ENDA ETS762 User manual

Counting inputs
(INA, INB) 3 channels (5V to 30V pulses)
40ms, 20ms, 10ms, 1ms, 0.5ms, 0.1ms, 50 (selectable by programming)ms
* 72x72mm sized.
* 2x6 digits display.
* Easy to use by front panel keypad.
* On and Off times of the input pulses can be selected.
* Sampling time can be adjusted between 0.2s and 16.0s.
* Output can be energized while process value is greater or lower than the
preset value.
* Ti utput operation.
* Display configuration can be adjusted.
.
* Easy connection by removable screw terminals.
* Haing CE mark according to European Norms.
* Sensor type can be selected as PNP or NPN.
* Selectable functional reset.
* Double set-points control is made by 2 relays outputs.
me delay can be included to the o
* Output can be energized continuously or just for a time interval of 0.1
to 999.9 seconds.
* Decimal point can be adjusted between 1. and 5. digits.
* Prescaler factor can be adjusted between 0.00001 and 999.999 for calibration.
* Parameter access protection on 3 levels
Minimum On and Off times
for pulses
ENDA ETS762 TACHO LINE/SPEED METER
Thank you for choosing ENDA ETS762 TACHOMETER.
INPUTS
Adjustable between 0.2s and 16.0s.
Sampling time
1/5 ETS762-E-03
ENDA
PRESET TACHO/LINE SPEED METER
IN A IN B OUT1 OUT2
PRESET RESET
SET
ETS762
Read this document carefully before using this device. The guarantee will be expired by
damaging of the device if you don't attend to the directions in the user manual. Also we don't
accept any compensations for personal injury, material damage or capital disadvantages.
ENVIRONMENTAL CONDITIONS
Height Max. 2000m
Ambient/storage temperature
Max. relative humidity
0 ... +50°C/-25 ... +70°C (with no icing)
Rated pollution degree
TECHNICAL SPECIFICATIONS
80% up to 31 decreasing linearly 50% at 40 .°C °C
According to EN 60529 Front panel : IP60
Rear panel : IP20
Do not use the device in locations subject to corrosive and flammable gases.
Supply 230V AC +%10 -%20, 50/60Hz or 24V AC ±%10, 50/60Hz or optional 9-30V DC SMPS module.
Power consumption Max. 7VA
2.5mm² screw-terminal connections
Wiring
Date retention
EMC
Safety requirements
EN 61326-1: 1997, A1: 1998, A2: 2001 (Performance criterion B for the EMC standard)
EEPROM (Min. 10 years)
EN 61010-1: 2001 (pollution degree 2, overvoltage category II)
ELECTRICAL CHARACTERISTICS
OUTPUTS
Control output (OUT1) Relay : 250V AC, 2A (for resistive load), NO+NC
Control output (OUT2)
Open collector output (S.S. OUT1): Max. 30V DC, 100mA.
Relay : 250V AC, 2A (for resistive load), NO+NC
Auxiliary power supply
Open collector output (S.S. OUT2): Max. 30V DC, 100mA.
12V DC, Max. 50mA (without regulation)
.Mechanical 30.000.000 operation; Electrical 300.000 operation
Life expectancy for relays
Note : Relay and S.S.OUT outputs are in synchronization . When OUT1 relay is energized S.S. OUT1 transistor goes into saturation.
Similarly, when OUT2 relay is energized S.S. OUT2 transistor goes into saturation.
HOUSING
Housing type Suitable for flush-panel mounting according to DIN 43 700.
Dimensions W72xH72xD97mm
Weight Approx. 405g (after packing)
Enclosure material Self extinguishing plastics
While cleaning the device, solvents (thinner, benzine, acid etc.) or corrosive materials must not be used.
PNP: 5V to 30V pulse with adjustable pulse time between 2ms and 50ms.
NPN: GND terminal is connected to the RESET IN or HOLD IN terminal.
RESET and HOLD inputs
Accuracy ±%0.1
Supply Voltage Order Code
230V AC +%10 -%20 ETS762
24V AC ±%10 ETS762-24AC
9-30V DC SMPS module ETS762-12AC

TERMS
( 2 ) Digital display
( 4 ),( 5 ),( 6 ),( 7 ) Keypad
Panel cut-out
Connection
cables
Depth
97mm 75mm
84mm
DIMENSIONS
68 mm
+0.7
68 mm
+0.7
Rubber packing
Flush mounting
clamp
Panel
72mm
78mm
1
2
2/5 ETS762-E-03
ENDA
PRESET TACHO/LINE SPEED METER
IN A IN B OUT1 OUT2
PRESET RESET
SET
ETS762
ENDA
PRESET TACHO/LINE SPEED METER
IN A IN B OUT1 OUT2
PRESET RESET
SET
ETS762
3HOLD IN
4 RESET IN
5 S.S. OUT2
6 S.S. OUT1
7 IN B
8 IN A
9 GND
10 +12V 50mA
11
12
13
14
15
16
17
18
OUT1
AC 250V 2A
RESISTIVE
LOAD
OUT2
AC 250V 2A
RESISTIVE
LOAD
ENDA
INDUSTRIAL
ELECTRONICS
ETS762
SN: XXXXXXXXX
230V AC +10% -20%
50/60Hz 7VA
3HOLD IN
4 RESET IN
5 S.S. OUT2
6 S.S. OUT1
7 IN B
8 IN A
9 GND
10 +12V 50mA
11
12
13
14
15
16
17
18
OUT1
AC 250V 2A
RESISTIVE
LOAD
OUT2
AC 250V 2A
RESISTIVE
LOAD
ENDA
INDUSTRIAL
ELECTRONICS
ETS762-24AC
SN: XXXXXXXXX
24V AC ±10%
50/60Hz 7VA
input
type
Set.dsp.
