Delta DCS User manual


3
Preface
Thank you for using this product. This manual provides information regarding safe operation of Delta
SCARA robot that users must take note in following. Before operating the SCARA robot, to ensure your
safety, please be sure to carefully read through this manual. Content of this manual includes:
Installation and inspection of the robot
Functions and descriptions for operating the human-machine interface(HMI)
Checkup and maintenance
Troubleshooting
Considering operation environment and safety of operating personnel, we offer specialized training for
staffs of different types of robot applications. This manual is suitable for reference by the following types of
users:
Designers for integration ofsystem
Personnel performing installation orwiring
Personnel performing test run and adjustment on themachine
Maintenance and inspectionpersonnel
Personnel operating theequipment
Before using, please read this manual carefully to ensure proper use of the robotic arm. Also, please place
the manual at a safe location for reference at any time. Before finishing reading this manual, be sure to
follow these guidelines:
The installation environment must be from water vapor, corrosive, and flammable gas.
When wiring, do not connect the 3-phase power tothe connectors on U, V,W motor.Erroneous connection
willdamagetheservoelectrics.
Grounding must be performedcorrectly.
When connecting power, do not disassemble drive, motor, or changewiring.
Beforeconnectingpowertoruntheroboticarm,makesuretheemergencystopdevicecanstartatanytime.
When connecting power and running the robotic arm, do not touch heat sink to avoid burninjury.
Should you still have questions on use of the robot, please contact your sales agent or our customer ser-
vice center.

4
Safety Precaution
SCARA robot series includes the All-in One DCS controller which integrates motion controller, robot
controller and four servo drives in one single unit with high-speed computing capability. For the safety use,
take precaution on safety of the work environment during the operation and ensure safety of operation for
the users. Also, the teach pendant and the driver cannot be operated separately.
DCS series control cabinet can be used on industrial applications and are recommended for installa- tion in
a wiring (electric) box specified in the manual (controller, wires, and motors must all be installed in a
location that meets the minimum requirement from UL level 1 for the environment of installation). Take the
following precautions at any time when receiving, inspecting, installing, wiring, operating, maintaining, and
checking the robot.
Meanings represented by symbols for “Danger”, “Warning”, and “Stop”:
Please follow the methods specified for use with servo drives and servo motors, as
doing otherwise might cause fire or failure ofequipment.
Means there might be a potential danger that non-compliance might result in
medium level hazard, serious damage, or failure of theproduct.
Means forbidden acts that non-compliance might result in damage or failure of the
product beyond use.
Receiving and inspecting
Please follow the methods specified for use with the robotic arm, as doing otherwise
might cause fire or failure of equipment.
Note upon installation
It is forbidden to expose the product to places with water vapor, corrosive gas, and
flammable gas. Otherwise electric shock or fire might result.
Note upon
wiring
Please connect ground protection terminals with grounding systems. Improper
grounding might result in electric shock or fire.
Do not connect three-phase power to U, V,W motor output terminals as personnel
injury or fire might result if doneotherwise.
Tighten fixing screws for the power and motor output terminals, as fire might result if
done otherwise.
Toavoid hazard, refer to selection of wires when performingwiring.

5
Note upon operating
Maintenance
and check
Before starting to run, the robot needs adjustment on settings based on parameters
set by users. If not adjusted to the correct matching value, loss of control or failure
for the operation of machine might result.
Before starting to run, make sure the emergency stopping device could be started
at any time.
When robot moves, do not touch any moving part of the robot, as personnel injury
might result if done
After robot connecting, any error in operation will not only cause damages on the
robot but also result in bodily harm.
Strongly recommended: Test to see if the robot would operate normally under no
loading and then connect the load to prevent unnecessaryhazard.
Do not touch the controller when running the machine, as doing otherwise might
result in burn injury or danger of electric shock because of hightemperature.
Do not touch the controller and inside of the robot, as electric shock might result if
done otherwise.
When turning on power, do not disassemble HMI, as electric shock and damage on
the HMI might result if doneotherwise.
Do not touch the wiring terminals within 30 minutes after turning off the power as
residual voltage may cause electrical shocks.
Do not change wiring with power on, as electric shock or personnel injury might
result if done otherwise.
Only trained and qualified professional electric personnel are allowed to perform
installation, wiring, repairing, and maintaining thisrobot.
Wiring of circuits
When wiring, disassemble the terminal base from the servodrive.
Plug one wire into one plug on the terminalbase
When plugging wires, do not short-circuit the core wire and its nearbywires.
Before powering on, thoroughly check for properwiring.
Do not frequently switch the power on or off. If there is a need to turn the power on
and off in succession, keep the frequency below once within oneminute.

6
Table of Contents
Preface ..................................................................................................................... iii
Safety Precaution..................................................................................................... iv
1.Product description
1.1 Operating direction.............................................................................................1
1.2 Dimensional drawing.......................................................................................... 2
1.3 Motion range ...................................................................................................... 3
1.4. Robot specification............................................................................................ 4
1.5 Specification of DCS controller .......................................................................... 5
2. Wiring sequence
3. Exterior Look of DCS controller and Descriptions ofConnectors
3.1 Exterior look and dimension................................................................................. 8
3.2Descriptions of external ports on theDCS controller........................................... 9
3.3
Definitions and descriptions for terminals on the DCS controller .......................10
3.3.1
Definitions of pins on major loop power terminal:..........................................................11
3.3.2
Definitions of pins on control power terminal:................................................................11
3.4 Wiring for ROBOT and controller:.......................................................................12
3.4.1
Specifications for connectors on the base and controller............................................. 12
3.4.2
Definitions for connectors on motor power cable ......................................................... 13
3.4.3
Definitions for connectors for motor brake (BRK.DIO)................................................. 14
3.4.4
Definition of Encoder connector .................................................................................... 15
3.4.5 STD.DIO connectors...................................................................................................... 16
DI12 & DI19~DI24................................................................................................................... 16
3.4.6 SYS.DIO connectors...................................................................................................... 17
3.4.7 Specifications of the communication connector............................................................ 22
3.4.8. I/O Input wiring examples............................................................................................. 24
3.4.9 Wiring example of I/O Output.....................................................................................25
3.4.10 SCARA body connector description............................................................................ 26

vii
4. Battery replacement
4.1 Notes....................................................................................................................28
4.2 Battery replacement procedures .........................................................................29
5. Hardware components
5.1 Connector components........................................................................................30
5.2 Optional items......................................................................................................32
6. Descriptions for Troubleshooting
6.1 Display of status .............................................................................................. 33
6.1.1 Display of system status............................................................................................33
6.1.2 Display of alert message...............................................................................................34
6.2 Description of P0-01 parameter...........................................................................34
6.3 Troubleshooting of abnormal alarms................................................................35
6.4 Index of alarm......................................................................................................36
6.4.1 Group type .....................................................................................................................36
6.4.2 Axis type.........................................................................................................................37
6.4.3 Control type....................................................................................................................38

