CKD MN4KB1 Series User manual

SM−200164−A
INSTRUCTION MANUAL
BLOCK MANIFOLD
MN4KB1 SERIES
●Please read this instruction manual
carefully before using this product,
particularly the section describing safety.
●Retain this instruction manual with the
product for further consultation whenever
necessary.
4th Edition

[SM-200164-A/4] ―1
―
SAFETYPRECAUTIONS
WhendesigningandmanufacturingadeviceusingCKDproducts,themanufacturerisobli-
gatedtomanufactureasafeproductbyconfirmingsafetyofthesystemcomprisingthefol-
lowingitems:
・Devicemechanism
・Pneumaticorwatercontrolcircuit
・Electriccontrolthatcontrolstheabove
Itisimportanttoselect,use,handle,andmaintaintheproductappropriatelytoensurethat
theCKDproductisusedsafely.
Observewarningsandprecautionstoensuredevicesafety.
Checkthatdevicesafetyisensured,andmanufactureasafedevice.
1. Thisproductisdesignedandmanufacturedasageneralindustrial
machinepart.
Itmustbehandledbysomeonehavingsufficientknowledgeandexperience.
2. Usethisproductwithinitsspecifications.
Thisproductcannotbeusedbeyonditsspecifications.Additionally,theproductmustnot
bemodifiedormachined.
Thisproductisintendedforuseingeneralindustrialdevicesandparts.Usebeyondsuch
conditionsisnotconsidered.ConsultwithCKDfordetailswhenusingtheproductbeyond
theuniquespecificationrange,outdoors,orinthefollowingconditionsorenvironments.In
anycase,measuresforsafetyshallbeprovidedwhenthevavlemalfunctions.
①Useforspecialapplicationsrequiringsafetyincludingnuclearenergy,railroad,aviation,
ship,vehicle,medicalequipment,equipment orapplicationscominginto contact with
beverageorfood,amusementequipment,emergencyshutoffcircuits, pressmachine,
brakecircuits,orforsafeguard.
②Use for applications where life or assets could be adversely affected, and special
safetymeasuresarerequired.
3. Observecorporatestandardsandregulations,etc.,relatedtothe
safetyofdevicedesignandcontrol,etc.
ISO4414,JISB8370(pneumaticsystemrules)
JFPS2008(principlesforpneumaticcylinderselectionanduse)
IncludingHighPressureGasMaintenanceLaw,OccupationalSafetyandSanitationLaws,
othersafetyrules,standardsandregulations,etc.
WARNING

[SM-200164-A/4]
−2−
4. Donothandle,pipe,orremovedevicesbeforeconfirmingsafety.
①Inspect and service the machine and devices after confirming safety of the entire
systemrelatedtothisproduct.
②Notethattheremaybehotorchargedsectionsevenafteroperationisstopped.
③Wheninspectingorservicingthedevice,turnofftheenergysource(airsupplyorwater
supply),andturnoffpowertothefacility.Releaseanycompressedairfromthesystem,
andpayenoughattentiontopossiblewaterleakageandleakageofelectricity.
④When starting or restarting a machine or device that incorporates pneumatic
components,makesurethatsystemsafety,suchaspop-outpreventionmeasures,is
secured.
5. Observe warnings and cautions on the pages below to prevent
accidents.
The safety cautions are ranked as "DANGER", "WARNING" and
"CAUTION"inthissection.
:Whenadangeroussituationmayoccurifhandlingismistaken
leading to fatal or serious injuries, or when there is a high
degreeofemergencytoawarning.
:Whenadangeroussituationmayoccurifhandlingismistaken
leadingtofatalorseriousinjuries.
:Whenadangeroussituationmayoccurifhandlingismistak-
enleadingtominorinjuriesorphysicaldamage.
Notethatsomeitemsdescribedas"CAUTION"mayleadtoseriousresultsdepending
onthesituation.Inanycase,importantinformationthatmustbeobservedisexplained.
DANGER
WARNING
CAUTION