config
Digital display (1) : 9.1mm
Digital display (2) : 7.1mm
4 red LEDs
6 digits, seven segment red LED
6 digits, seven segment yellow LED
Micro switch
Character height
( 3 ) State indicators
( 1 ) Digital display
- Push up the flush-mounting
clamp in direction 1as
shown in the figure above.
- Then, pull out the clamp in
direction 2.
For removing mounting clamps:
Note 1) While panel mounting, additional distance required for
connection cables should be considered.
2) Panel thickness should be maximum 10mm.
3) If there is no 90mm free space at back side of the device,
it would be difficult to remove it from the panel.
CONNECTION DIAGRAM
ENDA ETS762 is intended for installation in control panels. Make sure that the device is used only for intended
purpose. During an installation, all of the cables that are
connected to the device must be free of energy. The device must be protected against inadmissible humidity,
vibrations, severe soiling and make sure that the operation temperature is not exceeded. All input and output
lines that are not connected to the supply network must be laid out as shielded and twisted cables. These cables
should not be close to the power cables or components.
The shielding must be grounded on the instrument side.
The installation and electrical connections must be
carried on by a qualified staff and must be according to the relevant locally applicable regulations.
12
11
184-253V AC
50/60Hz 7VA
Switch
Fuse
F 100 mA
250V AC
Neutral
Line
SUPPLY :
NOTE :
Fuse should
be connected.
230V AC Supply
Cable size: 1,5mm²
1) Mains supply cords shall meet the requirements of IEC 60227
or IEC 60245.
2) In accordance with the safety regulations, the power supply
switch shall bring the identification of the relevant instrument
and it should be easily accessible by the operator.
Note :
Holding screw 0.4-0.5Nm Equipment is protected throughout
by DOUBLE INSULATION.
(3) State indicators shows the state of the device.
(7) Used for selecting run or programming modes or for adjusting parameters.
(4) Used for adjusting the preset values in the run mode.
Increment or parameter selection key during programming mode.
(5) Decrement or reset key in the run mode.
Decrement or parameter selection key during programming mode
(6) Used for selecting preset1, preset2 or user defined message in the run mode.
Used for selecting oPtion. s or parameter to be changed in the programming mode.
(2)
The value of the parameter selected by parameter during run mode.
Parameter value during programming mode.
(1) The value of the measurement selected by parameter during run mode.
Parameter name during programming mode.

PRESET
SET
Run mode
Process value defined by the parameter is shown on the top display.
Variable selected by the parameter is shown on the bottom
Preset value for out1.
See NOTE 1 for programming.
Preset value for out2.
See NOTE 1 for programming.
PRESET
PRESET
outPut
oPtýon. PRESET
dýsP.
oPtýon.
SEcur.
oPtýon.
There are eight different input types.
Measurement methods for different input
types are on the next page.
See NOTE 2 for adjustment.
Minimum On and Off times for the input
pulses can be selected.
See NOTE 2 for adjustment.
Sensor type can be selected.
See NOTE 2 for adjustment.
There are 4 different output types for out1 and out2.
If output type is selected lo, output is energized under
prset value. In contrary, if it
is selected Hi, output is
energized over prset value.
See NOTE 2 for adjustment.
out1 pulse time can be adjusted between 0.1 and 999.9s .
If it is adjusted to 0.0, out1 is energized continuously when
process value reaches PrSEt1 value.
.See NOTE 1 for adjustment
out2 pulse time can be adjusted between 0.1 and 999.9s .
If it is adjusted to 0.0, out2 is energized continuously when
process value reaches PrSEt2 value.
See NOTE 1 for adjustment.
A time delay between 0.0 and 999.9s can be included to the
operation of out1. If process value do not stay over prset1
value for a time interval less than time delay, out1 will not be
energized.
See NOTE 1 for adjustment.
A time delay between 0.0 and 999.9s can be included to the
operation of out2. If process value do not stay over prset2
value for a time interval less than time delay, out2 will not be
energized.