8
List of Tables
Table 1-1 Specification of DRS40L series..............................................................................4
Table 1-2 Specification of DCS Controller.................................................................................5
Table 3-1 Manual power pin.................................................................................................10
Table 3-2 Definitions for 4.2 in-flight connectors on motor power cable................................13
Table 3-4 Definitions of the pins on Encoder connector.........................................................15
Table 3-5 Definitions of the pins on Delta Encoder...............................................................15
Table 3-6 Definitions of pins for user’s IO...............................................................................16
Table 3-7 Definitions of the pins for system IO ........................................................................16
Table 3-8 Definitions of functions for the system I/O.............................................................18
Table 3-9 Definitions of the connectors...................................................................................22
Table 5-1 DCS Accessories List..............................................................................................30
Table 6-1 System Status Display.............................................................................................33
Table 6-2 Alert Message Display.............................................................................................34
Table 6-3 P0-01 Parameter Description..................................................................................34
Table 3-3 Definitions of the motor pins....................................................................................14
Table 3-10 Definitions of RS232/RS485 pins..........................................................................23

9
List of Figures
Figure 1-1 Directions of SCARA Motions.............................................................................. 1
Figure 1-2 External Dimension of the SCARA...................................................................... 2
Figure 1-3 SCARA Motion range ........................................................................................... 3
Figure 2-1 Peripheral Device Wiring Diagram....................................................................... 7
Figure 3-1 Exterior look of DCS Controller............................................................................ 8
Figure 3-2 Descriptions of external pins on the back of the controller................................. 9
Figure 3-3 Actual main circuit circuit power connector figure............................................... 11
Figure 3-4 Definition for the motor power terminal ............................................................... 11
Figure 3-5 Connector for power oncontrol circuit ............................................................................11
Figure 3-6 Definition for the control power terminal.............................................................. 11
Figure 3-7 Wiring diagram for the SCARA and MS controller............................................. 12
Figure 3-8 Motor Power Cable.............................................................................................. 12
Figure 3-9 Motor Encoder Cable .......................................................................................... 12
Figure 3-10 Motor connectors................................................................................................ 13
Figure 3-11 Connectors on motor power cable..................................................................... 13
Figure 3-12 Definitions of Encoder pins................................................................................ 14
Figure 3-13 Brake Release Button Location......................................................................... 14
Figure 3-14 Definitions of pins on motor Encoder................................................................. 15
Figure 3-15 Definitions of pins on motor Encoder................................................................. 15
Figure 3-16 External View of the Connectors ....................................................................... 16
Figure 3-17 Configuration of Rear Pins................................................................................. 16
Figure 3-18 Definitions of SYS.DIO pins............................................................................... 17
Figure 3-19 E-STOP Wiring Example.................................................................................... 18
Figure 3-20 Wiring Example of the Safety Door ................................................................... 18
Figure 3-21 MODE SELECT Wiring Example....................................................................... 19
Figure 3-22 RUN/STOP SWITCH Wiring Example............................................................... 20
Figure 3-23 Reset Wiring Example........................................................................................ 20
Figure 3-24 TP connector....................................................................................................... 22
Figure 3-25 Configurations of RS232/RS485 Pins ............................................................... 23
Figure 3-26 Ethernet Port....................................................................................................... 23
Figure 3-27 USB B-type port5............................................................................................23
Figure 3-28 USB port ............................................................................................................. 23
Figure 3-29 DMCNet port....................................................................................................... 23
Figure 3-30 Wiring Example of the Button or Inching Switch .............................................24
Figure 3-31 Wiring example of proximity switch.................................................................24
Figure 3-32 Wiring example of light signal or relay (loading positive) .................................25
Figure 3-33 Wiring example of light signal or relay (loading negative)).............................. 25
Figure 3-34 SCARA Body Connector Configuration............................................................. 26
Figure 3-35 SCARA I/O Connector Description.................................................................... 26

10
Figure 3-36 SCARA Air Tube Configuration.............................................................................27
Figure 5-1 Delta DC24V Power Supply................................................................................32
Figure 6-1 7-segment Display...................................................................................................33
Figure 6-2 Display of MS board................................................................................................34
Figure 6-3 Seven-segment display of MS error code..............................................................35

1
1.Product description
1.1 Operating direction
DSR40L series is a robot consisted of four axes, which are first arm (J1), second arm (J2), axis
Z (J3), and axis R (J4). Directions of their motions are shown in Figure 1-1 Directions of SCARA
Motions, with (+) and (-) on the graph representing directions of each axis defined by user in the
editor program.
Cartesian coordi
Figure 1-1 Directions of SCARA Motions
(Z+)
(Y+)
(X+)
(Y-)
(Z-)

2
SCARA ROBOT DCS ELECTRIC CONTROL INSTRUCTIONS
1.2 Dimensional drawing
External dimensions of the mechanism are shown in Figure 1-2. Please use 4-M8 locking screws to
secure the mechanism on a platform
Unit: mm
Figure 1-2 External Dimension of the SCARA

3
1. PRODUCT DESCRIPTION
1.3 Motion range
When SCARA robots line up, the maximum turning radius for first arm is 400 mm and the range of
rotation movement is ±130°; when first arm reaches its limit, second arm can move for other 100°
to reach its limit. The maximum turning radius for second arm is 200 mm and the range of rotation
movement is ±146.6°. The detailed motion range of SCARA is as shown in Figure 1-3.
First Arm
Figure 1-3 SCARA Motion range