[SM-200164-A/4] ―3
―
Precautionswithregardtoguarantee
・Guaranteeperiod
Theguaranteeperiodofourproductshallbeone(1)yearafteritisdeliveredtotheplace
specifiedbythecustomer.
・Guaranteecoverage
IfanyfailureforwhichCKDCORPORATIONisrecognizedtoberesponsibleoccurswithin
theabovewarrantyperiod,asubstituteornecessaryreplacementpartsshallbeprovided
freeofcharge,ortheproductshallberepairedfreeofchargeattheplantofCKDCOR-
PORATION.
However,theguaranteeexcludesfollowingcases:
①Defectsresultingfromoperationunderconditionsbeyondthosestatedinthecatalogue
orspecifications.
②Failure resulting from malfunction of the equipment and/or machine manufactured by
othercompanies.
③Failureresultingfromwronguseoftheproduct.
④FailureresultingfrommodificationorrepairingthatCKDCORPORATIONisnotinvolved
in.
⑤Failureresultingfromcausesthatcouldnotbeforeseenbythetechnologyavailableat
thetimeofdelivery.
⑥FailureresultingfromdisasterthatCKDisnotresponsibleof.
Guaranteestatedherecoversonlythedeliveredproducts.Anyotherdamageresultingfrom
failureofthedeliveredproductsisnotcoveredbythisguarantee.
・Confirmationofproductcompatibility
Our customer shall be responsible of confirming compatibility of our product used in our
customer’ssystem,machineryordevice.

[SM-200164-A/4]
−4−
UNPACKING (Section 3)
Bags containing solenoid valves should be opened only
when you are ready to connect the valves to the pipes
immediatelyafterward.
Ifbagsareopenedbeforethevalvesarereadytobecon-
nectedtothepipes,theentryofforeignmatterfromthe
piping ports could cause the solenoid valves to fail or
malfunction.
INSTALLATION (Section 4)
Ifyouhavetousetheproductunderconditionsthatare
differentfromthespecifiedconditionsorifyouintendto
usetheproductforaspecialapplication,besuretocon-
sultusabouttheproductspecificationsbeforeusingthe
product.
ENVIRONMENT (Section 4.1)
a) Inadustyenvironment,foreignmattermayentereven
throughtheexhaustport.
Themovementoftheexhaustvalvecausesarespiratory
actionattheexhaustvalve,whichmaycauseinhalationof
foreignmatterneartheexhaustport. Thispotentialsit-
uation would be worse if the exhaust port is facing up-
ward. Attachasilencertotheexhaustportorhavethe
exhaustportfacedownward.
b) Keep the solenoid valve system dry. Take care to
avoiddirectcontactwithdrippingwaterorsplashesof
cuttingoil.
If the solenoid valve system is wet by a direct contact
withwaterorcuttingoil,anelectricalleakorburntsole-
noid coils may result. Protect the solenoid valve system
byusingacoverorbyinstalling
itinsideapaneledcasing.
Ifthecylinderrodissplashedwithcuttingoil,theoilmay
penetrate through the cylinder into the secondary side
piping ofthe solenoid valve. This must be prevented to
avoidmalfunctions. Consultusforpreventivemeasures.
c) Thecoilswillproduceheat.
Particularly if the solenoid valve system is installed in a
controlboardorifthesolenoidcoilsneedtobeenergized
foralongtime,considerprovidingsufficientventilationto
releasetheheat. Thecoilscangetveryhot.
d) Do not use the solenoid valve system in an atmos-
pherethatincludesacorrosivegasorsolventvapors.
Do not use the solenoid valve system in an atmosphere
that includes a corrosive gas such as the sulfur dioxide
gasorinanatmospherethatincludessolventvapors.
e) Vibrationsandshocks
Do not subject the solenoid valve system to vibrations
50m/s2orstrongerorshocks300m/s2orstronger.
!
CAUTION:
!
CAUTION:
!
CAUTION:

[SM-200164-A/4] ―5
―
f) Avoidusingthesolenoidvalvesysteminahumiden-
vironment because the humidity is likely to cause
condensationwithachangeinthetemperature.
g) Donotusethenormaltypesolenoidvalvesforanap-
plicationthatrequiresconformitywithexplosion-proof
specifications. Choose explosion-proof solenoid
valvesinstead.
h) Thepackingandgasketsmaydeterioratesoonerthan
usual if used in an atmosphere with a higher than
normaldensityofozone(forexample,theatmosphere
near a beach or in an area with frequent thunder-
storms).
Consultusforthe packingandgasketstobe used inan
atmospherewithahigherozonedensity.
INSTALLATION (Section 4.2)
When installing a solenoid valve unit, never attempt to
holditinpositionbymeansofthepipesconnectedtoit.
Mountthesolenoidvalvebyapplyingthemountingscrews
and/ormountingplatetothesolenoidvalve.
!
WARNING:
!
CAUTION:

[SM-200164-A/4]
−6−
PIPING (Section 4.3)
a)Makesurethatthepipeswillnotbedisconnectedatthe
jointsbymechanicalmovements,vibrationsortension.
If the exhaust piping of the pneumatic circuit is discon-
nected,theactuatorspeedcontrolisdisabled.
If the above happens to a chuck holding mechanism, the
chuck will open. The inadvertent opening of the chuck
maycauseaseriousaccident.
b)Whensupplyingthecompressedairforthefirsttimeafter
completingthepiping,besuretocheckeveryjointinthe
pipingforairleakage.
c)Whensupplyingthecompressedairforthefirsttimeafter
completing the piping,increase theair pressure gradually
butneverintroduceahighly-pressurizedairsuddenly.
A sudden introduction of a highly-pressurized air may
disconnectpipesatjointsand/orcausethetubestojump
around,anyofwhichmaycauseaninjury.
d)Do not decrease the inside diameter of the piping from
anyofthesolenoidvalveexhaustportstoadiameterless
thantheexhaustpipeconnectingportsize.
Normal operation of the actuator depends on the
smoothnessoftheexhaustflow. Withamanifoldsystem,
arestrictiontotheexhaustflowmaypreventnormalop-
erationofothersolenoidvalves.
e)Removalofforeignmatter
Rust and other foreign matter in the pneumatic circuit
may cause a malfunction or leakage from the valve seat.
Insert a filter (maximum allowable particle size 5μm or
less)immediatelyupstreamofthesolenoidvalve.
f)Airsupply
Donotrestricttheflowofairthroughtheairsupplypip-
ing. Withamanifoldsystemwithmultiplestations,adrop
in the air supply pressure may cause trouble through a
delayintheoperationtiming.
!
CAUTION:

[SM-200164-A/4] ―7
―
WIRING (Section 4.4)
Before wiring, read the instruction manual carefully and
understandtheinstructions.
A person who wires needs to have knowledge for safely
performing such operation based on the understanding
aboutthemechanismsandoperatingprinciplesofsolenoid
valves.
Before supplying the power, check the power supply
voltageandthecurrenttype(ACorDC).
MANUAL OPERATING DEVICE (Section 5.2)
a) Oncethemanualoperatingdevicehasbeenoperated,
alwaysreturnittoitsorigin(initialposition),andthen
starttheoperationofthedevice.
b) Before using the manual operating device, make sure
that nobody is present near the cylinder to be acti-
vated.
AIR QUALITY (Section 5.3)
a) Donotsupplyanythingotherthancompressedair.
b) Supply clean compressed air without any mixture of
corrosivegas.
a)
Compressed air usually contains a large amount of
drain, oxidized oil, tar, foreign matter, and rust from
thepiping. Filterout thoseelementsinthesupplied
air because they may cause a malfunction and de-
crease service life. In addition, clean the exhaust
beforeitisreleasedtotheairtominimizepollution.
b) Once you have lubricated a pre-lubricated valve, the
valveisnolongercapableofrunningwithoutbeinglu-
bricated from the outside. Do not leave the valve
withoutlubricationbutkeepitlubricated.
c) Do notusespindleoilor machineoil. They mayin-
duceexpansionoftherubberparts,whichmaycause
amalfunction.
!
WARNING:
!
CAUTION:
!
WARNING:
!
WARNING:
!
CAUTION:

[SM-200164-A/4]
−8−
ELECTRIC CIRCUITS (Section 5.4)
a) Check forthe presenceof any currentleak fromthe
external control device because it may cause an er-
roneousvalveoperation.
When a programmable controller or a similar controlde-
vice is used, a current leak may prevent the normal re-
turningofthevalvewhenthesolenoidisde-energized.
b) Restrictiononcurrentleak
When controlling solenoid valves using a programmable
controllerorasimilarcontroldevice,makesurethatthe
current leak in the programmable controller output is
equal to o
rless than thelevelshown in thetable below.
A current leak larger than the allowable level may cause
anerroneousvalveoperation.
PERIODIC INSPECTION (Section 6.1)
Before providing a maintenance service, cut the power
and the supply of compressed air and confirm the ab-
senceofresidualpressure.
Theaboveisrequiredtoensuresafety.
Regularly perform the daily and periodic inspections to
correctlymaintainproductperformance.
If the productis not correctly maintained , product per-
formance may deteriorate dramatically, resulting in a
shorter service life, fractures of components, and mal-
functions.
DISASSEMBLING AND REASSEMBLING (Section 6.2)
Before disassembling and reassembling solenoid valves,
readtheinstructionmanualcarefullyandunderstandthe
instructions.
A person who disassembles and reassembles a solenoid
valve system needs to have knowledge for safely per-
formingsuchoperationbasedontheunderstandingabout
the mechanisms and operating principles of solenoid
valves.
Personnel involved in this step must have passed the
PneumaticPressureSkillTestClass2orhigher.
!
CAUTION:
AC100V 3.0mAorlower
AC200V 1.5mAorlower
DC24V 1.8mAorlower
CRcircuit
Leakage
current
Solenoidvalve
Contact
C
R
Programmable
controller
!
CAUTION:
!
WARNING:
!
WARNING:

―9
―
INDEX
Block Manifold
Manual No. SM-200164-A/4
1. PART NAME AND DESCRIPTION 10
2. INTERNATIONAL SYSTEM OF UNITS (SI) 11
3. UNPACKING 12
4. INSTALLATION
4.1 Environment 13
4.2 Installation Method 14
4.3 Piping 15
4.4 Wiring 18
5. OPERATING RECOMMENDATION
5.1 Operation 24
5.2 Manual operating device 26
5.3 Air Quality 27
5.4 Electric Circuits 29
6. MAINTENANCE
6.1 Periodic Inspection 30
6.2 Disassembling and Reassembling 31
7. TROUBLE SHOOTING 34
8. PRODUCT SPECIFICATIONS AND HOW TO ORDER
8.1 Product Specifications 35
8.2 How to Order 36
8.3 Accessory 39
8.4 Consumable parts 43

[SM-200164-A/4]
−10−
PRODUCT
1
1. PARTNAMEANDDESCRIPTION
No. Part Name Description
①Valve unit mounting screw
Tw
o
mounting screws are provided for each valve unit.
They are used for mounting the valve unit to one of the
various types of bases.
②
Valve unit
③
Air supply or
exhaust block A block with a supply port and an exhaust port.
④Connecting key
The key is pushed in after the connection of the blocks
in order to secure the connection.
⑤
Mounting screw
DIN rail on the manifold.
⑥
DIN rail
⑦End block
It
has a function of common supply/exhaust flow plu
g-
ging.
⑧
Riping adapter
(one-touch joint)
Port P is the supply port : Port R and PR is the ex-
haust port : Port A and B is the output port.
⑨Valve block
A block of assembled solenoid valve unit and valve
block.
⑩Partition block
Shuts off the supply and exhaust as required and
is
used for different pressure circuits or the like.
①
⑩
②
③
④
⑤
⑥
⑦
⑧
⑨

[SM-200164-A/4] ―11
―
SIUNIT
2
2. INTERNATIONALSYSTEMOFUNITS(SI)
In this manual, values are expressed using the International System of Units
(SI).
Use the table below to convert them into values expressed in conventional
units.
Table of conversion between SI units and conventional units
(The values printed in Bolds fonts are values given in the International System of Units (SI)):
Force
N dyn kgf
1 1×1051.01972×10-1
1×10-5 1 1.01972×10-6
9.80665 9.80665×1051
Stress
Pa or N/m2MPa or N/mm2kgf/mm2kgf/cm2
1 1×10-6 1.01972×10-7 1.01972×10-5
1×1061 1.01972×10-1 1.01972×10
9.80665×1069.80665 1 1×102
9.80665×1049.80665×10-2 1×10-2 1
Note:1Pa=1N/m2, 1MPa=1N/mm2
Pressure
Pa kPa MPa bar kgf/cm2atm mmH2O mmHg or Torr
1 1×10-3 1×10-6 1×10-5 1.01972×10-5 9.86923×10-6 1.01972×10-1 7.50062×10-3
1×1031 1×10-3 1×10-2 1.01972×10-2 9.86923×10-3 1.01972×1027.50062
1×1061×1031 1×10 1.01972×10 9.86923 1.01972×1057.50062×103
1×1051×1021×10-1 1 1.01972 9.86923×10-1 1.01972×1047.50062×102
9.80665×1049.80665×10 9.80665×10-2 9.80665×10-1 1 9.67841×10-1 1×1047.35559×102
1.01325×1051.01325×1021.01325×10-1 1.01325 1.01323 1 1.03323×1047.60000×102
9.80665 9.80665×10-3 9.80665×10-6 9.80665×10-5 1×10-4 9.67841×10-5 1 7.35559×10-2
1.33322×1021.33322×10-1 1.33322×10-4 1.33322×10-3 1.35951×10-3 1.31579×10-3 1.35951×10 1
Note:1Pa=1N/m2
Example (converting a pressure value):
1kgf/cm2→0.0980665MPa 1MPa →1.01972×10kgf/cm2