See NOTE 1 for adjustment.
RESET
Calibration (prescaler) value can be adjusted between 0.00001
and
To change the position of decimal point, press and
keys for 0,6s.
999.999. Process value is multiplied by prescaler value
and the result is displayed on the screen.
See NOTE 1 for adjustment.
Decimal point can be adjusted between 1. and 5. digits.
If desired, decimal point is not included.
See NOTE 2 for adjustment.
Display configuration can be selected.
See NOTE 2 for adjustment.
Measurement unit, a message, a constant etc. should be entered
by the user.
See NOTE 1 for adjustment.
If the duration of the pulses at the input is
shorter than the selected minimum pulse time,
this error message appears.
IN A
If the duration of the pulses at the input IN B is
shorter than the selected minimum pulse time,
the error message appears.
If no signal is detected at the input AIN during the
selected limit time, this error message appears.
If no signal is detected at the input IN B during the
selected limit time, this error message appears.
If both IN A and IN B are required in a measurement
methods and no signal is detected at the both inputs
during the selected limit time, this error message
appears.
Overflow error.
Indicates that process value
was greater than 999 999.
RESET RESET
The time base used changes depending
on the selected measurement method.
See NOTE 2 for adjustment.
Sampling time can be selected.
Sampling time defines the time interval
for successive refreshing of the display.
See NOTE 2 for adjustment.
If no input signal is detected during the
defined limit time, an error message
appears on the display.
See NOTE 2 for adjustment.
Minimum pulse time for the external
reset input can be selectable.
See NOTE 2 for adjustment.
PARAMETER TABLE
output oPTIoN.
DisP. oPTIoN.
SEcur. oPTIoN.
inPut
typE
input
t.base
micro
second
meter
per.sec.
rotate
per.sec.
meter
per.min.
rotate
per.min.
meter
per.hr.
rotate
per.hr.
mili
second
0.1
second
Tacho.
Tacho.
inA-inB.
ratio
in1-in2.
ratio
line
speed.
line
speed.
period
period
time
inter
out1.lo.
out2.lo.
out1.Hi.
out2.Hi.
out1.Hi.
out2.lo.
out1.lo.
out2.Hi.
time
inter
PUls
time
PUls
time
Count.
per.pls.
Count.
per.Cyc.
dEci.
Point
output
config
diSP.
CAL.
out1
PULs.ti.
set.dsp.
config. prset1 prset2
User
define
out2
pUls.t2
User
define.
inP.opt
seCUr.
dSP.oPt.
seCUr.
out.oPt.
seCUr.
nonE
Prog.
no
Prog.
yES
nonE
Prog.
no
Prog.
yES
nonE
Prog.
no
Panel
reset
Prog.
yES
reset
input
SEcur.
codE 1111
0 0.0 0.00 0.000 0.0000 0.00000
000..0
000..0
000..0
000..0
0.00001
.............
.............
.............
.............
.............
999.9
999.9
999.9
999.9
999.999
dEFAuL.
SEt.
disp.
resEt.
no
no
yES
reset
both
3/5
SET
99999
100000
PrSEt1
100000
PRESET
PRESET
RESET
RESET
RESET
RESET
RESET
RESET
RESET
ýnPut
oPtýon.
out1
del.ti
out2
del.ti
prset1
equ.
prset1 Pr2.sub
pr1
input oPTIoN.
reset
puls
0.002
second
0.005
second
0.010
second
0.020
second
0.050
second
limit
time 1
0.2
100
16.0
0.04
second
0.02
second
0.01
second
0.001
second
0.0005
second
0.0001
second
0.00005
second
npn pnp
Puls
time
sensor
type
sample
time
ETS762-E-03
PrSEt2
150000
input
type
input
type
RESET
output
config.
input
t.base
Puls
time
Sensor
type
sample.
time
Limit
time
reset
puls
RESET RESET
RESET
RESET
RESET
RESET
deci.
point.
secur.
Code.
inp.opt.
seCUr.
out.opt.
seCUr.
dsp.opt.
seCUr.
disp.
reset
defaul.
set
puls
err.ýna
puls
err.ýnb
ýna no
puls
ýnb no
puls
ýna.ýnb.
no.puls
HýgH.
input
RESET
disp.
CAl
RESET
set.dsp.
config.
set.dsp.
config.
User.
define.
RESET
out1
pUls.tý
RESET
out2
PUls.tý
RESET
out1
del.tý
RESET
out2
del.tý
prset1
eqU.
&
This menu appers, If or is selected
as input type input.
This menu appers, If , or is
selected as input type.
This menu appears if selected as input type.
Measurement unit, a message, a constant etc. entered by the user appears.
ERROR MESSAGES
PRESET
SET
if key is pressed while holding key, the
programming mode is entered.
Pr2.Sub.
Pr1
= Output is energized when measured value reaches PrSEt1
value.