4
SCARA ROBOT DCS ELECTRIC CONTROL INSTRUCTIONS
1.4. Robot specification
The specification of DRS40L series is shown in Table 1-1.
Table 1-1 Specification of DRS40L series
Model
DRS40L
Axis count
4
Arm length( Arm 1+Arm 2 )
400 mm
Rated/Maximum payload
1 Kg / 3 Kg
Maximum speed
X-Y
4710 mm / sec
Z
1250 mm / sec
R
1875°/ sec
Range of motion
J1
±130°
J2
±146.6°
Z
150 mm
RZ
±360°
Standard time for a cycle *
0.42 sec
Accuracy of repetition
X/Y
±0.01 mm
Z
±0.01 mm
R
±0.01°
Motor power
J1
200 W
J2
200 W
Z
100 W
RZ
100 W
Rated/max. pressing strength (Z)
100 / 250N
Max. allowable load inertia (R)
0.0091 / 0.075 Kg-m2
Cable connector for customer installation
15Pin D-Sub
Air pipe for customer installation
ø4 mmx2, ø6 mmx1
Body weight
16 Kg
*25mm-300mm-25mm & Payload: 1Kg, test environment temperature 25oC, environmental relative humidity 45% ~65% RH
*Delta reserves the right tochange specifications without further notice.

5
1. PRODUCT DESCRIPTION
1.5 Specification of DCS controller
The detailed specification shown as below:
Table 1-2 Specification of DCS Controller
ModelDCSseries
PowerSupply
PhaseNumber /Voltage
Singlephase: 200~230VAC,-15%~10%,23.8A(for DRS40L: 5A)
Control PowerSupply
24VDC, -10%~10%, 5A(for DRS40L: 3A)
Size (W) X (H) X (D) mm / Weight
175 mm x 300 mm x 159 mm / 5.6 kg
CoolingMethod
Fancooling
External Optical Scale orEncoder
A, B, and Zformat
RobotControl
Programming Language
Delta robotlanguage
MotionModel
Point-to-pointmotion,linearinterpolation, andcircularinterpolation
MemoryCapacity
20MB: for programming editor and data users
1K location point is available for global variables
(which can beshared among different programs).
30K location point is available for all programming editors.
Input /Output
StandardI/O
User I/O: 24 sets of input and 12 sets of output
System I/O: 8 sets of output and 8 sets of input
Communication
Interface
Ethernet
Onechannel
RS-232 /RS-485
One connectingport
(one connecting port allows switching between two communication
functions)
DMCNET
Onechannel
USBHost
Two connectingport
Environmental
Specification
InstallationSite
Indoor (avoid direct sunlight) and no corrosive vapor
(avoid oily fume, inflammable gas, and dust)
Elevation
Less than 1000Mabove sea level
AtmospherePressure
86 kPa ~ 106kPa
Ambient Temperature
0°C ~ 55°C (Please force surrounding aircirculation when ambient
temperature is above45°C)
Storage Temperature
-20°C ~65°C
Humidity
0 ~ 90% RH (nofog)
Vibration
9.80665 m/s2 (1G) below 20 Hz, 20 ~ 50 Hz 5.88 m/s2 (0.6G)
IPGrade
IP20
ElectricalSystem
TNsystem*
SafetyCertification
IEC/EN 61800-5-1,UL508C, C-tick
Note: TN system refers to that the neutral point of the electrical system is directly connected to the ground and the exposed
metal components areconnected to theground via protective grounding conductor.

2. Wiring sequence
1. Please lock SCARA and the DCS drive controller in place properly.
2. Connect SCARA and the ASDA -MS drive controller:
(1) Encoder Cable: Connect the encoder connector of the encoder cable to the motor encoder feedback
connector on DCS.
(2) Motor Power Cable:
A. Connect the power connector of the power cable to the servo motor output (U, V,W) on the DCS; please
note the connector label when connecting and do not connect the wrong cable.
B. Connect the brake connector of the power cable to the BRK.DIO connector on the DCS and connect the
brake input power. Please refer to 3.4.3 break connector (BRK.DIO) definitions for the BRK.DIO pins.
3. E-STOP signal: Please connect the E-STOP cable properly and please refer to the E-STOP wiring
example as illustrated in 3.4.6 SYS.DIO connector.
4. Connecting the power:
(1) Main circuit power input: Connect the single-phase AC 200V to 230V single-phase 50/60 Hz to the
main circuit power input terminal of the drive controller and properly ground it.
(2) Control circuit power input: Connect 24V (3A) DC power (please use Class 2) to supply control power
for the DCS drive controller.
5. Teach pendant can be purchased optionally.
(1) Please insert or remove the teach pendant when it is unpowered.
(2) If the teach pendant is not connected, please connect the teach pendant short-circuit connector.
Please refer to the specification manual for details on the specifications of the teach pendant
6

7
POWER SUPPLY(At lease 5A)
Figure 2-1 Peripheral Device Wiring Diagram
Set to prevent damages to the driver
due to excessive instant current
generated when powering on/off or
short-circuit.
750W Single-phase /
Three-phase 200-230V
Filter
Reduce the electromagnetic interference
transmitted through the power cable
between the device and power.
Teach Pendant (Optional)
Teach pendant can be
purchased to operate SCARA
Magnetic Control (MC)
Connected to the emergency
stop. when the user presses
the emergency stop button,
the MC will be triggered and
cut the power of driver.
DROE software shall
be installed
POWER BUS connector
Shielding recommended
3M MDR Connector 50PIN
DI 24 sets
DO 12 sets
D-sub connector 26PIN
DI 8sets
DO 8sets
Computer
POWER
connector
Motor brake
connector
Standard I/O
System I/O
CONTROL BUS
connector
Power Supply
No-fuse breaker (NFB)
RJ45 cable
ENCODER connector

8
8
175.2175.2
mmmm
300.8300.8
mmmm
175.2175.2
mmmm
50.3 mm
50.3 mm
159.3159.3
mmmm
7070
mmmm
50.3 mm
50.3 mm
3.
ExteriorLookofDCScontroller and
DescriptionsofConnectors
3.1 Exterior look and dimension
175.2 mm
Figure 3-1 Exterior look of DCS Controller
175.2 mm
300.8 mm
70 mm
159.3 mm
50.3mm
50.3mm