[SM-200164-A/4]
−12−
UNPACKING
3
3. UNPACKING
Bags containing solenoid valves should be opened only
when you are ready to connect the valves to the pipes
immediatelyafterward.
Ifbagsareopenedbeforethevalvesarereadytobecon-
nectedtothepipes,theentryofforeignmatterfromthe
piping ports could cause the solenoid valves to fail or
malfunction.
a) Check the model number imprinted on the product to make sure that the
product you received is exactly the product you ordered.
b) Check the exterior of the product for any damage.
c) Before using the product, read the supplied documentation.
!
CAUTION:

[SM-200164-A/4] ―13―
INSTALLATION
4
4. INSTALLATION
Ifyouhavetousetheproductunderconditionsthatare
differentfromthespecifiedconditionsorifyouintendto
usetheproductforaspecialapplication,besuretocon-
sultusabouttheproductspecificationsbeforeusingthe
product.
4.1 Environment
a) Inadustyenvironment,foreignmattermayentereven
throughtheexhaustport.
Themovementoftheexhaustvalvecausesarespiratory
actionattheexhaustvalve,whichmaycauseinhalationof
foreignmatterneartheexhaustport. Thispotentialsit-
uation would be worse if the exhaust port is facing up-
ward. Attachasilencertotheexhaustportorhavethe
exhaustportfacedownward.
b) Keep the solenoid valve system dry. Take care to
avoiddirectcontactwithdrippingwaterorsplashesof
cuttingoil.
If the solenoid valve system is wet by a direct contact
withwaterorcuttingoil,anelectricalleakorburntsole-
noid coils may result. Protect the solenoid valve system
byusingacoverorbyinstallingitinsideapaneledcasing.
Ifthecylinderrodissplashedwithcuttingoil,theoilmay
penetrate through the cylinder into the secondary side
piping of the solenoid valve. This must be prevented to
avoidmalfunctions. Consultusforpreventivemeasures.
c) Thecoilswillproduceheat.
Particularly if the solenoid valve system is installed in a
controlboardorifthesolenoidcoilsneedtobeenergized
foralongtime,considerprovidingsufficientventilationto
releasetheheat. Thecoilscangetveryhot.
d) Do not use the solenoid valve system in an atmos-
pherethatincludesacorrosivegasorsolventvapors.
Do not use the solenoid valve system in an atmosphere
that includes a corrosive gas such as the sulfur dioxide
gasorinanatmospherethatincludessolventvapors.
e) Vibrationsandshocks
Do not subject the solenoid valve system to vibrations
50m/s2orstrongerorshocks300m/s2orstronger.
f) Avoidusingthesolenoidvalvesysteminahumiden-
vironment because the humidity is likely to cause
condensationwithachangeinthetemperature.
!
CAUTION:
!
CAUTION:

[SM-200164-A/4]
−14−
INSTALLATION
4
g) Donotusethenormaltypesolenoidvalvesforanap-
plicationthatrequiresconformitywithexplosion-proof
specifications. Choose explosion-proof solenoid
valvesinstead.
h) Thepackingandgasketsmaydeterioratesoonerthan
usual if used in an atmosphere with a higher than
normaldensityofozone(forexample,theatmosphere
near a beach or in an area with frequent thunder-
storms).
Consult us forthe packing and gaskets to be used in an
atmospherewithahigherozonedensity.
4.2 Installation method
When installing a solenoid valve unit, never attempt to
holditinpositionbymeansofthepipesconnectedtoit.
Mountthesolenoidvalvebyapplyingthemountingscrews
and/ormountingplatetothesolenoidvalve.
4.2.1 A work space for installation, removal, wiring, and piping opera-
tions should be provided around the installed solenoid valve sys-
tem.
4.2.2 Direct mounting
Use two mounting holes both ends of the DIN rail.
8
5.5
!
WARNING:
!
CAUTION:

[SM-200164-A/4] ―15―
INSTALLATION
4
4.3 Piping
a) Make sure that the pipes will not be disconnected at
the joints by mechanical movements, vibrations or
tension.
If the exhaust piping of the pneumatic circuit is discon-
nected,theactuatorspeedcontrolisdisabled.
If the above happens to a chuck holding mechanism, the
chuck will open. The inadvertent opening of the chuck
maycauseaseriousaccident.
b) When supplying the compressed air for the firsttime
after completing the piping, be sure to check every
jointinthepipingforairleakage.
c) When supplying the compressed air for the first time
after completing the piping, increase the air pressure
gradually but never introducea highly-pressurized air
suddenly.
A sudden introduction of a highly-pressurized air may
disconnectpipesatjointsand/orcausethetubestojump
around,anyofwhichmaycauseaninjury.
d) Donotdecreasetheinsidediameterofthepipingfrom
anyofthesolenoidvalveexhaustportstoadiameter
lessthantheexhaustpipeconnectingportsize.
Normal operation of the actuator depends on the
smoothnessoftheexhaustflow. Withamanifoldsystem,
arestrictiontotheexhaustflowmaypreventnormalop-
erationofothersolenoidvalves.
e) Removalofforeignmatter
Rust and other foreign matter in the pneumatic circuit
may cause a malfunction or leakage from the valve seat.
Insert a filter (maximum allowable particle size 5μm or
less)immediatelyupstreamofthesolenoidvalve.
f) Airsupply
Donotrestricttheflowofairthroughtheairsupplypip-
ing. Withamanifoldsystemwithmultiplestations,adrop
in the air supply pressure may cause trouble through a
delayintheoperationtiming
!
CAUTION:

[SM-200164-A/4]
−16−
INSTALLATION
4
4.3.1 Flushing
Before connecting pipes, flush the interiors of the tubes, solenoid valves, and
connected devices to remove foreign matter.
4.3.2 Blow circuit
Do not open the cylinder port circuit to the air because a drop in the air sup-
ply pressure may cause a malfunction. Select the external pilot type design
instead of the internal pilot type design. The lowest allowable pressure with
the internal pilot type design is 0.2 MPa.
4.3.3 Exhaust port
Minimize the restriction to the flow of the exhaust air because such re-
striction may cause a delay in the cylinder response. If such a delay hap-
pens, the speed needs to be adjusted between the cylinder and solenoid valve.
4.3.4 Pipe connections
(1) Tubes to be used
For use with solenoid valves with one-touch joints, select tubes of the type
specified by us:
Soft nylon tubes (F-1500 Series)
Urethane tubes (U-9500 Series)
(2) For installation at a site that has spatters in the air, select incombustible
tubes or metal pipes.
(3) For a piping used for both hydraulic and pneumatic controls, select a hydrau-
lic hose.
When combining a spiral tube with a standard one-touch joint, fix the tube
origin using a hose band. Otherwise the rotation of the tube will decrease
the efficiency of the clamping.
For use in a high-temperature atmosphere, select fastener joints instead of
one-touch joints.

[SM-200164-A/4] ―17―
INSTALLATION
4
(4) When selecting from tubes commercially available, carefully study the accu-
racy of the outside diameter as well as the wall thickness and the hardness.
The hardness of an urethane tube should be 93°C or more (as measured by
a rubber hardness meter).
With a tube that does not have a sufficient accuracy of the outside diameter
or the specified hardness, a decrease in the chucking force may cause dis-
connection or difficulty in inserting.
Tube dimensions
Outside diameter
mm
Inside diameter mm
Nylon Urethane
φ4 φ2.5 φ2
φ6 φ4 φ4
φ8 φ5.7 φ5
φ10 φ7.2 φ6.5
(5) Minimum bending radius of tubes
Observe the minimum bending radius of tubes. Neglecting the minimum
bending radius may cause disconnection or leaks.
Tube bore Minimum bending radius mm
Nylon Urethane
φ4 10 10
φ6 20 20
φ8 30 30
φ10 40 40
(6) Cutting a tube
To cut a tube, use a tube cutter to cut the tube perpendicularly to the length
of the tube. Inserting an obliquely cut end of a tube may cause air leakage.
(7) Tube connections
Do not bend a tube immediately at where it is connected to the joint but lead
it out straight from the end of the joint for a length equal to or greater than
the outside diameter of the tube. The tension applied sideways through the
tube should not exceed 40N.
(8) Blank plug to be used
For use with a solenoid valve with a one-touch joint, select the blank plug
specified by us:
Blank plug GWP□-B Series
Outside diameter allowance
Soft or hard nylon ±0.1mm
Urethane φ4, φ6 +0.1mm
-0.15mm
Urethane φ8, φ10 +0.1mm
-0.2mm

[SM-200164-A/4]
−18−
INSTALLATION
4
4.4 Wiring
Beforewiring,readtheinstructionmanualcarefullyand
understandtheinstructions.
Apersonwhowiresneedstohaveknowledgeforsafely
performing suchoperationbasedontheunderstanding
aboutthe mechanismsandoperatingprinciplesofsole-
noidvalves.
Before supplying the power, check the power supply
voltageandthecurrenttype(ACorDC).
1) Caution for wiring
(1) When using the small terminal box and water-proof is required, use cab-tire
cords φ4 to φ6.5 in outer diameter (water-resistance is improved, but not
for outdoor use).
(2) The connector type (C, C1, C2, C3, D, D1, D2, D3) should be used in a place
with little dust and not directly exposed to water and oil.
(3) For the electrical circuit, use a switching circuit free of chattering.
(4) The electrical circuit should have fuses.
(5) Be sure that the operation voltage is within 10% of the rated voltage.
!
WARNING:
!
CAUTION:

[SM-200164-A/4] ―19―
INSTALLATION
4
2) Wire connection
Name Grommet (standard) Small terminal box Small terminal box
with indicator light
Small terminal box
with surge suppressor
and indicator light
Option
code No code B L LS
Shape
Circuit
Name Plug-in connector C type
with lead wire
Plug-in connector C type
without lead wire
Plug-in connector C type
with lead wire, surge
suppressor and indicator
light
Plug-in connector C type
without leadwire,
surge suppressor and
indicator light
Option
code C C1 C2 C3
Shape
Circuit
Lead wire
300mm
(20/0.18)
90
°
(
)
(
)
DC
(
〜
)
(
〜
)
AC
(
〜
)
(
〜
)
AC
Lead wire
300mm
(11/0.16)
Lead wire
300mm
(11/0.16)
(
)
(
)
DC
Red
Black
(
〜
)
(
〜
)
AC
Table of contents
Other CKD Control Unit manuals
Popular Control Unit manuals by other brands
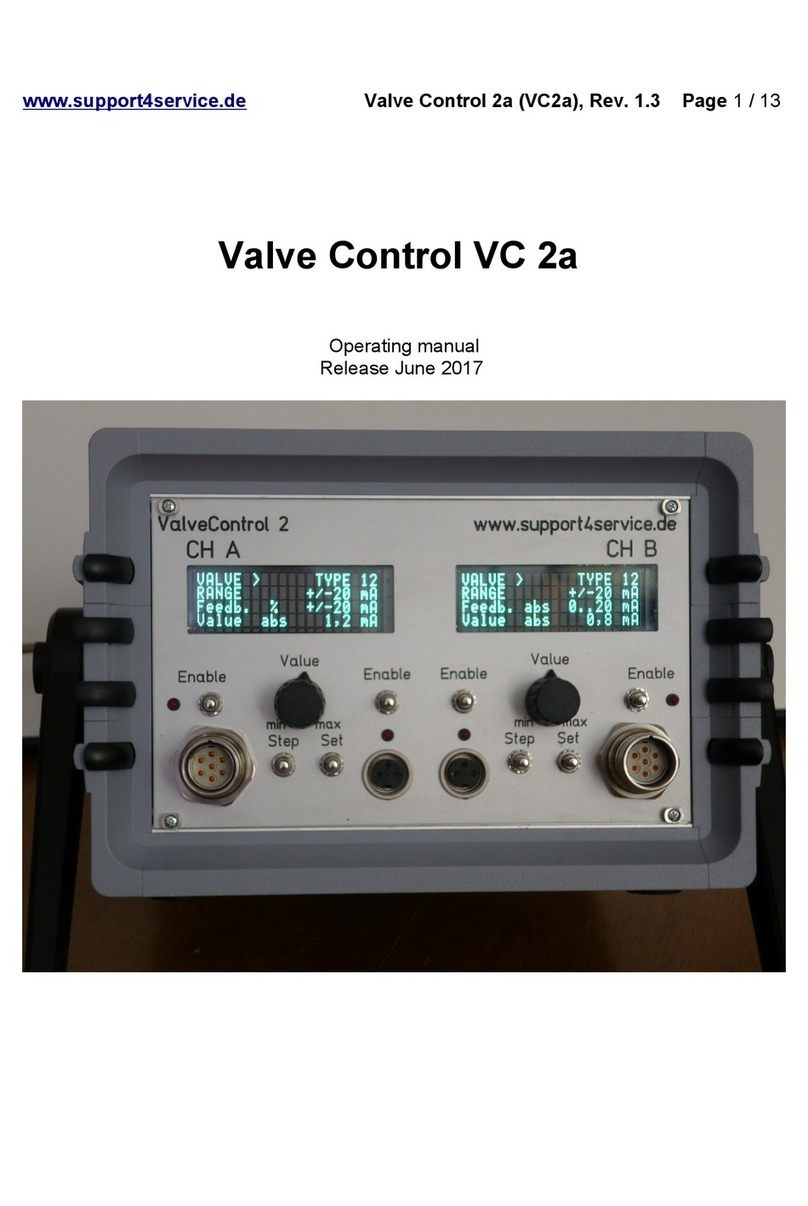
S4S
S4S VC 2a operating manual
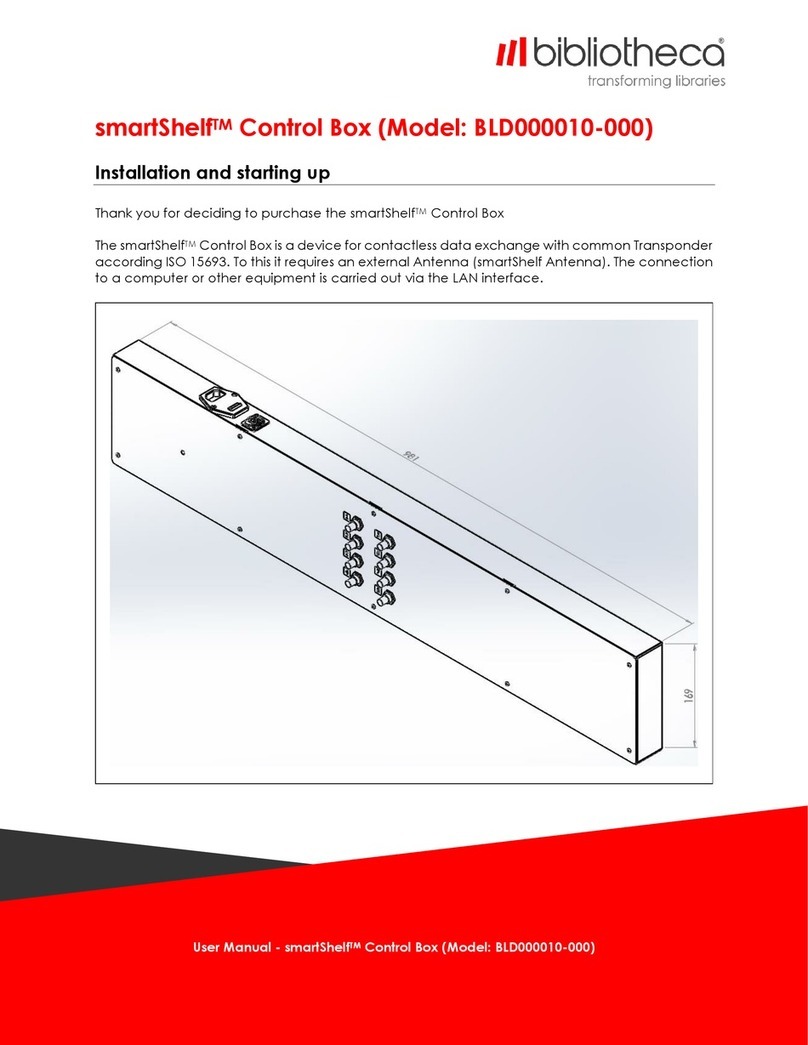
Bibliotheca
Bibliotheca smartShelf BLD000010-000 user manual