= The difference between PrSEt2 and PrSEt1 becomes the new
value of PrSEt1'. It means -
Now, o
PrSEt1 (new) = PrSEt2 PrSEt1(old).
utput is energized when process value reaches
PrSEt1(new) value.
See NOTE 2 for adjustment.
PrSEt1
Access code for entering security option menu.
This parameter should be 1111.
See NOTE 2 for modification.
Prog.
yES
Prog.
yES
nonE
nonE
Prog.
no
Prog.
no
no
reset
both
See NOTE 2. for modification.
PAnE.
reSEt
reSEt
inPut.
While leaving the programming mode,
no = All the modifications are saved.
Yes = Default values are set to parameters.
See NOTE 2. for modification.
Prog.
yES
nonE
Prog.
no
= No menu is seen.
= No menu is seen.
= No menu is seen.
See NOT 2. for adjustment.
See NOT 2. for adjustment.
See NOT 2. for adjustment.
= Menu is seen but can not be programmed.
= Menu is seen and programming is possible.
= Menu is seen but can not be programmed.
= Menu is seen and programming is possible.
= Menu is seen but can not be programmed.
= Menu is seen and programming is possible.
= Display can not be reset.
= Both RESET input and the key can
be used for resetting.
= Display
= Display can be reset by the RESET input.
can be reset by key.
RESET
RESET
PARAMETER ADJUSTMENT METHOD
To modify non-mumerical parameters, hold key and use keys.
SET
RESET
SET
PRESET RESET
SET
RESET
SET
NOTE 1
NOTE 2
Holding key the value of the selected parameter is seen on the display. While holding key, the value of the selected parameter can be
changed by using keys. In order to reset all the digits, first press and hold key. And then, press both and keys together.
SET SET SET SET
SET
1.00000
1.00000
1.00000
1.01000
1.00000
PRESET RESET
PRESET
Selected
numerical
parameter

MEASUREMENT METHODS ACCORDING TO INPUT TYPES
inPut
tyPE
tacho
inA.inb
ratio
Line
speed
time
inter.
pUls
time.
Count
per.pls.
Count
per.CYc.
period
IN A input
IN A input
IN A input
IN A input
IN A input
IN A input
IN inputA
IN inputA
IN B input
IN inputB
IN inputB
HOLD IN input
HOLD IN input
HOLD IN input
IN inputB
IN Binput
RESET IN
RESET IN
H
H
H
H
H
H
H
H
1
1
2
2
3
3
4
4
5
5
6
6
7
7
8
8
9
9
1
1
2
2
3
3
4
4
5
5
6
6
7
7
8910
8 9 10 11 12 13
H
H
H
H
H
H
H
H
H
H
H
L
L
L
L
L
L
L
L
L
L
L
L
L
L
L
L
L
L
L
Note: should be selected according to the minimum On and Off times of the input pulses.
Note: should be selected according to the minimum On and Off times of the input pulses.
Note: should be selected according to the minimum On and Off times of the input pulses.
Note: should be selected according to the minimum On and Off times of the input pulses.
Note: should be selected according to the minimum On and Off times of the input pulses.
Note: should be selected according to the minimum On and Off times of the input pulses.
Note: should be selected according to the minimum On and Off times of the input pulses.
Note: should be selected according to the minimum On and Off times of the input pulses.
Revolution measurement method (rpm: revolution/minute)
4/5 ETS762-E-03
Process value
Process value
Process value
Process value
Process value
Process value
Process value
Process value
Previous value
Previous value
Previous value
Previous value
Previous value
Previous value
Previous value
Previous value
process value do not changes
process value do not changes
process value do not changes
(T1+T2+ ..... +Tn)/n
T1
Counting value: 9
Counting value: 9
T2
Counting value: 9
Counting value : 13
(1/T1x60) rpm
(1/Ta) / (1/Tb)
(1/T1x60)m/dk.
T1
(1/T2x60)m/dk.
T2.
(1/T3x60)m/dk.
T3
(1/T2x60) rpm (1/T2x60) rpm
T1
Ta
T1
T1
T1
T1
T
T
T
T
T2
sampling time
Tn
T2
Td
Td
T
T3 T4
T4
ZERO
ZERO
Tb Tb Tb Tb
T2
Ta
Td
Td
T3
Ta
T2
T2
Td
Td
T3
T3
Ratio of the revolutions of IN A and IN B
Speed measurement method
Time difference measurement method
Pulse duration measurement method
Pulse counting method
Pulse counting method
Period measurement method
second
second
second
second
second
second
second
second
second
second
second
second
second
second
second
second
second
out1.Hi
out2.Hi
999,999
Reset
Preset1
Out1
Out2
Preset2
0
out1
del.ti
out2
del.ti
out1.lo
out2.lo
999,999
Reset
Preset2
Out1
Out2
Preset1
0
out1
del.ti
out1
del.ti
out2
del.ti
out2
del.ti
out1.Hi.
out2.lo.