9
3. EXTERIOR LOOK OF DCS CONTROLLER AND DESCRIPTIONS OF CONNECTORS
3.2Descriptionsof externalportson the DCS controller
Teaching Pendant Connection Port
Used to connect the teaching pendant
Serial Communication Port
For MODBUS communication control, sup-
porting RS-485 / RS-232 serial
communication.
High-speed Communiction Port
(Ethernet) / USB Connetion Port
(USB1, USB2) / DMCNET
Connection Port (DMCNET)
•Ethernet: Used to connect PCs
or ntebooks, capable of accesing
data through DROE software.
•USB1, USB2: Direct connectivity
to USB flash drives
•DMCNET: Used to connect
DMCNET peripherals
LED Display
The 5 digit, 7 segment
LED displays the controller status
or fault codes.
Main Circuit Terminal (R, S)
Used to connect 200 ~ 230Vac,
50/60Hz commercial power
supply.
Servo Motor Output (U, V,W)
Used to connect servo motor.
Never connect the output terminal
to main circuit power as the AC
drive may be damaged beyond
repair if incorrect
cables are connected
to the output terminals.
Motor Brake Output Terminal
(BRK. DIO) Standard I/O Terminal
(STD. DIO)
STO I/O Terminal
(Safe Torque Off)
Used to connect a certified
safety relay or switch for
controlling STO I/O signals.
Control Circuit Terminal
Used to connect DC24V
power supply.
System I/O Terminal
(SYS. DIO)
Full-Closed Loop Control
Interface (EXT. ENG)
Used to connect linear scale
and encoder. Feeds back
the position signals of the full
closed linear scale and encoder
for controlling A, B, Z phase
signals.
Motor Encoder Interface
(MOTOR. ENC.)
Used to connect the encoder
signals of four servo motors
Ground Terminal
Used to connect grounding
wire of power supply and servo
motor.
Figure 3-2 Descriptions of external pins on the back of the controller