American
American TIM-48 quick start guide

Parker Pneumatic
Parker Pneumatic CCJ1-1S Series Installation & service instructions
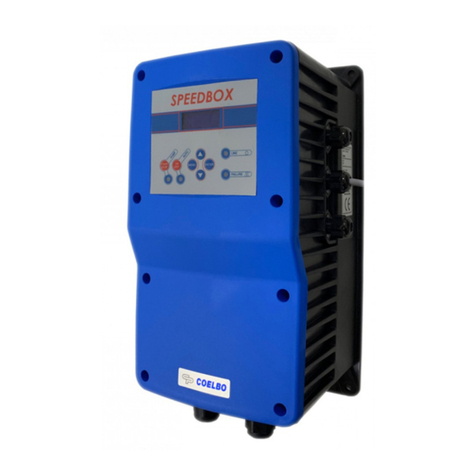
Coelbo
Coelbo 1305TT Installation and operating instructions
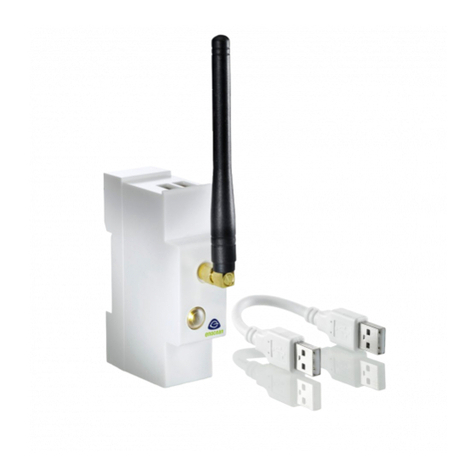
Overkiz
Overkiz HATTARA DIN RAIL MR-ENO manual