999,999
Reset
Preset2
Out1
Out2
Preset1
0
out1
del.ti
out2
del.ti out2
del.ti
out1.lo.
out2.Hi.
999,999
Reset
Preset1
Out1
Out2
Preset2
00
out1
del.ti
out2
del.ti
out1
del.ti
OUTPUT TYPES
T³20ms
T³20ms
Td³20ms
out2
puls.ti. out2
puls.ti.
Adjusting or to a value between 0.1 and 999.9 seconds,
a pulse output is obtained.
Adjusting or to 0.0, a continuous output is obtained.
out1
Puls.ti. out1
puls.ti.
1
7
8
2
3
4
5
6
Puls
time
Puls
time
Puls
time
Puls
time
Puls
time
Puls
time
Puls
time
Puls
time
output
config.
output
config.
output
config.
output
config.
=
==
=

PNP PROXIMITY SWITCH
GND
OUT
+ 12V
PNP PROXIMITY SWITCH
PNP PROXIMITY SWITCH
GND
+ 12V
+ 12V
GND
OUT
OUT
TYPICAL SENSOR CONNECTIONS
TERMINAL CONNECTIONS
Terminal descriptions
3 : Hold input
4 : Reset input
5 : Solid state out2 (Max 30V 100mA open collector NPN)
6 : Solid state out1 (Max 30V 100mA open collector NPN)
7 : IN A input (Max 30V 10kHz)
8 : IN B i input (Max 30V 10kHz)
9 : GND
10 : +12V 50mA auxiliary power supply
11,12 : SUPPLY inputs
13,14,15 : 1. relay output (Max 2A 250V AC)
16,17,18 : 2. relay output (Max 2A 250V AC)
SÝSEL MÜHENDÝSLÝK ELEKTRONÝK SAN. VE TÝC. A.Þ.
Yukarý Dudullu 34775 - ÜMRANÝYE/ÝSTANBUL-TÜRKÝYE
Tel : +90 216 499 46 64 Pbx. Fax : +90 216 365 74 01
url : www.enda.com.tr
Barbaros Cad. Kutup Sok. No:20
5/5 ETS762-E-03
230V AC Supply
Switch
Cable size: 1,5mm²
Fuse
F 100 mA
250V AC
230V AC Supply
Switch
Cable size: 1,5mm²
Fuse
F 100 mA
250V AC
3HOLD IN
4 RESET IN
5 S.S. OUT2
6 S.S. OUT1
7 IN B
8 IN A
9 GND
10 +12V 50mA
11
12
13
14
15
16
17
18
OUT1
AC 250V 2A
RESISTIVE
LOAD
OUT2
AC 250V 2A
RESISTIVE
LOAD
ENDA
INDUSTRIAL
ELECTRONICS
ETS762
SN: XXXXXXXXX
230V AC +10% -20%
50/60Hz 7VA
3HOLD IN
4 RESET IN
5 S.S. OUT2
6 S.S. OUT1
7 IN B
8 IN A
9 GND
10 +12V 50mA
11
12
13
14
15
16
17
18
OUT1
AC 250V 2A
RESISTIVE
LOAD
OUT2
AC 250V 2A
RESISTIVE
LOAD
ENDA
INDUSTRIAL
ELECTRONICS
ETS762
SN: XXXXXXXXX
230V AC +10% -20%
50/60Hz 7VA
3HOLD IN
4 RESET IN
5 S.S. OUT2
6 S.S. OUT1
7 IN B
8 IN A
9 GND
10 +12V 50mA
11
12
13
14
15
16
17
18
OUT1
AC 250V 2A
RESISTIVE
LOAD
OUT2
AC 250V 2A
RESISTIVE
LOAD
ENDA
INDUSTRIAL
ELECTRONICS
ETS762
SN: XXXXXXXXX
230V AC +10% -20%
50/60Hz 7VA
NOTE: NPN PROXIMITY SWITCH connection is the same as PNP PROXIMITY SWITCH connection.