10
SCARA ROBOT DCS ELECTRIC CONTROL INSTRUCTIONS
3.3 Definitions and descriptions for terminals on the
DCS controller
Table 3-1 Manual power pin
Terminal marking
Name
Description
24V,0V
24V power inputend
Connect 24V DC power supply
R, S,
Power input endfor
major loop
Connect single-phaseAC powersupply(220VAC)
U1, V1, W1
U2, V2, W2
U3, V3, W3
U4, V4, W4
FG
Motor connectingwire
Connect to the motor power cable
Terminal
marking
Description
U
Main power cable for the motor
V
W
FG
Connect to grounding terminal of the drive
Groundingterminal
Connect with ground wires for the power supply and motor
STD.DIO
I/Oconnector
Connect USERI/O
SYS.DIO
I/Oconnector
Connect SYSTEMI/O
BRK.DIO
DOconnector
Release electromagnetic brake onthemotor
EXT.ENC.
Encoderconnector
Connect externalEncode
MotorENC.
Encoderconnector
Connect the motorEncode
TP
TeachPendant
connector
Connect HMIinterface
RS232
Communicationport
connector
ConnectRS-232(supports ModbusASCIIServer)
RS485
Communicationport
connector
ConnectRS-485
ETHERNET
Communicationport
connector
Connect the internet (supports Modbus TCP/IPServer)
USB1
Communicationport
connector
ConnectPC
USB2
Communicationport
connector
Connect USBdrive
DMCNET
