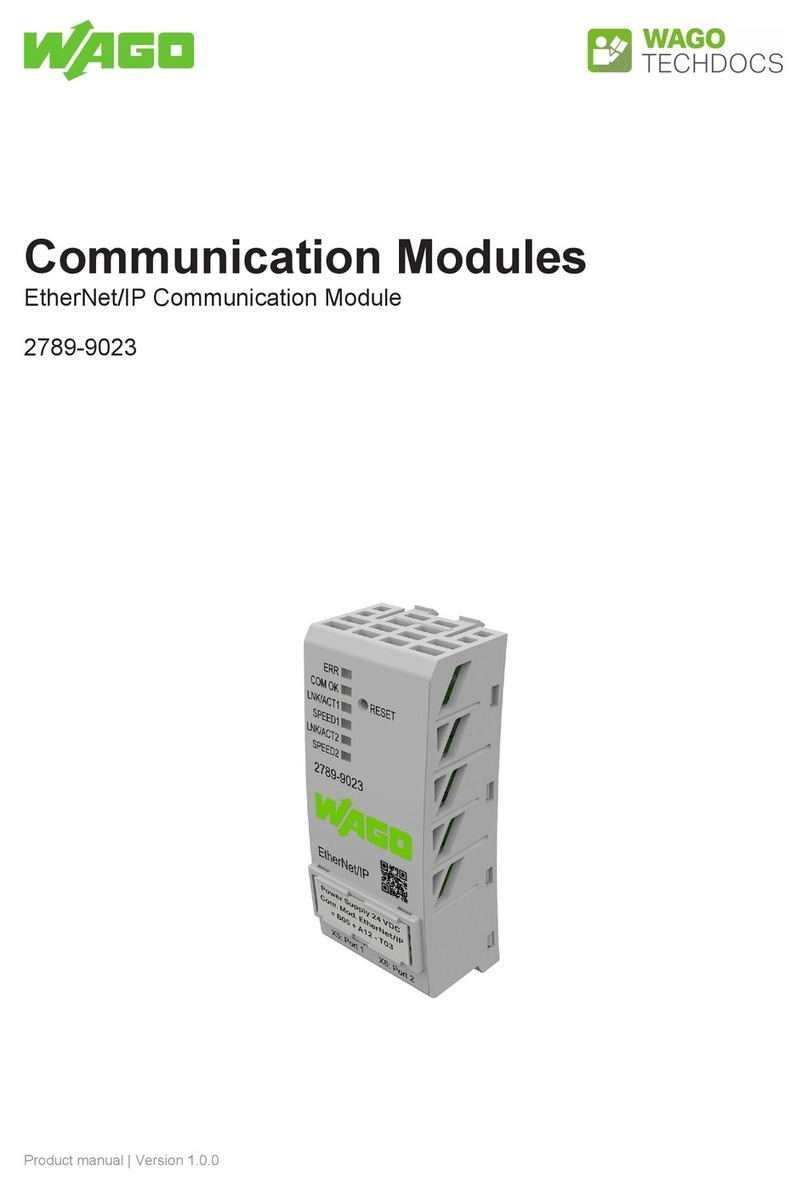
WAGO
WAGO 2789-9023 manual
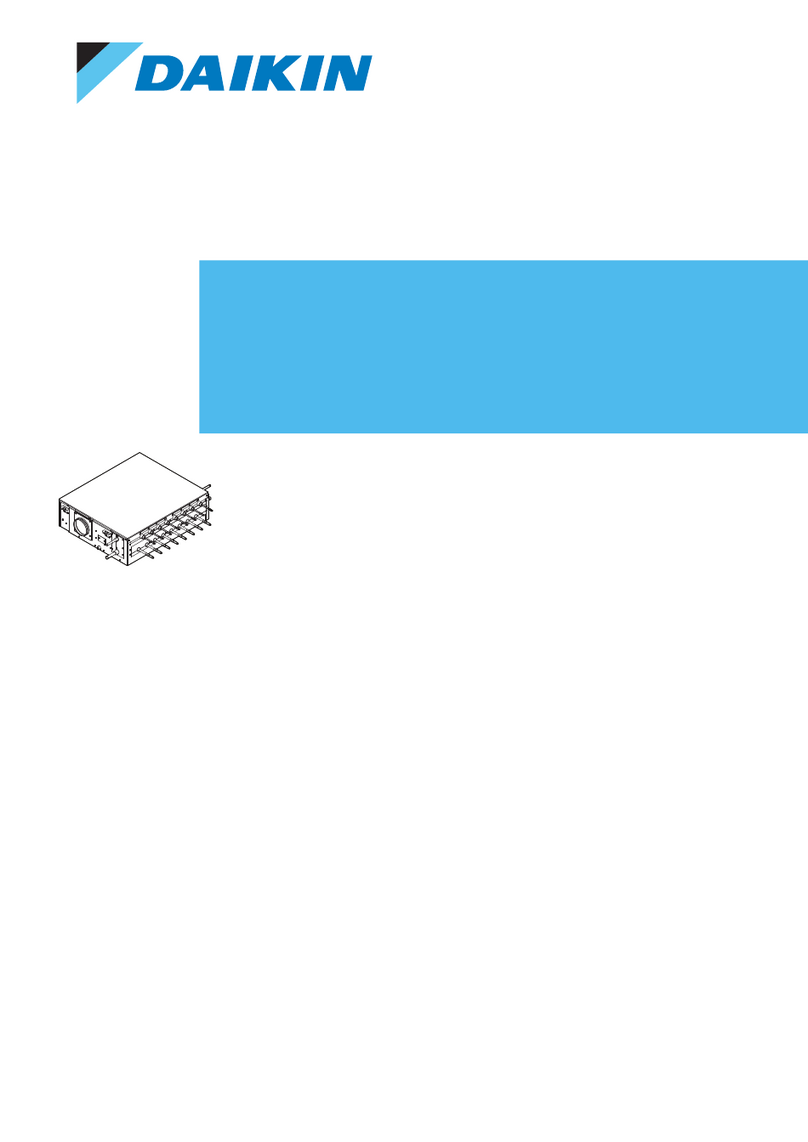
Daikin
Daikin SV1A25AJV1B User reference and installation manual
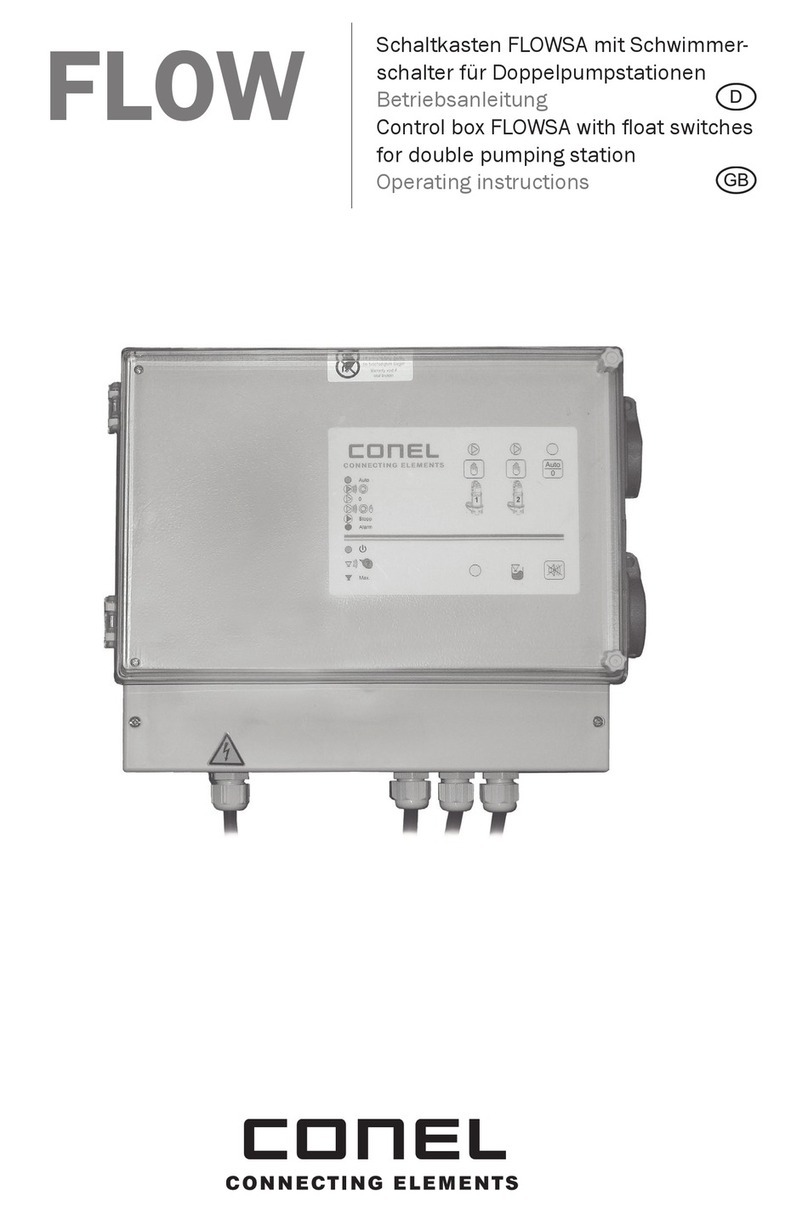
Conel
Conel FLOW SWITCHGEAR operating instructions

ADTRAN
ADTRAN jobAid+ SFP+ 11.3 G BIDI 20KM manual
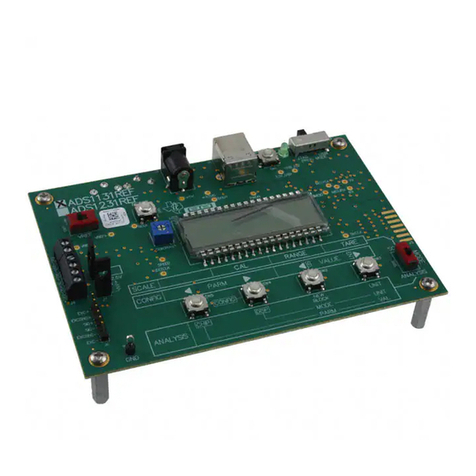
Texas Instruments
Texas Instruments ADS1131REF user guide