Table of contents
Other ENDA Measuring Instrument manuals
Popular Measuring Instrument manuals by other brands
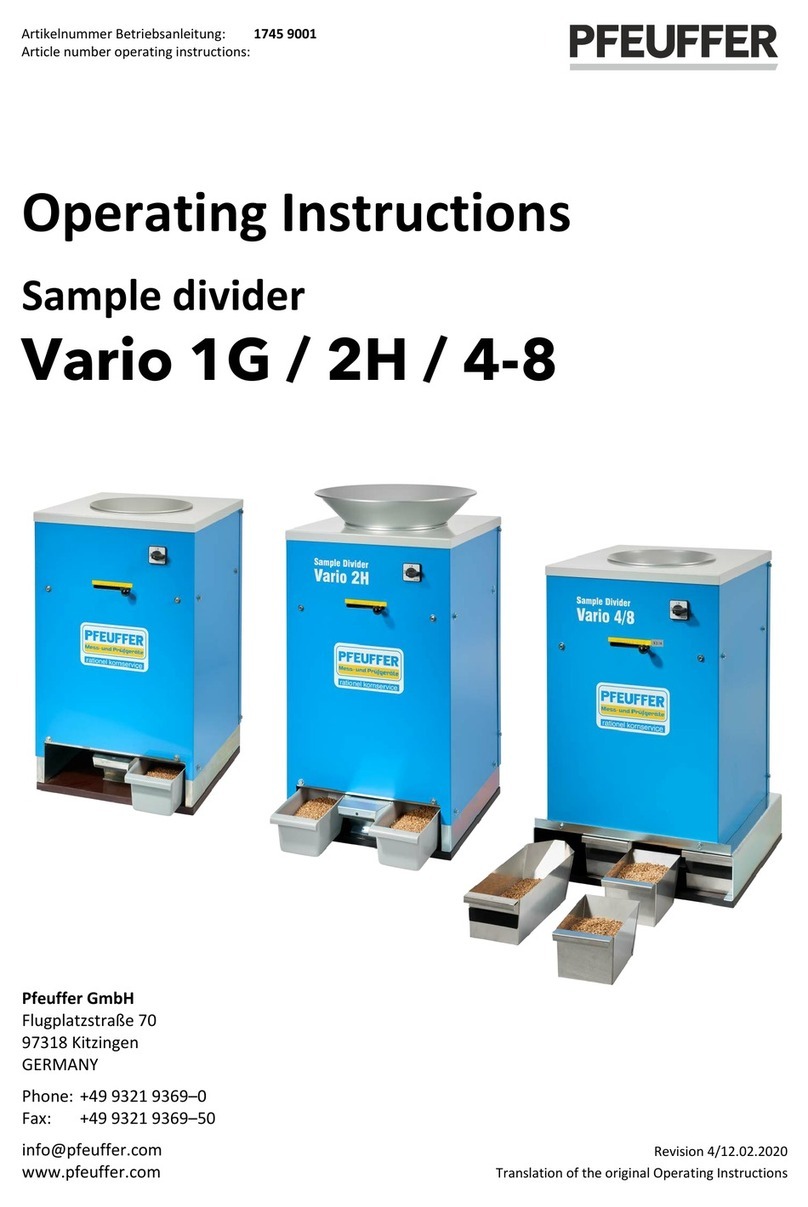
Pfeuffer
Pfeuffer Vario 1G operating instructions
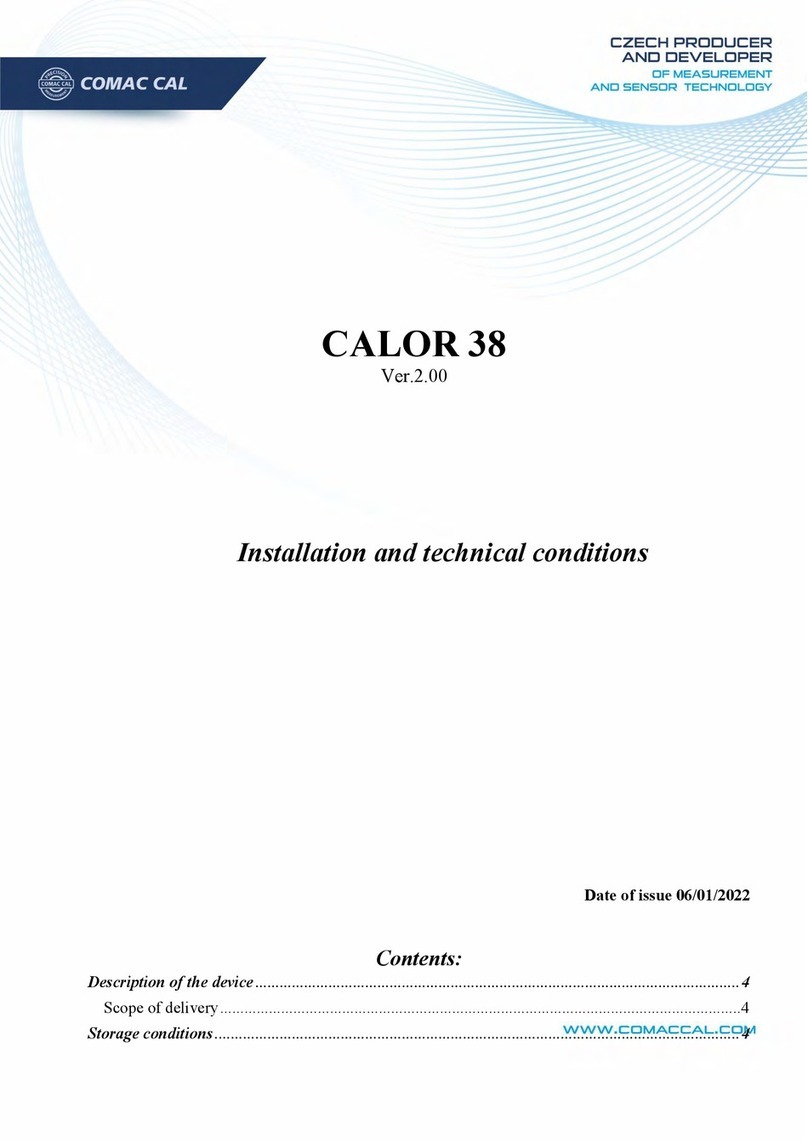
COMAC CAL
COMAC CAL CALOR 38 Installation and technical conditions
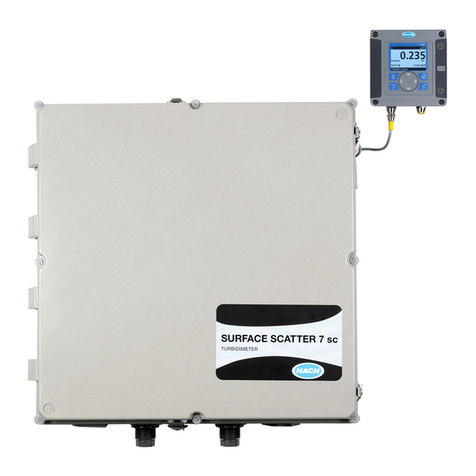
Hach
Hach Surface Scatter 7 sc user manual