Communicationport
connector
ConnectrelatedDeltaproducts
Table of contents
Other Delta Controllers manuals
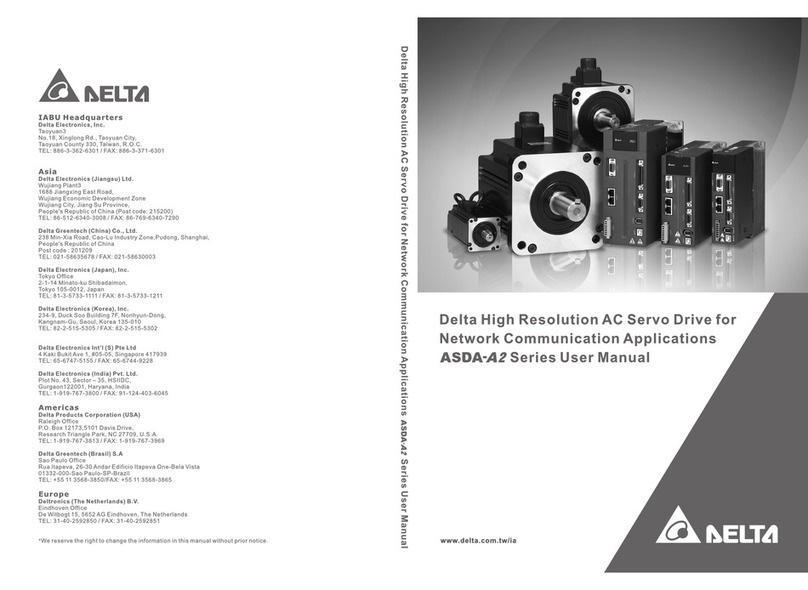
Delta
Delta ASDA-A2 Series User manual
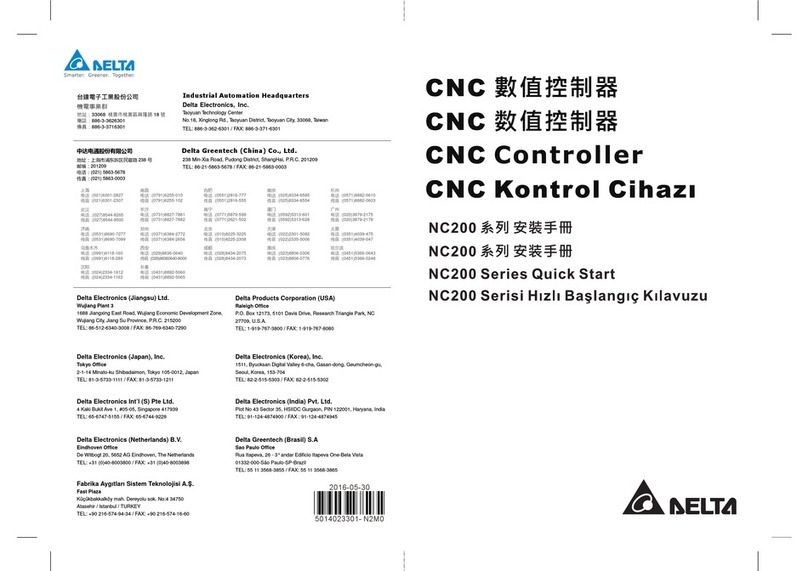
Delta
Delta NC200 User manual
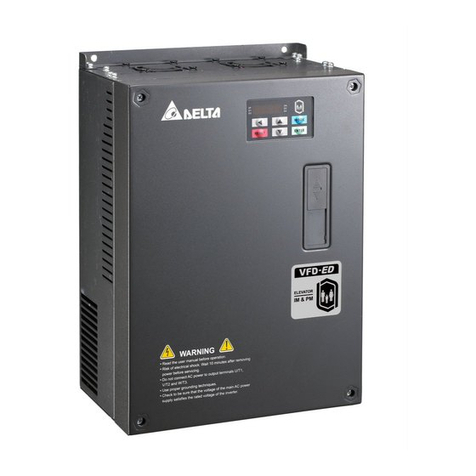
Delta
Delta VFD-ED Series User manual
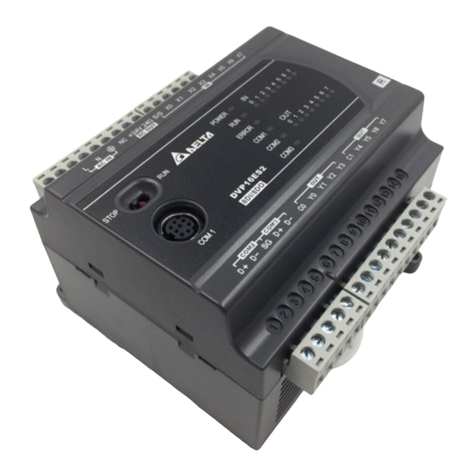
Delta
Delta DVP-ES2 User manual
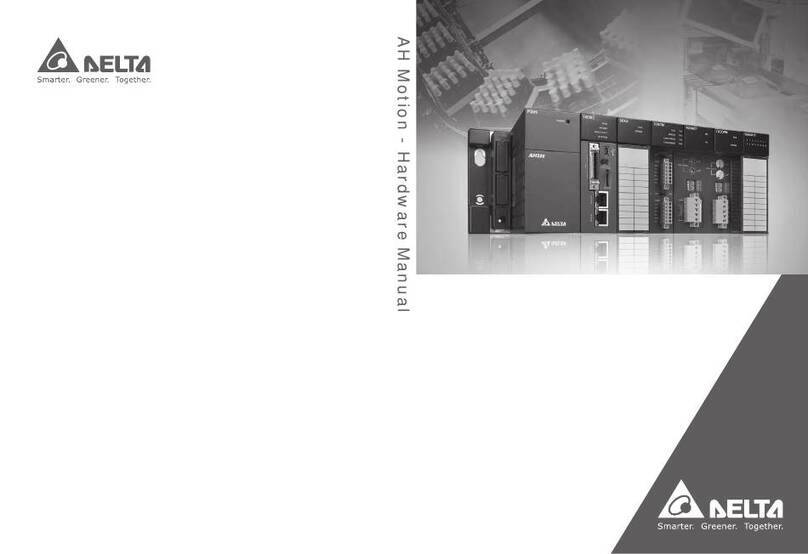
Delta
Delta AH Motion Series User manual
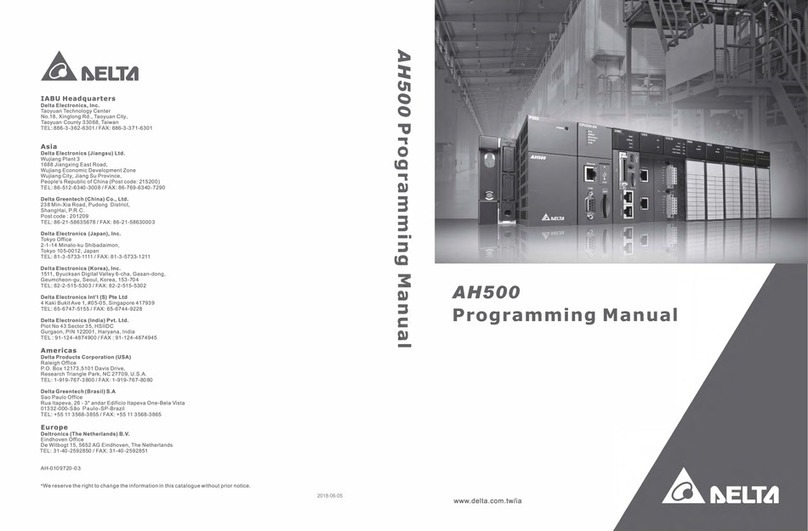
Delta
Delta AH500 series Owner's manual
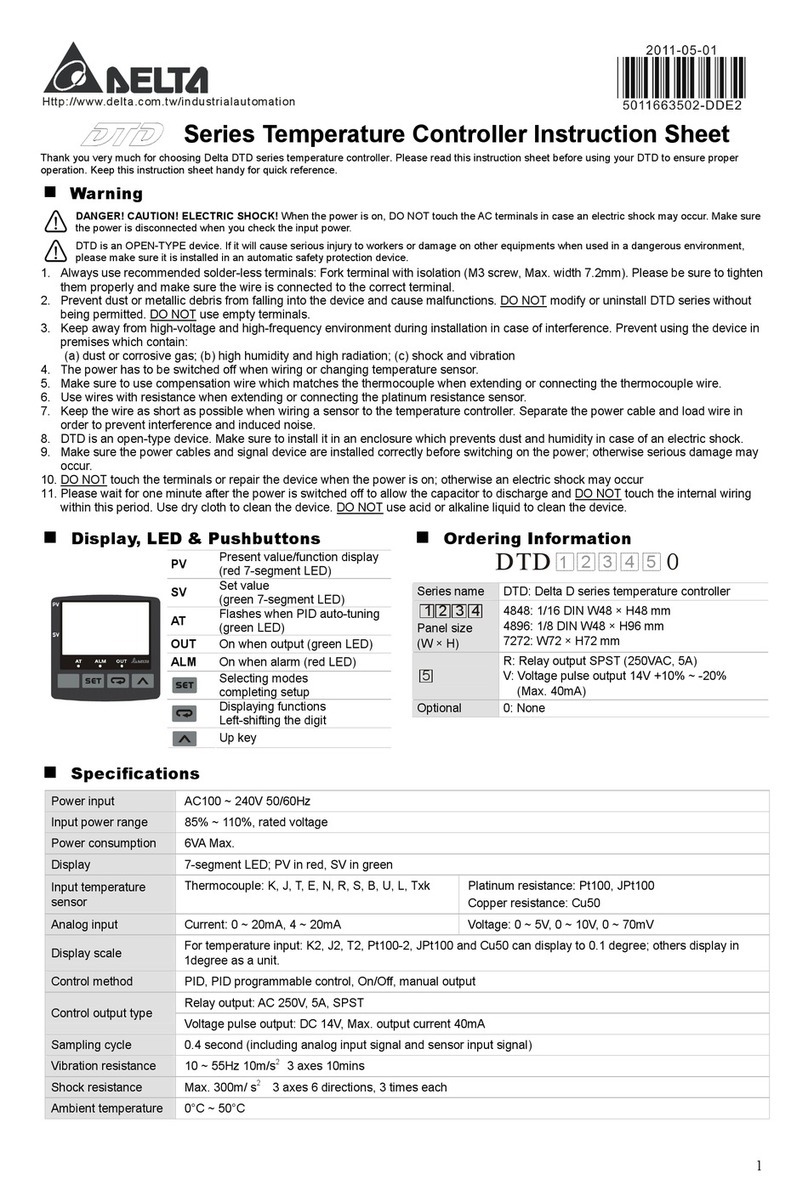
Delta
Delta DTD Series User manual
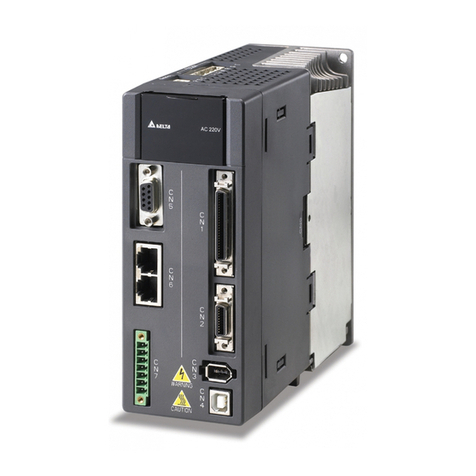
Delta
Delta ASDA-A2 Series User manual
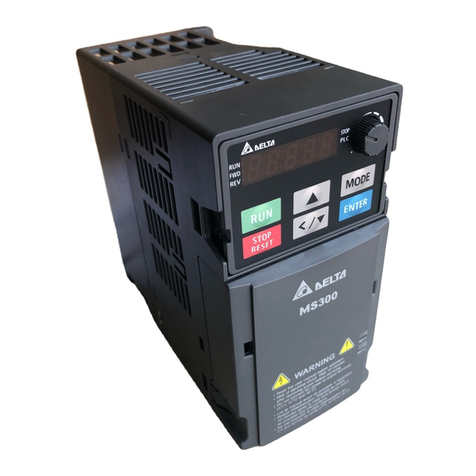
Delta
Delta VFD7A5MS23ANSHA User manual
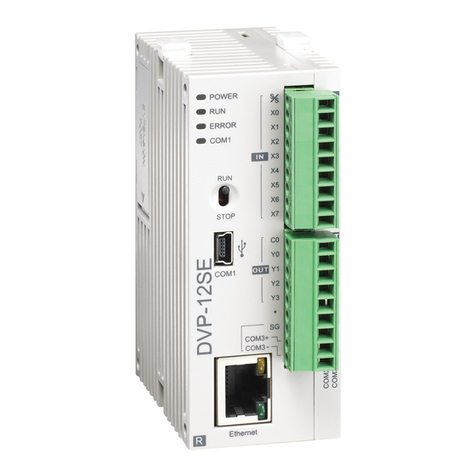
Delta
Delta DVP-PLC Instructions for use
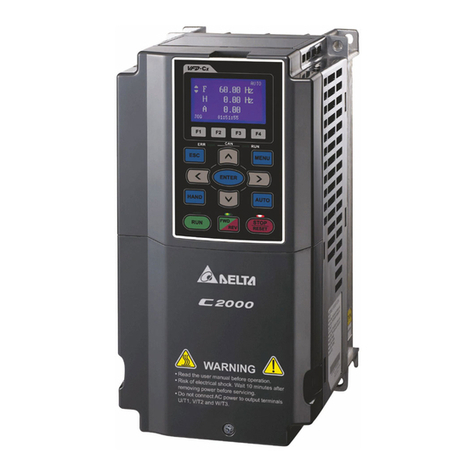
Delta
Delta C2000 Series User manual
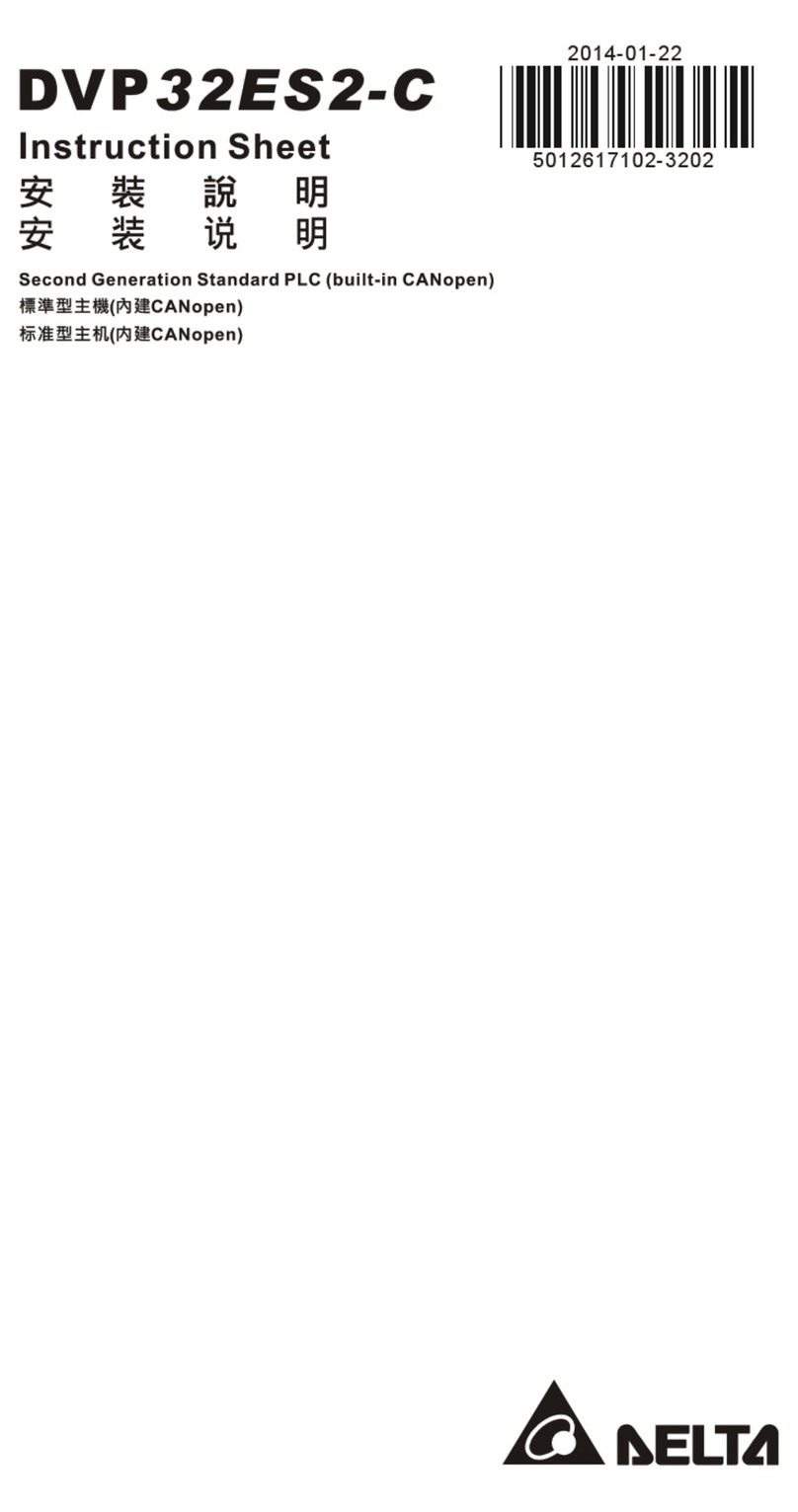
Delta
Delta DVP32ES200RC User manual
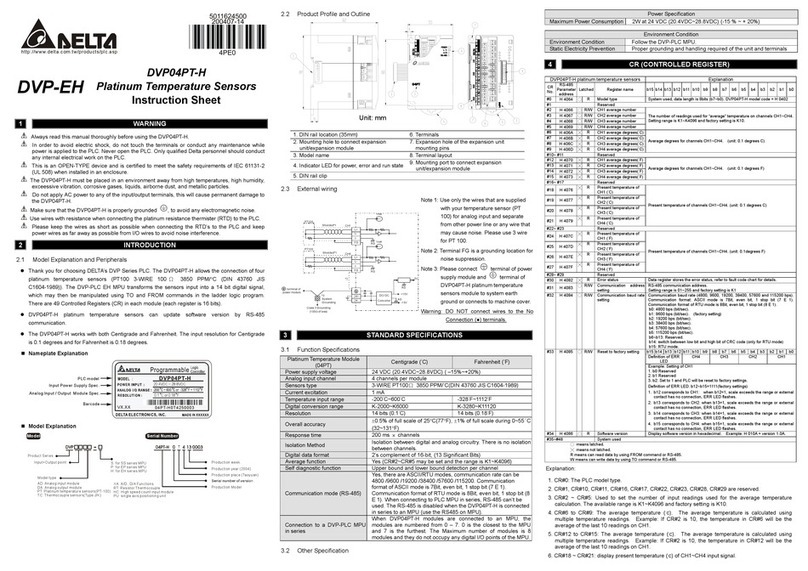
Delta
Delta DVP-EH User manual
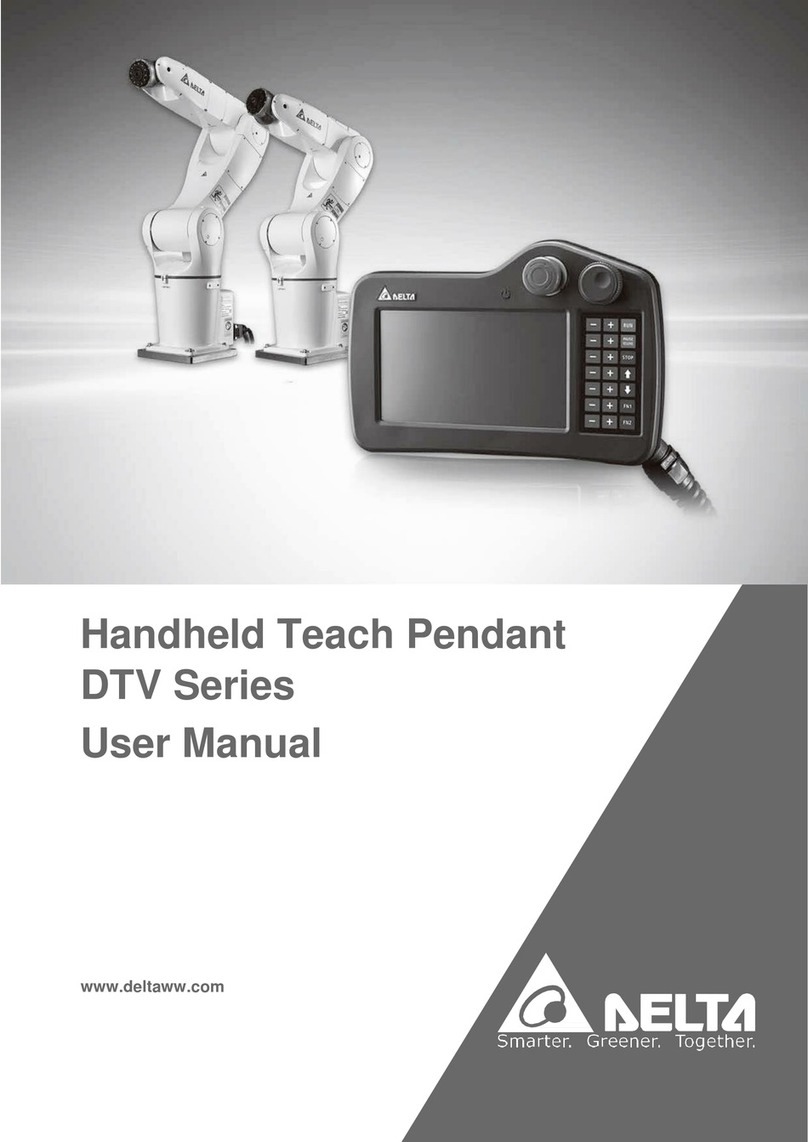
Delta
Delta DTV Series User manual