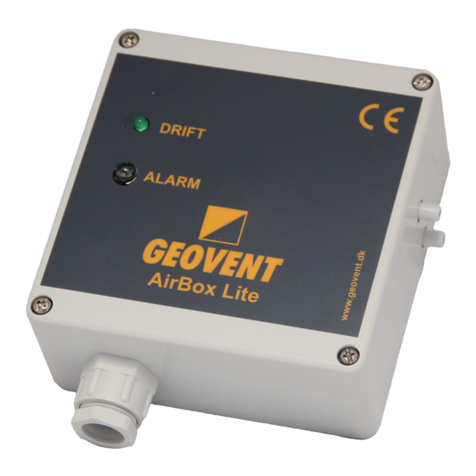
Geovent
Geovent Airbox Lite instruction manual
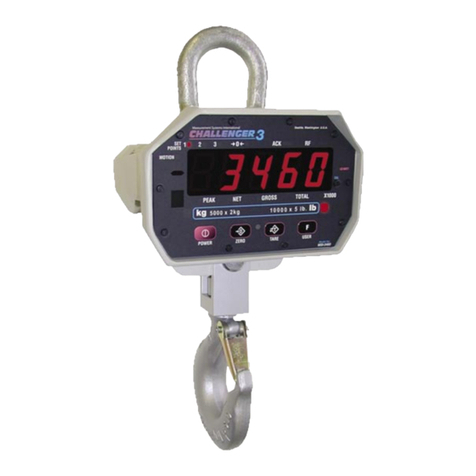
Measurement Systems International
Measurement Systems International MSI3460 user guide

Pentax
Pentax W-800 Series Basic instruction manual
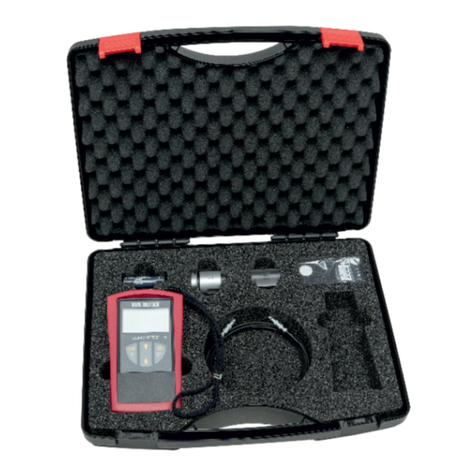
KARL DEUTSCH
KARL DEUTSCH ECHOMETER 1077.080-A operating instructions
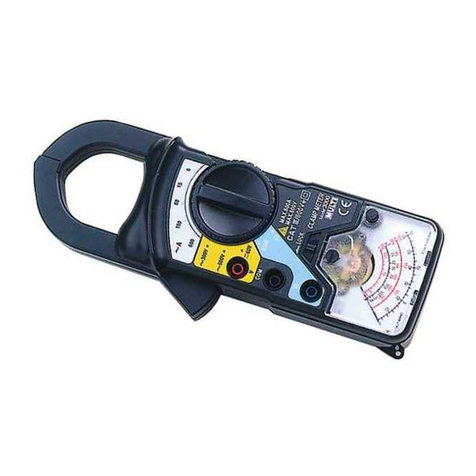