Delta
Delta DVP-SA2 User manual
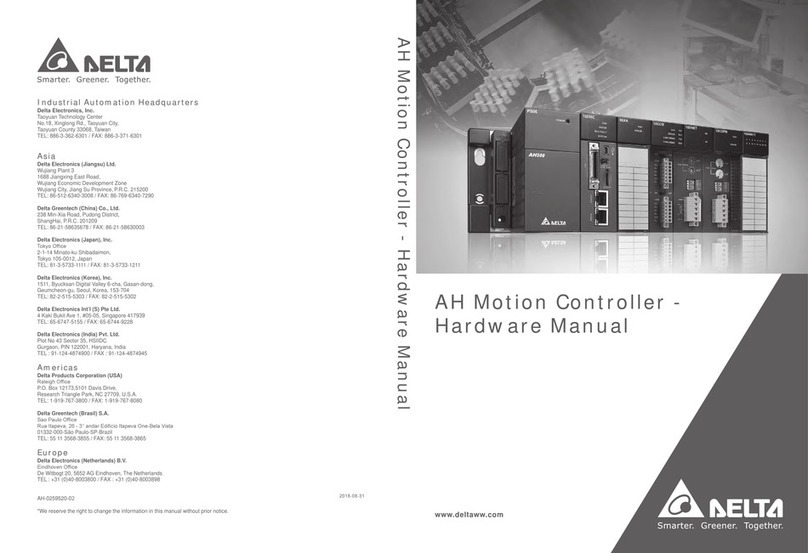
Delta
Delta AH Series User manual
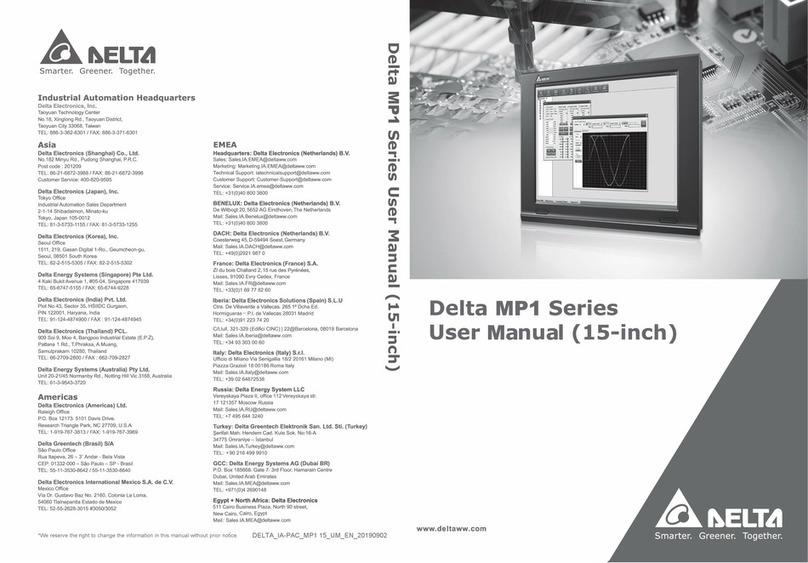
Delta
Delta MP1 Series User manual

Delta
Delta DVP-SX2 User manual
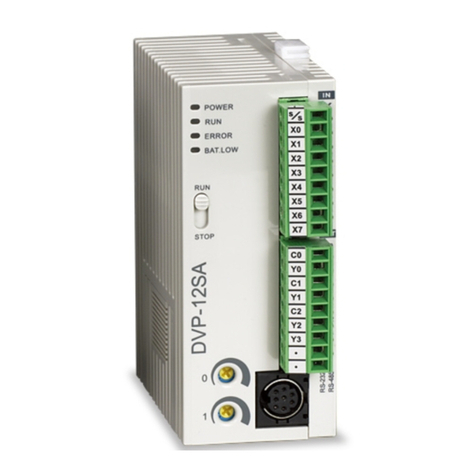
Delta
Delta DVP08SM11N User manual
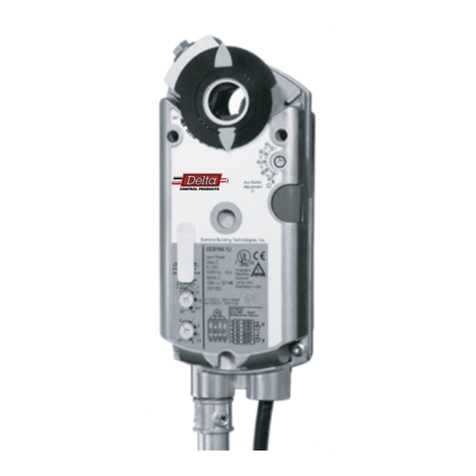
Delta
Delta DC-132 Series User manual