MULTI MEASURING INSTRUMENTS
MULTI MEASURING INSTRUMENTS M-3000 instruction manual
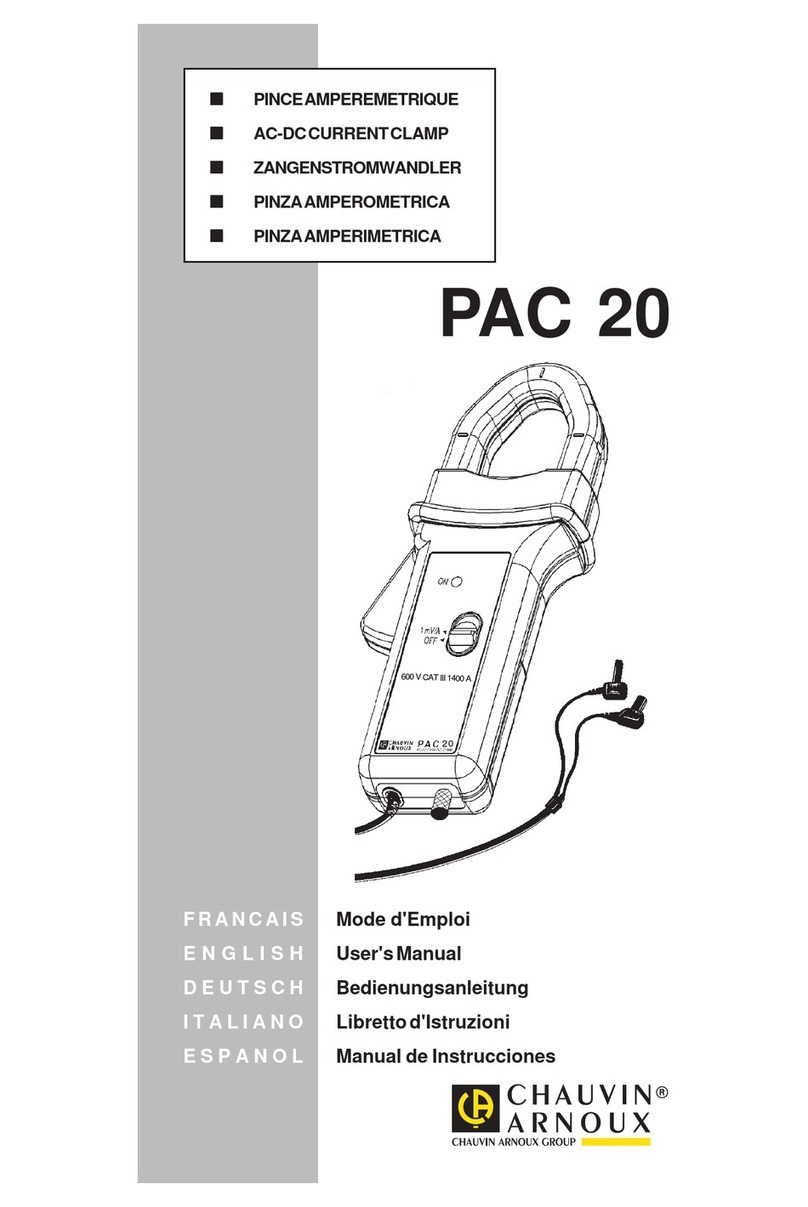
Chauvin Arnoux
Chauvin Arnoux PAC 20 user manual
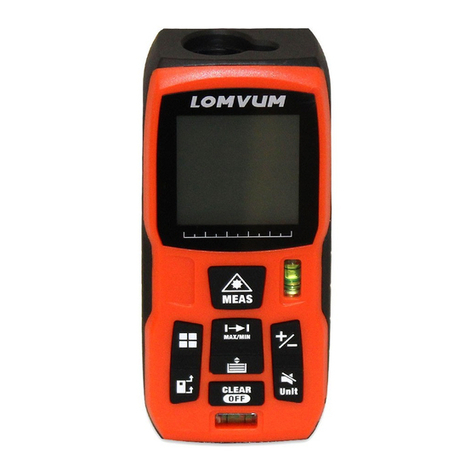
LOMVUM
LOMVUM LV Series user guide

ACOEM
ACOEM Fixturlaser SMC BALANCER Quick tips
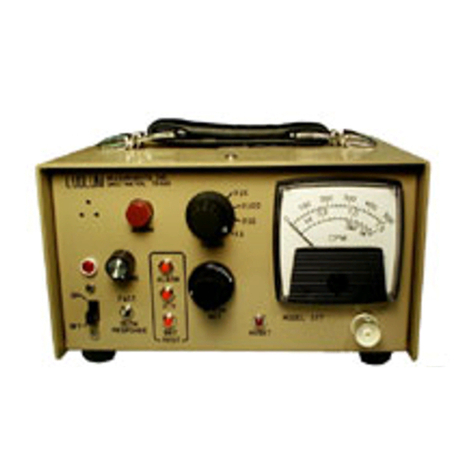
Ludlum Measurements
Ludlum Measurements 177 manual